Научные основы и технологические решения получения высокопрочных алюминийсодержащих коррозионностойких сталей для мединструмента
Вид материала | Автореферат диссертации |
СодержаниеВ четвертой главе В пятой главе В шестой главе В седьмой главе |
- Применение коррозионностойких сталей, 24.02kb.
- Ная деятельность и достаточен ли этот уровень для модернизации страны очевидны: уровень, 127.16kb.
- Влияние дополнительной термообработки на структуру и механические свойства феррито-бейнитных, 482.48kb.
- Улучшения структуры и повышения механических свойств стальных отливок является внепечное, 179.71kb.
- Технологические возможности ионного азотирования в упрочнении изделий из конструкционных, 142.1kb.
- Физико-химические свойства и технологические основы получения пирротинов из пирита, 328.59kb.
- Применение хладостойких сталей, 77.34kb.
- Carboweld 625 Стандарты, 41.02kb.
- Программа и задания экзамена для поступающих в магистатуру по специальности 6M072400, 129.72kb.
- Принцип устойчивого развития как средство решения современных экологических, социальных, 415.19kb.
Несомненно, что благоприятное влияние на эффективность упрочнения при волочении оказывает и протекающее мартенситное превращение. Причем его роль может заключаться не только в облегчении протекания пластической деформации и вследствие этого устранения локальных пиковых напряжений, но и в непосредственном участии в структурном упрочнении благодаря образованию дисперсных кристаллов мартенсита. Выявлена количественная зависимость между уровнем упрочненного состояния деформированной стали и объемной долей мартенситной фазы.
С целью определения температурно-временных условий выделения при старении упрочняющих фаз проводилось изучение влияния температуры последеформационного нагрева на изменение механических свойств, фазового состава и структуры исследуемой стали 03Х14Н11К5М2ЮТ. Продолжительность выдержки при старении составляла 1 ч. На рис. 1 (пунктирные кривые) видно, что чем больше количество мартенсита, образовавшегося в процессе деформирования (волочения), тем выше прирост прочностных свойств (в и 0,2), при сохранении достаточно высоких характеристик пластичности ( = 1,5..2 % и = 43 %). Изменение периода кристаллической решетки мартенсита деформированной (е = 2,32) проволоки от температуры старения свидетельствует о процессах распада пересыщенного твердого раствора. Эта характеристика достигает минимальных значений при температурах на 50 С выше температуры наибольшего упрочнения при старении. Температура, при которой период а достигает минимума, соответствует стадии перестаривания и является температурой метастабильного равновесия между матрицей и частицами интерметаллидных фаз. Ранее проведенными исследованиями было показано, что метастабильная коррозионностойкая аустенитная сталь 03Х14Н11К5М2ЮТ в закаленном состоянии практически не старится, следовательно, выделение упрочняющей интерметаллидной фазы происходит из ОЦК-фазы (мартенсит деформации), который при нагреве выше температуры 550 С испытывает обратное превращение. Этому превращению соответствует эндотермический пик на кривых ДТА. Если первый пик (экзотермический) в интервале температур 380..550 С связан с процессами выделения упрочняющей фазы, то второй пик (тоже экзотермический) в интервале температур 650..850 С связан с процессами выделения высокотемпературной интерметаллидной фазы. Знание температурных интервалов выделения интерметаллидных фаз при нагреве, позволяет правильно подбирать режим термической или термомеханической обработки исследуемой стали.
Электронно-микроскопическое исследование тонкой структуры изучаемой стали 03Х14Н11К5М2ЮТ после различных режимов оптимального и высокотемпературного старения предварительно деформированных образцов показало следующее (рис. 3).
а б в
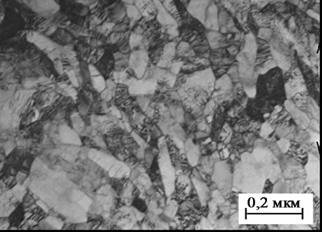
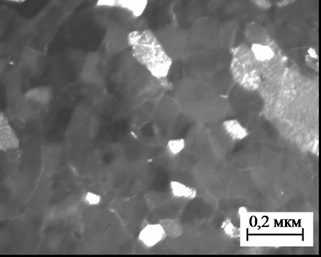
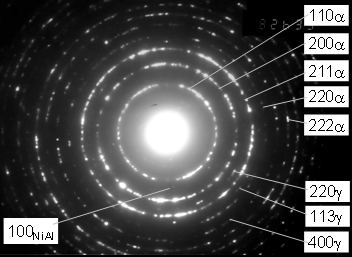
г д е
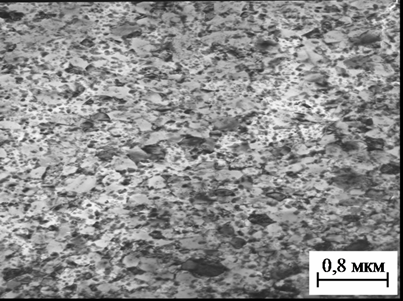
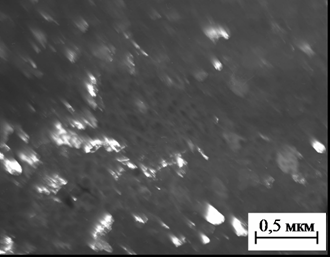
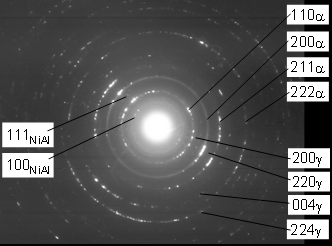
Рис. 3. Структура стали 03Х14Н11К5М2ЮТ после закалки от 1000° С, деформации е = 2,32 и старения: а-в – при 500º С (1 ч); г-е – при 500º С (1 ч) + 650º С (2 ч);
б, д – темнопольное изображение в рефлексе α-фазы (110)α; в, е – микродифракция
Структурные составляющие деформированной и состаренной стали представляют собой ОЦК и ГЦК фазы. Основным механизмом старения в интервале температур 500..650 С является гетерогенное выделение интерметаллидных фаз из ОЦК-твердого раствора. В структуре деформированной и состаренной при 500 С метастабильной аустенитной стали наблюдается вблизи контуров экстинкции контраст типа ряби, обусловленный, по-видимому, появлением высокодисперсных частиц. Увеличение температуры и времени старения (650 С, 2 ч) приводит к некоторому росту размеров выделяющихся частиц. На ранних стадиях старения частицы имеют форму, близкую к сферической. После старения деформированных образцов при 650 С на электронограммах появляются рефлексы, принадлежащие уже подросшим частицам интерметаллидной фазы NiAl.
