Повышение качества резьбовых соединений путем применения ультразвука
Вид материала | Автореферат диссертации |
- Резцы (гребенки), имеющие наибольшее применение, и резьбонакатные головки с роликами, 1909.14kb.
- Федеральный государственный образовательный стандарт среднего профессионального образования, 845.28kb.
- Автореферат Повышение конкурентоспособности предпринимательской структуры путем введения, 327.73kb.
- Развитие программно-целевых методов бюджетного планирования, 145.21kb.
- Контроль качества сварных соединений трубопроводов стальных, из полимерных материалов,, 375.15kb.
- Программа обучения по курсу «Принципы проектирования резьбовых соединений обсадных, 16.28kb.
- Повышение качества функционирования комбинированного нечеткого регулятора системы управления, 98.69kb.
- Содержание: Введение, 302.8kb.
- Проект г. Донецк, 194.74kb.
- Повышение надежности грузовых автомобилей путем применения системы эксплуатационной, 247.7kb.
На правах рукописи
ШУВАЕВ Игорь Вячеславович
ПОВЫШЕНИЕ КАЧЕСТВА РЕЗЬБОВЫХ СОЕДИНЕНИЙ ПУТЕМ ПРИМЕНЕНИЯ УЛЬТРАЗВУКА
Специальность 05.02.08 – Технология машиностроения
Автореферат
диссертации на соискание ученой степени
кандидата технических наук
Самара 2006
Работа выполнена на кафедре «Автоматизация технологических процессов в машиностроении» Самарского государственного технического университета
Научный руководитель: заслуженный работник ВШ РФ
доктор технических наук, профессор
ШТРИКОВ Борис Леонидович
Официальные оппоненты: доктор технических наук, профессор
ДЕМИН Феликс Ильич
кандидат технических наук, доцент
ХОЛОДКОВА Альбертина Григорьевна
Ведущая организация: ОАО «Завод Магнето», г. Самара
Защита состоится 9 июня 2006 г. в 14-00 часов на заседании диссертационного совета Д 212.217.02 в Самарском государственном техническом университете по адресу: г. Самара, ул. Галактионовская 141, корпус № 6, ауд. 28.
С диссертацией можно ознакомиться в библиотеке Самарского государственного технического университета.
Автореферат разослан «2» мая 2006 г.
Просим Вас принять участие в обсуждении работы и направить свой отзыв, заверенный гербовой печатью, по адресу: 443100, г. Самара, ул. Молодогвардейская 244, Главный корпус, ученому секретарю диссертационного совета Д 212.217.02
Ученый секретарь
диссертационного совета Д 212.217.02 Денисенко А.Ф.
ОБЩАЯ ХАРАКТЕРИСТИКА РАБОТЫ
Актуальность темы. Проблема обеспечения заданных и стабильных показателей качества машиностроительной продукции в условиях жесткой конкуренции рыночной экономики имеет большое значение. Рациональная и эффективная технология сборки изделий машиностроения необходима для обеспечения их надежности и долговечности.
Важная роль в обеспечении эксплуатационных показателей машин и механизмов принадлежит сборочным операциям. При этом большую группу соединений составляют резьбовые соединения, от надежности и качества которых во многом зависят функциональные параметры узлов. В то же время, получившие распространение традиционные методы сборки и контроля этих соединений не всегда удовлетворяют все возрастающим требованиям к качеству узлов.
Перспективным направлением повышения эффективности традиционных процессов сборки и контроля качества резьбовых соединений является введение ультразвуковых колебаний в зону контакта поверхностей деталей, когда наряду с основными движениями, предусмотренными технологической схемой сборки, деталям сообщаются колебания ультразвуковой частоты. Совместное действие ряда факторов и явлений, возникающих в ультразвуковом поле, открывает качественно новые возможности в организации и проведении процессов сборки и контроля качества соединений.
Вмести с тем, несмотря на известные достоинства ультразвуковой сборки, область ее рационального применения раскрыта еще недостаточно и требуют дальнейшего углубленного изучения. В частности, практически не изучена возможность использования колебаний в диагностических целях. В то же время получаемая при этом информация может быть использована как для оценки качества формируемого соединения, так и для оперативного управления ходом технологического процесса сборки.
Поэтому выявление механизма воздействия ультразвука на формирование связей в резьбовом соединении и управление состоянием этих связей непосредственно в процессе сборки является актуальной задачей.
Тематика работы входит в состав научно-исследовательских работ, проводимых в рамках тематического плана СамГТУ по заданию Федерального агентства по образованию на 2002-2006 годы по теме «Исследование теоретических основ волновых технологий сборки и разборки прессовых и резьбовых соединений с сертификацией их качества», регистрационный номер НИР 1.8.02; Номер государственной регистрации НИР 01200212230.
Цель работы. Повышение эффективности ультразвуковой сборки и качества резьбовых соединений путем управления состоянием формируемого соединения по параметрам вибрационных сигналов в процессе сборки.
Методы исследований. Для достижения поставленной цели использован системный подход к изучению процесса ультразвуковой сборки резьбовых соединений с одновременной оценкой качества формируемого соединения. Использованы основные теоретические положения технологии машиностроения, теории контактного взаимодействия твердых тел, методы исследования колебательных систем и вибрационной диагностики.
Для подтверждения полученных результатов применялись методы экспериментального исследования и моделирования с использованием программного комплекса ANSYS.
Научная новизна. Исследованы особенности процесса ультразвуковой сборки резьбовых соединений, с учетом которых разработана модель, связывающая характеристики деталей и режимы сборки с их эксплуатационными показателями.
Обоснован алгоритм повышения эффективности ультразвуковой сборки резьбовых соединений с учетом изменений характеристик трения и прочностных свойств материала деталей.
Синтезированы и исследованы в программном комплексе ANSYS динамические модели резьбовых соединений при дополнительных ультразвуковых воздействиях.
Установлена возможность управления качеством резьбовых соединений непосредственно в процессе сборки по их динамическим параметрам.
Разработаны патентнозащищенные способы оценки качества формируемого соединения по динамическим параметрам эквивалентной колебательной системы.
Практическая ценность. На основании выполненных теоретических и экспериментальных исследований реализован комплекс конструкторско-технологических решений, позволяющих повысить эффективность технологического процесса сборки и улучшить качество формируемых соединений.
Разработаны способы и изготовлены устройства для их реализации, позволяющие проводить динамический контроль качества резьбовых соединений в процессе ультразвуковой сборки, защищенные патентом РФ № 2228256, решением о выдаче патента РФ № 2004132740/02, патентами РФ на полезные модели № 31350 и № 31448.
На защиту выносятся:
- выявленные теоретическими и экспериментальными исследованиями основные особенности механизма формирования контактных связей в элементах резьбового соединения при ультразвуковой сборке, а также разработанный способ эффективного технологического управления ими;
- созданные конечно-элементные статические и динамические модели резьбовых соединений: модели напряженно-деформированного состояния резьбового соединения, модели собственных форм и частот колебаний резьбовых соединений, резонансные модели резьбовых соединений;
- разработанные способы динамического контроля качества резьбовых соединений при ультразвуковой сборке на основе анализа резонансных свойств механической колебательной системы;
- устройства, оборудование для осуществления ультразвуковой сборки и контроля качества формируемых соединений.
Апробация работы. Основные результаты научных исследований докладывались, обсуждались и получили положительную оценку на Международном научно-техническом семинаре «Сборка в машиностроении и приборостроении» (Брянск, 2001 г.); международных научно-технических конференциях «Высокие технологии в машиностроении» (Самара, 2002 г., 2004 г. и 2005 г.); Всероссийской научной конференции молодых ученых «Наука. Технологии. Инновации» (Новосибирск, 2003 г.).; XXIX Самарской областной научной конференции «Общественные, естественные и технические науки» (Самара, 2003 г.); Международной конференции «Актуальные проблемы надежности технологических, энергетических и транспортных машин» (Самара, 2003 г.); 5-ой Международной научно-технической конференции «Обеспечение и повышение качества машин на этапах их жизненного цикла» (Брянск, 2005 г.).
Публикации. По теме диссертации опубликовано 11 работ, в числе которых 1 патент РФ и 1 решение о выдаче патента РФ на изобретение и 2 патента РФ на полезные модели.
Структура и объем работы. Диссертация состоит из введения, четырех разделов и общих выводов, изложенных на 148 страницах машинописного текста, содержит 85 рисунков, 19 таблиц, список использованных источников из 145 наименований.
СОДЕРЖАНИЕ РАБОТЫ
Во введении обоснована актуальность темы диссертации, поставлена цель исследования, изложены основные положения, выносимые на защиту, определены научная новизна и практическая ценность.
Первая глава посвящена анализу проблемы повышения эффективности процесса сборки и контроля качества резьбовых соединений на основе применения ультразвуковых колебаний. Дан обзор литературных источников по рассматриваемому вопросу, проведен анализ предъявляемых требований к показателям качества резьбовых соединений, исследованы факторы, приводящие к отклонениям этих показателей, проведен анализ современного состояния методов и средств определения качества резьбовых соединений.
Большой вклад в развитие науки о сборке, в том числе ультразвуковой, внесли ученые Б.С. Балакшин, В.П. Бобров, А.Г. Герасимов, А.А. Гусев, А.М. Дальский, Ю.З. Житников, Д.Я. Ильинский, Н.И. Камышный, И.И. Капустин, И.М. Колесов, В.В. Косилов, А.Н. Малов, К.Я. Муценек, М.П. Новиков, Г.Я. Пановко, А.Н. Рабинович, А.Г. Холодкова, Б.Л. Штриков, В.А. Яхимович и др.
Необходимо отметить, что функциональные параметры машин и приборов во многом определяются показателями качества деталей, образующих соединение. Эта взаимосвязь получила глубокое осмысление благодаря работам А.П. Бабичева, В.Ф. Безъязычного, Ф.И. Демина, Б.А. Кравченко, А.А. Маталина, Д.Д. Папшева, А.С. Проникова, Э.В. Рыжова, А.М. Сулимы, А.Г. Суслова, Л.В. Худобина, Ю.Г. Шнейдера, А.В. Якимова, П.И. Ящерицина и др. и получила дальнейшее развитие в исследованиях Б.М. Базрова, В.Г. Митрофанова, Ю.С. Соломенцева и др., направленных на достижение требуемых показателей изделий путем управления технологическими процессами средствами автоматизации. При этом в основе большинства технологических работ лежат фундаментальные исследования Д.Н. Гаркунова, М.Н. Добычина, И.В. Крагельского, В.С. Комбалова, Н.М. Михина, А.В. Чичинадзе и др. по проблеме контактного взаимодействия поверхностей сопряжения.
В создание теоретических основ и практическую реализацию ультразвуковой технологии большой вклад внесли ученые О.В. Абрамов, Б.А. Агранат, В.К. Асташев, В.А. Вероман, А.И. Исаев, М.Г. Киселев, Ю.И. Китайгородский, В.В. Клубович, Е.Г. Коновалов, Б.А. Кравченко, А.В. Кулемин А.И. Марков, В.Д. Мартынов, М.С. Нерубай, И.Г. Полоцкий, В.П. Северденко, А.В. Степаненко, И.И. Теумин, Б.Л. Штриков, а также зарубежные исследователи Л. Баламуз, Л. Колуэлл, Д. Кумабэ, Б. Лангенекер, У. Мезон и др.
На основе проведенного анализа сформулированы основные задачи исследования:
- провести сравнительный анализ методов и средств определения характеристик качества резьбовых соединений;
- исследовать влияние факторов, приводящих к отклонениям характеристик качества резьбовых соединений;
- определить оптимальные параметры процесса по критериям качества резьбовых соединений и силовым параметрам процесса сборки;
- исследовать влияние УЗК на трение и прочностные свойства материалов и на этой основе построить эффективный алгоритм сборки резьбовых соединений, позволяющий существенно снизить силовые параметры процесса и повысить эксплуатационные показатели резьбовых соединений;
- на основе конечно-элементного анализа и программного комплекса ANSYS построить и исследовать трехмерные модели напряженно-деформированного состояния резьбовых соединений, а также динамические модели собственных частот и форм колебаний и резонансные модели в условиях колебательных воздействий;
- разработать, экспериментально исследовать и внедрить способ контроля характеристик формируемого соединения при ультразвуковой сборке.
Во второй главе обосновывается выбор дополнительных ультразвуковых колебательных воздействий при проведении сборки резьбовых соединений как для повышения эффективности процесса, так и для получения дополнительной диагностической информации о динамических параметрах формируемого соединения. Описан разработанный алгоритм сборки резьбовых соединений и обосновывается его эффективность. Рассмотрен разработанный патентозащищенный способ сборки резьбовых соединений с контролем добротности как параметра качества.
