Российская федерация федеральная служба по интеллектуальной собственности, патентам и товарным знакам
Вид материала | Документы |
- Российская федерация федеральная служба по интеллектуальной собственности, патентам, 56.11kb.
- Российская федерация федеральная служба по интеллектуальной собственности, патентам, 18.96kb.
- Российская федерация федеральная служба по интеллектуальной собственности, патентам, 520.15kb.
- Российская федерация федеральная служба по интеллектуальной собственности, патентам, 92.21kb.
- Российская федерация федеральная служба по интеллектуальной собственности, патентам, 31.66kb.
- Российская федерация федеральная служба по интеллектуальной собственности, патентам, 35.17kb.
- Российская федерация федеральная служба по интеллектуальной собственности, патентам, 73.08kb.
- Российская федерация федеральная служба по интеллектуальной собственности, патентам, 72.99kb.
- Российская федерация федеральная служба по интеллектуальной собственности, патентам, 59.93kb.
- Российская федерация федеральная служба по интеллектуальной собственности, патентам, 38.13kb.
РОССИЙСКАЯ ФЕДЕРАЦИЯ ![]() ФЕДЕРАЛЬНАЯ СЛУЖБА ПО ИНТЕЛЛЕКТУАЛЬНОЙ СОБСТВЕННОСТИ, ПАТЕНТАМ И ТОВАРНЫМ ЗНАКАМ | (19) | RU | (11) | 2224045 | (13) | C1 | | |
(51) МПК 7 C22C38/50, C22C38/58 | ||||||||
(12) ОПИСАНИЕ ИЗОБРЕТЕНИЯ К ПАТЕНТУ
|
(21), (22) Заявка: 2002115586/02, 11.06.2002 (24) Дата начала отсчета срока действия патента: 11.06.2002 (46) Опубликовано: 20.02.2004 (56) Список документов, цитированных в отчете о поиске: US 6406562, 16.05.2000. RU 94033442 A, 10.04.1997. RU 2016130 C1, 15.07.1994. RU 2039121 C1, 09.07.1995. RU 2125110 C1, 20.01.1999. SU 429132, 25.05.1974. SU 885331, 30.11.1981. SU 1148892 А, 07.04.1985. SU 1397536 A, 23.05.1988. WO 96/41032, 19.12.1996. WO 97/31130, 28.08.1997. WO 96/18750, 20.06.1996. Адрес для переписки: 195251, Санкт-Петербург, ул. Политехническая, 29, Государственное образовательное учреждение высшего профессионального образования "Санкт-Петербургский государственный политехнический университет", патентный отдел | (71) Заявитель(и): Государственное образовательное учреждение высшего профессионального образования "Санкт-Петербургский государственный политехнический университет" (72) Автор(ы): Паршин А.М., Кикичев Р.Н., Петкова А.П. (73) Патентообладатель(и): Государственное образовательное учреждение высшего профессионального образования "Санкт-Петербургский государственный политехнический университет" |
(54) АУСТЕНИТНАЯ КОРРОЗИОННО-СТОЙКАЯ СТАЛЬ
(57) Реферат:
Изобретение относится к металлургии аустенитных коррозионно-стойких высокоплотных свариваемых сталей. Сталь используется как конструкционный материал для атомных энергетических установок, а также в судостроении, энергофизическом аппаратостроении, в вакуумной технике. Сталь содержит компоненты, мас. %: углерод 0,005-0,015; кремний 0,1-0,3; марганец 1,3-1,8; сера 0,005-0,010; фосфор 0,005-0,015; хром 17-18; никель 13,5-14,5; титан 0,005-0,03; ниобий 0,1-0,3; азот 0,005-0,015; кислород 0,001-0,005; иттрий 0,04-0,09; цирконий 0,1-0,3; вольфрам 1,3-1,6; железо - остальное. Сталь обладает улучшенной свариваемостью, повышенной газоплотностью, высокой чистотой по вредным примесям и неметаллическим включениям, сопротивляемостью межкристаллитной коррозии в широком интервале температур и коррозионному растрескиванию в хлорсодержащих средах. 5 табл.