Таким образом, имеющиеся данные позволяют сделать вывод, что практически безуглеродистая коррозионностойкая аустенитная сталь в результате правильно подобранного легирования сочетает в себе достоинства трех сталей: метастабильных аустенитных, трип-сталей и мартенситностареющих сталей. В результате использования всех возможных механизмов упрочнения было достигнуто высокопрочное состояние.
Проведенное исследование безуглеродистой аустенитной метастабильной стали 03Х14Н11К5М2ЮТ позволило установить закономерности структурных и фазовых превращений, происходящих при термической и термомеханической обработках.
В четвертой главе решалась задача создания принципиально новых металлических сплавов для стержневого медицинского инструмента, прежде всего тончайших сечений (до 100 мкм), на которых при необходимой высокой коррозионной стойкости должны быть получены высокая твердость, прочность и упругость, обеспечивающие сохранение необходимой жесткости и отсутствие формоизменений в процессе эксплуатации. С этой целью разработаны и комплексно изучены новые аустенитно-ферритные стали двух составов, на один из которых получен патент. В данной главе рассмотрены фазовые превращения и изменения свойств при различных режимах термопластической обработки двухфазной аустенитно-ферритной стали 03Х14Н10К5М2Ю2Т.
В исследуемой стали соотношение между аустенитом и δ-ферритом примерно 50 : 50 сохраняется при нагреве под закалку в интервале температур 800..1000 С (рис. 4 а, б) и только при 1300 С, согласно фазовому анализу, структура стали состоит из одного δ-феррита, в котором даже при больших скоростях охлаждения (закалка в воду) не удается полностью подавить выделения вторичного аустенита. Колонии вторичного аустенита в некоторых участках образуют структуру типа видманштеттовой с характерным игольчатым (пластинчатым) строением (рис. 4 в).
а б в
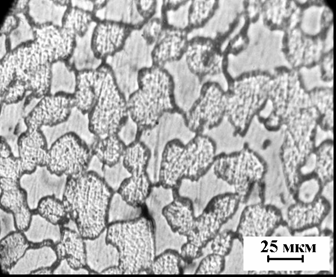
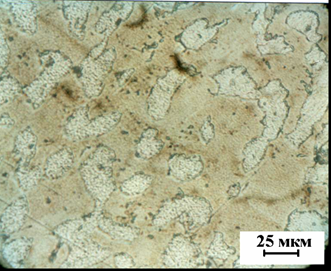
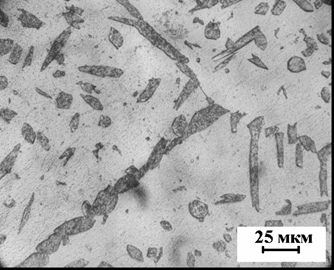
Рис. 4. Микроструктура аустенитно-ферритной стали 03Х14Н10К5М2Ю2Т: а – закалка от 1000 С; б – закалка от 1000 С, цветное травление; в – закалка от 1300 С
Микрорентгеноспектральный анализ закаленных образцов аустенитно-ферритной стали 03Х14Н10К5М2Ю2Т показал, что -феррит оказывается обогащенным ферритообразующими элементами (Cr, Al, Mo), аустенит аустенитообразующими элементами (Ni, Со).
Следует отметить, что в двухфазной аустенитно-ферритной стали размер зерен обеих фаз практически не изменяется до 1100 С, а затем при температуре интенсивного превращения (выше 1200 С) происходит резкий рост зерен феррита, что объясняется, по-видимому, превышением порога собирательной рекристаллизации стали, а также более значительной диффузионной подвижностью атомов решетки ОЦК феррита по сравнению с решеткой ГЦК аустенита.
В исследуемой аустенитно-ферритной стали 03Х14Н10К5М2Ю2Т, структура которой в закаленном состоянии состоит, как указывалось выше, из аустенита и -феррита, обнаружена аномально высокая микротвердость -феррита (свыше 500 HV), в то время как микротвердость аустенита находится в пределах 200 HV. Наличие двухфазной структуры, состоящей из фаз различной твердости, обуславливает относительно невысокую интегральную твердость закаленных аустенитно-ферритных сталей ( 28 HRC), что является необходимым условием для достаточно хорошей пластичности этих сталей в закаленном состоянии.
Столь значительное различие микротвердости фазовых составляющих вряд ли объясняется только степенью пересыщения аустенита и -феррита легирующими элементами, так как оно в обеих фазах (по данным МРСА) достаточно велико. Методом электронной микроскопии показано наличие в -феррите закаленной стали высокодисперсных равномерно распределенных частиц округлой формы с решеткой типа В2. На электронограммах с участков -феррита закаленной стали 03Х1410К5М2Ю2Т (рис. 5 д) обнаружены сверхструктурные рефлексы, которые свидетельствуют о наличие в структуре упорядочения. Темнопольные изображения в сверхструктурном рефлексе (001)NiAl (рис. 5 ж) показывают присутствие («свечение») в -феррите упорядоченной фазы типа NiAl.
Оптическая металлография не выявила заметных структурных изменений в исследуемой стали при старении вплоть до 650 С включительно. При старении 500..650 С наблюдается появление неоднородности структуры как аустенита, так и -феррита, связанная с распадом твердого раствора (-феррита) и возможным частичным превращением . Применение метода электронной микроскопии позволило проследить протекание процесса распада -феррита. При температурах оптимального старения (закалка от 1000 С и последующее старение при 500 С в течение 1 ч) в ОЦК фазе (-феррит) присутствуют дисперсные включения интерметаллидной фазы типа NiAl уже размером 50..70 нм, которые «светятся» в темнопольных изображениях в рефлексе (120)NiAl. После старения закаленных образцов при 650 С в течение 1 ч (в перестаренном состоянии) наблюдаются подросшие равномерно распределенные в ОЦК матрице включения интерметаллидной фазы NiАl.
Таким образом, результаты электронно-микроскопических исследований показали, что упрочнение закаленных аустенитно-ферритных сталей обусловлено равномерным выделением высокодисперсной интерметаллидной фазы типа NiAl, которая и является ответственной за упрочнение.
