Технология машиностроения
Вид материала | Документы |
- Экзаменационные вопросы по предмету «Технология машиностроения», 36.61kb.
- «Технология машиностроения» Специализация «Дизелестроение», 37.35kb.
- Рабочая программа и методические указания к выполнению контрольной работы для заочной, 305.14kb.
- Программа преддипломной практики студентов специальности 1-36 01 01 «Технология машиностроения», 336.91kb.
- Программа и контрольные задания для учащихся-заочников по специальности 2-36, 764.27kb.
- Кафедра «Технология машиностроения», 27.73kb.
- Методические указания по выполнению лабораторных работ по курсу «Системы автоматизированного, 369.98kb.
- Рабочая программа учебной дисциплины по дисциплине «Детали машин и основы конструирования», 251.9kb.
- Программа вступительных испытаний (междисциплинарного экзамена) для поступающих в магистратуру, 97.78kb.
- Рабочая программа по дисциплине: опд. В. 01 Экономика машиностроения образовательной, 426.43kb.
1 2
Расчет и конструирование технологической оснастки
Наиболее ответственной, сложной и трудоемкой в изготовлении частью технологической оснастки является приспособление.
Неправильные технологические и конструктивные решения при проектировании приспособлений приводят к удлинению сроков подготовки производства, к снижению эффективности и качества технологических процессов. Это обстоятельство требует выделить в самостоятельный раздел курсового проектирования расчет и конструирование приспособления.
В зависимости от направленности курсового проекта в нем могут проектироваться: станочные приспособления, приспособления для закрепления рабочего инструмента, сборочные приспособления, контрольные приспособления, приспособления для захвата, перемещения и изменения положения обрабатываемых деталей.
