Анализ производственного травматизма причины производственного травматизма и методы его анализа
Вид материала | Задача |
- Анализ производственного травматизма за 2010 год, 105.76kb.
- Информация о состоянии охраны труда, производственного травматизма в организациях Осиповичского, 170.88kb.
- О состоянии производственного травматизма в организациях города Минска в Iполугодии, 80.28kb.
- О состоянии производственного травматизма в организациях города Минска в 2011 году, 100.14kb.
- На заседании комиссии были заслушаны вопросы: Осостоянии охраны труда и производственного, 41.17kb.
- Информационный бюллетень состояние производственного травматизма, условий и охраны, 725.94kb.
- Динамика производственного травматизма по г. Полоцку за 2007 -2011, 59.64kb.
- О состоянии производственного травматизма и заболеваемости медицинских работников, 232.38kb.
- План финансового обеспечения предупредительных мер по сокращению производственного, 30.59kb.
- Сведения о состоянии производственного травматизма со смертельным и тяжелым исходами, 12.63kb.
1. АНАЛИЗ ПРОИЗВОДСТВЕННОГО ТРАВМАТИЗМА
1.1. Причины производственного травматизма
и методы его анализа
Для улучшения условий труда на производстве всегда ставится задача – установить причины и закономерности появления несчастных случаев и профессиональных заболеваний. Этому предшествует отклонение производственного процесса от нормального хода.
Причины производственного травматизма
В настоящее время при анализе выделяют нижеследующие причины производственного травматизма.
1. Организационные – отсутствие или неудовлетворительное проведение инструктажа и обучения безопасным методам ведения работ; отсутствие проекта производства работ, руководства и надзора за работой; неудовлетворительный режим труда и отдыха; неправильная организация рабочего места, движение пешеходов и транспорта; отсутствие, неисправность или несоответствие условиям работы спецодежды, индивидуальных средств защиты и др.
2. Технические причины подразделяют на три вида:
а) конструкторские – несоответствие строительных конструкций, технологического оборудования, транспортных и энергетических устройств требованиям безопасности; несовершенство конструкции монтажной оснастки, ручного и переносного механизированного инструмента; отсутствие или несовершенство оградительных предохранителей и других технических средств безопасности;
б) технологические – неправильный выбор оборудования, оснастки грузоподъемных механизмов и средств механизации; нарушение технологического процесса;
в) неудовлетворительное техническое обслуживание – отсутствие плановых профилактических осмотров, технических уходов и ремонта оборудования, оснастки и транспортных средств; неисправность ручного и переносного механизированного инструмента.
3. Причины неудовлетворительного состояния производственной среды – неблагоприятные метеорологические условия; неудовлетворительная освещенность; повышенный уровень шума и вибрации; повышенная концентрация вредных веществ в воздухе рабочей зоны; наличие вредных облучений и др.
4. Психофизиологические – несоответствие анатоморфологических и психологических особенностей организма человека условиям труда; неудовлетворительный психологический климат в коллективе; алкогольное опьянение и др.
Методы анализа производственного травматизма
При анализе производственного травматизма с целью установления и устранения вызывающих их причин применяют различные методы:
