Й подачи продукции, толщины упаковочной пленки в пределах 5%, постоянной подачи сжатого воздуха давлением 7-8 атмосфер, обслуживания машины согласно инструкции
Вид материала | Документы |
СодержаниеФормообразующий сборочный узел Узел передач Узел захвата Конвеер снятия пакетов |
- Правила подачи заявки 4 критерии отбора заявки 5 Использование средств гранта 6 сроки, 112.23kb.
- Методика расчёта центробежного компрессора с радиальными лопатками, 253.33kb.
- Выставки в Пекине, 66.27kb.
- Извещение №125п о продлении срока подачи котировочных заявок, 161.64kb.
- Машина листовая офсетная ряда офсет-52, 65.86kb.
- Анализ результатов исследования образцов, наплавленных автоматической наплавкой под, 158.72kb.
- Упаковочной индустрии, 21.47kb.
- Администрация города тобольска единая комиссия по размещению заказов на закупку товаров,, 1264.49kb.
- Правила составления, подачи и предварительной экспертизы заявки на выдачу патента, 714.45kb.
- Повышение эффективности систем естественной вентиляции в помещениях для содержания, 291.06kb.
Группа компаний по продаже пищевого и емкостного оборудования
г. Москва, тел. (495) 972-56-58, (916) 640-86-86, (926) 375-43-87, (963) 672-33-33
E-mail: hardom@list.ru Сайт: www.e4a.ru ICQ: 239-76-70-70
Производительность упаковочной машины составляет 55-60 пак/мин со штуцером и зависит от вязкости и непрерывной подачи продукции, толщины упаковочной пленки в пределах 5%, постоянной подачи сжатого воздуха давлением 7-8 атмосфер, обслуживания машины согласно инструкции.
Точность дозировки упаковочной машины составляет 0,5-1% и зависит от регулярной очистки дозатора и постоянства удельного веса продукции.
Принципы работы Оборудования:
Тип машины РК-90 : Горизонтальное формирование пакетика / Наполнение / Запечатывание
Тип наполняющего приспособления: Пневматический для пастообразных и жидких продуктов.
Для того, чтобы сформировать пакетик, наполнений продуктом, лента упаковочного материала проходит через сборочные узлы машины том порядке, как показано. Пожалуйста смотрите чертеж внешней компоновки( G.A. drawing) (Рис. № 5.1 и 5.2).
ФОРМООБРАЗУЮЩИЙ СБОРОЧНЫЙ УЗЕЛ:
- Рулон устанавливается на рулонный вал этого узла.
- Рулон проходит через различные роликовые опоры к складывающему плугу.
- Складывающий плуг сгибает ленту упаковочного материала в форме "V".
Если машина предназначена для вертикального пакетика, для образования вставки на донной стороне предусмотрен узел вставки.
УЗЕЛ ЧЕРНИЛЬНОГО КОДИРОВЩИКА (По дополнительному заказу):
- После складывающего плуга на X - Y каретке предусмотрен чернильный кодировщик.
- Настройкой этой каретки можно получить кодировку на требуемом месте на пакетике.
ДАТЧИК МЕТКИ Eye mark
- Ha X - Y каретке предусмотрен датчик с фотоэлементом.
- Датчик с фотоэлементом реагирует на метку Eye mark на ленте и подает сигнал на контроллер.
- Программируемый контроллер управляет натяжением ленты с помощью механически и пневматически управляемого поршня в соответствии с сигналом, поданным датчиком.
ЗАПЕЧАТЫВАЮЩИЙ АВТОМАТ (Общая компоновка):
Пожалуйста чтобы увидеть компоновку вашей машине, обратитесь к чертежу общей компоновки (G.A. drawing) (Рис. № 5.1 и 5.2).
- Данная машина РК-90 имеет три комплекта механически и пневматически открываемых запечатывающих узлов.
- Донное запечатывание выполняется пневматическим способом на первом запечатывающем узле.
УЗЕЛ ПЕРЕДАЧ:
Узел передачи пневматическим способом передает разрезанные поштучно пакетики одновременно по 2 шт. на узел захвата.
УЗЕЛ ФОРМИРОВАНИЯ ФИГУРНОГО ПАКЕТА, ЗАКРУГЛЕНИЯ УГЛОВ (согласно Приложениям №№ 2-5)
Узел состоится из пунсона и матрицы, который вырезают необходимую фигуру и передают разрезанные поштучно пакетики одновременно по 2 шт. на узел захвата.
УЗЕЛ ЗАХВАТА:
Узел захвата имеет восемь(8) отдельных подузлов. Подузел, который принимает по 2 пакетика, считается первым.
