П. Н. Рудовский Общая характеристика работы
Вид материала | Автореферат |
- Содержание лекций Модели местного самоуправления в России Местное самоуправление:, 786.51kb.
- Общая характеристика работы актуальность работы, 336.09kb.
- Общая характеристика работы актуальность работы, 236.99kb.
- Общая характеристика работы актуальность работы, 227.87kb.
- Общая характеристика работы актуальность работы, 227.87kb.
- Задачи физического воспитания детей дошкольного возраста. Общая характеристика средств, 34.6kb.
- Реферат по курсу: экология на тему: Общая характеристика экосистем, как, 726.64kb.
- Научная работа студентов, 2153.55kb.
- Научная работа студентов, 2114.42kb.
- Общая характеристика работы актуальность работы, 487.01kb.
На правах рукописи
УДК 677.487.5
Киселев петр николаевич
РАЗРАБОТКА МЕТОДа АВТОМАТИЗИРОВАННОГО контроля формы паковок крестовой намотки
Специальность:
05.19.02 – «Технология и первичная обработка
текстильных материалов и сырья»
АВТОРЕФЕРАТ
диссертации на соискание ученой степени
кандидата технических наук
Кострома 2006
Работа выполнена в Костромском государственном технологическом университете.
Научный руководитель: | доктор технических наук, профессор Рудовский Павел Николаевич |
Официальные оппоненты: | доктор технических наук, профессор Наумов Андрей Константинович кандидат технических наук, доцент Безденежных Алла Германовна |
Ведущая организация: | ОАО «Костромской НИИ льняной промышленности» |
Защита состоится 29 июня 2006 г. в 10-00 часов на заседании диссертационного совета Д.212.093.01 в Костромском государственном технологическом университете по адресу: 156005, г. Кострома, ул. Дзержинского, 17, ауд. 214.
С диссертацией можно ознакомиться в библиотеке Костромского государственного технологического университета.
Автореферат разослан «___» мая 2006 г.
Ученый секретарь диссертационного совета,
доктор технических наук, профессор П.Н. Рудовский
Общая характеристика работы
Актуальность
Повышение качества и конкурентоспособности готовой продукции текстильных предприятий напрямую зависит от систематического и эффективного контроля качества полуфабрикатов и сырья на всех этапах текстильного производства. Одним из существенных этапов текстильного производства является формирование бобин крестовой намотки, которые получают либо на современных пневмомеханических прядильных машинах, либо путем перематывания початков, получаемых на кольцевых прядильных машинах. Пряжа в бобинах может использоваться в качестве основы и утка на бесчелночных ткацких станках, поэтому от качества намотки бобин в значительной степени зависит эффективность процессов снования и ткачества. Качество паковок крестовой намотки определяется целым комплексом параметров, в который входят плотность намотки и ее равномерность по радиусу и образующей, форма паковки и ее отклонение от требуемой, наличие ряда дефектов в виде уплотненных участков, жгутовой и ленточной намотки, слетов витков и др.
В настоящее время нет отработанных эффективных методик контроля всех параметров паковок крестовой намотки, влияющих на их качество. Систематически в приготовительном отделе ткацкого производства контролируется только диаметр бобин (стандартом регламентировано отклонение не более 5%) и их средняя плотность, которая оценивается по массе намотанной нити при известном диаметре намотки.
Второй по значимости составляющей качества паковок является форма намотки и ее отклонения от заданной. Наличие дефектов формы может привести к росту обрывности при сматывании, что приведет к снижению эффективности снования и ткачества. Своевременное обнаружение таких дефектов позволит устранить причины их появления путем соответствующей наладки оборудования. И отправить бобины с дефектами на повторное перематывание, при этом затраты, связанные с дополнительным перематыванием значительно ниже затрат связанных с ликвидацией обрывов в сновании и ткачестве. Таким образом, создание метода автоматизированного контроля формы паковок и его внедрение на производстве позволит повысить эффективность процессов снования и ткачества и повысить качество ткани за счет устранения дефектов, сопутствующих ликвидации обрывов.
В связи с этим работа, направленная на создание автоматизированных методов для контроля формы паковок крестовой намотки представляется актуальной.
Цель и задачи исследования
Целью работы является повышение эффективности процессов снования и ткачества обеспечиваемого за счет автоматизированного контроля формы бобин и своевременного устранения их дефектов путем наладки технологического оборудования.
Для реализации заявленной цели необходимо решить ряд задач:
- провести сравнительный анализ современных методов и средств контроля геометрических параметров паковок крестовой намотки;
- разработать методику и устройство для съема первичных данных, характеризующих форму паковок;
- оценить погрешности измерения первичных данных о форме паковки и сформулировать требования к точности изготовления устройства.
