Курс лекций для студентов Института природных ресурсов, направления 120700 «Землеустройство и кадастры» (18 часов)
Вид материала | Курс лекций |
- Программа вступительных испытаний в магистратуру по направлению 120700. 68- «Землеустройство, 177.22kb.
- Образовательный стандарт высшего профессионального образования по направлению подготовки, 344.1kb.
- Основная образовательная программа высшего профессионального образования Направление, 4128.43kb.
- Базовый курс рабочая программа и методические указания для студентов 1 курса заочной, 348.1kb.
- Программа вступительных испытаний по направлению магистерской подготовки 120700., 188.61kb.
- Тематика семинарских занятий для студентов I курса энергетического института (энин), 670.95kb.
- Курс лекций дисциплины «Компьютерные технологии и сапр» для студентов специальностей, 1793.82kb.
- Основная образовательная программа высшего профессионального образования Направление, 3396.78kb.
- За курс 9 класса билет, 42.57kb.
- Описание направления подготовки «Землеустройство и кадастры», 31.91kb.
НЕМЕТАЛЛИЧЕСКИЕ КОНСТРУКЦИОННЫЕ МАТЕРИАЛЫ
Ограничения в применении металлов
Металлические конструкционные материалы прочны и надежны в эксплуатации, технологичны и во многих случаях экономически эффективны. Но металлы обладают, тем не менее, рядом существенных недостатков, ограничивающих их применение.
Во-первых, многие металлы и сплавы подвержены коррозии в агрессивных средах. Высокая тепло- и электропроводимость металлов тоже не всегда является достоинством, так как необходимы и теплоизолирующие, и электроизолирующие материалы. Металлические материалы не всегда обеспечивают необходимую твердость и износостойкость в условиях трения. Во многих случаях недостаточной оказывается жаропрочность и жаростойкость металлов. Наиболее прочные металлические материалы имеют большую плотность, т. е. не позволяют получить высокую удельную прочность, необходимую для авиа- и космической техники. Наконец, технологическая цепочка от добычи руды до готового металлического изделия очень длинна по времени, включает огромное число операций и является весьма трудоемкой.
Поэтому во многих случаях применяют неметаллические материалы. Их обычно подразделяют на полимеры (пластмассы), керамики и стекла, о чем говорилось на первой лекции.
Полимеры, или пластмассы
Пластмассы – искусственные твердые материалы, получаемые на основе органических полимерных связующих веществ. Имеют большую молекулярную массу (свыше 10 000).
Состав пластмасс
1) Связующее – обязательный компонент. Это синтетические смолы или эфиры. Простые пластмассы (органическое стекло, полиэтилен, полипропилен) состоят почти из одного связующего.
2) Наполнители. Их содержание может доходить до 70 %. Могут быть порошковыми (сажа, графит, тальк, древесная мука), волокнистыми (хлопковые, стеклянные, асбестовые волокна), листовыми (бумага, ткани, древесный шпон). Наполнители повышают механическую прочность, снижают стоимость пластмасс и придают им нужные эксплуатационные свойства.
3) Стабилизаторы. Они нужны, чтобы макромолекулы полимеров не изменяли свою пространственную структуру, и свойства пластмасс с течением времени не менялись.
4) Пластификаторы. Их добавляют в количестве до 20 %. Они улучшают формуемость пластмасс, снижают хрупкость. Это обычно олеиновая кислота, стеарин, дибутилметафталат.
5) Отвердители. Их добавляют в пластмассы на основе термореактивных смол в качестве катализаторов отверждения. Это органические перекиси.
6) Специальные добавки – красители, смазки, антистатики, добавки против горения, против плесени и др.
Свойства пластмасс
Достоинствами пластмасс по сравнению с другими конструкционными материалами являются:
- малая плотность;
- высокая удельная прочность σв/γ;
- химическая стойкость;
- электроизоляционные свойства;
- теплоизоляционные свойства;
- меньшая трудоемкость переработки пластмасс по сравнению с переработкой металлов: изделие и материал создаются одновременно;
- меньшее количество отходов, чем при переработке металлов (коэффициент полезного использования материала не менее 0,9);
- как правило, не нужны отделочные операции.
При замене металлических деталей пластмассовыми масса снижается в 4–5 раз, трудоемкость уменьшается тоже в 4–5 раз, число операций уменьшается в 5–6 раз. Себестоимость снижается в 2–3 раза.
Основные недостатки пластмасс:
- ограниченная теплостойкость: максимальная температура эксплуатации термопластов – 250 С (фторопласт-4), а термореактивных пластмасс – около 400 С (стеклотекстолит);
- малая жесткость и вязкость;
- склонность к старению, т. е. к изменению свойств с течением времени.
Структура полимеров
Структурной единицей в полимерах является макромолекула, состоящая из огромного числа одинаковых групп атомов – звеньев. Каждое звено – это измененная молекула исходного низкомолекулярного вещества – мономера. В полимере молекулы мономера объединяются друг с другом и образуют длинные цепочки, в которых атомы соединены ковалентными связями.