Параметры, влияющие на качество сборки резьбового соединения, входят в выражение

где
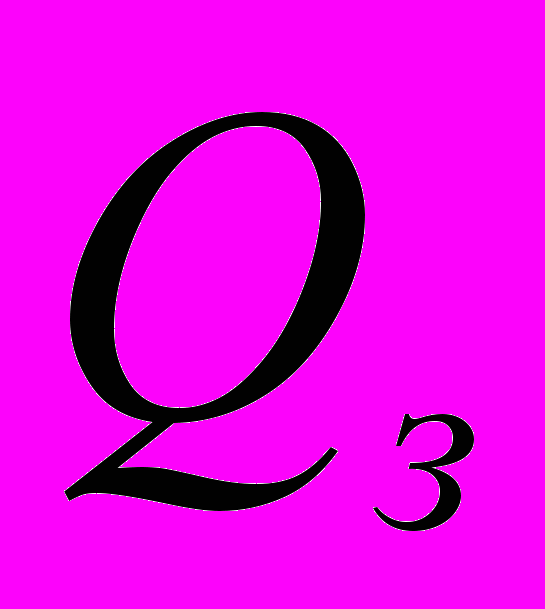
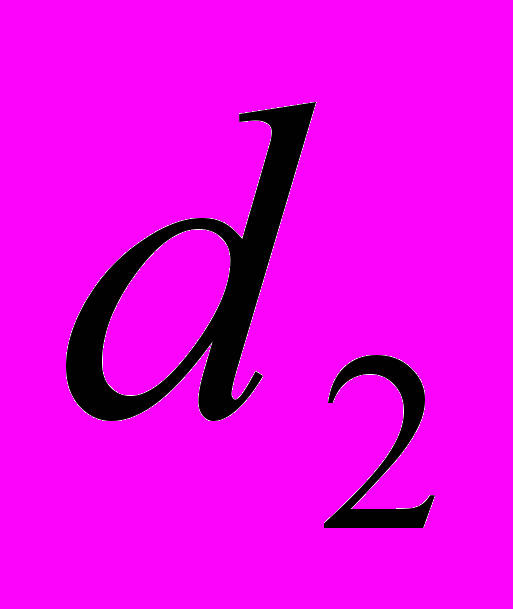
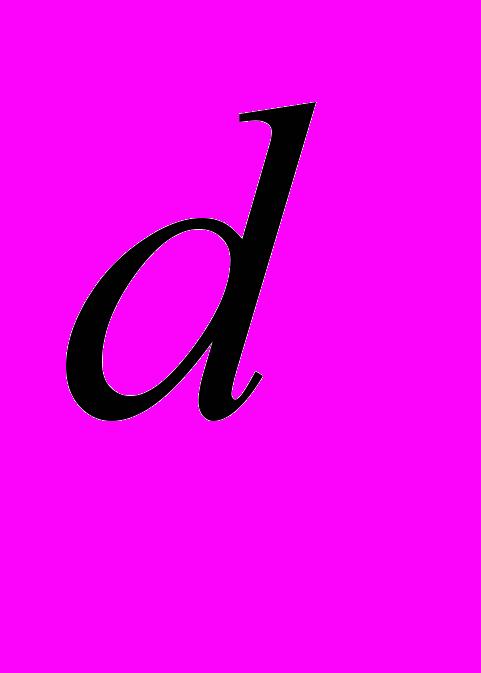
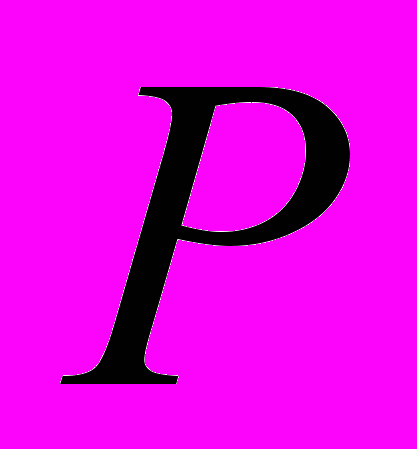
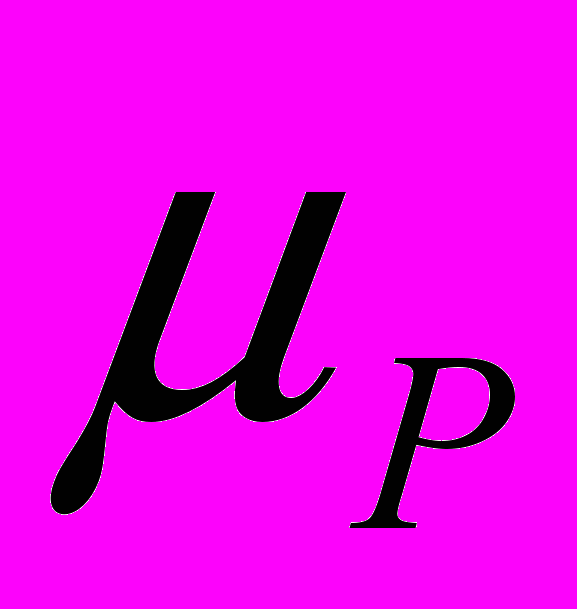
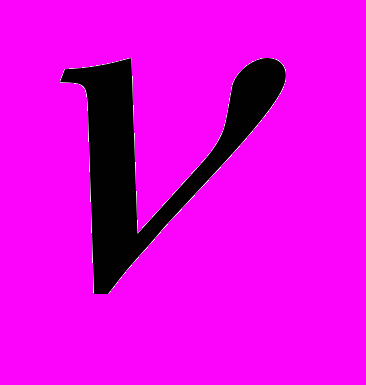
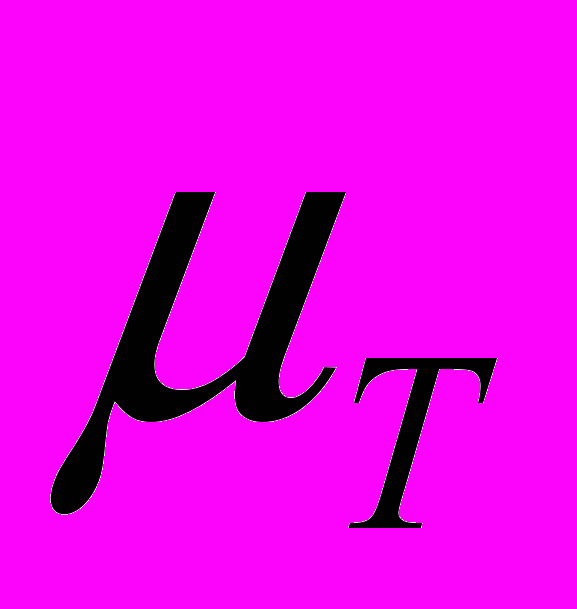
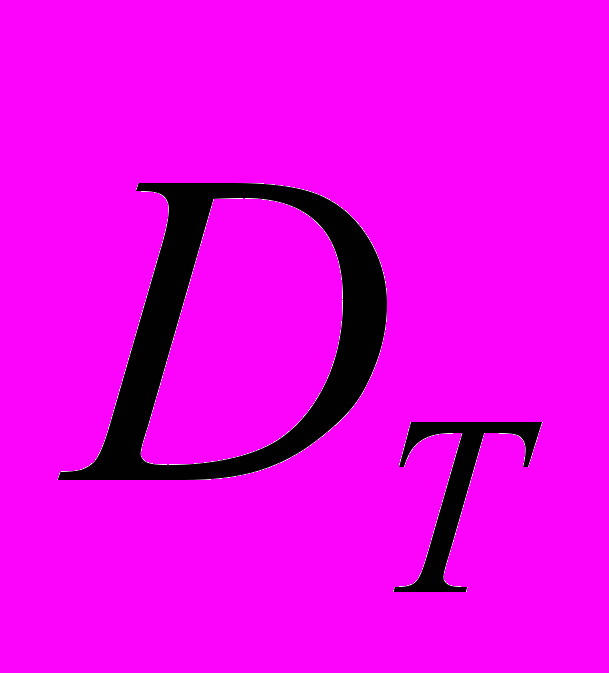
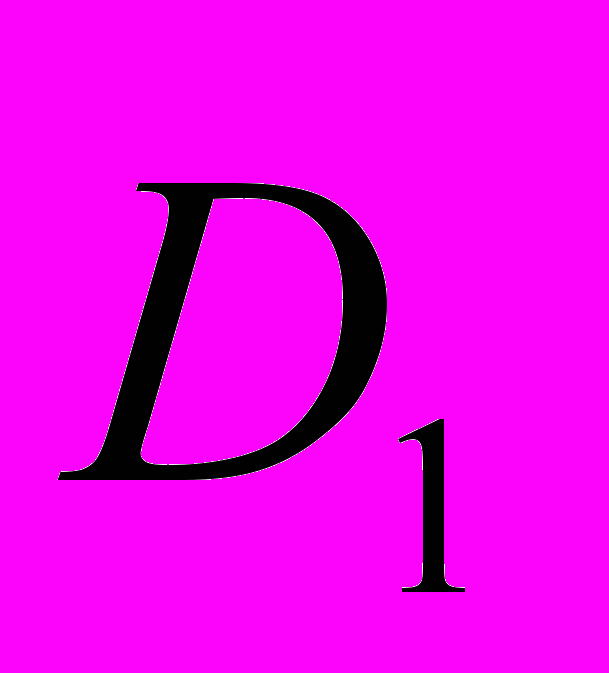
Приведенная зависимость является исходной для определения момента при затяжке резьбовых соединений деталей и учитывает момент сопротивления, как в резьбовой паре, так и по торцу гайки или головки болта. Эта зависимость показывает многофакторную связь между моментом на ключе гайковерта и силой затяжки, которая в значительной мере изменяется из-за колебаний приведенных коэффициентов трения
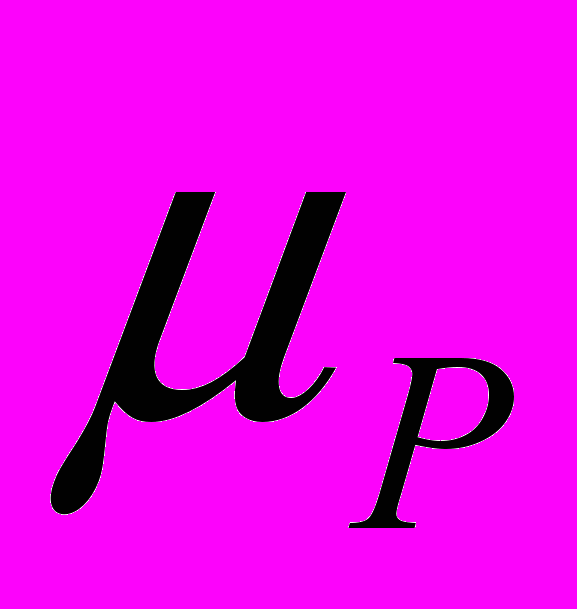
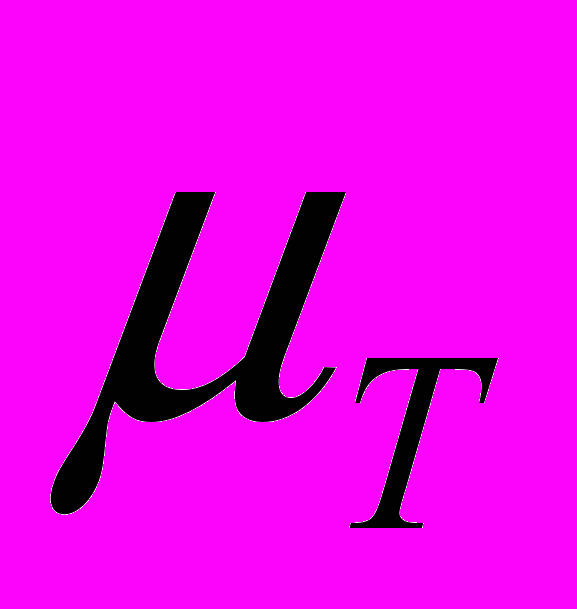
При сборке резьбовых соединений работа момента, прикладываемого к болту, распределяется на работу по преодолению сил трения в резьбе, на работу преодоления сил трения в поверхностях контактирования головки болта и гайки с собираемыми деталями и на работу создания силы предварительной затяжки. Проведенные исследования показали, что до 90 % работы момента на ключе расходуется на преодоление сил трения, и лишь 10 % затрачивается на формирование силы затяжки. Соответственно, чем меньше коэффициент трения, тем меньшая часть работы расходуется на преодоление сил трения и тем большая ее часть расходуется на создание силы предварительной затяжки.
Приложение ультразвуковых колебаний при сжатии и растяжении материалов способствует снижению сопротивления пластической деформации, пределов текучести и прочности. Расширение исследуемого диапазона параметров ультразвуковых колебаний позволило установить, что максимальная степень деформации образцов из стали 45 в резонансном режиме наступает при амплитуде
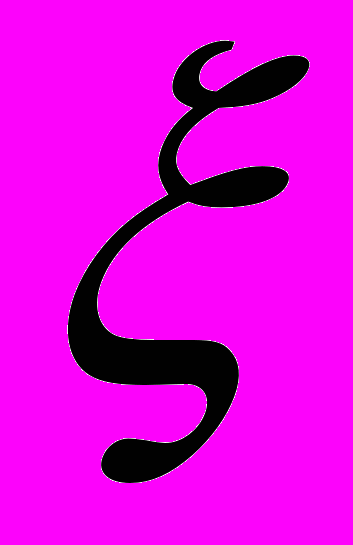
Наряду с объемным эффектом введение ультразвука в зону контакта оказывает существенное влияние на характер фрикционного взаимодействия и на его основные показатели. Механизм воздействия ультразвука на силы трения заключается в изменении кинематических условий контактирования поверхностей, а также в изменении характера напряженного состояния металла в зоне трения. Установлено, что в зависимости от схемы подведения колебаний при оптимальных амплитудах и от величины удельных нагрузок коэффициент трения
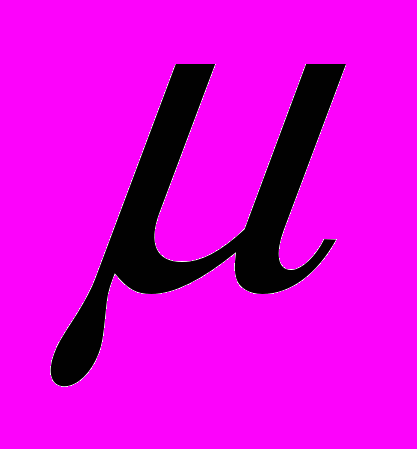
Следует учитывать, что при ультразвуковой сборке с прекращением ультразвукового воздействия условный предел текучести
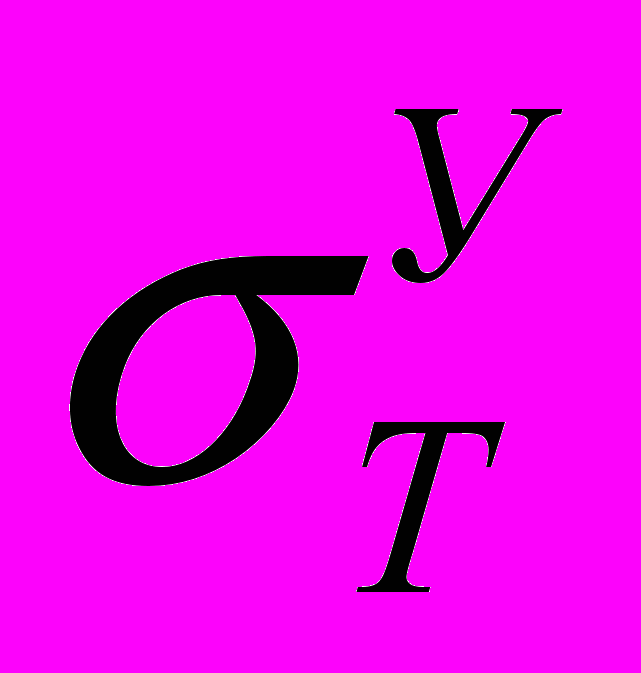
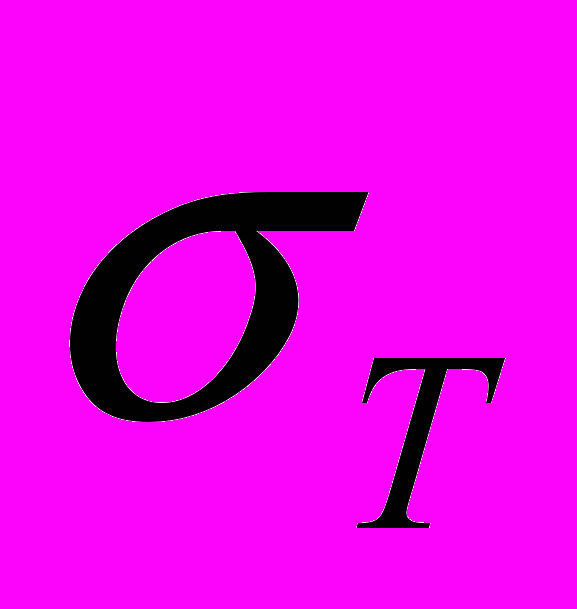
Для крепежной детали можно рассчитать и изобразить графически зависимость между прикладываемым моментом, коэффициентом трения, величиной силы затяжки и пределами текучести и прочности. Разработан алгоритм ультразвуковой сборки резьбовых соединений, в соответствии с которым затяжку производят с использованием эффектов снижения предела текучести и трения при воздействии ультразвуковых колебаний (рис. 1).
