Строительная керамика на основе техногенного грубодисперсного сырья 05. 23. 05 строительные материалы и изделия
Вид материала | Автореферат |
В четвертом разделе В пятом разделе Т – температура, С; R В шестом разделе В седьмом разделе |
- Гипсовые строительные материалы и изделия, полученные механохимической активацией техногенного, 457.25kb.
- Безобжиговые строительные материалы и изделия на основе бесклинкерных и малоклинкерных, 607.91kb.
- Строительные материалы и изделия по сниженным ценам «Строительная неделя Московской, 42.24kb.
- Теплоизоляционные строительные материалы на основе низинных торфов Томской области, 275.61kb.
- Наноструктурные металлы, сплавы, керамика и композиционные материалы, 47.02kb.
- Строительные смеси на основе продуктов утилизируемого керамзитобетона. 05. 23. 05 Строительные, 329.54kb.
- Отпускные цены на основные строительные материалы, изделия и конструкции, производимые, 2880.69kb.
- Стекло и керамика, композиты, нетканные материалы, 35.77kb.
- Зернистый теплоизоляционный материал на основе высокомодульной жидкостекольной композиции, 246.73kb.
- Керамические материалы и изделия, 768.56kb.
В четвертом разделе приводится разработка технологии получения керамических строительных материалов на основе техногенного алюмосиликатного сырья: ГО, ФГС, ОГС, ЦП. Выбор гранитных отсевов обусловлен тем, что улучшение показателей керамических материалов прочности при сжатии и изгибе, термическую устойчивость, водонепроницаемость возможно за счет более полного спекания.
Были проведены исследования с целью подбора составов керамического кирпича на основе гранитных отсевов с использованием метода математического планирования эксперимента. На основе анализа исследуемой системы выбраны следующие диапазоны изменения факторов (таблица 1). В качестве целевой выходной переменной У выбраны показатели прочности при сжатии (МПа), сырцовой прочности (МПа), средней плотности (кг/м3) и морозостойкость F (циклов).
В качестве факторов использованы следующие входные параметры: Х1 – отношение тонкомолотой части к грубодисперсной; Х2– отношение суммы связующего к сумме тонкомолотой и грубодисперсной части; Х3 – температура термообработки, °С. Регрессионные зависимости устанавливают причинно – следственные связи между переменными, корреляционные связи между равноправными переменными. Корреляционный анализ особенно удобен там, где имеются недоступные или труднодоступные для непосредственных замеров параметры объекта исследования, а также возникает необходимость сокращения числа экспериментов.
Таблица 1 – Диапазон изменения факторов
Факторы | Х1 | Х2 | Х3 |
Нижний уровень (-1) | 0,20 | 0,20 | 950 |
Верхний уровень (+1) | 0,3 | 0,3 | 1050 |
Нулевой уровень (0) | 0,25 | 0,25 | 1000 |
Интервал ворьированя | 0,05 | 0,05 | 50 |
Плечо + α | 0,3341 | 0,3341 | 1084 |
Плечо – α | 0,1659 | 0,1659 | 916 |
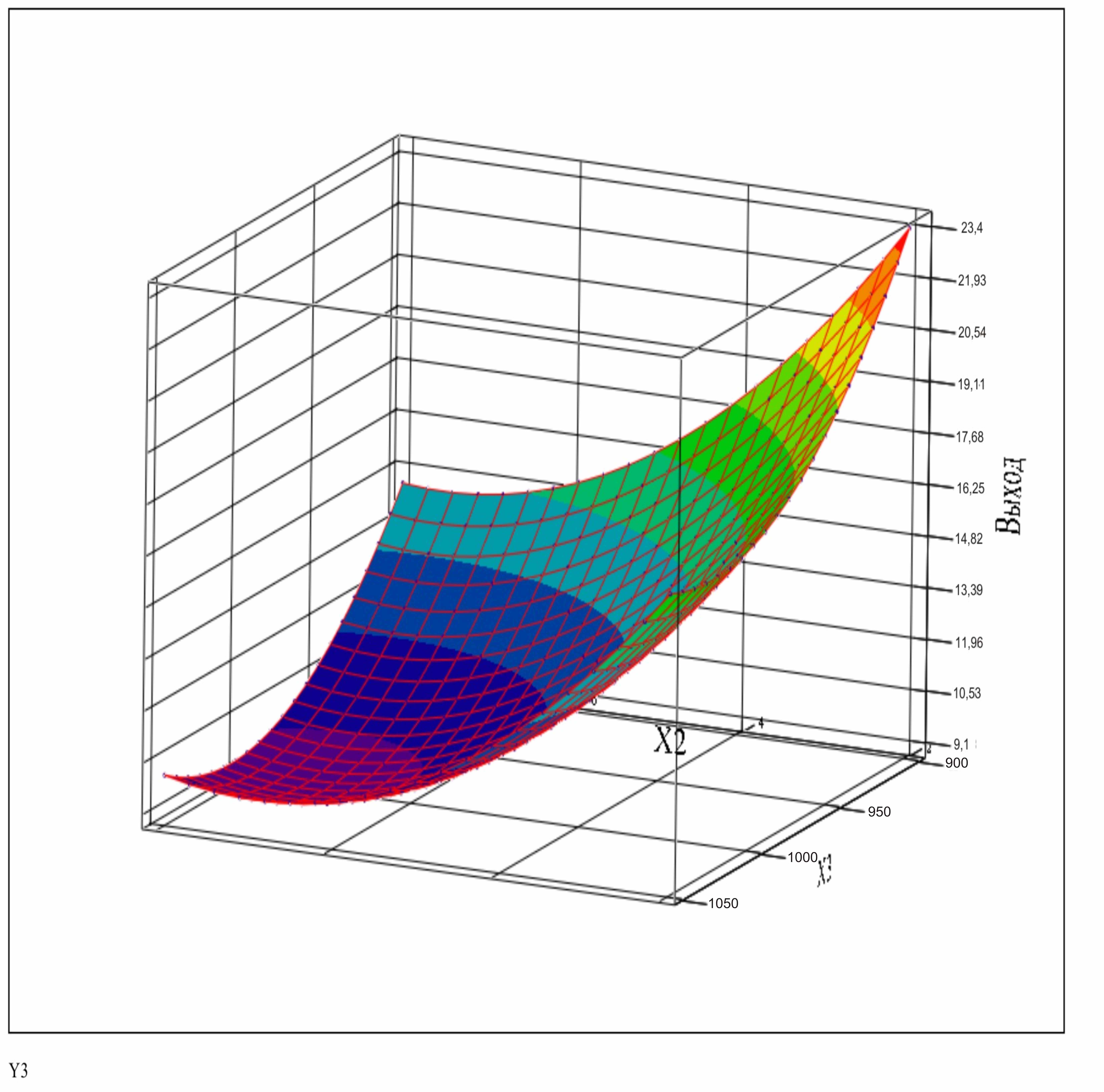
Рисунок 3 – Трехмерный график функции Y при фиксированном значении X1 со значением в середине плана (X1 = 60)
Модель прочности показывает (рисунок 3), что максимум Rmax = 23,4 МПа наблюдается у составов с х1=0,25; х2=0,25; х3=1084; минимум у состава Rmin = 8,4 МПа, с Х1 = 0,25, Х2 = 0,25, Х3 = 916; приросты: абсолютный 15 МПа и относительный R = 2,79. Так же были исследованы свойства керамических стеновых материалов с использованием каолинитовой Ленгерской глины, суглинка и гранитного отсева. Образцы готовили полусухим формованием из масс содержащих гранитные отсевы фракции < 2,5 мм – 55-60%; фракции < 0,14 мм – 5%; суглинок – 25-35%; каолинитовая глина – 10-15%. В состав исследуемых масс вводили разное количество гранитных отсевов, благодаря чему соотношение RO: R2O изменялось от 1,5 до 1, так же изменялось соотношение и других оксидов, влияющих на образование жидкой фазы, на плотность и прочность образцов (таблица 2).
Таблица 2 – Соотношение RO: R2O
Оксид | Соотношение RO: R2O | ||||
1,5 | 1,4 | 1,3 | 1,2 | 1,1 | |
SiO2:Al2O3 | 3,5 | 3,6 | 3,7 | 3,8 | 3,9 |
SiO2 : R2O | 16 | 19 | 22 | 25 | 28 |
RO:(R2O+RO+Fe2O3) | 0,6 | 0,5 | 0,4 | 0,3 | 0,2 |
При уменьшении соотношения RO:R2O исследуемая масса после обжига обладает минимальным водопоглощением, высокой механической прочностью и плотностью. Повышение соотношения SiO2:R2O (до 28) приводит к увеличению количества стеклофазы и частичному растворению SiO2, что подтверждается минимальным водопоглощением.
Положительное влияние на свойства керамического материала оказывает железосодержащий расплав, который можно охарактеризовать соотношением RO: (R2O+RO+Fe2O3) равный в данном случае 0,2-0,3. Зависимость основных свойств образцов от соотношения RO:R2O приведены на рисунке 4.
