Тема 1 теоретические основы планирования
Вид материала | Курс лекций |
- 1. теоретические основы стратегического планирования развития предприятия, 38.46kb.
- 1 Особенности стратегического планирования на предприятиях пищевой промышленности, 1908.71kb.
- Программа курса «экономическая теория», 2990.51kb.
- 3 глава теоретические основы макроэкономического планирования и прогнозирования, 1661.1kb.
- Бизнес план организации производства из пластиковых материалов (ооо 'ххх') оглавление, 1023.76kb.
- Методические указания по выполнению курсового проекта по дисциплине «Теоретические, 304.06kb.
- И в срок Содержание введение 3 теоретические и методологические аспекты бизнес планирования, 81.32kb.
- Бизнес-план сущность и задачи 7 2 Структура бизнес-плана 9 1 Обзорный отдел (резюме), 859.42kb.
- Нп «сибирская ассоциация консультантов», 86.89kb.
- Методические указания и задания для выполнения домашних контрольных работ, 953.98kb.
1. Содержание плана материально-технического обеспечения
нормальная работа предприятия зависит от обеспеченности производственного процесса необходимыми ресурсами требуемого качества и в заданном количестве.
Эта задача решается в ходе материально-технического (м-т) обеспечения предприятия.
Основным содержанием м-т снабжения являются:
- Определение оптимальной потребности предприятия в материальных ресурсах (на основе прошлого опыта, тех. карт);
- установление сроков и источников покрытия потребности в материалах;
- определение нормативных запасов материала;
- снижение затрат на приобретение, хранение и доставку материалов;
- обеспечение полного и экономического расходования материалов;
- учет, контроль и анализ выполнения планов материально – технического снабжения.
План материально-технического снабжения разрабатывается в натуральном и стоимостном выражении и включает следующие разделы:
- Расчет потребности в материальных ресурсах (сырье, топливо, материалы, энергия, комплектующие);
- баланс материально-технического обеспечения.
Определение потребности в материальных ресурсах производится на основе: программы выпуска, коммерческой деятельности предприятия, ремонтно-эксплутационных и хозяйственных нужд, прогрессивных норм.
Материальный баланс определяет общую потребность предприятия в ресурсах и устанавливает источники и сроки покрытия. При этом должна соблюдаться следующая формула:
Мн+Мп = Мр+Мк,
где Мн – остатки материала на начало планового периода;
Мп – потребность в материалах;
Мр – расход материала в плановом периоде;
Мк – запас материала на конец планового периода.
Основными плановыми документами МТС являюся:
- Годовой план снабжения (или материальный баланс);
- Квартальный план. Составляется в специализированном ассортименте с календарным распределением получения материальных ресурсов;
- Месячный план или лимит отпуска материалов подразделениям предприятия.
2. Планирование потребности в материальных ресурсах
Планирование потребности в материалах может осуществляться следующими методами:
- Метод прямого счета.
М =
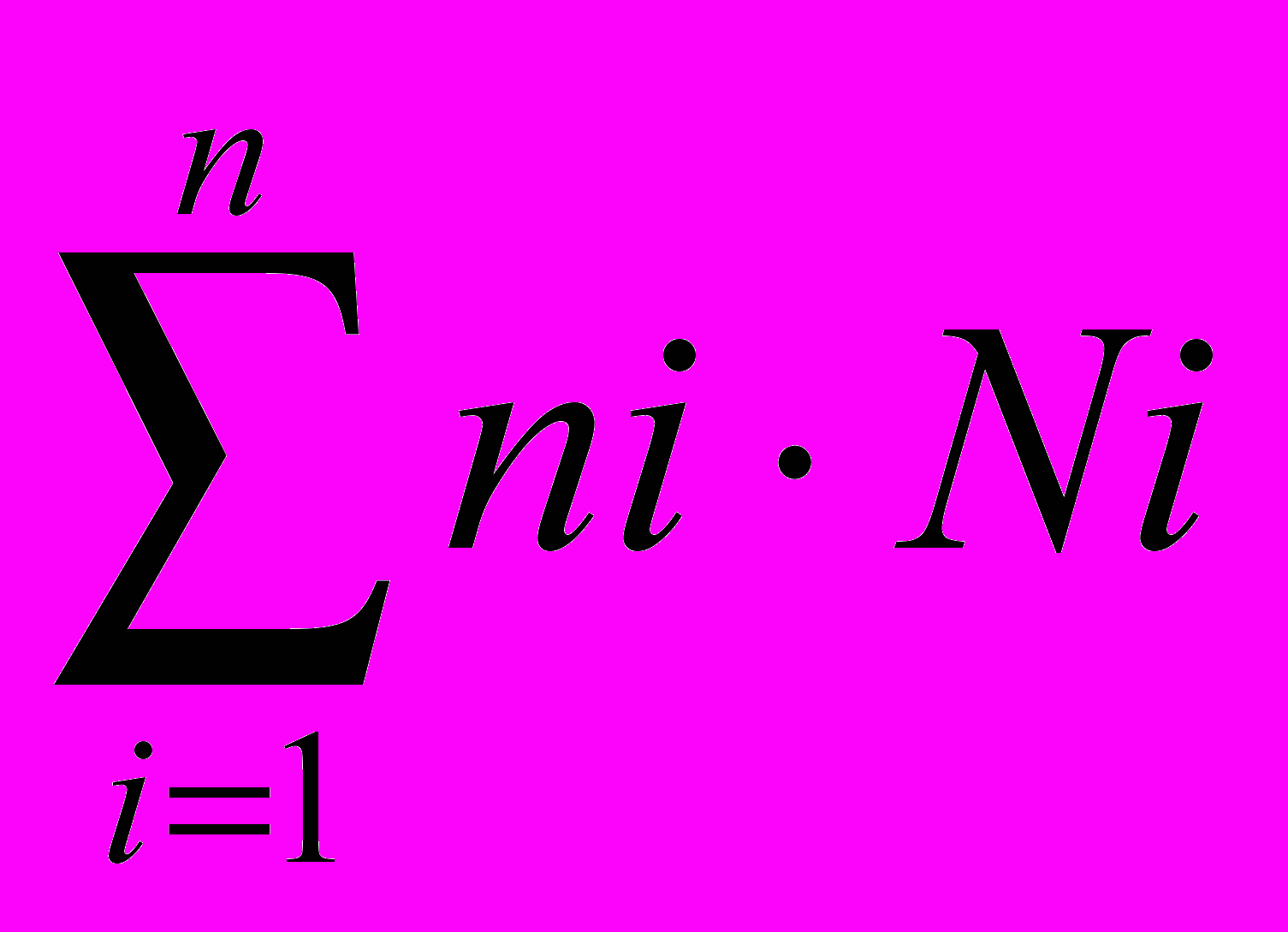
ni – норма расхода на одно изделие,
N – программа выпуска.