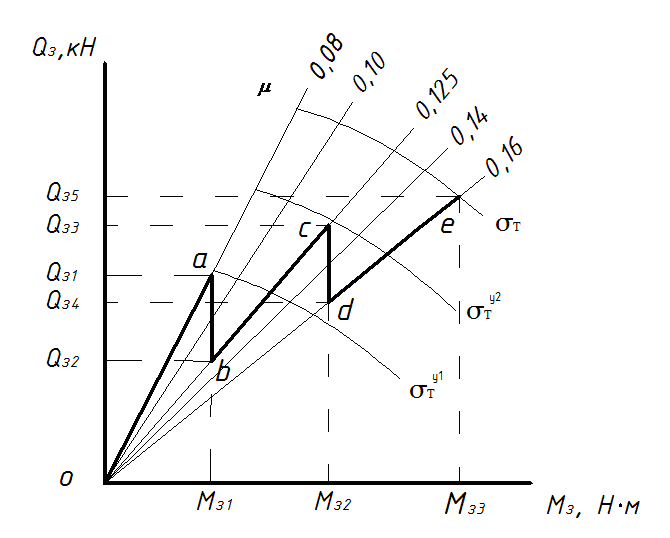
Рис. 1. Алгоритм ультразвуковой сборки:
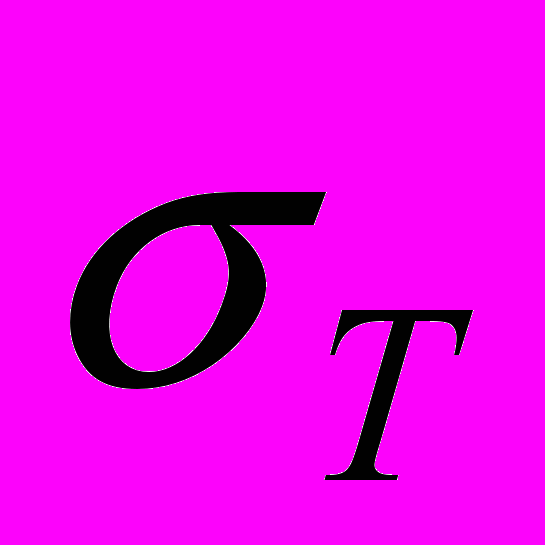
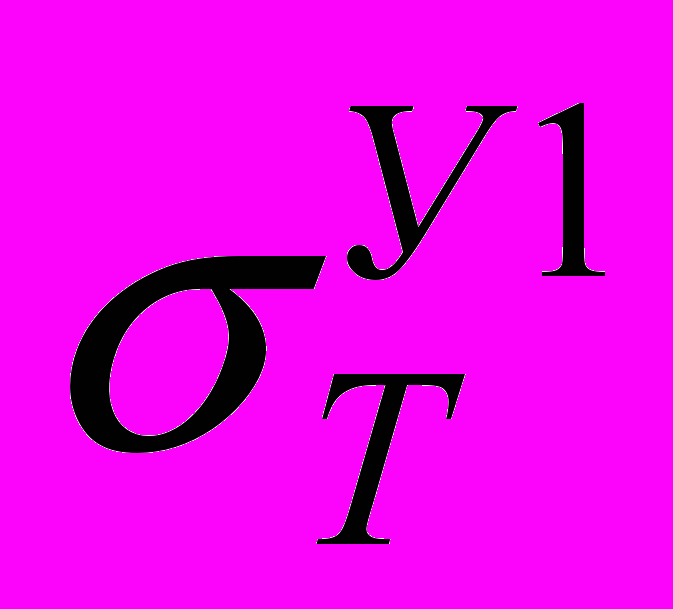
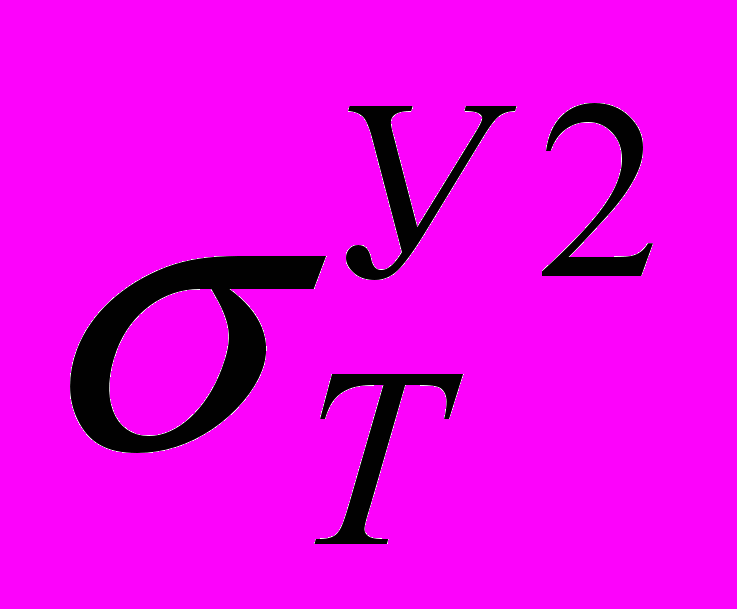
Предложено операции наживления, свинчивания и основную фазу затяжки проводить при максимальных значениях амплитуды ультразвуковых колебаний. Затем последовательно снижать амплитуду до минимального значения, причем уменьшение амплитуды колебаний производить при изменении знака приращения крутящего момента, соответствующего достижению предела текучести для данной амплитуды ультразвуковых колебаний.
Процесс затяжки необходимо завершать при минимальной амплитуде ультразвуковых колебаний (1-2 мкм), чтобы не превысить предел текучести материала
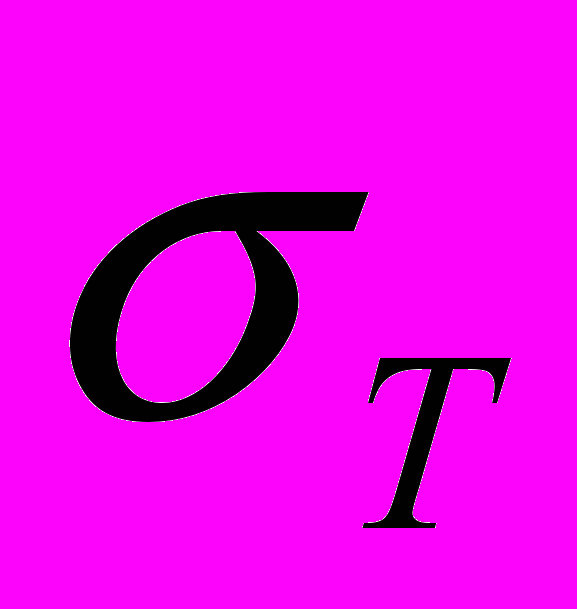
Целью управления процессом затяжки резьбовых соединений является снижение его силовых параметров, и рациональном использовании прочностных свойств крепежной детали.
Для эффективной реализации разработанного алгоритма сборки резьбовых соединений необходимо оперативно определять момент вхождения процесса затяжки в область пластических деформаций и, в соответствии с этим, изменять параметры ультразвуковых колебаний. Для этой цели контролируется изменение знака приращения крутящего момента. Если
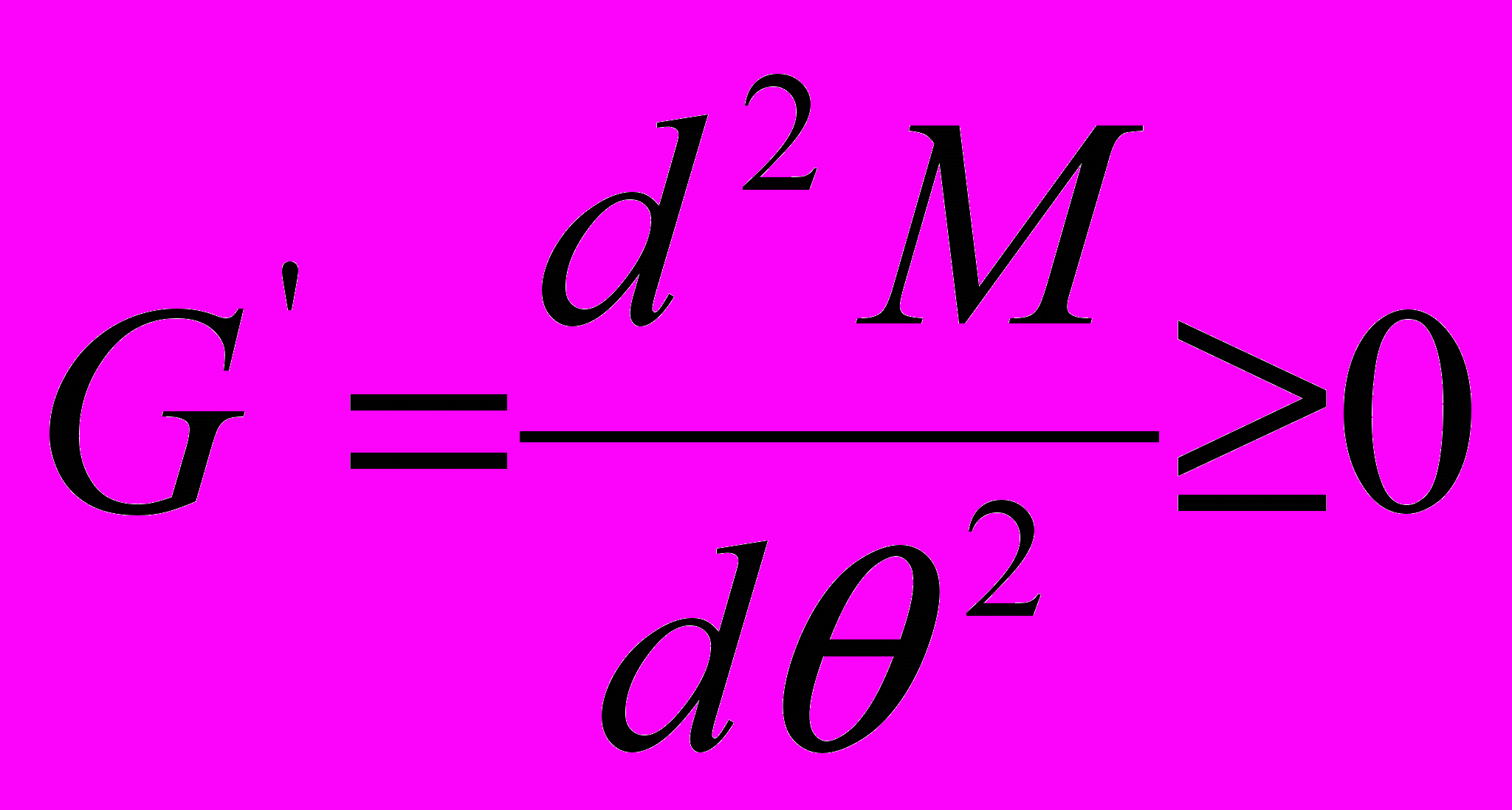
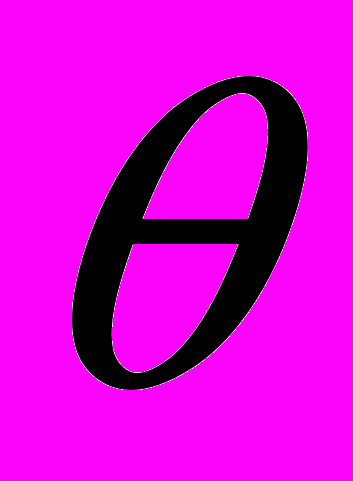
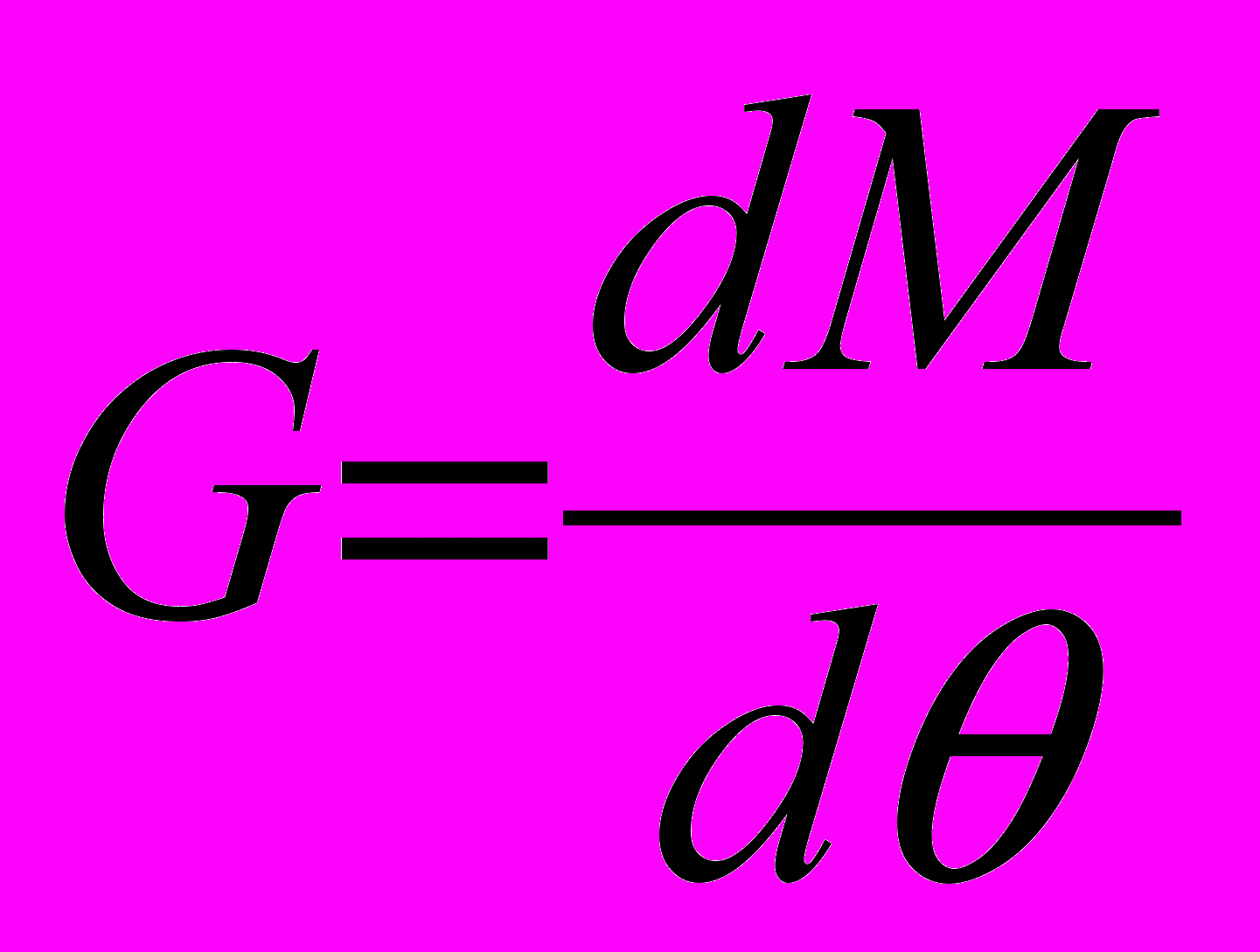
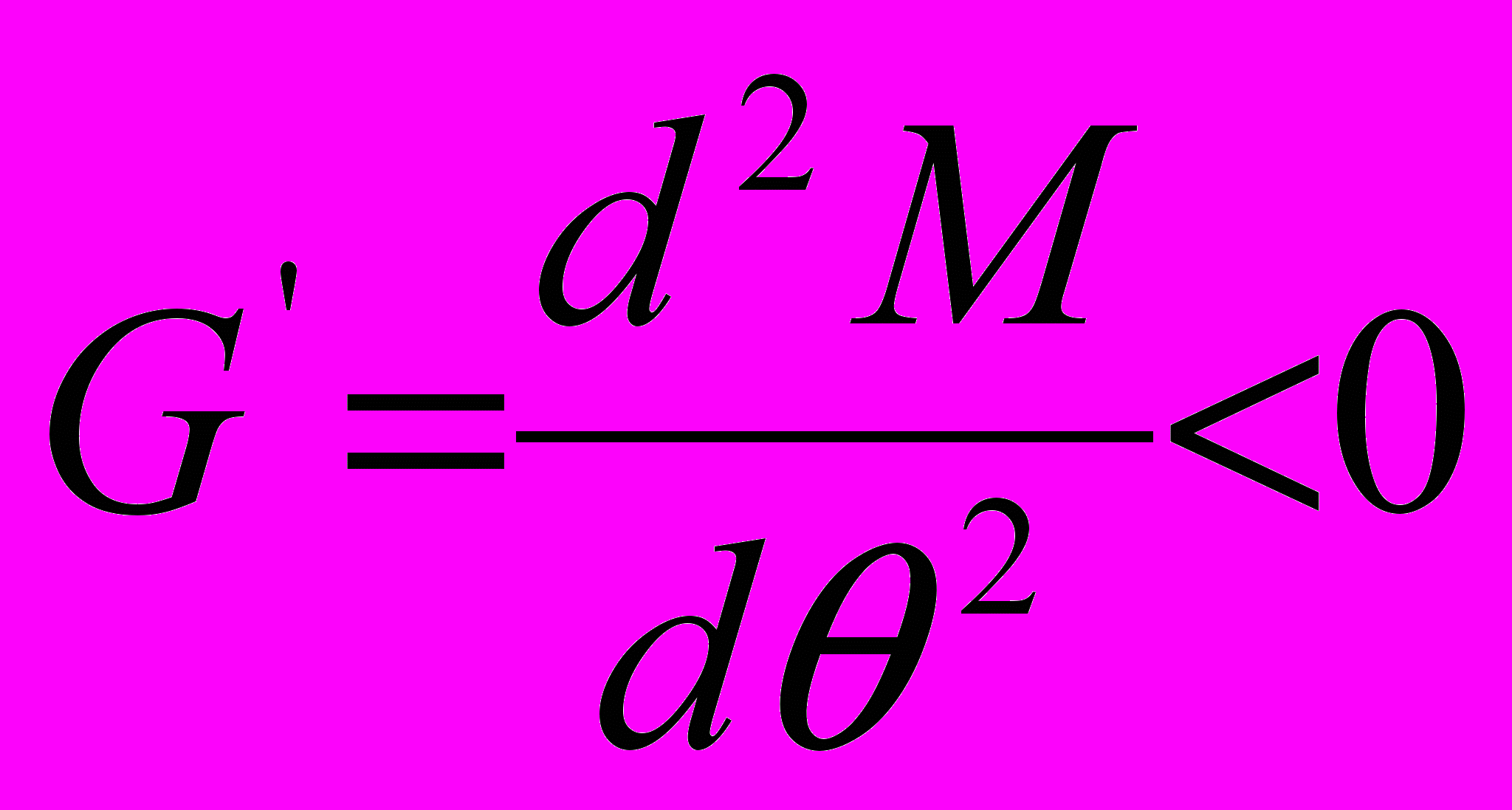
При прекращении воздействия на соединение крутящего момента целесообразно приложение ультразвуковых колебаний для увеличения фактической площади контактирования поверхностей, приводящего к возрастанию количества очагов возникновения адгезионных связей, что приводит к повышению прочности соединения.
