Обработка металлов резанием
Вид материала | Документы |
Накатка резьбы Э. П. Луговой. Сверлильная головка Ручные машины М. Л. Гельфанд. А. А. Шишкин. |
- Шифр специальности: 05. 16. 01 Металловедение и термическая обработка металлов и сплавов, 25.46kb.
- Обработка металлов давлением при обработке металлов давлением, 131.9kb.
- Программа профессиональной переподготовки мтф п/п-1 «металловедение и термическая обработка, 34.45kb.
- Лекция 7 термическая обработка металлов, 136.74kb.
- Научные основы и технологические способы обработки гетерофазных сплавов с высоким уровнем, 572.64kb.
- Программа вступительного испытания по направлению «Металлургия», 51.65kb.
- 05. 16. 01 Металловедение и термическая обработка металлов, 25.25kb.
- Развитие научных основ и разработка совмещенных методов обработки металлов давлением,, 606kb.
- Реферат по теме: «Металлы. Свойства металлов.», 196.2kb.
- Закономерности превращения, 589.18kb.
Накатка резьбы, процесс получения резьбы в результате пластической деформации заготовки резьбонакатным инструментом. Инструмент для Н. р. — плашки, резьбовые сегменты, ролики с винтовой или кольцевой нарезкой, затылованные ролики. Н. р. производят на резьбонакатных автоматах и полуавтоматах, а иногда на токарных и револьверных станках.
Основные методы Н. р.: тангенциальный, радиальный и осевой (в зависимости от направления подачи инструмента и заготовки), при которых выбирают определённые технологические схемы и соответствующий инструмент (рис.).
Накатывают метрические и дюймовые резьбы, с треугольным, круглым, трапецеидальным и др. профилем, на наружных и внутренних поверхностях. Этим способом получают резьбу на деталях из сталей и цветных металлов (крепёжные детали, резьбонакатный и резьбонарезной инструмент, резьбовые калибры, микрометрические и ходовые винты), а также получают мелкие шлицы, зубья, рифления, кольцевые выступы и канавки на тонкостенных изделиях и т.п. Точность резьбы 4—6-й степени, шероховатость — до 10-го класса.
Лит.: Дейнеко В. Г., Новые способы непрерывного накатывания резьб и других профилей, М., 1961; Миропольский Ю. А., Насонов А. Н., Технология и оборудование для накатывания резьб и профилей, М., 1971.
Э. П. Луговой.


