Курс лекций для студентов Института природных ресурсов, направления 120700 «Землеустройство и кадастры» (18 часов)
Вид материала | Курс лекций |
СодержаниеНеорганические стекла Технические Строительные Бытовые Композиционные материалы |
- Программа вступительных испытаний в магистратуру по направлению 120700. 68- «Землеустройство, 177.22kb.
- Образовательный стандарт высшего профессионального образования по направлению подготовки, 344.1kb.
- Основная образовательная программа высшего профессионального образования Направление, 4128.43kb.
- Базовый курс рабочая программа и методические указания для студентов 1 курса заочной, 348.1kb.
- Программа вступительных испытаний по направлению магистерской подготовки 120700., 188.61kb.
- Тематика семинарских занятий для студентов I курса энергетического института (энин), 670.95kb.
- Курс лекций дисциплины «Компьютерные технологии и сапр» для студентов специальностей, 1793.82kb.
- Основная образовательная программа высшего профессионального образования Направление, 3396.78kb.
- За курс 9 класса билет, 42.57kb.
- Описание направления подготовки «Землеустройство и кадастры», 31.91kb.
Неорганические стекла
Неорганические стекла – это сложные расплавы высокой вязкости, состоящие из основных и кислотных оксидов.
С
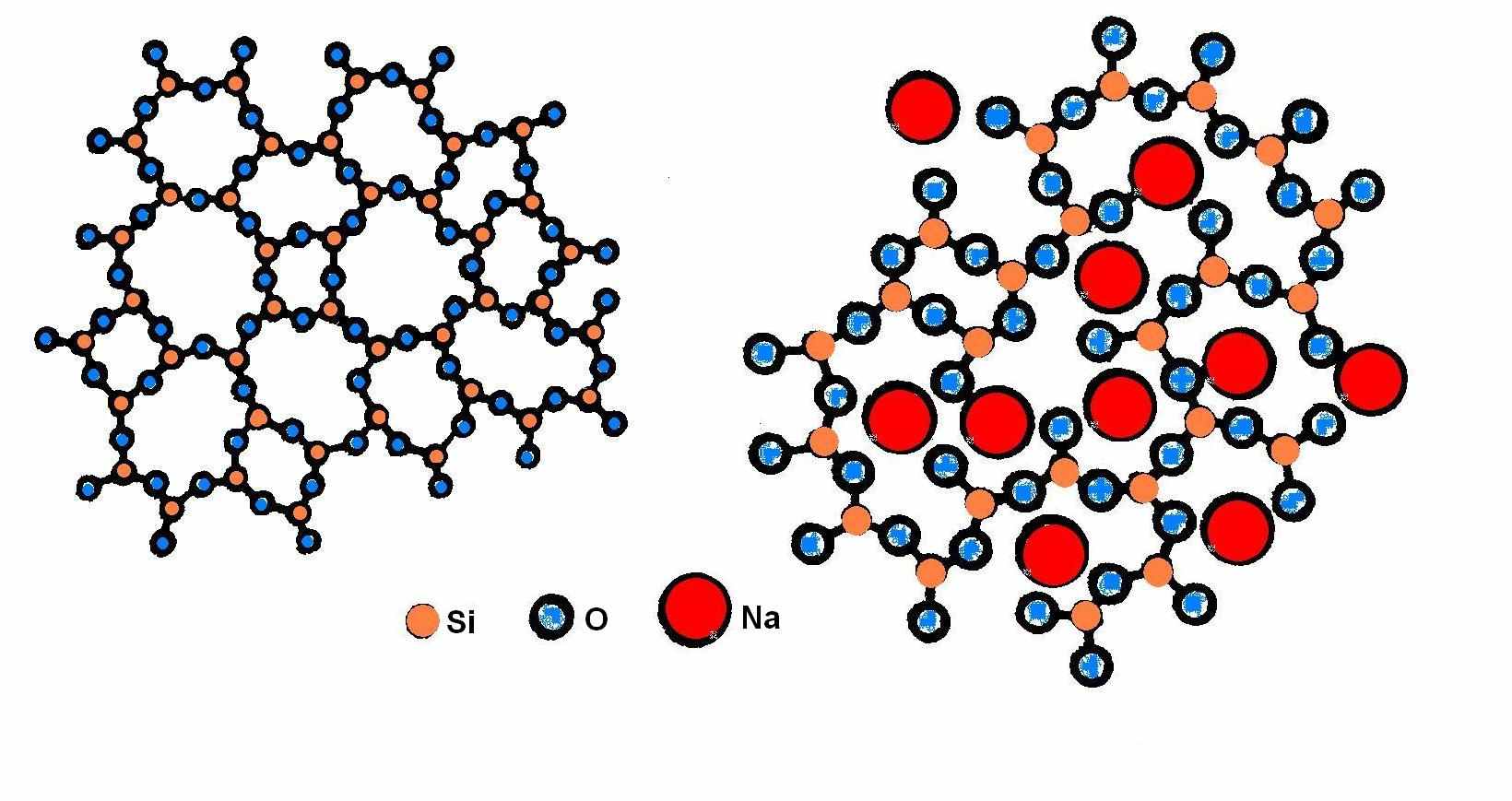
теклообразное состояние является разновидностью аморфного. Беспорядочная структура жидкости при охлаждении «замораживается». Получается неправильная пространственная сетка (рис. 114). Стекло имеет рыхлую неоднородную структуру с поверхностными дефектами.
а б
Рис. 114. Структура стекла: а – кварцевое; б – щелочное
В состав стекол входят:
- стеклообразующие оксиды SiO2, B2O3, P2O5, GeO2, As2O5. Они образуют структурный каркас стекла, или сетку;
- модифицирующие оксиды натрия, калия, лития, кальция, магния, бария. Они изменяют физико-химические свойства стекломассы, облегчая технологию производства;
- оксиды для придания нужных характеристик. Это оксиды алюминия, железа, свинца, титана, бериллия. Сами они структурный каркас не образуют, но частично замещают стеклообразующие оксиды.