Изобретение относится к области металлургии аустенитных коррозионно-стойких высокоплотных свариваемых сталей, являющихся наиболее перспективными твердорастворно-упрочняемыми конструкционными материалами для атомных энергетических установок. Предложенная сталь также может найти применение в судостроении, энергофизическом аппаратостроении, в вакуумной технике.
Наиболее широкое применение в отечественных атомных энергетических установках на тепловых нейтронах нашли аустенитные хромоникелевые стали типа 18-8, стабилизированные титаном (стали марок 08Х18Н9Т, 08Х18Н10Т, 12Х18Н12Т) [1] . В зарубежной практике наряду со сталями упомянутых композиций (сталь марки 321(06Х18Н10Т) в основном применяются хромоникелевые материалы, стабилизированные ниобием (стали марок 347(10Х18Н11Б), 348(10Х18Н10Б) по стандарту AISI). Вышеупомянутые стабилизированные титаном или ниобием аустенитные хромоникелевые материалы имеют высокое сопротивление общей коррозии, при оптимальном легировании элементами-стабилизаторами не проявляют склонности к межкристаллитной коррозии, относительно устойчивы против язвообразования, щелевой коррозии и коррозионного растрескивания, достаточно технологичны, удовлетворительно деформируются при высоких температурах (ковка, штамповка, прошивка и т. д. ), также могут подвергаться холодной гибке, развальцовке, правке и т. д., хорошо свариваются [2]. В аустенитных сталях, стабилизированных ниобием, практически не наблюдается пористость, характерная для аустенитных материалов с титаном ("титановая пористость"), однако они хуже свариваются.
Однако всем упомянутым стабилизированным титаном или ниобием аустенитным хромоникелевым сталям свойственно выкрашивание титан- и ниобийсодержащих фаз внедрения (карбидов, нитридов и карбонитридов титана и ниобия), что обусловлено как неблагоприятным расположением этих фаз (скопления, строчечность), так и относительно низкой сцепляемостью их с матрицей. Выкрашивание карбидных и карбонитридных титан- и ниобийсодержащих фаз внедрения приводит не только к снижению вязкопластических свойств аустенитных сталей при относительно пластичной матрице, но и к потере герметичности конструкций, особенно тонкостенных, и отравлению их содержимого выкрошившимися частицами [3].
Применение аустенитных хромоникелевых материалов, не стабилизированных титаном (или ниобием), позволяет предотвратить выкрашивание карбидных и карбонитридных фаз [3]. Однако нестабилизированные стали, применяемые в зарубежной практике (стали марок 304(07Х18Н9), 3042(03Х18Н10) по стандарту AISI), склонны к межкристаллитной коррозии вследствие образования хромистых карбидов Сr23С6 по границам зерен. Такие материалы могут использоваться только при сравнительно невысоких температурах без применения сварки [2].
За прототип выбрана нестабилизированная аустенитная сталь марки 304L по стандарту AISI (30304 L по стандарту SAE, S30403 по стандарту UNS), содержащая, мас.%:
Углерод -

Кремний -

Марганец -

Сера -

Фосфор -

Хром - 18-20
Никель - 8-12
Железо - Остальное
Кроме элементов, указанных в марочном составе, в стали-прототипе неизбежно присутствуют такие элементы внедрения, как азот и кислород, количество которых определяется способом выплавки и чистотой применяемых шихтовых материалов. В стали прототипе также присутствует некоторое небольшое количество титана, не указанное в марочном составе, о чем свидетельствует наличие в стали-прототипе карбидных и карбонитридных фаз внедрения титана (2,5 балла). Содержание азота в стали-прототипе может достигать 0,04% и более, что также способствует образованию титансодержащих фаз внедрения. Хрупкое разрушение фаз внедрения, особенно их скоплений, при тепловой и механической обработке, и их выкрашивание снижают прочностные и вязко-пластические свойства стали, приводят к потере герметичности тонкостенных конструкций.
