Определение требований к посадочным поверхностям вала и отверстия в корпусе 3 Расчет допусков размеров, входящих в размерную цепь
Вид материала | Реферат |
СодержаниеТогда степень точности колеса будет записана 9С ГОСТ 1643-81 |
- Определение требований к посадочным поверхностям вала и отверстий корпуса 3 Расчет, 143.72kb.
- Состав дипломного проекта специальности “ технология машиностроения, 60.43kb.
- Расчёт параметров зубчатых передаточных механизмов с учётом требований iso, 105.35kb.
- Мышцы головы, 154.77kb.
- 1. Предварительный расчет поверхности теплообмена, 39.68kb.
- Практическая работа № (заочное отделение) Дисциплина: «Основы экономики», 98.7kb.
- Тема: Грыжи пищеводного отверстия диафрагмы, 28.51kb.
- Теоретические вопросы для сдачи допусков к лабораторным работам по курсу «химия нефти», 62.2kb.
- Нормирование точности гладких цилиндрических элементов деталей. Расчет и выбор допусков, 46.36kb.
- Темы курсовых работ: «Расчет и разработка схем ввода-вывода на мс кр1533»; «Анализ, 22.11kb.
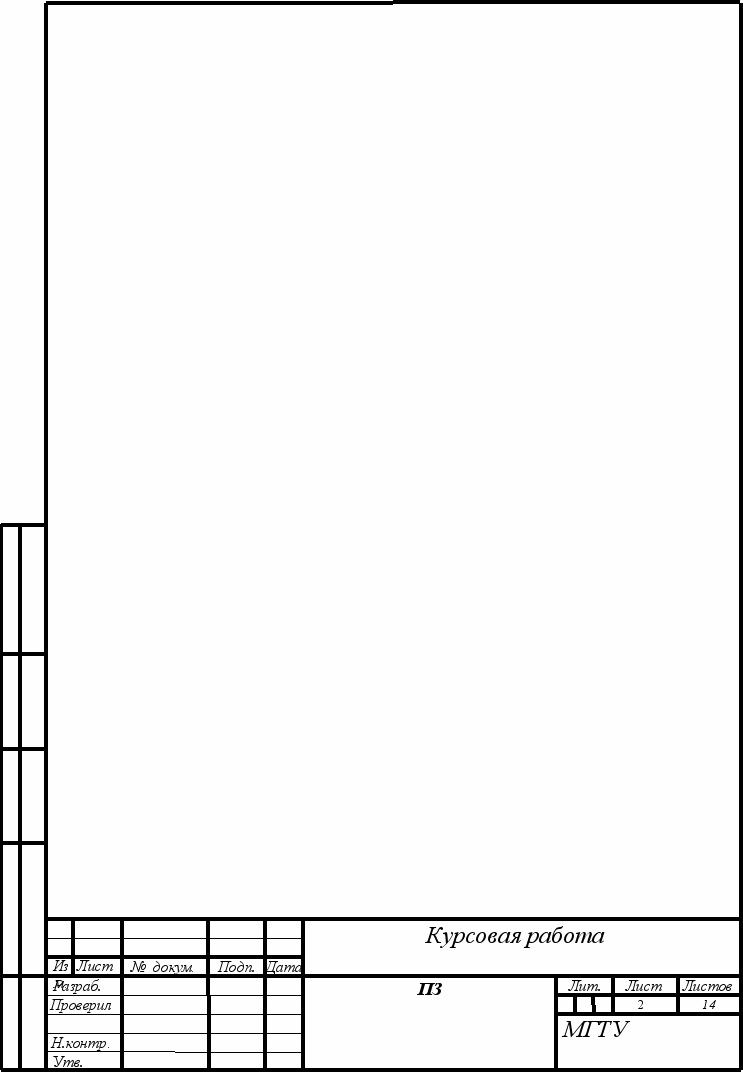
Содержание
Введение1Расчет и нормирование зубчатой передачи 1.1 Выбор степени точности зубчатой передачи 1.2 Выбор вида сопряжения зубьев колес передачи 1.3 Выбор показателей для контроля зубчатых колес 2 Расчёт и нормирование точности гладких цилиндрических соединений 2.1 Расчет и выбор посадок неподвижного соединения с дополнительным креплением 2.2 Расчет калибров 2.2.1 Расчет калибров пробок 2.2.2 Расчет калибров скоб 2.3 Расчет и выбор посадок подшипников качения 2.3.1 Расчет и выбор посадок подшипников качения на вал и корпус 2.3.2 Определение требований к посадочным поверхностям вала и отверстия в корпусе 3 Расчет допусков размеров, входящих в размерную цепь Список используемой литературы | 34 4 4 4 7 7 8 8 9 9 9 11 13 14 |
Введение
Для развития машиностроения большое значение имеет организация производства машин и других изделий на основе взаимозаменяемости, применение и создание надежных средств технических измерений и контроля.
В машиностроении созданы и освоены новые системы современных, надежных и эффективных машин для комплексной автоматизации производства, что позволяет выпускать продукцию высокого качества с наименьшими затратами труда. В настоящее время непрерывно совершенствуются конструкции машин и других изделий, технология и средства их производства и контроля. Расширяется внутриотраслевая и межотраслевая специализации на основе унификации и стандартизации изделий, широко используются методы комплексной опережающей стандартизации, повсеместно внедряются системы управления и аттестации продукции, а также система технологической подготовки производства.
Точность и ее контроль служат исходной предпосылкой важнейшего свойства совокупности изделий – взаимозаменяемости, определяющей в значительной мере технико-экономический эффект, получаемый при эксплуатации современных технических устройств.
1 Расчет и нормирование зубчатой передачи
- Выбор степени точности зубчатой передачи
Исходные данные:
число зубьев шестерни z1=41;
число зубьев колеса z2=287;
межосевое расстояние aw=328мм;
модуль m=2 мм;
делительный диаметр d=574 мм;
окружная скорость Vокр=3,2 м/с.
Система допусков цилиндрических передач (ГОСТ 1643-81) устанавливает 12 степеней точности зубчатых колес. Степень точности проектируемого зубчатого колеса устанавливается в зависимости от окружной скорости колеса. По таблице 2.1[2],исходя из Vокр=3,2 м/с, для цилиндрических колес выбираем 9 степень точности по норме плавности. Используя принцип комбинирования, назначаем 9-ю степень точности по кинематической точности, а по норме полноты контакта на одну степень точнее-9.
1.2 Выбор вида сопряжения зубьев колес передачи
Вида сопряжения передачи выбирается по величине гарантированного зазора.
Боковой зазор - это зазор между нерабочими профилями зубьев, необходимый для размещения смазки, компенсации погрешностей при изготовлении. Величину бокового зазора, необходимого для размещения смазки, ориентировочно можно определить:
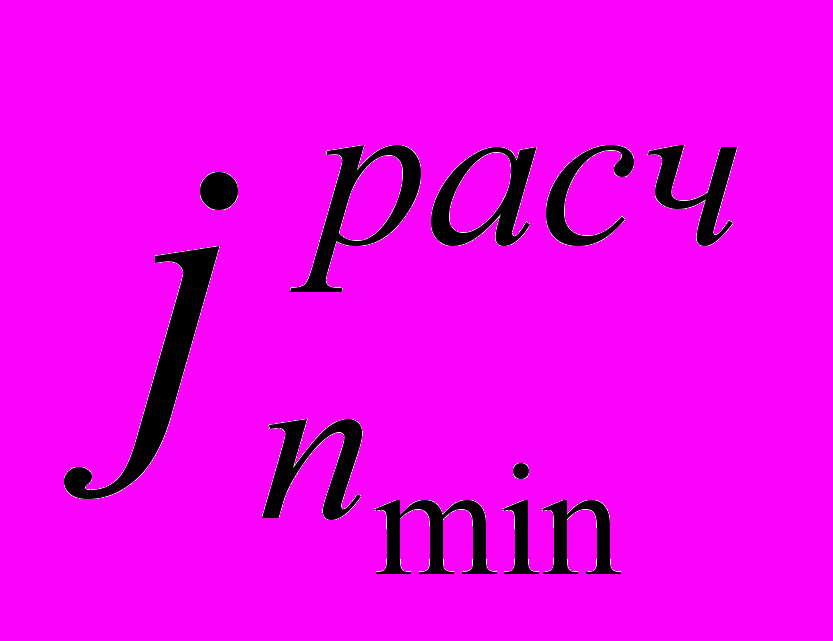
По найденному значению
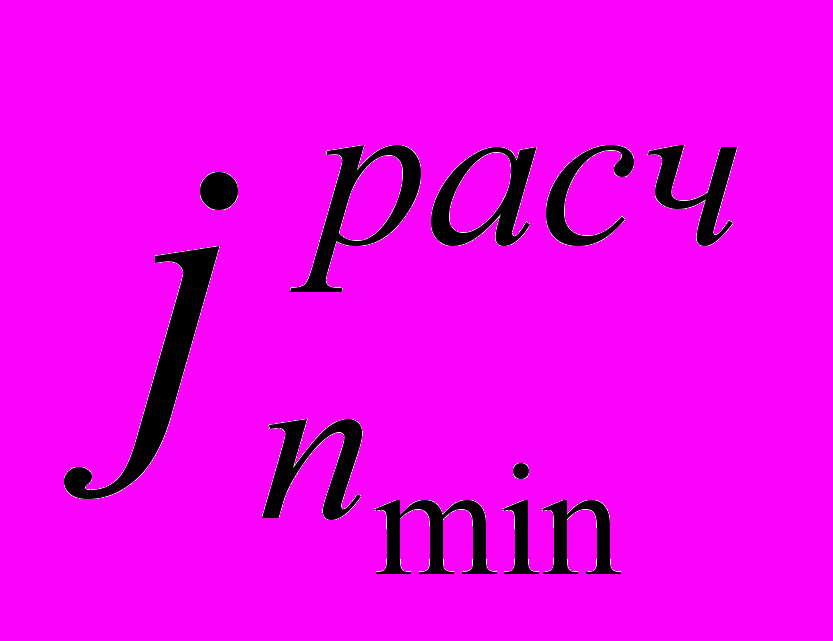
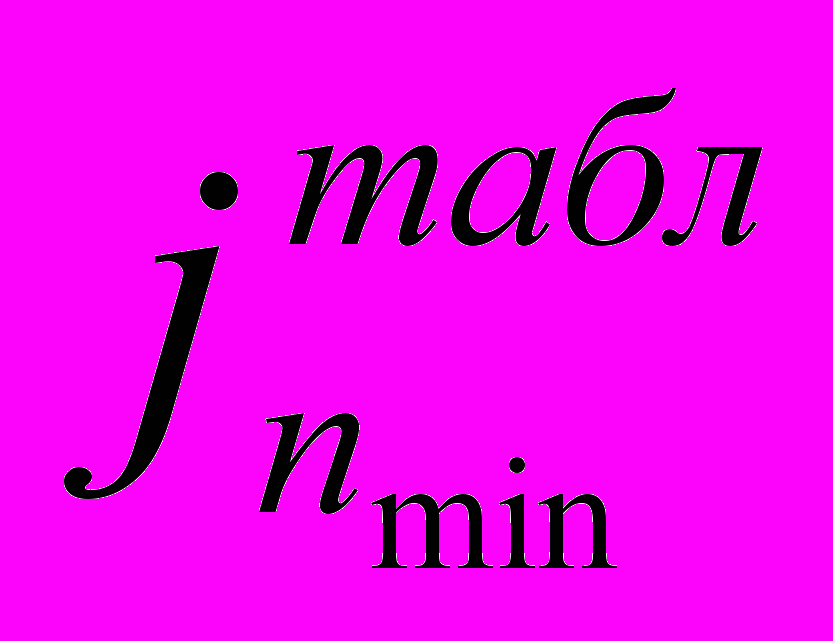
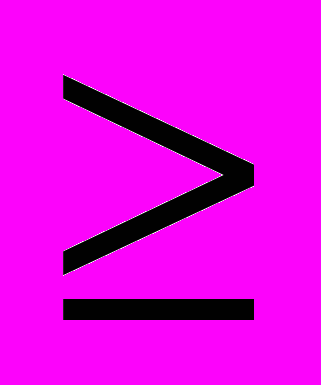
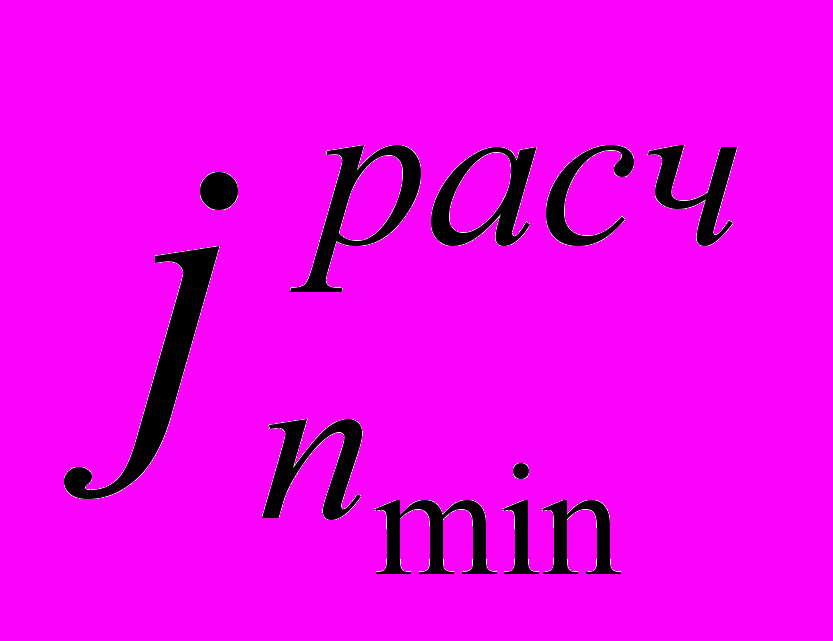
0,01
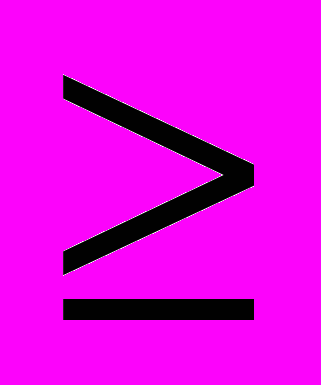
Тогда степень точности колеса будет записана 9С ГОСТ 1643-81
1.3 Выбор показателей для контроля зубчатых колес.
Выбор показателей для контроля зубчатого колеса производится согласно рекомендациям [2] по таблицам 2, 3, 5 ГОСТ 1643-81, а по таблицам 6, 8, 12, 22 ГОСТ 1643-81 назначаем на них допуски.
Средство для контроля показателей выбираем по таблице 5 с.400-405[5]. Результаты выбора показателей, допуска на них и средств контроля сводим в таблицу 1.
Таблица 1- Показатели и приборы для контроля зубчатых колеса.
Нормы точности | Наименование и условное обозначение контролирующего параметра | Условное обозначение и численное значение допуска, м | Наименование и модель прибора |
1.Кинематическая | Fir'' - колебания измерительного межосевого расстояния за один оборот колеса | Fi''=140 | Межцентромер МЦ-400Б |
2.Плавность работы | fir'' - колебания измерительного межосевого расстояния на одном зубе | fir''=45 | Межцентромер МЦ-400Б |
3. Норма полноты контакта | Fβr – погрешность направления зуба | Fβ=25 | Ходомер БВ-5075 |
4. Боковой зазор | Ews – наименьшее отклонение длины общей нормали Tw – допуск на отклонение длины общей нормали | Ews =-160 Tw =45 | Нормалиметр МЦ-400Б |
Определим длину общей нормали W:
W=m*W1,
где W1-коэффициент, определяемый по таблице справочника [4] в зависимости от числа зубьев z1=287.
W=2*44.5560=89.112
Из ГОСТа 1643-81 выбираем отклонение на длину общей нормали:
Ews =-90 (наименьшее отклонение на длину общей нормали).
По таблице 18 находятся значения допуска на длину общей нормали Tw=110, исходя из значения радиального биения зубчатого венца Fr=100 мкм, которое выбирается по таблице 6.
Наибольшее отклонение длины общей нормали будет рассчитано по формуле:
Ewe= Ews-Tw;
Ewe=-0.03 мм;
W=
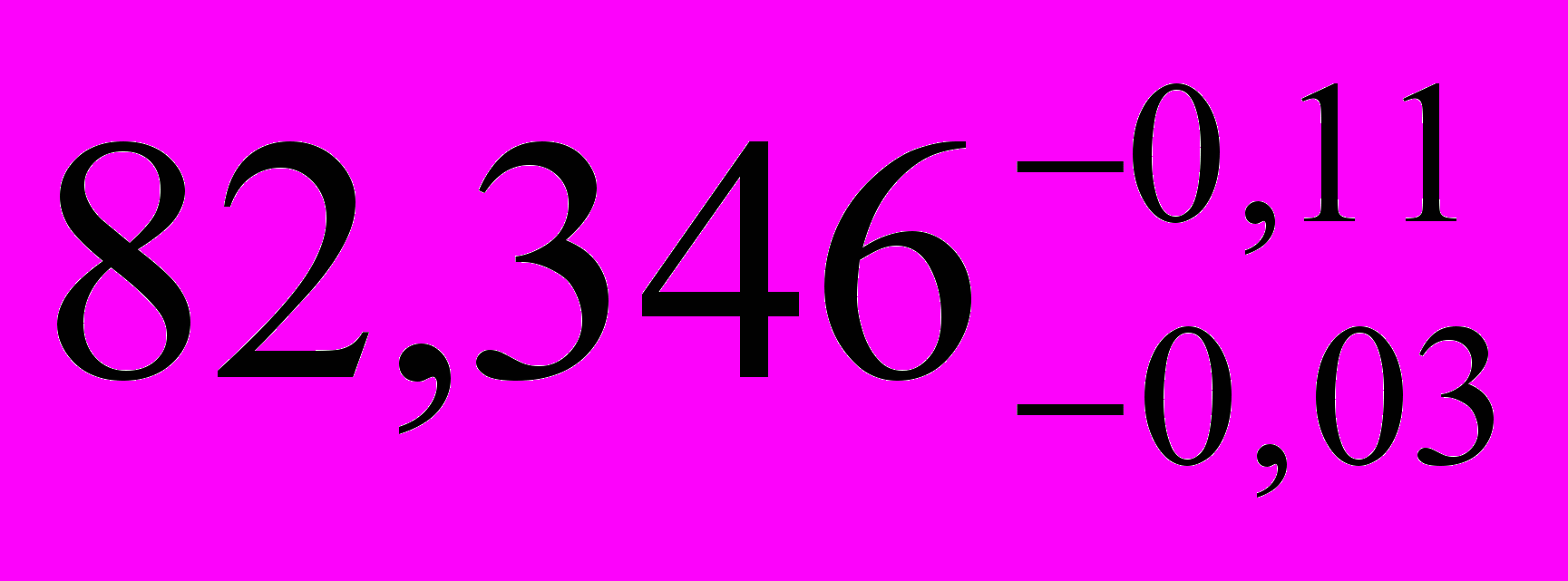
Требования к точности заготовки определяются допусками на диаметры выступов da, радиальным и торцевым биениями. Допуски на диаметры выступов назначаются по 14 квалитету точности Tda=IT14, т.к. нагруженный диаметр в процессе контроля не является базой.