Процессы распада исследуемой аустенитно-ферритной стали идут аналогично процессам распада в мартенситностареющих сталях, следовательно, после высокой температуры старения возможно образование фазы Лавеса. По данным ФФХА на образцах, закаленных от 1200 С и состаренных при 650 С, была определена выделившаяся в осадок интерметаллидная фаза типа (Fe74Cr12Ni14)2,09(Mo64,4Ti35,6). Отметим, что фаза Лавеса в аустенитно-ферритной стали имеет несколько иной химический состав, чем обнаруженная в мартенситностареющих сталях.
а б в
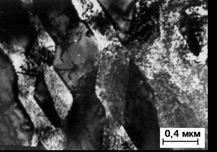
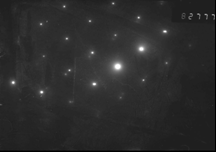
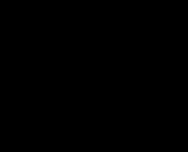
г д е
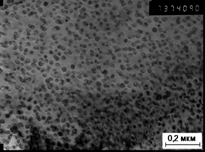
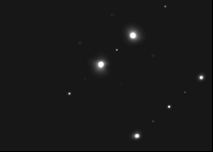
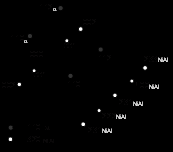
ж
Рис. 5. Микроструктура стали 03Х14Н10К5М2Ю2Т после закалки от 1300 С: а, г – светлопольное изображение;
б, д – микродифракция; в, е схема расшифровки;
ж – темнопольное изображение в рефлексе (001)NiAl
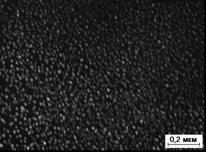
Холодная пластическая деформация является надежным и простым способом достижения высокопрочного состояния. Основные эксперименты, по изучению влияния холодной пластической деформации, а также последующего старения на фазовый состав, структуру и свойства аустенитно-ферритной стали 03Х14Н10К5М2Ю2Т, были выполнены на проволочных образцах диаметром 0,8 мм. При этом деформация осуществлялась волочением с различных исходных диаметров на диаметр 0,8 мм и составляла 20, 40, 60 и 80 %. На исходном диаметре вся проволока была закалена от температуры 1000 С. На рис. 6 показано влияние степени холодной пластической деформации при волочении проволоки с диаметра 2,0 до 0,8 мм на механические свойства и количество ОЦК фазы. Деформация вызывает интенсивное упрочнение и после максимального обжатия ( 80 %) временное сопротивление разрыву исследуемой стали возрастает почти вдвое по сравнению с закаленным состоянием и составляет порядка 1840 МПа. Как показали результаты рентгеноструктурного фазового анализа, аустенит исследуемой стали 03Х14Н10К5М2Ю2Т является метастабильным и при деформации порядка 80 % в структуре наблюдается ≈100 % ОЦК фазы, т.е. аустенит полностью переходит в мартенсит деформации. Упрочнение исследуемой стали при деформации обусловлено совокупным и сложным воздействием различных факторов: во-первых, деформацией аустенита, а затем и мартенсита, во-вторых, деформацией -феррита, в третьих, фазовым превращением, протекающим по бездиффузионному механизму и приводящим к формированию в аустенитной матрице высокодисперсных кристаллов мартенсита, способных наследовать дефекты аустенита. Структура деформированной стали имеет типичный волокнистый характер (рис. 7), наблюдается значительное раздробление зерен -феррита (светлые зерна) и наличие большого количества мартенсита деформации (темные зерна).

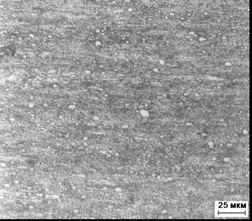
Рис. 6. Влияние холодной пластической деформации на механические свойства
и количество ОЦК фазы
Рис. 7. Микроструктура стали
после деформации ( 80 %)
Исследуемая аустенитно-ферритная сталь имеет более низкий коэффициент деформационного упрочнения, чем метастабильная аустенитная сталь типа 12Х18Н10Т, вследствие более низкого содержания углерода в исследуемой стали. Однако, за счет гетерофазной структуры он выше, чем в мартенситностареющих и аустенитной сталях с таким же содержанием углерода.
В табл. 3 приведены сравнительные данные по механическим свойствам проволоки для исследуемой аустенитно-ферритной и мартенситностареющей сталей в следующих состояниях: в закаленном (на диам. 2,0 мм) и после деформации на 80 % на конечном диаметре 0,8 и 0,15 мм. Наблюдается значительный рост временного сопротивления разрыву при волочении проволоки, причем прирост в для стали 03Х14Н10К5М2Ю2Т составляет 900 МПа. Из приведенных данных видно, что как после закалки, так и после деформации сталь 03Х14Н10К5М2Ю2Т имеет более высокую равномерную пластичность () и меньшую сосредоточенную пластичность (ψ) по сравнению со сталью ЗИ90-ВИ. В то же время, число скручиваний до разрушения в аустенитно-ферритной стали больше. При этом прочностные свойства аустенитно-ферритная сталь 03Х14Н10К5М2Ю2Т имеет в закаленном состоянии ниже, а после деформации на 80 % значительно выше. Для обеих сталей наблюдается четко выраженный масштабный фактор: при одинаковой степени деформации в на тончайшем размере (диам. 0,15 мм) почти на 1000 МПа выше, чем на диаметре 0,8 мм. При этом пластичность тончайшей проволоки, оцениваемая по величине разрыва с узлом, достаточно высока и составляет 52..53 %.
Таблица 3
Механические свойства аустенитно-ферритной
и мартенситностареющей сталей
Свойства | 03Х14Н10К5М2Ю2Т (62) | 03Х12Н8К5М2ЮТ (ЗИ90-ВИ) |
Закалка 1000 С | ||
в ψ Кручение l=100d | 940 71 10 87..90 | 1020 79 1,5 20..30 |
Закалка 1000 С, деформация 80 % (диам. 0,8 мм) | ||
в ψ Кручение l=100d | 1840 56 1 30..33 | 1530 73 1 3..4 |
Закалка 1000 С, деформация 80 % (диам. 0,15 мм) | ||
в Рузл | 2300 52 | 1620 53 |
И
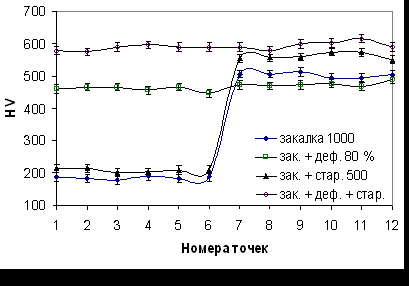
Рис. 8. Микротвердость аустенитно-ферритной стали после различных обработок
зменение микротвердости структурных составляющих аустенитно-ферритной стали после различных режимов термической обработки показано на рис. 8. Наблюдается заметное изменение микротвердости
-феррита при старении примерно на 100 HV, при этом получаемые значения микротвердости -феррита превышают 600 HV. Наиболее значительно при старении изменяется микротвердость мартенсита деформации (500..550 HV) и приближается к значениям микротвердости -феррита. Такое выравнивание свойств структурных составляющих двухфазной аустенитно-ферритной стали при одновременном образовании волокнистой гетерогенной структуры является причиной получения высоких проч-ностных свойств холодно-деформированной проволоки при сохранении достаточной пластичности.