Схемы накатки резьбы: а — плоскими плашками; б — резьбовым сегментом и роликом; в — двумя затылованными роликами; г — тремя роликами; 1 — подвижная плашка; 2 — заготовка; 3 — неподвижная плашка; 4 — резьбовой сегмент; 5 — ролик; 6 — затылованный ролик; 7 — ролики с винтовой нарезкой.
Сверлильная головка, узел или приспособление металлорежущего станка (главным образом сверлильного) для закрепления режущих инструментов: свёрл, зенкеров, развёрток, метчиков. С. г. изготовляются несамодействующие и самодействующие (с индивидуальным приводом), с одним или несколькими шпинделями. С. г., устанавливаемые на многошпиндельных и агрегатных сверлильных станках, могут иметь шпиндели, располагаемые жестко (применяются в массовом производстве), и шпиндели, которые можно фиксировать в том или ином заданном положении (применяются в серийном производстве).
Ручные машины, механизированный инструмент, группа технологических машин со встроенными двигателями, при работе которых их вес полностью или частично воспринимается руками оператора, производящего подачу и управление машиной. Р. м. обычно весит от 1,5 до 10 кг. Для приведения в действие рабочего органа в Р. м. используют главным образом пневматический или электрический привод (реже гидравлический) от двигателя внутреннего сгорания или порохового заряда. По назначению различают свыше 100 видов Р. м., которые в соответствии с классификацией делятся на самостоятельные группы.
Сверлильные машины (рис. 1) предназначаются для образования отверстий. По исполнению делятся на прямые (общего назначения) и угловые (для работы в труднодоступных местах). Различают Р. м. одно-, двух-, многоскоростные, с плавной регулировкой частоты вращения рабочего органа, реверсивные и нереверсивные. В эту группу Р. м. входят также машины ударно-вращательного действия, у которых на шпиндель при его вращении передаются осевые удары, увеличивающие рабочее усилие и, следовательно, производительность, особенно при обработке бетона, кирпича и т.п. материалов. Сверлильные Р. м. при оснащении специализированным инструментом или насадками используются для зачистки, резки, шлифовки, распиловки, фрезерования и других работ.
Шлифовальные машины (рис. 2) применяют не только для шлифовки, но и для зачистки и полировки разных материалов. По исполнению шлифовальные Р. м. бывают прямые и угловые. Наиболее распространены прямые шлифовальные Р. м. с абразивными цилиндрическими кругами. Для зачистки, отрезки и полировки обычно используют угловые шлифовальные Р. м. с различными рабочими инструментами: чашечными абразивными кругами, металлическими щётками, абразивными дисками и подкладными эластичными кругами с абразивной шкуркой. Для обработки дерева часто применяют ленточно-шлифовальные Р. м. с бесконечной абразивной лентой. Для обработки больших металлических и деревянных плоскостей используются плоскошлифовальные Р. м. с рабочим органом-платформой, которая совершает круговое плоскопараллельное движение (рабочий инструмент — обычно абразивная шкурка). Для зачистки отливок, сварных швов, разделки кромок деталей под сварку используют Р. м., у которых вращение рабочему органу передаётся от привода через гибкий вал. Многие модели шлифовальных Р. м. оснащены пылеотсасывающими устройствами.
Резьбозавёртывающие машины предназначены для сборки резьбовых соединений. Распространение получили гайковёрты (рис. 3). В эту группу входят также шуруповёрты, шпильковёрты, муфтовёрты для завёртывания и отвёртывания винтов, шпилек, трубных муфт.
Молотки и другие Р. м. ударного действия (например, клепальные, зачистные, рубильные машины) применяют на сборочных и металлообрабатывающих операциях. Очистку металлических деталей от старой краски, ржавчины, окалины осуществляют пучковыми молотками, рабочий инструмент которых представляет собой пучок стальных закалённых стержней. В строительстве, горной и других отраслях промышленности для разрушения бетона, горных пород и т.п. используют отбойные молотки. Для образования размерных отверстий в горных породах, бетоне, кирпиче и т.п. материалах применяют перфораторы, рабочий инструмент которых не только совершает удар, но и вращается. Для обработки и зачистки каменных, бетонных и т.п. поверхностей служат бучарды с рабочим инструментом в виде стального башмака с закалёнными шипами. К этой же группе относятся гвоздезабивные, скобозабивные и другие Р. м. (рис. 4).
Фрезерные машины используют для образования пазов, гнёзд, различных углублений в металлических, деревянных, пластмассовых и других изделиях. Рабочий инструмент таких Р. м. — обычно пальцевая концевая фреза. К этой группе машин относятся рубанки (рис. 5), долбёжники, шаберы, напильники и т.д.
Ножницы (рис. 6) предназначаются для прямолинейной и фигурной резки листового материала из стали, сплавов цветных металлов, пластмасс, резины и т.п. Применяются на сборочных, ремонтно-монтажных, санитарно-технических и кровельных работах. Различают четыре типа ножниц: ножевые, вырубные, дисковые и рычажные (см. Ножницы).
Пилы (рис. 7) используются для резания древесины, пластмасс, мягких строительных материалов и реже — мелкого металлического проката, арматуры и труб. Пилы бывают дисковые, цепные, пилы-лобзики, пилы-ножовки (см. Пила, Лобзик, Ножовка).
Лит.: Бармаш В. Н., Левин Д. И., Фрейдберг В. З., Ручные машины для монтажных и отделочных работ, М., 1960; Судакович Д. И., Вернадский Г. И., Справочник по механизированному ручному инструменту, 2 изд., М. — Л., 1961; Пневматические ручные машины. Справочник. Л., 1968.
М. Л. Гельфанд.