1-й подузел: Принимает обрезанные пакетики.
2-й подузел: Входное отверстие пакетика открывается с помощью вакуумных присосок и для того, чтобы открыть пакетик полностью, подается под давлением воздух.
3-й подузел: Механический раскрыватель пакетика открывает пакетик и датчик, имеющийся на этом подузле, определяет, открыт пакет или нет, наполняет пакет инертным газом и подает сигнал программируемому контроллеру.
4-й подузел: Первый дозатор наполнения. Наполнение на этом подузле выполняется при помощи наполняющего приспособления, соответсвующего пакуемому продукту.
5-й подузел: Второй дозатор наполнения.
6-й подузел: Пакетики на этом подузле натягивается, с тем, чтобы получить качественный верхний шов.
7-й подузел: На этом подузле пневматически производится верхнее запечатывание с помощью одного комплекта губок из "оружейного металла" и другого комплекта охлаждающих губок.
8-й подузел: Пакетик отделяется от этого подузла на конвейер снятия заряда. Если пакетик закрыт, он не наполнится. Верхний шов не будет сделан и на этом подузле он будет продут воздухом.
КОНВЕЕР СНЯТИЯ ПАКЕТОВ
Конвейер снятия пакетов забирает пакетики с узла захвата.
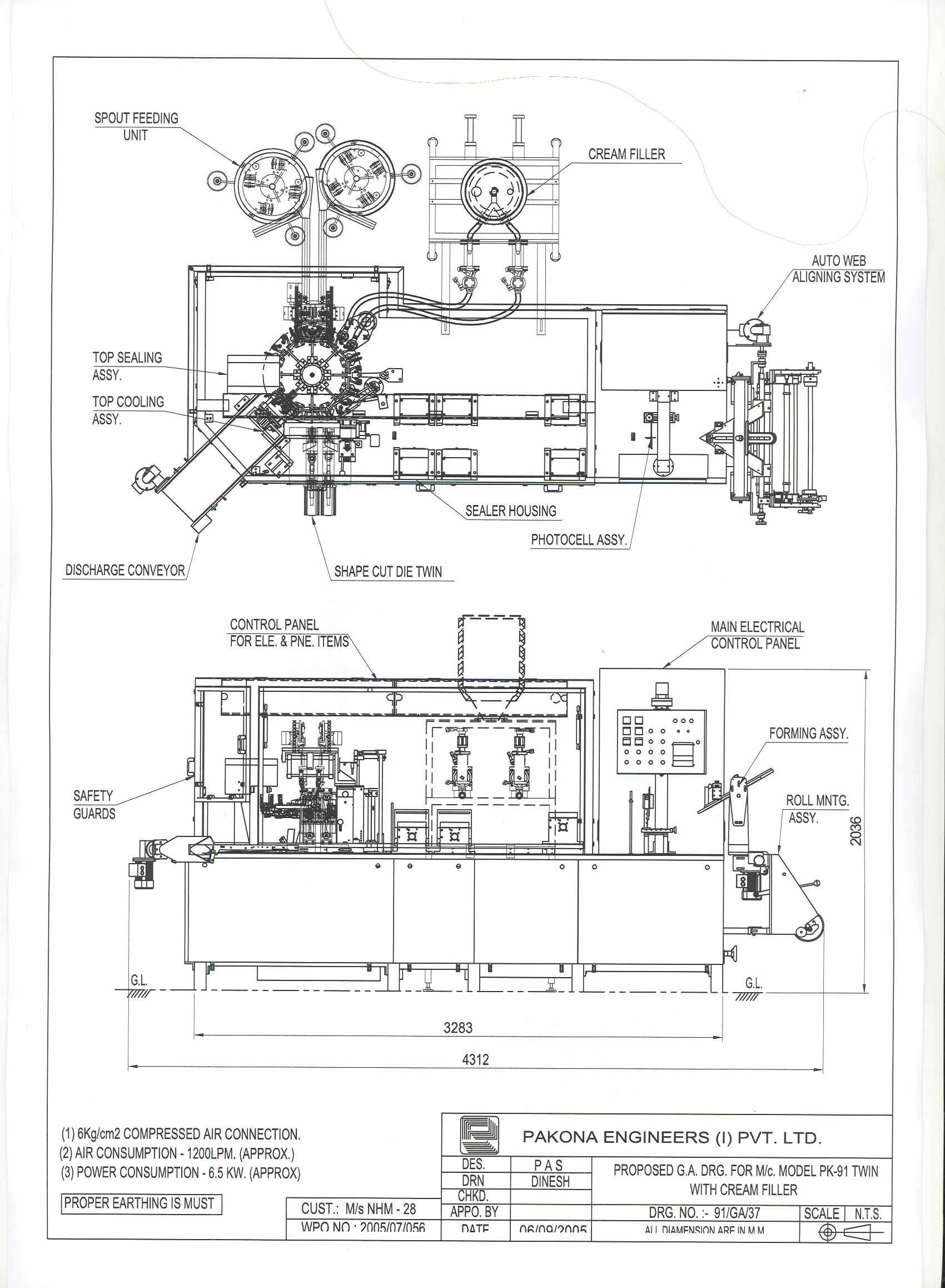
Рис. №5.1
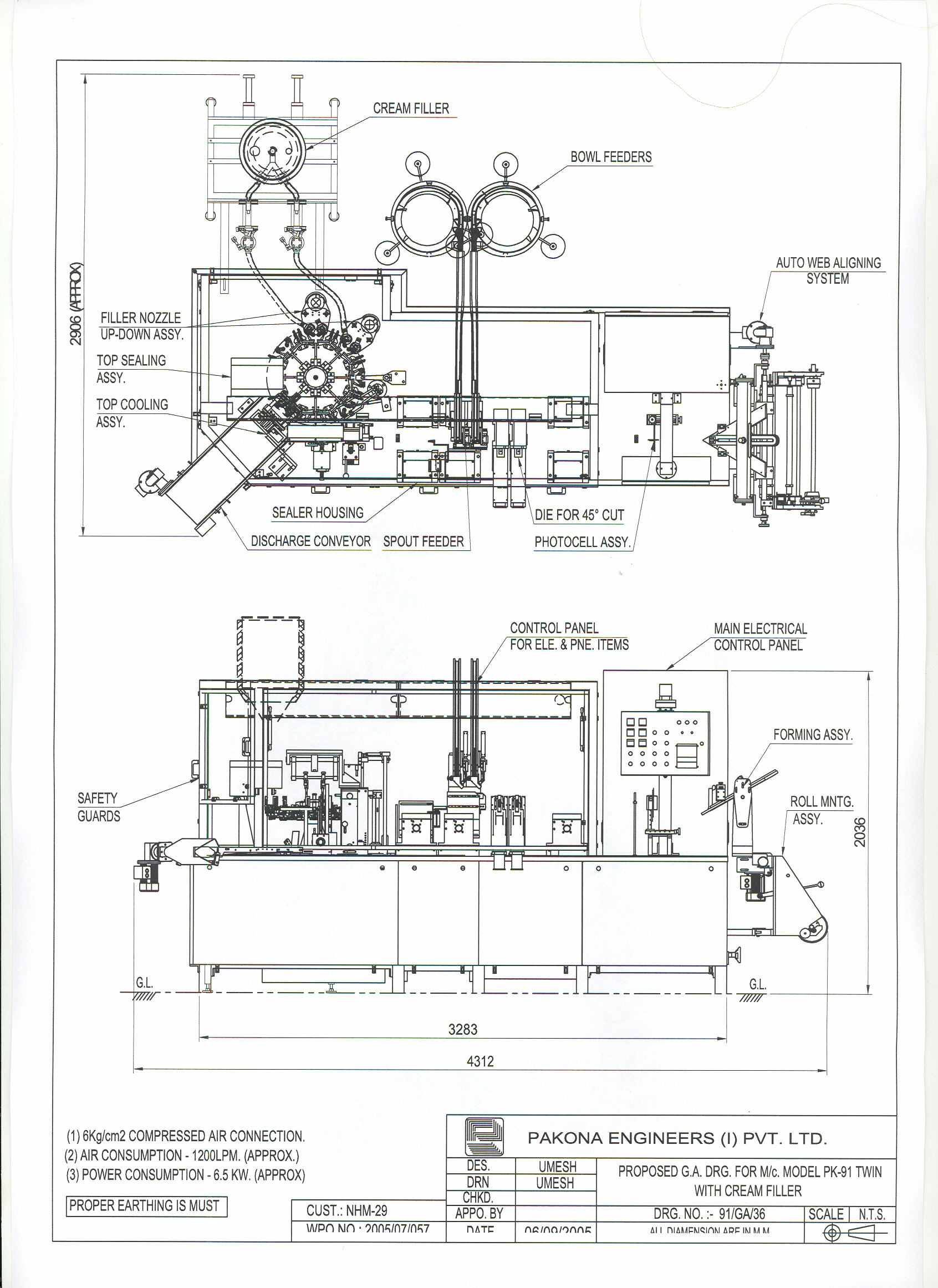
Рис. №5.2
- Основные функции оборудования
- Горизонтальная полностью автоматическая упаковочная машина прерывистого принципа, модель - РК-90;
- Формирование стоячего пакета типа Дой-Пак из пленки в рулоне, пригодной к термопайке;
- Впаивание готовых открываемых угловых клапанов в срезанный под 45о угол пакета, в области бокового верхнего шва на одной машине и впаивание готовых открываемых центральных клапанов на другой машине;
- Простановка даты изготовления на шве пакета;
- Продувка пакета инертным газом;
- Наполнение пакета при помощи дозатора с максимальной погрешностью ± 1%, кетчупом или другим вязким продуктом;
- Запаивание наполненного пакета;
- Охлаждение швов и перемещение готового пакета с помощью выходного конвейера.
