Т. А. Дуюн моделирование тепловых деформаций с целью обеспечения точности механической обработки
Вид материала | Документы |
СодержаниеNu – безразмерный комплекс, называемый критерием Нуссельта; С L – длина выделенной части поверхности; s |
- 05. 02. 07 Технология и оборудование механической и физико-технической обработки, 24.16kb.
- Деформационная точность механической обработки сложных криволинейных поверхностей изделий, 54.64kb.
- Математическое моделирование процессов в тепловых микросенсорах, 21.43kb.
- Программа-минимум кандидатского экзамена по специальности 05. 02. 07 «Технология, 256.06kb.
- Прогрессивные методы, такие как намотка, прессование, литье, экструзия, 58.38kb.
- Кафедра технологии машиностроения и методики профессионального обучения курсовой проект, 88.72kb.
- Кафедра технологии машиностроения и методики профессионального обучения курсовой проект, 81.68kb.
- Технологическое обеспечение финишной ультразвуковой обработки вязких высокопрочных, 823.11kb.
- Кафедра технологии машиностроения и методики профессионального обучения курсовой проект, 89.23kb.
- Курсовой проект разработка технологического процесса механической обработки детали, 81.31kb.
Вестник Брянского государственного технического университета. 2009. № 2(22)
УДК 621
Т.А. Дуюн
МОДЕЛИРОВАНИЕ ТЕПЛОВЫХ ДЕФОРМАЦИЙ С ЦЕЛЬЮ ОБЕСПЕЧЕНИЯ ТОЧНОСТИ МЕХАНИЧЕСКОЙ ОБРАБОТКИ
Представлена методика моделирования тепловых деформаций обрабатываемого изделия в процессе механической обработки на примере точения медной контактной поверхности коллектора электродвигателя постоянного тока.
Ключевые слова: моделирование, тепловые деформации, точение, коллектор, электродвигатель.
Точность механической обработки деталей всегда являлась одной из актуальных проблем технологии машиностроения. При этом требования к точности изготовления постоянно возрастают. Обеспечение повышающихся требований возможно только при широком внедрении методов математического моделирования и использовании средств вычислительной техники.
В процессе механической обработки возникает ряд погрешностей, снижающих точность. Разработаны различные методики вычисления отдельных погрешностей и их суммирования. Вычисление погрешности от тепловых деформаций технологической системы сопряжено со значительными трудностями, и до настоящего времени не разработано достаточно точных методик. Зона резания является мощным источником выделения тепла. Направления движения тепловых потоков, поступающих в инструмент, деталь и стружку, имеют достаточно сложный характер и зависят от ряда факторов: режимов резания, геометрических параметров инструмента, физико-механических свойств инструментального и обрабатываемого материалов. Величины тепловых деформаций, возникающих под действием тепловых потоков, зависят от условий обработки, схемы базирования и закрепления. Влияние погрешности от тепловых деформаций в некоторых случаях может быть очень существенно или даже иметь определяющее значение. Это касается нежестких тонкостенных деталей, а также изделий из высокотеплопроводных материалов, таких, как медь.
Коллектор электрической машины является одним из наиболее сложных и ответственных узлов. Коллектор представляет собой осесимметричную конструкцию и состоит из активной и крепежной частей. Активная часть набрана из чередующихся медных и изоляционных пластин трапецеидального профиля.
К точности формы и шероховатости контактной поверхности коллектора предъявляются весьма жесткие требования. Для обеспечения хороших условий коммутации биение коллектора в готовой машине должно быть не более 0,03…0,04 мм. Половина этого значения обусловливается зазором подшипников и эксцентриситетом подшипниковых щитов, т.е. на долю допустимого биения коллектора остается 0,007…0,01 мм (для машин средней мощности). Нарушение цилиндричности коллектора, превышающее допустимую норму, может быть причиной серьезных повреждений. Эллипсность и эксцентриситет контактной поверхности вызывают искрение в контактах щеток, а как следствие – круговой огонь на коллекторе, пробой изоляции коллектора и обмотки якоря. Требования к шероховатости контактной поверхности коллектора регламентируются величиной Ra = 0,2…0,8 мкм.