Расчет приспособления включает решение двух основных задач: обеспечение требуемой точности координирования обрабатываемой заготовки относительно баз станка и обоснование конструктивных параметров приспособления. Известно, что при изготовлении партии деталей на них получается погрешность
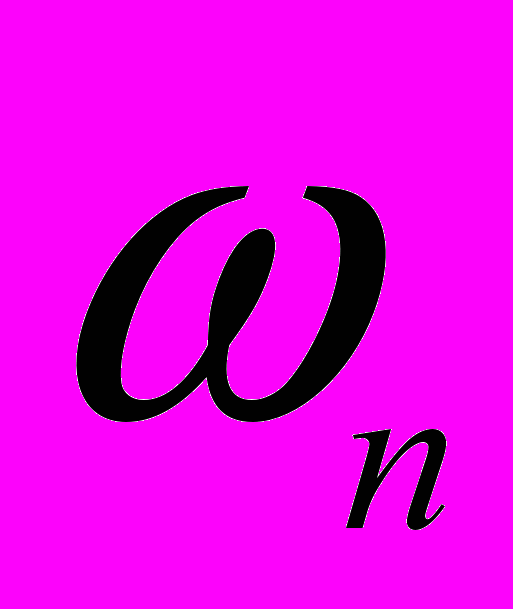
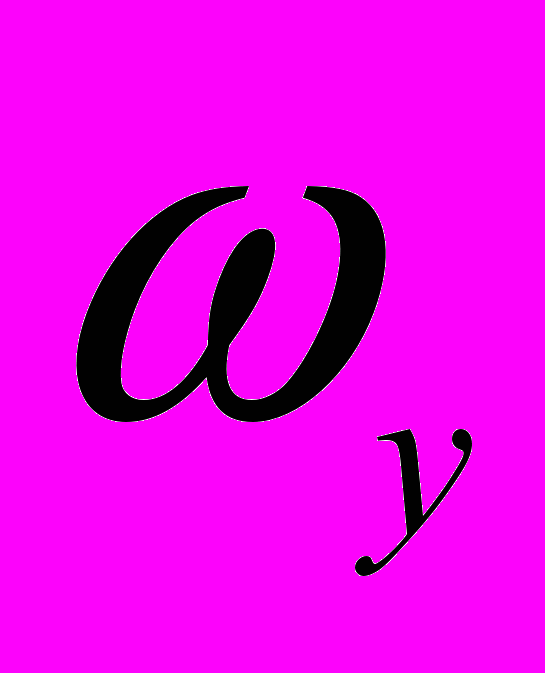
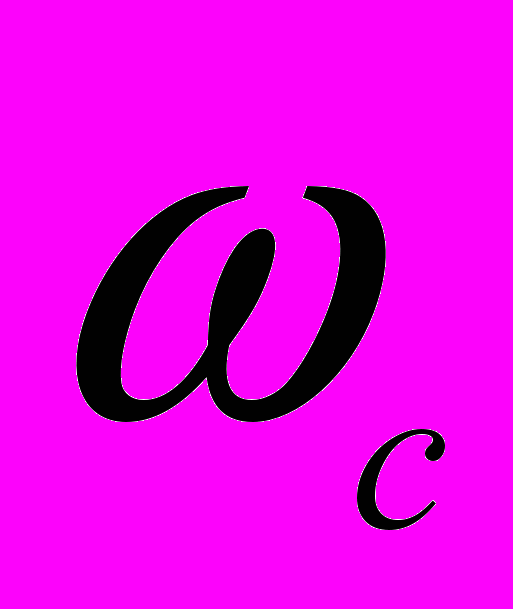
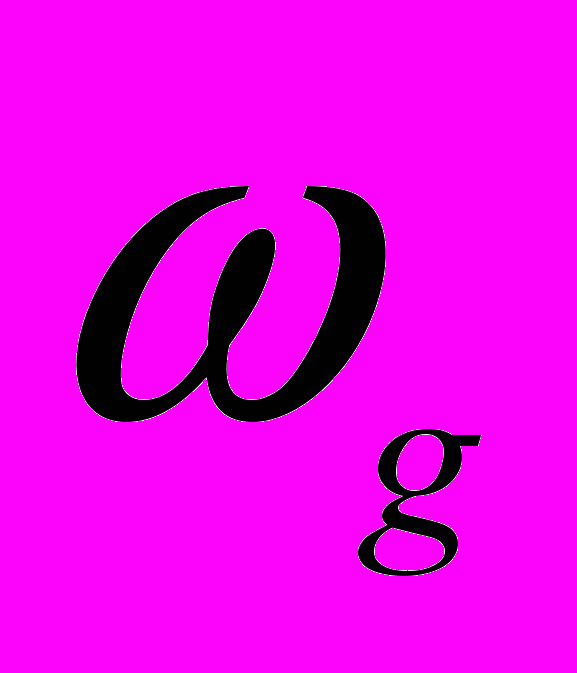
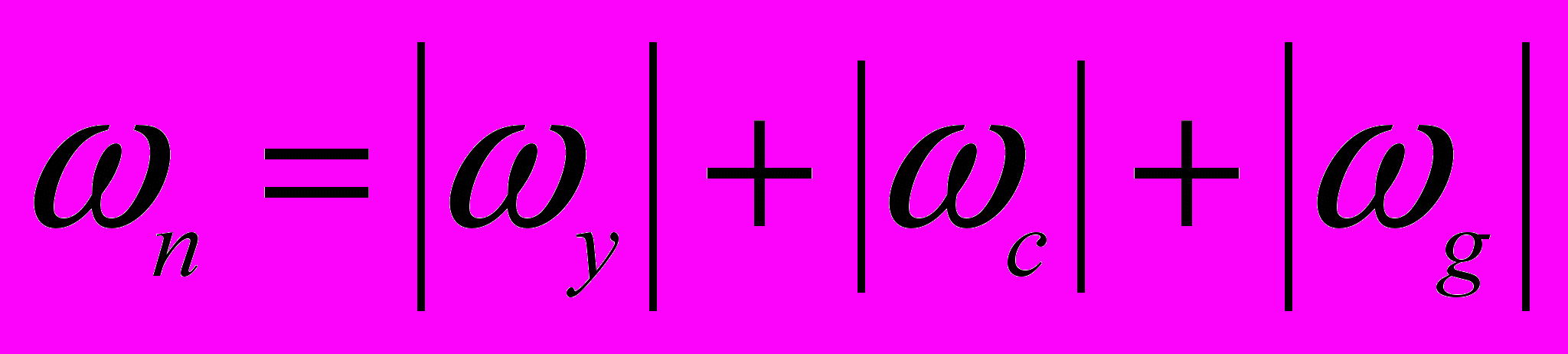
Поскольку приспособления включаются в размерные и кинематические цепи системы СПИД, аналогично можно представить и структуру погрешности положения заготовки в приспособлении
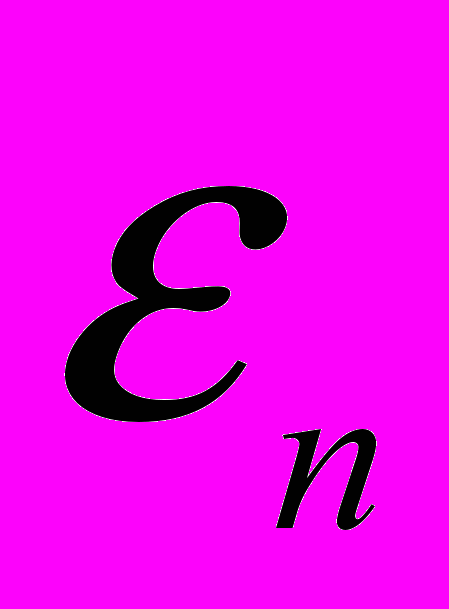
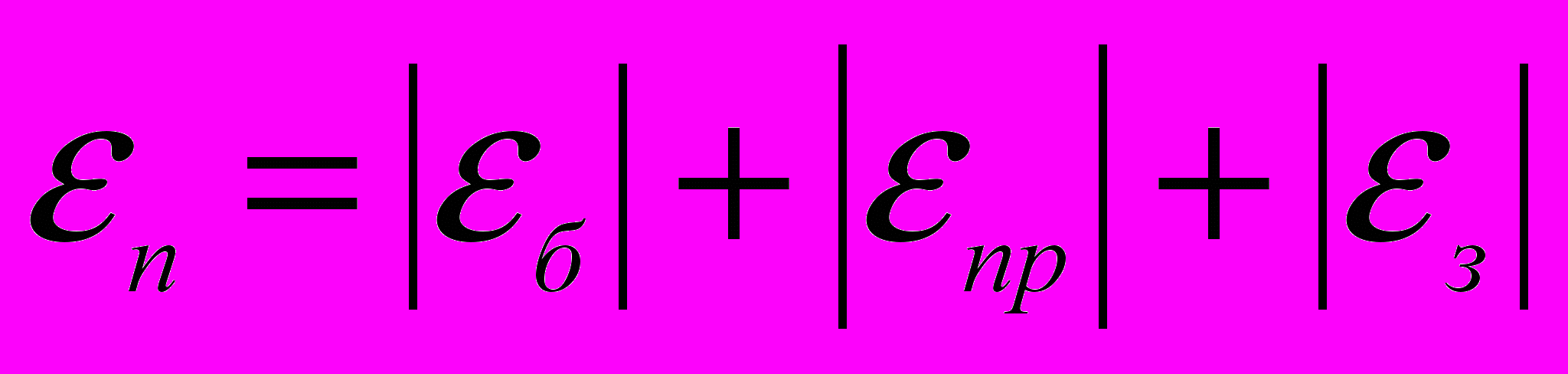
где
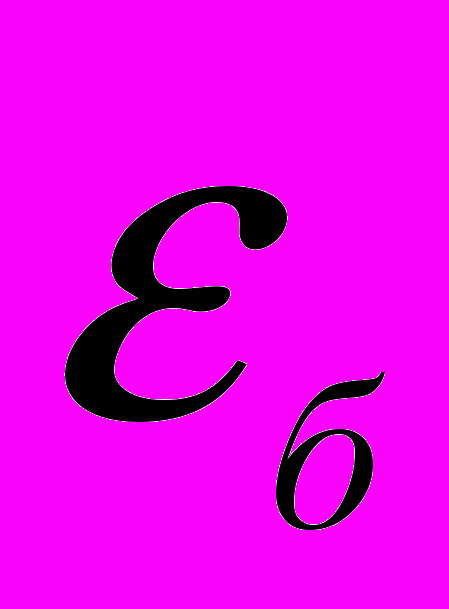
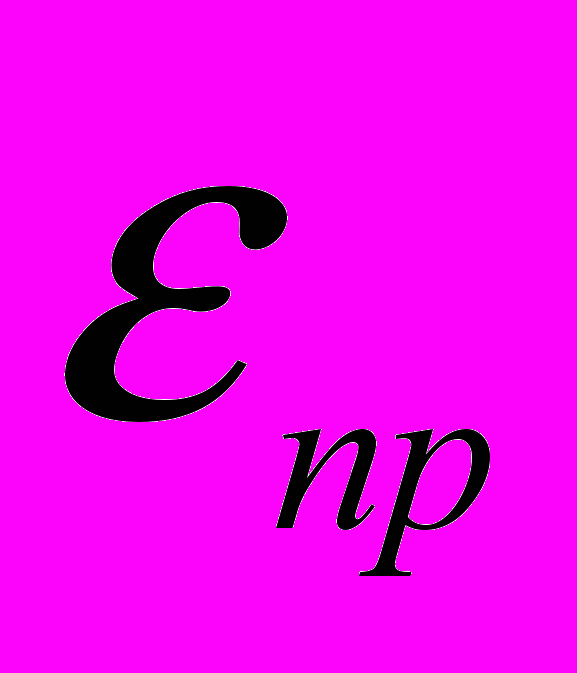
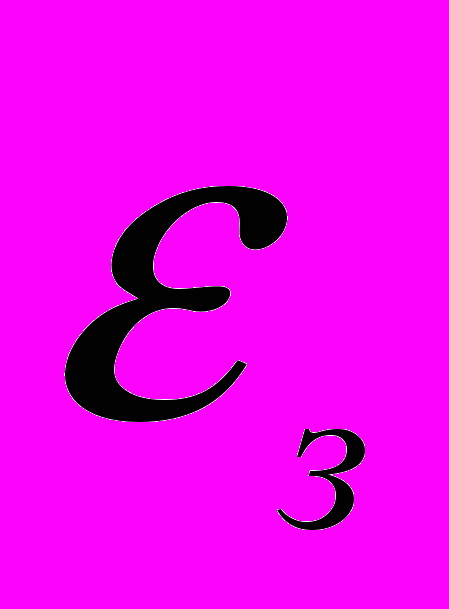
Тогда задача точностного расчета приспособления сводится к определению допустимых значений смещений и поворотов заготовок и последующему установлению допусков на составляющие каждой из погрешностей положения заготовки
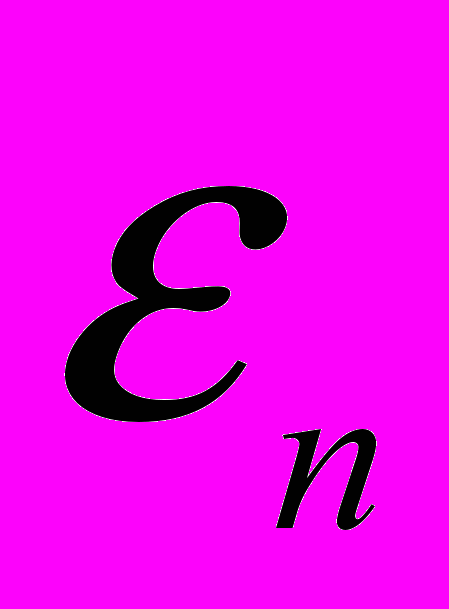
При конструировании необходимо выбрать такую схему базирования заготовки, величину и схему приложения сил зажима, установить такие допуски на составляющие звенья размерных цепей приспособления, при которых составляющие погрешности
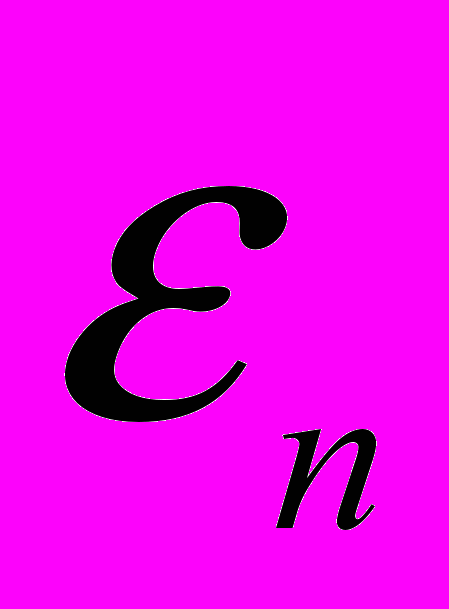
Схема расчета приспособления на точность координирования заготовки представлена на рисунке 1.