Присутствие кислорода в стали-прототипе, обусловливающее достаточно высокое содержание оксидных включений (2,5-3 балла), слабо или практически не деформирующихся как при низких, так и при высоких температурах, снижает технологичность при горячей обработке давлением, вызывает снижение прочностных и пластических свойств и потерю герметичности тонкостенных конструкций при операциях холодной пластической деформации.
Достаточно высокое содержание серы в стали-прототипе в пределах 0,03% приводит к образованию легкоплавких и хрупких сульфидов, расположенных вдоль направления проката или ковки. Эти включения вызывают негазоплотность тонкостенных конструкций, расплавляясь при операциях термической обработки, снижают технологичность стали, вызывая образование межзеренных трещин при горячей обработке давлением, выкрашиваются при операциях холодной пластической деформации, вызывая снижение прочностных и пластических свойств и потерю герметичности тонкостенных конструкций.
Существенным недостатком стали-прототипа является ее склонность к межкристаллитной коррозии при высоких температурах, что позволяет применять ее только в изделиях, не подвергаемых сварке и работающих при температурах, не превышающих 300oС, а также проявление склонности к коррозионному растрескиванию в хлорсодержащих средах.
Задачей является обеспечение свариваемости, повышенной газоплотности, высокой чистоты по вредным примесям и неметаллическим включениям, сопротивляемости межкристаллитной коррозии в широком интервале температур и коррозионному растрескиванию в хлорсодержащих средах при достаточной технологичности.
Предлагается аустенитная коррозионно-стойкая сталь, имеющая следующий химический состав, мас.%:
Углерод - 0,005-0,015
Кремний - 0,1-0,3
Марганец - 1,3-1,8
Сера - 0,005-0,010
Фосфор - 0,005-0,015
Хром - 17-18
Никель - 13,5-14,5
Титан - 0,005-0,03
Ниобий - 0,1-0,3
Азот - 0,005-0,015
Кислород - 0,001-0,005
Иттрий - 0,04-0,09
Цирконий - 0,1-0,3
Вольфрам - 1,3-1,6
Железо - Остальное
Обеспечение весьма низкого содержания углерода (0,005-0,015%) в предлагаемой стали необходимо как для весьма значительного снижения содержания карбидов и карбонитридов титана, так и для обеспечения стойкости ее к межкристаллитной коррозии, что достигается применением особо чистых шихтовых материалов и специальных видов вакуумных переплавов (при обычном металлургическом переделе содержание углерода может быть снижено только до 0,02%). Ограничение содержания азота (0,005-0,015%) при весьма низком содержании углерода способствует значительному снижению количества фаз внедрения в предлагаемой стали (табл.1). (Таблицы 1-5 см. в конце описания).
Ограничение содержания кислорода в предлагаемой стали (0,001-0,005%) позволяет значительно снизить количество оксидов (0,5-1 балл), способствует улучшению технологичности стали при горячей обработке давлением, повышению газоплотности тонкостенных конструкций при операциях холодной пластической деформации.
Ограничение содержания фосфора (0,005-0,015%) и серы (0,005-0,01%) повышает стойкость разработанной стали против образования горячих трещин.
Резкое снижение содержания углерода и азота в предлагаемой стали, являющихся сильными аустенитообразующими элементами, а также введение вольфрама (феррито-образующего элемента) будут способствовать увеличению количества

Низкое содержание титана (0,005-0,03%), т.е. присутствие его следов в разработанной стали, при очень малом количестве углерода и азота позволяет заметно снизить содержание нитридов и карбонитридов титана (0,5-1 балл) (табл. 2).
Введение ниобия в количестве 0,1-0,3% необходимо как для повышения стойкости разработанной стали против межкристаллитной коррозии, так и для обеспечения изотропности механических свойств.