Классификация стекол
- По назначению



Технические Строительные Бытовые
оптические, оконные посуда
светотехнические витринные зеркала
электротехнические армированные стеклотара
химико-лабораторные стеклоблоки
приборные
трубные
- П
о стеклообразующему веществу
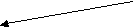




Силикатные (SiO2) Боросиликатные(B2O3–SiO2) Алюмофосфатные (Al2O3–P2O5)
Алюмосиликатные (Al2O3–SiO2) Алюмоборосиликатные(Al2O3– B2O3–SiO2)
- П
о содержанию модификаторов
Щелочные Бесщелочные Кварцевые
Свойства стекол
Плавятся в интервале температур, размягчаются при температуре 600–800 С; переработка требует свыше 1000 С.
Свойства стекол изотропны, т. е. не зависят от направления.
При сжатии прочность высокая: до 2000 МПа, а при растяжении – низкая (менее 100 МПа). Твердость стекол составляет 0,5–0,7 твердости алмаза, но они очень хрупкие. Несколько выше механические свойства у кварцевых и бесщелочных стекол.
Важнейшие свойства стекол, определяющие их применение, – оптические: прозрачность, отражение, рассеяние, поглощение, преломление. Обычное листовое стекло 90 % видимого света пропускает, а ультрафиолетовое излучение поглощает. Кварцевые стекла прозрачны для ультрафиолетовых лучей.
Стекла можно закаливать, нагревая выше температуры стеклования и быстро охлаждая в масле или потоке воздуха. Ударная вязкость стекла увеличивается при закалке в 5–7 раз, прочность – в 3–6 раз, повышается термостойкость.
Триплекс – это два листа закаленного стекла, склеенные прозрачной полимерной пленкой. Могут быть плоскими и гнутыми. При разрушении триплекса осколки удерживаются на полимерной пленке и не травмируют окружающих.
Термопан: между двумя стеклами имеется воздушный промежуток, который обеспечивает теплоизоляцию.
Есть стекла с высокой защитой от инфракрасных лучей. Они содержат индий и олово, изготавливаются многослойными. Ими остеклены, например, японские машины («Ниссан», «Тойота»), предназначенные для эксплуатации в жарких странах.
