Объявление о защите кандидатской диссертации
Вид материала | Автореферат |
- Объявление о защите кандидатской диссертации, 317.31kb.
- Объявление о защите кандидатской диссертации, 208.4kb.
- Диссертация принята к защите 21. 05. 2009 г. Текст объявления о защите диссертации, 3414.73kb.
- Научно-исследовательская работа и выполнение кандидатской диссертации 110 недель Подготовка, 76.87kb.
- Структура диссертации, 1163.53kb.
- Ответы на вопросы Сколько времени должно пройти после опубликовании статьи, чтобы она, 9.98kb.
- Фамилия, имя, отчество, 61.64kb.
- Кандидатской диссертации: "Решение задач комбинаторного характера как средство развития, 18.33kb.
- Межлабораторные семинары отдела экологии и микробиологии иоэб со ран время, 11.06kb.
- Е. В. Гладченко (Доклад по материалам кандидатской диссертации) Вдоклад, 8.66kb.
ОБЪЯВЛЕНИЕ О ЗАЩИТЕ КАНДИДАТСКОЙ ДИССЕРТАЦИИ
Ф.И.О | Берстнев Александр Александрович |
Название диссертации | Повышение качества поверхности точных отливок из жаропрочных сталей совершенствованием технологического процесса литья по выплавляемым моделям |
Специальность | 05.16.04 - «Литейное производство» |
Отрасль науки | Технические науки |
Шифр совета | Д 212.110.05 |
Тел. ученого секретаря | (499)141-9495 |
| a_paltievich@mati.ru |
Предполагаемая дата защиты | 29 октября 2009 |
Место защиты диссертации | Оршанская, 3, ауд. 523А |
Автореферат и текст объявления были размещены на сайте «МАТИ»−Российского государственного технологического университета им. К.Э.Циолковского в сети Интернет 28 сентября 2009 года.
Ученый секретарь
диссертационного совета А.Р. Палтиевич
На правах рукописи
БЕРСТНЕВ АЛЕКСАНДР АЛЕКСАНДРОВИЧ
ПОВЫШЕНИЕ КАЧЕСТВА ПОВЕРХНОСТИ
ТОЧНЫХ ОТЛИВОК ИЗ ЖАРОПРОЧНЫХ СТАЛЕЙ
СОВЕРШЕНСТВОВАНИЕМ ТЕХНОЛОГИЧЕСКОГО
ПРОЦЕССА ЛИТЬЯ ПО ВЫПЛАВЛЯЕМЫМ МОДЕЛЯМ
Специальность 05.16.04 – Литейное производство
Автореферат
диссертации на соискание учёной степени
кандидата технических наук
Москва – 2009
Работа выполнена на кафедре «Материаловедение, литье и сварка» Государственного образовательного учреждения высшего профессионального образования «Рыбинская государственная авиационная технологическая академия имени П. А. Соловьева»
Научный руководитель: доктор технических наук, профессор
Серебряков Сергей Павлович
Официальные оппоненты: доктор технических наук
Смыков Андрей Федорович
кандидат технических наук, доцент
Гаранин Владимир Федорович
Ведущее предприятие: ОАО «НПО «САТУРН» (г. Рыбинск).
Защита состоится «29» октября 2009 года в 14 часов на заседании диссертационного Совета Д 212.110.05 в Государственном общеобразовательном учреждении высшего профессионального образования «МАТИ»– Российском государственном технологическом университете имени К.Э.Циолковского,
по адресу:
121552 Москва, ул. Оршанская, д.3, аудитория № 523А, корп. А.
С диссертацией можно ознакомиться в библиотеке «МАТИ» - РГТУ имени К. Э. Циолковского.
Телефон для справок 8-499-141-94-95.
Автореферат разослан « 22 » сентября 2009 года.
УЧЕНЫЙ СЕКРЕТАРЬ Диссертационного Совета Д 212.110.05 Кандидат технических наук, доцент Палтиевич А.Р. | ![]() |
Общая характеристика работы
Актуальность диссертации. До 60% отливок из жаропрочных сталей, изготавливаемых в керамических формах методом литья по выплавляемым моделям (ЛВМ), поражаются точечными поверхностными дефектами (ТПД), также называемыми «питтинг коррозией», «оспенными отметинами», «далматинцем», «темными пятнами», «черными точками», «разъеданием. Наличие ТПД на поверхности отливок снижает чистоту поверхности, ухудшает товарный вид литой заготовки. Глубина внедрения ТПД в отливку находится в пределах 0,1 – 1,4 мм и, часто превышают припуск на механическую обработку, а назначение дополнительных припусков снижает КИМ, увеличивает трудоемкость и себестоимость литья.
Из литературных источников известно, что ТПД формируются локальными включениями веществ, содержащих оксиды металла и формы. На данный момент единого мнения по механизму формирования этих включений нет. Преобладает точка зрения, что в основе образования ТПД лежат реакции взаимодействия металл-керамическая форма. Приводимые в литературе данные противоречивы, а современное представление о пригарообразовании, например, в исследованиях И.В. Валисовского, Ю.П. Васина, С.П. Дорошенко, Ф.Д. Оболенцева, не объясняет образование локальных повреждений поверхности отливки при её контакте с литейной формой. В связи с вышеизложенным, работа по выявлению влияния причин возникновения ТПД на отливках из жаропрочных сталей, получаемых методом ЛВМ, является актуальной. Практическая значимость темы подтверждается её выполнением в рамках НИР с ОАО НПО САТУРН (№ 587 – 00 от 19.04.2000) в 1997 – 2002 гг.
Целью работы является снижение брака отливок из жаропрочных сталей получаемых методом ЛВМ по ТПД на основе изучения технологических факторов, влияющих на их образование.
Для достижения поставленной цели требуется решение следующих задач:
1) Исследование влияния качества металла (содержание различных типов неметаллических включений (НМВ)) на пораженность отливок ТПД;
2) Исследование влияния технологических факторов (состава керамической формы, температуры заливки сплава, условий литья) на образование ТПД на отливках;
3) Изучение состава и строения ТПД;
4) Выявление механизма возникновения ТПД на стальных жаропрочных отли-вках, получаемых ЛВМ, на основании теоретических положений и экспериментальных данных;
5) Разработка и опробование практических рекомендаций по предупреждению ТПД на стальных жаропрочных отливках, получаемых ЛВМ.