- разработать алгоритмы:
- предварительной обработки изображения;
- фильтрации изображения;
- формирования данных о профилях исследуемых поверхностей;
- построения графической 3-х мерной модели паковки;
- определить частные показатели, характеризующие отклонения формы паковок от заданной;
- разработать комплексный показатель качества формы паковок крестовой намотки;
- разработать алгоритм и программную реализацию расчета комплексного показателя качества формы;
- выполнить экспериментальную проверку разработанного метода.
Методы исследования
В работе использовали теоретические и экспериментальные методы исследования механико-технологических процессов текстильной промышленности. Применяли методы математической статистики, геометрической оптики, математического моделирования, методы информационных технологий обработки и анализа изображений и видео роликов. Исследования проводились как стандартными, так и оригинальными методами и средствами. Обработка экспериментальных данных проводилась средствами MS Excel 2000, MS Access 2000, Adobe Photoshop CS, а автоматизированная оценка качества партии бобин с помощью оригинального программно-аппаратного комплекса, программная часть которого разработана в среде Borland Delphi 6 Studio.
Научная новизна
В диссертационной работе впервые:
- разработан автоматизированный метод контроля геометрических параметров паковок крестовой намотки, основанный на теневой проекции сечения;
- проведен анализ влияния погрешностей взаимного расположения элементов установки для распознавания геометрических параметров паковок крестовой намотки на точность их определения;
- на основе экспертного опроса выявлена зависимость между количественными значениями отклонений формы намотки и качеством бобины;
- разработан метод визуального моделирования бобины с учетом отклонений ее формы от заданной;
- разработан комплексный показатель для оценки качества формы паковки на основе ее геометрических параметров полученных в результате автоматизированного контроля;
Практическая значимость
- Предложены способ и устройство для автоматизированного контроля геометрических параметров паковок крестовой намотки, основанное на теневой проекции сечения, защищенные патентом РФ на изобретение;
- Разработано алгоритмическое и программное обеспечение для реализации автоматизированного метода контроля геометрических параметров паковок крестовой намотки, основанного на теневой проекции сечения;
- Разработано алгоритмическое и программное обеспечение, для визуального моделирования бобин крестовой намотки;
- Экспериментально обоснована эффективность комплексного показателя для оценки качества формы паковки на основе ее геометрических параметров, полученных в результате автоматизированного контроля;
- Разработанный программный комплекс принят к использованию на ООО «БКЛМ-Актив» (г.Кострома).
Апробация работы
Основные положения диссертационной работы докладывались и обсуждались на: всероссийской научно-технической конференции «Современные технологии и оборудование текстильной промышленности» - Текстиль 2003, МГТУ им. А.Н. Косыгина 2003 г. межвузовской научно-технической конференции аспирантов и студентов «Молодые ученые – развитию текстильной и легкой промышленности» («Поиск - 2004»), г. Иваново; международной научной конференции «Математические методы в технике и технологиях», КГТУ 2004 г.; на семинаре по технологии текстильных материалов АИН имени Прохорова А.М., г. Кострома, 2005; на всероссийской научно-практической конференции «Инновационный инжиниринг организационного, технического и информационного сервиса», КГУ им. Н.А. Некрасова, 2005 г. на расширенном заседании кафедры механической технологии волокнистых материалов КГТУ.
Публикации
По теме диссертации опубликовано 8 печатных работ. В том числе один патент РФ на изобретение.
Структура и объем работы
Диссертационная работа состоит из введения, четырех глав и общих выводов. Работа содержит 127 страниц, 9 таблиц, 60 рисунков, список литературы, включающий 62 наименования, 2 приложения.
Содержание работы
Во введении обоснована актуальность темы диссертационной работы, определены цель и задачи исследований, указана научная новизна и практическая значимость работы.
В первой главе проведен анализ влияния дефектов формы паковок крестовой намотки на их пригодность к переработке на последующих переходах - в сновании и ткачестве. Показано, что нарушения формы паковки приводят к повышенной обрывности при их сматывании. Это связано с тем, что дефекты формы часто вызываются нарушениями в ходе технологического процесса наматывания, такими как неправильная раскладка, нерациональный закон изменения усилия прижима бобины к мотальному валу, неправильный выбор натяжения нити при перематывании, нарушения структуры намотки или нарушениями условий транспортирования и хранения бобин. Многие из этих нарушений технологического процесса могут быть выявлены путем анализа формы паковки.
Проведен обзор существующих методов оценки формы бобины, выявлены их достоинства и недостатки. Рассмотрены конструкции приборов, реализующие приведенные методы.
Причины образования дефектов намотки в виде отклонения ее формы от заданной и методы контроля формы паковок изучались в трудах ведущих отечественных и зарубежных ученых Севостьянова А.Г., Прошкова А.Ф., Ефремова Е.Д., Гордеева В.А., Lünenschloß J., Wegener W., Schubert G.
