Оао «Челябэнергоремонт» является одним из крупнейших энергоремонтных предприятий России
Вид материала | Документы |
СодержаниеПодразделения ОАО “Челябэнергоремонт» |
- Годовой отчет за 2009 год Генеральный директор ОАО, 218.36kb.
- Характеристика компании ОАО концерн «Калина», 190.66kb.
- Торговая Фирма " агроинвест-конпрок", 24.55kb.
- Тепловыделяющие элементы ввэр-1000, изготовляемые на ОАО «мсз», 81.15kb.
- С. Н. Серова к заседанию Совета по взаимодействию Алтайского краевого Закон, 87.4kb.
- Предварительно утвержден Наблюдательным советом ОАО «Авиакомпания «ЮТэйр», 2101.88kb.
- Годовой отчет открытого акционерного общества «курганский завод химического машиностроения», 448.86kb.
- Ежегодник 2007-2008 гг. Союз мороженщиков россии, 676.66kb.
- Цена дипломной работы с чертежом 500 рублей содержание, 51.27kb.
- Театры Новосибирска, 54.59kb.
ОАО «Челябэнергоремонт»
О
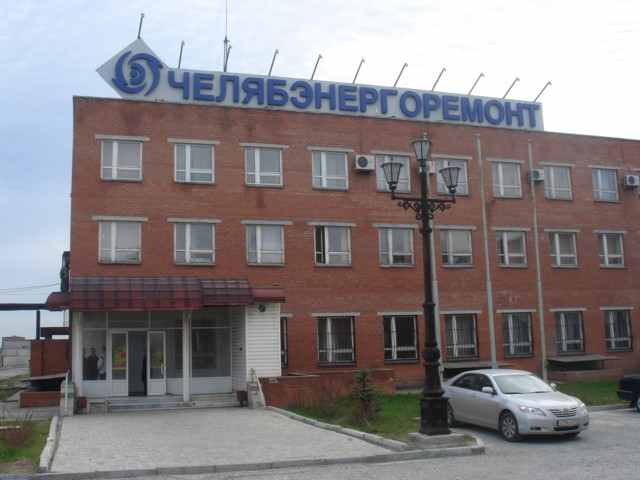
Производство эмальпровода, оснащенное современным австрийским оборудованием, позволяет изготавливать провод по качественным характеристикам один из лучших в России.
На предприятии имеется проектно-конструкторский отдел, обеспечивающий конструкторскую проработку всех выполняемых работ. Высоковольтная лаборатория и лаборатория контроля металла, отдел качества, оснащенные широким спектром измерительно-испытательного оборудования, осуществляют все необходимые испытания и контроль качества продукции и услуг.
Предприятие имеет высококвалифицированный персонал, подразделения оснащены современным высокотехнологичным оборудованием, что позволяет качественно и в срок выполнять работы и обеспечивать бесперебойную работу энергетического оборудования наших заказчиков.
Система управления качеством предприятия сертифицирована на соответствие требованиям ГОСТ Р ИСО 9001-2001
Подразделения ОАО “Челябэнергоремонт»:
Котельный цех внешних ремонтов выполняет нетиповые работы по реконструкции и ремонту котлоагрегатов электростанций и котельно-вспомогательного оборудования. В цехе разработан и применяется метод крупноблочной замены поверхностей нагрева, что позволяет значительно уменьшить трудозатраты и сократить сроки ремонта котлоагрегатов. Перечень работ, выполняемых ремонтов:
1. Монтаж (пусконаладка) объектов котлонадзора и вспомогательного оборудования:
- паровых котлов с давлением до 4,0 МПа;
- водогрейных котлов теплопроизводительностью до 180 Гкал\час;
- трубопроводов пара и горячей воды 1-4 категорий;
- сосудов, работающих под давлением 1-4 групп.
2. Капитальный ремонт, реконструкция и модернизация объектов Котлонадзора:
- паровых и водогрейных котлов (поверхностей нагрева, коллекторов, барабанов, трубопроводов в пределах котла);
- трубопроводов пара и горячей воды 1-4 категорий;
- сосудов, работающих под давлением 3-4 групп;
- металлоконструкций каркасов котлов;
- горелочных устройств.
