Бурильные машины § классификация бурильных машин и способов бурения
Вид материала | Документы |
- 1 Эволюционная классификация ЭВМ, 555.23kb.
- 1. Общая классификация строительных машин. Производительность машины и ее категория, 651.54kb.
- Комплекс машин для заготовки прессованного сена. Марки машин и их технические характеристики, 8.88kb.
- Программа вступительного экзамена в аспирантуру по специальной дисциплине 05. 02., 266.3kb.
- Ательный материал «Электронный курсовой проект «Проектирование машин постоянного тока», 47.15kb.
- Краткое содержание: Прямая задача динамики машин. Понятие о динамической модели машины, 252.59kb.
- Симанкин Федор Аркадьевич, к т. н., доцент Вид учебной работы Аудиторные занятия самостоятельная, 155.96kb.
- 1. Классификация швейных машин Начертить кинематическую схему механизма иглы машины, 47.12kb.
- Машины с электрическим приводом, 61.22kb.
- Программа дисциплины по кафедре "Cтроительные и дорожные машины " технические основы, 254.17kb.
1 2
БУРИЛЬНЫЕ МАШИНЫ
§ 1. КЛАССИФИКАЦИЯ БУРИЛЬНЫХ МАШИН И СПОСОБОВ БУРЕНИЯ
По назначению бурильные машины делятся на машины для образования шпуров по углю и горным породам и для проведения скважин различного назначения — разведочных, сбоечных, вентиляционных, дренажных, дегазационных и др.
Шпурами принято называть цилиндрические полости, выполненные в горной породе, глубиной до 5 м при диаметре до 75 мм. Шпуры большего диаметра называют скважинами, а длиной более 5 м — глубокими скважинами.
Бурильные машины, кроме того, классифицируют по способу разрушения горной породы, роду потребляемой энергии.
По первому признаку их подразделяют на машины с механическим, физическим и комбинированным способами разрушения породы, по роду потребляемой энергии — на электрические, пневматические, гидравлические и комбинированные.
При механическом способе разрушения осуществляется непосредственное воздействие специального бурового инструмента на разрушаемую породу. К этому способу относят ударно-поворотное, вращательное, ударно-вращательное и вращательно-ударное бурение.
При физическом способе разрушения на породу воздействуют газами, жидкостями, электрическим током, теплом или другими видами энергоносителя. К этому способу относят огневое (термическое), взрывное, ультразвуковое, гидравлическое и электрогидравлическое бурение.
При комбинированном способе разрушения на породу воздействуют с помощью механического и физического способов одновременно.
Ударно-поворотное бурение (рис. IV.34, а) характеризуется тем, что клиновидный инструмент внедряется в породу под действием кратковременной, но значительной по величине ударной нагрузки Fyд, направленной по оси инструмента. При этом осевое усилие прижатия инструмента Foc очень мало и обеспечивает только контакт инструмента с породой в момент удара. Крутящий момент MKР также очень мал. После каждого удара вследствие упругости породы и инструмента последний отскакивает от забоя и поворачивается механизмом поворота на некоторый угол β (рис. IV.35), обычно равный 10—20°. Под действием ударной нагрузки происходит разрушение породы под действием бура (борозды 1—1, 2—2 и 3—3) глубиной h и скалывание ее под действием горизонтальной составляющей F6:
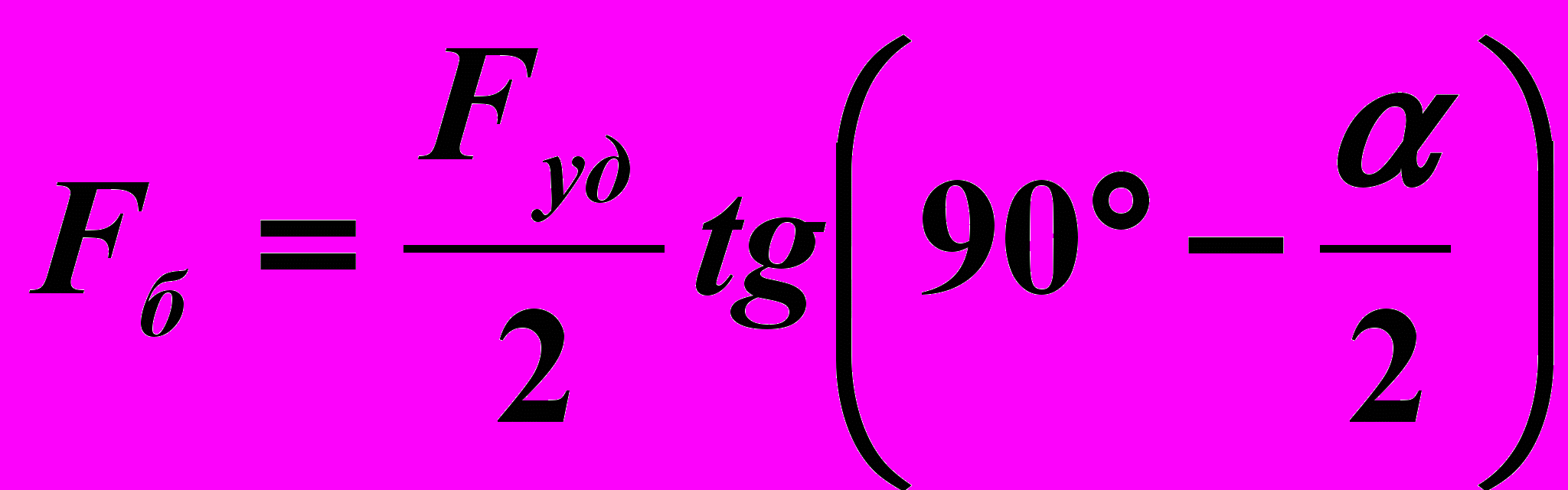
где α = 90 ÷120° – угол заострения бура.
Разрушенную породу удаляют из шпура или скважины промывкой, продувкой или другим способами. Основное достоинство ударно-поворотного бурения — возможность бурить породы крепостью f = 6 ÷ 20.
