Х а д т є. Ф. Соболєв М. Р. Захарян Конспект
Вид материала | Конспект |
СодержаниеЕлектрофізичні й електрохімічні методи обробки (ЭФЭХ) Електроконтактна обробка. Електрохімічне полірування. Лазерна обробка |
- В. О. Соболєв, докт соц наук, проф., О. Н. Ярмиш, 150.32kb.
- Разработала: Захарян С. В., воспитатель мбдоу црр д/с №57 «Катюша», 113.95kb.
- Захарян Нонна мы – дети космоса, 74.53kb.
- Міліція І населення – партнери, 1673.58kb.
- Как составить конспект урока русского языка. Конспект урока, 4218.04kb.
- Соболєв олексій валерійович, 41.87kb.
- Конспект и самоанализ одного зачетного занятия. Конспект и самоанализ досугового мероприятия, 1222.92kb.
- Курс лекцій Рецензенти: Доктор соціологічних наук, проф. Соболєв В. О. Доктор соціологічних, 2781.7kb.
- В. С. Середюк Матеріалознавство Конспект, 2044.1kb.
- Конспект лекций 2010 г. Батычко Вл. Т. Муниципальное право. Конспект лекций. 2010, 2365.6kb.
ЛЕКЦІЯ
Електрофізичні й електрохімічні методи обробки (ЭФЭХ)
Характеристика електрофізичних і електрохімічних методів обробки
Ці методи призначені в основному для обробки заготівель із дуже міцних, досить грузлих, тендітних і неметалічних матеріалів.
Ці методи мають наступні переваги:
- відсутнє силовий вплив інструмента на заготівлю (або дуже мало й не впливає на сумарну погрішність обробки);
- дозволяють міняти форму поверхні заготівлі й впливають на стан поверхневого кулі: наклеп обробленої поверхні не утвориться, дефектний куля незначний; підвищуються корозійні, міцнісні й інші експлуатаційні характеристики поверхні;
- можна обробляти дуже складні зовнішні й внутрішні поверхні заготівель.
ЭФЭХ методи обробки є універсальними й забезпечують безперервність процесів при одночасному формоутворенні всієї оброблюваної поверхні. Ці методи впроваджуються в різних галузях промисловості.
Електроерозійні методи обробки
Ці методи засновані на явищі ерозії електродів зі струмопровідних матеріалів при пропущенні між ними імпульсного електричного струму.
Розряд між електродами відбувається в газовому середовищі або при заповненні міжелектродного простору діелектричною рідиною - гаснув, мінеральне масло.
При наявності різниці потенціалів на електродах відбувається іонізація міжелектродного простору. При певному значенні різниці потенціалів - утвориться канал провідності, по якому спрямовується електроенергія у вигляді імпульсного іскрового або дугового розряду.
На поверхні заготівлі температура зростає до 10000…120000C. Відбувається миттєве оплавлення й випар елементарного обсягу металу й на оброблюваній поверхні утвориться лунка.
Вилучений метав застигає в діелектричній рідині у вигляді гранул діаметром 0,01...0,005 мм.
При безперервному підведенні до електродів імпульсного струму процес ерозії триває доти, поки не буде вилучений весь метав, що перебуває між електродами на відстані, при якому можливий електричний пробій (0,01...0,05 мм) при заданій напрузі.
Для продовження процесу необхідно зблизити електроди до зазначеної відстані. Електроди зближаються автоматично за допомогою систем, що стежать.
Електроіскрова обробка
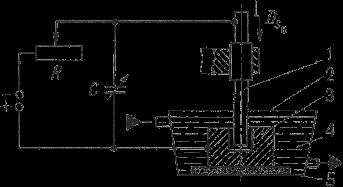
Схема електроіскрового верстата:
1 - електрод-інструмент; 2 - ванна; 3 - заготівля-електрод; 4 - діелектрична рідина; 5 - ізолятор
При електроіскровій обробці - використовують імпульсні іскрові розряди між
електродами ( оброблювана заготівля (анод) - інструмент (катод)).