Ремонт оборудования топливоподачи (систем пылеприготовления, газового и мазутного хозяйства).
Монтаж объектов газового хозяйства ТЭС, ТЭЦ, ГРЭС, промышленных котельных, ГРП, ГРУ, наружных надземных газопроводов природного газа с давлением до 1,2 МПа.
Капитальный ремонт и реконструкция подъёмных сооружений: расчетных металлоконструкций и крановых путей мостового и стрелового типов (в том числе кранов-перегружателей) общего назначения грузоподъёмностью до 125 тс, подъёмников (вышек).
Турбинный цех внешних ремонтов выполняет следующие виды работ:
- Реконструкция, модернизация и капитальный ремонт турбин тепловых электростанций, в т.ч:
- корпусов цилиндров с контролем состояния металла;
- лопаточного аппарата роторов с переоблопачиванием отдельных ступеней и заменой бандажей;
- диафрагменных и концевых уплотнений;
- центровка деталей проточной части и роторов;
- соплового аппарата;
- маслосистемы;
- опорных, упорных и уплотняющих подшипников исоединительных муфт роторов;
- валоповоротного устройства;
- системы автоматического регулирования и парораспределения;
- виброобследование и балансировка роторов;
- очистка, ремонт, частичная или полная замена трубок и трубных досок конденсатора.
- Монтаж и ремонт вспомогательного насосного оборудования ТЭС (питательные, циркуляционные, сетевые и другие насосы), статическая балансировка роторов насосов.
- Ремонт деаэраторов, сепараторов, расширителей, маслоочистительных установок.
- Ремонт сетевых и регенеративных подогревателей.
- Ремонт поршневых и центробежных компрессоров.
- Виброобследование и балансировка роторов вращающихся механизмов.
Ремонтно-обмуровочный цех выполняет следующие виды работ:
- все виды ремонта (капитальный, средний, текущий) обмуровки паровых и водогрейных котлов любой мощности;
- ремонт тепловой изоляции энергооборудования электростанций (котло- и турбоагрегатов, трубопроводов пара и горячей воды, сосудов), котельных и тепловых сетей;
- ремонт футеровки оборудования газоочистки (скрубберов, электрофильтров и т.д.);
- антикоррозийная защита металлоконструкций.
К
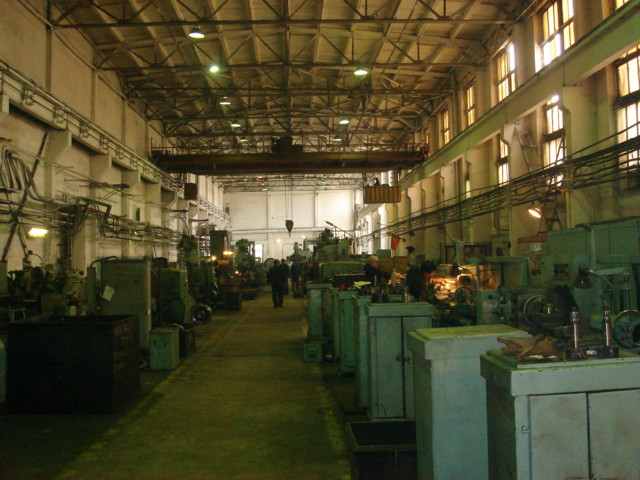
- восстановление уплотнительных поверхностей задвижек: проточка, притирка, наплавка;
- замена быстроизнашивающихся деталей - шток, крепежные изделия и др.
Отремонтированные задвижки проходят проверку на специальной испытательной станции на прочность и плотность согласно действующим нормам и ТУ.
Производится ремонт стальных и чугунных задвижек отечественного и иностранного исполнения.
Ремонт арматуры проводится в стационарных условиях, приближенных к заводским, благодаря чему достигается:
- восстановление технических характеристик до значений завода-изготовителя.
