И. И. Ползунова Стуров Д. С., Белоусова Н. Н., Авдеев Е. Н. Определение загрязненности воздуха рабочей зоны Методические указания
Вид материала | Методические указания |
- И. И. Ползунова Стуров Д. С. Защита от электрического тока техническими средствами, 345.62kb.
- И. И. Ползунова Кафедра Безопасность жизнедеятельности Шамов Ю. А. Белоусова, 911.68kb.
- И. И. Ползунова Кафедра «Безопасность жизнедеятельности» Гергерт В. Р., Стуров, 299.13kb.
- А. И. Заиченко 22 декабря 1988 г. N 4945-88 методические указания, 2791.75kb.
- Методические указания мук 2460-09 измерение концентраций хлорантранилипрола в воздухе, 167.19kb.
- Методические указания по определению вредных веществ в сварочном аэрозоле (твердая, 3900.72kb.
- Методические указания к лабораторной работе по курсу «Безопасность жизнедеятельности», 141.95kb.
- Список литературы, представленной на выставке «Промышленные выбросы и контроль качества, 63.47kb.
- И. И. Ползунова Бийский технологический институт С. В. Щигрев методические указания, 350.11kb.
- Методические указания по измерению концентрации вредных веществ в воздухе рабочей зоны, 203.02kb.
1 2
Министерство образования Российской федерации
Алтайский государственный технический
Университет им И.И. Ползунова
Стуров Д.С., Белоусова Н.Н., Авдеев Е.Н.
Определение загрязненности воздуха рабочей зоны
Методические указания для выполнения лабораторной работы
студентов АлтГТУ всех форм обучения
Барнаул 2002
УДК 628.822
Стуров Д.С., Белоусова Н.Н., Авдеев Е.Н. Определение загрязненности воздуха рабочей зоны: методические указания к лабораторной работе для студентов, изучающих дисциплину “Безопасность жизнедеятельности” всех форм обучения / Алтайский государственный технический университет им. И.И. Ползунова. – Барнаул: 2002г.
В работе приведены производственные процессы, загрязняющие воздух рабочей зоны парами и газами вредных веществ, даны сведения о их воздействии на организм человека и окружающую среду, указаны основные меры защиты от загрязнений и методы контроля качества воздуха.
В методических указаниях описаны лабораторный стенд, разработанный авторами, приведены контрольные вопросы, требования к отчету о проделанной работе и список литературы для самоподготовке по теме: ”Оздоровление воздушной среды рабочей зоны производственных помещений”.
Методические указания рассмотрены и одобрены методической комиссией кафедры БЖД
1 Цель работы
- – Освоить теоретические основы контроля загрязнений воздушной среды и защиты работающих от вредных выделений производственных процессов.
- – Приобрести опыт измерений и оценки загрязненности воздуха рабочей зоны.
2 План выполнения лабораторной работы
2.1 Внимательно прочесть методические указания и уяснить их содержание (время 20-25 минут).
2.2 Выбрать (самостоятельно или с помощью преподавателя) вариант производственного процесса (см. приложение А) с выделениями в атмосферу паров (газов) вредных веществ, соответствующих источникам выделений, установленных на стенде (рисунок 3. поз.13), (время 5-10 минут).
- Используя комплект индикаторных средств (рисунок 3. поз.16), руководствуясь п. 4.2, собрать индикаторную трубку и по изложенной методике провести эксперимент, (25-30 мин)
- Оформить отчет согласно п.6, ответить на контрольные вопросы и защитить отчет у преподавателя (20-25 минут).
-
Краткие сведения о производственной воздушной среде и способах ее оздоровления (нормализации)
3.1 Производственные процессы – главные источники загрязнений воздуха рабочей зоны на производстве
Воздух представляет собой физическую смесь различных газов, образующих атмосферу Земли. Идеально чистый воздух содержит 78,09% азота; 20,95% кислорода; 0,93% аргона и 0,03% углекислого газа.
В производственных условиях чистого воздуха практически не бывает. Вредные вещества (ВВ) в воздухе могут присутствовать в виде паров, газов и пылей. Источниками выделений паров, газов и пылей являются разнообразные производственные процессы, в которых вредные для человека вещества входят либо как исходные материалы (например приготовление различных растворов, смесей, электролитов и т.д.), либо это могут быть вторичные продукты в результате температурных, силовых или иных физических воздействий на предметы труда (например: сварка металлов, горячая штамповка, покраска и др, процессы). Варианты производственных процессов с выделениями ВВ приведены в приложении А.
3.2 Воздействие вредных веществ на организм человека
Вредными веществами признаются такие вещества, которые при контакте с организмом человека, в случае нарушений требований безопасности, вызывают травмы или заболевания как непосредственно в процессе труда, так и потом в отдаленном будущем самого рабочего или его потомства.
В организм человека ВВ проникают через дыхательные пути, кожу и с пищей. Вредные вещества, как химические опасные и вредные производственные факторы по ГОСТ 12.0.003-74 делятся на:
- раздражающие (хлор, аммиак, сернистый газ и др.), которые оказывают раздражающее действие на слизистую оболочку и кожу человека;
- токсические (окись углерода, свинец, ртуть и др.), которые могут вызывать тяжелые отравления или заболевания;
- канцерогенные (никель и его соединения, окислы хрома, асбест, сажа, бензопирен и др.). вызывающие раковые заболевания;
- мутагенные (свинец, марганец, радиоактивные вещества), вызывающие нарушение генетического кода клеток;
- сенсибелизирующие (формальдегиды, растворители, спирты, бензин и др.) которые вызывают аллергию;
- вещества, влияющие на репродуктивную (половую) функцию человека - ртуть, свинец, кобальт, радиоактивные вещества.
3.3 Основные меры защиты воздушной среды от загрязнений
Одной из эффективных защитных мер является регламентация (нормирование) содержания вредных веществ в воздухе рабочей зоны. Согласно ГОСТ 12.1.005-88 присутствие ВВ в воздухе производственных помещений не должно превышать предельно допустимой концентрации (ПДК) в мг/м3. Величины ПДК, оговорены стандартом для всех известных на сегодня 1307 веществ, которые могут находиться в воздухе в виде паров, газов или пылей. Величина ПДК является элементом правовой защиты безопасности трудовой деятельности человека и потому подлежит обязательному учету и контролю во всех сферах жизнедеятельности человека. Все другие меры и средства защиты от загрязненности воздуха строятся с учетом стандартизованных величин ПДК.
