Московский государственный открытый университет Научно-образовательный материал
Вид материала | Реферат |
- Московский государственный открытый университет Научно-образовательный материал, 891.3kb.
- Министерство образования и науки РФ московский государственный открытый университет, 1119.23kb.
- Министерство образования и науки РФ московский государственный открытый университет, 705.26kb.
- Ассоциация Московских Вузов» федеральное государственное бюджетное образовательное, 96.41kb.
- Дорожный Государственный Технический Университет (мади) Научно-образовательный материал, 127.07kb.
- Многофункциональный нанотехнологический комплекс «Нанофаб» нтк -5 Научно-образовательный, 123.37kb.
- «Московский государственный медико-стоматологический университет Росздрава», 320.44kb.
- Гоу впо «Московский государственный открытый университет», 633.31kb.
- Гоу впо «Московский государственный открытый университет», 281.64kb.
- Гоу впо «Московский государственный открытый университет», 358.86kb.
1.2.2. Технологии для снижения выбросов оксидов серы на угольных тепловых электростанциях
Основным твердым топливом в России являются энергетические угли Кузнецкого, Канско-Ачинского, Экибастузского, Интинского (Воркутинского) и Донецкого бассейнов, Азейского, Мугунского, Головинского, Артемовского, Партизанского и других месторождений, а также ряд местных углей.
Приведение отечественных нормативов в соответствие с европейскими будет сопровождаться введением для действующих ТЭС технических нормативов на выбросы загрязняющих веществ, в том числе диоксида серы. Технологии сероочистки для отечественных тепловых электростанций, обеспечивающие регламентированные концентрации SO2 в очищенных газах, в зависимости от мощности котельных агрегатов и сернистости сжигаемого топлива, можно разделить на три категории:
- для котлов малой и средней мощности, сжигающих мало- и среднесернистое топливо, - со степенью сероочистки 30-35%;
- для котлов малой и средней мощности, сжигающих среднесернистое топливо, - со степенью сероочистки 50-60%;
- для котлов всех мощностей, сжигающих высокосернистое топливо, - со степенью сероочистки не менее 85%.
Для котлов малой и средней мощности, сжигающих мало- и среднесернистое топливо, разработаны технологии с использованием имеющихся на ТЭС объемов котельного агрегата и золоуловителей – скрубберов Вентури. (или других подобных аппаратов с использованием воды) и электрофильтров.
Сухая известняковая технология основана на обжиге в опочной камере котла при 1000-1100 0С тонко размолотого известняка, который превращается в этих условиях в активную известь. Интенсивность улавливания диоксида серы известью в диапазоне температур 500-8500С зависит от тонины помола реагента, поскольку процесс сорбции определяется преимущественно поверхностью контакта реагента с газом, которая, в свою очередь, зависит от размера частиц. Естественно, что обжиг известняка сопровождается использованием части тепла дымовых газов, что снижает КПД котла. Например, при сжигании бурых углей, продукты сгорания которых содержат 4г/м3 SO2, ввод в дымовые газы известняка в относительном количестве CaCO3/SO2 =2 снижает КПД котла на 1,1%. Оправданная (без заметного влияния на экономичность котельного агрегата) степень сероочистки дымовых газов с помощью такой технологии составляет 30-35%.
Модификацией рассмотренного метода является подача тонкодисперсной извести (известковая технология) в конвективную шахту котла или соды в газоходы уходящих газов.
Если котел оснащен мокрыми золоуловителями, то общая степень сероочистки может быть повышена до 60-65% за счет того, что непрореагировавшая известь в мокром золоуловителе, орошаемом водой, дополнительно сорбирует SO2. В результате пульпа характеризуется повышенным содержанием кальция. Для предотвращения образования отложений в мокром золоуловителе и системе внутреннего и внешнего гидорозолоудаления выбран безопасный солевой режим работы золоотвала и системы оборотного водоснабжения, исключающий отложения карбонатов и сульфатов.
