Пояснительная записка к проекту на тему Расчёт осесимметричной арматуры работающей с большими пластическими деформациями и разрушением
Вид материала | Пояснительная записка |
- Пояснительная записка к курсовому проекту на тему №13: «Цех по ремонту строительных, 141.43kb.
- Пояснительная записка к курсовому проекту по курсу: «Процессы и аппараты химической, 41.88kb.
- Пояснительная записка к курсовому проекту по курсу: «Процессы и аппараты химической, 39.47kb.
- Пояснительная записка к курсовому проекту по курсу: «Технология промышленных производств», 57.96kb.
- Расчётно-пояснительная записка к курсовому проекту по дисциплине: "Теория механизмов, 22.29kb.
- Пояснительная записка к курсовому проекту по курсу: «Процессы и аппараты химической, 61.26kb.
- Пояснительная записка к курсовому проекту по курсу: «Процессы и аппараты химической, 52.08kb.
- Пояснительная записка содержит: 5 рис., 4 источника, 22 стр, 223.14kb.
- Пояснительная записка к курсовому проекту на тему «Ранг матрицы» по дисциплине, 251.76kb.
- Пояснительная записка к курсовому проекту на тему «Машина Тьюринга» по дисциплине, 256.01kb.
ПОЯСНИТЕЛЬНАЯ ЗАПИСКА
к проекту на тему
Расчёт осесимметричной арматуры работающей с большими пластическими деформациями и разрушением
Руководитель проекта (автор)
Консультант
Логин
Самара 2010
Реферат
Пояснительная записка: 58 страниц, 51 рисунок, 1 таблица, 3 источников,
МЕМБРАНА ПРОРЫВА, ДИАФРАГМА, метод конечных элементов, Рама, расчет на прочность, граничные условия Деформации, расчётные случаи нагружения.
Объектом исследования являются мембранный узёл служащий одноразовым предохранительным клапаном и металлический разделитель газовой и жидкостной полостей.
Цель работы – Разработка инженерной методики для расчета осесиметричных конструкций работающих с большими пластическими деформациями и с разрушением.
Проведение опыта на растяжение материала, получение графика растяжения. Исследование механизма разрушения мембраны прорыва. Подбор оптимального вида прорези и формы мембраны. Исследование механизма деформации диафрагмы. Проверка работоспособности данной детали. Решение контактной задачи, получение результатов деформирования диафрагмы по стенке бака.
Эффективность работы заключается в необходимости предварительной оценки прочности и критерия разрушения мембраны прорыва с помощью метода конечных элементов. Для диафрагмы оценка предварительной прочности и работоспособности. Так же получение графика растяжения материала для наиболее точного расчета. Для расчетов использовался конечно-элементный пакет ANSYS v12.
СОДЕРЖАНИЕ
стр.
ВВЕДЕНИЕ…………………………………………………………………..…..5
1 Используемый материал…..……………………………..…………..…......8
1.2 Получение диаграммы растяжения материала………………...……9
2 мембрана прорыва…………..……………………………..…………..…....13
2.1 Назначение и описание конструкции………………………………..13
2.2 Создание конечно-элементной модели
мембраны прорыва………………………………………….…………….16
2.2.1 Выбор расчётной схемы……………………….…………….16
2.2.2 Конечно-элементное моделирование……………………….17
2.2.3 Задание нагрузки, граничных условий и
дополнительных опций решения………………………………….20
2.3 Обработка результатов, изменение геометрии прорези……………21
2.4 Повторное решение мембраны прорыва с
изменённой геометрией с помощью функции
«смерть элементов»……………………………………………………….23
3 Анализ работоспособности диафрагмы
сферического топливного бака..................................………..……………………………..…………..…27
3.1 Назначение и описание диафрагмы
сферического топливного бака.............................................……..27
3.2 Создание конечно-элементной модели
диафрагмы..….....................................................................................…….32
3.2.1 Выбор расчётной схемы……...........………………….…………….32
3.2.2 Конечно-элементное моделирование и
задание граничных условий...................................……………………….34
3.2.3 Обработка результатов бесконтактного
деформирования.............................................................................…36
3.3 Обработка результатов контактного деформирования .........……….44
4 Технико-экономическое обоснование проекта....................…..…...55
ЗАКЛЮЧЕНИЕ……………………………………………………......57
СПИСОК ИСПОЛЬЗОВАННЫХ
ИСТОЧНИКОВ………..............................................................……58
Введение
Разработка новых конкурентоспособных изделий ракетно-космической техники требует постоянного совершенствования процесса проектирования конструкций. Использование технологии виртуального проектирования позволяет решать задачи выбора проектных вариантов силовых схем перспективных средств ракетно-космической техники, повысить качество проекта, уменьшить сроки проектирования и количество ошибок, значительно снизить расходы на весь цикл проектировочных работ от эскиза до запуска изделия в производство.
В настоящей работе на основе конечно-элементного моделирования в среде современного программного комплекса ANSYS проведено исследование мембраны прорыва и металлического разделителя, устанавливаемых на изделии. Выполнены расчеты на прочность. Исследован механизм разрушения мембраны прорыва. Для диафрагмы исследован механизм деформации как в отдельности, так и в составе бака.
Предложены варианты модификации формы мембраны и параметров насечки для гарантированного срабатывания клапана при заданных условиях
В разделе технико-экономического обоснования проекта проведена оценка затрат на разработку конечно-элементной модели ; выявлены основные технико-экономические преимущества от использования результатов исследования в процессе проектирования и эксплуатации конструкции.
На рисунке 1 представлен типичный график растяжения материала. В основном работа всех деталей и конструкций проектируется и рассчитывается таким образом, что бы они работали в упругой зоне деформаций. На этом участке применим закон Гука. Т.е. после снятия нагрузки деталь вернётся в исходное положение без остаточных деформаций. Во многих расчетах критерием неработоспособности детали является превышение зоны упругого деформирования.
Участок B-C соответствует площадке текучести. На данном участке материал деформируется без приращения усилия. После снятия нагрузки в детали появятся остаточные деформации. На участке С - D происходит упрочение материала и далее разрушение. Точку D принято называть пределом прочности материала. В данном проекте рассмотрено 2 расчета в которых детали работают на участках B-C и B-D.
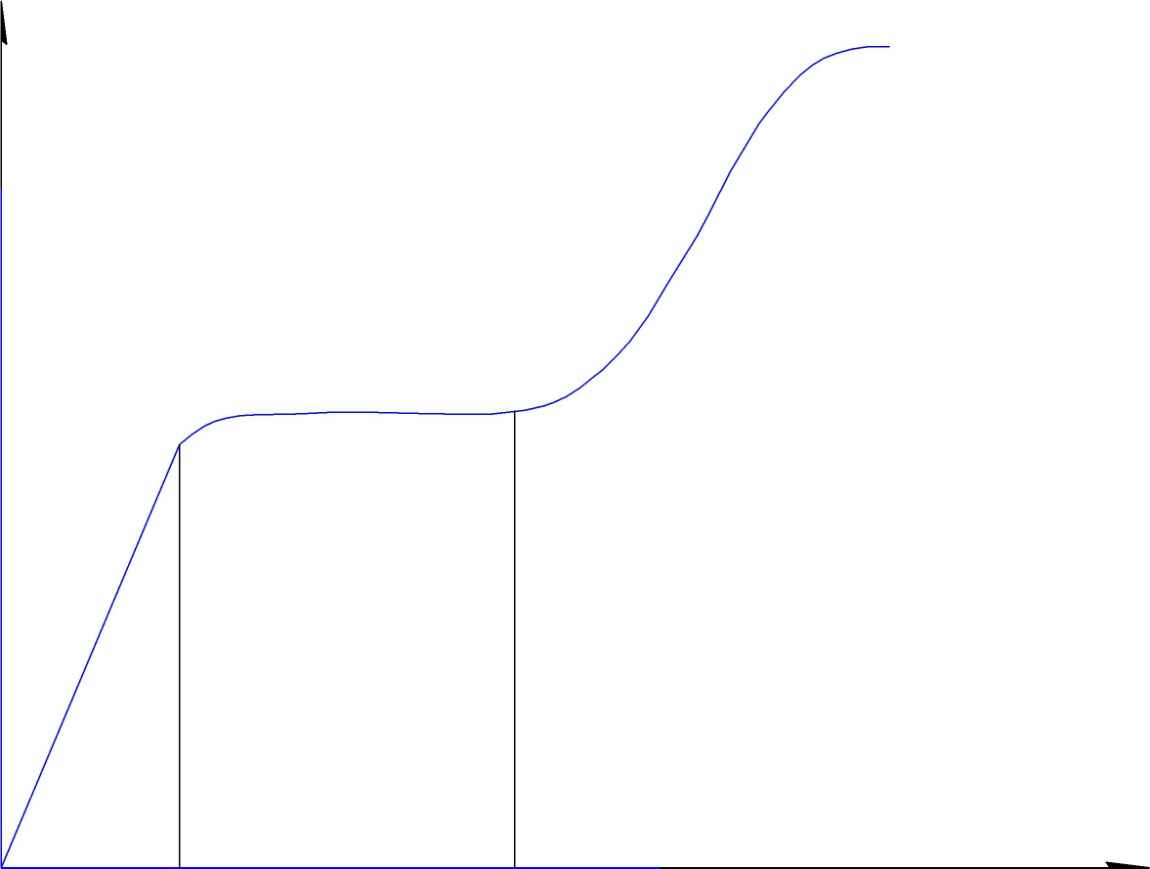







Рис.1 - график растяжения материала
В процессе работы нашего отдела постоянно возникают проблемы, и возникает необходимость расчетов как большинства агрегатов в целом, так и различных деталей в отдельности.
Множество деталей имеют одну или несколько осей симметрии. В программном комплексе ANSYS хорошо реализован расчет деталей имеющих ось симметрии. В данном проекте рассмотрены случаи, когда деталь имеет круговую ось симметрии. Это позволяет использовать для расчета только сечение. Весь расчет осесимметричных деталей можно условно разделить на следующие пункты :
- Выбор расчетной схемы;
- Нахождение оси симметрии, выделение сечения детали;
- Импортирование сечения детали из графического редактора в ANSYS;
- Определение характеристик материала детали. Выбор образцов для испытаний. Проведение испытаний и получение графика растяжения;
- Обработка результатов. Если материал очень пластичный, то требуется пересчет в истинные значения в зависимости от логарифмической деформации.
- Расчет детали в ANSYS, обработка полученных результатов, визуализация
1. Используемый материал
Рассматриваемые конструкции работают в зоне пластических деформаций, а мембрана прорыва разрушается. Так как мембрана прорыва срабатывает при достаточно низком давлении и должна сохранять целостность при заданных нагрузках, а диафрагма имеет большие пластические деформации, был выбран материал А5М.
А5М – это чистый первичный алюминий. Химический состав показывает, что содержание алюминия в нём достигает 99,5%. Это очень пластичный материал, его относительное удлинение при разрыве достигает 30-40%. Гарантированный предел прочности более 60 МПа.
В паспорте на поставку металлического проката указанные сведения не
дают возможности восстановить полноценно диаграмму деформирования при растяжении и доведении его до разрушения. Поэтому возникла необходимость в проведении опытов на растяжение
1.2 Получение диаграммы растяжения материала.
По ГОСТ 1497-73 была изготовлена партия из 5 образцов с головками из листа А5М, из которого были изготовлены мембраны. Опыты проводились на современном оборудовании позволяющем получить до 1500 точек диаграммы растяжения материала.
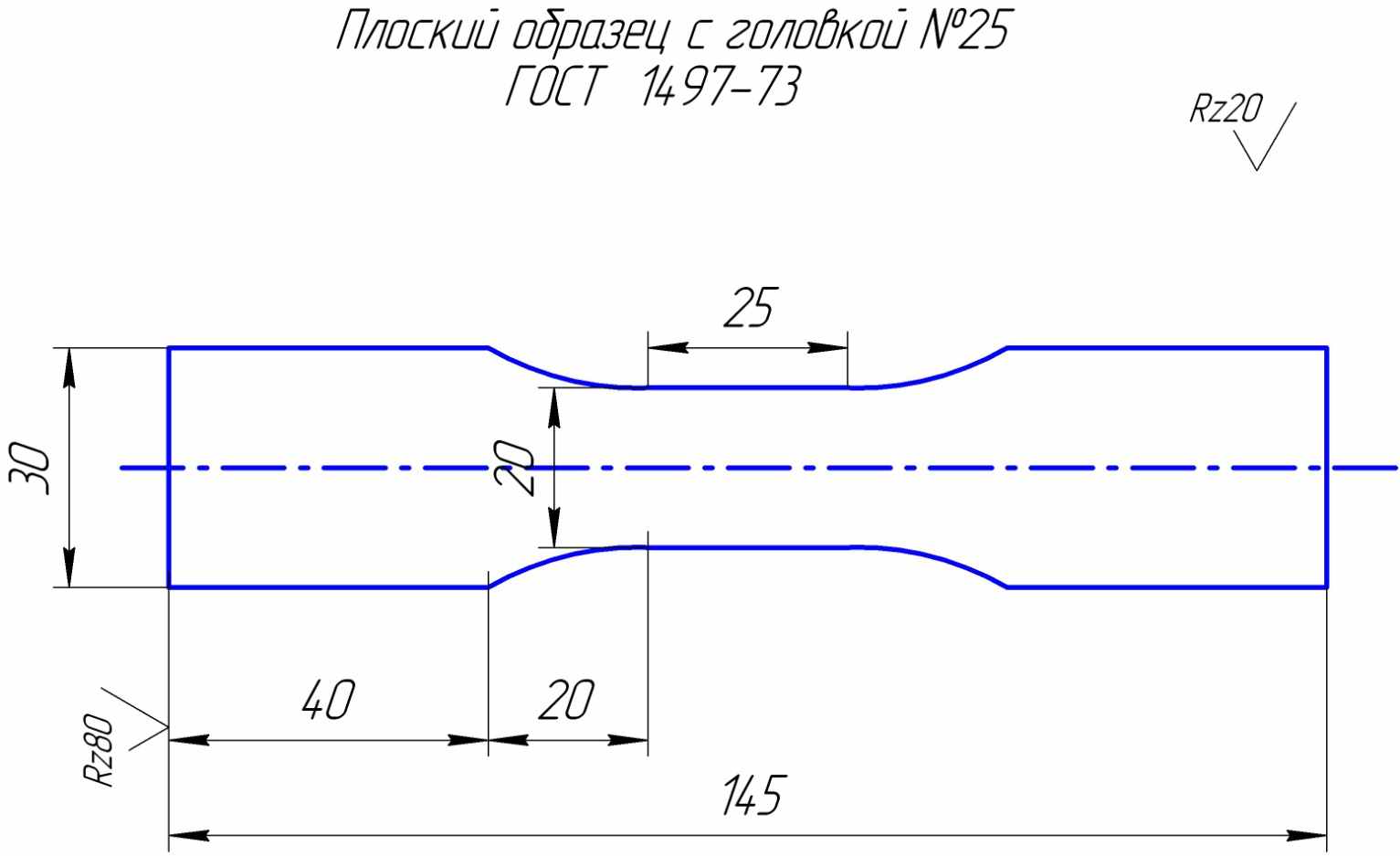
Рис. 1.1 – плоский образец с головкой
На рисунке 1.2 Была получена зависимость номинальных напряжений от относительного удлинения образца.. Из графика видно что предел прочности 79 МПа, а относительное удлинение при разрыве достигает 60%.
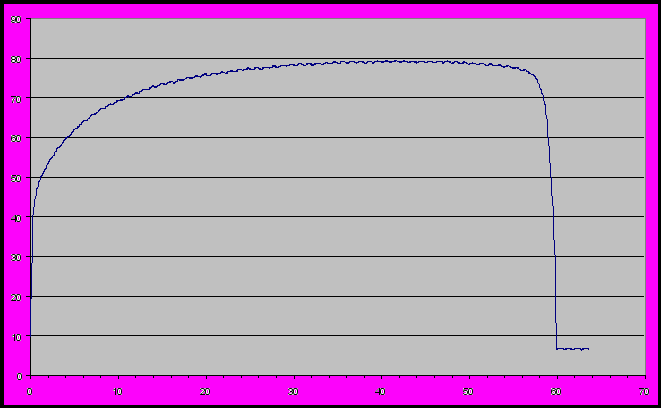
Рис. 1.2 – диаграмма растяжения
Из теории по Биргеру для очень пластичных материалов предлагаются формулы пересчёта напряжений в истинные значения в зависимости от логарифмической деформации. Эти формулы позволяют учесть утонение материала при сильных деформациях возникающих после образования шейки в образце. На рисунке 1.3 изображена диаграмма растяжения материала после пересчёта. В данном виде используя 50 точек можно применять данную диаграмму для расчёта в конечноэлементном пакете ANSYS.
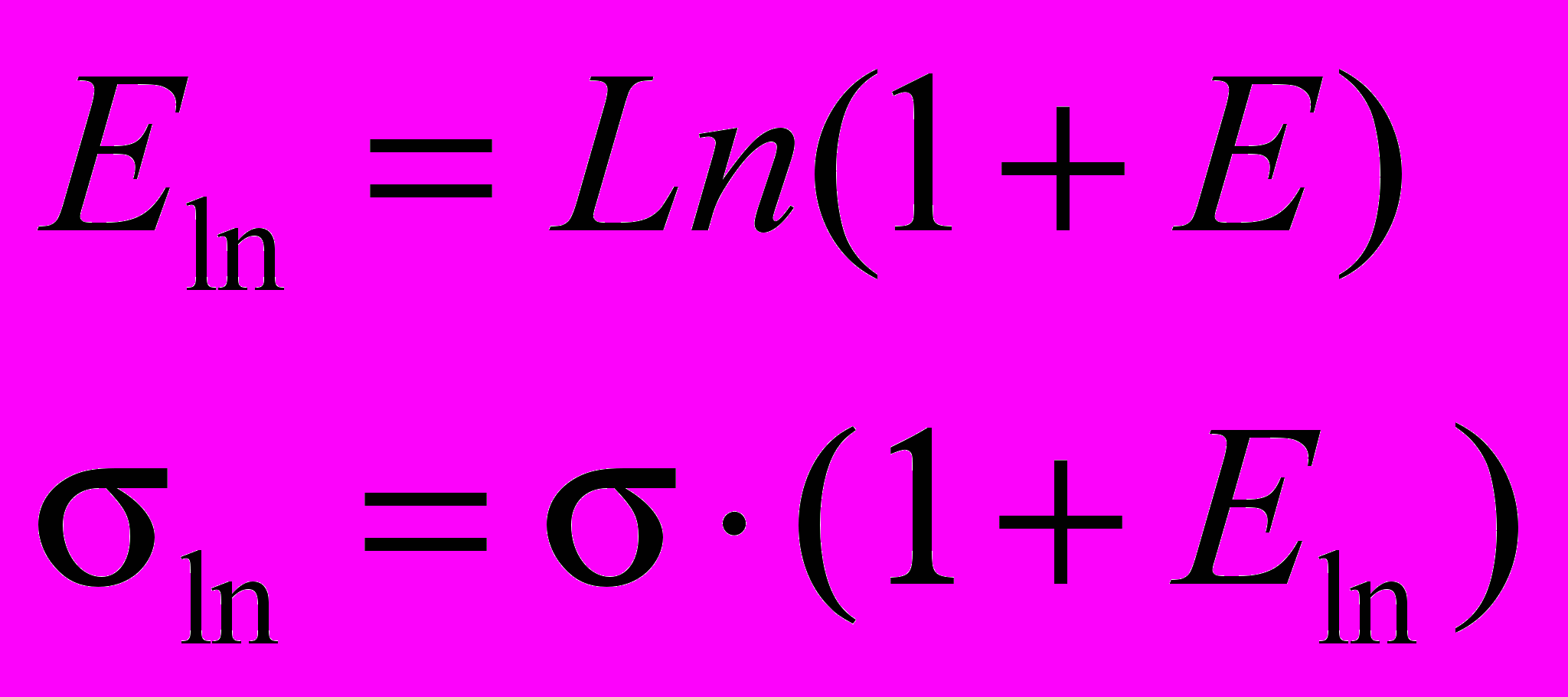
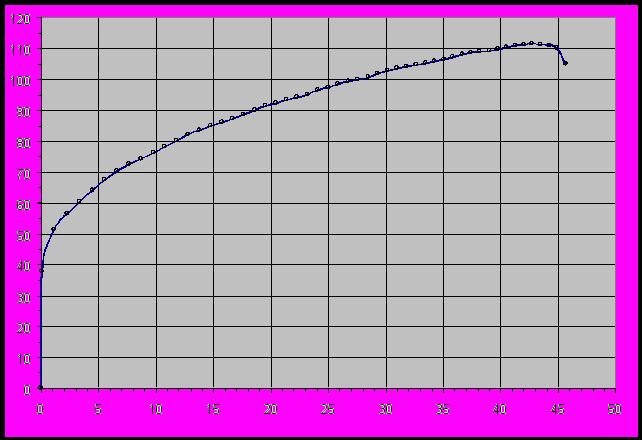
Рис. 1.3 – истинная диаграмма растяжения А5М
Таблица 1 – табличная запись кривой диаграммы растяжения материала
ε | σ |
0.055427 | 37.83563 |
1.158669 | 51.27709 |
2.268926 | 56.37762 |
3.370127 | 60.29249 |
4.461476 | 64.07963 |
5.542368 | 67.3522 |
6.608652 | 70.20017 |
7.667846 | 72.43454 |
8.710567 | 74.19841 |
9.743424 | 76.19523 |
10.77086 | 78.15689 |
11.78461 | 80.21293 |
12.78826 | 82.15658 |
13.7761 | 83.5669 |
14.76187 | 84.89475 |
15.73492 | 86.13831 |
16.70287 | 87.35808 |
17.65756 | 88.7693 |
18.60361 | 90.20604 |
19.53631 | 91.36179 |
20.46765 | 92.42741 |
21.38851 | 93.3885 |
22.30332 | 94.38707 |
23.20386 | 95.16972 |
24.09974 | 96.47399 |
24.98802 | 97.52904 |
25.86883 | 98.65909 |
26.73611 | 99.25445 |
27.60211 | 99.85782 |
28.45888 | 100.6824 |
29.30967 | 101.8127 |
30.15288 | 102.7656 |
30.98822 | 103.5627 |
31.81745 | 104.2632 |
32.63818 | 104.6924 |
33.45464 | 105.3061 |
34.26343 | 106.0214 |
35.06663 | 106.567 |
35.86396 | 107.4115 |
36.64902 | 108.2364 |
37.43599 | 108.6471 |
38.21226 | 109.1247 |
38.98383 | 109.3968 |
39.74668 | 109.7113 |
40.50617 | 110.4232 |
41.26215 | 110.9508 |
42.00949 | 111.3624 |
42.75196 | 111.5165 |
2 Мембрана прорыва
2.1 Назначение и описание конструкции
Мембрана прорыва предназначена для герметизации баков системы выдачи импульсов тяги с компонентами топлива при хранении после заправки до подготовки СВИТ к штатной работе.
