Аннотационный отчет за 2010 год по Программе II «Наноструктурные слои и покрытия: оборудование, процессы, применение»
Вид материала | Отчет |
Исследование гетерогенных состояний со сменами знаков приращения масс компьютерными моделями T-x-y диаграмм. |
- Информационное сообщение Российская школа-конференция молодых ученых «Биосовместимые, 109.06kb.
- Аннотационный отчет о научно-исследовательской работе за 2010 год, 1473.89kb.
- Открытая школа-конференция стран СНГ «Ультрамелкозернистые и наноструктурные материалы - 2010», 62.58kb.
- Отчет в твердой копии в двух экземплярах (1-ый сброшюрованный, 2-ой расшитый). Аннотационный, 37.09kb.
- 1 в наименовании слова «2010 год» заменить словами «2010 2011 годы», 799.81kb.
- Отчёт о работе пцк музыкально-эстетического цикла за 2009 2010 учебный год, 243.6kb.
- Отчет о финансовом положении по состоянию на 31 декабря 2010 года 4 Отчет о прибылях, 1202.33kb.
- Методология разработки нормативной документации, определяющей потребительское качество, 171.5kb.
- Отчет о финансовом положении за 31 декабря 2010 года 5 Отчет о прибылях и убытках, 1799.06kb.
- Отчет о финансовом положении за 31 декабря 2010 года 5 Отчет о прибылях и убытках, 2345.51kb.
Высокоскоростная деформация и откольное разрушение металлических материалов с субмикро- и нанокристаллической структурой при воздействии наносекундного релятивистского сильноточного электронного пучка.
Выполнены эксперименты (электронный ускоритель «СИНУС-7», пиковой плотности мощности 3.41010 Вт/см2 при длительности импульса электронного тока на полувысоте 45 нс) и показано, что c ростом толщины мишени в интервале от 1,7 до ~6 мм толщина отколотого слоя (скорость деформации ~106 c-1) растет от 0,2 до 0,6 мм. Установлено, что в случае крупнозернистого титана относительная деформация отколотого слоя составляет ~ 20 %, что в ~1,5 раза меньше деформации до разрушения при квазистатическом растяжении. При переходе к нанокристаллическому титану деформация материала в зоне откола резко снижается, фиксируется интенсивное трещинообразование, что коррелирует с пониженной вязкостью данного материала. Выявлено, что независимо от размера зерна финишная стадия откольного разрушения осуществляется путем вязкого ямочного отрыва, типичного для квазистатического нагружения. Размер ямок отрыва слабо зависит от скорости деформирования и уменьшается при измельчении зерна, что согласуется с пониженной вязкостью ультрамелкозернистой структуры.
Разработка генератора кислородной плазмы на основе разрядной системы с инжекцией электронов и распыляемым металлическим катодом-мишенью; измерение параметров разрядов и генерируемой плазмы
Разработан генератор газо-металлической плазмы на основе разрядной системы с инжекцией электронов. Показано, что наличие внешнего эмиттера электронов обеспечивает некритичность параметров основного объемного разряда к образованию оксидных пленок на поверхности его катода, что обеспечивает стабильную генерацию объемной плазмы кислорода без использования импульсно-периодических высокочастотных источников питания. Измерены характеристики разрядной системы и параметры генерируемой плазмы. Ресурсные испытания разработанной разрядной системы при работе с кислородом составили не менее 500 часов. Показано, что параметры плазмы основного разряда в процессе работы остаются практически неизменными. При этом в ходе выполнения всей экспериментальной программы проекта, не требовалось проведения регламентных работ, либо замены электродов для восстановления работоспособности устройства.
Проект II.7.4.3. Процессы образования поверхностных наноструктурных слоев и покрытий боридов и карбидов при интенсивном воздействии электронным пучком (Отдел физических проблем БНЦ СО РАН).
Научный руководитель проекта – д.т.н. Н.Н.Смирнягина
Исследование кинетики и выявление механизмов формирования слоев боридов и карбидов в высоком вакууме под воздействием электронного пучка.
а) Осуществлен анализ закономерностей формирования наноструктур при воздействии мощного электронного пучка в поверхностных слоях на основе карбидов и боридов переходных металлов. Исследованы условия образования, структура и свойства слоев на основе боридов железа на углеродистых сталях (3, 20, 45 и У8А) при электронно-лучевом борировании и в результате электронно-лучевой наплавки продуктов взаимодействия оксида Fe2O3, бора и углерода в вакууме.
Применение высококонцентрированного источника энергии (электронного пучка) позволяет очень быстро передавать энергию электронного пучка при его соударении с поверхностью обрабатываемого металла (насыщающая обмазка, содержащия борирующий компонент), нагревать зону контакта до очень высоких температур. Это способствует увеличению диффузии бора из насыщающей обмазки по поверхности и проникновению его в объем металла, взаимодействию и образованию боридов железа. Толщина боридного слоя зависит от состава борирующего компонента. Слои толщиной 300-360 мкм получены при использовании аморфного бора, а толщиной 100-150 мкм – карбида бора. При воздействии электронного пучка на реакционные обмазки, содержащие оксид Fe2O3, бор и углерод наблюдается наплавка продуктов (боридов Fe2B и FeB) Толщина боридных слоев составляла 200-280 мкм (Fe2B ) и 50-80 мкм (FeB).
