План І. Теоретичне питання: Ремонтне обслуговування устаткування. Системи ремонтного обслуговування устаткування. Характеристика та склад ремонтного господарства. ІІ. Практичні завдання
Вид материала | Документы |
СодержаниеТеоретичне питання Практичні завдання У першому 2. Визначити такт потокової лінії. Такт потокової лінії |
- Аналіз регуляторного впливу Положення про технічне обслуговування устаткування коксохімічних, 2076.41kb.
- Аналіз регуляторного впливу Положення про технічне обслуговування устаткування коксохімічних, 2024.41kb.
- Ето «монтаж І обслуговування теплотехнічного устаткування І систем теплопостачання», 41.27kb.
- В. С. Середюк Матеріалознавство Конспект, 2044.1kb.
- Організація ремонтного господарства на Богородчанському виробничому управлінні підземного, 847.58kb.
- Методичні вказівки, 677.24kb.
- План вступ ст. 3 Основні дані про підприємство ст. 5 Розміщення та викладка товарів, 452.56kb.
- Програма вступних фахових випробувань з фундаментальної та професійної підготовки, 48.46kb.
- Науково-технічна підтримка державного нагляду – гарантія безпеки виробничого устаткування, 18.57kb.
- Затверджено, 7410.01kb.
Міністерство освіти і науки України
Дніпродзержинський індустріальний технікум
Контрольна робота
з дисципліни: «Організація та планування діяльності підприємств»
Студентки групи БО-03 1/11
Шифр: 03058
Юрченко Сузани Вікторівни
Адреса: с.м.т. Кринички
м. Дніпродзержинськ
2005
План
І. Теоретичне питання: Ремонтне обслуговування устаткування. Системи ремонтного обслуговування устаткування. Характеристика та склад ремонтного господарства.
ІІ. Практичні завдання
Теоретичне питання
Ремонтне обслуговування устаткування. Системи ремонтного обслуговування устаткування. Характеристика та склад ремонтного господарства.
Від організації процесу керування ремонтним і технічним обслуговуванням устаткування в значній мірі залежить ефективність виробничої системи в цілому. Простої устаткування через ремонт і несправність, порушуючи виробничий процес, погіршують всі економічні і фінансові показники його діяльності, а зниження точності негативно позначається на якості продукції, що випускається.
На жаль досягнення науково-технічного прогресу в основному виробництві, ускладнення його техніки і технології, насичення підприємств дорогим устаткуванням не внесли істотних змін в організацію ремонту і технічного обслуговування на вітчизняних підприємствах. Витрати на ремонт основних фондів як і раніше складають у собівартості продукції від 6 до 14%. У сфері ремонту зайнятоі більш третини верстатного парку країни. Засоби, затрачувані на ремонт устаткування за час його експлуатації, перевищують вартість нового обладнання більш ніж у 6 разів.
В економічній літературі питанням органічного сполучення розвитку основного і ремонтного виробництва, підвищенню наукового рівня обґрунтованості міжремонтного обслуговування устаткування, зниженню витрат на заміну фізично зношених частин і усуненню поломок у процесі експлуатації приділяється серйозна увага ще із середини 60-х років. Практично у всіх роботах обговорювалися в основному двох проблем: вибір найбільш раціональної форми керування ремонтним і технічним обслуговуванням устаткування й обґрунтування доцільності капітальних ремонтів. У сучасних умовах ці проблеми не тільки не втратили актуальності, але і придбали ще більше значення.
Існують три форми керування ремонтним і технічним обслуговуванням : децентралізована, змішана і централізована. Кожна з них має свої достоїнства і недоліки.
При централізованій формі весь обсяг ремонтних робіт виконується цеховими ремонтними базами, що, як показала практика, не оснащені комплектом сучасного устаткування й інструмента для забезпечення необхідної якості ремонту. Роботі ремонтних бригад при такій формі обслуговування придается другорядне значення, що приводить до низького рівня їхньої організації і неефективному використанню кадрів. Однак ця форма має немаловажну перевагу – витрати на усі види ремонтів включаються в собівартість по місцеві їхнього виконання, що дозволяє проводити аналіз цих робіт в аспекті матеріальних і трудових витрат.
