Определение требований к посадочным поверхностям вала и отверстий корпуса 3 Расчет допусков размеров, входящих в размерную цепь
Вид материала | Реферат |
- Определение требований к посадочным поверхностям вала и отверстия в корпусе 3 Расчет, 165.16kb.
- Состав дипломного проекта специальности “ технология машиностроения, 60.43kb.
- Спецификация, 2544.91kb.
- С. В. Дятченко, Н. С. Овсеев, Н. Х. Лыонг Рассмотрены современные тенденции проектирования, 210.15kb.
- Расчёт параметров зубчатых передаточных механизмов с учётом требований iso, 105.35kb.
- 1. Предварительный расчет поверхности теплообмена, 39.68kb.
- Практическая работа № (заочное отделение) Дисциплина: «Основы экономики», 98.7kb.
- Теоретические вопросы для сдачи допусков к лабораторным работам по курсу «химия нефти», 62.2kb.
- Гост 25379-82. Станки металлорежущие. Диаметры отверстий под инструмент с цилиндрическим, 9.14kb.
- Нормирование точности гладких цилиндрических элементов деталей. Расчет и выбор допусков, 46.36kb.
Содержание
Введение
1 Расчет и нормирование червячной передачи.
1.1 Выбор степеней точности червячной передачи
1.2 Выбор вида сопряжения зубьев колес передачи
1.3 Выбор показателей для контроля червячных колес
2 Расчет и нормирование точности гладких цилиндрических соединений
2.1 Расчет и выбор посадок неподвижного соединения с
дополнительными креплениями
2.2 Расчет калибров
2.2.1 Расчет калибров пробок
2.2.2 Расчет калибров скоб
2.3Расчет и выбор посадок подшипников качения
2.3.1Расчет и выбор посадок подшипников качения на вал и в корпус
2.3.2 Определение требований к посадочным поверхностям вала и
отверстий корпуса
3 Расчет допусков размеров, входящих в размерную цепь
Список используемых источников
Введение
Для развития машиностроения большое значение имеет организация производства машин и других изделий на основе взаимозаменяемости, применение и создание надёжных средств технических измерений и контроля.
В машиностроении созданы и освоены новые системы современных, надёжных и эффективных машин для комплексной автоматизации производства, что позволяет выпускать продукцию высокого качества с наименьшими затратами труда. В настоящее время непрерывно совершенствуются конструкции машин и других изделий, технология и средства их производства и контроля. Расширяется внутриотраслевая и меж-
отраслевая специализация на основе унификации и стандартизации изделий, широко используются методы комплексной опережающей стандартизации, повсеместно внедряются системы управления и аттестации продукции, а также система технологической подготовки производства.
- Расчет и нормирование червячной передачи.
- Выбор степеней точности червячной передачи
- Выбор степеней точности червячной передачи
Исходные данные
Число зубьев шестерни z1 = 44
Межосевое расстояние передачи a =120 мм
Модуль m = 5 мм
Делительный диаметр колеса d = 220 мм
Окружная скорость v = 4,6 м/c
Ширина зубчатого венца b =52 мм
Система допусков червячных передач (ГОСТ 3675-81) устанавливает 12 степеней точности червячных колес.
Степень точности проектируемого червячного колеса устанавливается в зависимости от окружной скорости колеса. По таблице 2.1 [2] исходя из Vокр=4,6 м/с для червячных колес выбираем 8 степень точности по норме плавности. Используя принципы комбинирования норм по различным степеням назначаем 8 степень точности по кинематической норме, а по норме полноты контакта на 1 степень точнее…
- Выбор вида сопряжения зубьев колес передачи.
Вид сопряжения передачи выбирается по величине гарантированного бокового зазора.
Боковой зазор – зазор между нерабочими профилями зубьев, который необходим для размещения смазки, компенсацией погрешностей при изготовлении, при сборке и для компенсации изменения размеров от температурных деформаций.
Величину бокового зазора, необходимую для размещения слоя смазки ориентировочно можно определить по зависимости
jn min расч.=V= 0,02*m (для тихоходной передачи)
По рассчитанной величине jn min расч.=0,1 мм в зависимости от межосевого расстояния aw=120 мм из таблицы 17 Гост 3675-81 выбираем вид сопряжения B, причем выполняется условие
jnminтабличное
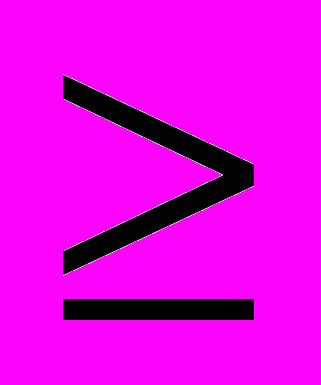
0,1
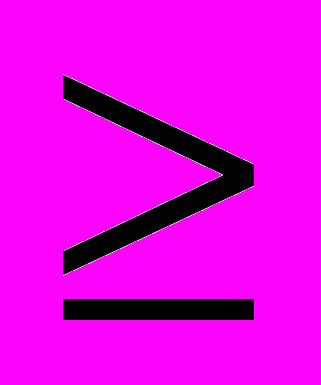
Тогда степень точности червячного колеса будет записана 8B
- Выбор показателей для контроля червячных колес.
Выбор показателей для контроля червячного колеса производятся согласно рекомендациям [2] по таблицам 2,3,5 ГОСТ 3675-81, а по таблицам 6,8,22 этого же ГОСТа назначаем на них допуска.
Средства для контроля показателей выбираем по таблице 6 с 400-405 [5]. Результаты выбора сводим в таблицу 1.