Фазовый состав боридного слоя также зависит от состава борирущего компонента. По данным РФА, слои содержат бориды Fe2B и FeB, но количественное соотношение их различно. В боридном слое, сформированном на основе аморфного бора, преобладает борид Fe2B. Борид FeB является преобладающей фазой в слое, образованном из насыщающей обмазки на основе карбида В4С. На рентгенограммах присутствуют также линии, принадлежащие ферриту (-Fe), отсутствуют рефлексы борированного цементита (Fe23(C,B)6).
б) Исследованы и сопоставлены микроструктуры, микротвердость и износостойкость боридных слоев, сформированных различными методами – диффузионном насыщение (электронно-лучевом борировании в вакууме и химико-термической обработке из насыщающих обмазок), а также при электронно-лучевой наплавке продуктов СВС, инициируемых воздействием элекронным пучком.
В низкоуглеродистых сталях (Сталь 3) боридный слой имеет игольчатое строение, при котором иглы боридов, срастаясь в основаниях, образуют сплошной слой Непосредственно к иглам боридов примыкают перистые выделения карбоборидной фазы. Микротвердость боридных игл составляет 1300-1350 HV, перистых выделений 300-330 HV. Толщина слоя - 70-90 мкм.
Боридный слой на стали Ст3, сформированный из обмазки на основе карбида бора состоит из округлых включений, располагающихся на поверхности слоя и эвтектики, имеющих микротвердость 820-840 HV и 510-530 HV. Боридный слой, сформированный из обмазки на основе аморфного бора, имеет другую структуру. Он состоит из частиц различной формы: ромбической, призматической, дендритной. На поверхности слоя располагается сплошная светлая пленка с иглами, направленными вглубь образца. Микротвердость ее составляет 1200-1250 HV. Внутри пленки встречаются редкие (1-2) крупные включения с микротвердостью 1750-1820 HV. Под пленкой находятся первичные кристаллы и эвтектика с микротвердостью 840-880 HV и 500-540 HV, соответственно.
Структура слоев боридов Fe2B и FeB сложная, включает первичные кристаллы борида, дендритные включения и эвтектики. Во всех слоях наблюдали эвтектики, имеющие микротвердость 650-700 HV. Округлые и протяженные включения имели упорядоченное расположение в слое, их микротвердость в слоях была: FeB (1080 и 1150 HV), FeB+B2O3 (1250 1150 HV), соответственно. Округлые включения были лишь в слоях Fe2B (1200 HV) и Fe2B+B2O3 (1150 HV).
Приработка упрочняющих слоев производилась на машине трения ЛТС. Исследование проводили в режиме «диск по колодке» при постоянной нагрузке (Р=1,5 кг) и постоянной скорости скольжения (v=0,2 м/сек). В качестве контр-тела использовали закаленный образец стали У8А с твердостью HRC=63.
Установлено, что наименьшим износом обладают слои на основе боридов Fe2B и FeB, сформированных из реакционных обмазок, содержащих оксид Fe2O3, бор аморфный и углерод. Вероятно, это связано с тем, что твердые частички боридов железа находятся в пластичной матрице эвтектики слоя. Износостойкость этих слоев выше, у диффузионных боридных слоев, полученных методами химико-термической обработки и электронно-лучевым борировании. Модифицированные диффузионные боридные слои после воздействия электронным пучком имеют в два раза ниже износостойкость.
Таким образом, комплексная электронно-лучевая обработка углеродистой стали Ст3 позволяет модифицировать поверхностные свойства. Электронно-лучевое борирование расширяет эксплуатационные характеристики деталей машин, работающих в условиях сухого трения.
в) Исследованы и сопоставлены микроструктуры и микротвердость боридных слоев, сформированных различными методами - электронно-лучевом борировании в вакууме и химико-термической обработке из насыщающих обмазок. Сформированные слои обладают гетерогенной структурой, сочетающей твердые и пластичные компоненты, приводящие к уменьшению хрупкости боридного слоя.
Боридные слои испытывали на термическую устойчивость и жаропрочность. Для этого все образцы нагревали в печи сопротивления КО-14 до определенных температур и выдерживали в течение 2 часов для установления равновесия.
Измерена микротвердость отдельных составляющих боридных слоев, а именно, игл, сформированных при твердофазном борировании, округлых включений и эвтектики в слоях после электронно-лучевого борирования. Если в исходном состоянии боридные слои, полученные в результате твердофазного борирования, обладают более высокой твёрдостью по сравнению со слоями, полученными при электронно-лучевом борировании, то при нагреве до температуры 800-900оС микротвёрдость становится практически сопоставимой.
Исследованием микроструктуры установлено, что, начиная с температуры 700С в боридных слоях, полученных в результате твердофазного борирования, начинают образовываться трещины. Зарождение трещины начинается с поверхности. Увеличение температуры нагрева приводит к росту трещины вглубь слоя и к её раскрытию. В слоях, полученных при ЭЛБ, трещины не обнаружены.