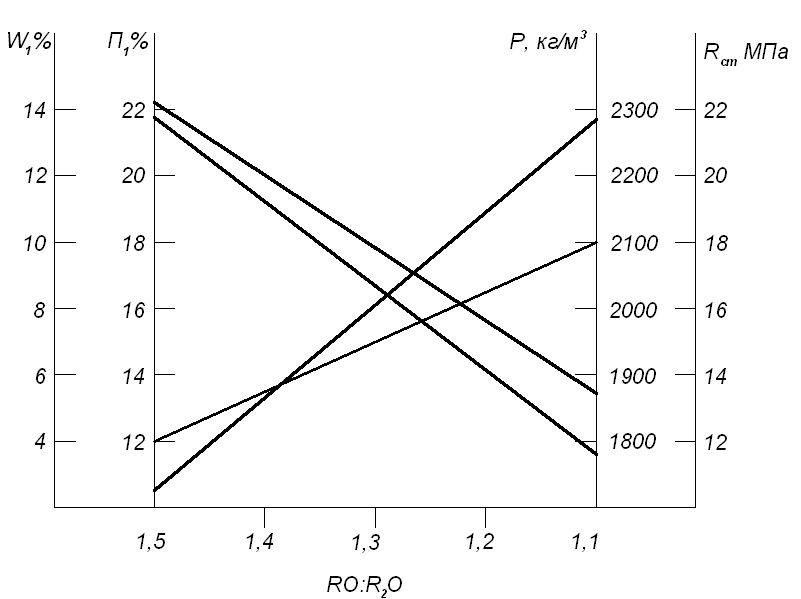
1 – водопоглощение; 2 – пористость; 3 – водостойкость; 4 – прочность при сжатии
Рисунок 4 – Зависимость свойств образцов от соотношения RO:R2O
При температуре 1000-1050ºС образуется реакционноспособная жидкая фаза, интенсифицирующая растворение кремнезема и глинозема, что способствует повышению термостойкости образцов. Образец оптимального состава имеет следующие свойства: водопоглощение – 7-8%, пористость 12-13%, предел прочности при сжатии 20-22 МПа, термостойкость – 14-15 теплосмен за 8-10с.
При разработке сосотавов керамических материалов на щелочном алюмосиликатном связующем и гранитных отсевах, в качестве наполнителя был выбран тонкомолотый гранитный отсев, а щелочные компоненты представлены едким натром, карбонатом натрия (технической содой), содо-сульфатной смесью. Расход щелочного компонента составлял до 5% по Na2О. Заполнителем является гранитные отсевы фракции 1-3 мм – 50%; 0,14 – 1 мм – 40%; менее 0,14 – 10%. Количество молотого и немолотого гранитного отсева, а так же количество связки варьировалось исходя из свойств формовочной смеси и трещиностойкости образцов (таблица 3).
Для интенсификации процесса обжига и обеспечения необходимых физико-механических свойств плит в процессе скоростного обжига в роликовой щелевой печи в состав плиточных масс был введен стеклобой в количестве 5-10% и добавки в виде 5% фосфогипса или шлака. Выявлено, что газопроницаемость при 120ºС составляет 0,68·10-5, а после 800ºС – 0,82·105 м2/Па·с. Эти показатели почти в 2 раза превышают газопроницаемость обычных керамических масс на основе глинистых материалов. В этом случае через проницаемые поры будет диффундировать кислород во внутрь изделия, способствуя окислению органических веществ, и значительному прогреву изделия.
Были определены предельно безопасные кривые сушки плиток различного назначения. Так облицовочные плитки размером 300х200х5мм при однорядной укладке могут быть высушены без дефектов за 7-8 мин, плитки для полов размером 300х300х10мм за 40-50 мин. Также были определены безопасные скорости нагрева и охлаждения и допустимые перепады температур по плоскости плиток, которые исключают возможность образования трещин при нагревании до максимальной температуры и последующего охлаждения.
Таблица 3 – Составы сырьевой смеси и физико-механические свойства керамических материалов на основе гранитных отсевов
Состав сырьевой смеси соотношение в частях по массе | Щелочной компонент | Прочность образцов при сжатии, МПа | Средняя плотность, кг/м3 | ||
в связке SiO2 Na2О | ГО-заполнитель связка | Сушка 1050С | Обжиг 950-1100°С | ||
2,5 | 6,0 | NaOH | 10,5 | 38,2 | 2110 |
2,6 | 5,8 | NaOH | 10,9 | 38,8 | 2140 |
2,7 | 5,6 | NaOH | 11,6 | 39,1 | 2180 |
2,8 | 5,7 | NaOH | 12,1 | 40,4 | 2220 |
2,9 | 5,2 | Сода | 7,4 | 25,8 | 2020 |
3,0 | 5,0 | Сода | 7,8 | 26,3 | 2040 |
3,1 | 4,8 | Сода | 8,4 | 26,9 | 2060 |
3,2 | 4,6 | Сода | 9,3 | 28,2 | 2080 |
3,3 | 4,4 | ССС | 5,1 | 15,3 | 1820 |
3,4 | 4,2 | ССС | 5,5 | 15,8 | 1850 |
3,5 | 4,0 | ССС | 5,7 | 16,4 | 1870 |
Исследования свойств керамических строительных материалов на основе фосфатно-глинистых сланцев проводились в сырьевых системах фосфатно-глинистый сланец – суглинок – фосфогипс. Для установления функциональных зависимостей свойств образцов от состава с целью их оптимизации, применяли симплекс решетчатый метод планирования Шеффе. За параметры оптимизации керамических масс принимались: коэффициент чувствительности к сушке – как критерий сушильных свойств смеси и прочность при сжатии готовых изделий – как показатель качества изделий.
В качестве варьируемых факторов были выбраны: Х1 – фосфатно-глинистые сланцы; Х2 – суглинок; Х3 – фосфогипс;
Уравнения поверхности отклика для выбранного приближения имеют вид: для сырцовой прочности:
у=0,36х1+1,2х2+0,46х3-0,145х1х2+0,627х1х3+0,95х1х2х3 (1)
для прочности при сжатии:
у=8,2х1+15,8х2+6,4х3+1,35х1х2–2,25х1х3–4,05х2х3+8,1х1х2(х1–х2)–
–0,45х1х3(х1–х3)–0,45х2х3(х2–х3)+24,75х1х2х3 (2)
Анализ диаграмм «состав-свойство» в системе фосфатно-глинистый – суглинок – фосфогипс показывает, что увеличение содержания суглинка повышает показатели сырцовой прочности при сжатии обожженных образцов. За оптимальные составы рассматриваемых систем принимали смеси, обладающие удовлетворительной сырцовой прочностью и прочностью при сжатии готовых изделий. В рассматриваемых системах этим требованиям соответствуют составы сырьевых смесей, находящиеся в области ограниченной следующими предельными концентрациями компонентов, мас.%: фосфатно-глинистый сланец 70-75; суглинок 23-27; фосфогипс 5-10. Прочная структура керамики, обеспечивающая высокие эксплуатационные свойства формируется на стадии обжига. В этом случае процесс фазообразования во многом определяются составом шихты и свойствами составляющих ее компонентов. Процессы фазообразования в глинах и в сочетании различных добавок достаточно хорошо изучены. Однако очень мало сведений по фазообразованию в указанной системе.
Чтобы установить тип кристаллических фаз и соединений, образующихся в обожженных при различных температурах керамических массах системы Са3(РО4)2 – A12О3 – SiО2, на основе которых получены керамические материалы, с использованием ФГС нами использован термодинамический метод анализа. Для синтезированных керамических материалов предусмотрены варианты реакций, в результате которых можно было ожидать образования перечисленных ранее кристаллических фаз:
Са3 (РO4)2 + 6 А12О3 + 8 SiО2→3Al2O3∙2SiО2 +3(CaO·Al2O3∙2SiO2)+P2O5·SiO2
Са3 (РО4)2 + 6 (А12O3∙2 SiО2∙2 Н2O)→3 А12O3 ∙2 SiО2+3(CaO∙А12O3∙2 SiO2)+Р2O5·SiO2+ +12Н2O,
Са3 (РO4)2+5 А12O3 + 7SiO2→3Al2O3 + 2SiO2+2(CaO∙Al2O3∙2SiO2)+CaO∙SiO2+ P2O5· SiO2
Ca3 (PO4)2+5 (Al2O3∙2SiO2∙2H2O)→3 Al2O3∙2 SiO2+2 (CaO∙Al2O3∙2 SiO2)+CaO∙SiO2 +P2O5·SiO2+10H2O. 3CaO+CaF2+2SiO2=Ca4(Si2O7)F2 (3)
Чтобы установить предпочтительность протекания той или иной реакции, рассчитывали изменения энергии Гиббса ΔG по известной методике с привлечением термодинамических констант веществ, участвующих в реакциях. Расчеты проводили по формуле
ΔG=ΔHo+Δ a Т ℓn T – Δb Т2/2 - Δc Т–1 /2 + y Т, (4)
где ΔHo – теплота образования вещества, кДж/моль; Δa, Δb, Δc – коэффициенты; Т – температура, К; у – константа интегрирования.
Высокие отрицательные значения ΔG0т этих реакций свидетельствуют об окончательном формировании в структуре синтезированных керамических материалов кристаллических фаз муллита, анортита, витлокита, волластонита и куспидина.
Для исследования спекания содержание сланцев в составах композиции изменяли от 50 до 70 %. При этом охватываются как критические (30-35%), так и наиболее вероятные (35-50%) интервалы содержания глинистых сланцев агрегатов, обуславливающих возможность получения прочных структур с ядром из непластичных силикатов, к которым относятся глинистые сланцы. Для получения частиц сланца с максимальным размером 1,25-3,0 мм и преимущественным – 0,5-1 мм и глинистых агрегатов с размерами в границах 0,05-0,25 мм, установленных при моделировании структур как наиболее оптимальные, сланцы после предварительной сушки мололи до прохождения через сито с ячейкой 3 мм, а глины – 1 мм. После помола содержание оптимальных по размерам сланцевых и глинистых агрегатов составляют 47,7 и 62,7% соответственно. С учетом относительно высокого содержания оптимальных по размеру агрегатов после помола и с учетом последующего домола в процессе приготовления смеси, в том числе наиболее крупных и легко измельчаемых агрегатов сланца, предполагалось, что принятая подготовка сланца и глин будет приемлемой для прочных структур из их композиций.
