Бурильные машины § классификация бурильных машин и способов бурения
Вид материала | Документы |
- 1 Эволюционная классификация ЭВМ, 555.23kb.
- 1. Общая классификация строительных машин. Производительность машины и ее категория, 651.54kb.
- Комплекс машин для заготовки прессованного сена. Марки машин и их технические характеристики, 8.88kb.
- Программа вступительного экзамена в аспирантуру по специальной дисциплине 05. 02., 266.3kb.
- Ательный материал «Электронный курсовой проект «Проектирование машин постоянного тока», 47.15kb.
- Краткое содержание: Прямая задача динамики машин. Понятие о динамической модели машины, 252.59kb.
- Симанкин Федор Аркадьевич, к т. н., доцент Вид учебной работы Аудиторные занятия самостоятельная, 155.96kb.
- 1. Классификация швейных машин Начертить кинематическую схему механизма иглы машины, 47.12kb.
- Машины с электрическим приводом, 61.22kb.
- Программа дисциплины по кафедре "Cтроительные и дорожные машины " технические основы, 254.17kb.
1 2
ОБЩИЕ СВЕДЕНИЯ
Способ механизации горных работ, при котором все или основная часть операций технологического процесса осуществляется за счет энергии движущегося потока воды, называется гидромеханизацией.

При гидравлической добыче применяются гидравлический, механогидравлический и взрывогидравлический способы разрушения полезного ископаемого.
При гидравлическом способе вода высоконапорным насосом по водоводу подается к гидромонитору, из насадки которого выбрасывается струя воды под большим давлением (до 16 МПа), которая разрушает некрепкий уголь и некрепкие породы.
Размытые уголь или порода образуют вместе с водой гидросмесь, которая транспортируется самотеком по металлическим желобам (или по почве) с уклоном не менее 0,05 к камере гидроподъема (думпфу). При этом соотношение твердой. (Т) и жидкой (Ж) фаз по объему, называемое консистенцией гидросмеси, составляет обычно 1/4–1/10.
Гидроподъем угля из неглубоких шахт производится углесосами, а из глубоких (более 400 м) –эрлифтами. Затем по трубопроводам гидросмесь поступает на обогатительную фабрику. Отработанная вода из обогатительной фабрики поступает в систему отстойников, а из них – в резервуар осветленной технической воды. Благодаря этому вода используется многократна в замкнутом цикле. Потери воды периодически компенсируются из шахтного водопровода или путем естественного притока шахтных вод.
На открытых горных работах гидросмесь из зумпфа перекачивается по трубам грунтонасосами (землесосами) к месту укладки – гидроотвалу.
При отстаивании в гидроотвале вода отделяется от породы, осветляется и подается к насосной станции для повторного использования.
Горная порода разрушается потоком воды, притекающим к всасывающей трубе, и при разработке забоя плавучим землесосным снарядом (землесосом).
Преимущества гидромеханизации, благодаря которым она получила распространение в горном деле при подземной и открытой разработках полезных ископаемых: высокая производительность труда; возможность попутного обогащения полезного ископаемого; относительная простота и малооперационность технологического процесса; отсутствие пылеобразования; низкаяс стоимость и малые размеры оборудования.
Механогидравлический способ предусматривает разрушение угля или некрепкой породы механическим способом (исполнительными органами механогидравлических комбайнов), а смыв разрушенной горной массы из забоя — водой, подводимой к комбайну при давлении около 5 МПа. Механогидравлический способ получил распространение при выемке крепких углей, когда использовать гидромониторы нецелесообразно. К этому способу можно отнести выемку пород на открытых работах землесосными снарядами, снабженными рыхлителями.
Взрывогидравлический способ предусматривает разрушение полезного ископаемого или породы с применением буровзрывных работ, а транспортирование разрушенной горной массы — смывом водой под давлением.
Этот способ в настоящее время не получил широкого распространения и применяется иногда на подземных рудниках.
ГИДРОМОНИТОРЫ
Гидромониторы, представляющие собой устройства для формирования напорной струи и управления ее полетом с целью разрушения и смыва горных пород, классифицируют по следующим признакам:
по области применения – для подземных и открытых горных работ;
по способу управления – с ручным, дистанционным и программным управлением;
по способу перемещения – несамоходные (передвигаемые на салазках вручную, посредством гидропередвижчиков, лебедками, тракторами и другими способами) и самоходные, имеющие гусеничные или шагающие органы перемещения.
Гидромониторные струи разделяют на низконапорные (до 1 МПа), средненапорные (от 1 до 5 МПа), высоконапорные (от 5 до 50 МПа) и сверхвысоконапорные (более 50 МПа).
На открытых горных работах промышленное применение получили средненапорные струи с давлением 1,5–3 МПа, а на гидрошахтах – высоконапорные струи с давлением 12–16 МПа.
Для формирования струи, выходящей из ствола гидромонитора, служат насадки, представляющие собой фасонные трубки из стального литья со шлифованной внутренней поверхностью в форме конуса, переходящего плавно в цилиндр.
К основным техническим характеристикам гидромониторов можно отнести: рабочее давление воды (МПа), расход воды (м3/с), диаметр канала проточной части гидромонитора (мм), диаметр насадок (мм), угол поворота ствола (градус), вид управления, размеры и масса.
Гидромониторы ГМДЦ-4 (рис. 4.1) предназначены для гидроотбойки угля в очистных и подготовительных забоях при разработке пластов мощностью более 0,8 м с углами падения более 6°.
Основанием гидромонитора являются салазки 12, на которых закреплена труба 22 напорного водовода диаметром 100 мм для подвода к стволу гидромонитора воды под давлением. На вертикальном участке 11 подводящей трубы установлена головка с крестовиной 13, которая дает возможность поворачиваться стволу 4 в горизонтальной плоскости. Поворотная головка имеет две полые цапфы 3, вокруг которых могут вращаться бобышки 14 и осуществлять поворот ствола 4 в вертикальной плоскости. К поворотным бобышкам 14 прикреплены два обводных канала 23 для подвода воды к стволу 4 гидромонитора. В стволе имеется гидравлический сотовый успокоитель 5, который разделяет с помощью продольных ребер поток воды на несколько параллельных потоков меньшего сечения. Это способствует формированию компактной водяной струи. Насадка 7 крепится к конусной части ствола 6 накидной гайкой 8.
Ствол гидромонитора с помощью гидродомкрата 15 и зубчатого сектора 10 может поворачиваться в горизонтальной плоскости на угол 90°, а при перестановке фиксирующего пальца — до 210°. Гидродомкратом 9 ствол может поворачиваться вверх на 80° и вниз на 20°.