Дальнейшее повышение температуры нагрева до 1300оС на воздухе приводит к постепенному уменьшению толщины боридных слоев. Наиболее интенсивно это наблюдается в слоях, сформированных при твердофазном борировании., в которых происходит потеря массы слоя и полное его разложение при температурах выше 1150-1300оС. В слоях, полученных при электронно-лучевом борировании, трещины не обнаружены.
Известно, что наряду с высокой твёрдостью и износостойкостью, боридные слои обладают и существенным недостатком – повышенной хрупкостью. Проведенные исследования показали, что использование электронного нагрева позволяет снизить хрупкость и повысить пластичность.
Из анализа полученных данных следует, что после электронно-лучевого борирования слои более пластичны, чем после твердофазного. Кроме того, слои после электронно-лучевого борирования имеют гетерогенную структуру, сочетающую твёрдые (хрупкие) и более пластичные структурные составляющие. Такое сочетание отчасти объясняет отсутствие термических трещин при нагреве боридных слоёв до высоких температур.
Хрупкость боридных слоев зависит от фазового состава. Балл хрупкости борида Fe2B меньше в два раза по сравнению FeB. В целом, балл хрупкости определяется фазовым составом боридного слоя. По данным рентгенофазового анализа слои после твердофазного борирования состоят из боридов Fe2B, FeB и борированного цементита. Слои двухфазны. Первая зона состоит из боридов, на поверхности располагаются иглы FeB, под ними Fe2B, а затем переходная зона, содержащая борированный цементит. Наряду с высокой хрупкостью боридный, двухфазный слой имеет ярко выраженную склонность к скалыванию. Скалывание происходит на границе раздела фаз. В однофазном слое скалывание наблюдается на границе непрерывного слоя. Следовательно, однофазные слои боридов меньше склонны к скалыванию.
Выравнивание микротвёрдости боридных слоёв после твердофазного и ЭЛБ при высоких температурах (900оC) позволяет сделать вывод об использовании ЭЛБ для упрочнения режущих инструментов и др., испытывающих разогрев в процессе работы до столь высоких температур без существенного снижения эксплуатационных свойств.
г) Исследованы и обсуждены условия образования, структура и стойкостные свойства боридных слоев на поверхности режущих пластин из быстрорежущей стали Р18, сформированных при электронно-лучевой обработке в вакууме.
При электроннолучевом борировании стали Р18 с плотностью мощности электронного пучка J =2.8104 (Вт/см2) слой образовывался в результате глубокого проплавления, что определило его строение. Из анализа структуры поверхностного слоя видно, что при направленной кристаллизации главная ось линейчатых дендритов ориентирована в направлении отвода тепла. Строение дендритов (цепочка отдельных глобулей) говорит о прерывистом характере их образования. При плотности мощности электронного пучка J =2.5104 (Вт/см2) слой состоит преимущественно из звездчатых дендритов. При уменьшении плотности мощности до пучка J =2.2104 (Вт/см2) поверхностный слой также содержит звездчатые дендриты, однако их количество не является доминирующем. Микротвердость слоя составляет 1100-1860 кг/мм2. Толщина слоя 25-100 мкм.
Для оценки трибологических свойств полученного слоя проводились стойкостные испытания резцов. Испытания проводили на токарно-винторезном станке 1А616 на следующих режимах: подача - 0,1 мм/об, частота вращения - 224 об/мин, глубина резания - 1,0 мм. Обрабатываемый материал – стали 45 и 12Х18Н10Т. Износ резцов определяли по задней поверхности с помощью лупы Бринеля. Геометрические параметры резцов: передний угол =15o, главный задний угол =8о, главный угол в плане =45о. За критерий стойкости резцов принято время достижения предельного износа по задней поверхности равного 0,6 мм.
Результаты испытаний кинетики износа резцов из стали Р18 показали, что образование боридного слоя толщиной 8-10 мкм на передней поверхности, позволяет увеличить стойкость резцов почти в 1,5 раза (для обрабатываемой стали 12Х18Н10Т).
Более значительное повышение стойкости резцов связано с увеличением толщины боридного слоя. При электронно-лучевом борировании толщина борированного слоя может достигать 300 мкм, однако температура обработки при этом составляет 1100-1200оС. Время обработки 2-3 мин. Исходя из этого, электронно-лучевое борирование может быть рекомендовано не как заключительная, а как промежуточная операция обработки режущего инструмента, например, перед закалкой. Необходимо отметить, что для получения аналогичного по толщине слоя при традиционном борировании (например, при борировании в герметичных контейнерах с плавким затвором) требуется не менее 3 часов.
Исследование гетерогенных состояний со сменами знаков приращения масс компьютерными моделями T-x-y диаграмм.
а) Выполнен аналитический вывод геометрических характеристик границ трехфазных областей, вызывающих возникновение условий смены типа реакции (с эвтектического на перитектическое, с эвтектоидного на перитектоидное, с синтектического на монотектическое), проведено математическое моделирование явлений смены типа трехфазных превращений при кристаллизации сплавов.