К примеру, полимер полиэтилен (–CH2–CH2–)n, макромолекулы которого состоят из звеньев CH2, получают полимеризацией n-го числа молекул мономера – газа этилена CH2=CH2. Число n составляет тысячи.
Н


Рис. 101. Схематичные изображения макромолекул
полиэтилена и поливинилхлорида
Свойства полимеров определяются не только химическим составом, но и строением и взаимным расположением молекул.
Л
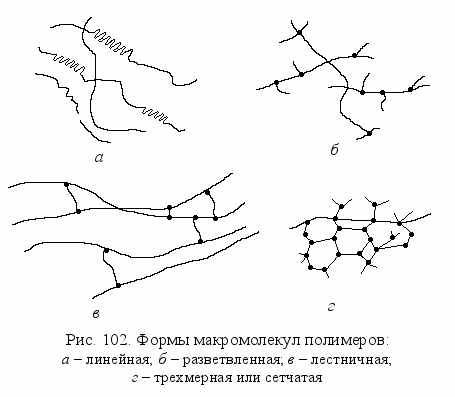
У полимеров с разветвленным строением силы притяжения между макромолекулами слабее, полимеры менее прочны (рис. 102, б). Они более плавкие, рыхлые.
В полимерах с лестничным строением имеются ковалентные связи между молекулами (рис. 102, в). Они прочные, неплавкие, нерастворимые (могут только размягчаться и набухать).
В полимерах с сетчатым строением все линейные участки связаны поперечными ковалентными связями. Все изделие представляет собой гигантскую пространственную молекулу (рис. 105, г). Такие полимеры хрупкие, стойкие к нагреву и растворителям (не размягчаются, не набухают). Это – термореактивные полимеры.
Строение линейной макромолекулы
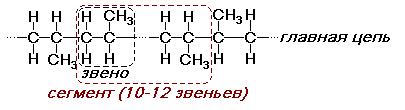
Рис. 103. Схематичное
изображение линейной
макромолекулы
Энергия ковалентной связи между атомами в главной цепи велика: Eсвязи = 350 КДж/моль. А энергия межмолекулярной связи примерно в 30 раз меньше. Поэтому макромолекулы сравнительно легко могут быть сдвинуты друг относительно друга. Кроме того, макромолекула – гибкая структурная единица: сегменты могут вращаться друг относительно друга, сохраняя валентный угол α (рис. 104). В этом причина нестабильности свойств полимеров: огромные гибкие макромолекулы не могут сохранять раз навсегда заданное пространственное положение.
В
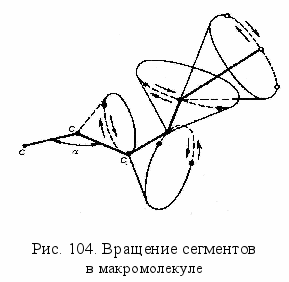
О
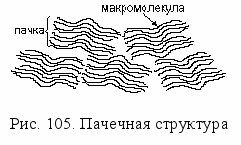
Б
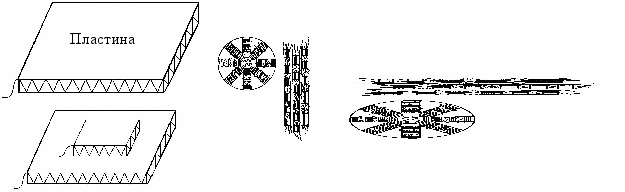
олее сложные и устойчивые упорядоченные участки называются кристаллами. Вначале макромолекулы «складываются» в ленты за счет многократного поворота сегментов на 180°. Ленты соединяются в пластины, которые наслаиваются и образуют кристаллы. В объеме полимера происходит чередование аморфных и кристаллических областей (рис. 106). Стопроцентной кристаллизации полимер никогда не достигает. Кристаллические полимеры прочнее при нагрузке и нагреве.
а б в
Рис. 106. Разные формы кристаллов:
а – образование кристалла из пластин; б – сферолит; в – фибриллы
Поведение полимеров при нагреве
Чтобы показать зависимость величины деформации ε от температуры, строят термомеханические кривые (при постоянном напряжении и скорости нагрева).
Р
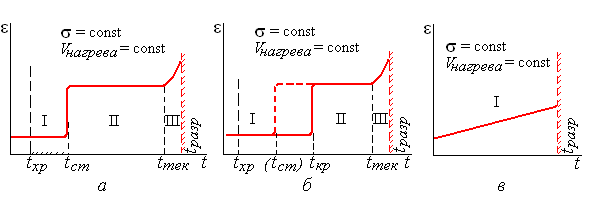
а – аморфный термопласт; б – кристаллический термопласт; в – термореактивный полимер
На рис. 107, а показано поведение при нагреве аморфного термопластичного полимера. При низких температурах полимер находится в стеклообразном состоянии (область I) и ведет себя как упругое твердое тело. Затем нагрев переводит его в высокоэластичное состояние (область II). Деформация полимера может достигать здесь сотен процентов (800 % у резин), но она обратима. При дальнейшем нагреве наступает вязко-текучее состояние; полимер ведет себя как вязкая жидкость (область III). Деформация необратима. Это область переработки пластмасс в изделия. Выше температуры термического разложения полимера tразр разрываются ковалентные связи в макромолекулах, выделяются низкомолекулярные соединения, и полимер разрушается. Однако при охлаждении у термопластов происходит полимеризация, структура и свойства полимера восстанавливаются.