Применение сухой известняковой технологии может приводить к изменению температуры плавления золы. Например, при сжигании углей, зола которых имеет температуру размягчения 13000С, применение этой технологии возможно. Но при использовании углей, которые размягчаются при 1100-11750С, ее применение может вызвать повышенное шлакование поверхностей нагрева котла.
Использование мокрых золоуловителей для сероочистки приемлемо при сжигании твердого топлива, в летучей золе которого имеются повышенные концентрации оксида кальция.
Такой режим работы мокрого золоуловителя обеспечивает 35%-ное улавливание диоксида серы и 98%ное- улавливание летучей золы.
Технология с выщелачиванием золы позволяет достигнуть указанной степени сероочистки при капитальных вложениях на уровне 8-15 дол/кВт при увеличении расхода энергии на собственные нужды, не превышающем 0,05%.
Обеспечить очистку дымовых газов с помощью скрубберов на 50-60% можно за счет использования в качестве реагента соды Na2CO3 (двойная щелочная технология). В этом варианте при нейтрализации диоксида серы содой образуются сульфиты и бисульфиты натрия. Обработка этих солей второй щелочью (отсюда название технологии)- известью – дает гипс, который в смеси с золой можно сбрасывать на золоотвал. Образовшаяся после регенерации щелочь возвращается на орошение золоуловителя. Применение регенератора и двух реагентов – соды и извести – увеличивает капитальные затраты на такую сероочистку до 15-20 дол/кВт. Также увеличивается до 0,07% и расход электроэнергии на собственные нужды.
Для котельной установки большой мощности, оснащаемой электрофильтрами, в аналогичных условиях целесообразны мокросухие технологии сероочистки. В них реагент вводят в дымовые газы в виде суспензии, вода которой за счет тепла этих газов полностью испаряется до начала процесса электрогазоочистки. Испарение воды сопровождается охлаждением и увлажнением уходящих из кола дымовых газов, в результате чего их физический объем уменьшается на 15-18% и соответственно увеличивается время пребывания в активной части электрофильтра.
Отходом мокросухой сероочистки является сухая смесь золы с кальциевыми соединениями – сульфитами, сульфатами и непрореагировавшей известью. Эта смесь может быть использована в дорожном строительстве, при производстве строительных изделий или для засыпки земельных неудобий при рекультивации ландшафтов.
При приведенной сернистости менее 0,3 кг/МДж предпочтительна упрощенная мокросухая технология, основанная на впрыске тонкодисперсной известковой суспензии перед форкамерой электрофильтра. Такая технология позволяет очистить продукт сгорания углей типа кузнецких на 50-60% и не требует громоздкого дорогостоящего оборудованих.
Мокросухая технология с циркулирующей инертной массой (роснована на вводе в дымовые газы перед электрофильтром увлажненной смеси из уловленной в электрофильтре золы с известью. В этом процессе зола является инертным материалом, на поверхность которого наносится тонкий слой реагента. При влажности не более8% такая смесь имеет хорошие сыпучие свойства, что позволяет надежно транспортировать твердый реагент к газоходу и равномерно распределять его в объеме уходящих дымовых газов перед их электрогазоочиткой. Технология реализуется следующим образом. Уловленная в первом и втором электрополях зола направляется в смеситель, куда вводится также необходимое количество реагента и воды. Эта смесь подается в газоход перед электрофильтром. Большая поверхность золы, на которую нанесен реагент, позволяет максимально интенсифицировать процессы массообмена, а существующая абразивность пылегазового потока исключает возможное образование на стенках газохода отложений.
Мокросухие технологии приводят к увеличению концентрации соединений кальция в складируемых на золоотвале отходах. Если уловленная зола транспортируется на золоотвал гидравлически, то повышение в ней содержания кальция требует уточнения режима работы золоотвала во избежание образования отложений в пульпопроводах и трубопроводах осветленной воды. Наиболее приемлемым способом транспортирования золы в таких технологиях является сухие системы.
Мокрые технологии сероочистки для организации сорбции диоксида серы из дымовых газов реализуются с применением специальных аппаратов устанавливаемых после эффективного золоуловителя. Степень улавливания SO2 в таких технологиях максимальна (99% и более). Кроме того, некоторые мокрые технологии позволяют улавливать в одном аппарате два или три компонента дымовых газов, что существенно удешевляет процесс всей газоочистки по сравнению с индивидуальными процессами.