– топографический: состоит в изучении причин несчастных случаев по месту их происшествия. Все несчастные случаи систематически наносят условными знаками на планах производства работ, в результате чего наглядно видны места и производственные участки, где произошли травмы;
– статистический: основан на изучении причин травматизма по документам, регистрирующим совершившиеся факты несчастных случаев (акты по форме Н-1) за определенный период времени. Этот метод позволяет получить сравнительную динамику травматизма по отдельным производственным объектам. При углубленном статистическом анализе его проводят по виду работ, где анализируются сведения о пострадавших (профессия, стаж работы, пол, возраст и т.п.) и данные о времени происществия (год, месяц, день недели, смена, час рабочего дня и т.п.);
– групповой: основан на изучении повторяющихся несчастных случаев вне зависимости от тяжести повреждения. Имеющийся материал расследования распределяется по группам с целью выявления несчастных случаев, одинаковых по обстоятельствам, происшедших при одинаковых условиях, а также повторяющихся по характеру повреждений. Это позволяет определить наиболее травмоопасные профессии и виды работ;
– монографический: включает в себя детальное исследование всего комплекса производственных условий, при которых произошел несчастный случай: трудовой и технологический процессы, рабочее место, основное и вспомогательное оборудование, индивидуальные средства защиты, общие условия производственной обстановки и т.п. [1].
Количественная оценка производственного травматизма
Для оценки уровня производственного травматизма используют ряд показателей.
Коэффициент частоты травматизма
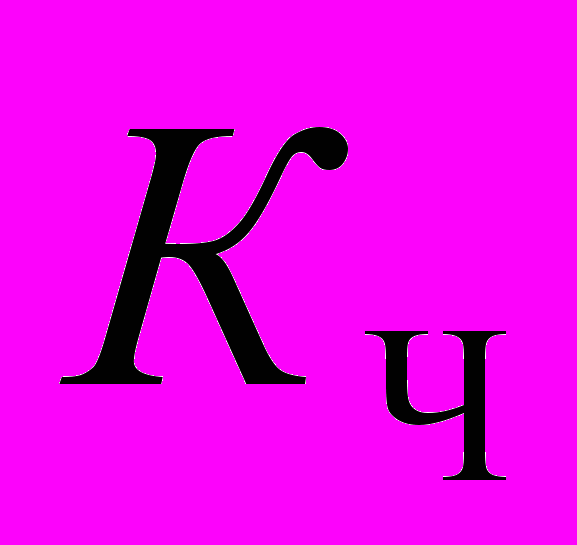
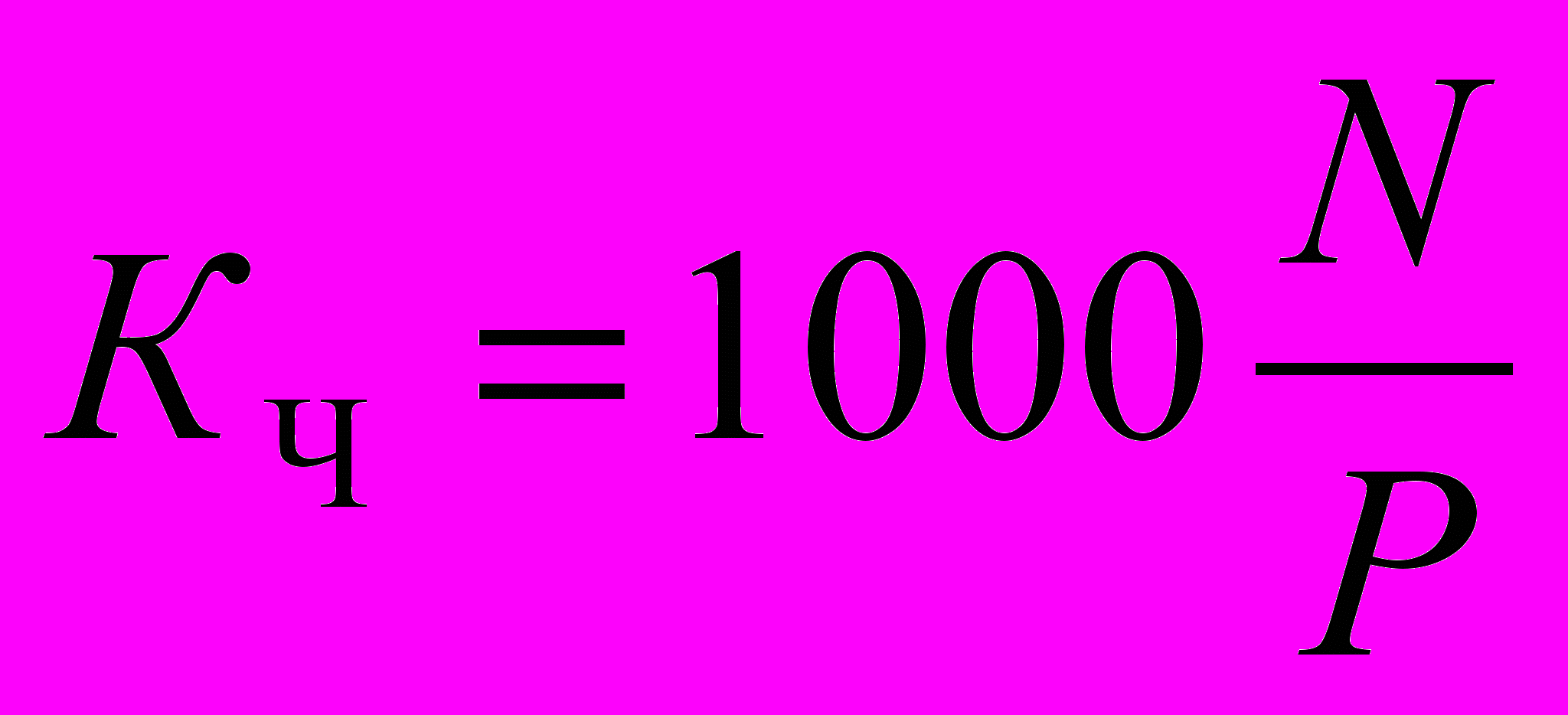
где N – количество несчастных случаев, произошедших в организации за рассматриваемый период;
Р – среднесписочный состав работников в организации за рассматриваемый период.
Коэффициент тяжести травматизма
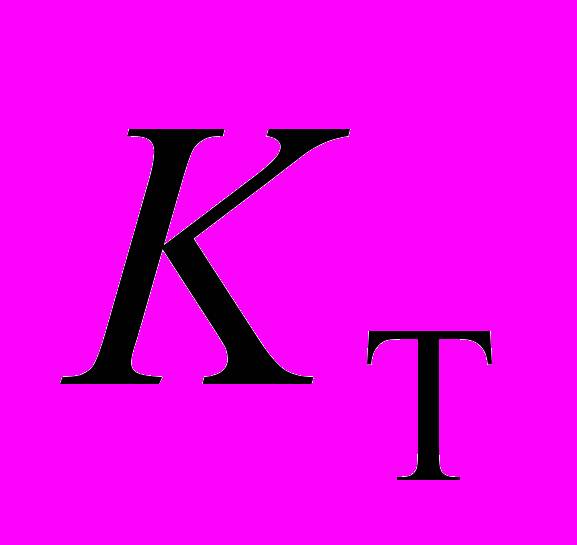
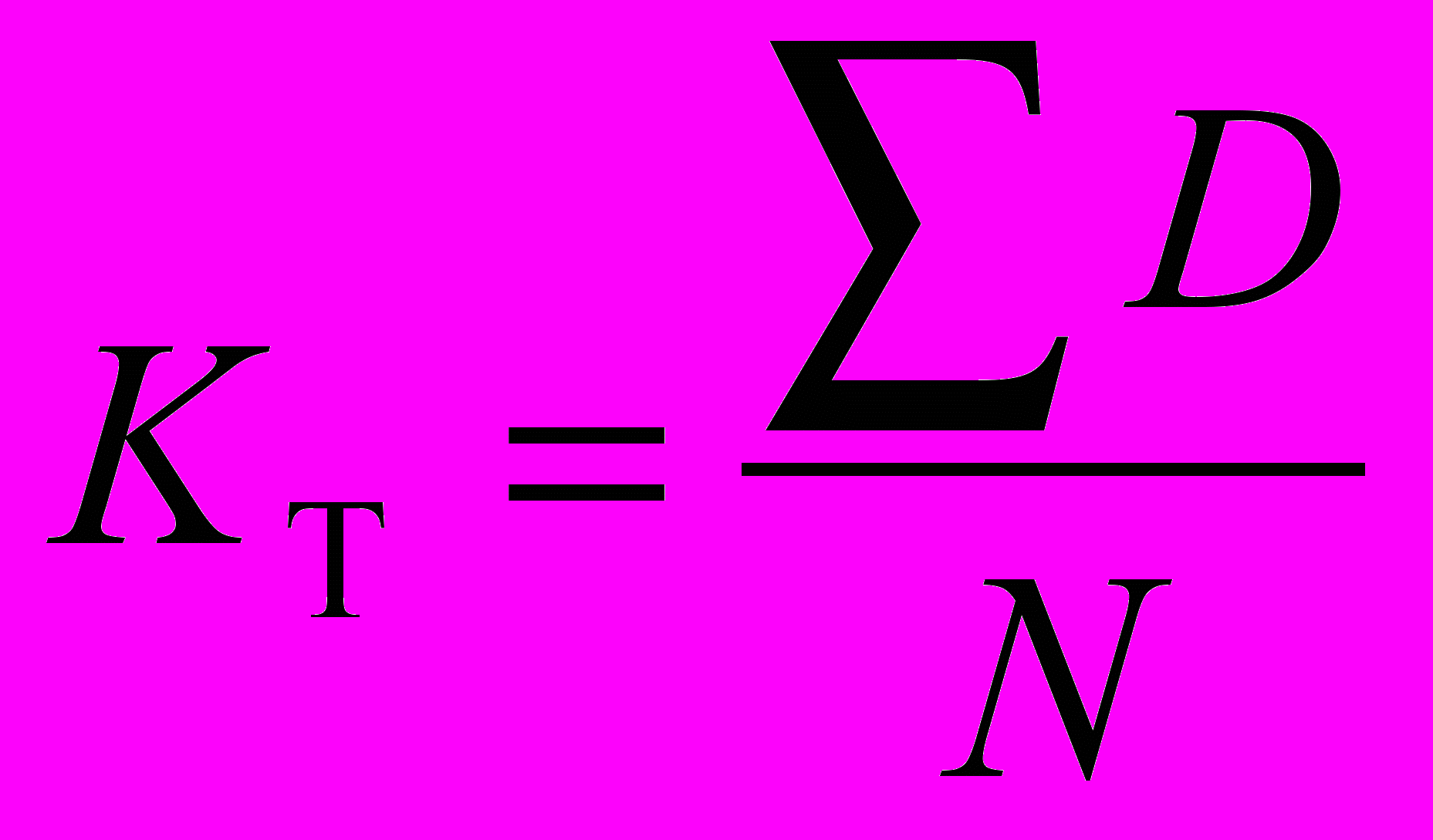
где
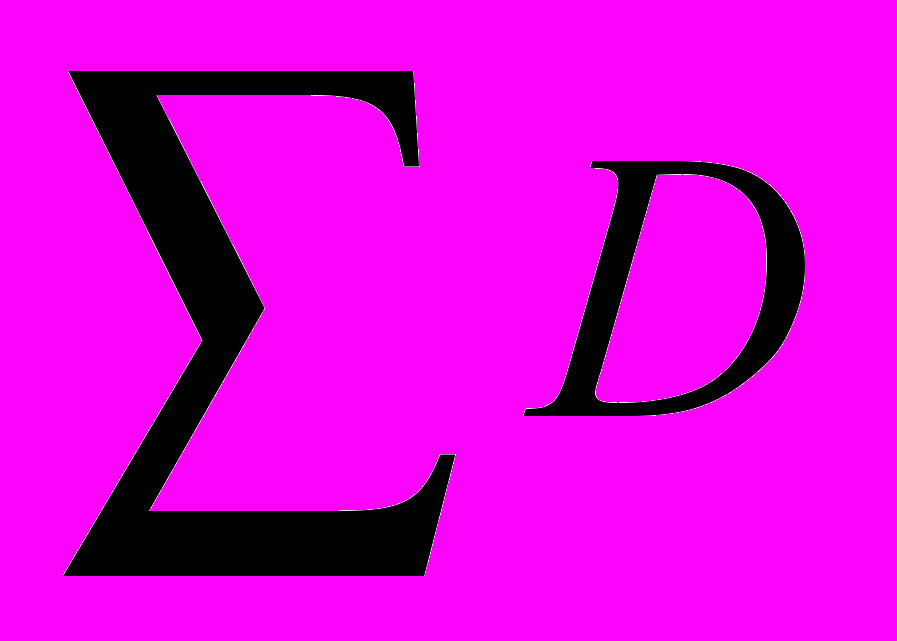
Коэффициент частоты несчастных случаев со смертельным исходом
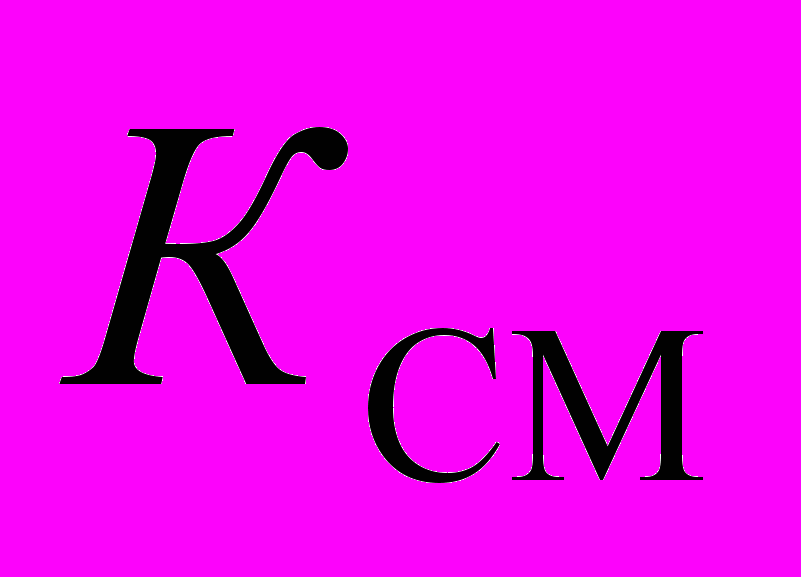
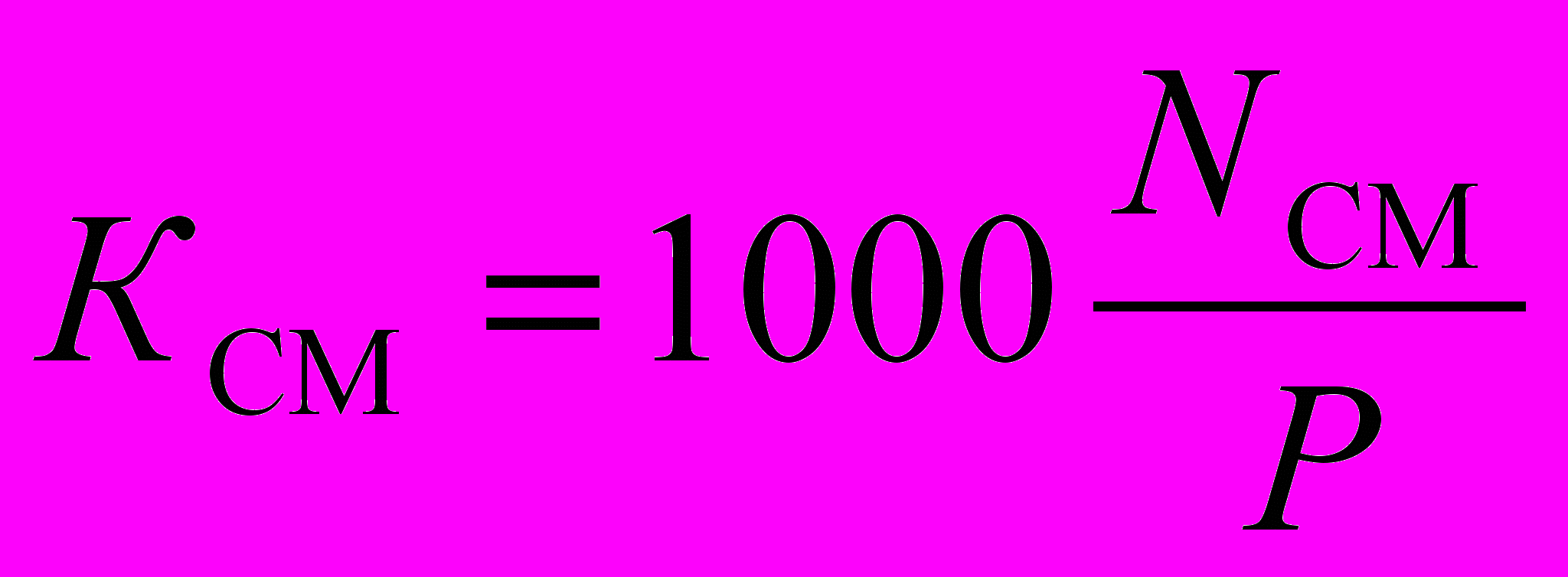
где
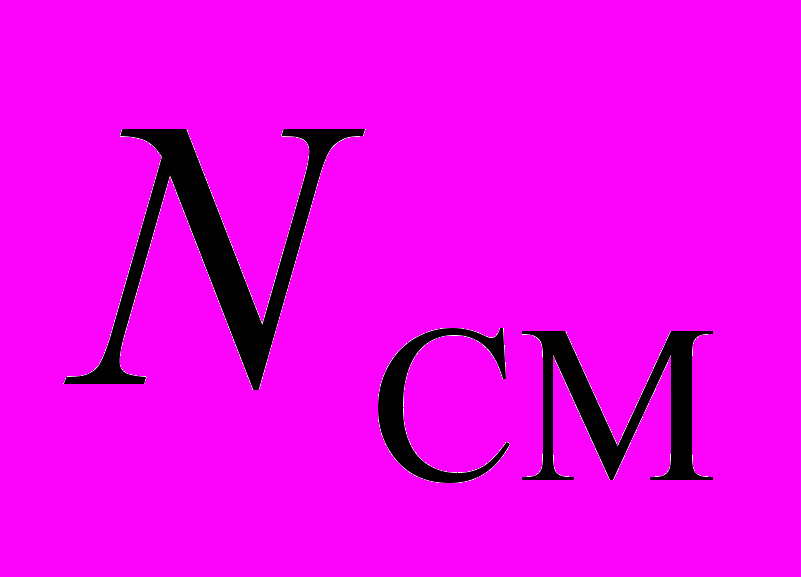
Пример: Рассчитать коэффициент частоты и коэффициент тяжести травматизма для строительной организации численностью 800 человек, если известно, что за пять лет ее работы произошло 6 несчастных случаев с потерей временной трудоспособности общей продолжительностью 72 дня.
Решение: Для определения коэффициентов частоты и тяжести травматизма в организации используем формулы (1.1) и (1.2):
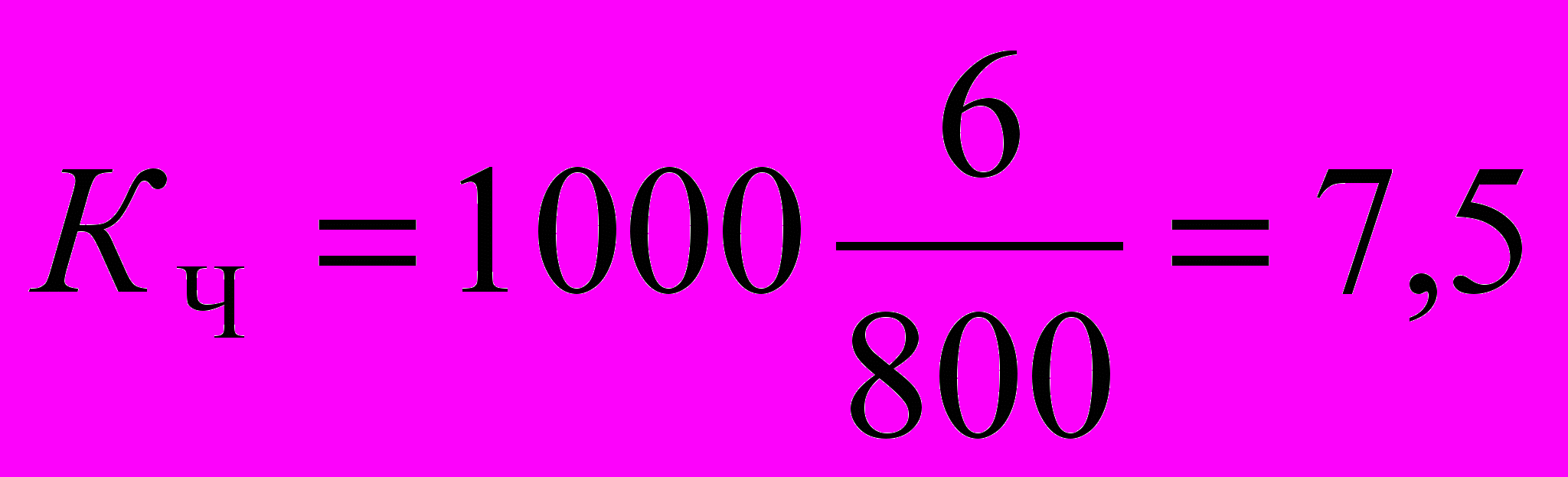
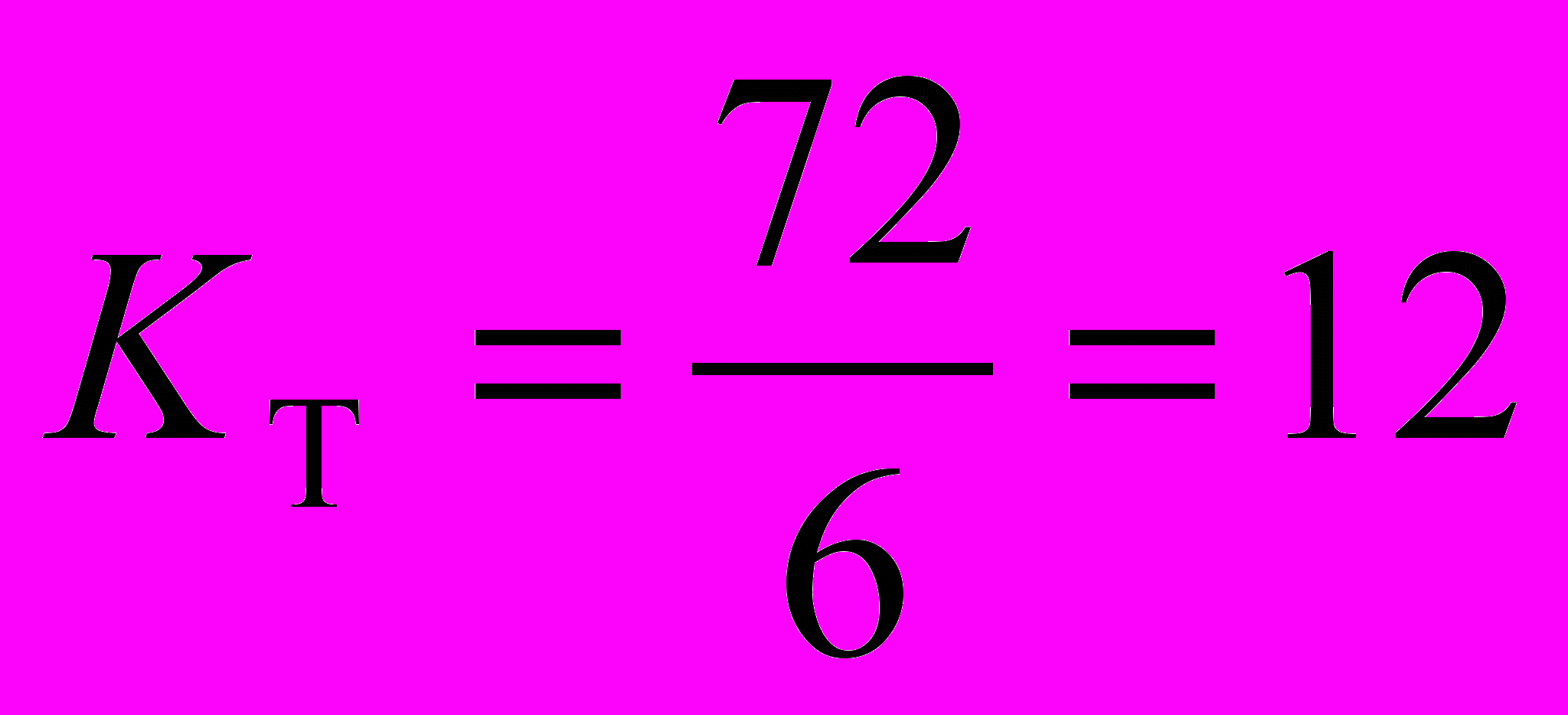
1.2. Методы анализа риска
Риск – количественная оценка опасности, которая выражается отношением числа тех или иных неблагоприятных последствий к их возможному числу за рассматриваемый период.
Применительно к производственной деятельностью используется понятие риска производственного травматизма как количественный показатель безопасности. Он определяет фактическую меру вероятности повреждения здоровья или гибели работающего вследствие воздействия на него опасных производственных факторов при исполнении своих трудовых обязанностей. Риск производственного травматизма во многом определяется квалификацией и обученностью работников действиям в опасной ситуации и их защищенностью. При анализе значение риска не определяется для каждого работника. Это значение может быть определено для группы людей, характеризующихся одинаковым временем нахождения в опасных условиях, например, для бригады отделочников и т.п.
