«новое в разработке, производстве и применении специальных сталей и сплавов»
Вид материала | Семинар |
- Технологическая инструкция по пайке сталей и сплавов. Ти№12-58-02 1 Область применения, 785.98kb.
- 2 принят межгосударственным Советом по стандартизации, метрологии и сертификации протокол, 620.54kb.
- 2 принят межгосударственным Советом по стандартизации, метрологии и сертификации протокол, 748.91kb.
- Материалы, применяемые в автомобилестроении и ремонтном производстве, 496.34kb.
- План-конспект урока по теме "Классификация и термическая обработка сталей", 100.32kb.
- Ю. М. Дедков, М. Г. Слотинцева Сб. «Свойства и применение платиновых металлов и сплавов, 100.81kb.
- Пленум Верховного Суда РФ постановлением №2 о применении судами закон, 21.98kb.
- 2. принят межгосударственным Советом по стандартизации, метрологии и сертификации протокол, 762.17kb.
- 2. принят межгосударственным Советом по стандартизации, метрологии и сертификации протокол, 555.05kb.
- Л итейный консилиум №3 «Литейная форма. Решение проблем формообразования при производстве, 175.36kb.
РЕЗУЛЬТАТЫ И ПЕРСПЕКТИВЫ международного сотрудничества по автоматизации
металлографического контроля специальных сталей
Терновой Ю.Ф. 1, Душенко Г.А. 2, Вахрушева В.С. 3, Борек П. 4,
Верцанова Е.В. 5,Пантелеев В.Г. 6, Яценко Р.В. 7
УкрНИИспецсталь 1, Минпромполитики 2, ГП "НИТИ"3, LECO 44, Сarl Zeiss 5, ВидеТесТ 6
(Украина 1-3, Чехия 4, Германия 5, Россия 6)
Министерством промышленной политики Украины в марте 2006 г. утверждена НИР: “Розроблення національних стандартів на методи автоматичного металографічного контролю продукції металургійного виробництва, гармонізованих з міжнародними і європейскими стандартами”. Основанием для принятия такого решения явились протоколы и рекомендации совещаний и семинаров, в которых приняли участие головные институты отрасли (УкрНИИспецсталь, ГП "НИТИ" им. Я.Е. Осады), крупнейшие металлургические и машиностроительные предприятия (Запорожсталь, Днепроспецсталь, Нижнеднепровский трубопрокатный, Криворожсталь, Мотор Сич и др.), представители ВУЗов, а также зарубежные фирмы "LECO", Чехия; "Carl Zeiss", Германия; "ВидеоТесТ", Россия:
-Решение технического совещания: "Проблемы металлографического контроля качества продукции на предприятиях отрасли с применением систем анализа изображений и компьютерной металлографии" от 6 июля 2005 г., за подписью зам. директора Департамента Минпромполитики, нач. управления Душенко Г.А.; УкрНИИспецсталь, г. Запорожье;
- Рекомендации семинара "Современные технологии в металлографии", 14-15 сентября 2005 г., ВидеоТесТ, Санкт-Петербург;
- Решение семинара: "Повышение качества контроля материалов металлургического производства" 20-23 сентября 2005 г., УкрНИИспецсталь;
- Протокол совещания по реализации в условиях ОАО "Днепроспецсталь"…автоматизированных методов компьютерной металлографии" от 28.10. 05 г., УкрНИИспецсталь, ВидеоТесТ, Днепроспецсталь;
- Технико-экономические обоснования НИР УкрНИИспецстали за 2003-2005 г.г.
Подведены итоги сотрудничества УкрНИИспецстали с ведущими зарубежными фирмами, поставляющими на украинский рынок современные системы анализа изображений, программно-аппаратные комплексы, а также программное обеспечение новейших методик количественной и компьютерной металлографии: "LECO", "Carl Zeiss", "ВидеоТесТ" и др.