- Расчет по аналогии. Применяется при отсутствии нормативной базы или при большой номенклатуре.
М = ∑ni·Ni·K,
ni – расход материала на аналогичное базовое изделие;
K – коэффициент, учитывающий потребление материала для нового изделия.
- Расчет по типовому представителю. Применяется когда разнообразна номенклатура.
М = nт + Nг,
nт – норма расхода на типовой представитель;
Nг – программа выпуска всех изделий данной группы.
- Метод динамических коэффициентов. Применяется при отсутствии данных по норме и по объему выпускаемой продукции. (в единичном производстве).
М = Рф Iпп·Iн,
Рф – расход материалов в базовом периоде;
Iпп – индекс изменения производственной программы;
Iн – индекс изменения норм расхода.
Потребность во вспомогательных материалах определяется следующими методами:
- Расчет на основе норм расхода на изделие (станкочас, кв.м. площади,…)
600 с/ч; n = 20 кг. М = 600·20 = 12000 кг.
- Расчет на основе расчетно-статистических данных расхода вспомогательных материалов с учетом изменения выполняемого объема работ (метлы, тряпки, к-е не зависят от объема производства).
- Планирование запаса материалов.
Определение производственных запасов осуществляется на основе норм запасов.
Норма запаса – это величина запаса материальных ресурсов, обеспечивающая бесперебойную работу предприятия.
Объем производственных запасов измеряется в днях обеспеченности, в натуральном и стоимостном выражении.
Например:
- Закупка – 2 дня
- Транспорт – 1 день
- Складирование – 0,5 дней
- Подготовка к производству – 0,5 дней
- Участие в производственном процессе – 6 дней
ИТОГО: 10 дней.
В день 20 кг.
Нз = 20(кг)*10(дн) = 200 (кг) в натуральном выражении;
Нз = 200 (кг) * 15 (руб) = 3000 (руб) в стоимостном выражении.
В зависимости от условий образования и потребления ресурсов различают: текущий, подготовительный и страховой запас.
Текущий запас обеспечивает бесперебойную работу предприятия между двумя поставками материала. Величина текущего запаса изменяется от максимального до минимального значения. Зависит от величины ежедневного потребления, степени равномерности потребления и времени между двумя очередными поставками. Максимальная величина текущего запаса определяется по формуле:
Мт max = d · T,
d – среднедневной расход материала;
Т – период между двумя поставками;
Подготовительный запас обеспечивает возможность подготовки материала к использованию в производстве (сушка материала, сортировка, приемка и разгрузка и тд.).
Мподг = d · ∑t,
t- сумма времени на операцию технологического процесса.