Научная новизна работы заключается в следующем:
1. Определен механизм возникновения ТПД, заключающийся в проникновении неметаллических включений с расплавом при заливке, их адгезии на поверхно-сти формы и последующем физико-химическом взаимодействии с отливкой и формой;
2. Установлены закономерности пораженности отливок ТПД от состава НМВ, их содержания в металле и технологическими факторами ЛВМ;
3. Получены регрессионные зависимости, описывающие влияние технологических факторов на пораженность отливок ТПД и позволяющие прогнозировать качество поверхности стальных жаропрочных отливок.
Практическая ценность. На основе представленного механизма формирования точечных поверхностных дефектов на отливках из жаропрочных сталей для наиболее применяемых жаропрочных сталей разработаны технологические рекомендации по предупреждению ТПД, включающие:
- снижение содержания силикатов и соединений железа в форме;
- использование восстановительной атмосферы в форме при формировании отливок.
Производственное опробование. Результаты работы были внедрены на «ОАО «НПО «САТУРН», а так же используются в РГАТА им. П.А.Соловьева в учебном процессе на лекциях и практических занятиях в курсе «Производство отливок из черных и цветных сплавов».
Апробация работы. Материалы работы доложены на всероссийских научно-технических конференциях в Рыбинске в 2002 и 2007 годах.
Публикации. Основные положения работы опубликованы в 6 работах из них 2 статьи в центральных журналах «Литейное производство», «Инженерный справочник» и 1 патент на изобретение.
Структура и объем работы. Диссертационная работа изложена на 234 страницах, состоит из введения, 7 глав, заключения, библиографического списка из 105 наименований российских и зарубежных источников, 5 приложений, 40 таблиц и 125 рисунков.
ОСНОВНОЕ СОДЕРЖАНИЕ РАБОТЫ
Во введении изложена актуальность исследуемой проблемы, общая характеристика и цель работы, а также основные научные положения, выносимые на защиту.
В первой главе проведен анализ состояния вопроса по поверхностным дефектам на жаропрочных отливках. Выполнена классификация различных видов поверхностных дефектов в зависимости от причины их образования и особенностей технологии. Рассмотрены работы, посвященные образованию ТПД на отливках из жаропрочных сталей. Большинство исследователей полагают, что возникновение данного типа дефектов связано с химическим взаимодействием металл-керамическая форма. Влияние других факторов: условий литья, химического состава сплава, температуры заливки, носит противоречивый и ограниченный характер. Рассмотрены теоретические аспекты образования пригара, являющегося результатом взаимодействия металла, формы и атмосферы. Показано, что для стального жаропрочного литья по выплавляемым моделям изучение ТПД проведено в ограниченном количестве работ, а количество работ посвященных изучению взаимодействия металл-керамическая форма ничтожно мало. В результате отсутствует единое мнение о механизме и природе образования этих дефектов.
На основании литературного обзора явлений, способствующих образованию локальных поверхностных повреждений, возникающих, например, при высокотемпературной коррозии проточных частей ГТУ и некоторых литературных данных о роли НМВ в питтинг-образовании, была предложена гипотеза о НМВ, присутствующих в заливаемом металле, как источнике образования ТПД. В настоящей работе выполнена оценка достоверности данного предположения.
На основании анализа литературных данных сформулирована цель и поставлены задачи исследований.
Во второй главе приведено описание материалов и технологий, использованных в работе, а также применяемых методик исследований. В качестве основных методов исследования ТПД, НМВ, окалин и продуктов взаимодействия металл-форма использовали металлографический, микрорентгоспектральный (МРА) и рентгенофазовый анализы. Предложена методика оценки загрязненности отливок ТПД, для чего была введена количественная единица – пораженность поверхности ТПД, представляющая собой отношение площади дефектной поверхности ко всей площади поверхности стандартного образца (или отливки).
Изучение процесса заполнения полости формы проводили на специально сконструированной установке, исследования проводились на основных типах литнико-питающих систем (ЛПС) при использовании реальных керамических форм.
В качестве рабочих составов керамических оболочек использовались как базовые составы керамических форм, рекомендуемые для точного литья по ВМ отливок из жаропрочных сталей – маршалитовый (наполнитель огнеупорной суспензии маршалит, обсыпка кварцевый песок), электрокорундовый (наполнитель огнеупорной суспензии электрокорунд, обсыпка электрокорунд), дистенсиллиманитовый (наполнитель огнеупорной суспензии дистенсиллиманит, обсыпка дистенсиллиманит), цирконокорундовый (наполнитель огнеупорной суспензии циркон, обсыпка электрокорунд) и корундодистенсиллиманитовый (наполнитель огнеупорной суспензии дистенсиллиманит, обсыпка электрокорунд), так и опытные составы оболочек. В качестве связующего применялся этилсиликат 40. Исследования выполнялись на хромистой стали ЭИ 736, хромоникелевой стали ЭИ 402 и хромоникельмолибденовой стали ВНЛ 5.
Третья глава посвящена анализу процессов, происходящих при литье хро-мистой стали в керамическую форму.