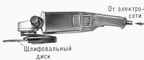
Рис. 2б. Шлифовальная ручная машина электрическая.

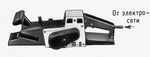
Рис. 5. Электрический ручной рубанок.

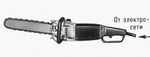
Рис. 7. Цепная электрическая ручная пила.

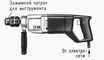
Рис. 1. Прямая сверлильная электрическая ручная машина.

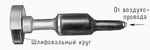
Рис. 2а. Шлифовальная ручная машина пневматическая.

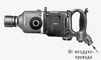
Рис. 3. Пневматический гайковёрт.

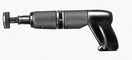
Рис. 4. Монтажный пороховой пистолет.


Рис. 6. Электрические ручные ножницы.
Сверление, 1) в металлообработке — процесс получения сквозных и глухих отверстий в сплошном материале на сверлильных, токарных, револьверных, расточных, агрегатных и других станках, а также при помощи сверлильных ручных машин. Точность изготовления отверстий при С. — 4—5-й класс. Отверстия более высокой точности получают после С. растачиванием, зенкерованием или развёртыванием.
Главное движение при С. — вращательное, движение подачи — поступательное. При работе на сверлильных станках оба движения осуществляет сверло, при работе на других станках вращение совершает обрабатываемая заготовка, поступательное осевое движение — сверло.
Режим резания при С. определяется скоростью резания v и подачей s. Скорость резания (теоретическая) — окружная скорость наиболее удалённой от оси сверла точки режущей кромки: = Dn/1000 м/мин, где D — диаметр сверла (по ленточкам) в мм; n — частота вращения сверла в об/мин. Допускаемая скорость резания при С.:
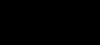

Производительность С. характеризуется основным технологическим временем: To= L/ns мин, где L — длина прохода сверла в мм в направлении подачи.
Д. Л. Юдин.
2) В деревообработке — процесс получения сквозных отверстий в сплошной древесине или древесных материалах сверлом, а также обработка пазов, гнёзд под шипы и т. п. Точность обработки — 2—3-й класс (по диаметру), 3—4-й класс (по глубине). Частота вращения сверла по дереву достигает 3000—12000 об/мин, подача 0,1—0,5 мм/об (для твёрдых материалов) и 0,7—2,2 мм/об (для мягких материалов).
В. С. Рыбалко.
Лит.: Бершадский А. Л., Расчет режимов резания древесины, М., 1967. См. также лит. при ст. Обработка металлов резанием.
Строгание, процесс обработки материалов резанием со снятием стружки, осуществляемый при относительном возвратно-поступательном движении инструмента (строгального резца, ножа и т.п.) или изделия. При С. стружка, как правило, снимается при рабочем ходе.
В металлообработке скоростью резания при С. называется скорость Vp (в м/мин) прямолинейного движения резца (на поперечно-строгальном станке, рис. 1) или обрабатываемого изделия (на продольно-строгальном станке) при рабочем ходе. Подача х (в мм/дв. ход) — поперечное перемещение изделия за один двойной ход резца (на поперечно-строгальном станке) или резца за один двойной ход обрабатываемого изделия (на продольно-строгальном станке). Глубина резания t (в мм) — расстояние между обрабатываемой и обработанной поверхностями. Основное технологическое время при С.:

