Технологические возможности ионного азотирования в упрочнении изделий из конструкционных и инструментальных сталей
Вид материала | Документы |
- Методика выполнения работы : Вариант Влияние легирующих элементов на структуру конструкционных, 128.12kb.
- Программа учебной дисциплины "Химия конструкционных материалов" для подготовки, 124.47kb.
- И надежную работу материала в условиях эксплуатации, и хороших технологических свойств, 135.99kb.
- Методические указания к выполнению лабораторной работы №6 для студентов всех форм обучения, 197.64kb.
- Примерная программа дисциплины технология конструкционных материалов рекомендуется, 242.94kb.
- Научные основы и технологические решения получения высокопрочных алюминийсодержащих, 586.93kb.
- Задачи: Учебные: Знать основные свойства, которыми должен обладать материал для режущих, 770.45kb.
- Материалы, применяемые в автомобилестроении и ремонтном производстве, 496.34kb.
- Приборы и материалы, 62kb.
- Реферат по дисциплине " Технологические процессы микроэлектроники " на тему: Технологические, 1398.5kb.
Технологические возможности ионного азотирования в упрочнении изделий из конструкционных и инструментальных сталей
М. Н. Босяков, С. В. Бондаренко, Д.В.Жук, П.А.Матусевич
СП «Авиценна Интернешнл », Республика Беларусь, г. Минск,
Ул. Сурганова, 2а, 220012, тел. +375 17 2355002
Ионно-плазменное азотирование (ИПА) – метод химико-термической обработки изделий из стали и чугуна с большими технологическими возможностями, позволяющий получать диффузионные слои нужного состава путем использования разных газовых сред, т.е. процесс диффузионного насыщения управляем и может быть оптимизирован в зависимости от конкретных требований к глубине слоя и твердости поверхности.
Температурный диапазон ионного азотирования шире, чем газового и находится в пределах 400-600 0С. Обработка при температурах ниже 500 0С особенно эффективна при упрочнении изделий из инструментальных легированных сталей для холодной обработки, быстрорежущих и мартенситно-стареющих сталей, т.к. значительно повышаются их эксплуатационные свойства при сохранении твердости сердцевины на уровне 55-60 HRC.
Упрочняющей обработке методом ИПА подвергаются детали и инструменты практически всех отраслей промышленности (рис.1).
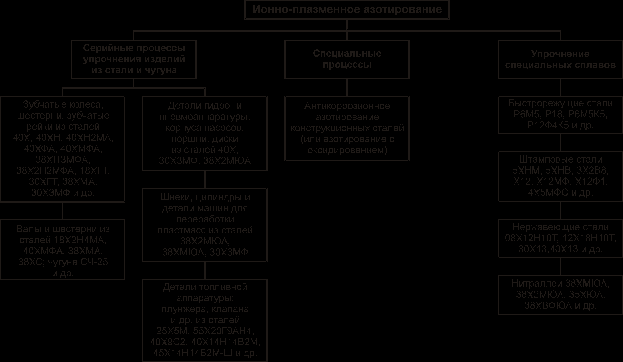
Рис. 1. Применение ионно-плазменного азотирования для упрочнения различных изделий
В результате ИПА можно улучшить следующие характеристики изделий: износостойкость, усталостную выносливость, антизадирные свойства, теплостойкость и коррозионную стойкость.
В сравнении с широко используемыми способами упрочняющей химико-термической обработки стальных деталей, такими, как цементация, нитроцементация, цианирование и газовое азотирование в печах, метод ИПА имеет следующие основные преимущества:
- более высокая поверхностная твердость азотированных деталей;
- отсутствие деформации деталей после обработки и высокая чистота поверхности;
- повышение предела выносливости и увеличение износостойкости обработанных деталей;
- более низкая температура обработки, благодаря чему, в стали не происходит структурных превращений;
- возможность обработки глухих и сквозных отверстий;
- сохранение твердости азотированного слоя после нагрева до 600-650 С;
- возможность получения слоев заданного состава;
- возможность обработки изделий неограниченных размеров и форм;
- отсутствие загрязнения окружающей среды;
- повышение культуры производства;
- снижение себестоимости обработки в несколько раз.