С помощью бурильных молотков (перфораторов) бурят шпуры и скважины диаметром 20—150 мм и глубиной до 12 м и более, а станками ударно-канатного бурения — скважины диаметром до 300 мм и глубиной до 40 м и более.
К недостаткам ударно-поворотного бурения следует отнести периодичность воздействия инструмента на породу, причем время, затрачиваемое на удар, в десятки раз меньше времени на движение инструмента по направлению к забою, отскок и поворот. Кроме того, для ударно-поворотного бурения характерны значительные пылеобразование, шум и вибрация при работе.
Вращательное бурение (рис. IV.34, б) характеризуется тем, что резец под воздействием осевого усилия подачи F,,c и крутящего момента МКР движется поступательно на забой, отделяя по винтовой линии срез толщиной h. Ударные нагрузки при этом отсутствуют. Разрушение породы может осуществляться резанием, смятием и раздавливанием. Удаление продуктов бурения из шпура или скважины производится с помощью витых штанг или шнеков, сжатого воздуха и воды.
К бурильным машинам вращательного действия относятся ручные и телескопные сверла, бурильные станки, длинноходовые бурильные машины вращательного действия, буросбоечные и буро-шнековые машины. Область их применения — малоабразивные породы с коэффициентом крепости до f = 6 ÷ 8, а при оснащении рабочего инструмента алмазами — крепкие и очень крепкие породы (f >10).
При вращательном бурении различают бурение сплошным забоем, когда порода разрушается по всей его площади, и кольцевым забоем, когда в центре забоя шпура (скважины) остается колонка (керн) неразрушенной породы. Преимущества вращательного бурения: непрерывность процесса, обеспечивающая высокую производительность; разрушение породы крупным срезом, что уменьшает пылеобразование и
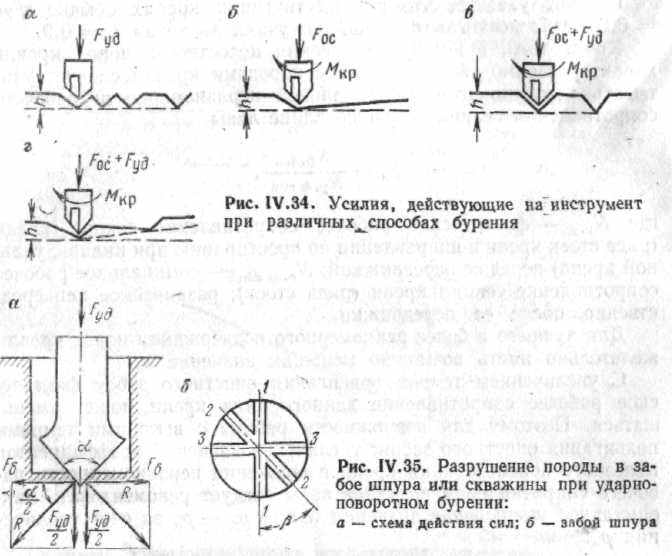
удельные энергозатраты; отсутствие вибрации машин при работе. К недостаткам следует отнести ограниченную область применения по крепости горных пород.
Ударно-вращательное бурение (рис. IV.34, в) можно рассматривать как ударное с непрерывным вращением инструмента. Разрушение породы происходит под действием большой ударной нагрузки Fуд, передаваемой клиновидному инструменту (долоту), постоянно прижатому к забою с относительно небольшим осевым усилием Fоc при непрерывном вращении инструмента под воздействием небольшого крутящего момента Мкр, достаточного для того, чтобы производить зачистку шпура (или скважины) от разрушенной породы и срезать небольшую часть ее, слабо связанную с массивом.
Этот способ бурения реализован в буровых агрегатах, применяемых в рудной промышленности при бурении скважин диаметром 85—150 мм и глубиной до 70 м в крепких и абразивных породах (f = 8 ÷20).
Вращательно-ударное бурение (рис. IV.34, г). Разрушение породы происходит под воздействием значительных по величине осевой нагрузки Foc, ударной Fyjr, а также крутящего момента МКР. При таком сочетании усилий основная часть энергии затрачивается на разрушение породы резанием, а ударная нагрузка увеличивает глубину внедрения резца. Область применения — неабразивные породы с коэффициентом крепости f = 6 ÷ 14.
Этот способ бурения реализован в основном на тяжелых бурильных машинах для бурения шпуров и скважин диаметром до 100 мм.
Огневой (термический) способ бурения из всех физических способов получил наибольшее распространение и применяется для прожигания скважин диаметром до 300 мм и глубиной до 30 м. Разрушение породы происходит за счет термонапряжений, возникающих при ее нагреве высокотемпературными газовыми струями (2000—2500 °С), вылетающими из сопел горелки со скоростью до 2000 м/с. Под действием этих напряжений тонкий слой породы растрескивается и под механическим воздействием газовых струй разрушается на мелкие частицы, которые транспортируются из скважин паро-газовой смесью. Наиболее эффективной областью применения являются породы, имеющие кремнистое основание, или породы с низким коэффициентом теплопроводности, которые растрескиваются раньше, чем начинается их плавление.
Ультразвуковой способ бурения основывается на принципе совместного воздействия на горную породу высокочастотных ультразвуковых колебаний, накладываемых на инструмент, и кавитационного эффекта промывочной жидкости.
Гидравлический способ бурения основан на действии струй воды небольшого диаметра (0,8—1 мм), подаваемой на забой под высоким давлением (до 200 МПа) и со сверхзвуковой скоростью.
Электрогидравлический способ бурения осуществляется подачей высокого напряжения на контакты электрической цепи, расположенные на забое скважины, заполненной водой. При этом происходит пробой межэлектродного промежутка с образованием газового канала в месте пробоя. Давление в искровом канале в зависимости от параметров разрядного контура достигает 600–1500 МПа. Расположение искрового канала в непосредственной близости от породы приводит к ее разрушению.