Таблица 1 – Показатели и приборы для контроля червячных колес
Норма точности | Наименование и условное обозначение контролируемого параметра | Условное обозначение и численное значение допусков, мкм | Наименование и модель прибора |
1 Кинематическая точность | колебание измерительного межосевого расстояния за один оборот колеса ![]() Погрешность обката ![]() | ![]() Fc=50 | межцентромер МЦ400Б Прибор для автоматическо- го измерения кинематичес- кой погрешнос- ти зубофрезер- ных станков КН-6М |
2 Норма плавности работы | Колебание измерительного межосевого расстояния на одном зубе ![]() | ![]() | межцентромер МЦ400Б |
3 Норма полноты контакта | Суммарное пятно контакта | по высоте не менее 40% по длине не менее 50% | Контрольно-обкатной станок |
4 Боковой зазор | Верхнее Ess и Ts’ нижнее отклонения измерительного межосевого расстояния за один оборот колеса | Ess=330 Ts’=140 | Зубомер хордовый ЗИМ-16 |
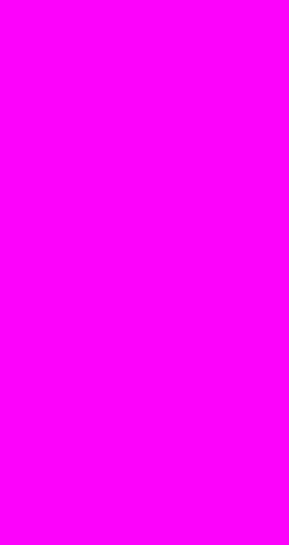
Еss=130+200=330 мкм
Допуск на толщину витка по хорде выбирается по таблице 20
Ts=110 мкм
Требования к точности заготовки определяются допусками на диаметры выступов da , радиальным и торцовым биением. Допуски на диаметры выступов назначаются по 14 квалитету точности Tda=IT14, так как наружный диаметр в процессе контроля не является базой.
Допуск на радиальное биение поверхности вершин находится по зависимости
Fda=0.1m=0,1*5=0,5мм
Допуск на торцевое биение определяется по зависимости
Fт=Fтаб=20 мкм
Где Fтаб определяется по таблице справочника [4]
Fт=20мкм
Шероховатость рабочей поверхности зубьев выбирается по таблице [1]
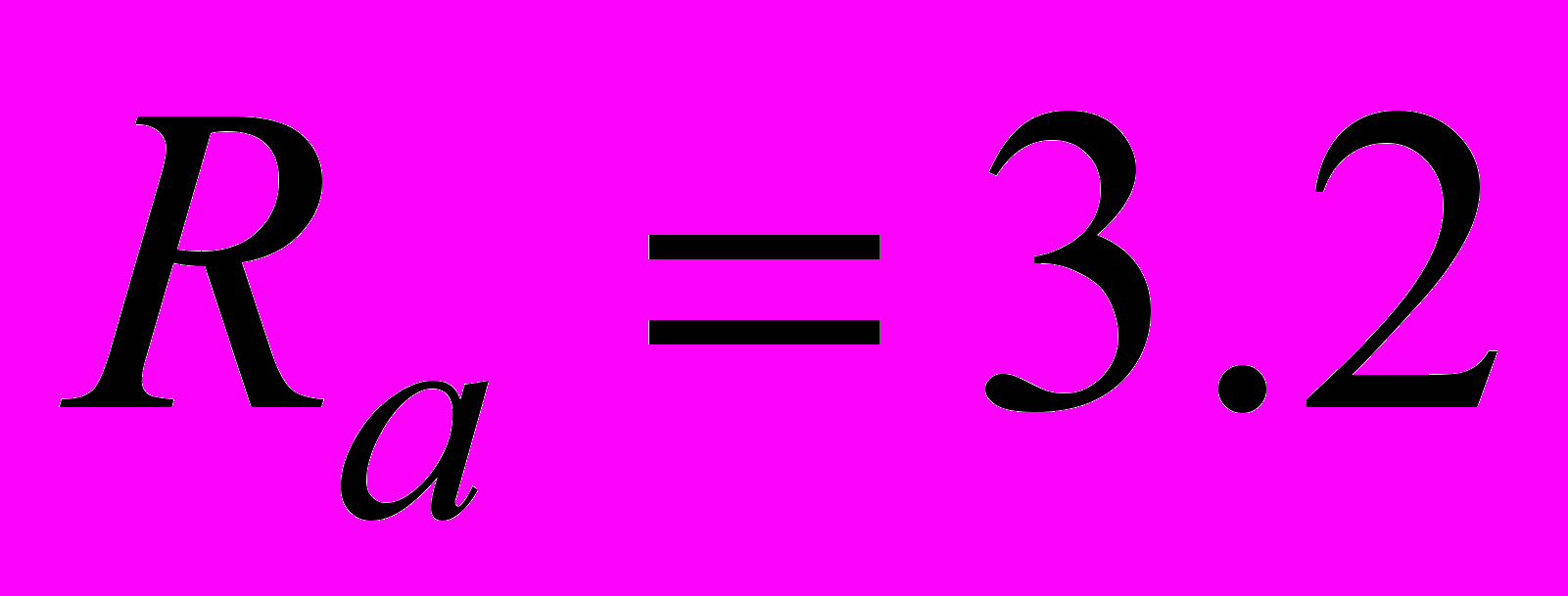
2 Расчет и нормирование точности гладких цилиндрических соединений.
2.1 Расчет и выбор посадок неподвижного соединения с дополнительными креплениями.