Преимущества ИПА проявляются и в существенном сокращении основных издержек производства.
Так, например, по сравнению с газовым азотированием в печах, ИПА обеспечивает:
- сокращение продолжительности обработки в 2–5 раз, как за счет снижения времени нагрева и охлаждения садки, так и за счет уменьшения времени изотермической выдержки;
- снижение хрупкости упрочненного слоя;
- сокращение расхода рабочих газов в 20–100 раз;
- сокращение расхода электроэнергии 1,5-3 раза;
- исключение операции депассивации;
- снижение деформации настолько, чтобы исключить финишную шлифовку;
- простота и надежность экранной защиты от азотирования неупрочняемых поверхностей;
- улучшение санитарно-гигиенических условий производства;
- полное соответствие технологии всем современным требованиям по охране окружающей среды.
По сравнению с закалкой обработка методом ИПА позволяет:
- исключить деформации;
- увеличить ресурс работы азотированной поверхности в 2-5 раз.
Применение ИПА вместо цементации, нитроцементации, газового или жидкостного азотирования, объемной или ТВЧ закалки позволяет сэкономить основное оборудование и производственные площади, снизить станочные и транспортные затраты, уменьшить расход электроэнергии и активных газовых сред.
Принцип действия ИПА заключается в том, что в разряженной (р =200-1000 Па) азотсодержащей газовой среде между катодом – деталями – и анодом – стенками вакуумной камеры – возбуждается аномальный тлеющий разряд, образующий активную среду (ионы, атомы, возбужденные молекулы), обеспечивающую формирование азотированного слоя, состоящего из внешней – нитридной зоны и располагающейся под ней диффузионной зоны.
Технологическими факторами, влияющими на эффективность ионного азотирования, являются температура процесса, продолжительность насыщения, давление, состав и расход рабочей газовой смеси.
Температура процесса, площадь садки, участвующей в теплообмене и эффективность теплообмена со стенкой (количество экранов) определяют мощность, необходимую для поддержания разряда и обеспечивающую нужную температуру изделий. Выбор температуры зависит от степени легированности азотируемой стали нитридообразующими элементами: чем выше степень легированности, тем выше температура.
Температура обработки должна быть как минимум на 10-200С ниже температуры отпуска.
Длительность и температура процесса насыщения определяют глубину слоя, распределение твердости по глубине и толщину нитридной зоны.
Состав насыщающей среды зависит от степени легирования обрабатываемой стали и требований к твердости и глубине азотированного слоя.
Давление процесса должно быть таким, чтобы обеспечивалось плотное «облегание» разрядом поверхности изделий и получение равномерного азотированного слоя. Однако, при этом следует иметь в виду, что разряд на всех стадиях процесса должен быть аномальным, т. е. поверхность всех деталей в садке полностью должна быть покрыта свечением, а плотность разрядного тока должна быть больше нормальной плотности для данного давления с учетом эффекта нагрева газа в катодной области разряда.
С появлением установок ИПА нового поколения, использующих в качестве рабочей среды регулируемые по составу смеси водорода, азота и аргона, а так же плазму «пульсирующего», а не постоянного тока, технологичность процесса ионного азотирования существенно возросла.
Использование комбинированного нагрева («горячие» стенки камеры) либо усиленной тепловой защиты (тройной теплозащитный экран) наряду с возможностью независимо регулировать состав газа и давление в камере позволяют при обработке режущего инструмента избежать перегрева тонких режущих кромок в процессе разогрева садки, точно регулировать время насыщения а, соответственно, и глубину слоя, т.к. разогрев изделий возможно производить в безазотной среде, например, в смеси Ar+H2.
Эффективная теплоизоляция в рабочей камере (тройной теплозащитный экран) позволяет обрабатывать изделия с низким удельным энергопотреблением, что позволяет свести к минимуму температурные различия внутри садки во время обработки. Об этом свидетельствует распределение микротвердости по глубине азотированного слоя для образцов, располагавшихся в разных местах садки (рис. 2).