Установлено, что развитие методов оценки формы бобины шло от органолептических методов, основанных на экспертной оценке. Однако такие негативные факторы как субъективность, низкая производительность обусловили необходимость в создании инструментальных методов. Были предложены механические методы контроля формы бобин, в которых используются разнообразные щупы и шаблоны. Эти методы имеют существенные ограничения и недостатки, такие как деформация контролируемого объекта под действием измерительного усилия, точечный характер измерений и длительная обработка результатов измерения.
Дальнейшим развитием методов контроля формы являются оптические методы. Они являются бесконтактными и не вносят искажения в форму контролируемого объекта. Наиболее простой из них фотографический, заключающийся в том, что контролируемая бобина фотографируется на фоне измерительной линейки, после чего с фотографии можно снять размеры, требуемые для оценки ее формы. Более совершенные оптические методы используют для получения информации направленный поток света, в том числе и лазерное излучение, и регистрирующие фотоэлементы. О форме контролируемой поверхности судят по характеру фотосигнала, для анализа которого используются специальные электронные схемы, в том числе и построенные на основе микропроцессоров. Такие устройства, как правило, очень сложны в изготовлении, настройке и обслуживании, предназначены для контроля паковок только строго определенных размеров и формы. Основным их недостатком является то, что с помощью небольшого числа фотоэлементов невозможно получить полную информацию о форме паковки. С появлением оптоэлектронных регистрирующих матриц появилась возможность получения оцифрованного изображения в предметной плоскости устройства наблюдения, которое содержит информацию о форме исследуемого объекта, в этой плоскости. Для получения полной информации о форме исследуемой паковки необходимо сделать ряд снимков с нескольких точек наблюдения. Однако при этом возникает проблема выделения из большого объема визуальной информации требуемых данных и формирование на их основе показателей для оценки формы паковок.
Методы светового сечения и теневой проекции позволяют вести наблюдение в каждый момент времени за вполне определенным узким участком контролируемой паковки и таким образом выделить информацию о форме бобины из общего потока. Эти методы в комплексе с методами распознавания образов позволяют создать автоматизированный комплекс для контроля формы паковок крестовой намотки. По результатам анализа сформулирован ряд задач, решение которых необходимо для разработки нового метода автоматизированного контроля формы паковок и его техническое реализации.
Во второй главе проведен теоретический анализ контроля профиля образующих паковок крестовой намотки методом теневой проекции сечения
![]() Рисунок 1. – схема получения изображения профиля методом теневой проекции | На рисунке 1 приведена схема формирования изображения про-филя поверхности при освещении ее параллельным пучком света направленным вдоль оси О1 О1 под углом α к нормальной плоскости. Часть пучка света отсекается непрозрачной шторкой Ш. В результате чего на поверхности формируется тень, повторяющая ее профиль. Изображение тени фиксируется прибором наблюдения, оптическая ось О2 – О2 которого направлена |
под углом β к нормальной плоскости. Полученное изображение тени отличается от реального профиля на масштаб преобразования, который можно рассчитать по формуле
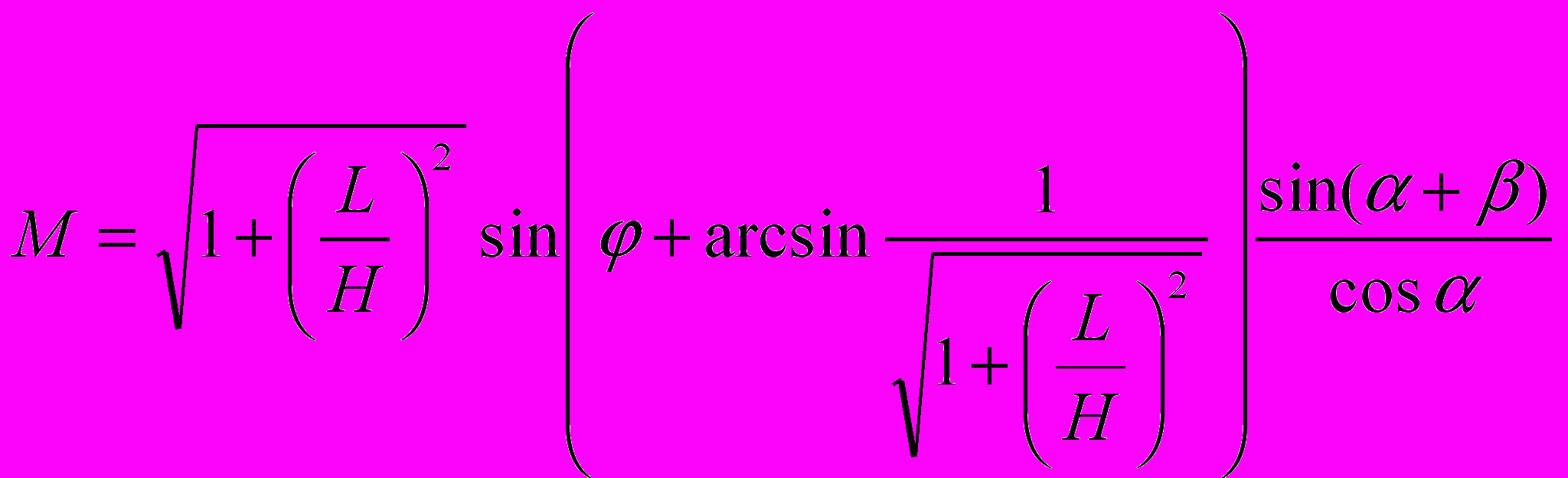
где φ – угол наклона плоскости, проходящей через прямые О2 – О2 и О1 О1 к нормали n-n.