Спекание композиции глин с глинистыми сланцами проводили на образцах-цилиндрах диаметром и высотой 25мм. В качестве добавок были использованы кальций содержащие компоненты как фосфогипс, дефекционный шлам в количестве 5 мас.%, а в качестве выгорающей добавки – угольную пыль в количестве 1-3%. Смесь компонентов в заданном соотношении перемешивали и при 8 % прессовали образцы под давлением 20-25 МПа. Сушка образцов производилось в радиационной сушилке при максимальной температуре 105°С в течение 5 ч, обжиг в муфеле 3 ч при температуре 1100°С с изотермической выдержкой 0,3 ч. При содержании глин в количестве 40%, гарантирующем достаточную плотность упаковок, эффект спекания становится значительным и прочность образцов составляет 40-45МПа. С увеличением количества глины в композициях выше 40% эффект спекания продолжает возрастать. При содержании глин в критических границах (25-42%) эффект спекания проявляется в меньшей мере и прочность образцов находится в пределах 30-40 МПа. При содержании глин менее 25% эффект спекания самый низкий и прочность образцов составляет 15-25 МПа.
Спекаемость композиций глинистых сланцев с глинами находится в хорошем соответствии с прогнозом, сделанным на основе их структур. При температурах обжига ниже (1000°С) эвтектических, агрегаты из частиц сланца спекаются хуже, чем агрегаты из глинистых частиц. Поэтому спекание композиций из сланцев с глинами происходит за счет спекания глин. При этом высокая прочность образцов из композиций достигается при содержании глин 40-90%, обеспечивающем плотность упаковок, и относительно толстые спекающиеся глинистые сланцы вокруг ядер.
Как и прогнозировалось при моделировании структур, агрегаты сланцев, связанные оболочками из глинистых агрегатов, являются основой реальных структур. Однако в отличие от модельных, в реальных структурах отмечается случайное неравномерное распределение агрегатов и их конгломерация. Чем больше содержание сланца в композиции и чем выше степень конгломерации агрегатов сланца, тем неравномернее толщина связующей глинистой оболочки и степень спеченности в отдельных зонах. Эти факторы в сочетании со снижением плотности упаковок при уменьшении содержания глинистых агрегатов от 40 до 20% являются причинами понижения прочности образцов. Вместе с тем формирование благоприятного фазового состава обуславливает сохранение достаточно высоких значений прочности образцов из композиций, содержащих глину в количестве 20-30%.
Как уже отмечалось, при обжиге сланцев в них, так же как и в глинах образуется муллитоподобная фаза. При обжиге смеси сланцев с глинами образование муллитоподобной фазы активизируется. Так, если на рентгенограммах глин и сланцев, обожженных при температурах 1000-1050°С, муллитоподобная фаза проявляется единичными отражениями, то на рентгенограмме смеси компонентов, обожженных при этих же температурах муллитоподобная фаза проявляется всеми d/n (3,42; 2,68; 2,56; 2,12)·10-10м. Одновременно усиливается образование анортита, о чём свидетельствует увеличение количества и интенсивностей его максимумов на рентгенограммах образцов, обожженных при температурах 1000-1050°С. Дополнительно при обжиге смеси глины со сланцами образуются волластонит (2,79∙10-10м).
Петрографические исследования фазового состава обожженной при 1000°С керамики из композиций с 60% сланца, подтверждают, что связующая оболочка вокруг крупных зёрен сланца содержит порядка 10 - 20% кристаллов и около 20% зёрен кристаллов полевого шпата (анортита) размером 0,1 мм.
В пятом разделе приводятся результаты исследовании по технологии стеновой керамики на основе высококварцевого техногенного сырья фосфатно-кремнистых и углисто-кремнистых сланцев.
В системе углисто-кремнистых сланец – суглинок – фосфогипс для установления функциональных зависимостей свойств образцов от состава с целью их оптимизации, применяли симплекс решетчатый метод планирования Шеффе. За параметры оптимизации керамических масс принимались: прочность при сжатии готовых изделий, сырцовая прочность – как показатели качества изделий. Анализ диаграмм «состав-свойство» в системе углисто-керамические сланцы-суглинок-фосфогипс показывает, что увеличение содержания суглинка и фосфогипса повышает показатели сырцовой прочности, а также прочность при сжатии обожженных образцов.
За оптимальные составы рассматриваемых систем принимали смеси, обладающие удовлетворительной сырцовой прочностью и прочностью при сжатии готовых изделий. В рассматриваемой системе этим требованиям соответствуют составы сырьевых смесей, находящиеся в области ограниченной следующими предельными концентрациями компонентов, мас%: углисто-кремнистые сланцы 60-70%; суглинок30-35%; фосфогипс 5-10%. Установлено, что в синтезированных материалах присутствуют кристаллические фазы муллита, анортита, витлокита, волластонита. Изучен процесс спекания обжиговой связки с участием жидкой фазы шихты, состоящей из тугоплавких фосфатно-кремнистых сланцев 10-20%, Ленгерской глины 65-80% (Тпл=1530°С) и легкоплавкого стеклобоя 10-15% (Тпл=850°С).
Для анализа полученных кривых усадки был использован метод математического моделирования процесса. Предложенная модель позволила систематизировать результаты и произвести расчет линейной усадки в зависимости от режима спекания, включая стадию нагревания. Для этого были построены графики динамики усадки в координатах (∆l/l)-, при этом за нулевой момент времени для каждого образца было принято начало усадки. Процесс спекания, сопровождаемый усадкой, начинался практически при одной и той же температуре (900°С) независимо от режима предварительного нагревания. Для каждого образца вычислили относительную усадку, считая исходным состояние в нулевой момент времени при температуре 900°С. Результаты перевода кривых усадки в новую систему координат приведены на рисунке 5. Для удобства усадку считали положительной величиной.
Как видно из рисунка 5, где стрелкой обозначен момент выхода на постоянную температуру выдержки, до точки С все кривые усадки весьма разнородны, тогда как при постоянной температуре они имеют экспоненциальный характер-процесс спекания как бы затухает. Ввиду того, что температуру на лабораторной установке регулировали вручную, скорость усадки в неизотермическом режиме была существенно неравномерной. Поэтому для определения кинетических параметров воспользовались участками кривых, снятыми в изотермических условиях. Эти участки носили затухающий характер, и для каждой температуры имеем свое предельное значение усадки –
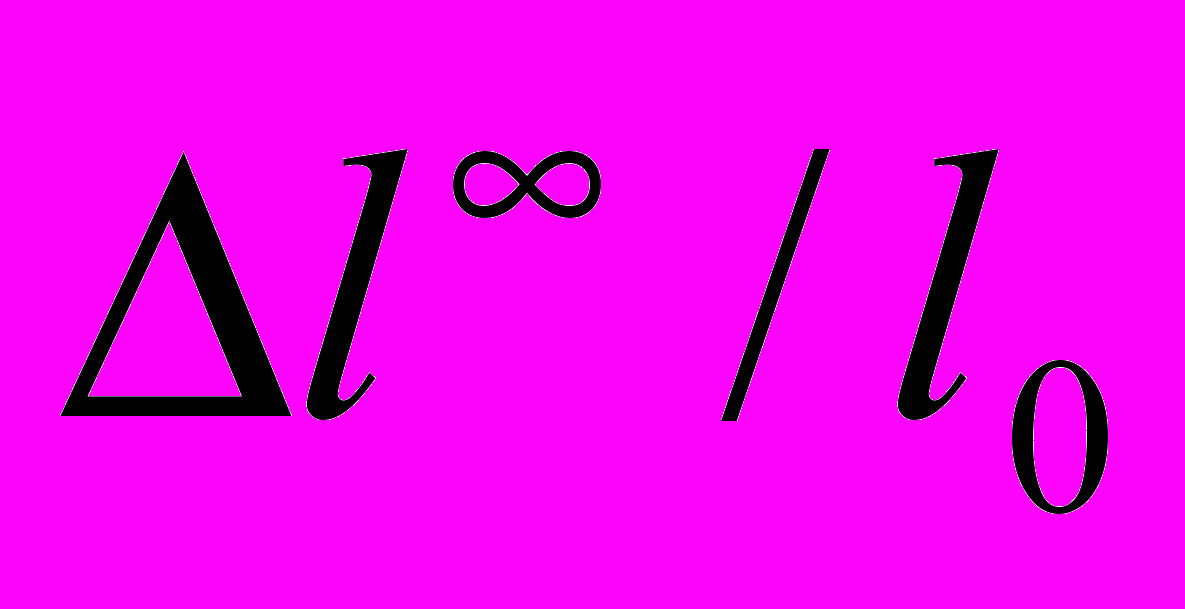
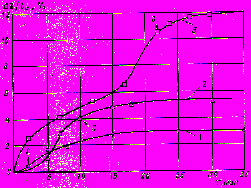
1 – при конечной температуре спекания 800°С, 2 – то же, 900°С, 3 – то же 1000°С
Рисунок 5 – Динамика линейной усадки во времени
Глубина и скорость протекания необратимой реакции первого порядка выражается следующим уравнением:
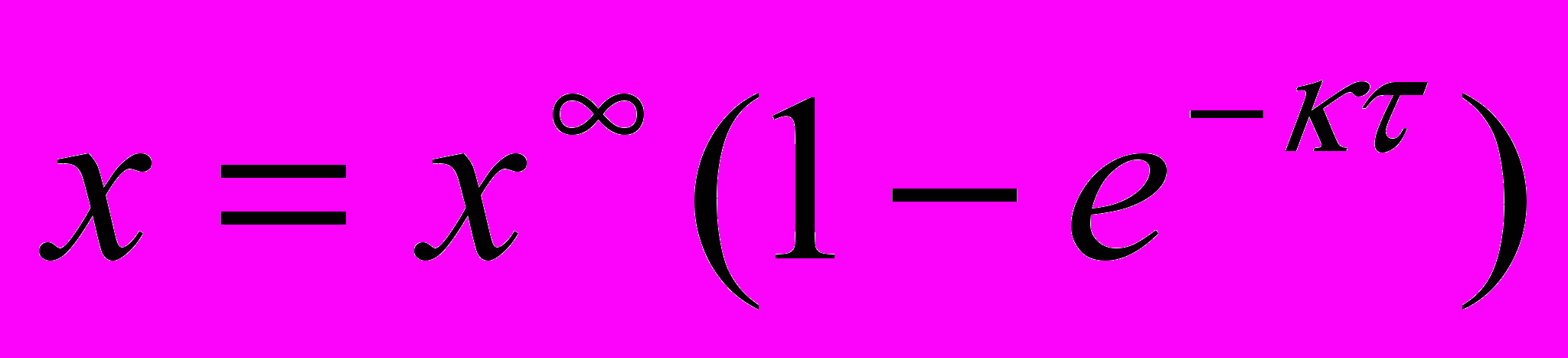
где х – степень превращения компонента (в нашем случае аналогом этой величины является линейная усадка); к – константа скорости реакции, зависящая от температуры.