Механическая обработка контактной поверхности коллектора является важным и ответственным этапом в технологии изготовления коллектора, так как в ее процессе формируются необходимые показатели качества поверхности. Точность формы контактной поверхности в основном формируется на операциях точения. Ввиду высокой теплопроводности меди необходимо исследовать величину тепловых деформаций обрабатываемого изделия. Аналитическое решение в данном случае неприемлемо, необходимо применять численные методы.
В настоящее время разработано достаточно много универсальных численных методов, которые применяются для решения дифференциальных уравнений в частных производных. Наиболее приемлемым для решения задачи определения теплового и напряженно-деформированного состояния коллектора является метод конечных элементов (МКЭ). Основная идея МКЭ состоит в том, что любую непрерывную величину, такую, как температура, можно аппроксимировать дискретной моделью, которая строится на множестве кусочно-непрерывных функций, определенных на конечном числе подобластей (конечных элементов). Кусочно-непрерывные функции определяются с помощью значений непрерывной величины в конечном числе точек (узлов) рассматриваемой области.
Для программной реализации конечноэлементного численного метода используем расчетный комплекс COSMOSWorks, интегрированный в CAD-систему SolidWorks [1].
Первым этапом решения поставленной задачи является обоснование расчетного контура. Точение контактной поверхности коллектора выполняется после его сборки. Активная часть коллектора отделена от крепежной изоляционным материалом, теплопроводность которого на два порядка меньше теплопроводности меди. За время обработки крепежные конусы не успеют прогреться, поэтому из расчетного контура можно исключить крепежную часть коллектора. В связи с осесимметричностью конструкции активной части (круговой арки) в расчетный контур можно включить только одно коллекторное деление, содержащее одну коллекторную пластину. После создания объемной модели расчетного контура началом программной реализации МКЭ является генерирование сетки конечных элементов (рис.1).
В
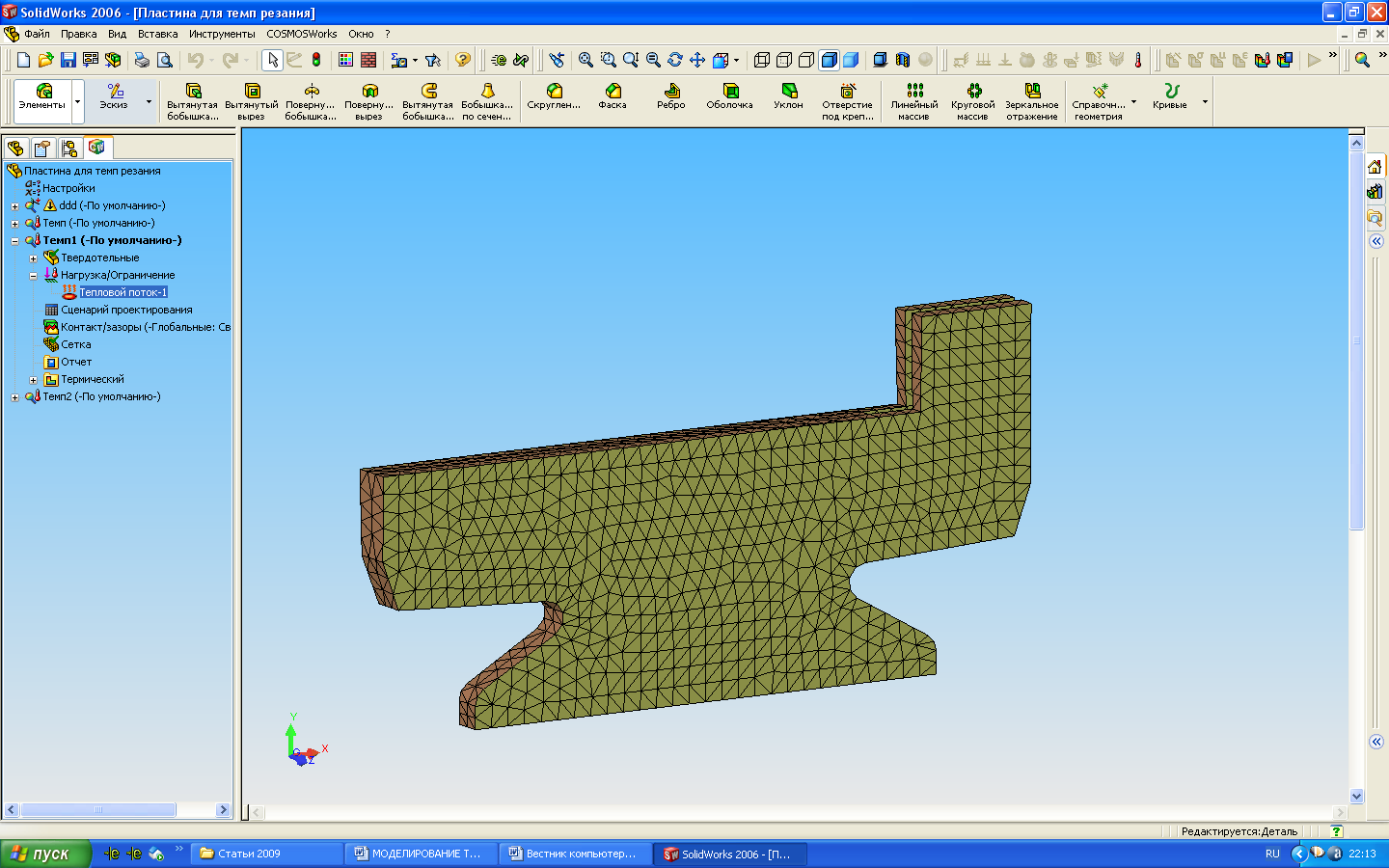
Граничное условие 2-го рода имеют:
1