Ультразвуковой, гидравлические и электрогидравлический способы бурения в настоящее время находятся в стадии теоретических и экспериментальных исследований и в промышленности не применяются.
К физическому способу относится также взрывобурение, которое может осуществляться с помощью патронов жидких или твердых взрывчатых веществ, а также струйным способом.
В первом случае в промывочному жидкость, циркулирующую по спущенным до забоя скважины трубам, с определенной частотой подаются патроны с жидким или твердым ВВ, взрывающиеся от удара в забой. Во втором случае по специальным трубкам из емкостей к дозирующим приспособлениям забойного взрывобура поступают жидкие компоненты ВВ (горючее и окислитель), которые затем подаются на забой и с помощью инициатора (сплава калия и натрия) взрываются.
Взрывобурение в настоящее время находится в стадии проверки.
Термомеханическое бурение относится к комбинированному способу разрушения горной породы. Сущность способа заключается в том, что с помощью высокотемпературных газовых струй в поверхностном слое забоя скважины создается предварительное напряженное состояние, благодаря которому значительно облегчается последующее разрушение породы механическим воздействием (шарошечным долотом или другим буровым инструментом). Производительность станков термомеханического бурения на 30— 50% выше по сравнению с чисто шарошечным бурением.
МАШИНЫ УДАРНО-ПОВОРОТНОГО БУРЕНИЯ
Машины ударно-поворотного бурения предназначены для бурения шпуров диаметром до 52 мм и глубиной до 5 м и скважин диаметром до 150 мм в породах средней крепости и крепких.
К машинам ударно-поворотного бурения относят бурильные молотки (перфораторы) и станки ударно-канатного бурения.
Бурильные молотки классифицируют:
по виду потребляемой энергии — на пневматические, электрические и гидравлические;
по способу удаления буровой мелочи из шпура или скважины — с промывкой, продувкой и отсасыванием;
по частоте ударов – обычного типа и быстроударные (соответственно до 2000 ударов в минуту и более);
по способу воздухораспределения – с клапанным, золотниковым, самораспределением и комбинированным распределением воздуха;
по способу установки и поддержания молотка при бурении – на ручные, колонковые и телескопные.
Помимо этого, различают обычные молотки, располагаемые вне шпура или скважины, и входящие в скважину (погружные молотки), а по массе условно различают легкие, средние и тяжелые молотки. При этом к средним относят ручные молотки массой 20–25 кг, колонковые – 40–50 кг, телескопные – 35–45 кг и погружные 20–30 кг.
При бурении ручные перфораторы массой не более 12,5 кг держат в руках, а при большей массе устанавливают на специальных приспособлениях – пневмоподдержках. Телескопные перфораторы оборудуют пневматическими поддерживающими и подающими телескопными механизмами. Колонковые перфораторы — наиболее тяжелые, и для бурения их монтируют на винтовых распорных колонках, манипуляторах или буровых каретках, оснащенных автоматическими подающими механизмами – автоподатчиками. Погружные перфораторы входят непосредственно в выбуриваемую скважину и крепятся на конце штанги, закрепляемой в патроне подающего механизма.
В общем случае бурильный молоток состоит из корпуса и смонтированного в нем ударно-поворотного механизма, воздухораспределительного устройства, механизма управления и устройства для очистки шпуров (скважин) от буровой мелочи.
Корпус ручного перфоратора, в свою очередь, состоит из головки 1 (рис. IV.36), цилиндра 4 с направляющей втулкой 8 и патрона 9 с буродержателем 11. Ударно-поворотный механизм служит для нанесения ударов по буровому инструменту и его поворота. Он состоит из поршня-ударника 7 с поворотной гайкой 13, поворотного винта 6 с храповым устройством 5, поворотной буксы 10 и гранбуксы 12. Воздухораспределительное устройство 3 предназначено для попеременной подачи сжатого
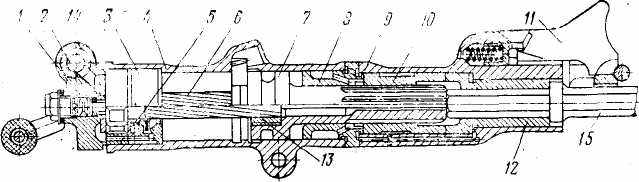
Рис. IV.36. Ручной перфоратор ПР19
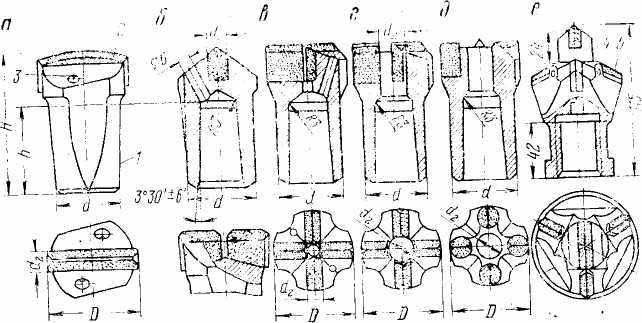
Рис. IV.37. Буровые коронки
воздуха в наружную или заднюю полость цилиндра перфоратора. Механизм управления смонтирован в головке перфоратора и состоит из пускового крана 14 с рукояткой. Устройство 2 служит для выноса буровой мелочи и подавления пыли. Сущность работы перфоратора заключается в том, что сжатый воздух с помощью воздухораспределительного устройства подается попеременно в правую или левую полость цилиндра, обеспечивая возвратно-поступательное движение поршню-ударнику 7.
При движении вперед (рабочий ход) поршень-ударник наносит удар по буровому инструменту 15, а при обратном (холостом) ходе поворачивается на некоторый угол вокруг винта 6, поворачивая через буксу 10 и гранбуксу 12 буровой инструмент.
Рабочий инструмент. В качестве рабочего инструмента при ударно-поворотном бурении применяют буры или буровые штанги с головками или буровыми коронками. При этом буры могут быть цельными и составными.