Маслостанция для дистанционного управления состоит из насоса 2 с приводом от гидравлической турбины 17, масляного бака 19, фильтра 20 и контрольно-измерительной аппаратуры. Турбина приводится в действие водой, которая подается по напорному рукаву 21 от гидромонитора. Рукава 18 (напорный и сливной) соединяют маслостанцию с-пультом дистанционного управления 1, закрепленным на винтовой стойке в 8—10 м от забоя. Рукава 16 соединяют маслостанцию с гидродомкратами 9 и 15 поворота ствола гидромонитора.
Гидромонитор ГПД12-5 работает в тех же условиях, что и гидромонитор ГМДЦ-4, но рабочее давление воды у него ниже (до 12 МПа).
Гидромонитор 12ГД-2 имеет большие диаметры насадок, больший расход воды и соответственно большие габариты и массу комплекта.
Создан самоходный (на гусеничном ходу) гидромонитор 12ГП-2, рассчитанный на давление воды до 12 МПа. Управление гидромонитором полуавтоматическое с дистанционным изменением программы. Скорость передвижения гидромонитора До 2,5 м/мин. Масса —3200 кг.
Готовится к производству гидромонитор 16ГД с рабочим давлением воды до 16 МПа и с дистанционным управлением. Диаметры насадок составляют 22; 25 и 28 мм. Общая масса — 550 кг.
Производительность гидромониторов для гидрошахт составляет 30—60 т/ч для углей средней крепости и 50—100 т/ч — для некрепких углей.
В гидромониторах, применяющихся на открытых горных работах, используют насадки диаметром 52—200 мм.
При работе на гидромониторах необходимо соблюдать следующие правила безопасности:
проводить работы по гидроотбойке с разрешения горного мастера или другого лица технического надзора, имеющего на это право;
при давлении воды свыше 3 МПа применять гидромониторы только с дистанционным управлением;
на открытых горных работах не допускается установка гидромониторов вдоль откосов и неукрепленных вертикальных стенок в пределах призмы обрушения породы;
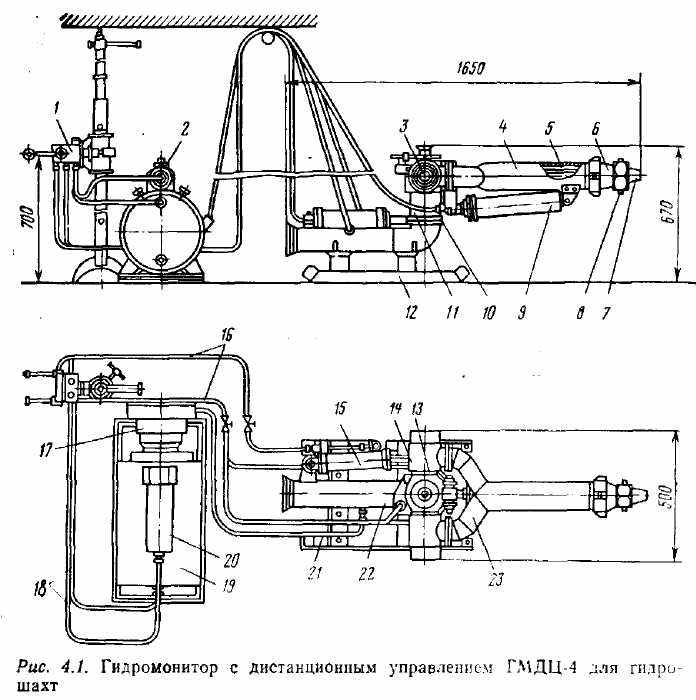
при подземных горных работах гидромониторщику следует находиться в надежно закрепленном безопасном месте и работать только при исправном оборудовании и хорошем освещении;
не допускать одновременного двустороннего размыва заходки встречными струями двух гидромониторов, установленных в соседних забоях;
для исключения несчастных случаев, вызванных разрывами гидромониторов, запорной арматуры и трубопроводов, не допускается превышение давления, установленного инструкцией по эксплуатации;
запрещается работать на гидромониторе с неисправным манометром или без него;
при отсутствии воды в напорном трубопроводе необходимо плотно закрыть задвижку, выяснить причину отсутствия воды и после устранения неполадок или отказов получить разрешение на дальнейшее производство работ;
ремонт и подготовку высоконапорного водовода к работе производить при закрытой задвижке;
по окончании работы выключать все оборудование.
МЕХАНОГИДРАВЛИЧЕСКИЕ МАШИНЫ
На гидрошахтах для проведения подготовительных выработок, осуществления нарезных и очистных работ короткими забоями на пластах средней мощности с углами падения до 15° применяется комбайн со стреловидным исполнительным органом К56МГ с гидросмывом разрушенной горной массы.
Производительность комбайна – 2,25 т/мин, расход воды – 100 –150 м3/ч, давление воды – 1–1,15 МПа. Комбайн проводит выработки высотой 1,9–2,5 м, шириной 2–3,4 м; мощность разрабатываемых пластов – 1,8–2,5 м; масса комбайна – 12,7 т.
Комбайн может работать по углям с сопротивляемостью резанию до 250 кН/м и присекать породы с коэффициентом крепости f ≤ 4 до 30% от площади забоя и абразивностью до 5 мг. Размеры выработки вчерне – 4–8,5 м2.
Для дистанционного управления гусеничным ходом комбайна, его исполнительным органом и вспомогательными механизмами применяется аппаратура дистанционного управления ПДУ, изготавливаемая заводом «Гидромаш» в г. Новокузнецке Применение переносного пульта для дистанционного управления комбайном позволяет находиться машинисту в безопасном закрепленном пространстве на расстоянии 8—12 м от комбайна (в пределах видимости).
Копейским машиностроительным заводом им. С. М. Кирова выпускается для гидрошахт комбайн «Урал 38», который предназначен для проведения нарезных выработок и очистных работ.
Вода для гидросмыва отбитого угля и гидротранспортирования его самотеком по почве пласта подводится к коронке стрелы под давлением до 3 МПа.
Производительность комбайна до 2 т/мин. Комбайн может проводить выработки с площадью сечения от 1,6 до 5,4 м2 по углю с сопротивляемостью резанию до 200 кН/м с углом наклона до 15°. Расход воды на гидротранспортирование – 150–300 м3/ч. Масса комбайна – 9,8 т. Комбайн снабжен пультом дистанционного управления.
Для подводной разработки пород гидравлическим способом применяются землесосные снаряды — плавучие землесосно-транспортирующие машины непрерывного действия.
Плавучий землесосный снаряд представляет собой судно с надстройкой (рис. 4.3), имеющее: рыхлитель 1, раму 2 рыхлителя, канат 3 подвески рамы рыхлителя с подъемной лебедкой 14, стрелу 4 с подвеской 5, двигатель 6 рыхлителя, всасывающий патрубок 7, грунтовый насос 8, двигатель 9 грунтового насоса, напорный пульпопровод 10.