Для определения состояния резьбовых соединений при сборке с ультразвуком перспективным является использование методов вибродиагностики, основанных на наличии корреляционных зависимостей динамических характеристик всего узла от контактного давления в соединениях и жесткости стыков. Изменение жесткости отдельных элементов приводит к изменению приведенной жесткости узла, а вместе с тем и присущих ему динамических характеристик искусственно создаваемого вибрационного поля: частот и амплитуд резонансных колебаний, показателей демпфирования, импедансных и фазовых соотношений.
Механические колебания используются одновременно для осуществления двух полезных функций: во-первых, возбуждение резонансных колебаний приводит к снижению трения, устраняет перекосы и деформации в процессе свинчивания; во-вторых, механические колебания являются источником информации о параметрах динамического качества колебательной механической системы.
Одной из динамических характеристик, используемых для определения качества процесса является коэффициент динамичности
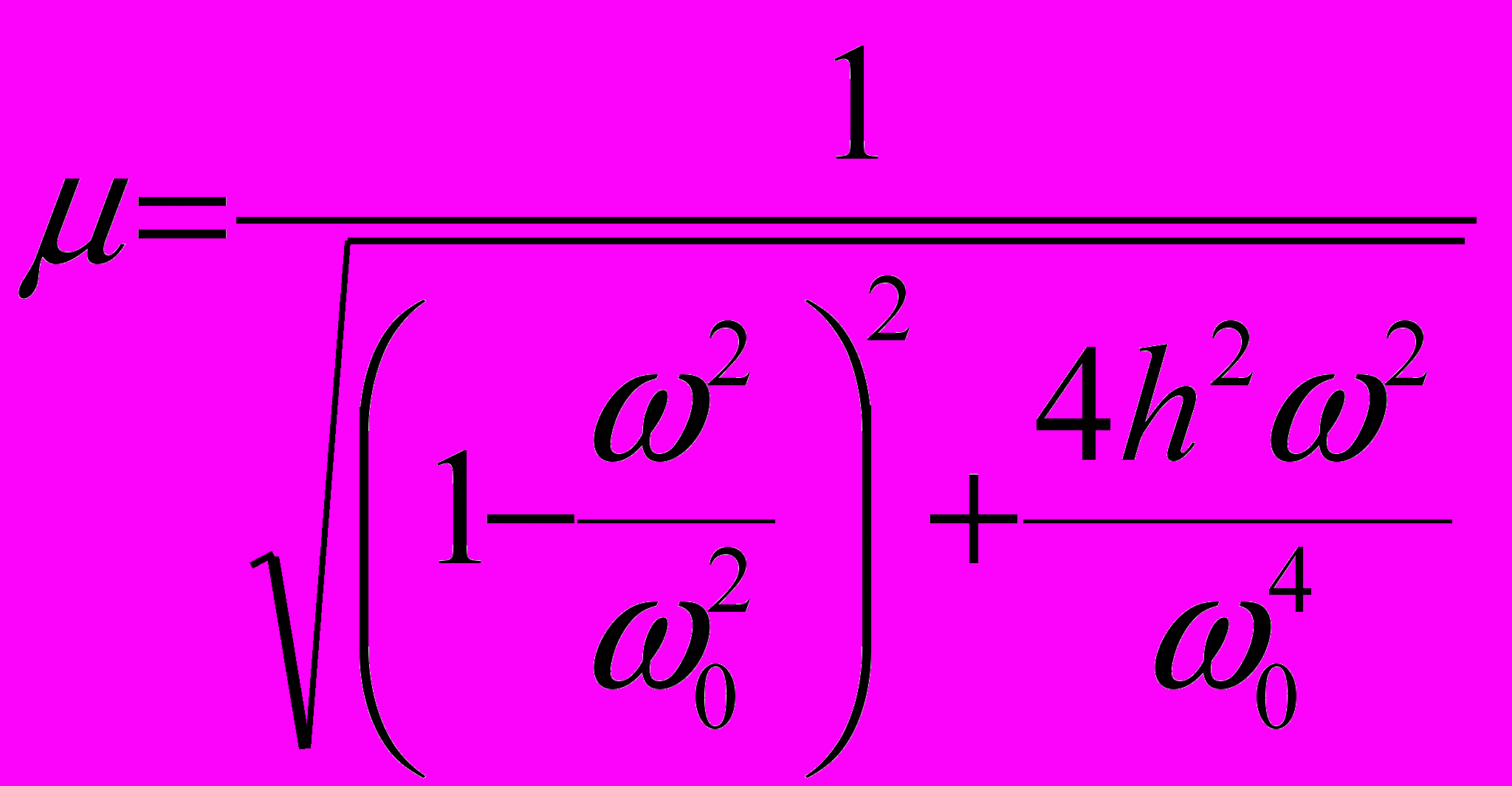
показывающий, во сколько раз амплитуда установившихся вынужденных колебаний больше перемещения
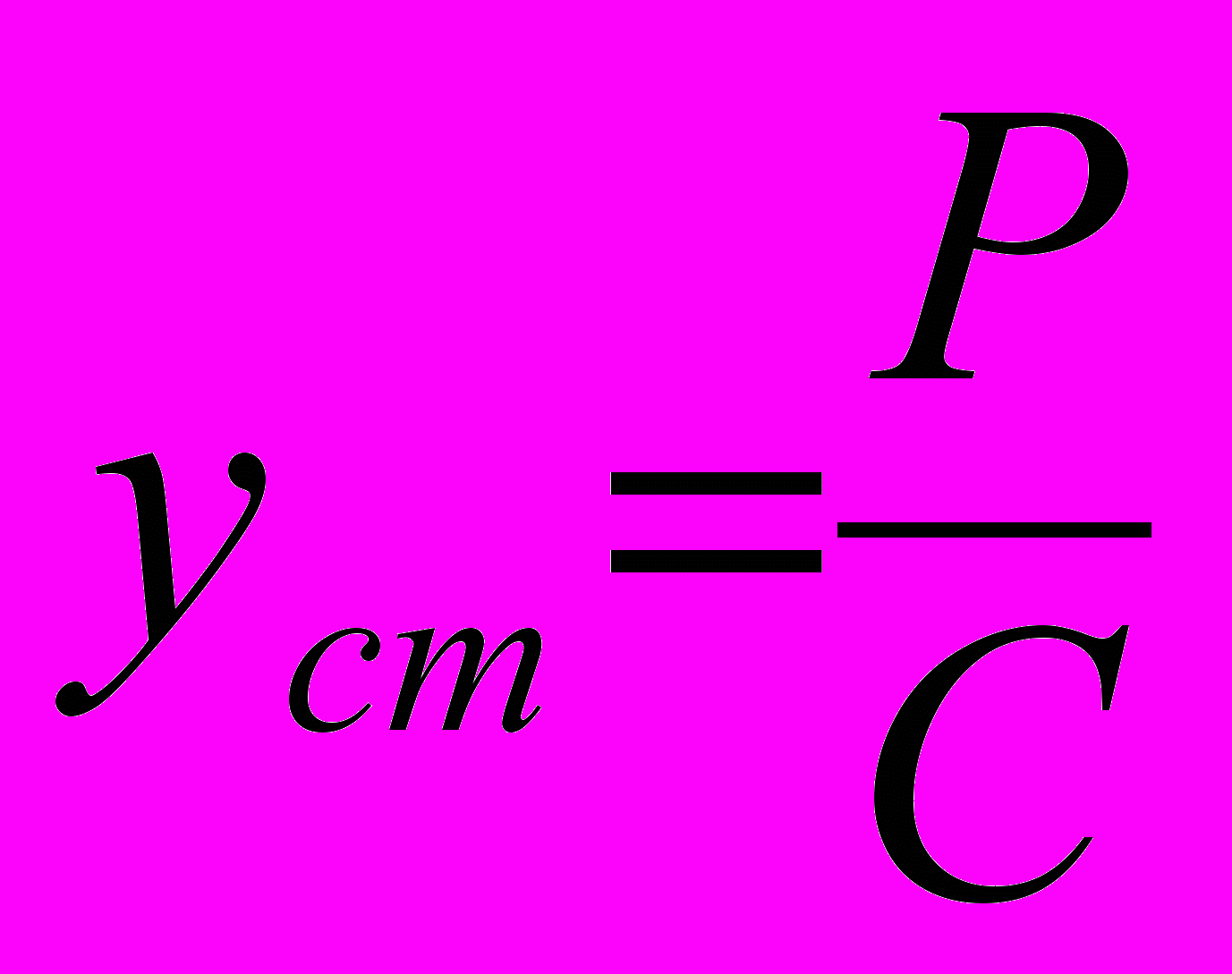
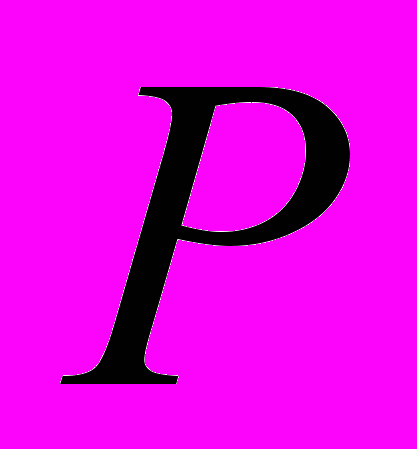
Рассмотренные параметры динамического качества колебательной механической системы (добротность и коэффициент динамичности) положены в основу разработанных патентнозащищенных способов ультразвуковой сборки резьбовых соединений.