Рис.1. Сетка конечных элементов на расчетной модели
. Часть обрабатываемой поверхности пластины, контактирующая с резцом, через которую поступает тепловой поток, возникающий при резании.
2. Теплоизолированные поверхности, т.е. поверхности, имеющие интенсивность теплового потока, равную нулю. В качестве теплоизолированных поверхностей приняты боковые поверхности коллекторных пластин, контактирующие с изоляционными прокладками. Такое допущение сделано вследствие низкой теплопроводности изоляционных материалов, которая на два порядка меньше теплопроводности меди.
Граничное условие 3-го рода имеют поверхности пластины, контактирующие с наружным воздухом.
Основным действующим тепловым потоком является тепловой поток, возникающий при резании и поступающий в обрабатываемое изделие. Для его определения воспользуемся известной методикой [2].
В процессе резания без искусственного охлаждения изделия и инструмента существует три основных источника выделения тепла: деформация материала, трение стружки по передней поверхности инструмента и трение между задней поверхностью инструмента и изделием. При этом наблюдается сложное переплетение маршрутов движения потоков.
Теплота деформации материала возникает в узкой области вблизи плоскости сдвига и эквивалентна работе пластической деформации. Теплота от этого источника распределяется между стружкой и изделием. Стружка, проходя мимо площадки контакта площадки с передней поверхностью резца, отдает последнему часть полученной ею теплоты. Эта теплота в виде потока может передаваться через инструмент в изделие, поскольку существует теплообмен между задней поверхностью резца и поверхностью резания. Часть теплоты, возникающей в результате трения по передней поверхности инструмента, в виде потока уходит в стружку, а другая часть – в резец. Теплота от третьего источника распределяется между изделием, резцом и стружкой.
Таким образом, тепловой поток в изделие будет определяться как
Qи= Qди+ Qтз – Qз,
где Qди – часть теплоты деформации, уходящая в изделие; Qтз – теплота, возникающая в результате трения между изделием и резцом; Qз – итоговый тепловой поток, возникающий в результате теплообмена на площадке контакта поверхности резания с задней поверхностью инструмента.