За период с 2000 по 2005 г., благодаря перечисленным фирмам, металлографические лаборатории крупнейших металлургических, машиностроительных и др. предприятий Украины оснастились системами анализа изображений (САИ) IA-3001 (Днепроспецсталь), IA-32 (Запорожсталь, НТЗ), программно-аппаратными комплексами (ПАК) "ВидеоТесТ" на базе микроскопа "ZEISS. Axiovert 200 MAT" (Азовсталь), адаптерами, камерами, программным обеспечением (УкрНИИспецсталь), а также линиями пробоподготовки ( НТЗ) и др. современным оборудованием. В освоении и аттестации импортного оборудования. а также количественных методов анализа УкрНИИспецсталь оказывает постоянную помощь заводам "Днепроспецсталь", "Запорожсталь", Нижнеднепровский трубопрокатный и др. За этот период в рамках трех договоров институтом выполняются научно-методические работы для заводов Днепроспецсталь и НТЗ, а также исследовательские работы по двум контрактам с фирмой
"LECO" (в 2003.- 2006 г.г.) и трехстороннему соглашению между УкрНИИспецсталью, ООО "Carl Zeiss" и ООО "ВидеоТесТ". От заводов в этих работах активно участвуют специалисты ЦЗЛ и цеха испытаний Днепроспецстали , с которыми составлен перспективный план развития количественной металлографии до 2009 года. Для оперативного решения намеченных задач целесообразно создание при ТК 81 специального подкомитета по количественной и компьютерной металлографии, аналогичного подкомитету Е 04.14 при комитете Е 4 ASTM.
Влияние технологий гарнисажной электронно-лучевой плавки
на структуру и свойства сплавов циркония
Вахрушева В.С., Буряк Т.Н. (ГП «НИТИ», г. Днепропетровск),
Ладохин С.В., Чернявский В.Б. (ФТИМС НАНУ, г. Киев)
В виду высокой коррозионной стойкости, сплавы на основе циркония являются востребованными материалами в атомной энергетике, химической, ювелирной промышленности, медицине и других отраслях. Химический состав и структура циркониевых сплавов оказывает основополагающее влияние на формирование их физико-механических, технологических и служебных свойств.
Выполнены комплексные исследования качества слитков из сплавов циркония с 1% Nb и сложнолегированных с Nb, Sn, Fe. Установлена эффективность получения указанных сплавов методом гарнисажной электронно-лучевой плавки с электромагнитным перемешиванием расплава, с возможностью равномерного распределения химических и структурных составляющих в объеме слитка, с пониженным содержанием вредных примесей и удовлетворительным уровнем технологической пластичности. Данные химического анализа подтверждены результатами металлографических исследований, механических испытаний на растяжение, ударный изгиб, измерение твёрдости. Разработаны взаимоувязанные критерии оценки качества литых заготовок, включающие параметры микроструктуры, ударной вязкости, твёрдости, отношения предела текучести к пределу прочности, содержания примесей и легированных элементов.
Непосредственно из слитков сплава Zr c 1% Nb способом высокотемпературной термомеханической обработки ( 90%, охлаждение в воде) получены трубы с однородной структурой бейнито-мартенситного типа, что обеспечивает высокую вязкость металла (KCV в трубах 80-150 Дж/см2), однородное строение поверхности излома «чашечного» типа, характерно для вязкого механизма разрушения.
Прокатка высоколегированных инструментальных сталей на обжимно-заготовочном стане 1050/950 взамен ковки
Тумко А. Н., Сальников А. С., Козлов О. Е., Голубицкий Ф. А.
(ОАО «Днепроспецсталь», г. Запорожье)
Основной целью освоения прокатки высоколегированных инструментальных сталей на стане 1050/950 взамен ковки является уменьшение расходов по переделу, увеличение объемов производства, ускорение выполнения заказов и уменьшение расходов металла в угар, окалину и стружку.
Наиболее эффективной работой в этом направлении, стало освоение и совершенствование технологии прокатки порошковых сталей на обжимно-заготовочном стане. Для интенсификации режима деформации прессовок сталей типа Р6М5К8Ф3-МП, Р12М3К8Ф2-МП, Р6М5Ф4-МП, Р6М5К5-МП и других проведены исследования энергосиловых параметров прокатки на блюминге и реологических свойств названных сталей, в результате чего увеличены обжатия до 50мм в первом проходе и до 30-40мм в последующих.
Это позволило сократить число проходов на гладкой части бочки валка с 12 до 6 и уменьшить торцевую обрезь с 8-9% до 5-6% при уменьшении времени томления прессовок перед прокаткой в три раза: с 6-8 ч до2-3ч. За 2004-2005 годы на стане 1050/950 произведено 725т катаной заготовки порошковых сталей 17 марок, из которых 13 впервые были прокатаны на обжимном стане.
Другой эффективной работой стало освоение производства сортового проката и заготовок из сталей 3Х3М3Ф, 4Х5М3Ф, 9Г2Ф, 95ХГВФ диаметром 140-190мм. Разработанные температурно-деформационные режимы прокатки обеспечили получение плотной макроструктуры: при УЗК более 1000т сортового проката по группе 3, классам Сc методики SEP 1921 внутренних дефектов не обнаружено.