В мокрых технологиях сероочистки дымовые газы интенсивно промывают водными суспензиями или растворами реагентов с высокой степенью диссоциации на ионы. При промывке газов улавливаемый диоксид серы растворяется в воде и также переходит в ионную форму SO32-, что ускоряет его связывание реагентом. Количество орошающей воды, содержащей реагент, обычно велико, и теплом дымовых газов можно испарить только не большое ее количество – не более 0,5%. При этом дымовые газы сильно охлаждаются, так что их приходится дополнительно нагревать, чтобы избежать коррозии последующего газового тракта, дымососов и дымовой трубы.
Использование морской воды является близким аналогом мокрой известняковой технологии, поскольку в морской воде содержится большое количество ионов щелочно-земельных металлов, которые могут связывать диоксид серы с образованием устойчивых сульфатов. При средней концентрации солей в морской воде 35г/кг на долю ионов натрия приходится около 10,80%; калия - 0,38%; кальция – 0,40%; магния – 1,29%; гидрокарбоната – 0,14%. В данной технологии дополнительные реагенты не требуется.
Побочный продукт сероочистки – смесь сульфатов указанных элементов, которые являются естественными компонентами морской воды, поэтому отработанную суспензию можно непосредственно сбрасывать в море, не вызывая никакого загрязнения акватории.
Аммиачно-сульфатная технология интересна следующим:
- высокая активность реагента обеспечивает полное его использование в соответствии со стехиометрическим соотношением при минимальном расходе орошающего раствора аммонийных солей и минимальных размерах абсорбера;
- побочным продуктом сероочистки является сульфат аммония - ценный товарный продукт который может быть использован в качестве удобрения или сырья для производства кормовых дрожжей;
- одновременно с диоксидом серы улавливается до 30% оксидов азота.
Озонно - аммиачная технология основана на окислении с помощью озона диоксида серы и оксидов азота до высших оксидов, растворении их в воде с образованием смеси серной аммиачной водой [5]. Получаемая смесь сульфата и нитрата аммония является еще более эффективным удобрением, чем (NH4)2SO4
Одновременно с газообразными компонентами из продуктов сгорания угля улавливается часть летучей золы, которая при этом длительное время контактирует с жидким реагентом. В результате часть микроэлементов золы выщелачивается в орошающий раствор (анологичный процесс происходит и в аммиачно-сульфатной технологии), улучшая товарные свойства смешанного удобрения. Испытания, проведенные специалистами сельского хозяйства, показали его явное преимущество перед обычными промышленными смесями, не обогащенными микроэлементами.
В сульфатно-магниевой технологии применяется природный реагент – магнезит MgCO3, а также такие соединения магния, как оксид MgO и гидроксид Mg(OH)2. При ее использовании образуется сульфат магния, который является удобрением и сырьем для целлюлозно-бумажной и текстильной промышленности. Из-за низкой растворимости соединений магния в воде эта сероочистка по своим технологическим особенностям близка к мокрой известняковой. Сульфатно-магниевую технологию целесообразно применять в первую очередь на ТЭС, расположенных недалеко от источника природного реагента. В России месторождение магнезита расположено на Урале в Челябинской области. Для Верхнетагильской ГРЭС, например при степени сероочистки 90%, удельные капитальные вложения в такую установку равны 1500 руб/кВт (общие - мость реагента и рабочих сред, зарплата) – 22,5 млн. руб./год.
Некоторые отечественные ТЭС постоянно или сезонно сжигает мазут, продукты сгорания которого в зависимости от его исходной сернистости и от тепловой мощности котла необходимо очищать от диоксида серы на 30-80%. При постоянном сжигании мазута применимы мокрые технологии сероочистки: известняковая, аммиачная, магнезитовая. Важным условием их применения является глубокое обеспыливание газов, поскольку мазутная зола содержит частицы сажи и пентоксида ванвдия, оказывающие отрицательное влияние на процесс сероочистки. При сезонном сжигании мазута продолжительностью до 20-30% рабочей компании котла целесообразны недорогие технологии, способные к простым пуску и остановку при переходе котла с природного газа на мазут и обратно.