Н – наибольшая наблюдаемая высота профиля,
L – ширина поля зрения прибора наблюдения
Проведен анализ зависимости масштаба преобразования профиля от конструктивных параметров устройства. Выявлены основные погрешности, влияющие на процесс съема первичных данных методом теневой проекции:
Это погрешности вызванные кривизной изображения края тени и погрешности масштаба преобразования:
- отклонения, вызванные линейным смещением осветителя,
- отклонение, вызванное линейным смещением бобины,
- отклонения, вызванные поворотом шторки.
Проведен анализ отдельных составляющих погрешности масштаба преобразования, вызванных линейными и угловыми смещениями отдельных составных частей установки для контроля формы паковки.
Установлено, что погрешность вызванная кривизной изображения края тени является систематической. Установлен закон ее образования. Данная погрешность учтена при разработке программного обеспечения.
Были сформулированы основные требования, которым должно отвечать устройство наблюдения, входящее с состав аппаратного комплекса для контроля формы паковок:
- разрешающая способность матрицы не менее 2 мегапикселей , позволяющая регистрировать линейные размеры с погрешностью 0,25 мм.
- оцифровывание изображения и непосредственная передача его для обработки в ЭВМ;
- возможность оперативной, последовательной съемки изображений на вращающейся паковке.
В результате в качестве устройства наблюдения была выбрана цифровая камера с возможностью записи видеороликов.
В третьей главе разработан программно аппаратный комплекс для контроля геометрических параметров текстильных паковок и программное обеспечения для него. Схема устройства для получения первичных данных о форме паковки приведена на рисунке 2.
Устройство состоит из бобинодержателя с приводом бобины 1, который может поворачиваться на стойке 2 и фиксироваться в двух положениях, для контроля боковой и торцевых поверхностей бобины. Осветителя 3, цифровой камеры 4 и шторки 5.
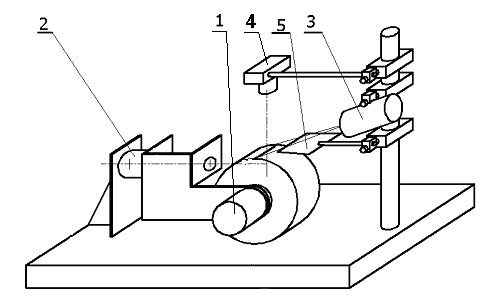
Рисунок 2 – схема устройства для снятия первичных данных
Регистрация первичной информации о профиле каждой бобины проводится в режиме съемки видеоролика трижды: для двух торцевых и боковой поверхности за время одного оборота бобины. Полученные видеоролики передаются через порт USB в компьютер и сохраняются на жестком диске в формате MOV.
Их дальнейшая обработка осуществляется с помощью специального программного обеспечения, которое реализует следующие алгоритмы:
- определения масштаба изображения;
- разбивки видеороликов на кадры;
- поиска изображения паковки в кадре,
- фильтрации изображения от помех
- получения координат профиля паковки;
- построения трехмерной модели паковки;
- расчет единичных и комплексного показателей качества паковки по ее форме.
Масштаб изображения определяется на основании данных о длине мерного отрезка, границы которого на изображении вводятся оператором с помощью манипулятора «мышь».
Для разбивки видеоролика на кадры используются библиотека пакета QuickTime.
Поиск изображения в кадре реализован двумя способами. При первом способе оператор должен указать точку, принадлежащую бобине. При втором способе проводится последовательный просмотр изображения по столбцам. Если за найденным в каком либо столбце пикселе с цветом бобины, следует столбец, в котором пиксель с цветом бобины имеет координату, отличающуюся от координаты пикселя в предыдущем столбце на величину не более заданной, то считается, что первый и все последующие столбцы содержат изображение бобины. Первый способ требует вмешательства оператора, но требует меньшего времени для реализации задачи.
Фильтрация изображения от помех также реализована двумя способами. Более быстрым является второй способ, в котором фильтрация совмещена с определением координат точек на границе профиля исследуемой паковки.