Введение в предлагаемую сталь вольфрама в количестве 1,3-1,6% обеспечивает повышение кратковременных прочностных характеристик (


Микродобавки циркония (0,1-0,3%) способствуют более однородному распределению неметаллических включений в объеме зерна, повышению деформационной способности материала.
Введение иттрия (0,04-0,09%) значительно повышает сопротивляемость разработанной стали коррозионному растрескиванию (табл. 5). Так, при испытании в водном растворе 25% NaCl+5% К2Сr2O7 (tисп=200oC, Р=1,6 МПа,


Вакуумно-индукционная выплавка предлагаемой стали и последующий вакуумно-дуговой переплав, а также горячая ковка заготовок осуществлялись на Челябинском металлургическом комбинате. Химсостав предлагаемой стали марки 01Х18Н14В2ЧЦВИ+ВД и стали-прототипа приводится в таблице 1. Для предлагаемой и известной сталей оценено содержание неметаллических включений (табл. 2), исследована равномерность их распределения по сечению поковки (табл. 3), а также оценена склонность к межкристаллитной коррозии (табл. 4) и коррозионному растрескиванию (табл. 5).
Снижение содержания вредных примесей, неметаллических включений и фаз внедрения (табл. 1, 2) и достаточно равномерное их распределение в объеме зерен (отсутствие скоплений, направленного распределения, строчечности) (табл. 3), что достигалось применением вакуумно-индукционной выплавки и особо чистых шихтовых материалов, обеспечивает повышение газоплотности тонкостенных конструкций из предлагаемой стали.
Предлагаемая сталь обладает высокой сопротивляемостью межкристаллитной коррозии при испытании по методу AM ГОСТ 6032-89. После провоцирующего нагрева при температуре 650oС (выдержка в течение 1 ч), в отличие от стали-прототипа, она не обнаружила склонности к межкристаллитной коррозии (табл. 5). Это значит, что изделия из предлагаемой марки стали могут подвергаться сварке. Для оценки сопротивляемости предлагаемой стали межкристаллитной коррозии в широком интервале температур после длительного старения выдержка при температурах провоцирующего нагрева 500, 550, 600 и 650oС была увеличена до 1000 и 2500 ч. Во всех случаях не обнаружено склонности к межкристаллитной коррозии при загибе образцов. При металлографическом анализе коррозионное разъедание также не обнаружено. Таким образом, предлагаемая сталь не склонна к межкристаллитной коррозии при высоких температурах даже после длительного старения и кипячения в высокоагрессивной среде (метод AM ГОСТ 6032-89).
Предлагаемая сталь обладает повышенной сопротивляемостью коррозионному растрескиванию в хлорсодержащих средах по сравнению со сталью-прототипом (табл. 5). Так, при испытании в водном растворе 25% NaCl+5% К2Сr2O7 (tисп= 200oС, Р=1,6 МПа,


Таким образом, предлагаемая сталь обладает улучшенными характеристиками: свариваемостью, повышенной газоплотностью, высокой чистотой по вредным примесям и неметаллическим включениям, сопротивляемостью межкристаллитной коррозии в широком интевале температур и коррозионному растрескиванию в хлорсодержащих средах при досточной технологичности.
Источники информации
1. Баландин Ю. Ф., Горынин И.В., Звездин Ю.И., Марков В.Г. Конструкционные материалы АЭС. М.: Энергоатомиздат, 1984, 280 с.
2. Паршин А.М. Структура, прочность и радиационная повреждаемость коррозионно-стойких сталей и сплавов. Челябинск: Металлургия, 1988, 656 с.
3. Пути создания особо чистой аустенитной коррозионно-стойкой свариваемой стали /Паршин А.М., Бардин В.А., Колосов И.Е. и др.//ВАНТ, сер. Термоядерный синтез, 1993, вып.1-2, с. 21-28.