При прохождении трехкомпонентным центром масс в процессе кристаллизации трехфазной области участие одной из фаз трехфазного превращения может временно прекратиться, а затем возобновиться, но уже с другим знаком приращения массовой доли этой фазы. Например, если приращения масс участников фазовой реакции NА+В в некотором температурном интервале имеют знаки mN<0, mA>0, mB>0, то при некоторой температуре Т эта реакция может принять вид NА с mB=0, а затем трансформироваться в N+BA с mB<0. Аналогичные трансформации могут иметь место в различных сочетаниях фаз N, А и В в левой и правой частях реакции. Чаще всего встречается вариант перехода с участием жидкой фазы N=L, когда эвтектическое превращение сменяется перитектическим.
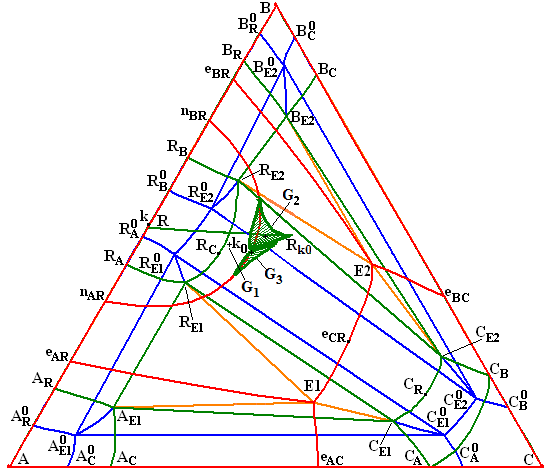
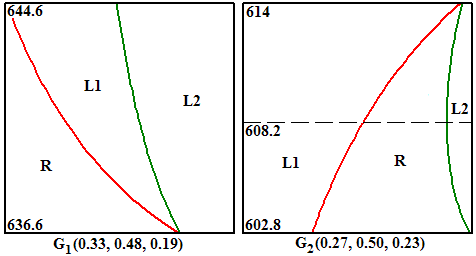
Рис. 1. Синтектическое превращение L1+L2R (сплав G1)
и переход его в монотектические реакции L1R+L2 (G2), L2R+L1 (G3)
Подобного рода явления обнаружены экспериментально, например, в системе Ti-Ru-Ir конгруэнтный характер кристаллизации L+Ru (=TiIr3) меняется на инконгруэнтный L+Ru и в системе Zr-Ru-Ir - с инконгруэнтного L+ на конгруэнтный L+ (=ZrIr3, =ZrIr2) (Еременко В.Н., Хоружая В.Г., Штепа Т.Д. Порошковая металлургия, 1985. № 5. С. 51-56; 1987. № 11. С. 72). Изменение эвтектоидного типа превращения на перитектоидный в металлических системах отмечалось в работах Шрамма (Schramm J. Kupfer-Nickel-Zink-Legierungen. Wursburg. Konrad Triltsch. 1935) и Куо (Kuo K. J. of the Iron and Steel Institute. 1955. V. 181. P. 223): «если трансформировать двухфазную область у+z бинарной системы в трехфазную область x+y+z тройной системы, необходимо рассматривать один их трех ее вариантов с приращением фазы x: у+zx, уx+z, zx+y». Подобный переход (от синтектического L1+L2R превращения к монотектическому L1R+L2 или L2R+L1) имеет место в системах с расслаиванием (рис. 1).
Смена знака приращения массы одной из твердых фаз при изменении типа трехфазной реакции с эвтектической на перитектическую или наоборот оказывает влияние на качественный состав формируемой микроструктуры. Изменению типа трехфазного превращения соответствуют поверхности (рис. 2,а) двухфазной реакции при индифферентном поведении третьей фазы: LА при mС=0 (рис. 2,б) и LС при mА=0 (рис. 2,в). В первом случае охлаждаемый расплав G1 (рис. 2,а) при прохождении трехфазной области сначала участвует в эвтектической реакции LАе+Се, а затем ниже температуры 430о выделившиеся до этого первичные кристаллы А1 и эвтектические кристаллы Ае реагируют с расплавом по перитектической схеме L+ACp и их количество убывает, оставляя после себя смесь Ср+Се. Во втором случае охлаждение исходного состава G2 приводит к замене перитектической реакции L+САр на эвтектическую, в результате чего в субсолидусную смесь входят кристаллы А двойного происхождения: Ар+Ае.
