Обработка металлов резанием
Вид материала | Документы |
- Шифр специальности: 05. 16. 01 Металловедение и термическая обработка металлов и сплавов, 25.46kb.
- Обработка металлов давлением при обработке металлов давлением, 131.9kb.
- Программа профессиональной переподготовки мтф п/п-1 «металловедение и термическая обработка, 34.45kb.
- Лекция 7 термическая обработка металлов, 136.74kb.
- Научные основы и технологические способы обработки гетерофазных сплавов с высоким уровнем, 572.64kb.
- Программа вступительного испытания по направлению «Металлургия», 51.65kb.
- 05. 16. 01 Металловедение и термическая обработка металлов, 25.25kb.
- Развитие научных основ и разработка совмещенных методов обработки металлов давлением,, 606kb.
- Реферат по теме: «Металлы. Свойства металлов.», 196.2kb.
- Закономерности превращения, 589.18kb.
Фрезерный станок в металлообработке, металлорежущий станок для обработки резанием при помощи фрезы, наружных и внутренних плоских и фасонных поверхностей, пазов, уступов, поверхностей тел вращения, резьб, зубьев зубчатых колёс и т.п.
Принцип фрезерования, по-видимому, зародился в Европе в 16 в. — Леонардо да Винчи дал эскиз прототипа фрезы в виде вращающегося круглого напильника. Известен станок с вращающимся напильником, построенный в Пекине в 1665. Прототипы современных Ф. с. появились в 19 в.: консольный в 1835, универсальный в 1862, продольный в 1884. В дальнейшем конструкции Ф. с. быстро развивались, типы их дифференцировались.
По назначению Ф. с. разделяют на универсально-, горизонтально-, вертикально-, продольно-, копировально-, резьбо-, шпоночно-, карусельно-, барабанно-фрезерные и др. По конструкции Ф. с. могут быть консольные и бесконсольные. Главное движение у Ф. с. (вращательное) осуществляется фрезой, движение подачи (поступательное) — заготовкой; в некоторых случаях (например, при обработке крупных изделий) движение подачи может сообщаться фрезе.
Универсально-фрезерный станок (рис., а) консольной конструкции характеризуется горизонтальным расположением оси шпинделя, имеет хобот с подвеской для крепления оправки фрезы и предназначен для работы с разными типами фрез. Станок имеет поворотный (в горизонтальной плоскости) стол, что позволяет фрезеровать винтовые канавки; стол может перемещаться в продольном, поперечном и вертикальном направлениях. Горизонтально-фрезерный станок аналогичен универсально-фрезерному, но его стол не имеет возможности поворачиваться. Вертикально-фрезерный станок (рис., б) по конструкции близок к горизонтально- и универсально-фрезерным станкам, но отличается от них вертикальным расположением оси шпинделя. Продольно-фрезерный станок (рис., в) предназначен для обработки различных плоскостей у крупногабаритных заготовок (или их групп), установленных в многоместных приспособлениях на столе станка, главным образом торцовыми фрезами. На вертикальных стойках станка, смонтированных на станине, расположены боковые фрезерные головки, а также поперечина с вертикальными фрезерными головками. Каждая головка имеет индивидуальный привод вращения шпинделя; оси шпинделей могут перемещаться в горизонтальной и вертикальной плоскостях, а также устанавливаться под углом. Продольную подачу имеет стол, поперечную — вертикальные фрезерные головки, а вертикальную — боковые. Все фрезерные головки имеют общий привод подач. Шпоночно-фрезерный станок используется для фрезерования шпоночных пазов (по замкнутому полуавтоматическому циклу движений) вращающейся шпоночной фрезой (вертикальная подача на глубину паза, затем прямолинейная горизонтальная подача вдоль оси паза и обратная горизонтальная подача в конце хода). Эти станки бывают одно- и многошпиндельные. Карусельно-фрезерный станок служит для непрерывного фрезерования плоскостей литых, кованых и штампованных заготовок торцовыми фрезами. Стол станка имеет круговую подачу. Барабанно-фрезерный станок предназначен для одновременной обработки двух торцовых поверхностей заготовок (шатунов, валов, вилок и т.п.), а также фрезерования пазов (см. также статьи Зубообрабатывающий станок, Копировально-фрезерный станок, Резьбофрезерный станок).