Ситаллы (кристаллические стекла)
Их еще называют стеклокерамикой. Они состоят из стекловидной и кристаллической фазы. Структура ситаллов однородная, мелкозернистая: зерна имеют размер 1–2 мкм.
Получают ситаллы введением в расплав стекла веществ, служащих центами кристаллизации (солей золота, серебра, меди). В результате 95 % объема занимает кристаллическая фаза, остальное – стекловидная прослойка (см. рис. 115).
Свойства ситаллов: их твердость близка к твердости закаленной стали, они термостойки до 700–900 С. Их ударная вязкость в 3–4 раза выше, чем у стекол. Они износостойки, являются диэлектриками и проявляют высокую химическую стойкость.
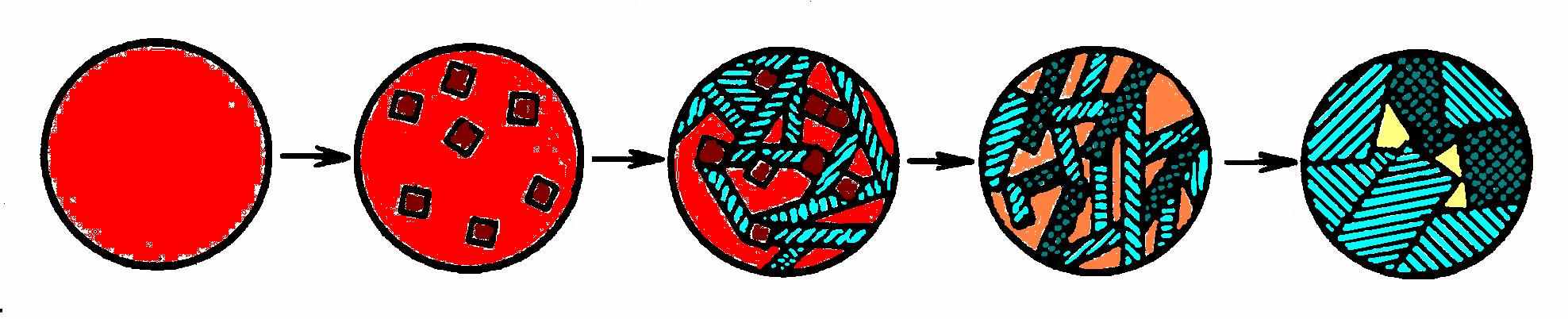
Рис. 115. Кристаллизация стекла при введении модификаторов в расплав
Применение ситаллов включает детали ДВС, подшипники, трубы для химической промышленности, оболочки вакуумных электронных приборов, детали радиоэлектроники, жаростойкие покрытия на металлах, фильеры для вытягивания синтетических волокон, лопасти компрессоров и сопла реактивных двигателей.
Композиционные материалы
Композиционные материалы (композиты) – это новый класс легких и высокопрочных материалов с большим сопротивлением развитию трещины.
По удельной прочности и удельной жесткости композиты превосходят все обычные конструкционные материалы. Кроме того, они сохраняют высокую прочность при повышенных температурах, хорошо сопротивляются усталостному разрушению.
Композиты – сложные материалы, в состав которых входят сильно отличающиеся по свойствам, не растворимые друг в друге компоненты, разделенные ярко выраженной границей.
Сам принцип создания композитов заимствован у природы: стволы деревьев состоят из жестких волокон целлюлозы и мягкого лигнина, кости человека и животных строятся из жестких нитей фосфатных солей и мягкого, вязкого белка коллагена.
Свойства композиционных материалов (КМ) зависят от свойств компонентов и прочности связи между ними. Отличительная особенность: композиты проявляют достоинства компонентов, а не их недостатки. Вдобавок появляются свойства, которых не имели отдельно взятые компоненты. Поэтому для создания композитов выбирают компоненты с дополняющими друг друга свойствами.
Строение композитов
Композиционный материал состоит из основы, или матрицы (металлической или полимерной) и наполнителя, или армирующего компонента.
Матрица связывает материал в единое целое, придает ему форму. От свойств матрицы зависят технология получения материала, рабочая температура, удельная прочность σв/γ, предел усталости σ-1.