На рис. 2 показана схема устройства для реализации предлагаемого способа.
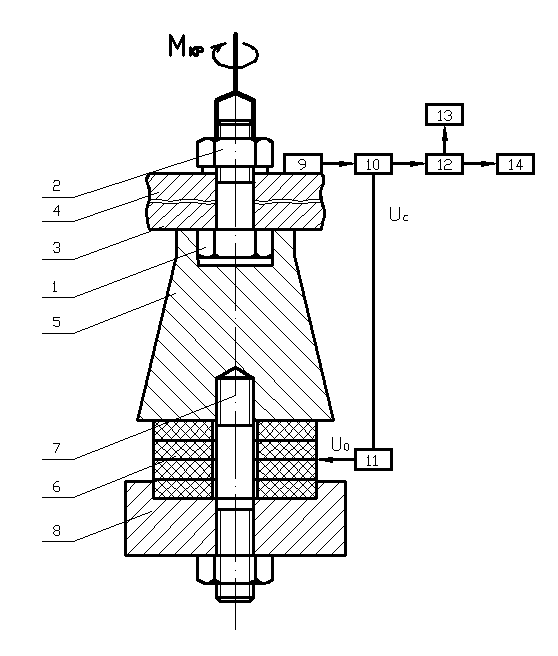
Рис. 2. Схема устройства для реализации способа сборки
В контролируемом изделии, состоящем из собираемых деталей 3 и 4, в процессе свинчивания возбуждают и принимают колебания, добиваясь резонанса. Колебания возбуждают пьезокерамическим преобразователем 6 и усиливают по амплитуде концентратором 5. Колебания, прошедшие через испытуемое соединение, воспринимаются вибродатчиком 9 и преобразуются в электрический сигнал, который после усиления в усилителе 10 поступает на вход блока возбуждения колебаний 11. С помощью усилителя 10 и блока возбуждения 11 подбирают условия, обеспечивающие возбуждение колебаний на собственной частоте контролируемого соединения. Учитывая, что амплитуда сигнала
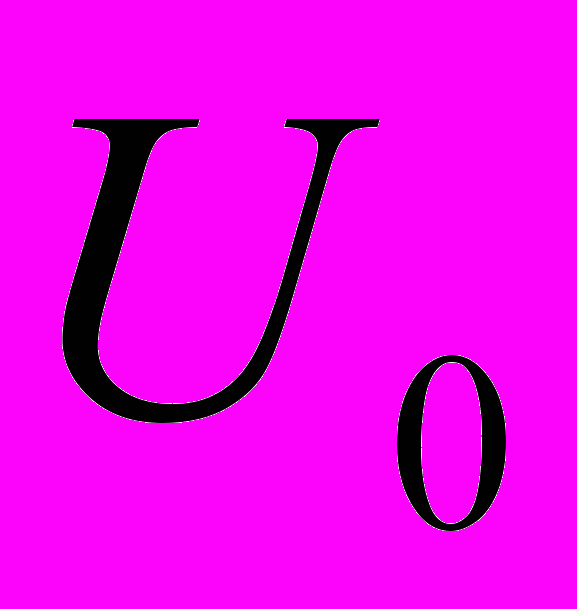
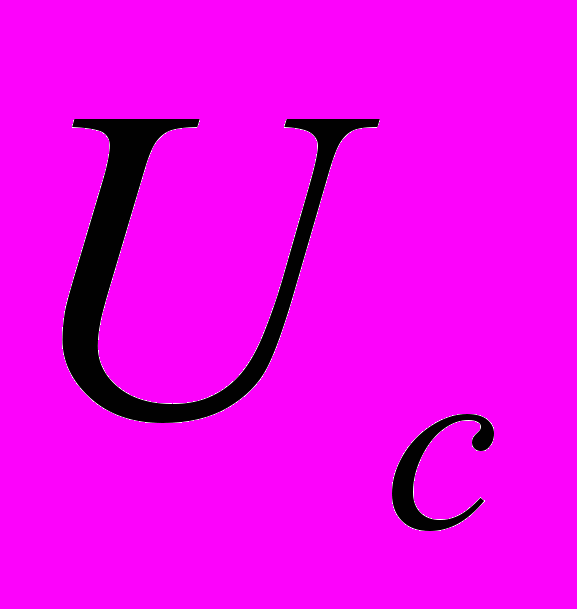
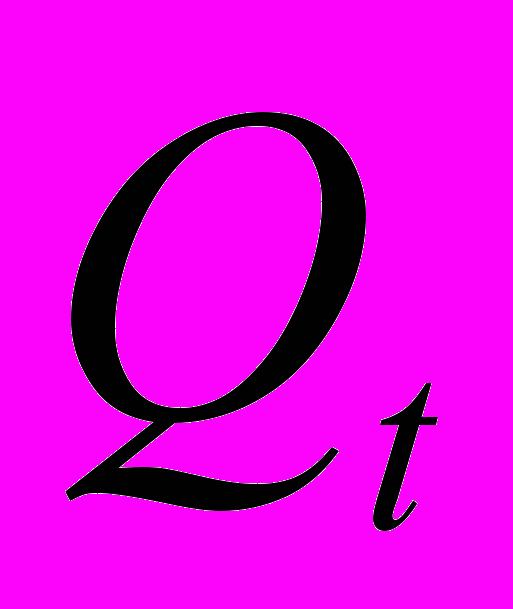
Предлагаемый способ сборки резьбовых соединений позволяет обеспечить гарантированное качество каждого соединения без ужесточения технологии изготовления и сборки деталей за счет соответствующих средств контроля.
В третьей главе на основе разработанной конечно-элементной модели в рамках программного комплекса ANSYS проводится компьютерный анализ напряженно-деформированного состояния резьбового соединения при ультразвуковой сборке, с учетом динамики процесса ультразвуковой сборки проведен модальный и частотный анализ компьютерной модели резьбового соединения c использованием данных, полученных при статическом анализе.
Применение ультразвуковых колебаний при сборке коренным образом изменяет характер поведения системы, переводя ее из статического в динамическое состояние, при котором необходим учет сил инерции и демпфирования. Общее уравнение движения системы представляется в виде:

где [ M] – матрица масс; [D] – матрица демпфирования; [K] - матрица жесткостей; {F(t)} - вынуждающая сила; {y} - вектор перемещений.
Моделирование процесса сборки резьбового соединения при воздействии ультразвуковых колебаний представляет собой сложную задачу, поэтому она была разбита на три более простые части, являющиеся частным случаем общего уравнения движения (3):
- моделирование напряженно-деформированного состояния (НДС) двухмерной и трехмерной модели резьбового соединения с использованием специального элемента PRETS179 (статический анализ);
- определение собственных форм и частот соединения (модальный анализ);
- определение реакции системы на вынуждающее гармоническое воздействие (частотный анализ).
При этом процесс затяжки рассматривался как совокупность четырех этапов расчета, на каждом из которых проводились перечисленные виды анализа. Каждому этапу соответствовала определенная сила затяжки.
Рассматривалось соединение двух деталей при помощи резьбового соединения болт-гайка. Эксперименты проводились для резьбы М8х1.25. Материал – сталь 45, модуль упругости, E=2·1011 Па, коэффициент Пуассона =0,3, предел текучести
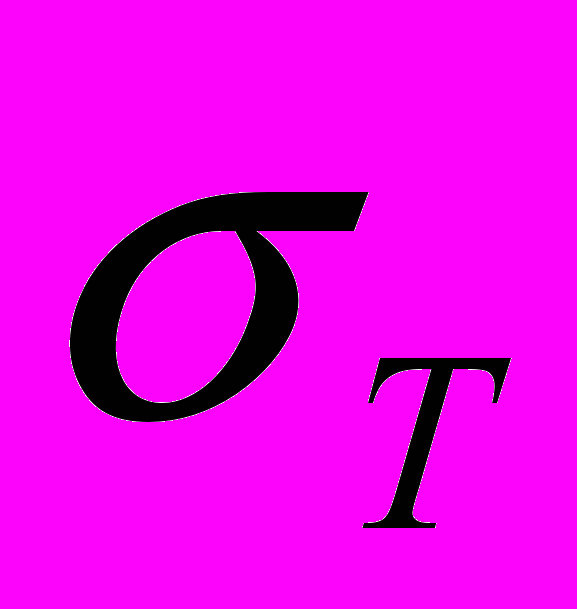
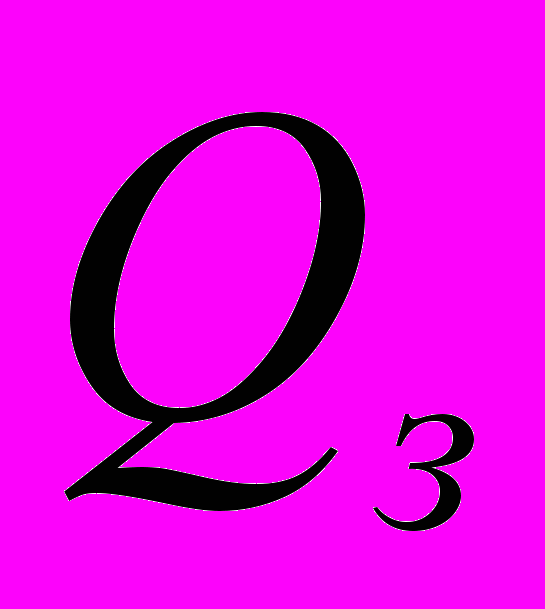
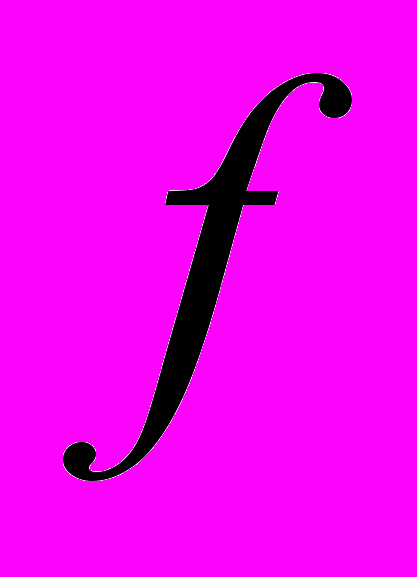
Проведение статического анализа необходимо для получения картины распределения НДС в резьбовом соединении и для определения значений контактной жесткости в стыках, необходимых для гармонического анализа.
При анализе результатов решения были получены значения контактной жесткости для стыков головки болта с деталью (контакт № 1), детали с деталью (контакт № 2) и стыка витков гайки и болта (контакт № 3), приведенные в таблице 1.