Опробована технология прокатки слитков массой 1,15т сталей Р6М5 и Х12, слитков массой 1,93т вакуумированной стали Х12МФ и слитков массой 3,6т вакуумированной стали Х12. При прокатке слитков массой 1,15 и 1,93т не получили ожидаемых результатов из-за отваливания прибыльных частей слитков во время первых проходов на клети 1050. Лучшие результаты по расходу металла и деформируемости на стане 1050 получены при прокатке кованой заготовки сечением квадрат 250мм на заготовку квадрат 145мм.
Разработка технологии термообработки поковок
диаметром более 400 мм из мартенситных сталей
Пересаденко О.В.
(ОАО «Днепроспецсталь», г. Запорожье)
В связи с поступлением заказов от НПКГ «Зоря»-Машпроект» на поковки диаметром более 400 мм из мартенситных и флокеночувствительных сталей марок ЭП609-Ш (07Х12НМБФ-Ш) и ЭП517-Ш (15Х12Н2МВФАБ-Ш) была разработана технология выплавки, передела (ковки) и термообработки, обеспечивающая требования ТУ 14-1-1531-75.
Слитки ЭШП диаметром 800 мм из указанных сталей проходили двойной отжиг для полного прохождения превращений по сечению и снижения трещиночувствительности.
Была опробована ковка слитков по схемам через осадку слитка на различную величину.
После ковки поковки отправляли на накопление для последующего проведения ПФО. Режим ПФО был разработан на основании действующего режима, с учётом содержания водорода, фазового и химического состава, температуры фазовых превращений, сечения поковок.
После накопления поковки охлаждали на воздухе, затем загружали в печь, чтобы выровнять температуру по сечению, обеспечить распад аустенита.
После охлаждения металл повторно нагревали до температуры межкритического интервала. После высокотемпературной выдержки поковки охлаждали при тех же условиях, что и после накопления для более полного распада аустенита.
Перечисленные операции совмещались с длительной выдержкой при 680С и замедленным охлаждением после неё, для удаления легкоподвижного атомарного водорода.
Учитывая крупные размеры поковок, после ПФО производили отжиг.
По механическим свойствам и макроструктуре металл аттестован годным.
Кроме того, была детально исследована микроструктура по сечению поковок.
Особенности использования проката коррозионностойких марок стали
при производстве изделий товаров народного потребления
Шестопалов А.В.
(ОАО «Запорожсталь»)
На комбинате «Запорожсталь» осуществляется производство двух видов товаров народного потребления из нержавеющих марок стали – кухонных моек и посуды.
Учитывая высокую стоимость никелесодержащих нержавеющих сталей, в том числе обычно используемой при производстве посуды за рубежом стали марок AiSi 304 и AiSi 321, на комбинате, были испытаны и освоены марганцовистые марки стали для производства товаров народного потребления.
Для производства кухонных моек была выбрана экономичная нержавеющая сталь марки ДИ61У (10Х13Г18ДУ), для кастрюль и других товаров народного потребления - сталь марки ДИ13 (10Х14АГ15), которая разрешена СЭС для контактов с пищевыми продуктами.
По заказу комбината итальянской фирмой «Монета» была спроектирована штамповая оснастка и конструкция моек, позволяющая использование стали марки ДИ 61У, имеющей более высокие прочностные характеристики, чем хромоникелевые марки стали.
Штамповка кухонных моек производится на полностью автоматизированной линии штамповки, состоящей из четырех гидравлических прессов и агрегата полной офланцовки (для врезных моек).
Автоматическая линия штамповки и штамповая оснастка позволяют производить 3 типа накладных и 24 исполнения врезных моек, с сатинированной, матовой или декорированной поверхностью.
Специалистами цеха разработана технология и спроектирована штамповая оснастка, для производства ТНП, которое осуществляется на механических прессах двойного действия
Ассортимент выпускаемых ТНП включает в себя: кастрюли емкостью 1-7 литров, крышки к ним, сковороды, хозяйственные баки, сотейник и др.
Окончательная отделка корпусов кастрюль состоит из полировки наружной поверхности и шлифовки внутренней поверхности на автоматических станках.
Технология производства заготовок из сталей марок ДИ61У и ДИ13 включает в себя: зачистку поверхности слябов до полного удаления видимых дефектов, горячую прокатку, обрезку боковых кромок, термообработку и травление горячекатаных полос-заготовок, холодную прокатку, термообработку, травление, дрессировку и обрезку боковых кромок (при необходимости) холоднокатаной полосы-заготовки.
Заготовкой для производства моек являются дрессированные рулоны, поставляемые в цех без предварительной отделки. На агрегате сатинирования лицевая поверхность рулона шлифуется (сатинируется), затем рулон обклеивается пленкой с обеих сторон и режется на мерные листовые заготовки.
