Очистить форматирование удаляет форматирование выделенного текста и сбрасывает на нормальное
Вид материала | Документы |
3. Основные разновидности биологических испытаний |
- Название доклада, 103.9kb.
- Название и. И. Иванов, 41.51kb.
- Приказ по школе. Красноармейцу Сухову доставить в целости и сохранности учениц 9 класса, 26.48kb.
- Название и. О. Фамилия, 33.04kb.
- Электронные таблицы в Microsoft Excel, 156.17kb.
- Название тезисов (не более 3 строк), 24.32kb.
- Название тезисов (не более 3 строк), 24.93kb.
- Microsoft Office Excel. Интерфейс программы. Заполнение и редактирование ячейки. Форматирование, 1488.42kb.
- Форматирование документа, 63.56kb.
- Вопросы для контрольной работы по дисциплине «итпд», 12.37kb.
Выделяют испытания на динамические и статические воздействия пыли, а также на пыленепроницаемость.
Испытание на динамическое воздействие пыли проводят с целью проверки устойчивости ЭС к разрушающему (абразивному) воздействию пыли. При испытании (без электрической нагрузки) ЭС обдувают воздухом, содержащим просушенную пылевую смесь.
Испытание на статическое воздействие пыли проводят с целью проверки способности изделий сохранять параметры в среде с повышенной концентрацией пыли. Для этого ЭС (при электрической нагрузке) подвергают воздействию пыли, находящейся во взвешенном состоянии в воздухе камеры. Затем пыли дают осесть при отсутствии циркуляции воздуха в камере. При обоих видах испытания проводят внешний осмотр и измерение контролируемых параметров ЭС до и после испытаний.
Испытание на пыленепроницаемость служит для проверки возможности проникновения пыли через корпуса и кожухи ЭС внутрь изделий, находящихся в среде с повышенной концентрацией пыли. При испытании в пыль добавляют флуоресцирующий порошок. Чтобы выявить, попала ли пыль внутрь изделий, после испытания их переносят в затемненное помещение, вскрывают и подвергают ультрафиолетовому облучению. При проверке устойчивости к абразивному действию пыли изделия считают выдержавшими испытание, если их внешний вид удовлетворяет оговоренным в стандартах требованиям; в случае проверки пыленепроницаемости признаком брака служит проникновение пыли внутрь изделий.
Конструкция камеры пыли, предназначенной для испытания, представлена на рис. 4 8. Испытываемые изделия устанавливают на столе 3 таким образом, чтобы воздействие пыли было наиболее эффективным и соответствовало возможному воздействию пыли при эксплуатации. Максимальное расстояние от изделия до стенок камеры и между изделиями должно быть не менее 0,1 м. Вентилятор 4 прогоняет воздух с пылевой смесью, скорость которого регулируется наклоном шибера 9 заслонки. Стол вращается в горизонтальной плоскости с частотой 9 мин-1, что позволяет проводить опыление изделий равномерно со всех сторон.
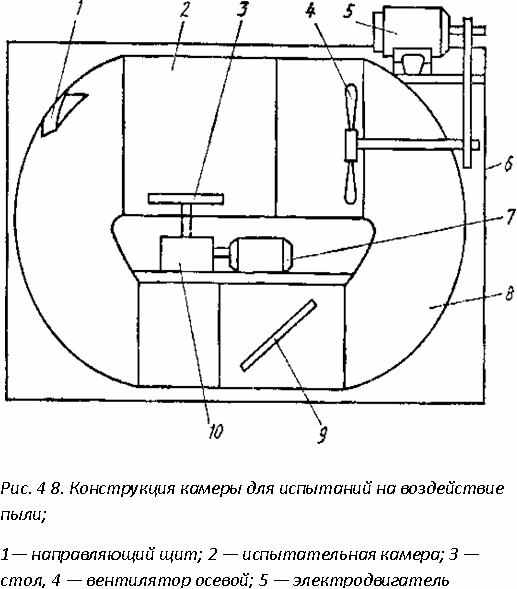
Билет 18
1. Планы испытаний на надежность
При контроле готовой продукции необходимо однозначно определить такие данные, как время испытаний tи, объем выборки n и приемочное число С — максимальное число отказавших изделий за время испытания выборки, при котором партия принимается. Совокупность этих данных составляет план контроля, для формирования которого пользуются, как правило, специальными таблицами и графиками. Продолжительность tи определенного испытания на надежность и число n испытываемых изделий связаны соотношением:
n*tи = k*T, (7.1)
где k — коэффициент, зависящий от вида испытаний; T— среднее время безотказной работы.