![]() |
Рис. 2. Распределение микротвердости по глубине азотированного слоя для трех образцов располагавшихся в разных местах садки.
а, в – шестерня массой 10,1 кг, 51 шт., ст – 40Х, модуль 4,5, выдержка 16 часов, Т= 530 0С;
б, г – шестерня массой 45 кг, 11 шт., ст – 38ХН3МФА, модуль 3,25 (наружный венец)
и 7 мм (внутренний венец), выдержка 16 часов, Т=555 0С.
Ионное азотирование – эффективный метод упрочняющей обработки деталей из легированных конструкционных сталей: шестерен, зубчатых венцов, вал-зубчатых шестерен, валов, прямозубых, конических и цилиндрических шестерен, муфт, валов-шестерен сложной геометрической конфигурации и др.
Цементация, нитроцементация и ТВЧ-закалка оправдывают себя при изготовлении тяжелонагруженных деталей (зубчатые колеса, оси, валы и др.) низкой и средней точности, не требующих последующей шлифовки.
Указанные виды термообработки экономически нецелесообразны при изготовлении средне- и низконагруженных высокоточных деталей, т.к. при данной обработке наблюдается значительное коробление и требуется последующая шлифовка. Соответственно, при шлифовке необходимо снимать значительную толщину упрочненного слоя.
ИПА позволяет существенно снизить коробление и деформацию деталей при сохранении шероховатости поверхности в пределах Ra=0,63…1,2 мкм, что позволяет в подавляющем большинстве случаев использовать ИПА как финишную обработку.
Применительно к станкостроению, ионное азотирование зубчатых колес в существенной мере снижает шумовые характеристики станков, тем самым, повышая их конкурентоспособность на рынке.
ИПА наиболее эффективно при обработке крупносерийных однотипных деталей: шестерен, валов, осей, зубчатых валов, вал-зубчатых шестерен и др. Шестерни, подвергнутые плазменному азотированию, имеют лучшую стабильность размеров по сравнению с цементованными шестернями и могут использоваться без дополнительной обработки. При этом несущая способность боковой поверхности и прочность основания зуба, достигаемые с помощью плазменного азотирования, соответствуют цементованным шестерням (таб. 1).
Таблица 1
Характеристики сопротивления усталости сталей в зависимости от способов упрочнения зубчатых колес
Тип стали | Вид обработки | Предел выносливости при изгибе, МПа | Предел контактной выносливости поверхности, МПа | Твердость боковой поверхности зубъев, HV |
Легированные | Упрочнение | 200-350 | 570-920 | 200-400 |
Улучшаемые (40Х, 40ХН, 40ХФА, 40ХН2МА, 40ХМФА, 38ХМ, 38ХН3МФА, 38Х2Н2МФА, 30Х2НМ и др.) | Азотирование | 400-500 | 770-1200 | 350-650 |
Нормализованные | Плазменная или индукционная закалка | 250-400 | 980-1370 | 500-650 |
Специальные азотируемые (38ХМЮА, 38Х2МЮА, 35ХЮА, 38ХВФЮА, 30Х3МФ и др.) | Азотирование | 520-690 | 1150-1450 | 700-850 |
Легированные | Цементация и нитроцементация | 400-700 | 1250-1650 | 650-850 |
При упрочняющей обработке методом ионного азотирования деталей из цементуемых, низко- и среднелегированных сталей (18ХГТ, 20ХНЗА, 20ХГНМ, 25ХГТ, 40Х, 40ХН, 40ХФА и др.) необходимо в начале проводить улучшение поковок – объемную закалку и отпуск до твердости 241-285 НВ (для некоторых сталей – 269-302 НВ), затем механическую обработку и в завершение – ионное азотирование. Для обеспечения минимальной деформации изделий перед азотированием для снятия напряжений рекомендуется проводить отжиг в атмосфере защитного газа, причем температура отжига должна быть выше температуры азотирования. Отжиг следует проводить перед точной механической обработкой.