где В — относительное перемещение резца или обрабатываемого изделия в направлении подачи в мм; n — число двойных ходов резца или изделия в мин; i — число проходов резца.
Для более полного использования мощности станка применяется многорезцовое С. (рис. 2). Высокопроизводительное чистовое С. осуществляется широкими строгальными резцами со вспомогательной режущей кромкой под углом 1 = 0°, длиной (1,2—1,8) s, оснащенными пластинками из твёрдых сплавов: С. ведётся при больших подачах — до 20 мм/дв. ход и более. Рациональный режим резания при С. определяют по той же методике, что и при точении, с учётом соответствующих поправочных коэффициентов (см. Обработка металлов резанием, Резец).
Основные недостатки С.: удар инструмента (резца) в начале каждого рабочего хода и наличие холостого хода, что снижает стойкость инструмента и производительность обработки.
В деревообработке под С. понимают операции снятия стружки ручными деревообрабатывающими инструментами (рубанками и т.п.), а также обработку древесины при получении строганого шпона.
Лит.: Обработка металлов резанием, 2 изд., М., 1962; Резание конструкционных материалов, режущие инструменты и станки, под ред, П. Г. Петрухи, М., 1974; Аршинов В. А., Алексеев Г. А., Резание металлов и режущий инструмент, 2 изд., М., 1967.
Д. Л. Юдин.


Рис. 2. Схема многорезцового строгания: 1, 2, 3 и 4 — резцы; s — подача.


Рис. 1. Схема процесса строгания на поперечно-строгальном станке: 1 — обрабатываемая поверхность; 2 — плоскость резания; 3 — основная плоскость; 4 — опорная поверхность резца; 5 — обработанная поверхность; 6 — поверхность резания; а и b — толщина и ширина срезаемого слоя.
Шлифование, шлифовка (от польск. szlifować, нем. schleifen — точить, полировать, шлифовать),
1) обработка поверхностей заготовок абразивным инструментом. Производится на шлифовальных станках, на металлорежущих станках других групп с помощью специальных приспособлений (например, шлифовальных головок), вручную. По скорости вращения абразивного инструмента различают обычное Ш. — окружная скорость инструмента около 20 м/сек и скоростное — окружная скорость выше 50 м/сек. Ш. позволяет изготовлять металлические детали с точностью до 1-го класса и получать поверхности до 10-го класса шероховатости. Ш. широко применяется при обработке наружных и внутренних плоских, цилиндрических, конических и фасонных поверхностей заготовок из металлов, пластмасс, керамики, ферритов, камня, дерева и т.д. Некоторое распространение получило также черновое (обдирочное) Ш. для удаления больших припусков с литых чугунных и стальных заготовок.
Известны различные виды Ш.: круглое наружное и внутреннее, планетарное, бесцентровое наружное и внутреннее, плоское, фасонное и др. (подробнее см. в ст. Шлифовальный станок).
Для обработки труднообрабатываемых металлов применяют также электрохимическое (электролитическое) Ш. токопроводящими шлифовальными кругами с подводом к зоне резания постоянного электрического тока и электролита (см. в ст. Электрофизические и электрохимические методы обработки). Ш. может производиться абразивным порошком, взвешенным в жидкости, с помощью методов вибрационной обработки.
Ш. заготовок из древесины производят как абразивными материалами (шлифовальной шкуркой), так и специальными инструментами (щётками, проволочными кругами и др.) непосредственно после строгания, фрезерования или циклования, а также шпаклевания или грунтовки. При Ш. нелакированных поверхностей движение шлифующих материалов осуществляется вдоль волокон, т.к. при поперечном движении волокна перерезаются и при последующем нанесении лака или красителей они поднимаются, образуя ворс.
Для Ш. камней применяют обычно карборундовый абразивный инструмент; обработку осуществляют на шлифовальных станках или ручным инструментом.
2) В крупяном производстве — удаление зародыша и наружных частей ядра, придание дроблёным зёрнам определённой формы и однородности.
Лит.: Маслов Е. Н., Теория шлифования материалов, М., 1974; Вульф А. М., Резание металлов, 2 изд., Л., 1973; Буглай Б. М., Технология отделки древесины, 2 изд., М., 1973.
А. А. Шишкин.