Допуск на радиальное биение поверхности вершин находится по зависимости:
Fda=0.1*m=0.2.
Допуск на торцевое биение определяется по зависимости:
FT =
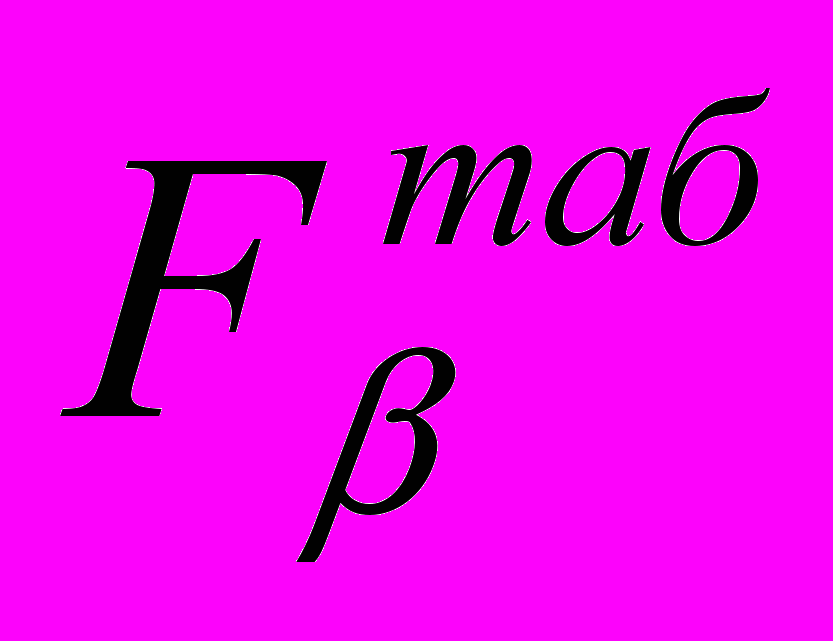
где
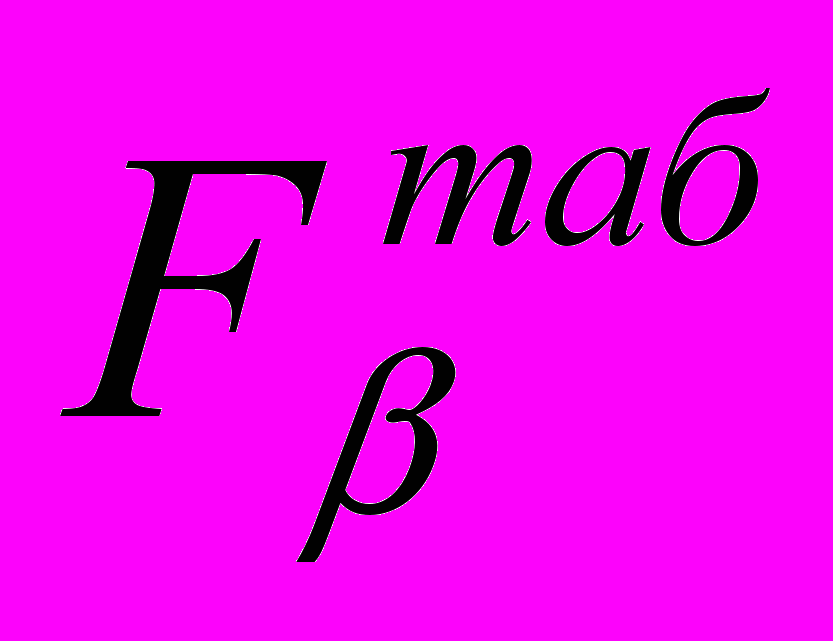
d – делительный диаметр колеса.
FT=0.02*574/100=0.1148 мкм.
Шероховатость рабочей поверхности зубьев выбирается по таблице [1] Ra=6.3.
2 Расчёт и нормирование точности гладких цилиндрических соединений
2.1 Расчет и выбор посадок неподвижного соединения с дополнительным креплением
Исходные данные:
точность зубчатого колеса 9,
номинальный диаметр соединения d=70 мм,
ширина шпоночного паза b=49 мм,
число зубьев колеса z1=287,
модуль m=2 мм,
допуск на радиальное биение зубчатого венца Fr=100 мкм.
Соединение зубчатого колеса с валом редуктора с дополнительным креплением при помощи шпонки является разъемным неподвижным соединением, образованным переходной посадкой. Расчет разъемных соединений, образованных переходными посадками, производится исходя из условия:
- обеспечение высокой точности центрирования зубчатого колеса на валу;
- обеспечение легкой сборки и разборки соединения.
Сочетание этих двух условий возможно лишь при небольших натягах или зазорах в соединении.
Хорошее центрирование зубчатого колеса на валу необходимо для обеспечения высокой кинематической точности передачи, ограничения динамических нагрузок и т.д. Известно, что наличие зазора в сопряжении за счет одностороннего смещения вала в отверстии, вызывает появление радиального биения зубчатого венца колеса, определяющего кинематическую точность.
В этом случае наибольший допустимый зазор, обеспечивающий первое условие, может быть определен по формуле:
Smax
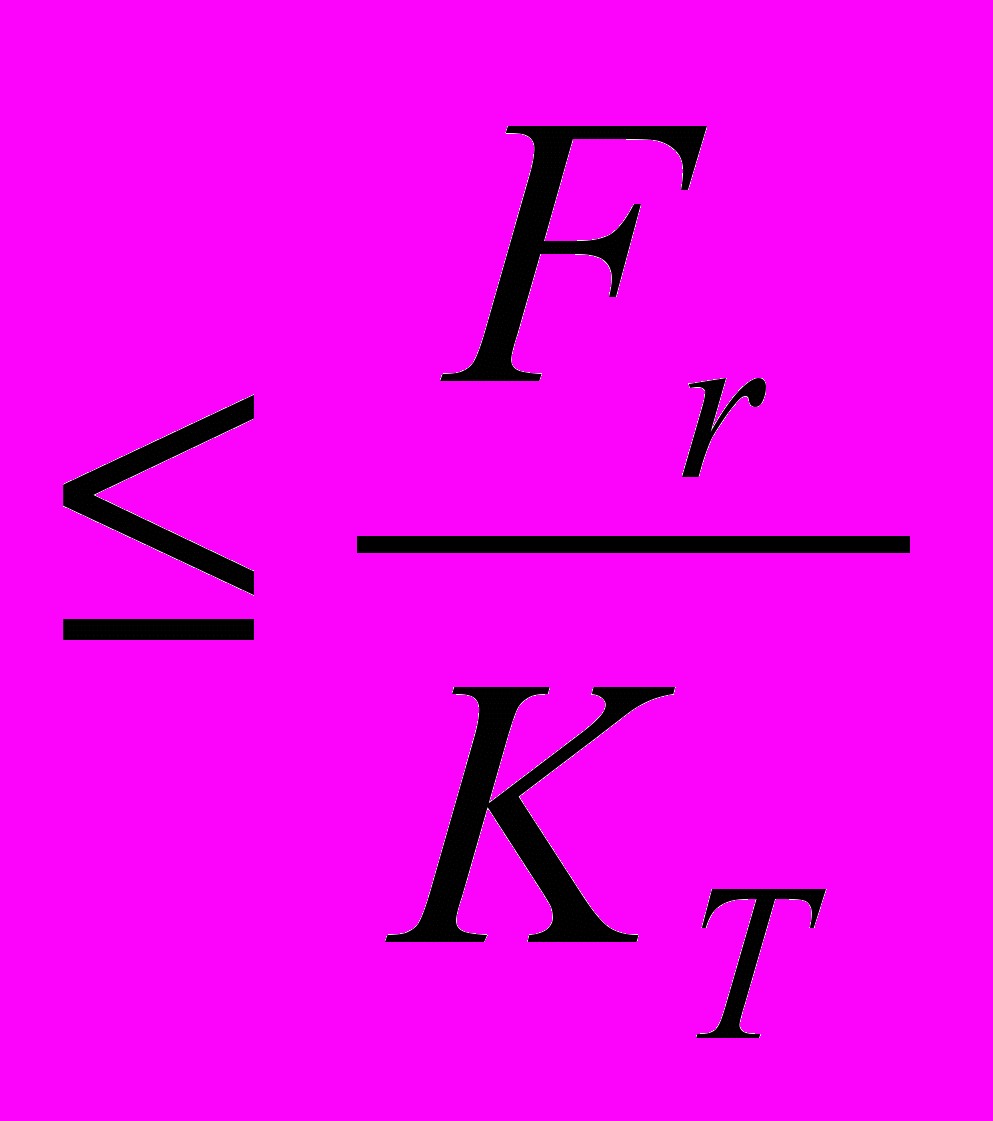
где KT – коэффициент запаса точности (KT =2…5), принимаем KT =2.
Fr – допуск радиального биения зубчатого венца (Fr =100 мкм).
Smax=100/2=50 мкм.
Наибольший возможный натяг в соединении рассчитывается по формуле:
Nmax= Smax
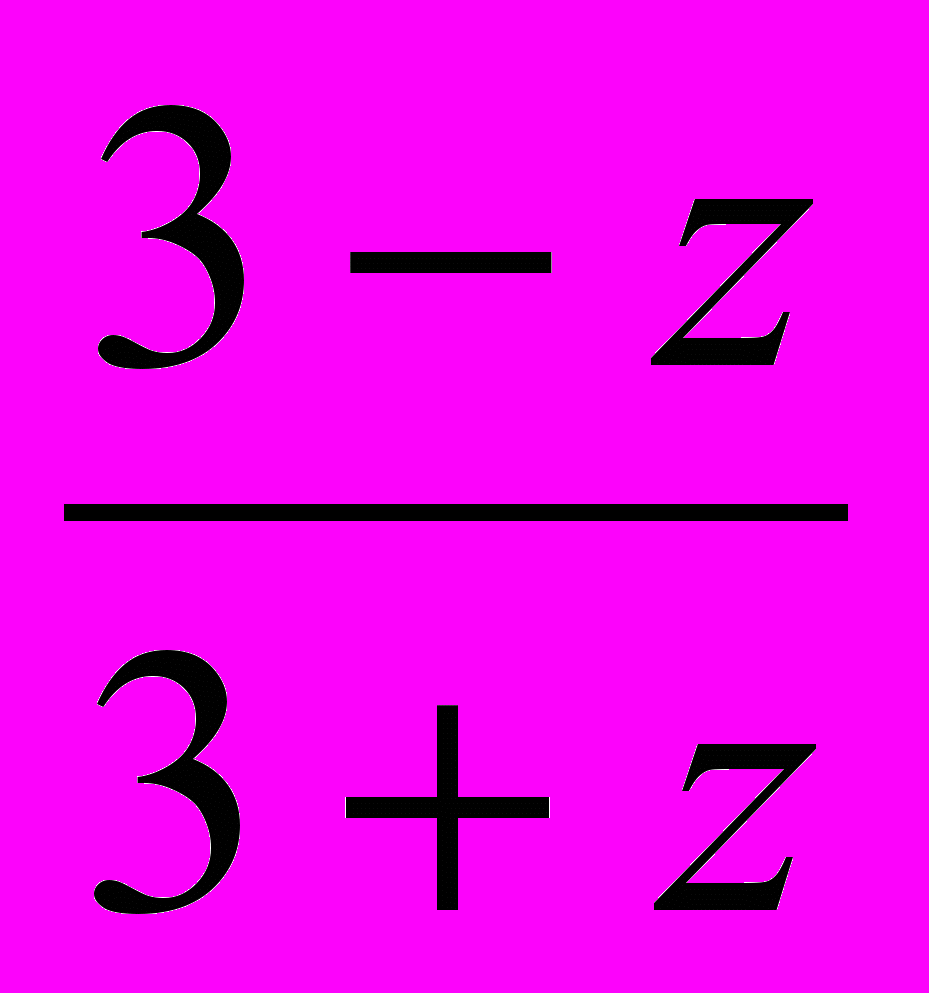
где z – аргумент функции Лапласа, который определяется по ее значению:
Ф0(z)=PΔ-0.5;
где PΔ – вероятность получения зазора в соединении, при 9 степени точности по кинематической норме точности PΔ=0.3.
Ф0(z)=0.3-0.5=-0.2.
По таблице [4] находим z=-0.843.
Nmax=50*
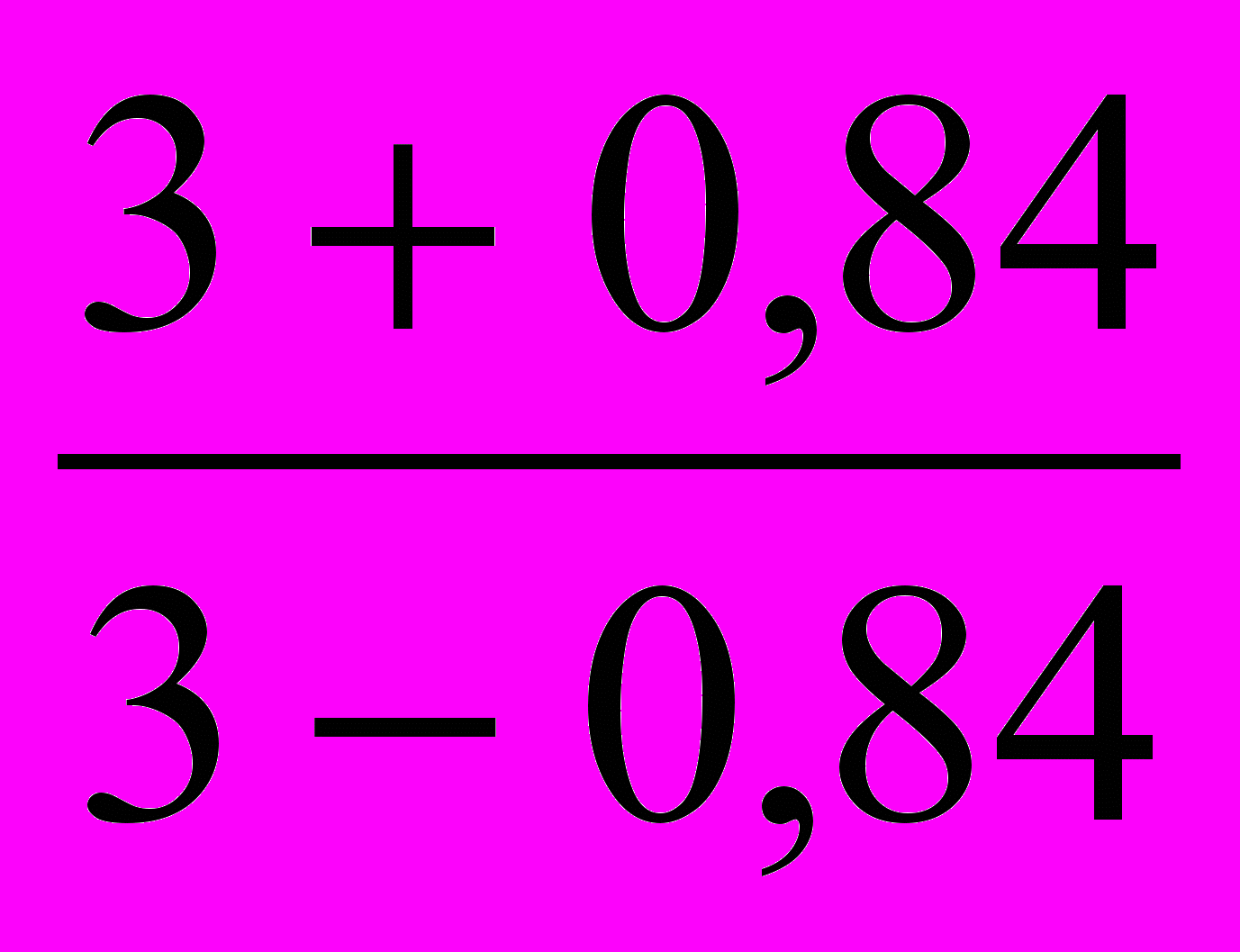
По номинальному диаметру соединения d=70 мм и
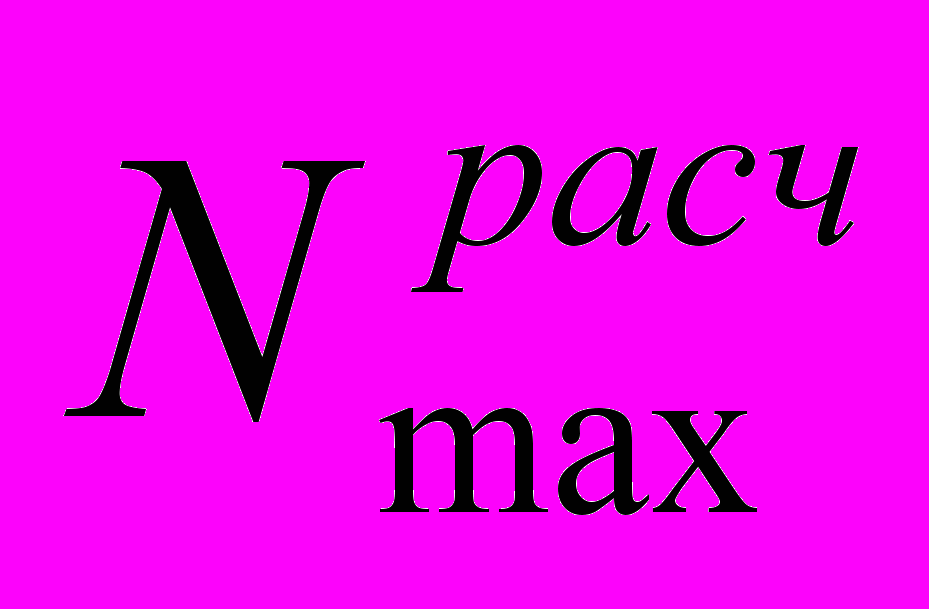

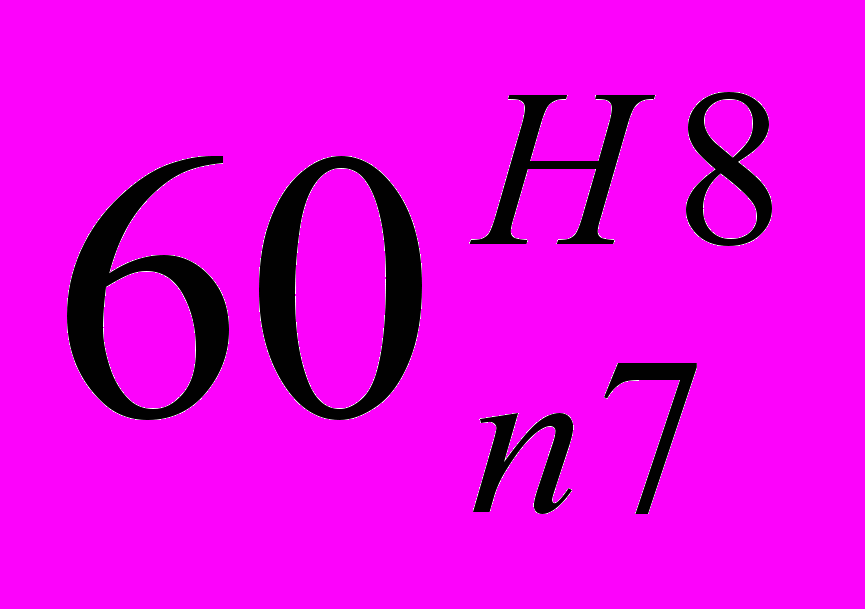
Для обеспечения неподвижности зубчатого колеса с валом применяется призматическая шпонка. Работоспособность шпоночного соединения определяется точностью посадки по ширине шпонки (паза) b.