Справедливость предложенной аналогии подтверждает прямолинейный характер зависимостей
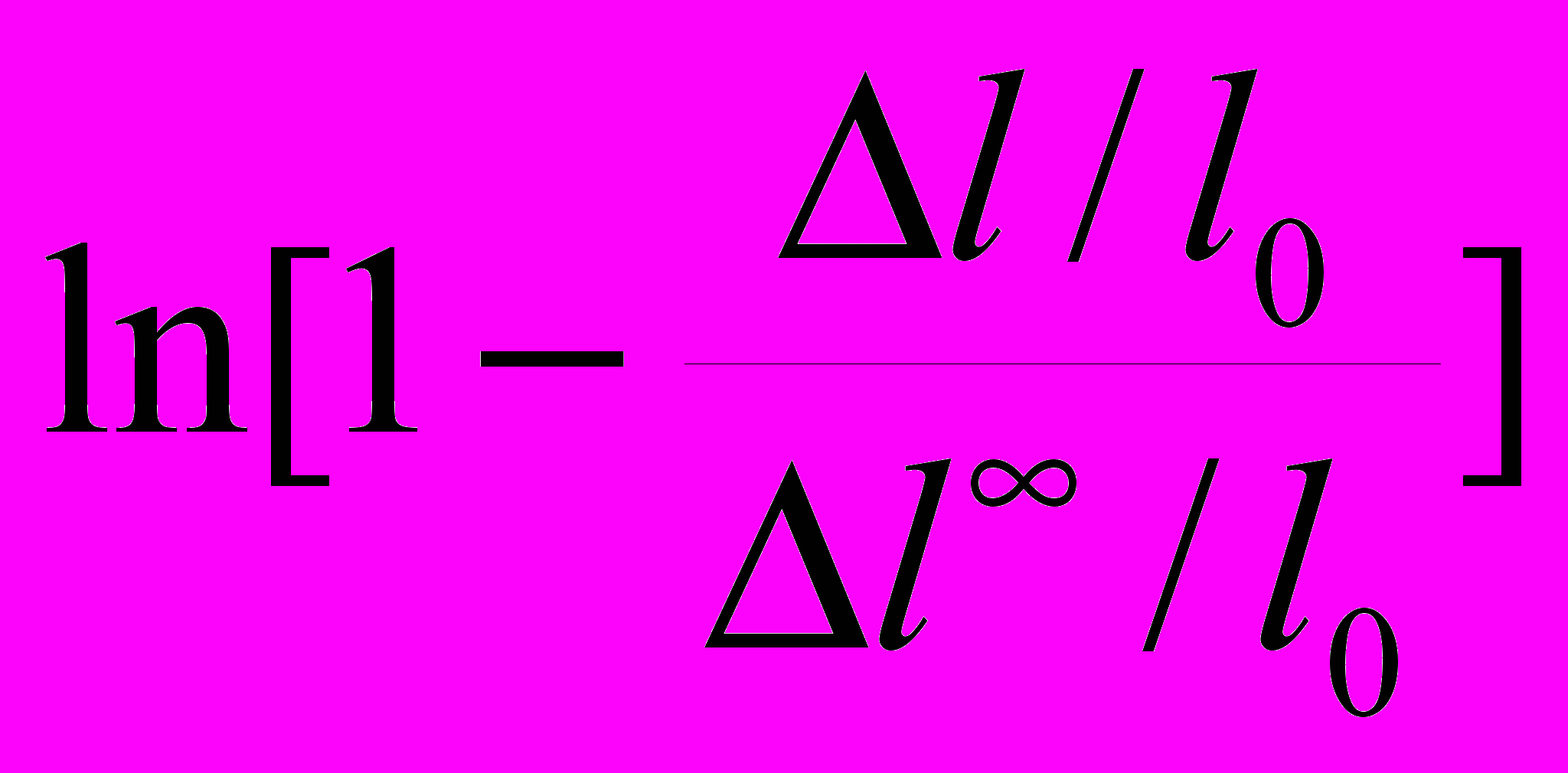
Как и в химической реакции связь константы скорости с температурой принято выражать уравнением Аррениуса:
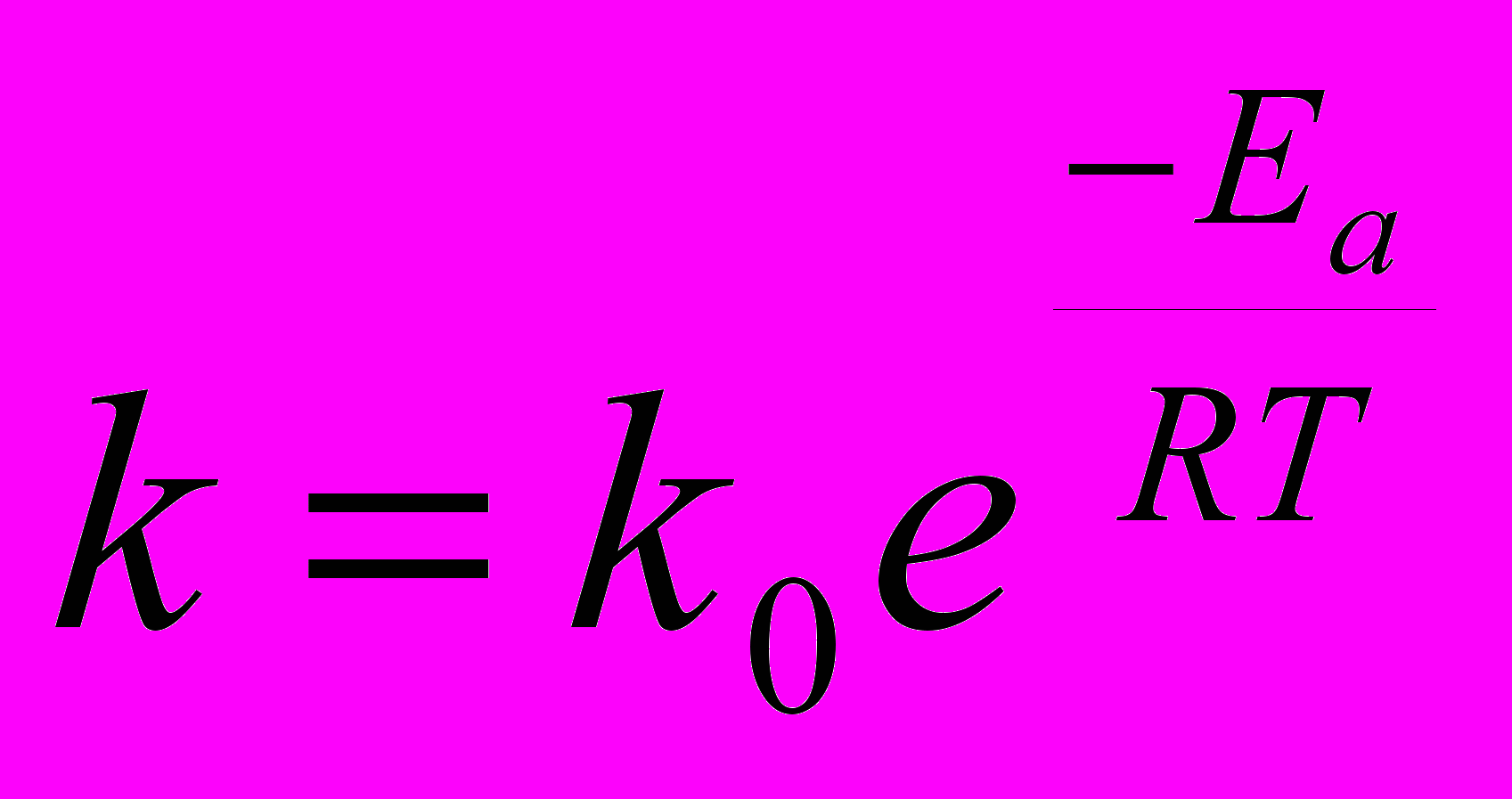
где Еа – энергия активации, кДж/моль; Ко – экспериментально определяемая постоянная, мин-1; Т – температура, 0С; R – газовая постоянная. Прологарифмировав уравнение (6), графоаналитическим способом определили постоянную
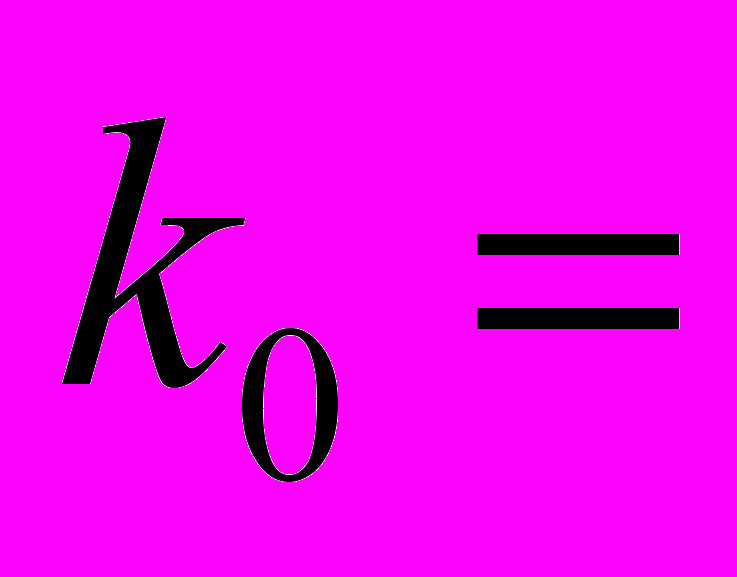
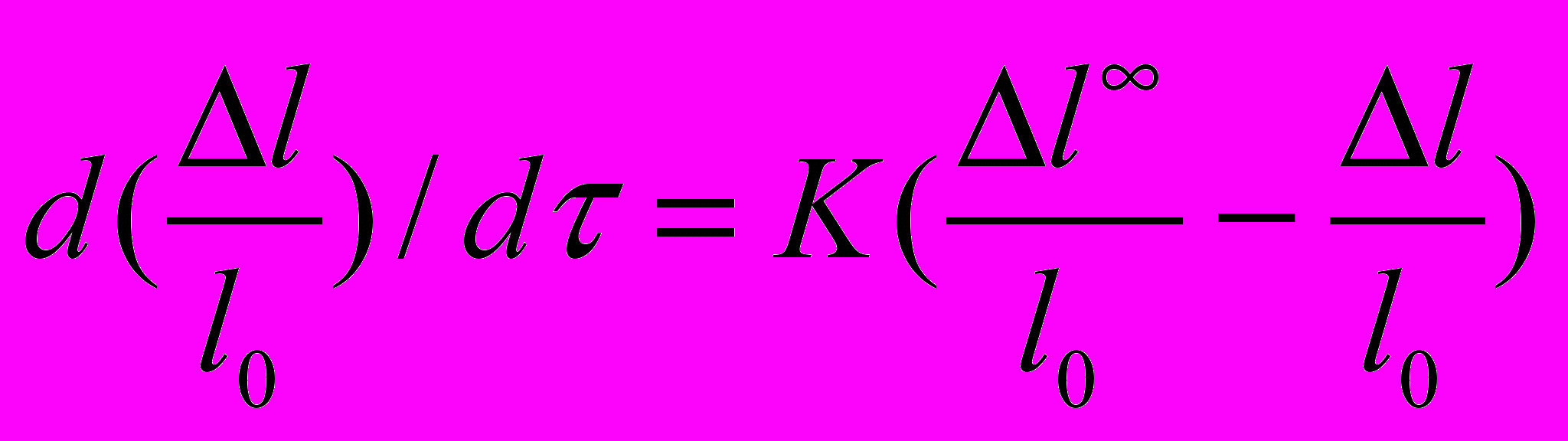
где
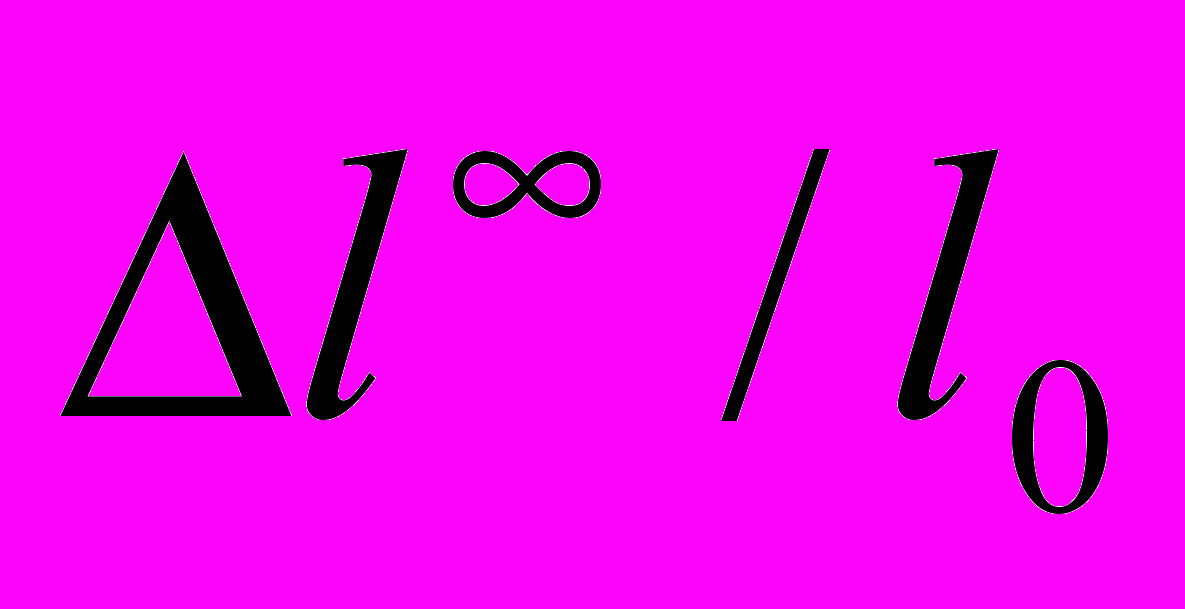
По-видимому, во всем температурном интервале кинетика спекания может характеризоваться этим уравнением, однако до выхода на изотермический режим на константу скорости влияет переменная температура, в свою очередь являющаяся функцией времени. Величина предельной усадки также будет переменной, зависящей от текущего значения температуры.
Предполагая, что режим нагревания задан в произвольной форме, можно записать в общем виде математическую модель динамики спекания:
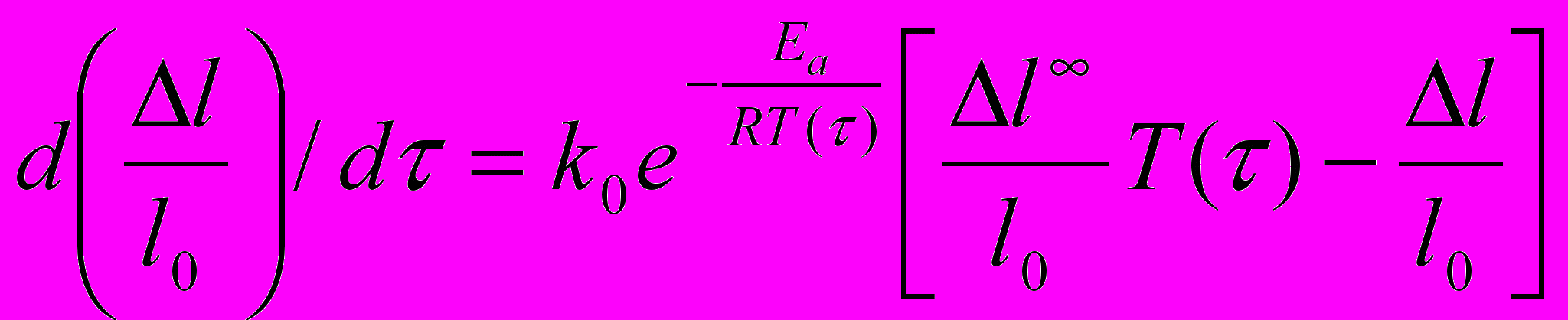
Поскольку уравнение (8) в общем виде не имеет аналитического решения, его необходимо интегрировать численными методами. Была использована программа , реализующая стандартный метод Рунге-Кутта для решения дифференциального уравнения первого порядка с правой частью.