Змішана форма керування, при якій поточний ремонт і технічне обслуговування здійснюються цеховими ремонтними базами, а капітальний – ремонтно-механічним цехом, не усуває недоліки децентралізованої форми. Ремонтні ресурси підприємства розосереджені між ремонтно-механічним цехом і цеховими ремонтними базами, що виключає можливість маневреного використання і матеріальних, і трудових ресурсів. Практично виключається можливість доцільної спеціалізації ремонтних робіт як по видах устаткування і ремонтів, так і по складу робіт (механічні, електротехнічні, теплотехнічні). При такій організаційній структурі витрати на ремонт, виконуваний цеховими ремонтними базами, включаються в собівартість робіт цеху, а витрати ремонтно-механічного цеху оформляються у виді послуг. Це утрудняє організацію керування витратами ремонтного обслуговування в цілому.
При централізованій структурі керування усі види ремонту і технічного обслуговування технологічного устаткування й устаткування допоміжних підрозділів здійснює централізована ремонтна служба. Недоліком такої структури є те, що ремонт електричної, теплотехнічної й іншої частин устаткування виконуються відповідними підрозділами заводу, що найчастіше приводить до простоїв через непогодженість дій окремих керівників.
При всій очевидності переваг централізованої організаційної структури її створення викликало різку протидію з боку керівників підрозділів основного виробництва. Це порозумівається тим, що планова директивна система керування підприємством, прийнята в радянський час, головною метою ставила виконання встановлених завдань. Механіки цехів, знаходячись у прямому підпорядкуванні начальникам цехів основного виробництва, не завжди могли зупинити устаткування на ремонт, передбачений графіком планово-попереджувального ремонту (ППР), через погрозу зриву виконання плану по обсязі виробництва. У країнах же з розвитий ринковою економікою застосовується тільки централізована форма керування ремонтом устаткування.
У сучасних умовах переходу до ринкової економіки не викликає сумнівів доцільність створення централізованої структури керування ремонтним обслуговуванням, тому що фінансова стійкість підприємства залежить від ефективності кожної служби підприємства. Тільки в рамках централізованої структури керування ремонтним обслуговуванням можна проводити єдину технічну й економічну політику. Що стосується економічної політики, те її основними цілями стають скорочення витрат на ремонт, проведення регулярного контролю за дотриманням їхніх нормативних значень, встановлених у рамках планованих кошторисів на проведення ремонтних робіт (ремонтного фонду, що включається в собівартість продукції).
Під технічною політикою мається на увазі індустріалізація ремонту, використання вузлових методів ремонту, застосування передових методів відновлення зношених деталей і інші заходи. Перехід на ринкові умови роботи ставить під сумнів доцільність застосування типової системи планово-попереджувального ремонту.
Практика роботи підприємств показує, що витрати на непланові ремонтні роботи складають більш 50% усіх витрат на ремонт, тобто перевищують вартість планових ремонтів.
Можна виділити наступні недоліки типової системи планово-попереджувального ремонту.
Тверда регламентованість міжремонтних періодів, що дозволяє гнучко планувати висновок устаткування в ремонт.
Обов'язковість планового проведення капітального ремонту без складання економічного обґрунтування і визначення його доцільності.
Відсутність ефективних методів і засобів технічної діагностики устаткування для уточнення термінів висновку устаткування в капремонт, використання єдиних нормативів витрати матеріалів без диференціації умовної одиниці для верстатів і машин різної ваги.
Однак цілком відмовлятися від системи ППР не випливає. Вивчення закордонного досвіду показує, що в країнах з розвитий ринковою економікою теж використовуються елементи системи ППР. Так, на більшості підприємств США застосовується система планово-попереджувального обслуговування. Цією системою охоплюються не все устаткування, а тільки найбільш високопродуктивне і важливе для виробництва, а для устаткування, що має дублерів, використовувати систему ППР вважається не вигідно.
По публікаціях, присвяченим проблемам удосконалювання організації ремонтного обслуговування, складається представлення про великі обсяги капітального ремонту, виконуваних ремонтно-механічними цехами. Однак насправді, незважаючи на високий ступінь зношеності устаткування, питома вага капітального ремонту складає в загальному обсязі ремонтних робіт тільки 22%. Таким чином, майже 80% всього обсягу ремонтних робіт виконується децентралізовано, тобто силами цехових ремонтних баз.