Полосы-заготовки для производства посуды предварительно подвергаются шлифованию на агрегате шлифования полос до получения шероховатости поверхности Ra не более 0,32 мкм, после чего с одной стороны обклеиваются защитной пленкой.
Расширение ассортимента выпускаемых товаров из коррозионностойких марок стали, планируется за счет: разработки и освоения новых видов ТНП, использования декорированного проката, производства моек с улучшенной отделкой поверхности, использование заготовок толщиной 0,6мм.
ТРАНСФОРМАЦИЯ ТОНКОЙ СТРУКТУРЫ ЛИТОГО ЖАРОПРОЧНОГО СПЛАВА ЖС6У-ВИ В ПРОЦЕССЕ ГОРЯЧЕГО ИЗОСТАТИЧЕСКОГО ПРЕССОВАНИЯ И ТЕРМИЧЕСКОЙ ОБРАБОТКИ ЛОПАТОК ТУРБИНЫ
О.Г.Осипенкова, М.Р.Орлов
(Федеральное государственное унитарное предприятие ММПП «САЛЮТ»
Россия, Москва)
Микроструктурные и фрактографические исследования рабочих лопаток турбины низкого давления (ТНД) из жаропрочного сплава ЖС6У-ВИ, выявляют дендритную ликвацию легирующих компонентов сплава, а также литейную пористость в тепловых узлах переходных сечений пера бандажных полок лопаток, образующихся в процессе равноосной кристаллизации отливок.
Целью настоящей работы было исследование тонкой структуры сплава ЖС6У-ВИ, формирующейся в процессе равноосной кристаллизации, и последующей ее трансформации на операциях горячего изостатического прессования (ГИП) и термической обработки (ТО), а также анализ влияния технологических операций на механические свойства сплава и обоснование выбранной технологической схемы производства рабочих лопаток ТНД.
Как показал анализ микроструктуры отлитых лопаток, выполненный методом растровой электронной микроскопии, усадочная пористость расположена в межосных участках дендритов, в зонах кристаллизации остатков жидкой фазы при достижении металлом температуры солидус. Сопутствующим признаком пористости является образование многофазной эвтектики с неоднородной микроструктурой. Состав фазовых составляющих многокомпонентной эвтектики, определенный методом рентгеноспектрального микроанализа позволил определить, что эвтектика содержит фазы с повышенным содержанием циркония, и ниобия.
Соотношение содержания в эвтектической фазе циркония и никеля в пропорции 1:5, дает основание предполагать о формировании в процессе кристаллизации интерметаллида типа ZrNi5 с ГЦК решеткой, соответствующей пространственной группе
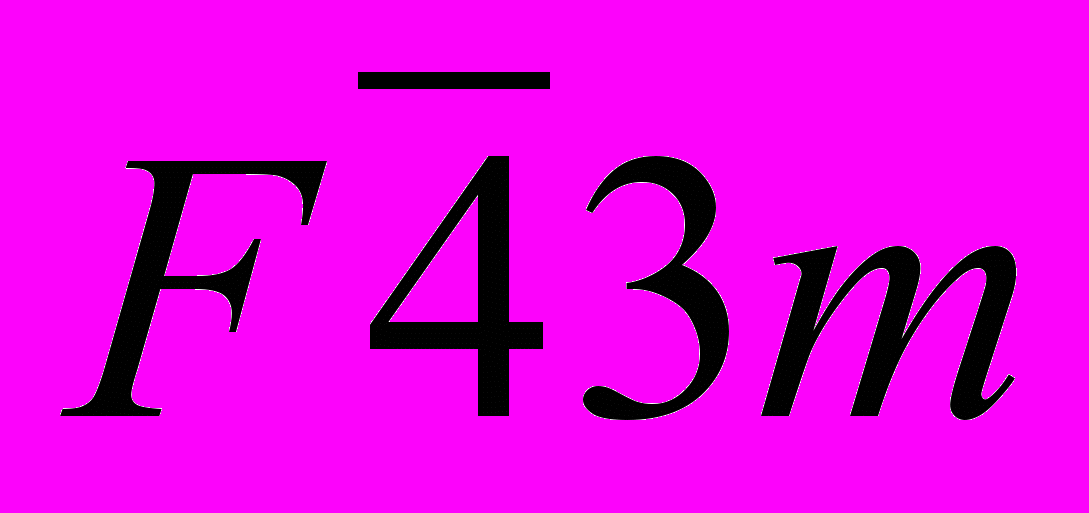
Известными способами снижения пористости и улучшения микроструктуры жаропрочных сплавов являются технологические операции ГИП и ТО. Операцию ГИП целесообразно совмещать с операцией ТО, однако, недостаточно высокая скорость охлаждения рабочей камеры газостата не позволяет получать упрочняющую - фазу необходимого размера и морфологии. Исходя из этих ограничений, часть времени высокотемпературной гомогенизации сплава реализуют на операции ГИП при температуре ТО, при этом давление для ГИП лопаток с равноосной структурой выбирают максимальным. В соответствии со стандартным интервалом температуры гомогенизации сплава ЖС6У-ВИ 1210 10 оС, режим ГИП лопаток и образцов был проведен при параметрах: T = 1200 оС, P = 160 МПа, = 2,5 ч, режим ТО при T = 1220 оС, = 4 ч.