В системе будет находиться 2 изделия:
- 1 на линии подачи окислителя
- 1 на линии подачи горючего.
Вскрытие мембраны прорыва должно производиться давлением компонентов при предварительном наддуве баков. Давление прорыва должно быть не более 1,1 МПа. Необходимо так же обеспечить герметичность топливных компонентов при давлении 0,3 МПа.
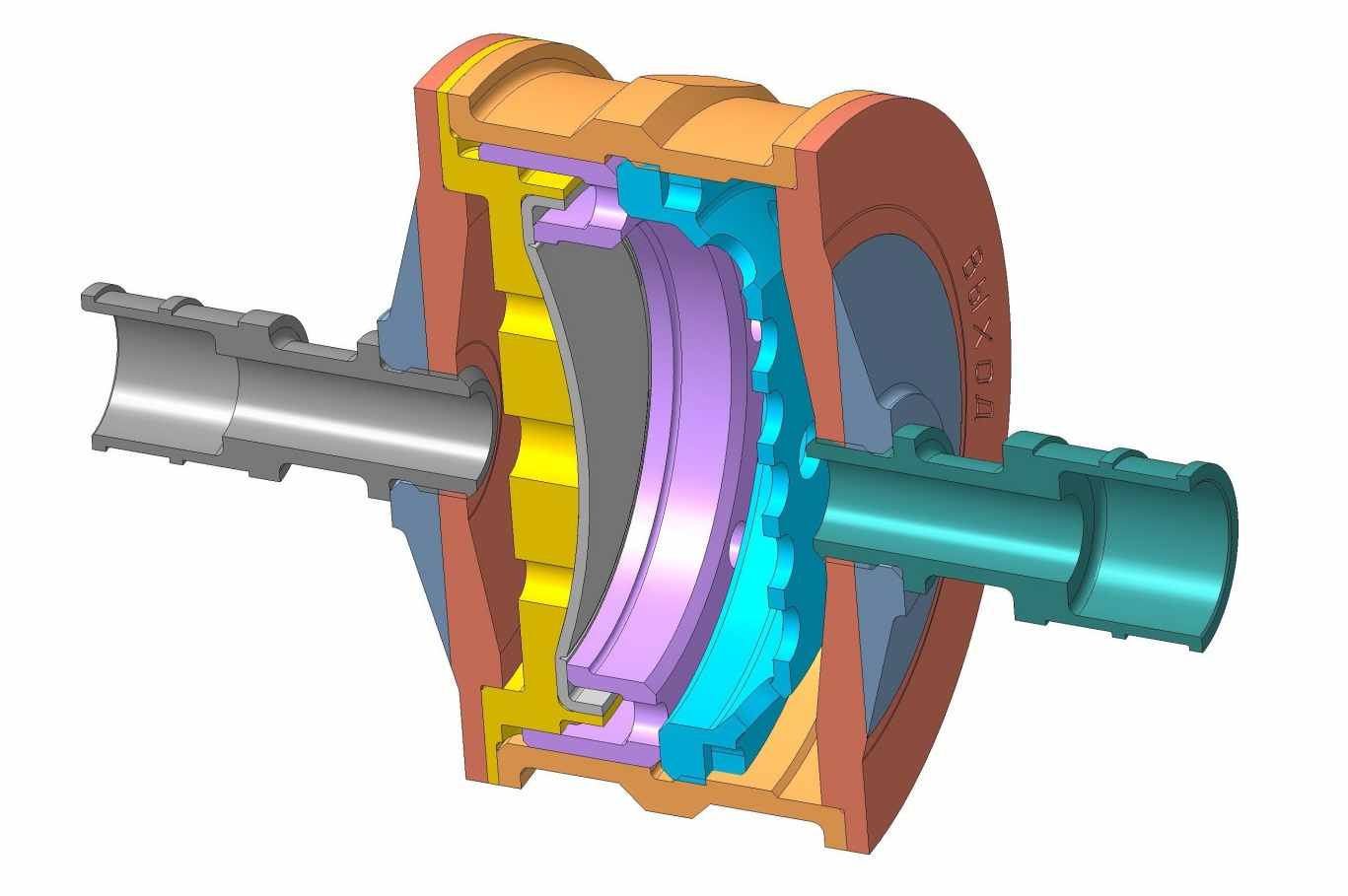
Рис. 2.1 – общий вид мембранного узла
На рисунке 2.2 представлены эскизы с размерами. Мембрана прорыва имеет сферическую область, которая позволяет ей держать определённое давление. По краям сферической части имеется насечка, по которой должен происходить прорыв. Стоит заметить, что имеется часть мембраны, на которой отсутствует насечка. Она составляет 30º и служит для того, что бы после срабатывания центральная часть мембраны не полностью перекрыла отверстия для подачи топлива. Прорезь имеет клиновидную форму, что служит концентратором напряжений в этой области.
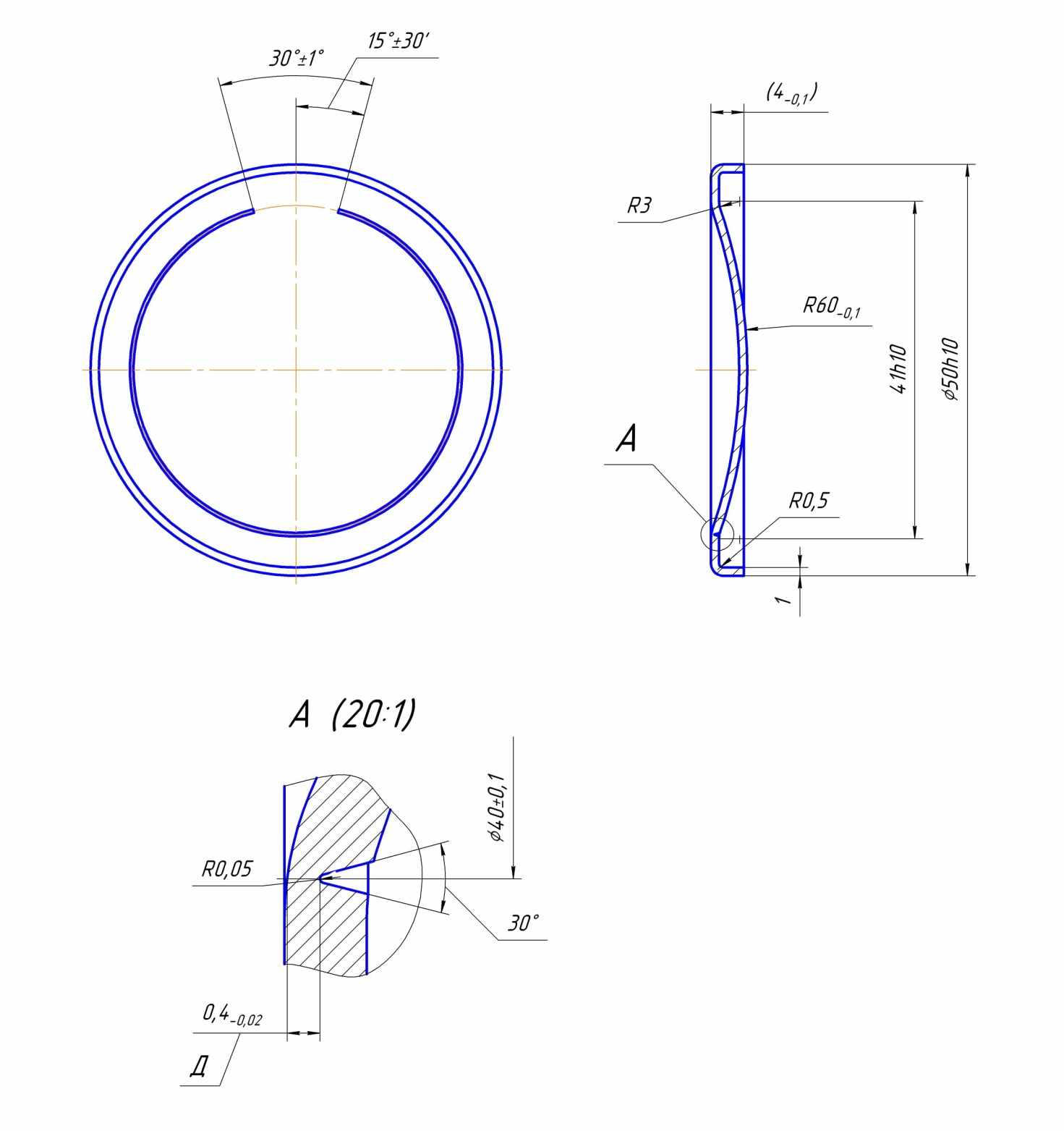
На рисунке 2.3 представлен общий вид мембраны прорыва.
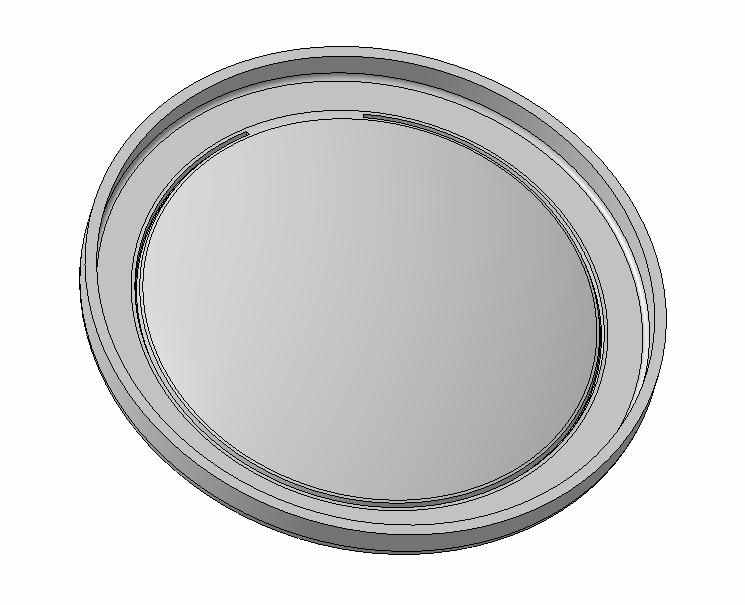
Рис. 2.3 – мембрана прорыва
2.2 Создание конечно-элементной модели мембраны прорыва.
2.2.1 Выбор расчётной схемы
В данном расчете мембраны прорыва будет использовано допущение, позволяющее сократить разработку конечно-элементной модели и время расчёта. В силу симметричности нагружения распределенным давлением по внутренней поверхности мембраны очевидно, что очаг разрушения зарождается в области, диаметрально противоположной участку мембраны без насечки. Данная область и прилегающая к ней часть мембраны работает в однородных условиях, что позволяет нам рассматривать задачу о нагружении мембраны в осесимметричной постановке. Кроме того в модель заложен учет геометрической и физической нелинейности поведения конструкции. Для создания конечно-элементной модели будет использовано только сечение в срезе мембраны рис. 2.4

Рис. 2.4 – поперечное сечение мембраны
2.2.2 Конечно-элементное моделирование.
Для решения данной задачи будет использоваться геометрия импортированная из программы Компас с помощью формата IGES. Для дальнейшего построения необходимо и достаточно импортировать набор линий образующий контур самой детали.
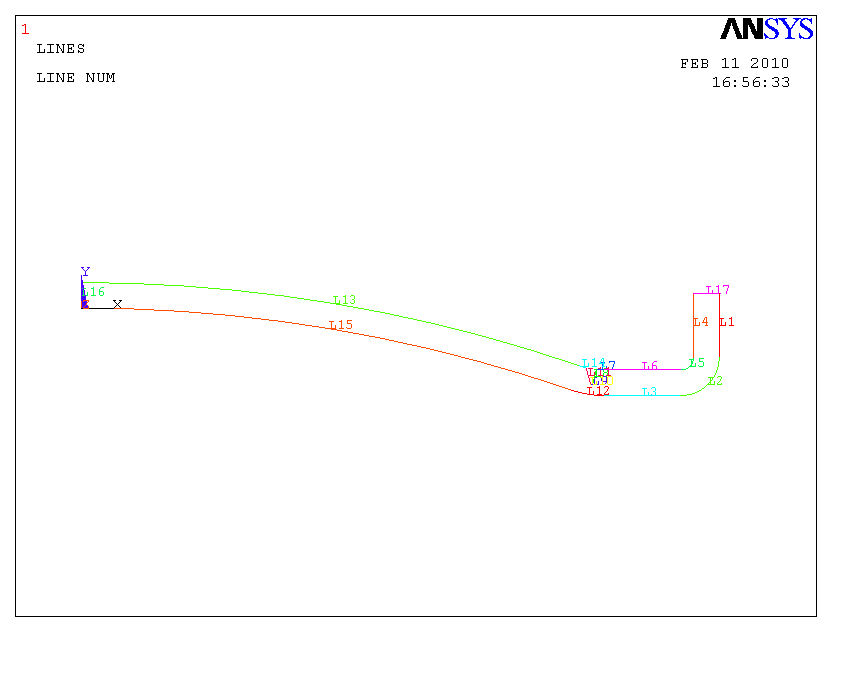
Рис. 2.5 – импортированное сечение
Далее из импортированных линий создаётся поверхность, которая в свою очередь уже разбивается на конечные элементы. В начале следует задать свойства материла во вкладке Material Models. Необходимо создать 2 свойства Linear Isotropic и задать модуль упругости равным Е=70000 МПа и коэффициент Пуассона μ=0,3. И второе свойство Multilinear Isotropic с опцией Stress versus Total Strain в которой и будет содержаться график растяжения материала. В нашем случае будет использовано 50 точек графика.
Для решения использовался плоский 8-ми узловой конечный элемент твёрдого тела PLANE 183 с включенной опцией K3 - Axisymmetric.
Это позволяет решать плоскую задачу с условиями круговой симметрии. На рисунке 2.6 представлена модель с готовой конечно-элементной сеткой.
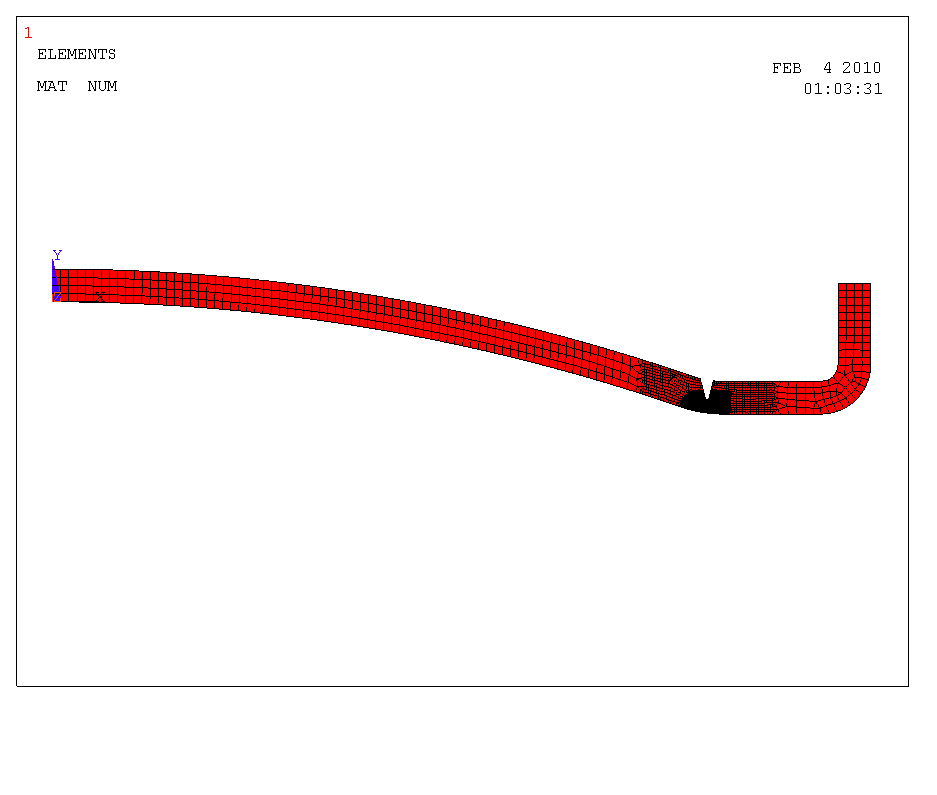
Рис. 2.6 – сетка конечных элементов
Следует отметить, что очень сильное сгущение сетки достигается в области прорези, так как именно там происходит разрушение. Сгущение сетки проводилось выборочно с использованием функции Refine. Preprocessor>Meshing>MeshTools>Refine>Elements.
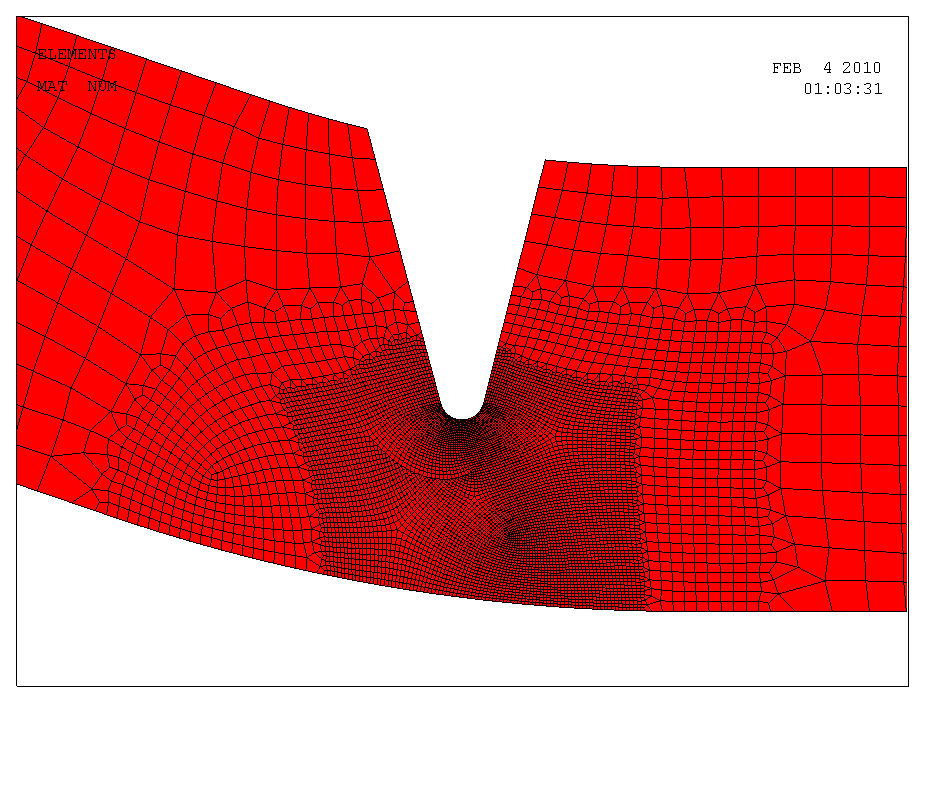
Рис. 2.7 – сгущение сетки в области прорези
2.2.3 Задание нагрузки, граничных условий и дополнительных опций решения.
Так как решается осесимметричная задача, необходимо кроме необходимых закреплений сечения так же закрепить сечение в районе, где Х=0 от перемещений по оси Х. Необходимо для обеспечения сплошности тела запрертить радиальные перемещения узлов, лежащих на оси вращения. В нашем случае закрепление по всем степеням свободы производится по краям мембраны в соответствии с геометрией и условиями защемления при сборке мембранного узла.
Нагрузки и закрепления задаются в меню Solution>Define Loads>Apply>Structural
После задания нагрузки и закреплений, необходимо включить опцию больших деформаций материала. Задача решается в квазистатической постановке, и время играет роль относительного параметра и фактически является множителем при нагрузке на текущем шаге.
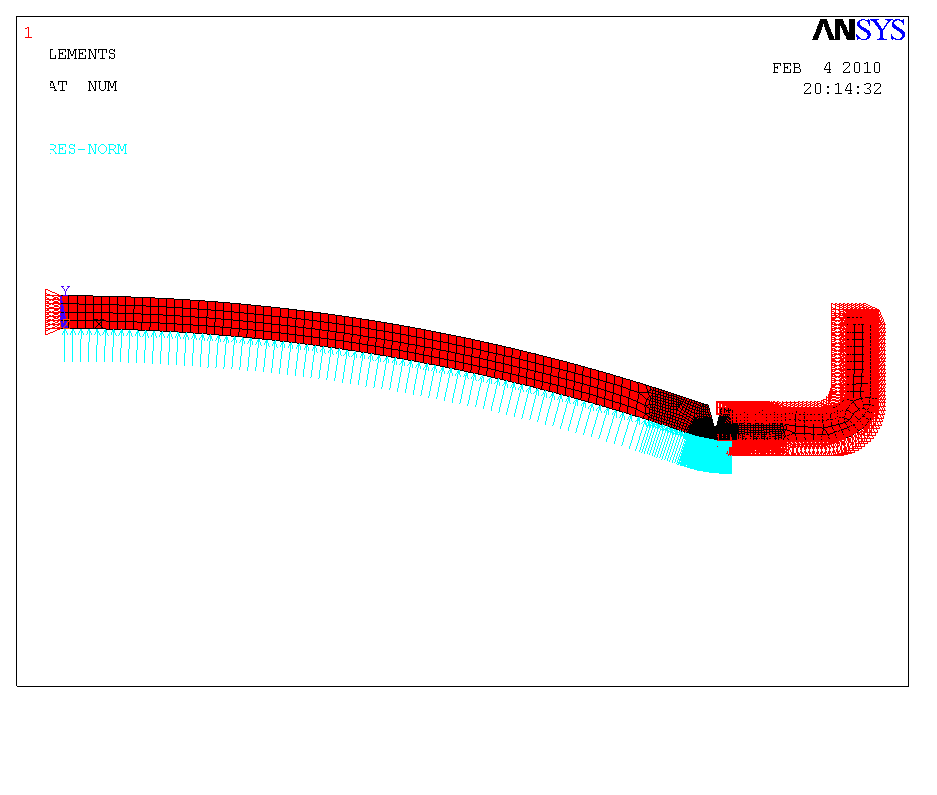
Рис. 2.8 – задание нагрузок и условий закрепления
2.2 Обработка результатов, изменение геометрии прорези
В результате расчета мы получили изменение напряженно-деформированного состояния по шагам нагружения.