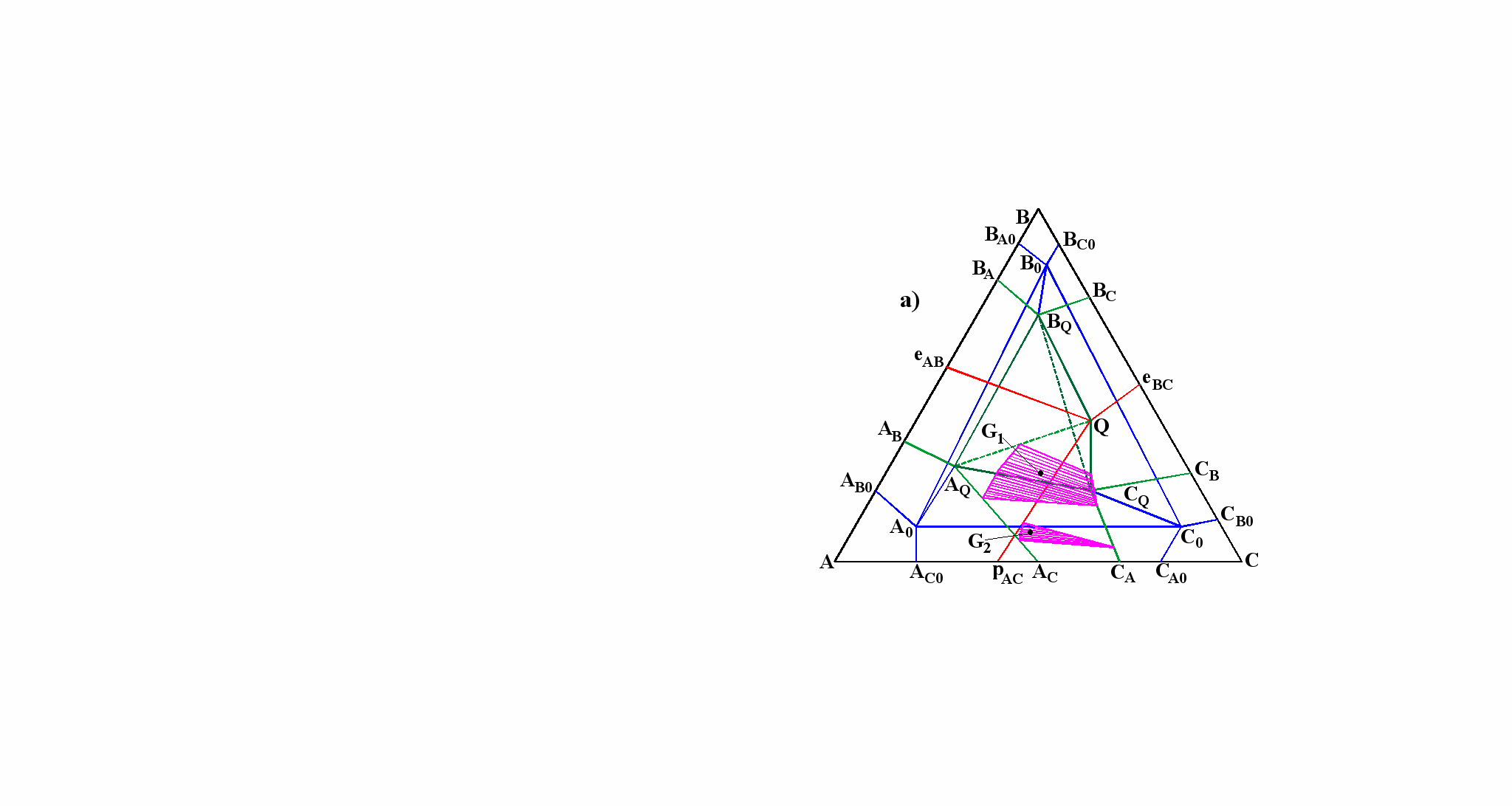
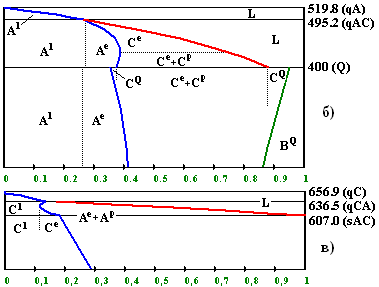
Рис. 2. T-x-y диаграмма с нонвариантным превращением типа L+ABQ+CQ (а) и двойной сменой типа трехфазного превращения: с LAe+Ce на L+ACp (G1) и с L+CAp на LAe+Ce (G2)
Один и тот же расплав может несколько раз проходить через такие стадии кристаллизации, которые требуют особенно пристального исследования формируемой микроструктуры. Так, например, в центре масс G1 (рис. 2,а) после смены типа реакции с LAe+Ce на L+ACp происходит нонвариантная перегруппировка фаз L+ABQ+CQ: количество первичных и эвтектических кристаллов А после взаимодействия с расплавом L уменьшается, а в состав затвердевшей гетерогенной смеси к мелкодисперсным образованиям Ср+Се добавляются продукты нонвариантной перитектической реакции CQ+BQ. Результирующая микроструктура состоит из A1+Аe+Сe+Cр+BQ+CQ.
В общем случае, условия mА=0, mВ=0 и mN=0 задают в каждой трехфазной области A+B+N по три виртуальные двухфазные NB, NA, AB поверхности. Реальное появление каждой из них зависит от конкретных температурно-концентрационных границ области, а именно - от формы и кривизны направляющих линий у трех линейчатых поверхностей. Поэтому в трехфазной области могут проявиться одна (в областях L+A+B1, L+B+C, L+B1+C на рис. 3,а), две (области L1+L2+R на рис. 1,а и L+A+C на рис. 2,а) или все три (область А+В1+С на рис. 3,а) двухфазные поверхности.