Большой объем является одной из характерных особенностей испытаний на надежность. Эта особенность обусловлена статистическим подходом к определению количественных показателей надежности, значения которые с ростом надежности растут, а следовательно, увеличивается объем испытаний на надежность с целью подтверждения заданного или определения неизвестного показателя. При планировании определительных испытаний на надежность принципиально невозможно однозначно указать объем испытаний, так как точность оценок показателей надежности при заданной достоверности зависит от объема полученной при испытаниях информации, т.е. от числа отказов. Следовательно, значение Vи может быть определено лишь ориентировочно исходя из априорного уровня надежности ЭС. Ошибки планирования приводят к завышению или занижению требуемого объема испытаний, что выявляется при обработке их результатов.
Время проведения контрольного испытания ЭС на надежность обычно регламентировано гарантированным временем безотказной работы или выбирается произвольно при известном законе распределения наработки на отказ испытываемых изделий. При планировании контрольных испытаний учитывают интересы либо поставщика и заказчика — планирование по приемочному и браковочному уровням, либо только заказчика— планирование по браковочному уровню. В первом случае контроль осуществляют по двум заданным значениям P1 и Р2 вероятности безотказной работы и соответствующим им рискам альфа и бета поставщика и заказчика. Планирование по браковочному (гарантированному) значению Р2 вероятности безотказной работы, т. е. минимальному значению вероятности Р2 безотказной работы, применяют внутри предприятий-поставщиков для подтверждения соответствия производственной надежности изделий требованиям заказчика. В этом случае учитывают только интересы заказчика, которому с доверительной вероятностью Р*=1—бета гарантируется, что в принятой партии надежность изделий не хуже браковочного уровня Р2.
План контроля должен позволять быстро оценивать с определенным риском заказчика или поставщика и заказчика надежность принимаемой партии. Время испытаний не должно быть слишком длительным, а стремление достигнуть минимальных значений альфа или бета
не должно приводить к чрезмерному увеличению объема выборки.
В настоящее время применяют различные методы контрольных испытаний на надежность. При выборе того или иного метода испытаний следует учитывать закон распределения контролируемого показателя надежности (вероятности безотказной работы, наработки на отказ, интенсивности отказов), ограничивающий фактор или критерий прекращения испытаний, порядок замены или восстановления отказавшего изделия
2. Термовакуумные испытания
Эксплуатация ЭС в условиях космоса оказывает существенное влияние на тепловой режим работы изделий.
Термовакуумные испытания проводят для исследования работоспособности ЭС в зависимости от их теплового режима в условиях космоса. Для обеспечения теплового режима ЭС в лабораторных условиях, аналогичных условиям их эксплуатации в космосе, достаточно воспроизвести основные факторы космического пространства: глубокий вакуум; солнечное излучение; излучения планет солнечной системы, влияющие на условия эксплуатации ЭС (например, Земли, если ЭС эксплуатируются на околоземной орбите); «холод» и «черноту» пространства за пределами телесных углов, занимаемых Солнцем и рассматриваемой планетой. Цикл отработки теплового режима ЭС включает; проверку работоспособности ЭС и их составных частей в условиях реальных нестационарных градиентов температуры; исследование поля температур в отсеках космического аппарата (КА), где
размещены ЭС, и взаимного влияния температурных полей различных тепловыделяющих устройств КА на работоспособность ЭС; выбор оптимального размещения ЭС и тепловыделяющих устройств КА; определение фактических температурных пределов работоспособности ЭС; проверку эффективности работы системы терморегулирования в условиях, максимально приближающихся к реальным; исследование работы системы терморегулирования в аварийных ситуациях; определение ресурса ЭС и их составных частей; исследование деформаций конструкций ЭС, вызванных температурными воздействиями.