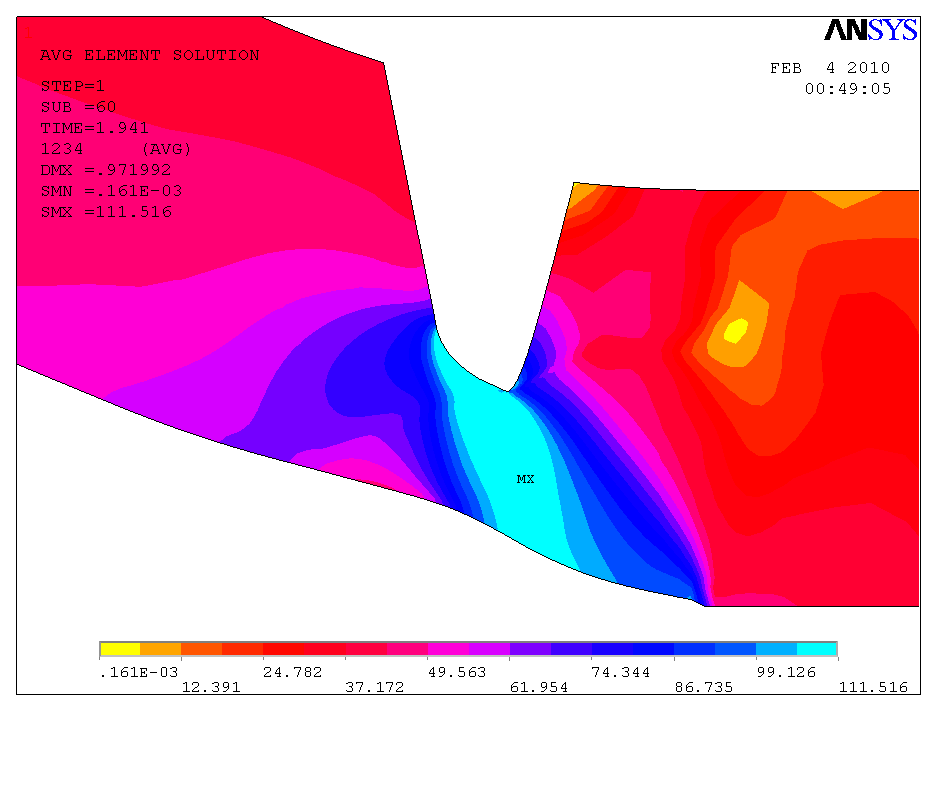
Рис. 2.9 – Эквивалентные напряжения по теории Мизеса
Из полученного результата видно что данная мембрана будет разрушаться при 1.9 МПа, что соответствует 19 атм. Такой результат не удовлетворяет техническому заданию и требует изменение конструкции мембраны.
Было внесено предложение об изменении формы прорези в сторону уменьшения остаточной толщины до 0,2 мм и увеличения ширины просеченной части до 0,4 мм
На рисунке 2.10 представлен эскиз с новой геометрией прорези.
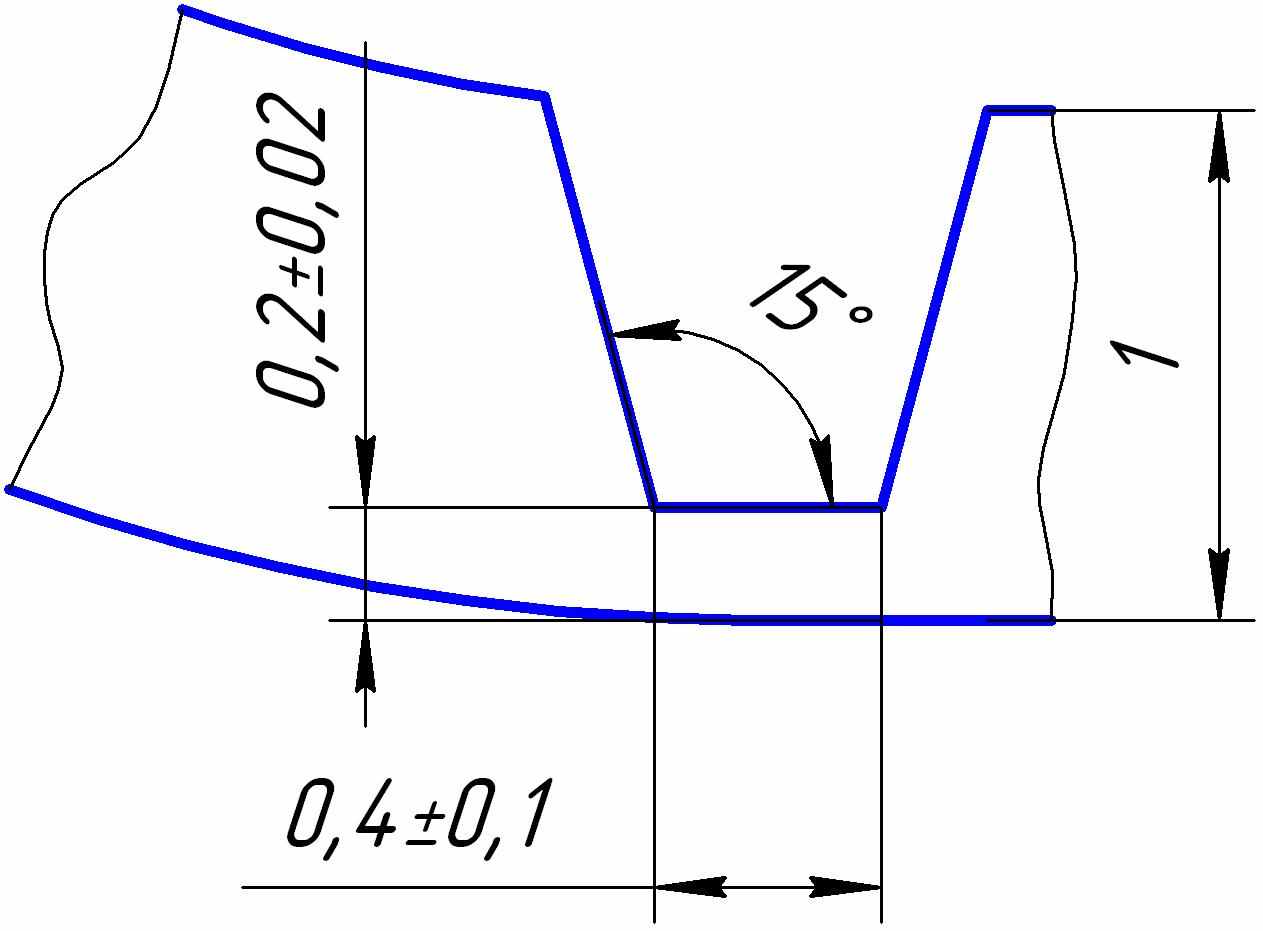
Рис. 2.10 – эскиз новой прорези
2.3 Повторное решение мембраны прорыва с изменённой геометрией с помощью функции «смерть элементов».
Повторное решение данной задачи осуществляется с изменённой геометрией и применением опции «смерть элементов».
Смерть элементов позволяет отследить последовательное разрушение мембраны прорыва, путём отключения из расчёта элементов, не проходящих заданный критерий.
В первом приближении задаётся нагрузка близкая к ожидаемой разрушающей и производится решение. В данном случае была задана нагрузка 0,85 МПа. После 1 шага решения создаётся таблица элементов. General Postproc>Element Table> Define Table. В ней выбирается критерий по-которому будут исключаться элементы. В данном расчёте были выбраны эквивалентные напряжения по Мизесу. Stress>von Mises SEQV. Далее необходимо выбрать элементы, не проходящие данный критерий и отрисовать их. Select>Entities. В появившемся меню выбираем элементы по результату. Elements> By Results. Далее вводим критическое напряжение для нашего материала, которое составляет 110 МПа и нажимаем кнопку Plot. Это позволяет скрыть все остальные элементы, оставив лишь не проходящие критерий. Далее с помощью командной строки вводится команда Ekill,ALL. Далее выбираются снова все элементы и проводится решение с новой нагрузкой. После нескольких приближений можно отчетливо видеть картину лавинообразного разрушения мембраны прорыва. Иными словами при появлении первых исключенных элементов и признаков образовавшейся трещины, другие элементы выбывают из расчета при достаточно малом приращении давления. Иллюстрации данного решения представлены на рисунках 2.11, 2.12, 2.13,2.14
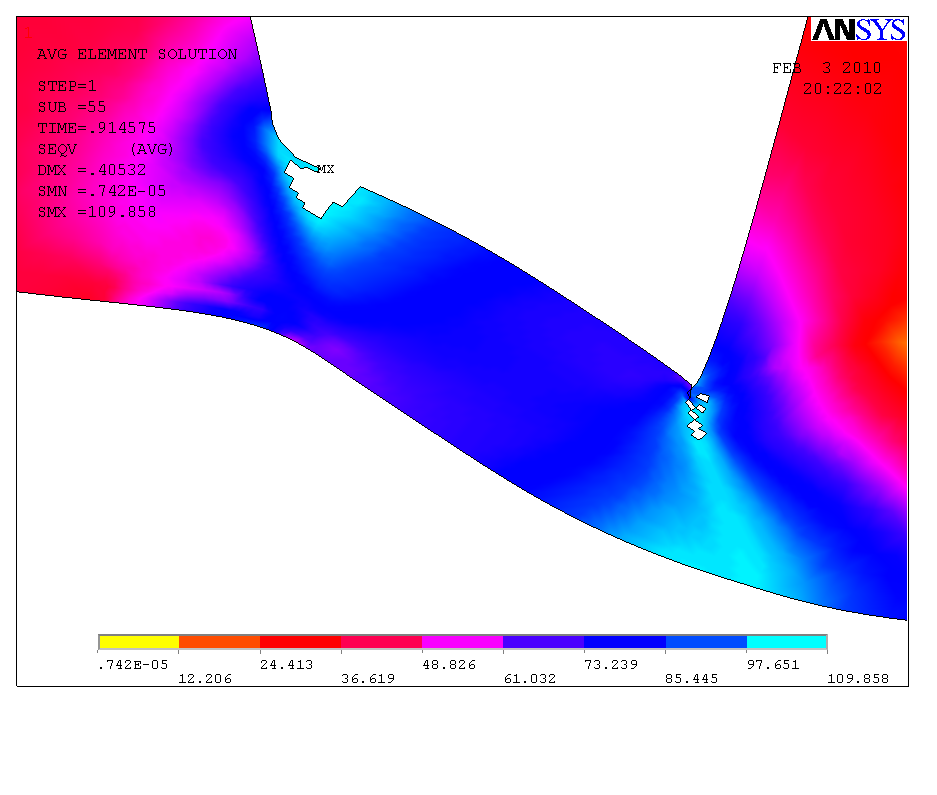
Рис. 2.11 – разрушение мембраны давление 0,91 МПа
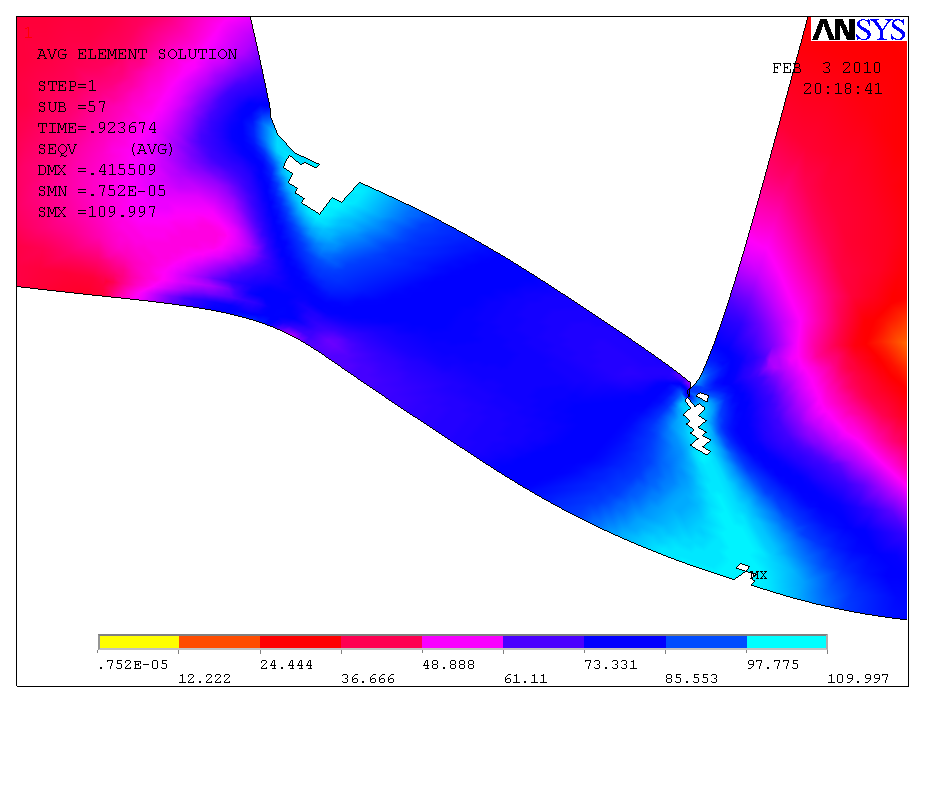
Рис. 2.12 – разрушение мембраны давление 0,923 МПа
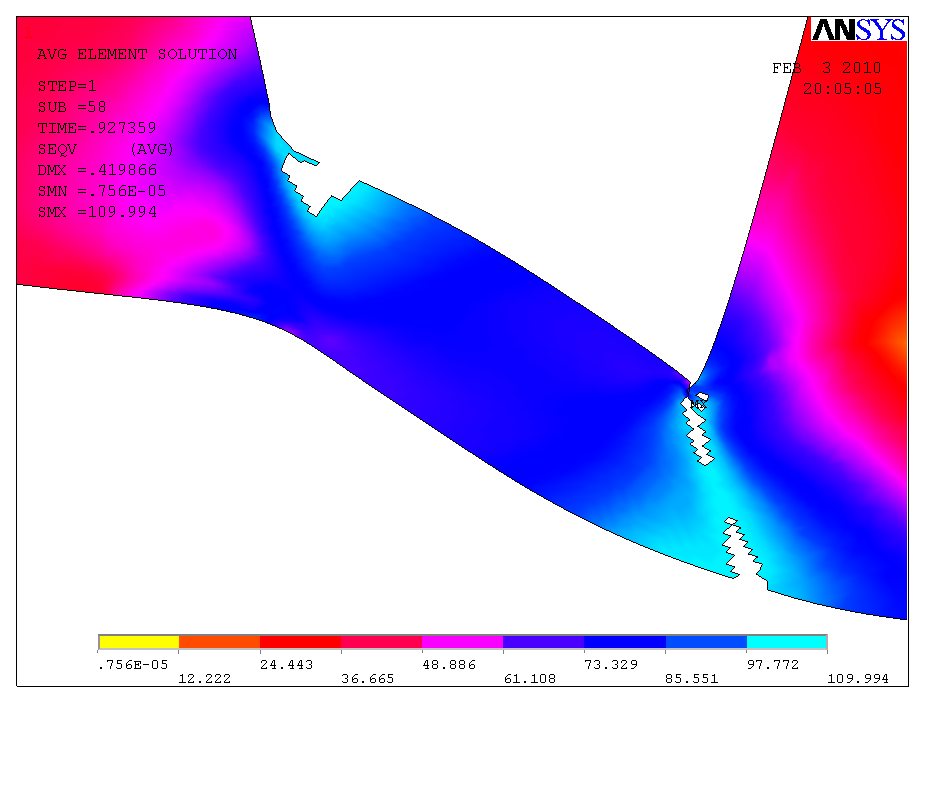
Рис. 2.13 – разрушение мембраны давление 0,927 МПа
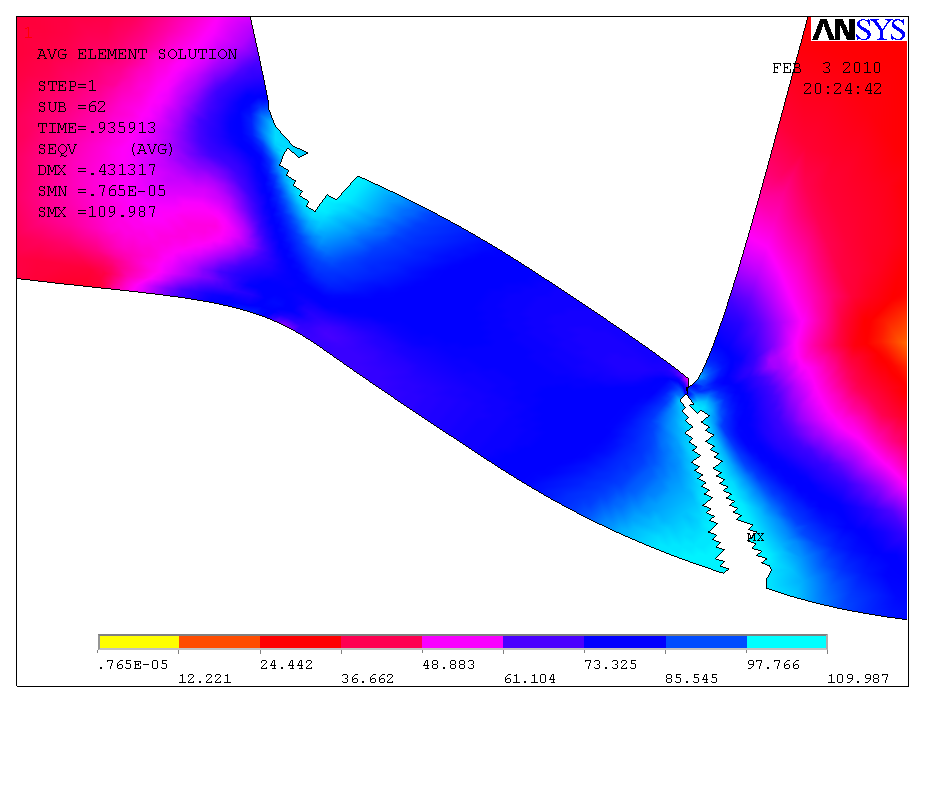
Рис. 2.14 – разрушение мембраны давление 0,935 МПа
Из полученных результатов видно, что разрушающим давлением для данной мембраны прорыва является 0,93 МПа, что удовлетворяет техническому заданию.
При исследовании мембраны прорыва была подобрана форма насечки, при которой мембрана прорыва срабатывает в нужном диапазоне давления. Сделаны предложения по доработке конструкции мембранного узла.
3 Анализ работоспособности диафрагмы сферического топливного бака.
3.1 Назначение и описание диафрагмы сферического топливного бака.
Металлический разделитель представляет собой штампованную конструкцию, состоящую из трёх участков: сферического, тороидального и конического. Диафрагма выполнена из материала А5М. Это позволяет ей работать в области пластических деформаций без разрушения, не нарушая герметичность между газовой и жидкостной полостями.
На рисунке. 3.1 представлен общий вид сферического топливного бака.
На рисунке 3.2 представлен бак с диафрагмой.
На рисунке 3.3 представлена диафрагма.
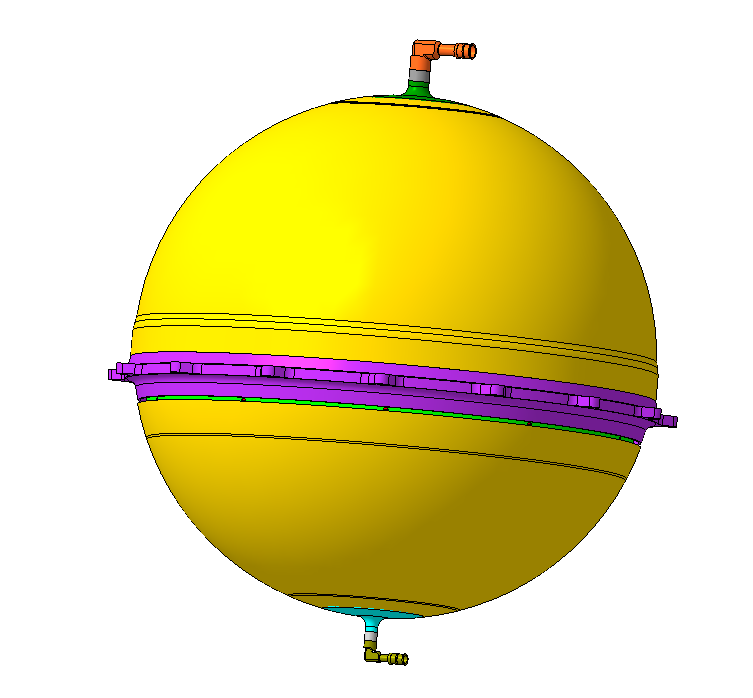
Рисунок 3.1 – Сферический топливный бак
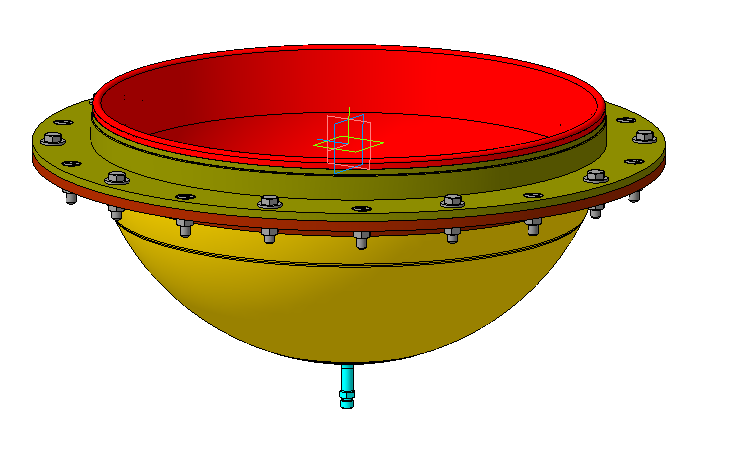
Рисунок 3.2 – Диафрагма с баком
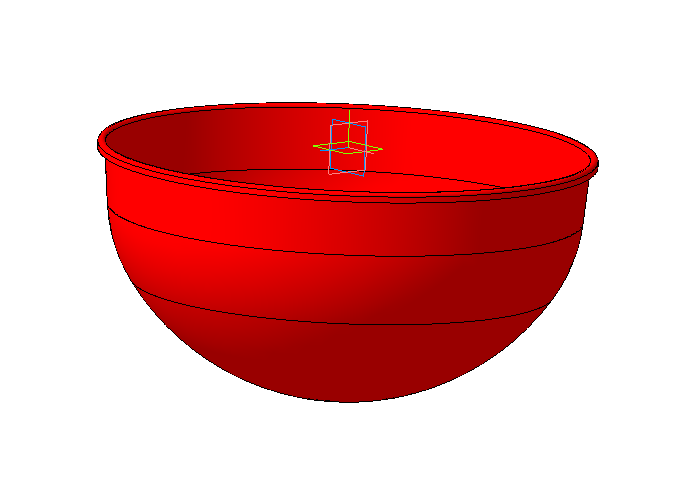
Рисунок 3.3 - Диафрагма
На рисунке 3.4 представлен эскиз топливного бака с диафрагмой.