Формула изобретения
Аустенитная коррозионно-стойкая сталь, содержащая углерод, кремний, марганец, серу, фосфор, хром, никель, железо, отличающаяся тем, что она дополнительно содержит титан, ниобий, азот, кислород, иттрий, цирконий, вольфрам при следующем содержании компонентов, мас.%:
Углерод 0,005-0,015
Кремний 0,1-0,3
Марганец 1,3-1,8
Сера 0,005-0,010
Фосфор 0,005-0,015
Хром 17-18
Никель 13,5-14,5
Титан 0,005-0,03
Ниобий 0,1-0,3
Азот 0,005-0,015
Кислород 0,001-0,005
Иттрий 0,04-0,09
Цирконий 0,1-0,3
Вольфрам 1,3-1,6
Железо Остальное
РИСУНКИ
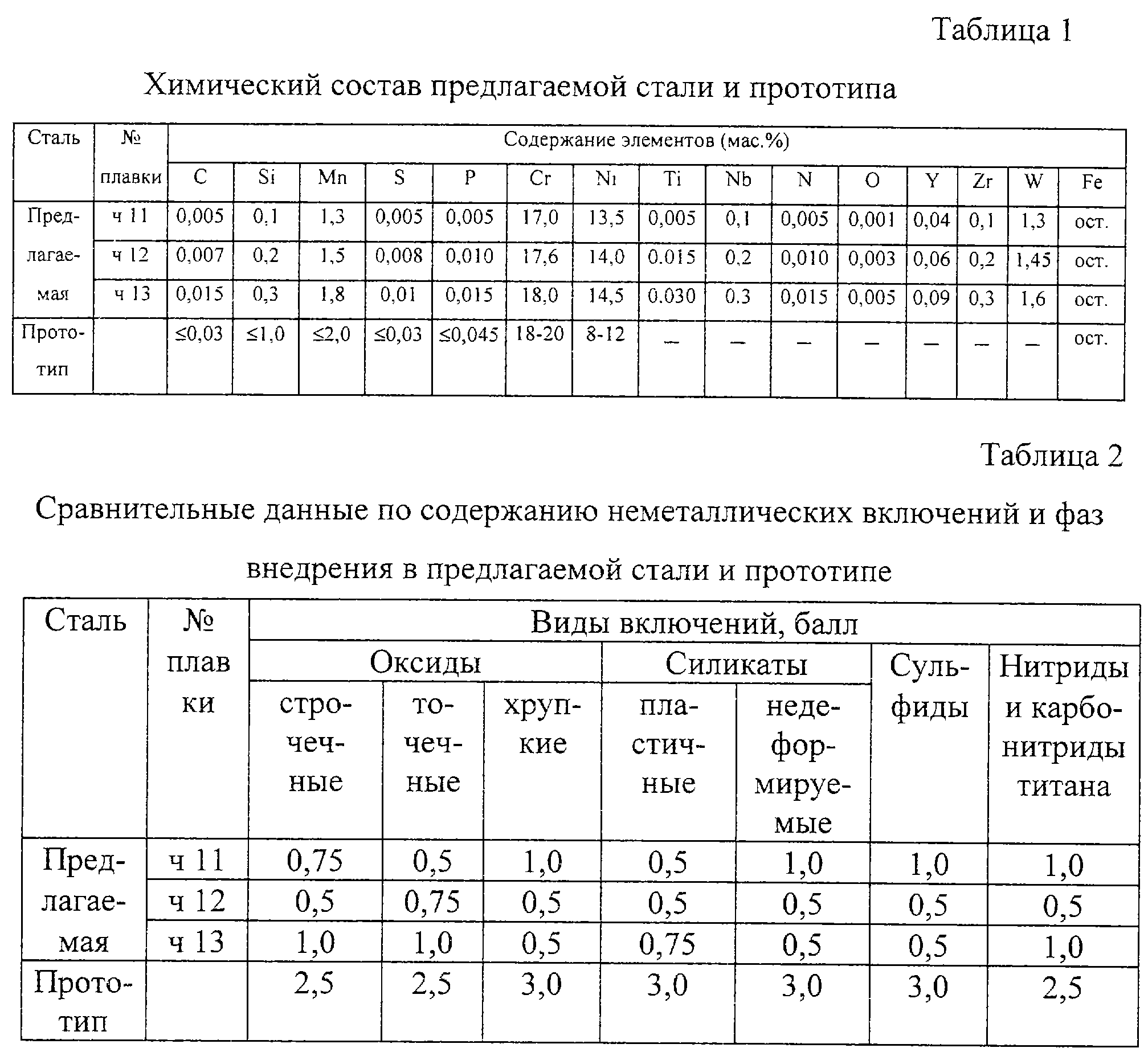
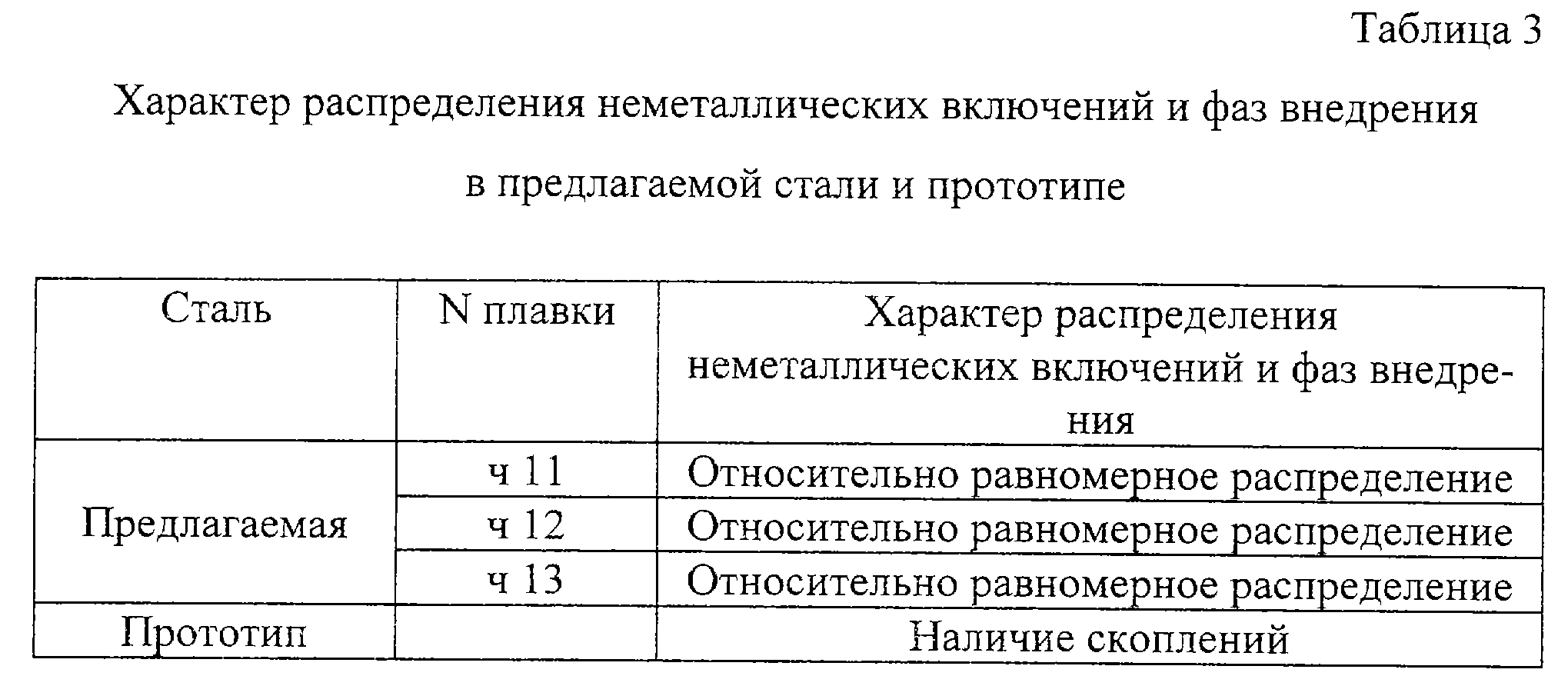
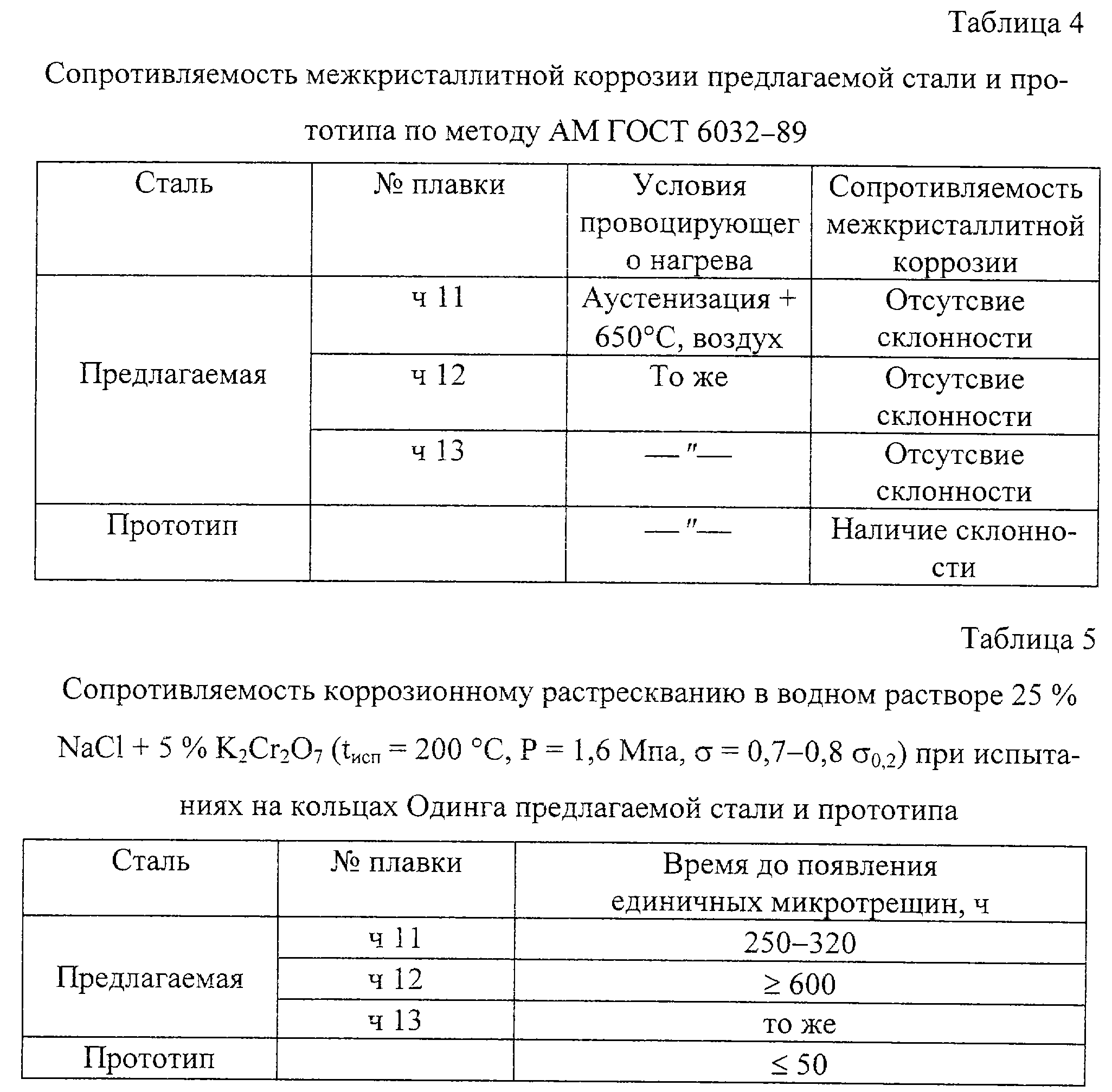