Глубина азотированного слоя, формируемого на указанных изделиях, изготовленных из сталей 40Х, 18ХГТ, 25ХГТ, 20Х2Н4А и др., составляет 0,3-0,5 мм при твердости 500-800 HV в зависимости от марки стали (рис 3).
Для передач, работающих в условиях более тяжелых нагрузок, азотированный слой должен быть на уровне 0,6-0,8 мм с тонкой нитридной зоной или вообще без нее.
![]() | ![]() |
Рис. 3. Распределение микротвердости по глубине азотированного слоя для разных сталей
Оптимизация свойств упрочненного слоя определяется совокупностью характеристик основного материала (твердость сердцевины) и параметрами азотированного слоя. Характер нагрузки определяет глубину диффузионного слоя, тип и толщину нитридного слоя:
- износ – g’- или e-слой;
- динамическая нагрузка – ограниченная толщина нитридного слоя или вообще без нитридного слоя;
- коррозия – e-слой.
Независимое управление расходом каждого из компонентов газовой смеси, давлением в рабочей камере и вариация температурой процесса позволяют формировать слои различной глубины и твердости (рис. 4), обеспечивая тем самым стабильное качество обработки с минимальным разбросом свойств от детали к детали и от садки к садке (рис. 5).
![]() |
Рис. 4. Распределение микротвердости по глубине азотированного слоя стали 40Х
1, 3, 5 – одностадийный процесс;
2,4 – двухстадийный процесс по содержанию N2 в рабочей смеси
1,2 – T=5300C, t=16 часов; 3 – T=5600C, t=16 часов;
4 – T=5550C, t=15 часов, 5 – T = 460 0С, t = 16 часов
![]() а | ![]() б |
Рис. 5. Разброс микротвердости по глубине азотированного слоя
для стали 40Х (а) и 38ХНЗМФА (б) для серийных процессов.
Ионное азотирование широко известно и как один из эффективных методов повышения износостойкости режущего инструмента, изготовленного из быстрорежущих сталей марки Р6М5, Р18, Р6М5К5, Р12Ф4К5 и др.
Азотирование повышает износостойкость инструмента и его теплостойкость. Азотированная поверхность инструмента, обладающая пониженным коэффициентом трения и улучшенными антифрикционными свойствами, обеспечивает более легкий отвод стружки, а также предотвращает ее налипание на режущие кромки и образование лунок износа, что дает возможность увеличить подачу и скорость резания.
Оптимальной структурой азотированной быстрорежущей стали является высокоазотистый мартенсит, не содержащий избыточных нитридов. Указанная структура обеспечивается насыщением поверхности инструмента азотом при температуре 480-5200С в процессе кратковременного азотирования (до 1 часа). При этом формируется упрочненный слой глубиной 20-40 мкм с микротвердостью поверхности 1000-1200 HV0,5 при твердости сердцевины 800-900 HV (рис. 6) , а стойкость инструмента после ионного азотирования увеличивается в 2–8 раз в зависимости от его типа и вида обрабатываемого материала.
![]() а | ![]() б |
Рис. 6. Структура азотированного слоя стали Р6М5 (а) и распределение микротвердости по глубине слоя (б).
Главным достоинством ионного азотирования инструмента является возможность получения только диффузионного упрочненного слоя, либо слоя с монофазным нитридом Fe4N (’-фаза) на поверхности, в отличие от классического газового азотирования в аммиаке, где нитридный слой состоит из двух фаз - ’+, что является источником внутренних напряжений на границе раздела фаз и вызывает хрупкость и отслаивание упрочненного слоя при эксплуатации.
Ионное азотирование является также одним из основных методов увеличения долговечности штампового инструмента и литьевой оснастки из сталей 5ХНМ, 4Х5МФС, 3Х2В8, 4Х5В2ФС, 4Х4ВМФС, 38Х2МЮА, Х12, Х12М, Х12Ф1.
В результате ионного азотирования можно улучшить следующие характеристики изделий:
- Ковочные штампы для горячей штамповки и пресс-формы для литья металлов и сплавов – повышается износостойкость, уменьшается прилипание металла.