В данном уравнении зависимость температуры от времени может быть произвольной. В программе использовалась кусочно-линейная аппроксимация температуры от времени. Для выражения связи предельной усадки с температурой для данной серии опытов было получено и использовано эмпирическое уравнение:
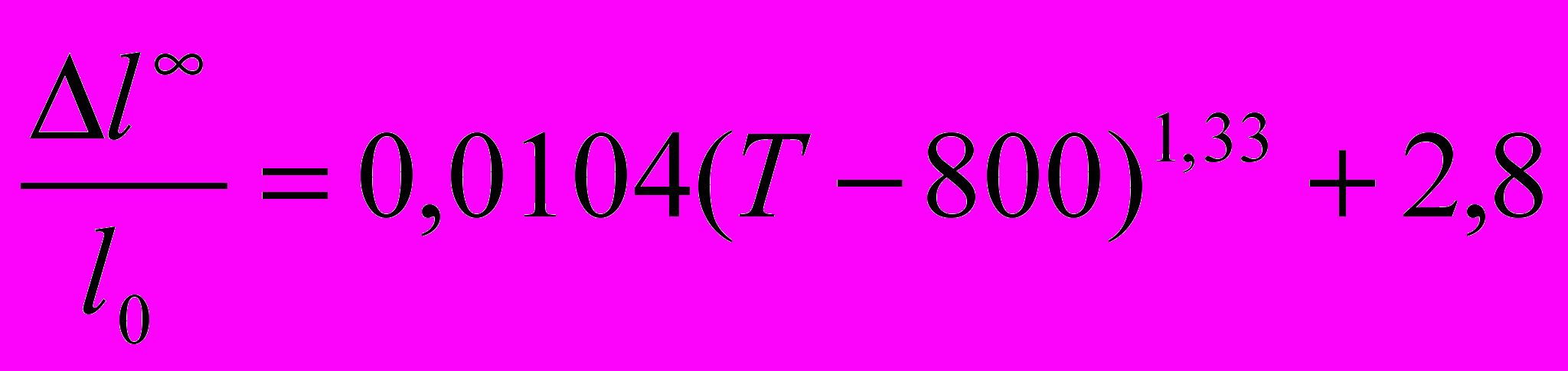
Предложенное уравнение может быть использовано для поиска оптимального режима жидкофазного спекания обжиговой связки в системе фосфатно-кремнистый сланец – глина – стеклобой. При разработке составов стеновой керамики на основе фосфатно-кремнистых сланцев были учтены результаты подбора фракционного состава, по результатам которого максимальным размером зерен принят размер фракции менее 2 мм. Учитывая, что с уменьшением размера зерен увиличивается расход связующего или тонкомолотой части, применяли фосфатно-кремнистый сланец фракции < 2,0 мм, смесь суглинка и каолинитовой глины, молотого стеклобоя. Для снижения энергозатрат как при приготовлении исходной шихты, так и при ее термической обработке предложена сырьевая смесь для получения стеновых обжиговых изделий и способ их изготовления. Данная смесь состоит из немолотых углисто-кремнистых сланцев, раствора R2O – содержащего компонента, взятого в виде растворов солей, содержащих компоненты, выбранные из группы КОН, Na2CO2, Na2O∙mSiO2, NaSiO3, NaSiO4, NaNO3, либо их комбинации. Кроме того, в качестве добавок могут применятся отходы различных производств, содержащие вышеперечисленные компоненты по отдельности или в любых сочетаниях в виде растворов солей, обеспечивающих 1,5-3% влажности формовочных смесей в соотношении, приведенном в таблица 4.