Страховой запас обеспечивает непрерывность производственного процесса в случае задержки поступления очередной партии материалов.
Мстр = d·Tср,
Тср – время срочного выполнения заказа включая время на оформление документов, погрузку, разгрузку, транспортировку.
Величина страхового и подготовительного запаса остаются неизменными.
Различают следующие уровни производственных запасов:
- Максимальный производственный запас. Используется для расчета складских помещений.
Тпр max =Мт max + Мподг + Мстр
- Средний уровень производственного запаса. Используется для расчета потребности в оборотных средствах.
Мпр ср = Мт max/2 + Мподг + Мстр
- Минимальный запас.
Мпр min = Мподг + Мстр
у




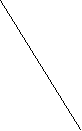

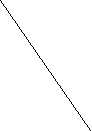




размер заказа


Мпр max Mт max t время, в течении которого необходимо
Восстановить запас



t
Основной задачей планирования и регулирования запасов является их оптимизация.
Критерием оптимальности являются минимальные расходы, связанные с хранением и образованием запаса.
При планирован запасов необходимо определить оптимальный размер партии и количество партий на плановый период. Оптимальный размер партии определяется:
Р =
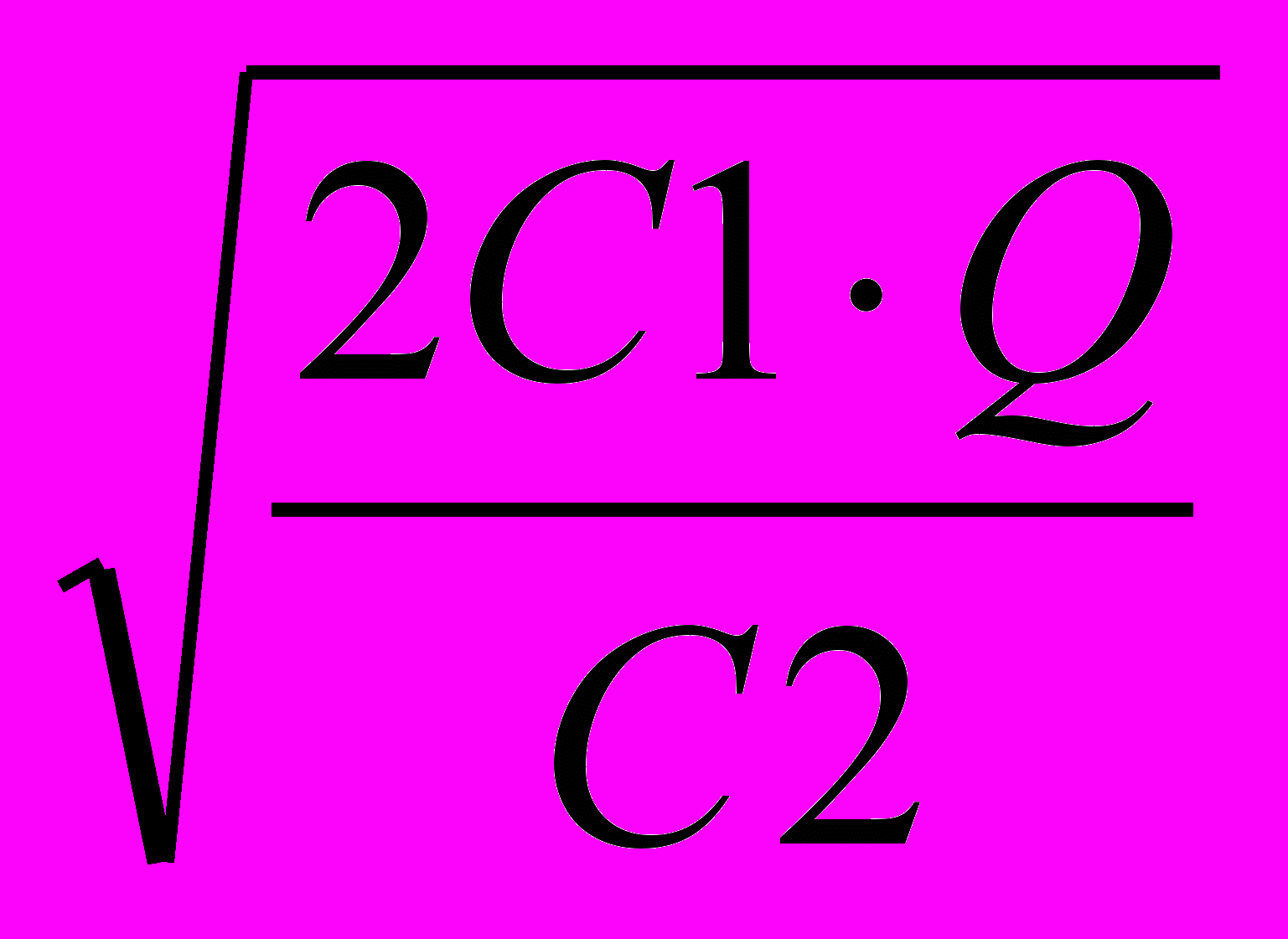
С1 – постоянные транспортные расходы на одну партию;
Q – годовой объем закупаемых материалов в натуральном выражении;
С2 – условно-переменные затраты на хранение единицы продукции (10-25 % от себестоимости закупаемых материалов).
Количество закупаемых партий в плановом периоде:
n =
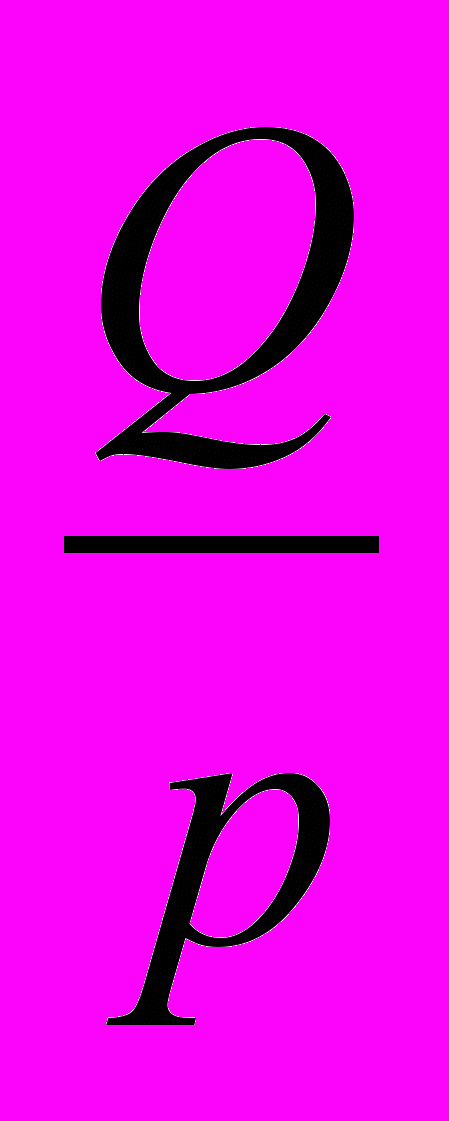
Тема: 6 Оперативно-производственное планирование.
- Содержание и задачи оперативно-производственного планирования.
ОПП предполагает детальную разработку годового плана экономического и социального развития предприятия и заключается в распределении плановых заданий по исполнителям и коротким промежуткам времени.
Основными задачами ОПП являются:
- обеспечение ритмичной работы предприятия и равномерного выпуска продукции;
Q

Qфакт 12 12 10 10 11 55 ед. Кр = Qфакт/Qплан.
- Наиболее полное и эффективное использование ресурсов;
- Максимальное сокращение длительности производственного цикла:
Коэффициент прерывности производственного цикла Кп =
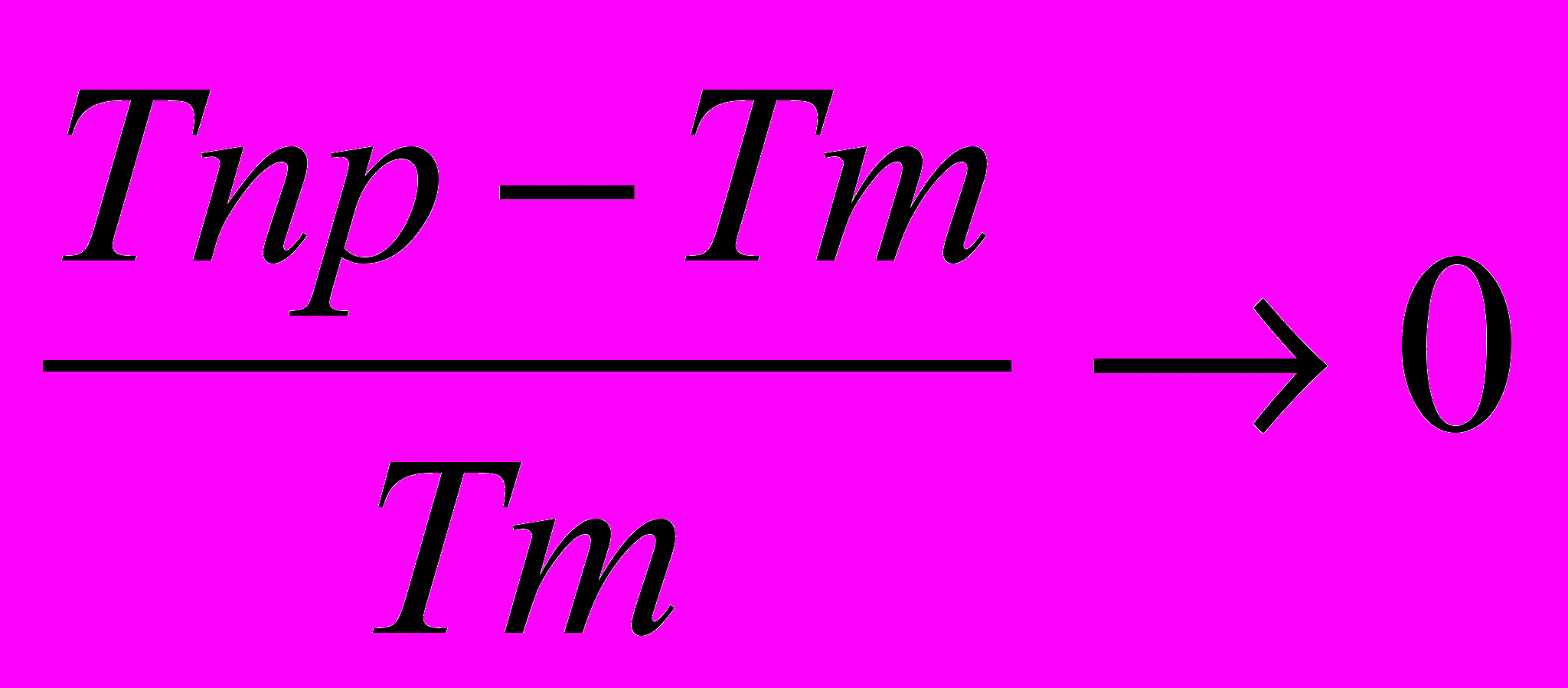
Тпр – длительность производственного цикла
Тт – длительность технологического цикла
Основным содержанием ОПП является:
- установление места и времени изготовления продукции;
- расчет календарно-плановых нормативов;
- разработка календарных графиков изготовления и выпуска продукции;
- учет и регулирование хода производственного процесса.