Силовое оборудование землесосных снарядов может быть электрическим и дизельным.
По производительности Q (м3/ч) земснаряды делятся на три группы: малой мощности Q ≤ 100 м3/ч, средней Q = 100÷500 м3/ч и большой Q≥500 м3/ч.
Земснаряды, применяемые на открытых горных работах, имеют обычно электропривод.
Технические данные плавучих землесосных снарядов, выпускаемых отечественной промышленностью, приведены ниже.
Грунтонасосами породы разрушаются за счет энергии потока воды, засасываемой насосом. Необходимая скорость транспортирования для песка составляет 0,35—0,7 м/с, для гравия – более 2,5 м/с.
Для разработки пород с каменистыми включениями используют фрезерные рыхлители.
Для удержания земснаряда на рабочем месте и осуществления его рабочих перемещений служат свайный аппарат 11 с лебедками 12 лебедки поворота 13 и канаты 15 с якорями, при помощи которых производятся веерообразные перемещения всасывающего устройства и поступательное движение земснаряда. Лебедки поворота одновременно служат для создания давления на фрезерном рыхлителе.
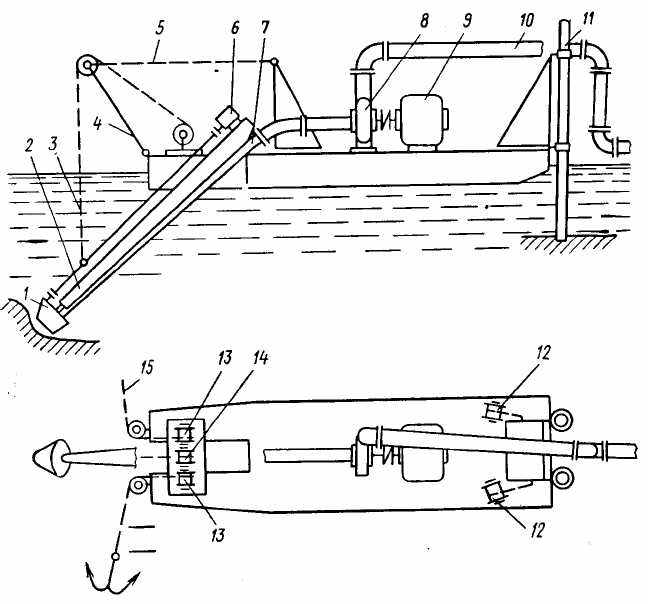
Рис. 4.3. Схема плавучего землесосного снаряда
ЭКСКАВАТОРЫ
Для погрузки породы в камерах мощных пологих месторождений, а также при проведении выработок большого сечения успешно применяют одноковшовые экскаваторы типа прямой механической лопаты. При этом в ряде случаев для работы в подземных условиях используют обычные маломощные универсальные полноповоротные строительные экскаваторы типов Э652, Э801 с ковшом емкостью 0,65—1,25 м3, комплектуемые сменным оборудованием крана, прямой и обратной лопат. Основными недостатками строительных экскаваторов являются большие габариты и неприспособленность к эксплуатации в подземных условиях, не могут перемещаться по подземным выработкам, не разбираются на транспортабельные блоки, их монтаж и демонтаж в подземных условиях чрезвычайно затруднены.
К подземным экскаваторам предъявляется ряд дополнительных требований: обеспечение высокой производительности (до 500 т/смену) при небольших габаритах, позволяющих не только работать в небольших камерах, но и транспортировать машину по горным выработкам, высокая маневренность, способность грузить негабаритные куски и зачищать почву, обеспечивать безопасность и комфортность работы машиниста.
Специализированными подземными экскаваторами являются Э6514, Э7515, ЭП1 и ЭПГ1 и другие, технические характеристики которых приведены в табл. VI. 1.
Экскаватор ЭП1 предназначен для очистных забоев подземных рудников. С его помощью можно грузить горную массу кусковатостью до 800 мм в камерах высотой не менее 6 и шириной не менее 10 м.
Рабочее оборудование экскаватора ЭП1 (рис. VI. 1) помимо сварного ковша 4 емкостью 1 м3, рукояти 3 с жестким напором и стрелы 1, состоящей из двух продольно сваренных из листового проката балок коробчатого сечения, включает в себя головные и стрелковые блоки 2 и 5, тяговые цени 6 напора и механизм 8 открывания днища 7 ковша. Нижний конец стрелы шарнирно крепится к поворотной платформе, а верхний – поддерживается стреловыми канатами 9, проходящими через блоки 5. Подъемное усилие на ковше создается с помощью подъемных канатов 10, переходящих через головные блоки 2. Напорное усилие на ковше создается механизмом напора, привод которого расположен на поворотной платформе, а исполнительный механизм – на стреле. Передача крутящего момента на исполнительный механизм осуществляется тяговой цепью 6. В качестве привода механизма открывания днища ковша служит пневмоцилиндр. Закрывание ковша происходит автоматически при его опускании.
Конструктивными особенностями экскаватора ЭП1 являются: возможность его разборки на отдельные транспортабельные узлы; уменьшенные габариты по сравнению с другими экскаваторами данного типа (емкостью ковша 1 м3); защита бронированными листами рабочего места машиниста и задней части машины; усиленное освещение призабойного пространства; применение легированных сталей для изготовления наиболее нагруженных узлов и деталей и т. д.
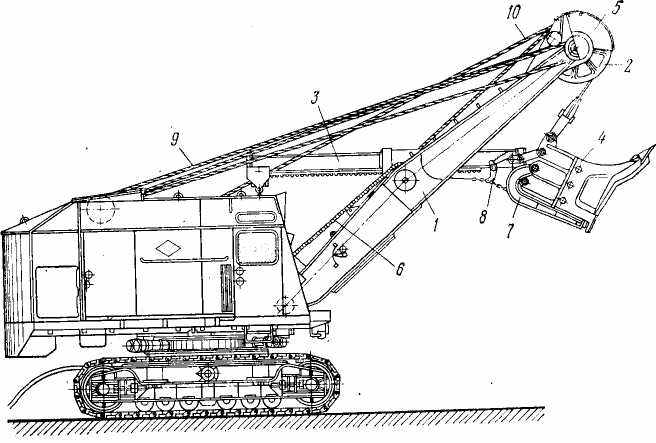
Рис. VI. 1. Подземный экскаватор ЭП1
Производительностью экскаватора называют объем горной массы, отгруженной за единицу времени. Различают теоретическую, техническую и эксплуатационную производительности экскаваторов.