Моделирование теплового режима ЭС производят в вакуумной камере, в которой устанавливают имитаторы лучистых потоков Солнца, планеты и орбиты КА. Для испытания выбирают КА, аналогичный предназначенному для полета в космос. На нем устанавливают датчики температуры в точках, наиболее полно характеризующих его тепловое поле, и датчики других величин (давления, расхода теплоносителя и др.).
Качество имитатора солнечного излучения характеризуется плотностью потока лучистой энергии и углом расхождения лучей в рабочей зоне, соответствием спектра лучистого потока спектру естественного излучения Солнца и поляризацией лучей. Для весьма совершенного имитатора не должны быть превышены следующие значения: неоднородность плотности потока лучистой энергии но всем объеме рабочей зоны ±5%, расхождение лучей ±2°, среднее квадратическое отклонение спектральных плотностей энергии излучения имитатора от соответствующих спектральных плотностей солнечного излучения ±5% в диапазоне длин волн 0,2 ..3 мкм, степень поляризации 3...5 %.
3. Основные разновидности биологических испытаний
Испытание на биологические воздействия проводят для проверки способности изделий сохранять свои параметры в пределах, установленных НТД, при воздействии и после него биологических факторов (биофакторов). В настоящее время ГОСТами регламентируется учет следующих биофакторов: плесневых грибов, насекомых, грызунов и почвенных микроорганизмов. Наибольшие разрушения ЭС наблюдаются при воздействии грибковой плесени. Поэтому испытание на грибоустойчивость — самый распространенный вид испытания на биологические воздействия.
Испытание на грибоустойчивость проводят с целью определения способности материалов и покрытий, применяемых при изготовлении ЭС, противостоять грибковой плесени в среде, зараженной плесневыми грибами. Это испытание осуществляют на образцах, которые не подвергались каким-либо другим воздействиям. В качестве образцов допускается использовать изделия, забракованные по электрическим параметрам. Число образцов устанавливают в соответствии с НТД или ПИ. Для испытания выбирают широко распространенные виды плесневых грибов, которые быстро растут, обладают высокой стойкостью к фунгицидам (противогрибковым препаратам) и способны наносить наибольший вред ЭС. Виды грибов, применяемых при испытании, установлены ГОСТ 9.048—75.
Для испытания на грибоустойчивость используют следующее оборудование: камеры грибообразования (например, типа КВТ/Г) или термостаты (например, типа ТС-80), обеспечивающие температуру нагрева 29+/-2 градуса цельсия и относительную влажность в рабочем объеме более 90%; эксикаторы; сушильные шкафы; автоклавы, биологические микроскопы; пульверизаторы; чашки Петри; пробирки и т.д.
Различают два метода испытаний на грибоустойчивость. При первом методе образцы ЭС, отобранные для испытания, тщательно очищают от загрязнений этиловым спиртом, при втором — выборку из четного числа образцов делят на две равные части. Для выявления причин поражения изделий грибами подвергают очистке от загрязнений этиловым спиртом только первую группу образцов. Таким образом, при использовании первого метода устанавливается, содержат ли ЭС источники питания для развития и роста грибов; при втором методе, кроме того, устанавливается наличие фунгицидных свойств у изделий и влияние внешних загрязнений на грибоустойчивость ЭС, т.е. он является более информативным.
Испытание на устойчивость материалов к воздействию термитов. В лабораторных условиях испытание осуществляют в термостатах при температуре 26+/- 0,5градуса С и влажности воздуха, близкой 100 %.
Испытание проводят следующим образом. На образец материала, имеющий форму пластины размером 40X80 мм, накладывают полоску фильтровальной бумаги так, чтобы она закрывала половину поверхности образца. Смачиваемая бумага является источником питания и влаги. Затем на каждый образец устанавливают по два стеклянных садка и прижимают их к образцу пружинами или резиновыми кольцами. В каждый садок помещают по 50 термитов. Для наблюдения за жизнеспособностью термитов готовят контрольные садки. Садки с образцами и контрольные садки вводят в термостаты. Три раза в неделю визуально учитывают степень повреждения термитами образцов (отверстия, царапины, разрыхление и т.д.) и заменяют погибших термитов равным числом жизнеспособных. Продолжительность испытания составляет 30 сут.