Исходные данные:
точность червячного колеса 8B
номинальный диаметр соединения d=42 мм
ширина шпоночного паза t=12
число зубьев колеса z=44
модуль m=5
допуск на радиальное биение зубчатого венца Fr=71 мкм
Соединение червячного колеса с валом редуктора с дополнительным креплением при помощи шпонки является разъемным неподвижным соединением, образованным переходной посадкой. Расчет разъемных соединений, образованных переходными посадками производится исходя из условий:
- обеспечение высокой точности центрирования зубчатого колеса на валу
- обеспечение легкой сборки и разборки соединения
Сочетание этих двух условий возможно лишь при небольших натягах или зазорах в соединении.
Хорошее центрирование червячного колеса на валу необходимо для обеспечения высокой кинематической точности передачи, ограничения динамических нагрузок. Известно, что наличие зазора в сопряжении за счет одностороннего смещения вала в отверстии вызывает появление радиального биения зубчатого венца колеса, определяющего кинематическую точность. В этом случае наибольший допустимый зазор, обеспечивающий первое условие ,может быть определен по формуле
Fr
Smax≤----;
KT
где KT - коэффициент запаса точности (KT=2..5), принимаем KT= 2
Fr - допуск на радиальное биение зубчатого венца, (Fr=71 мкм)
Smax= 71\2=35,5 мкм