Нормируемая стандартом величина ПДК не опасна для организма человека в течение всей его трудовой деятельности при условии, что рабочий день длится не более 8 часов, а рабочая неделя не превышает 40 часов. При большей продолжительности труда величины ПДК должны быть скорректированы в меньшую сторону.
Величины ПДК вредных веществ предложены Минздравом РФ исходя из степени опасности ВВ. По степени опасности ВВ (по ГОСТ12.1.007-76) делятся на четыре класса:
- Вещества чрезвычайно опасные, например, ртуть, свинец, бензопирен, для которых ПДК≤0,1мг/м3;
- Вещества высоко опасные, например окислы азота, аэрозоли марганца, кобальт, хлор и др., их ПДК=0,1 – 1,0 мг/м3;
- Вещества умеренно опасные, например медь, диоксид кремния, толуол, табак, азотная кислота и др., ПДК=1,1 – 10,0 мг/м3;
- Вещества мало опасные. Это ацетон, аммиак, этиловый спирт и др., для которых ПДК> 10,0 мг/м3;
Согласно требованиям безопасности любой производственный процесс должен протекать, не превышая нормы выбросов вредных веществ (ПДК). Но в реальных условиях это не всегда удается, часто из-за того, что укрыть и герметизировать очаги выделений просто невозможно.
Тогда в технологическом процессе необходимо предусматривать местную вытяжную вентиляцию - отсос ВВ из очага выделений (приложение Б). Там же, где по каким-либо причинам невозможно организовать местную вентиляцию, должна действовать общеобменная (общецеховая) приточно-вытяжная вентиляция. В общем случае, в целях более эффективной защиты от загрязнений необходимо использовать общеобменную и местную вентиляции; при проектировании или модернизации техпроцессов и оборудования надо стремиться к тому, чтобы в производственных условиях выделение вредных веществ, как по количеству, так и по степени опасности было наименьшим для человека. При этом важную роль играет достоверность информации о загрязненности воздуха.
Таким образом, основными мерами защиты от загрязнения воздуха на производстве являются:
- нормирование содержания ВВ;
- проектирование и выбор более безопасной техники и технологии;
- устройство эффективной общеобменной и местной вентиляции;
- замена вредных опасных веществ на менее вредные и опасные;
- применение более совершенных методов и средств контроля за состоянием воздушной среды
- применение средств индивидуальной защиты (СИЗ).
3.4 Контроль воздушной среды
В целях сохранения здоровья работающих администрация предприятий и органы государственного надзора обязаны контролировать состояние воздушной среды. Информация о загрязненности воздуха необходима рабочим и специалистам:
- для оценки санитарно-гигиенической обстановки рабочих мест и установления класса условий труда. Там, где условия труда относятся к третьему классу – вредные, работникам должна быть назначена компенсация за вредность согласно приложению В;
- при расследовании причин профессиональных заболеваний и отравлений, а также при анализе общей заболеваемости в цехе;
- для проектирования или модернизации вентиляционной системы цеха.
Чтобы достоверно определить количественное содержание ВВ, необходимо прежде всего тщательное изучение технологического процесса, установление мест, где происходят выделения, загрязняющие воздух. А затем уже следует произвести отбор пробы и ее анализ. В производственных условиях отбор проб должен проводится в зоне дыхания на расстоянии 0,5 м от лица. Такую работу нужно периодически проводить на каждом производственном участке. Периодичность и методика проверок - согласно ГОСТ 12.1. 005-88.
Существует много методов отбора и анализа загрязненного воздуха. Большинство из них лабораторные очень точные, но трудоемкие, так как требуют применения сложной аппаратуры, высокой квалификации лаборантов и значительных затрат времени.
В охране труда получили распространение менее точные экспрессные, т.е. быстрые методы отбора и анализа воздуха в производственных условиях.
Экспрессные методы основаны на получении цветной реакции при взаимодействии вредных веществ с твердым сорбентом - индикаторным порошком, который заключен в стеклянную трубку. При протягивании (всасывании) исследуемого воздуха через трубку с индикаторным порошком, последний окрашивается на определенную величину столбика h. По величине окрашенного столбика h с помощью специальной шкалы или графика определяют концентрацию q (мг/м3 ) ВВ в воздухе помещений.
В качестве основного прибора для таких целей широко применяется универсальный переносный газоанализатор типа УГ-2, а также аспиратор сильфонный АМ-5. С помощью УГ-2 отбирают нужный объем газовоздушной смеси и определяют концентрацию q (мг/м3) паров или газов следующих веществ:
1 Аммиак
2 Ацетон
3 Ацетилен
4 Бензин
5 Бензол
6 Ксилол
7 Окись углерода
8 Окислы азота
9 Сернистый ангидрид
10 Сероводород
11 Толуол
12 Хлор
13 Углеводороды нефти
14 Этиловый эфир (спирт)
В комплект прибора входят (рисунок 1):
1 - паспорт изделия;
2 – воздухозаборное устройство;
3 – коробки (14 шт.) с комплектом индикаторных средств, каждая из которых предназначены для обнаружения в воздухе только того вещества, которое указано на коробке. Гигиенические характеристики искомых веществ и исходные данные для эксперимента приведены в таблице 1.
Конструкция воздухозаборного устройства представлена на рисунке 2. В металлическом корпусе 4 помещена гофрированная пневмокамера (сильфон) 5, нижняя часть которой жестко прикреплена к корпусу прибора, а верхняя – эластично, посредством пружины 3 (прикреплена к траверсе) 11. Отбор нужного объема загрязненного воздуха производится пневмокамерой с помощью штока 1.