ГОСТ 23360-78 предусматривает посадки, образующие нормальное, плотное и свободное соединения шпонок с пазами вала и втулки в системе основного вала.
Принимаем нормальный тип соединения. Для нормального соединения установлены поля допусков ширины b для паза на валу N9 и для паза во втулке JS9.Предельные отклонения указанных полей допусков соответствуют ГОСТ 25347-82. Шпонка как основной вал имеет поле допуска h9.
В этом случае посадка в соединении со шпоночным пазом вала будет 70
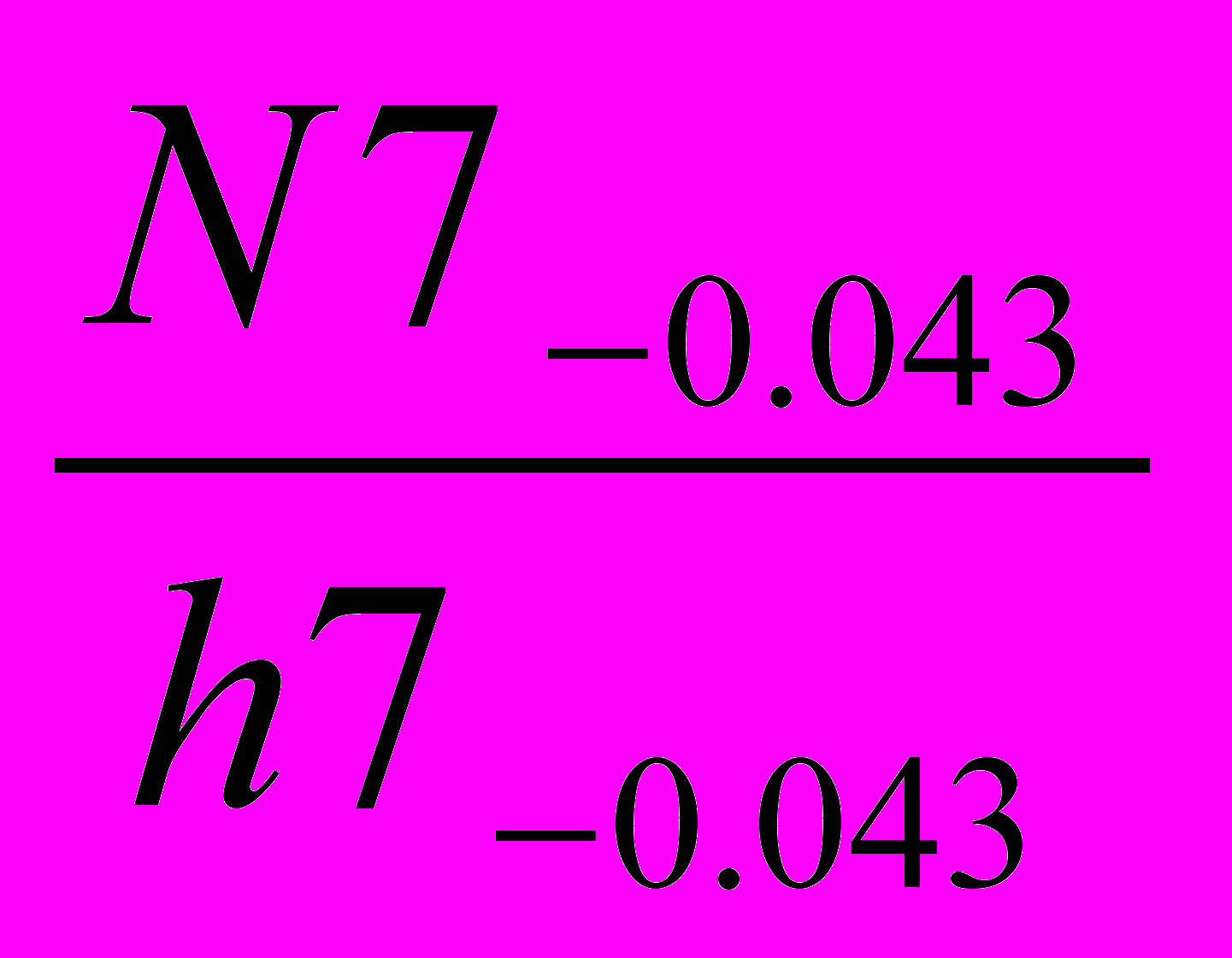
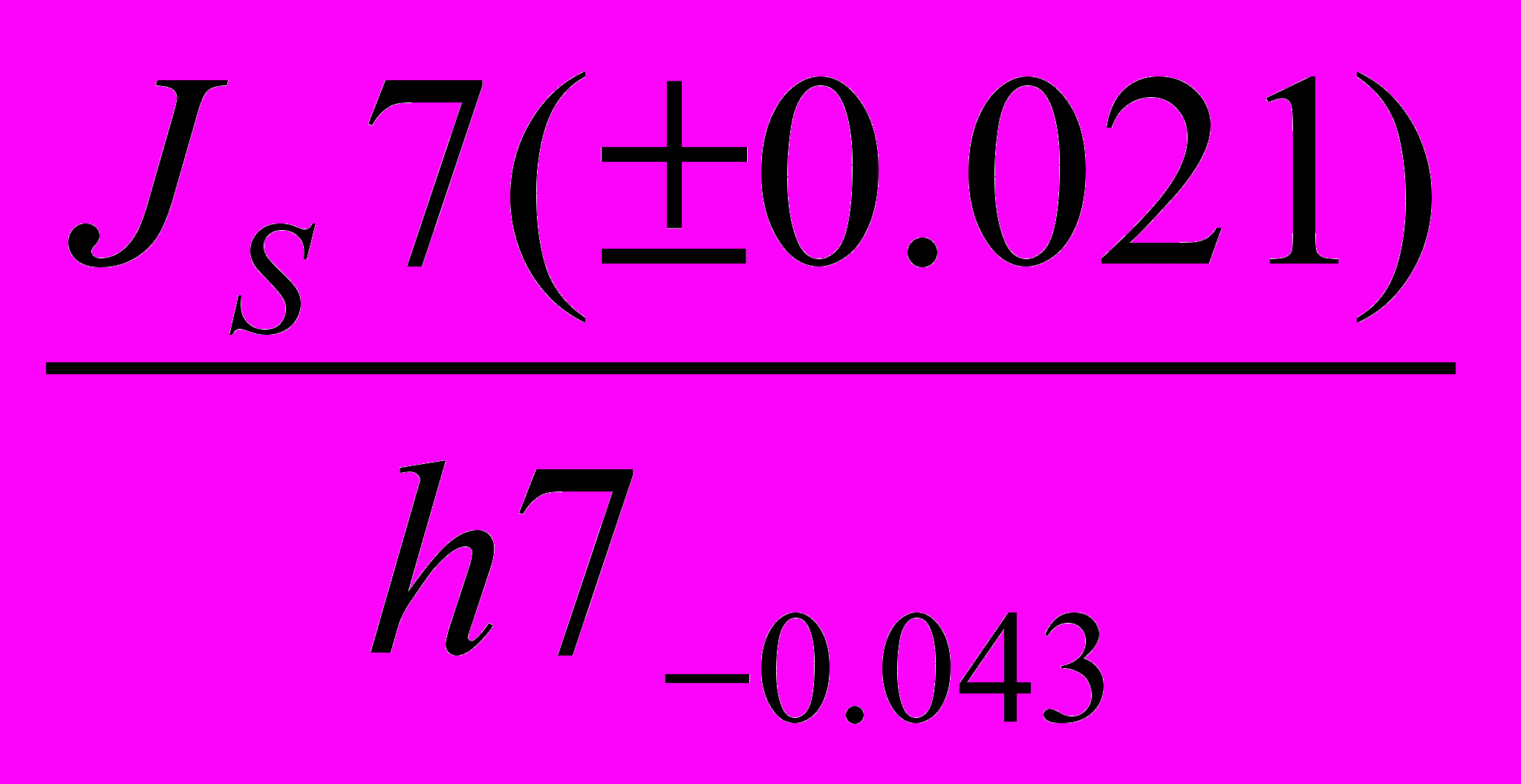
2.2 Расчет калибров
2.2.1 Расчет калибров пробок
Исходные данные:
Отверстие D=70H8+0.046,
Максимальный предельный диаметр отверстия Dmax=70.046,
Минимальный предельный диаметр отверстия Dmin=70.
Калибры для контроля отверстий называются пробками. Калибры изготавливаются комплектом из проходного (ПР) и непроходного (НЕ) калибра. При контроле деталей калибрами, она признается годной, если проходной калибр проходит, а непроходной не проходит через проверяемую поверхность. Допуски на изготовление калибров нормируются по ГОСТ 24853-81.
Для определения предельных и исполнительных размеров пробок из таблицы указанного стандарта находятся численные значения параметров H,y,z,