Испытание изделий и материалов на устойчивость к воздействию грызунов. Для проведения испытания используют взрослых особей грызунов, которых заранее дрессируют, чтобы приучить доставать пищу, преодолевая преграду — картон толщиной 2...3 мм. Клетки для проведения испытания изготовляют из каркаса и сетчатых металлических стенок с размером ячейки не более 5...8 мм. В середине клетки имеется перегородка с отверстиями 70X70 мм, которое закрывают преградой—испытываемыми образцами. Продолжительность испытания 24 ч. По окончании испытания образцы осматривают, отмечают характер и размеры повреждений. Образцы считают выдержавшими испытание, если они не повреждены (0 баллов) или на их поверхности имеются следы зубов грызунов в виде неглубоких царапин (1 балл).
Билет 19
1. Общие принципы обработки результатов испытаний и принятия решений по ним
Для последующего анализа и подготовки заключения по результатам испытаний ЭС проводят статистическую обработку измеренных значений параметров — критериев годности. Достоверность полученных результатов определяется погрешностью измерения каждого параметра, объемом исходных статистических данных и качеством их обработки. Для математической обработки наблюдений применяют методы теории вероятности и математической статистики. Существует специфика в обработке данных, полученных при выборочном и сплошном (100%-ном) контроле параметров ЭС.
Выборочный метод является основным, но не единственным при контроле готовой продукции. В условиях опытного и серийного производства ЭС подвергают и сплошному контролю. На первый взгляд может показаться, что проблема риска поставщика и риска заказчика, связанная с выборочным методом контроля, при 100 %-ном контроле готовой продукции отсутствует. Однако это не так. Риск и поставщика и заказчика остается и при 100 % контроле, хотя оба имеют иной смысл, чем при выборочном контроле, поскольку обусловлены существенными погрешностями намерений контролируемых параметров.
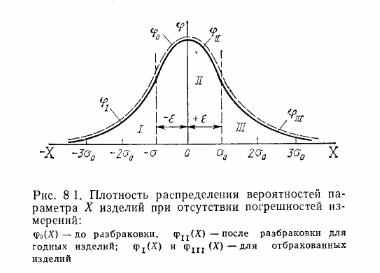
На рис. 8.1 показана плотность распределения вероятностей параметра Х изделий до и после их разбраковки при пренебрежимо малых погрешностях измерений. Процесс контроля и измерения в этом случае сводится к разделению площади, ограниченной исходной (в данном случае гауссовская) плотностью распределения вероятностей ф(Х) параметра X и осью абсцисс, на три области. При этом в область 2 входят изделия, значения параметра которых находятся в пределах заданного поля допуска ±е: в области 1 и 3 — изделия со значениями параметра, выходящими да левую и правую границы поля допуска соответственно.
Иначе проводят контроль при наличии существенной погрешности измерении ПКГ. В этом случае, хотя изделия при разбраковке также разбивают на области 1-3, распределение значений параметра в каждой из них, установленное по результатам измерений, не будет совпадать с распределением истинных значении этого параметра. Если отклонение значений параметра от границ ноля допуска (±в) превышает ошибку У измерения, можно считать, что отбраковка выполнена правильно. Если же это отклонение меньше ошибки измерения, отбраковка выполнена неверно, т. е. изделие является фактически годным. При существенных погрешностях измерении определенная часть годных изделий попадает в забракованные (риск поставщика), тогда как часть негодных изделий принимается (риск заказчика).