Константа скорости полиморфного превращения кварца (в высокотемпературные модификации) при нагревании приближенно может быть вычислена по формуле:
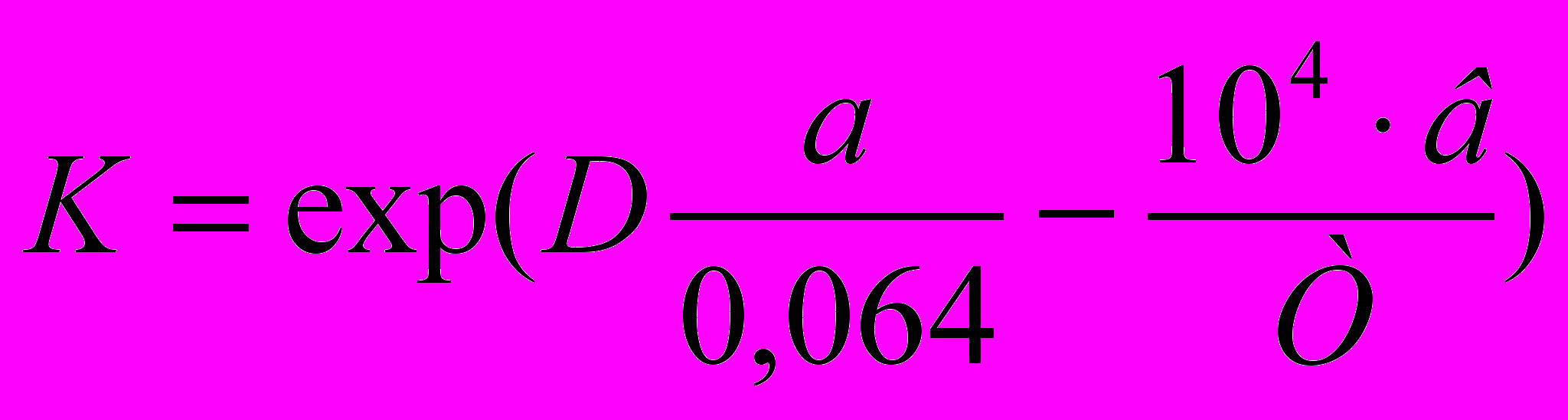
где D – диаметр зерна, мм; Т – абсолютная температура, К; а – постоянная, для кварца – 10,7, халцедона – 11,6, в – постоянная, для кварца – 3,16, халцедона – 3,02.
Вычисленная константа скорости реакции превращения кварца для зерен диаметром 0,15 мм при температуре 1100˚С– составляет 1,2 10-4.
При изучении реакции взаимодействия между Na2CO3 и SiO2 при молекулярном соотношении в смеси SiO2 - Na2CO3 равном 4:1 и температуре 1000˚С были получены величины представленные в таблице 5
Таблица 4 – Составы смеси для производства на основе углисто-кремнистый сланец по обжиговой технологии
№ состава | Содержание компонентов сырьевой смеси, мас. % | ||||
| Раствор соли R2O–содержащего компонента (в пересчете на NaOH) | УКС фракция ![]() | Молотый УКС | Стеклобой | Фосфогипс |
1 2 3 4 | 0,5-3 0,5-3 0,5-3 0,5-3 | 77-79,5 77-79,5 72-74,5 72-74,5 | 10 10 5 5 | 5 5 10 10 | 5 5 10 10 |
Таблица 5 – Количество прореагировавшего SiO2 от времени
Время, мин | Количество прореагировавшего SiO2 , доли единицы |
5 | 0,25 |
10 | 0,29 |
15 | 0,34 |
20 | 0,38 |
25 | 0,42 |
30 | 0,48 |
Константы скорости для случая, когда реакция лимитируется диффузией по Будникову и Гинстлингу, равны:
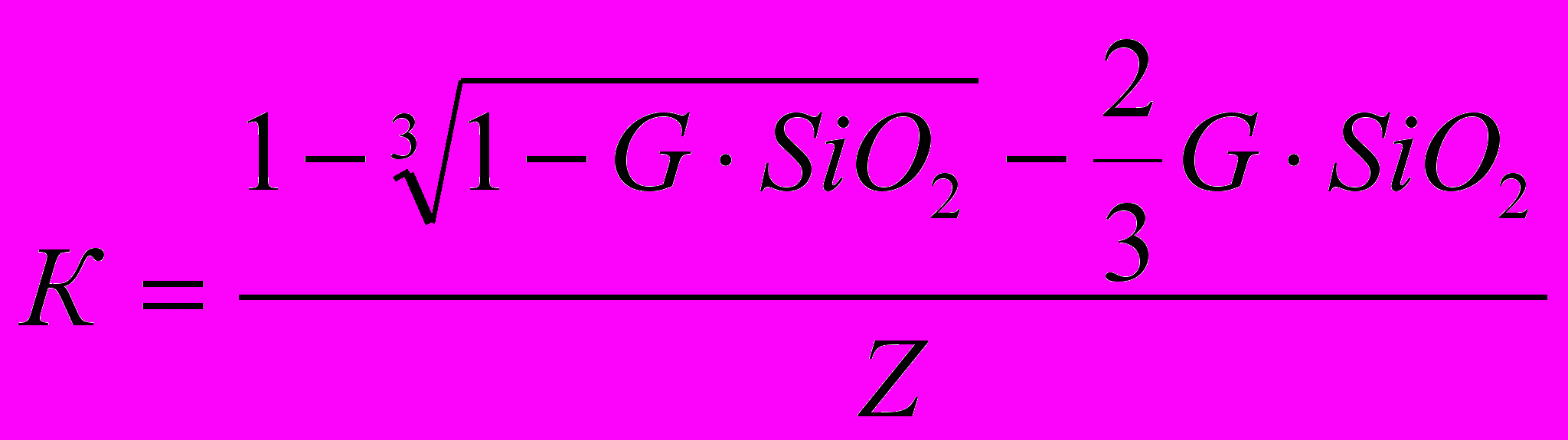
К при 60 мин равна 0,36·10-4, т.е. скорость процесса устанавливается через 60-90 мин. Предложенные составы позволяют получать стеновые керамические материалы, удовлетворяющие требованиям для мелкоштучных дорожно-строительных материалов (плотность, кг/м3 – 1400-1900; предел прочности при сжатии, МПа – 15-50; морозостойкость, циклы – 100-200; водопоглощение, % – 0,4-6; истираемость, г/см2 – 0,4). Разработанный способ горячего прессования материалов и изделий при температуре 150-200°С и давлении 20-30МПа позволяет раскрыть и максимально использовать ценные свойства растворимых стекол - высокоэффективного связующего вещества, обладающего высокими цементирующими свойствами и твердеющего в условиях повышенных температур аналогично полимерному связующему веществу. Полимеризационный характер твердения силикатных смесей в условиях повышенных температур и давлений оказывает заметное влияние на скорость технологического процесса изготовления материалов, выражающееся в значительной интенсификации процесса твердения. Форсирование процесса твердения силикатных смесей за счет горячего формования дает возможность в кратчайшее время получить изделие, сократив при этом процесс твердения силикатных смесей и одновременно повысить прочность сырца.
Метод горячего прессования минеральных смесей является не сложным и высокопроизводительным, а технологические процессы могут быть полностью механизированы и автоматизированы, что ведет к снижению трудоемкости и стоимости выпускаемой продукции. В результате исследований установлены оптимальные режимы горячего прессования силикатных смесей, разработаны рецептурные составы, изучены свойства полученного материала.