В зависимости от содержания различают следующие виды оперативного планирования:
- Календарное планирование включает распределение годовых плановых заданий по подразделениям предприятия и срокам исполнения с доведением плановых заданий до конкретных исполнителей;
- Текущее планирование предполагает оперативный контроль и регулирование производственного процесса, учет выпуска продукции и расходования ресурсов.
2. Система оперативно-производственного планирования
Под системой оперативного планирования производства понимается методика и технология плановой работы, которые определяются планово-учетной единицей, составом и точностью календарно-плановых нормативов, порядком учета и движения продукции и оформления учетной документации. В зависимости от типа производства и характера продукции различают следующие системы:
- Позаказная система. Применяется в единичном и мелкосерийном производстве. Объектом планирования является заказ, изделие или комплект деталей. Данная система предполагает определение запуска изделий в производство при установленном сроке выпуска продукции (объект планирования – заказ);
- Комплектная система. Применяется в серийном производстве. Планово-учетной единицей является комплект деталей объединенных по определенным признакам. Различают:
Комплектно-сборочную систему объектом планирования является комплект деталей, входящих в одну сборочную единицу; и Комплектно-узловую систему, включающую детали с одинаковыми календарно-плановыми нормативами;
- Подетальная система. Её применение требует разработки сложных календарно-оперативных планов, содержащих показатели объема выпуска и маршрут движения деталей каждого наименования по всем производственным стадиям и технологическим операциям. Данную систему целесообразно применять при ограниченной и устойчивой номенклатуре выпускаемой продукции, что имеет место в крупносерийном и массовом производстве. Объектом планирования является деталь каждого наименования.
3. Календарно-плановые нормативы.
Состав, содержание и методы календарно-плановых нормативов определяются типом производства и принятой планово-учетной единицей.
Существуют следующие календарно-плановые нормативы:
- Серия изделий – это количество одновременно запускаемых в производство изделий.
- Партия деталей – это количество одинаков запускаемых в производство с одной наладкой оборудования.
Размер оптимальной партии запуска-выпуска деталей определяется соотношением издержек предприятия на хранение заготовок и наладку технологического оборудования. Нормальная величина партии рассчитывается по формуле:
nн =
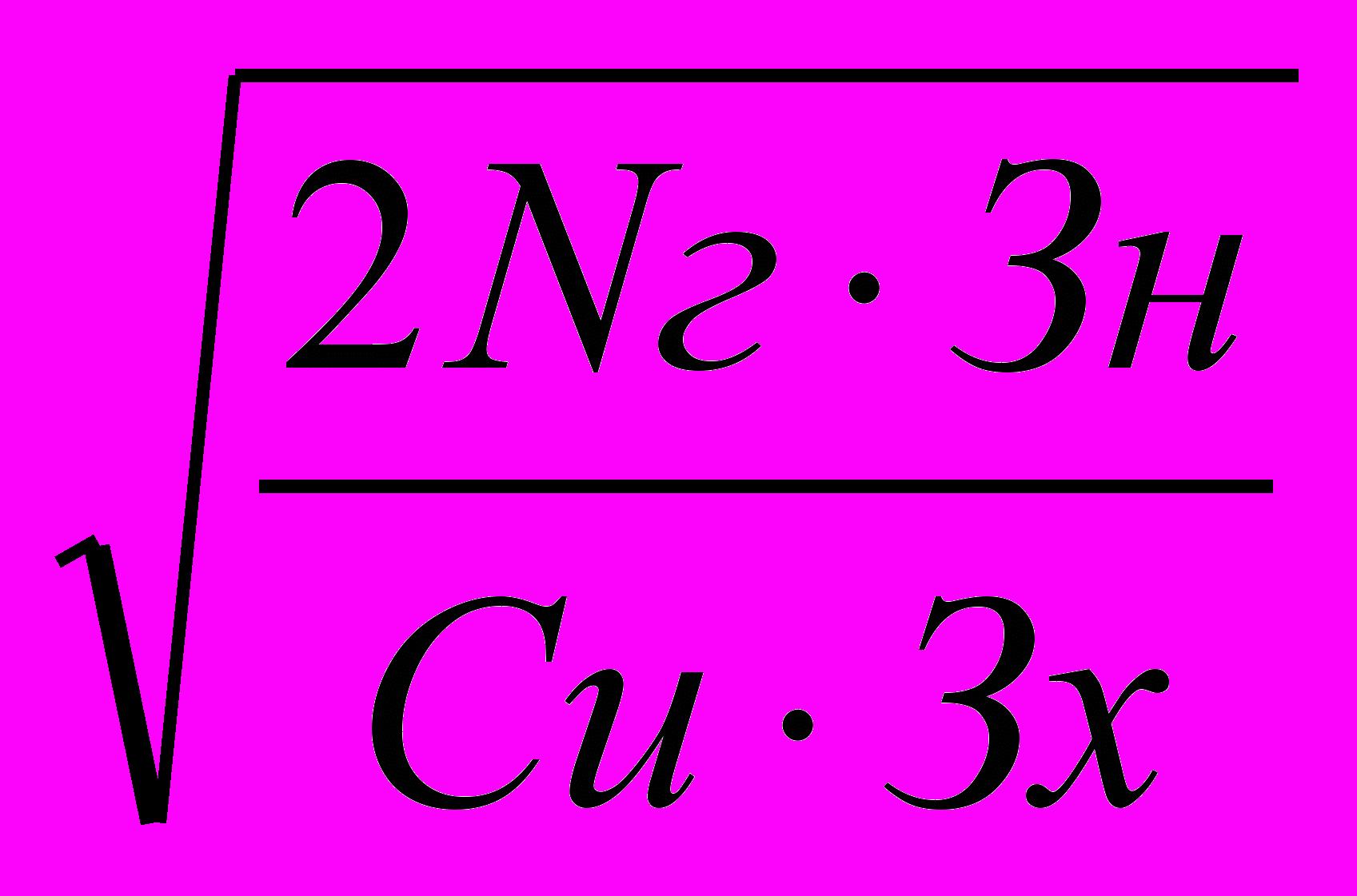
Nг – годовой объем выпуска продукции, шт;
Зн – затраты на наладку технологического оборудования;
Си – себестоимость одной детали, руб/шт.;
Зх – затраты на хранение деталей в процентах от стоимости запасов (авные примерно 10 -25%)
Упращенный метод расчета минимальной партии деталей:
nmin =
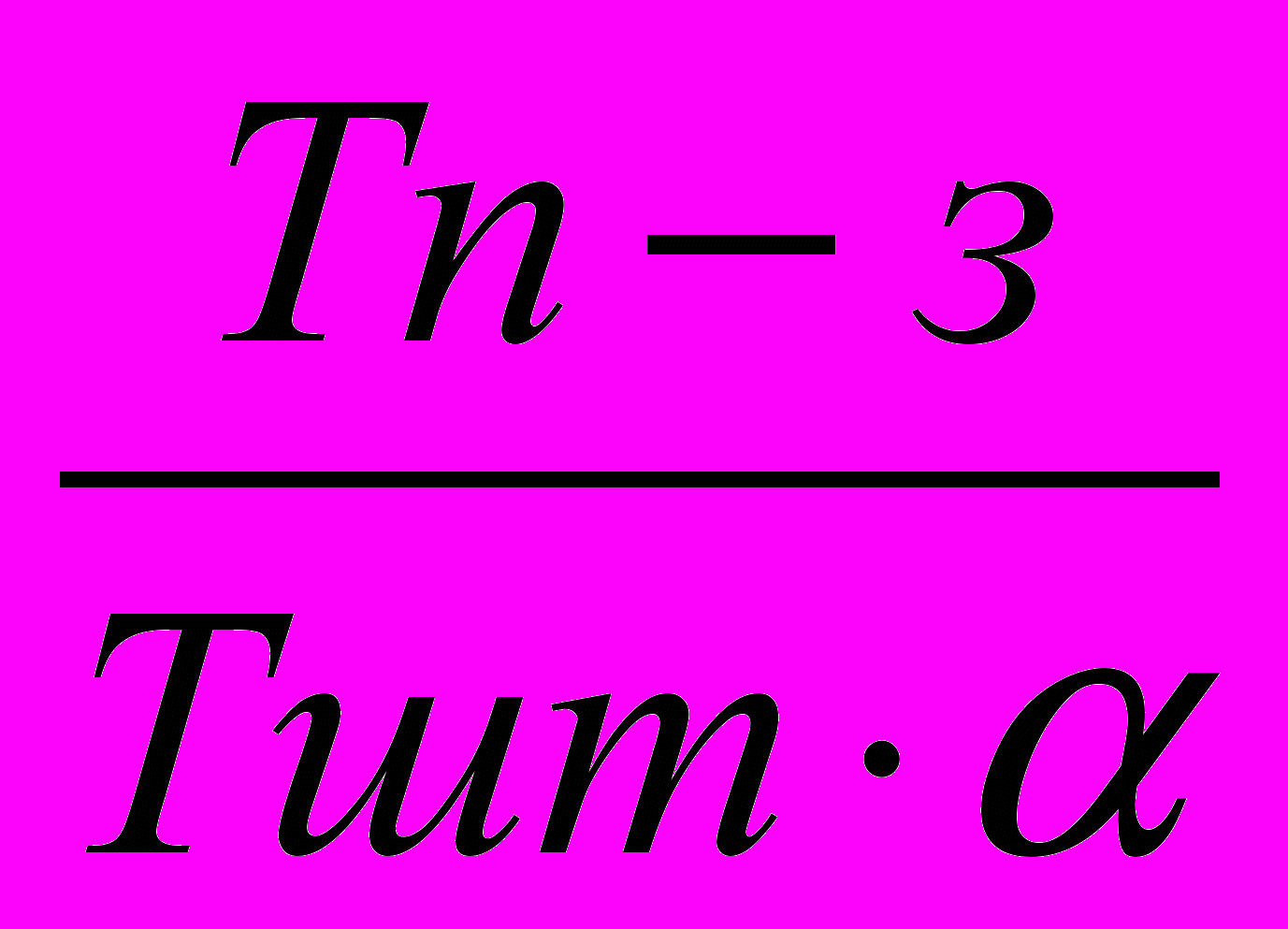
Тп-з – подготовительно-заключительное время;
Тшт- штучное время на одну деталь;
α – коэффициент допустимых потерь времени на переналадку оборудования (от 0,05 до 0,1).