Тепловой поток в изделие определяется в результате решения системы уравнений
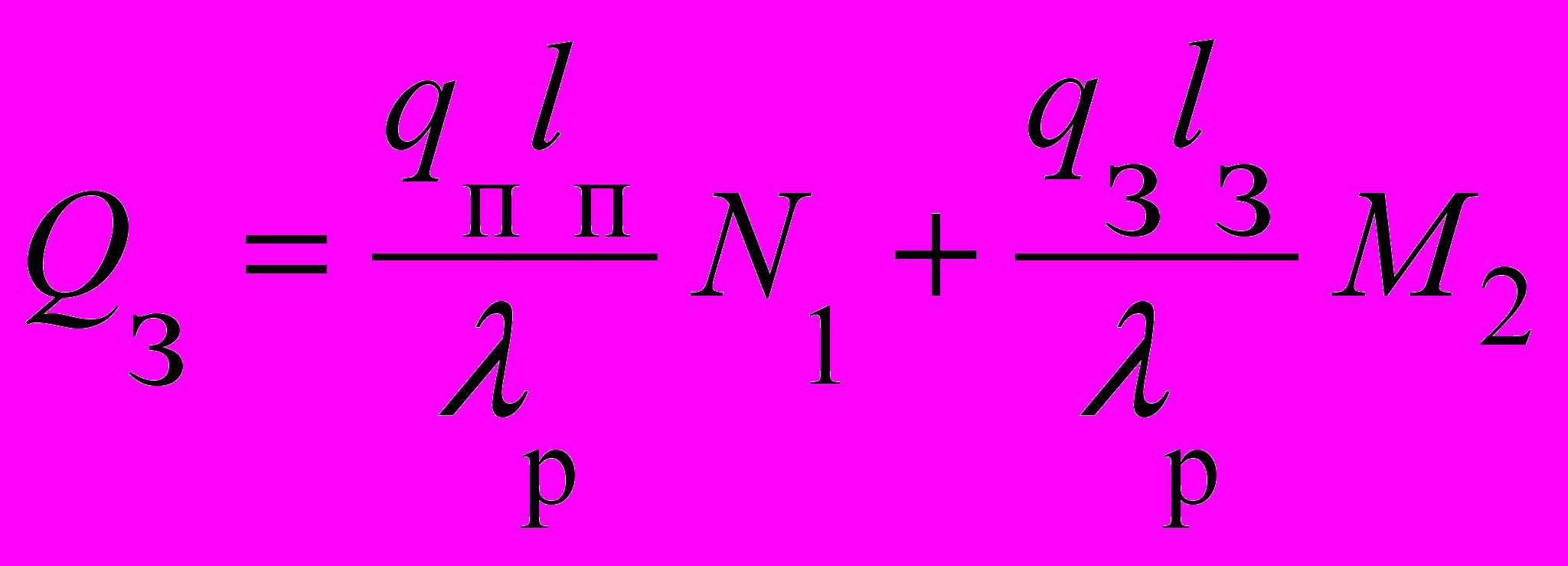
(1)
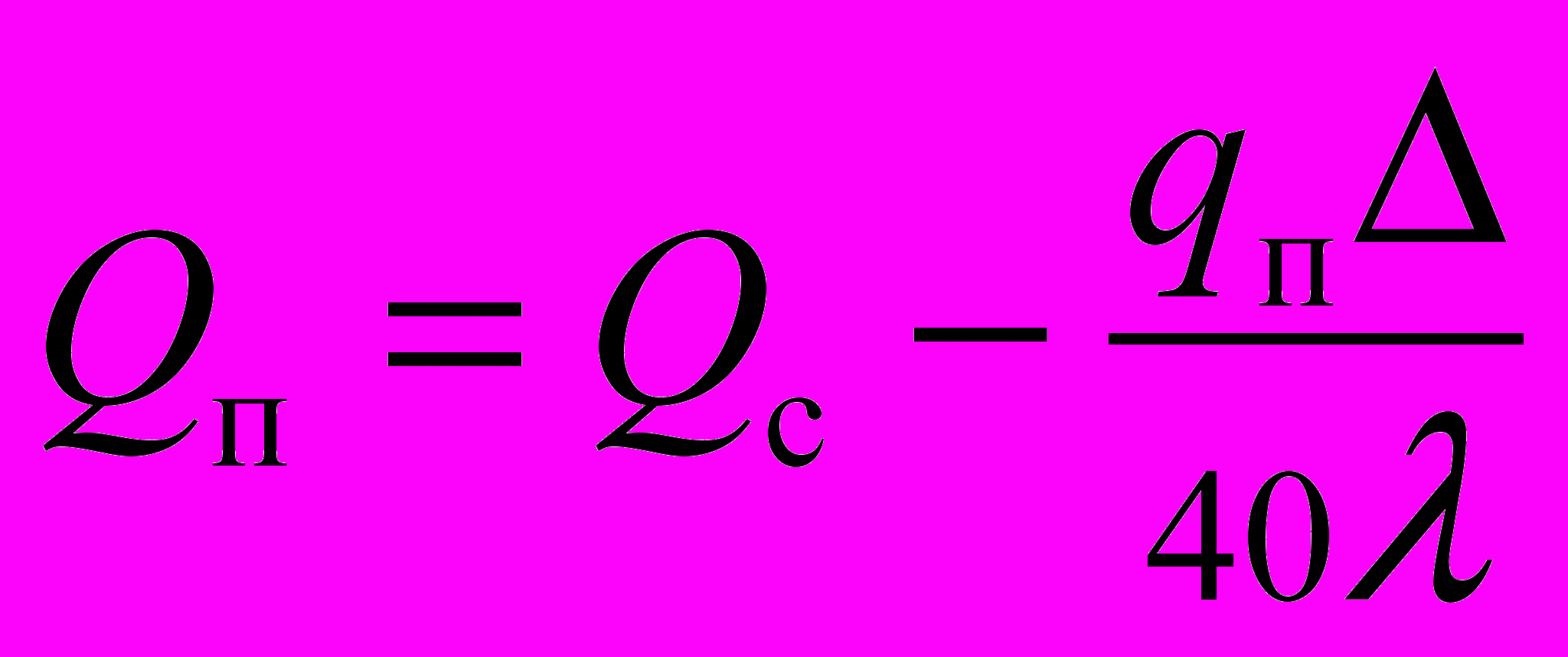
где qп – суммарный удельный тепловой поток, поступающий в резец по передней поверхности; lп – длина контакта стружки с резцом; λр – теплопроводность материала режущей части резца; qз – суммарный удельный тепловой поток по задней поверхности резца; lз – длина контакта резца с изделием по задней поверхности; N1 и M2 – коэффициенты, зависящие от геометрических параметров режущего инструмента; Qп – итоговый тепловой поток, действующий по передней поверхности; Qс – тепловой поток, уходящий со стружкой; Δ – наибольшая толщина заторможенного слоя стружки; λ – теплопроводность обрабатываемого материала.
Система уравнений (1) решается относительно суммарных удельных тепловых потоков по передней и задней поверхностям инструмента.
Для реализации граничного условия 3-го рода основной исходной величиной является коэффициент конвективного теплообмена, для определения которого воспользуемся критериальным уравнением .