В промышленности находят всё более широкое применение различные типы Ф. с. с программным управлением. В этих станках движение по каждой из трёх координат станка управляется сигналами, записанными на двух дорожках магнитной ленты. Сигналы, возникающие в обмотках шести катушек магнитной головки через усилители, формирователи импульсов и узел распределения импульсов, подаются на тяговые двигатели, а затем через соответствующие гидроусилители на ходовые винты подач станка.
Лит. см. при от. Металлорежущий станок.
Д. Л. Юдин.
Ф. с. в деревообработке имеет вращающийся вертикальный шпиндель, на котором укрепляется фреза, и применяется для плоскостной, профильной и фасонной обработки резанием заготовок. Различают Ф. с. простые (одно- или двухшпиндельные), карусельного типа и копировальные. Одношпиндельные Ф. с. имеют станину со столом и шпиндель, укрепленный на подвижном суппорте. Обработка заготовок осуществляется при помощи направляющих линеек. В двухшпиндельном Ф. с. шпиндели вращаются в противоположные стороны, что облегчает обработку заготовок криволинейной формы и уменьшает вероятность возникновения сколов и задиров. Для плоского и фигурного фрезерования используют Ф. с. карусельного типа с вращающимся столом, на котором укрепляются заготовки. Копировальный Ф. с. снабжен устройством для работы по копиру (шаблону) и служит для производства мелких, точных и скульптурных работ.
Лит. см. при ст. Деревообрабатывающий станок.
Н. К. Якунин.

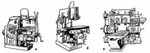
Основные типы фрезерных станков: а — универсально-фрезерный; б — вертикально-фрезерный; в — продольно-фрезерный.
Шлифовальный станок,
1) в металлообработке — металлорежущий станок для обработки заготовок абразивным инструментом. Первый Ш. с. современного типа (универсальный круглошлифовальный) был построен в 1874 в США. Вначале Ш. с. работали с кругами, изготовленными из цельных кусков природных абразивных пород, затем стали использоваться более прочные круги из размолотых природных абразивов. Изобретение в 1893 способа изготовления искусственных абразивов (карборунда) значительно расширило распространение Ш. с.
В соответствии с принятой для металлорежущих станков классификацией Ш. с. подразделяют на кругло- и внутришлифовальные (в т. ч. бесцентрово-шлифовальные, планетарные), специализированные, плоскошлифовальные и др., работающие абразивным инструментом (зубо- и резьбошлифовальные станки относят к группе зубо- и резьбообрабатывающих станков). Специфика используемого инструмента предъявляет к конструкции и конструкционным материалам некоторые дополнительные требования: виброустойчивость, износостойкость, интенсивный отвод абразивной пыли. Главное движение Ш. с. (см. в ст. Металлорежущий станок) — вращение абразивного инструмента, причём его скорость, как правило, значительно выше скорости подачи и других движений.
Наибольшее распространение получили круглошлифовальные станки. На этих станках заготовку устанавливают на центрах или в патроне (рис., а) и приводят во вращение навстречу шлифовальному кругу; вместе со столом станка она может совершать возвратно-поступательное движение. Шлифовальный круг в конце каждого (или двойного) хода стола получает поперечное перемещение на глубину резания (см. Обработка металлов резанием). На круглошлифовальных станках обычно шлифуют наружные цилиндрические и конические поверхности и торцы заготовок. На врезных круглошлифовальных станках шлифование наружных цилиндрических, конических и фасонных поверхностей производится широким кругом (шире размера заготовки); продольная подача здесь отсутствует.
Внутришлифовальные станки предназначены для шлифования внутренних поверхностей вращения. Наиболее распространены внутришлифовальные станки, у которых обрабатываемая заготовка вращается вокруг оси шлифуемого отверстия, а шлифовальный круг — вокруг своей оси (рис., б). Продольную и поперечную подачи осуществляют кругом. При обработке отверстий крупных заготовок, которые привести во вращение трудно, применяют планетарные внутришлифовальные станки. В этих станках шлифовальный круг вращается вокруг своей оси и вокруг оси шлифуемого отверстия одновременно (рис., в).