- Длительность производственного цикла – это время от запуска исходного сырья в производство до выхода готовой продукции;
Производственный цикл включает рабочий период выполнения заготовительных, обрабатывающих и сборочных процессов, а также контрольных, транспортных и складских операций. Общая продолжительность производственного цикла при последовательном способе передачи обрабатываемой партии деталей определяется по формуле:
Тпосл =
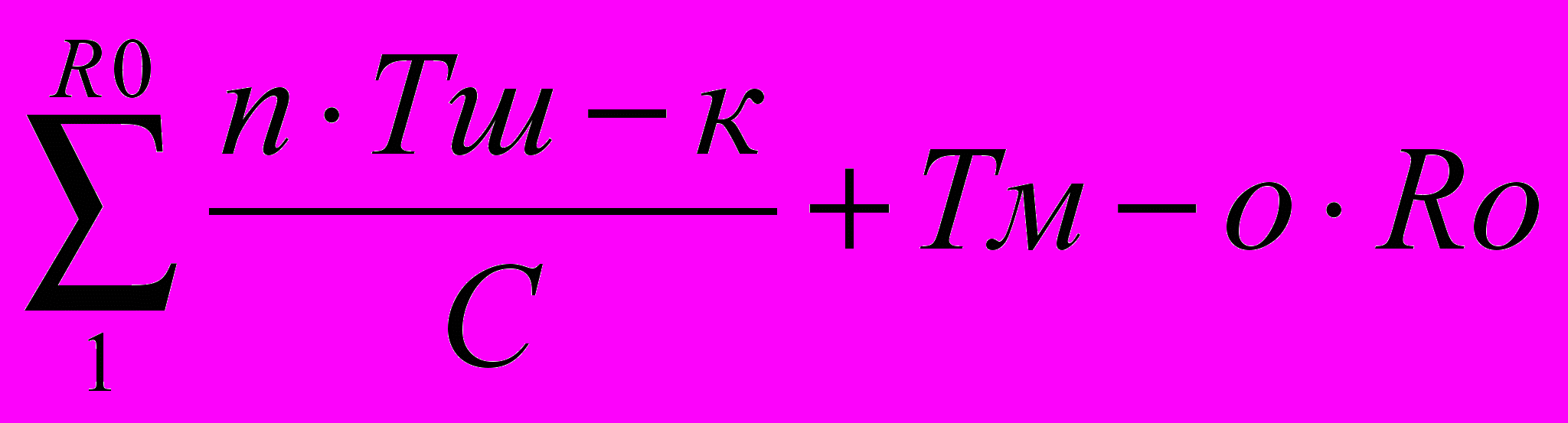
Тпосл- длительность последовательного цикла (мин);
R0 – число операций;
n – размер партии деталей;
Тш-к – штучно-калькуляционное время;
С- число станков на операции;
Тм-о – время межоперационных перерывов.
- Норматив опережения – период времени в днях, на который должны быть раньше закончены все предыдущие операции по отношению ко времени выполнения последующих и завершающей стадией производственного процесса.
Расчет циклов ведется в обратном направлении от заключительной до начальной стадии с прибавлением резервного или страхового времени между отдельными стадиями.
Пример: заказ выполняется на трех стадиях производства: заготовительной, механической и сборочной, продолжительность которых равна 3; 6 и 5 дней, резервное время между ними составляет 1 день. Построить цикловой график выполнения заказа и рассчитать нормативы опережения.










Товм



Товз


Общий производственный цикл:
Тпц = Тсб+Тр+Тмех+Тр+ Тзаг = 5+1+6+1+3 =16;
Норматив опережения выпуска с механической стадии:
Товм = Тсб + Тр = 5+1=6;
Норматив опережения запуска на механическую обработку:
Тозм = Тсб+Тр+Тмех = 5+1+6 = 12;
Норматив опережения выпуска с заготовительной стадии:
Товз= Тсб+Тр+Тмех+Тр = 5+1+6+1 = 13;
Норматив опережения запуска деталей на заготовительную стадию (равен производственному циклу):
Тпц = Тозз =16.
- Производственный задел – педполагает поддержание на требуемом расчетном уровне запаса заготовок, полуфабрикатов и комплектующих, предназначенных для дальнейшей обработки и сборки на каждой стадии производства. Размер производственных заделов представляет собой соответствующий запас заготовок.. По назначению заделы бывают технологические, транспортные, страховые, межоперационные или межцикловые.
Общий задел принимается равным сумме всех слагаемых запасов заготовок и деталей.
- Оперативное планирование в различных типах производства.
Основными объектами оперативного учета и контроля на предприятии являются многие планово-экономические показатели: от часовых заданий до годовых объемов производства и продажи продукции.
- Единичное производство: в единичном производстве ОПП заключается в обеспечении выполнения заказов в соответствии с установленными сроками при равномерной загрузке производства и минимальном производственном цикле выполнения заказа.. ОПП тесно связано с технической подготовкой производства. Для единичного производства используются следующие календарно-плановые нормативы:
- расчет длительности производственного цикла планового заказа и построение цикловых графиков его изготовления;
- определение календарных опережений;
- составление сводного графика выполнения заказа;
- расчет загрузки производственного оборудования, площадей и корректировка графика с целью выравнивания загрузки по плановым периодам.
- расчет длительности производственного цикла планового заказа и построение цикловых графиков его изготовления;
- Серийное производство. В серийном производстве объектами оперативного планирования выступают сроки запуска и выпуска партии деталей, соблюдение нормативов опережений по стадиям обработки и т.д. серийное производство включает следующие календарно-плановые нормативы:
- определение партии изделий;
- определение партии деталей и периодичность их изготовления;
- определение длительности производственного цикла и календарных опережений;
- построение календарных графиков;
- расчет заделов.
- Массовое производство. в массовом производстве в качестве объектов оперативного планирования выступают показатели такта и ритма работы поточных линий , нормативы межоперационных заделов, а также суточные и часовые графики поставки готовой продукции на рынок. В условиях массового производства ОПП включает следующие календарно-плановые нормативы:
- такт и ритм поточных линий;
- расчет цикловых заделов;
- построение графиков работы участков и линий.
Тема 7: Организация производственного процесса во времени.
- Производственный цикл и его структура.
- Виды движения предметов труда.
- Пути сокращения длительности производственного цикла.
- Производственный цикл и его структура.
Производственный цикл – это календарный период времени в течении которого сырье и основные материалы превращаются в готовую продукцию.
П


В





(20-40%) (60-80%)
Технологические Нетехнологические Межоперационные Межцеховые Межсменные
Операции операции перерывы перерывы перерывы
- штучное время - контрольные -перерывы -перерывы - нерабочие
операции партионности комплектации дни
-подготовительно- -транспортные - обед.пер-
заключительное операции (тран- -перерывы ерывы
время (уборка) спортировка ме- ожидания - перерывы
жду цехами) м/у сменами
-время
естественных
процессов (сушка,
охлаждение)
Время естественных технических процессов – это время, в течение которого предмет труда изменяет свои характеристики без воздействия людей или техники (сушка, охлаждение и т.д.). Принимается по минимальному времени их осуществления в соответствии с технологией или данными наблюдений.