Наибольший возможный натяг в соединении рассчитываем по формуле
3-z
Nmax=Smax-----,
3+z
где z-аргумент функции Лапласа, который определяется по её значению
Ф0(z)=P∆-0.5,
где P∆ -вероятность получения зазора в соединении. При 8 степени точности по кинематической норме точности P∆=0.2, тогда Ф0(z)=0.2-0.5=-0.3
По таблице [4] находим z=-0,843
3+0.843
Nmax = 35,5*--------- 63,1 мкм ,
3-0.843
По номинальному диаметру соединения d=42мм и
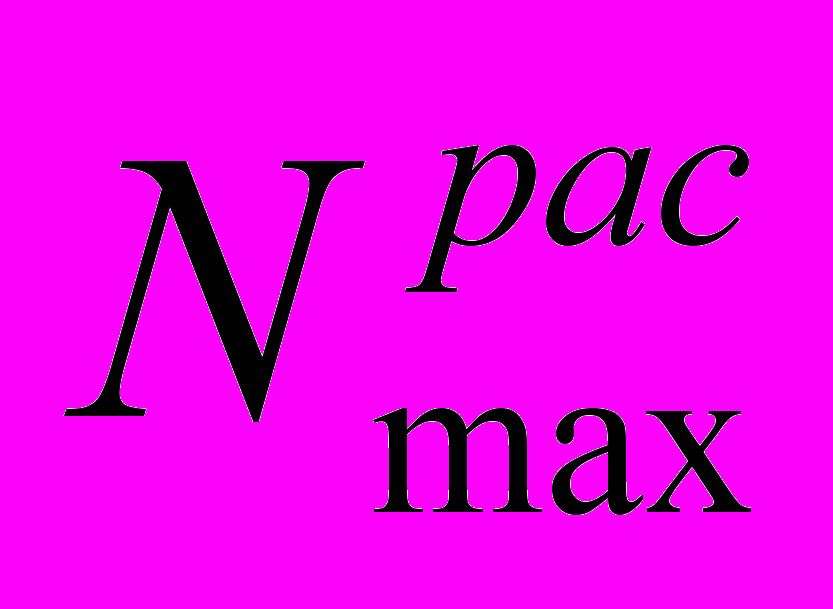
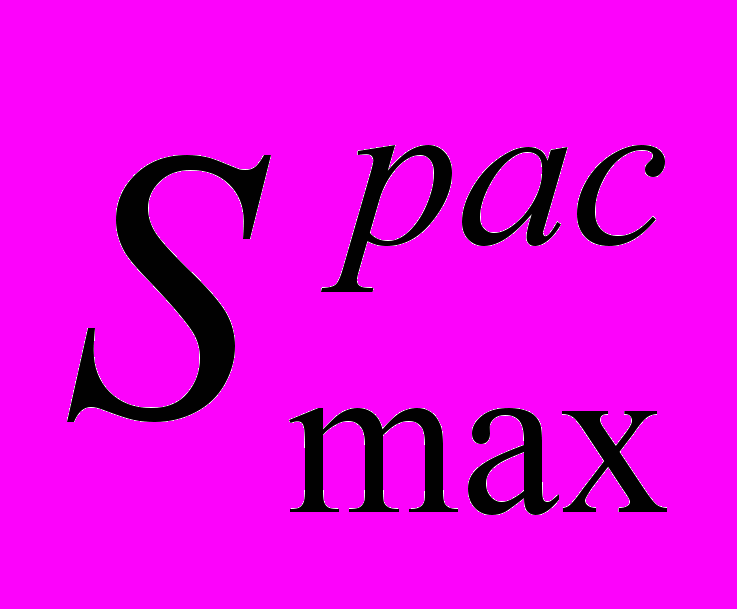
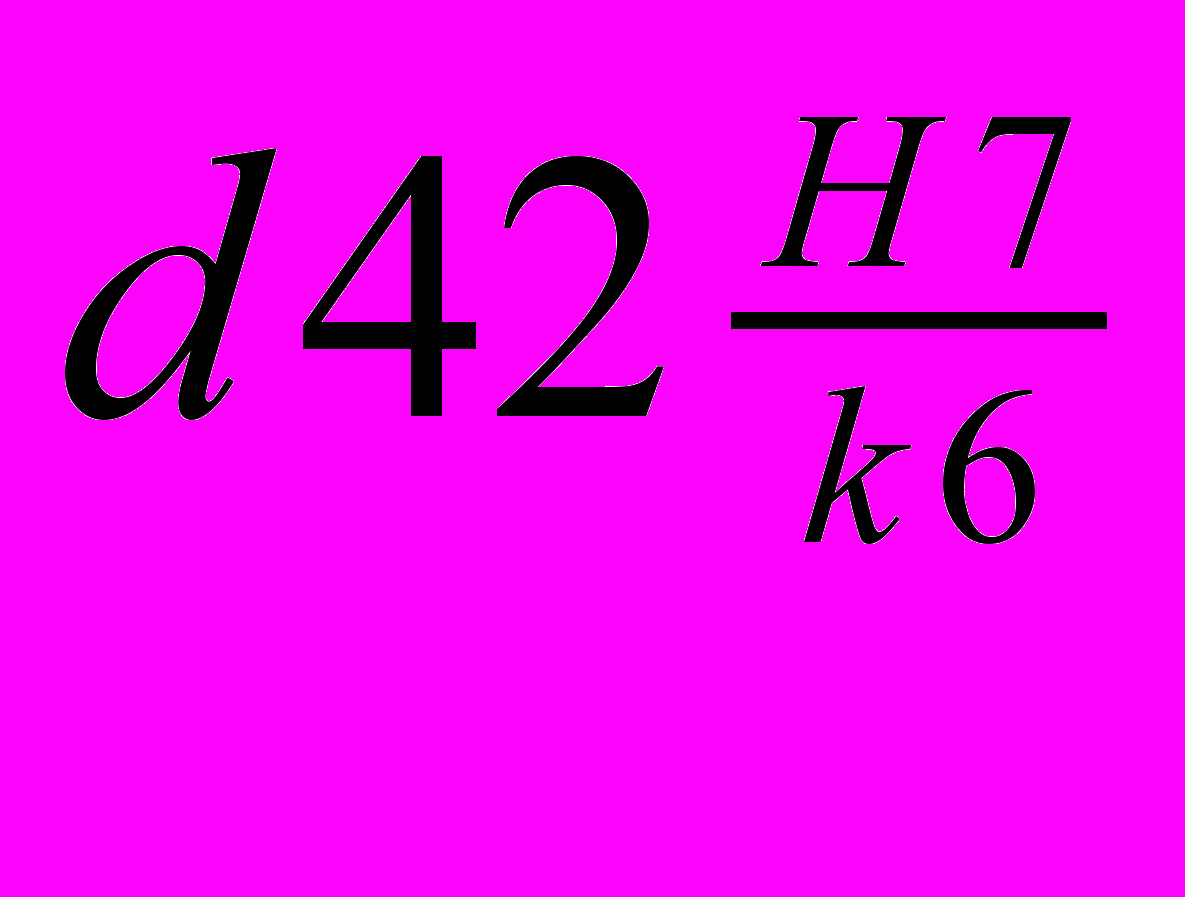
Smaxт =26
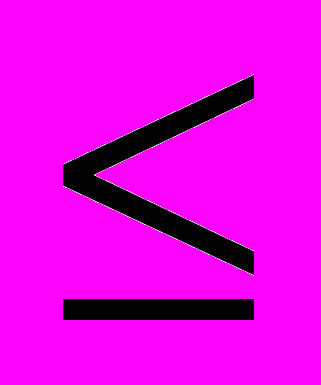
Nmaxт =50 ≤Nmaxр = 63,1
Причем выполняются требования ГОСта по соответствию степени точности червячного колеса точности отверстия (табл. 2.2 [3]).
Для обеспечения неподвижности червячного колеса с валом применяется призматическая шпонка. Работоспособность шпоночного соединения определяется точностью посадки по ширине шпонки (паза) b.
ГОСТ 23360-78 предусматривает посадки образующие нормальное, плотное и свободное соединение шпонок с пазами вала и втулки в системе основного вала.
Применяем плотный тип соединения. Для плотного соединения установлены поля допусков ширины b для паза на валу P9. И для паза во втулке P9. Предельные отклонения указанных полей допусков соответствуют ГОСТ 25347-82, шпонка как основной вал имеет поле допуска h9.