Электронографические исследования показали, что при старении исследуемой аустенитно-ферритной стали, обработанной по режиму: закалка + деформация + старение 500° С происходит выделение NiAl из ОЦК твердого раствора как δ-феррита, так и мартенсита деформации (рис. 9). После закалки, пластической деформации и старения при температуре 650 С наблюдается появление участков аустенита, в ряде случаев в аустените появляются двойники. Образующийся аустенит также не содержит интерметаллидной фазы.
а б в
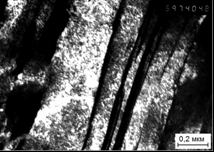
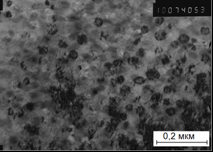
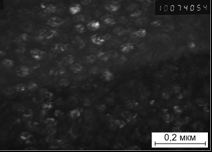
Рис. 9. Микроструктура стали 03Х14Н10К5М2Ю2Т после закалки, деформации (75 %) и старения (500° С, 1 ч): а – темнопольное изображение в рефлексе (
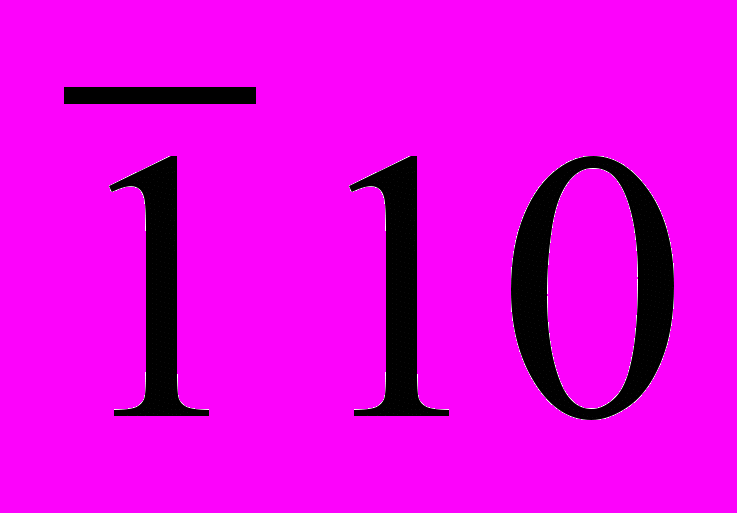
в – темнопольное изображение в сверх-структурном рефлексе (
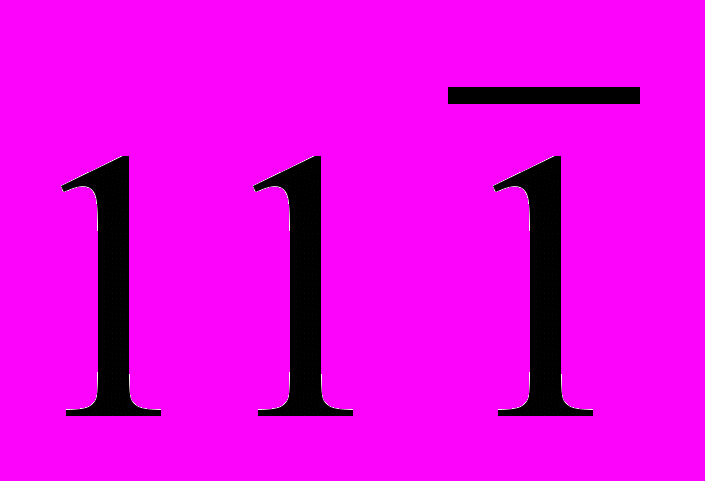
г – микродифракция; д – схема расшифровки
г д
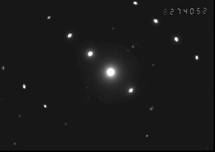
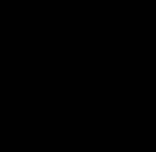
Изучение кинетики изменения механических свойств холоднодеформированной проволоки (диам. 0,8 мм) исследуемой стали при различных температурах старения показало, что наиболее высокие значения прочностных свойств получены при старении 500 С и выдержке 1..3 ч., при этом достигаются высокие прочностные свойства: в = 2550 МПА, относительное сужение находится в пределах 43..45 %. В то время как на диам. 0,15 мм в > 2900 МПа при Рузл ~ 50%.
Таким образом, отличие разработанной двухфазной аустенитно-ферритной стали 03Х14Н10К5М2Ю2Т от применяемых в промышленности сталей, заключается в возможности реализации многофакторных механизмов упрочнения, в том числе и дисперсионного твердения пересыщенных твердых растворов с выделением интерметаллидных фаз, дающего существенный прирост прочностных свойств.
В пятой главе рассматривается новая алюминийсодержащая высоко-прочная сталь ферритного класса (патент № 2323998), которая отличается от описанной выше аустенитно-ферритной стали повышенным содержанием алюминия (выше 5,1 % А1), что позволило перевести исследуемую сталь в ферритный класс. Предварительно были проведены исследования влияния содержания алюминия в количестве 2,0..3,5 % на структуру и фазовый состав практически при одной и той же базе легирования. Увеличение содержания а
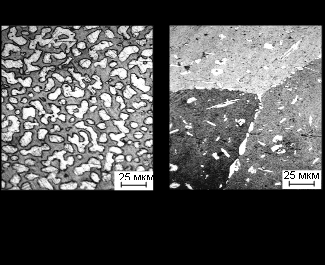
Для получения чисто ферритной структуры с целью оценки ее свойств и потенциальных возможностей после теоретических расчетов и пробных опытных плавок была выплавлена опытная плавка, имеющая состав 03Х14Н10К5М2Ю6Т. Изучение свойств ферритной стали в зависимости от температуры закалки показало, что микроструктура стали после закалки от 1000 до 1200 С полностью состоит из 100 % -феррита (рис. 11 б, в) и лишь после закалки от 900 С в структуре стали наблюдается незначительное количество (8 %) аустенита (рис. 11 а). Как показали данные рентгеноструктурного анализа, после закалки от всех температур в структуре присутствует незначительное количество интерметаллидной фазы NiAl.