Рис. 107, б показывает поведение термопластичного полимера, способного кристаллизоваться. Ниже температуры кристаллизации tкр полимер имеет упорядоченную структуру, выше – переходит в аморфное состояние. Так как на разрушение кристаллической структуры необходимо затратить энергию, кристаллический полимер становится высокоэластичным при более высокой температуре, чем аморфный.
На рис. 107, в показано поведение при нагреве термореактивного полимера. Он способен только на небольшую деформацию в упругой области, а затем, при нагреве выше tразр, необратимо разрушается. При охлаждении полимеризации не происходит, свойства не восстанавливаются.
Область рабочих температур полимера – ниже температуры стеклования tст, хотя кратковременно он может работать и немного выше этой температуры. Но надо учитывать, что ниже температуры хрупкости tхр полимер хрупко разрушается (для начала деформации здесь нужно напряжение, превышающее предел прочности). Таким образом, полимер надежно работает под нагрузкой в интервале температур от tхр до tст. Чем этот интервал шире, тем лучше.
Надо представлять, что температуры переходов полимера из одного состояния в другое (tст и tтек – температура текучести) не являются константами. Они зависят от условий нагружения. Чем больше скорость деформирования, тем выше эти температуры. В этом отличие от фазовых переходов в сплавах.
Поведение полимеров при нагружении (диаграммы растяжения)
Аморфный линейный полимер в стеклообразном состоянии способен на довольно большую упругую деформацию – до 20 % (область I на рис. 108, а). Модуль упругости E (tg α) у полимеров намного меньше, чем у металлов. Высокоэластическая деформация может составлять сотни процентов (рис. 108, а, область II). Она происходит за счет разгибания свернутых макромолекул. При дальнейшем увеличении нагрузки начинается смещение макромолекул друг относительно друга. Это – вязко-текучее состояние (рис. 108, а, область III).
При механическом нагружении полимер проходит до разрушения те же стадии, что и при нагреве, только энергию для перехода в новое состояние он получает за счет работы деформирования, а не за счет подвода тепла.
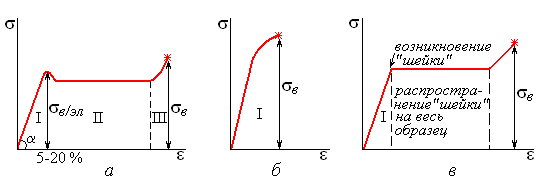
Рис. 108. Диаграммы растяжения полимерных материалов:
а – аморфный линейный полимер; б – термореактивный полимер;
в – кристаллический термопласт
Термореактивный полимер с сетчатой структурой способен испытывать только упругую деформацию, после чего наступает разрушение (рис. 108, б). Такие полимеры имеют большую жесткость E и прочность σв, чем термопласты.
Кристаллический полимер при температуре ниже tкр после равномерной упругой деформации (рис. 108, в, область I) образует местное сужение – «шейку», которая постепенно распространяется на весь образец. При этом идет изменение кристаллической структуры; деформация получается остаточная. Жесткость и прочность кристаллического полимера выше, чем у такого же полимера в аморфном состоянии.
Применение полимеров
Примеры применения пластмасс прочитать самостоятельно.
Надо заметить, что наиболее широко применяются не так уж много пластмасс из всего их разнообразия. Например, современный автомобиль имеет порядка 400 пластмассовых узлов и деталей. Но, в основном, они изготовлены из 5 полимерных материалов: полиуретанов, поливинилхлорида, стеклопластиков (наиболее прочные и жесткие, σв до950 МПа), полипропиленов, и АБС-пластиков (акрилонитрильный сополимер с добавкой СКС – бутадиенстирольного каучука в виде дискретной фазы, повышающей ударную вязкость пластмассы примерно в 15 раз).
Керамические материалы
Керамика – неорганические твердые материалы, получаемые высокотемпературным обжигом из отформованных минеральных масс. Можно сказать, что керамика – это все материалы, не являющиеся полимерами и металлами. В керамических материалах между атомами существует ковалентная или ионная связь.
Для получения керамики имеется огромное количество природных соединений; они составляют до 85 % земной коры. Только на долю кремния приходится около 40 %. В Томской области имеются собственные ресурсы для производства керамики: глинозем в Ачинске, Туганское месторождение циркониевых песков.
Современная техника использует более 7000 различных изделий из керамики: от ферритов, величиной с булавочную головку, и тонких пленок для сенсорных устройств до огромных изоляторов ЛЭП.
Структура керамики
Основа строительной, бытовой и художественной керамики – природные глины. Техническая керамика имеет более однородный состав, изготавливается из оксидов или безоксидных соединений.