В таблице 1.3 приведены обобщающие сведения по применению разных технологий сероочистки, в зависимости от сжигаемого топлива.
Таблица 1.3. Применение технологий сероочистки
Регион РФ | Сжигаемое топливо | Приоритеты | Удельные капитальные затраты, дол/кВт |
Северная часть европейской территории | Высосернисттые угли и мазуты | Мокрая известняковая или известковая технология Технология с использованием морской воды(для ТЭС, расположенных на берегах Белого и Баренцева морей) | 80-120 (60-85) 60-90 (5-65) |
Центральная и южная части европейской территории | Высокосернистые угли и мазуты | Аммиачно-сульфатная технология | 35-55 (30-45) |
Малосернистые восточные угли | Озоннно- аммиачная технология Мокрая известняковая или известковая технология Мокросухая известковая технология в форкамере электрофильтра Мокросухая известковая технология с циркулирующей инертной массой Использование скрубберов Вентури | 50-80 (40-70) 80-120 (60-85) 6-8 15-17 8-20 | |
Урал | Высокосернистые угли и мазуты | Сульфатно-магниевая технология | 80-100 (60-75) |
Среднесернистые угли | Мокрая известняковая или известковая технология Мокросухая известковая технология с циркулирующей инертной массой Использование скрубберов Вентури | 80-120 (60-85) 15-17 8-20 | |
Сибирь | Малосернистые угли | Мокросухая известковая технология в форкамере электрофильтра Использование скрубберов Вентури Сухая известняковая технология | 6-8 8-20 3-5 |
Дальний восток | Сернистые и среднесернистые угли | Мокросухая известковая технология с циркулирующей инертной массой Морская вода Мокрая известняковая или известковая технология | 15-17 60-90 (50-65) 80-120 (60-85) |
| Использование скрубберов Вентури Сухая известняковая технология | 8-20 3-5 |
Выбор технологий сероочистки для конкретных условий ТЭС и котлов производится на основе технико-экономического сопоставления возможных вариантов, а в качестве основного критерия их сравнения принимается стоимость улавливания 1 т диоксида серы. Технологии сероочистки, целесообразные для применения в основных регионах Российской Федерации в порядке их приоритета, указаны в таблице 1.3 Набор их может показаться чрезмерно широким. Но только наличие такого набора с учетом разнообразия продуктов сгорания отечественных энергетических видов топлива позволяет снижать выбросы диоксида серы при минимальных капитальных вложениях и эксплуатационных затратах.
Сероочистка дымовых газов не вносит перемен в традиционную технологию производства энергии и может приводить к получению ценных товарных продуктов (гипса, сульфатов аммония), продажа которых позволяет улучшить экономические показатели электростанции.
Технологии одновременного снижения выбросов NOx и SO2 на
пылеугольных котлах ТЭС
Ожидаемое в ближайшие годы замещение природного газа твердым топливом на большинстве электростанций европейской части России приведет к существенному увеличению выбросов в атмосферу оксидов азота и серы (NOx и SO2), а также золовых частиц.
Очистка дымовых газов от твердых частиц исследована отечественными специалистами достаточно хорошо и возможность повышения эффективности золоуловителей до 99,0…99,5% сдерживается только отсутствием финансирования. Что же касается выбросов газообразных загрязнителей, которые являются причиной «кислотных дождей», то в этой области еще идет интенсивный поиск наиболее эффективных технологий, рассчитанных на максимальное снижение выбросов NOx и SO2 при минимальных капитальных затратах и умеренных эксплуатационных расходах.
Ниже рассматриваются два метода которые в условия России можно было бы реализовать на отечественных ТЭС без покупки лицензии и привлечения комплектующих из-за рубежа.