Выбранный температурно-временной режим ГИП позволяет полностью устранить литейную пористость, но не устраняет ликвационную неоднородность сплава ЖС6У-ВИ, что выражается в сохранении эвтектических фаз переменного состава. Операция ТО лопаток, выполненная по стандартному режиму после операции ГИП, устраняет ликвационную и структурную неоднородность в межосных зонах дендритов, формирует типичную для сплава ЖС6У-ВИ бимодальную структуру (двухразмерную структуру упрочняющей - фазы).
Сочетание технологических операций ГИП и ТО устраняет литейную пористость, устраняет ликвационную неоднородность, обеспечивает оптимальную микроструктуру и повышает уровень длительной прочности сплава ЖС6У-ВИ в составе лопаток ТНД.
Горячая правка толстолистового проката на РПМ-1 стана 3000 роликами из
низковольфрамовой стали взамен импортных и стандартизация
Н.Ф. Анищенко, Н.Ф. Тюрин, В.П. Скубий, П.Н. Кирильченко, Е.И. Фомицкий,В.В. Бурховецкий
(ДонНИИчермет (г. Донецк), ОАО «ММК им. Ильича» (г. Мариуполь))
Ролики (рабочие валки) горячей правки РПМ-1 толстолистового стана 3000 меткомбинат им. Ильича изготавливал из стали марки 40ХН2МА (ГОСТ 4543-71) или закупал по импорту чешские из стали марки 19552 (по цене 17 дол. США/кг) и использовал их с упрочнением поверхности наплавкой слоем высоковольфрамовой (до 11% W) наплавочной порошковой проволокой ПП-Нп-35В9Х3СФ (ПП-3Х2В8) (ГОСТ 26101-84). На наплавке после механической обработки обнаруживались кальциевые, точечные раковины глубиной до 2-3, шириной 6-10 мм и многочисленные хаотично расположенные тонкие извилистые трещины, исключающие использование роликов для правки.
Для ликвидации указанных дефектов, повышения стойкости и долговечности роликов без наплавки их изготовили из поковок низковольфрамовой стали марки ДИ42. Сталь произвели в основных дуговых печах ДСП-25 емкостью до 30 т ФСЛЦ меткомбината по разработанной технологической инструкции на выплавку. Произведено 8 плавок с заливкой в кузнечные 8- гранные слитки типа К-5 массой по 5,3 т. Всего использовано 40 слитков (212 т) с отжигом. Из каждого слитка отковано по одной заготовке роликов и по 2 цапфы к ним. Поковки отожжены. Твердость (192…228) НВ.
Механической обработкой изготовлено 4 комплекта роликов с цапфами (по 9 роликов в комплекте) с внутренними 3-х ступенчатыми цилиндрическими полостями для охлаждения проточной водой при эксплуатации.
Термообработку бочки роликов производили по 2-м вариантам: 1. Поверхностная закалка роликов (l = 3790 мм) вертикально на вертикальном закалочном станке ТВЧ модели КУ-199 с расстоянием между центрами 5000 мм с нагревом поверхности бочки роликов индуктором до (920 + 20 оС), охлаждение поверхностей из спрейера эмульсией (или водой); отпуск – в камерно-шахтной электропечи по 2 ролика горизонтально при (200 + 10 оС), 3 ч. Твердость поверхности – 53 HRC, что соответствовало минимальной твердости по чертежу; 2. Цементация поверхности роликов в твердом карбюризаторе после дробеструйной обработки. Выдержка при температуре цементации (910 + 10) оС, 120 ч. Глубина цементации – (5,0…5,5) мм. После правки цементованных роликов – поверхностная термообработка на установке ТВЧ с отпуском. Твердость поверхности роликов – (56…62) HRCэ, что соответствовало верхнему интервалу твердости.