П
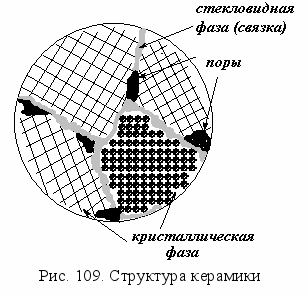
Кристаллическая фаза представляет собой химические соединения или твердые растворы. Она является основной и определяет прочность, жаропрочность и другие важнейшие свойства керамики.
Стекловидная, или аморфная фаза – это связка; ее количество может колебаться в широких пределах: от 1 до 40 %. Она снижает прочность и термостойкость, но облегчает технологию производства.
Газовая фаза находится в порах керамики. По доле пор в объеме материала керамика делится на пористую и плотную. В технике чаще используется плотная керамика. Но и она содержит определенную долю пор.
Свойства керамики
Достоинствами керамики являются:
- высокая твердость и износостойкость;
- высокие рабочие температуры (до 3500 С);
- высокая коррозионная стойкость в различных средах;
- низкая тепло- и электропроводимость: керамические материалы – диэлектрики и теплоизоляторы;
- малая плотность, легкие материалы.
Основной недостаток керамики:
- в
ысокая хрупкость. Ударная вязкость керамики примерно в 40 раз меньше, чем у металлов. Это ограничивает ее применение в технике. Керамика имеет низкую прочность при растяжении и изгибе. Пластически не деформируется.
Высокие твердость и температуры плавления керамических материалов обусловлены большой энергией связи между атомами. Это ковалентные или ионные соединения. Сильная межатомная связь определяет высокое сопротивление деформации (рис. 110), поэтому специальной упрочняющей обработки для керамики не требуется.
В металлах с ненаправленной межатомной связью дислокации перемещаются легко (рис. 110, а). В керамике с ковалентными связями их движение затруднено, так как требует разрыва и нового формирования локализованных межатомных связей (рис. 110, б). В кристаллах с ионной связью есть плоскости лёгкого скольжения (под углом 45° на рис. 110, в) и очень затруднённого, где сила отталкивания одноимённых зарядов препятствует ему (горизонтальные и вертикальные плоскости на рис. 110, в).
Для повышения вязкости керамики применяют различные способы. Прежде всего, в керамическом материале должно быть как можно меньше пор, являющихся зародышами трещин. На сегодняшний день разработаны следующие основные способы увеличения вязкости керамики:
- легирование или модифицирование,
- упрочнение дисперсными частицами,
- упрочнение нитевидными кристаллами более прочной керамики,
- «затупление» трещины за счет создания множества микротрещин: тогда магистральная трещина не развивается.
Над решением актуальной проблемы – повышением трещиностойкости (вязкости) керамики – работают ученые-материаловеды во всем мире, в том числе и ученые Томского Института физики прочности и материаловедения.
Классификация и применение керамики
Техническую керамику можно подразделить на 3 группы: оксидную, безоксидную (бескислородную) и металлокерамику.
1) Оксидную керамику получают из оксидов различных элементов: Al, Mg, Zr, Si, Be, U. Она состоит в основном из кристаллической фазы и пор. Стекловидная фаза появляется только за счет примесей.
Оксидная керамика твердая, огнеупорная, химически стойкая в кислотах, щелочах, на воздухе. Рабочие температуры составляют 0,8–0,9 от температур плавления (от 2000 до 3300 С). Но резких изменений температуры она не выдерживает.
Пористая керамика этой группы применяется как теплоизоляционный материал и огнеупорная футеровка камер сгорания, металлургических печей и ковшей (динасовый, магнезитовый, шамотный кирпич). Вспененная керамическая теплоизоляция «Бурана» имела всего 5 % материала и 95 % пор, заполненных инертным газом. Из пористой керамики делают также фильтры для различных жидкостей (воды, вина, масла).
Керамику на основе оксида алюминия Al2O3 называют корундовой. Она применяется очень широко:
- обтекатели радиолокационных антенн,
- подшипники печных рольгангов,
- вводы и поддерживающие устройства для нагревателей термических печей,
- электроизоляторы,
- сопла аргоно-дуговых горелок, форсунок для закачки воды в скважину (давление 150 атм), пескоструйных и дробеструйных установок,
- фильеры для волочения проволоки,
- нитеводители в текстильной промышленности,
- режущий инструмент,
- распределители и шайбы в бытовой сантехнике,
- торцевые уплотнители для насосов.
Керамика на основе оксида циркония ZrO2 имеет очень важную особенность. ZrO2 испытывает 3 полиморфных превращения при нагреве: моноклинная решетка превращается в тетрагональную, а затем в кубическую. Тетрагональную решетку можно сохранить при низких температурах с помощью модифицирования. Тогда фазовое превращение начинается за счет приложенного напряжения. Такая модифицированная керамика имеет прочность
3000 МПа при критерии трещиностойкости K1C = 20-25 (у обычной керамики – не более 4). Из ZrO2 делают твердооксидные топливные ячейки (для выработки электроэнергии), датчики содержания кислорода в расплаве стали.