Был выполнен термодинамический анализ реакций образования оксидов основных активных компонентов жаропрочных сталей, их взаимодействия с атмосферой и формой. Оценка вероятности окисления компонентов хромоникелевой стали основывалась на сравнении парциального давления кислорода в атмосфере литейной формы с давлением упругости диссоциации окисла. Расчеты показывают что, даже при плавке-заливке металла в вакууме (остаточное давление кислорода 1.33 ÷ 133.32 Па) происходит окисление основных компонентов хромоникелевой стали:
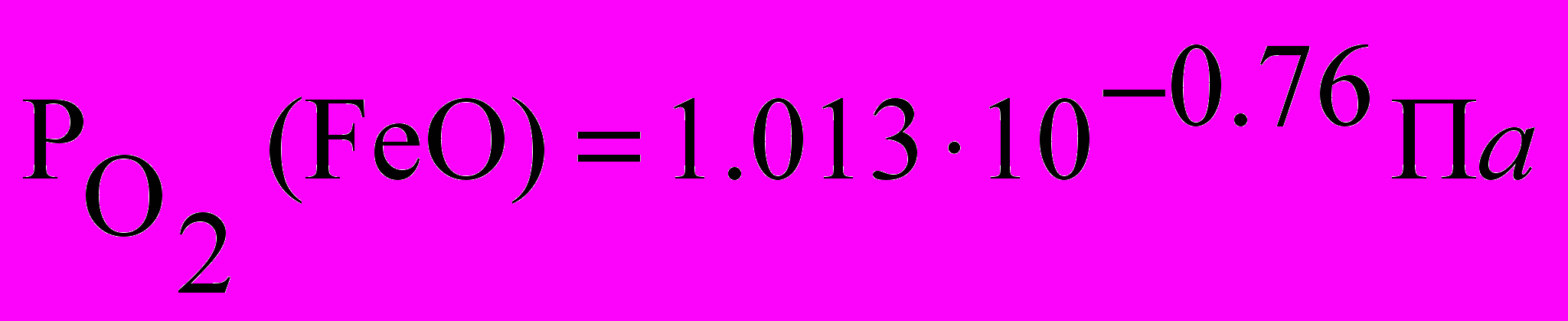

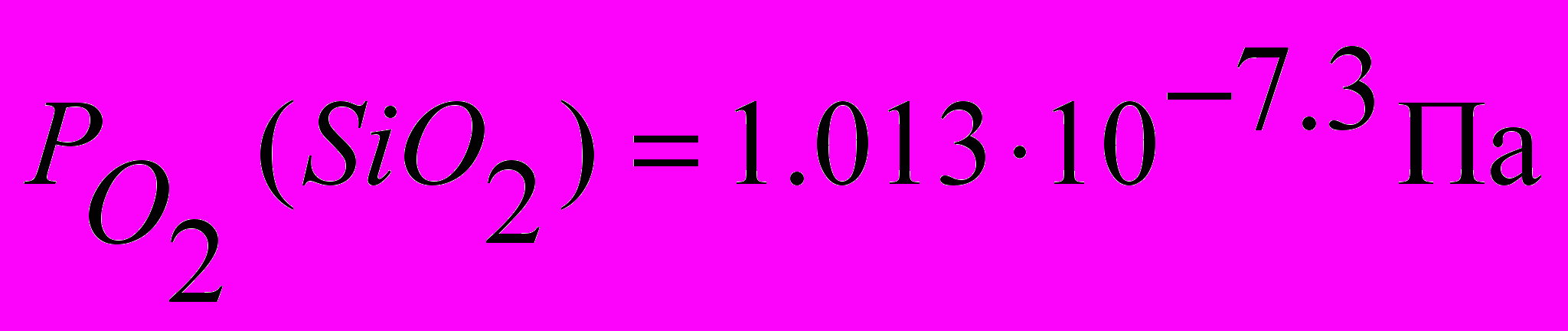

Анализ существующих методов проектирования ЛПС показал, что их конструкция ЛПС предусматривает только надежное питание отливок после заполнения форм. В ходе заполнения происходит, как правило, безнапорное течение расплава от плавильного тигля (или литейного ковша) до отливки, что повышает вероятность проникновения в отливку оксидов (НМВ) с поверхности расплава, которые могут являться источником формирования ТПД. Разработан метод расчета площади поверхности струи расплава при заливке форм по ВМ, на основе которого показано, что при заливке на воздухе окисление поверхности струи стали приводит к образованию пленки оксидов толщиной 2·10-4мм, не способной сформировать ТПД.
При лабораторном физическом моделировании процесса заполнения сери-
йных литейных форм водой зафиксировано, что при всех вариантах расхода жидкости (для принципиально разных вариантов конструкции форм с литниковыми системами: вертикальный стояк, стояк – прибыль, горизонтальный коллектор, 2-х ярусный горизонтальный коллектор) движение потока на протяжении от тигля (ковша) до отливки является безнапорным. Это создает условия для проникновения в отливку НМВ, находящихся на поверхности ванны, в отливку.
Экспериментальное изучение взаимодействия твердой хромистой стали с различными по составу керамическими формами проводилось при использовании тигельного метода. Установлено, что при всех режимах экспериментов (нагрев в диапазоне от 900 до 1300°C и времени выдержки от 5 до 90 мин) высокотемпературный контакт между керамической формой и твердым металлическим образцом состоит в появлении на образце сплошного слоя окалины и её физико-химическим взаимодействием с лицевым слоем керамической формы. Таким образом, исследования показали, что взаимодействие твердого металла с формой не приводит к возникновению ТПД или дефектов, им подобных.
В четвертой главе выполнено исследование состава и строения ТПД. Металлографические исследования показали, что точечные дефекты представляют собой локальные лункообразные углубления в поверхностном слое отливки. Основу углублений составляет фаза светло- и темно- коричневого цвета, в которой произвольно расположены включения фазы белого цвета. МРА показал, что основу светло- и темно- коричневой фаз составляют кремний, марганец и железо, причем характер кривых распределения этих элементов указывает на их присутствие в дефектном участке в виде оксидных соединений состава кремний-железо и кремний-марганец; белой фазе соответствуют кривые распределения железа и хрома. Рентгенофазовый анализ выявил преобладание железа в дефектных участках поверхности в виде оксидов – магнетита, гематита (Fe3O4 и Fe2O3), файалита (Fe2SiO4) и хромита железа (FeCr2O4). Травление поверхностного слоя отливки, граничащего с точечными поверхностными дефектами, показало отсутствие каких-либо видоизмененных зон или участков в ней. В строении поверхностного слоя металла отливки, непосредственно прилегающего к точечному дефекту, присутствуют участки, указывающие на прохождение межкристаллитной коррозии, причем количество таких участков для сталей аустенитного класса (например, ЭИ 268) в 3-4 раза больше, чем для сталей мартенситного класса (ЭИ 736, ВНЛ5). Дефектная зона не приводит к изменению в строении и расположении составляющих металл фаз.
В пятой главе представлены результаты по изучению влияния технологи-ческих факторов на пораженность отливок ТПД: состава и содержания НМВ в литом металле, состава керамической формы, температуры заливки, условий литья.
Металлографические исследования показали, что основными типами НМВ для сталей ЭИ 736 и ЭИ 402 являются силикаты различного состава (рис.1). Преобладающими среди них (до 90 %) выступают силикатные включения состава кремний-железо - марганец (FeO – SiO2 – MnO) и более сложные соединения (FeO – SiO2 – MnO – Cr2O3).
К остальным включениям относятся: силикат марганца, алюмосиликаты, марганцовистое железо, корунд и хромит.