Наполнитель равномерно распределяется в матрице в определенном порядке. Наполнитель воспринимает нагрузку, поэтому должен иметь высокие прочность, твердость, модуль упругости.
Матрица распределяет нагрузку между частицами наполнителя, защищает их поверхность и повышает энергию распространения трещины, предупреждая хрупкое разрушение. Сама матрица не упрочняется, и в этом отличие композитов от металлических сплавов.
По форме наполнители могут быть нуль-мерными, одномерными и двумерными (рис. 116).
Композиционные материалы, упрочненные мелкими частицами наполнителя, называют дисперсно-упрочненными. Композиты, содержащие волокна, – волокнистыми. Двумерные наполнители применяются, в основном, в полимерных композитах.
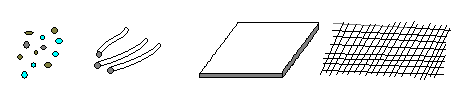
а б в
Рис. 116. Форма наполнителей в композиционных материалах:
а – частицы; б – волокна; в – пластины, листы, ткань
Дисперсно-упрочненные композиционные материалы
Н
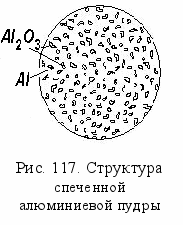
Для матриц используют либо материалы с малой плотностью (алюминий, магний, титан и их сплавы), либо жаропрочные материалы (никель).
Получают дисперсно-упрочненные КМ прессованием и спеканием или введением наполнителя в жидкую матрицу перед разливкой.
В
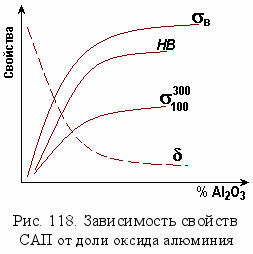
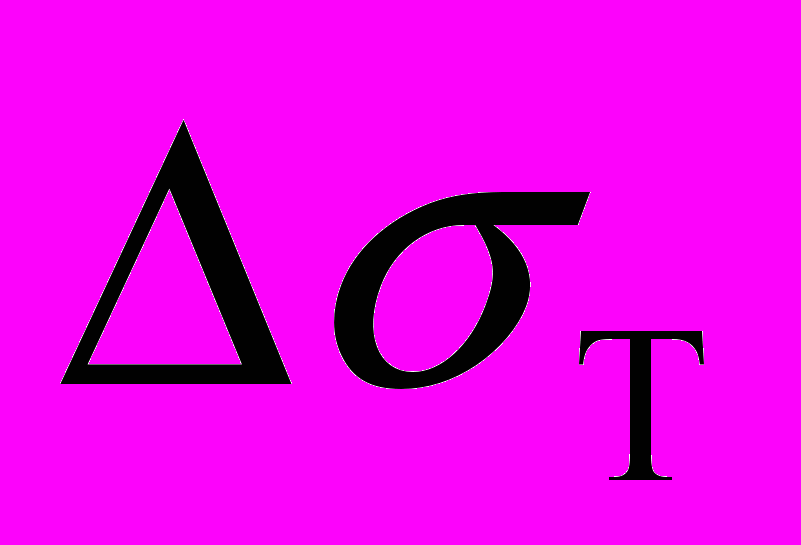
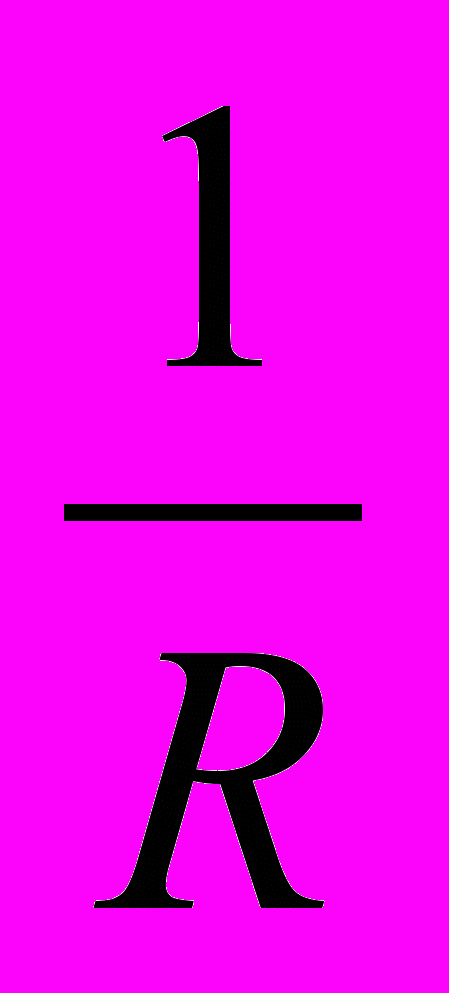
Примером является спеченная алюминиевая пудра (САП). Она имеет высокую жаропрочность и коррозионную стойкость. Состоит из алюминия и частиц Al2O3 в виде чешуек толщиной менее 1 мкм (рис. 117). Чем больше в этом материале доля Al2O3, тем выше прочность, твердость, жаропрочность, но ниже пластичность (см. рис. 118).