Як показав аналіз, по багатьом видам устаткування витрати на капітальний ремонт значно перевищують вартість устаткування. У той же час капітальний ремонт деяких видів устаткування коштує недорого. Однак на підставі розрахункової вартості капітального ремонту не можна зробити висновок про його доцільність (чи недоцільності), оскільки в умовах кризової ситуації великі витрати можуть свідчити про необхідність проведення ремонту, а незначні - про невідповідність дефектним відомостям, неповному усуненні зношених деталей у зв'язку з відсутністю засобів.
Тільки при об'єднанні служб, що виконують ремонт механічної, електротехнічної, теплотехнічної й електронної частин устаткування, можна говорити про відповідальний підхід до організації ремонту і його проведенню. Централізована система дозволить реалізувати усі функції керування службою ремонту устаткування: організацію, планування, координацію, облік і мотивацію.
Висновок цехових механіків з під підпорядкування керівникам цехів основного виробництва створить умови для здійснення єдиної технічної політики в області ремонту устаткування: використання індустріальних методів ремонтних робіт, спеціалізації ремонтних бригад, застосування передових методів організації праці і його оплати.
У типовій системі ППР враховуються ремонтні особливості кожної одиниці устаткування, що підлягає технічному обслуговуванню і ремонту, і на підставі об'єктивної оцінки її зносу установлюються види ремонту, їхнє чергування, тривалість ремонтних циклів, трудомісткість, вартість, тарифікацію робіт.
Реалізувати ці положення можна було, працюючи тільки на вітчизняному устаткуванні, однак у даний час на багатьох підприємствах використовується і закордонна техніка. Крім того, при модернізації устаткування перестає відповідати діючим стандартам, що виключає можливість застосування типової системи ППР. Тому сьогодні значна частина діючого парку устаткування не може бути охоплена єдиною системою ППР. Істотний фізичний знос вітчизняного устаткування через перевищення термінів його служби також не дозволяє використовувати нормативи системи ППР, тобто виникає необхідність розробки індивідуальних нормативів трудомісткості, витрат, міжремонтних циклів.
Не менш важливої є проблема удосконалювання міжремонтного технічного обслуговування, тому що, на думку автора, ремонтне і технічне обслуговування устаткування не можуть розглядатися як самостійні ізольовані системи.
У цьому зв'язку великий інтерес представляє досвід обслуговування устаткування японських промислових фірм.
За прикладом США в Японії в 1951 році почалося впровадження системи профілактичного обслуговування устаткування. Поступово ця система перетворювалася в систему експлуатаційного обслуговування американського типу, суть якої полягала в тім, що функції безпосередньо виробничого характеру виконуються на виробництві, а експлуатаційні бригади несуть повну відповідальність за технічне обслуговування устаткування. Виключення складає автоматизоване устаткування, оператори якого здійснюють профілактичне обслуговування самостійно.
Досвід японських фірм показує, що застосування загальної експлуатаційної системи різко підвищує ефективність виробництва. Так, витрати на обслуговування устаткування скоротилися на 30%, наявний виробничий запас запчастин і інструмента зменшився наполовину, а продуктивність, обмірювана в обсягах чистої продукції, збільшилася на 50%.
Однієї з задач загальної експлуатаційної системи є створення організаційних структур, відповідальних за стан устаткування й обеспечивающих його надійну й ефективну експлуатацію до стадії зносу, з метою мінімізації витрат за увесь час експлуатації.
Аналіз закордонного досвіду свідчить про необхідність повної централізації функцій по ремонті і технічному обслуговуванні основних фондів. Для цього потрібно створити комплексну систему ремонтного і технічного обслуговування устаткування, безпосередньо підлеглу головному інженеру підприємства. Основою цієї системи повинне стати повне звільнення цехів основного виробництва від проведення ремонтного і технічного обслуговування устаткування. Принципово новими задачами єдиної служби ремонтного і технічного обслуговування устаткування є:
- Перенос центра ваги з ремонтного на технічне обслуговування устаткування.