В шестом разделе приводится разработка составов и технологий керамических строительных материалов на основе доменных шлаков Таразского металлургического завода. Для исследования использовали шлак ферросиликомарганца Таразского металлургического завода с размером зерен менее 3 мм, суглинок и фосфогипс. С целью изучения процессов спекания в данной композиции и возможности получения керамических материалов на ее основе были исследованы двойные композиции «суглинок-фосфогипс» и «суглинок – доменный шлак». Процессы спекания в композициях «суглинок – фосфогипс» изучались с целью получения на их основе обжиговых связок. Визуальный осмотр образцов, обожжённых при высоких температурах, показал, что образцы с содержанием фосфогипса выше 30% проявляют склонность к деформации и при этом наблюдаются явления вспучивания и оплавления краев образцов. Поэтому основное внимание уделялось изучению образцов, содержащих 10-30% фосфогипса. С увеличением содержания фосфогипса в исследуемой смеси растет водопоглощение, а усадка при этом изменяется незначительно. Этот факт свидетельствует об образовании пористой структуры обожженных образцов. Причем, пористость структуры и высокое водопоглощение существенно не влияют на степень прочности исследуемых образцов. С повышением температуры растет усадка образцов, водопоглощение относительно уменьшается, показатели прочности повышаются. Было замеченно, что увеличение содержания фосфогипса в массе уменьшает показатели прочности образцов. По данным ДТА процесс разложения CaSO4 начинается уже при 900°С и значительно ускоряется с повышением температуры. Этот факт подтверждается тем, что на ренгенограммах обожженных образцов выявляется линия анортита уже при 1000°С. С увеличением содержания фосфогипса в массе интенсивность линий анортита растет. Интенсивность линий кварца на рентгенограммах заметно снижается, что свидетельствует об активном участии кремнезема в химических реакциях. Наряду с анортитом при 1000°С выявлены кристаллические фазы: муллит (0,530;0,378;0,288 нм), волластонит (0,268;0,219 нм) и α-кристобалит (0,404;0,249 нм). Результаты исследования процессов спекания композиций суглинок-фосфогипс свидетельствуют о том, что процесс спекания масс до температуры возникновения эвтектического расплава (1050°С) идет в твердом состоянии без участия жидкой фазы, а затем – до температуры плавления (1150°С) с участием жидкой фазы. Природа сырьевых компонентов и их соотношение значительно влияют на свойства обожженных образцов. В изученном интервале составов и температур все образцы характеризуются пористой структурой и по физико-химическим свойствам близки к пористым керамическим материалам. Композиция «суглинок – доменный шлак». Исследования показали, что в массах, содержащих 40% доменных шлаков и 60% суглинка, температура спекания заметно снижается благодаря образованию большого количества жидкой фазы.
Рентгенографический анализ обожженных образцов показывает, что основными кристаллическими фазами спекшихся образцов являются муллит, гематит, силикаты Са и Mg, кварц, тридимит. На рентгенограммах образцов, содержащих 30% доменных шлаков, наблюдается постепенное нарастание линий кристаллических фаз с ростом температуры от 500°С до 1200°С. При температуре 1200°С интенсивность линий кристаллических фаз несколько снижается, что объясняется тем, что при такой температуре происходит плавление компонентов доменного шлака.
В результате рентгенографического, петрографического и электронно-микроскопического исследований фазового состава и структуры керамических материалов установлено, что конечным продуктом спеченных образцов является муллит, анортит, гематит, как правило, обусловливающие высокие показатели свойств образцов. Композиция «суглинок – фосфогипс». Составы масс для изучения керамических свойств и процессов спекания композиций «суглинок – доменный шлак – фосфогипс» были приготовлены с учетом данных, полученных при изучении двойных композиций: «суглинок – фосфогипс» и «суглинок – доменный шлак». Увеличение водопоглощения при повышении процентного содержания фосфогипса в исследуемой смеси, вероятно, связано с образованием пористой структуры полученных спеченных образцов. Пористость их связана с диссоциацией фосфоангидрита и выделением SO3 в газовую среду. Степень диссоциации фосфоангидрита зависит от вида сопутствующих примесных оксидов и, согласно литературным данным, оксиды Al2O2, SiO2, F2O3 оказывают значительное влияние на скорость диссоциации фосфогипса. Необходимо отметить что, несмотря на образование пористой структуры, образцы отличаются высокой прочностью. Результаты исследований показали что спекание происходит с участием жидкой фазы уже при температуре 1000°С, чему способствуют флюсующие свойства доменных шлаков. Твердофазные реакции минералообразования в изучаемых композициях ускоряются, возможно, благодаря присутствию примесей в фосфогипсе, в частности P2O5 и F. Например, установлено, что в присутствии Р2О5 ускоряется образование соединений более насыщенных кальцием. Кривые нагревания масс М1 и М2 показывают, что после процесса удаления гигроскопической воды при 120-150°С интенсивно идет процесс перехода растворимой формы CaSO4 (III) в нерастворимую CaSО4 (II) и процесс модификационного превращения низкотемпературной формы кварца β – SiО2 в высокотемпературную α – SiО2 (при 575-590°С). Реакция диссоциации фосфоангидрита начинается уже при температуре 960°-980°С. Эти процессы интенсифицируются флюсующим свойством доменного шлака.
Рентгенографический анализ исследуемых образцов показывает, что в случае образцов из массы (22,5% доменного шлака) уже при температуре 1000°С наблюдается отсутствие ангидрита CaSO4 и появление кристаллических фаз aноргита, α–кристобаллита и муллита, интенсивность линий которых на рентгенограммах увеличивается с повышением температуры. Электронномикроскопическое исследование спеченных образцов состава суглинка – 70; доменного шлака – 20-22,5; фосфогипс – 7,5 показало, что основные элементы структуры, это многочисленные хаотично расположенные кристаллы: игольчатые – муллита (0,71-3,14 ммк), призматические – анортита (2,85-3,71 ммк), таблетчатые – волластонита (0,86-1,71 ммк), скрепленные стеклом. Для направленного изменения свойств керамических материалов в зависимости от состава нами была составлена математическая модель экспериментов с использованием симплекс решетчатых планов. Получены математические уравнения регрессии для четырех свойств исследованной композиции: «состав-усадка», «состав-водопоглощение», «состав-Rизг», «состав-Rсж». Для исследования зависимости свойств строительной керамики от размера зерен высококальциевого шлака в массах использовали шлак Таразского металлургического завода с максимальными размерами зерен меньше 3 мм и керамические связки на основе глин с содержанием стеклобоя от 30 до 50%. Подбор зернового состава шлака с минимальной пустотностью проводили с учетом существующих представлений о рациональном зерновом составе смесей и с учетом имеющегося опыта изготовления керамических материалов, в частности огнеупоров, из шихт грубого помола. Исходя из этого, пробы шлака с размером зерен 3 мм рассеивали на сите с размером ячейки 0,5 мм, определяли их межзерновую пустотность, затем готовили смеси фракций. Количество фракций с размером зерен более 0,5 мм оставляли в пределах 60-65%, количество фракций с размером зерен менее 0,5 мм - в пределах 35-40%.
В композициях со шлаком использовали те же легкоплавкие связки из смеси суглинка с монтмориллонитовой, каолинитовой глины со стеклобоем. Связки из смеси суглинка с пластичной Ленгерской глиной (П=19-29) со стеклобоем характеризуются хорошей спекаемостью и за счет образования в них кварца и анортита обладают сродством к зернам шлака, сложенным богатой кремнеземом стеклофазой и кварц-анортитовой кристаллофазой. Кривые плавкости связок лишь с максимальным содержанием стеклобоя (40-50%) лежат выше кривой плавкости шлака и только в интервале температур разового появления расплава и его первоначального роста. Кривые плавкости этих же связок при более высоких температурах, а связок с содержанием 20-30% стеклобоя при всех температурах, отстают от кривой плавкости шлака. Однако это отставание невелико и в реальных условиях оно, вероятнее всего, компенсируется за счет тонкой дисперсности связок, с одной стороны, и за счет известного влияния кальциевых ионов, переходящих в расплав при взаимодействии связок с поверхностью зерен шлака и тончайшими его зернами в пробе, на снижение температуры плавления связок и повышение их активности, с другой.
При обжиге смеси связок со шлаком, хотя и в меньшей степени, но так же усиливается образование анортита и дополнительно отмечается образование волластонита, улучшающих свойства керамики.
Экспериментальные исследования подтверждают, что приведенные свойства керамических связок обуславливают спекание композиций со шлаком. Причем, за счет влияния кальциевых ионов, как и предполагалось, образцы из композиций со шлаком спекаются легче, чем образцы из композиций с кварц-полевошпатовым песком. Для достижения примерно одинаковой степени спекания в композиции со шлаком требуется вводить меньшее количество связки, снижать количество стеклобоя в них и понижать температуру обжига образцов. При этом можно манипулировать одновременно всеми тремя факторами, можно двумя или одним из них. Например, спекание образцов из композиций с высококальциевым шлаком до водопоглощения 6-7% достигается при использовании 30% связки с содержанием 30% стеклобоя в ней при температуре обжига 1100°С. Спекание образцов из композиций со шлаком до водопоглощения менее 1% достигается при использовании связок с содержанием 30-50% стеклобоя и смеси суглинка и глины в составе композиции в количестве от 30 до 50% в составе композиций при температуре 1120°С. Структура образцов из композиций зернистого шлака со связками является наиболее ярко выраженным вариантом структур по типу "ядро – оболочка". А характер структур шлака со связками наиболее четко отражает процесс их формирования. По структуре образцов с водопоглощением 6-8% видно, что связка образует оболочки вокруг крупных и расположенных между ними средних и мелких зерен шлака. Видно, что оболочки взаимодействуют с поверхностью зерен с образованием кристаллических фаз волластонита и анортита. Взаимодействие оболочки с зерном протекает очень активно, от поверхности зерна шлака к оболочке образуется достаточно заметная переходная зона как результат этого взаимодействия. Образование переходной зоны обуславливает согласованность шлакового зерна с оболочкой и растрескивания зерен шлака не происходит. Поэтому прочность образцов высокая и составляет 190-210 МПа при сжатии и 16-19 МПа при изгибе.