- проведение ремонтов в оптимальные сроки.
- стоимость ремонта 40 - 50% нового изделия.
Также производятся работы по перезаливке подшипников скольжения турбоагрегатов, мельниц, вентиляторов, дымососов и т.д. баббитом Б-83, Б-16. Внутренний диаметр расточки до 1,5 м.
Предприятие выполняет работы по обслуживанию электротехнического оборудования электрических станций, сетей и промышленных предприятий. Электроремонтное производство включает 2 цеха, осуществляющих монтаж, ремонт и наладку электрооборудования.
Производство оснащено современным технологическим оборудованием и приборами, позволяющими выполнять ремонты по новейшим технологиям в сжатые сроки, установки для подготовки трансформаторного масла с самыми высокими показателями и химлабораторию, оснащенную современным оборудованием для выполнения любых анализов трансформаторного масла.
Измерительно-испытательная аппаратура позволяет выполнять диагностику, способную выявить все скрытые дефекты изоляции (методом частичных разрядов), высоковольтные испытания с поднятием напряжения до 400 кВ, что обеспечивает гарантию длительной работы отремонтированного оборудования.
Основные виды работ, выполняемые электроремонтным производством:
Р
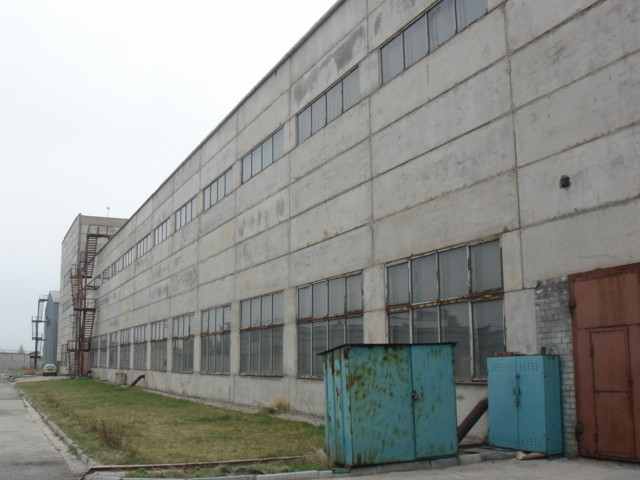
- капитальный ремонт турбогенераторов всех типов без смены обмоток;
- капитальный ремонт высоковольтных электродвигателей любой мощности;
- капитальный ремонт общепромышленных двигателей переменного тока любой мощности;
- изготовление высоковольтных секций для электродвигателей;
Ремонт оборудования электросетей:
- заводской ремонт силовых масляных трансформаторов I - IV габаритов на напряжение 6-110 кВ с заменой обмоток и главной изоляции;
- капитальный ремонт силовых масляных трансформаторов III-V габаритов на 35-500 кВ в местах их установки с восстановлением изоляционных характеристик главной изоляции и трансформаторного масла без смены обмоток;
- капитальный ремонт измерительных трансформаторов тока и напряжения на 35 500 кВ без смены обмоток, с восстановлением изоляционных характеристик, с полной разборкой и заменой уплотнительных прокладок;
- капитальный ремонт трансформаторов напряжения
НТМИ-6/66 и НТМИ-10/66;
- ремонт, регулировка и испытание предохранительных клапанов масляных трансформаторов;
- капитальный ремонт высоковольтных вводов напряжением 110-500 кВ, герметичных и негерметичных, для силовых трансформаторов, автотрансформаторов, реакторов, масляных выключателей, линейных вводов с восстановлением изоляционных характеристик, с полной разборкой и заменой всех уплотнительных прокладок, ремонтом и заменой узлов;
