Выбор входных параметров для построения модели процесса резания на основе нейронных сетей
Вид материала | Документы |
СодержаниеСписок литературы |
- Заочный Государственный Университет Внастоящее время все большее применение в разработке, 64.47kb.
- Нейрокомпьютерная техника: Теория и практика, 2147.23kb.
- Ю. Н. Шунин Лекции по теории и приложениям искусственных нейронных сетей,Рига,2007, 190.96kb.
- Конспект лекций Представление знаний в информационных системах Лекция№1, 194.32kb.
- Я. А. Трофимов международный университет природы, общества и человека «Дубна», Дубна, 71.95kb.
- Исследование сил резания, возникающих при точении, фрезеровании, сверлении, 394.69kb.
- Курсовая работа по дисциплине " Основы систем искусственного интеллекта" Тема: Опыт, 903.59kb.
- Особенности применения нейронных сетей в курсе «Интеллектуальные информационные системы», 82.99kb.
- Критерии оценки эпизоотической ситуации и прогнозирование заболеваемости крупного рогатого, 359.75kb.
- Классификация и характеристика движения резания. Режимы резания. Качество обработанной, 88.77kb.
УДК 004.896:621.9
Выбор входных параметров для построения модели процесса резания на основе нейронных сетей
Коновалова Т.В.
Харьковский национальный технический университет „ХПИ”
В статье анализируется проблема группирования и выбора сигналов, полученных в результате измерения показателей процесса резания, также представлен подход к группированию сигналов для обучения нейронной сети, а также основные аспекты конструирования нейронной сети для решения задач теории резания.
Постановка задачи
Современное машиностроение характеризуется ростом автоматизации при снижении себестоимости обработки и повышении качества продукции. Повышение качественных показателей деталей, изготавливаемых на металлорежущих станках, идет по нескольким направлениям: интенсификация рабочих процессов, совершенствование конструкции режущих инструментов, разработка схем высокоскоростной и комбинированной обработки. Определение и назначение оптимальных режимов обработки осуществляются либо с помощью эмпирических статических моделей процесса, которые применимы в узких рамках технологических условий, либо посредством проведения предварительных технологических испытаний, которые требуют значительных временных и материальных затрат. Применение математических моделей позволяет прогнозировать процессы обработки. Множество имеющихся на сегодняшний день математических моделей не всегда позволяет использовать накопленную информационную базу знаний, собранную в результате множества лабораторных измерений и технических испытаний. Для создания моделей используются аналитические, числовые и вероятностные методы.
Целью исследования в данной работе являются исследования возможности применения метода нейронных сетей к решению задачи технологического обеспечения изготовления машиностроительных изделий. Создание модели процесса резания с использованием искусственных нейронных сетей дает возможность применить накопленный исследовательский опыт, а также эмпирические зависимости. База знаний для процесса резания применяется для обучения сети, которая впоследствии может быть использована как адаптивная модель управления и контроля над процессом резания, подбором оптимальных режимов резания, прогнозированием износа инструмента.
Выбор параметров входа-выхода для построения модели резания
Эффективность диагностики и оптимизации процесса резания целиком и полностью определяется информативностью используемых параметров. Входными параметрами для искусственных нейронных сетей могут быть сигналы и их свойства. Сигналы могут характеризоваться электрическими переменными, скоростью их изменения и связанной с ними энергией и мощностью.
В табл. 1 сведены основные физические явления в процессе резания, измеряемые при помощи датчиков величины, параметры сигнала и возможное использование параметров для определения результатов обработки резанием. В зависимости от вида обработки (черновая, чистовая, прецизионная) те или иные параметры сигналов дают представление о явлениях и процессах, происходящих при резании, а также позволяют сделать заключение о качестве обработки.
Традиционное использование для этой цели изменения силы резания, температуры, крутящего момента на валу двигателя, тока двигателя, различные комбинации этих параметров в ряде случаев оказываются сложными в исполнении, неприемлемыми или недостаточно информативными и адекватными. В последние годы большое внимание привлекает перспектива акустической диагностики процесса резания. Высокая помехозащищенность акустических сигналов из зоны резания в области частот, превышающих частоты от шумов работающих агрегатов станка, обеспечивает получение надежной информации о таких важнейших параметрах обработки, как износ инструмента, качество поверхностного слоя детали, оптимальность режима резания.
Таблица 1 - Сигналы в процессе резания
Явление | Параметр сигнала | Определение |
Сила резания | Величина, изменение во времени, амплитуда сигнала | Износа, поломки инструмента, качества и формы поверхности |
Крутящий момент на шпинделе | Величина сигнала, изменение во времени | Износа, внезапных поломок инструмента |
Температура в зоне резания | Величина сигнала | Износа, внезапных поломок инструмента, качества поверхности |
Вибрации, акустические сигналы | Длина, частота, период колебания, скорость волны, спектр, интенсивность | Качества поверхности, износа инструмента |
В качестве входных параметров могут также выступать и другие, приведенные в табл. 2 факторы.