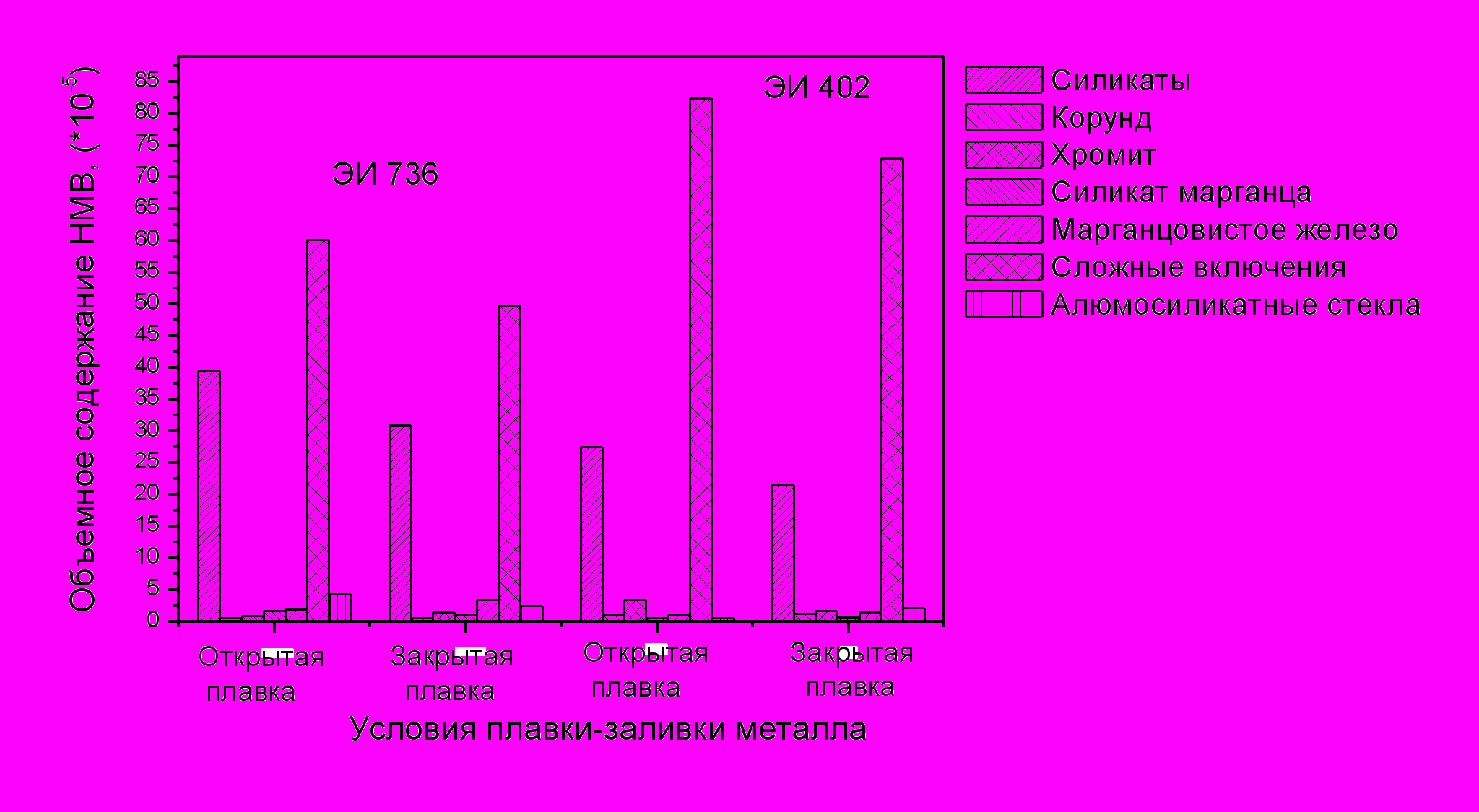
Рис. 1 Распределение НМВ в стали ЭИ 736 и ЭИ 402
При изучении влияния состава керамической формы на пораженность отливок ТПД установлено, что пораженность снижается со снижением содержания кремнезема в материалах образующих оболочку (рис.2). Наибольшая пораженность поверхности наблюдается на отливках, полученных в маршалитовых формах, наименьшая на отливках полученных в электрокорундовых формах (26 – 31 % и 11 – 18 % поверхности отливки соответственно).
Металлографические исследования показали что между точечным дефектом и керамической формой образуется металлооксидная зона, толщина кото- рой возрастает с увеличением содержания кремнезема в форме и температуры
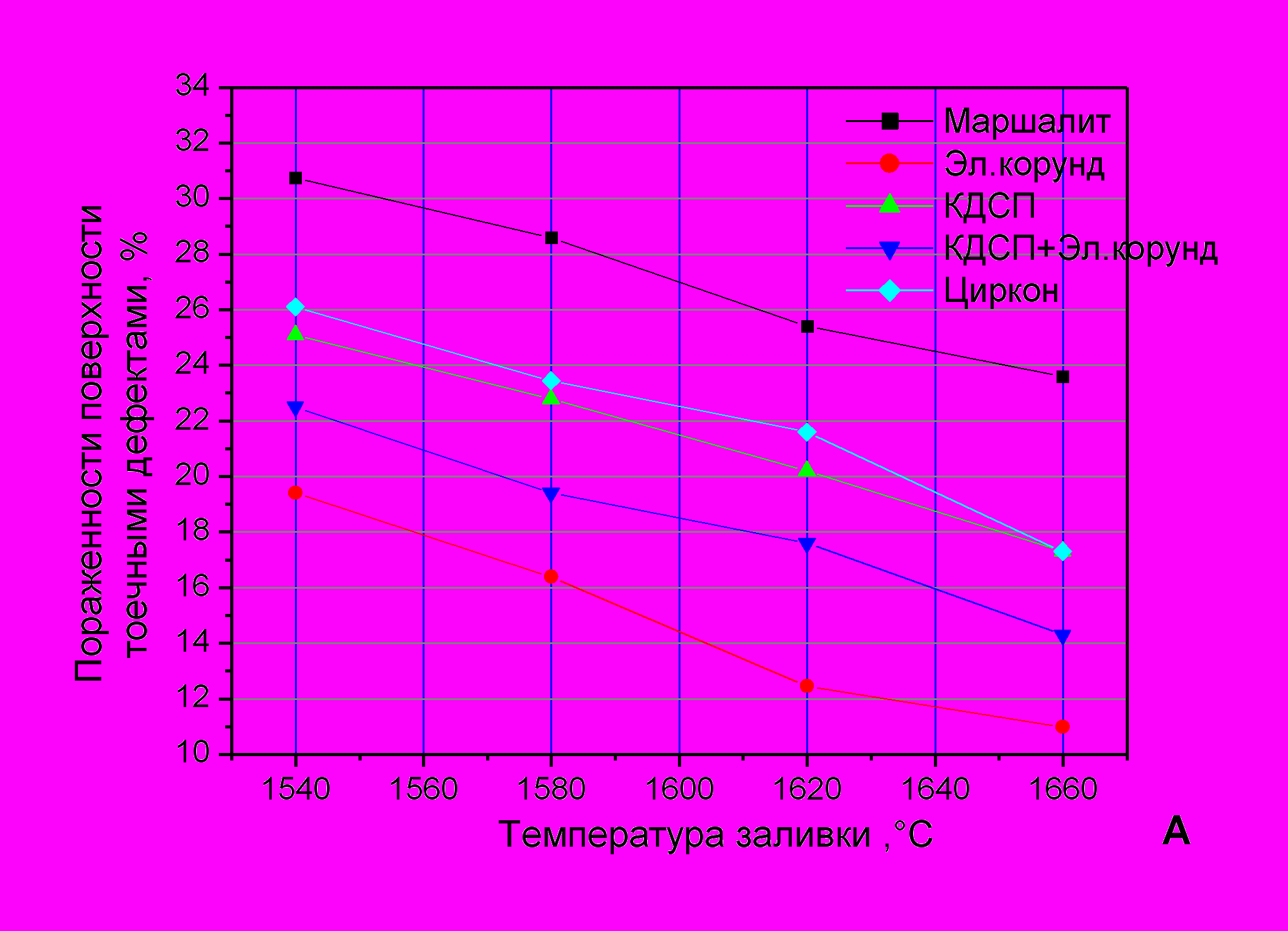
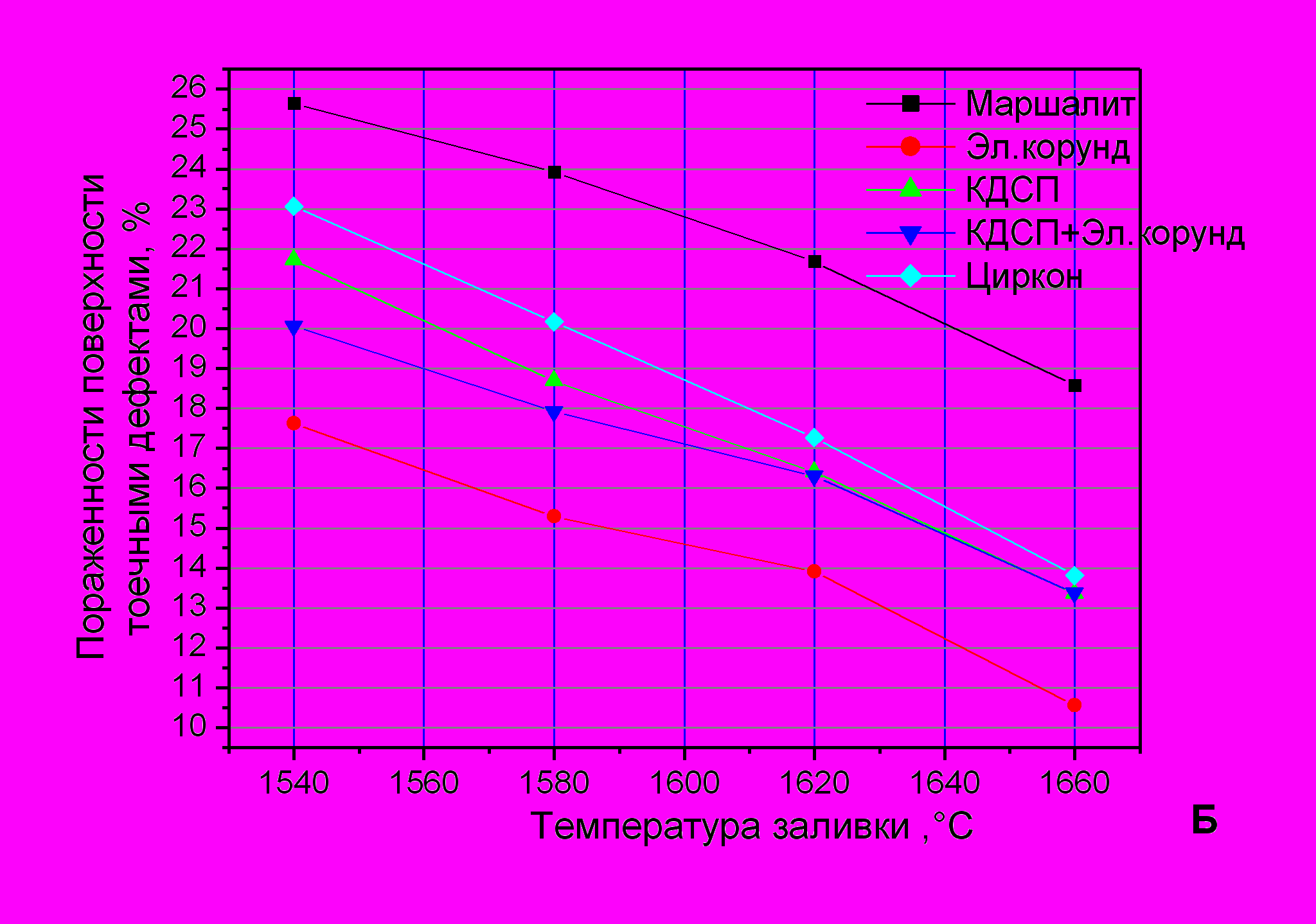
Рис. 2 Влияние температуры заливки и состава формы на
пораженность сплава ЭИ 736 ТПД; условия литья: А – воздух, Б - аргон
заливки металла.
Кремнезем, находящийся в форме, увеличивает наружный размер ТПД (диаметр „ пятна ” на поверхности отливки или наибольший размер дефекта по диагонали). Эксперименты показали, что на отливке полученной в комбинированной форме – форме, где одна половина модели была окрашена маршалитовой огнеупорной суспензией, а другая электрокорундовой – размеры ТПД существенно различаются. На половине отливки, полученной в маршалитовой форме, наибольший размер ТПД составляет 4.05 мм, а на половине, полученной в электрокорундовой форме, 2.38 мм; при этом увеличивается содержание кремния в дефектной зоне с 21.83 % до 29.6 % (соответственно для электрокорундовой и маршалитовой части оболочки). Таким образом, установлено, что повышение содержания оксидов кремния в составе керамической формы способствует увеличению размеров ТПД и не является определяющим фактором в их возникновении.
При анализе исходных формовочных материалов, применяемых при изготовлении керамических оболочковых форм, выявлено значительное количество соединений железа. Особенно их много – в кварцевом песке (до 1.18 %). Оксиды железа способны взаимодействовать с кремнеземистым связующим формы с образованием легкоплавких соединений на поверхности отливки. Для нейтрализации железа был предложен способ его удаления из формы путем перевода в водорастворимое состояние за счет комплексной обработки керамической оболочки - тепловой (нагрев и выдержка при 550 °C) и последующей промывки формы в подкисленной ионоактивированной воде с уровнем рН = 2…5 . Такая обработка позволяет снизить содержание железа в 5 раз, что уменьшает пораженность отливок ТПД в 1.8 раза.