Значение риска R можно определить как ожидаемое значение ущерба n, причиненного за промежуток времени , отнесенное к группе людей численностью P человек:
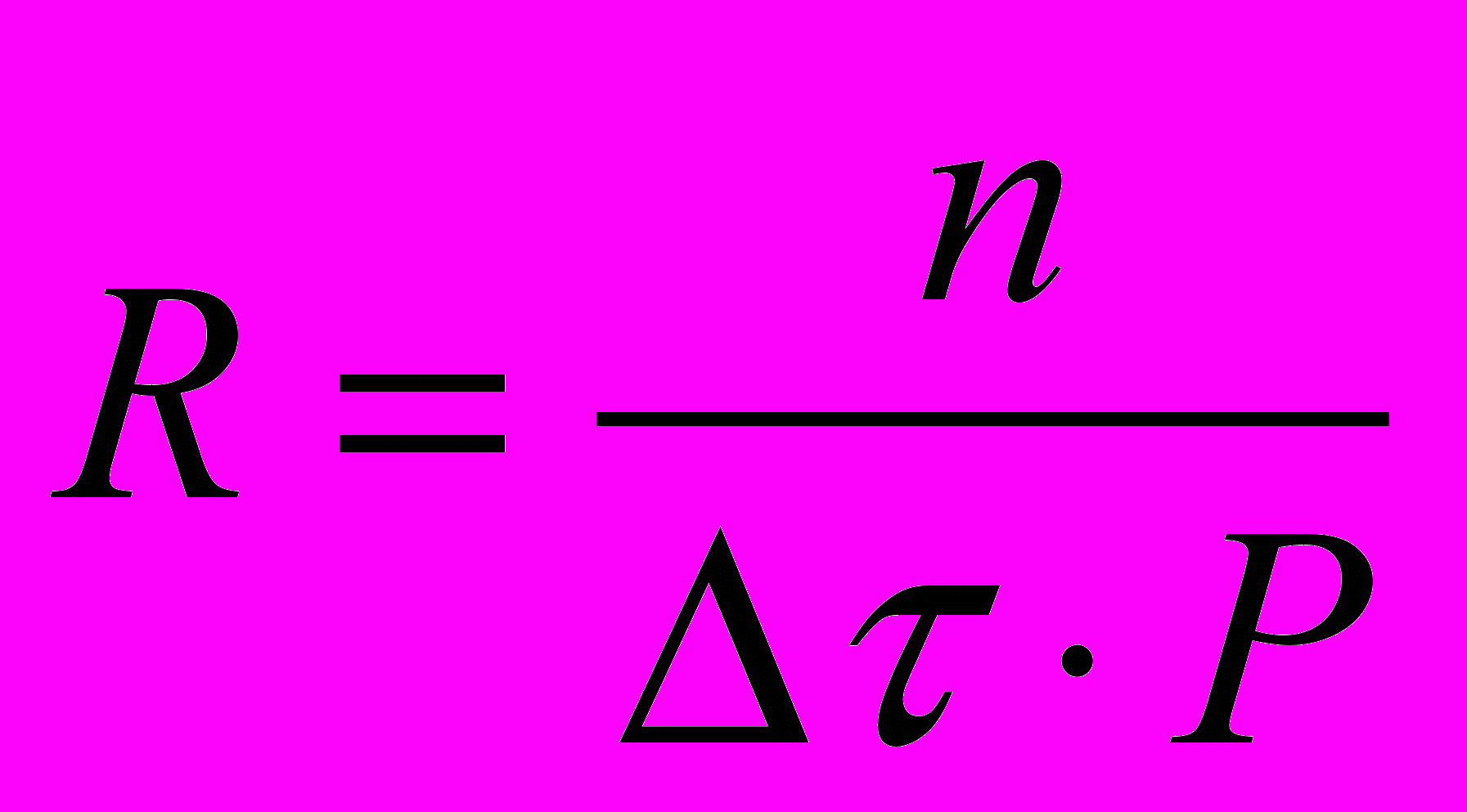
Понятие риска всегда включает два элемента: частоту, с которой осуществляется опасное событие, и последствия опасного события.
Оценка риска включает в себя анализ частоты, анализ последствий и их сочетание. Поэтому анализ риска целесообразно рассматривать как часть системного подхода к принятию решения и практических мер в решении задач предупреждения или уменьшения опасности для жизни человека, заболеваний или травм, ущерба имуществу и окружающей среде.
Анализ производственного риска рекомендуется проводить поэтапно по следующей схеме:
планирование и организация работ;
идентификация опасностей;
оценка риска;
разработка рекомендаций по уменьшению риска.
При планировании и организации работ описываются причины и проблемы, которые вызвали необходимость проведения анализа риска.
При идентификации опасностей основной задачей является выявление (на основе информации о безопасности данного объекта, результатов экспертиз и опыта работы подобных систем) и четкое описание всех присущих системе опасностей.
В принципе процесс анализа риска может заканчиваться на этапе идентификации опасностей. Только при необходимости после идентификации опасностей можно перейти к другим описанным выше этапам [13].
1.3. Методы идентификации опасностей
Идентификация опасностей может производиться следующими основными методами:
«что будет, если … ?»;
проверочного листа;
«дерево отказов»;
«дерево событий»;
эквивалентным.
Методы можно применять каждый в отдельности или в дополнении друг к другу. Качественные методы могут включать количественные критерии риска. Полный количественный анализ риска может включать все указанные методы.
Методы «что будет, если … ?» и проверочного листа относят к группе качественных методов оценки опасности. Результатом этих методов является перечень вопросов и ответов о соответствии объекта требованиям безопасности и выработанные рекомендации по обеспечению безопасности.
Анализ причин несчастных случаев на производстве показывает, что их возникновение, как правило, характеризуется комбинацией случайных локальных событий (неполадки оборудования, человеческие ошибки и т.д.). Для выявления причинно-следственных связей между этими событиями используют логико-графические методы «дерево отказов» и «дерево событий». При анализе методом «дерева отказов» выявляются комбинации неполадок оборудования, ошибок персонала, приводящих к несчастному случаю на производстве. Метод используется для анализа возникновения опасных ситуаций и расчета ее вероятности (на основе знания вероятностей исходных событий).
Для анализа развития опасной ситуации используется метод «дерево событий». По этому методу частота каждого сценария развития несчастного случая рассчитывается умножением частоты основного события на вероятность конечного события.
Методы анализа «деревьев» наиболее трудоемки и применяются для анализа проектов или модернизации сложных технических систем и производств, и требуют высокой квалификации исполнителей. Поэтому рассмотрим более подробно применение метода «дерево отказов», который используется на производстве для определения причин возникновения отказов оборудования [4].
Метод заключается в построении и анализе модели, представляющей собой логико-вероятностную модель причинно-следственных связей отказов изделия с отказами его элементов и другими событиями. Основной принцип построения «дерева отказов» состоит в последовательной постановке вопросов и дачи ответов, по каким причинам может произойти отказ изделия. Для наглядного представления причинной взаимосвязи с помощью «дерева отказов» используют логические символы и символы событий. Логические символы связывают события в соответствии с их причинными взаимосвязями. Обозначения символов приведены в табл. 1.1, а символы событий в табл. 1.2.
Таблица 1.1
Обозначения логических символов
Символ логического знака | Название логического знака | Причинная взаимосвязь |
![]() | «И» | Выходное событие происходит, если все входные события случаются одновременно |
![]() | «ИЛИ» | Выходное событие происходит, если случается любое из входных событий |
![]() | «ЗАПРЕТ» | Наличие входа вызывает появление выхода тогда, когда происходит условное событие |
![]() | Приоритетное«И» | Выходное событие имеет место, если все входные события происходят в нужном порядке слева направо |
![]() | Исключающее «ИЛИ» | Выходное событие происходит, если случается одно (но не оба)из входных событий |
![]() m n | «m» из «n» | Выходное событие происходит, если случается «m» из «n» входных событий |
Таблица 1.2
Обозначения символов событий
Символ события | Содержание события |
![]() | Исходное событие, обеспеченное достаточными исходными данными |
![]() | Событие недостаточно детально разработанное |
![]() | Событие, вводимое логическим элементом |
![]() | Условное событие, используемое с логическим знаком «запрет» |
![]() | Событие, которое может случаться или не случаться |
![]() ![]() | Символ перехода |
Схемы применения символов логических знаков и символов событий в зависимости от исходных событий 1,2,…, n в схемах «дерева отказов» показаны на рис. 1.1. и 1.2.
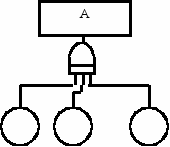
1 2 … n
Рис. 1.1. Применение логического символа «И»
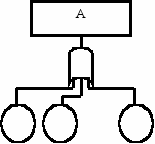
1 2 … n
Рис. 1.2. Применение логического символа «ИЛИ»
Пример 1: Определить риск R гибели человека в строительном производстве в нашей стране за 1 год, если известно, что ежегодно погибает 600 человек, а численность рабочих составляет 700000 человек.
Остановка станка
А





Параметрический отказ
Б
Функциональный отказ
В





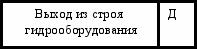
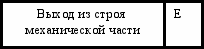
Выход из строя
электрооборудования
Г





















































Рис. 1.3. «Дерево отказов» для металлорежущего станка
Решение: Для определения риска гибели человека используем формулу (1.4):
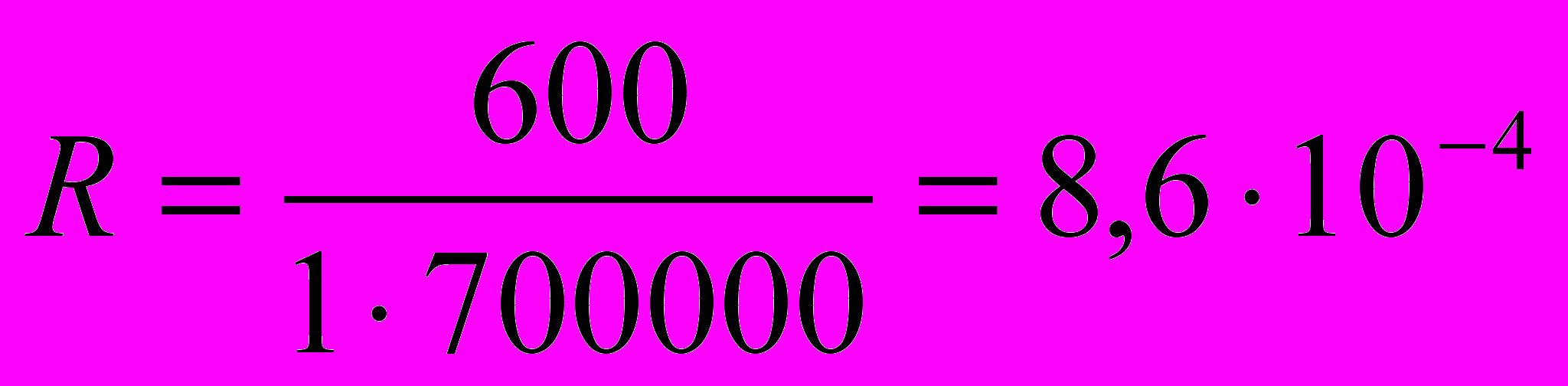
Пример 2. Используя метод «дерево отказов», оценить вероятность отказа работы станка сверлильно-расточной группы. Основными движениями у станка являются: главное движение резания, т.е. вращение инструмента и движение подачи резца.
Решение. Отказ станка может произойти из-за функционального отказа, явившегося следствием внезапных отказов блоков, узлов, деталей станка, или из-за параметрического отказа, который произойдет, когда будет исчерпана технологическая надежность, как показано на рис. 1.3.
Функциональный отказ может иметь место, если будут реализованы приводимые ниже прогнозируемые причинно-следственные цепи опасностей, которые вызовут остановку станка:
отказ электродвигателя;
отказ концевого выключателя;
короткое замыкание кабеля на землю;
отказ предохранителя;
короткое замыкание электропровода на корпус;
отказ насоса;
отказ пружины предохранительного клапана;
отказ дросселя;
отказ обратного клапана;
отказ предохранительного клапана;
потеря герметичности в маслопроводе;
отказ муфты главного двигателя;
отказ муфты первого вала коробки скоростей;
отказ зубчатых колес коробки скоростей;
отказ ограничителя передвижных зубчатых колес коробки скоростей остановка станка;
отказ шестерни коробки подач;
отказ муфты сцепления шестерен коробки подач.
На основании наших рассуждений построим «дерево отказов» металлорежущего станка, как показано на рис. 1.3.
На рис. 1.3 обозначено: 1 отказ электродвигателя; 2 отказ концевого выключателя; 3 короткое замыкание кабеля на землю; 4 отказ предохранителя; 5 короткое замыкание на корпус; 6 отказ насоса; 7 поломка пружины клапана; 8 отказ дросселя; 9 отказ обратного клапана; 10 отказ предохранительного клапана; 11 утечки маслопровода; 12 отказ муфты главного двигателя; 13 отказ муфты первого вала коробки скоростей; 14 отказ зубчатых колес коробки скоростей; 15 отказ ограничителя передвижных зубчатых колес коробки скоростей; 16 отказ шестерен коробки подач; 17 отказ муфты сцепления шестерен коробки подач.
1.4. Основные показатели опасности и риска
на производстве
Несчастные случаи на производстве (профессиональные заболевания не рассматриваются) в зависимости от последствий принято классифицировать следующим образом:
– несчастные случаи со смертельным исходом;
– со стойкой утратой трудоспособности (инвалидность);
– с временной потерей трудоспособности на 1 и более рабочих дней;
– с оказанием только первой помощи без утраты трудоспособности.
Характеристику опасности и риска для персонала оценивают числом факторов опасности или исходом несчастных случаев в их взаимосвязи с общими производственными показателями. Наиболее часто используют следующие показатели.