Выбор типа бура и коронок определяется физико-механическими свойствами породы и условиями бурения.
Наиболее широкое распространение в горной промышленности получили однодолотные и крестовые коронки, применяемые соответственно для бурения однородных монолитных и трещиноватых пород. Соединение коронок и буров осуществляется за счет конусности с углом наклона 3° 30' или резьбы. Комплект коронок для бурения подбирают таким образом, чтобы каждая следующая Коронка имела диаметр на 1—3 мм меньше, чем предыдущий.
Буровая коронка состоит из корпуса / (рис. IV.37, а), который изготовляется из стали У7А или У8А и армируется твердым сплавом 2 в виде пластинок или штырей. Для промывки шпура коронка имеет отверстие 3. Лезвие коронки затачивается под углом заострения 90—120°.
Долотчатые коронки (рис. IV.37, а, б) для перфораторного бурения обычно имеют диаметр D, равный 32—65 мм, а крестовые — до 85 мм.
Крестовые коронки (рис. IV.37, в—д) обычно выполняют с центральным отверстием для промывки.
Коронки с опережающим лезвием (рис. IV.37, ё) используют для бурения скважин тяжелыми колонковыми и телескопными, а также погружными перфораторами.
§ 3. МАШИНЫ ВРАЩАТЕЛЬНОГО БУРЕНИЯ
При вращательном бурении разрушение горной породы происходит спиральными слоями за счет постоянного сообщения буровому инструменту осевого усилия подачи и крутящего момента.
К машинам вращательного бурения относят: ручные и колонковые сверла, применяемые в основном для бурения шпуров по углю и породам ниже средней и средней крепости, станки для бурения разведочных и взрывных скважин по породам любой крепости и гезенкобурильные и сбоечные машины. Последние применяют для бурения подземных вертикальных и наклонных выработок диаметром 1000—1500 мм по мягким и средней крепости породам.
Современные ручные сверла подразделяют:
по способу подачи бурового инструмента на забой — на сверла с ручной и механической подачей;
по роду потребляемой энергии — на электрические (соответственно подаче типа ЭР или СЭР или ЭМ), пневматические (СПР и СПМ) и гидравлические (СГР);
по типу управления — на сверла с непосредственным управлением и дистанционным (Д).
Ручное электрическое сверло (рис. IV.38) состоит из электродвигателя, редуктора, выключателя и механизма подачи (если он
имеется).
Сверла с принудительной подачей могут применяться как для работы непосредственно с рук, так и с установкой их на поддержках или легких распорных колонках.
Принципиальное отличие ручных сверл с принудительной подачей от обычных заключается в устройстве дополнительного барабана, на который наматывается с определенным тяговым усилием трос, создающий усилие подачи сверла на забой. Например, в сверле СРП-2 барабан подачи 14 (см. рис. IV.38) приводится во вращение с помощью дополнительной червячной передачи 12 и цилиндрической пары 10—11. Переключением шлицевой муфты 8 можно получить две скорости вращения шпинделя 9. Крутящий момент при этом будет передаваться от двигателя 1 через зубчатые передачи 2—3 и 5—4 или 2—3 и 7—6. Передаточное отношение редукторов подбирается с таким расчетом, чтобы частота вращения буровой штанги находилась в пределах 300—900 мин"1.
В сверлах предусмотрена возможность замены зубчатых передач 2—3 для изменения частоты вращения коронки. Одновременно с вращением вала шпинделя вращаются шестерни 10—11, которые через червячную передачу 12 подсоединяются к малым дискам фрикционной муфты 15. Барабан подачи 14 связан с большими дисками фрикционной муфты и предназначен для наматывания троса 13 с крюком 17. Вращением штурвала 16, оборудованного резьбовым соединением, можно через пружину изменять усилие, сжимающее диски фрикционной муфты и тем самым регулировать величины передаваемых крутящего момента и тягового усилия на тросе. Электродвигатели ручных горных сверл должны иметь малую массу при сравнительно большой мощности и быть взрывобезопас-ными для применения в шахтах, опасных по газу или пыли. Напряжение тока электродвигателей составляет 127 В.
Колонковые сверла, как имеющие большую массу и значительное усилие подачи, устанавливают на распорной колонке. Подача бурового инструмента на забой осуществляется выдвижением шпинделя неподвижного сверла.
Колонковые сверла подразделяют на два типа: с гидравлической и механической подачей шпинделя. Они предназначены для бурения шпуров в углях и породах с коэффициентом крепости / < 8.
Для установки колонковых сверл используют колонки, которые раскрепляются в выработке распорным винтом.
Механические вращательные бурильные машины являются очень тяжелыми, поэтому их устанавливают на гидравлических манипуляторах бурильных установок или погрузочных машин.
Буровые машины основаны на применении мощных буровых головок, выполняющих функции вращателя. Кроме того, приводы вращателя и податчика разделены, что дает возможность обеспечить независимость их работы и получить на исполнительном органе большие крутящие моменты и осевые усилия, необходимые для бурения крепких пород.