Р
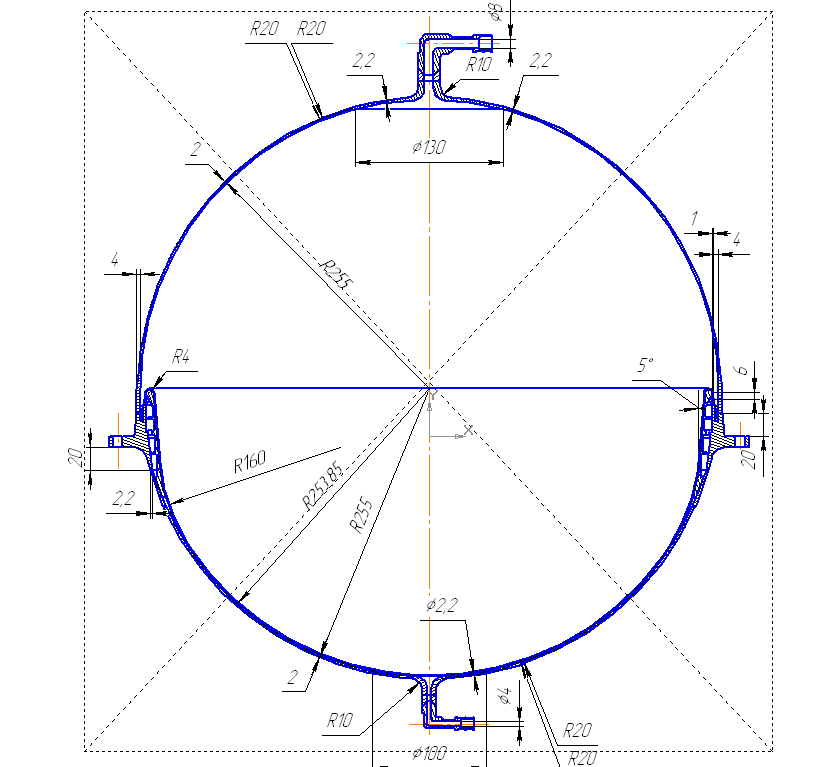
3.2 Создание конечно-элементной модели диафрагмы.
3.2.1 Выбор расчётной схемы
Для решения использовался плоский 8-ми узловой конечный элемент твёрдого тела PLANE 183 с включенной опцией K3 - Axisymmetric.
Это позволяет решать плоскую задачу с условиями круговой симметрии.
Так как решается осесимметричная задача, необходимо кроме необходимых закреплений сечения так же закрепить сечение в районе, где Х=0 от перемещений по оси Х. Необходимо для обеспечения сплошности тела запрертить радиальные перемещения узлов, лежащих на оси вращения. В нашем случае закрепление по всем степеням свободы производится в месте сварки диафрагмы с баком в соответствии с геометрией и условиями защемления при сборке бака.
Нагрузки и закрепления задаются в меню Solution>Define Loads>Apply>Structural
После задания нагрузки и закреплений, необходимо включить опцию больших деформаций материала. Задача решается в квазистатической постановке, и время играет роль относительного параметра и фактически является множителем при нагрузке на текущем шаге.
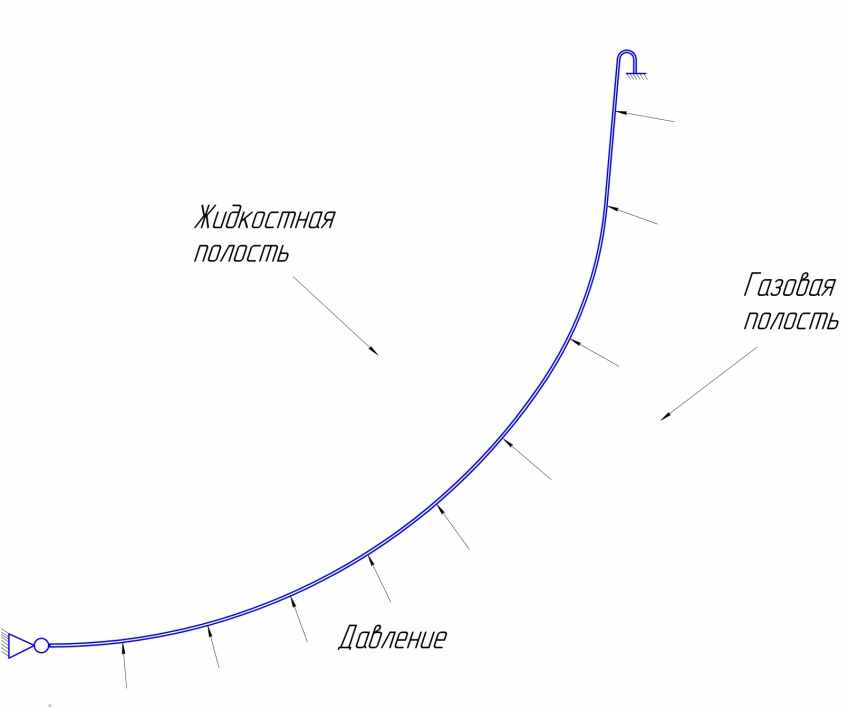
Рис. 3.1 - Сечение диафрагмы
На рисунке 3.1 представлена импортированная модель с заданными граничными условиями и нагрузкой. В качестве нагрузки используется максимально допустимый перепад между газовой и жидкостной полостями 0,2 МПа. Давление задавалось по внешней кромке диафрагмы.
Граничные условия задаются таким образом, что в районе сварного шва закрепление соответствует полной заделке. На полюсе блокируется поступательное движение по оси Х, что необходимо для создания условий симметрии.
3.2.2 Конечно-элементное моделирование и задание граничных условий
Для решения данной задачи будет использоваться геометрия импортированная из программы Компас с помощью формата IGES. Для дальнейшего построения необходимо и достаточно импортировать набор линий образующий контур самой детали.
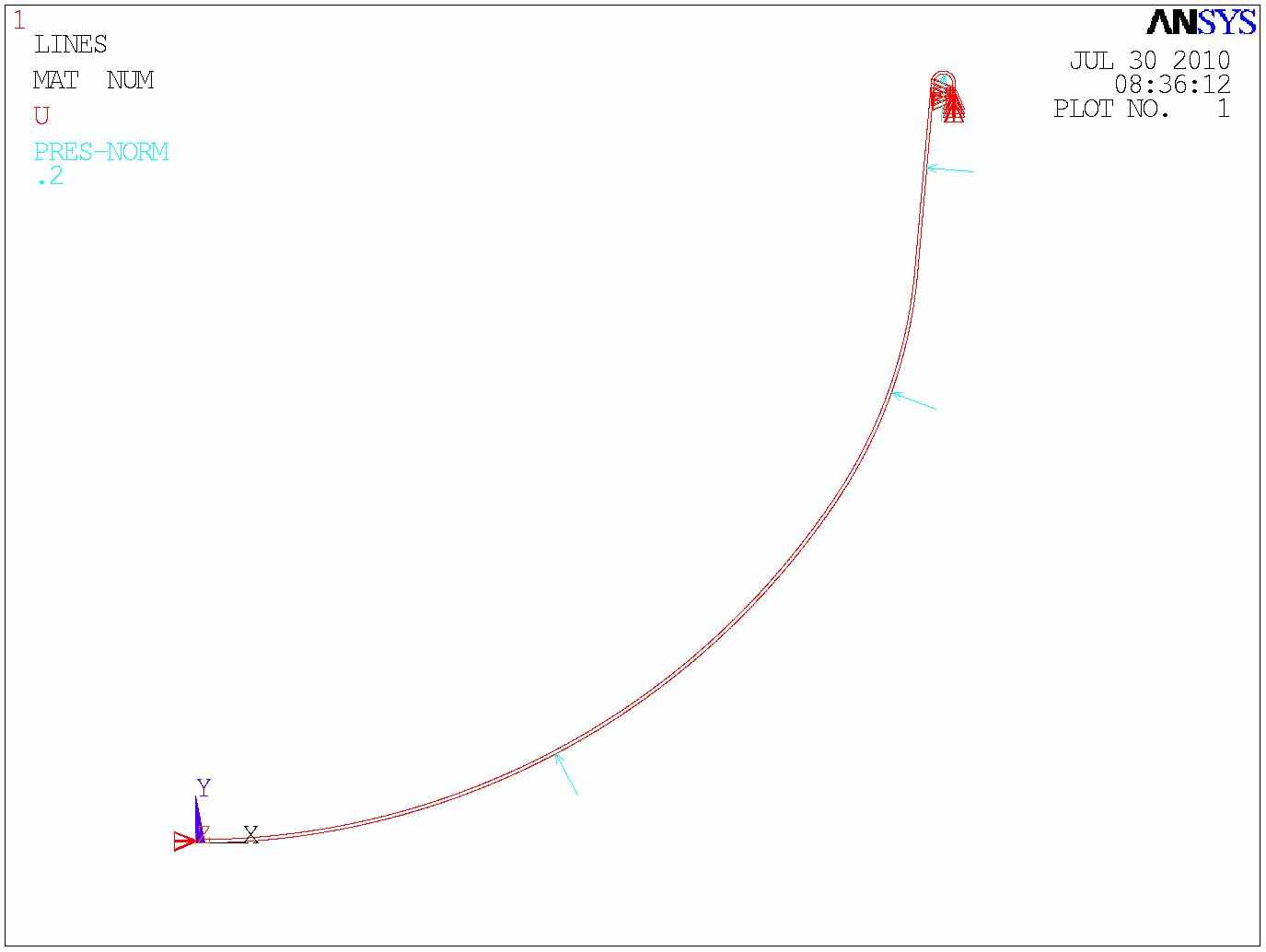
Рис. 3.2 – импортированное сечение
Далее из импортированных линий создаётся поверхность, которая в свою очередь уже разбивается на конечные элементы. В начале следует задать свойства материла во вкладке Material Models. Необходимо создать 2 свойства Linear Isotropic и задать модуль упругости равным Е=70000 МПа и коэффициент Пуассона μ=0,3. И второе свойство Multilinear Isotropic с опцией Stress versus Total Strain в которой и будет содержаться график растяжения материала. В нашем случае будет использовано 50 точек графика.
Для решения использовался плоский 8-ми узловой конечный элемент твёрдого тела PLANE 183 с включенной опцией K3 - Axisymmetric.