а б в
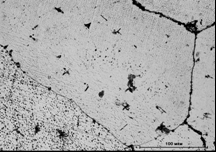
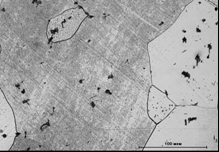
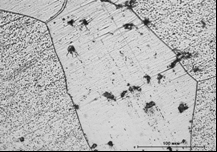
Рис. 11. Микроструктура закаленной ферритной стали от температур: а – 900° С;
б – 1000° С; в – 1200° С
При таком сложном составе в исследуемой стали вполне могут быть и другие интерметаллидные фазы, которые растворяются с увеличением температуры нагрева. На протекание процессов растворения указывает изменение периода кристаллической решетки -феррита с увеличением температуры нагрева под закалку от 800 до 1000 С.
Измерение твердости и микротвердости исследуемой стали показало чрезвычайно высокую твердость -феррита уже в закаленном состоянии, причем твердость (как по Виккерсу, так и микротвердость) мало изменяется от температуры нагрева под закалку от 1000 до 1200 С и составляет соответственно 475 HV5/12,5 и 550 HV. При температуре нагрева под закалку 900 С наблюдается значительно меньшая твердость и микротвердость, соответственно, 380 HV5/12,5 и 410 HV. Чрезвычайно высокая твердость -феррита как в аустенитно-ферритной стали, так, по-видимому, и в ферритной обусловлена присутствием в феррите закаленной стали упорядоченной интерметаллидной фазы типа NiAl. В диссертационной работе не ставилась задача подробного изучения структурообразования и фазовых превращений, протекающих в безуглеродистой высокопрочной ферритной стали 03Х14Н10К5М2Ю6Т. Основное внимание было сосредоточено на -феррите, который обладал такой же высокой твердостью как и -феррит в аустенитно-ферритной стали.
Последующее старение исследуемой ферритной стали приводит к дополнительному повышению твердости и микротвердости, что связано с протеканием процессов старения в ОЦК фазе. Температурой, при которой достигается наибольший прирост твердости при старении, является 500 С, при этом твердость составляет 550 HV5/12,5, а микротвердость 650 HV. Таким образом, в исследуемой ферритной стали 03Х14Н10К5М2Ю6Т высокопрочное состояние достигается в две стадии термической обработки: закалка на пересыщенный твердый раствор и последующее старение при 500 С.
В шестой главе рассматриваются способы дополнительного поверхностного упрочнения исследуемых сталей. Известно, что лазерная обработка является эффективным способом поверхностного упрочнения металлических изделий. Особенностью лазерной обработки являются чрезвычайно высокие скорости нагрева и охлаждения. В работе были исследованы изменения микроструктуры и микротвердости по глубине зоны оплавления, зон термического влияния и сердцевины предварительно закаленных сталей: экономнолегированной мартенситностареющей 03Х13Н8М2Т, аустенитной 03Х14Н11К5М2ТЮ, аустенитно-ферритной 03Х14Н10К5М2Ю2Т и ферритной 03Х13Н10К5М2Ю6Т, подвергнутых лазерной обработке с оплавлением и без оплавления поверхности, с последующим старением или без него. При этом определяли возможность получения упрочненного поверхностного слоя без снижения свойств сердцевины изделия.
Микроструктура после лазерной обработки с оплавлением всех исследуемых сталей приведена на рис. 12. При лазерной обработке с оплавлением на всех исследуемых сталях аустенитного, аустенитно-ферритного и ферритного классов на поверхности обнаружен слой δ-феррита различной глубины (в зависимости от режима обработки и структуры исследуемой стали от 522 мкм до 700 мкм), за исключением мартенситностареющей стали, в которой при лазерной обработке мощностью до 900 Вт слой δ-феррита не был обнаружен. Структура мартенситностареющей стали 03Х13Н8М2Т в зоне термического влияния отличается неоднородностью (см. рис. 12 а). На поверхности наблюдается существенное измельчение пакетов мартенсита, которые образовались в результате рекристаллизации аустенита, при температурах близких к температуре плавления, и последующей закалки. Затем располагается зона крупнопакетного мартенсита с последующим переходом к структуре матрицы. На рис. 13 а приведено распределение микротвердости в зоне термического влияния мартенситностареющих сталей, обработанных
а б в г
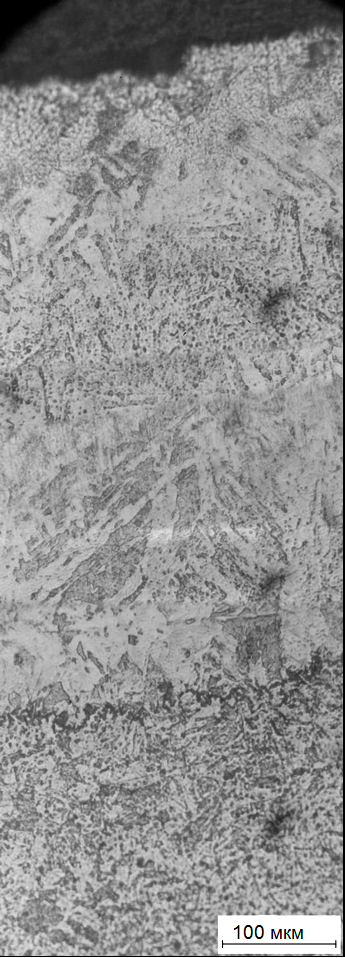
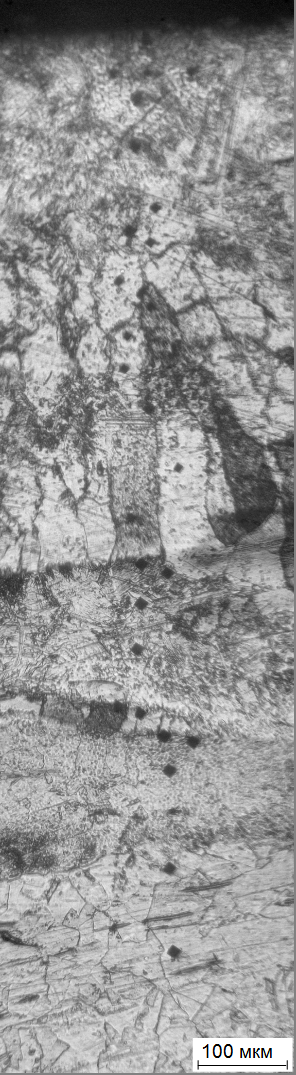
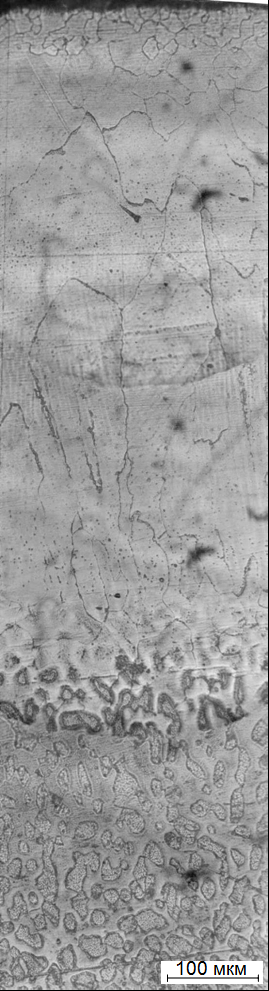
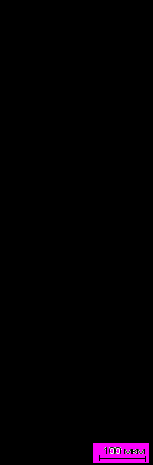