- капитальный ремонт высоковольтных масляных выключателей на 35-220 кВ;
- монтаж и демонтаж оборудования РУ;
- текущее обслуживание сетевого электрооборудования 6-10 кВ в местах установки;
Р
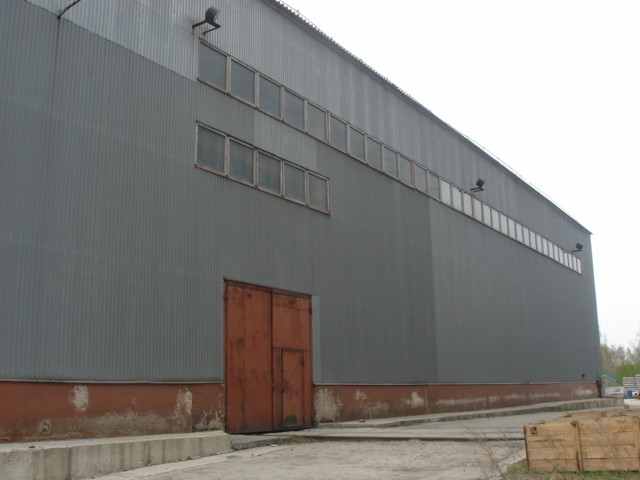
- комплексное обследование силовых масляных трансформаторов III-V габаритов с выдачей рекомендаций по дальнейшей эксплуатации и ремонту;
- измерение параметров и испытание силовых масляных трансформаторов III-V габаритов до и после ремонта;
- ремонт и наладка переключающих устройств типа РНТ и РС со снятием круговых диаграмм и осциллографированием временных характеристик контактора;
- измерение сопротивления изоляции электрооборудования, электропроводок и кабеля;
- испытание изоляции электрооборудования и кабелей повышенным напряжением (до 100кВ);
- определение мест повреждения кабелей;
- полный анализ характеристик трансформаторного масла с использованием штатного оборудования химической лаборатории и хроматографа «Кристалл-2000»;
- испытание средств защиты.
К
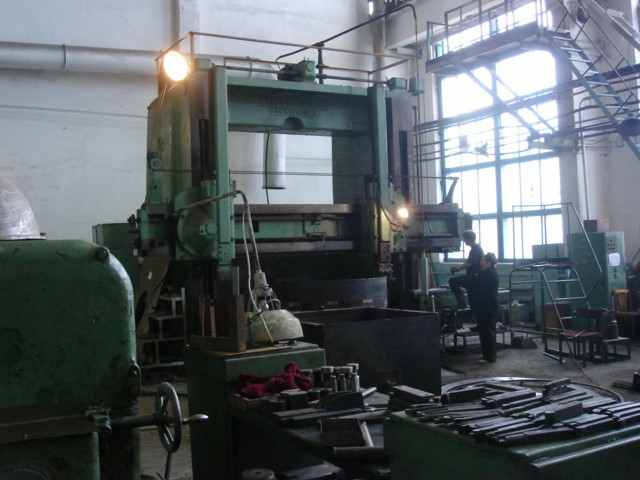
Цех оснащен кузнечным, металлорежущим, сварочным оборудованием, а также оборудованием для термической обработки. Установлены прессы усилием до 260 тс, гильотинные ножницы, вальцы, на которых изготавливают обечайки и брони шахтных мельниц с толщиной стенки до 30 мм, трубогибочные станки для производства отводов без подогрева и с нагревом труб токами высокой частоты.
Сварка труб малого диаметра (от 28 до 42 мм) при изготовлении поверхностей нагрева производится на стыкосварочной машине.
Качество сварных швов проверяется ультразвуковым контролем, опрессовкой гидропрессом и механическими испытаниями экспресс-образцов.
Установлены токарные станки, позволяющие обрабатывать детали диаметром до 1500 мм с длиной до 7500 мм. На карусельных станках обрабатывают детали диаметром до 3000 мм, высотой до 1500 мм и весом до 7 т.
Шлифовально-прошивной станок с адаптивно-программным управлением позволяет получать прошиваемые отверстия с точностью 0,02 мм.
Основные виды выполняемых работ:
- Изготовление объектов котлонадзора:
- труб поверхностей нагрева и их элементов в пределах котла, коллекторов паровых и водогрейных котлов с давлением до 24,0 МПа и температурой до 560 °С;
- металлоконструкций каркасов паровых и водогрейных котлов;
- элементов трубопроводов пара и горячей воды 1-4 категорий;
- сосудов, работающих под давлением 1-4 групп.