Делается это следующим образом:
Оттянув фиксатор 2, вставляют в отверстие прибора шток 1 и сжимают штоком пневмокамеру 5 до появления щелчка, т.е. до тех пор, когда фиксатор войдет в верхнее углубление 13 на штоке 1. При сжатии избыточный объем воздуха из камеры должен по каналу 9 и шлангу 8 свободно выходить наружу. В таком «сжатом» состоянии воздухозаборное устройство считается подготовленным к работе. Теперь только надо вставить в шланг 8 индикаторную трубку 7 и освободить шток 1 от фиксатора 2. Для этого нужно сначала нажать на шток и вывести фиксатор из углубления 13, затем плавно отпустить шток. Под действием растянутой пружины 3 (рисунок 2,б) пневмокамера 5 начнет подниматься вверх и увеличиваться в объеме, засасывая при этом через трубку 7 загрязненный воздух. При наличии в воздухе искомого вещества индикаторный порошок в трубке изменит свой первоначальный цвет.
Таблица 1 - Гигиенические характеристики искомых веществ и исходные данные
Исследуемое вещество | Гигиенические характеристики | Исходные данные для эксперимента | ||||
Класс опасности | Величина ПДК мг/м3 | Особенности действия на человека | Просасываемый объем пробы, см3 | Время просасывания, с | ||
До защелкивания | Общее | |||||
аммиак | IV | 20 | – | 200 | ≤160 | 240 |
ацетон | IV | 200 | – | 300 | ≤240 | 420 |
ацетилен | IV | 500 | – | 300 | ≤230 | 300 |
бензин | IV | 100 | – | 300 | ≤230 | 420 |
бензол | III | 5 | К | 300 | ≤290 | 420 |
ксилол | III | 50 | – | 300 | ≤130 | 240 |
окись углерода | IV | 20 | О | 200 | ≤280 | 480 |
окислы азота | III | 5 | О | 300 | ≤330 | 420 |
сероводород | III | 10 | О | 300 | ≤200 | 300 |
сернистый ангидрид | III | 10 | – | 300 | ≤160 | 300 |
толуол | III | 50 | – | 300 | ≤230 | 420 |
углеводороды нефти | IV | 300 | – | 300 | ≤230 | 420 |
хлор | II | 1 | О | 300 | ≤330 | 420 |
этиловый спирт | IV | 1000 | – | 400 | ≤430 | 600 |
Примечание: О – остродействующие; К – канцероген; |

Рисунок 1 - Комплект прибора УГ – 2.
1 – Паспорт прибора; 2 – Воздухозаборное устройство; 3 – Набор коробок с комплектами индикаторных средств (КИС)
Содержимое коробок (КИС)
4 –этикетка со шкалой; 5 –ампула с содержимым для приготовления поглотительного патрона; 6 –фольга; 7 – термометр; 8 – трубка стеклянная; 9 – стержень; 10 – штырек; 11 – заглушка; 12 – воронка;13 – ампула; 14 – шток; 15 – вата для тампонов; 16 – фильтрующий патрон;
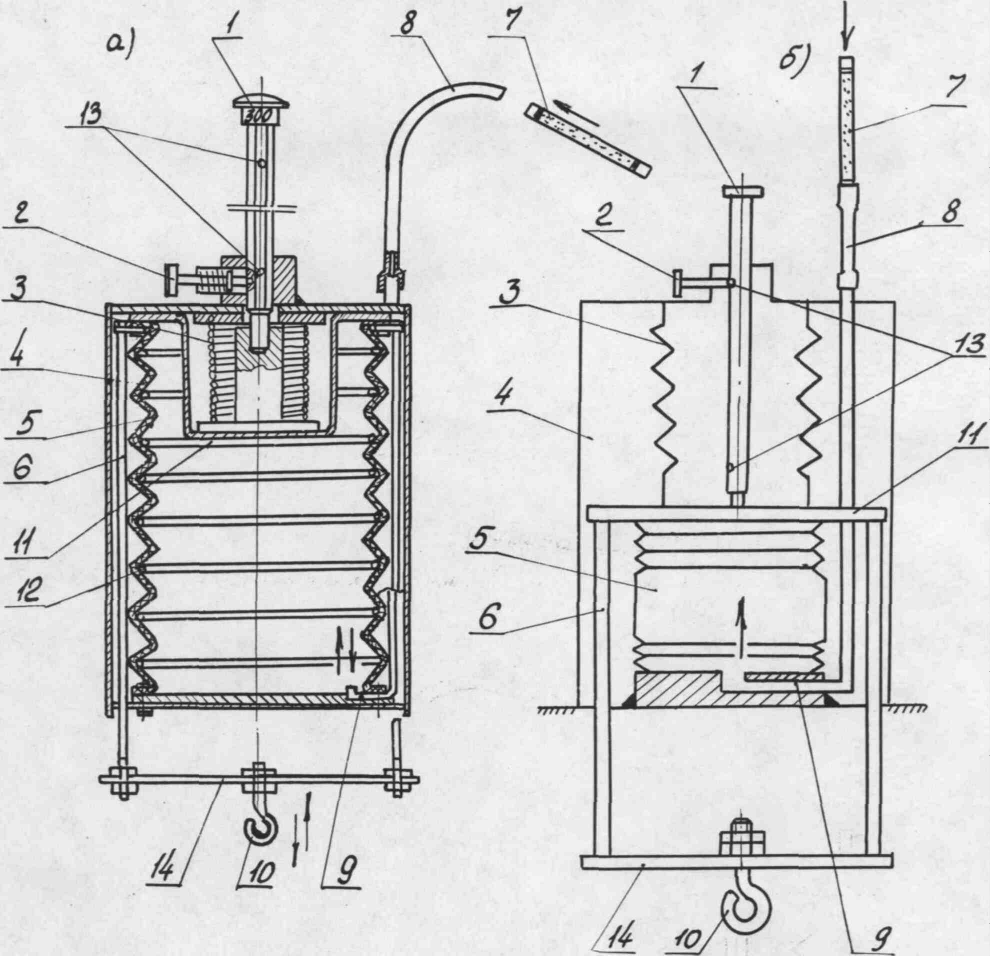
Рисунок 2 - Воздухозаборное устройство.