Это позволяет решать плоскую задачу с условиями круговой симметрии.
Так как решается осесимметричная задача, необходимо кроме необходимых закреплений сечения так же закрепить сечение в районе, где Х=0 от перемещений по оси Х. Необходимо для обеспечения сплошности тела запрертить радиальные перемещения узлов, лежащих на оси вращения. В нашем случае закрепление по всем степеням свободы производится в месте сварки диафрагмы с баком в соответствии с геометрией и условиями защемления при сборке бака.
Нагрузки и закрепления задаются в меню Solution>Define Loads>Apply>Structural
После задания нагрузки и закреплений, необходимо включить опцию больших деформаций материала. Задача решается в квазистатической постановке, и время играет роль относительного параметра и фактически является множителем при нагрузке на текущем шаге.
3.2.3 Обработка результатов, бесконтактного деформирования
Для расчёта использовалось 5900 конечных элементов, что обеспечивает приемлемую сходимость результата. Позволяет получить распределение напряжений по всей толщине диафрагмы и полностью отследить её деформирование. Расчёт проведён с учётом физической и геометрической нелинейности.
На рисунках 3.3 - 3.14 представлено распределение напряжений по сечению диафрагмы и её деформирование.
. Просмотр результатов для каждого конкретного шага осуществляется в общем постпроцессоре General PostProc.. General Postproc>Read Results>by Pick. Деформацию удобно оценивать по величине экивалентных напряжений по 4 теории Мизеса
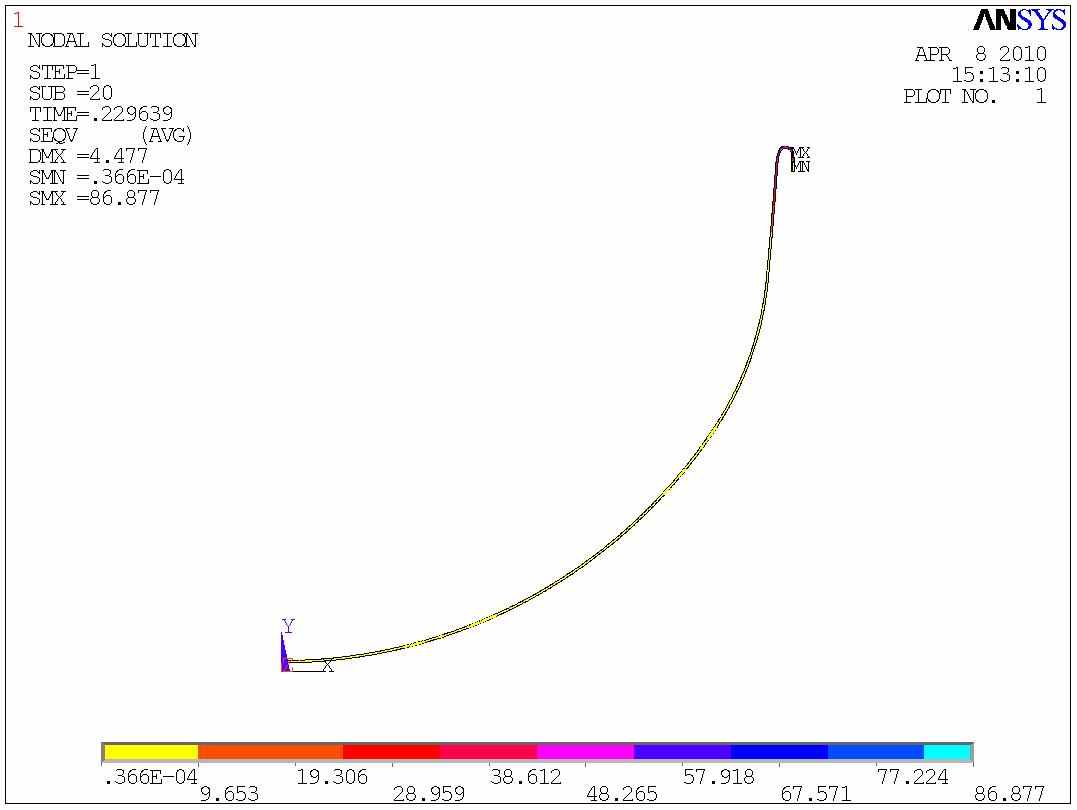
Рисунок 3.3 - Поднятие полюса на 4,48 мм
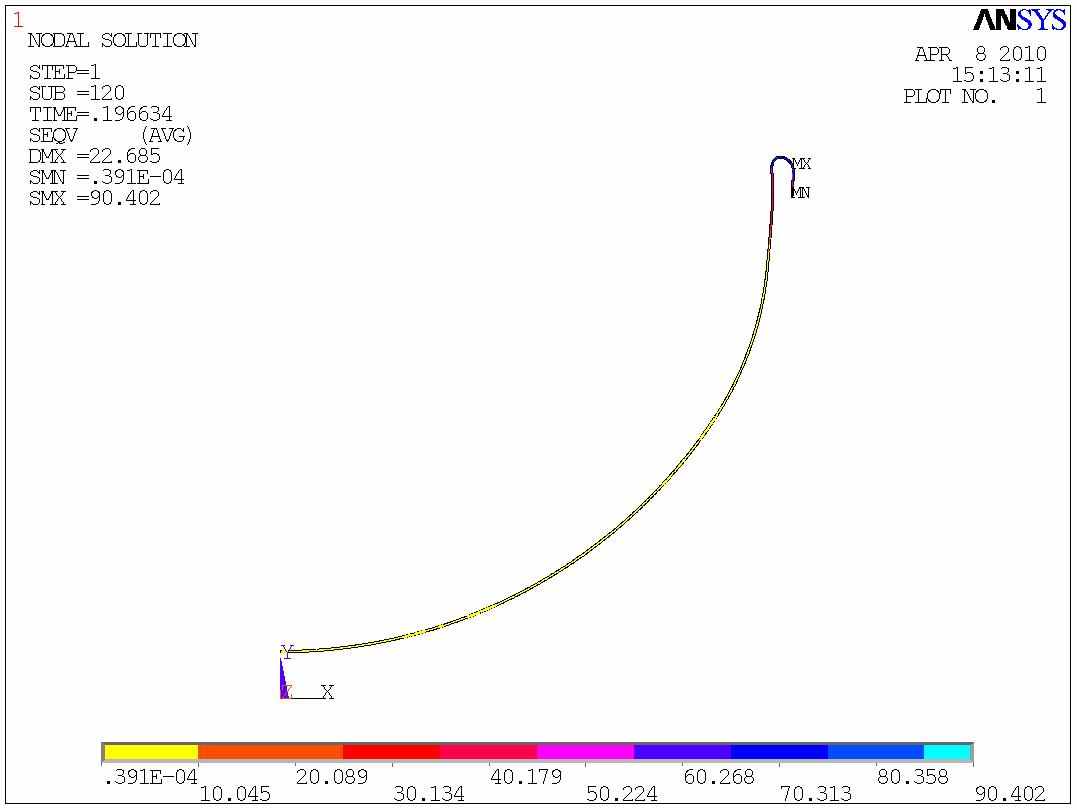
Рисунок 3.4 - Поднятие полюса на 22,685 мм
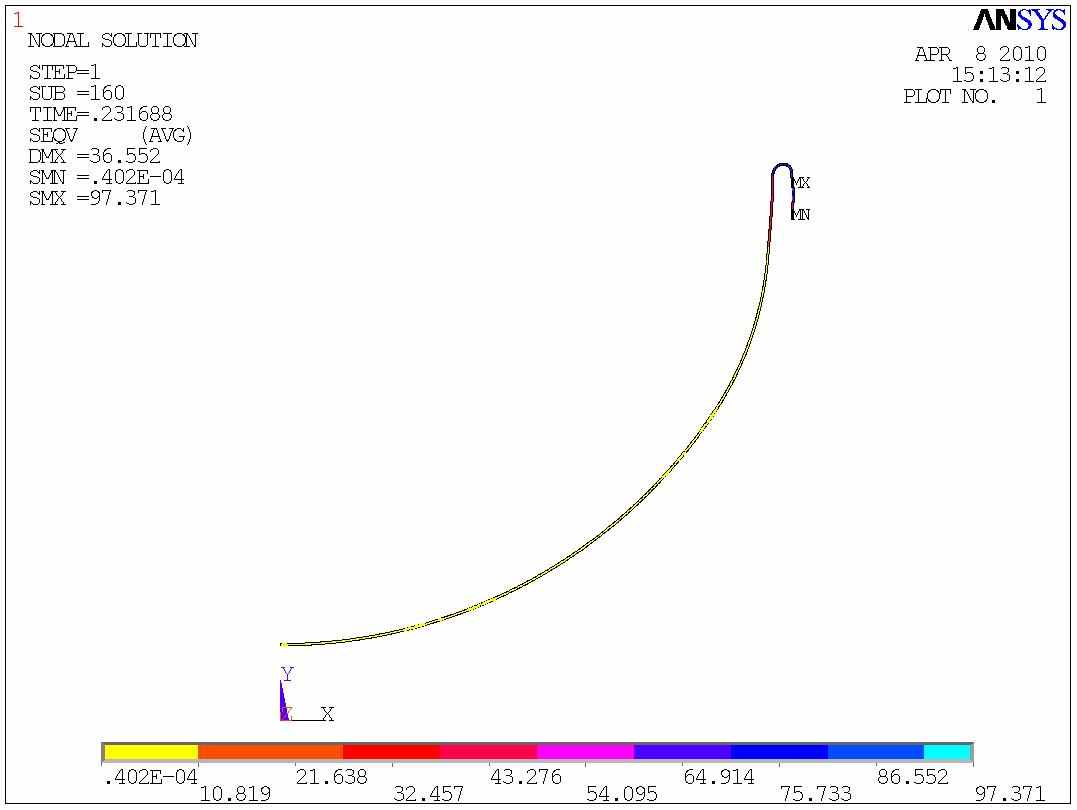
Рисунок 3.5 - Поднятие полюса на 36,552 мм
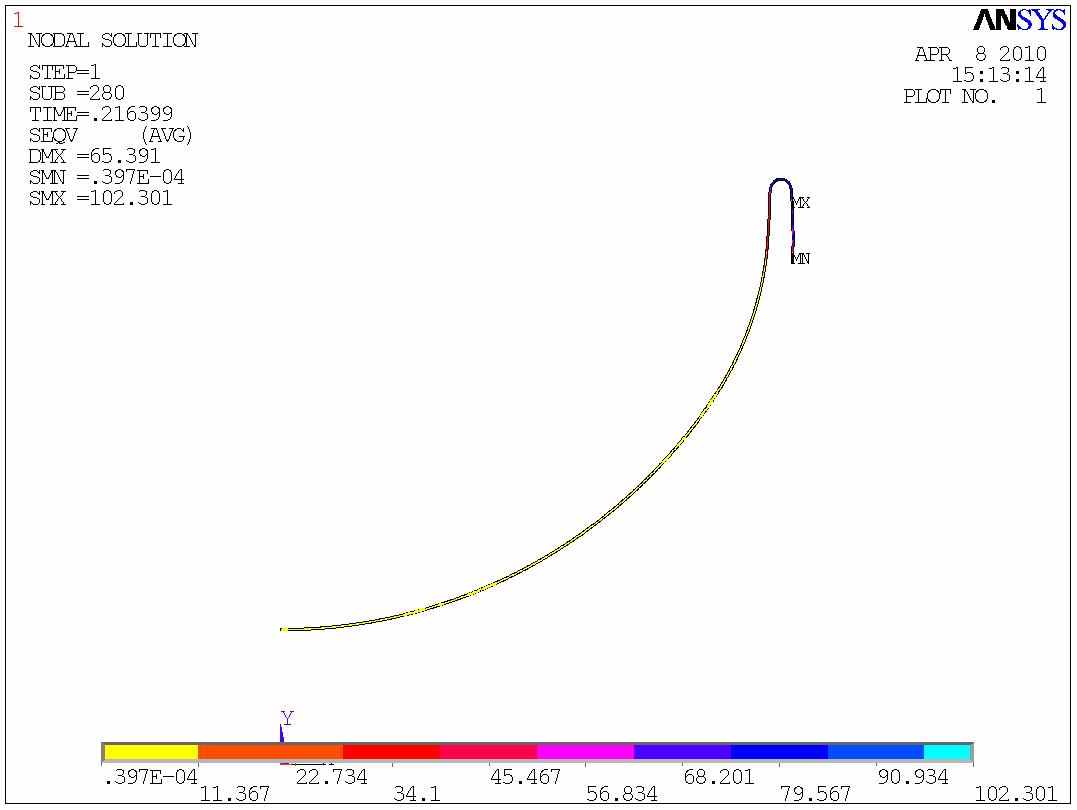
Рисунок 3.6 - Поднятие полюса на 65,4 мм
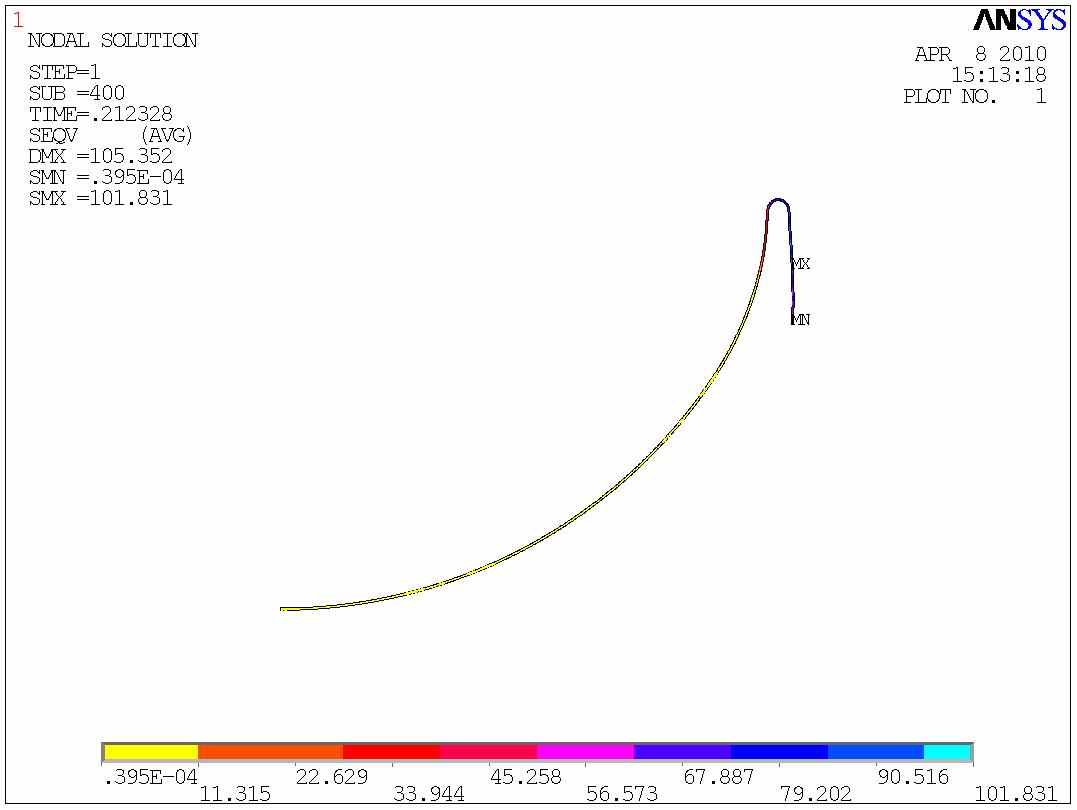
Рисунок 3.7 - Поднятие полюса на 105,3 мм
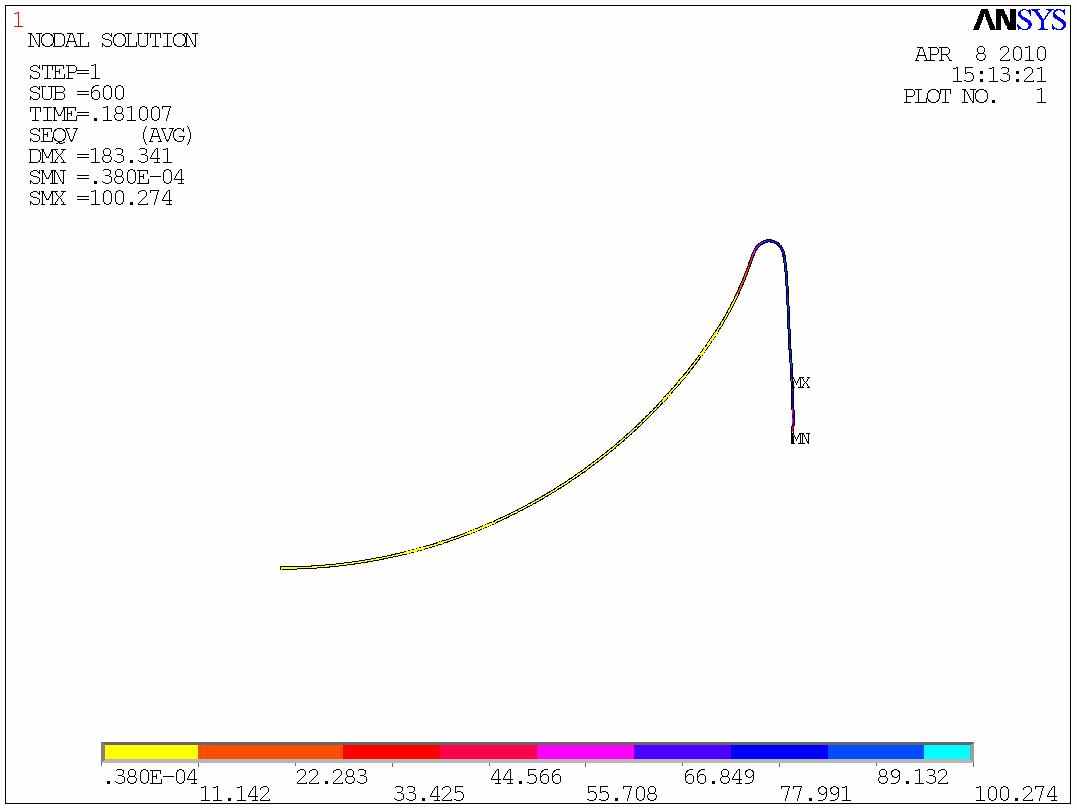
Рисунок 3.8 - Поднятие полюса на 183 мм
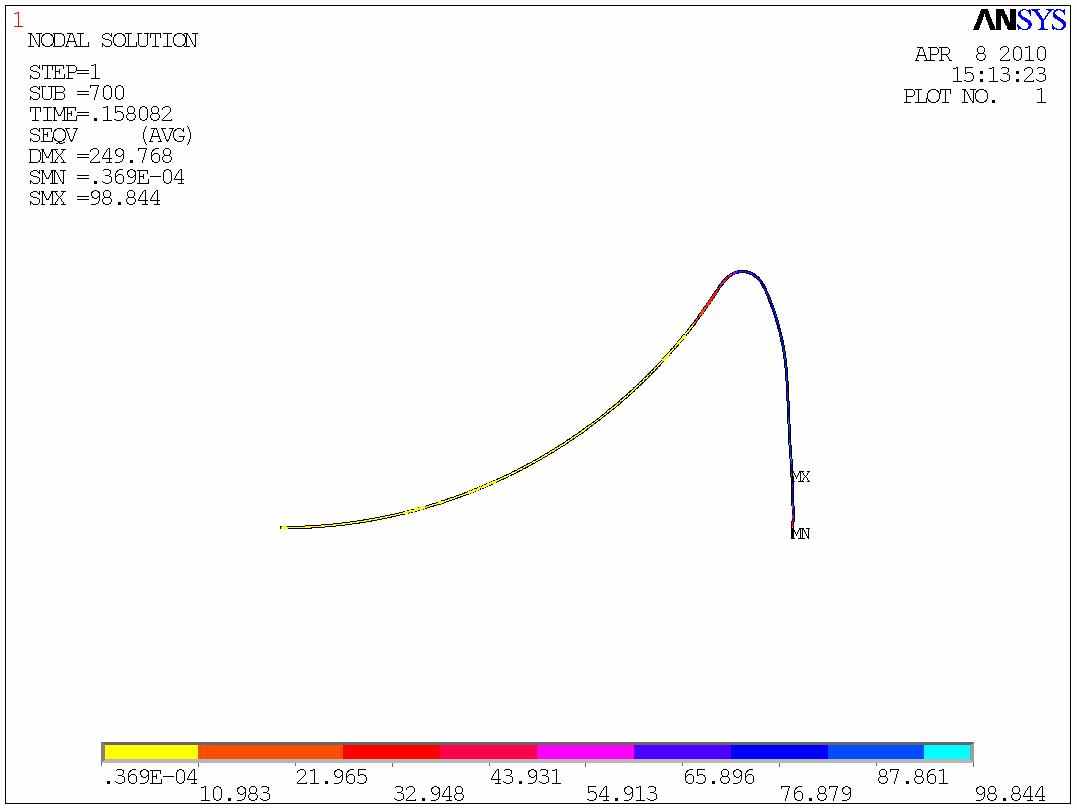
Рисунок 3.9 - Поднятие полюса на 250 мм
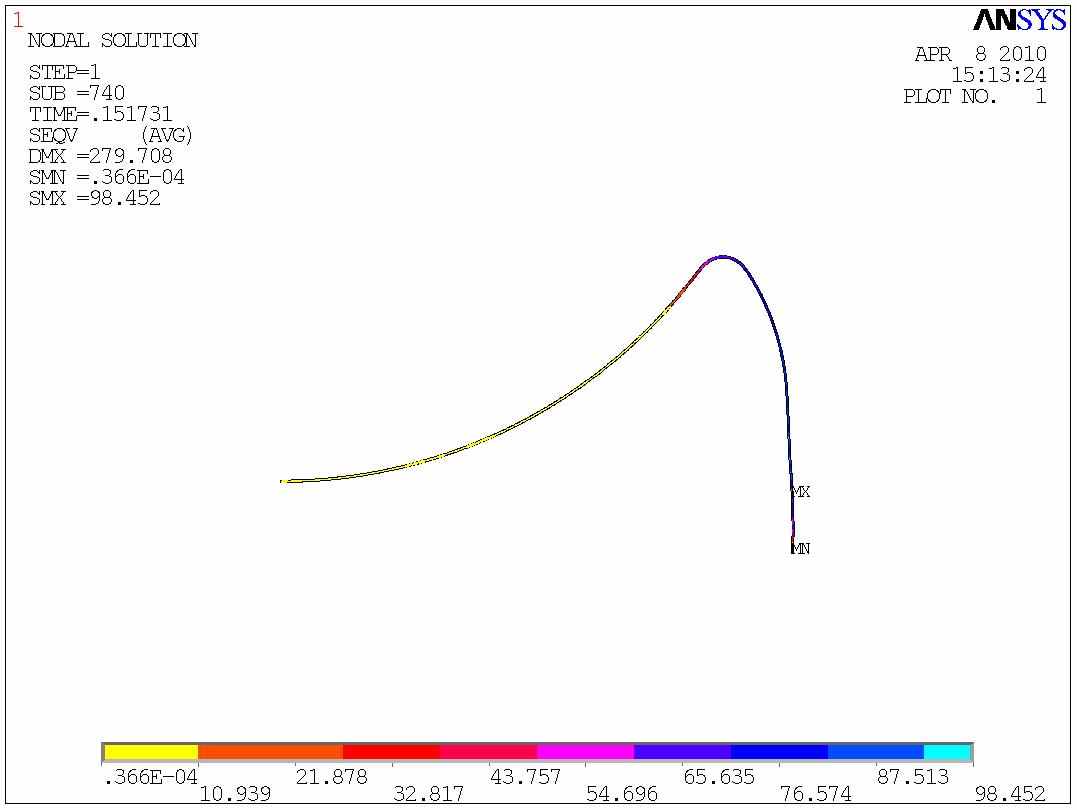
Рисунок 3.10- Поднятие полюса на 279,7 мм
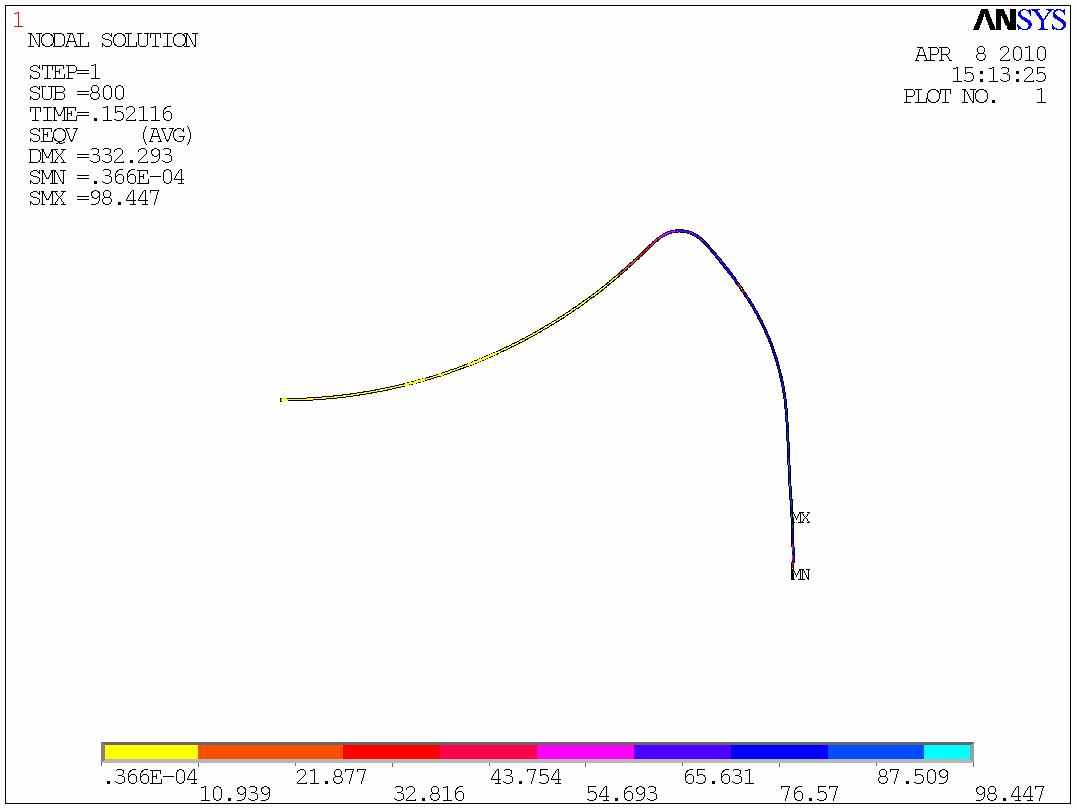
Рисунок 3.11 - Поднятие полюса на 332,29 мм
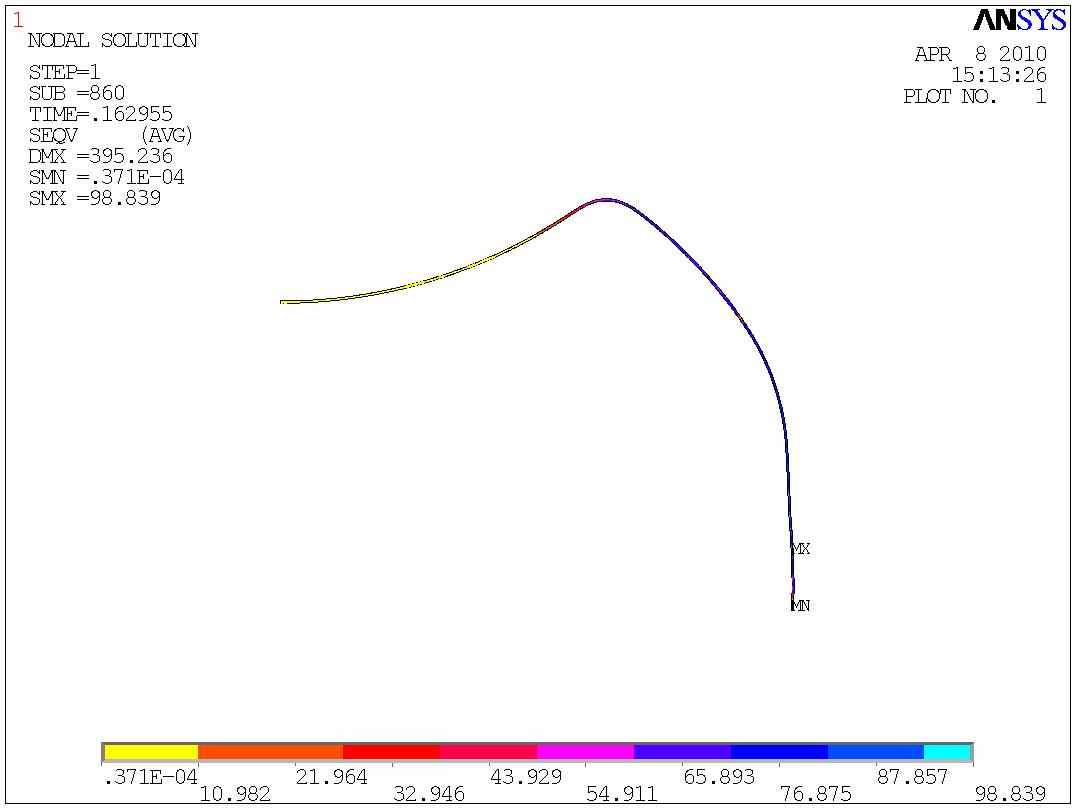
Рисунок 3.12 - Поднятие полюса на 395,24 мм
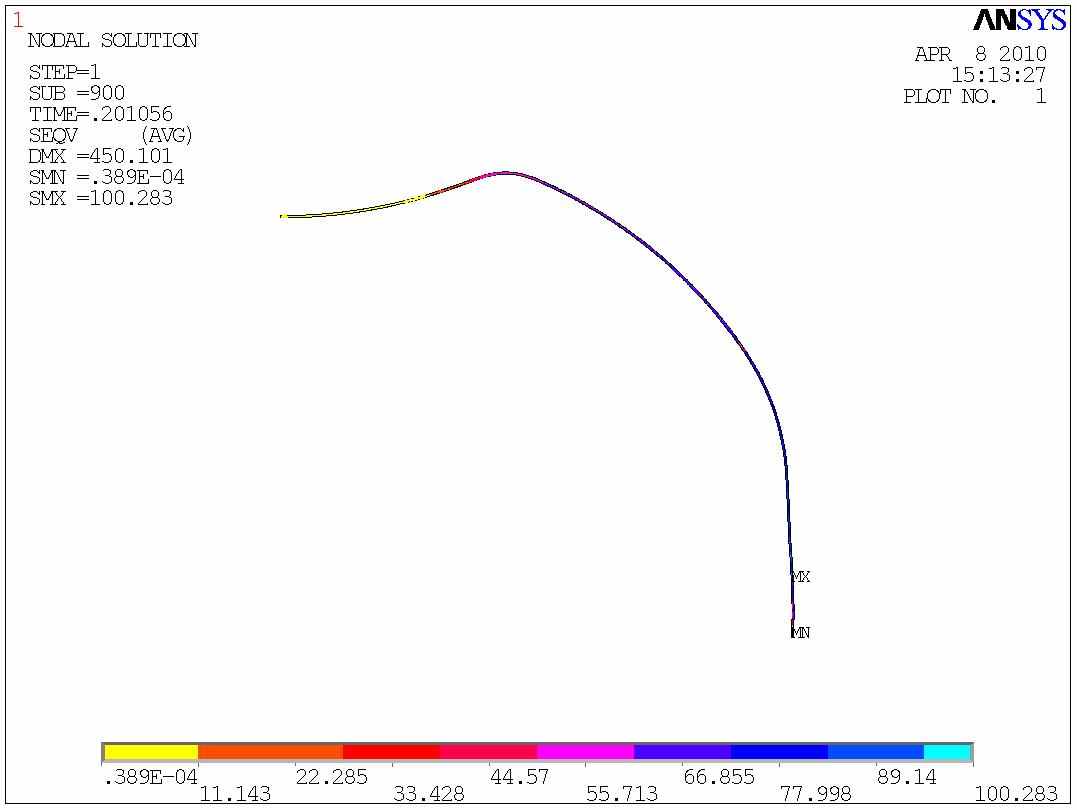
Рисунок 3.13 - Поднятие полюса на 450,1 мм
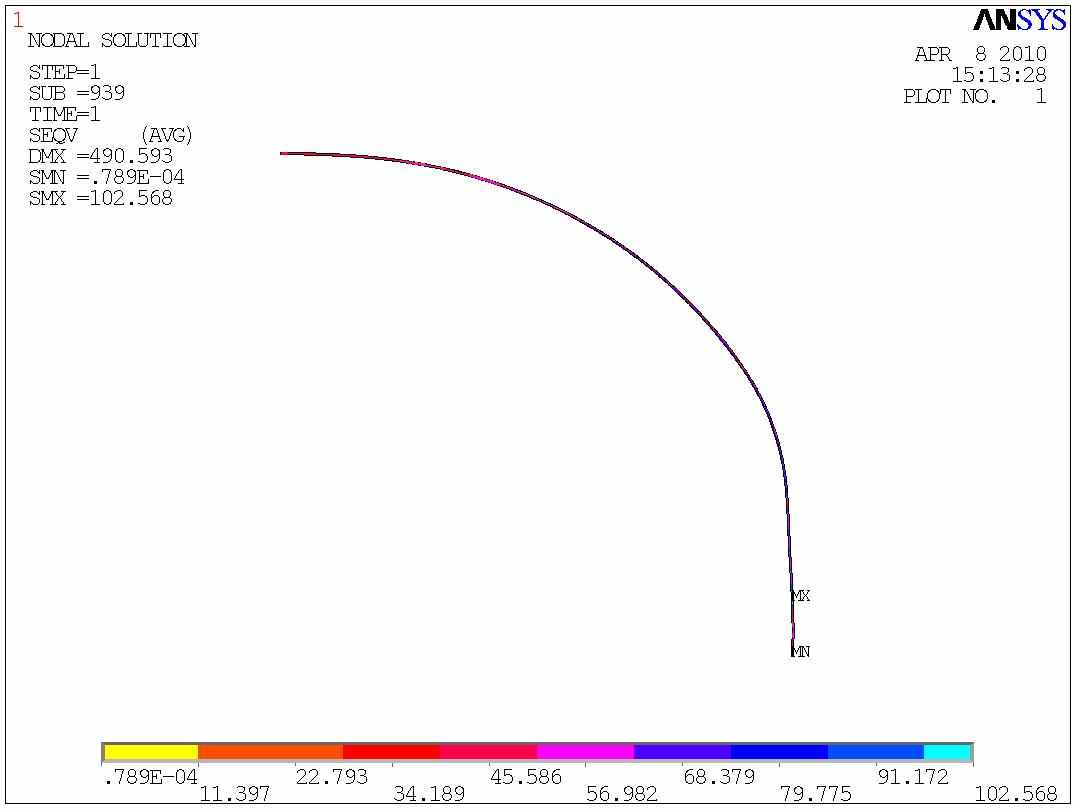
Рисунок 3.14- Поднятие полюса на 490 мм
На всех участках деформирования в конструкции возникают напряжения меньше разрушающих. Конструкция деформируется в соответствии с требованиями технического задания.