Все ролики прошли эксплуатационные испытания с установкой в РПМ-1 горячей (710…705) оС правки толстолистового проката текущего производства стана 3000 (~ 20 % штрипса марок Х65…Х70).
Наработка 3–х партий роликов с поверхностной термообработкой ТВЧ по 1-й переточке (износ на диаметр составил 0,85 мм – 0,425 мм на сторону. Это на 0,025 мм больше износа поверхности с наплавкой) составила по 213515 т выправленного проката, партии роликов с цементацией + поверхностная термообработка ТВЧ – 403000 т, что равно наработке импортных роликов с наплавкой. Обеспечено отсутствие различных дефектов, многократные перешлифовки до допустимого диаметра 260 мм, эксплуатация и освобождение от дорогостоящего импорта.
Сталь марки ДИ42 используется с 1973 г., начатого производством на ОАО «ДСС им. Кузьмина» по ЧМТУ 1-1007-70 (ножи холодной резки толстолистового проката на вырезке проб на ОАО «МК «Азовсталь»), прошивные иглы на ОАО «АЗОЦМ»; пластины пресс-форм, ножи горячей и холодной резки толстолистового проката на всех прокатных станах, различные штампы на ОАО «ММК им. Ильича» с собственной выплавкой, прокаткой, ковкой заготовок. В настоящее время – ТУ У 14-6-004-99.
Сталь марки ДИ41 по ЧМТУ 1-1007-70 производства «ДСС» используется в промышленности с 1972 г. для изготовления прессового инструмента при прессовании сплавов на медной и цинковой основах на ОАО «АЗОЦМ» (г. Артемовск) и 4-х родственных предприятиях РФ с повышением стойкости в 1,5-3,0 раза против инструмента из стали марки 3Х2В8Ф. В настоящее время ТУ 14-1-1157-96.
Донниичермет и «ММК им. Ильича» предлагают в связи с низким содержанием дефицитного вольфрама и активным промышленным использованием ввести обе марки стали в ГОСТ 5950-73 при его очередном пересмотре. Необходимые данные представляет Донниичермет.
ОПЫТ ОСВОЕНИЯ И ПРОИЗВОДСТВА ВЫСОКОЛЕГИРОВАННЫХ ИНСТРУМЕНТАЛЬНЫХ СТАЛЕЙ И СПЛАВОВ С ИСПОЛЬЗОВАНИЕМ ЧЕТЫРЕХБОЙКОВОГО КОВОЧНОГО БЛОКА НА ПРЕССЕ АКП-500
Артамонов Ю.В., Бедросова Л.В., Зубкова В.Т., Мельников Ю.В., Разаренов А.Н.,
Яценко Р.В. (УкрНИИспецсталь, г. Запорожье)
Повышение эффективности производства сложнолегированных сталей и сплавов имеет важное значение для специализированных предприятий металлургической промышленности Украины.
Опытно-экспериментальная база института «УкрНИИспецсталь» оснащена универсальным оборудованием, позволяющим осуществлять полный металлургический цикл, включая выплавку специальных сталей и сплавов, в т.ч. порошковых, ковку слитков и прессовок на заготовки различного профильного сортамента, преимущественно круглого сечения.
Традиционная технология ковки сложнолегированных сталей и сплавов на прессе АКП-500 с использованием двух бойков, приводит к значительным потерям времени на переналадку бойков, снижению производительности ковки, уменьшению выхода годного металла, повышению энергозатрат и не позволяет деформировать малопластичные стали и сплавы.
Установлено, что причиной пониженной деформируемости при ковке слитков из сложнолегированных сталей, например быстрорежущих типа Р9М4К8, Р12М3К5Ф2, Р12М3К8Ф2 и др. является разнотипность деформирующихся эвтектик: в периферийной зоне – веерная эвтектика А+Ме2С, в центральной – скелетообразная эвтектика А+Ме6С, которая отличается большим сопротивлением горячей пластической деформации [1].
Создание и внедрение в производство института «УкрНИИспецсталь» уникального ковочного устройства, под названием четырехбойковый ковочный блок, позволило повысить эффективность производства и получить высококачественные сложнолегированные стали и сплавы с карбидным и интерметаллидным упрочнением.
Технология ковки в четырехбойковом ковочном блоке основана на принципе формоизменения заготовки без ее уширения при четырехсторонней схеме обжатия, что обеспечивает глубокую деформационную проработку структуры металла по всему сечению, отсутствие разрывов в центральной части заготовки и исключает развитие поверхностных дефектов [2].