Влияние состава керамической формы выражается также в увеличении содержания силикатных включений состава FeO – SiO2 – MnO и FeO – SiO2 – MnO – Cr2O3, причем доля последних возрастает по мере увеличения количества кремнезема в материалах керамической формы (рис.3). Наибольшее количество указанных включений присутствует в отливках, полученных в маршалитовых формах. На количестве остальных типов НМВ состав керамической формы практически не сказывается.
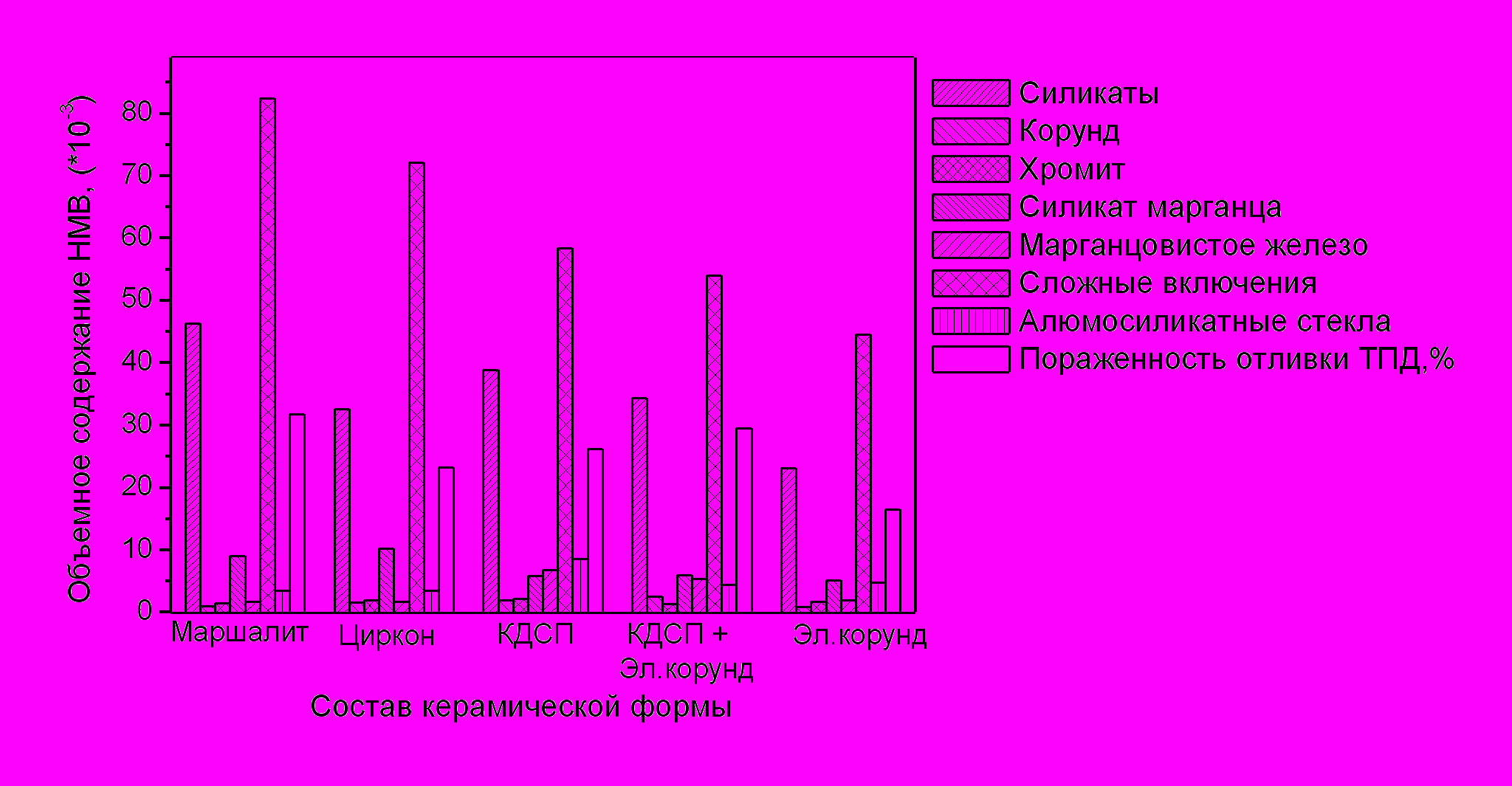
Рис. 3 Влияние состава керамической формы на содержание НМВ и
пораженность отливки ТПД (сплав ЭИ 736)
При определении влияния температуры заливки на пораженность отливок ТПД установлено, что для всех рассмотренных в работе марок сталей и составов керамических форм увеличение температуры заливки приводит снижает пораженность отливки ТПД (рис.2). Это объясняется тем, что с повышением температуры при плавке металла происходит снижение количества НМВ за счет их частичной диссоциации.
Результаты экспериментов (рис.4) показывают, что наименьшая поражен-ность отливок ТПД наблюдается в тех случаях, когда исключается продолжи-тельный контакт жидкого и затвердевающего металла с кислородом. Так при плавке и литье в аргоне пораженность отливки ТПД снижается в 1,2 раза по сравнению с литьем на воздухе.
Как показали эксперименты, пораженность отливок ТПД снижается одновременно с понижением содержания НМВ силикатного происхождения. Резко снизить пораженность отливок ТПД (с 28 – 31 % до 4 – 5 %) и количество НМВ пленочного происхождения оказалось возможным при создании восстановительной атмосферы в форме в период заливки и охлаждения, например, вводом углеродосодержащих добавок в керамическую оболочку или опорный наполнитель, окружающий её.