Таблица 2 - Факторы, влияющие на параметры процесса резания
Фактор | Параметр |
Материал детали, режущего инструмента, покрытия режущего инструмента | Структура, текстура, твердость, прочность на растяжение, прочность на сжатие, прочность на разрыв, ударная вязкость и хрупкость, усталость, ползучесть, кристаллическая структура, скольжение и дислокации, химический состав, коэффициент трения, теплопроводность, склонность к адгезии, внутреннее напряжение |
Геометрия резца | Задний угол, передний угол, угол наклона режущей кромки, главный угол в плане, угол заострения, вспомогательный угол в плане, угол при вершине, угол закругления |
Смазывающе-охлаждающая жидкость | Химический состав, коэффициент трения, теплопроводность |
Станок | Жесткость станка |
Другие влияющие величины | Условия контакта режущего инструмента с деталью, трение в зоне контакта, механизм образования стружки, глубина резания, подача, скорость резания |
Конфигурации пары вход-выход для определенных заданий
Благодаря тому, что искусственные нейронные сети имеют дело с нелинейными зависимостями, с большим количеством параметров и недостающими данными, они могут применяться для моделирования процессов резания. Благодаря обучению, ИНС могут использоваться даже в случаях, когда нет точных данных о взаимосвязях между различными параметрами процесса. Предлагается рассмотреть пять возможных вариантов применения ИНС в резании материалов (табл. 3).
Одним из примеров применения ИНС является планирование качества изделия [1-3]. При точении детали необходимо получить требуемую шероховатость поверхности. Входным вектором сети является ряд параметров для определения наиболее целесообразного технологического процесса.
Следующим примером применения ИНС является получение требуемой шероховатости заданным инструментом [1-3]. Входы ИНС при этом - вид обработки, условия резания, тип крепления заготовки, ее материал, выходы - параметры, определяющие режущий инструмент.
Третья задача – контроль процесса резания при заданной силе резания и мощности. Измеренные значения этих параметров могут использоваться для определения текущего состояния процесса резания. Оператор станка с ЧПУ должен выбрать соответствующие режимы резания для получения требуемого качества поверхности.
Четвертая задача сходна с третьей, но при этом оператор может изменять только подачу и глубину резания при установленной скорости резания.
Пятой задачей является классификация стружки [4].
Таблица 3 - Конфигурация пары вход-выход в зависимости от задания
Задание | Параметр на выходе | Параметр на входе |
Планирование качества | Шероховатость обработанной поверхности | Параметры режущего инструмента: угол резания, радиус закругления, параметры процесса резания: подача, глубина резания, скорость резания, расчетные величины: сила резания, мощность, стойкость инструмента |
Получение необходимой шероховатости определенным инструментом | Шероховатость обработанной поверхности, угол резания, радиус закругления | Подача, глубина резания, скорость резания, сила резания, мощность, стойкость инструмента |
Контроль процесса резания при измерении силы резания и мощности | Подача, глубина резания, скорость резания, стойкость инструмента | Шероховатость обработанной поверхности, угол резания, радиус закругления, сила резания, мощность |
Контроль процесса резания при измерении силы резания и мощности | Подача, глубина резания, скорость резания, стойкость инструмента. | Шероховатость обработанной поверхности, угол резания, радиус закругления, сила резания, мощность, скорость резания |
Классификация стружки | Тип стружки | Подача, глубина резания, скорость резания, сила резания, мощность |
Модель резания на основе нейронных сетей
Самый простой подход при построении модели оптимизации процесса резания - это использование всех входных параметров для построения одной искусственной нейронной сети и ее обучение на основе существующей базы знаний. Для данного подхода, даже для упрощенной модели, необходим набор параметров для полного описания модели. Объем работы колоссальный, и при этом нет возможности уменьшить его за счет малозначимых параметров. Существует вероятность того, что после выполнения большой работы получится модель, применимая только в жестких рамках упрощений и допущений, принятых при исходной схематизации объекта. Целесообразно разбить модель на подмодели, использовать смешанный подход для решения задачи, создать упрощенную нейронную сеть-модель процесса, которую можно подвергнуть анализу и выявить степень влияния параметров модели на процесс резания, модель заготовки.
Информационная модель процесса представляет собой множество взаимосвязанных сущностей (вид обработки, свойства обрабатываемого и инструментального материалов, геометрия режущей части инструмента, цели управления и др.) и их атрибутов. Сложные физические явления, имеющие место в процессе лезвийной обработки, обусловили необходимость использования иерархических принципов построения системы управления процессом лезвийной обработки.