В этом случае посадка в соединении со шпоночным пазом вала будет
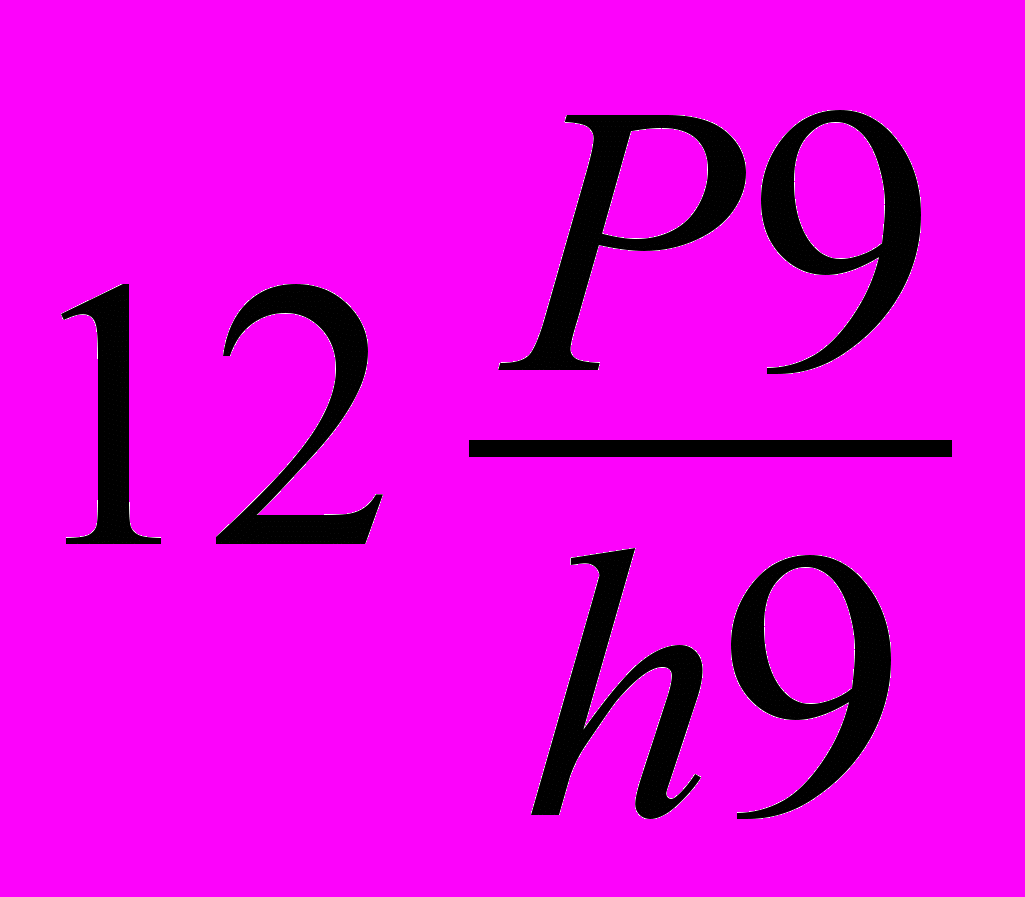
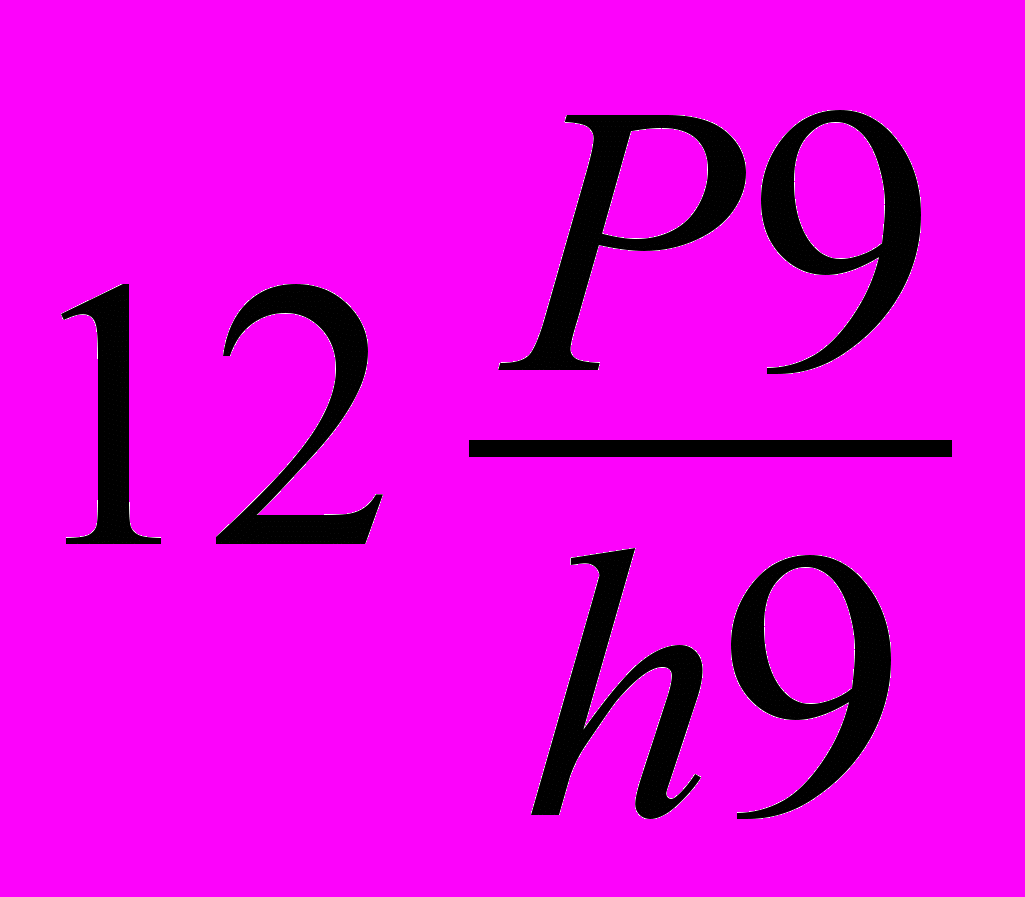
2.2 Расчет калибров.
2.2.1 Расчет калибров пробок
Исходные данные:
Отверстие d42Н7(+0,025)
Максимальный предельный диаметр отверстия Dmax =42,025
Минимальный предельный диаметр отверстия Dmin=42
Калибры для контроля отверстий называются пробками. Калибры изготовляются комплектом из проходного (ПР.) и непроходного (НЕ) калибров. При контроле деталей калибрами она признается годной, если проходной калибр проходит, а непроходной не проходит через проверяемую поверхность.
Допуски на изготовление калибров нормируются по ГОСТ 24853-81.