Бесцентрово-шлифовальные станки предназначены для шлифования наружных и внутренних цилиндрических поверхностей. При шлифовании наружных поверхностей заготовку (ряд состыкованных заготовок) помещают между двумя абразивными кругами — шлифовальным (режущим) и ведущим (рис., г) и прижимают к опорному ножу. Вследствие наклонной установки ведущего круга за счёт сил трения заготовка не только вращается, но и поступательно перемещается (продольная подача). Поперечную подачу осуществляют также ведущим кругом. При шлифовании внутренних поверхностей (например, колец подшипников) заготовки устанавливают между двумя поддерживающими роликами и ведущим кругом (рис., д), который и вращает заготовку. Шлифовальный круг, если необходимо, перемещается вдоль и поперёк оси отверстия или только радиально (при врезном шлифовании). Бесцентрово-шлифовальные станки менее универсальны, но конструктивно проще и производительнее кругло- и внутришлифовальных.
Плоскошлифовальные станки предназначены для обработки плоскостей заготовок периферией или торцом шлифовального круга. На таких станках, работающих периферией круга (рис., е), стол с закрепленной на нём заготовкой совершает возвратно-поступательное или вращательное движение, а вращающийся шлифовальный круг получает поперечную подачу на каждый ход или оборот стола, а также перемещение на глубину резания. В плоскошлифовальных станках, работающих торцом шлифовального круга (рис., ж), в отличие от станков, работающих периферией круга, поперечная подача отсутствует, т.к. диаметр круга больше поперечного размера обрабатываемой заготовки (врезное шлифование).
Специализированные Ш. с. предназначены, как правило, для обработки деталей заданной формы, например для шлифования шеек коленчатых валов, деталей штампов, шаблонов, шлицевых деталей и т.д. Обработку заготовок на этих станках осуществляют в основном методом копирования, реже методом огибания.
В общую группу Ш. с. входят также станки: притирочные, полировальные, доводочные, заточные, шлицешлифовальные, хонинговальные и др., работающие абразивным инструментом.
2) В деревообработке— деревообрабатывающий станок для шлифования деталей и изделий из древесины и древесных материалов. В зависимости от типа абразивного инструмента, формы, придаваемой шлифовальной шкурке, и назначения различают Ш. с.: дисковые, ленточные, барабанные (цилиндровые), бабинные, виброшлифовальные и полировальные. В зависимости от характера движения подачи детали Ш. с. бывают позиционные и проходные. В позиционных Ш. с. абразивный материал или обрабатываемая деталь совершают возвратно-поступательное движение, а в проходных Ш. с. обрабатываемая деталь (или изделие) проходит через зону абразивного материала. К позиционным относятся некоторые Ш. с. для полирования лакированных деталей. Шлифовку лакированных поверхностей производят чаще на виброшлифовальных станках, у которых шкурка в зоне контакта совершает вместе с прижимным механизмом колебательные движения (около 1400 колебаний в 1 мин). Наиболее производительны широколенточные Ш. с. проходного типа и Ш. с. барабанного типа.
Лит.: Металлорежущие станки, М., 1973; Маслов Е. Н., Теория шлифования материалов, М., 1974.
А. А. Шишкин, Н. К. Якунин.


Схемы работы шлифовальных станков: а — круглошлифовального; б — внутришлифовального; в — внутришлифовального планетарного; г — бесцентрово-шлифовального; д — бесцентрового внутришлифовального; е — плоскошлифовального, шлифующего периферией круга; ж — плоскошлифовального, шлифующего торцом круга; 1 — шлифовальный круг; 2 — хомутик; 3 — обрабатываемая деталь; 4 — патрон; 5 — ведущий круг; 6 — опорный нож.