Преимуществом такого материала по сравнению с обычными сплавами алюминия являются очень мелкие зерна, равномерное распределение упрочняющих частиц, отсутствие линейных дефектов.
Изделия из САП: листы, фольга, профили, трубы. Получают детали для работы при 300–500 С: лопатки компрессоров, лопасти турбин и вентиляторов.
Волокнистые композиционные материалы
Наполнителями в них служат волокна или нитевидные кристаллы: углеродные, борные, из SiC, Al2O3, стекла, а также проволока из коррозионно-стойкой стали, молибдена, вольфрама, бериллия. Волокна являются элементами, воспринимающими нагрузку. Для матриц используются те же металлы, что и для предыдущей группы.
Для достижения максимальной прочности композиционного материала волокна должны быть расположены параллельно направлению действия напряжения. Поэтому расположение волокон может быть одноосным, двухосным или трехосным (рис. 119).
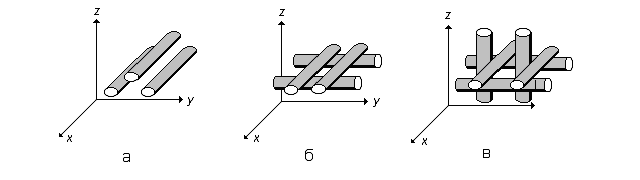
а б в
Рис. 119. Расположение армирующих волокон в композитах:
а – одноосное; б – двухосное; в – трехосное
П
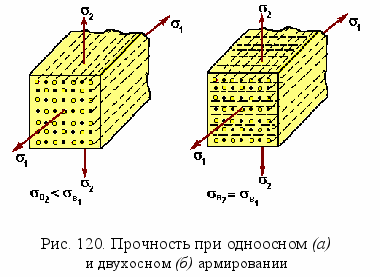
а)
б)
ри одноосном армировании проявляется анизотропия: в направлении волокон прочность выше, чем в поперечном (так как нагрузку воспринимает волокно, а матрица – передающая среда). При двухосном армировании анизотропии нет, но прочность вдоль оси волокон уменьшается примерно в 3 раза (рис. 120).
Чем тоньше и длиннее волокно, тем выше степень упрочнения (см. рис. 121).
Объемная доля волокна составляет от нескольких процентов до 80–90 %. Увеличение доли наполнителя повышает прочность и другие характеристики.
Н

П
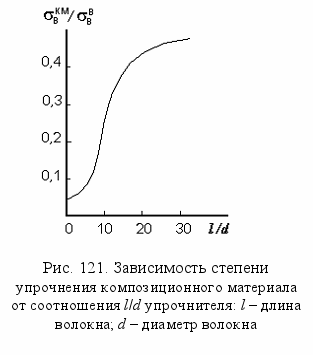
Проблемы технологии композитов в том, что волокна бора, углерода, карбида кремния и другие плохо слипаются с матрицей, не смачиваются жидким металлом матрицы. Прочность сцепления обеспечивается диффузионными процессами и химическими реакциями (обычно на границе матрица-волокно образуются интерметаллиды). Приходится применять различные приемы, например, наносить предварительно металлические покрытия на волокна, которые улучшают сцепление, но удорожают материал. Или проводят травление поверхности волокна. Это тоже улучшает схватываемость с металлом матрицы. На поверхности борных или углеродных волокон выращивают монокристаллы карбида кремния SiC. Получаются ворсистые волокна – борсик. Если основой волокна является тончайшая вольфрамовая проволока диаметром 12 мкм, то на ней можно нарастить кристаллы бора. Все волокно будет иметь диаметр 70–200 мкм. Такие волокна прочнее сцепляются с матрицей.