Для определения радиальных и исполнительных размеров пробок из таблицы указанного стандарта находятся численные значения параметров
H, Z, Y
Где H - допуск на изготовление калибра
Z- координата середины поля допуска проходной пробки
Y- координата, определяющая границу износа проходной пробки
H=4мкм, Z=3,5мкм, Y=3мкм.
Определяем предельные и исполнительные размеры пробок ПР и НЕ.
Dпрmax=Dmin+z+H/2=42+0,0035+0,004/2=42,0055 мм;
Dпрmin=Dmin+z-H/2=42+0,0035-0,004/2=42,0015 мм;
Dпризн=Dmin-y=42-0,003=41,997 мм;
Dпр исп=Dпрmax –H =42,0055-0,004 мм;
Dнеmax=Dmax+H/2=42,025+0,004/2=42,027 мм;
Dнеmin=Dmax-H/2=42,025-0,004/2=42,023 мм;
Dне исп=Dнеmax –H=42,027-0,004 мм ;
2.2.2 Расчет калибров скоб
Исходные данные:
Вал d = 42k6(
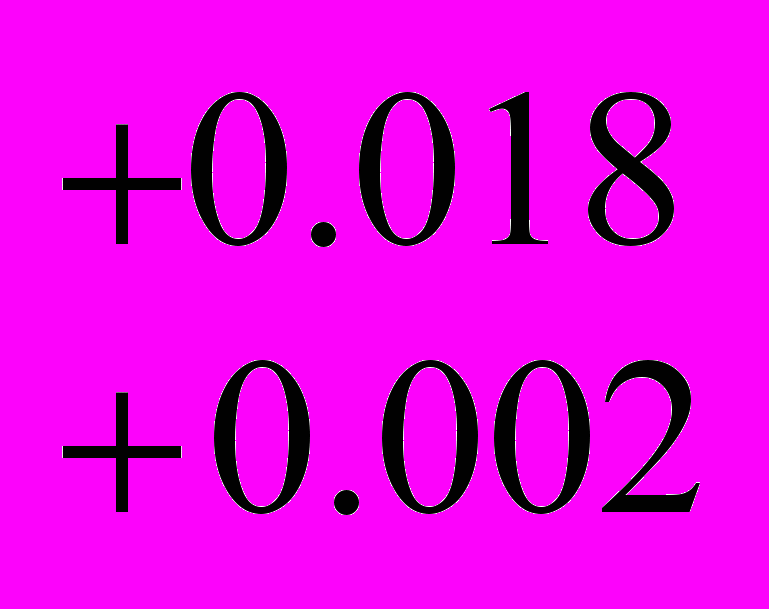
dmax= 42,018 мм,
dmin=42,002 мм.
Калибры для контроля валов называются скобами, которые, так же как и пробки имеют проходную и непроходную сторону.
Для определения предельных и исполнительных размеров скобы из таблицы ГОСТ 24853-81 выписываем координаты:
H1 = 4 мкм, Z1 = 3,5 , Y1 = 3 мкм ,Hр = 1,5 .
Определяем предельные и исполнительные размеры скобы ПР и НЕ
dПРmax=dmax-z1+H1/2=42,018-0,0035+0,002=42,0165 мм;
dПРmin=dmax-z1-H1/2=42,018-0,0035-0,002=42,0235 мм;
dПРизн=dmax+y1=42,018+0,003=42,021 мм;
dПРисп=dПРmin+H1=42,0235+0,004 мм;
dНЕmax=dmin+H1/2=42,002+0,002=42,004 мм;
dНЕmin=dmin-H1/2=42,002-0,002=42 мм;
dHEисп=dHEmin+H1=42+0,004 мм;
2.3Расчет и выбор посадок подшипников качения
2.3.1Расчет и выбор посадок подшипников качения на вал и в корпус
Исходные размеры:
Подшипник № 307
D=80 мм, d=35 мм, B=21 мм, r=2.5 мм
Радиальная нагрузка Fr=8 кН
Вал вращается, вал сплошной, корпус массивный, нагрузка умеренная.
Посадка внутреннего с валом всегда осуществляется в системе основного отверстия, а наружного кольца в корпус в системе основного вала.
Выбор посадок для подшипников качения зависит от характера нагружения колец. В подшипниковых узлах редукторов кольца испытывают циркуляционное и местное нагружение. Внутреннее кольцо подшипника является циркуляционно-нагруженным, при котором результирующая радиальная нагрузка воспринимается последовательно всей окружностью его дорожки качения и передается всей посадочной поверхностью вала.
Наружное кольцо подшипника испытывает местное нагружение, при котором постоянная по направлению результирующая радиальная нагрузка воспринимается лишь ограниченным участком окружности дорожки качения и передает её соответствующему ограниченному участку посадочной поверхности корпуса.
Класс точности подшипника для зубчатой передачи выбирается в зависимости от степени точности зубчатой передачи по таблице 3.6 [2].
Степень точности зубчатой передачи 8, тогда класс точности подшипника 6.
Так как в изделии вращается вал, внутреннее кольцо подшипника является циркуляционно-нагруженным, наружное кольцо, соединяющее с неподвижным корпусом, испытывает местное нагружение, следовательно, внутреннее кольцо должно соединяться с валом по посадке с натягом, наружное – с отверстием в корпусе – с небольшим зазором.