Четырехбойковое ковочное устройство способствует измельчению эвтектических карбидов, как в поверхностной, так и в центральной зоне заготовки, а также эффективно воздействует на характер распределения карбидных фаз, что повышает изотропность механических свойств и структуры металла. Так при ковке в четырехбойковом ковочном блоке штамповой стали Х12МФ, происходит интенсивное дробление крупных карбидов типа Ме7С3 (Ме23С6) и их скоплений. Достигается снижение карбидной неоднородности в 2-2,5 раза на половине радиуса и в центре сечения заготовки по сравнению с ковкой на РОМ [3].
Впервые на базовом оборудовании института «УкрНИИспецсталь» реализовано производство сплавов с интерметаллидным упрочнением современными методами порошковой металлургии и деформационного передела с использованием четырехбойкового ковочного блока. Получены опытные партии износостойких инструментальных материалов USP18K23 и USP20K18 с высокооднородным распределением мелкодисперсных интерметаллидных фаз типа (Fe, Co)7(W, Mo)6 и фазы Лавеса Fe2W(Mo), обладающих высокими технологическими и служебными характеристиками [4].
Внедрение разработанной высокой прогрессивной технологии получения сложнолегированных инструментальных сталей и сплавов позволит повысить их качество и конкурентоспособность на рынках стран СНГ и Европейского Союза.
Список использованных источников
1. Мошкевич Л.Д., Тишаев С.И., Евлампиевна Н.Е., Курасов А.Н. Закономерности формирования эвтектических карбидов в быстрорежущих сталях // Сталь. – 1983. - №10. – С.62-67.
2. Лазоркин В.А., Терновой Ю.Ф., Артамонов Ю.В. Четырехбойковое ковочное устройство для гидравлических ковочных прессов // Кузнечно-штамповочное производство. – 2000 - № 8.-С. 43-44.
3. Лазоркин В.А., Яценко Р.В., Мельников Ю.В. Качество поковок, изготовляемых радиальной ковкой на гидравлическом ковочном прессе // Кузнечно-штамповочное производство. – 2005. - № 5.- С. 8-11.
4. Пригунова А.Г., Терновой Ю.Ф., Зубкова В.Т., Терехов В.Н. Влияние различных способов производства на структуру и свойства инструментальных сплавов с интерметаллидным упрочнением. ЗГИА. Металлургия, 2002. – С. 40-44.
ПЕРСПЕКТИВНЫЕ ТЕХНОЛОГИИ СОВМЕЩЕННОЙ ДЕФОРМАЦИОННО-ТЕРМИЧЕСКОЙ ОБРАБОТКИ ПРОКАТА СПЕЦИАЛЬНЫХ СТАЛЕЙ
Спектор Я. И., Ноговицин А.В, Артамонов Ю. В., Тумко А. Н., Яценко Ю. В., Куницкая И. Н.
(УкрНИИспецсталь, Минпромполитики, ОАО "Днепроспецсталь")
Специальные стали и сплавы используются в аграрно-промышленном комплексе, в энергетике, автомобилестроении, транспорте, турбодвигателестроении, оборонной, космической, электронной технике и других приоритетных отраслях промышленности.
Большая часть сортамента сортового проката специальных сталей и сплавов производится с термообработкой, необходимой для обеспечения технологичности в металлургическом переделе (умягчающий отжиг перед обдиркой, рекристаллизационный - перед калибровкой), для формирования технологических и эксплуатационных свойств у потребителя (при холодной высадке, штамповке; высокой износостойкости и выносливости тел качения и режущих свойств инструмента).
В связи с этим одной из проблем производства металлопродукции является высокая энергоёмкость, в том числе из–за длительной термообработки. В настоящее время получили развитие энергосберегающие технологии термической и термомеханической обработки (ТМО) в потоке сортопрокатных станов, использование которых позволяет достигать:
- значительного сокращения длительности термообработки (используется тепло прокатного нагрева взамен дополнительного нагрева проката, деталей). Экономия энергозатрат составляет 150–700 кВт/час на тонну;
- повышения надежности машин и снижения веса крепежа на 15- 25%;
- изготовления металлопродукции из спецсталей с микроструктурой и свойствами, недостижимыми для традиционной технологии.
Эффекты ТМО можно реализовать только с использованием новых сквозных наукоемких технологий и при наличии соответствующего специального оборудования на сортопрокатных станах. Так называемые "прокатно–термические комплексы" — интегрированные в поток стана линии, совмещающие деформационную и термическую обработку (ТМО) - для сталей и проката массового назначения (арматура, проволока, лист, рельсы и др.) уже используется на практике. В производстве проката специальных сталей эта концепция начала реализовываться только в последние годы отдельными передовыми западными фирмами при проектировании и изготовлении новых (строящихся) сортопрокатных станов. Это связано с тем, что для реализации выявленных в последние десятилетия структурных (и, соответственно, прочностных) эффектов ТМО требуется создание отдельных линий для каждой (или 2-3 родственных) группы проката спецсталей разного сортамента и назначения, вследствие большого различия их состава, кинетики структурных и фазовых превращений, широкого диапазона требований к термообработке, свойствам, микроструктуре готовых изделий.