По описанным алгоритмам производится определение координат профиля двух торцов бобины и ее боковой поверхности. После чего в памяти компьютера формируется массив информации о координатах точек поверхности бобины с достаточно мелким шагом, который содержит полную информацию о размерах и форме исследуемой паковки. Эта информация может использоваться для построения визуальной трехмерной модели паковки и для расчета единичных показателей, характеризующих отдельные дефекты намотки.
Для построения графической модели, полученные профили сечений паковки располагаются в плоскостях полученных поворотом каждой последующей плоскости, по отношению к предыдущей на угол
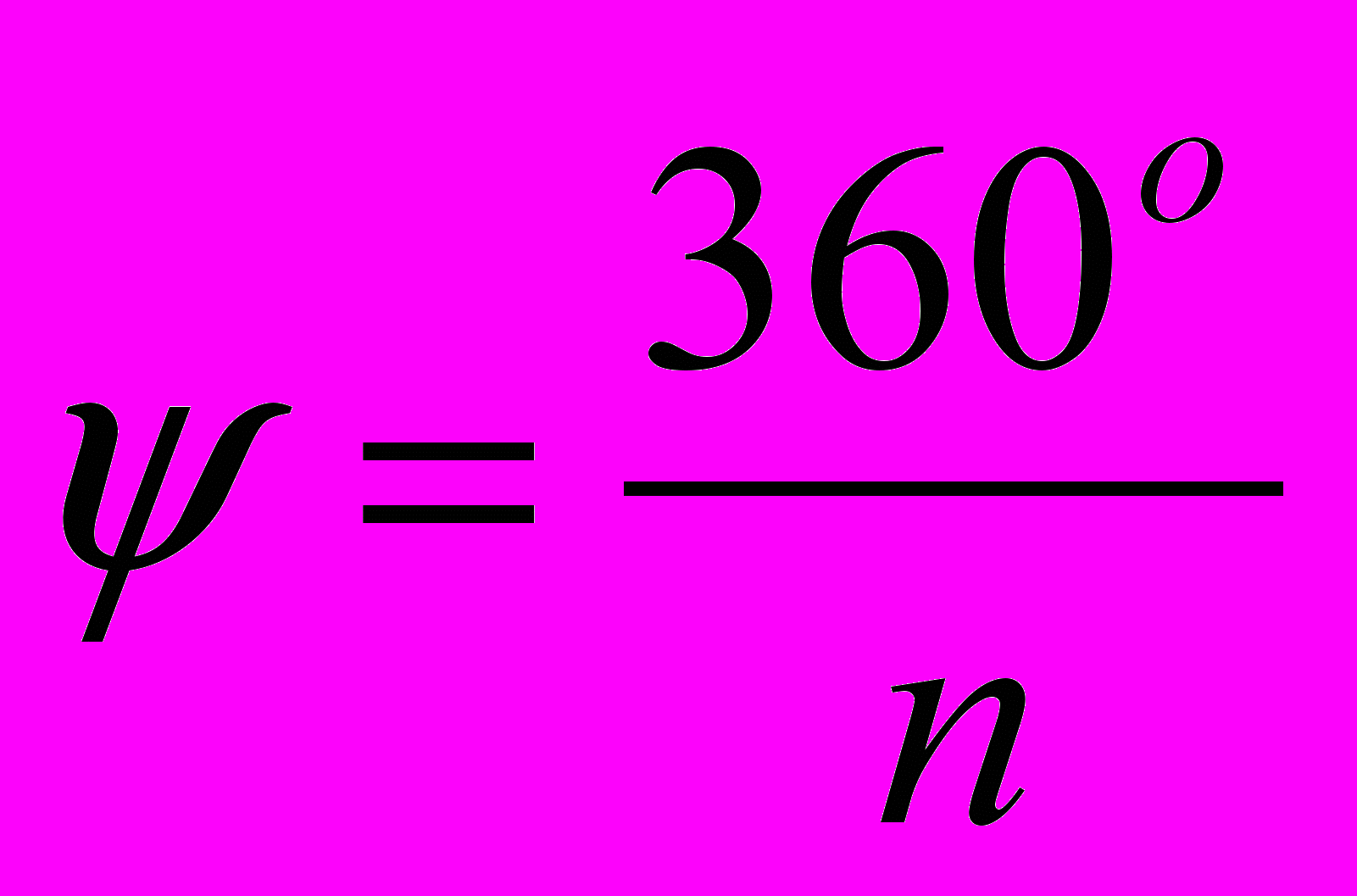
где n-количество кадров отснятых за один оборот паковки.
На рисунке 3 приведена схема формирования трехмерной модели паковки. После обработки результатов измерений профили паковки получены в координатах YOZ. Трехмерная модель паковки строится в системе координат OX’Y’Z’. Ось OZ’ совпадает с осью ОZ. Плоскость YOZ для каждого сечения получается поворотом плоскости Y’OZ’ относительно оси OZ’ на угол nψ, где n – номер профиля. На рисунке 3 показано построение второго профиля.