Теоретическая производительность Q (м3/ч) определяется по формуле
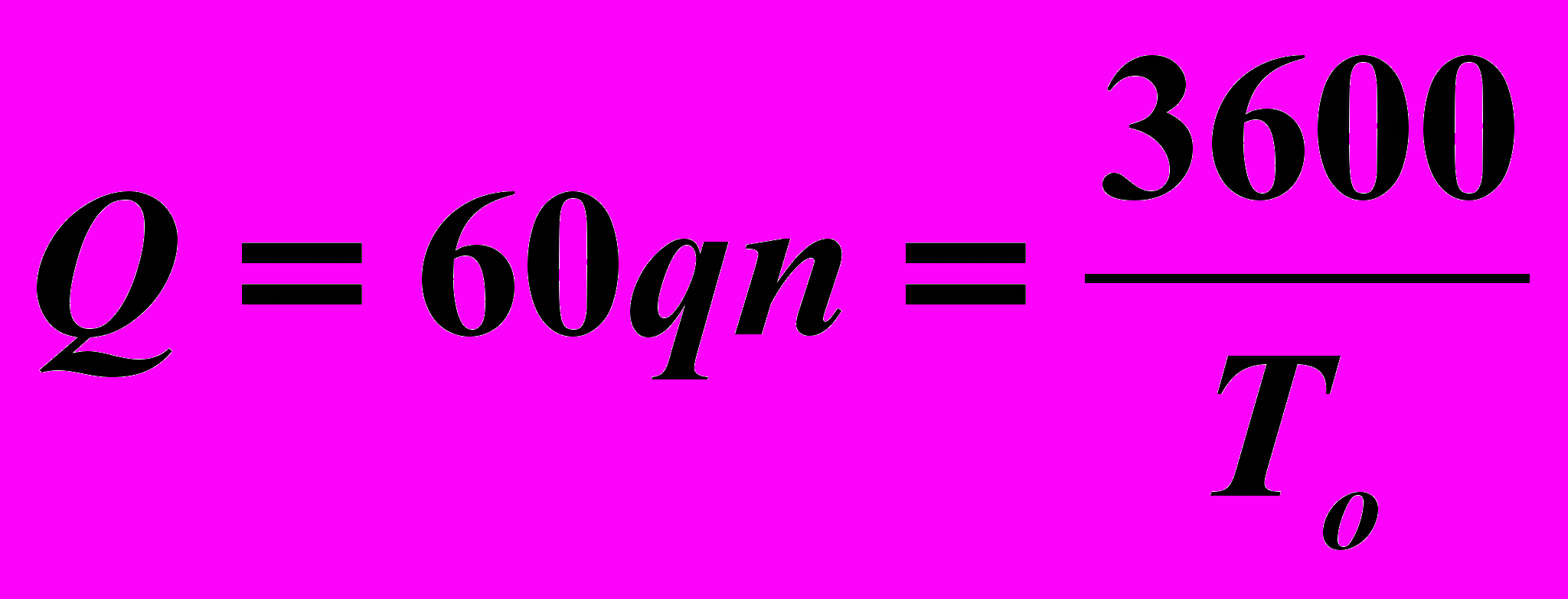
где q — емкость ковша, м3; п — число циклов работы экскаватора в минуту, 1/мин; То — теоретическая длительность цикла, с.
Техническая производительность Qтех (м3/ч) определяется с учетом свойств разрабатываемых пород и потерь времени на перемещение экскаватора из одного забоя в другой:
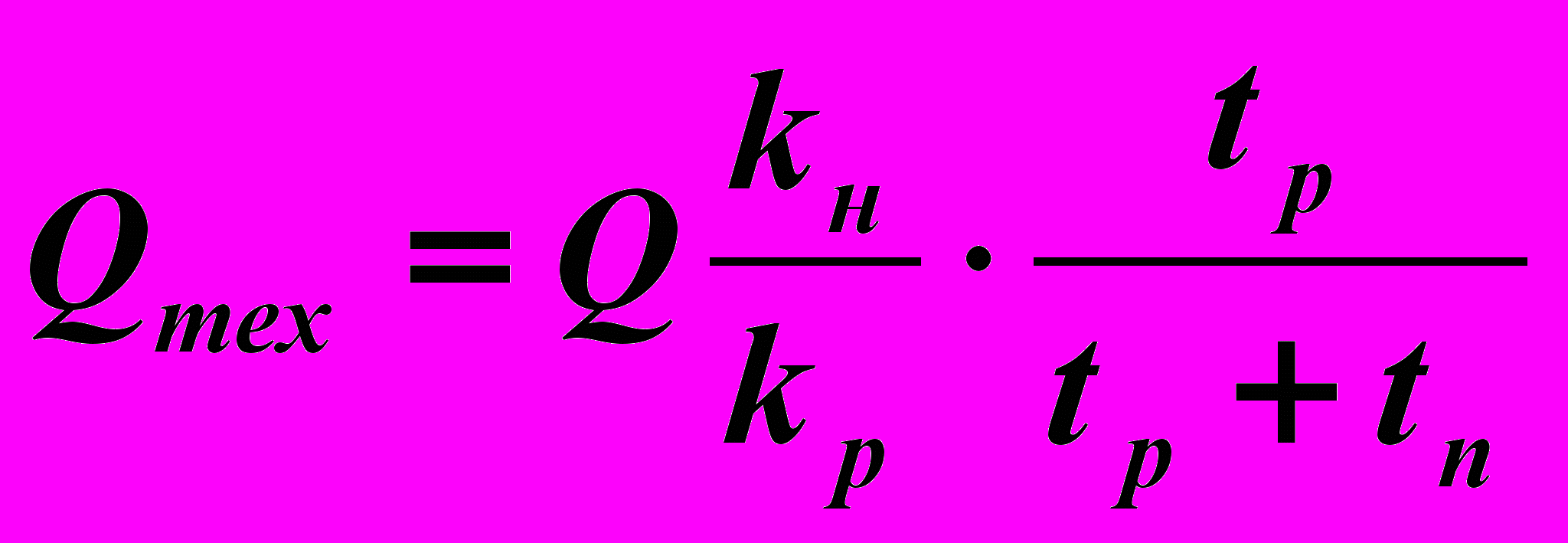
где kн = 0,8÷1,1 — коэффициент наполнения ковша; kр = 1,1÷1,5 — коэффициент разрыхления породы в ковше экскаватора; tр — время работы экскаватора из одного положения, с; tп — время на одну передвижку экскаватора, м.