а) конструктивное изображение; б) схема;
1 – шток; 2 – фиксатор; 3 – пружина растяжения; 4 – корпус прибора; 5 – камера гофрированная (сильфон); 6 – шпилька; 7 – индикаторная трубка; 8 – шланг; 9 – воздушный канал; 10 – крючок; 11 – траверса; 12 – кольцо распорное; 13 – углубление для фиксатора; 14 – поперечина;
Часто в реальных производственных условиях в смеси (воздух-вредное вещество) присутствует не одно, а несколько вредных веществ, обусловленные технологическим процессом. Для того, чтобы определить искомое ВВ в присутствии других ВВ, используются фильтрующие патроны. Это стеклянные трубки d= 10,0 мм с одной или несколькими перетяжками, заполненные соответствующими поглотительными порошками (рисунок 3,поз.3).
Например, при определении концентрации этилового эфира, необходимо использовать фильтрующий патрон, служащий для улавливания паров воды, этилового спи рта, органических кислот (муравьиной и уксусной) и фенола.
Необходимый по условиям эксперимента объем просасываемой пробы воздуха ограничивается величиной хода штока от верхнего до нижнего углублений 13 на штоке и временем просасывания, указанным в таблице 1. Концентрация q мг/м3 ВВ определяется по величине окрашенного столбика h мм в индикаторной трубке с помощью специальных шкал (рисунок 1 поз. 4) или графиков.
4. Экспериментально-практическая часть
Порядок выполнения:
- ознакомление с устройством и работой стенда;
- проведение эксперимента в соответствии с предлагаемой методикой;
4.1 Устройство и работа лабораторного стенда
Уважаемые студенты, помните! Бережное обращение, строгое соблюдение методических указаний и ограниченное «рукоприкладство» к хрупким и нежным принадлежностям стенда гарантируют его надежность и удовлетворенность работой.
Лабораторный стенд оригинальной конструкции (рисунок 3) предназначен для исследования загрязненности воздуха вредными веществами. Стенд рассчитан на двоих человек, причем у каждого есть свой независимый пульт, т.е. приборная секция, благодаря которой одновременно исследуются разные вещества. Тем самым обеспечивается индивидуальная работа студентов.
В лабораторных условиях загрязнение воздуха создается искусственно, благодаря испарениям легколетучих жидкостей типа ацетон, аммиак, спирт, бензин и др., помещенных в специальные сосуды с управляемыми кранами. Отбор пробы и ее анализ (т.е. определение концентрации) выполняется экспрессным методом с помощью универсального газоанализатора УГ-2, модернизированного для этих целей кафедрой БЖД по проекту Стурова Д.С.
Основой стенда является стол 24, на котором смонтированы все узлы:
а) основание приборное 23, на котором стационарно закреплены подставка 11 для штока 10, модернизированное воздухозаборное устройство 12 (конструкцию его смотри рисунок 2), обойма 14 с источниками выделений ВВ 13 (стеклянные сосуды с испаряющейся жидкостью, в которые герметично вмонтированы газосборники 5 с переходниками 6. Газосборники снабжены кранами "К", которыми регулируется выход паров из сосудов 13 в атмосферу, масштабная линейка 15 для измерения величины окрашенного столбика индикаторного порошка в трубке (смотри рисунок 1), подставка 16 с набором индикаторных принадлежностей для приготовления (сборки) индикаторных трубок, стаканчик 17 с ватой для тампонов, чаша 18 для отходов (отработанные трубки и др.).
б) полка мебельная 22, прикрепленная к столу с помощью кронштейна 29. Для наглядности внутри полки, на ее задней стенке, расположены детали из комплектов индикаторных средств УГ-2. Наверху полки установлены вытяжные зонты, имитирующие отсос вредных веществ от источников выделений 13 и розетки 9 для подключения ЭВМ.
в) тумба 20, на которой смонтированы образцы поглотительных патронов 3, таблицы исходных данных и набор индикаторных графиков (диаграмм) 2, а также система сигнализации о работе стенда: выключатель 1, контрольная лампочка 19, сигнальные лампочки 4, которые контролируют работу воздухозаборного устройства 12 с помощью конечного выключателя 28 и упора 27, закрепленного на тяге 26.
г) рычажная система управления воздухозаборным устройством, состоящая из оси 30, педалей 25 и тяги 26, шарнирно связывающая педаль и траверсу 2 пневмокамеры 5 посредством шпилек 6, поперечины 14 и крючка 10 (рисунок 2) Рычажный привод сжатия пневмокамеры позволяет отказаться от приложения ручного усилия на шток 1 и перейти на ножное. При этом общее усилие на педаль уменьшается более чем в 2 раза и становится под силу любому студенту» особенно девушкам. В этом главное достоинство рычажного привода, тем более что он нисколько не мешает пользоваться традиционным ручным способом управления воздухозаборным устройством.