В кинематической схеме длинноходового электрического сверла ДЭС4 (рис. IV.39) обозначены: вращатель / с электродвигателем 10, автоподатчик с люнетами 6 для поддержания буровых штанг 8 с резцом 9. Податчик крепится на манипуляторах с помощью кронштейна 7 и состоит из рамы 4 с направляющими для каретки удвоителя подачи 15, гидроцилиндров 2 подачи и 3 распора со штоком 5, упирающимся в забой. Подача буровой головки и создание осевого усилия на буровой штанге осуществляются гидроцилиндром 2, шарнирно прикрепленным к раме податчика и оборудованным на конце штока двумя звездочками 13, входящими в зацепление с двумя цепями 12 удвоителя хода подачи. Цепи образуют замкнутый контур на каретке удвоителя подачи 15 и прикреплены с одной стороны к кронштейну 14 рамы податчика и с другой стороны — к основанию 11 буровой головки. Такая кон-
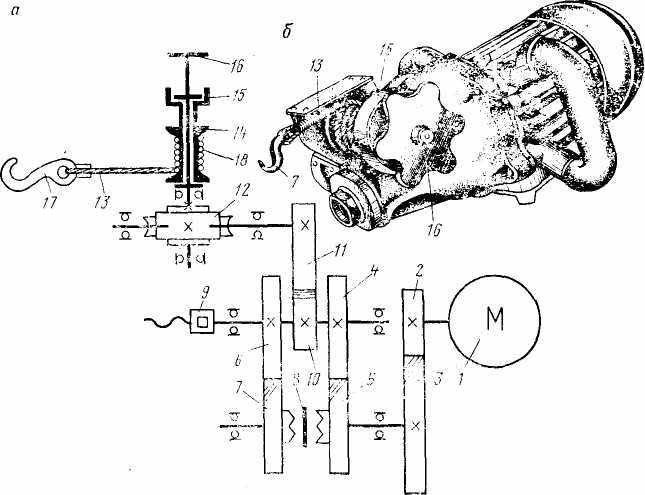
Рис. IV.38. Электрическое ручное сверло СРП2: а — кинематическая схема; б — общин вид
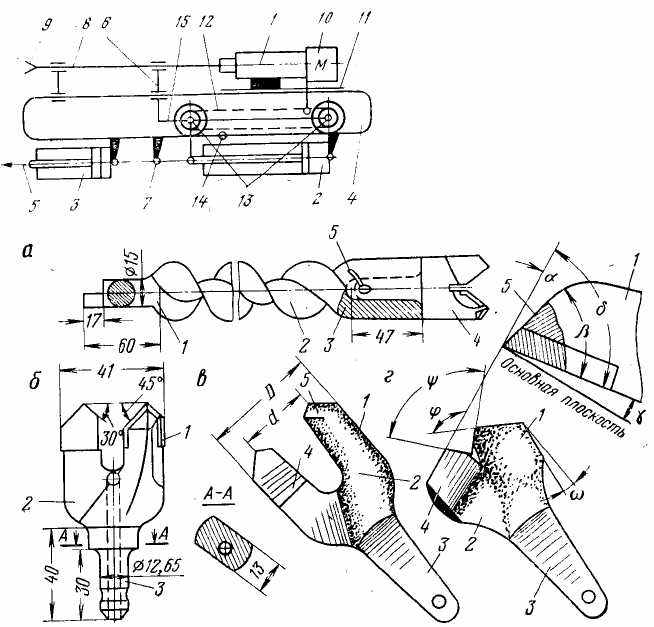
Рис. 1V.39. Кинематическая схема длинноходового электрического сверла ДЭС4
Рис. 1V.40. Рабочий инструмент машин вращательного бурения
струкция позволяет удваивать величину подачи по сравнению с ходом штока гидроцилиндра до 3,5 м при осевом усилии 10 кН. Скорость подачи при рабочем и холостом ходах достигает соответственно 3,2 и 6 м/мин.
Рабочий инструмент. В качестве рабочего инструмента машин вращательного бурения применяют витые или сплошные буровые штанги и резцы. Буровая штанга состоит из хвостовика 1 (рис. IV.40, а), тела 2 буровой штанги, головки 3 с отверстием для закрепления резца 4 и крепежного штифта 5.
Съемные буровые резцы (рис. IV.40, б—г) состоят из корпуса 2, хвостовика 3 и перьев /, заканчивающихся режущими лезвиями. Буровые резцы двух основных типов: РУ (рис. IV.40, в) и РП (рис. IV.4), г) соответственно для бурения по углю и породе армируют пластинками 4 из твердого сплава ВК-6, ВК-8или ВК-8В.
МАШИНЫ УДАРНО-ВРАЩАТЕЛЬНОГО И ВРАЩАТЕЛЬНО-УДАРНОГО БУРЕНИЯ
Машины ударно-вращательного и вращательно-ударного бурения предназначены для бурения шпуров и скважин в породах средней крепости и крепких. Бурение этими машинами основано на комбинированном способе разрушения породы, объединяющем основные свойства ударного и вращательного воздействия на породу. При этом внедрение бурового инструмента в породу происходит в основном под действием удара, а лучшему скалыванию или срезанию породы способствует значительный крутящий момент, непрерывно прикладываемый к буровому инструменту мощным вращателем. Благодаря этому появляется возможность значительно уменьшить усилие подачи по сравнению с вращательным режимом бурения, что уменьшает истирание бурового инструмента при одновременном увеличении скорости бурения по сравнению с ударно-поворотным бурением. В зависимости от крепости породы основной объем разрушения может происходить как под действием удара, так и благодаря вращению инструмента. Соответственно преобладанию затрат энергии на основное разрушение и принято различать ударно-вращательное и вращательно-ударное бурение.
Машины вращательно-ударного и ударно-вращательного бурения состоят из независимо работающих ударного и вращатель


В большинстве ударно-вращательных и вращательно-ударных буровых машин ударные механизмы используют пневматическую энергию, а вращательные и подающие–пневматическую, электрическую или гидравлическую. Основными преимуществами ударно-вращательных буровых машин являются сохранение энергии удара на буровой коронке независимо от глубины скважины и возможность приложения к буровому инструменту большого крутящего момента. Машины вращательно-ударного действия создают буровому инструменту высокий крутящий момент, однако поворот бура у них не согласован с движением поршня-ударника. Поэтому машины ударно-вращательного действия обычно применяют для бурения глубоких скважин, а машины вращательно-ударного действия – для бурения неглубоких эксплуатационных скважин или шпуров.
Машины ударно-вращательного бурения. При ударно-вращательном бурении буровой машиной является погружной ппевмо-ударник, которому через штанги передаются вращение и подача м на забой от установленных вне скважины вращателя и податчика. По ГОСТ 13879–73 погружные пневмоударники выпускают четырех основных типоразмеров соответственно для бурения скважин диаметром 105, 125, 160 и 200 мм с ударной мощностью не менее 2,2; 3,1; 4,3 и 5,8 кВт при давлении сжатого воздуха 0,5 МПа.