3.3 Обработка результатов контактного деформирования
В контактном деформировании диафрагмы рассмотрен случай штатной работы в составе бака. Для создания математической модели необходимо импортирование геометрии в формате IGES. Импортированная геометрия включает контур диафрагмы и бака (рисунок 16).
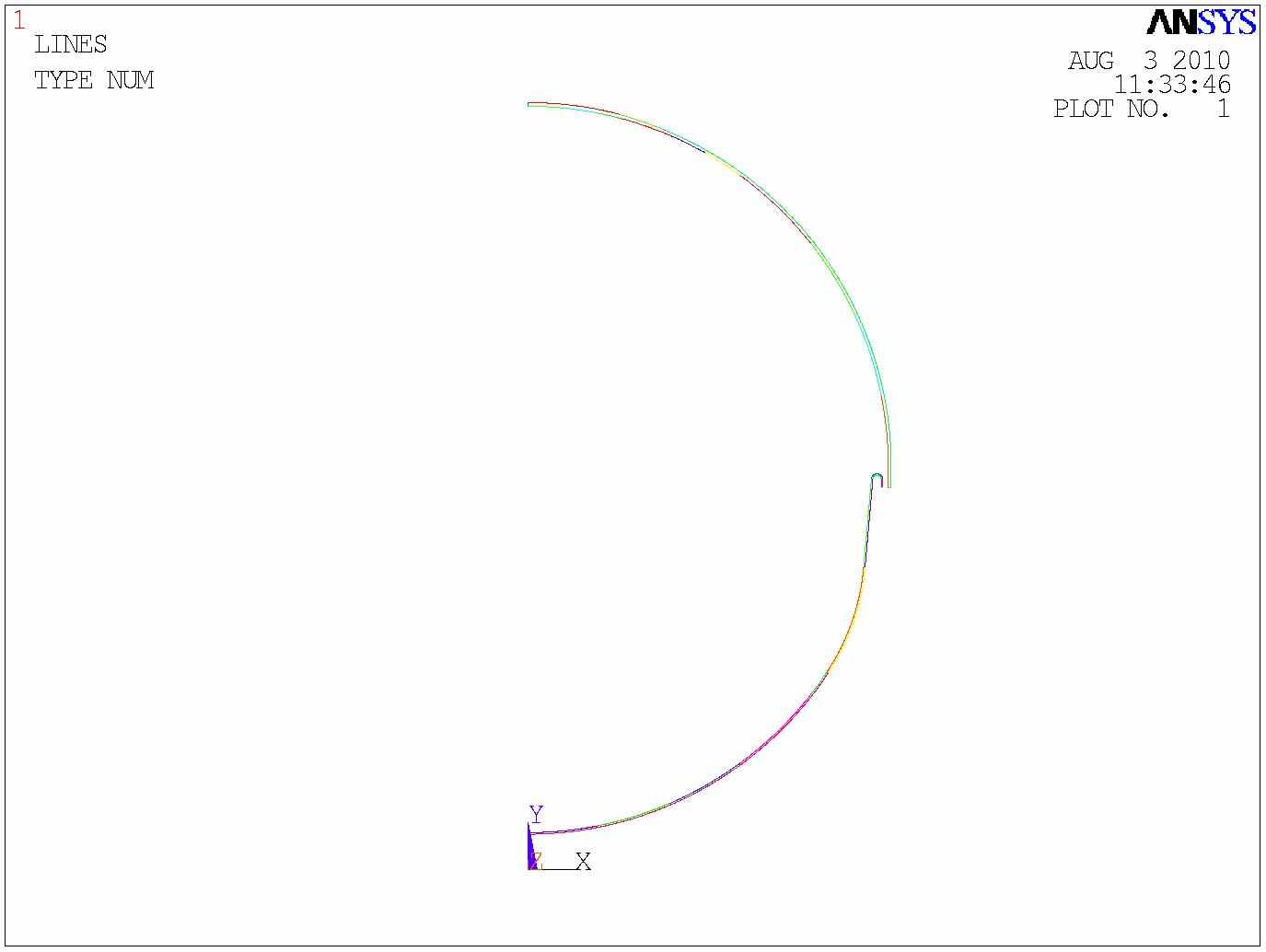
бак



диафрагма

Рисунок 3.15 - Импортированная геометрия для расчёта
контактного деформирования
Условия закрепления диафрагмы соответствуют случаю, рассмотренному в п.4.2. Контур бака закрепляется в верхней и нижней части полной заделкой (рисунок 17).
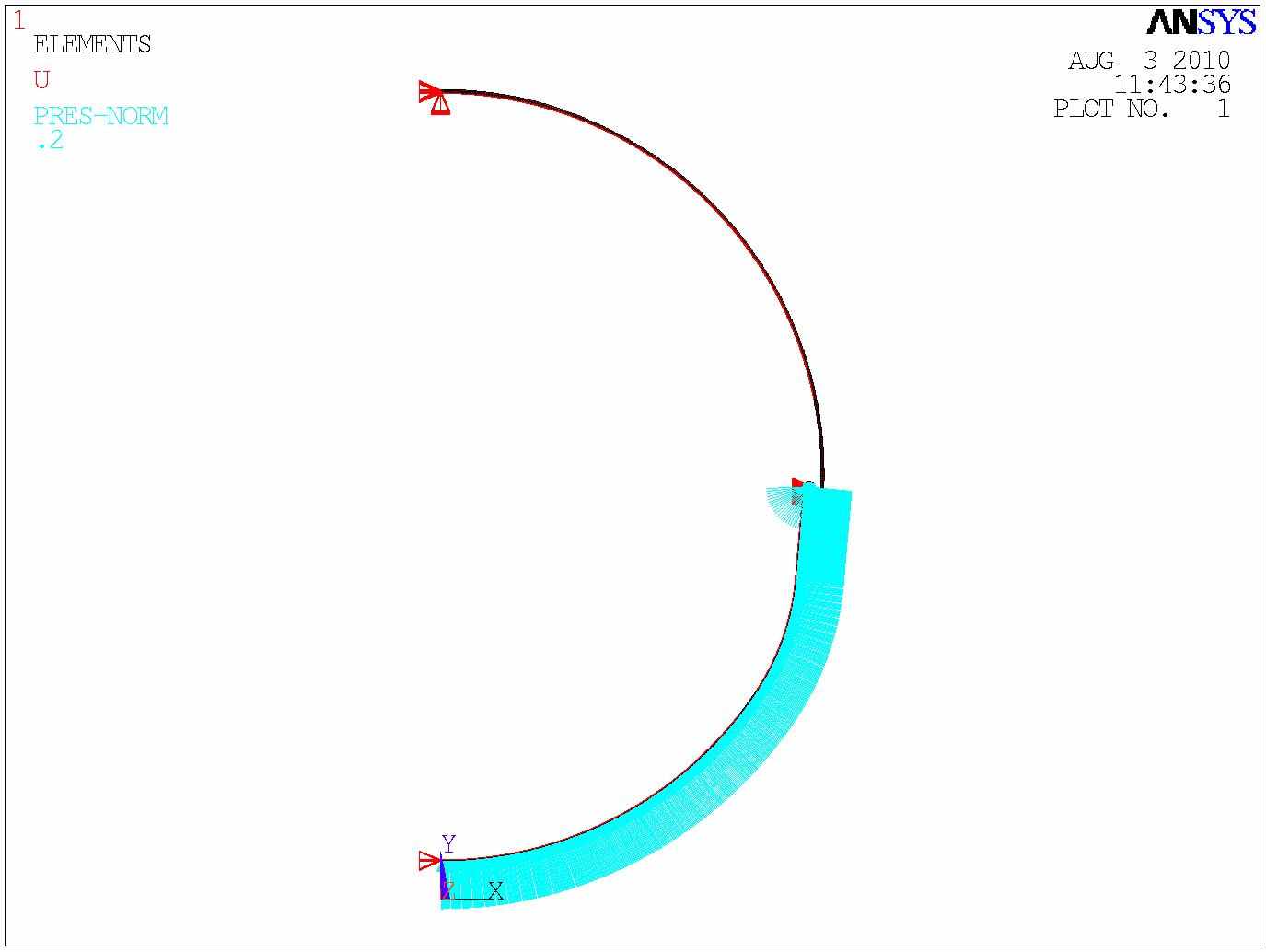
Рисунок 3.16 - Граничные условия и нагрузки
Для решения контактной задачи необходимо создание контактных пар с помощью элементов Targe169 Conta172. Для получения точного решения в данном случае создается 5 контактных пар в которых деформируемой поверхностью выбирается кромка диафрагмы контактирующая с баком, а в роли не деформируемой поверхности - кромка бака. Нормали контактирующих поверхностей в процессе расчета должны быть направлены друг к другу. На рисунке 19 и 20 представлены все 5 контактных пар, образующих общую линию контакта.
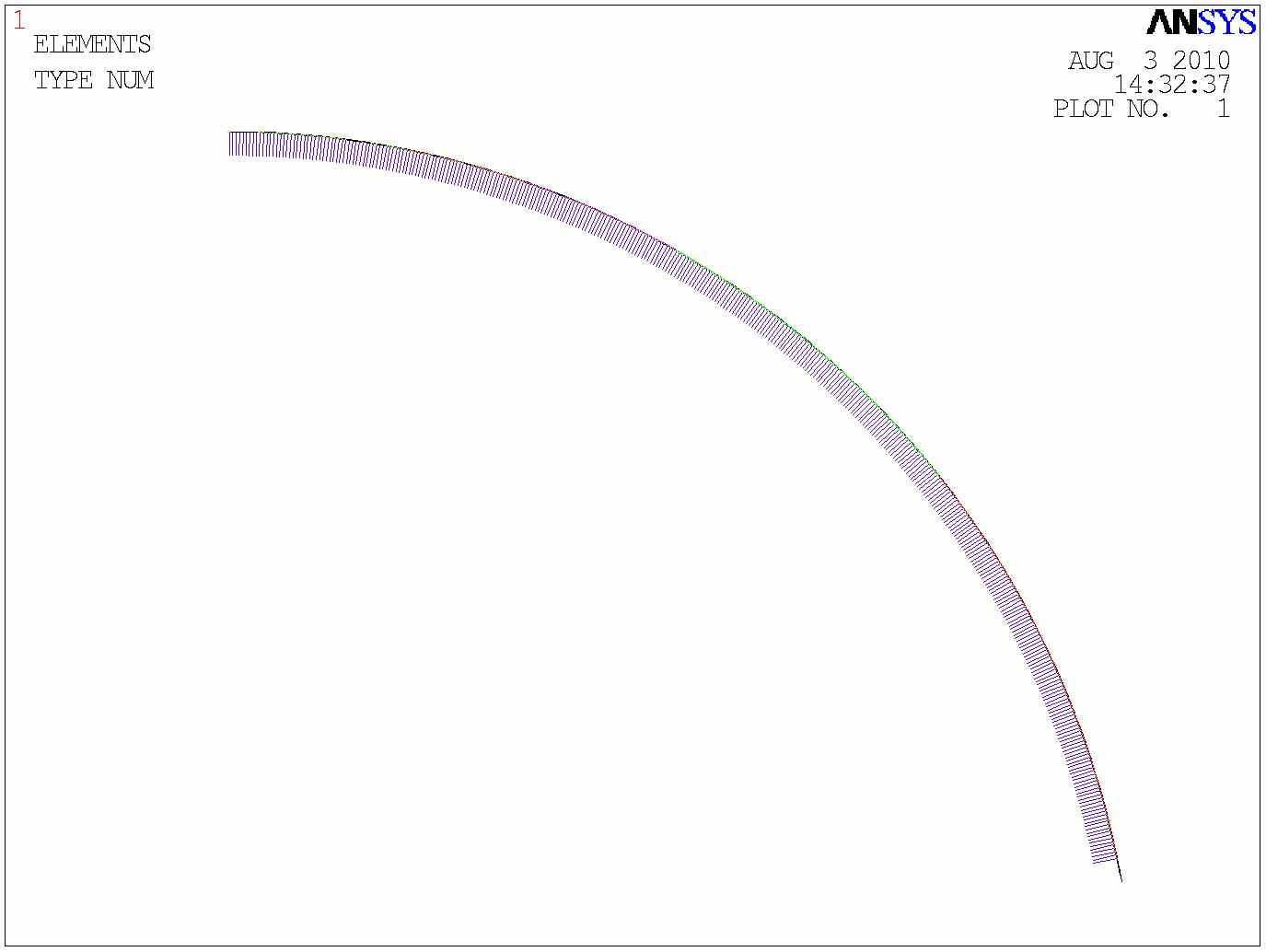
Рисунок 3.17 - расположение нормалей ответной поверхности
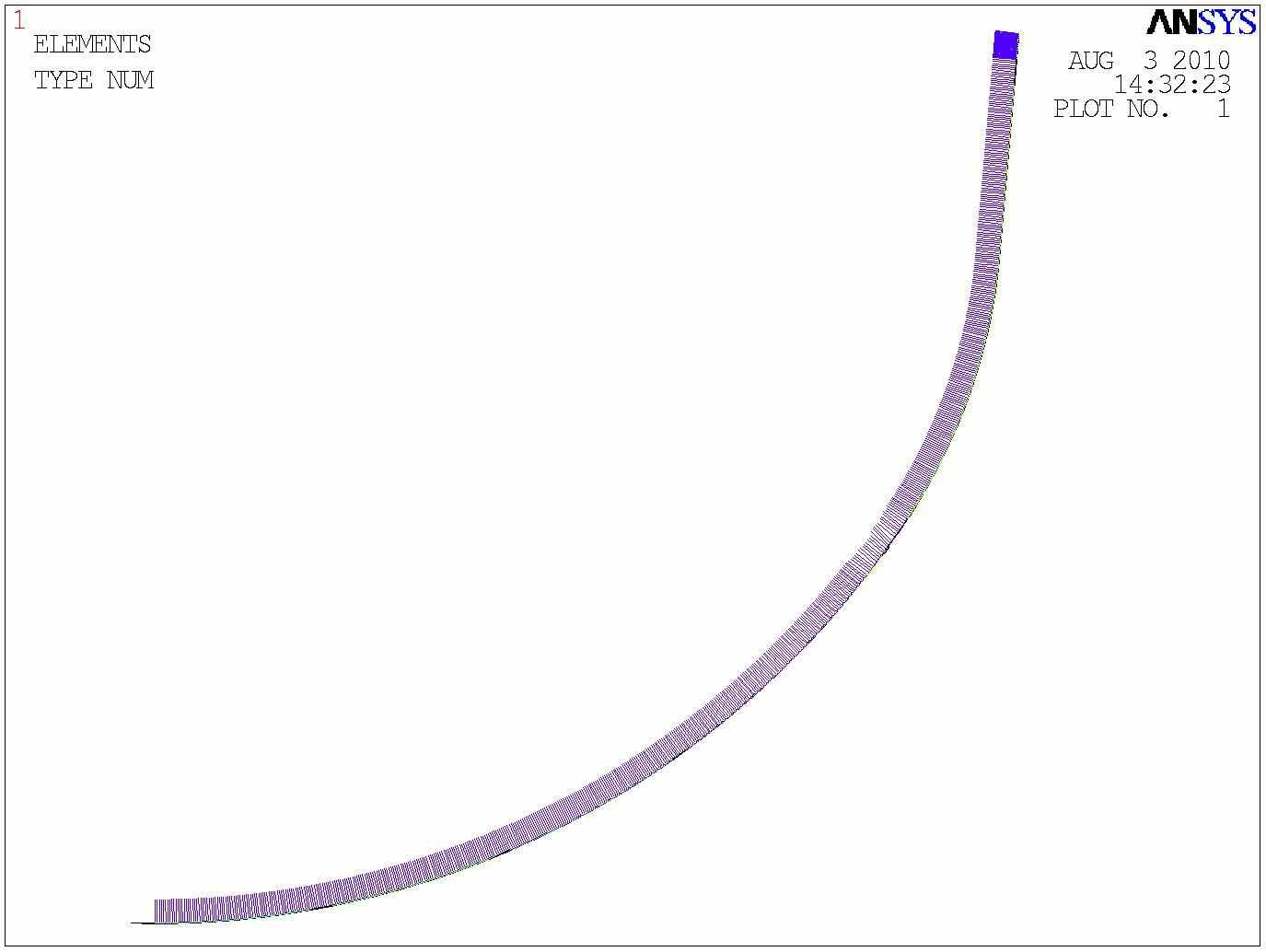
Рисунок 3.18 - расположение нормалей контактирующей поверхности
Материал бака принимается изотропным, модуль упругости имеет значение Е=70000 МПа коэффициент Пуассона μ=0,3.
Для расчёта использовалось 7200 конечных элементов, что обеспечивает приемлемую сходимость для данной контактной задачи. Данное количество конечных элементов позволяет получить подробное распределение напряжений как в области контакта, так и по всей толщине диафрагмы. Отследить деформирование и контакт с баком.
Расчет проводится с учётом физической и геометрической нелинейности. На рисунках 3.19 - 3.32 представлена общая картина деформирования диафрагмы с учётом контакта по стенке бака.