Для случая вынужденной конвекции (теплообмен вращающегося коллектора с воздухом) критериальное уравнение имеет вид:

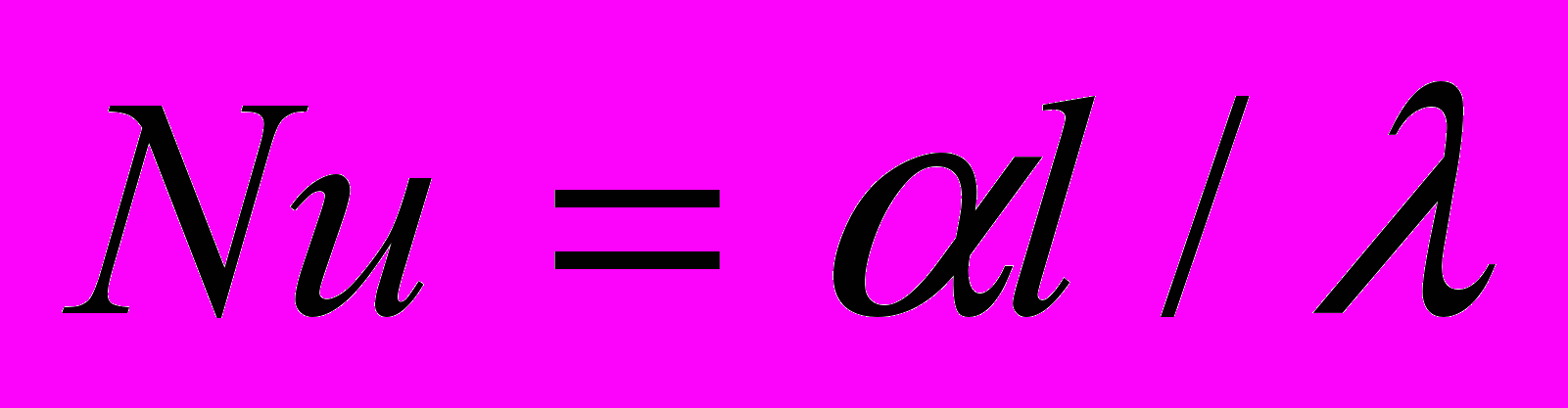
где Nu – безразмерный комплекс, называемый критерием Нуссельта; С, n, m, p – коэффициенты; Pr0, Prs – критерий Прандтля соответственно для охлаждающей среды и охлаждаемой поверхности; Gr0 – критерий Грасгофа охлаждающей среды; Re0 – критерий Рейнольдса охлаждающей среды; α – среднее по омываемой поверхности значение коэффициента теплоотдачи, Вт/(м2ּºС); l – характерный размер, м; λ – коэффициент теплопроводности среды, Вт/(мּºС).
Коллектор является телом вращения, поэтому в качестве характерного размера примем его диаметр.
Критерий Рейнольдса характеризует скорость движения среды относительно твердого тела:
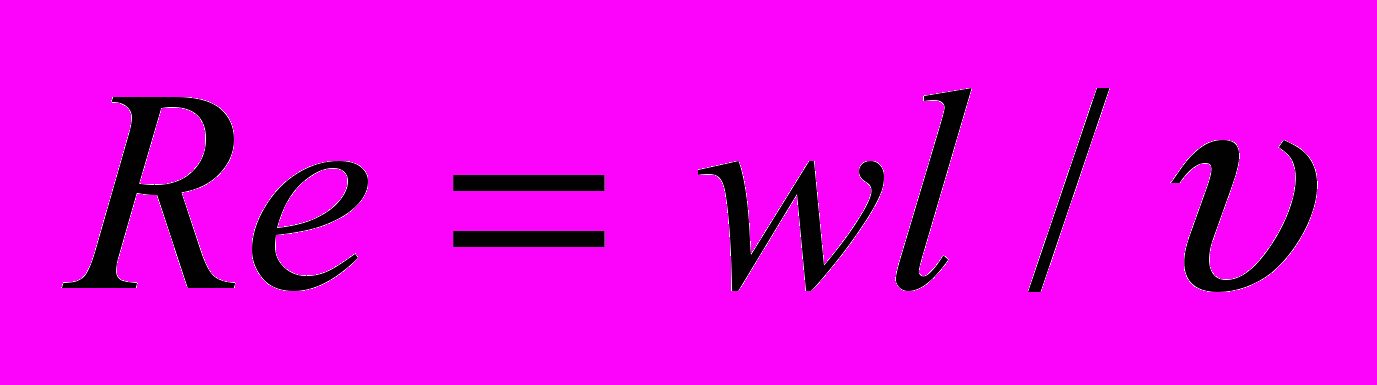
где w – скорость потока, м/с; υ – кинематический коэффициент вязкости среды, м2/с.