Выделяют две основные схемы ТМО: предварительная ТМО в процессе прокатки, умягчающий или сфероидизирующий отжиг проката, изготовление деталей у потребителя и их стандартная термообработка; прямая ТМО проката без термообработки деталей у потребителя.
При "прямой" ТМО возможны полная закалка с отпуском (либо с самоотпуском), неполная (прерванная) закалка на заданную твердость (прочность) и нормализующая ТМО с прокатного нагрева. Для конструкционных сталей с ТМО достигнуто следующее повышение механических свойств: прочности в 1,5–2 раза; пластичности в 1,2–1,4 раза; сопротивления разрушению при динамической нагрузке –– в 1,4–1,8 раза; сопротивления разрушению при циклической нагрузке — в 1,5 раза; эксплуатационной стойкости (долговечности) длинномерных изделий (например, буровых штанг) — в 2–3 раза и др. Кроме того, устраняется нормализационная термообработка деталей у потребителя.
Второй вариант "прямой ТМО" – изотермическая закалка - предусматривает регулируемую прокатку и ускоренное охлаждение до 550–650 С (термоупрочненные бунты из малоуглеродистых экономнолегированных сталей для холодной высадки высокопрочного крепежа).
Схема "прямой ТМО" может использоваться также в производстве сортового проката коррозионностойких, жаростойких и др. специальных высоколегированных сталей и сплавов. Основными элементами технологии ТМО в этой схеме являются регулируемая прокатка и ускоренное охлаждение. Эффект ТМО (требуемая стандартами термообработка изделий (закалка) совмещается с процессом прокатки) для аустенитных сталей заключается в повышении в 1,5–2,0 раза предела текучести при сохранении достаточного уровня пластических свойств.
Реальной технологической схемой является "предварительная ТМО". "Предварительная ТМО" путем регулируемой прокатки и ускоренного охлаждения обеспечивает измельчение зерна аустенита, уменьшение выделений карбидной сетки (на 1–2 балла), среднего размера карбидов с 0,8 до 0,45 мкм и остатков пластинчатого перлита; обеспечивается однородность зернистого перлита и его более дисперсная структура в высокоуглеродистых сталях. В результате повышается долговечность подшипников, возрастает на 30–50 % контактная выносливость, увеличивается в 1,2–1,5 раза работа разрушения пальцев траков, шариков подшипников и других деталей из проката с ТМО. Эффект ТМО, кроме улучшения качества по структуре и свойствам, заключается в ускорении технологических процессов дальнейшего передела: структурного отжига и холодного волочения.
Эффекты термомеханической обработки проката
подшипниковой стали
Я.И. Спектор, А.Г. Пригунова, И.Н. Куницкая, Ю.В. Яценко, Р.В.Яценко
( УкрНИИспецсталь, г. Запорожье, Минпромполитики Украины, г. Киев)
Влияние термомеханической обработки (ТМО) на гетерофазные мартенсито-карбидные подшипниковые стали типа ШХ15, 110Х18М связано с изменением комплекса структурных факторов, определяющих эксплуатационные свойства подшипников (изменения в матрице, карбидной фазе). Немаловажное влияние оказывают неметаллические включения.
Матрица подшипниковых сталей представляет собой низкоотпущенный высокоуглеродистый мартенсит, свойства которого зависят от состояния границ, размера зерна аустенита. Степень измельчения зерна может регулироваться при ТМО за счет процессов горячего наклепа и рекристаллизации аустенита. Размер исходного аустенитного зерна прямо связан как с выделением избыточных карбидов по его границам, так и с размерами фазовых составляющих пластинчатого и сфероидизированного перлита при последующем охлаждении, сфероидизирующем отжиге и закалке деталей подшипников. Зарождение и рост новых зерен сопровождается «наследованием» дислокационной структуры горячей деформации. Особенностью является обогащение границ зерен примесями (фосфором), легирующими элементами (хром) и углеродом (использован метод ОЖЕ-спектроскопии поверхности изломов). Степень сегрегации фосфора существенно уменьшается с деформацией при 850 0С в сравнении с уровнем обогащения границ исходного зерна перед деформацией.