б) Поверхности T-x-y диаграмм, кроме нелинейчатых границ областей гомогенности (ликвидус, солидус и т.д.) и их производных линейчатой природы, дополнены новым классом поверхностей, отвечающих изменению типа фазового превращения при пассивной роли одной из фаз.
Очевидно, что двухфазные поверхности должны рассматриваться в качестве таких же важных геометрических элементов фазовой диаграммы, как и границы ее фазовых областей (поверхности ликвидуса, солидуса, сольвуса, трансуса), и должны отображаться на изотермах (RS на рис. 3,б) и изоплетах (QS на рис. 3,а).
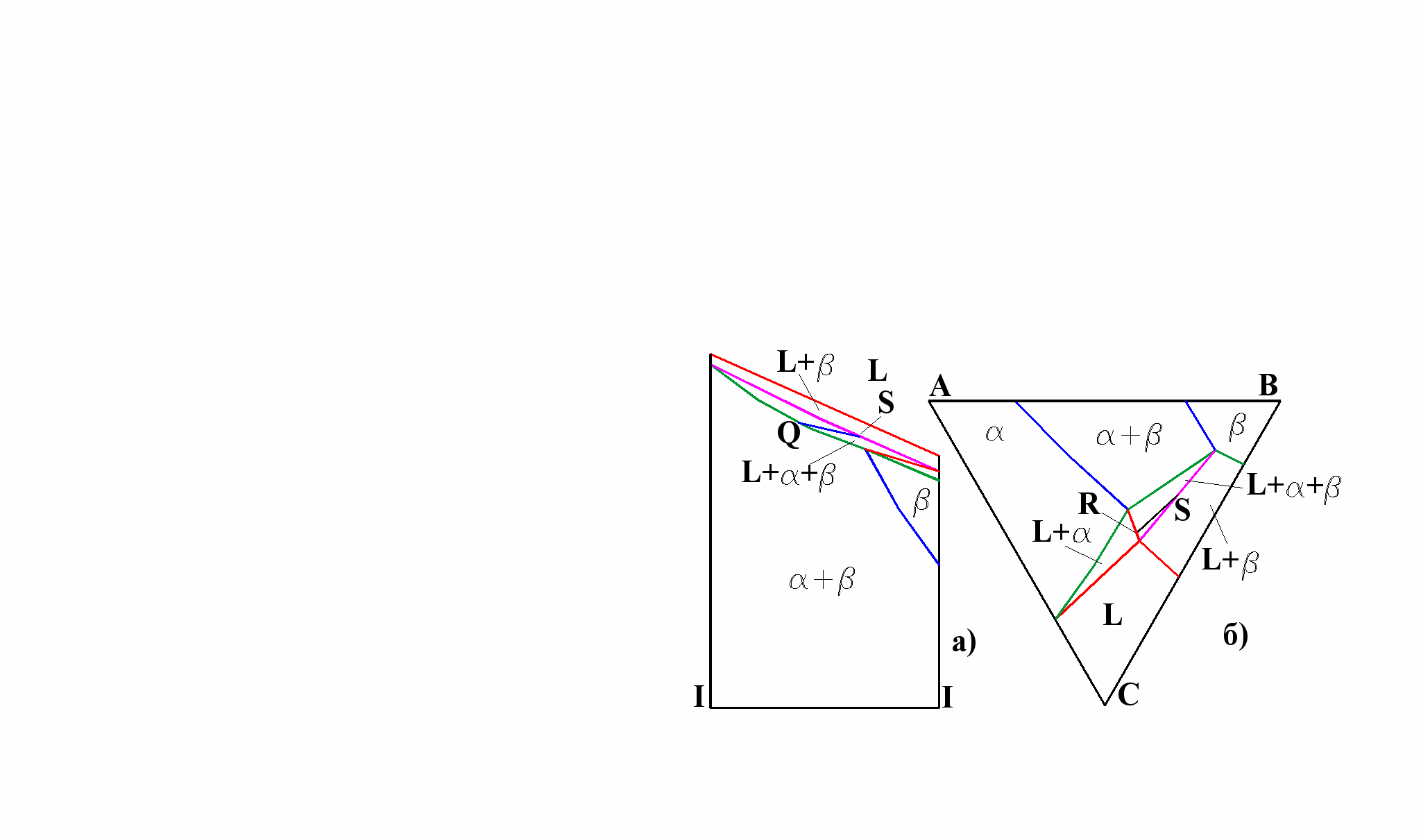
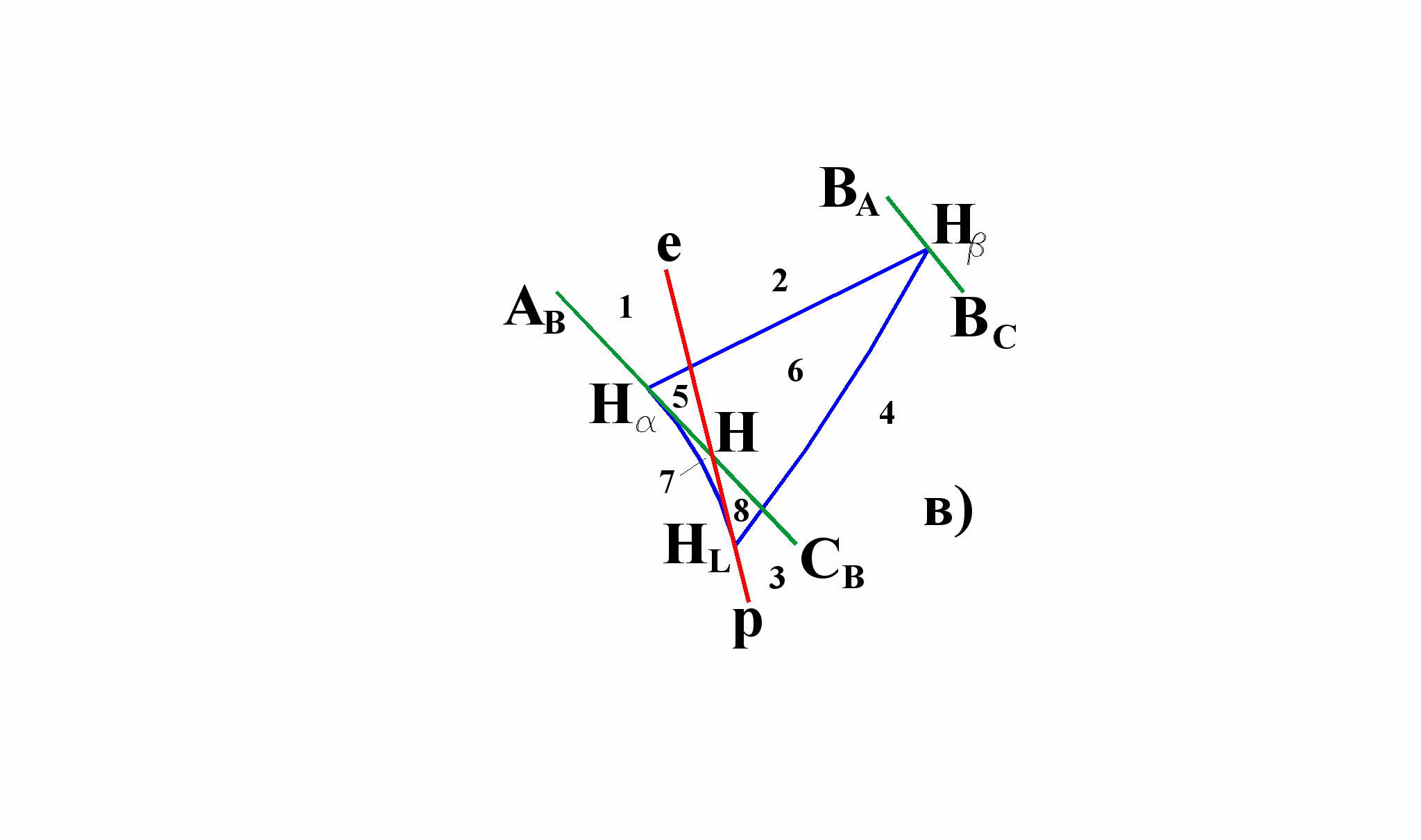
Рис. 3. Сечения двухфазной поверхности смены типа трехфазной реакции с L+ на L+: QS - на политермическом (а), RS - на изотермическом разрезах (б); концентрационные поля 1-8 как проекции фрагментов трехфазной области L++ (в)
Концентрационные проекции двухфазных поверхностей являются важным дополнением для оценки картины кристаллизации и формирования микроструктуры. Так, например, после проецирования границ фазовой области L++ и поверхности смены типа трехфазного превращения получаются 8 полей с различными микроструктурами, в состав которых входят первичные a1, эвтектические aе и перитектические aр кристаллы фазы a. Количество вариантов микроструктур будет увеличиваться, если учитывать, что на перитектическом этапе L+ трехфазной реакции первичные кристаллы b1 могут конкурировать с более мелкими кристаллами эвтектического происхождения bе.
Двухфазные поверхности нулевого приращения одной из масс являются линейчатыми, с горизонтальной образующей. Они имеют общую направляющую. Каждая двухфазная поверхность пересекает одну из линейчатых границ фазовой области по ее криминанте (HHL на рис. 3,в). Крайние положения точек на криминантах соответствуют температурному интервалу, в котором происходит смена типа трехфазной реакции, причем для каждого конкретного состава эта смена происходит при строго определенной температуре.
в) Для отображения микроструктурного состава гетерогенных смесей разработаны алгоритмы конструирования диаграмм материального баланса, которые отображают для заданного центра масс в температурном поле историю изменения состава каждой фазы с учетом ее происхождения (первичная кристаллизация, эвтектическая или перитектическая реакция и т.п.).