Точка А, имеющая на профиле, т.е. в системе координат YOZ, координаты y, z, в системе координат OX’Y’Z’ будет иметь координаты x’, y’, z’, которые можно рассчитать по формулам
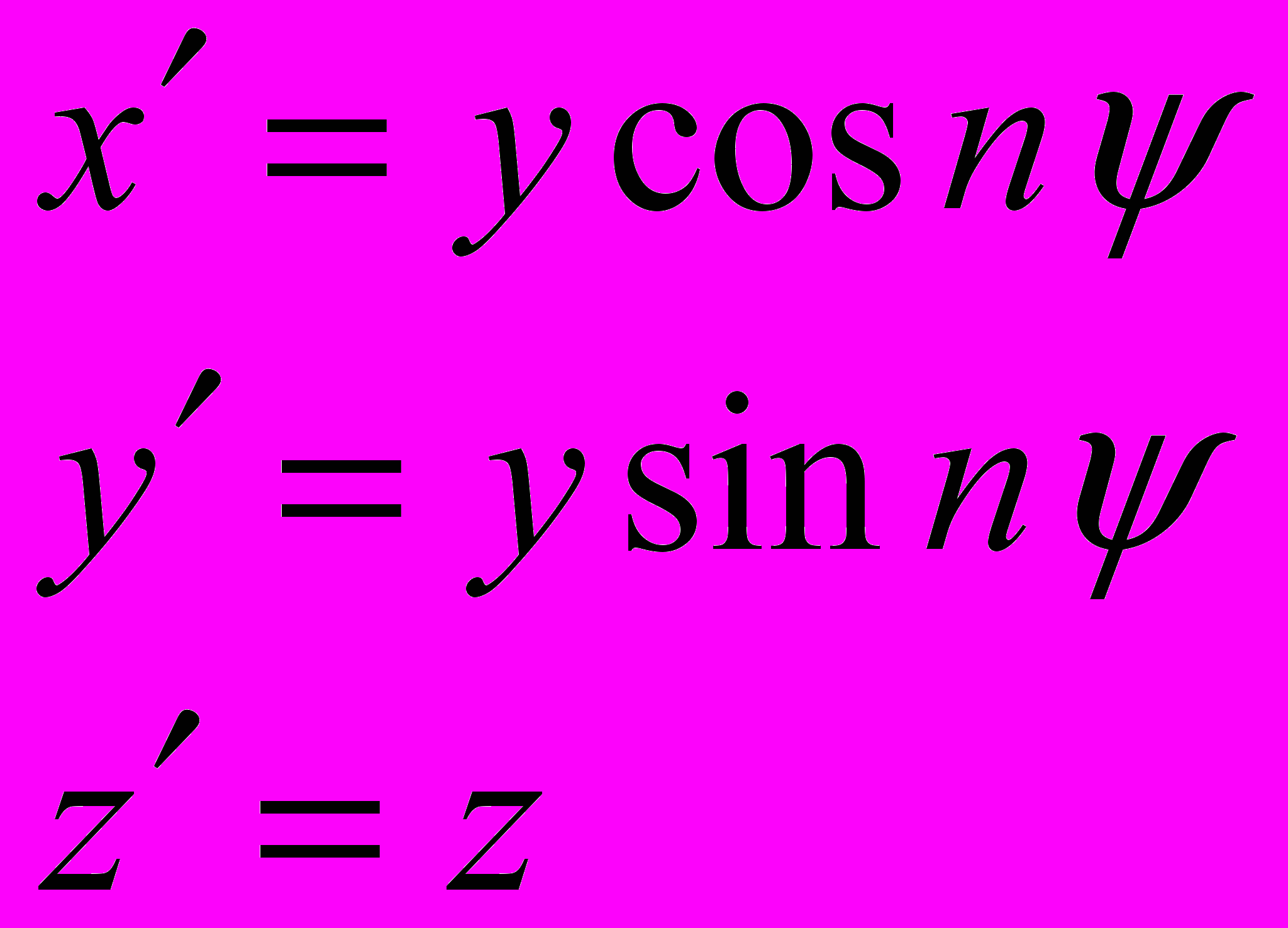
Визуальное построение модели реализовано с использованием библиотеки OpenGL.
![]() Рисунок 3. -схема построения объемной графической модели паковки. | Трехмерная визуальная модель паковки, полученная с помощью разработанного ПО представлена на рисунках 4 и 5. В четвертой главе разработан метод оценки качества формы паковок крестовой намотки. Для этого методом экспертного опроса проведено ранжирование дефектов формы паковок по степени их влияния на пригодность паковок к переработке на последующих технологических переходах |
Выявлено шесть основных дефектов формы паковок: отклонение торца от прямолинейности, уступы на торце бобины, уплотнения и уступы на боковой поверхности бобины, жгутовая намотка, гофры на торцах возле патрона, отклонение от конусности.