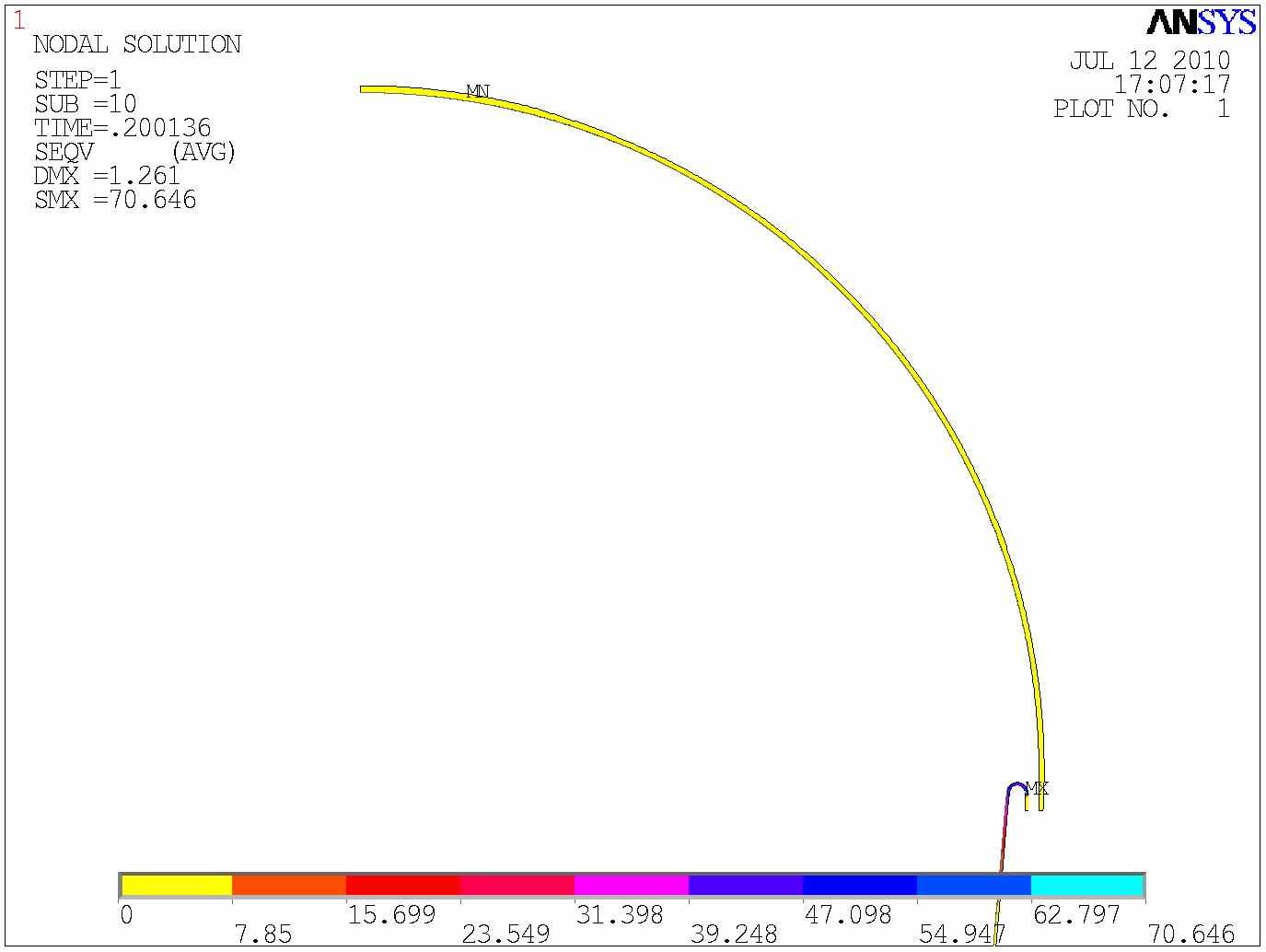
Рисунок 3.19

Рисунок 3.20
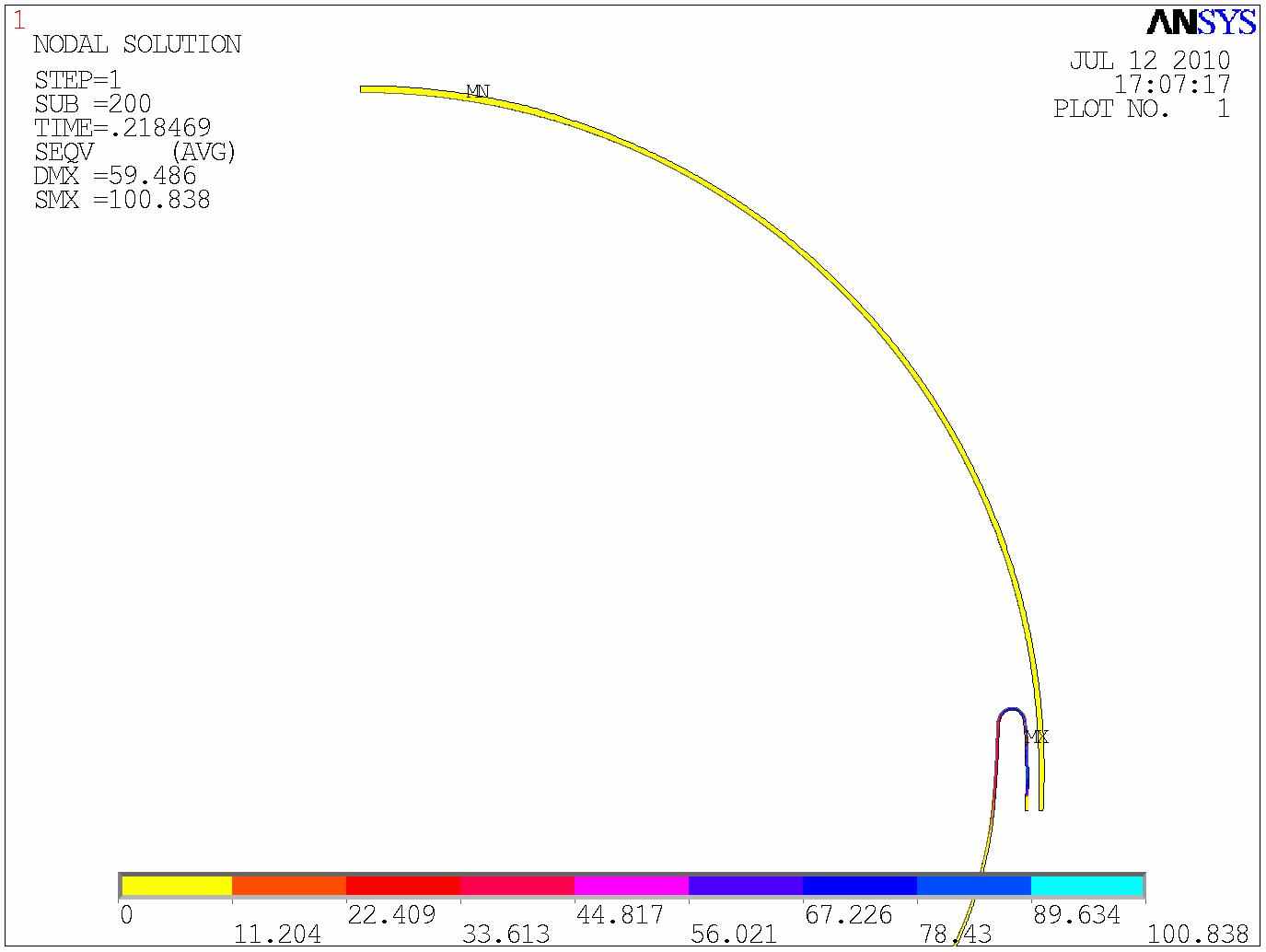
Рисунок 3.21
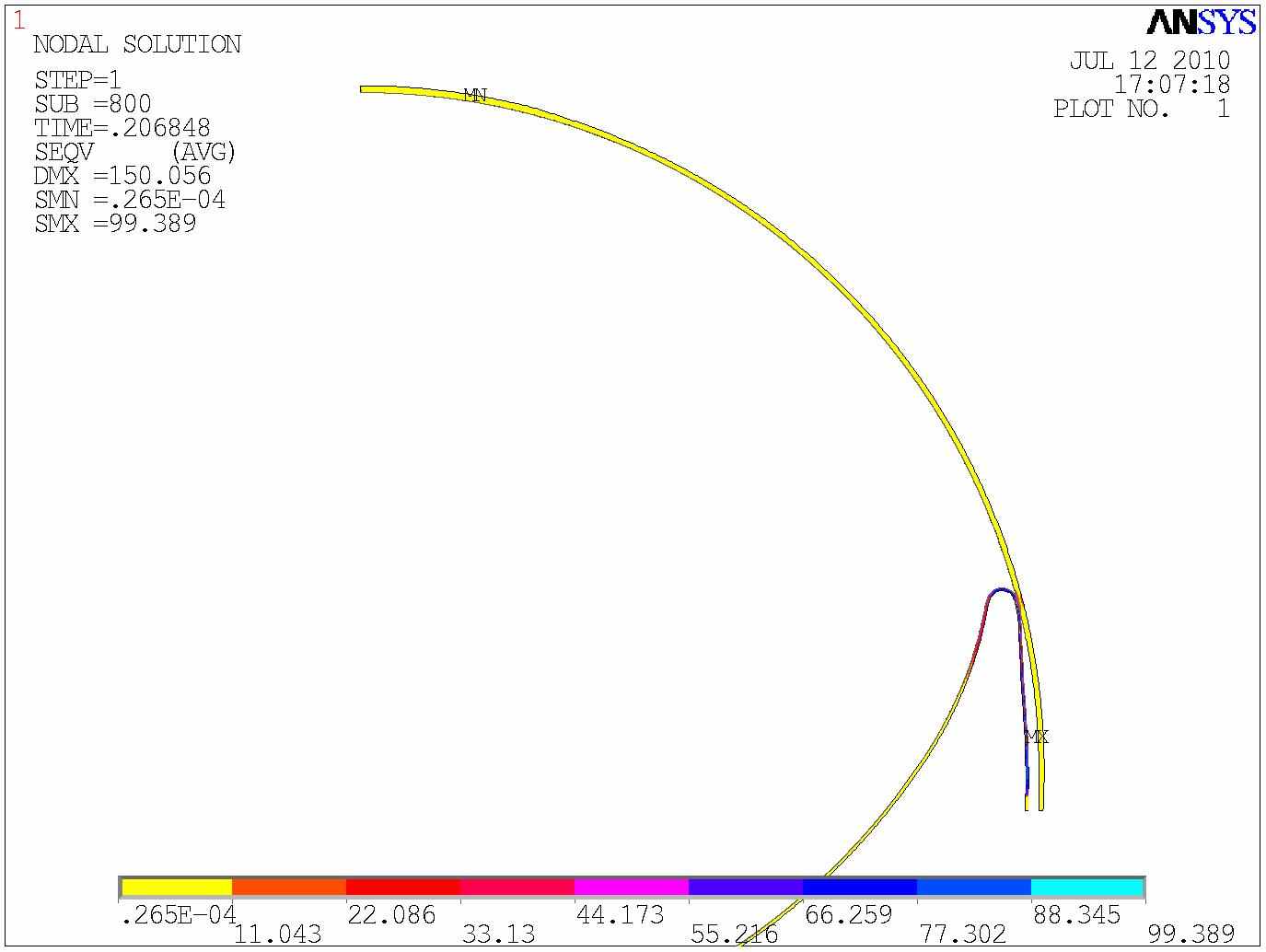
Рисунок 3.22
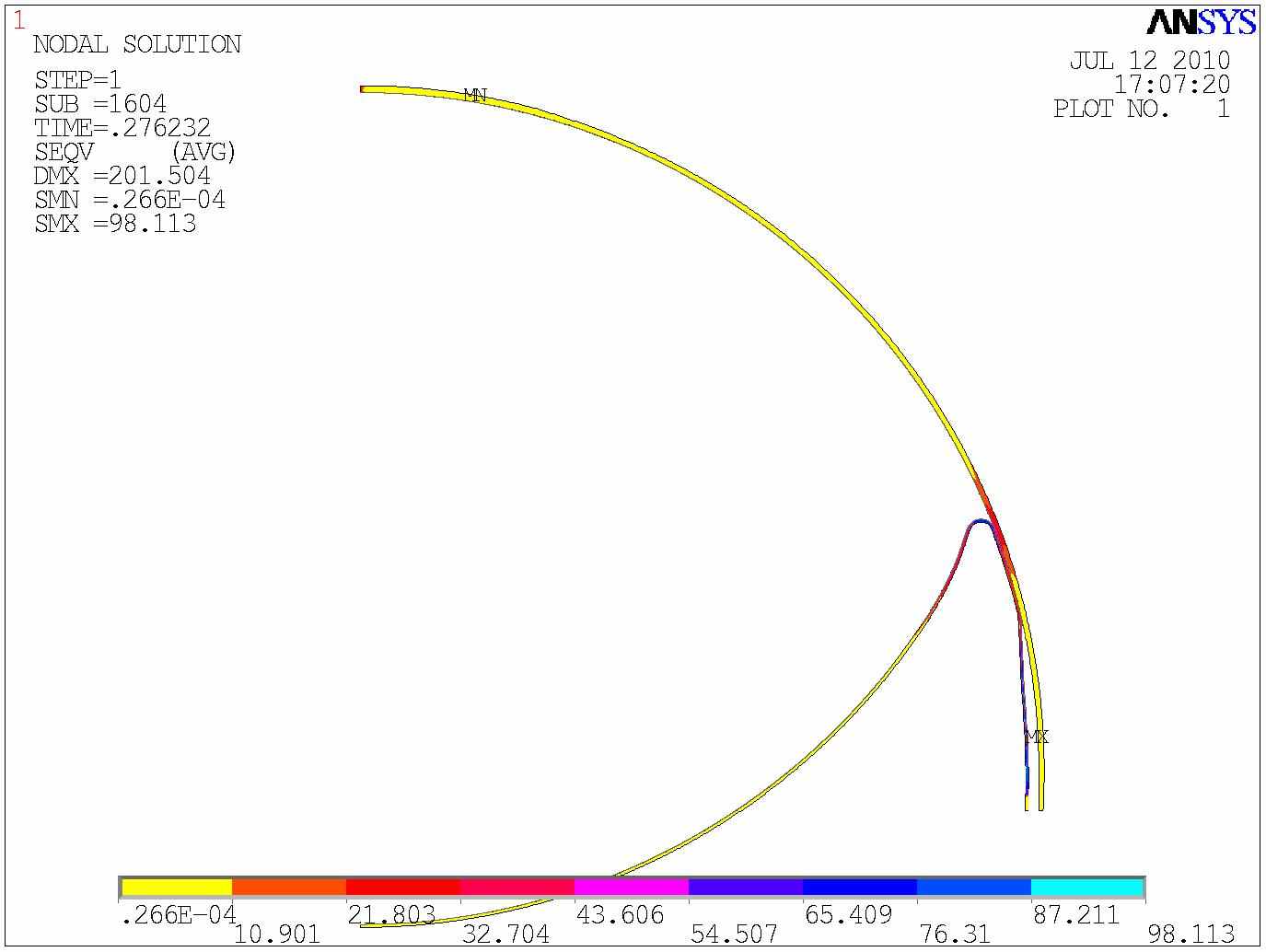
Рисунок 3.23

Рисунок 3.24
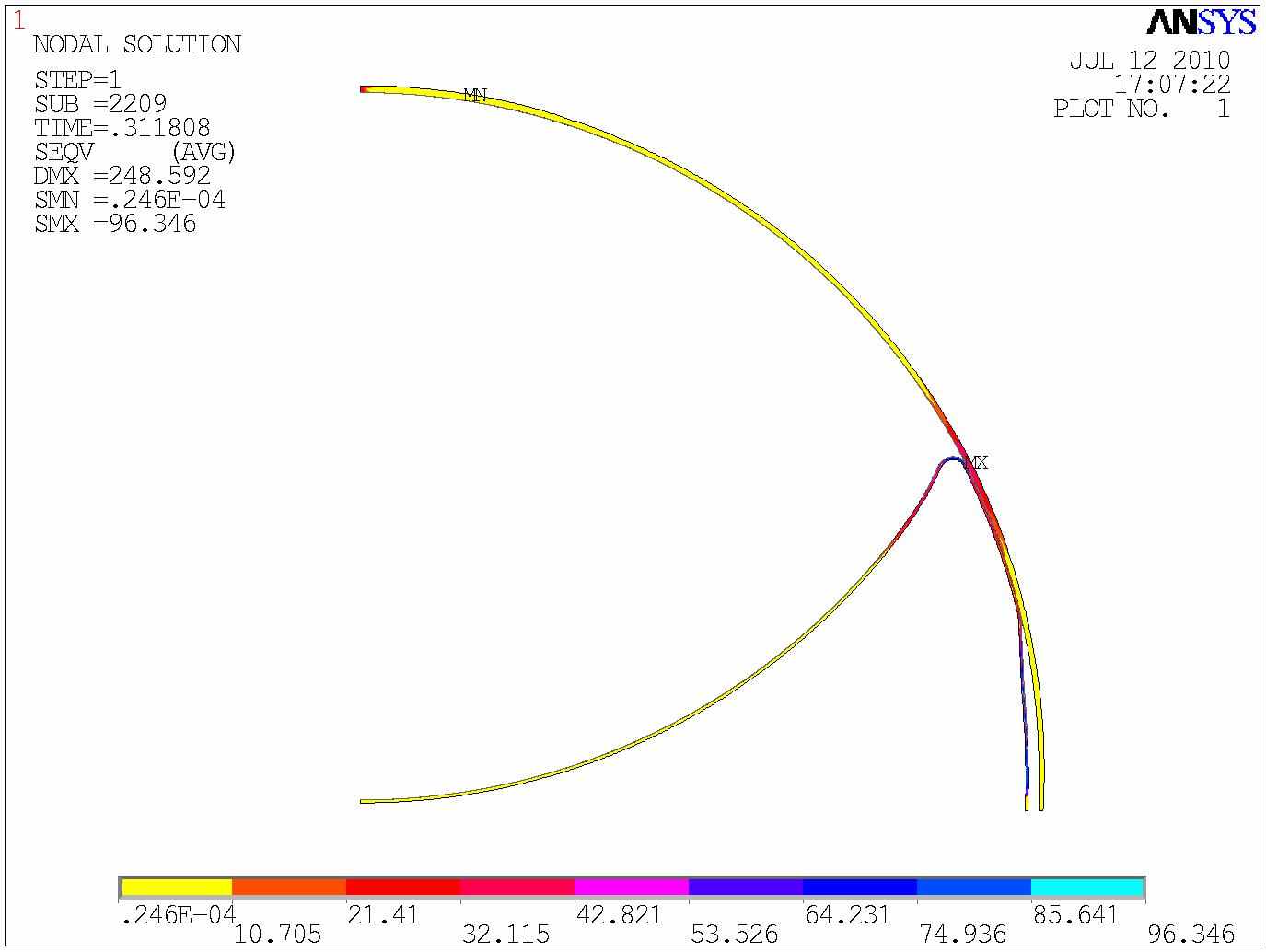
Рисунок 3.25
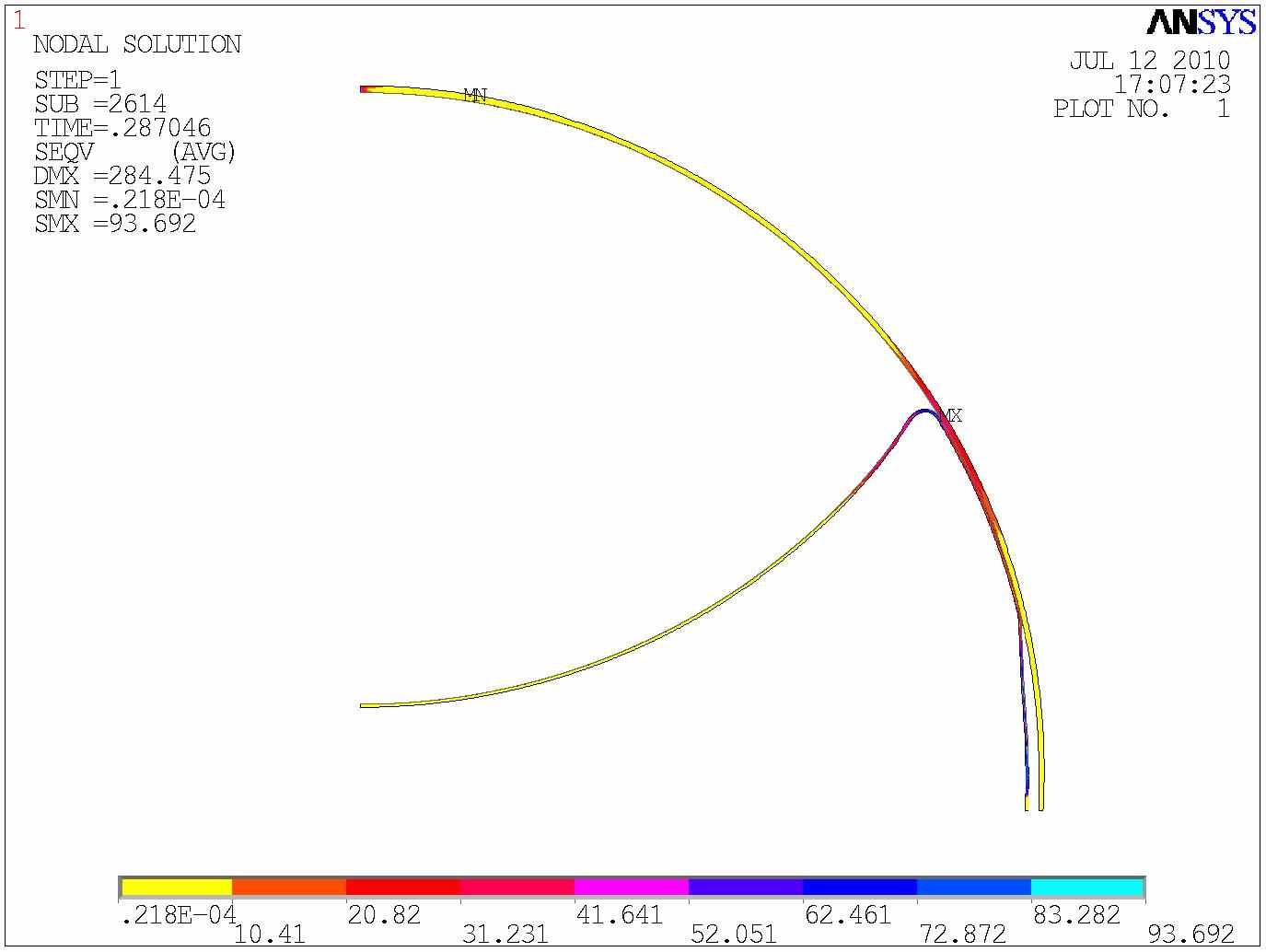
Рисунок 3.26
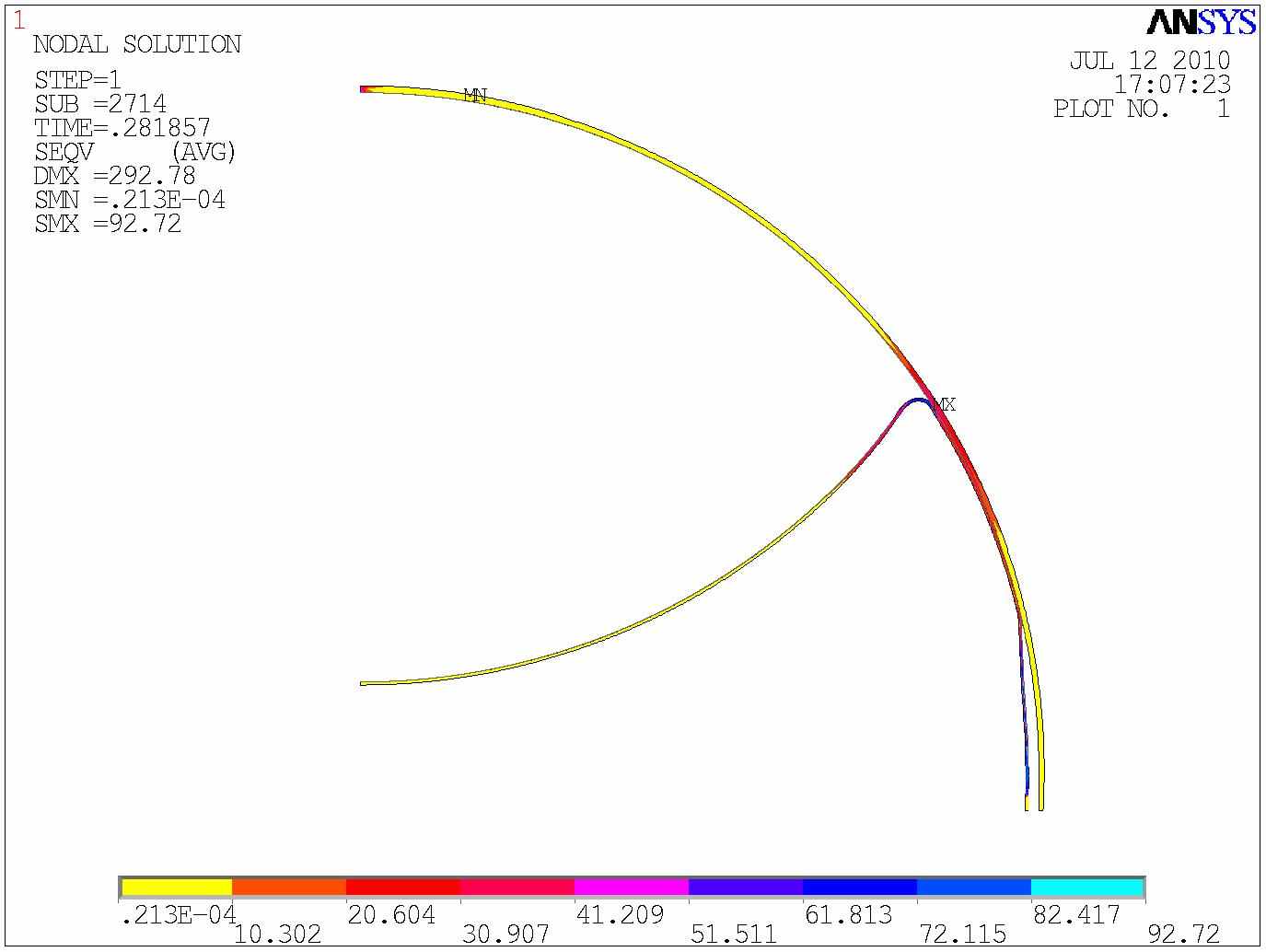
Рисунок 3.27
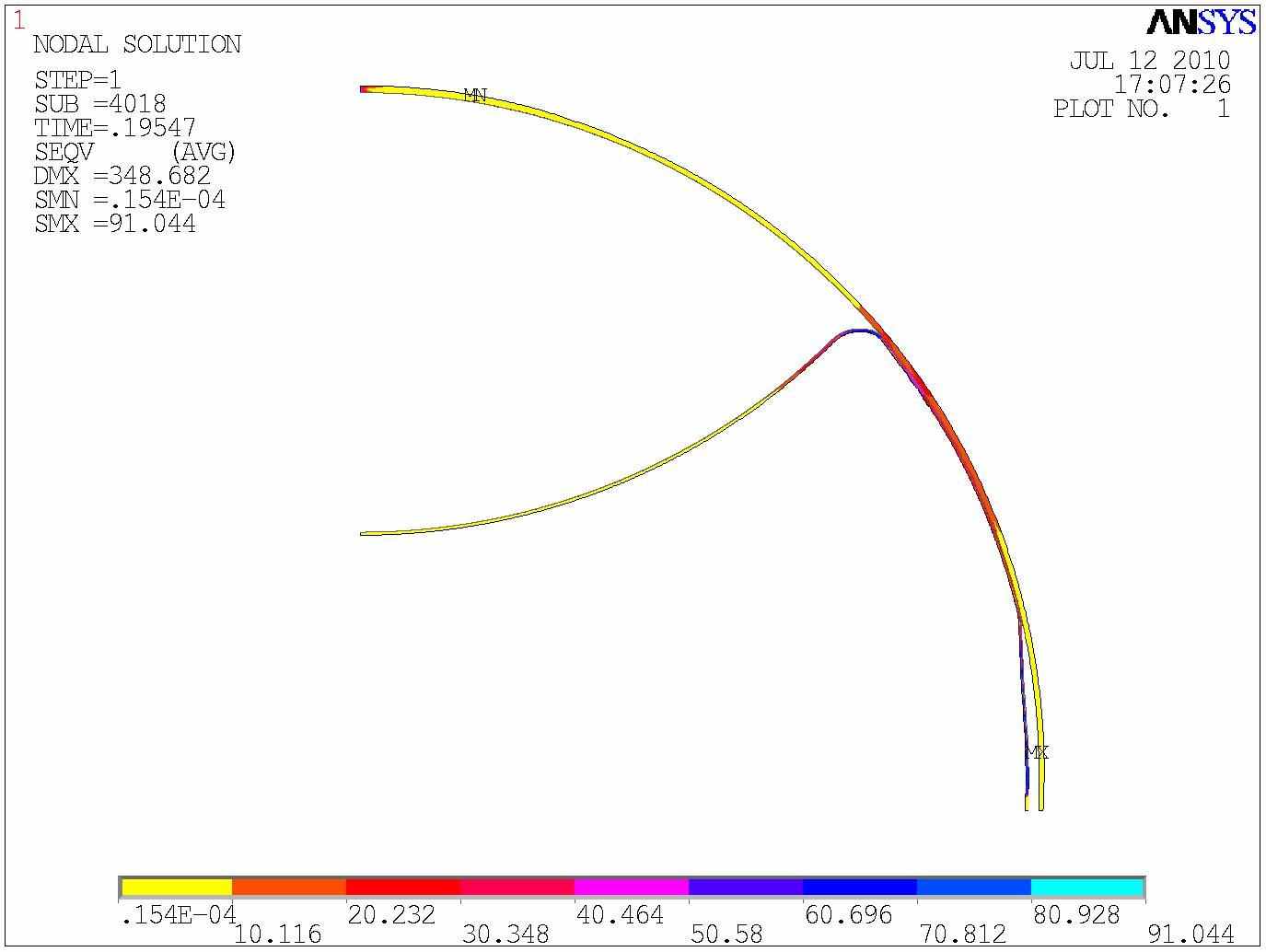
Рисунок 3.28
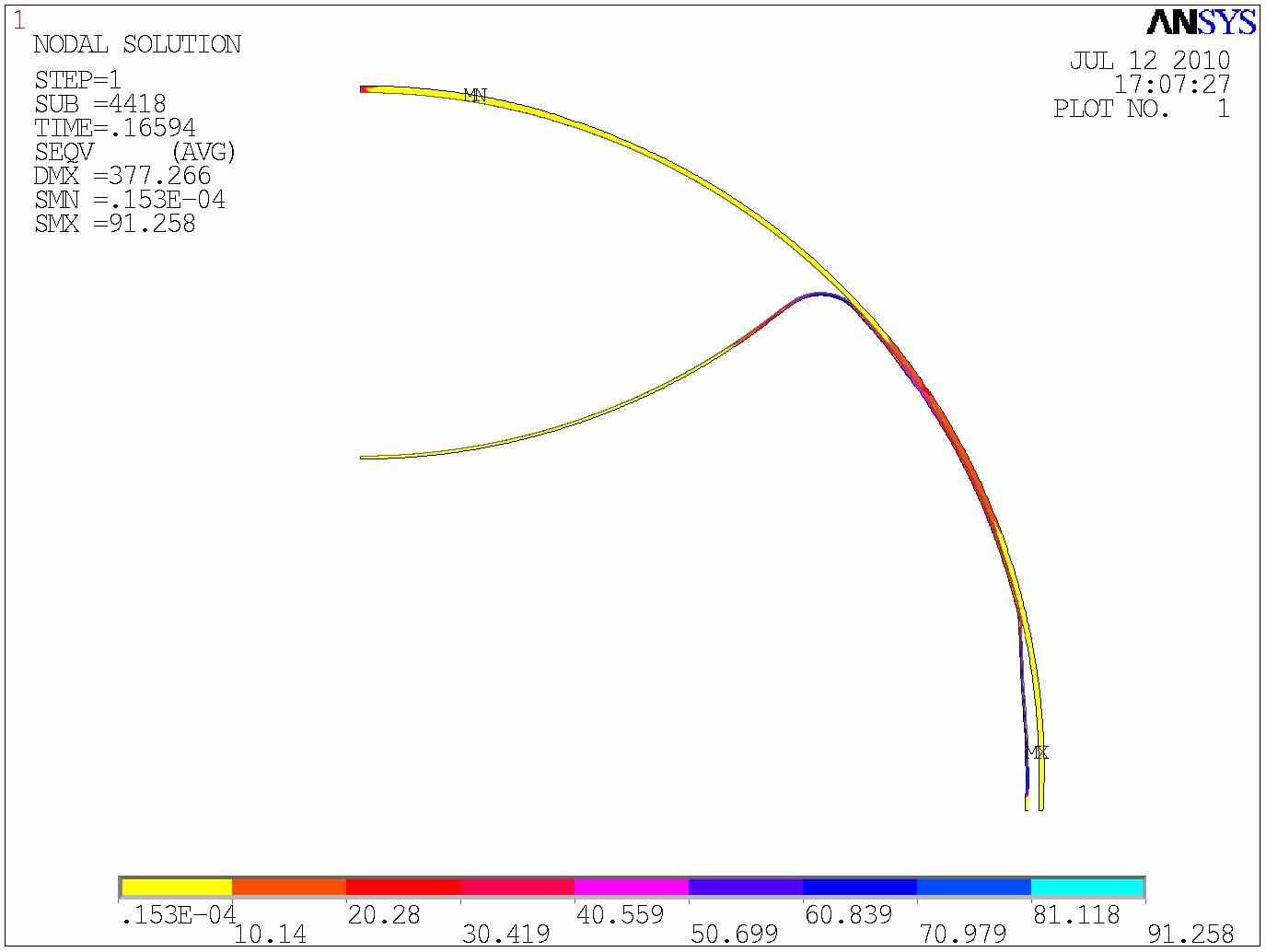
Рисунок 3.29
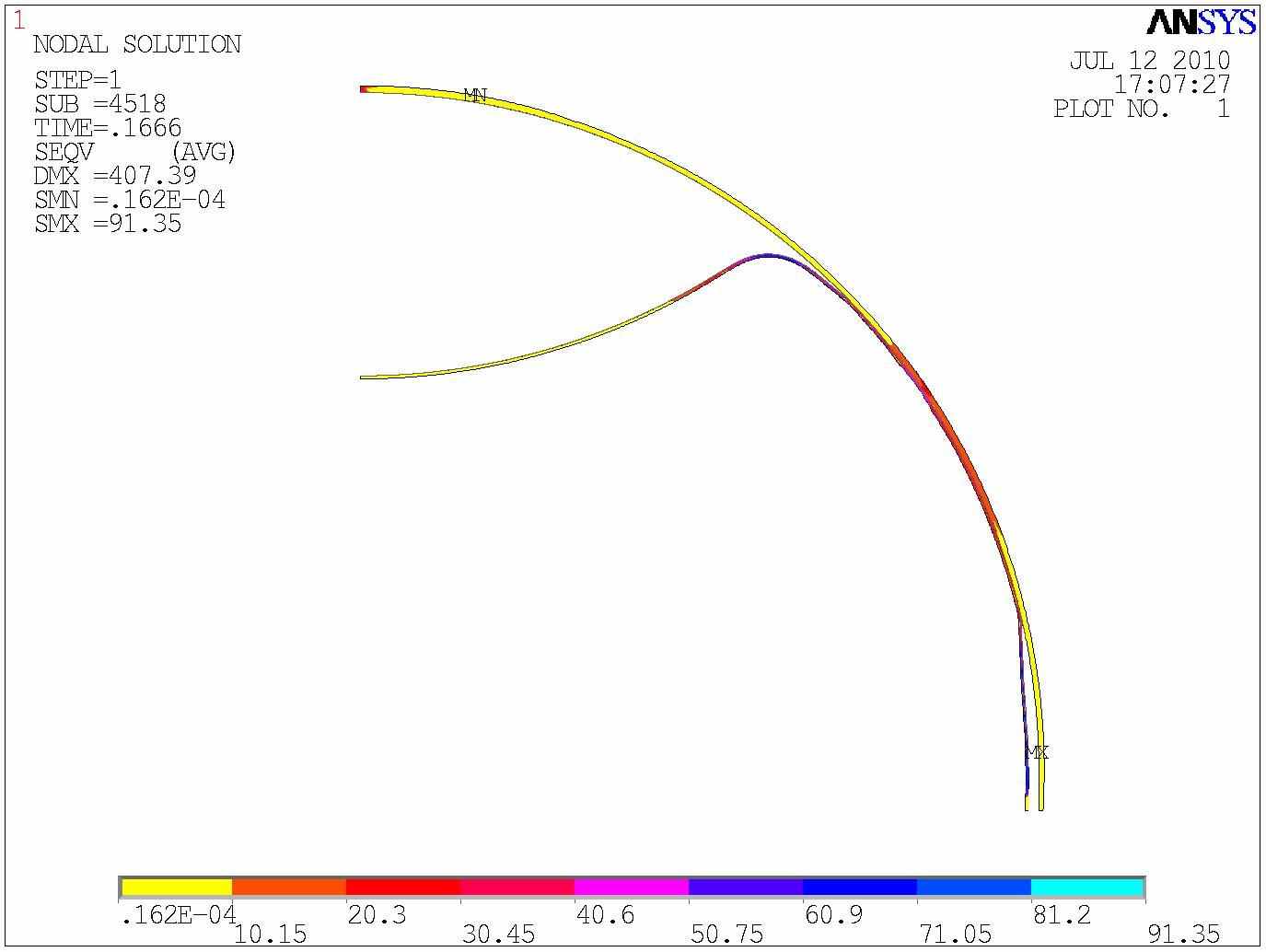
Рисунок 3.30
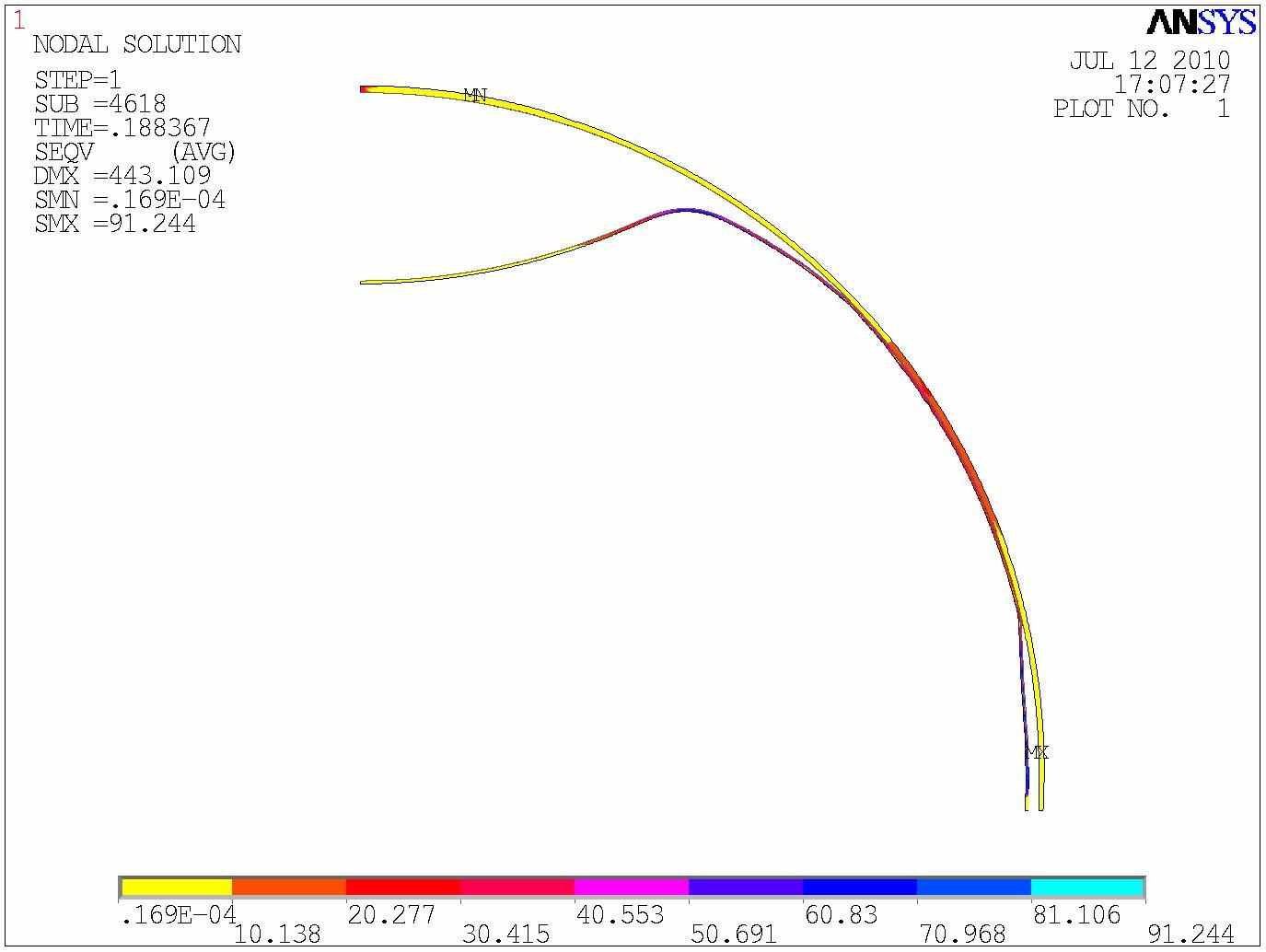
Рисунок 3.31
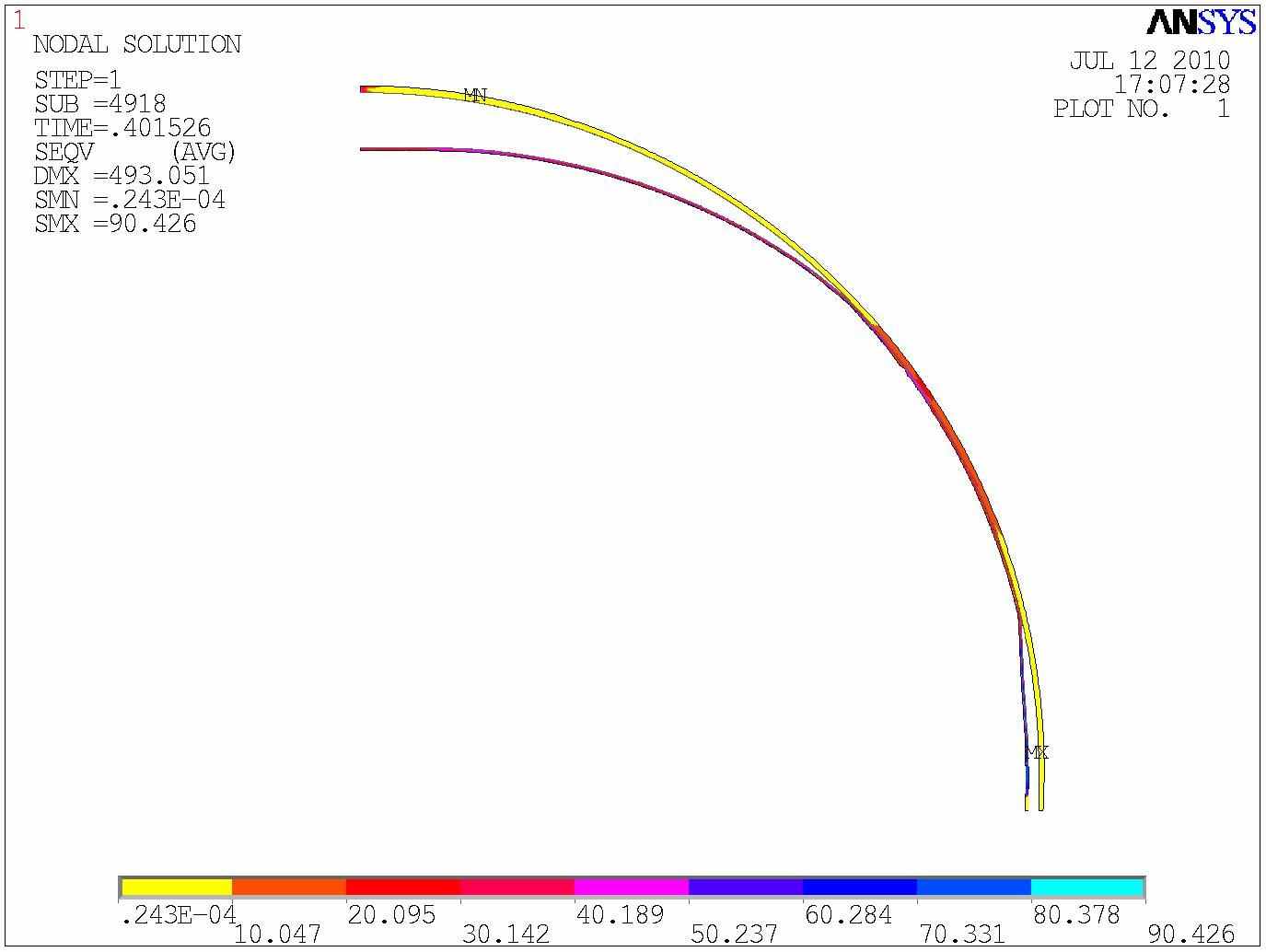
Рисунок 3.32
В результате расчета диафрагмы с контактным прилеганием по стенке бака установлено, что напряжения во всех стадиях деформирования не превышают разрушающих.
4 Технико-экономическое обоснование проекта
В настоящее время потребность в разработке новых агрегатов возрастает в очень большой степени. А сроки на их производство постоянно уменьшаются. Проводимые испытания (ЛОИ, КДИ) могут проходить очень долго и быть дорогостоящими. Если же во время проведения испытаний в конструкторской документации вносятся изменения, то это потребует дополнительного времени и средств на изменение, как испытательного оборудования, так и изделия. В данном проекте сравниваются затраты на проведение 1ого этапа КДИ диафрагмы (без учёта себестоимости изготовления) с виртуальными испытаниями и доработкой кд.
Рассчитаем стоимость компьютерных испытаний :
Стоимость программного обеспечения (1 лицензия) в год составляет 25000$.

Где :




N -


В результате получим :

Во время 1ого этапа КДИ геометрия диафрагмы менялась 2 раз
Для последующего расчета не требуется заново составлять и отлаживать программу расчета, а требуется лишь ввести новые исходные данные.