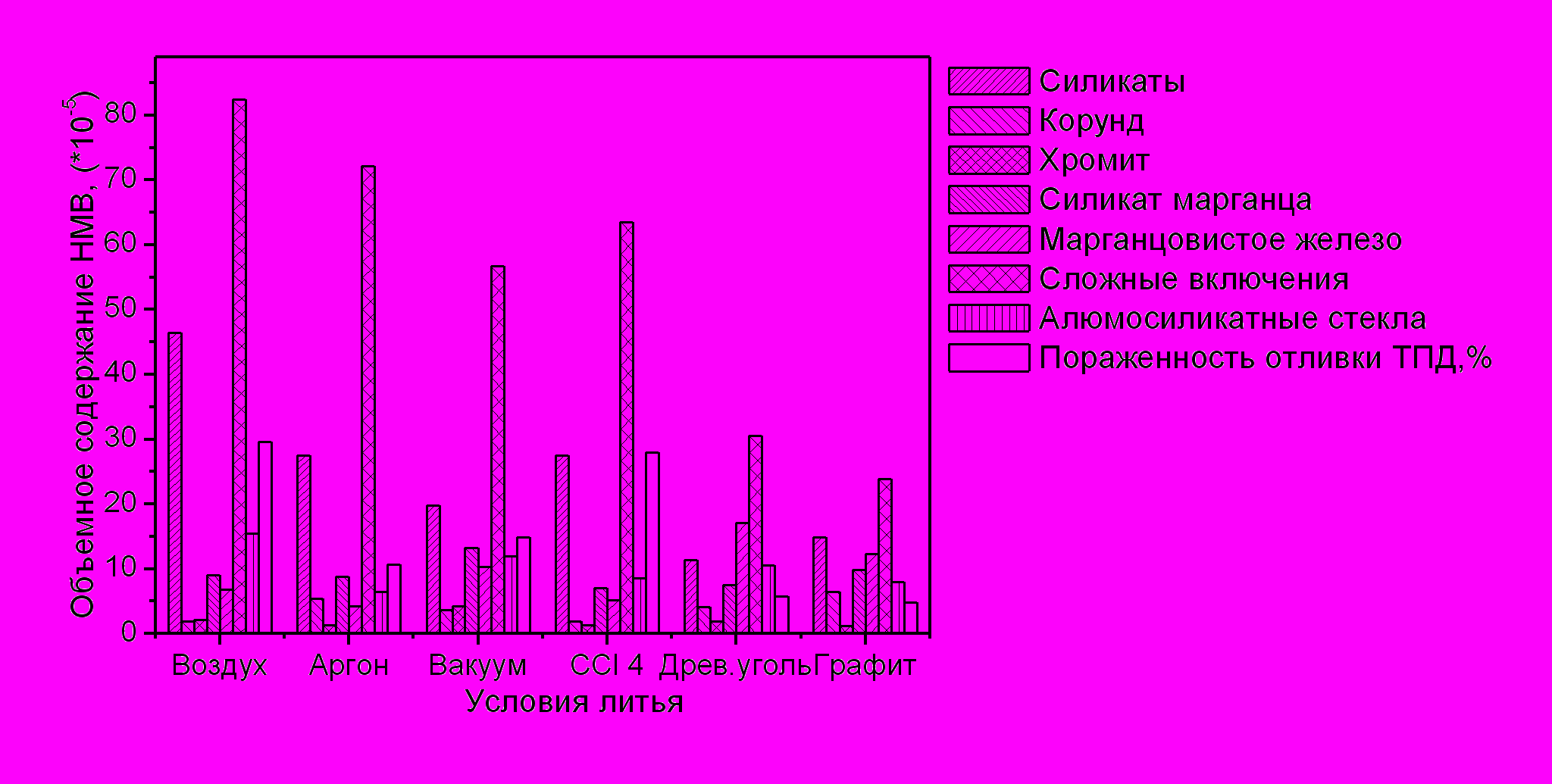
Рис. 4 Влияние условий плавки-заливки и охлаждения отливки на
содержание НМВ и пораженность отливки ТПД (сплав ЭИ 736)
При определении условий влияние условий плавки и литья на содержание НМВ установлено, что наименьшее количество включений состава FeO – SiO2 – MnO и FeO – SiO2 – MnO – Cr2O3 наблюдается при заливке металла в восстановительной атмосфере, осуществляемой путем ввода в форму углеродосодержащих веществ (рис.4).
Установлено, что повышение содержания хрома в составе жаропрочной стали, на примере сталей ЭИ 736 (13 – 15 % Сr) и ЭИ 402 (18 – 20 % Cr) приводит к увеличению содержания включений состава FeO – SiO2 – MnO – Cr2O3 с 75% до 86 % в то время как содержание соединений состава FeO – SiO2 – MnO уменьшается с 76 % до 64 %.
В шестой главе описан механизм образования ТПД (рис.5), который зак-лючается в следующем.
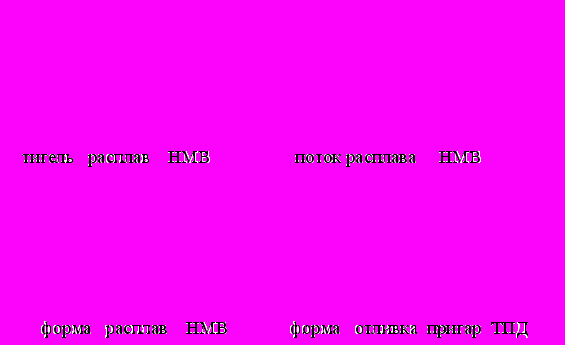
Рис. 5 Стадии формирования ТПД: А – положение НМВ при плавке, Б - положение НМВ в потоке, В – положение НМВ в форме, Г – ТПД на отливке
Вследствие технологических особенностей плавки жаропрочных хромистых и хромоникелевых сталей в жидкой металлической ванне плавильного тигля образуются оксиды кремния и марганца. Являясь основными элементами - раскислителями данных сталей, они образуют в металле жидкие взвеси с низкой температурой плавления, способные к коагуляции, а также к шлакованию легко окисляющихся компонентов стали (хром, железо). Окисные частицы представляют собой соединения системы FeO – SiO2 – MnO и относятся, очевидно, к пленочным стеклам – силикатам железа и марганца, имеющих температуру плавления 1170 – 1250 ºC. В силу своей меньшей плотности, чем жидкая сталь, эти соединения располагаются преимущественно на зеркале металла и в близлежащих поверхностных слоях.
При переливе металла из тигля и последующем его течении в форме (безнапорный режим) окисная пленка на зеркале металла под действием сил трения разрывается и прилипает к стенкам формы, т. к. угол смачивания формы силикатами меньше 90º. Фрагменты окислов за счет сил поверхностного натяжения стягиваются в округлые частицы.