где H – допуск на изготовление калибра,
z – координата середины поля допуска проходной пробки,
y – координата, определяющая границу износа проходной пробки.
H=5 мкм;
z=4 мкм;
y=3 мкм.
Определяем предельные и исполнительные размеры пробок ПР и НЕ:
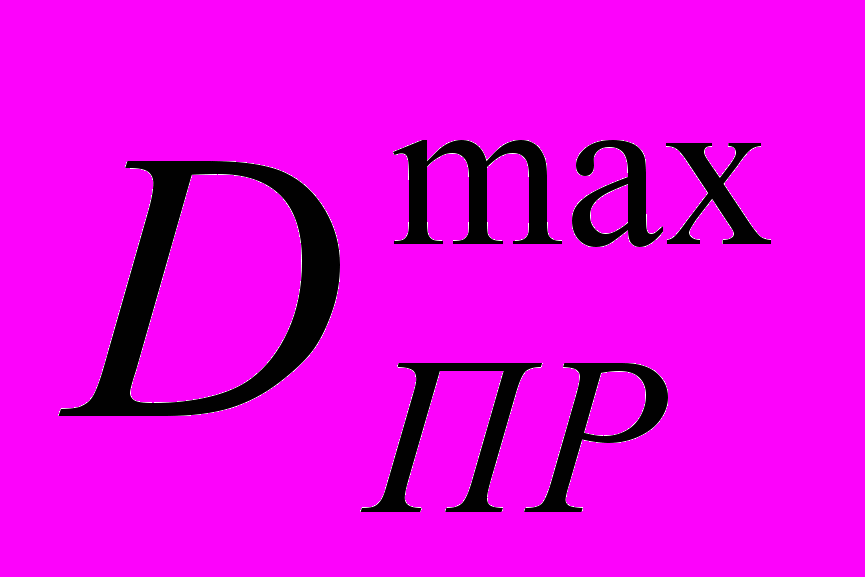
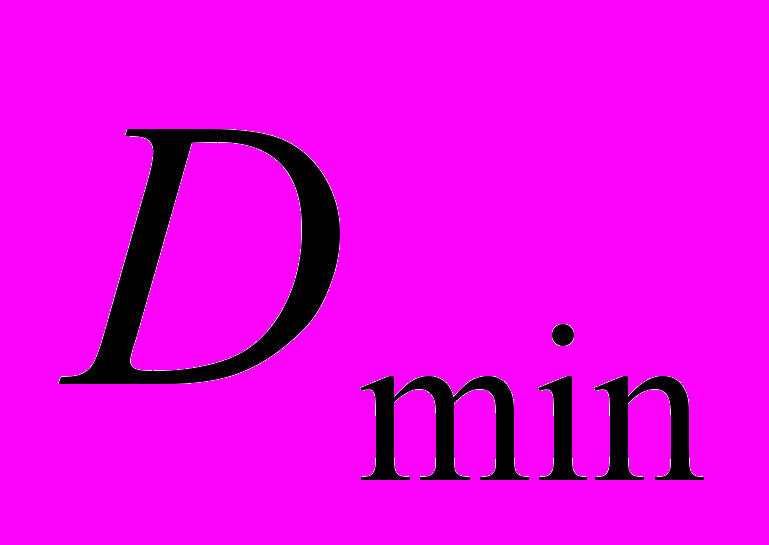
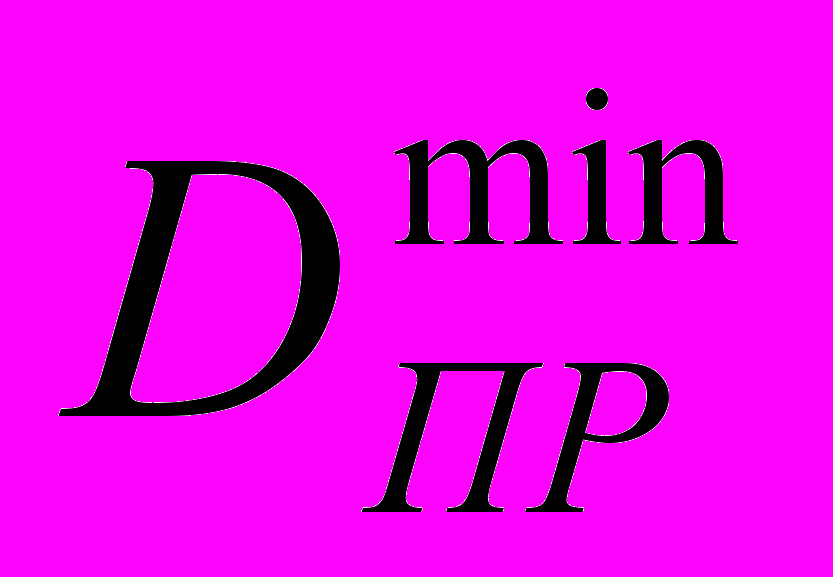
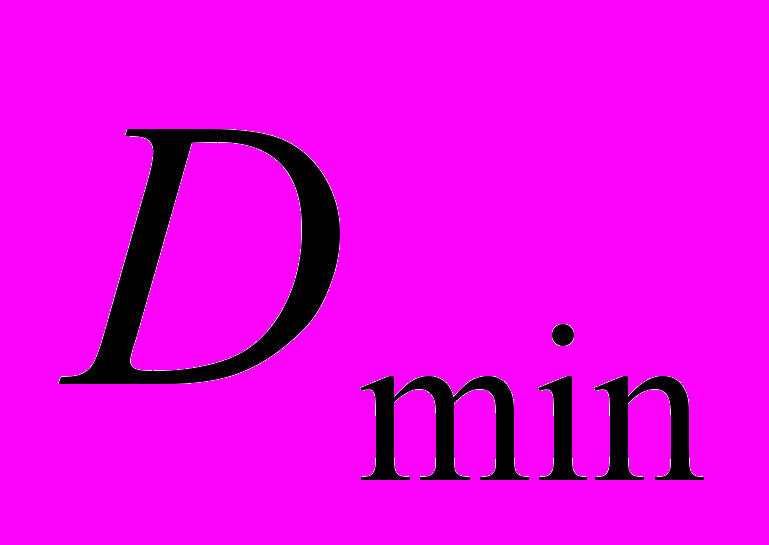
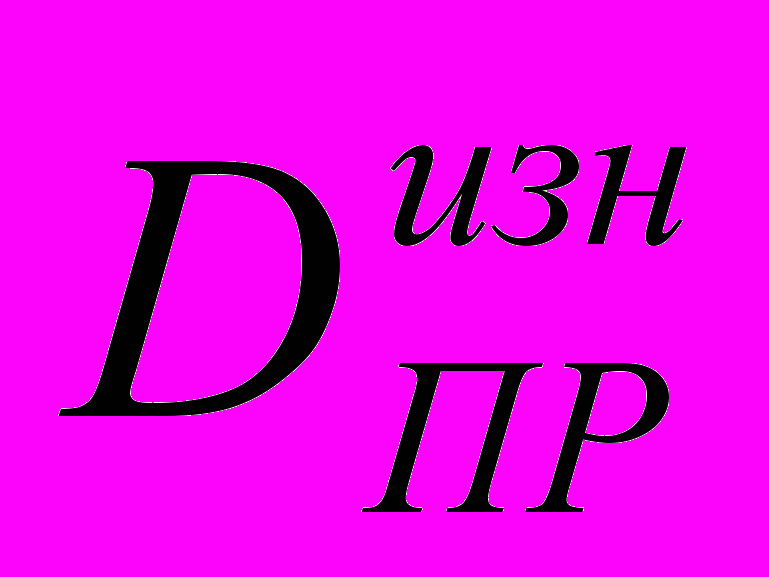
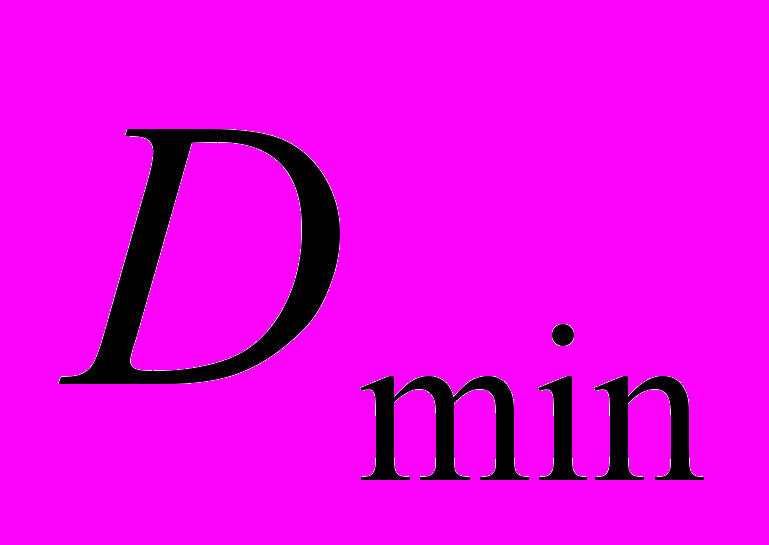
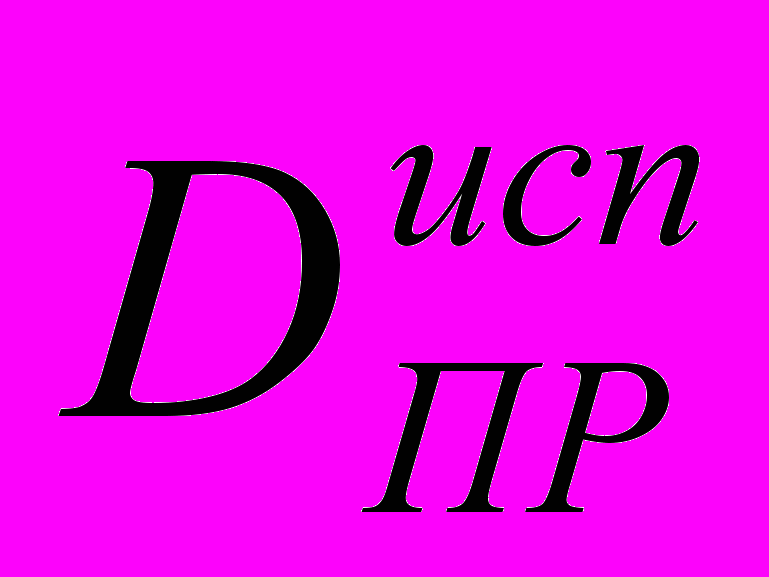
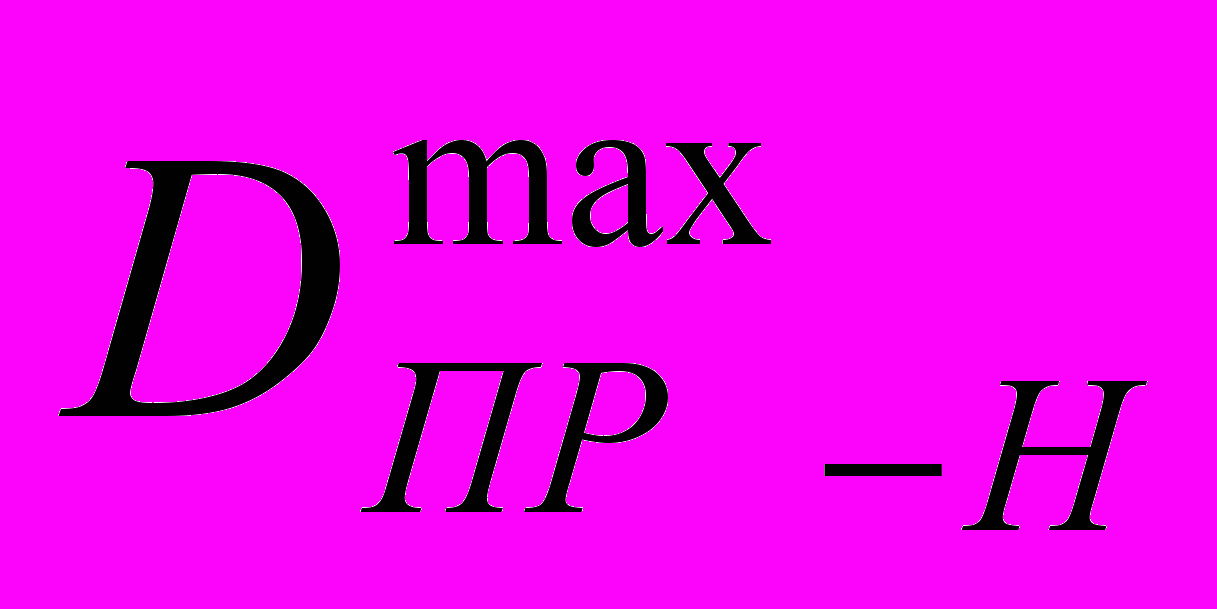
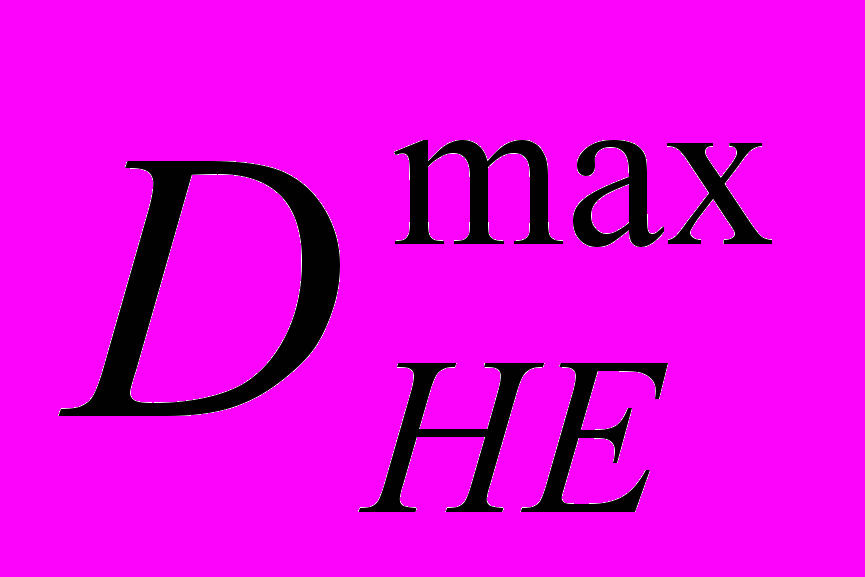
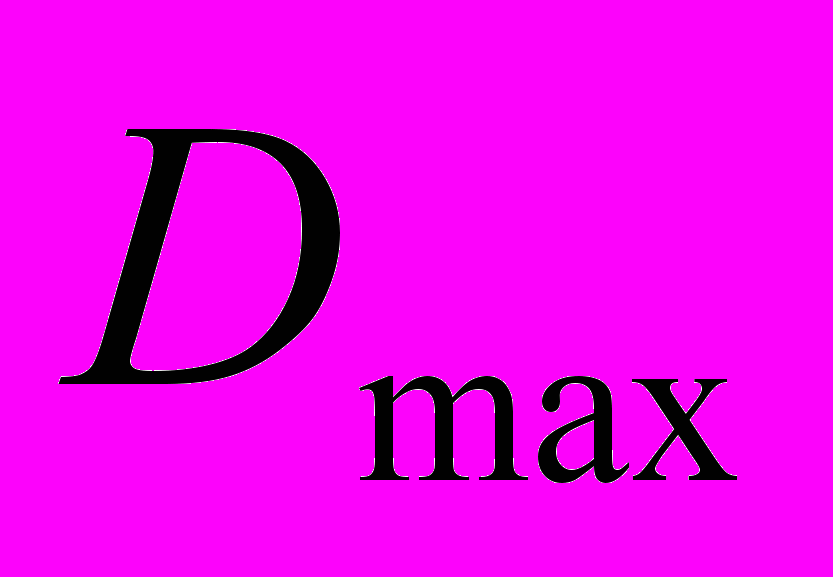
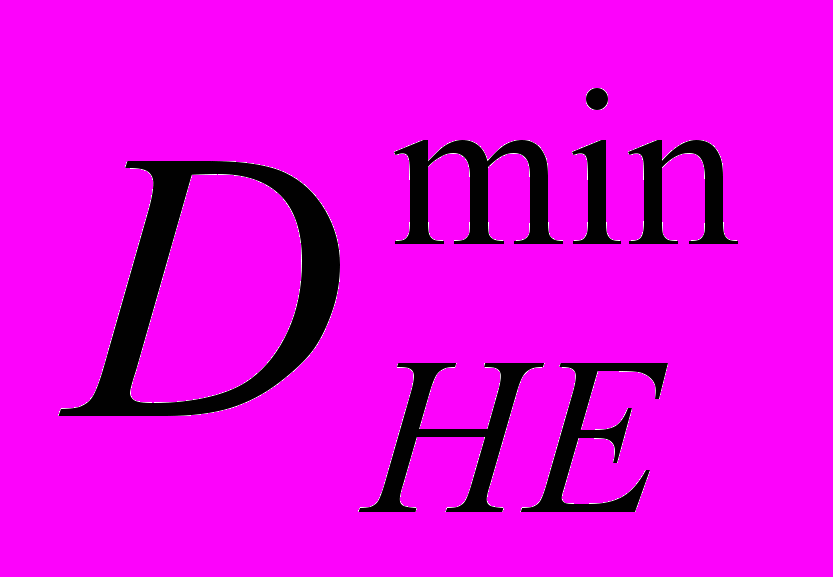
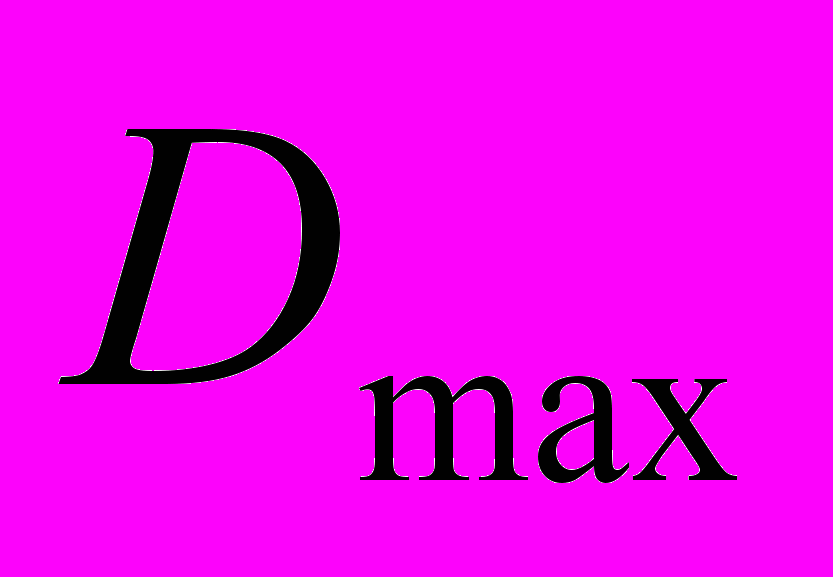
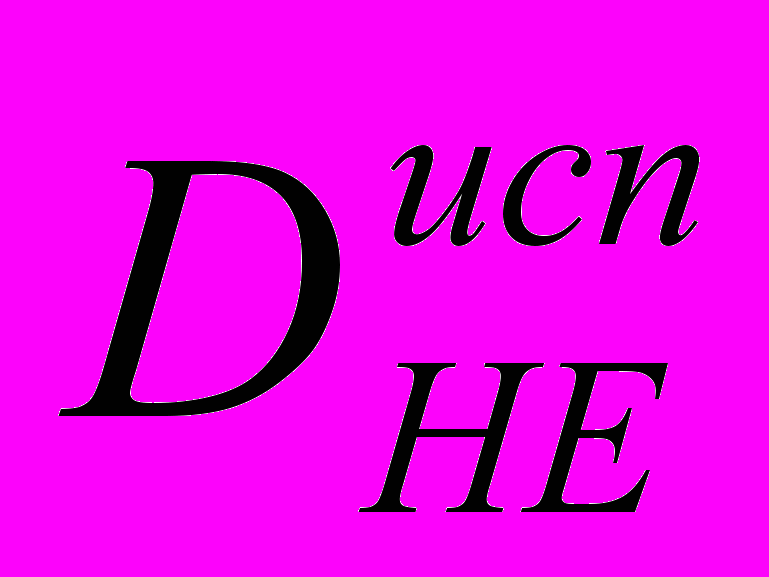
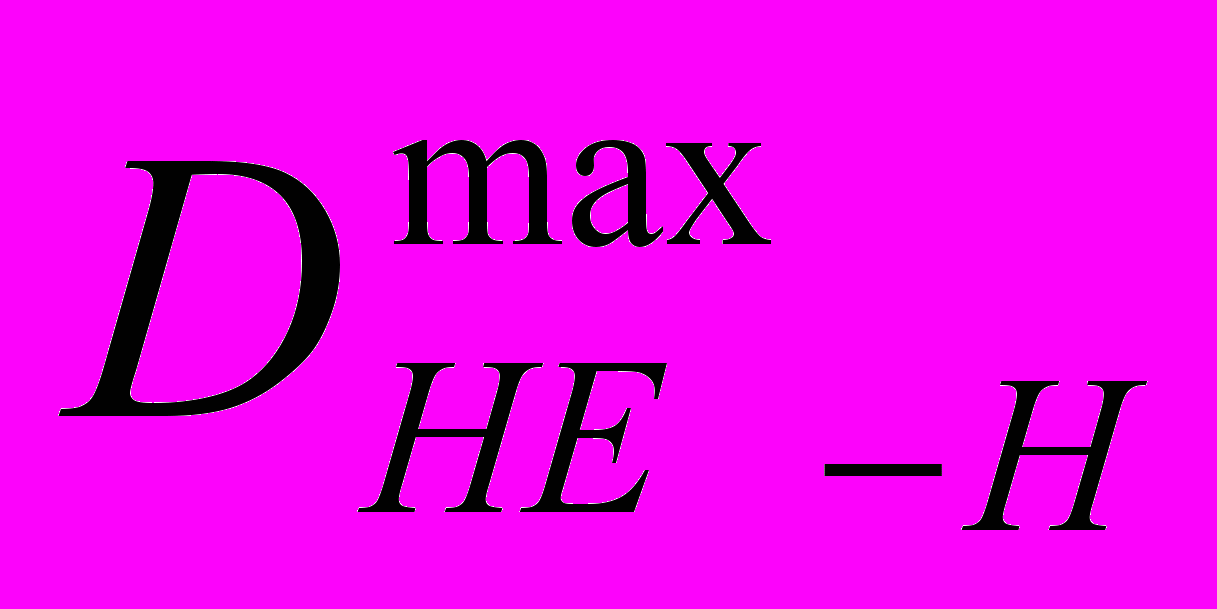
2.2.2 Расчет калибров скоб
Исходные данные:
Вал d=70m6(
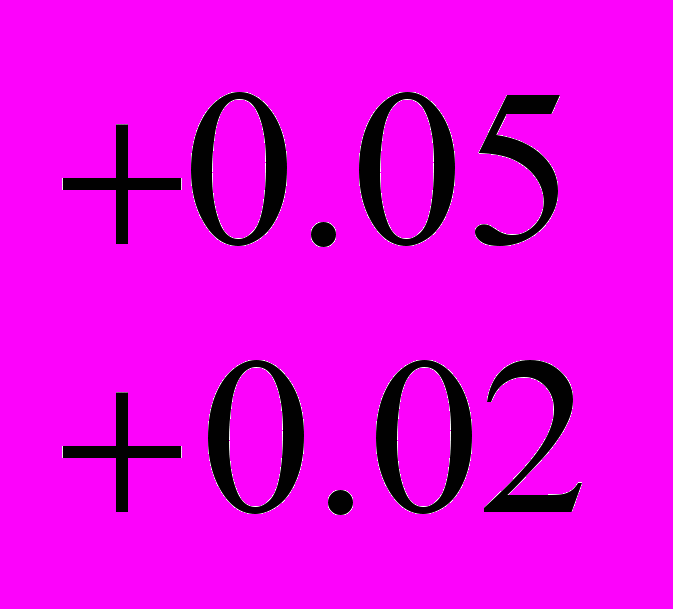
dmax=70.03 мм,
dmin=70.011 мм,
калибры для контроля валов, которые также как пробки имеют проходную и непроходную стороны.
Для определения предельных исполнительных размеров скобы из таблицы ГОСТ 24853-81 выписываем координаты:
H1=5 мкм;
z1=4 мкм;
y1=3 мкм;
Hp=2 мкм.