Первый метод предполагает сжигание примерно 85% твердого топлива в зоне основного сгорания. Остальное топливо в виде природного газа подается в топочный объем после основной зоны горения с недостатком воздуха. В результате этого создается восстановительная зона, в которой происходит частичный переход оксидов азота в молекулярный азот N2.
Выше по ходу факела в топку инжектируется кальцийсодержащий сорбент для связывания диоксида серы. Именно этим рассматриваемый метод отличается от традиционного трехступенчатого сжигания, уже реализованного нашими специалистами на ряде пылеугольных котлов.
Демонстрационный проект предполагал внедрение метода на двух объектах: котлах энергоблоков 80 МВт и 40 МВт. Первый котел был оборудован топкой с твердым шлакоудалением и тангенциальным расположением прямоточных горелок. Второй имел топку с циклонными предтопками. Основным топливом на обеих ТЭС был каменный уголь с содержанием серы около 3 %.
Цель работы состояла в снижении выбросов NOx на 60% и связывании 50% выбросов SO2 путем использования сорбента.
На котле с тангенциальной топкой максимальное снижение выбросов NOx составило 75%,а среднеэксплуатационное уменьшение выбросов оксидов азота при доле газа по теплу 18%-67%. На этом котле подача в топку гашеной извести при мольном отношении Ca/S, равном 1,75, позволила снизить выбросы SO2 на 53%.
На котле с циклонными предтопками после внедрения метода GR-SI максимальное снижение выбросов NOx достигло 74%, а среднеэксплуатационное значение (при подаче газа в количестве 22% по теплу в камеру дожигания) – 66%. Степень связывания SO2 при использовании гашеной извести (Ca/S = 1,8) составила 58% (это соответствует, как и в первом случае, использованию 24% сорбента).
Второй метод, который может быть реализован на отечественном оборудовании, известен под названием LIMB (limestone injection – multistage burner) – многоступенчатая горелка в сочетании с инжекцией известняка.
Удельные выбросы NOx, за котлом на завершающем этапе испытаний составляли 0,185 г/МДж, что соответствует концентрации NOx, равной примерно 350 мг/м3 (при O2 = 6%). Снижение выбросов оксидов азота в случае применения малотоксичных горелок типа DRB – XCL составило 40…50%. Эти значения хорошо согласуются с полученными ранее результатами внедрения таких же горелок на других пылеугольных котлах.
С ростом промышленного производства, его индустриализацией, технические мероприятия по защите окружающей среды, становятся недостаточными для снижения уже образовавшихся загрязнений. Поэтому необходим поиск укрупненных характеристик, которые, отражая реальное состояние сред, помогли бы выбору экологически и экономически оптимального варианта.
1.2.3. Технологии для улавливания углекислого газа на угольных тепловых электростанциях
Одним из основных загрязнителей является диоксид углерода количество выбросов диоксида углерода в мире составляет более 22 млрд. т/год. Дальнейшее развитие этого процесса будет усиливать нежелательную тенденцию в сторону повышения среднегодовой температуры на планете. Перед исследователями стоит задача снижения выбросов диоксида углерода как за счет его утилизации, так и за счет исключения его образования при термической переработки углерод содержащего сырья. Полностью исключить содержание диоксида углерода продуктов сгорания практически невозможно, поэтому необходимо разрабатывать эффективные технологии его утилизации.