- Горизонтальная полностью автоматическая упаковочная машина прерывистого принципа, модель - РК-90;
2. Требования к оборудованию
2.1. Станина машины выполнена из материалов пригодных к использованию в пищевой промышленности;
2.2. Все части соприкасающиеся с продуктом, сделаны из нержавеющей стали (марка ___AISI304__);
2.3. Техника безопасности и защита от несчастных случаев – в соответствии с требованиями Европейского Союза;
2.4. Обслуживание - одним человеком, соответствующего образования и подготовки, общее состояние которого позволяет решать текущие задачи на работающем оборудовании, включая смену рулона;
2.5. Электрическое подключение 220 В/380 В, 3PH+N или PE, 50 Гц;
2.6. Заявленная производительность – 55-60 пакетов в минуту с угловым клапаном на одной машине и с центральным клапаном на другой машине, определяемая подсчетом количества пакетов выработанных за одну минуту непрерывной работы;
2.7. Уровень шума не выше 80 dВ;
2.8. Наличие защитного кожуха с электроблокировкой;
2.9. Наличие лотка из нержавеющей стали для сбора утечки продукта;
2.10. Двойной перфоратор на участке протяжки пленки для вырубки отверстий для фиксации дна устойчивого пакета;
2.11. Централизованная смазка узлов и механизмов;
2.12. Клемные присоединения для влагозащищенных нагревательных элементов и проводов датчиков с прочным подключением;
2.13. Управление температурным режимом для каждой пары нагревательных элементов с пульта;
2.14. Невозможность попадания смазочных материалов на производимый продукт;
2.15. Отсутствие некачественных швов, как следствие неэффективности охлаждения швов пакета;
2.16. Механическое устройство бескрасочного тиснения на боковом шве пакета даты изготовления (с подогревом);
2.17. Контроль на формирователе пакета (нет пакета – нет наполнения) и синхронизация с дозатором;
2.18. Бункер с рубашкой для продукта объемом 50 л, с устройством отсчета времени расхода упаковываемой продукции и датчиком верхнего уровня;
2.19. Диаметр пневмопривода дозирующего устройства – по усмотрению завода-изготовителя, после проверки характеристик продукции, но не менее 50 мм;
2.20. Визуальная сигнализация выхода из строя нагревательных устройств на панели управления;
2.21. Устройство для продувки пакета инертным газом;
2.22. Уплотнение поршня дозирующего устройства выполнить из фторопласта;
2.23. Управление машиной при помощи PLC управления и со сенсорным экраном всех электрических устройств, исключая аварийный останов и ограждение;
2.24. Все надписи на машине на русском языке;
2.25. Наличие счетчиков: наработанных часов, готовых пакетов за смену, общего количества пакетов с начала работы;
2.26. Используемые в машине полимерные шланги и материалы, контактирующие с продуктом должны иметь разрешение для применения в пищевой промышленности и быть термостойким.
«Технические требования к пленке, клапанам
и фасуемому продукту»
1. Продукт: густой томатный соус/кетчуп с твердыми включениями овощей, кусочков и семечек перца Чили, волокнами корня имбирь (до 1000 мм³), разливаемый при температуре 75-85°С.
2. Вес (нетто) продукта/объем: 250г ± 1% для пакета с центральным клапаном
220г ± 1% для пакета с угловым клапаном
3. Упаковочный материал: - термосвариваемая пленка, подаваемая с рулона, нанесение печати на верхний слой;
- PET 12 / Al 8 / PE 100 мkм;
- PET 12 / PE 100 mkm. и PET 12 / PE 130 mkm.
- Максимальный вес рулона __20__ кг;
- Максимальный наружный диаметр рулона 350 мм;
- Максимальная ширина рулона 500 мм;
- Максимальный диаметр внутренней втулки 76 мм.