Частота несчастных случаев (коэффициент частоты травматизма)
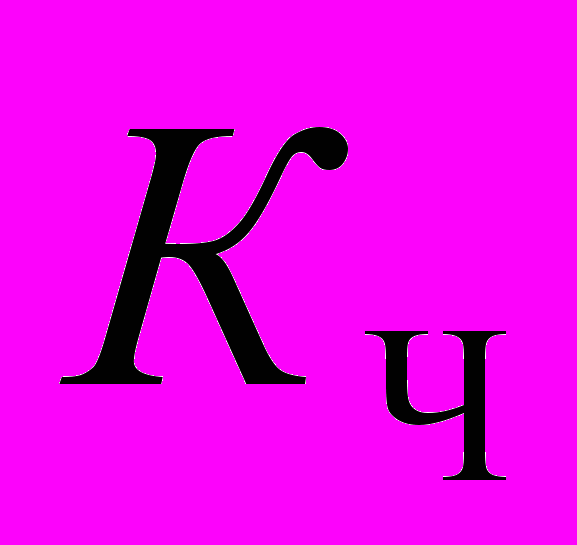
Коэффициент частоты несчастных случаев со смертельным исходом
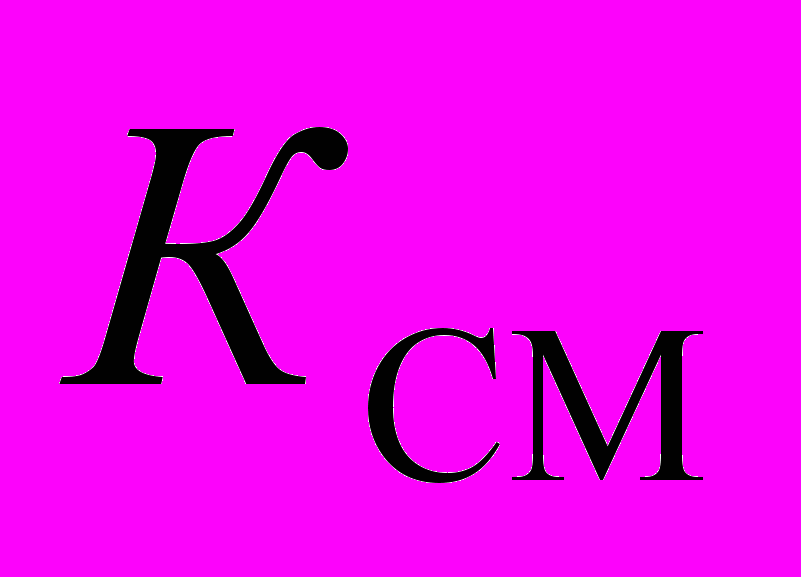
Частота несчастных случаев на 1 млн эффективных часов работы:
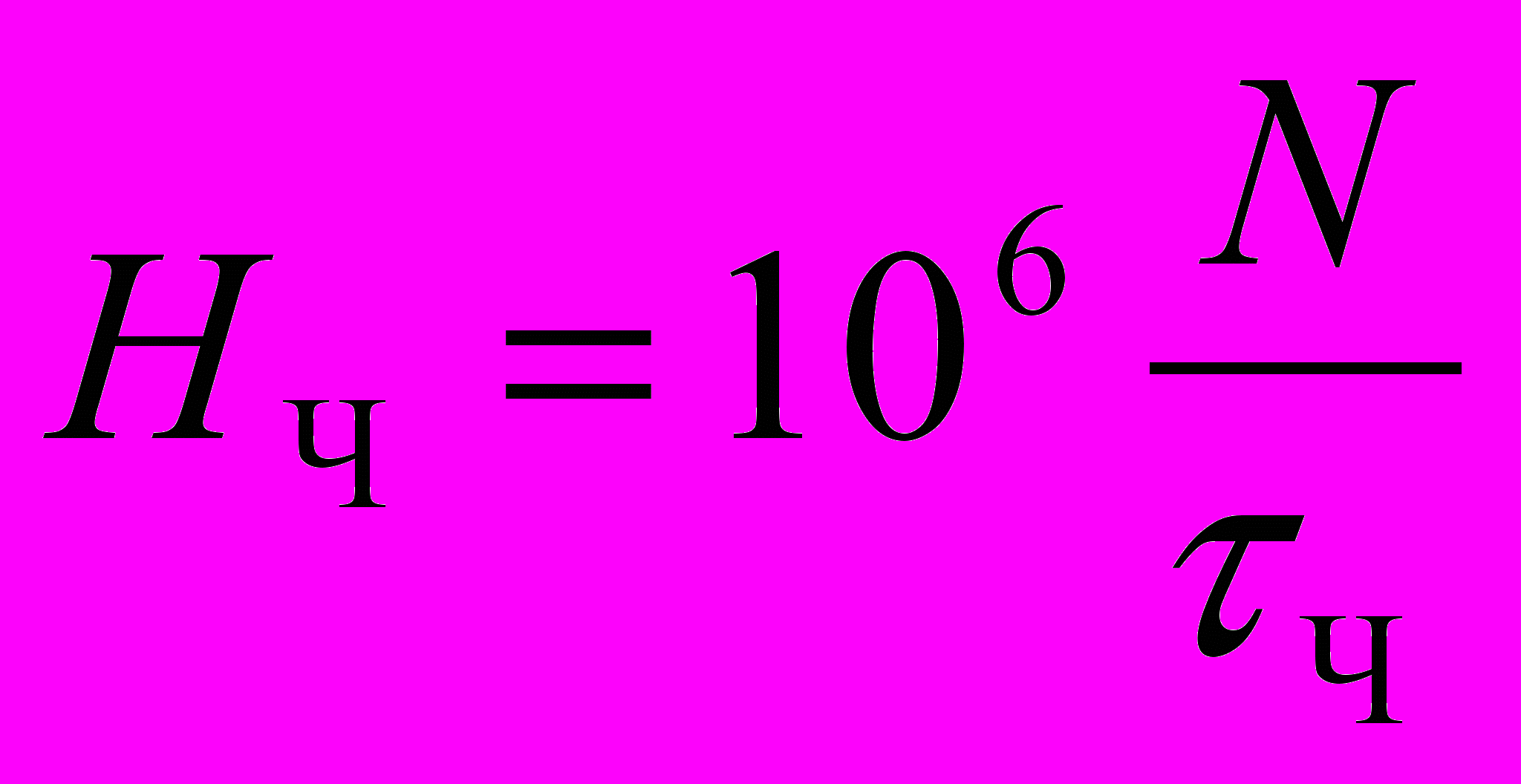
где
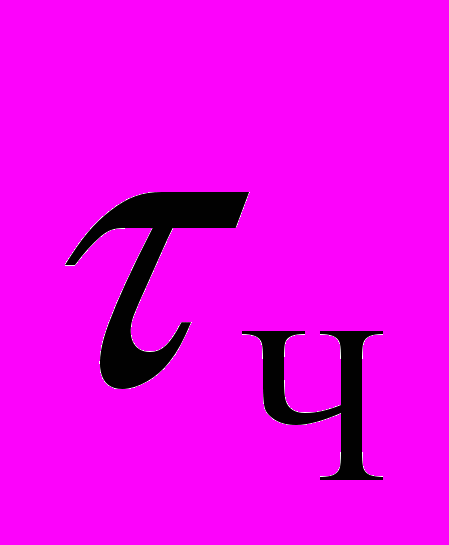
Потенциал опасности травмирования рабочих
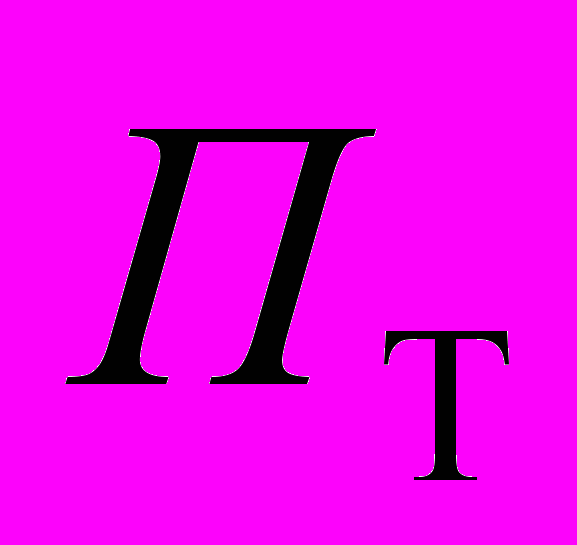
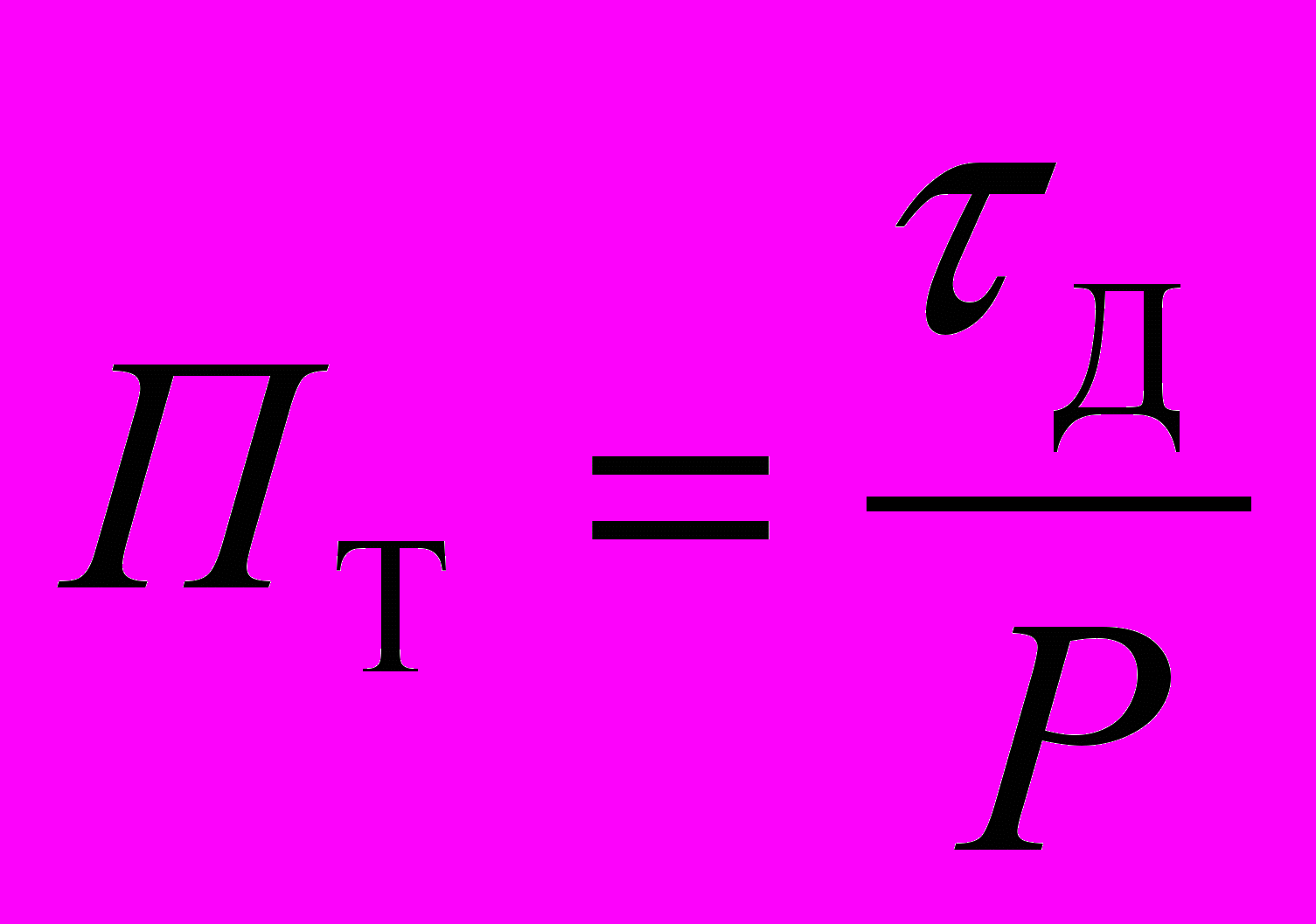
где
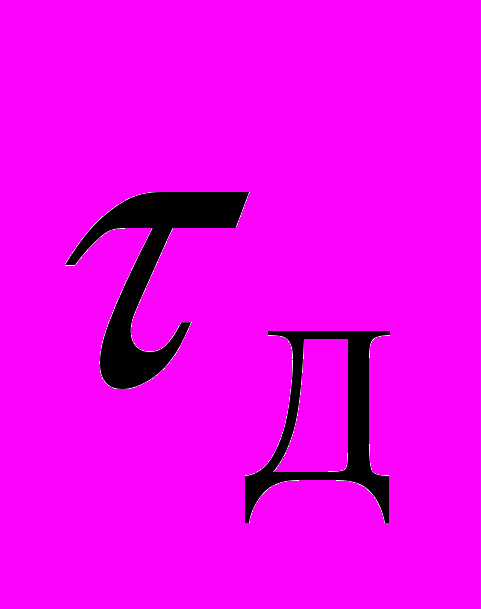
Р численность работающих.