2) Бескислородная (безоксидная) керамика – это карбиды MexCy, нитриды MexNy, бориды MexBy и т. п. Это тугоплавкие соединения, их огнеупорность достигает 3500 С. Твердость приближается к твердости алмаза. Они обладают высокой износостойкостью и жаростойкостью.
Карборунд SiC – твердый, химически стойкий, легкий, жаростойкий материал. Из него делают нагреватели печей, чехлы термопар, лопатки газовых турбин, детали ДВС, шлифовальные круги, защитные покрытия на графите.
Нитрид кремния Si3N4 стоек в расплавленных металлах и шлаках. Применяется для деталей газовых турбин, жаростойких инструментов, тиглей, кристаллизаторов, деталей насосов для перекачки расплавленных металлов.
3) Керамико-металлические материалы, или керметы, получают путем перемешивания порошков тугоплавкого керамического соединения и металла. Затем смесь порошков прессуется и спекается. Металл играет роль связки; он повышает пластичность и вязкость. При этом возрастает и σизг. В качестве связок используются кобальт, никель, железо, молибден. Керамическая составляющая может быть как оксидной, так и бескислородной.
Широко применяемые керамико-металлические материалы – это инструментальные твердые сплавы. Из них делают режущие пластины для фрез, сверл, зенкеров, резцов, а также штампы, волоки, бурильный инструмент. Они состоят из карбидов WC, TiC, TaC и кобальтовой связки. Применяются также материалы Cr7C3 – Ni, Al2O3 – Cr, BeO – W.
Поскольку главным ограничением в применении керамики является недостаточная вязкость, то особое значение имеет определение вязкости разрушения керамических материалов.
Вязкость разрушения К1С характеризует локальное повышение растягивающих напряжений у вершины трещины при переходе ее от стабильной к нестабильной стадии роста:
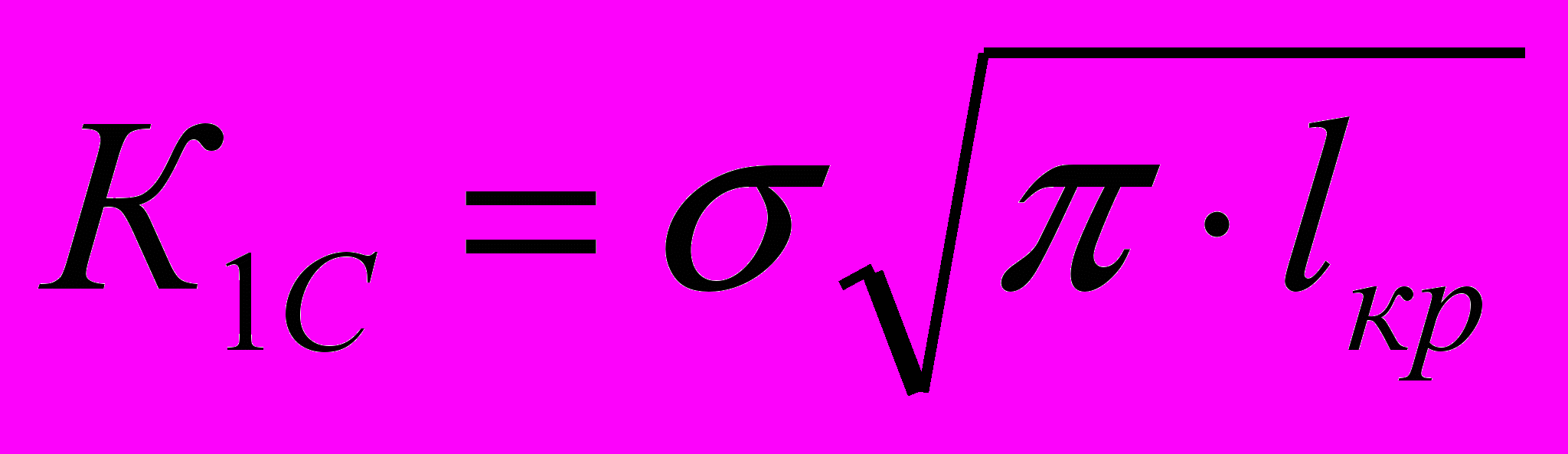
Т
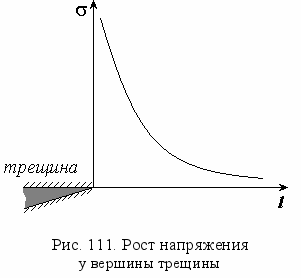
При превышении критической длины (при данном среднем напряжении
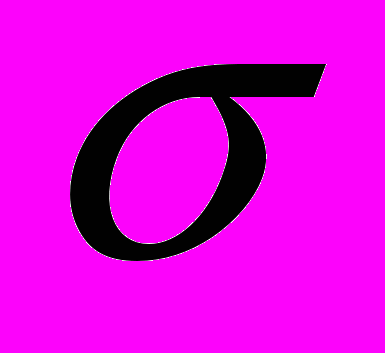
Зная вязкость разрушения, или трещиностойкость, можно определить размер допустимой трещины lкр при данном рабочем напряжении
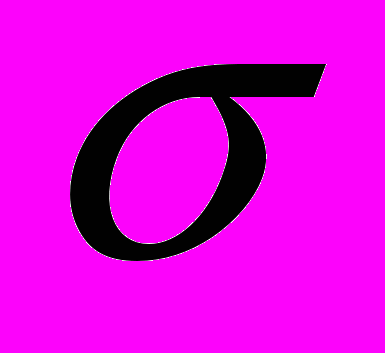
Чем выше значение К1С, тем меньше опасность хрупкого разрушения и выше надежность конструкции. У керамики величина К1С примерно в 50 раз ниже, чем у пластичных металлов. Для керамических материалов вязкость разрушения определяют по величине самой длинной трещины, образовавшейся в ходе испытаний твердости по методу Виккерса.