- Изготовление запасных частей для оборудования объектов газового хозяйства.
- Изготовление секций бойлеров, регистров отопления, водяных нагревателей, нестандартного оборудования.
- Изготовление грузоподъемных приспособлений (тара, стропы, скобы, струбцины, траверсы и т.п. грузоподъемностью до 15 т.с.)
- Изготовление металлоконструкций из конструкционной и нержавеющей стали массой сборочной единицы до 15 тонн.
- Изготовление стальных дымовых труб.
Л
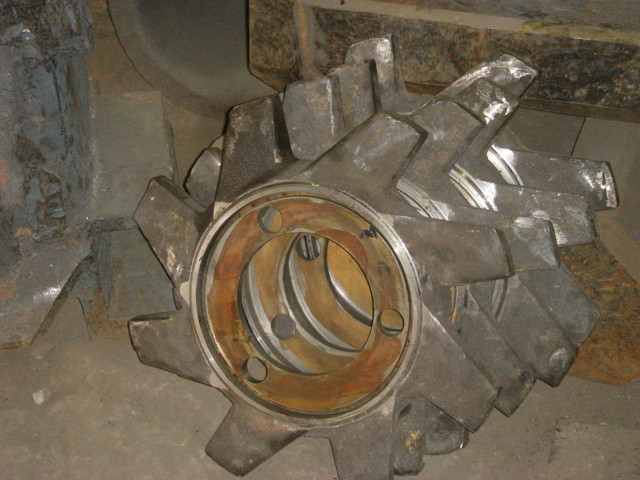
Применяемые сплавы:
- Сталь 25Л, ЗОЛ, 35Л, легированные стали 35ГЛ, 35ХГЛ, 35ХГСЛ, 35ХМЛ, 40ХЛ, 70ХЛ и другие.
- Чугун марок СЧ10, СЧ15, СЧ20, СЧ25, ЧХ1, ЧХ2.
- Сплавы на основе алюминия и меди.
Способ формообразования:
- Изготовление форм на встряхивающих машинах на основе песчано-глинистых смесей массой отливок до 200 кг с габаритными размерами не более 700x600x300 мм.
- Ручная формовка на плацу крупногабаритных отливок массой до 1,5т.
Плавильные агрегаты:
- Электрическая дуговая печь емкостью 1,5т;
- Индукционные печи емкостью 0,16; 0,4; 1,0 тн.
Основная продукция литейного цеха:
- Била угольных мельниц и дробилок (монолитные и с наплавкой) различной конфигурации.
На протяжении многих лет наши инженеры проводят научно-практическую работу по выбору наиболее оптимальной конфигурации, размеров и материала бил. На сегодняшний день мы подобрали наилучшее сочетание конфигурации, размеров и марки стали для литых монолитных бил, соответствующее их стоимости.
Как показала практика, срок службы монолитных утолщенных бил из стали 35ХГЛ в зависимости от вида угля составляет до 550 часов, срок службы наплавленных бил до 1200 часов.
- Литые билодержатели различной конфигурации.
Как показала практика, литые билодержатели по сравнению с изготовленными из проката обладают большей стойкостью и в среднем эксплуатируются до 2500 часов. Материал билодержателей - сталь 30Л.
Предприятие готово изготовить била и билодержатели любой конфигурации и массы по чертежам заказчика.
- Броня футеровки для молотковых и шаровых угольных мельниц плоской и криволинейной формы.
Броня из этой стали, установленная на Челябинской ТЭЦ-1, эксплуатируется в течение 15 лет при режиме работы мельницы не менее 3 месяцев в году.
- Рабочие колёса насосов (96 марок).
- Втулки для изготовления подшипников скольжения, вкладышей и т. п.
Материалы: чугун, бронза, алюминиевые сплавы.
Длина втулок - 300 мм;
Диаметр наружный: 150-300 мм;
Диаметр внутренний: 100-250 мм.