Таблица 1. Контактная жесткость
Сила затяжки, Н | Жесткость в контакте № 1, ![]() | Жесткость в контакте № 2, ![]() | Жесткость в контакте № 3, ![]() |
3034 | ![]() | ![]() | ![]() |
6069 | ![]() | ![]() | ![]() |
9102 | ![]() | ![]() | ![]() |
12137 | ![]() | ![]() | ![]() |
Модальный анализ. Состояние механической системы, работающей в условиях вибрационных нагрузок, определяется графическим изображением форм ее колебаний на собственных частотах. Форма колебаний линейной системы, колеблющейся с одной из собственных частот, является собственной формой или модой колебаний.
Информация о собственных частотах и формах колебаний необходима не только при изучении свободных колебаний, но и для анализа резонансных состояний, а также устойчивости замкнутой системы.
В программном комплексе ANSYS модальный анализ - это решение задачи о свободных, затухающих или незатухающих, колебаниях дискретной системы, которая описывается следующим уравнением движения:

Модальный анализ проводился для предварительно напряженных конструкций.
При модальном анализе в диапазоне частот от 0 до 40000 Гц для соединения, затянутого с силой 3034 Н было найдено три моды, данные о которых сведены в таблицу 2.
Таблица 2. Собственные частоты резьбового соединия, определенные при модальном анализе
Номер моды | Частота, Гц |
1 | 1695 |
2 | 17087 |
3 | 26418 |
Мода 1 – продольные колебания тела болта. Мода 2 – продольные колебания болта и скрепляемых деталей при неподвижной гайке. Мода 3 – поперечные колебания тела болта, при неподвижной головке болта. Также были найдены собственные частоты для других значений сил затяжки. Собственные формы для всех значений сил затяжки совпадали.
Гармонический анализ. Анализ гармонического воздействия используется для определения параметров установившегося движения линейной системы при синусоидальном силовом возбуждении. Этот вид анализа актуален при исследовании влияния нагрузок, меняющихся во времени по гармоническому закону.
Уравнение для этого вида анализа представляет собой специальный случай общего уравнения движения (5), в котором вынуждающая сила {F(t)} является синусоидальной функцией времени с известной амплитудой F и частотой :

Для определения в программе ANSYS гармонических параметров колебательной системы была построена динамическая модель, показанная на рис. 3. Так как затянутые резьбовые соединения характеризуются низким коэффициентом демпфирования, в построенной динамической модели он не учитывался.
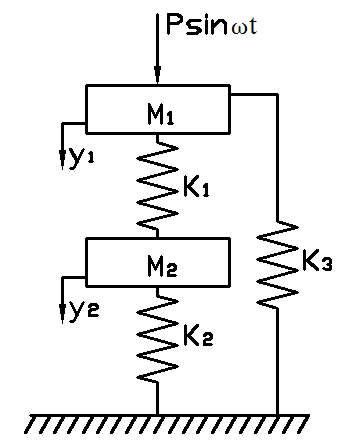
Рис. 3. Динамическая модель резьбового соединения
Дифференциальные уравнения движения полученной динамической модели имеют вид
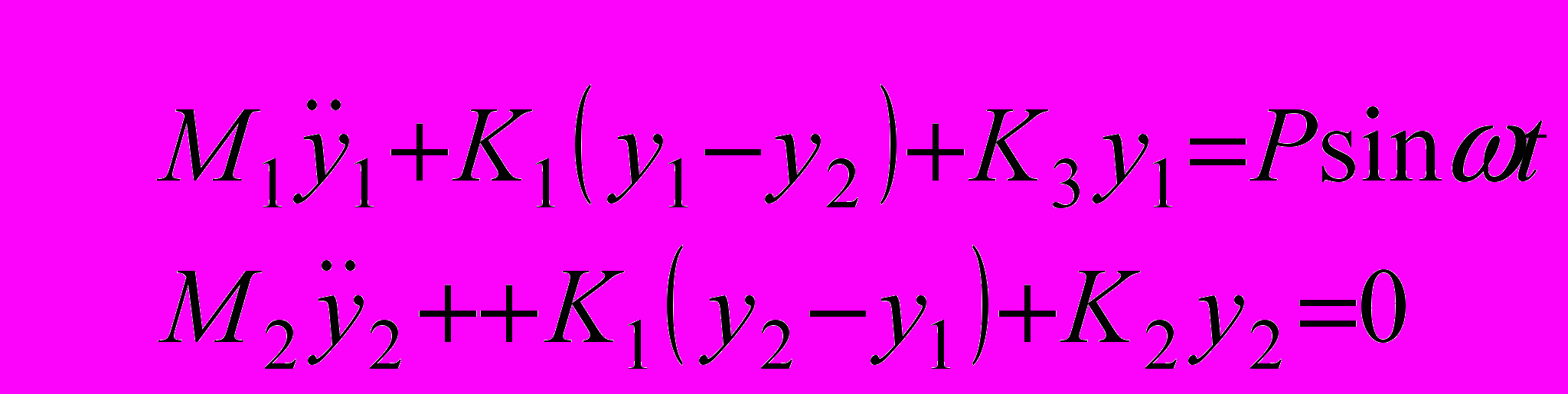
Принимая во внимание, что массы
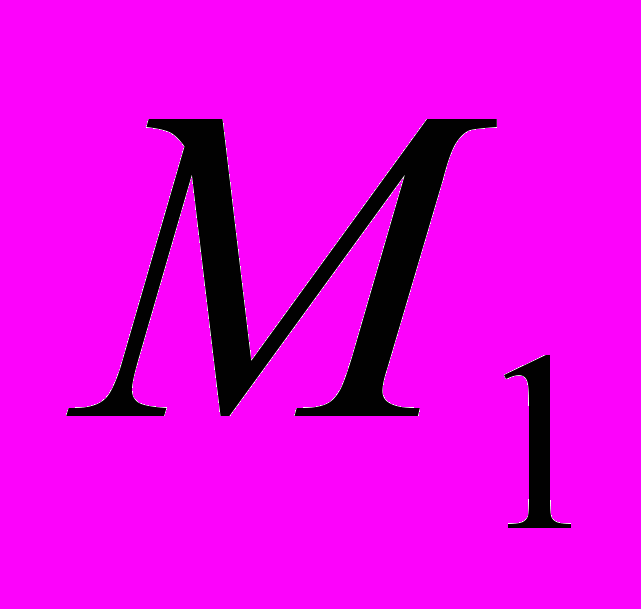
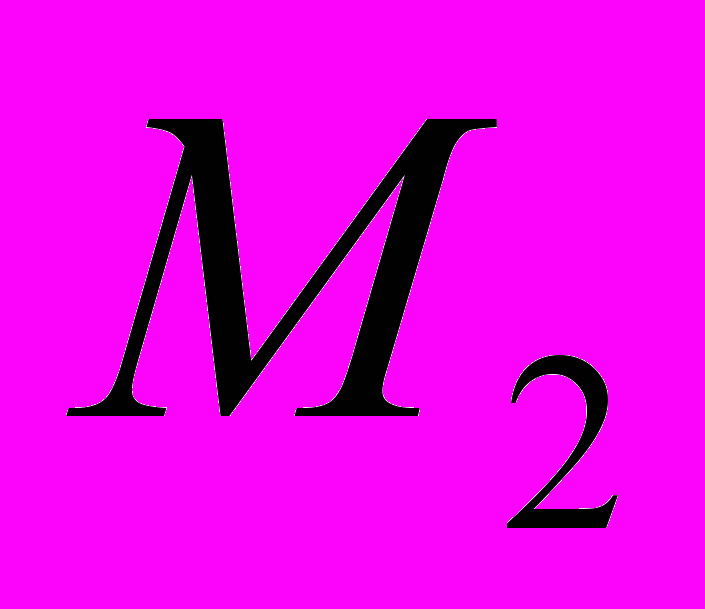
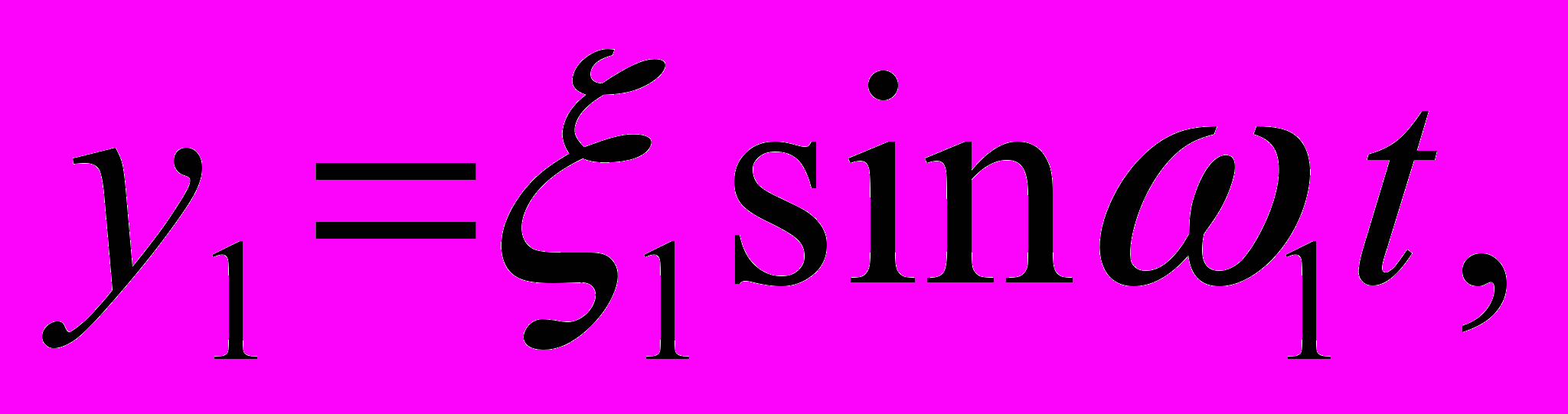
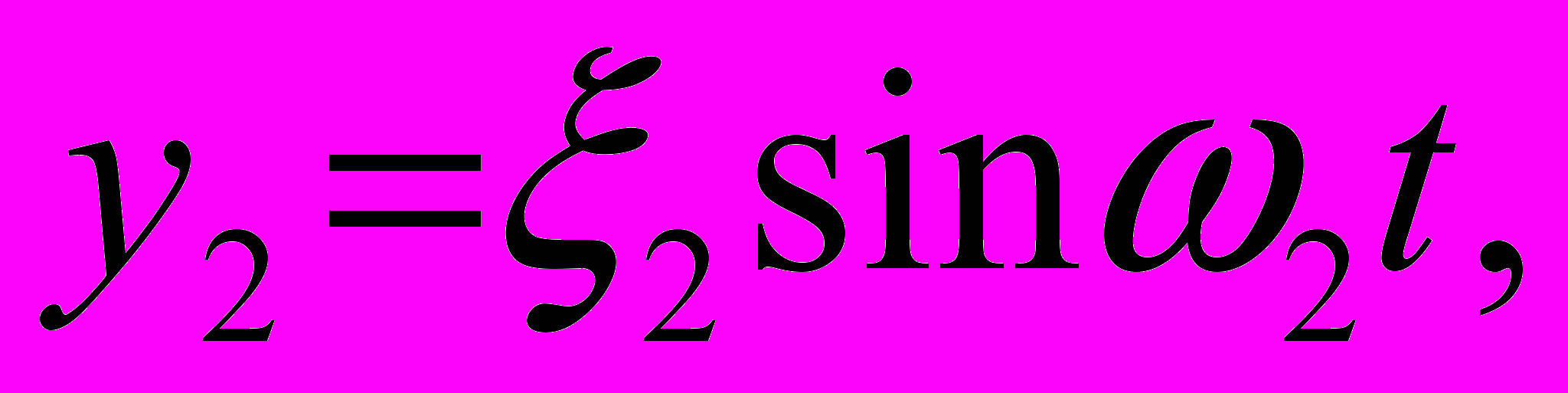
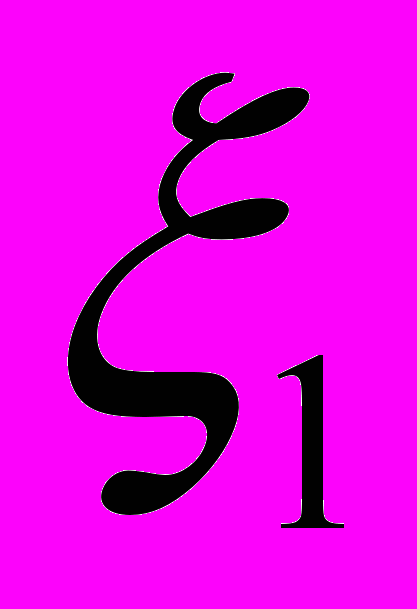
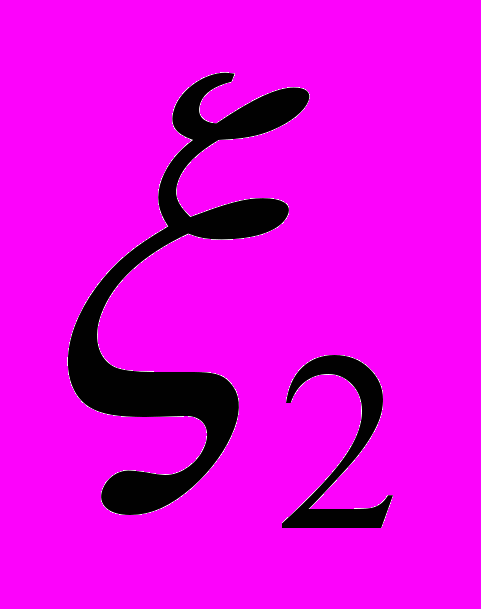
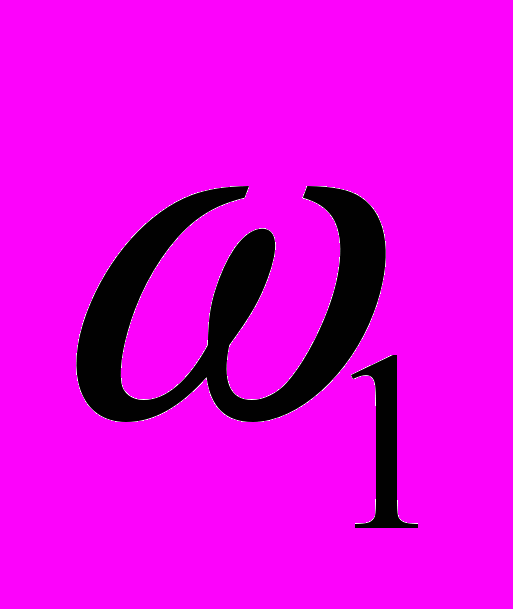
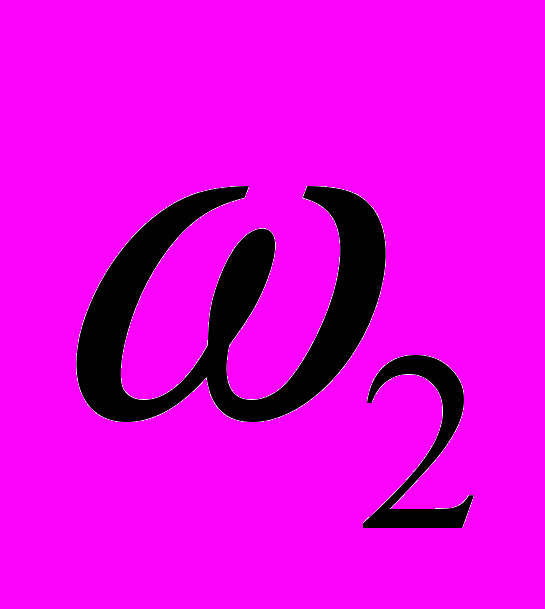
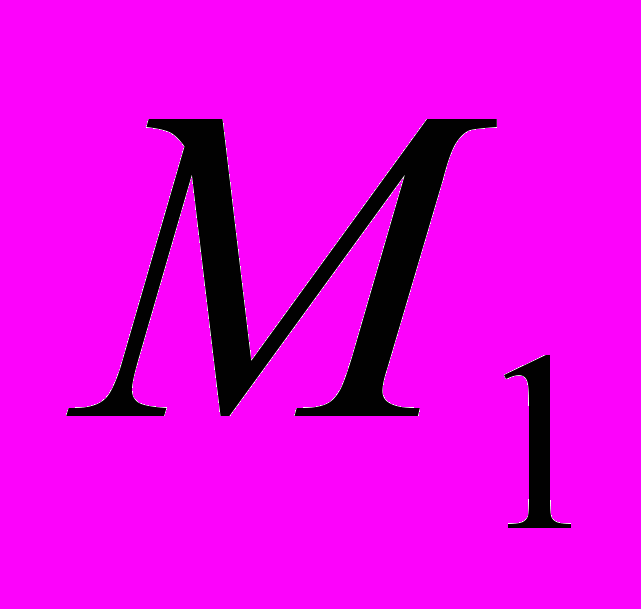
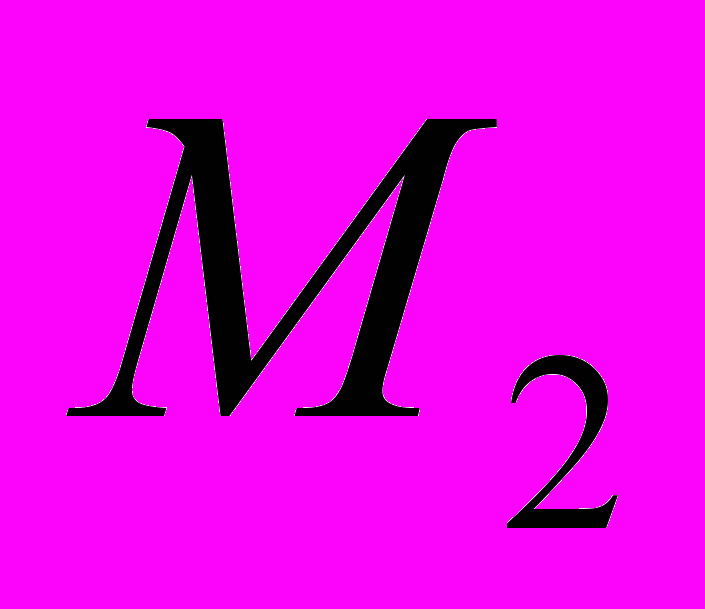