Практическое занятие 8
Строительная керамика
Строительные керамические материалы – это кирпич, цемент, бетон и природный камень.
Кирпичи и керамические плитки изготавливают из глины, которую формуют во влажном пластичном состоянии, а затем высушивают и обжигают. Глина состоит из водных алюмосиликатов типа Al2(Si2O5)(OH)4 с различными примесями. После обжига изделие состоит из кристаллических силикатов, связанных аморфной фазой на основе SiО2. Аморфная фаза образуется и плавится при обжиге, растекаясь по поверхности кристаллов и связывая их воедино. Этой технологии уже более 5000 лет, хотя на современном предприятии процессы, в отличие от древних времен, механизированы и автоматизированы.
Цемент представляет собой смесь известняка CaO, диоксида кремния SiО2 и оксида алюминия Al2O3, которая отвердевает при смешивании с водой. Цемент твердеет вследствие химической реакции, а не из-за высыхания, поэтому важно сохранять его влажным вплоть до завершения химических реакций. Это быстротекущее схватывание за первые 4 часа и более медленные реакции отверждения, для завершения которых нужно примерно 100 дней. Реакции гидратации идут с выделением тепла. В крупномасштабных конструкциях, таких как плотины, это может вызвать проблемы. Тогда в бетон закладывают охлаждающие трубы, которые затем становятся дополнительной арматурой.