Процесс изменения и последующего расчета с двумя видами новой геометрии занял ещё 4 часа. Подставляя в формулу (1) получим :

Общая сумма затрат составила :
77800+16400= 84054 р.
Затраты на проведение 1ого этапа КДИ составили
Сырьё и материалы - 18230 р
Расходы на оплату труда производственных рабочих - 228450 р
Единый социальный налог - 63280р
Накладные расходы - 240100р
Общая производственная себестоимость составила - 550060 р.
При изменении конструкции диафрагмы во время КДИ 2 раза потребуется доработать как начальное производство, так и провести ещё раз 1й этап КДИ.
Не трудно догадаться что любое изменение геометрии или проработка нескольких вариантов конструкции будет очень дорогостоящей. Проработка нескольких вариантов конструкции с использование Ansys будет намного быстрее и экономнее.
Заключение
В данном проекте рассмотрены лишь два примера расчета по предложенной методике. В базе данных системы "Лоцман" имеются отчеты по испытаниям мембраны прорыва (входит в состав мембранного узла 14Ф148.7103-0) и диафрагмы (входит в состав топливного бака 14Ф148.7101-0). Данная методика может быть улучшена за счет написания различных макросов и подпрограмм в среде Ansys, способных сократить время как на ввод начальных данных, так и на обработку результатов и составление отчетов по решённым задачам.
Список использованных источников
- Ansys – Quick Reference Guide. Файл документации.
- Лизин В.Т. Пяткин В.А. Проектирование тонкостенных конструкций – М.: Машиностроение, 1984 – 482с
- Викторова, А.Н. Технико-экономическое обоснование дипломных проектов научно-исследовательского профиля: методические указания по дипломному проектированию/ А.Н. Викторова. – Изд-во Самар. гос. аэрокосм. ун-та, 2007. –23 с.