Для отображения не только фазового состава микроструктуры, но и учета содержания кристаллов различного происхождения, разработана технология построения диаграмм материального баланса (ДМБ), которые отображают состояние заданного центра масс G в температурном поле. Эта технология может применяться при моделировании образования многокомпонентных эвтектических сплавов или процессов формирования тонкодифференцированной структуры, близкой к той, которая реализована в быстроохлажденных сплавах. ДМБ позволяют сравнивать результаты дизайна микроструктур, отличающихся степенью участия кристаллов различной дисперсности в нонвариантных перегруппировках масс и в случае смены знака приращения массы одной из фаз трехфазной области. Поэтому изменение типа трехфазного превращения, то есть наступление условий для выполнения двухфазной реакции при индифферентной третьей фазе и вытекающая из этого смена знака приращения этой фазы, хорошо видно на диаграммах материального баланса (рис. 2,б и в; 3,б; 4;б).
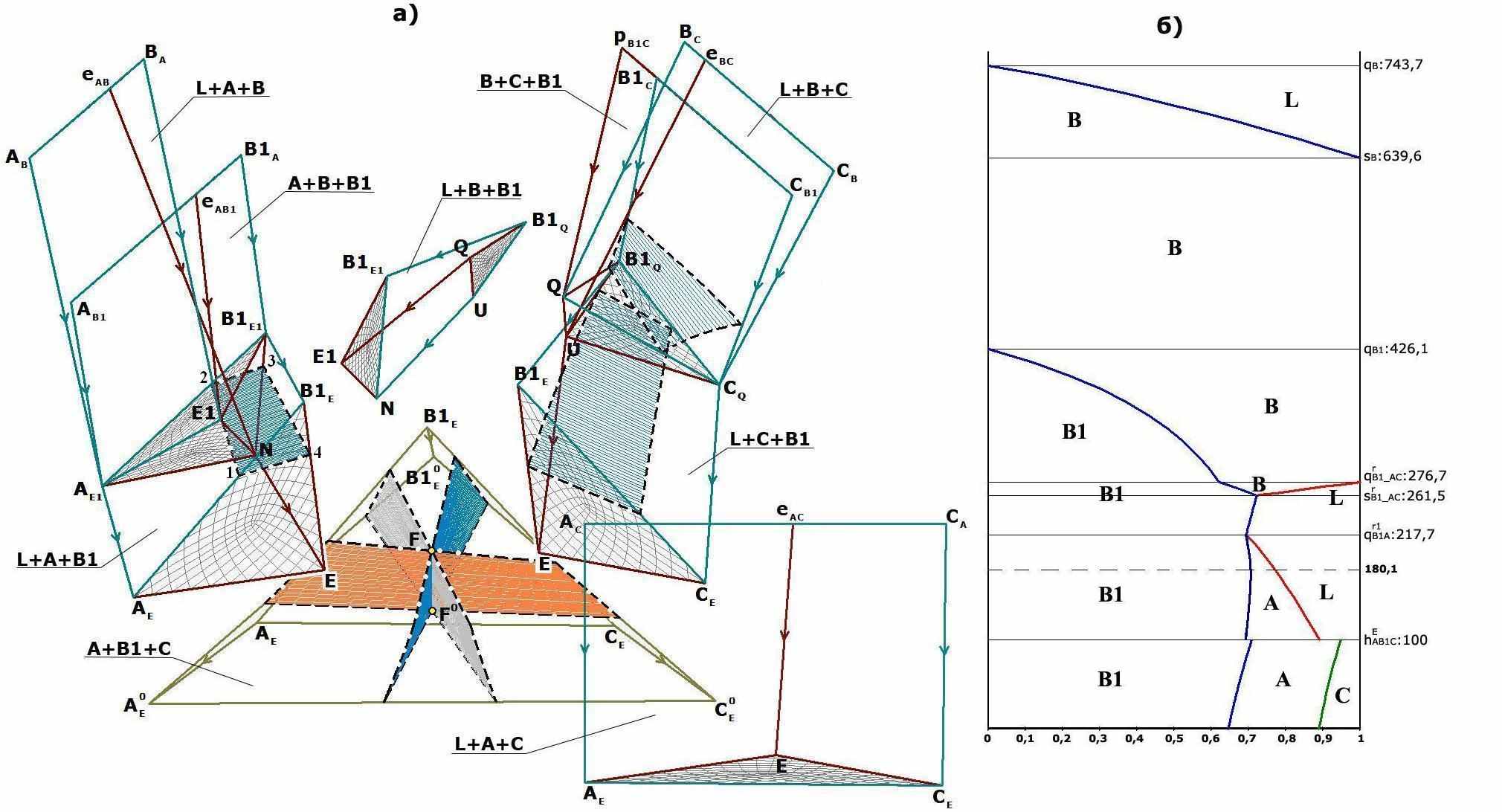
Рис. 4. Пространственная схема трехфазных реакций в T-x-y диаграмме с внутренним полем первичной кристаллизации низкотемпературной полиморфной модификации В1 компонента В (а) и диаграмма материального баланса для расплава G(0.27, 0.40, 0.33), кристаллизация которого проходит через область L+A+B1 (а) с поверхностью 1-2-3-4 двухфазной реакции LА при mB1=0 (б)