Для расчета коэффициента тяжести травматизма
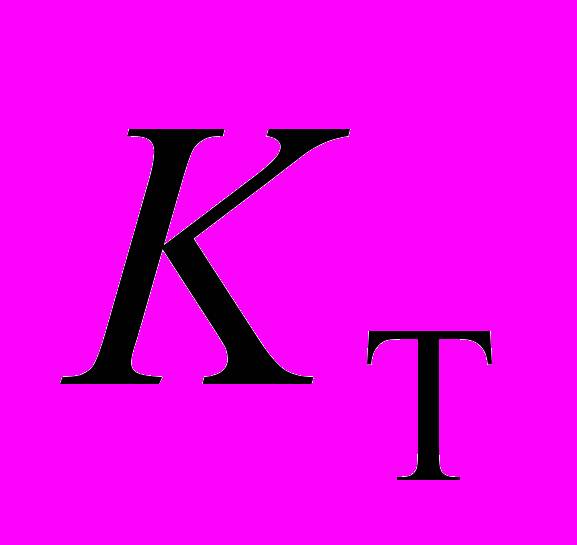
Коэффициент подверженности опасности (угрозы опасности) травмирования работников
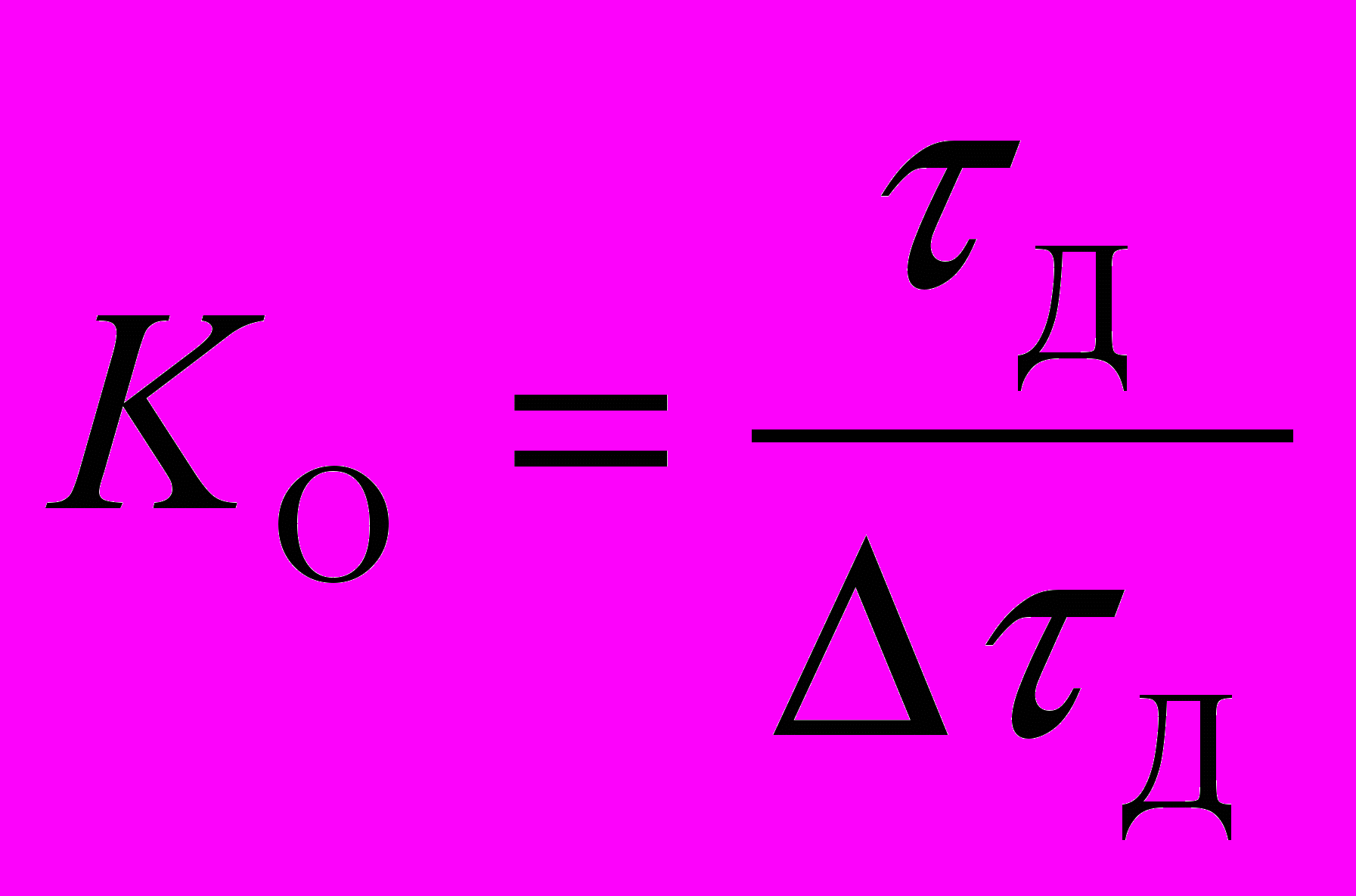
или в пересчете на 1 млн часов эффективного рабочего времени
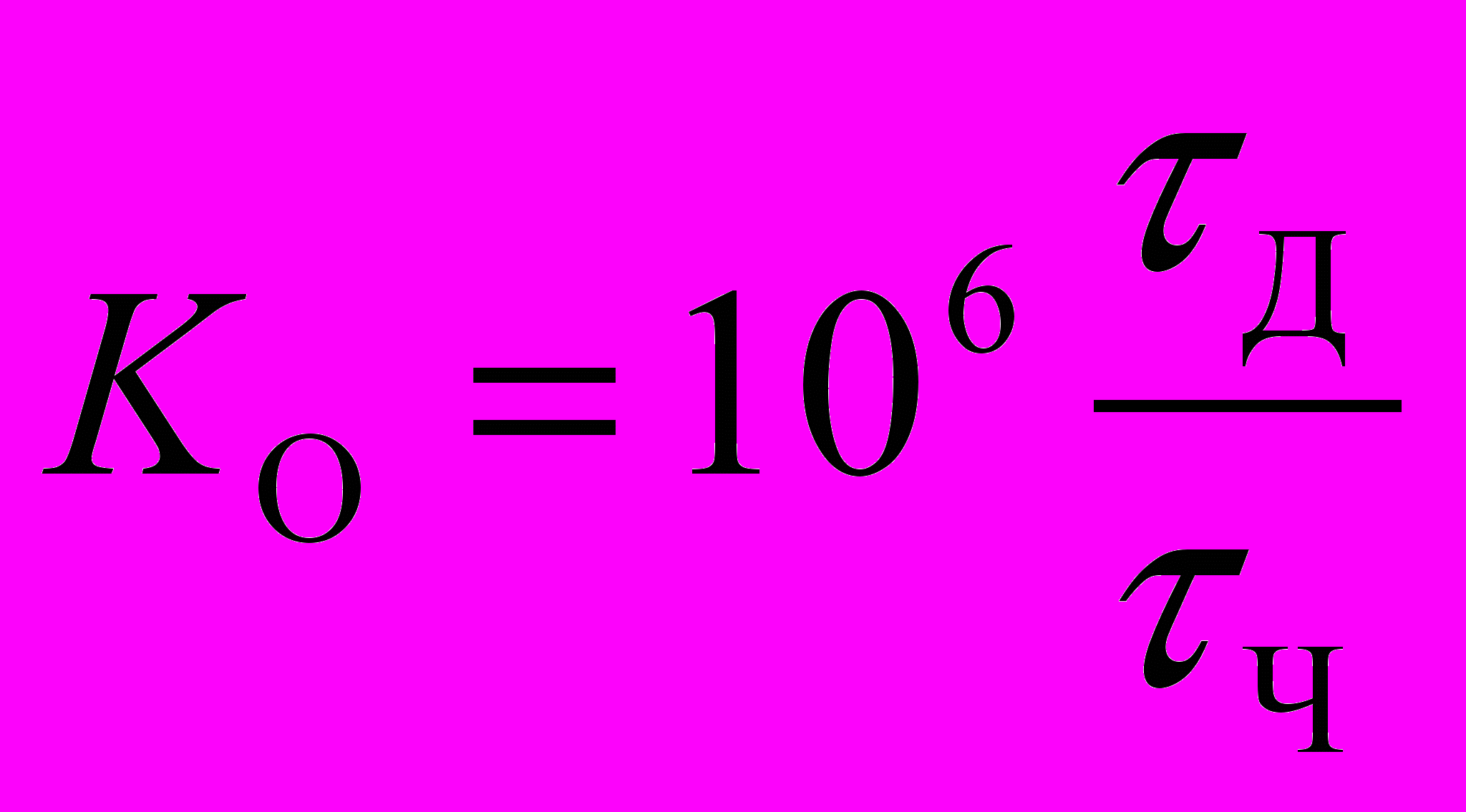
где
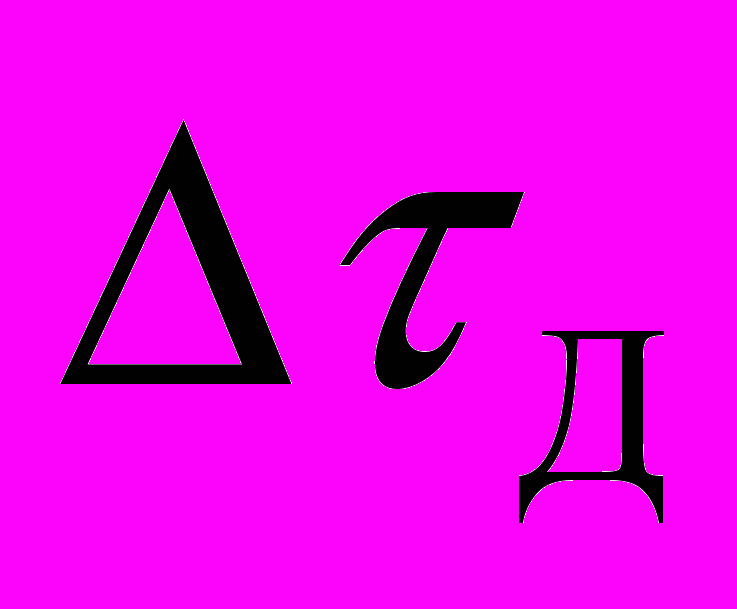
Среднее рабочее время (за год или другой определенный для анализа интервал времени) на одного работника:
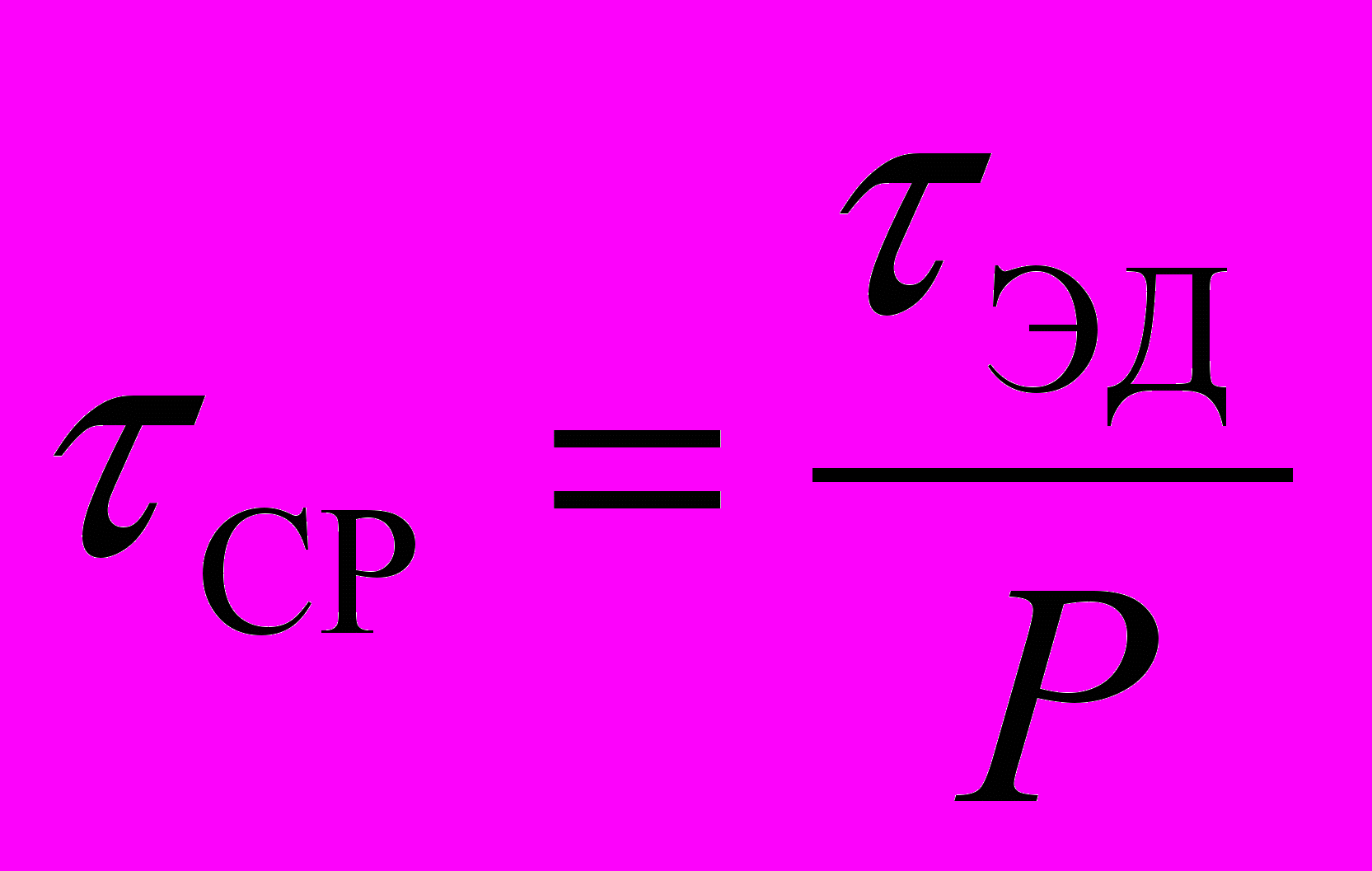
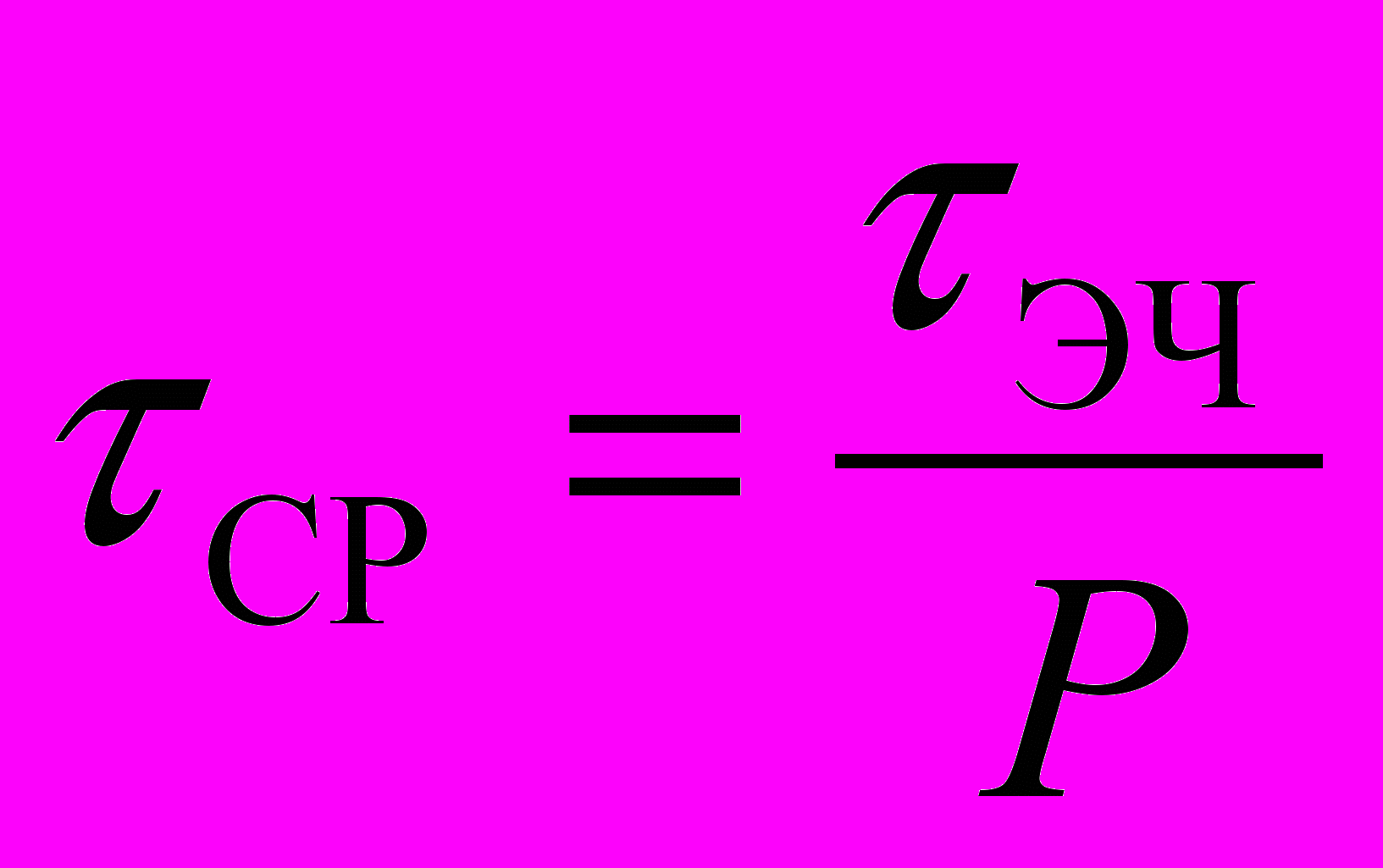
где
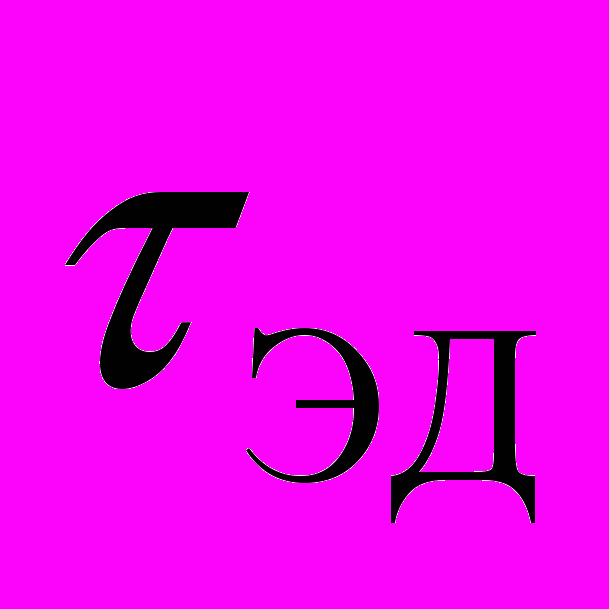
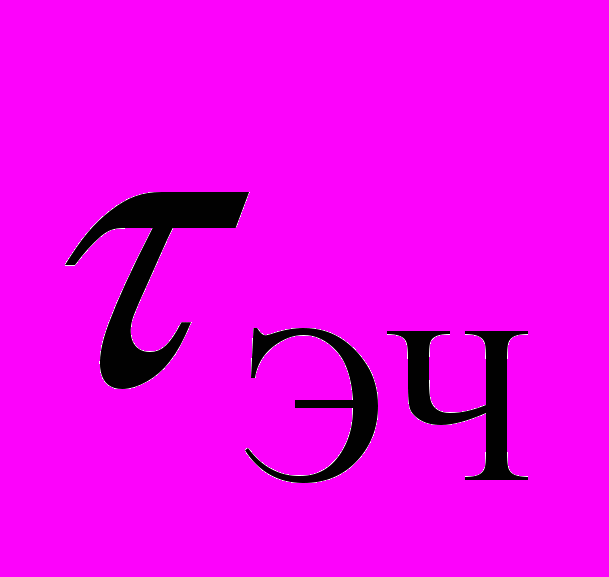
Класс опасности работ
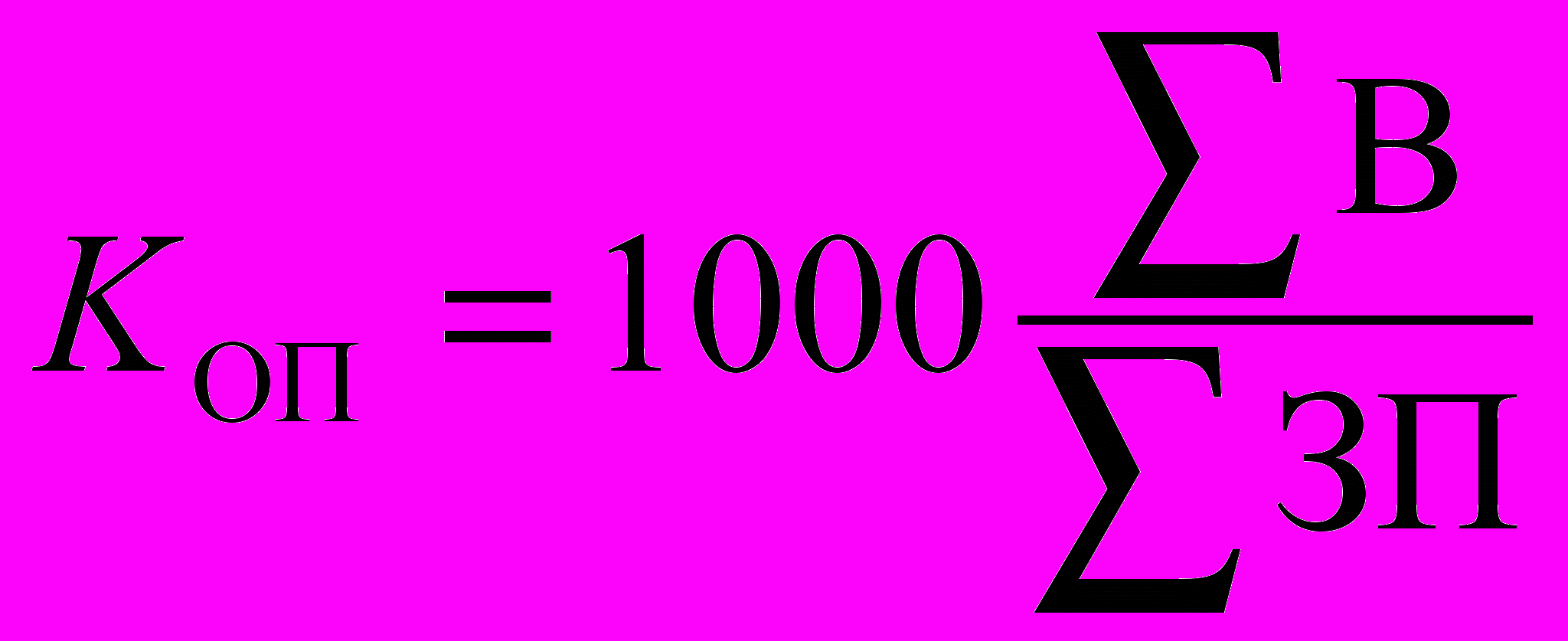
где
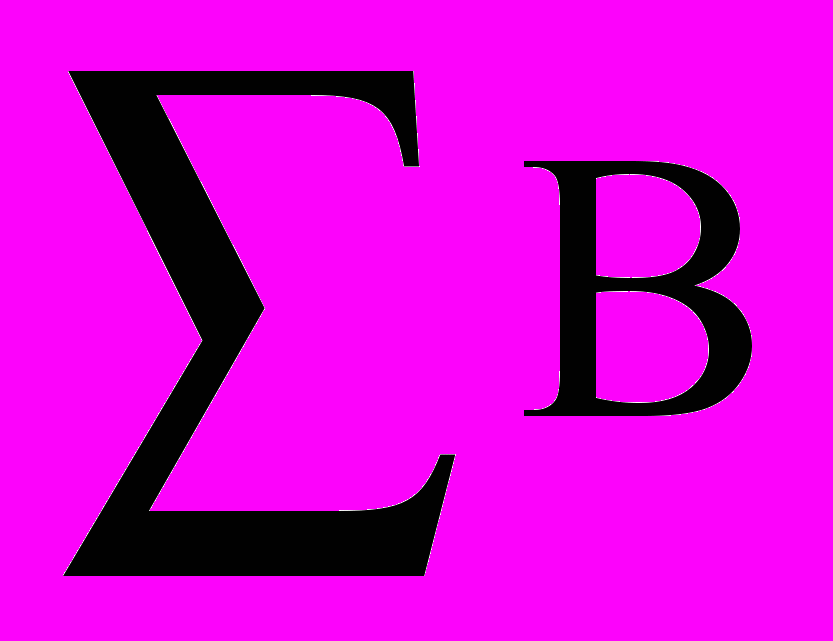
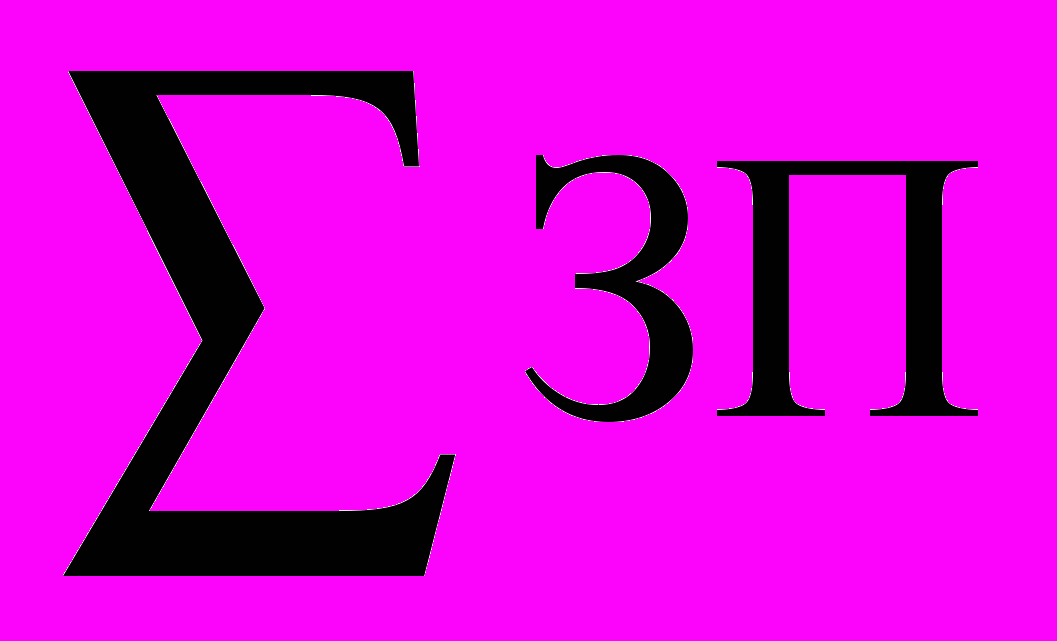
Значение риска R производственного травматизма может быть рассчитано по формуле (1.4) [5].