На рис. 8 2 представлена плотность распределения вероятностей ПКГ после разбраковки при наличии существенных погрешностей измерений
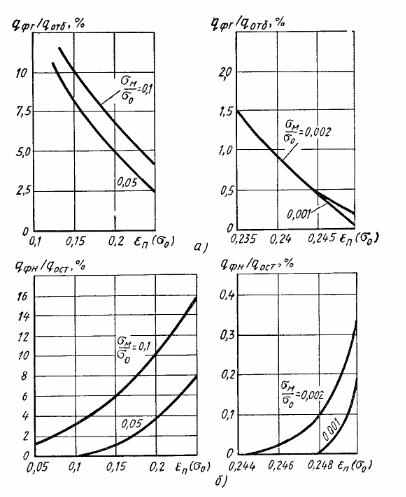
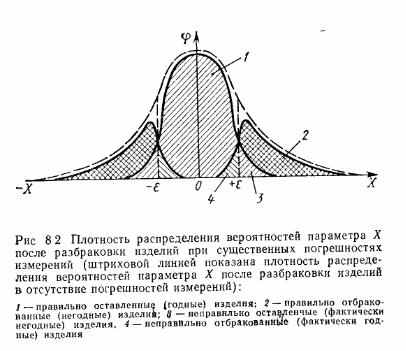
На рис.8.3 построены зависимости рисков поставщика и заказчика (Qфг/Qотб) от производственного допуска Е при заданном гарантированном допуске Ег и различной точности измерении ПКГ изделий.
Под гарантированным полем допуска +/- Ег понимают допуск, превышение которого не гарантирует работоспособности изделия в период его эксплуатации. Под производственным полем допуска +/-Еп понимают допуск, которым руководствуется поставщик в процессе производства изделий. Очевидно, что Еп<=Eг/
С помощью графиков, представленных на рис. 8.3, можно решить ряд практических задач, например:
- при заданном гарантированном допуске на ПКГ изделия и с учетом конкретного значения точности измерительных средств определить риски поставщика и заказчика;
- при запланированном риске поставщика или заказчика и заданном гарантированном допуске определить точность измерительных средств и необходимый производственный допуск;
- при запланированных рисках поставщика и заказчика и заданных гарантированном и производственном допусках определить необходимую точность измерительных средств.
2. Испытания на воздействие радиации
Радиационное испытание ЭС. Испытание проводят с целью проверки работоспособности и сохранения внешнего вида ЭС в соответствии с НТД (требования ТЗ и ТУ) во время и после воздействия радиации. Испытание проводят в электрических режимах, оговоренных в стандартах и программах испытаний, по специально разработанной методике, которая составляется на каждый вид радиоактивного излучения. При выборе контролируемых параметров необходимо исходить из требования получения максимального объема информации и из технологических возможностей методов измерения параметров ЭС в условиях облучения.
Испытательный комплекс, схема одного из возможных вариантов которого приведена на рис. 6.17, должен обеспечивать одновременное испытание выбранного числа образцов, дистанционное измерение и регистрацию контролируемых параметров. Состав блоков комплекса и их функции определяются видом испытаний, типом моделирующего источника радиоактивного излучения и характеристиками контролируемого параметра.
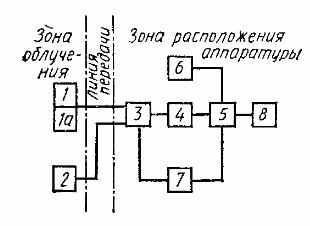
Рис. 6 17. Структурная схема
испытательного комплекса-
1 — испытываемые изделия; 1а — дозиметры и датчики температуры; 2 — блок датчиков; 3 — блок коммутации и согласования; 4 — регистрирующая аппаратура; 5 — командный блок, 6 — вспомогательная аппаратура; 7 —блок измерений, 8 — блок питания
// Блок датчиков содержит датчик формы импульса гамма-излучения и датчик импульса запуска регистрирующей аппаратуры (электронных осциллографов). Этот блок необходим только при импульсных источниках излучения. В качестве датчика формы импульса служит фотоэлектронный умножитель с фотолюминесцентным кристаллом. Датчик импульса запуска электронных осциллографов вместе с блоком согласования обеспечивают запуск разверток с опережением сигнала реакции ЭС на излучение, что необходимо для качественной записи импульса реакции и его фронта. Опережение определяется временем срабатывания схемы развертки осциллографа и длительностью фронта импульса воздействующего излучения
Блок коммутации и согласования обеспечивает переключение каналов регистрации параметров ЭС на одно регистрирующее устройство при проведении испытания на статическом ядерном реакторе и временное согласование сигналов от испытываемых изделий и сигналов на запуск регистрирующей аппаратуры при испытании на импульсной моделирующей установке. Командный блок предназначен для программного автоматического или ручного управления работой аппаратуры и1мерительного комплекса. Вспомогательная аппаратура служит для градуировки осциллографов и проверки измерительных трактов.