Предприятие готово рассмотреть любые предложения по изготовлению стальных и чугунных отливок, в том числе с последующей механической обработкой.
У
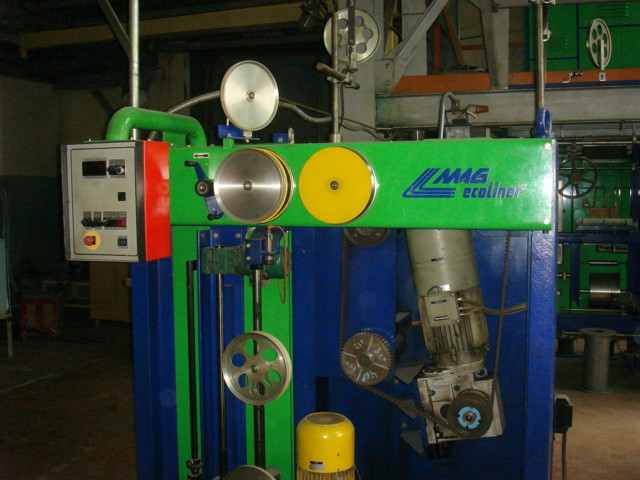
Эмальпровод ПЭЭИ-200 (аналог W-200 IЕС 317-8) предназначен для использования в производстве и ремонте различных видов электротехнического оборудования (электрических машин, трансформаторов, магнитных катушек, приборов, аппаратов).
Производство и контроль качества осуществляются на оборудовании и по технологии австрийской фирмы «MAG» с использованием итальянских покровных лаков «Deatech» по международному стандарту IEC 317-8. Провод изготавливается с двумя типами изоляции:
- ПЭЭИ1-200 (W200-1L) - провод с изоляцией класса 1 (8 слоев эмалевого покрытия);
- ПЭЭИ2-200 (W200-2L) - провод с изоляцией класса 2 (12 слоев эмалевого покрытия)
Основные характеристики:
диапазон диаметров проводов 0,2 - 4,0 мм;
температурный индекс 200 по ГОСТ 10519-76;
пробивное напряжение не менее 5000 В для проводов ПЭЭИ1-200 и не менее 8000 В для проводов ПЭЭИ2-200;
высокая механическая прочность изоляции;
стойкость к воздействию трансформаторных масел, холодильных агентов и растворителей;
совместимость со всеми основными типами пропиточных составов.
Провод данной марки по техническим характеристикам превосходит провода марок ПЭТВ-2, ПЭТВМ, ПЭТ-155 (180) и не уступает проводам ПЭТМ-155, ПЭТД-180, ПЭТ-200. Провод соответствует требованиям ГОСТ 26615-85, качество провода подтверждено сертификатом соответствия.
В 2001, 2003 годах высокое качество провода ПЭЭИ-200 подтверждено дипломами конкурса «100 лучших товаров России».
Среди постоянных потребителей известные российские производители электродвигателей и крупнейшие промышленные предприятия Уральского региона.
Участок защитных покрытий
Полимерные покрытия
Участок полимерных покрытий производит нанесение покрытий из любых порошкообразных полимерных материалов, как термопластов (типа полиэтилена), так и реактопластов (эпоксидных) в электростатическом поле.
Наиболее широко применяются покрытия из фторопласта Ф40. Эти покрытия стойки во всех агрессивных средах (кислоты, щелочи) и могут эксплуатироваться при температуре от -100 °С до +200°С. Фторопластовые покрытия имеют хорошую адгезию с поверхностью, что достигается применением особых технологий напыления и последующей термической обработкой покрытия. Область применения -защита деталей, узлов и агрегатов, работающих в агрессивных средах, воде, на открытом воздухе.
Покрытия из полимерных материалов различных цветов и оттенков также используются в качестве декоративных для придания товарного вида изделиям из металла, деталям и узлам машин.
Цинкование
На участке также производится нанесение цинк-диффузионного покрытия на метизы и мелкие детали. Толщина покрытия до 80 мкм. Максимальные размеры цинкуемых изделий диаметр 150 мм, длина 330 мм. Максимальная масса изделия - 10 кг.