Первые два типоразмера пневмоударников рассчитаны на бурение пород с коэффициентом крепости f = 6÷20, а другие два – с коэффициентом крепости f = 12÷20 при расходе воздуха на 1 кВт не более 2,3 м3/мин. Частота ударов в минуту составляет 1700—2500.
Рассмотрим конструкцию и принцип работы машины ударно-вращательного действия на примере пневмоударника П1-75 (рис. 41, а). Он состоит из цилиндра 2, в котором перемещается поршень 3, передней головки 5, в которую вставляется буровая коронка 4, закрепляемая шпонкой 6, и задней головки 1. Воздухо-распределение в пневмоударниках осуществляется так же, как в перфораторах. В пневмоударнике П1-75 применено, например, самораспределение сжатого воздуха поршнем. При холостом ходе поршня 3 сжатый воздух поступает через заднюю головку и каналы 12 в переднюю полость 13 цилиндра. Из задней полости 7 цилиндра в это же время происходит выхлоп по проточке 11 и выхлопным отверстиям 10. При рабочем ходе поршня впуск сжатого воздуха в заднюю полость цилиндра происходит по каналам 9, в то время как из передней полости происходит выхлоп.
Продувка скважин осуществляется отработанным воздухом через продувочный канал 8.
В качестве бурового инструмента пневмоударников наибольшее распространение получили долотчатые, крестовые и трехлег* вийные буровые коронки с опережающим лезвием (рис. IV.41, б).
Машины вращательно-ударного бурения применяются в основном для бурения шпуров и скважин при проведении выработок большого сечения. Основной отличительной чертой этих машин является большой крутящий момент, развиваемый специальным вращателем, работающим независимо от ударного механизма, но смонтированным в одном корпусе с ним.
Комплект из бурильной машины и автоподатчика называют бурильными установками. Эти машины классифицируют на отдельные группы по следующим признакам:
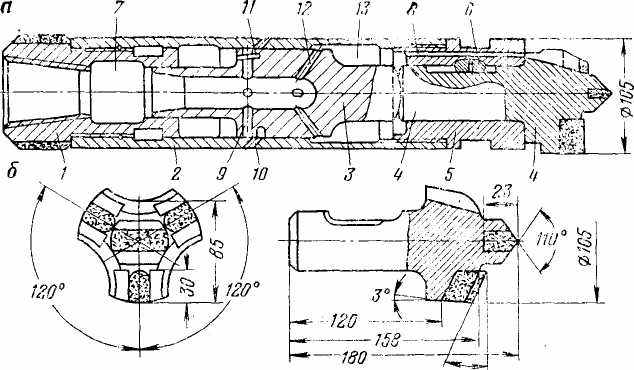
Рис. IV.4). Пневмоударник П1-75 (а) с трехлезвийной буропой коронкой (б)
по частоте ударов — с частотой ударов в минуту 5000—7000 и 2500—4000;
по энергии удара — с энергией до 50 Дж и 60—80 Дж;
по числу скоростей привода вращателя — одно-, двух- и трех-скоростные;
по конструкции привода подачи — с автоматическим регулированием осевого усилия и без регулирования последнего.
Остальные параметры вращательно-ударных бурильных машин обычно следующие: давление сжатого воздуха 0,4—0,6 МПа, расход воздуха 10—14 м3/мин, диаметр коронки 42 мм, длина шпура до 4 м; способ очистки и расход промывочной жидкости практически одинаковы во всех конструкциях.
Вращательно-ударные машины состоят из следующих основных частей: бурильной головки, механизма подачи, штанги и буровой коронки. Например, бурильная машина БУ1 (рис. IV.42) состоит из пневматического двигателя /, редуктора подачи 2, клапана 3, крана концевого выключателя 4, бурильной головки 5, подвижного люнета 6, распорного домкрата 7, буровой штанги 8 и буровой коронки 9. Бурильная головка 5 перемещается с помощью механизма подачи по направляющей балке и производит бурение шпура на заданную глубину, после чего автоматическим или ручным включением механизма подачи на обратный ход отводится в начальное положение.
Вода к бурильному инструменту подводится через муфту боковой промывки.
Подвижной люнет 6 служит для поддержания прямолинейности штанги 8 в процессе бурения шпура.
Масса бурильных установок вместе с ходовым колесным или гусеничным оборудованием составляет 2—3 т.
В качестве рабочего инструмента применяют коронки, аналогичные коронкам для перфоратора и имеющие несимметричную заточку. При этом для бурения пород мягких и ниже средней крепости передний угол у заточки лезвия принимается равным 10—15°, а для крепких пород — 20—25°. Угол заточки задней грани р = 45 ч-60°.
Основными параметрами бурильных машин этой группы являются энергия единичного удара, число ударов за один оборот бурового инструмента, частота вращения и величина усилия подачи бурового инструмента.
При этом особое значение имеет правильный выбор энергии единичного удара, которая должна быть достаточна для обеспечения объемного разрушения породы. Так, для пород с коэффициентом крепости/= 10-г-12и/= 14-1-16 энергию единичного удара рекомендуется принимать равной соответственно 40—50 и 70—80 Дж. При увеличении коэффициента крепости породы более 12 рекомендуется увеличивать частоту ударов на один оборот бурового инструмента с 20 до 30, а величину усилия подачи уменьшать с 12 до 8 кН.
П
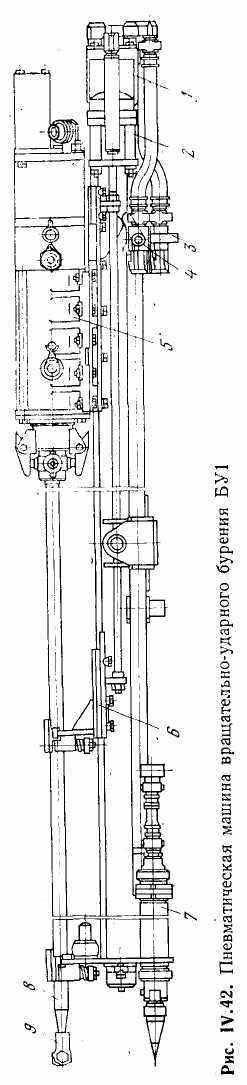
Теория работы и основы расчета ударного механизма в машинах ударно-вращательного и вращательно-ударного бурения аналогичны описанным для перфораторного (ударно-поворотного) бурения (см. § 2 гл. 3).