- Розробка ремонтних нормативів, що відрізняються від системи планово-попереджувального ремонту індивідуальним підходом з урахуванням особливостей конкретного виробництва.
- Організація керування витратами.
- Об'єднання всіх спеціалізованих бригад у рамках єдиного підрозділу.
Для реалізації цих задач буде потрібно організація спеціалізованої диспетчерської служби й інформаційної системи з використанням обчислювальної техніки.
Ремонтне господарство підприємства являє собою сукупність відділів і виробничих підрозділів, зайнятих аналізом технічного стану технологічного устаткування, наглядом за його станом, технічним обслуговуванням, ремонтом і розробкою заходів щодо заміни зношеного устаткування на більш прогресивне і поліпшенню використання. Виконання цих робіт повинне бути організоване з мінімальними простоями устаткування, у найкоротший термін і вчасно, якісно і з мінімальними витратами.
Ефективність роботи ремонтного господарства багато в чому визначає собівартість продукції, що випускається, її якість і продуктивність праці на підприємстві, тому що питома вага витрат на зміст і ремонт устаткування в собівартості продукції досягає 10 %.
Головною причиною значних витрат на ремонти і технічне обслуговування технологічного устаткування є низька його якість, унаслідок чого витрати в сфері експлуатації продукції машинобудування за нормативний термін використання в 5-25 разів більше її ціни. У порівнянні з кращими закордонними зразками аналогічного класу вітчизняне технологічне устаткування і транспортні засоби вимагають у 3-5 разів більше засобів на технічне обслуговування, використання і ремонти.
У свою чергу низька якість вітчизняної продукції машинобудування порозумівається низькою якістю маркетингових досліджень і НІОКР. І як підсумок - питома вага вітчизняної продукції машинобудування, конкурентноздатної на зовнішньому ринку, складав у 1995 р. усього близько 2 %.
Звідси випливає: ефективність ремонтного господарства залежить як від якості технологічного устаткування, що закладається на стадіях маркетингу і НІОКР і реалізованого на стадії виробництва, так і від рівня організації роботи ремонтного господарства в сфері споживання устаткування.
Організація ремонтного господарства діючого великого підприємства включає виконання комплексу робіт:
- аналіз виробничої й організаційної структури підприємства на предмет пропорційності, прямоточности, безперервності, паралельності й автоматичності виробничих процесів; аналіз рівня спеціалізації, комбінування з метою оптимізації цих параметрів; аналіз технологічного устаткування за наступними показниками (факторам):
- необхідність даного устаткування;
- питома вага невстановленого устаткування;
- питома вага устаткування, що знаходиться в ремонті;
- середній вік технологічного устаткування (по групах);
- питома вага фізично зношеного устаткування;
- коефіцієнт змінності роботи технологічного устаткування;
- коефіцієнт використання устаткування по продуктивності (по групах);
- коефіцієнт використання устаткування в часі (по групах);
- аналіз фондовіддачі;
- аналіз структури активної частини основних виробничих фондів;
- аналіз рівня механізації виробництва;
- розробка пропозицій по удосконалюванню форм організації виробництва, виробничої й організаційної структур підприємства; розробка пропозицій по поліпшенню використання устаткування (по видах); розробка норм потреби в устаткуванні для заміни зношеного, технічного переозброєння і капітального будівництва; розробка норм потреби в запасних частинах для технологічного устаткування; розробка норм потреби в різних видах матеріалів і енергії для технологічного устаткування й інших елементів виробничих фондів (ОПФ); розрахунок потреби у виробничих площах для ремонтного господарства; розрахунок потреби в трудових ресурсах для ремонтного господарства і фонду заробітної плати для них; розрахунок показників планово-попереджувального ремонту (ППР) устаткування (по видах):
- аналіз дотримання ППР на підприємстві;
- структура міжремонтного циклу по видах устаткування;
- тривалість міжремонтного періоду;
- трудомісткість ремонтів устаткування (по видах ремонту і видам устаткування);
- потреба по видах ресурсів для різних видів ремонту;
- річний обсяг ремонтних робіт;
- параметри організації ППР устаткування підприємства в часі й у просторі;
- організація ремонтних робіт; організація міжремонтного обслуговування; організація матеріально-технічного забезпечення ремонтного господарства підприємства; розробка, контроль і стимулювання стратегічного плану підвищення ефективності роботи ремонтного господарства.