- Размер готового пакета: (см. рисунок №1) 100*185+2*30 мм донная складка
(см. рисунок №2) 110*180+2*27,5 мм донная складка
Допуски на размеры (определяются качеством нанесения фотометки):
- пакета ± 1 мм (см. рисунок №1,2,3,4);
- углового / центрального клапана ± 0,5 мм (см. рисунок №6).
5. Размер и конструкция клапана: (см. рисунок № 6).
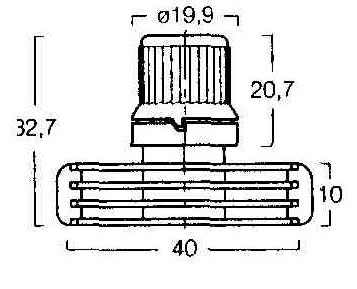
рис.6
штуцер в сборе
6. Требования к упаковочной пленке:
6.1. Пленки, толщиной 115 и 145 микрон (полиэтилен (100 или 130 микрон), полиэстер (12 микрон), алюминевая фольга (0 и 8 микрон) клей (3 микрон)), позволяющие производить упаковку горячего продукта.
6.2. В зоне нанесения фотометки не должно быть посторонних знаков, пометок. Должен соблюдаться четкий контраст между базовым цветом и цветом фотометки.
- Допустимое отклонение линейного размера между фотометками на 10 пакетов не более ± 1,0 мм, т.е. не более ±0,1 мм между соседними фотометками.
« Требования к качеству готовой продукции и методы испытания»
- Дозирование в соответствии с п. 5 настоящего приложения
- Точность дозирования ±1%;
- Точность дозирования ±1%;
- Проверка точности дозирования производится каждые 15 минут работы машины, путем измерения массы (нетто) одной единицы фасовки на весах для точного взвешивания (точность измерения - 0,01 гр)
2. Геометрия пакета в соответствии с п. 5 настоящего приложения
2.1. 100% соблюдение размеров пакета, согласно приложения №4 к настоящему контракту и размеров швов (ширина швов 5-10 мм);
2.2. Угловой клапан должен располагаться под 450;
2.3. В пустом пакете, без клапана, все вертикальные и горизонтальные швы - под углом 90 ± 10 (линия снаружи и линия внутри) согласно п. 5 настоящего приложения;
- проверка геометрических размеров готового пакета производится каждые полчаса работы машины при помощи линейных мер измерения (линейка, траспортир).
3. Внешний вид и информация в соответствии п. 5 настоящего приложения
3.1. Пакет целый, отсутствуют дырки, царапины;
- Угловой клапан в процессе нахождения в аппарате не должен быть поврежден (кольцо не должно быть оторвано, отсутствие вмятин, царапин);
3.3. Отсутствие подтеков соуса/кетчупа на пакетах и угловом клапане в том случае, если возможно изготовление специальных сопел в связи со спецификой свойств упаковываемого продукта;
3.4. Все края пакета абсолютно ровные – без зазубрин (при изготовлении пакета из одного рулона и при соблюдении к требованиям фотометки, согласно приложения №4);
3.5. Не допускается смещение сторон пакета относительно друг друга, видимое с оборотной или с лицевой стороны более чем ± 1 мм;
3.6. На всех швах должны отсутствовать морщинки, вмятины, вогнутости, изогнутости (за исключением цифр даты) видимые человеком с нормальным зрением с расстояния 1 м. За исключением шва на штуцер, на котором вогнутости связаны с формой штуцера;
3.7. Не допускается на лицевой и/или оборотной сторонах вогнутости, царапины в виде полосок, точек, видимые человеком с нормальным зрением с расстояния 1 м;
3.8. Дата пропечатана целиком и полностью;
3.9. При нанесении даты не должны образовываться дырки;
- Проверка внешнего вида и качества нанесения информации (дата на шве пакета) контролируется постоянно визуально.
4. Герметичность готового пакета в соответствии п. 5 настоящего приложения
4.1. Готовый пакет с запаянными швами и впаянным угловым клапаном должен выдерживать давление массы в 40 кг и сохранять герметичность после падения с высоты - 2 м
- Испытание не герметичность проводится в день выпуска , спустя 24 часа, 48 часов.
Для испытания в день выпуска – каждые полчаса работы машины отбираются два пакета, для последующих испытаний пакеты отбираются методом случайной выборки из расчета один пакет из тысячи.
5. Допустимый процент брака, исключая потери при пуско-наладочных работах и при аварийных ситуациях - не более 1,5 % в зависимости от:
5.1. Обслуживание согласно инструкции;
5.2. Квалификация обслуживающего персонала;
5.3. Количество переналадок машины под те или иные виды упаковываемой продукции;
5.4. Соответствие материала пленки и угловых клапанов требованиям Продавца.