Эксплуатационная производительность Qэ (м3/ч) составляет
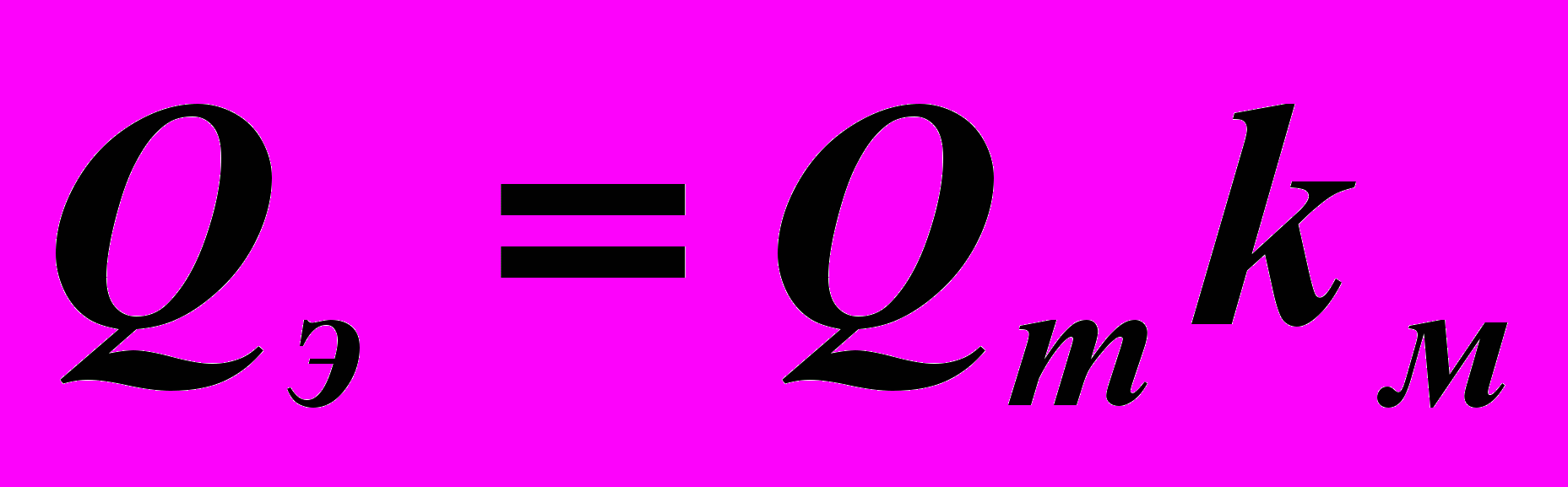
где kм – коэффициент машинного времени.
Повышения производительности подземных экскаваторов можно добиться сокращением длительности цикла работы благодаря более рациональной расстановке оборудования, уменьшением угла поворота и совмещением отдельных операций, а также лучшим дроблением горной массы, при котором увеличивается коэффициент заполнения ковша и сокращается длительность цикла в связи с более быстрым его заполнением.
Не менее важным являются организация обслуживания и ремонта, высокая квалификация обслуживающего персонала и соблюдение правил эксплуатации и техники безопасности всеми рабочими, находящимися в забое при ведении работ. В частности, во время работы, экскаватор должен быть заземлен и гусеницы его заторможены. При остановке экскаватора или ведении каких-либо работ на рабочем оборудовании ковш должен быть опущен на породу. При перемещении экскаватора путь для его движения должен быть спланирован, а ковш опорожнен и подтянут к стреле.
БУЛЬДОЗЕРЫ
Бульдозерами называют горные машины прерывного действия, предназначенные для послойного срезания, соскребания и продольного перемещения толканием-волочением насыпного груза на небольшие (обычно до 100 м) расстояния.
Бульдозер состоит из ходовой тележки 1 (рис. VI.2) с приводом 6, отвала 5, которым перемещается груз толканием-волочением, оборудования 2 для управления отвалом, двух толкающих брусов 3 с подкосами 4 и приводной лебедки 7.
В горной промышленности бульдозеры особенно широко применяют на открытых разработках и на поверхности шахт, однако в последние годы они находят все большее применение и на подземных работах для зачистки и выравнивания почвы забоя, концентрации горной массы в месте погрузки ее экскаватором, отодвигания взорванной горной массы от забоя с целью подготовки забоя к бурению, перемещения бутов, транспортирования горной массы на расстояние до 40—50 м, устройства и содержания дорог при безрельсовом транспорте и на других работах.
Принцип работы бульдозера заключается в том, что, перемещаясь собственным ходом (аналогично гусеничным тракторам), бульдозер подходит к требуемому месту работы, опускает отвал на почву и, перемещаясь вперед (а иногда и назад), соскребает горную массу, располагающуюся перед отвалом в виде призмы волочения. Дальше бульдозер перемещает захваченную горную массу на некоторое расстояние толканием-волочением и затем разгружается, сталкивая ее с откоса, поднимая отвал или отходя назад. Затем бульдозер возвращается к месту заполнения отвала, и рабочий цикл повторяется.
К конструкции бульдозера, применяемого на подземных работах, по сравнению с общепринятыми для строительных работ предъявляются дополнительные требования, связанные со спецификой их эксплуатации. Так, при зачистке почвы выработки неровности скальной породы не могут быть срезаны ножом отвала. В связи с этим отвал подземного бульдозера, который не срезает грунт, а перемещает скальную породу толканием-волочением, должен иметь повышенную точность управления, чтобы обходить встречающиеся неровности и принудительно прижиматься к почве выработки. В связи с
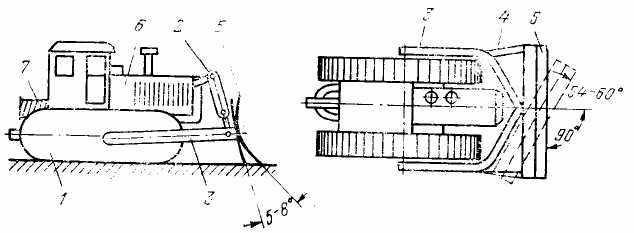
Рис. VI.2. Схема универсального поворотного бульдозера
необходимостью работы в тупиковых забоях и на отвалах, отвал подземного бульдозера должен быть выдвижным и двустороннего действия. Для перемещения породы насторону отвал должен иметь возможность поворачиваться в процессе движения в плане на 30—60°. Вся конструкция бульдозера и особенно отвала должна обладать повышенной прочностью, износостойкостью и проходимостью. В связи со стесненными условиями горных выработок бульдозер должен разбираться на транспортабельные узлы с учетом сборки в шахтных условиях.
С целью классификации подземные бульдозеры могут быть подразделены:
по способу управления отвалом — на канатные и гидравлические;
по возможности изменения угла установки отвала в плане (5—6°) — с поворотным и неповоротным отвалом;
по возможности изменения угла резания (5—6°) — с постоянным и переменным углом установки отвала;
по возможности перекоса отвала (3—6°) — допускающие перекос в вертикальной плоскости и не допускающие;
по типу ходового оборудования — гусеничные и колесные;
по роду потребляемой энергии — с двигателями внутреннего сгорания, электро- и пневмоприводом.
В отечественной горной промышленности в настоящее время используют несколько переоборудованные бульдозеры общего назначения и специально спроектированные для работы в подземных выработках.
Техническая характеристика основных типов бульдозеров, применяемых в подземных условиях, приведена в табл. VI.2.