ЭКСПЛУАТАЦИЯ БУРИЛЬНЫХ МАШИН
Высокопроизводительная безаварийная работа бурильных машин может быть достигнута лишь при наиболее полном соответствии горным условиям конструктивного типа, вспомогательного оборудования, технической исправности оборудования, соблюдении правил эксплуатации и техники безопасности.
Буровая машина обслуживается двумя рабочими. После того как она установлена в выработке под заданным углом наклона и надежно укреплена распорными домкратами, приступают к ее опробованию вхолостую. Перед этим проверяют правильность установки пылеуловителя и оросительного устройства. Перед бурением необходимо убедиться, что все вращающиеся части машины надежно закрыты ограждениями.
При забуривании следует избегать слишком больших подач и частоты вращения бурового инструмента во избежание искривления скважины. Особое внимание следует уделять правильности направления бурового инструмента. По мере углубления шпура или скважины можно увеличивать скорость подачи и осевое усилие, выбирая при этом оптимальный режим бурения.
Для соблюдения прямолинейности скважины необходимо: производить бурение исправным инструментом; следить за качественной заточкой резцов; правильно устанавливать и надежно закреплять машину; ставить вслед за коронкой опорный фонарь. Разность диаметров коронки и опорного фонаря не должна превышать 3—4 мм.
В случае обрыва буровой штанги или ее зависания в скважине работа должна производиться с соблюдением особых мер предосторожности. Во избежание несчастных случаев при внезапном обрыве штанги не следует находиться против устья скважины.
Чтобы исключить зажим бурового става в скважине, не следует прерывать бурение. При бурении скважин в пластах, опасных по внезапным выбросам угля или газа, применяют специальные меры предосторожности.
При работе с перфораторами следует особое внимание уделять борьбе с пылью, образующейся при бурении. Подавление пыли наиболее успешно осуществляется промывкой шпура водой или смачивающими растворами, а также отсасыванием пыли. Питание промывочной жидкостью наиболее удобно производить от шахтной водопроводной сети.
Работа перфораторов сопровождается значительными шумом и вибрацией. Для борьбы с шумом нужно использовать индивидуальные средства защиты типа наушников, а для уменьшения воздействия вибрации — оборудовать перфораторы виброгася-щими рукоятками.
Высокопроизводительная безаварийная работа бурильных машин, уменьшение износа и повышение работоспособности деталей в значительной мере зависят от ухода за ними, строгого соблюдения правил эксплуатации и своевременного осмотра, промывки, ремонта и смазки.
ОТБОЙНЫЕ МОЛОТКИ
§ 1. НАЗНАЧЕНИЕ, ОБЛАСТЬ ПРИМЕНЕНИЯ, УСТРОЙСТВО
Пневматический отбойный молоток представляет собой ручной инструмент ударного действия, который используется при работе как клин и рычаг. Его исполнительный орган (пика) внедряется в уголь (или породу), отделяя его от массива.
О
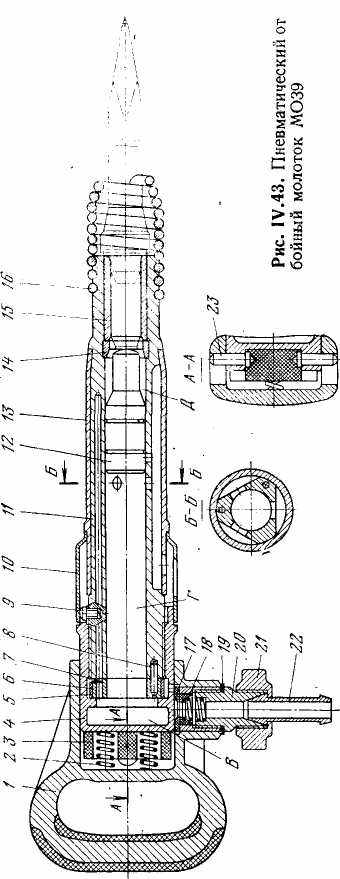
Пневматические отбойные молотки изготовляются Томским электромеханическим заводом им. В. В. Вахрушева. Их техническая характеристика дана в табл. IV.9. Рабочее давление воздуха в молотках принято 0,5 МПа.
Проведены большие работы по типизации и унификации основных узлов и деталей пневматических отбойных молотков. Исключение составляют только стволы и ударники, имеющие разные размеры, однако их диаметры тоже унифицированы. Дальнейшее совершенствование отбойных молотков ведется в направлении повышения их производительности, экономичности, надежности в работе, а также улучшения условии труда рабочего при их применении: уменьшения отдачи, вибрации, шума, пылеобразования.
Электрические отбойные молотки в подземных условиях не получили применения из-за меньшей производительности, надежности и большей массы, чем у пневматических отбойных молотков. Некоторое применение они имеют на поверхности шахт при строительных и других работах.
Пневматический отбойный молоток МО39 (рис. IV.43) состоит из исполнительного органа – пики, удерживающей ее пружины 16, ствола 11с промежуточным звеном 4, внутри которых расположен воздухораспределительный и ударный механизмы, рукояти / с виброгасящнм устройством.
Сжатый воздух подводится к молотку но гибкому рукаву, который присоединяется с помощью ниппеля 22, штуцера 20 и гайки 21. Для предотвращения самоотвертывания штуцера устанавливается пружинная шайба 19. Рукав имеет диаметр 16 мм и длину не более 12 м.