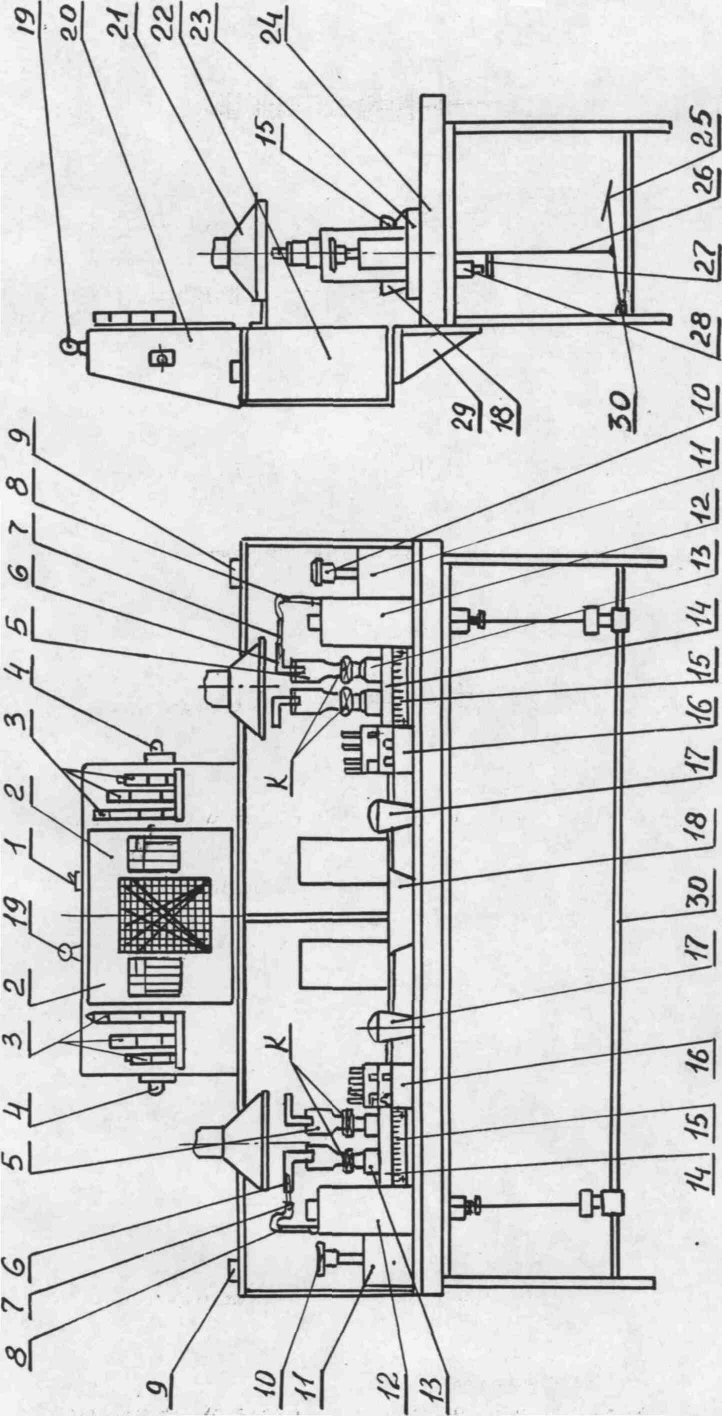

4.2 Методика проведения эксперимента и работа на стенде
Экспериментальная работа должна выполняться в следующей последовательности:
4.2.1 Выбрать вариант производственного процесса с выделениями в воздух рабочей зоны паров (газов) вредных веществ аналогичных источникам выделений, установленных на стенде по таблице 2.
Таблица 2
Номер производственного процесса в приложении 1 | Выделения вредных веществ в производственном процессе | Источник выделений ВВ на стенде (рисунок 3, поз. 13) |
1; 2; 3; 4; 5; 6 | пары спирта | этиловый спирт |
7; 8; 9; 10; 11 | пары бензина | бензин |
12; 13; 14; 15 | пары бензола | бензол |
16; 17; 18; 19 | пары толуола | толуол |
16; 17; 18; 19 | пары ксилола | ксилол |
20; 23; 24; 25 | пары аммиака | аммиак |
21; 22 | пары ацетона | ацетон |
26; 27; 28; 29; 30 | пары, газы хлора, брома, йода | галогены |
32; 31; 33 | пары углеводородов | углеводороды |
Например, если на стенде (рисунок 3, поз. 13), источником паров является бензин, то ваш вариант задания может быть производственный процесс один из номеров от 7 до 11 в приложении А.
4.2.2. Приготовление индикаторной трубки с использованием комплекта индикаторных принадлежностей (смотри рисунок 4 и 5).
Эта часть работы студента является самой важной и ответственной. Поспешность или небрежность приготовления индикаторной трубки отрицательно скажется на результатах исследования.
Порядок приготовления (сборки) следующий:
а,б) в чистую стеклянную трубку 2 с помощью стержня 3 и штырька 6 вставляется ватный тампон размером 2-3 мм и слегка уплотняется;
в,г) затем берется ампула 4 с индикаторным порошком, реагирующим на бензин (ваш вариант задания). снимается с трубки заглушка и засыпается в трубку порошок, как показано на рисунке 5, не досыпая до верху на 10-12мм. После заполнения трубки ампулу нужно быстро закрыть заглушкой и поставить ее на свое место - в гнездо подставки 1; вставить второй ватный тампон сверху и слегка постучать стержнем 3 по трубке с целью уплотнения порошка. После этого стержнем еще раз слегка надо поджать тампон к порошку, чтобы не было просвета между ними.
На этом заканчивается приготовление индикаторной трубки. Стержень и штырек возвращаются на свои места в подставке 1.
Примечание - ватные тампоны не допускается свертывать в жгут, они должны быть в распушенном состоянии.
4.2.3. Подготовка воздухозаборного устройства к работе
На этой стадии, прежде всего, нужно выписать из таблицы 1 гигиенические характеристики исследуемого вещества и исходные данные для проведения эксперимента. В нашем варианте для бензина: класс опасности - 1V; ПДК = 100 мг/м3; объем просасываемой пробы -300см3; время просасывания до щелчка 230 с. общее - 420 с.
Затем берется шток 10 из подстановки 11 и вставляется сверху в отверстие воздухозаборного устройства 12 (рисунок 3) той стороной к фиксатору 2 (рисунок 2), на которой под головкой выбита цифра (300), соответствующая заданному объему просасываемой пробы. Плавно нажимая ногой на педаль 25 и отводя фиксатор 2, заглубляют шток в отверстие до совпадения фиксатора с верхним углублением 13 на штоке. В этот момент вводят фиксатор в углубление 13 и снимают давление ноги с педали.