- Пресс-формы для литья алюминия под давлением – азотированный слой препятствует прилипанию металла в зоне подачи жидкой струи, и процесс заполнения формы является менее турбулентным, что увеличивает срок службы пресс-форм, а отливка получается более высокого качества.
Существенно улучшает ионное азотирование и эксплуатационные характеристики инструмента для холодной (T < 250 0С) обработки – вытяжка, гибка, штамповка, прессование, резка, чеканка и прошивка.
Основные требования, обеспечивающие высокую работоспособность такого инструмента – высокая прочность при сжатии, износостойкость и сопротивление холодной ударной нагрузке – достигаются в результате упрочняющей обработки методом ионного азотирования.
Если для инструмента используется высокохромистая сталь (12% хрома), то азотированный слой должен быть только диффузионным, если низколегированные стали – то дополнительно к диффузионному слою должен быть γ-слой – твердый и пластичный.
Особенностью ионного азотирования высокохромистых сталей является то, что выбирая температуру процесса можно в широких пределах сохранять твердость сердцевины изделия, задаваемую предварительной термической обработкой (табл. 2).
Для получения износостойкого поверхностного слоя при сохранении вязкой сердцевины штампа необходимо проводить вначале закалку с отпуском на вторичную твердость, размерную обработку и затем ионное азотирование.
Для исключения или сведения к минимуму деформаций, возникающих при ионном азотировании штампового инструмента, перед окончательной механической обработкой рекомендуется проводить отжиг в среде инертного газа при температуре как минимум на 20 С ниже температуры отпуска.
При необходимости применяют полировку азотированных рабочих поверхностей.
Таблица 2.
Характеристики легированных сталей после ионно-плазменного азотирования.
Марка стали | Твердость сердцевины, HRC | Температура процесса 0С | Характеристики слоя | Тип реко-менду-емого слоя соеди-нений | ||
Глубина, мм | Пов. тв-сть, HV 1 | Толщина слоя соед., мкм | ||||
Стали для горячей обработки | ||||||
4Х5МФС | 35-55 | 500-560 | 0,1-0,3 | 900-1100 | 2-6 | γ’ |
5ХНМ | 36-44 | 450-550 | 0,1-0,3 | 620-760 | 2-6 | γ’ |
3Х2В8 | 35-50 | 500-560 | 0,1-0,25 | 950-1100 | 2-5 | γ’ |
3Х3М3Ф | 35-51 | 500-560 | 0,1-0,3 | 900-1100 | 2-6 | γ’ |
Стали для холодной обработки | ||||||
Х12 | 50-55 | 450-520 | 0,1-0,2 | 1000-1100 | - | - |
Х12М | 53-60 | 400-520 | 0,1-0,2 | 1000-1200 | - | - |
Х12Ф1 | 52-60 | 480-550 | 0,1-0,2 | 1000-1250 | - | - |
Х12МФ | 56-58 | 400-480 | 0,1-0,2 | 1000-1300 | - | - |
Варьируя состав насыщающей среды, температуру процесса и его длительность можно формировать слои разной глубины и твердости (рис. 7,8).
![]() пуансон массой 237 кг ст. – 5ХНМ а | ![]() в |
![]() пресс-форма массой 1060 кг. ст. – 5ХНМ б | ![]() г |
Рис. 7. Примеры обработки штамповой оснастки (а, б) и распределение микротвердости по глубине азотированного слоя (в, г).
![]() | ![]() HV 0,5 d, мм |
![]() | ![]() HV 0,5 d, мм |
а | б |
Рис. 8. Примеры обработки литьевых форм из стали 4Х5МФС а – вид изделия, б – распределение микротвердости по глубине азотированного слоя. |
Таким образом, как показывает мировой опыт, применение технологии ионного азотирования для упрочняющей обработки изделий из конструкционных сталей, а так же режущего и штампового инструмента эта технология является эффективной и относительно легко реализуемой, особенно с применением плазмы пульсирующего тока.