Основным недостатком дизельного привода на бульдозерах, ограничивающим их применение на подземных работах, является выделение выхлопных газов, содержащих токсичные вещества. Поэтому необходимо наличие специальных устройств для очистки выхлопных газов дизелей и их разрежения, а также более интенсивное проветривание для поддержания в очистных забоях загазованности воздуха в пределах санитарных норм, что в ряде случаев затруднительно и неэкономично.
В последние годы для подземных работ созданы специальные подземные бульдозеры с пневмоприводом (БПП1) и электроприводом (БПДУ1 и БЭМ), которые выгодно отличаются от дизельных отсутствием загрязнения рудничной атмосферы выхлопными газами.
Подземные бульдозеры оборудованы гусеничным ходом и предназначены для механизации доставки руды с целью закладки при отработке камер на участках средней мощности, а также для работы в аналогичных условиях взамен скреперной доставки.
Интересна конструкция подземного малогабаритного электрического бульдозера БЭМ, который предназначен для доставки отбитой горной массы в выработках высотой не ниже 0,5 м на шахтах, не опасных по газу или пыли. Бульдозер оборудован гусеничным ходом / (рис. VI.3) и отвалом 2 длиной 2,32 м. Эластичная подвеска ходовых тележек увеличивает проходимость бульдозера массой около 7 т. Отвал выполнен выдвижным и с обратным ходом, что дает возможность доставлять горную массу как при ходе вперед, так и при ходе назад, например при работе в тупиковых выработках. Подъем, опускание и выдвижение отвала производят с помощью шарнирно закрепленной стрелы 3 и гидроцилиндров 4 и 5, работающих от гидропривода, развивающего давление 8 МПа. При работе прямым и обратным ходом нижняя, шарнирно прикрепленная часть 6 отвала отклоняется соответственно вперед или назад и опирается на кронштейн 7 стрелы или удерживается тягами 8. Для зачистки почвы бульдозер
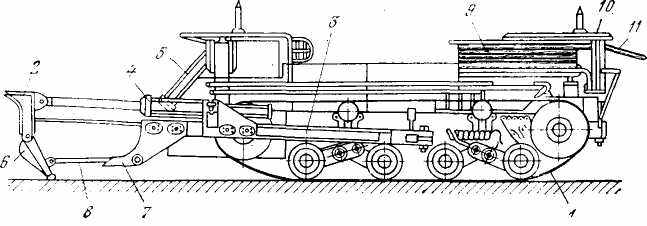
Рис. VI.3. Подземный электробульдозер БЭМ
комплектуется сменным отвалом и изменяемым углом резания. Кроме того, может применяться другое навесное оборудование.
Электродвигатель бульдозера переменного тока мощностью 41 кВт питается переменным током напряжением 380 В и развивает скорость перемещения 0,78—1,07 м/с при напорном усилии 40—60 кН. Кабельный барабан 9 для увеличения маневренности машины, оборудованной самоустанавливающейся стрелой 10 может наматывать кабель 11 длиной 55 м. Техническая производительность электробульдозера составляет до 44 м3/ч при уборке лавы длиной до 50 м.
Техническая производительность бульдозера QT (м3/ч) в плотном теле (в массиве)
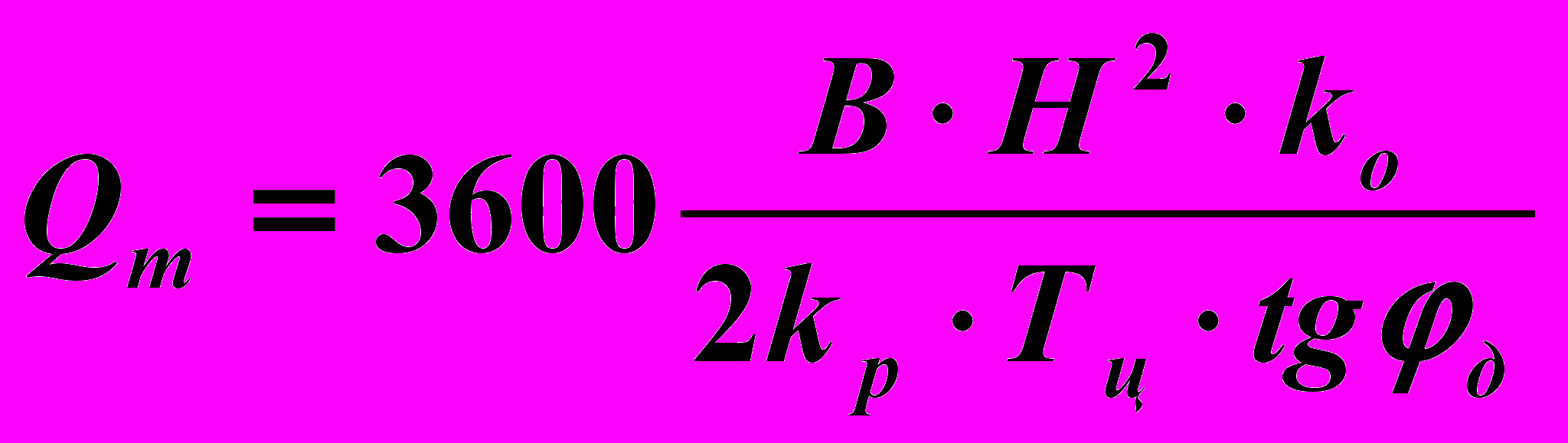
где В и Н – ширина и высота отвала, м; k0 – коэффициент потерь объема породы при перемещении, зависящий от длины транспортирования L, м, может определяться по приближенным формулам (k0 = (l ÷ 0,005L); kp – коэффициент разрыхления породы (kp = 1,25 ÷ 1,3); φд – угол естественного откоса породы в движении градус.