Ударный механизм состоит из ствола с запрессованными в него буксой 15 и перемычкой ствола 14 и ударника 12. Ударный механизм предназначен для преобразования энергии сжатого воздуха в механическую работу движущегося ударника, который наносит удары по хвостовику пики.
Воздухораспределительный механизм состоит из клапанной коробки 6 с кольцом 5 и двумя клапанами 7, выполненными в виде плоских сегментов. Воздухораспределительный механизм предназначен для подачи сжатого воздуха в цилиндр ствола, т. е. в камеру Г прямого хода ударника и в камеру Д обратного хода, а также для выпуска отработанного воздуха в атмосферу.
Для подвода сжатого воздуха к ударнику в стволе молотка просверлены продольные каналы, а для отвода отработанного воздуха используются каналы, которые образованы поверхностью ствола 11 и поверхностью стальной рубашки 13. На последней укреплено стопорное кольцо 10, которое удерживает от выпадания стопор 9 и используется для отвода воздуха из выхлопного канала. Стопор 0 предотвращает самоотвертывание резьбового ствола 11 и промежуточного звена 4. Два штифта 8 предотвращают самопроизвольное смещение клапанной коробки 6 относительно ствола 11.
Пусковое устройство выполнено в виде скользящего по промежуточному звену 4 вкладыша 17 из фторопласта. Этот вкладыш прижимается к промежуточному звену усилием пружины и сжатым воздухом. При нажатии на рукоятку 1 отверстие во вкладыше совпадает с отверстием в промежуточном звене и сжатый воздух поступает в воздухораспределительное устройство молотка, при этом пружины 2 сжаты.
При снятии усилия с рукоятки 1 пружины 2 разжимаются и отверстие в промежуточном звене 4 перекрывается вкладышем 17 – молоток включен. Для предотвращения утечек воздуха в пусковом устройстве установлена манжета 18 из маслостойкой резины.
Для снижения вибрации молотка и уменьшения вредного влияния отдачи на организм рабочего применена дополнительная камера В, которая расположена в конце обратного (холостого) хода ударника и позволяет значительно улучшить рабочий цикл и снизить отдачу молотка. Кроме того, применен виброизолятор 3, отделяющий корпус молотка от рукоятки. Соединение рукоятки и промежуточного звена осуществлено двумя фиксаторами 23, которые постоянно удерживаются в разжатом состоянии виброизолятором 3. При включении и выключении молотка фиксаторы перемещаются в пазах, имеющихся в рукоятке.
Принцип действия отбойного молотка заключается в следующем (рис. IV.44). К началу холостого хода ударник и клапан находятся в нижнем положении. Сжатый воздух под давлением р0 по каналам над клапаном и продольному каналу а поступает в камеру Б под ударник. В результате этого ударник перемещается вверх, вытесняя воздух из верхней полости А в атмосферу через выхлопные отверстия Ь1 и Ь.г. Когда ударник перекроет эти отверстия, воздух в камере Л начнет сжиматься и при этом будет оказывать давление на клапан снизу. При дальнейшем движении ударник откроет выхлопное отверстие Ь., вследствие чего давление в камере Б резко упадет и клапан переместится вверх, открыв путь сжатому воздуху в камеру А, — начнется рабочий ход ударника.
К началу рабочего хода ударник и клапан находятся в верхнем положении. Сжатый воздух по каналам под золотником поступает в камеру А над ударником. Под давлением сжатого воздуха и собственного веса ударник перемещается вниз, вытесняя наружу воздух из камеры Б через выхлопные отверстия Ьх и Ьг. Когда ударник перекроет эти отверстия, воздух в камере Б начнет сжиматься, увеличивая через канал а давление на клапан сверху. Далее ударник откроет своей задней кромкой выхлопное отверстие Ьъ давление в камере А и под золотником резко упадет — золотник переместится вниз, ударник нанесет удар по хвостовику пики, после чего начнется холостой ход ударника.
Для предохранения ствола молотка от разрыва при холостых ходах ударника в молотках типа МО предусмотрен воздушный буфер.
§
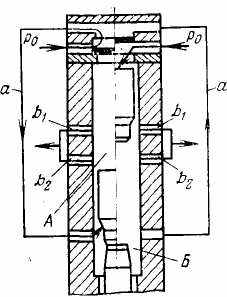
К основным параметрам отбойного молотка относят: энергию и мощность удара, частоту ударов, расход сжатого воздуха и производительность.
§ 3. ЭКСПЛУАТАЦИЯ ОТБОЙНЫХ МОЛОТКОВ
О
Рис. IV.44. Схема работы отбойного молотка
тбойные молотки, поступившие с завода, следует разобрать, очистить от смазки и пыли, промыть в керосине, собрать, смазать и опробовать в работе. Перед началом работы в забое необходимо убедиться, что забой надежно закреплен и находится в нормальном состоянии, что давление сжатого воздуха в пределах нормы и молоток исправен: ударник перемещается в стволе без заеданий, промежуточное ЗЕено надежно закреплено стопором, хвостовик пики и ее острие не повреждены.
Затем необходимо вставить хвостовик пики в буксу молотка и закрепить ее, навинтив и застопорив пружину или концевой колпак на стволе.
Далее следует смазать молоток, для чего нужно налить масло в штуцер и, нажав на рукоятку, подать масло в молоток. Затем необходимо тщательно продуть рукав сжатым воздухом и, присоединив его к молотку, опробовать молоток. Во время работы необходимо следить за исправностью молотка и рукава, не допуская перегиба последнего под острым углом. Два-три раза за смену следует смазывать молоток, заливая 25—30 г индустриального масла 20А с добавкой 25–40% керосина.
Профилактический осмотр и ремонт молотков рекомендуется производить еженедельно с разборкой, промывкой и смазкой деталей. Ремонт молотков производится на поверхности шахт в специально оборудованных мастерских. Разборка молотка в забое недопустима.
СРЕДСТВА ГИДРОМЕХАНИЗАЦИИ ГОРНЫХ РАБОТ