Определяем предельные и исполнительные размеры скобы ПР и НЕ:
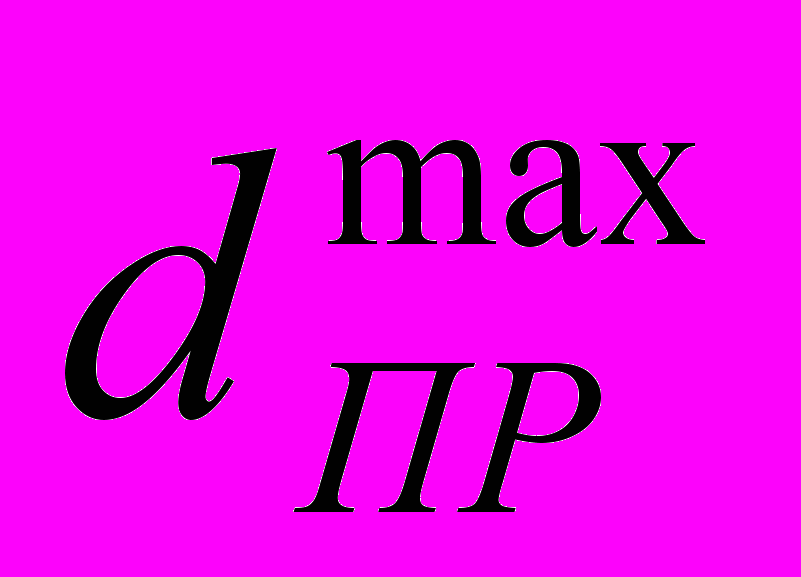
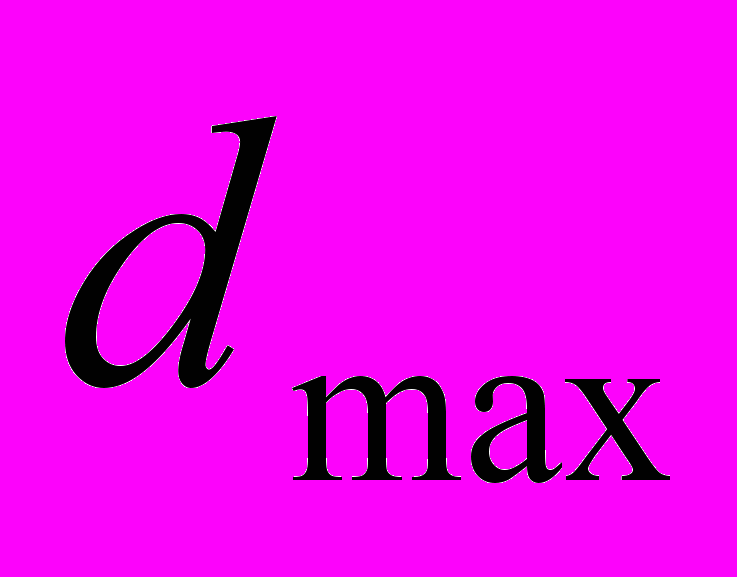
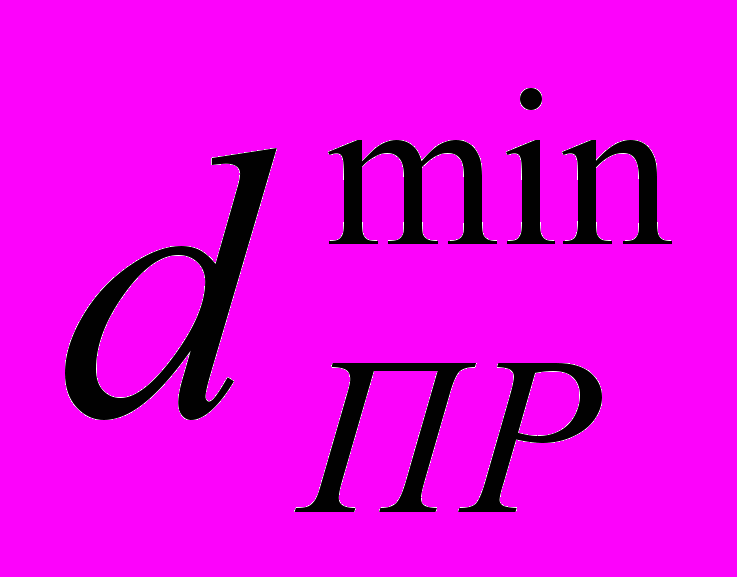
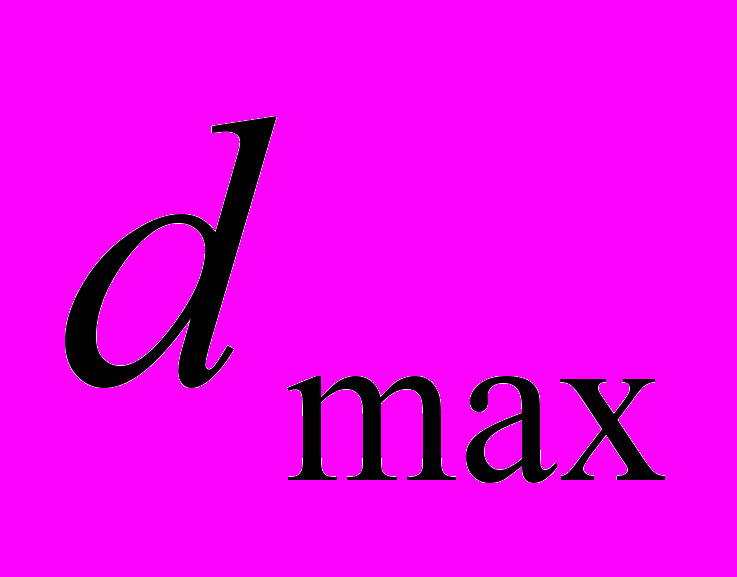
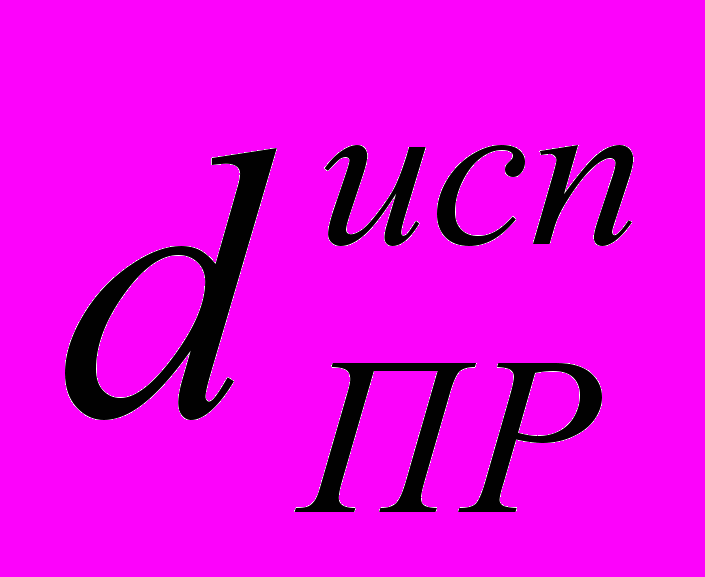
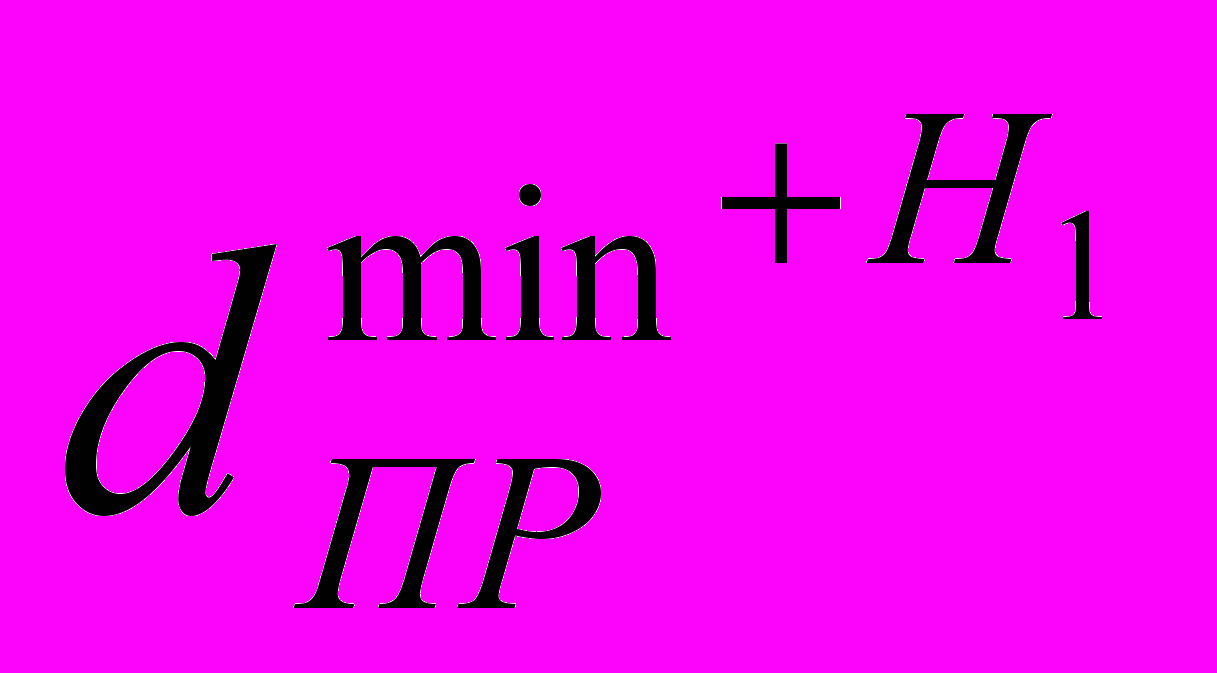
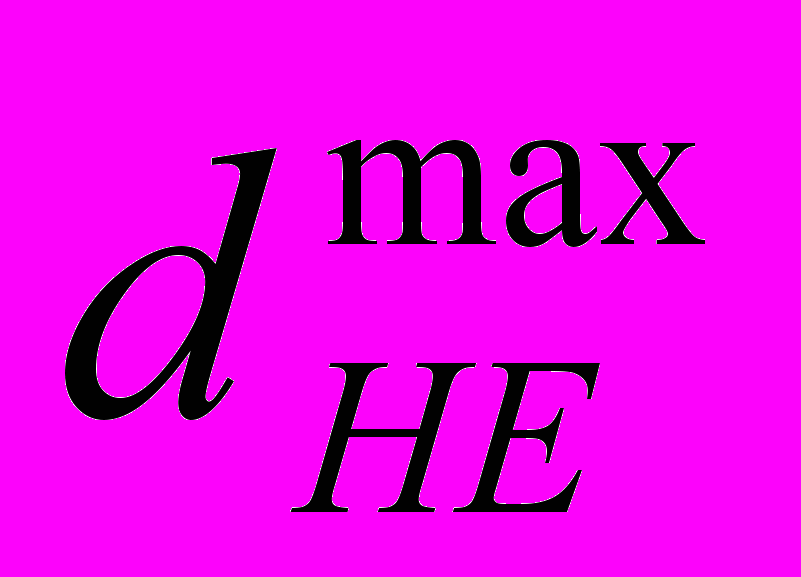
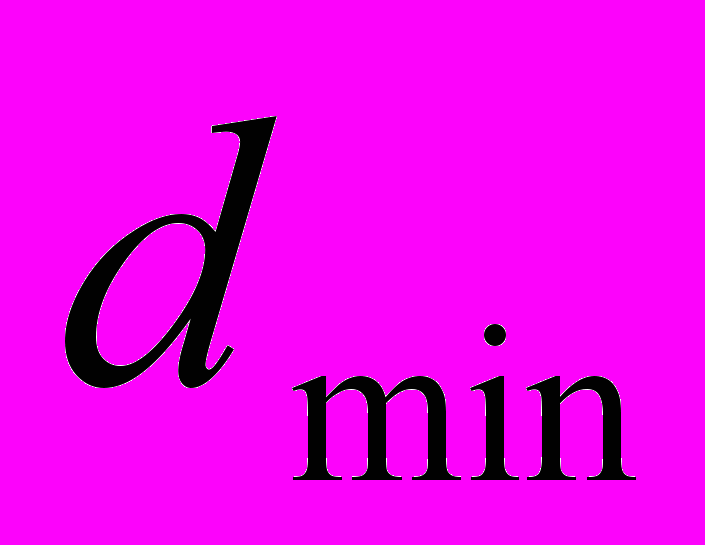
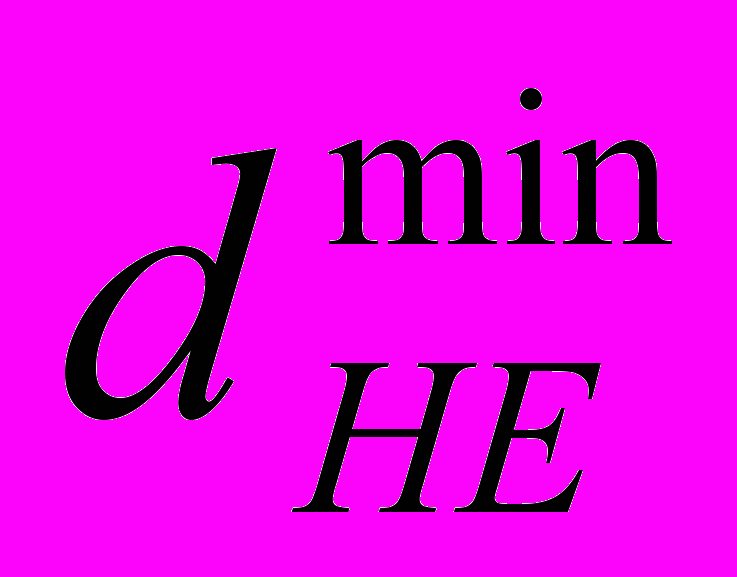
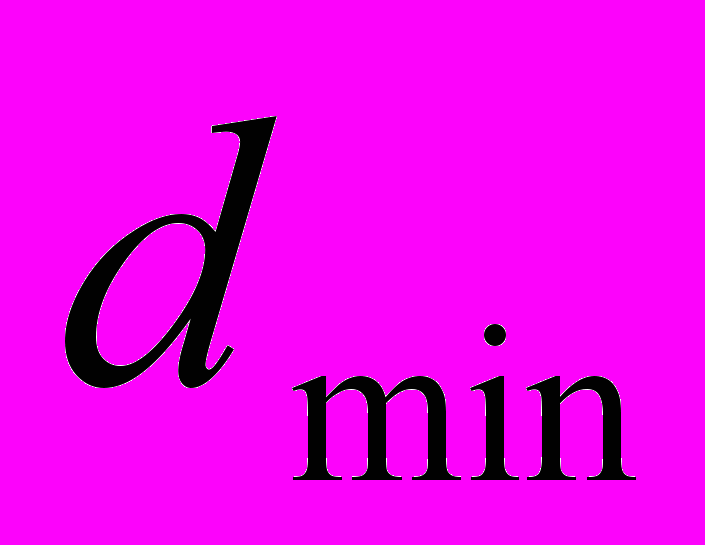
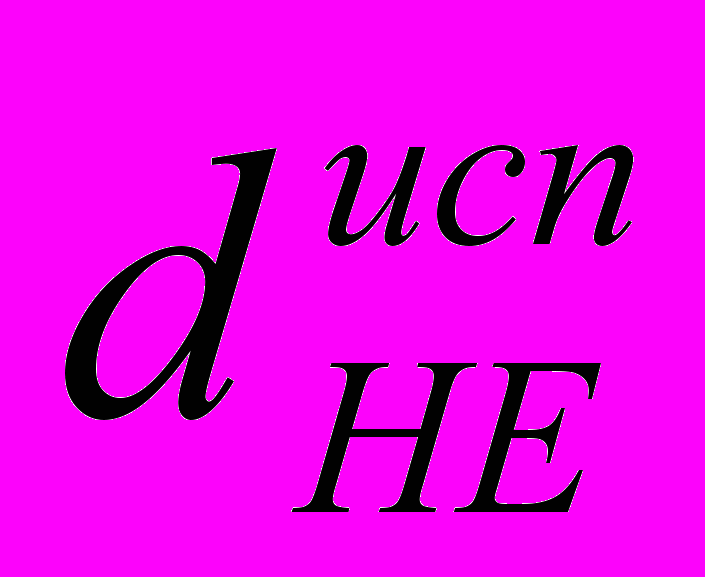
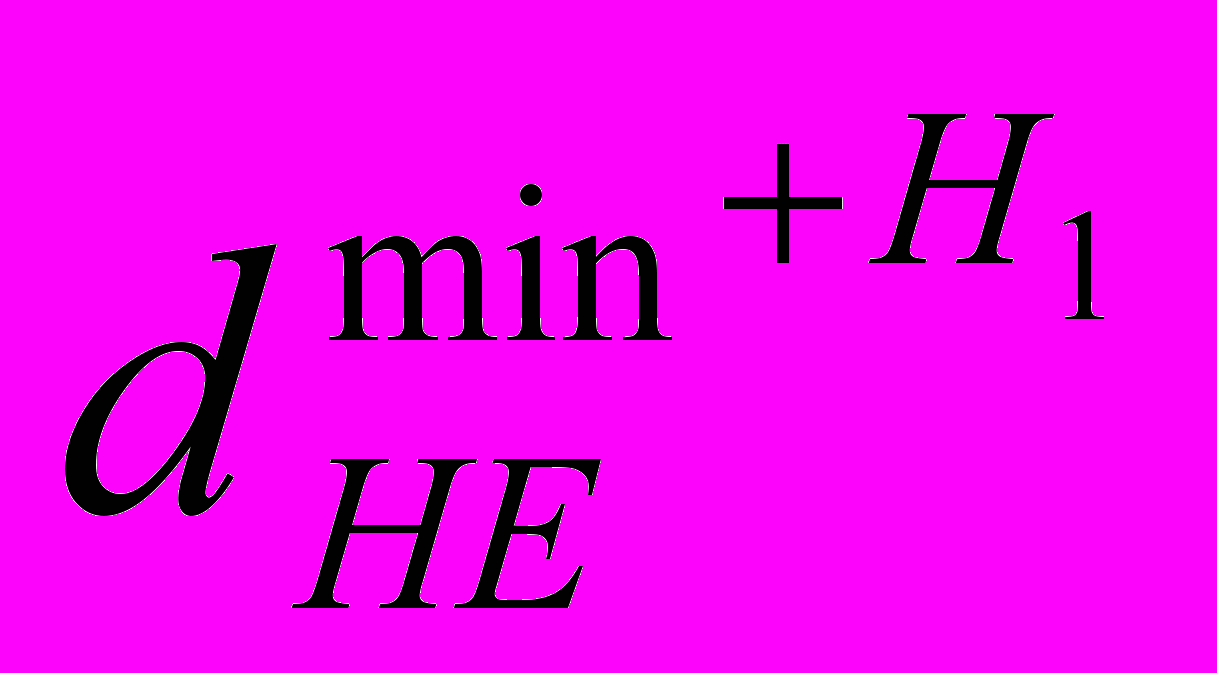
2.3 Расчет и выбор посадок подшипников качения
2.3.1 Расчет и выбор посадок подшипников качения на вал и корпус
Исходные данные:
подшипник №211,
D =110 мм,
d=60 мм,
В=22 мм,
r=2.5 мм,
радиальная нагрузка Fr=6000 Н,
вал вращается, вал сплошной, корпус массивный, нагрузка умеренная.