Подготовительно-заключительное время – затрачивается на подготовку рабочего места к выполнению производственного задания. Рассчитывается по нормам (в единичном производстве просчитать очень сложно).
Контрольные и транспортные операции. Время их осуществления может перекрываться временем межоперационного ожидания или приниматься по опытным данным.
Межоперационные перерывы. Обусловлены временем партионности и зависят от характера обработки партии деталей на операциях.
Перерывы партионности включают время которое деталь, поступающая на рабочее место в составе партии, пролеживает до и после обработки пока не будет обработана вся партия деталей.
Перерывы ожидания возникают при несогласованности длительности смежных операций технологического процесса.
Перерывы комплектации возникают в случае когда детали и узлы пролеживают в ожидании комплектации.
Межсменные перерывы определяются режимом работы предприятия и его подразделений и включают праздничные, выходные дни, обеденные перерывы и перерывы между сменами.
Структура и продолжительность производственного цикла зависят от типа производства, технических и организационных факторов.
(Длит. пр-ого цикла) Тц = ∑tо + ∑tпз + ∑tмо + ∑tе +∑tк +∑tт +∑tмц
tо – обработка; tпз – подг.-закл. время; tмо – межоперац. перерывы; tе – естественные процессы; tк – контрольные операции; tт – транспортные операции; tмц –межцеховые перерывы.
- Виды движения предметов труда.
Различают три вида движения предмета труда:
- Последовательное движение предмета труда (единичное и мелкосерийное производство).
Характеризуется тем, что при движении партии деталей каждая последующая операция технологического процесса начинается только после выполнения предыдущей операции над всей обрабатываемой партией.
Продолжительность технологического цикла обработки всей партии деталей можно рассчитать по формуле: m
Тпос = t1*n + t2*n + ….+tm*n = n ∑ti
i=1
t1,t2 …tm – норм времени на операции;
n-число деталей в партии;
m – количество операций.
ПР: n = 3 m ti, мин.
m = 3 1 2
2 1,5
3 3
Тпос = 3*(2+1,5+3)=19,5 мин.
Если на одной или нескольких операциях обработка деталей проводится одновременно на нескольких рабочих местах, то длительность технологического цикла определяется по формуле:
Тпос = n
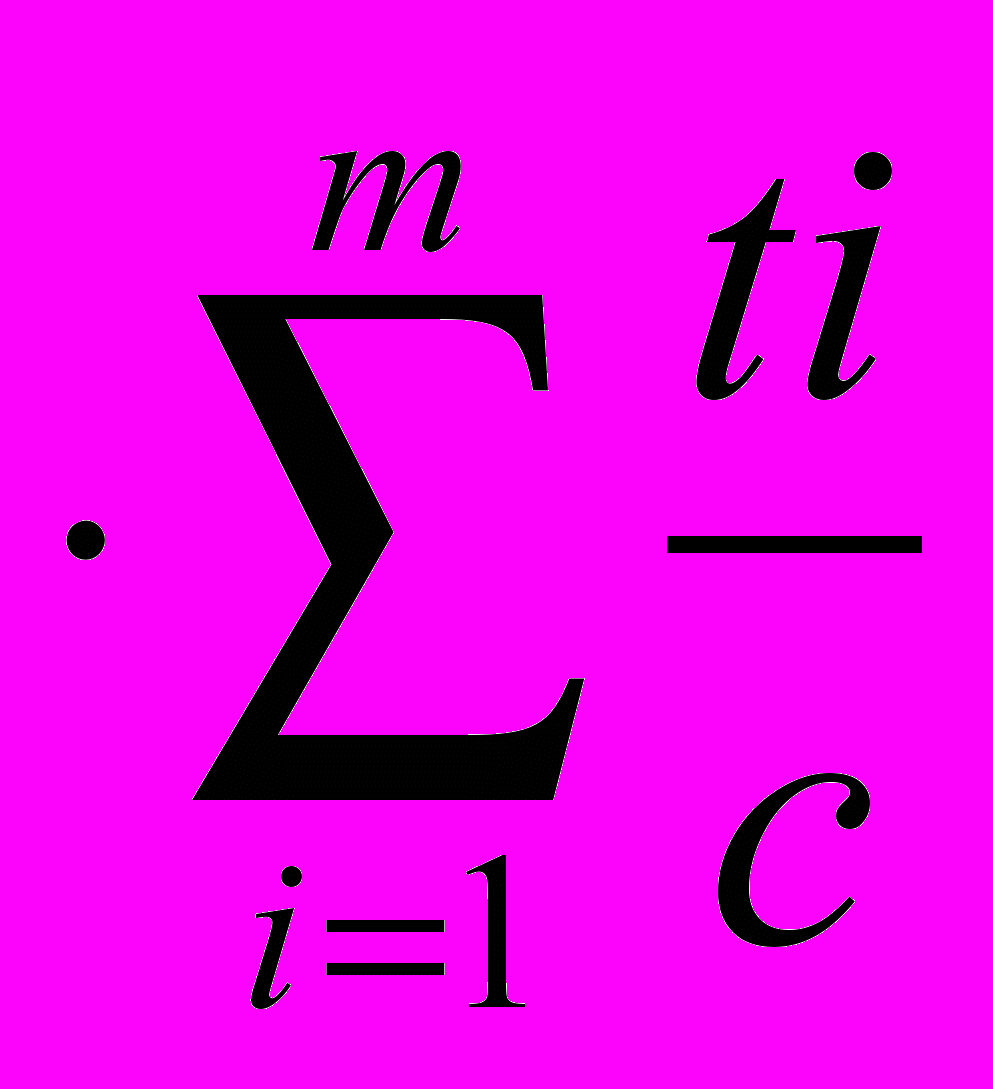
При передачи деталей целыми партиями в обработки каждой детали возникают большие перерывы, что увеличивает общую продолжительность прохождения партии по всем операциям.
Общее время внутрипартийного пролеживания одной детали на всех операциях определяется по формуле:
tпр = (n-1)* ∑ti = Тпос – tоб,
tоб- время обработки одной детали на всех операциях.
ПР: tпр = (3-1)*(2+1,5+3)=13 минут.