Рис. 12. Микроструктура исследуемых сталей после лазерной обработки с оплавлением:
а – мартенситностареющая 03Х13Н8М2Т; б – аустенитная 03Х14Н11К5М2ЮТ;
в – аустенитно-ферритная 03Х14Н10К5М2Ю2Т; г – ферритная 03Х13Н10К5М2Ю6Т
по различным режимам. Резкого изменения микротвердости от поверхности к центру не наблюдается. Лазерная обработка с последующим старением приводит к закономерному увеличению микротвердости, что связано с измельчением пакетов мартенсита. Причем значения микротвердости в зоне термического влияния при лазерной обработке близки к значениям микротвердости, полученным на образцах, обработанных по режимам «закалка+деформация» и «закалка+деформация+старение». Это указывает на влияние термического и фазового наклепа на упрочнение мартенситностареющих сталей. После лазерной закалки возникают термические и структурные напряжения, которые и стимулируют процесс старения. Лазерная обработка создает большую плотность дислокаций, являющихся в дальнейшем местами предпочтительного зарождения упрочняющей фазы. При старении упрочняющая фаза измельчается, расстояние между частицами уменьшаются, что существенно влияет на упрочняющий эффект.
Таким образом, лазерная обработка для мартенситностареющих сталей является неэффективной, в отличие от аустенитной 03Х14Н11К5М2ЮТ, аустенитно-ферритной 03Х14Н10К5М2Ю2Т и ферритной 03Х13Н10К5М2Ю6Т сталей, микроструктура которых после лазерной обработки с оплавлением приведена на рис.12 а, б, в, соответственно. При малых оптических увеличениях в образцах после лазерной закалки обнаружены три структурных зоны. Центральная является зоной расплавления металла при лазерной обработке стали, располагается вдоль оси лазерного луча и в поперечном сечении имеет форму округлой лунки. Особенностью ее микроструктуры является четко выраженная зона однофазного -феррита. Зона δ-феррита имеет разное строение. На поверхности образцов имеется очень узкая полоска -феррита, имеющего мелкозернистое строение. Эта зона, по-видимому, образовалась в результате рекристаллизации термически упрочненного -феррита. Далее идет зона крупнозернистого -феррита, имеющая характерное столбчатое вытянутое строение, при этом зерна направлены от поверхности вглубь образца. Такое строение зерен феррита обусловлено влиянием градиента температур. Следующая зона – зона с различно ориентированными зернами, представляющая собой двухфазную аустенитно-ферритную структуру, образовавшуюся вследствие малого времени нахождения сплава при этой температуре и интенсивной теплоотдачи (незаконченный процесс образования аустенита). Затем зона основного металла со стабильной структурой, представляющей собой зерна аустенита с двойниками отжига. В ней воздействие лазерной обработки на структуру металла визуально не обнаруживается.
Микротвердость в зоне воздействия лазерного излучения измеряли на образцах, обработанных по всем режимам. Распределение микротвердости в зоне лазерного излучения для аустенитной, аустенитно-ферритной и ферритной сталей приведено на рис. 13 а, б, в. Особенностью микроструктуры расплавленной зоны (зоны -феррита) является исключительно высокая его микротвердость. Причем такая высокая микротвердость наблюдается уже в закаленном состоянии, а последующее старение изменяет ее незначительно. Наблюдается резкое изменение микротвердости от поверхности к центру – уменьшение с 600 HV до 300 HV, первое значение соответствует микротвердости -феррита аустенитно-ферритной стали (в наружном оплавленном слое), второе – микротвердости аустенита аустенитной стали (сердцевине). Изменение микротвердости после лазерной закалки ферритной стали 03Х13Н10К5М2Ю6Т приведено на рис. 13 г. Микротвердость феррита поверхностной зоны незначительно отличается от микротвердости сердцевины и объясняется различием в величине зерна и скорости охлаждения.
Для получения информации о причинах столь высокой твердости -феррита были проведены электронно-микроскопические исследования трех зон воздействия лазерного излучения (рис. 14). Структура центральной зоны сформирована зернами -феррита с дисперсными ( 6,0 нм) частицами 2-фазы (упорядоченной ОЦК фазы на основе интерметаллида FeNiAl).