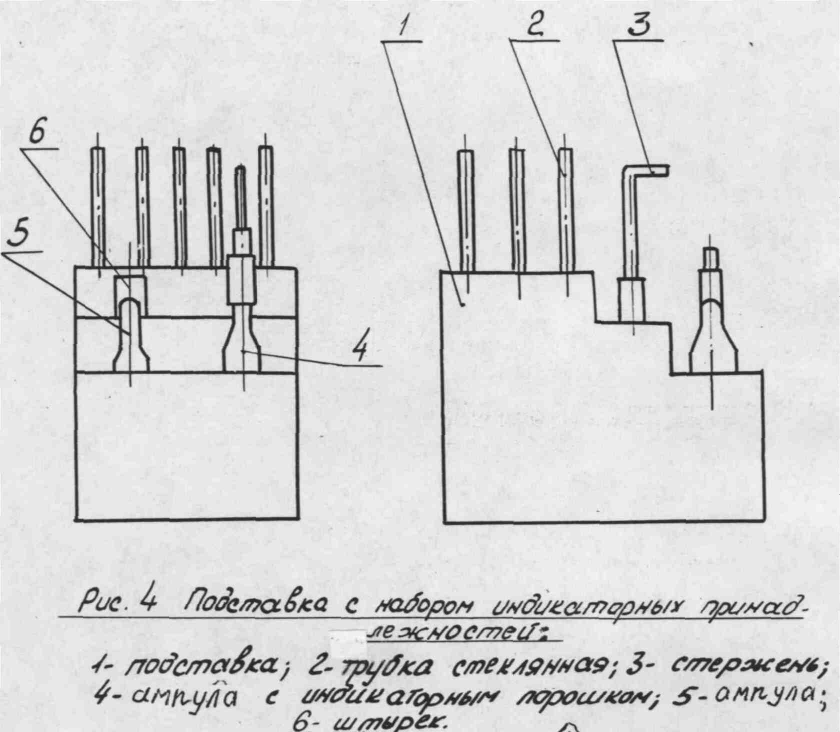

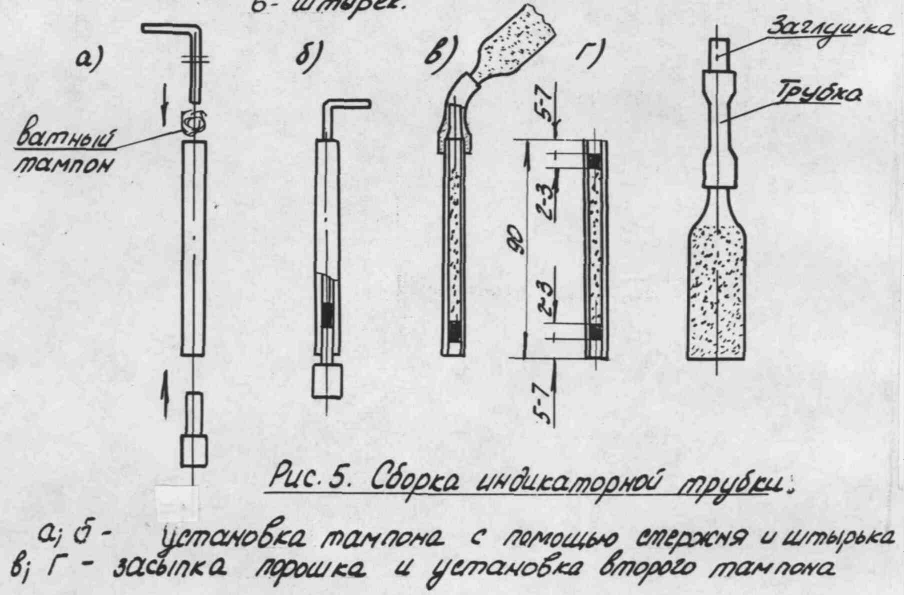
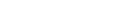
Воздухозаборное устройство в таком зафиксированном положении готово к работе.
Внимание!!!
- Во время нажатия на педаль избыточный воздух из пневмокамеры 5
(рисунок 2) должен свободно выходить наружу, т.е. шланг 8 должен быть открыт!
- При возникновении резкого повышения давления на педаль, во избежание поломок, остановите работу! Сообщите об этом преподавателю.
4.2.4. Просасывание загрязненного воздуха через индикаторную трубку.
Перед просасыванием необходимо включить сигнальную систему стенда (рисунок 3), для чего переключателем 1 включают стенд. При этом должна загореться контрольная лампочка 19 и сигнальная лампочка 4. После этого в конец шланга 8 на глубину 10-12 мм вставляют собранную индикаторную трубку 7 (любым концом) и вводят ее в угольник 6 газосборника 5. Затем открывают кран "К" поворотом его в вертикальное положение и снимают воздухозаборное устройство с фиксатора, для чего слегка нажимают на педаль и отводят фиксатор из заглубления на штоке. Освободив шток от фиксатора и педаль от давления, с этого момента начинается просасывание загрязненного воздуха, и отсчет времени от начала до конца эксперимента по секундомеру. Продолжительность просасывания должна соответствовать указанной в таблице 1 (в нашем варианте 420 с). По истечении этого времени индикаторная трубка вынимается из угольника 6 и шланга 8, высвобождается шток от фиксатора и устанавливается на свое место - в подставку II. Кран "К" газосборника поворачивают в горизонтальное положение, перекрывая поступление испарений в воздух лаборатории.
4.2.5. Определение концентрации ВВ в исследуемом воздухе
Концентрация ВВ в исследуемом загрязненном воздухе устанавливается следующим образом. Величина h окрашенного порошка в трубке измеряется по линейке 15 на стенде методом наложения. Полученный результат в мм переносится на соответствующий график рис.6 (в нашем варианте график 3*) и по графику определяется концентрация q , мг/м3
При h =60 мм, q=I400 мг/м3 ; ПДК = 100. Превышение допустимой концентрации в 14 раз
4.2.6. Окончание эксперимента
Полученные результаты заносятся в тетрадь. Использованные трубки и др. отходы укладывают в чашу 18, вату - в стаканчики 17, и выключают стенд переключателем I (лампочки 4 и 19 гаснут).