Посадка внутреннего кольца вала всегда осуществляется в системе основного отверстия, а наружного кольца в корпус – в системе основного вала.
Выбор посадок для подшипников качения зависит от характера нагружения колец. В подшипниковых узлах редукторов кольца испытывают циркулярное и местное нагружения. Внутреннее кольцо подшипника является циркуляционно нагруженным, при котором радиальная нагрузка воспринимается последовательно всей окружностью ее дорожки качения и передается всей посадочной поверхности вала. Наружное кольцо подшипника испытывает внешнее нагружение, при котором постоянная по направлению результирующая радиальная нагрузка воспринимается лишь ограниченным участком окружности дорожки качения и передает ее соответствующему ограниченному участку посадочной поверхности корпуса.
Класс точности подшипников качения для зубчатой передачи выбирается в зависимости от степени точности зубчатой передачи по таблице 3.6 [2]. Степень точности зубчатой передачи 9, тогда класс точности подшипника 6.
Так как в изделии вращается вал, внутреннее кольцо подшипника является циркуляционно нагруженным, наружное кольцо, соединяющееся с неподвижным корпусом, испытывает местное нагружение, следовательно, внутреннее кольцо соединяется с валом по посадке с натягом, наружное кольцо в корпусе – с небольшим зазором.
Посадку внутреннего кольца подшипника на вал определяем по интенсивности радиальной нагрузки Pr, которая определяется по выражению:
Pr=
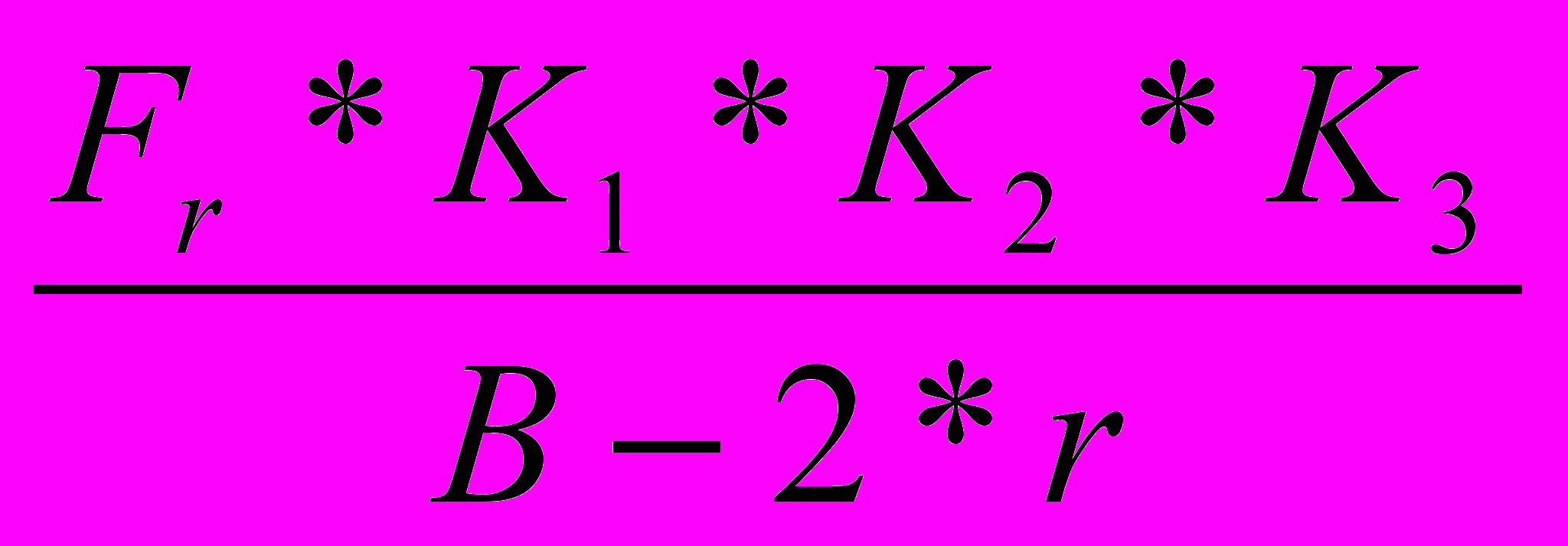
где Fr – радиальная нагрузка на ось,
К1 - динамический коэффициент посадки, при умеренной нагрузке К1=1 по таблице 3.8[2],
К2 – коэффициент, учитывающий степень ослабления натяга, при сплошном вале К2=1,
К3 – коэффициент, учитывающий тип подшипника, для однорядных несдвоенных подшипников К3=1,
B – ширина кольца подшипника, мм,
r – радиус фаски кольца, мм.
Pr=
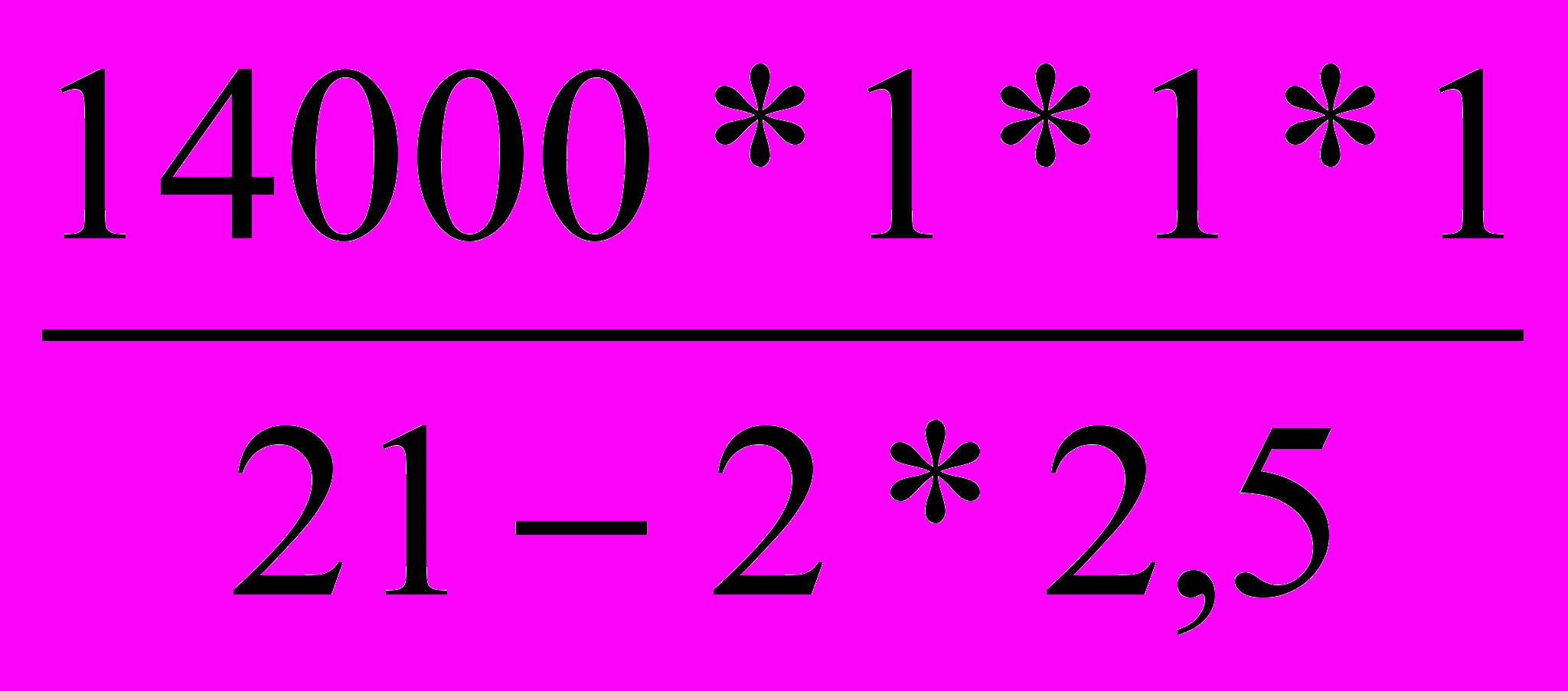
По рассчитанному значению Pr и номинальному диаметру d устанавливаем поле допуска вала k6(
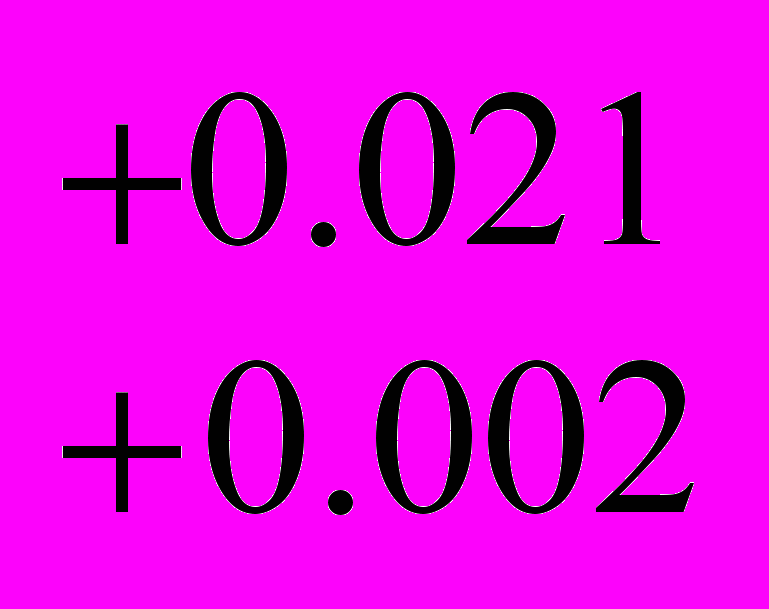
Доле допуска для отверстия в корпусе определяется в зависимости от диаметра D, характера нагрузки и конструкции корпуса по таблице 3.9[2]: H7+0.03.
Квалитет точности для отверстия и вала устанавливается в зависимости от класса точности подшипника. При 6 классе точности подшипника вал обрабатывается по 6, а отверстие по 7 квалитету точности.
Dотв=110H7+0.03;
dвала=60k6(
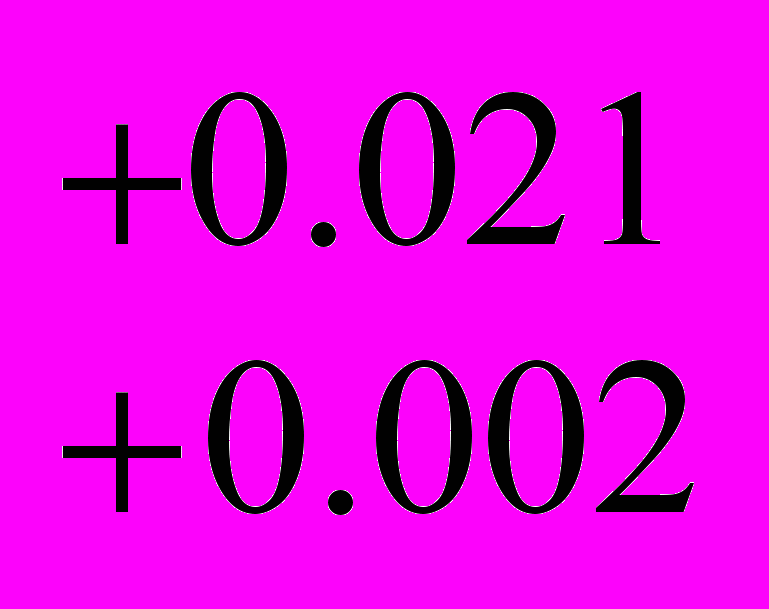
Предельное отклонение для колец подшипника определяется по ГОСТ 520-89:
Dподш=110l6(-0.013);
dподш=60L6(-0.012).
Таким образом, посадка по внутреннему кольцу подшипника Ø60
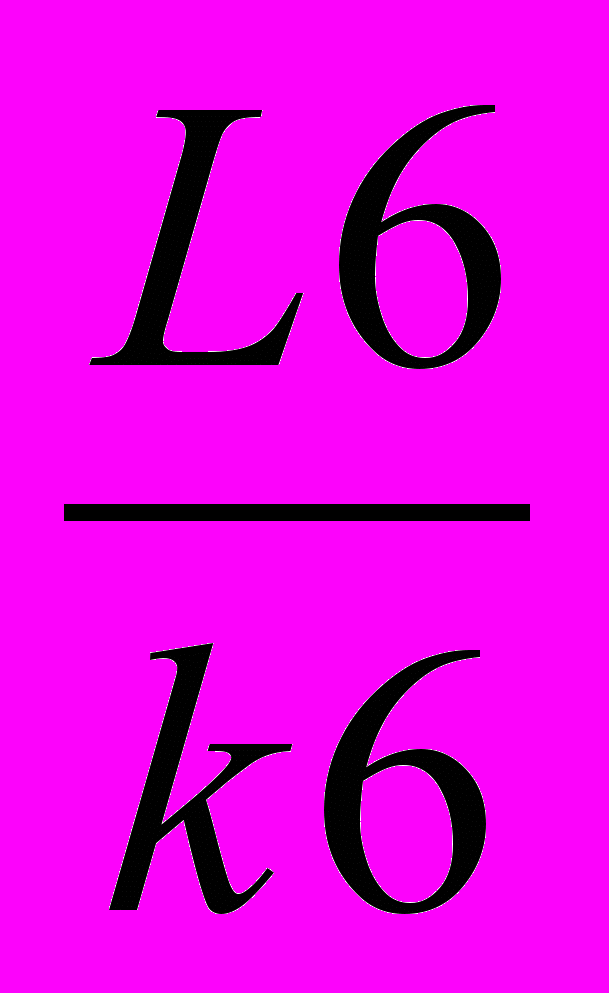
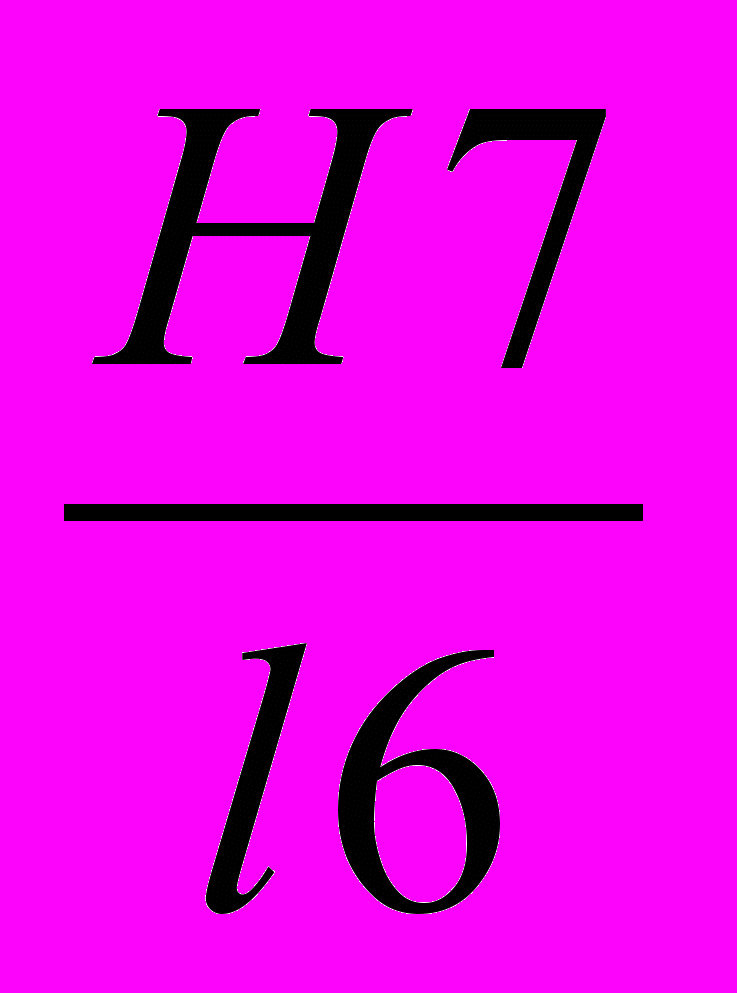
2.3.2 Определение требований к посадочным поверхностям вала и отверстия в корпусе
Требования к посадочным поверхностям вала и отверстия по ГОСТ 3325-85. Шероховатость поверхности определяется по таблице 3, допуски круглости и профиля продольного сечения по таблице 4, допуск торцевого биения опорного торца вала по таблице 5 этого ГОСТа.
Ra в=1.25 мкм;
Rа отв=2.5 мкм;
Rа тор=1.25 мкм;
Tкр в=Tкр пр.сеч.в=5.0 мкм;
Tкр отв=Tкр пр.сеч.отв=9 мкм.
3 Расчет допусков размеров, входящих в размерную цепь
Исходные данные:
сборочный чертеж,
исходное звено АΔ=0+0.95.
Предельные отклонения замыкающего звена:
ESAΔ=+950 мкм; EIAΔ=0 мкм.
Определяем допуск замыкающего звена и координату его середины:
EcAΔ=470 мкм;
TAΔ=ESAΔ- EIAΔ=+950-0=950 мкм.
По сборочному чертежу устанавливаем конструктивно номинальные размеры составляющих звеньев:
А1=11 мм; А2=33 мм; А3=2 мм; А4=31 м; А5=10 мм;
А6=11 мм; А7=17 мм; А8=130 мм; А9=15 мм.
Количество звеньев m =11.