Пример. Рассчитать основные показатели опасности и риска производственного травматизма для монтажных работ за пятилетний период работы предприятия при следующих показателях: число несчастных случаев на производстве за 5 лет составило 7, в том числе 2 несчастных случая со смертельным исходом; количество дней нетрудоспособности без учета смертельных исходов составило 84; численность работников 270; заработная плата всех застрахованных работников за 5 лет составила 3402000 руб.; среднедневная заработная плата монтажника 150 руб.
Решение. Обозначим исходные данные соответствующими показателями: N = 7;
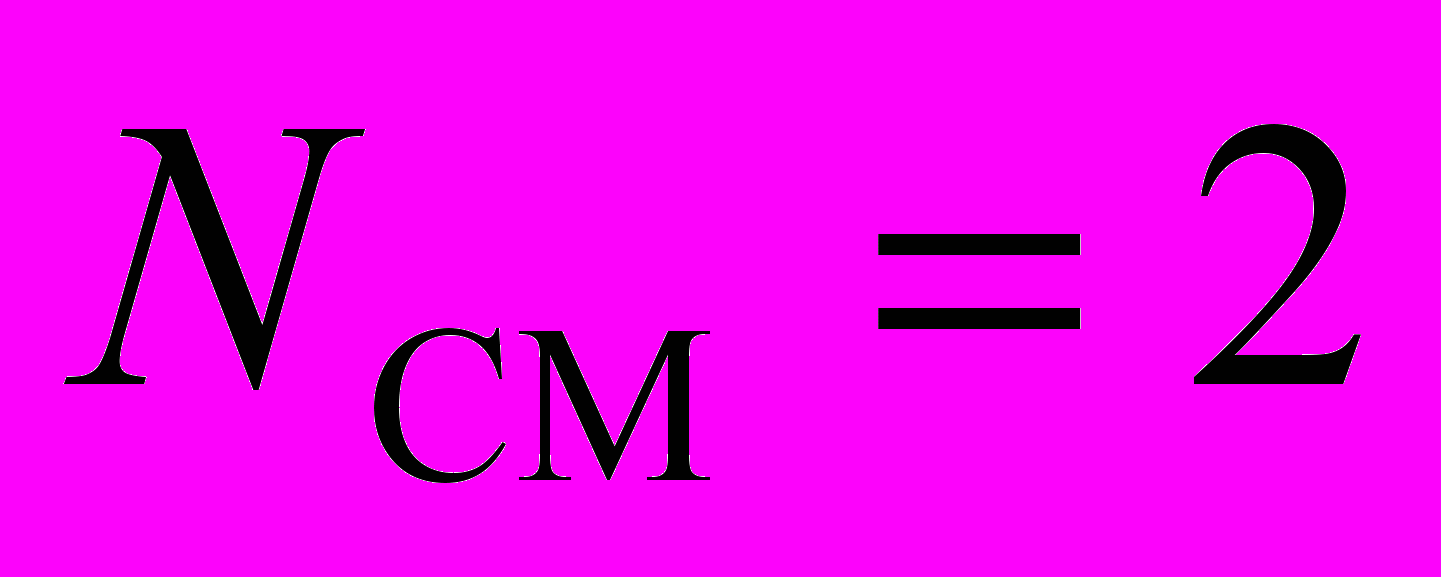
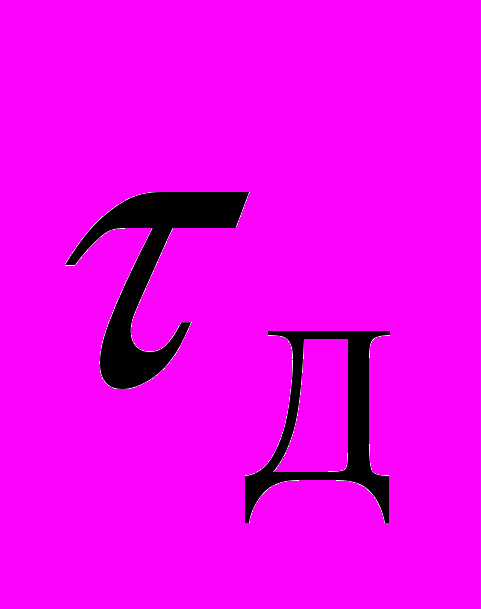
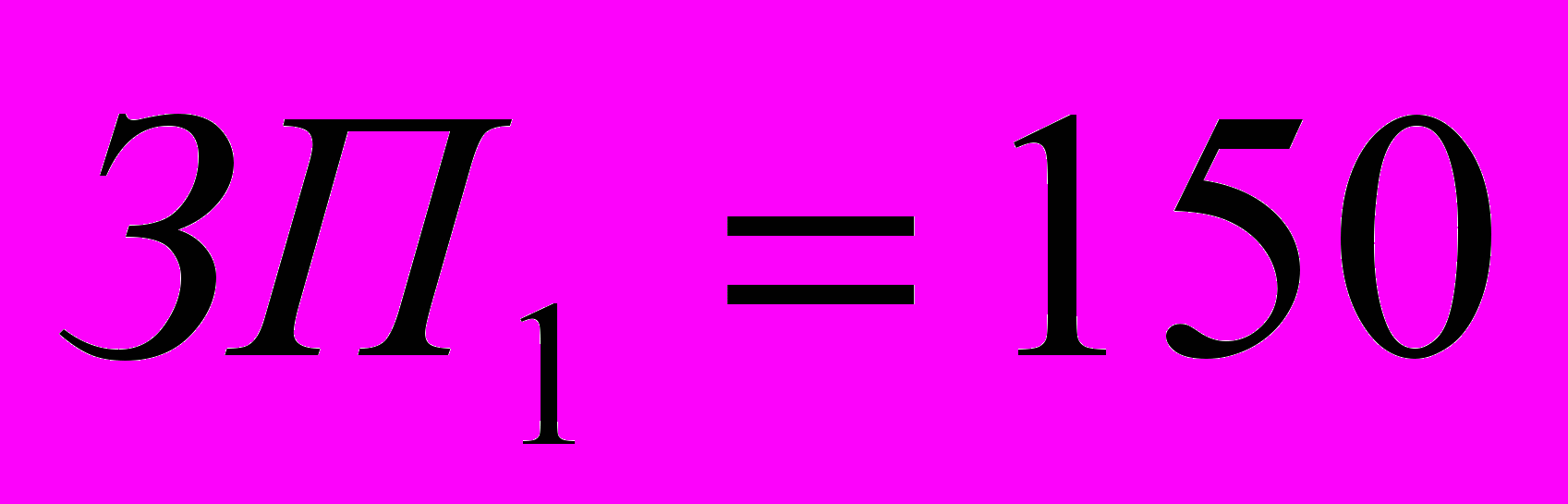
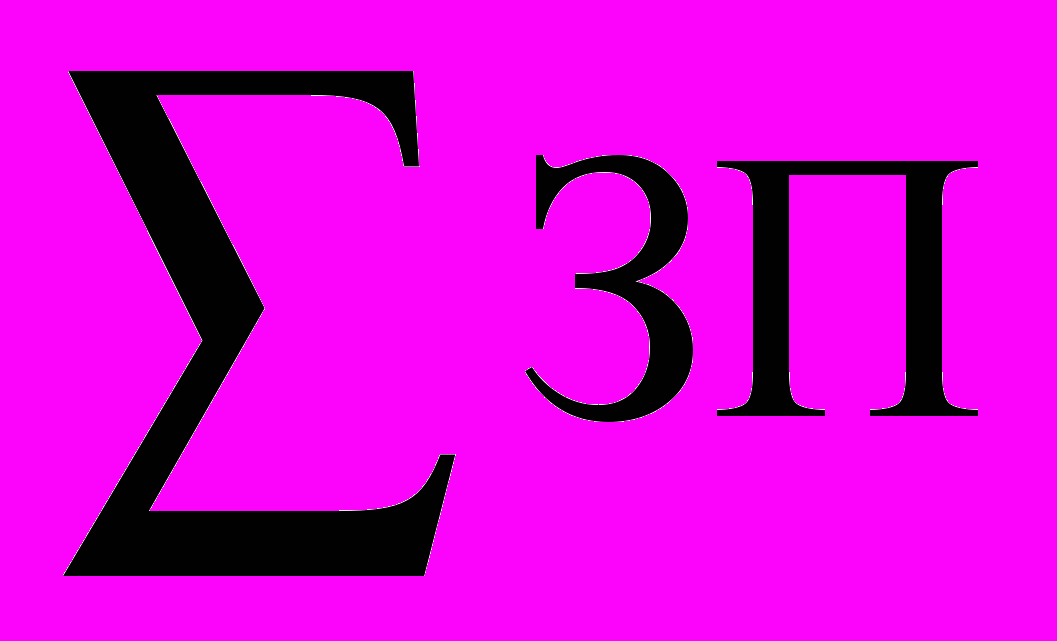
Для определения значений основных показателей опасности и риска при проведении монтажных работ воспользуемся вышеприведенными формулами.