Конденсатор заряджається через резистор від джерела постійного струму напругою 100...200 У. Коли напруга на електродах 1 і 3 досягає пробійного утвориться канал, через який здійснюється іскровий розряд енергії, накопиченої конденсатором.
Тривалість імпульсу 20...200 мкс.
Точність обробки до 0,002 мм, /0,63...0,16 напівтемний.
Для забезпечення безперервності процесу ( зазор = const) верстати забезпечуються системою, що стежить, і системою автоматичної подачі інструмента.
Одержують наскрізні відчини будь-якої форми поперечного перерізу, глухі відчини й порожнини, відчини із криволінійними осями, вирізують заготівлі з аркуша, виконують плоске, кругле й внутрішнє шліфування.
Виготовляють штампи й прес-форми, фільтри, різальний інструмент.
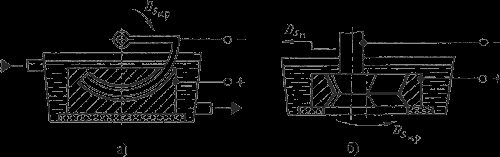
Схеми електроіскрової обробки:
а - прошивання отвору із криволінійною віссю; б - шліфування внутрішньої поверхні фільтри
Електроіскрову обробку застосовують для зміцнення поверхневого кулі металу. На поверхню виробу наносять тонка куля металу або композиційного матеріалу. Подібні покриття підвищують твердість, зносостійкість, жаростійкість, ерозійну стійкість і так далі.
Електроімпульсна обробка
При електроімпульсній обробці використовують електричні імпульси великої тривалості (5...10 мс), у результаті чого відбувається дуговий розряд.
Більші потужності імпульсів від електронних генераторів забезпечують високу продуктивність обробки.
Електроімпульсній обробку доцільно застосовувати при попередній обробці штампів, турбінних лопаток, фасонних отворів у деталі з корозійностійких і жароміцних сплавів.
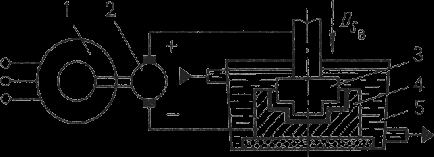
Схема електроімпульсної обробки:
1 - електродвигун; 2 - імпульсний генератор постійного струму; 3 - інструмент-електрод; 4 - заготівля-електрод; 5 - ванна.
Електроконтактна обробка.
Електроконтактна обробка заснована на локальному нагріванні заготівлі в місці контакту з електродом-інструментом і видаленні розм'якшеного або розплавленого металу із зони обробки механічним способом: відносним рухом заготівлі або інструмента.
Джерелом теплоти служать імпульсні дугові розряди.
Цей вид обробки рекомендується для великих деталей з вуглецевих і легованих сталей, чавуну, кольорових сплавів, тугоплавких і спеціальних сплавів .
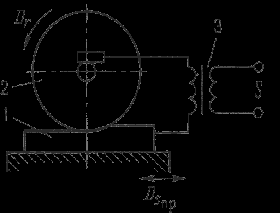
Схема електроконтактної обробки плоскої поверхні:
1 - оброблювана заготівля; 2 - інструмент-електрод; 3 - трансформатор
Цей метод застосовують для зачищення виливків від заток, відрізки ливникових систем, зачищення прокату, шліфування корозійних деталей з важкооброблюваних сплавів.
Електрохімічна обробка
Електрохімічна обробка заснована на законах анодного розчинення металів при електролізі.
При проходженні електричного струму через електроліт на поверхні заготівлі відбуваються хімічні реакції, і поверхневий куля металу перетворюється в хімічну сполуку.
Продукти електролізу переходять у розчин або віддаляються механічним способом.
Продуктивність цього способу залежить від електрохімічних властивостей електроліту, оброблюваного матеріалу й щільності струму.
Електрохімічне полірування.
Електрохімічне полірування здійснюється у ванні, заповненої електролітом (розчини кислот і лугів).
Оброблювану заготівлю підключають до катода (малий. 21.5). Катодом служити металева пластинка зі свинцю, міді, стали (іноді електроліт підігрівають).