Основной недостаток волокнистых композитов – их высокая стоимость и сложная технология получения.
Углеродные волокна несколько дешевле. Их получают из синтетических органических волокон высокотемпературной обработкой. Они могут быть изготовлены в виде жгутов, нитей, ткани, лент. Каждое волокно состоит из мельчайших ленточек – фибрилл.
Стекловолокно производят с квадратной, прямоугольной, шестигранной формой – для лучшей укладки в матрице.
Применение КМ увеличивается с каждым годом. Главный потребитель – авиа-, ракетная и космическая техника. Из них изготавливают легкие и прочные корпуса, камеры сгорания ракетных двигателей, лопатки турбин, лопасти винтов, кузовные детали автомобилей.
Важнейшая деталь турбины – лопатка, изготовленная из никелевого сплава, упрочненного нитями сапфира Al2O3, выдерживает температуру газов на входе 1650 С! При этом предел прочности нитей составляет более 700 МПа.
Сопла ракет изготавливают из порошков вольфрама или молибдена с керамическими нитями Al2O3 в виде волокон или войлока. При этом прочность увеличивается в два раза.
Композиционные материалы на полимерной основе
В композитах на полимерной основе усилие от матрицы передается армирующему волокну за счет сил межмолекулярного взаимодействия адгезионного характера. Необходимо полное смачивание жидким связующим поверхности волокон.
Борные и углеродные волокна лучше смачиваются эпоксидной смолой. Так получаются боропластики и углепластики.
Стекловолокниты имеют максимальную прочность и удельную прочность: σв составляет 700 МПа и даже 2400 МПа (при уменьшении диаметра волокон и добавке монокристаллов Al2O3 в матрицу).
Соединяют композиты точечной сваркой, склеиванием, клееболтовыми и клеезаклепочными соединениями.
Наноматериалы
Наноматериалы материалы, содержащие структурные элементы, геометрические размеры которых хотя бы в одном измерении не превышают 100 нм, и обладающие качественно новыми свойствами и эксплуатационными характеристиками.
К таким материалам можно отнести наноразмерные частицы (нанопорошки), нанопроволоки и нановолокна, очень тонкие пленки (толщиной менее 100 нм), нанотрубки и т. п. Такие материалы могут содержать от одного структурного элемента или кристаллита (для частиц порошка) до нескольких их слоев (для пленки).
Для наночастиц доля атомов, находящихся в тонком поверхностном слое (толщиной порядка 1 нм), по сравнению с микрочастицами (обычными зернами) заметно возрастает. Доля приповерхностных атомов пропорциональна отношению площади поверхности частицы S к ее объему V. Если характерный размер частицы D, то S/V D2/D3 1/D. У поверхностных атомов, в отличие от атомов, находящихся в объеме твердого тела, задействованы не все связи с соседями. В результате в приповерхностном слое возникают сильные искажения кристаллической решетки, и даже может происходить смена типа решетки. Кроме того, свободная поверхность является стоком бесконечной емкости для точечных и линейных кристаллических дефектов (в первую очередь вакансий и дислокаций). При малых размерах частиц это приводит к выходу большинства структурных дефектов на поверхность и очистке материала наночастицы от дефектов структуры и химических примесей. Установлено, что процессы деформации и разрушения протекают в тонком приповерхностном слое с опережением по сравнению с внутренними объемами металлического материала. В наночастицах же весь материал работает как приповерхностный слой, толщина которого оценивается величиной 0,5…20 мкм.
Из этого следует, что закономерности, характерные для микроструктурных объектов, не соблюдаются при переходе к наноразмерным частицам. Изучение и использование необычных свойств наноматериалов является важнейшей задачей современного материаловедения.