Прецизионный станок, металлорежущий станок для высокоточной (прецизионной) обработки деталей. П. с. представлены в токарной, сверлильно-расточной, шлифовальной, зубообрабатывающей и фрезерной группах и разделяются по классам на станки повышенной точности (класс точности П), высокой точности (В), особо высокой точности (А) и особо точные (С). Обработка на П. с. обеспечивает получение изделий с поверхностями правильной геометрической формы, с точным пространственным положением осей и низкой шероховатостью поверхности до 11-го класса чистоты с обеспечением 2-го класса точности, а при определённых условиях — 1-го. Условиями для получения высокой точности обработки (в пределах нескольких мкм) является применение ответственных деталей и узлов повышенной точности, прецизионных и сверхпрецизионных подшипников качения, а также гидродинамических и гидро- и аэростатических подшипников и др.; снижение тепловых деформаций и вибраций; повышение жёсткости узлов; применение высокоточных приборов контроля активного; оснащение станков системами отвода стружки и тонкой фильтрации смазочно-охлаждающих жидкостей; высокая степень автоматизации управления станком, загрузки и выгрузки изделий. Особо важное значение при обработке имеет точность перемещения подвижных узлов П. с., что обеспечивается применением высокоточных специальных базовых деталей, направляющих, основных элементов механизмов перемещения и подач, снижением трения в механизмах перемещения подвижных узлов и т.п.
Тепловые деформации заготовок, станины, приспособлений и др. деталей и узлов П. с. (возникающие в результате выделения тепла от трения, работы гидроприводов и электроустройств, а также тепла, переносимого смазочно-охлаждающей жидкостью из зоны резания) могут быть уменьшены путём удаления от станка источников нагрева, применения систем смазки со стабилизацией температуры, холодильных устройств в смазочно-охлаждающей системе и т.п. При обработке особо точных деталей П. с. устанавливают в помещении с постоянной температурой. Для устранения вибраций (особенно при большой частоте вращения шпинделей) вращающиеся части П. с. подвергаются тщательной динамической балансировке. Электродвигатели и насосы устанавливают вне станины или на ней на особых эластичных подкладках, фундамент П. с. виброизолированный (см. Виброизоляция).
Тенденция развития П. с.: расширение номенклатуры и типоразмеров, освоение П. с. с числовым программным управлением, повышение ресурса работы и надёжности станков, оснащенных прецизионными отсчётно-измерительными приборами и самонастраивающимися системами управления.
Лит.: Кучер И. М., Металлорежущие станки, 2 изд., Л., 1969; Технологическая надежность станков, М., 1971; Металлорежущие станки, М., 1973,
Б. В. Протопопов.
Классы точности средств измерений, обобщённая характеристика средств измерений, служащая показателем установленных для них государственными стандартами пределов основных и дополнительных погрешностей и др. параметров, влияющих на точность. Например, для концевых мер длины К. т. характеризуют пределы допускаемых отклонений от номинального размера и влияние изменений температуры, а также допустимую непараллельность рабочих поверхностей и отклонение их от идеальной плоскости. Введение К. т. облегчает стандартизацию средств измерений и их подбор для измерений с требуемой точностью.
Из-за разнообразия измеряемых величин и средств измерений нельзя ввести единый способ выражения пределов допускаемых погрешностей и единые обозначения К. т. Если пределы погрешностей выражены в виде приведенной погрешности (т. е. в процентах от верхнего предела измерений, диапазона измерений или длины шкалы прибора), а также в виде относительной погрешности (т. е. в процентах от действительного значения величины), то К. т. обозначают числом, соответствующим значению погрешности. Например: К. т. 0,1 соответствует погрешность 0,1%. Многие показывающие приборы (амперметры, вольтметры, манометры и др.) формируются по приведённой погрешности, выраженной в процентах от верхнего предела измерений. В этих случаях применяется ряд К. т.: 0,1; 0,2; 0,5; 1,0; 1,5; 2,5; 4,0. При нормировании по относительной погрешности обозначение К. т. заключают в кружок.
Для гирь, мер длины и приборов, для которых предел погрешности выражают в единицах измеряемой величины, К. т. принято обозначать номером (1-й, 2-й и т.д. — в порядке снижения К. т.). При указании конкретного К. т. слово «точность» обычно опускается, например гири 3-го класса. Ряды К. т., их обозначения и соответствующие требования к средствам измерений включаются в стандарты (ГОСТ) на отдельные их виды.
Лит.: ГОСТ 13600—68. Государственная система обеспечения единства измерений. Средства измерений. Классы точности. Общие требования: Широков К. П. и Раинович С. Г., О классах точности средств измерений, «Измерительная техника», 1969, № 4.
К. П. Широков.