Коэффициент частоты
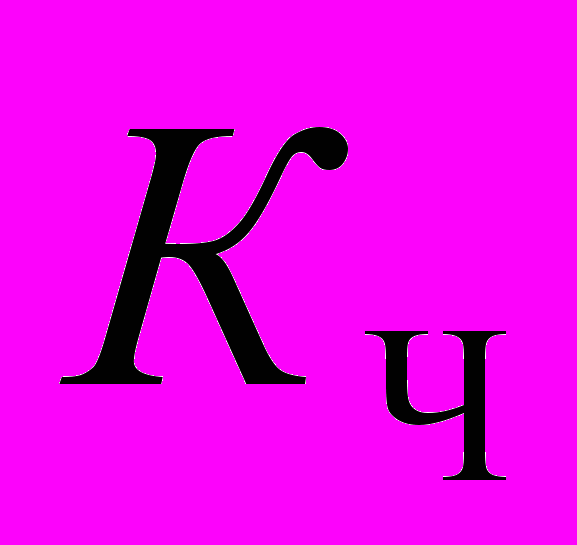
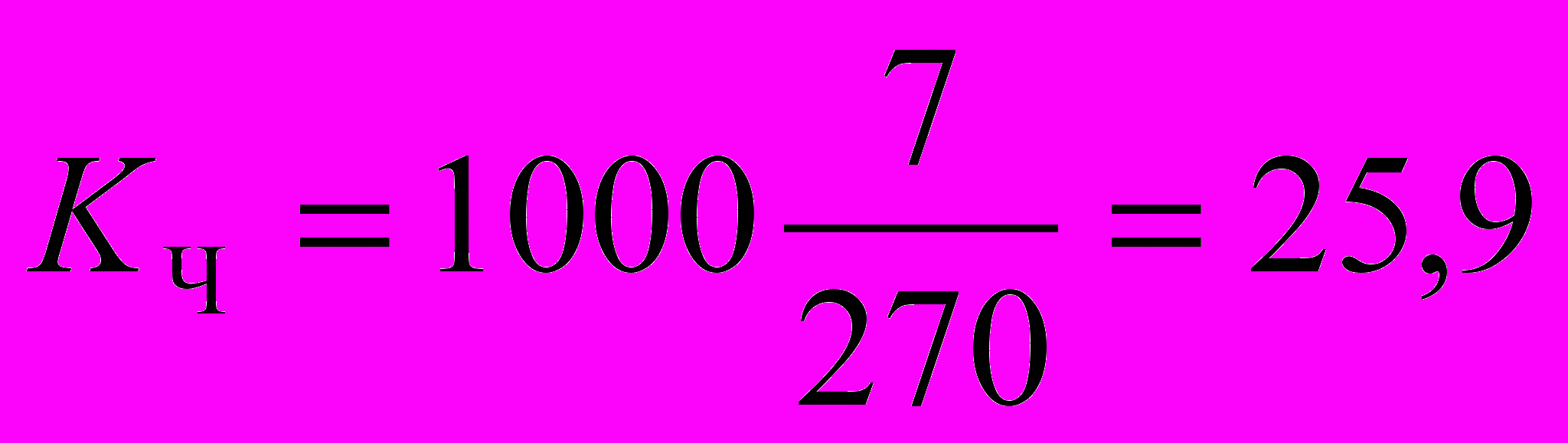
Коэффициент частоты несчастных случаев со смертельным исходом
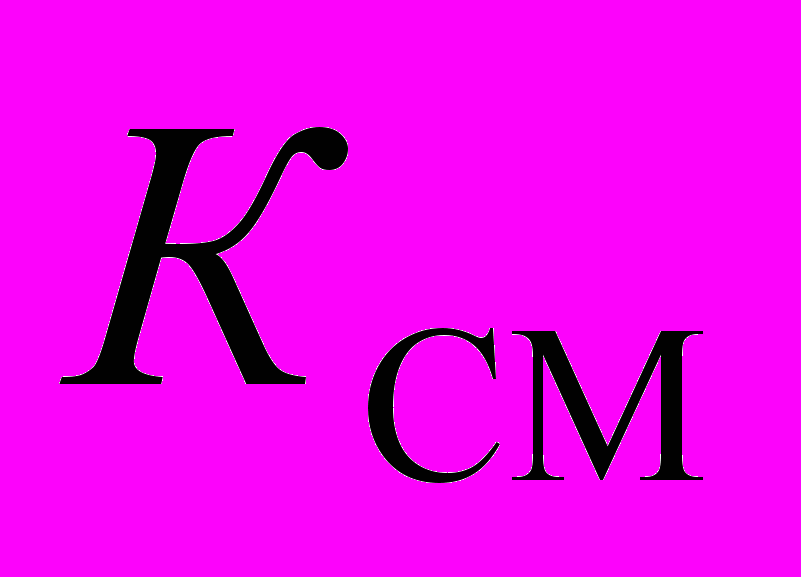
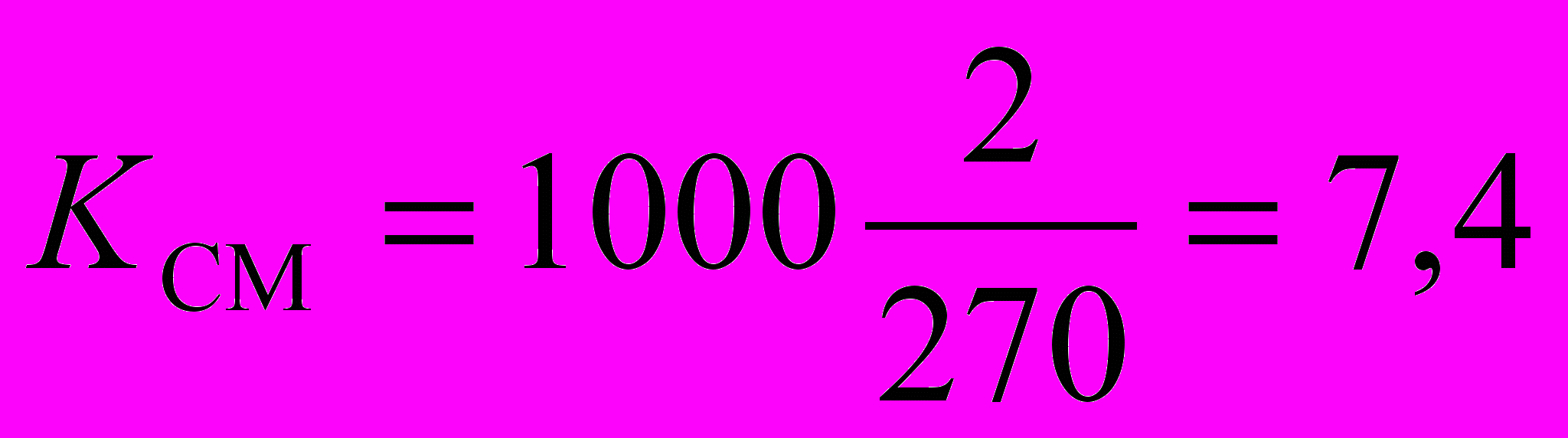
Потенциалы опасности травмирования рабочих без учета
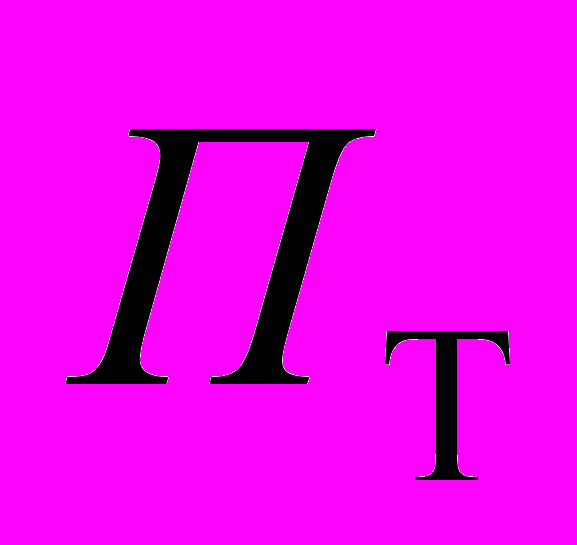
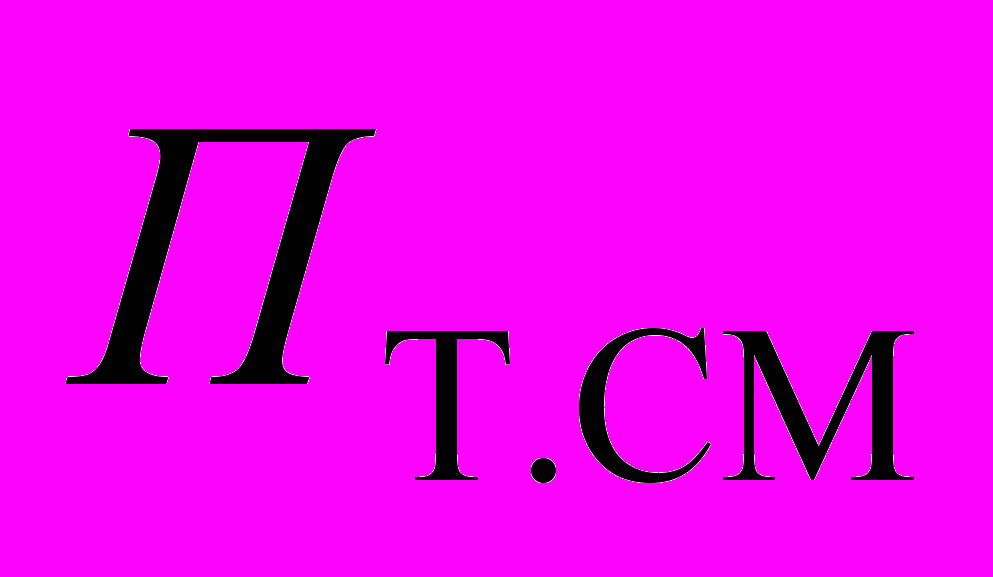
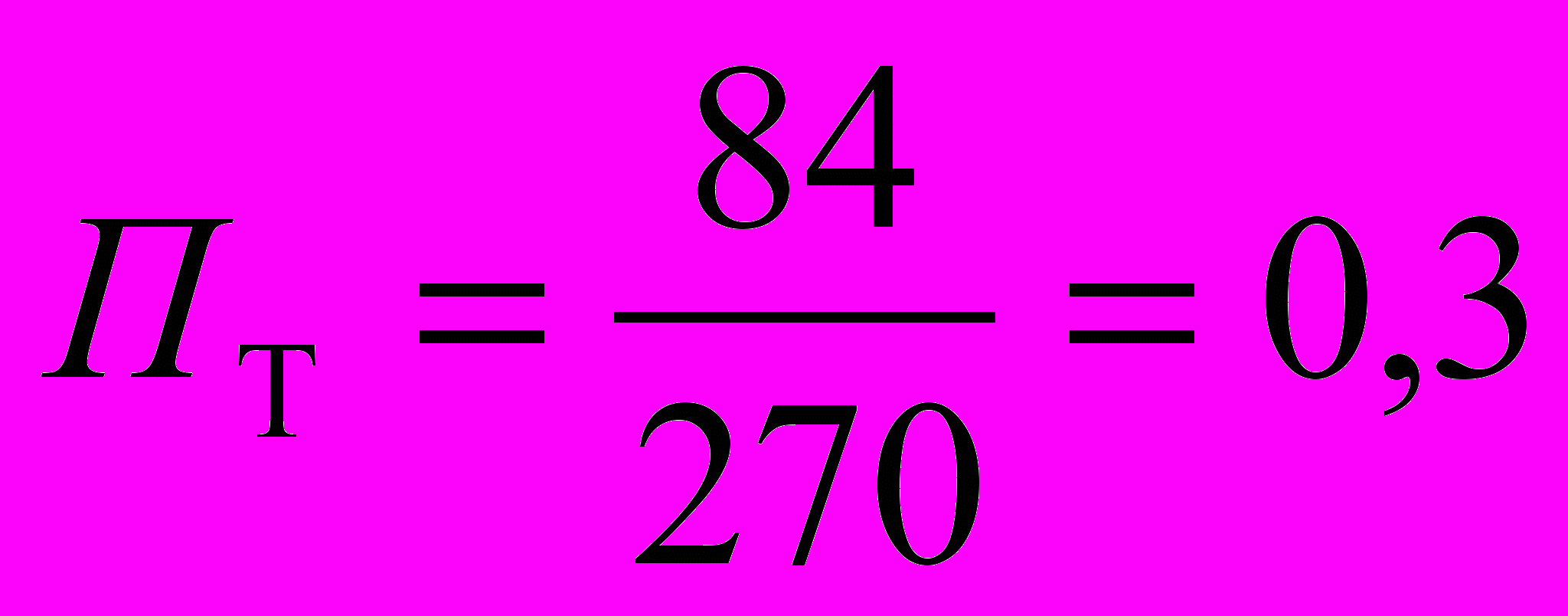

где последствия несчастного случая со смертельным исходом, согласно рекомендации Международной организации труда (МОТ), условно приравнены к 7500 дням потери трудоспособности.