Важнейшей характеристикой цемента служит его марка. Марку цемента определяют по пределам прочности при сжатии и изгибе образцов. Например, цемент марки М400 имеет предел прочности при сжатии 40 МПа.
Бетон – это композиционный материал, состоящий из песка и камней, связанных отвердевшим цементом. Наполнители имеют высокую твердость и прочность, слабой фазой в бетоне является затвердевшая цементная масса, определяющая его прочность. Для уплотнения наполнителя берется смесь песка и гравия в соотношении 60:40. Плотноупакованные частицы заполняют поры, которые понижают прочность и способствуют проникновению в бетонную конструкцию воды. Замерзание воды может вызвать растрескивание бетона. Цементная масса при твердении дает усадку, что приводит к возникновению мелких усадочных трещин. Насыщение бетона мелкими пузырьками воздуха до его заливки тормозит распространение таких трещин.
Главной прочностной характеристикой бетона служит его марка по прочности на одноосное сжатие (см. рис. 112 и 113). Марка бетона определяется по пределу прочности при сжатии образцов – кубов размером
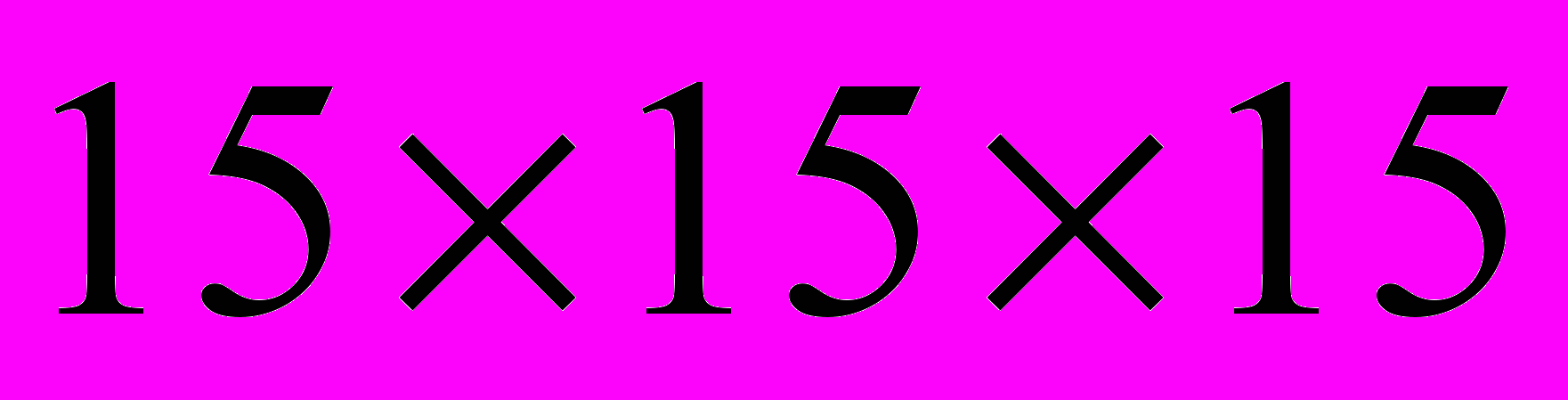
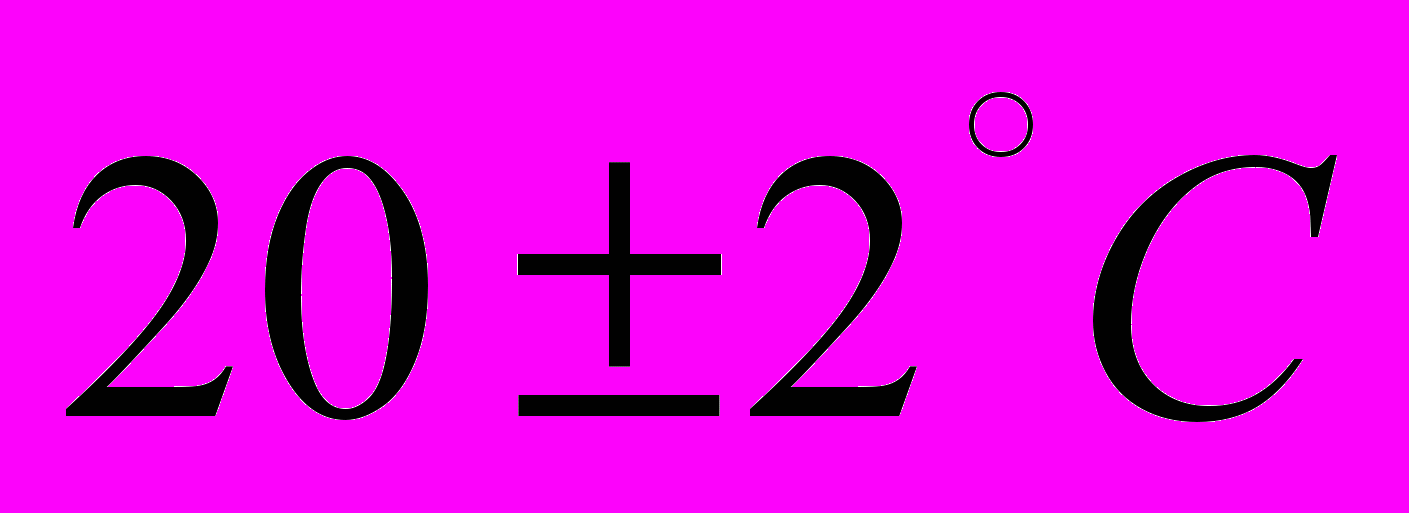
Классы бетонов также определяют по пределу прочности на сжатие (МПа): В1; B1,5; B2,5; B3,5; B7,5; B10; B15; B20; B25; B30; B40; B50; B55; B60. Вероятность получения заданной прочности по классам выше, чем по маркам; гарантия составляет 95 %, такой высокой гарантии у марок нет.