Значение максимального содержания диоксида углерода можно определить следующим образом:
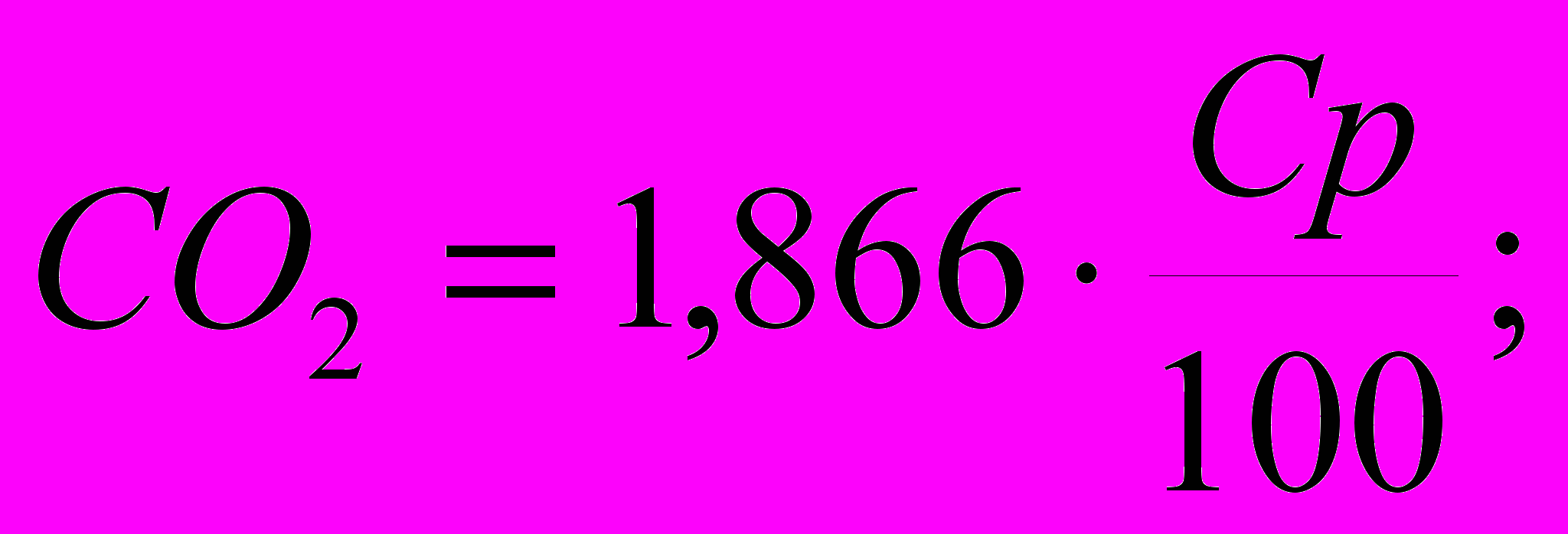
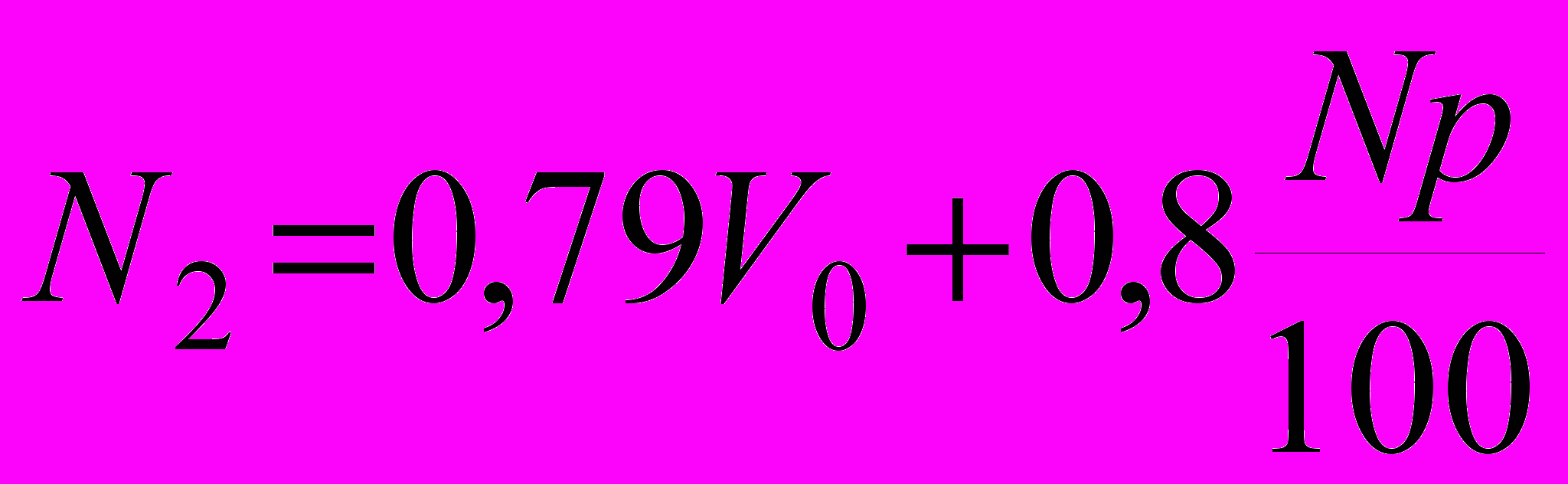
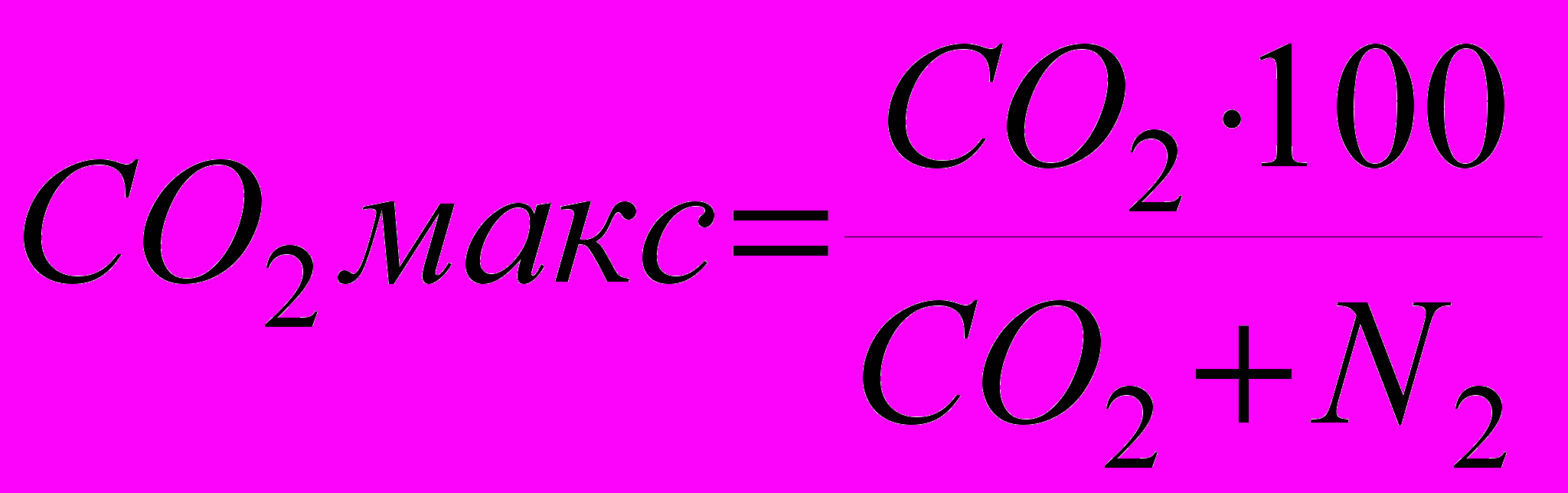
Эмиссия CO2 зависит от вида сжигаемого топлива и технологии его сжигания на тепловых электростанциях: 1) при сжигании природного газа почти вдвое уменьшается эмиссия CO2 за счет изменения химического состава топлива; 2) в газотурбинных установках наблюдается большее снижение эмиссии CO2 по сравнению со сжиганием угля на обычных тепловых электростанциях.
Для снижения эмиссии CO2 необходимо: а) сжигание топлива с пониженным содержанием углерода; б) улавливание CO2 из дымовых газов и его последующее захоронение или утилизация.
Удаление CO2 из дымовых газов т6епловых электростанций проводится с помощью различных систем очистки дымовых газов: мембранные технологии, адсорбция и абсорбция, криогенная техника. Например, дымовые газы из котла направляются в абсорбер, где промываются специальным раствором, после чего поступают на обогрев и сбрасываются в дымовую трубу. Перед поступлением в абсорбер газы должны быть охлаждены. Эффективность улавливания составляет до 95%.