![]() Рисунок 4. – трехмерная модель паковки с пневмомеханической машины R-40 фирмы Rietter | ![]() Рисунок 5. - трехмерная модель паковки с пневмомеханической машины ППМ-120 на жгутовом диаметре |
Для количественной оценки каждого из названных дефектов формы бобины определены единичные показатели, разработаны решающие правила и алгоритмы для их вычисление на основании полученного ранее массива данных о координатах точек поверхности бобины.
На основании экспертного опроса установлена бальная оценка влияния каждого из единичных показателей, характеризующих дефекты намотки на пригодность паковок к переработке на последующих технологических переходах. Полученные зависимости приведены на рисунках 6 – 11, а результаты их аппроксимации линейными зависимостями в таблице 1.
Таблица 1.
№ п/п | Наименование единичного показателя | Уравнение зависимости бальной оценки Yi от единичного показателя Xi |
1 | Максимальное отклонение торца от прямолинейности, мм | ![]() |
2 | Высота уступа на торце бобины, мм | ![]() |
3 | Ширина уплотнений у торцов бобины, мм | ![]() |
4 | Жгутовая намотка, число нитей | ![]() |
5 | Ширина гофров на торцах возле патрона, мм | ![]() |
6 | Отклонение бобины от конусности, град | ![]() |
Комплексная оценка качества формы паковки может быть получена методом средневзвешенного показателя. Средний взвешенный показатель строится как зависимость, аргументами которой являются единичные показатели качества и параметры их весомости. Исходя из этого, была выведена зависимость комплексного показателя качества формы бобины.
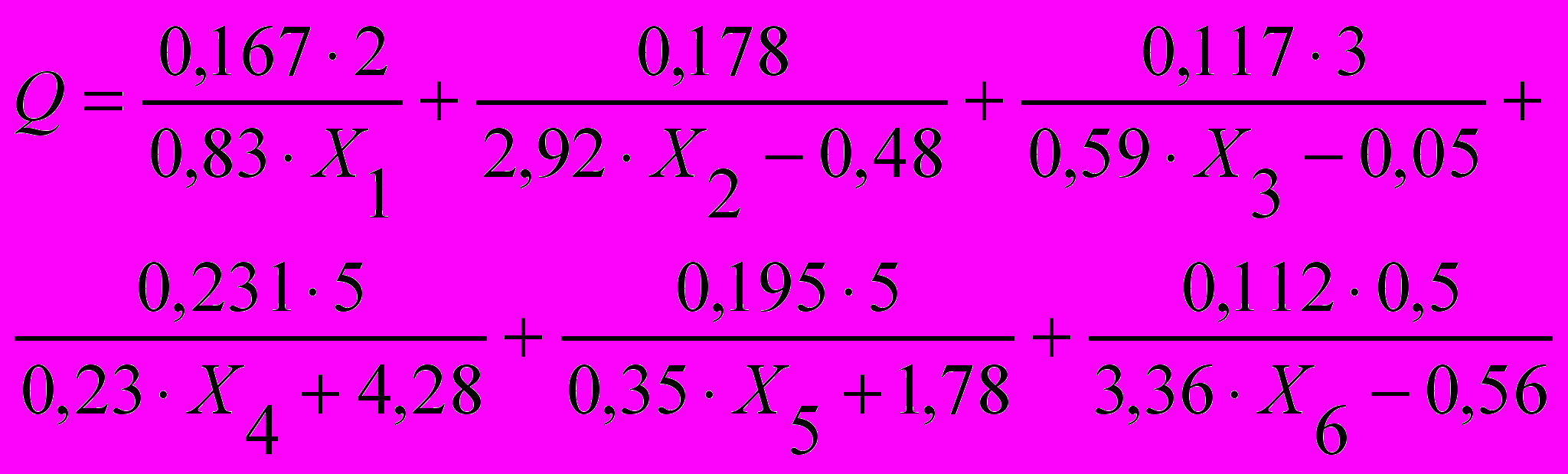
Чем большее значение принимает этот показатель, тем выше качество контролируемой паковки.
Проведена оценка применимости разработанного комплексного показателя для анализа формы паковок. Для этого проведен анализ партии паковок, который подтвердил воспроизводимость процесса анализа формы паковки с помощью предложенного комплексного показателя; а также соответствие оценок, полученных по предложенной методике, визуальным оценкам.