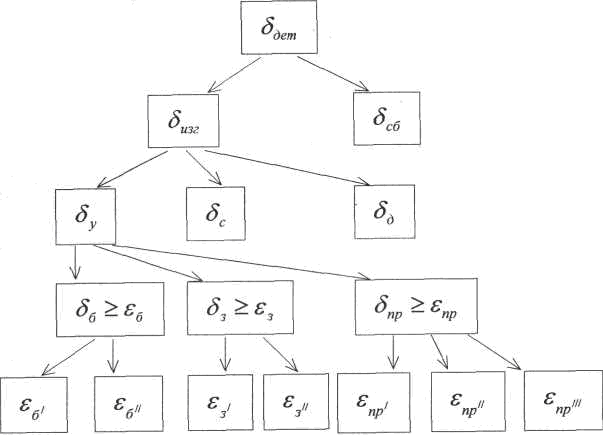
Рисунок 1. Схема расчета приспособления
на точность координирования заготовки
Исходным для расчета является допуск
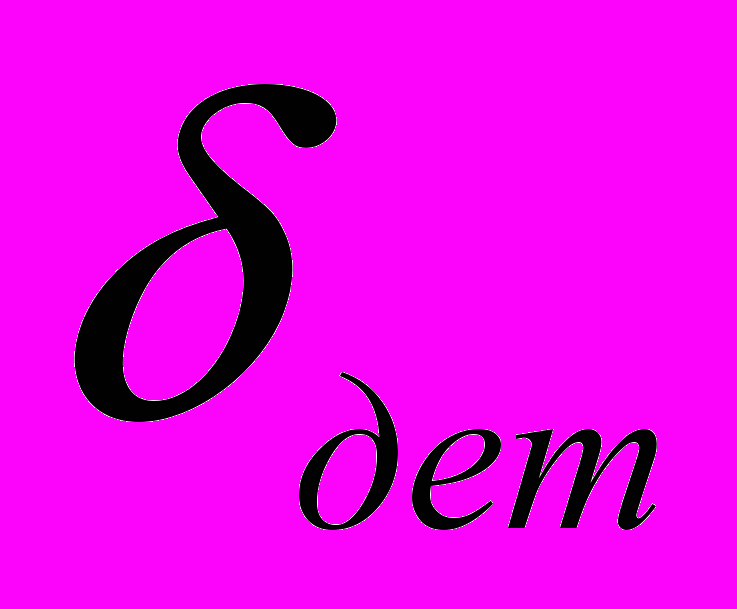
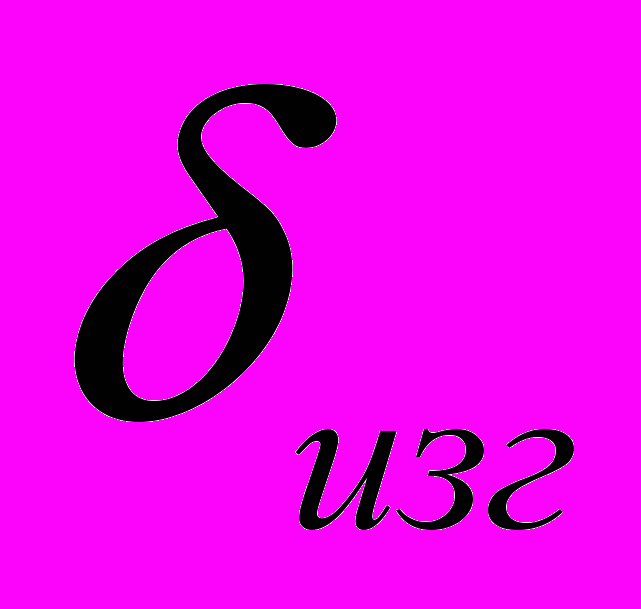

В свою очередь допуск на изготовление приходятся делить на три неравные части
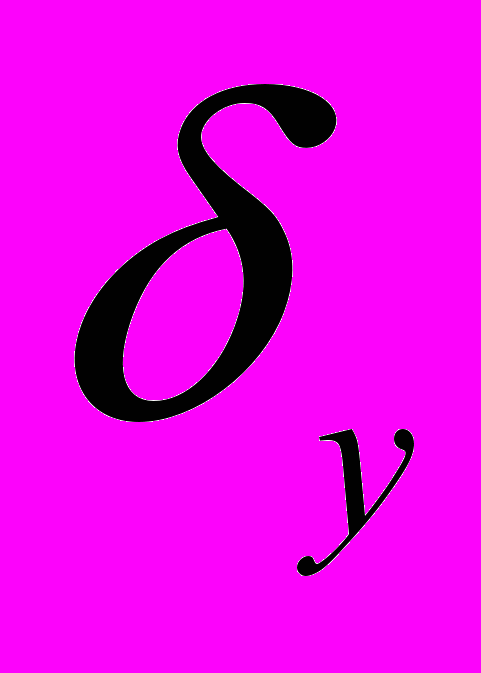
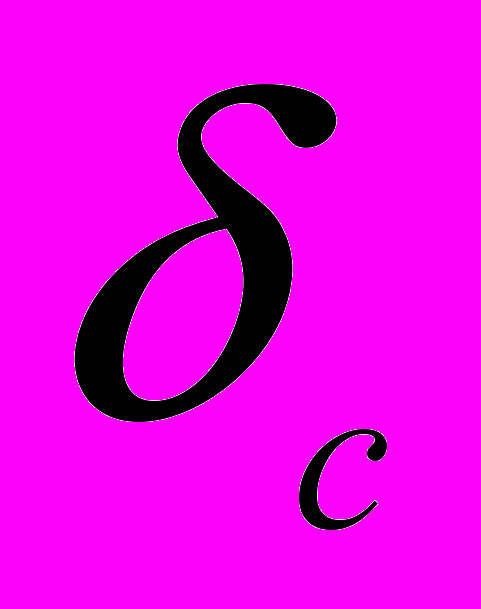
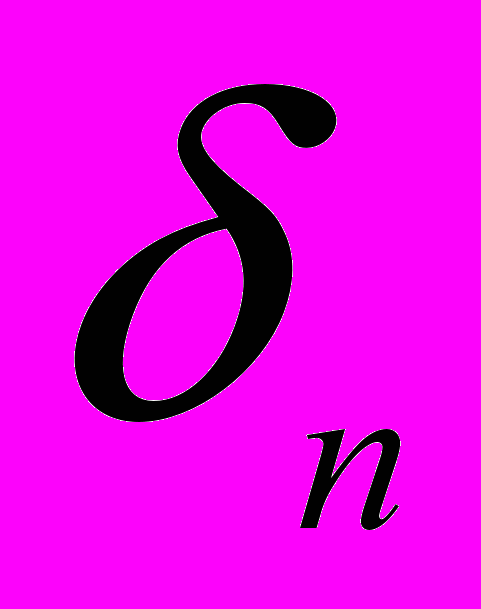
Принимая экономично достижимое и данных производственных условиях значение
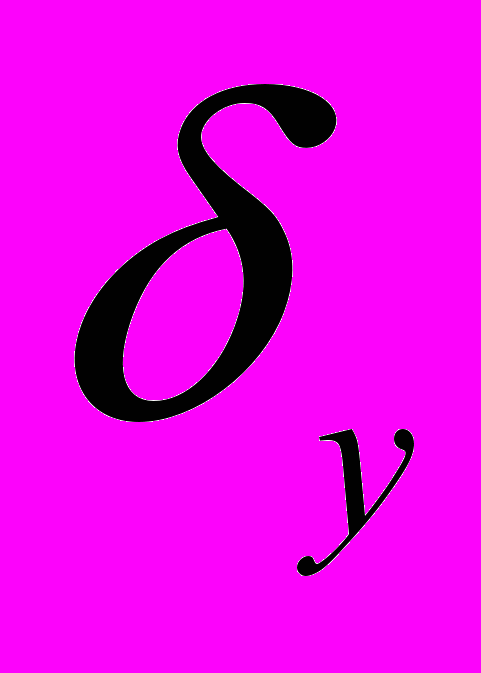
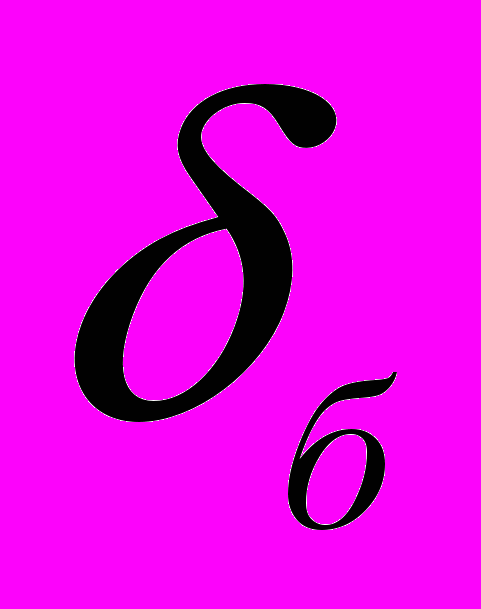
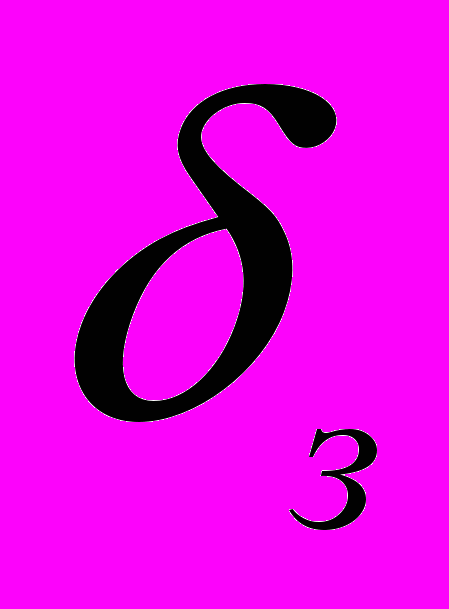
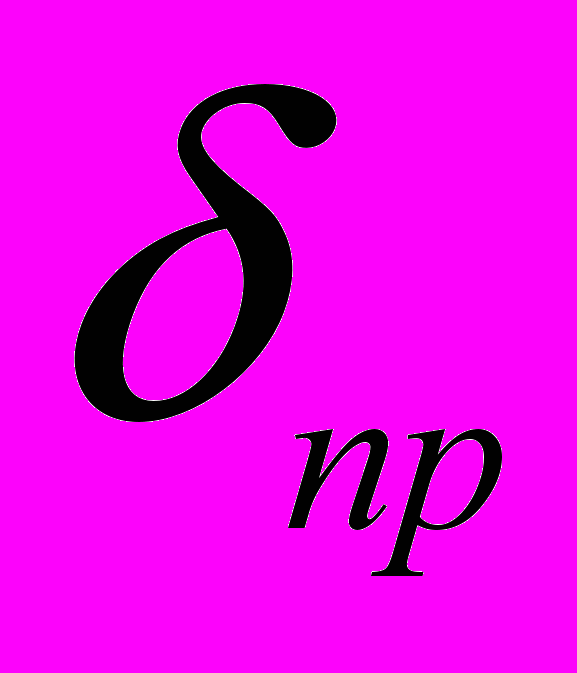
Далее определяют погрешности
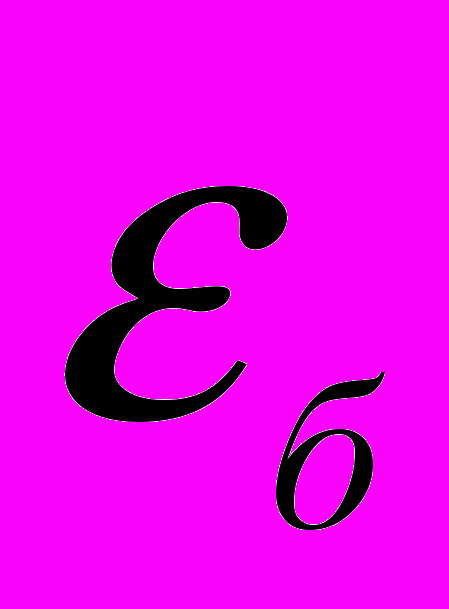
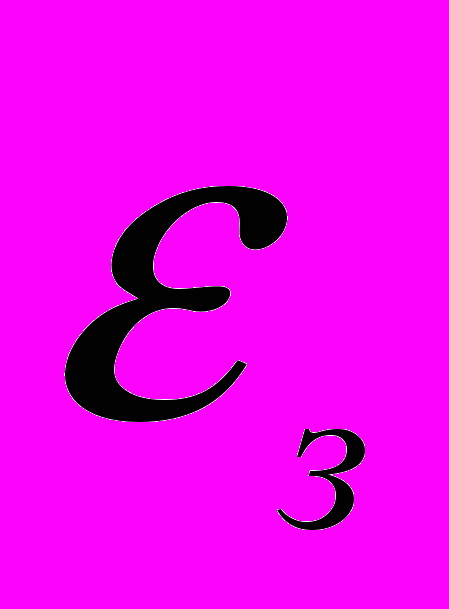
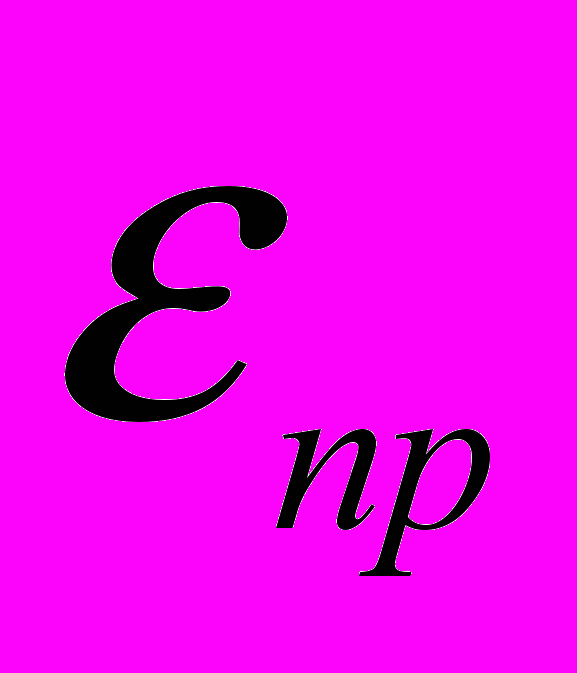
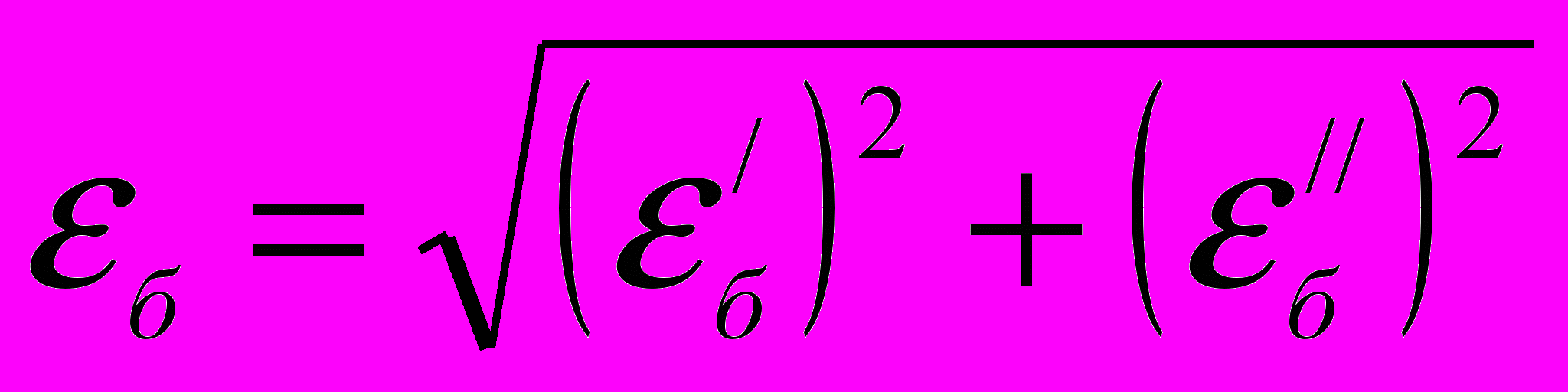
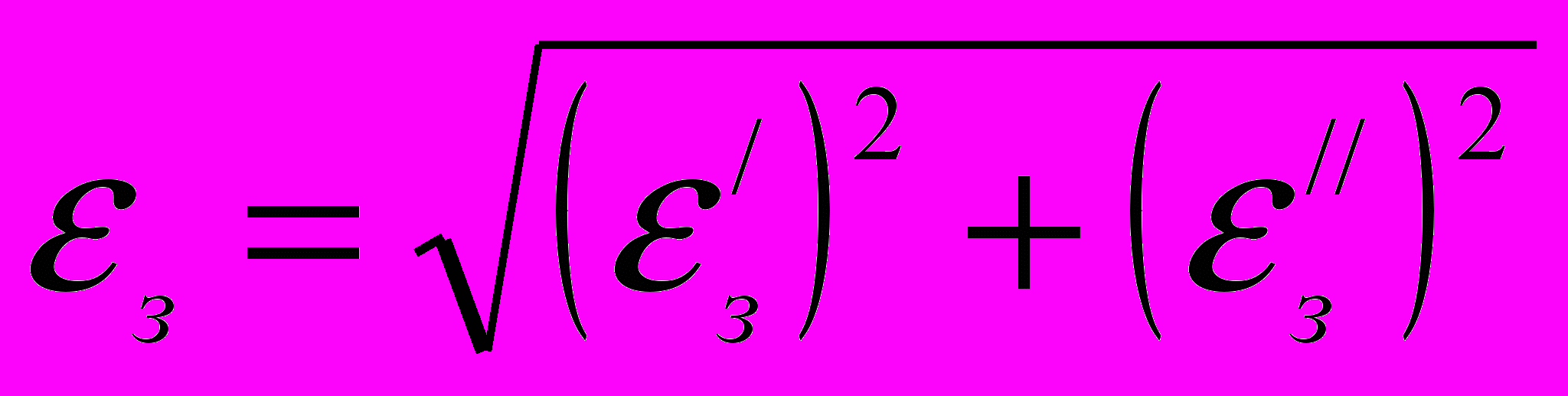

где
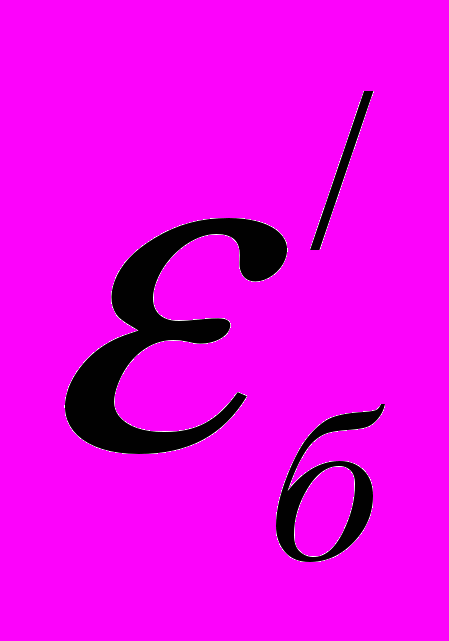
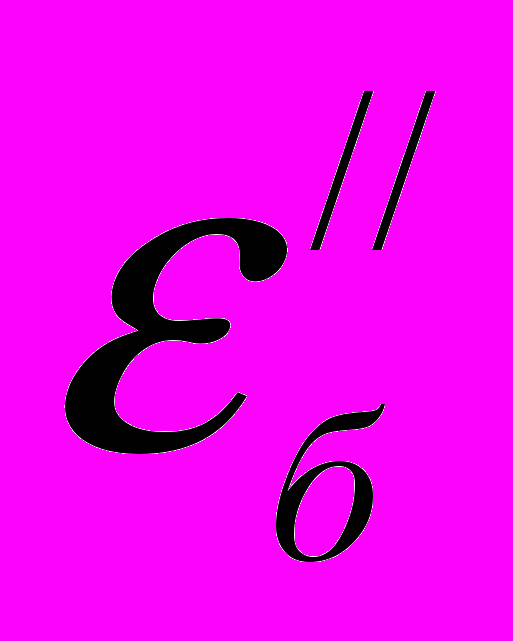
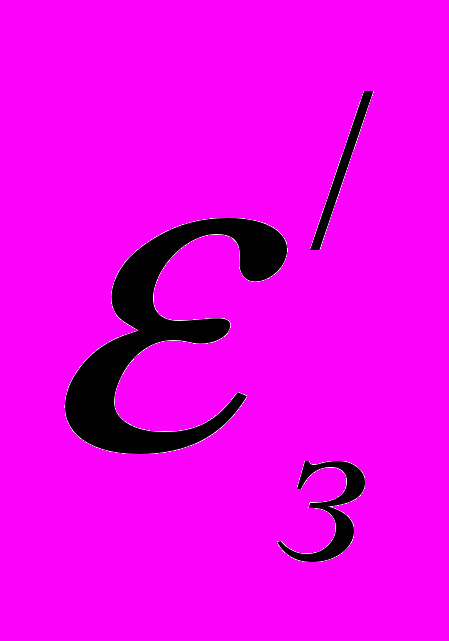
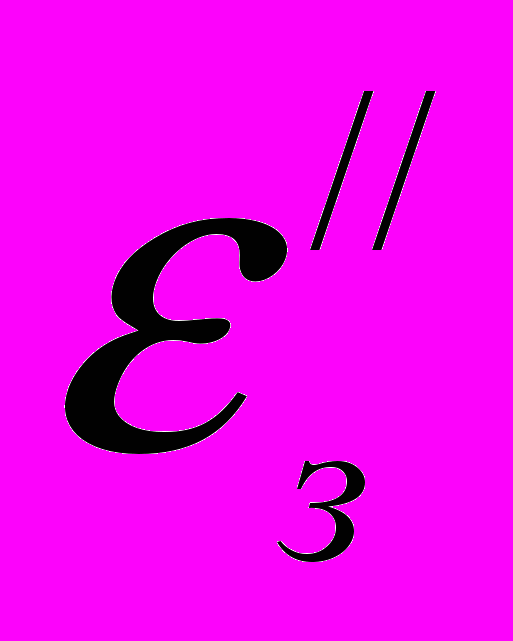