При гармоническом анализе резьбового соединения, проведенном в программном комплексе ANSYS, были получены амплитудно-частотные характеристики. На рис. 4 показана АЧХ для случая затяжки с силой 3034 Н.
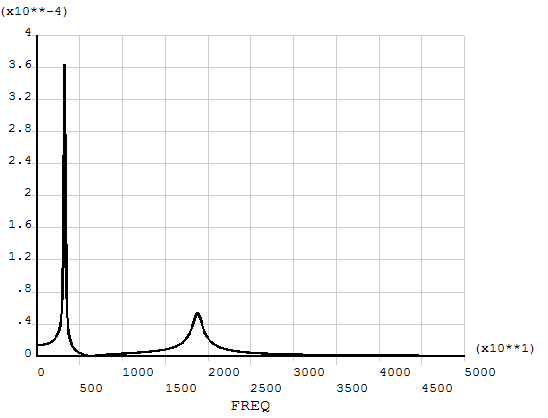
Рис.4. Амплитудно-частотная характеристика резьбового соединения затянутого с силой 3034 Н, полученная при моделировании в ANSYS.
При затяжке с силой 3034 Н система имеет два резонансных пика на частотах

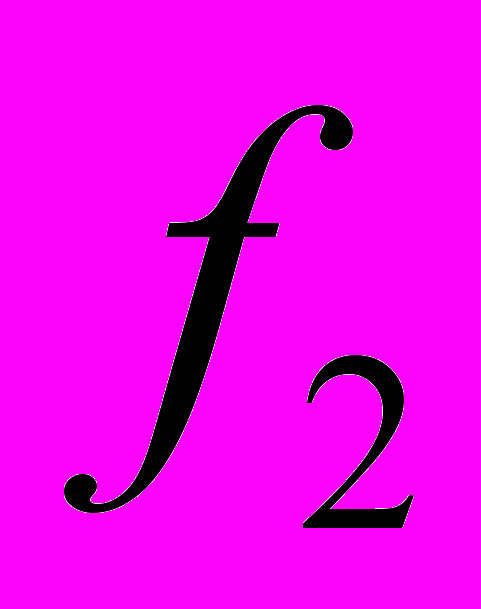
В таблице 3 приведены резонансные частоты для различных сил затяжки.
Таблица 3. Резонансные частоты, найденные при гармоническом анализе
Силы затяжки, Н | Частота первого резонансного пика, Гц | Частота второго резонансного пика, Гц |
3034 | 2500 | 18000 |
6069 | 3800 | 22900 |
9102 | 5070 | 31200 |
12138 | 7120 | 43800 |
На основе проведенных исследований можно сделать вывод, что при увеличении силы затяжки возрастает резонансная частота и снижается амплитуда перемещений в зоне резонанса, что характеризует повышение жесткости соединения.
Сравнение результатов модального и гармонического анализа показывает, что при одной силе затяжки различие между собственными частотами колебаний составляет 6 %.
В четвертой главе описаны проведенные экспериментальные исследования различных способов ультразвуковой сборки. В таблице 4 показан результат сравнения способов сборки с последовательным уменьшением амплитуды и с постоянной амплитудой колебаний
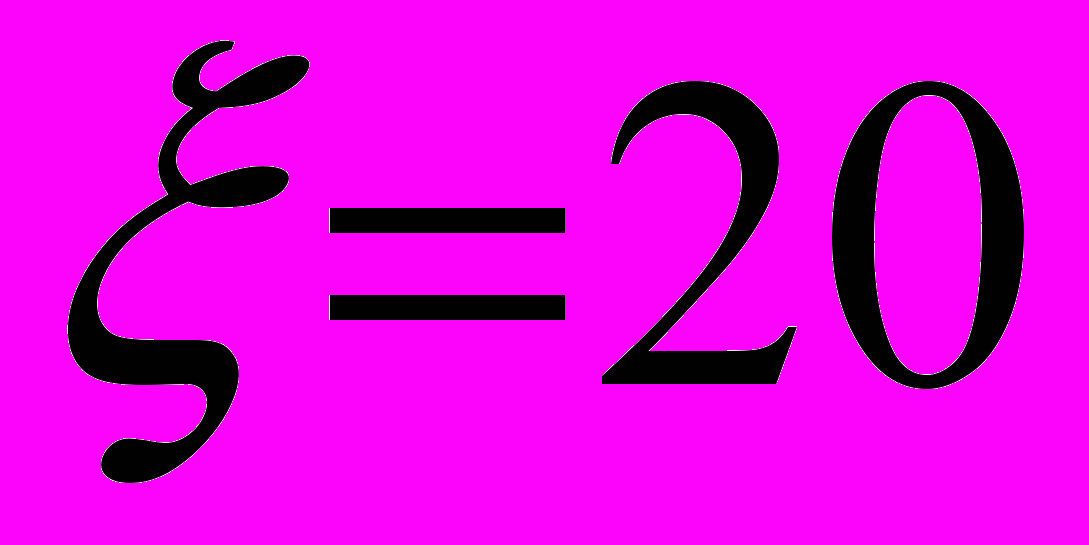
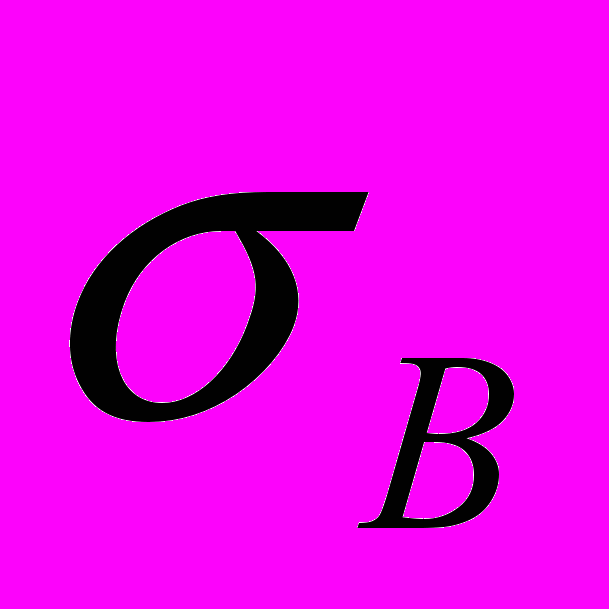
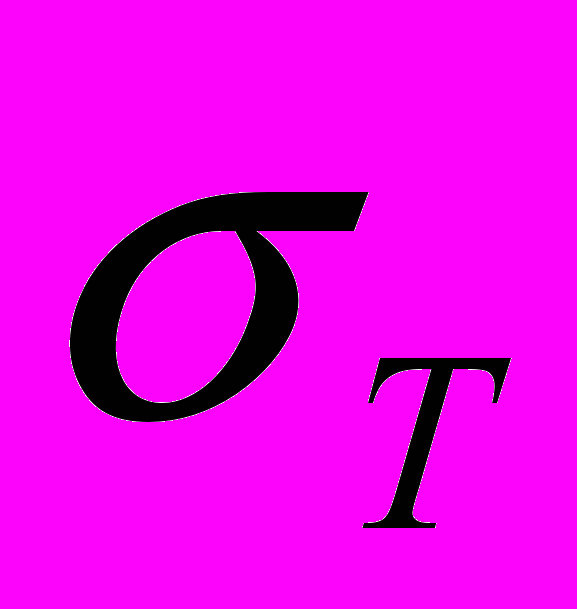
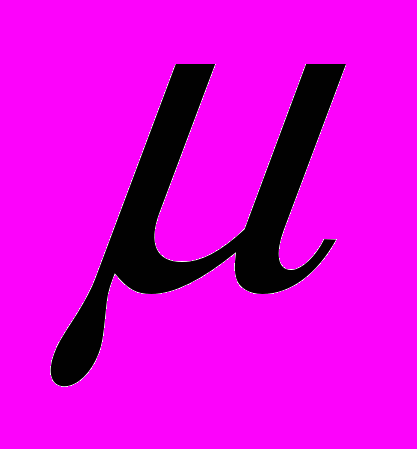
Таблица 4. Влияние способа ультразвуковой сборки на моменты развинчивания соединений.
Исследуемые болты | Болт М8х1,25 | Болт М10х1,25 | Болт М12х1,25 | |||
Моменты завинчивания и развинчивания | ![]() с УЗ | ![]() без УЗ | ![]() с УЗ | ![]() без УЗ | ![]() с УЗ | ![]() без УЗ |
С постоянной амплитудой | 20 | 22 | 42 | 44 | 48 | 52 |
С изменяющейся амплитудой | 36 | 39 | 61 | 65 | 72 | 75 |
Установлено, что при сборке с последовательно уменьшающимися амплитудами более полно используются прочностные свойства болтов, моменты развинчивания соединений, затянутых этим способом выше, чем соединений, затянутых с постоянной амплитудой ультразвуковых колебаний, на 45-75 %.
Кроме того, проведены исследования возможности использования частотных характеристик для определения качества затяжки соединения.
Исследования проводились в следующей последовательности.
Собираемые детали, закрепленные в тисках, затягивались болтом. Силу затяжки контролировали по удлинению болта, измеряемому микрометром.
- На собираемой детали крепился датчик вибрации KD 35, соединенный с аналого-цифровым преобразователем (АЦП) и генератором ультразвуковых колебаний. Затяжка производилась с приложением продольных ультразвуковых колебаний, возбуждаемых пьезокерамическим преобразователем. Система настраивалась на резонанс.
- Колебания соединения преобразовывались датчиком в электрический сигнал, который передавался в аналогово-цифровой преобразователь (АЦП), подключенный к ЭВМ. В АЦП сигнал преобразовывался в двоичный код, передавался в ЭВМ и там подвергался операциям двойного интегрирования и быстрого преобразования Фурье для получения амплитудно-частотных характеристик.