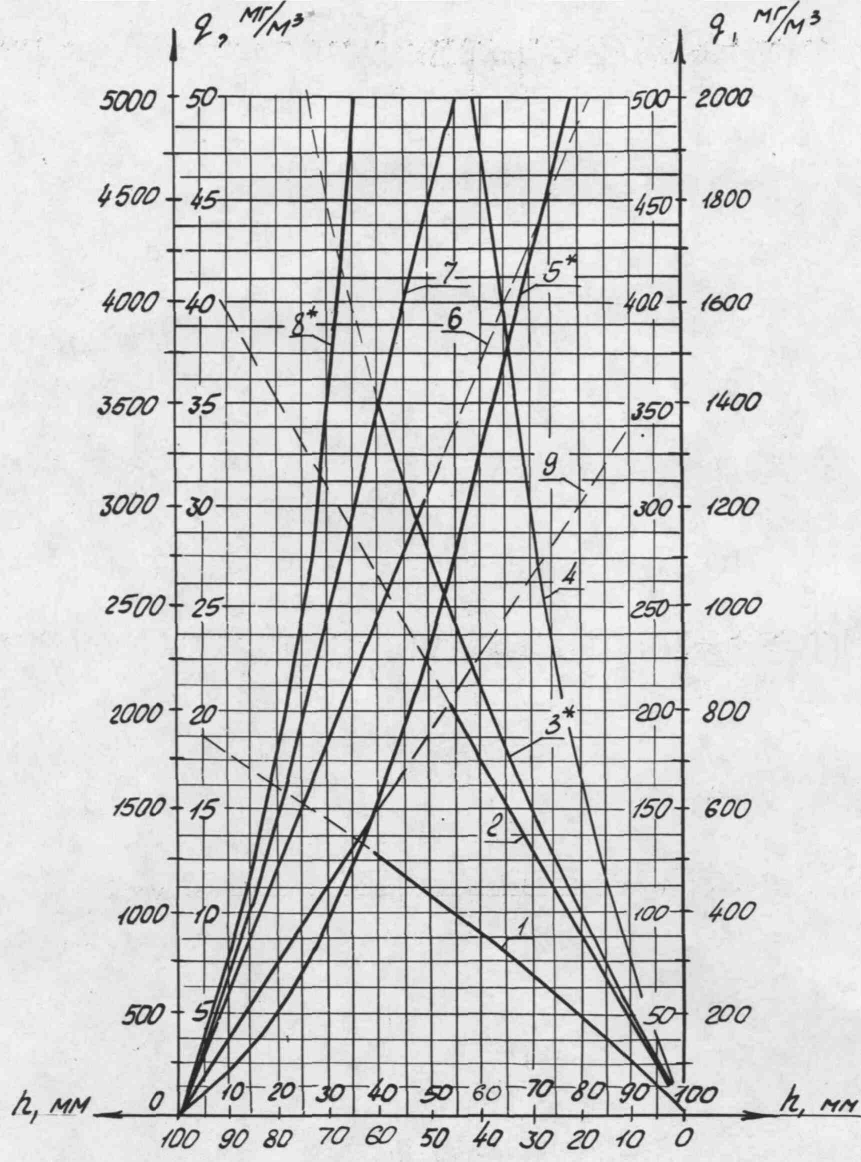
Рисунок 6. Зависимость концентрации q вредных веществ в загрязненном воздухе от величины h окрашенного порошка в индикаторной трубке.
1 – окись углерода; 2 –бензол; 3* - бензин, ацетилен, углеводороды нефти; 4 – толуол, ксилол; 5* - ацетон; 6 – аммиак, сероводород; 7 - окислы азота; 8* - этиловый спирт; 9 – хлор
* - q определяется по наружной шкале ординат
5 Контрольные вопросы
1 Причины и последствия загрязненности воздуха.
2 Характеристики вредных веществ в воздухе.
3 Для чего необходим контроль воздушной среды в производственном помещении?
4 Основные меры защиты воздушной среды от загрязнений.
5 Методы анализа загрязненности воздуха.
6 Принцип действия воздухозаборного устройства.
7 Порядок проведения эксперимента.
8 Состав (комплект) прибора УГ-2.
9 Виды компенсации за вредные условия труда (приложение В)
10 Состав комплекта индикаторных средств.
11 Нормирование загрязненности воздуха в производственном помещении.
12 Виды местных отсосов (приложение Б)
6 Содержание отчета
1 Название лабораторной работы и ее цель.
2 Вариант задания (приложение 1 выписать все данные).
3 Гигиенические характеристики исследуемого вещества и исходные данные для эксперимента (из таблицы 1 выписать все данные).
4 Схема воздухозаборного устройства (рис.2,б).
5 Результаты исследования: величина h ,мм окрашенного столбика индикаторного порошка, номер графика (рис.6) и величина q мг/м3 концентрации, полученная по графику.
6 Вывод о необходимости применения местного отсоса, и если отсос необходим - привести схему его в отчете.
7 Литература
1 Безопасность жизнедеятельности: учебник для вузов/С.В. Белов, А.В. Ильинская, А.Ф. Козьяков и др.; Под общ. ред. С.В. Белова, 3-е изд., испр. и доп. – М.: Высш. шк., 2001. – 485 с.
2 Средства защиты в машиностроении. Расчет и проектирование: Справочник /Под ред. Белова С.В., Козьякова О.Ф., Партолина О.Ф. и др. –М.: Машиностроение, 1989.- 368 с.
3 ГОСТ12.1.005-88.ССБТ. Общие санитарно-гигиенические требования к воздуху рабочей зоны.
4. ГОСТ 12.1.007-76.ССБТ. Вредные вещества. Классификация и общие требования безопасности.