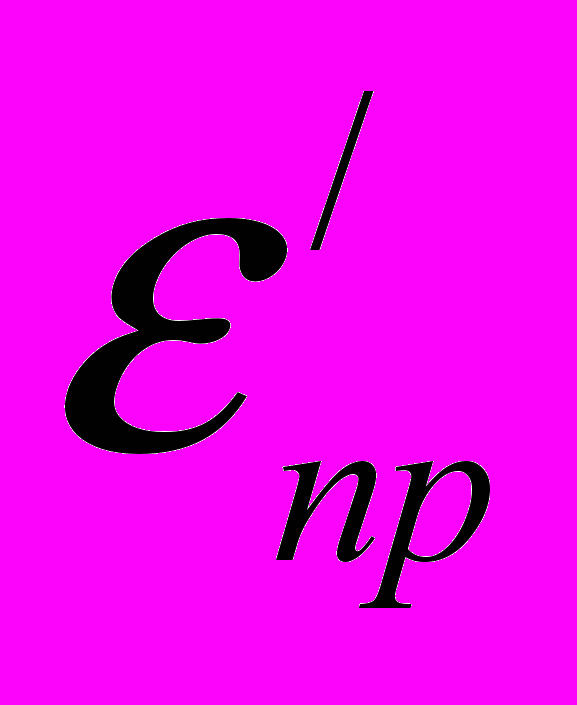
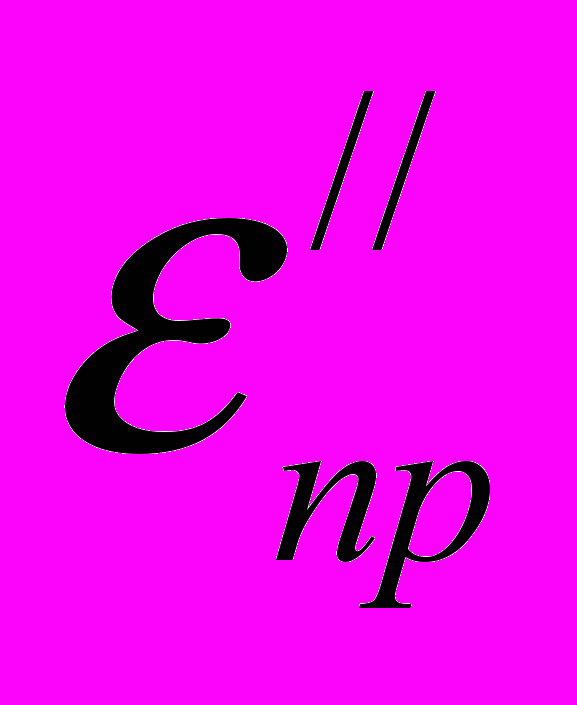
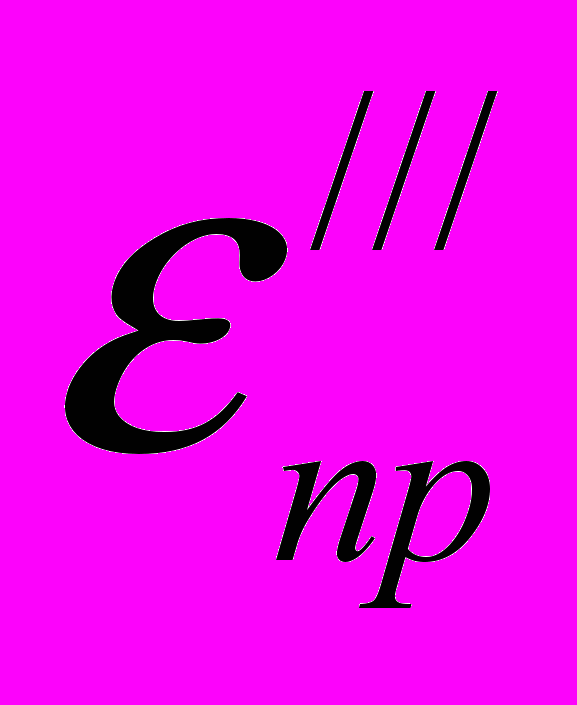
Практика показывает, что наиболее значительными по величине являются погрешности базирования и закрепления, однако в каждом конкретном случае удельное влияние той или иной соответствующей погрешности может меняться от 0 до max. Это обстоятельство следует учитывать при выборе конструктивно-технологических решений приспособлений.
Методика определения погрешности базирования
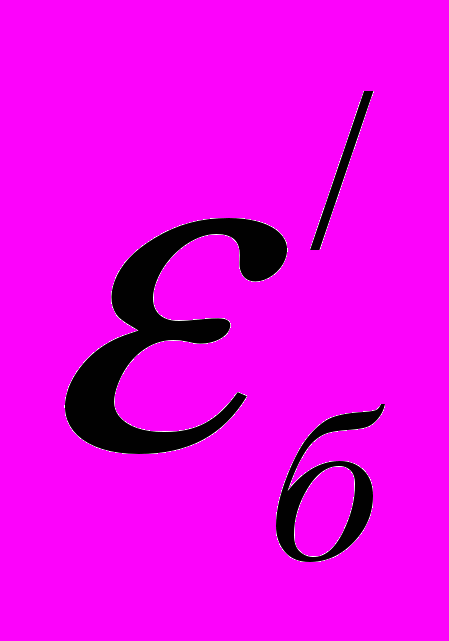
Обоснование конструктивных параметров приспособления включает кинематический и силовой расчет.
Целью кинематического расчета является определение размеров звеньев и передаточных отношений механизмов приспособления, обеспечивающих перемещение исполнительных поверхностей по определенному закону в заданное время.
Силовой расчет позволяет установить конструктивные параметры исполнительных, передаточных и приводных механизмов для обеспечения требуемого усилия зажима.
Силовой расчет приспособления следует выполнять в определенной последовательности:
- на эскиз заготовки наносят все действующие в процессе обработки силы (силы резания, силы зажима, реакции опор и силы трения, силы инерции и др.), направление действия и величины сил принимаются для наиболее неблагоприятного случая;
- для возможного упрощения расчетной схемы производят количественный анализ действующих сил, в дальнейшем рассматривают только значимые силы;
- составляют уравнения равновесия заготовки под действием приложенных сил, поскольку при обработке относительное перемещение заготовки и приспособления не допустимы;
- решают уравнения равновесия относительно сил зажима;
- определяют коэффициент запаса применительно к данным условиям обработки и требуемое усилие на выходном звене передаточного механизма приспособления;
- производят силовой расчет передаточного механизма и определяют усилие, потребное на выходном звене привода;
- рассчитывают конструктивные параметры привода приспособления (диаметр цилиндра, размеры диафрагмы, жесткость пружин и т. д.);
- расчетные величины параметров округляют до рекомендуемых ГОСТами и отраслевыми нормалями.