Перераховані види робіт можна укрупнено об'єднати в три блоки:
а) економічний блок , що поєднує роботи з: обліку й аналізу ефективності використання ОПФ; розробці норм потреби в устаткуванні для заміни зношеного, технічного переозброєння, капітального будівництва; розробці норм потреби в запасних частинах і матеріальних ресурсах для технічного обслуговування, використання (експлуатації) і ремонтів ОПФ; стратегічному плануванню відтворення ОПФ, плануванню ППР устаткування; плануванню матеріально-технічного забезпечення ремонтного господарства; розробці пропозицій по удосконалюванню організаційної і виробничої структур ремонтного господарства (спільно з фахівцями організаційного блоку);
б) технічний блок, що включає: здійснення технічного нагляду за станом устаткування й інших елементів ОПФ; проведення технічного обслуговування технологічного устаткування; проектування, виготовлення і відновлення запасних частин; виконання різних видів ремонту елементів ОПФ;
в) організаційний блок, що включає: організацію матеріально-технічного забезпечення ремонтного господарства; організацію вхідного і вихідного контролю якості матеріалів, що комплектують виробів, запасних частин і устаткування що надходять чи виходять з ремонтного господарства; розробку елементів ОПФ; упровадження прогресивних для даних умов форм організації виробництва; удосконалювання організаційної і виробничої структур ремонтного господарства.
Обсяг робіт з кожного блоку визначається чотирма основними факторами: 1) складністю і номенклатурою продукції, що випускається; 2) програмою випуску; 3) рівнем спеціалізації, комбінування і кооперування основного виробництва; 4) рівнем спеціалізації, комбінування і кооперування ремонтного господарства.
В умовах розвитку ринкових відносин спостерігається поглиблення і розширення спеціалізації й інтеграції. Тому більшість перерахованих робіт можуть виконуватися спеціалізованими фірмами (підприємствами, організаціями), що можуть забезпечити висока якість робіт і прийнятні ціни на їхнє виконання.
Ремонтне господарство на підприємстві очолює головний механік, що підкоряється головному інженеру (технічному директору).
Структура ремонтного господарства може складатися з наступних підрозділів:
- економічний відділ;
- технічний відділ;
- організаційний відділ;
- ремонтно-механічний цех;
- склад.
Функції відділів були розглянуті раніше.
Основними напрямками удосконалювання ремонтного господарства і підвищення ефективності його функціонування можуть бути: в області організації виробництва - розвиток спеціалізації і кооперування у випуску основної продукції, в організації ремонтного господарства; в області планування відтворення ОПФ - застосування наукових підходів і методів менеджменту; в області проектування і виготовлення запасних частин - уніфікація і стандартизація елементів запасних частин, застосування систем автоматизованого проектування на основі класифікації і кодування, скорочення тривалості проектних робіт і підвищення їхньої якості; в області організації робіт - дотримання принципів раціональної організації виробництва (пропорційності, паралельності і ін.), застосування мережних методів і ЕОМ; в області технічного нагляду, обслуговування і ремонтів ОПФ - розвиток предметної і функціональної спеціалізації робіт, підвищення технічного рівня ремонтно-механічного цеху, посилення мотивації якісної праці й ін.
Практичні завдання
№1
В механічному цеху промислового технологічний процес обробки партії деталей складається з декількох операцій з наступними вихідними донними:
Показник | Порядковий номер операції | ||||||
1 | 2 | 3 | 4 | 5 | 6 | 7 | |
1. Норма часу на виконання операції, хв. | 3 | 8 | 6 | 6 | 2 | 3 | 6 |
2. Кількість верстатів, які зайняті в процесі операційної обробки, од. | 1 | 2 | 3 | 2 | 1 | 1 | 2 |
Визначити тривалість операційного циклу обробки партії деталей в 100 шт. при умові паралельно-послідовного з’єднання технологічних операцій, а також поштучної передачі деталей, які обробляються, з одної операції на іншу.