Процесс взаимодействия между шлаковыми частицами (фрагментами оки-сного расплава) и стенкой керамической оболочки состоит из двух взаимодополняющих механизмов: капиллярной пропитки и диффузионной миграции. Находясь в контакте с поверхностным слоем, высокотемпературный окисный расплав прогревает и расплавляет его составляющие – прежде всего силикогель и зерна кварца. За счет реакции с кремнеземом количество жидкой фазы увеличивается. Образующаяся между отливкой и формой металлооксидная прослойка, пребывающая в жидком и твердо-жидком состоянии до 2 часов, способствует растворению окалины, что облегчает доступ кислорода к поверхности отливки. В итоге в металлооксидной прослойке происходит двухсторонняя диффузия: ионов металлов из отливки к форме, ионов кислорода к отливке. Оксиды железа и хрома вступают как во взаимодействие с кремнеземом формы, так и между собой. При охлаждении отливки скорость диффузионных процессов замедляется и из металлооксидной прослойки выкристаллизовывается темная фаза, состоящая из силикатов железа (файалита Fe2SiO4) , марганца (тефроит MnO ·SiO2), оксидов железа (магнетита и гематита Fe3O4 и Fe2O3) и хромита (FeCr2O4), изъязвляющая профиль литой поверхности.
В седьмой главе представлены результаты промышленной апробации проведенных исследований.
Разработаны и внедрены в производство следующие мероприятия:
1. Для повышения инертности керамической формы к заливаемому расплаву предложен и внедрен способ снижения активности и содержания основной её
составляющей - оксида кремния. В ходе приготовления огнеупорной суспензии в её состав вводили микропорошок алюминия (АСД-4). Основу предложенной технологии составляет способ изготовления керамических форм по А.С. № 1147515 (авторы Серебряков С.П.и Ларионов А.Я.). Разработанный способ может применяться при изготовлении отливок в дистенсиллиманитовых или цирконокорундовых формах. Метод позволяет снизить брак отливок по дефекту „разъедание” в 1,6 раза.
2. Разработан состав керамической формы, предусматривающий изготовление лицевого слоя оболочковой формы на основе микропорошков электрокорунда, позволяющий снизить взаимодействие составляющих сплава (железа) с формой. На основе предложенного способа полностью изменена технология изготовления керамических форм для всей номенклатуры стального жаропрочного литья на ОАО «НПО «САТУРН». Экономический эффект от внедренной технологии за 12 месяцев использования, за счет экономии металла, и уменьшения брака отливок (на 25%) составил 190 т.р.
3. Для снижения содержания соединений железа разработан и внедрен способ комбинированной обработки маршалитовых форм, обеспечивающий снижение брака по дефекту „разъедание” в 1.8 раза, дефекту „засор” в 3.4 раза, по дефекту „газовые раковины ” в 1.2 раза. Разработанный и внедренный способ защищен патентом РФ № 2285576.
Основные выводы по диссертации
1. На основании проведенного теоретического анализа и экспериментов выявлен механизм образования ТПД, включающий: проникновение НМВ в форму при заливке, их прилипание к форме и взаимодействие с отливкой и формой.
2.Установлено, что основу точечного дефекта составляют силикаты железа (файалит) и марганца (тефроит), в состав дефекта входит также железо в виде оксидов: магнетита, гематита и хромовой шпинели.
3.Изучено влияние технологических факторов: состава формы, температуры и атмосферы плавки и заливки на пораженность точечными поверхностными дефектами отливок из хромоникелевых сталей. Установлено, что повышение температуры заливаемого металла приводит к снижению ТПД на 8 – 10 %; показано, что размер ТПД, как и пораженность отливки ТПД, возрастают по мере увеличения содержания SiO2 в составе керамической формы и снижения содержания хрома в составе стали. Предложены математические зависимости пораженности отливок ТПД от выше указанных факторов.
4.Показано, что заливка металла и охлаждение отливки в восстановительной атмосфере, создаваемой за счет ввода углеродосодержащих добавок в состав формы позволяет получить отливки с минимальной пораженностью ТПД и одновременно низким содержанием макро- и микровключений в отливке.
5.Показано, что применение инертных к металлу огнеупорных формовочных материалов например, электрокорунда, позволяет снизить пораженность отливок ТПД от 1.7 до 8.2 раза; очистка оболочковых форм от загрязнения железом и его соединений путем дополнительного прогрева до 550°С и последу-ющей промывки подкисленной ионоактивированной водой снижает поражен-ность отливок ТПД в 1.8 раза.
6.Установлено, что процесс высокотемпературного взаимодействия твердой хромистой стали с керамической формой не является причиной образования ТПД.
7. Результаты исследований прошли апробацию и внедрены на «ОАО
«НПО Сатурн» при изготовлении всей номенклатуры жаропрочного стального литья ГТД.
Основные результаты работы представлены в следующих
публикациях:
1.Серебряков, С.П. Оценка окисления стали при заливке форм по выплавляемым моделям [Текст] / Серебряков С.П., Берстнев А.А // Справочник. Инженерный журнал. – 2005.– №10. – С.9 – 12.
2.Серебряков, С.П. Предупреждение поверхностных дефектов при производстве жаропрочного точного стального литья [Текст] / Серебряков С.П., Берстнев А.А // «Литейное производство». – 2004. – №11. – С.24 – 27.
3. Патент № 2285576 Российская федерация, (51) МПК В22С 9/04 Способ обработки форм по выплавляемым моделям [Текст] / Серебряков С.П..(RU), А.Я. Ларионов,.(RU), Берстнев А.А. (RU), Шитиков А.В. (RU) – заявитель ОАО «НПО Сатурн» (RU); № 2004128797; заявл. от 29.09.2004. – 3с.
4.Серебряков, С.П. Предупреждение поверхностных дефектов на жароп-рочных стальных отливках по выплавляемым моделям [Текст] / Серебряков С.П., Берстнев А.А., Ларионов А.Я. // Материалы Российской науч.-техн. конф. «Новые материалы, прогрессивные технологические процессы и управление качеством в заготовительном производстве» – Рыбинск. – РГАТА. – 2002.– С.89 – 91.
5.Серебряков, С.П. Анализ условий окисления жаропрочной стали при заливке [Текст] / Серебряков С.П., Ларионов А.Я., Берстнев А.А // Сборник тезисов докладов Всероссийской научно-технической конференции «Аэрокосмические технологии и образование на рубеже веков» – г. Рыбинск.– РГАТА.– 2002. – С. 71 – 72
6. Берстнев А.А. Использование микропорошка электрокорунда для устранения поверхностных дефектов на фасонных отливках из жаропрочных сталей [Текст] / Берстнев А.А., Серебряков С.П. // Материалы Российской научно-технической конференции «Новые материалы, прогрессивные технологические процессы и управление качеством в заготовительном производстве» Рыбинск.– РГАТА.– 2007.– Т1.– С.100–106.