Общее время пролеживания всех деталей в партии определяется по формуле:
Тпр = n*tпр
ПР: Тпр = 3*13=39 минут.
Продолжительность технологического цикла для последовательного движения предметов труда определяется по формуле:

Те- время естественных процессов;
tсм- продолжительность смены;
S-количество смен;
К-коэффициент календарности (рабочие дни/календарные дни)
Преимуществом последовательного движения является простая организация и отсутствие перерывов в работе рабочих и оборудования на всех операциях.
Недостатком является большой объем незавершенного производства и большая длительность производственного цикла.
- Последовательно - параллельное движение (серийное производство).
Характеризуется тем, что выполнение последующих операций начинается до окончания обработки всей партии деталей на предыдущей операции.
Передача деталей с предыдущей операции на последующую осуществляется поштучно или транспортными партиями.
Возможны следующие варианты последовательно – параллельного движения:
А) периоды выполнения смежных операций одинаковы;
Б) продолжительность последующей операции меньше предыдущей. Для обеспечения неприрывной работы на последующей операции создается необходимый задел деталей с предыдущей.
Для определения момента начала последующей операции от точки окончания предыдущей операции над всей партией деталей откладывается отрезок равный времени выполнения последующей операции над одной деталью и влево отрезок, равный продолжительности операции над предшествующими деталями.
В) продолжительность последующей операции больше предыдущей. Детали передаются на последующую операцию сразу после их обработки.
Время параллельности выполнения смежных операций определяется по формуле:
τ =(n-p)*tmin,
tmin – продолжительность наиболее короткой операции.
ПР: τ =(3-1)*1,5=3 мин.
Продолжительность технологического цикла изготовления партии деталей определяется по формуле:
Тпп=n
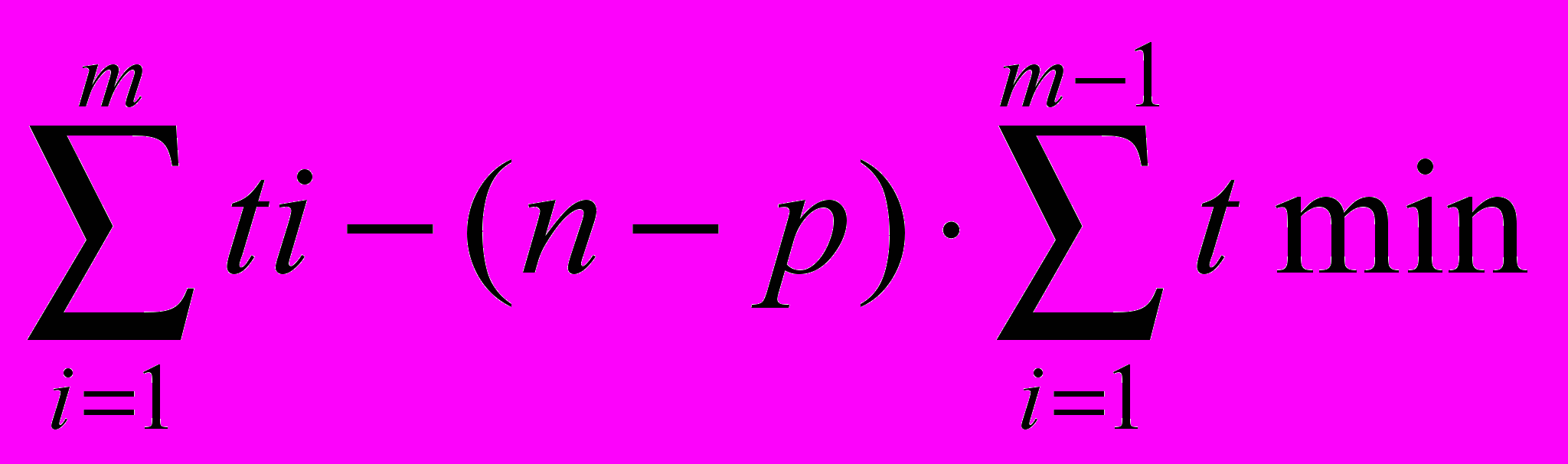
ПР: Тпп= 3(2+1,5+3) – (3-1)(1,5+1,5) = 13,5 мин.
tпр = Тпп-tобр= 13,5-6,5 = 7 минут.
Тпр = 3*7 = 21 минута.
Продолжительность производственного цикла при последовательно-паралельном движении определяется:
Тпп =

Преимуществом данного вида движения является значительное сокращение длительности производственного цикла по сравнению с последовательным движением и отсутствие перерывов в работе персонала и оборудования.
В) параллельное движение (массовое производство).
Предусматривает передачу деталей на последующую операцию немедленно после окончания обработки на предыдущей операции.
График параллельного движения партии деталей строится в следующей последовательности:
- Строится технологический цикл для первой транспортной партии по всем операциям без пролеживания между ними;
- На операциях с максимальной продолжительностью строится операционный цикл обработки деталей для всей партии без перерывов в работе оборудования.
- Достраиваются операционные циклы остальных транспортных партий.
Продолжительность технологического цикла изготовления партии деталей определяется по формуле:
Тпар = n*tmax + ∑pti – ptmax = (n-p)*tmax+p∑ti
ПР: Тпар = (3-1_*3+ 1(1,5+2+3)=12,5 мин.
tпр = 12.5-6.5 = 6 мин.
Тпр = 3*6=18мин.
Продолжительность производственного цикла определяется:
Тпар =

Данный вид движения предметов труда обеспечивает наименьшую продолжительность технологического цикла, но вызывает простои на рабочих местах, которые могут быть ликвидированы за счет синхронизации выполнения операций.
- Пути сокращения длительности производственного цикла.
Сокращение длительности производственного цикла осуществляется по следующим направлениям:
1) сокращение времени трудовых процессов:
- внедрение рациональных тех.процессов, оборудования и оснастки;
- механизация и автоматизация транспортных, складских и контрольных операций;
- рациональная организация трудовых процессов и рабочих мест;
- применение наиболее оптимальной системы движения предметов труда;
- повышение технологичности конструкций;
2) сокращение времени естественных процессов путем замены естественных процессов технологическими операциями;
3) сокращение времени перерывов:
- рациональная организация производственного процесса;
- увеличение сменности работ;
- применение наиболее эффективного вида движения предметов труда;
- устранение нерегламентированных перерывов