Нейронная сеть, обученная и построенная на базе знаний, в составе информационной управляющей системы обеспечивает достаточную гибкость управления любыми видами технологических процессов лезвийной обработки, такими, как точение, фрезерование, сверление и шлифование.
Обзор схем и видов нейронных сетей
На сегодняшний день ИНС широко применяются в адаптивном управлении, аппроксимации функционалов, создании экспертных систем, прогнозировании, процессах распознавания образов, в медицинской и технической диагностике, космической навигации и др. [5, 6]. ИНС уже успешно применяются в конструировании и оптимизации деталей. Дальнейшей областью их применения становится производство [7, 8]. Произведенный на основе литературных источников обзор наиболее распространенных схем нейронных сетей и возможных областей их применения для оптимизации процессов резания приведен в табл. 4.
Таблица 4 - Модели нейронных сетей
Название модели | Применение |
Многослойная нейронная сеть с обучением обратным распространениям ошибки | Классификация, аппроксимация функций, прогнозирование, управление |
Нейронная сеть с генетическим алгоритмом обучения | Классификация, прогнозирование |
Модель Хопфилда | Ассоциативная память, решение комбинаторных задач оптимизации |
Модели теории адаптивного резонанса | Категоризация |
Машина Больцмана | Классификация |
Сеть Кохонена | Классификация |
Модель Хемминга | Классификация, ассоциативная память, надежная передача сигналов в условиях помех |
Сеть встречного распространения | Ассоциативная память, сжатие данных (с потерями) |
Заключение
Подчеркивая важность точности моделей процесса при контроле технологического процесса, разработки и применения моделей процесса на основе ИНС, в статье был сделан акцент на конфигурацию входа - выхода общих моделей, которые могут удовлетворять требованиям точности моделирования. Было предложено совместное использование передовых технологий и обучения ИНС. Пользователю обычно известны некоторые параметры процесса, и задачей моделирования является определение других параметров с некоторыми ограничениями.
В работе представлены описание и возможность применения наиболее распространенных видов нейронных сетей и набор входных параметров для их обучения. При этом необходимо отметить, что все чаще применяется смешанный подход к использованию нейронный сетей, то есть задача разбивается на подзадачи, и для каждой подзадачи выбирается оптимальная конфигурация сети и алгоритма обучения.
На основе анализа публикаций по данной тематике можно сделать выводы о возможности применения нейронных сетей в области резания материалов:
- сбор и обработка информации, поступающей с датчиков системы;
- выдача заключения о возможности продолжения обработки, изменения параметров резания, оптимизация режимов резания;
- прогнозирования стойкости инструмента;
- прогнозирование качества поверхности и контроль;
- рекомендации по установке, типам датчиков;
SUMMARY
In the article is examined the problem of grouping and selection of signals’ parameters, obtained from the measurement of cutting process. As well, the paper presents the grouping of signals’ parameters for learning and tuning of neuron networks, it gives some possible schemes of construction and the structure of neuron networks applied in the cutting processes.
СПИСОК ЛИТЕРАТУРЫ
- Özel T., Karpat Y. Predictive Modeling of Surface Roughness and Tool Wear in Hard Turning Using Regression and Neural Networks // International Journal of Machine Tools and Manufacture. – 2005. -Т.45. - С. 467-479.
- Lieh-Dai Yang, Joseph C. Chen. An In-Process Surface Roughness Recognition System in End Milling Operations // The Journal of Technology Studies. – 2004. -T.30. – С. 98-103.
- Jemielniak К. Tool Wear Monitoring by Means of Artificial Neural Networks // II Int. Conf. of Advances in Production Engineering APE'2001. – 2001. -Т.2. – С.207-218.
- Viharos Zs.J.; Markos S; Szekeres Cs. ANN-based chip-form classification in turning // XVII IMEKO World Congress - Metrology in the 3rd Millennium. - 2003. - С. 1469-1473.
- Уоссермен Ф. Нейрокомпьютерная техника: Теория и практика. - М.: Мир, 1992. – 200 с.
- Tawil M. Künstliche Neuronale Netze - Methode und Anwendung // IMW Institutsmittelung. – 1999. -№ 24. - С. 69-72.
- Truchetet F., Laligant O. Wavelets in industrial applications: a review // SPIE. – 2004. -Т. 5607. - С. 1-14.
- Monostori L. A step towards intelligent manufacturing: Modelling and monitoring of manufacturing processes through artificial neural networks // CIRP Annals. – 1993. -Т.42. №1. – С. 485-488.
Поступила в редакцию 5 декабря 2005 г.
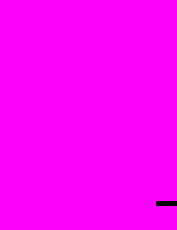