При конструировании приспособления необходимо придерживаться следующего порядка:
- устанавливают размеры зоны обработки и других связывающих размеров, зависящих от станка (размеры стола и шпинделя станка, длина рабочего и холостого хода, расстояние между центрами и высота центров и т. д.);
- уточняют конструкции установочных элементов приспособления, приводов, вспомогательных элементов;
- вычерчивают контур детали в рабочем положении в необходимом количестве проекций (предпочтительно в масштабе 1:1);.
- вычерчивают по контуру детали, установочные элементы, направляющие детали (кондукторные втулки, габариты и т. п.);
- вычерчивают передаточные и приводные механизмы приспособления;
- определяют и вычерчивают контур корпуса приспособления, используя стандартные заготовки корпусов;
- вычерчивают необходимое количество проекций, разрезов и сечений приспособления;
- проставляют координатные, посадочные и другие основные размеры с допусками, которые обоснованы расчетом на точность, указывают необходимые технические требования на сборку приспособления;
- составляют спецификацию на приспособление.
Технико-экономический анализ вариантов
технологического процесса
При проектировании может быть разработано несколько равнозначных с точки зрения достижения требуемого качества детали, вариантов технологических процессов. Из них путем расчетов должен быть выбран вариант, обеспечивающий лучшие экономические показатели. Без технико-экономического анализа и сравнения показателей вновь разработанного процесса и процесса уже реализованного на промышленном предприятии работа над курсовым проектом не может считаться завершенной.
Экономическая эффективность нового мероприятия определяется сопоставлением трат, т.е. суммы себестоимости годового изделий и капитальных затрат

где
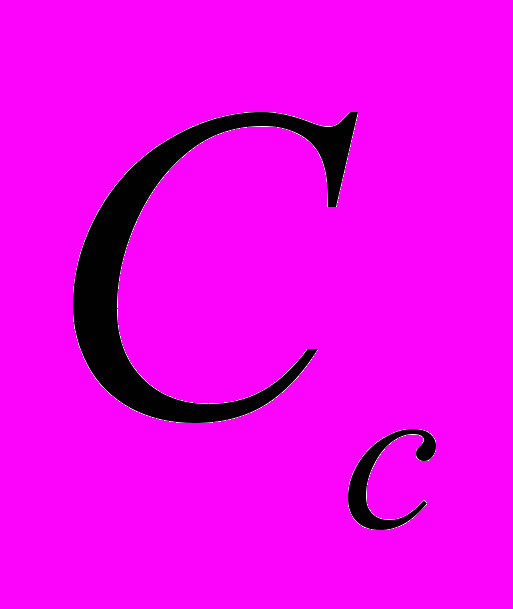
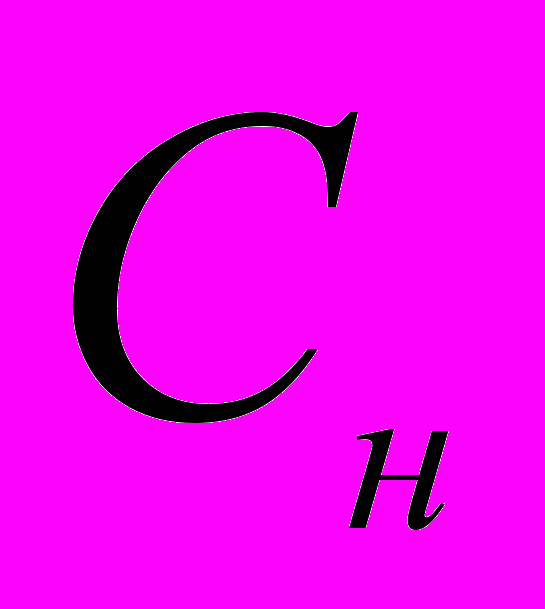
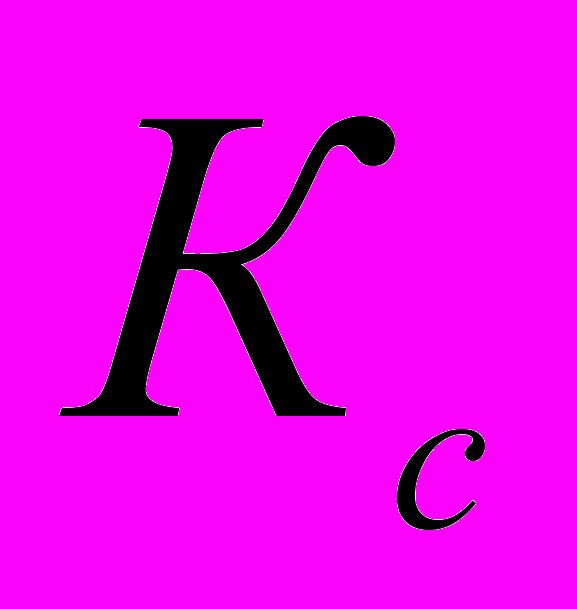
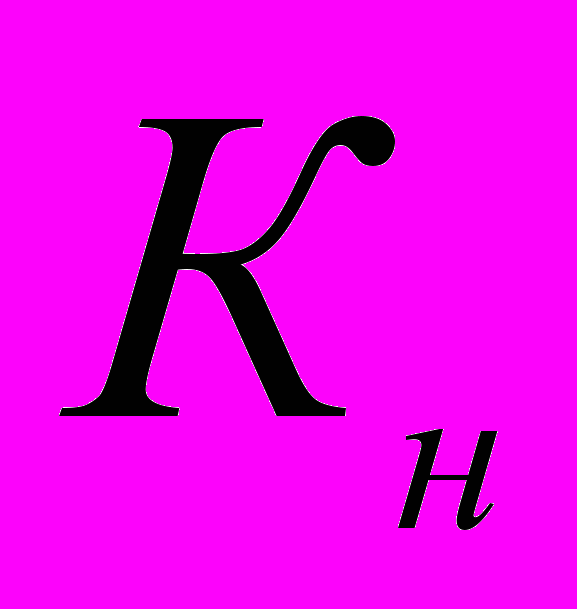
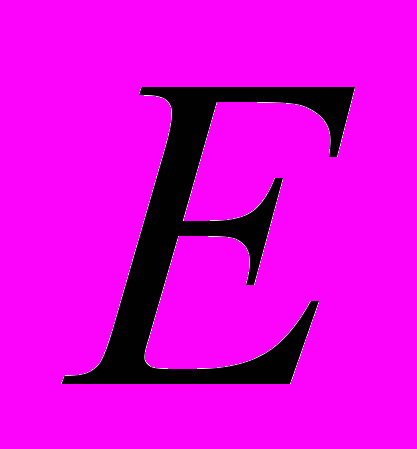
Годовая экономическая эффективность

В себестоимость включаются расходы на заработную плату рабочему и наладчику, расходы па материалы, содержанию и амортизацию оборудования, приспособлений и инструмента, расходы па энергию.
В капитальные затраты включаются расходы на оборудование, приспособления и комплект инструментов, настройку оборудования. Если обозначить первую группу расходов через b, вторую через т и количество изделий через m, то себестоимость изготовления х изделий выразится формулой
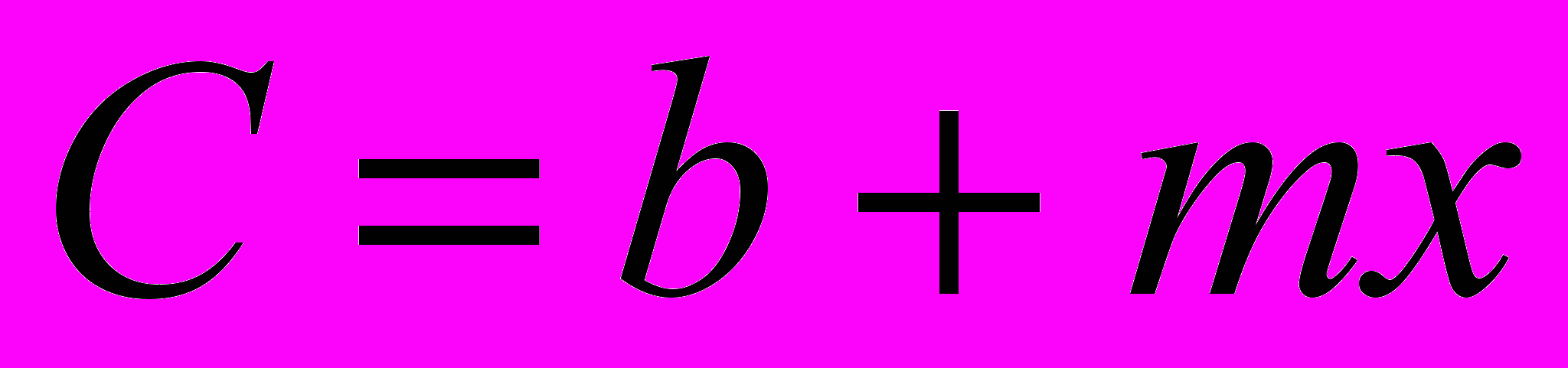
Вычерчивание графиков себестоимости обработки деталей по каждому вновь разработанному технологическому процессу, связанному с возможностью использования новых видов заготовок, изменения структуры и режимов выполнения технологического процесса, использования новых видов оборудования, приспособлений, инструмента и т.д., позволяет установить область экономичного использования этого процесса и определить его эффективность.