Проверяем правильность определения номинальных значений составляющих звеньев:
AΔ=

AΔ=- А1 - А2 - А3 - А4 - А5 - А6 + А7 + А8 + А9 - А10,
0 = 130 - 11 - 33 - 2 - 31 - 10 - 11 - 17 - 15.
Определяем среднее значение допусков составляющих звеньев:
TAicc=
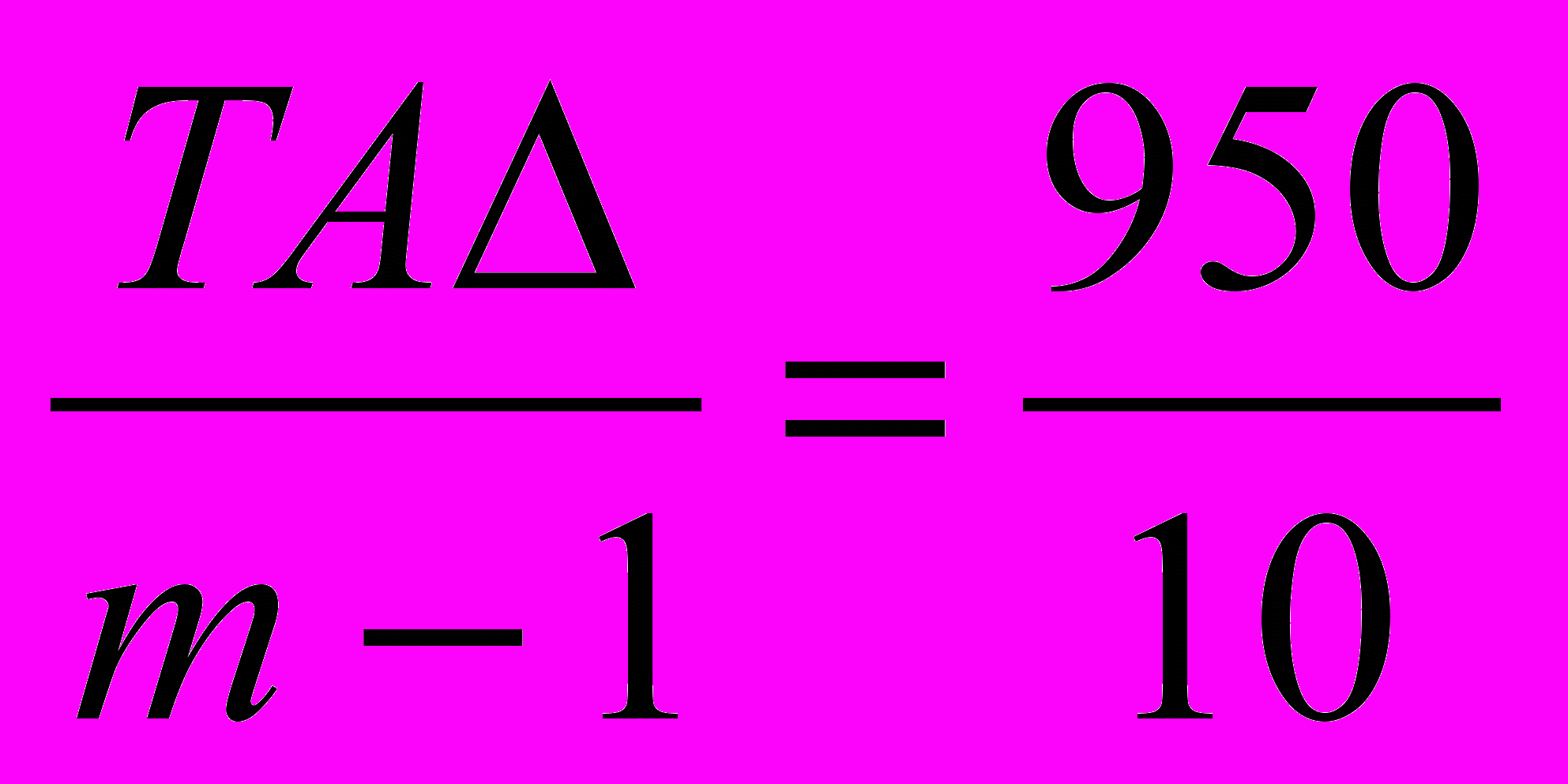
По номинальным размерам составляющих звеньев, используя ГОСТ 25347-82, определяем поля допусков:
TА1=12 мкм; TА2=0.1 мкм; TА3=0.1 мкм; TА4=0.1 мкм;
TА5=0.09 мкм; TА6=0.12 мкм; TА7=0.11 мкм; TА9=0.11мкм.
Определяем поле допуска звена А8:
TAΔ=
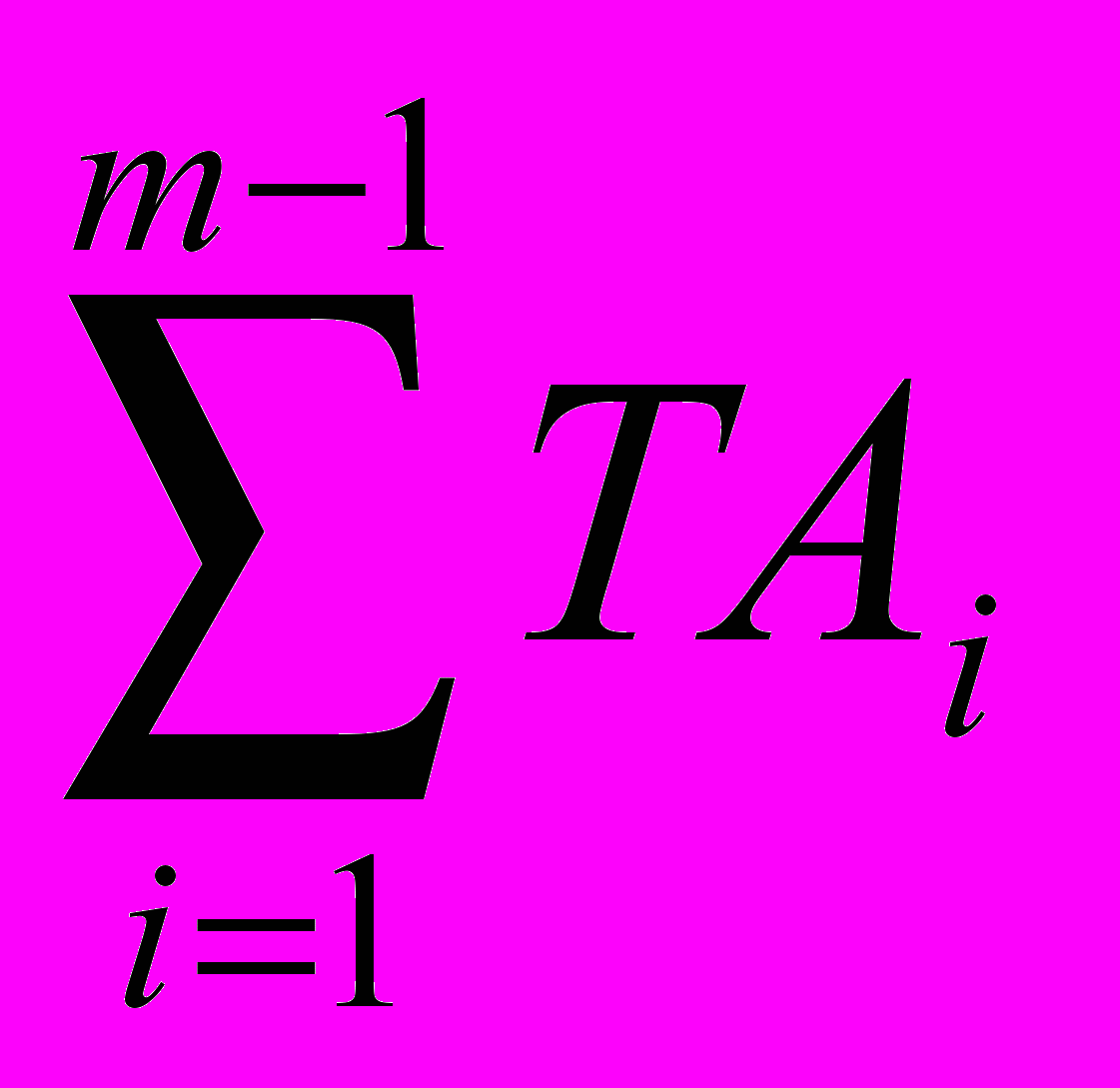
TAΔ= TА1 + TА2 + TА3 + TА4 + TА5 + TА6 + TА7 + TА8 + TА9 + TА10,
0.950 - 0.12 - 0.1 - 0.1 - 0.1 - 0.09 - 0.12 - 0.11 - 0.11= 0.1,
TA8 = 0.1 мкм.
Определяем координаты середин полей допусков составляющих звеньев, кроме одного:
Eci=
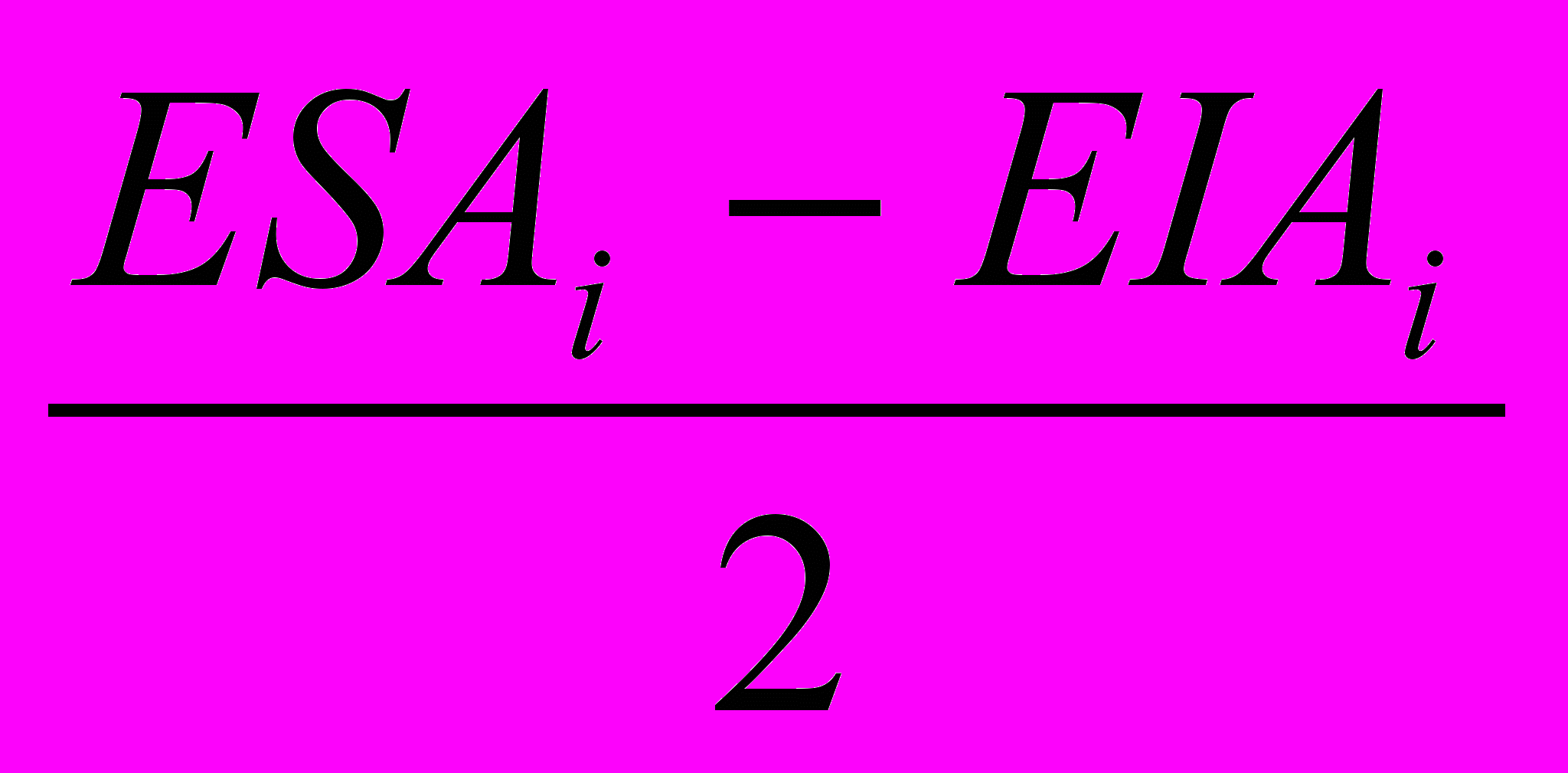
EcA1=-60 мкм; EcA2=-50 мкм; EcA3=-50 мкм; EcA4=-50 мкм;
EcA5=-50 мкм; EcA6=-60 мкм; EcA7=0; EcA9=0.
Определяем координату середины поля допуска оставшегося неизвестного звена:
EcAΔ=
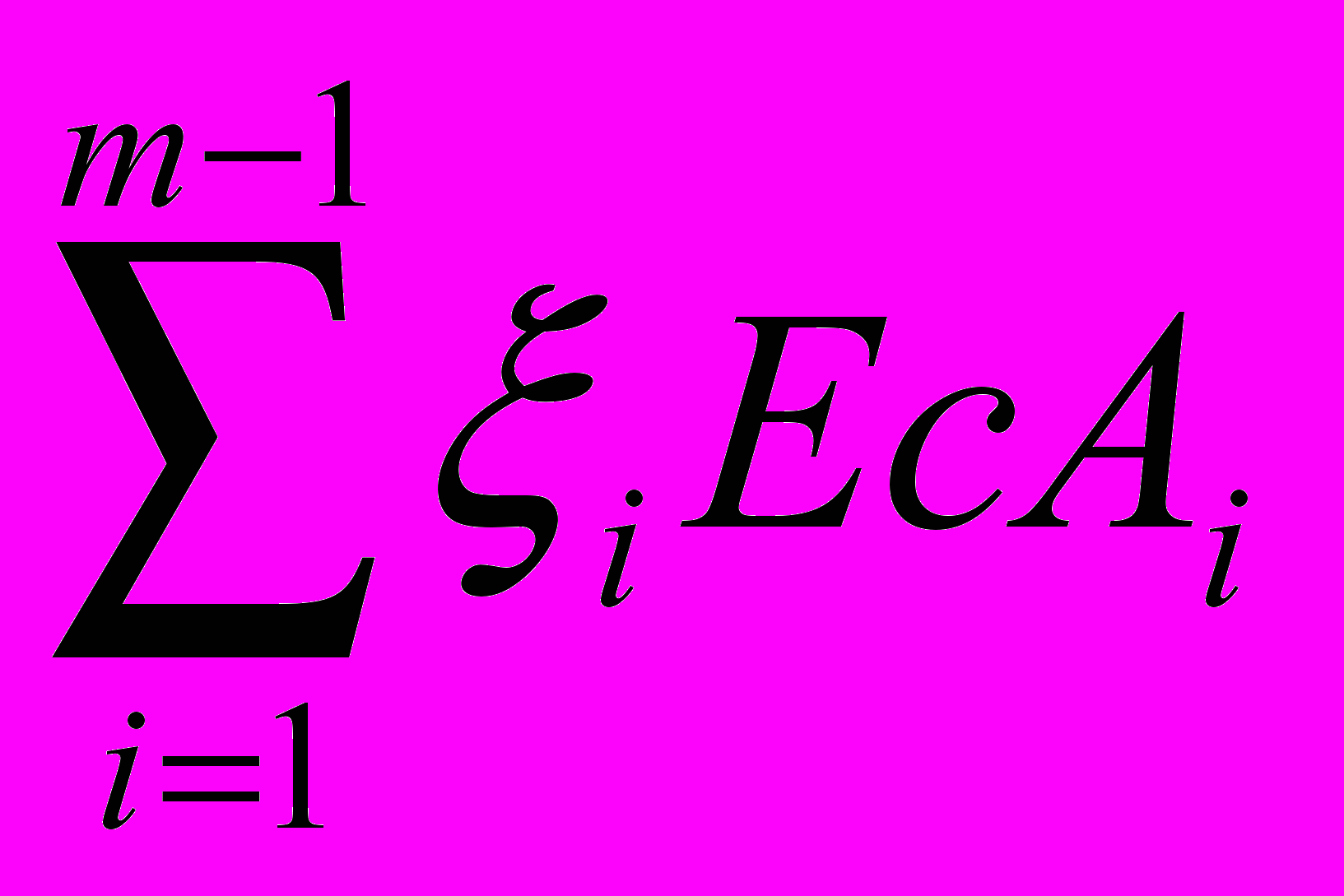
EcAΔ=- EcA1- EcA2- EcA3- EcA4- EcA5- EcA6+ EcA7+ EcA8+ EcA9- EcA10
+0.475= EcA8-(-0.06 - 0.05 - 0.05 - 0.05 - 0.45 - 0.06);
EcA8= 0.16.