Коэффициент тяжести травматизма
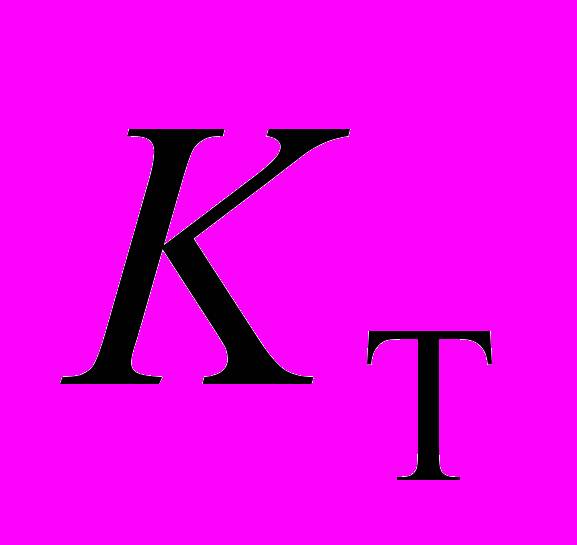
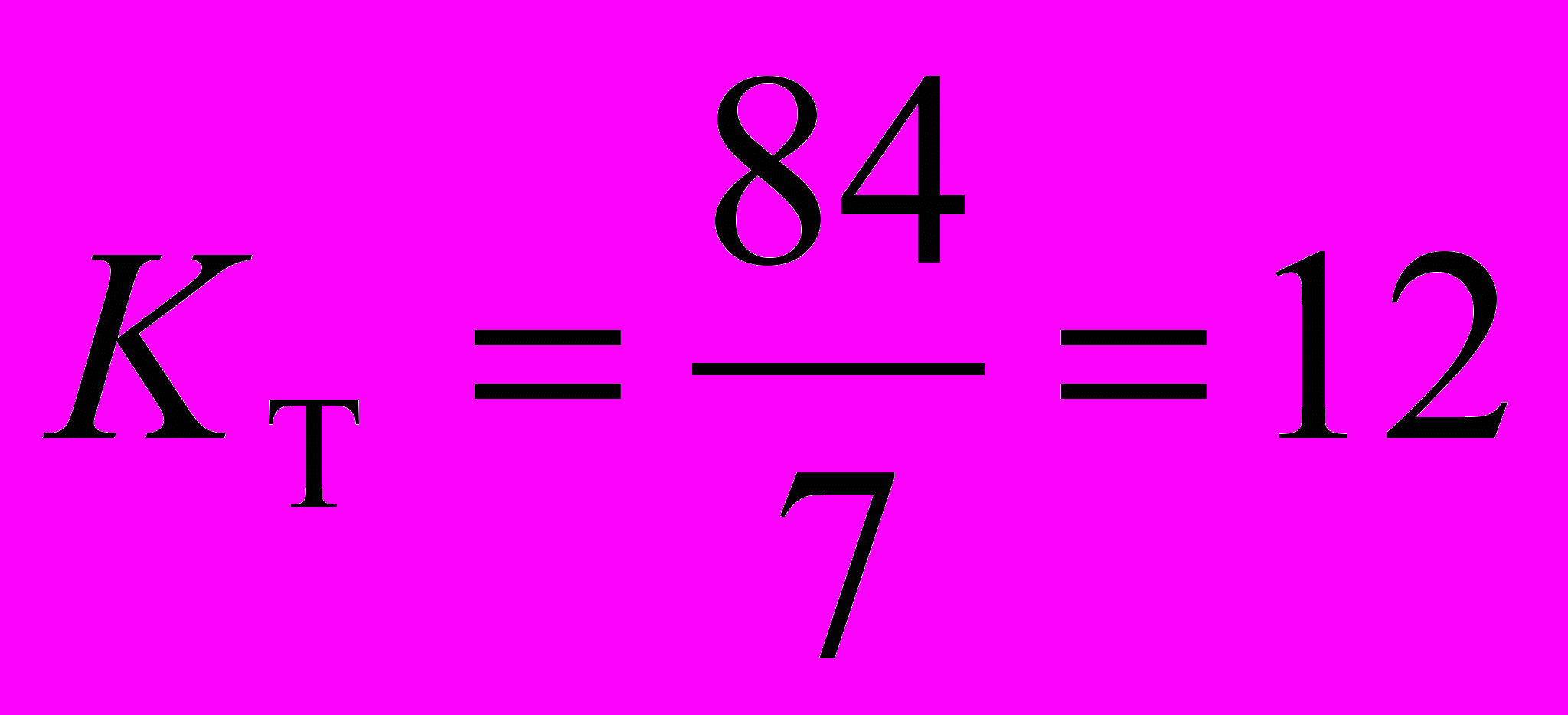
Коэффициент тяжести травмирования рабочих при летальном исходе:

Класс опасности работ (формула (1.10))
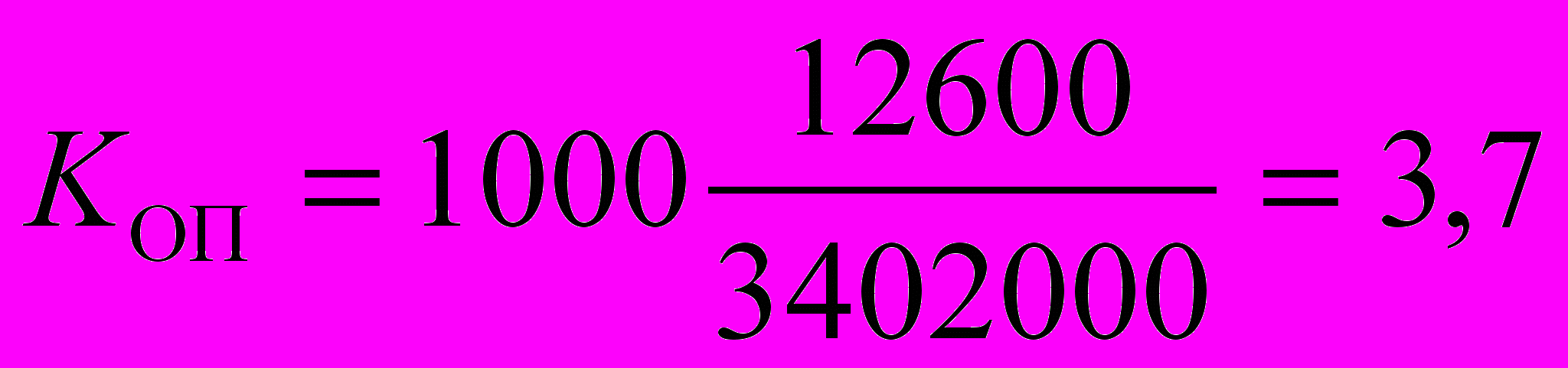
где сумма выплат пострадавшим составляет

Риск производственного травматизма R и риск травматизма со смертельным исходом
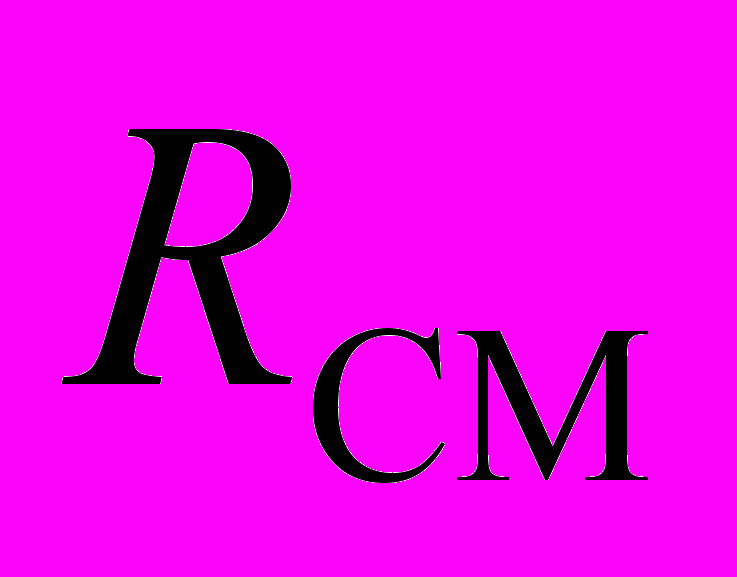
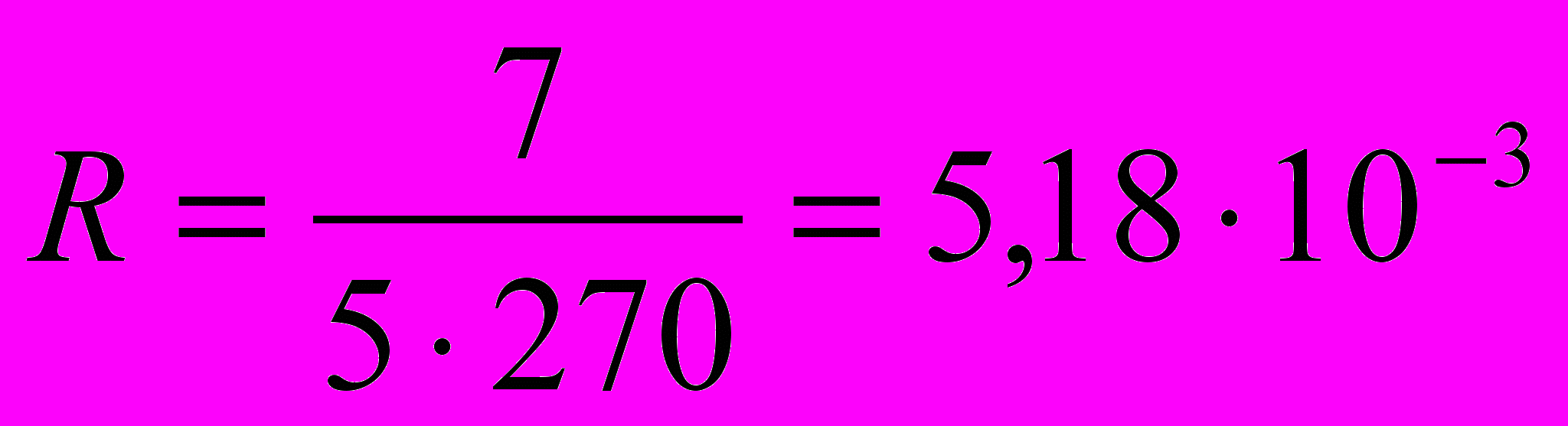
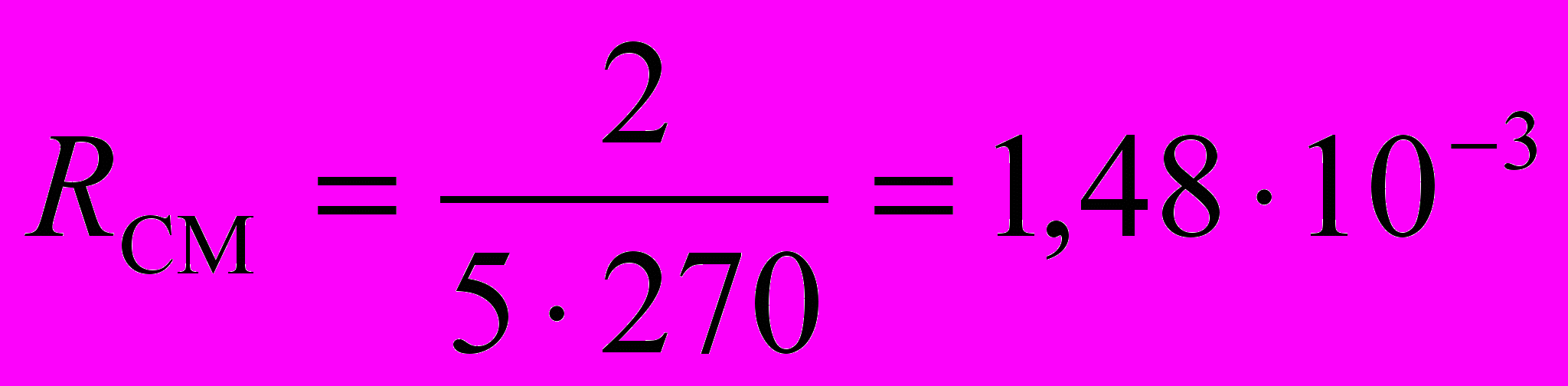
где = 5 лет.