Из структуры плотно спеченных образцов, которая достигается при использовании максимального (50%) количества стеклобоя в связке или после обжига при более высокой температуре (1120°С), видно, что мельчайшие зёрна шлака вовлекаются в процесс образования жидкой фазы в полном или почти полном объёме. Повышается количество и реакционная способность стеклофазы. Это выражается в увеличении толщины промежуточной зоны от поверхности крупных зёрен шлака к оболочкам вокруг них, в активизации кристаллизации новых фаз в виде волластонита и анортита в оболочке. Кроме того, понижение вязкости стеклофазы за счёт кальциевых ионов, увеличение её проникающей способности и сродство стеклофазы к зёрнам шлака способствуют её растеканию по поверхности образцов и образованию стекловидного покрытия, которое при охлаждении за счёт кристаллизации волластонита становится непрозрачным и белым по цвету.
При исследовании спекания образцов с зернистым шлаком из других проб установлено, что с увеличением максимального размера зёрен в пробах шлака до 3 мм снижаются прессовочные свойства композиций. Для получения достаточной прочности сырца приходится снижать количество шлака в композиции и увеличивать массивность образцов. Например, при увеличении максимального размера зёрен в шлаке с 1 до 3 мм его количество в композиции уменьшается с 70 до 50-60%, а толщина плоских образцов увеличивается с 10 до 15 мм.
Приведенные результаты показывают, что наиболее активное спекание и формирование плотных структур в грубозернистых композициях с высококальциевым шлаком происходит при содержании 30-50% связки. Наличие плавня в материале оболочки вокруг зерен шлака обуславливает менее заметное, чем при отсутствии плавня, снижение плотности образцов, при содержании связки ниже 40%, в частности при содержании связки 30%, что находится в соответствии с моделированием смешанных структур керамики.
В седьмом разделе приводятся рекомендации по внедрению разработанных составов и технологии в производство. Анализ спекания, структуры и свойств керамических образцов показывает (таблица 6), что можно выбрать составы композиций из смеси глин с грубозернистыми компонентами, гарантирующих получение кирпича марок 150-250 по прочности и марок 25-50 по морозостойкости, облицовочного камня, клинкерного кирпича и тротуарной плитки, керамической черепицы и тонкой строительной керамики. Для подтверждения возможности получения этих видов керамических изделий проведено их изготовление в условиях производства на предприятиях Жамбылской области. Для получения высокопрочного и морозостойкого кирпича можно использовать композиции из глин с отсевом глинистых сланцев в количествах 50-70%, композиции с высококальциевым шлаком в количествах 50-60% либо со смесью суглинка с бентонитовой и каолинитовой глинами. Прочность обожженных образцов при сжатии из этих композиций составляет 19,7-55,3 МПа, морозостойкость 24-50 и более циклов и плотность 1740-1820 кг/м3. Образцы из композиций глин с отсевом глинистых сланцев характеризуются небольшим расширением (0,3 %), образцы из композиций с другими непластичными компонентами – незначительной усадкой (- 0,8).
На кирпичном заводе (ТОО «Стройсервис – Эльф» г.Тараз) методом полусухого прессования проведено опробование трех составов, содержащих ГО, ОГС, ЦП, ФКС, ФГС, УКС. Подготовку компонентов проводили по технологии, полученной в ходе научных исследований и исходя из особенностей применяемых компонентов. При изготовлении кирпича глины мололи до прохождения через сито с размером ячейки 1 мм, ГО, ФКС, ФГС - до прохождения через сито с размером ячейки 3 мм. При промышленной апробации исследуемых композиций подтверждены результаты выполненных исследований. Изделия из разработанных композиций отвечают требованиям стандартов на кирпич и характеризуются более высокой прочностью и морозостойкостью по сравнению с кирпичом текущего производства (состав 4), что особенно важно для обеспечения устойчивости зданий в сейсмических районах, к которым относится Жамбылская и Южно-Казахстанская области. Прочность кирпича при сжатии составляет 19 - 25 МПа против 7,5-8,2 МПа для кирпича текущего производства, морозостойкость кирпича 28 - 50 циклов. Обожженные изделия характеризуются небольшой усадкой и отличаются от традиционных по цвету, что дает возможность расширить цветовую гамму кирпича и улучшить внешний вид зданий без применения отделочных работ. Кроме того, результаты работы использованы при внедрении в производство состава кирпича полусухого прессования марки 150 по прочности и 35 по морозостойкости (приложение) из композиции глины с грубозернистым шлаком. Композиции с ОГС, ЦП в количестве 50 - 60% (таблица 6), пустотелые и полнотелые образцы из которых после обжига при температуре 1050°С имеют водопоглощение менее 14 %, морозостойкость 48–50 циклов и более, имеют красивый светло-бежевый цвет, являются наиболее подходящими для изготовления облицовочного камня. Кроме этого, получение облицовочного камня возможно из композиций глин с гранитным отсевом. Образцы из композиций этих составов также характеризуются высокой прочностью, морозостойкостью и красивым внешним видом.
В соответствии с разработанным технологическим регламентом изготовление клинкерного кирпича и тротуарной плитки проводили в цехе производства кирпича из смеси суглинка (25%), глины (5%), шлака ферросиликомарганца (50%) и стеклобоя (25%) по технологии полусухого прессования. После обжига при температуре 1070°С водопоглощение изделий составляет 5,2 %, прочность при сжатии – 60-62МПа, при изгибе – 7,4МПа, морозостойкость более 50 циклов.
Изделия ленточной черепицы в соответствии с разработанным технологическим регламентом формовали полусухим способом из смеси каолинит-монтмориллонитовой глины с гранитными отсевами в количестве 50% (таблица 6). Глину измельчали до остатка 1,5-2,0 % на сите с размером ячейки 0,315 мм. Гранитные отсевы использовали в виде зернистого компонента фракции <1,25 мм. При обжиге (1000°С) применяли комбинированную садку черепицы с кирпичом. Черепица имеет высокую прочность при изгибе (17,5-19,2 МПа) и высокую морозостойкость (марка 35). Усадка черепицы составляет 2,1-2,4%, в результате коробление изделий отсутствует. Водопоглощение черепицы 8,2-8,7%, при ударе она издает чистый звук, в изломе имеет однородное и мелкозернистое строение.
Таблица 6– Состав, свойства и область применения строительной керамики из композиций глин с непластичными компонентами
Состав, % мас. | Т, °C | Свойства | Область применения | |||
нуглинок + глина | нНепластичный компонент | W, % | Rсж МПа | Мрз., циклы | | |
(30-40) | ГО (60-70) | 1050 | 13,1- 13,7 | 41-54 | > 50 | Лицевой кирпич (ЛК) |
(30-40) | ГО (10 - 65) | 950-1000 | 14,2-16,9 | 25,8-55,3 | 25-50, >50 | Высокопрочный и морозостойкий кирпич, декоративный кирпич |
(50) | УКС ФКС (50) | 950- 1000 | 17,6- 17,9 | 19,7-20,1 | 20-24 | Рядовой кирпич и декоративный камень |
(25) | ГО (50) + стеклобой (25) | 1070-1100 | 2,6-4,8 | 90-130 | >50 | ЛК, клинкерный кирпич, тротуарная плитка |
(60) | УКС (30) + стеклобой (10) | 950-1050 | 5,4-8,1 | 24,4-27,8 | >50 | Черепица |
(50) | ФГС (50) | 1000-1050 | 7,2-8,9 | Rизг= 12,1-15,9 | 40-50 | Черепица |
(25) | ФГС (50-70) + стеклобой (25) | 1090- 1150 | 0,2-13,8 | 95-140 | >50 | ЛК, плитка керамическая |
(30-65) | ФКС (30-50) + стеклобой (5-25) | 1070-1090 | 1,5-15,4 | Rизг 15,4-22,1 | >50 | Плитка керамическая |
Щелочные связки 30-40 | Неплас-тичные компоненты 60-70 | 950 | 13-15 | 10-15 | 25 | Обычная керамика |
Щелочные связки 30-40 | Непластич-ные компоненты 60-70 | 1000 | 10-12 | 25-30 | 25 | Лицевая керамика |
Для изготовления плиток из зернистых отходов на легкоплавких связках применяли циклонную пыль с преимущественным размером зерен 0,16-0,63 мм (~92%), высококальциевый шлак, содержащий 60-65 % фракции с размером зерен более 1,25 мм и 35-40 % фракции с размером зерен менее 0,5 мм, гранитный отсев с размером фракции < 1,25 мм. В качестве связки использовали смесь монтмориллонит-каолинитовой глины и стеклобоя. Содержание стеклобоя в смеси составляло 50%. При изготовлении плиток связку, увлажненную до 8-10%, смешивали с зернистым компонентом. Плитки прессовали под давлением 25 МПа. Сушку и обжиг проводили в роликовой конвейерной печи при температуре 1100-1120°С в течение 60 мин. Плитки из композиций с содержанием шлака 50%, циклонная пыль или гранитный отсев после обжига имеют водопоглощение 0,6-3,6%, прочность при изгибе 27-31 МПа и отвечают самым жестким требованиям, предъявляемым к плиткам для полов.
Разработанная технология изготовления плиток из зернистых отходов на керамических связках упрощает подготовку сырья для керамических масс, расширяет возможности полезной утилизации промышленных отходов, снижает себестоимость продукции. На изготовление плиток из шлака разработан технологический регламент. Таким образом, свойства строительной керамики, полученные при внедрении и опытно-промышленных испытаниях, подтверждают расчетные и экспериментальные результаты выполненных научных исследований.
Разработан программный комплекс, позволяющий расчитать энергосберегающий электропривод основного технологического оборудования производства строительной керамики. Рассмотрен алгоритм построения математической модели производства строительной керамики с использованием метода группового учета аргументов. Формализована постановка задачи оптимизации технологического процесса производства строительной керамики, определен критерий оптимизации управления процессом обжига, рекомендована программа решения полученной задачи линейного программирования.