Практика применения покрытий:
Более 5 лет ОАО «Челябэнергоремонт» производит сальниковые компенсаторы с фторопластовым покрытием. За это время было обработано более 1000 изделий. Практика их эксплуатации в Челябинских тепловых сетях показала, что при стоимости защитного покрытия не более 15 % от стоимости готового изделия, срок службы компенсаторов увеличился в 2-2,5 раза. Фторопластовое покрытие позволяет исключить "прикипание" сальниковой набивки к поверхности сальниковой камеры. Коэффициент трения покрытой фторопластом поверхности снижается на 40%, благодаря чему уменьшаются осевые нагрузки в трубопроводах и на опорах.
Проектно-конструкторскии отдел занимается разработкой следующих проектов:
на ремонт основного и вспомогательного оборудования тепловых электростанций;
производства и механизации ремонтных работ;
на элементы котлов (трубопроводов поверхностей нагрева, коллекторы, трубопроводы в пределах котла и т.д.);
на газоходы, воздуховоды, пылепроводы котлов, котловые паропроводы всех категорий;
на общестанционные трубопроводы воды, пара, конденсата, маслопроводы
на подземные наружные и внутренние газопроводы давлением до 1,7 Мпа, ГРП, ГРУ;
на горелки для сжигания топлива;
на сосуды под давлением;
обмуровки и теплоизоляции;
на теплообменное оборудование;
на сальниковые и линзовые компенсаторы;
на баки, емкости, резервуары;
на наружные сети: тепла, пара, сжатого воздуха, технологических трубопроводов, воды и т.д.;
на нестандартное оборудование и инструмент;
грузоподъемных механизмов и приспособлений и их ремонт;
на строительство зданий и сооружений I и II уровней ответственности;
компоновочных чертежей котельных, насосных, химводоочисток, маслохозяйств, компрессорных;
технологических карт на погрузо-разгрузочные работы;
проведение расчетов на прочность и устойчивость.
О
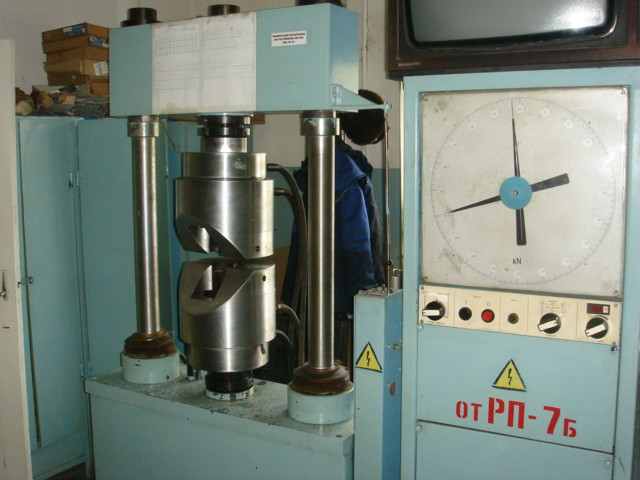
Выполняют следующие работы:
- проведение с высокой точностью на спектроанализаторе немецкой фирмы «Ве1ес» анализов химического состава углеродистых, низко- и высоколегированных сталей, (всего до 15 химических элементов, включая фосфор и серу), сплавов на основе меди, с определением марки и выдачей сертификата анализа;
- проведение механических испытаний образцов основного металла и сварных соединений на растяжение, изгиб, сплющивание и ударную вязкость, а также проведение работ по измерению твердости металла с выдачей заключения;
- неразрушающий контроль основного металла и сварных соединений (ультразвуковой, магнитный, спектральный);
- проведение практического экзамена при аттестации в АНО «Южно-Уральский аттестационный центр» элекросварщиков ручной сварки на I уровень профессиональной подготовки по ПБ 03-273-99 на право проведения работ на опасных производственных объектах, подконтрольных Ростехнадзору России (объекты котлонадзора, газового хозяйства, подъемные сооружения).