Измерение температуры окружающей среды или корпусов изделий следует проводить в случае ожидаемого нарушения температурного режима изделий за счет радиационного разогрева или повышенной температуры в доне облучения Датчики и блок измерении температуры обеспечивают одновременное измерение и регистрацию ее в заданном диапазоне. Они должны быть нечувствительны или мало чувствительны к воздействию проникающих излучений Обычно для этих целей используют термопары.
3. Испытания на повышенное гидравлическое давление
Цель испытания на воздействие повышенного гидростатического давления — определение работоспособности ЭС в условиях нахождения их под водой. Это испытание часто проводят в сочетании с испытанием на герметичность с целью проверки способности корпусов ЭС или их отдельных блоков и частей не допускать проникновения воздуха или воды в изделия. Оба вида испытания осуществляют, погружая изделия и резервуар с водой.
Испытание на воздействие повышенного гидростатического давления проводят в такой последовательности. Сначала в течение 15 мин ЭС выдерживают под водой при давлении, в 1,5 раза превышающем давление предельной глубины погружения. Затем давление снижают до нормального и повышают до значения, соответствующего предельной глубине погружения. В этих условиях ЭС выдерживают в течение 24 ч. По окончании испытания давление снижают до нормального и, не извлекая ЭС из воды, оценивают их качество по соответствию измеряемых выходных параметров значениям, заданным в ТУ и ПИ.
Испытание на герметичность в зависимости от требований, предъявляемых к ЭС, реализуют одним из следующих методов :
1) по утечке жидкости — для изделий, наполненных жидкостью или содержащих наполнитель, находящийся в твердом состоянии при нормальных климатических условиях и превращающийся в жидкость при температуре испытания;
2) по утечке газа с применением индикаторного газа и масс-спектрометра — для изделий, имеющих свободный внутренний объем и не обладающих повышенной адсорбцией, но способных выдерживать без остаточных деформации повышенное и пониженное давление относительно нормального атмосферного;
3) по проникновению газа или жидкости — для изделий, проникновение агрессивной среды в которые приводят к изменению их параметров;
4) по обнаружению утечки газа путем наблюдения его пузырьков при помещении ЭС в жидкость — для изделий, содержащих внутри некоторый объем газа и способных выдерживать без остаточных деформаций понижение и повышение давления;
5) по обнаружению утечки воздуха, подаваемого на изделия под давлением;
6) по проникновению влаги («влажный» метод) — для изделий, электрические характеристики которых изменяются от проникновения в корпус жидкости.
Для проведения испытания указанными методами используют камеры тепла, цветовые индикаторы, гелиевые камеры, масс-спектрометры, барокамеры, жидкостные ванны, контрольно-измерительную аппаратуру, устройства подачи сжатого воздуха.
При испытании ЭС по четвертому методу, одному и наиболее распространенных, в корпуса изделии через штуцера нагнетают воздух до избыточного давления .После этого изделия погружает не менее чем на 5 мин в резервуар с водой, имеющей температуру 25+/-10 градусов С. Изделия считают выдержавшими испытание, если во время нахождения их в воде под избыточным давлением не наблюдается выделения пузырьков воздуха из корпусов ЭС.
Количественную характеристику герметичности определяют одним из двух способов. При первом способе ЭС помешают в испытательную камеру под колпаком. Внутреннюю полость испытываемого образца соединяют с коленом жидкостного манометра. Для этого в испытываемых ЭС должна быть предусмотрена возможность установки штуцера, который по окончании испытания заменяют заглушкой. Другое колено манометра соединяют с окружающей атмосферой. Для повышения чувствительности манометра его заполняют маслом вместо ртути. В камере создают избыточное давление воздуха или разрежение (в зависимости от условий эксплуатация ЭС), что обеспечивает перепад давлений между внутренней полостью испытываемого образца и объемом камеры не менее 3*104 Па. Негерметичность натекания определяют по разности уровней жидкости в манометре через 15 мин после установлении заданного перепада давлений.