Критерий Прандтля характеризует способность теплоты распространяться в данной среде.
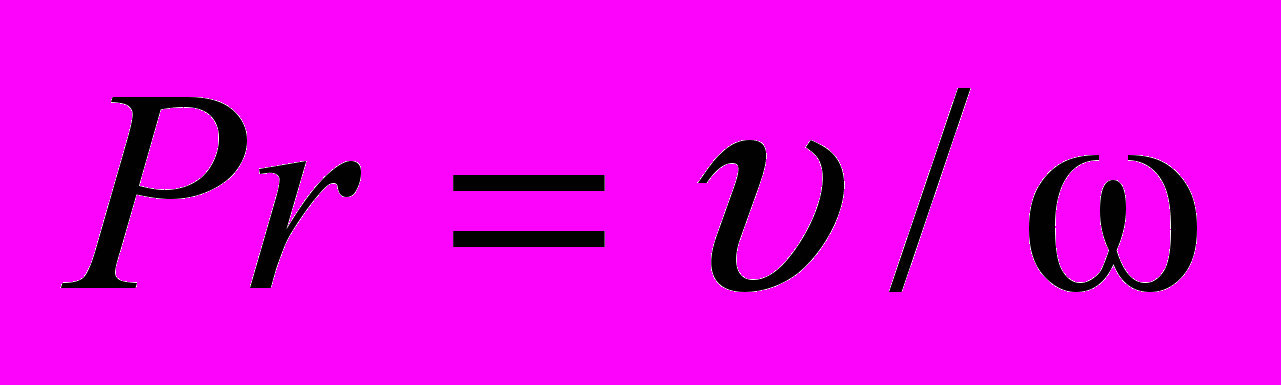
где ω – температуропроводность среды.
Критерий Грасгофа учитывает влияние естественной конвекции внутри среды. При вынужденной конвекции, которая характерна для вращающегося коллектора, показатель степени в критериальном уравнении для критерия Грасгофа равен нулю, следовательно, данный критерий равен единице, т.е. можно исключить из уравнения. При естественной конвекции критерий Грасгофа определяется выражением
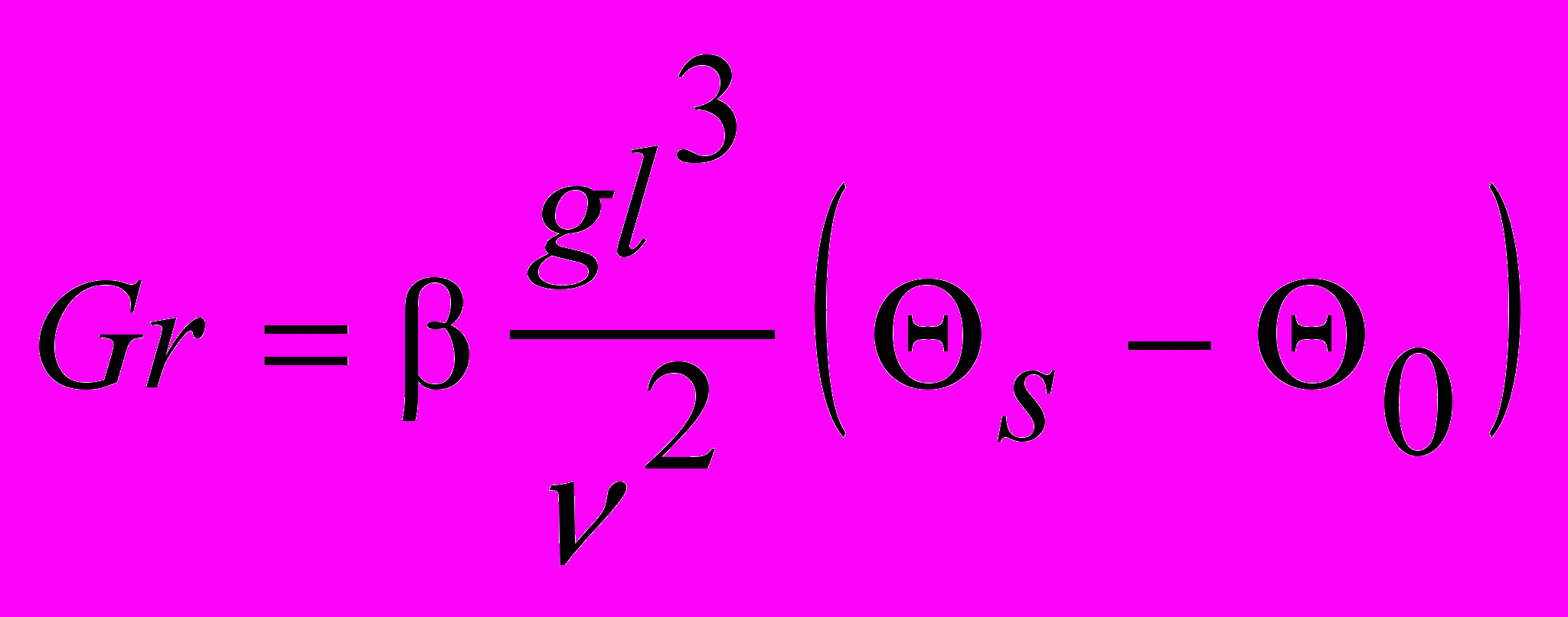
где β – коэффициент объемного расширения среды, 1/ºС; g – ускорение свободного падения, g = 9,81 м/с2; Θs, Θ0 – соответственно температуры охлаждаемой поверхности и охлаждающей среды, ºС.
При поперечном обтекании цилиндрических поверхностей и турбулентном характере потока коэффициенты в критериальном уравнении имеют следующие значения: С = 0,28; m = 0,6; n = 0,36.
Таким образом, можно записать выражение для определения коэффициента теплоотдачи при вращении коллектора:

Определение граничных условий является важной, но не основной задачей. Основной проблемой моделирования теплового поля обрабатываемого изделия в процессе резания является движущийся источник выделения тепла. Задача не может быть решена в статике с достаточной точностью, так как обрабатываемая поверхность в разные моменты времени имеет разные граничные условия: в момент контакта с резцом – 2-го рода (поступает тепловой поток), в остальное время – 3-го рода (осуществляется