К
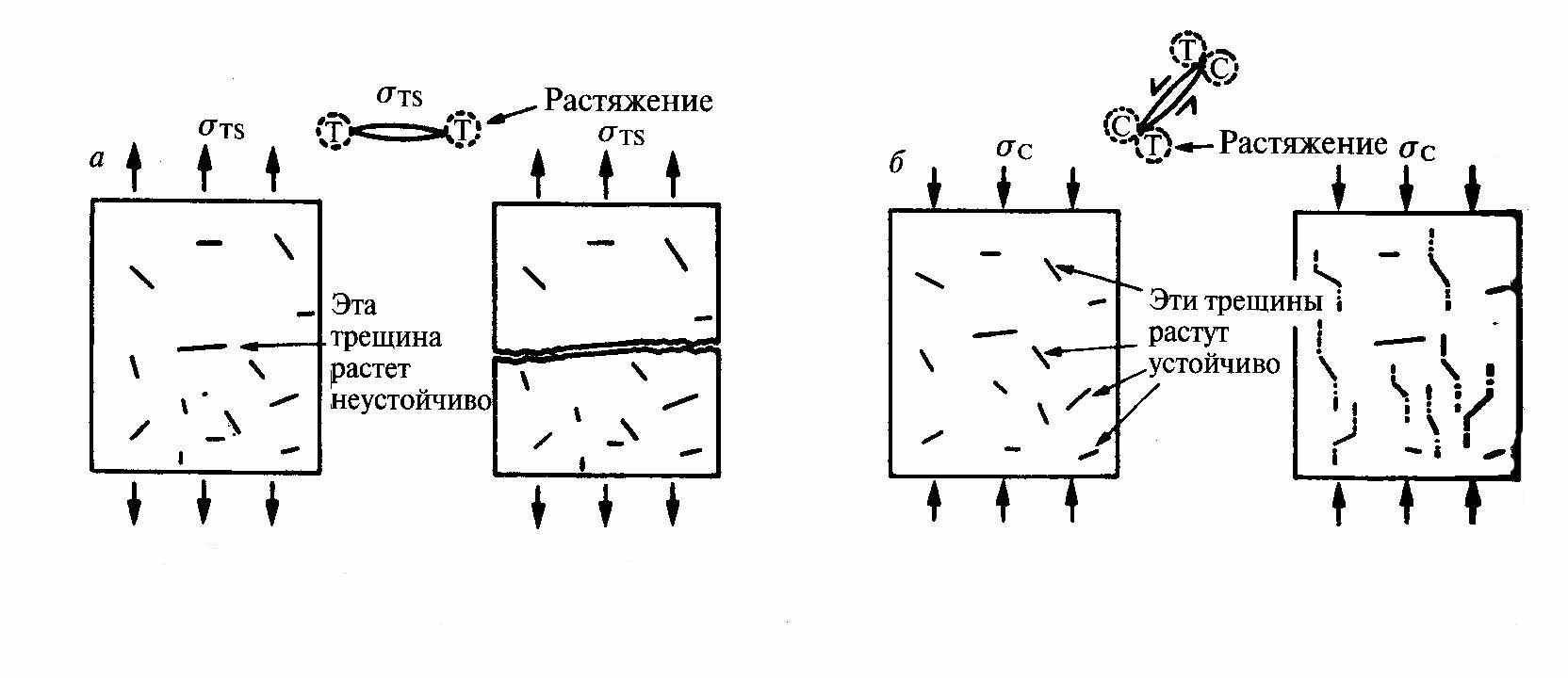
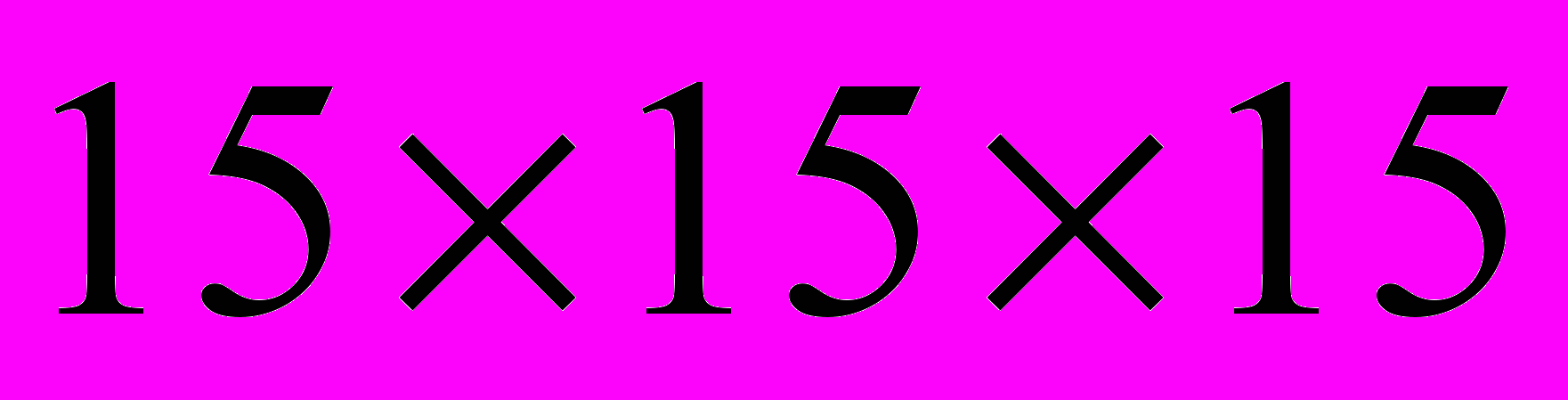
а б
Рис. 112. При растяжении самая длинная трещина растет неустойчиво (а);
при сжатии смятие образца вызывается устойчивым ростом множества трещин (б)
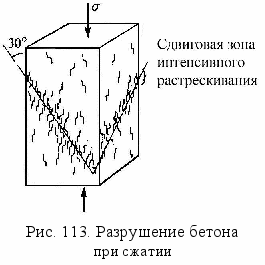
Прочность бетона при растяжении примерно в 15 раз меньше, чем при сжатии (не более 4 МПа). Зная вязкость разрушения (К1С = 0,5 МПа·м1/2), можно подсчитать, что критическая длина трещины составляет примерно 1 мм. Такие дефекты в бетоне присутствуют практически всегда. Поэтому его используют только в конструкциях, работающих на сжатие.
Армирование бетона стальными профилями позволяет увеличить предел прочности при растяжении до 410 МПа. Железобетон – комплексный строительный материал, в котором бетон и стальная арматура, имеющие прочное взаимное сцепление, работают совместно как единая система. Растягивающие усилия воспринимаются стальной арматурой, а сжимающие – бетоном.
При изготовлении бетона марка цемента должна быть выше проектной марки бетона, определяемой по пределу прочности при сжатии (табл. 5).
Таблица 5
Соответствие марок цементов и бетонов
Марка бетона | 150 | 200 | 250 | 300 | 350 | 400 | 450 | 500 | 600 и выше |
Марка цемента | 300 | 300, 400 | 400 | 400, 500 | 400, 500 | 500, 600 | 550, 600 | 600 | 600 |
Лекция 9