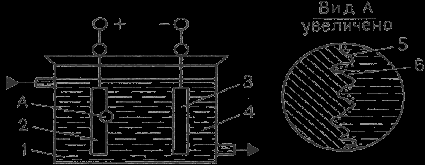
Схема електрохімічного полірування:
1 - ванна; 2 - оброблювана заготівля; 3 - пластина-електрод; 4 - електроліт; 5 - мікровиступ;
6 - продукти анодного розчинення
При подачі напруги починається процес розчинення металу заготівлі (в основному на виступах мікронерівностей). У результаті вибірного розчинення, мікронерівності згладжуються, і оброблювана поверхня здобуває металевий блиск.
Поліпшуються електрофізичні характеристики деталей: зменшується глибина мікротріщин, поверхневий куля не деформується, виключаються зміцнення й термічні зміни структури, підвищується корозійна стійкість.
Цим методом одержують поверхні під гальванічні покриття, доводять робочі поверхні різального інструменту, виготовляють тонкі стрічки й фольгу, очищають і декоративно обробляють деталі.
Електрохімічна розмірна обробка
Електрохімічна розмірна обробка виконується в струмені електроліту, що прокачується під тиском через міжелектродний проміжок.
Електроліт розчиняє заготівлі, що утворяться на поверхні, - анода солі й видаляє їх із зони обробки. Висока продуктивність процесу полягає в тім, що одночасно обробляється вся поверхня заготівлі.
Ділянки, що не вимагають обробки, ізолюють. Інструменту надають форму, зворотну формі оброблюваної поверхні. Формоутворення відбувається по методу копіювання .
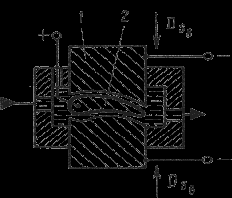
Схема електрохімічної розмірної обробки:
1 - інструмент - катод; 2 - заготівля - анод
Точність обробки підвищується при зменшенні робочого зазору. Для його контролю використовують високочутливі елементи, які вбудовують у систему, що стежить.
Цей спосіб рекомендують для обробки заготівель із високоміцних сталей, карбідних і важкооброблюваних матеріалів. Також можна обробляти тонкостінні деталі з високою точністю і якістю обробленої поверхні (відсутнє тиск інструмента на заготівлю).
Комбіновані методи обробки
Електроабразивна й електроалмазна обробка.
При таких видах обробки інструментом служить шліфувальне коло з абразивного матеріалу на електропровідному зв'язуванню (бакелітове зв'язування із графітовим наповнювачем).
Між анодом - заготівлею й катодом - шліфувальним колом є зазор, куди подається електроліт. Продукти анодного розчинення віддаляються абразивними зернами; шліфувальне коло має обертовий рух, а заготівля - рух подачі, які відповідають процесу механічного шліфування .
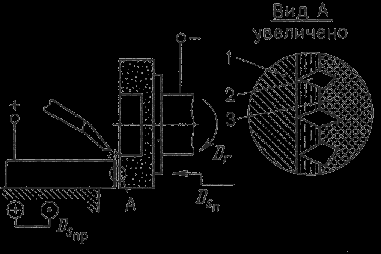
Схема електроабразивного шліфування:
1 - заготівля; 2 - абразивні зерна; 3 - зв'язування шліфувального кола.
Введення в зону різання ультразвукових коливань підвищує продуктивність в 2...2,5 рази при поліпшенні якості поверхні. Ці методи застосовуються для оздоблювальної обробки заготівель із важкооброблюваних матеріалів, а також нежорстких заготівель, тому що сили різання незначні.
Анодно-механічна обробка
Анодно-механічна обробка заснована на сполученні електротермічних і електромеханічних процесів і займає проміжне місце між електроерозійним і електрохімічним методами.
Заготівлю підключають до анода, а інструмент - до катода. Як інструмент використовують металеві диски, циліндри, стрічки, дріт.
Обробку ведуть у середовищі електроліту ( водяний розчин рідкого натрієвого скла).
Робочі рухи, як при механічній обробці різанням.
Електроліт у зону обробки подають через сопло .