Посадку внутреннего кольца подшипника на вал определяем по интенсивности радиальной нагрузки Pr, которая определяется по выражению
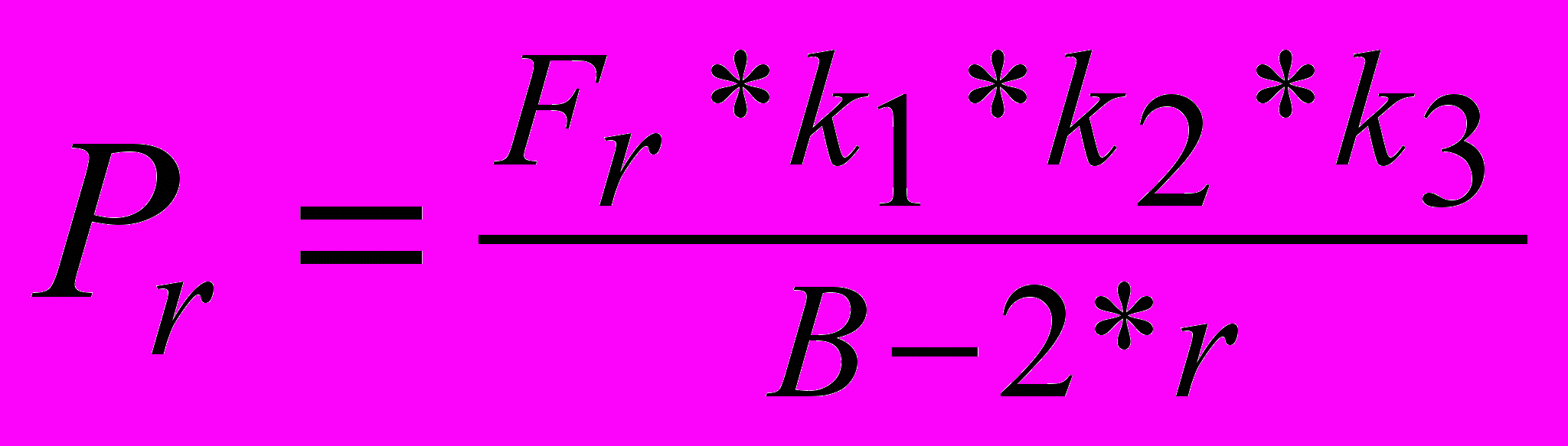
где Fr –радиальная нагрузкана опору, Н
к1- динамический коэффициент посадки (при умеренной нагрузке
к1=1 табл 3.8 [2])
к2- коэффициент, учитывающий степень ослабления натяга (при сплошном вале к2=1)
к3-коэффициент, учитывающий тип подшипника (для однорядных не сдвоенных подшипников к3=1)
В-ширина кольца подшипника, мм
Рr=8000*1*1*1/(21-2*2,5)=500 Н/м
По рассчитанному значению Рr и номинальному диаметру d=35 мм устанавливаем поле допуска вала к6 (табл 3.7 [2])
Поле допуска для отверстия в корпусе определяется в зависимости от диаметра D=80 мм, характера нагрузки и конструкции корпуса Н7 (табл 3.9 [2]).
Квалитет точности для отверстия и вала устанавливается в зависимости от класса точности подшипника при 6 классе точности вал обрабатывается по 6, а отверстие – по 7 квалитету точности
Dотв=80Н7(+0,025)
dвала=35к6(
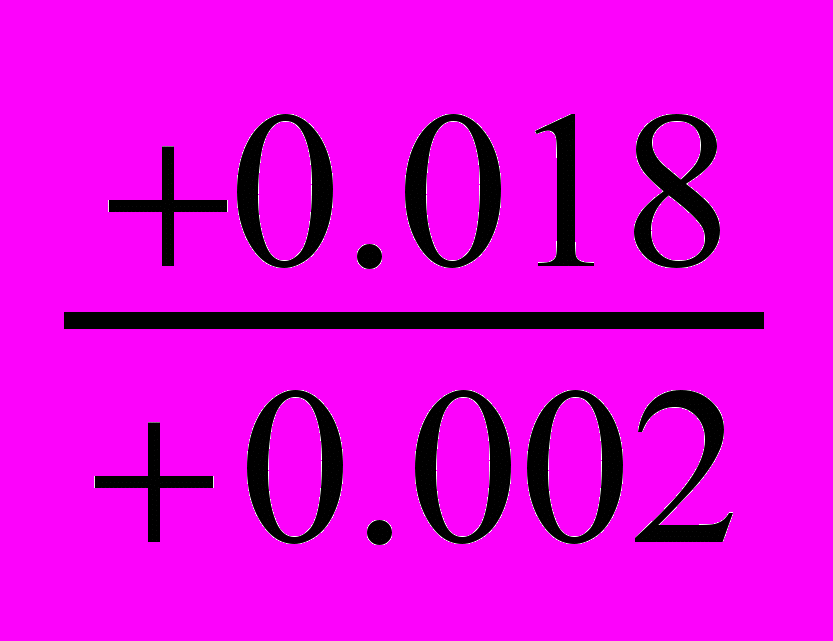
Предельное отклонение для колец подшипника определяем по
ГОСТ 520-89
Dподш=80l6(-0.013)
Dподш=35L6(-0,012)
Таким образом посадка по внутреннему кольцу подшипника будет 35
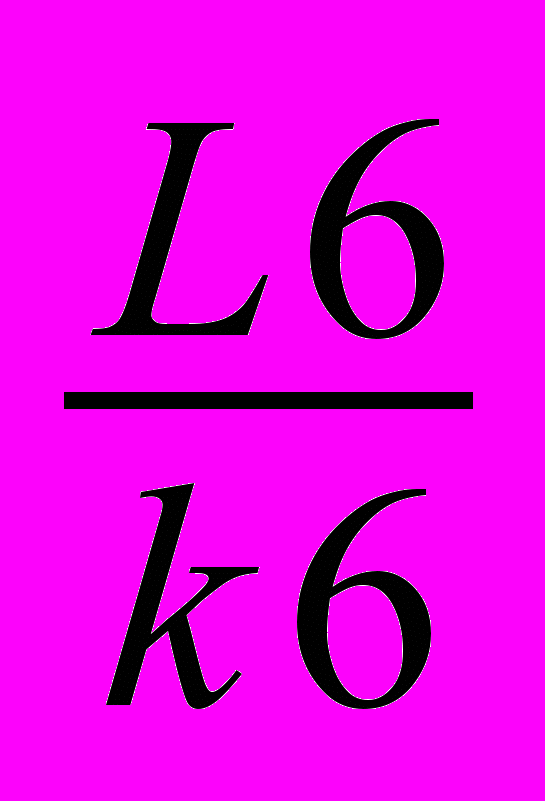
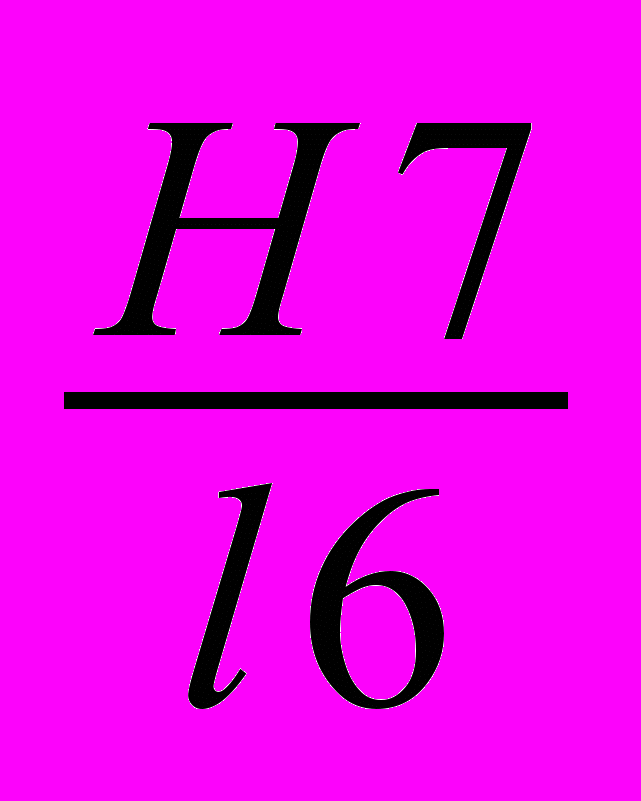
2.3.2 Определение требований к посадочным поверхностям вала и отверстий корпуса.