Рішення.
Паралельно-послідовний вид руху полягає в тому, що виготовлення виробів на наступній операції починається до закінчення виготовлення всієї партії на попередній операції з таким розрахунком, щоб робота на кожній операції по даній партії в цілому йшла без перерв. На відміну від рівнобіжного виду руху тут відбувається лише часткове сполучення в часі виконання суміжних операцій.
У практиці існує два види сполучення суміжних операцій у часі:
- час виконання наступної операції більше часу виконання попередньої операції;
- час виконання наступної операції менше часу виконання попередньої операції.
У першому випадку представляється можливість застосовувати рівнобіжний вид руху деталей і цілком завантажити робочі місця.
В другому випадку прийнятний паралельно-послідовний вид руху з максимально можливим сполученням у часі виконання обох операцій. Максимально сполучені операції при цьому відрізняються друг від друга на час виготовлення останньої деталі (чи останньої операційної партії) на наступній о

перації.
У даному випадку операційний цикл буде менше, ніж при послідовному виді руху, на величину сполучення кожної суміжної пари операцій:
- перша і друга операції — АБ = (3-1) tшт2 ;
- друга і третя операції — ВГ = (3-1) tшт2 ;
- третя і четверта операції — ДЕ = (3-1) tшт4, (tшт2 и tшт4 мают більш короткий час tшт.кор з кожної суміжної пари операцій).
Т
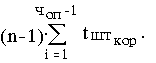
аким чином, час сполучень
Ф

ормула для розрахунку
П

ри виконанні операцій на рівнобіжних робочих місцях
П

ри передачі деталей операційними партіями
Паралельно-послідовний вид руху деталей (виробів) забезпечує роботу устаткування і робітника без перерв. Виробничий цикл при цьому виді більше в порівнянні з рівнобіжним, але менше, ніж при послідовному.
2. Визначити такт потокової лінії.
Річний план потокової лінії – 36000 виробів. Режим роботи – 251 день на рік, дві зміни на день, тривалість робочої зміни – 8 годин, дві перерви за зміну по 10 хв. Конвейер ремонтується у вільні зміни.
Рішення
Потокове виробництво забезпечує найвищу продуктивність праці, низьку собівартість продукції, найбільш короткий виробничий цикл. Основою (первинною ланкою) потокового виробництва є потокова лінія .
При проектуванні й організації потокових ліній виконуються розрахунки показників, що визначають регламент роботи лінії і методи виконання технологічних операцій.
Такт потокової лінії - проміжок часу між випуском виробів (деталей, складальних одиниць) з останньої чи операції їхнім запуском на першу операцію потокової лінії.
Такт потокової лінії розраховується по формулі
r = Fд / Qвип,
де r - такт потокової лінії (у хв);
Fд - дійсний річний фонд часу роботи лінії в планованому періоді (хв);
Qвип - планове завдання на той же період часу (шт.).
Fд = Dраб х dсм х Тсм х kпер х kрем,
де Dраб - число робочих днів у році;
dсм - кількість робочих змін у добу;
Тсм - тривалість зміни;
kпер - коефіцієнт, що враховує плановані перерви;
kпер = (Тсм - Тпер) / Тсм ,
де Тпер - час планованих внутрізмінних перерв;
kрем - коефіцієнт, що враховує час планових ремонтів, приймаємо за 1.
kпер = (480 – 20) / 480 = 0,96
Fд = 251 х 2 х 480 х 0,96 х 1 = 230920
r = 230920 / 36000 = 6,41
Використана література.
- Борисов С.Б. Организация управления ремонтным и техническим обслуживанием оборудования // Машиностроитель №12, 2000г
- Непомнящий Е.Г. Экономика и управление предприятием: Конспект лекций - Таганрог: Изд-во ТРТУ, 1997
- Организация, планирование и управление деятельностью промішленного предприятия. / Под ред. А.И. Бухало. – К.: Вища школа, 1989.
- Орлов О.О. Планування діяльності промислового підприємства. – Київ: «Скарби», 2002
- Управление производством в малом и среднем бизнесе - М.: ЗАО «МАРП», 2000