Продолжительность цикла работы бульдозера
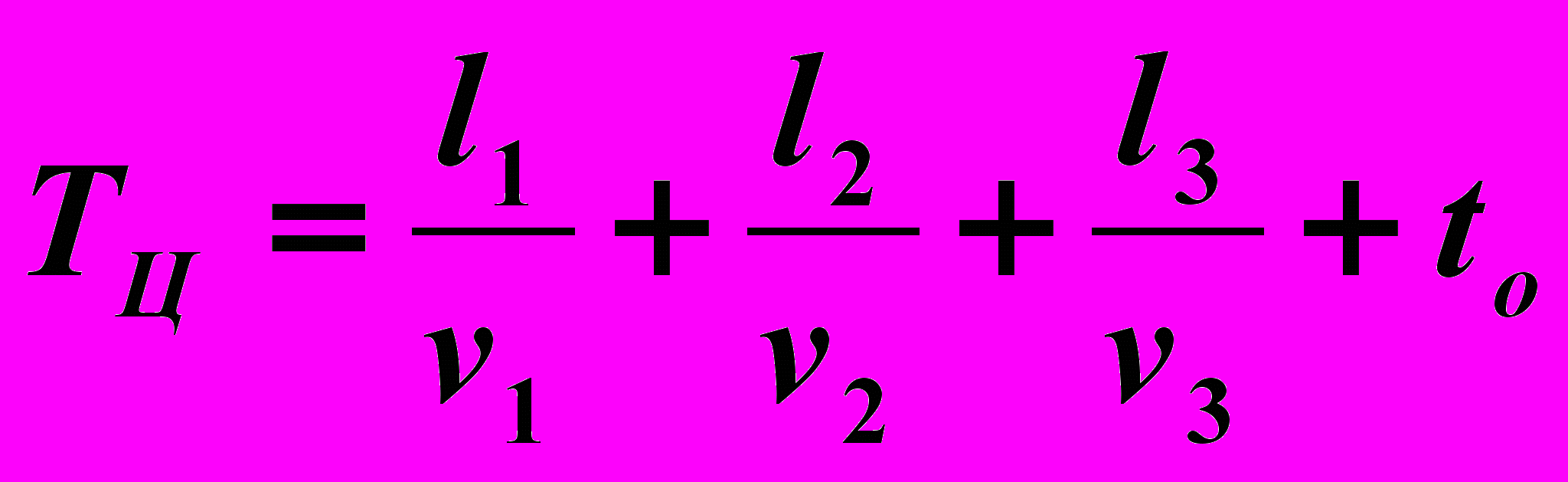
где l1, l2 и l3 — отрезки пути, на которых происходит соответственно заполнение отвала, транспортирование породы и движение без груза, м; v1, v2 и v3 – средние скорости движения бульдозера соответственно при заполнении отвала, перемещении породы и движении без груза, м/с; t0 = 8 ÷10 – время, затрачиваемое на разворот бульдозера, переключение скоростей, подъем и опускание отвала и другие вспомогательные операции, с.
Эксплуатационная производительность бульдозера Q3 (м3/см) будет
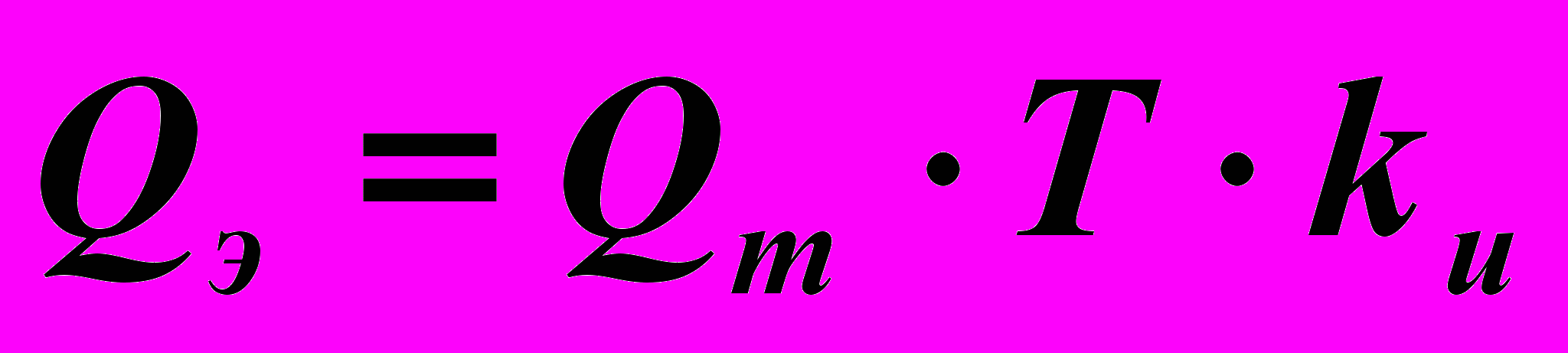
где Т — длительность смены, ч; kи — коэффициент использования бульдозера во времени.
При работе бульдозеров необходимо строго соблюдать правила техники безопасности. В частности, обслуживать бульдозеры могут только лица, прошедшие специальные курсы обучения и имеющие соответствующее удостоверение. Запрещается работа на бульдозере при уклонах более 30° или при поврежденной системе управления. Запрещается пребывание людей в сфере работы бульдозера и ремонт или регулировка бульдозера вплоть до полной его остановки. Должны строго соблюдаться правила пожарной безопасности и правила, относящиеся к эксплуатации машины с электроприводом и т. д. Нельзя оставлять бульдозер с включенным приводом и незаторможенным ручным тормозом.
При обслуживании и ремонте бульдозера и во всех других случаях категорически запрещается находиться под узлами и деталями, которые удерживаются фрикционными тормозами или гидроустройствами, без устойчивой опоры их на специальные подкладки. Запрещается подогревать двигатель открытым пламенем, а также находиться под машиной при работающем двигателе и вблизи гибких рукавов гидропривода, так как лопнувший рукав может причинить тяжелые увечья. Заправлять машины горючими и смазочными материалами следует днем или при нормальном электрическом освещении. При заправке категорически запрещается курить, зажигать спички или пользоваться керосиновыми или неисправными электрическими фонарями.
СКРЕПЕРЫ
Самоходными скреперами называют горные машины прерывного действия, предназначенные для соскребания или срезаниягорной массы, перемещения ее на некоторое расстояние в ковше, разгрузки и разравнивания. В отличие от бульдозера самоходные скреперы перемещают груз толканием-волочением только в период зачерпывания или разгрузки, одновременно разравнивая его, а транспортирование груза производят в ковше. Благодаря этому в сравнении с бульдозерами самоходные скреперы перемещают груз на значительно большие расстояния, обычно достигающие 300 м, а в отдельных случаях – 500 м.
По конструктивному исполнению самоходные, или колесные, скреперы подразделяют на машины для работы на поверхности и в подземных условиях. При этом на открытых работах и на поверхности шахт колесные скреперы получили широкое распространение как землеройно-транспортные машины, а на подземных работах их применяют в основном в очистных забоях. Соответственно назначению и условиям применения емкость ковша у скреперов, используемых на открытых работах, изменяется от 1,5 до 50 м3, а у подземных она не превышает 3 м3.
Колесный скрепер состоит из рамы 1 (рис. VI.4), ходового оборудования 2, прицепного устройства 3, ковша 4, заслонки 5 ковша и механизмов управления 6. Исполнительным органом колесного скрепера является ковш 4, который в начале заполнения опускается вниз до необходимого заглубления в почву, и его передняя заслонка 5 при этом приподнимается. По мере движения колесного скрепера вперед ковш заполняется срезаемым грунтом.