Требования к посадочным поверхностям вала и отверстия определяются по ГОСТ 3325-85. Шероховатость поверхностей определяется по таблице 3, допуски круглости и профили продольного сечения по таблице 4. допуск торцевого биения опорного торца вала по таблице 5.
Ra вала=0,63 мкм
Ra отв=0,63 мкм
Ra торц б=1,25 мкм
Тпр вала=Тпр сеч в=6,0 мкм
Тпр отв=Тпр сеч отв=7,5 мкм
Тторц б вала=19 мкм
3 Расчет допусков размеров, входящих в размерную цепь
Параметры замыкающего звена
UΔ=0+0,74
ESUΔ=+0.74
EIUΔ=0
TUΔ=+0.74
EcΔ=+0.37
Размерная цепь
Номинальные значения составляющих звеньев
U1=6, U2=1, U3=65, U4=0,071, U5=34, U6=5, U7=21
Проверка правильности установки номинальных значений
UΔ= U2+ U3-U1- U7- U6- U5- U4
0=1+65-6-21-5-34
Предельные отклонения составляющих кроме компенсирующего звена
U1=6
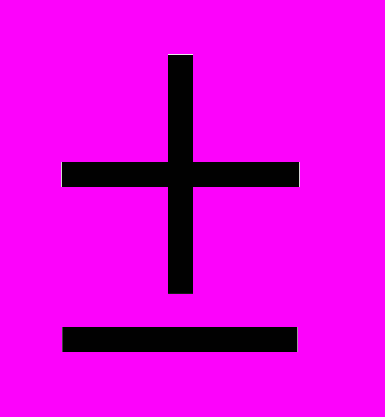
U2=1
U3=65-0,19
U5=34-0,16
U6=5-0,3
U7=21-0,084
Допуски и координаты середины полей допусков составляющих звеньев кроме компенсирующего звена
TU1=0.12
TU3=0.19
TU5=0.16
TU6=0.3
TU7=0.084
Ec1=0
Ec3= -0.095
Ec5=-0.08
Ec6=-0.15
Ec7=-0.042
Производственный допуск замыкающего звена
TU =0.12+0.16+0.3+0.19+0.07+0.84=0.925мм
Величина компенсаций
Тк= TU1- TU1+TU
Тк=0.925-0.74+0.08=0.265
Координата середины поля производственного допуска замыкающего звена
Ec1= Ec1- Ec2
Ec1=-0.095+0.08+0.15+0.042=0.177
Величина компенсации координаты середины поля производственного допуска замыкающего звена
Ecк= (Ec -Ec1)
Ecк=(0,37-0,177)=0,193
Предельное значение величины компенсации
ESk=0.193+0.265/2=0,3255
EIk=0.193-0.265/2=0.0605
Толщина одной прокладки
S=0.1
Число прокладок
N=0.265/0.1=2.65
N=3