Приложение А
Таблица 1 Производственные процессы – источники выделений вредных веществ
№ варианта | Производственный процесс | Помещение, цех, участок | Рабочее место или источник выделения вредных веществ | Вредные вещества, выделяемые в рабочую зону | Рекомендуемый тип отсоса |
1 | 2 | 3 | 4 | 5 | 6 |
1 | Суперфинишная обработка плунжерных пар пастами на спирту | Участок доводки и сборки медицинских ингаляторов | Стенд доводки плунжерных пар | Пары спирта | 1-В3 – вытяжной зонт круглой формы |
2 | Стерилизация масок для индивидуального пользования | Участок специальной обработки и упаковки средств защиты лица | Стол стерилизации СИЗ с использованием спиртового раствора | Пары спирта | 3-В3 – вытяжной зонт щелевой формы |
3 | Испытание спиртовых карбюраторов для ДВС | Испытательный участок моторного завода | Испытательный стенд | Пары спирта | 2-В3 – вытяжной зонт прямоугольной формы |
4 | Обезжиривание деталей пищевых аппаратов перед хромированием | Гальванический цех | Моечная ванна со спиртовым раствором | Пары спирта | 6-БО – бортовой отсос (однобортовой) |
5 | Полировка окуляров оптических приборов | Центральная заводская лаборатория (ЦЗЛ) | Установка для полировки оптического стекла | Пары спирта | 2-В3 – вытяжной зонт прямоугольной формы |
6 | Промывка плат в спиртовом растворе | Монтажный цех радиозавода | Моечный ванна и кассетный стол для сушки деталей | Пары спирта | 7-БО – бортовой отсос (однобортовой) |
7 | Суперфинишная обработка плунжерных пар пастами на бензине | Цех топливной аппаратуры моторного завода | Стенд доводки плунжерных пар топливных насосов | Пары бензина | 4-ВП – вытяжная панель круглой формы |
8 | Обезжиривание деталей КПП трактора Т-4М в бензиновом растворе | Мастерская по ремонту тракторов | Стол для разборки узла КПП и емкость для мойки деталей | Пары бензина | 5-ВП – вытяжная панель (наклонная) |
9 | Регулировка узлов топливной аппаратуры бензиновых двигателей | Цех топливной аппаратуры | Установка для испытания и регулировки топливных узлом ДВС | Пары бензина | 1-В3 – вытяжной зонт (круглый) |
10 | Реставрация и ремонт резиново-технических изделий автомобилей | Шиномонтажный цех АТП | Стол-станок для вулканизации и ремонта РТИ | Пары бензина | 2-В3 – вытяжной зонт (прямоугольной) |
11 | Производство паронита (прокладочный материал) | Заготовительный цех АТИ | Станок для приготовления паронитовой смеси | Пары бензина | 4-ВП – вытяжная панель |
12 | Производство формовочной смеси | Участок формовки литейного цеха | Установка для приготовления смеси | Пары бензола | 3-В3 – вытяжной зонт щелевой формы |
13 | Склеивание металлоизделий органоминеральным клеем | Механосборочный цех | Сборочный верстак | Пары бензола | 4-ВП – вытяжная панель |
1 | 2 | 3 | 4 | 5 | 6 |
14 | Изготовление и сушка модельных стержней | Стержневой участок литейного цеха | Стол-стеллаж | Бензол | 5-ВП – вытяжная панель |
15 | Приготовление асфальтобетона | Асфальтобетонный цех ДорСУ | Ванна для плавки сланцевого битума | Бензол | 8-БО – бортовой отсос (кольцевой) |
16 | Покраска и сушка мелких деталей распылителем | Молярно-упаковочный участок | Стол-стеллаж для покраски и сушки | Толуол, ксилол | 1-В3 – вытяжной зонт |
17 | Лакокрасочное покрытие корпусов измерительных приборов | Малярной участок механосборочного цеха | Окрасочная ванна | Толуол, ксилол | 7-БО – бортовой отсос |
18 | Приготовление стекловаты термическим способом | Участок плавки на заводе ячеистого бетона | Разлив в формы расплава | Толуол, ксилол | 3-В3 – вытяжной зонт щелевой формы |
19 | Смыв старой краски с поверхностей деталей при реставрации | Кузовной цех АТП | Ванна с растворителем | Толуол, ксилол | 7-БО – бортовой отсос |
20 | Азотирование деталей | Термический цех | Установка для азотирования | Аммиак | 6-БО – бортовой отсос |
21 | Обезжиривание дисков перед склеиванием фрикционных накладок | Участок муфт и тормозов станкозавода | Верстак с емкостью для обезжиривания в растворе ацетона | Ацетон | 5-ВП – вытяжная панель |
22 | Приготовление полистиролового клея для изделий ширпотреба | Цех пластмасс завода капролит | Установка для приготовления клея | Ацетон | 4-ВП – вытяжная панель |
23 | Проявление синекопий чертежей в аммиачной среде | Светокопия отдела техдокументации завода | Проявочная камера | Аммиак | 1-В3 – вытяжной зонт |
24 | Приготовление моющего раствора для автосервиса | Хим. цех завода | Установка для приготовления моющего раствора | Аммиак | 2-В3 – вытяжной зонт |
25 | Учебная лабораторная работа | Хим. лаборатория | Ванна с раствором нашатырного спирта | Аммиак | 8-БО – бортовой отсос (кольцевой) |
1 | 2 | 3 | 4 | 5 | 6 |
26 | Электрохимическая обработка металлоизделий в растворе соляной кислоты (травление, снятие заусенцев) | Механосборочный цех | Ванна с электролитом | Хлористый водород (хлор) | 6-БО – бортовой отсос |
27 | Химическая обработка металлов в растворах фтористо-водородой кислоты | Гальванический цех | Ванна с электролитом | Галогены (фтор, хлор, бром, йод) | 8-БО – бортовой отсос (кольцевой) |
28 | Закалка мелких деталей в соляной ванне | Термический цех | Ванна с электролитом | Галогены (хлор) | 7-БО – бортовой отсос |
29 | Металлообработка с применением водорастворимых СОЖ | Механический цех | Шлифовальный станок (металлорежущий станок) | Галогены (хлор) | 2-В3 – вытяжной зонт |
30 | Приготовление бром-йодистых препаратов | Фармацевтический цех | Установка по приготовлению лекарств | Галогены ( бром, йод) | 3-В3 – вытяжной зонт |
31 | Зуюонарезание шестерен, зубч. колес, вал-шестерни и т.д. | Зуборезный участок механического цеха ремонтной мастерской | Специальный зуборезный станок | Углеводороды нефти | 5-ВП – вытяжная панель |
32 | Закалка и отпуск деталей в масляной ванне | Термический цех | Ванна с электролитом | Углеводороды нефти | 6-БО – бортовой отсос |
33 | Промывка деталей двигателей в керосине на АТП | Участок разработки двигателей | Моечная ванна | Углеводороды нефти | 3-В3 – вытяжной зонт |