- Полученные при обработке сигналов характеристики соединения сравнивались и анализировались.
Сигналы, поступающие с датчика вибрации, анализировались в программном пакете Speaker Workshop 1.06, в котором были получены амплитудно-частотные характеристики сигналов для систем с различными силами затяжки.
На рис. 5 показан ультразвуковой сигнал резьбового соединения, затянутого с силой 3034 Н, во временной области.
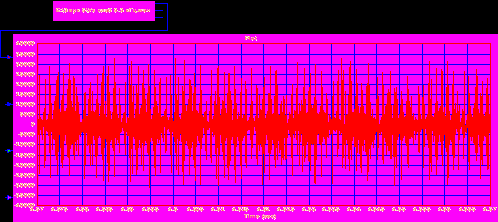
Рис. 5. УЗ сигнал системы, затянутой с силой 3034 Н
При проведении над сигналом во временной области быстрого преобразования Фурье были получены амплитудно-частотные характеристики (АЧХ) систем. На рис. 6 показана амплитудно-частотная характеристика (АЧХ) системы, затянутой с силой 3034 Н.
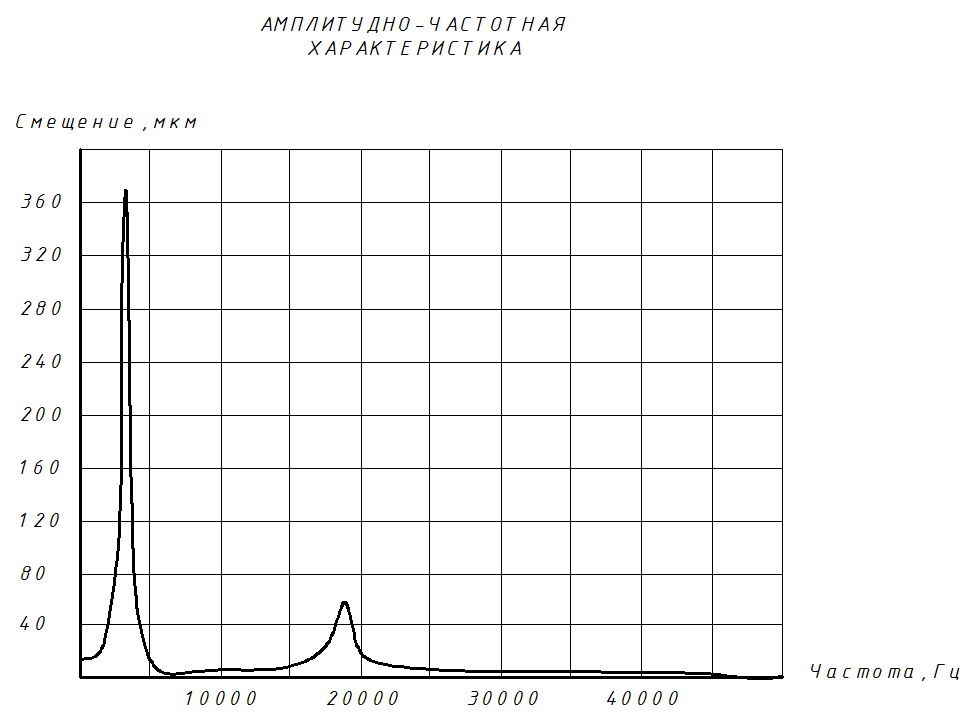
Рис. 6. Амплитудно-частотная характеристика соединения, затянутого с силой 3034 Н, полученная при экспериментальном исследовании
Собственные частоты системы
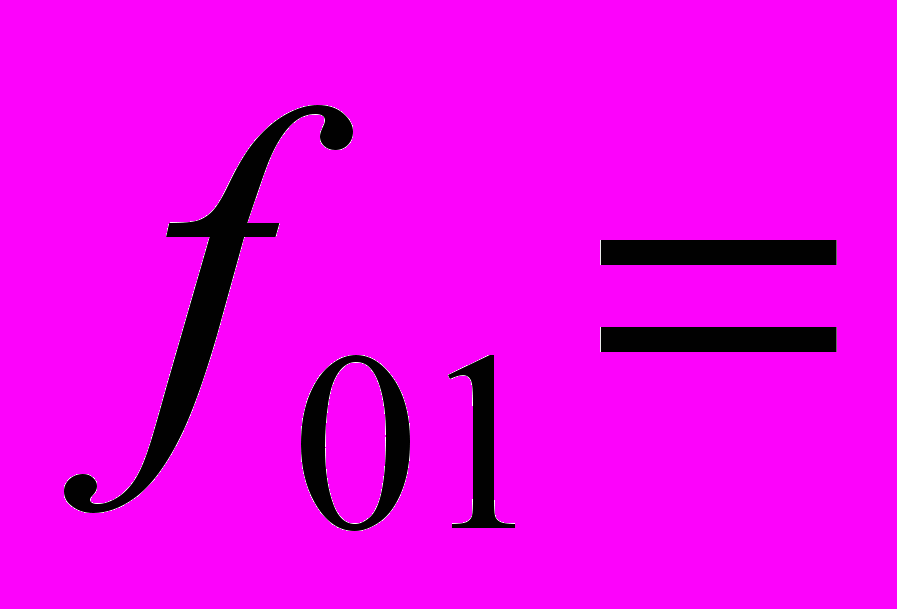
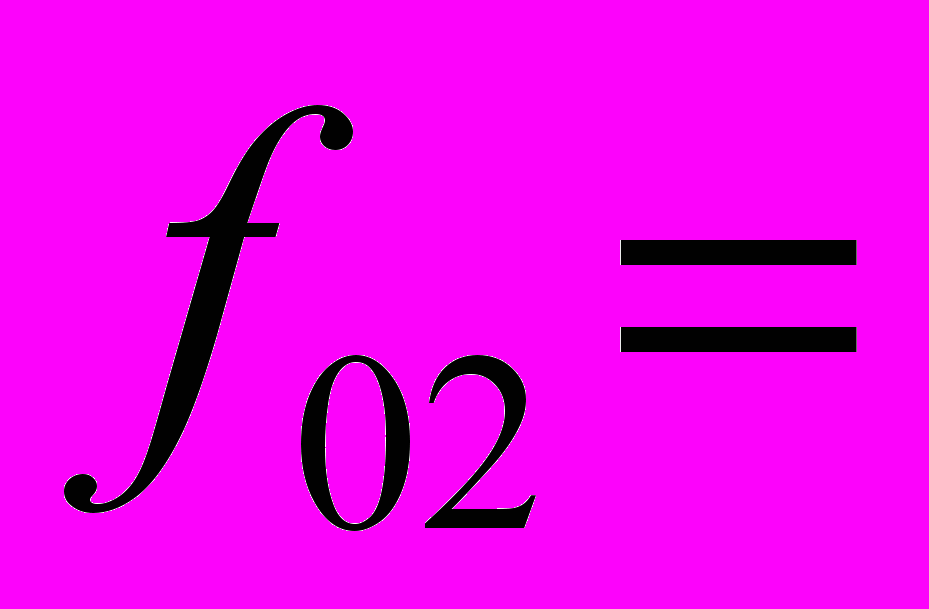
В табл. 5. приведены резонансные частоты для различных сил затяжки.
Сравнение АЧХ, полученных экспериментальным путем, с частотными характеристиками, вычисленными при моделировании в ANSYS, выявило расхождение между значениями их собственных частот в 8 %.
АЧХ, полученные экспериментально, при невысокой силе затяжки имеют большую ширину полосы пропускания, чем АЧХ, вычисленные при моделировании. При возрастающих силах затяжки различие между ними уменьшается, что объясняется уменьшением демпфирования в системах с высокой жесткостью.
Таблица 5. Экспериментально полученные резонансные частоты
Силы затяжки, Н | Частота первого резонансного пика, Гц | Частота второго резонансного пика, Гц |
3034 | 2720 | 18400 |
6069 | 3620 | 22630 |
9102 | 5140 | 37560 |
12138 | 7370 | 44100 |
Выполненные исследования показали возможность оценки динамических характеристик соединения при возбуждении ультразвуковых резонансных колебаний.
Разработанные технологии и оборудование были апробированы и внедрены на ОАО «Завод Магнето» при сборке ротора магнето с муфтой.
При применении ультразвуковой сборки была произведена замена специальных крепежных деталей, стоимость производства которых составляет от 2 % до 3 % от себестоимости изделий, на гайку М8-1.25 ГОСТ 5915-70. Проведенные испытания показали, что процент брака из-за самоотвинчивания снизился с 4 % до 0,1 %.
ОБЩИЕ ВЫВОДЫ
В результате комплексных теоретико-экспериментальных исследований решена актуальная задача, направленная на дальнейшее повышение эффективности сборки и повышения качества резьбовых соединений с применением ультразвуковых колебаний.
- Исследованы особенности процесса ультразвуковой сборки резьбовых соединений, с учетом которых разработана совокупность моделей, адекватно отражающих связь режимов ультразвуковой сборки с показателями эксплуатационных свойств резьбовых соединений.
- На основе выявленных особенностей механизма формирования контактных связей при ультразвуковой сборке обоснован алгоритм повышения эффективности ультразвуковой сборки резьбовых соединений с учетом изменений характеристик трения и прочности деталей, который позволяет управлять формированием контактных связей в соединении за счет введения дополнительного вибрационного воздействия и контроля динамических характеристик получаемой системы.
- Разработанные конечно-элементные статические и динамические модели резьбовых соединений, модели формирования напряженно-деформированного состояния соединения в условиях ультразвуковых воздействий дают возможность обоснованно подходить к проектированию и конструированию соединений.
- Синтезированы и исследованы в программном комплексе ANSYS динамические модели сборки резьбовых соединений с учетом дополнительных ультразвуковых воздействий, включающие модели собственных форм и частот колебаний болтовых и винтовых соединений, резонансные модели резьбовых соединений, позволившие провести исследование особенностей деформирования резьбовых соединений в динамических условиях.
- Показана эффективность использования колебательных воздействий, как в технологических, так и в диагностических целях в качестве дополнительного источника оперативной информации о характере динамических процессов, протекающих в формируемом соединении. В качестве динамических параметров используются частота колебаний, коэффициент динамичности и добротность.
- Разработан способ динамического контроля качества резьбовых соединений при ультразвуковой сборке, основанный на анализе резонансных свойств механической колебательной системы, который позволяет проводить контроль качества соединения непосредственно в процессе сборки.
- На основе проведенных исследований разработан и реализован способ сборки резьбовых соединений, позволяющий управлять формированием контактных связей в соединении за счет введения дополнительного вибрационного воздействия и контроля динамических характеристик получаемой системы.
- Разработан комплекс конструкторско-технологических решений и рекомендаций, направленных на повышение эффективности практического использования ультразвука при сборке резьбовых соединений, представлены устройства, оборудование и практические рекомендации для ультразвуковой сборки и контроля качества формируемых соединений.
НАУЧНЫЕ ПУБЛИКАЦИИ ПО ТЕМЕ ДИССЕРТАЦИИ
- Штриков Б.Л., Шуваев И.В. Повышение качества резьбовых соединений в условиях ультразвуковых воздействий / «Высокие технологии в машиностроении»: Материалы международной научно-технической конференции. Самара, 2004. – С.117
- Штриков Б.Л., Шуваев И.В. Обеспечение качества сборки резьбовых соединений/ «Обеспечение и повышение качества машин на этапах их жизненного цикла»: Материалы 5-ой международной научно-технической конференции, Брянск, БГТУ, 2005. – С.190
- Шуваев И.В. Применение ультразвуковых колебаний для формирования регулярных микрорельефов поверхностей/ Наука. Технологии. Инновации // Материалы докладов Всероссийской научной конференции молодых ученых в 6-ти частях. Часть 6. Новосибирск. 2003. – С.35
- Шуваев И.В. Моделирование динамических характеристик болтового соединения средствами программного комплекса ANSYS / «Высокие технологии в машиностроении»: Материалы международной научно-технической конференции. Самара, СамГТУ , 2005. – С.149
5. Штриков Б.Л., Шуваев И.В. Управление процессами формирования регулярных микрорельефов на контактирующих поверхностях с применением ультразвуковых колебаний / Материалы международной научно-технической конференции «Высокие технологии в машиностроении»: Самара. 2002. – С.255–257.
6. Штриков Б.Л., Шуваев В.Г., Шуваев И.В. Обеспечение надежности и качества механических соединений при ультразвуковой сборке / Актуальные проблемы надежности технологических, энергетических и транспортных машин. Материалы международной конференции. Самара. 2003. – С.127-129.
7. Шуваев В.Г., Шуваев И.В. Отделочно-упрочняющая обработка цилиндрических поверхностей с применением ультразвука / Тезисы докладов XXIX Самарской областной научной конференции. Часть I. «Общественные, естественные и технические науки»: Самара. 2003. – С.144
8. Патент РФ №2228256, МПК В 25 В 21/00. Способ сборки резьбовых соединений / Шуваев В.Г., Штриков Б.Л., Шуваев И.В. Опубл. в БИ № 10.05.2004.
9. Решение о выдаче патента на изобретение от 13.02.2006 по заявке №2004132740/02 МПК В 25 В 21/00. Способ сборки резьбовых соединений / Шуваев В.Г., Штриков Б.Л., Шуваев И.В.
10. Патент РФ на полезную модель № 31350, 2003 г. Центробежный ударный механизм / Штриков Б.Л., Шуваев В.Г., Папшев В.А., Кузнецов М.Б., Шуваев И.В.
11.Патент РФ на полезную модель № 31448, 2003 г. Стенд для виброударных испытаний изделий / Штриков Б.Л., Шуваев В.Г., Папшев В.А., Кузнецов М.Б., Шуваев И.В.
Тираж 100 экз. Заказ № 1030
Отпечатано на ризографе.
Самарский государственный
технический университет.
Отдел типографии и оперативной полиграфии.
443100, г. Самара, ул. Молодогвардейская, 244.