![]() Рисунок 6.- максимальное отклонение торца от прямолинейности | ![]() Рисунок 7. - уступы торца бобины |
![]() Рисунок 8 - уплотнения торцов (при ширине уплотнений) | ![]() Рисунок 9. - жгутовая намотка, число нитей |
![]() Рисунок 10 - гофры на торцах возле патрона при ширине | ![]() Рисунок 11. - отклонение бобины от конусности |
Метод комплексной количественной оценки формы паковок, изложенный в настоящей работе позволяет проводить оптимизационные эксперименты и на их основе назначать такие регулируемые параметры мотальных механизмов, которые позволят получать паковки требуемого качества. При разработке нового мотального оборудования можно будет заложить необходимые механизмы регулирования процесса намотки.
Предложенный программно-аппаратный комплекс оценки формы паковок принят для опытной проверки и последующего использования в ткацко-приготовительном цехе ООО «БКЛМ-Актив»
Основные результаты и выводы
- На основании анализа способов и устройств контроля формы паковок наиболее перспективными с точки зрения соотношения «цена-качество» являются устройства, основанные на анализе средствами специального программного обеспечения ЭВМ, изображения профилей торцов и образующей паковки, полученных методом теневой проекции.
- Проведен анализ структуры погрешностей контроля формы паковок крестовой намотки методом теневой проекции и получены выражения для отдельных составляющих погрешности контроля формы, что позволяет обоснованно подойти к назначению допусков на взаимное расположение отдельных элементов устройства.
- Проведен анализ устройств регистрации изображений с точки зрения возможности их применения в аппаратном комплексе для регистрации параметров формы паковок крестовой намотки.
- Разработано устройство для снятия первичных данных о форме паковки крестовой намотки, основанное на методе теневой проекции.
- Разработана система из шести единичных показателей для оценки формы паковок крестовой намотки и решающие правила, которые позволяют алгоритмизировать расчет предложенных единичных показателей.
- Разработано программное обеспечение, позволяющее получить первичные данные, произвести их обработку и построить трехмерную модель паковки крестовой намотки.
- На основе экспертного опроса получена оценка влияния каждого, из предложенных показателей, на качество паковки в целом и получена формула для расчета комплексного показателя качества формы бобины.
- Разработано программное обеспечение для расчета в автоматизированном режиме единичного и комплексного показателей, характеризующих форму паковок.
- Проведен анализ партии паковок, который подтвердил воспроизводимость процесса анализа формы паковки с помощью предложенного комплексного показателя; а также соответствие оценок, полученных по предложенной методике, визуальным оценкам.
- Предложенный программно-аппаратный комплекс оценки формы паковок принят для опытной проверки и последующего использования в ткацко-приготовительном цехе ООО «БКЛМ-Актив».
Публикации, отражающие основное содержание работы
- Киселев П.Н. Автоматизированный контроль формы паковок крестовой намотки / Киселев П.Н., Рудовский П.Н. // Сборник трудов молодых ученых КГТУ / КГТУ – вып. 5 – Кострома: КГТУ, 2004 –часть 1.
- Киселев П.Н., Автоматизированный контроль формы паковок крестовой намотки / Киселев П.Н., Рудовский П.Н. // Тезисы докладов всероссийской научно-технической конференции «Современные технологии и оборудование текстильной промышленности» - Текстиль 2003, изд. МГТУ им. А.Н. Косыгина 2003 г.
- Киселев П.Н., Построение модели паковки с использованием ЭВМ / Киселев П.Н., Рудовский П.Н. // Сборник материалов международной научно-технической конференции «Современные наукоемкие технологии и перспективные материалы текстильной и легкой промышленности» ПРО ГРЕСС-2004, ИГТА 2004 г.
- Киселев П.Н., Программное обеспечение для построения трехмерной модели паковки / Киселев П.Н., Рудовский П.Н., Палочкин С.В. // Вестник КГТУ № 9, Кострома 2004 г.
- Киселев П.Н. Влияние неточности установки осветителя на оценку отклонений формы паковок методом теневого сечения / Киселев П.Н., Рудовский П.Н. // Сборник трудов XVII международной научной конференции «Математические методы в технике и технологиях», КГТУ 2004 г.
- Киселев П.Н., Разработка комплексного показателя качества ткацкой паковки // Сборник материалов всероссийской научно-практической конференции «Инновационный инжиниринг организационного, технического и информационного сервиса», КГУ им. Н.А. Некрасова, 2005 г.
- Киселев П.Н. Способ контроля формы паковки и устройство для его осуществления. / Киселев П.Н., Рудовский П.Н., Палочкин С.В. Патент № 2275320 РФ на изобретение, МПК D 01H 7/46, опубл 27.04.2006. Бюллетень изобретений № 12. (Входит в перечень ведущих рецензируемых научных журналов).
- Киселев П.Н. Выбор устройства для первичной регистрации изображения в системе автоматизированного анализа формы паковок. / Н.и. труды молодых ученых КГТУ в 2 ч. Часть 1/ Костромской государственный технологический университет.- вып. 7.- Кострома КГТУ – 2006.