Подземные скреперы всегда выполняются самоходными и в значительной мере повторяют конструкции подземных бульдозеров, которые при небольших длинах доставки успешно заменяют скреперы. Для доставки горной массы на большие расстояния проектируются специальные подземные скреперы, состоящие из ходовой части гусеничного или колесного типа (аналогично применяемой на бульдозерах), ковша (навешивается вместо отвала бульдозера) и системы управления. Подземные самоходные скреперы только начинают внедряться на рудниках и находят применение в основном на очистных работах. Поскольку машины этого типа выполняют функции погрузки и доставки горной массы, их иногда называют погрузочно-доставочными с совмещенным органом погрузки и доставки. Более мощные машины данного типа выполняют по аналогичной схеме, но с различным конструктивным оформлением рабочего и ходового оборудования и большими емкостью, мощностью и грузоподъемностью. Так, машины ДК2,8 и ДК2.8Д массой около 20 т, предназначенные для работы в выработках сечением не менее 14 м2, выполняют с ковшом емкостью 2,8 и 5 м3.
Эксплуатационная производительность Qэ (тч) скрепера может быть определена по формуле
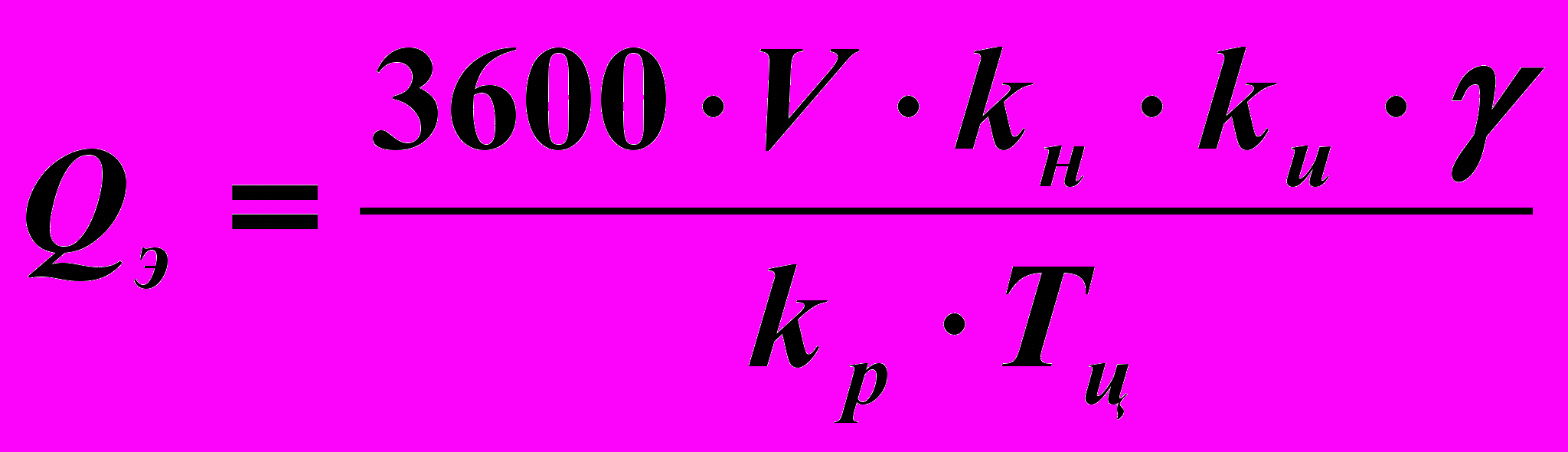
где V – геометрическая емкость ковша скрепера, м3; kн = 0,6÷1,25 — коэффициент наполнения ковша; kи – коэффициент использозания скрепера; kр – 1,1÷1,4— коэффициент разрыхления горной массы; γ – плотность горной массы, т/м3.
Продолжительность цикла работы скрепера
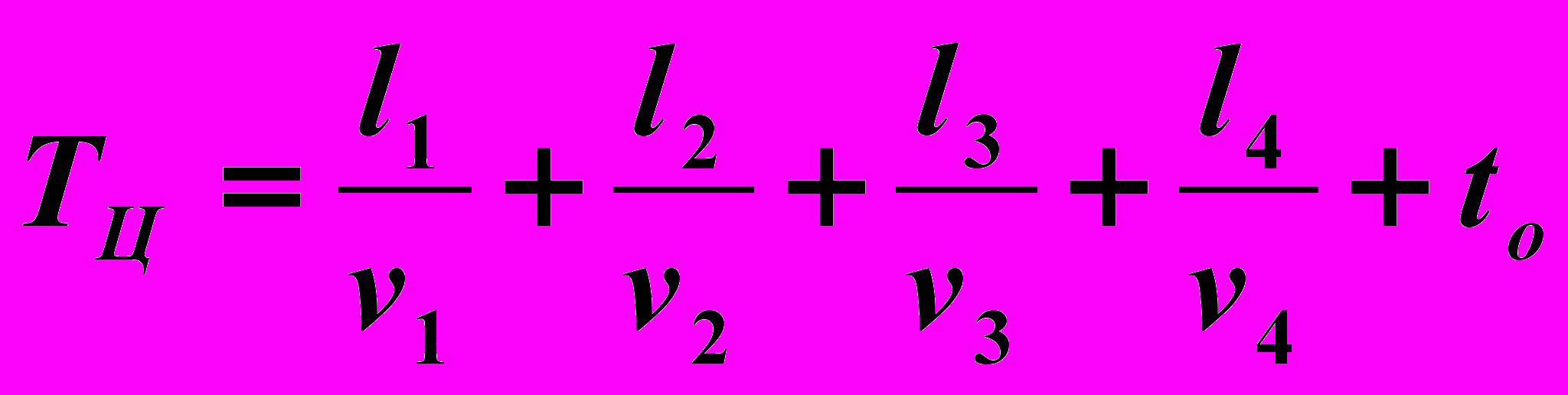
где l1, l2, l3, l4 – отрезки пути соответственно при заполнении ковша, транспортировании породы, разгрузке ковша и движении порожнего скрепера, м; v1, v2, v3, v4 – скорости движения соответственно при заполнении скрепера, груженого скрепера, при разгрузке и порожнего скрепера, м/с; to – время, затрачиваемое на неучтенные операции, с.
Особенности эксплуатации и правила техники безопасности во время ремонта подземных скреперов в значительной мере такие же, как и у бульдозеров. Помимо этого, запрещается накачивать шины воздухом сверх разрешаемого максимального давления, а разбирать и собирать колеса следует только после того, как давление будет понижено. Категорически запрещена перевозка людей в ковше скрепера.
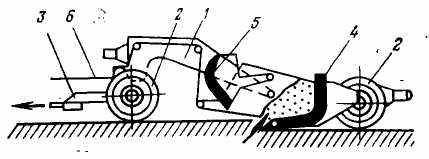
Рис. VI.4. Рабочее оборудование колесного скрепера