В работе [9] в достаточной мере освещена методика технико-экономического анализа вариантов технологического процесса.
Правила оформления пояснительной записки
Общими требованиями к пояснительной записке являются:
- четкость построения;
- логическая последовательность изложения материала;
- убедительность аргументации;
- краткость и точность формулировок, исключающих возможность субъективного и неоднозначного толкования;
- конкретность изложения результатов расчета;
- доказательность выводов и обоснованность рекомендаций.
Пояснительная записка должна включать:
- титульный лист;
- содержание (оглавление);
- перечень сокращений, символов и специальных терминов с их определениями;
- основную часть;
- список литературы;
- приложения.
Записка должна быть написано пли отпечатана на одной стороне листа белой бумаги формата А4 по ГОСТу 9327-89; 14 шрифт.
Поля должны оставляться по всем четырем сторонам листа. Размер левого поля - 35 мм, правого - не менее 10 мм, верхнего и нижнего - не менее 20 мм.
Нумерация страниц должна быть сквозной: первой страницей является титульный лист. Номер страницы ставят арабскими цифрами в правом нижнем углу. На титульном листе номер страницы не ставят.
Оформление таблиц, формул, схем списка литературы производится по ГОСТу 19600-74, ГОСТ 2.104-68.
В приложения входят спецификации, технологические карты, протоколы исследований и т.п. Примеры их оформления даны в руководстве.
6. Графическая часть проекта и
технологическая документация
К графической части проекта объемом 4 листов формата А1 по ГОСТу 2301-68 относятся:
1) чертеж детали, заданной для разработки технологического процесса;
2) чертеж заготовки;
3) операционные технологические эскизы механической обработки или, так называемая, графическая технология;
4) чертежи приспособления для механической обработки или контроля.
1. Чертеж детали следует вычерчивать только в том случае, если в конструкцию детали внесены студентом какие-либо изменения, и если чертёж не соответствовал требованиям ЕСКД. В противном случае к проекту достаточно приложить копию чертежа. Если размеры чертежа детали не более 0,5 листа, то его целесообразно подшить в расчетно-пояснительную записку после задания.
2. Чертеж заготовки выполняется с указанием всех технических требований, предъявляемых к ней.
Чертеж заготовки не вычерчивают, если деталь изготавливается непосредственно из проката (пруткового, трубного, листового, профильного). В этом случае профиль проката с учетом припуска на отрезку наносится на чертеж детали, с указанием всех размеров (с допусками). На чертеже заготовки наносят контур готовой детали. Размеры заготовки с допуском сопровождаются размерами детали (проставленными в скобках) с допусками.
В особых случаях по согласованию с руководителем проекта допускается совмещение чертежа заготовки с чертежом детали. При этом поверхность заготовки вычерчивается красным карандашом.
Припуск может быть заштрихован. На чертеже должны быть приведены технические требования отдельно па деталь и заготовку.
Примеры выполнения чертежей заготовок даны в приложении А.
3. Чертежи графической технологии выполняются на характерные наиболее сложные операции. При этом на первом переходе (позиции) изображается деталь, установочные и зажимные элементы приспособления, конструкция режущего инструмента. На последующих переходах вычерчивается только часть детали, примыкающая к обрабатываемой поверхности, и режущий инструмент. Если инструмент не повторяется на других позициях или переходах и метод его крепления оригинален, то он должен быть показан полностью с разрезом патрона или другого устройства для крепления. На чертеже указываются номера переходов, а также схема, объединяющая все позиции. Например, для токарных многошпиндельных станков - вид на шпиндельный блок с пронумерованными шпинделями, где стрелками показываются направления вращения деталей и направления вращения блока. Для токарно-револьверных станков с вертикальной осью револьверной головки - условная схема револьверной головки, например шестигранник, с обозначением номеров позиций и направлением периодического поворота головки. Для станков с горизонтальной осью револьверной головки -развертка головки с нумерацией каждого режущего инструмента. Для агрегатных станков - стол станка в виде окружности, разбитой на сектора, соответствующие каждой позиции и т.д.
Чертежи графической технологии должны быть выполнены с необходимым числом проекций, видов и разрезов; в них должны быть показаны устройства для установки режущих инструментов на выдерживаемые размеры и для ограничения их хода. На чертеже показываются конструктивные элементы приспособлений, обеспечивающих установку заготовки в требуемое положение.
Деталь на чертежах - схемах изображается черным цветом. Ее конфигурация должна соответствовать конфигурации, полученной в процессе обработки на данной операции пли переходе. Обработанные поверхности детали вычерчиваются черным карандашом, линией удвоенной толщины. Указываются операционные и настроечные размеры, их предельные отклонения, шероховатость.
Предпочтительный масштаб изображения 1:1. Для мелких деталей масштаб может быть увеличенным, а для крупных корпусных и других деталей уменьшенным (в отдельных случаях допускается произвольный масштаб).
Режущий инструмент, применяемый на данном переходе, вычерчивается в конечном положении. Показываются рабочие движения обрабатываемой детали и режущего инструмента, а также циклы движения суппортов.
Допускаются следующие варианты выполнения чертежей графической технологии:
1) при сложной операции - на одном и более листах формата А1;
2) при простых операциях - на листах формата А2. При этом графическая технология на каждую операцию выполняется как самостоятельный чертеж. Не допускаются разграничения переходов и позиций одной операции.
На листе вычерчивается и заполняется штамп с основной надписью по ГОСТу 2.104-68 и технологическая таблица, содержащая следующие столбцы: номер операции; номер позиции; номер перехода; наименование операций, позиций, переходов; оборудование; режимы резания (скорость круга, скорость детали, подача продольная, подача поперечная, глубина резания и др.). При числе характеристик режима резания свыше трех рекомендуется таблицу располагать не над штампом, а на свободном поле листа.
4. Общий вид приспособления должен содержать число проекций, разрезов и вырывов, достаточное для выполнения деталировочных чертежей и составления технологического процесса сборки всего приспособления. На чертеже проставляются габаритные, посадочные, присоединительные (диаметры и длины концов штоков, к которым присоединяются узлы, не показанные на чертеже) и другие размеры, вытекающие из служебного назначения приспособления. Обрабатываемая деталь, установленная в проектируемом приспособлении, вычерчивается прозрачной. Чертежи и технические требования к ним должны содержать все необходимые данные для комплектования деталей, сборки и контроля.
Технологическая документация
К технологической документации относятся:
1) маршрутная карта МК;
2) карта технологического КТП процесса;
3) карта эскизов КЭ.
Графы форм технологической документации заполняются в соответствии с положениями соответствующих стандартов. Так, в табл. 3 и 4 изложен порядок заполнения отдельных граф первых листов маршрутной карты.
Графы основной надписи технологических документов, в том числе и карты эскизов (приложение 4, лист 4), заполняют в соответствии с табл. 4 на примере операционной карты механической обработки (лист 5).
Таблица 3.
№ графы | Содержание графы |
| Маршрутная карта механической обработки (форма 2) |
7 | Количество деталей, изготовляемых из одной заготовки |
9 | Количество деталей, на которое установлена норма расхода материала (например, 1, 10, 100 шт и т.п.) |
10 | Норма расхода материала |
14 | Номер операции в технологической последовательности изготовления изделия (включая контроль и перемещения) |
15 | Наименование и содержание операции. Допускается в графе указывать технические требования |
18 | Наименование приспособлений, вспомогательного инструмента, режущего и измерительного |
Примечания.
1. В МК производится запись операций ковки, литья, штамповки, отрезки заготовок, термообработки и нанесения покрытий без расшифровки их содержания (операций), так как порядок их выполнения записывается в картах технологического процесса на эти виды работ.
2. К п. 14. Операции нумеровать трехзначными цифрами из ряда 005, 010, 015, 020, 025...105...
3. К п. 15. Перед наименованием операции, если на нее разрабатываются дополнительные технологические документы, указываются обозначения этих документов. Обозначения записываются в отдельную строку. Наименование операции записывается в виде заголовка с прописной буквы и подчеркивается. При наличии операционной карты или карты технологического процесса содержание операции не указывается. После изложения содержания операции, если за ней не следует контрольная операция, должны быть указаны параметры и объем контроля, выполняемого на рабочем месте.
Таблица 5.