Определяем предельные отклонения оставшегося неизвестного звена:
ESA8= EcA8 +
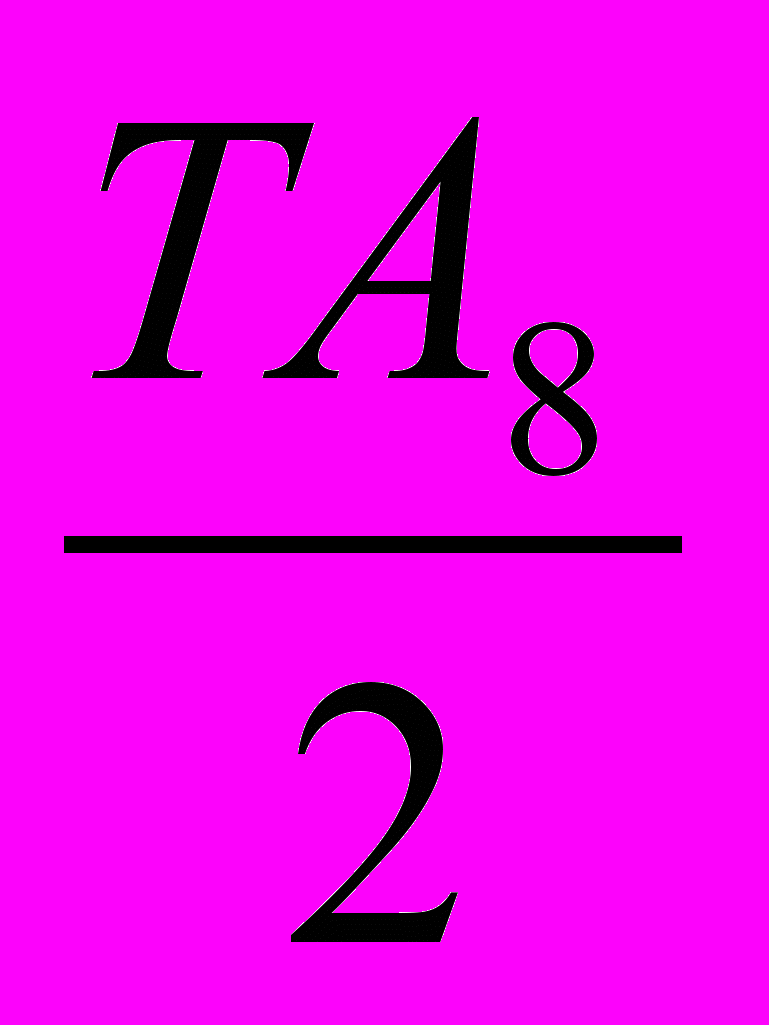
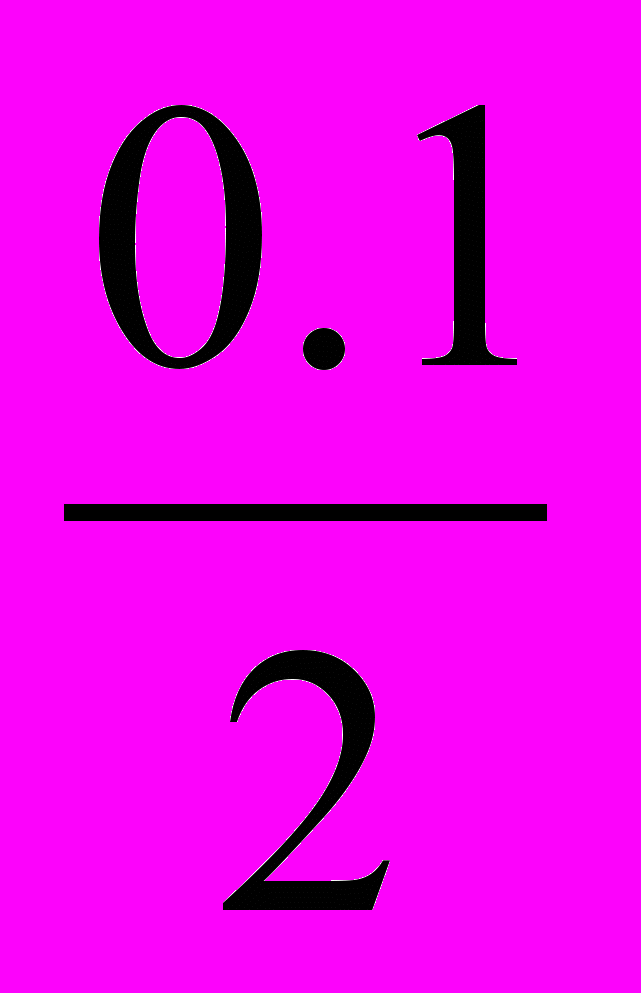
EIA8= EcA8 -
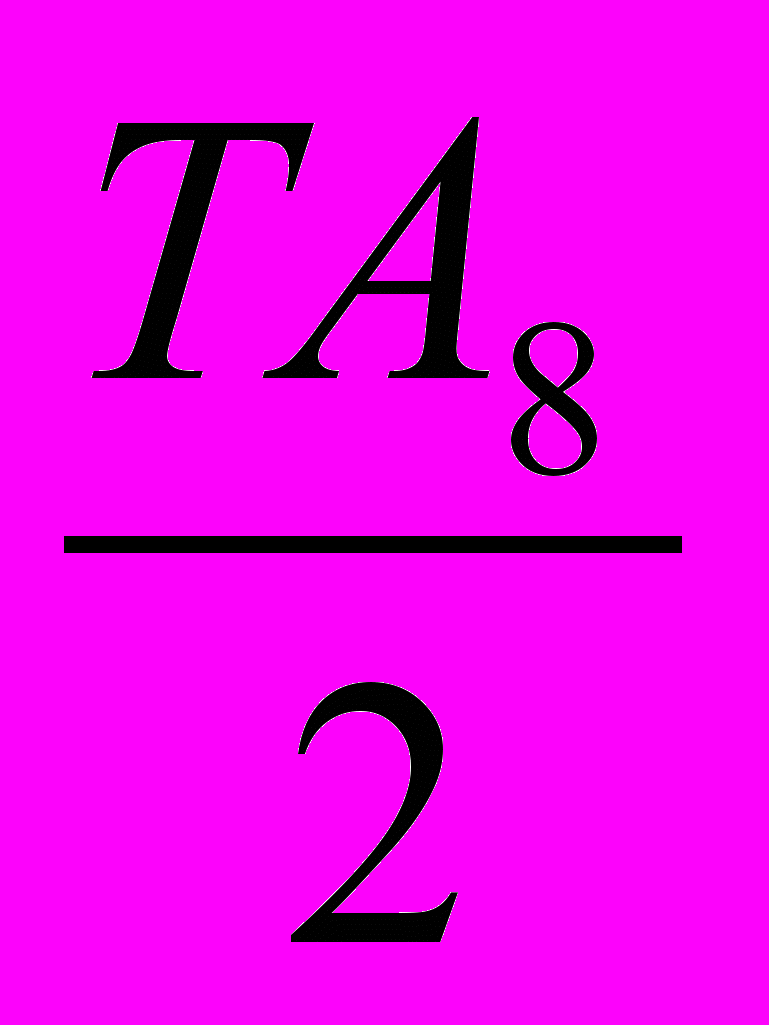
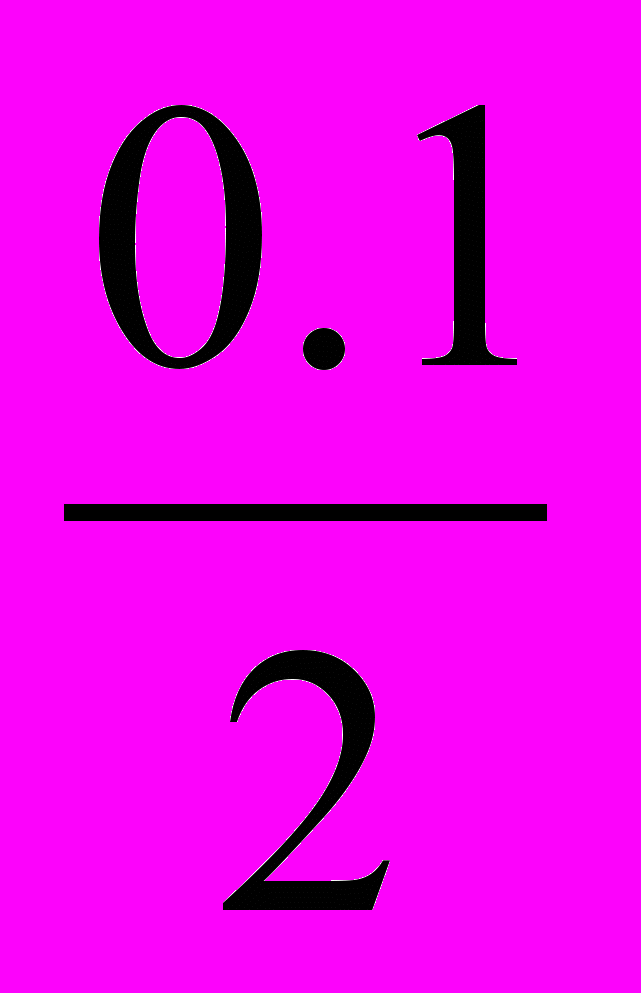
Записываем результаты расчетов:
A8=130
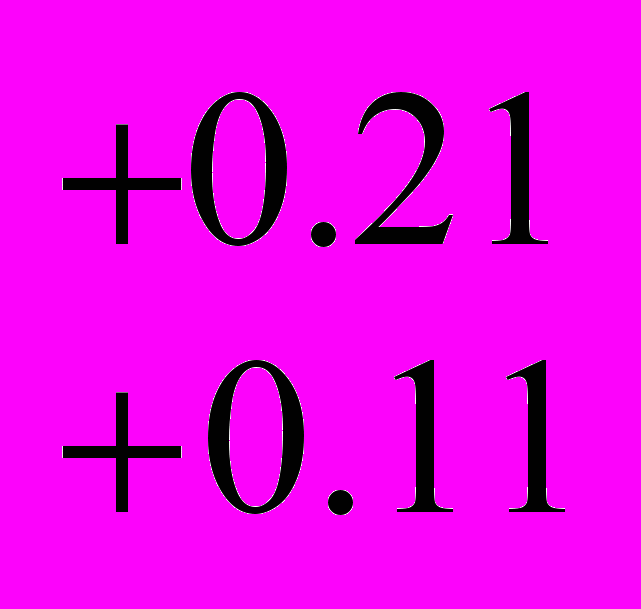
Проверяем правильность расчетов:
ESAΔ=
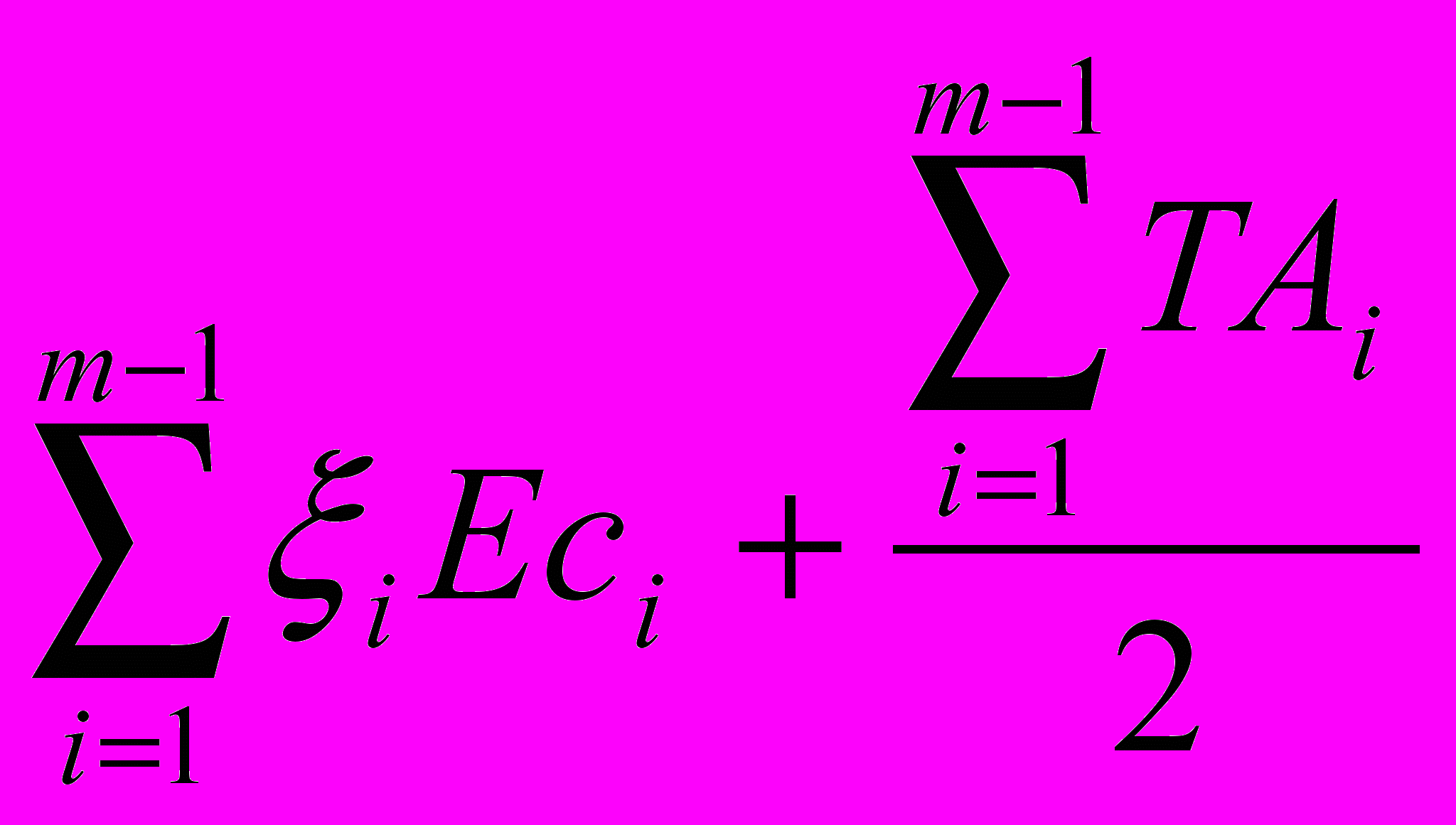
ESAΔ=0.16 – ( -0.06 – 0.05 – 0.05 – 0.05 – 0.45 – 0.06),
ESAΔ= 0.95 мкм.
EIAΔ=
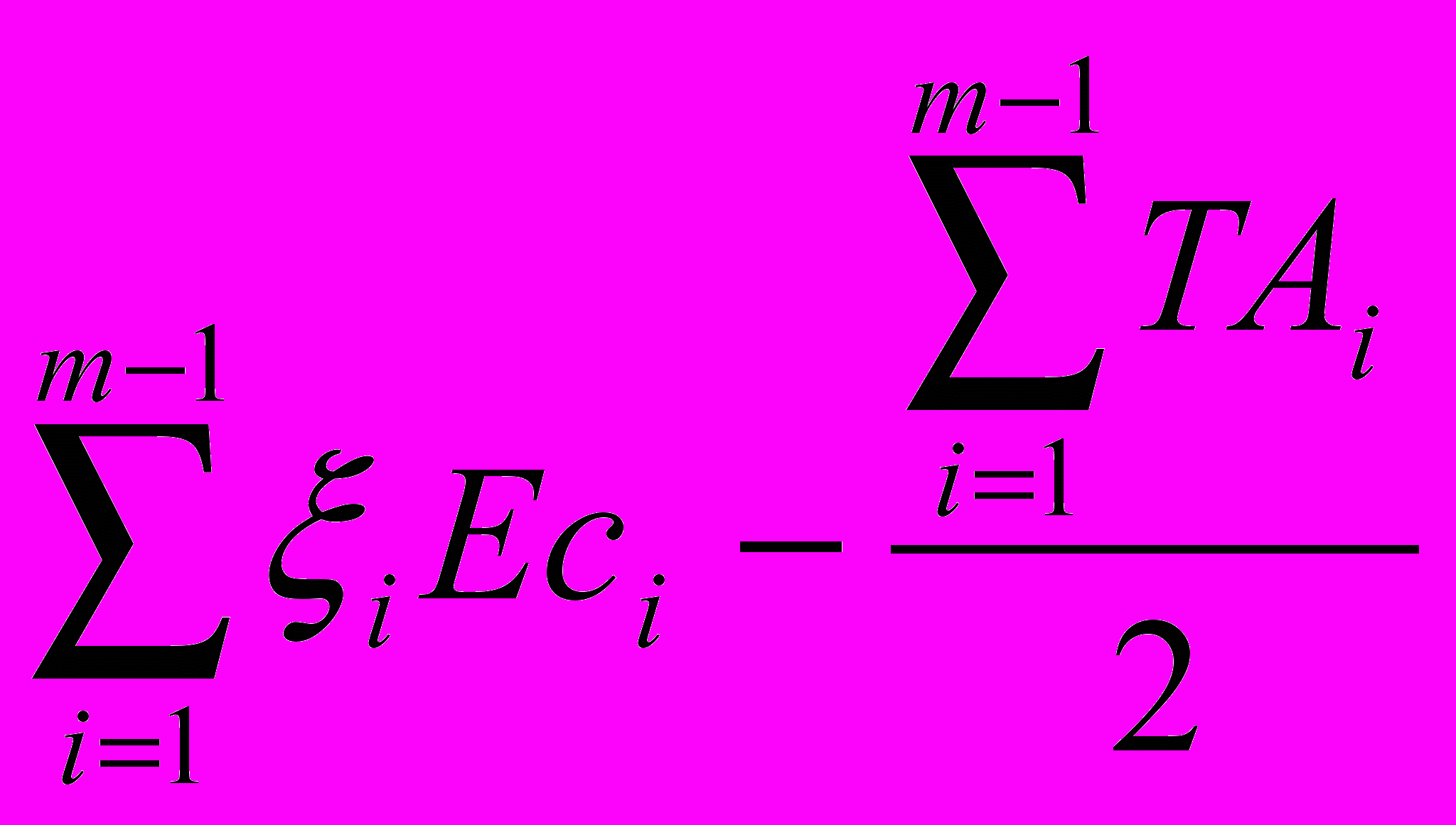
EIAΔ= 0.16 – ( - 0.06 – 0.05 – 0.05 – 0.058 – 0.45 – 0.6) – 0.95/2= 0.16 + 0.315 – 0.475 = 0.
Вывод: расчет выполнен правильно.
Список используемых источников
1 Зябрев Н.Н., Прелман Е.И. – Пособие к решению задач по курсу “Взаимозаменяемость, стандартизация и технические измерения”, - М.: Высшая школа, 1997, 282 с.
2 Курсовое проектирование по курсу “Взаимозаменяемость, стандартизация и технические измерения”, Методические указания в 2-х частях – Могилев, ММИ, 1990.
3 Лукашенко В.А., Шадуро Р.Н. Расчет точности механизма. Учебное пособие по курсу “Взаимозаменяемость, стандартизация и технические изменения” – Могилев, ММИ, 1990
4 Допуски и посадки. Справочник в 2-х ч. /В.Д. Мягков, М.А.. Полей, А.Б.Романов, - Л. Машиностроение, Ленинградское отделение, 1982, 543 с.
5 Якушев А.И. “Взаимозаменяемость, стандартизация и технические изменения”, - М. Машиностроение, 1987г