а б
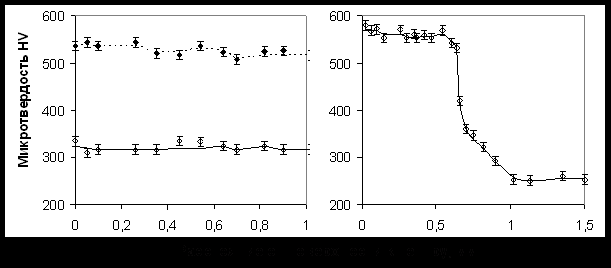
в г
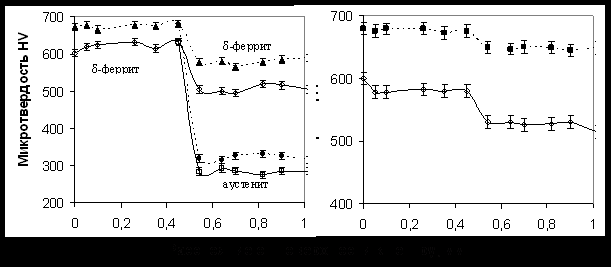
Рис. 13. Влияние лазерной обработки на микротвердость исследуемых сталей:
а – мартенситностареющая 03Х13Н8М2Т; б – аустенитная 03Х14Н11К5М2ЮТ;
в – аустенитно-ферритная 03Х14Н10К5М2Ю2Т; г – ферритная 03Х13Н10К5М2Ю6Т;
(


Соседние зерна -феррита обычно имеют существенно различную кристаллографическую ориентировку (рис. 14 а, б). Структура переходной зоны сформирована зернами двух фаз -феррита и аустенита. Для зерен -феррита характерно наличие слабо ориентированных субзерен, а также присутствие дисперсных включений 2-фазы. Других вторичных фаз в феррите не обнаружено. Размеры и распределение 2-частиц аналогичны наблюдаемым в
- феррите расплавленной зоны, что свидетельствует как о нагреве данной зоны при лазерной закалке до температур, превышающих температуру существования 2-фазы, так и о достаточно высокой скорости охлаждения металла переходной зоны в температурном интервале ее возникновения. Для аустенита характерно отсутствие выделений дисперсных внутризеренных фаз и наличие достаточно высокой плотности дислокаций.
а б в
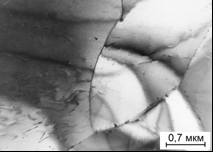
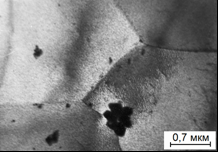
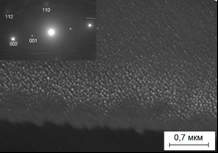
г д е
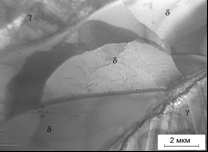
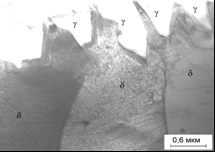
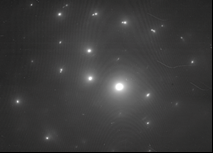
ж з и
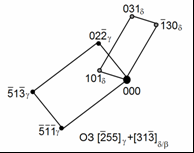
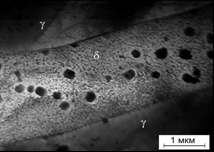
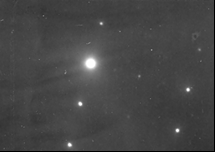
к л
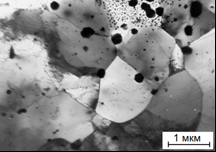
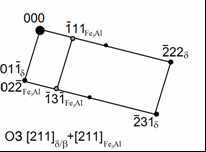
Рис. 14. Микроструктура стали 03Х14Н10К5М2Ю2Т после лазерной закалки с оплавлением: а-в – структура центральной зоны; г-ж – структура переходной зоны; з-л – структура наружной зоны; а, б, г, д, з, к – светлопольное изображение; в – темнопольное изображение в сверхструктурном рефлексе (001)NiAl; е, и – микродифракция; ж, л – схема индицирования
Рис. 14 иллюстрирует некоторые структурные особенности перехода от ферритной к ферритно-аустенитной структуре. В данном случае на периферии зерна -феррита из зоны расплава (несколько слабо ориентированных субзерен) располагаются фрагменты аустенита идентичной кристаллографической ориентации. При этом относительная ориентация решеток и близка к ориентационному соотношению Курдюмова-Закса, а протяженные плоские участки межфазной границы соответствуют следу плоскостей {111} {110}. На светлопольном изображении -зерна отчетливо видно присутствие дисперсной 2-фазы, тогда как в аустените дисперсного распада нет. Структура зоны под лункой расплава, как и структура переходной зоны, сформирована зернами двух фаз – феррита и аустенита. Но наиболее существенное отличие от переходной зоны связано с тем, что в феррите этой зоны обнаружены два типа вторичных фаз. Распределение частиц каждой из фаз по объему -зерна обычно достаточно равномерное, но плотность выделений более дисперсной из них выше, а вокруг крупных частиц имеется зона свободная от дисперсных выделений. Более дисперсная фаза имеет размеры частиц 30 нм и является 2-фазой.
Таким образом, применение лазерной обработки в аустенитной и аустенитно-ферритной сталях позволяет получить поверхностный слой с высокими значениями микротвердости непосредственно после закалки, т.е. лазерная обработка может служить эффективным способом повышения твердости поверхностного слоя.
Применение лазерной обработки с оплавлением для аустенитной и аустенитно-ферритной сталей позволило выявить последовательности фазовых превращений исследуемых сталей в процессе кристаллизации: жидкий расплав -феррит с упорядоченной 2-фазой аустенитно-ферритная структура аустенитная (в зависимости от содержания алюминия при одной и той же базе легирования).
В седьмой главе для оценки коррозионной стойкости разработанных сталей в сравнении с коррозионной стойкостью типовых сталей были проведены испытания на общую коррозию. Испытывали образцы следующих марок сталей: 40Х13, 12Х18Н10Т, 03Х12Н8К5М2ЮТ (ЗИ90-ВИ), 03Х13Н8М2Т, 03Х14Н11К5М2ЮТ, 03Х14Н10К5М2Ю2Т. Для проведения ускоренных испытаний в качестве коррозионной среды был выбран агрессивный раствор 3 % NaCl. Склонность сталей к локальным видам коррозии оценивали при осмотре на бинокулярном микроскопе при увеличении в 8..30 раз по наличию очагов коррозии: пятен, питтингов, язв. Из испытанных сталей наиболее низкую коррозионную стойкость имеет сталь 40Х13. Испытания на общую коррозию всех исследуемых сталей показали, что на всех этапах переработки (закалка, деформация, закалка+старение, закалка +деформация+старение) все исследуемые стали не склонны к общей коррозии (средняя скорость коррозии не превышала 0,004 г/м2ч). Испытания на коррозию под напряжением и межкристаллитную коррозию также показали, что все исследуемые стали, кроме 40Х13, не проявляют склонности к МКК и имеют высокую устойчивость против коррозионного разрушения.