№ графы | Содержание графы |
| А. Операционная карта механической обработки (форма 2) |
7 | Профиль и размеры заготовки на данной операции |
8 | Твердость заготовки, поступившей для обработки. Масса заготовки на данной операции |
14 | Номер перехода. Нумерацию переходов производить арабскими цифрами в технологической последовательности |
15 | Содержание перехода |
28 | Эскиз детали с размерами, получаемыми после выполнения операции |
| |
Продолжение таблицы 5. | |
29 | Наименование предприятия (организации) – разработчика технологических документов |
30 | Обозначение детали |
31 | Наименование типа обрабатываемых деталей (например, оси, шайбы, валы, втулки, шестерни и т. д.) |
32 | Обозначение технологического процесса маршрутной карты, карты технологического процесса по ГОСТу 3.1201-85 |
33 | Обозначение технологического документа по ГОСТу 3.1201-85 |
34 | Литера, присвоенная технологическому документу. Для типовых технологических процессов графу не заполняют |
35 | Фамилии лиц, подписавших документ |
36 | Подписи лиц, фамилии которых указаны в графе 35 |
37 | Дата подписания документа |
38 | Порядковый номер листа документа |
39 | Общее количество листов документа |
Примечание.
1. К пункту 15. После изложения всех переходов операции и, если последующей операцией обработки изделия согласно МК не является операция контроля, в ОК должны быть указаны параметры и объем контроля, выполняемого на рабочем месте. При наличии эскиза, на котором обозначены опорные точки (опоры) и зажимы, переходы типа «Установить и закрепить деталь» не пишутся. В этом случае при нормировании этих переходов учитываются все его элементы и суммарное время, необходимое на установку и снятие детали, проставляют в графе «Тв» на уровне первой строки. Если в операции необходимо произвести переустановку детали, на эскизе делается второе изображение детали с учетом ее перезакрепления.
| Б. Операционная карта обработки на многошпиндельных автоматах и полуавтоматах (форма 6) |
12 | Частота вращения шпинделя станка в минуту |
13 | Частота вращения шпинделя, необходимая для выполнения операции |
27 | Частота вращения шпинделей дополнительных устройств на рабочем ходу |
28 | Отношения частоты вращения шпинделя станка к частоте вращения шпинделя приспособления на рабочем ходу |
37 | Расчетная частота вращения шпинделя, необходимая для обработки детали на переходе. |
38 | Принятая частота вращения шпинделя, необходимая для обработки детали на переходе. |
40 | Угол рабочего хода на кулачке |
43 | Эскиз детали с размерами, получаемыми после выполнения операции |
44 | Обозначение технологического процесса маршрутной карты, карты технологического процесса по ГОСТу 3.1201-85 |
Графические документы. К графическим документам относят карту эскизов ГОСТ 3.1105-84. Карту эскизов следует разрабатывать для операций и переходов. Она включает в себя первый и последующие листы (формы 5 и 5 а). На карте эскизов должны быть указаны данные, необходимые для выполнения технологического процесса (размеры, предельные отклонения, обозначение шероховатости поверхностей, технические требования, теоретическая схема базирования, включающая упрощенное обозначения зажимов (ГОСТ .21495-76). По усмотрению руководителя теоретические схемы базирования студент может заменить схемами установки по ГОСТу 3.1107-81.
Таблицы, схемы и технические требования следует размещать на свободном поле карты эскизов оправа от изображения или под ним. Эскизы следует выполнять без соблюдения масштаба. Обрабатываемые поверхности изделия следует обводить сплошной линией толщиной, равной от 2s до 3s по ГОСТу 2.308-79.
Условные обозначения, установленные государственными стандартами, применяют на карте эскизов без разъяснения, со ссылкой па соответствующие стандарты.
Допускается на одной карте эскизов выполнять несколько эскизов к нескольким операциям. В основной надписи в этом случае в графе «Номер операции» должны проставляться номера операций, для которых выполнены эскизы.
Пример оформления первого или заглавного листа КЭ приведен в приложении 4, лист 4.
Текстовые документы. К текстовым относятся технологические документы, содержащие описания технологических (процессов или отдельных операций (МК, КТП, ВО, КЭ и др.). Допускается в документах применять краткую форму наименования операции, например «токарная» вместо «токарная операция».
В содержание операции (перехода) должно быть исключено наименование метода обработки, выраженное глаголом в повелительной форме (например, точить, сверлить и т. д.), наименование обрабатываемой поверхности материала или детали (например, торец, галтель, отверстие и т. д.), размеры и предельные отклонения обрабатываемых поверхностей (только при отсутствии эскиза). Если имеется эскиз, на котором все размеры обрабатываемых поверхностей условно пронумерованы, то в содержании операции (перехода) размеры и предельные отклонения обрабатываемых поверхностей не указываются, например, «развернуть отверстие 1», «точить торец 3», «расточить отверстие 2».
В содержании операции (перехода) указывают количество одновременно обрабатываемых поверхностей, например, «сверлит 5 отверстии», «нагреть 6 заготовок до температуры ковки».
При одновременной обработке в операции (переходе) нескольких поверхностей в тексте перечисляются все обрабатываемые поверхности.
Допускается указывать в описании операции (перехода) характер обработки (например, предварительная, окончательная, одновременная и т. д.).
Записи в документах следует делать на каждой строке в один ряд. Рекомендуется оставлять свободные строки (одну-две строки) между разделами и подразделами, между описаниями операций и переходов.
Все технологические документы подшивают в пояснительную записку. В приложении Б данные примеры оформления маршрутной карты (МК), карты технологического процесса (КТП), карты эскизов (КЭ), ведомость оснастки (ВО), операционной карты технического контроля (ОКТК).
Литература
- Ансеров И.А. «Приспособления для металлорежущих станков». - Л.: Машиностроение, 1975.
- Андреев Г.А., Новиков В.Ю., Схиртладзе А.Г. «Проектирование технологической оснастки машиностроительного производства». - Высшая школа, 2001.
- Белоусов А.П. «Проектирование станочных приспособлений». - М.Высшая школа, 1980.
- Вереина Л.И. «Справочник-токаря». Москва, Асадема, 2002.
- Воробьев A.M. «Технология машиностроения и ремонт машин». Москва «Высшая школа», 1981.
- Гельфгат Ю.Н. Сборник задач и упражнений по технологии машиностроения. М.: Высшая школа, 1986.
- Гусев А.А. Технология машиностроение. - М.: Машиностроение 1986.
- Горошин А.Х. Справочник «Приспособление для металлорежущих станков». Машиностроение 1979.
- Горбацевич А.Ф. «Курсовое проектирование по технологии машиностроения», 1975 г.
- Данилевский В.В. Технология машиностроения. - М.: Высшая школа, 1984.
- Добрыднев И.С. «Курсовое проектирование по предмету «Технология машиностроения». М.: Машиностроение, 1985
- Данилевский В.В., Гельфгат Ю.Н. Лабораторные работы и практические занятия по технологии машиностроения. М.: Высшая школа. 1988
- Дальский A.M. «Справочник технолога-машиностроителя». Москва. «Машиностроение» 2003.
- Егоров М.Е. Технология машиностроения. - М.:Высшая школа. 1976.
- Зайцев С.А. «Контрольно-измерительные приборы и инструменты», 2006.
- Ковшов А.Н. Технология машиностроения. - М.: Высшая школа. 1987
- Колесов И.М. Основы технологии машиностроения. - М.: Машиностроение 1986
- Клепиков В.В., Бодров A.M.. Технология машиностроения. Москва, Форум-ИНФРА. - М.,2004 г.
- Корсаков B.C. «Основы конструирование приспособлений». - М. машиностроение, 1983
- Кузнецов Ю.Н. «Технологическая оснастка для станков с ЧПУ с промышленных работ». - М.: Машиностроение 1979
- Коваленко А.А. Подшивалов Р.Н. «Станочные приспособления». - М.Машиностроение 1986
- Кузнецов Ю.Н. Маслов А.Р. Байков А.И. Оснастка для станков с ЧПУ. Справочник.-М.: Машиностроение 1990
- Малкин. Технология машиностроения «Машиностроение», 1985
- Мосталыгин, Н.Н. Толмачевский «Технология машиностроения», Машиностроение 1990
- Медведев В.А., Вороненко В.П., Брюханов В.П., «Технологическая оснастка ГПС».— М.: Машиностроение 1979
- Маслов «Приспособление для металлообрабатывающего инструмента». Машиностроение 2002
- Маханько A.M. «Контроль станочных и слесарных работ», Москва, 2000
- Раковин А.Г. «САПР станочных приспособлений». - Машиностроение 1986
- Справочник технолога-машиностроителя, т.т. 1,2.11 под редакцией Косиловой А.Г. и Мещерякова Р.К. - М:Машиностроение, 1985.
- Справочник технолога. Под редакцией Монахова Г.А. - М.Машиностроение, 1974
- Силантьева Н.Л., Малиновский В.Р. Техническое нормирование груда в машиностроении. - М.:Машиностроение 1990
- Система автоматизированного проектирования технологических процессов, приспособлений и режущих инструментов. Под редакцией С.Н.Корчака. - М. Машиностроение, 1988
- Суслов. Технология машиностроения «Машиностроение», Москва 2004
- Соломенцова Ю.М. «Проектирование технологии автоматизированного машиностроения», Москва «Высшая школа» 1999
- Худобин Л.В. Гурьянихин В.Ф. Берзин В.Р. «Курсовое проектирование по технологии машиностроения». - М.: Машиностроение 1989
- Черпаков «Технологическая оснастка». - Москва, 2003
- Черпаков Б.И., Альперович Т.А. Книга для станочника. Москва, 1999