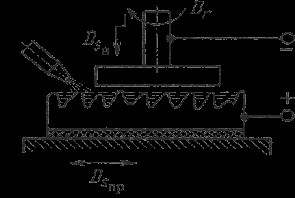
Схема анодно-механічної обробки плоскої поверхні.
При пропущенні через розчин електроліту постійного електричного струму відбувається процес анодного розчинення, як при електрохімічній обробці.
При зіткненні інструмента з мікронерівностями заготівлі відбувається електроерозія, властива електроіскровій обробці. Метав заготівлі в місці контакту з інструментом розігрівається й розріджується. Продукти електроерозії й анодного розчинення віддаляються при відносних рухах інструмента й заготівлі.
Цим способом обробляють заготівлі з високоміцних і важкооброблюваних сплавів, грузлих матеріалів.
Цим способом розріжуть заготівлі на частині, прорізають пази й щілини, обробляють поверхні тіл обертання, шліфують плоскі поверхні й поверхні, що мають форму тіл обертання, полірують поверхні, заточують різальний інструмент.
Променеві методи обробки
Електронно-променева обробка – заснована на перетворенні кінетичної енергії спрямованого пучка електронів у теплову енергію. Висока щільність енергії сфальцьованого електронного променя дозволяє обробляти заготівлю за рахунок нагрівання, розплавлювання й випари матеріалу з локальної ділянки.
Електронний промінь утвориться за рахунок емісії електронів з нагрітого у вакуумі катода. Він за допомогою електростатичних і електромагнітних лінз фокусується на заготівлі.
При розмірній обробці установка працює в імпульсному режимі, що забезпечує локальне нагрівання заготівлі.
Електронно-променевий метод ефективний при обробці отворів діаметром 1...0,010 мм, при прорізанні пазів, різанню заготівель, виготовленні тонких плівок і сіток з фольги, виготовленні заготівель із важкооброблюваних металів і сплавів, кераміки, кварцу, напівпровідникового матеріалу.
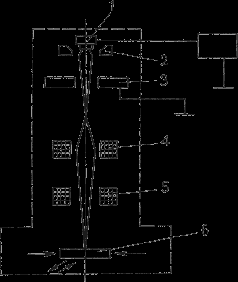
Схема установки для електронно-променевого зварювання: 1 - катод електронної гармати; 2 - електрод; 3 - анод; 4 і 5 - магнітна система, що відхиляє; 6 - заготівля
Лазерна обробка – заснована на тепловому впливі світлового променя високої енергії на поверхню заготівлі. Джерелом світлового випромінювання служити лазер - оптичний квантовий генератор.
Енергія світлового променя не велика 20…100Дж, але вона виділяється в мільйонні частки секунди й зосереджує в промені діаметром 0,01 мм. Тому температура в зоні контакту 6000…80000С.
Куля металу миттєво розплавляється й випаровується. За допомогою цього методу здійснюється прошивання отворів, розрізування заготівлі, прорізання пазів у заготівлях з будь-яких матеріалів (фольга з танталу, вольфраму, молібдену). Також за допомогою цього методу можна здійснити контурну обробку по складному периметрі.
Плазмова обробка
Сутність обробки полягає в тім, що плазму направляють на оброблювану поверхню.
Плазмова струмінь являє собою спрямований потік частково або повністю іонізованого газу, що має температуру 10000…200000С. Плазму одержують у плазмових пальниках, пропускаючи газ через стовп стислої дуги. У якості плазмоутворюючих газів використовують азот, аргон, водень, гелій, повітря і їхньої суміші.
За допомогою цього методу прошиваються відчини, вирізьблюються заготівлі з листового матеріалу, виробляється гостріння в заготівлях з будь-яких матеріалів.
При прошиванні отворів і різці головку встановлюють перпендикулярно до поверхні заготівлі, при струганні й гострінні – кутом 40…60 0
Плазмове напилювання.
Цей вид обробки здійснюється з метою одержання заданих розмірів.
У камеру плазмотрона подається порошкоподібний конструкційний матеріал і інертний газ під тиском.
Під дією дугового розряду конструкційний матеріал плавитися й переходити в стан плазми; струмінь плазми стискується в плазмотроні газом. Виходячи із сопла, струмлячи направляється на оброблювану заготівлю.