Проведенные коррозионные исследования аустенитной стали 03Х14Н11К5М2ЮТ электрохимическим методом в 20-% водном растворе Н2SO4 позволили выявить на поляризационных кривых наиболее положительный стационарный потенциал, наименьший ток начала пассивации и полной пассивации после формирования высокопрочного состояния.
На основании проведенных коррозионных исследований новых высокопрочных алюминийсодержащих сталей на Fe-Cr-Ni основе можно заключить, что все исследуемые стали обладают высокой коррозионной стойкостью, не уступающей стойкости промышленной коррозионностойкой стали 12Х18Н10Т и имеют более высокую коррозионную стойкость по сравнению со сталью 40Х13.
Изготовление различного медицинского инструмента и его испытания проводились в НПО «Мединструмент», ПТО «Медтехника» (Казань) и в АОЗТ « Ассоциация « Медицинские технологии»» (Екатеринбург). Были изготовлены и опробованы микроиглы для офтальмологии, атравматические микроиглы, хирургические иглы различного диаметра, иглы для рефлексотерапии, электроаккупунктуры, микротросы для эндоскопии и урологии, корневые иглы, дрильборы и другие виды медицинского инструмента. Проведение полупромышленных, стендовых и клинических испытаний показало высокие качество и функциональные свойства инструмента из новых сталей, во многих случаях превосходящие свойства медицинского инструмента, изготовленного из типовых коррозионностойких сталей 40Х13, 12Х18Н10Т и др.
На основании полученных результатов была внедрена и широко используется для медицинского инструмента мартенситностареющая сталь ЗИ90-ВИ, рекомендованы и переданы заказчику новая экономнолегированная мартенситностареющая сталь 03Х13Н8М2Т, двухфазная аустенитно-ферритная сталь 03Х14Н10К5М3Ю2Т, аустенитная сталь 03Х14Н11К5М3ЮТ, ферритная сталь 03Х13Н10К5М3Ю6Т, которые прошли промышленное опробование. Результаты промышленных опробований подтверждены актами внедрения. Сталь 03Х13Н8М2Т включена в ТУ на изготовление проволоки для медицинского инструмента. На составы сталей аустенитного, аустенитно-ферритного и ферритного классов получены патенты РФ.
Таким образом, на основании проведенных комплексных исследований можно сделать заключение, что общим для всех исследуемых сталей является следующее.
1. Единая база легирования, представляющая собой Fe-Cr-Ni основу с дополнительным легированием кобальтом, молибденом, титаном и изменяющимся содержанием алюминия. Все исследуемые стали являются практически безуглеродистыми, содержание в них углерода не превышает 0,02 %. Такая база легирования является одной из предпосылок высокой пластичности всех исследуемых сталей в закаленном состоянии. В то же время низкое содержание углерода обеспечивает образование аустенита при охлаждении непосредственно из расплава в последовательности: расплав -феррит аустенит, при этом безуглеродистая Fe-Cr-Ni основа стали исключает возможность образования аустенита по нонвариантным реакциям + ↔ или ↔ + , что подтверждается отсутствуем во всех исследуемых сталях -фазы. Все исследуемые стали дополнительно легированы алюминием в количестве 0,25..6,5 %, при этом роль алюминия в сталях различных структурных классов неодинакова: в мартенситностареющих сталях алюминий не образует самостоятельных упрочняющих фаз, а входит в состав интерметаллидной фазы (Ni,Fe)3(Тi,Al). Образование самостоятельных фаз NiAl или Ni3Al не обнаружено. При некотором повышении содержания никеля и хрома и одновременном увеличении количества алюминия до 0,8 % получили сталь другого структурного класса – аустенитного, при формировании которого алюминий непосредственного участия не принимает, однако играет роль основного упрочнителя за счет образования интерметаллидной фазы типа NiAl из ОЦК-твердого раствора (мартенсита деформации). При больших содержаниях алюминия влияние его как сильного ферритообразующего элемента приводит к получению сталей аустенитно-ферритного класса с различным соотношением аустенита и -феррита. Дальнейшее повышение содержания алюминия (до 6,0 % и выше) приводит к образованию стали полностью ферритного класса.
2. Наличие деформационно-метастабильного аустенита, который при пластической деформации частично или полностью переходит в мартенсит деформации. Так как количество аустенита в исследуемых сталях различно (10% в мартенситностареющих, 100% в аустенитных и 50..30 в аустенитно-ферритных), то и влияние образования мартенсита деформации, и связанного с ним трип-эффекта, неодинаково. Наиболее сильно выраженный трип-эффект имеет место в стали аустенитного класса 03Х14Н11К5М2ЮТ, что является одним из факторов, определяющих ее высокую пластичность, и позволяет проводить холодную пластическую деформацию с чрезвычайно высокими степенями обжатия и получить в структуре нанокристаллическое состояние.
3. Выделение интерметаллида типа NiAl только в ОЦК-фазе: мартенсите охлаждения, -феррите и мартенсите деформации. При этом интерметаллид NiAl обеспечивает значительное упрочнение сталей и может иметь различное происхождение, выделяясь как непосредственно при кристаллизации, так и при распаде мартенсита деформации при старении.
В выполненной работе впервые обнаружен -феррит с аномально высокой твердостью ( до 500HV) в большой степени влияющий на конечное упрочнение после обработки деформация + старение.
4. Многофакторные механизмы упрочнения, получаемые в результате обработки: закалка + деформация + старение. К ним относится: твердорастворное упрочнение матрицы (тип матрицы изменяется от ОЦК к ГЦК или смешанный); сдвиговой механизм превращения; механизм деформационного упрочнения за счет полиморфных или превращений, протекающих по бездиффузионному механизму; механизм деформационного упрочнения гетерофазной структуры (как мартенсита деформации, так и аустенита, а в некоторых случаях -феррита) за счет «наследования» дефектов аустенита высокодисперсными кристаллами мартенсита, и распада пересыщенного твердого раствора при старении с образованием упорядоченной, изоморфной по отношению к ОЦК фазе алюминида NiAl. Образовавшиеся выделения интерметаллидной фазы типа NiAl имеют нанокристаллические размеры (6..10 нм), что является чрезвычайно важным фактором при получении проволоки тончайших диаметров, т.к. размер частиц упрочняющей фазы должен быть много меньше диаметра проволоки.
5. Высокая коррозионная стойкость, практически не уступающая коррозионной стойкости промышленной стали 12Х18Н10Т.