конвективный теплообмен). Однократное решение динамической задачи также неприемлемо, так как граничные условия изменяются не только во времени, но и по координате приложения к расчетной модели. Поэтому необходимо решать ряд взаимосвязанных динамических задач. Версия COSMOSWorks 2007 года дает такую возможность.
Обрабатываемую поверхность необходимо разделить на определенное количество равных частей для решения взаимосвязанных подзадач. Количество частей зависит от требуемой точности решения: чем больше количество подзадач, тем точнее результат. В идеале один оборот изделия является одной подзадачей, однако при этом общее количество подзадач будет равно нескольким сотням, что неприемлемо. Поэтому необходимо найти некоторый компромисс. Длина обрабатываемой поверхности коллектора, равная 90 мм, была разделена на 9 частей по 10 мм каждая.
Для решения каждой отдельной подзадачи необходимо определить тепловой поток, поступающий в выделенную часть изделия. При наступлении теплового баланса между источниками и стоками тепла в процессе резания интенсивность удельного теплового потока в изделие можно считать постоянной. Удельный тепловой поток qз, поступающий в изделие по контактной площадке на задней поверхности резца, определяется из системы уравнений (1). Данный поток действует по винтовой поверхности в соответствии с величиной подачи. Необходимо пересчитать данный поток в усредненный, действующий на выделенной части поверхности, длина которой равна 10 мм. С некоторой погрешностью определим его по выражению
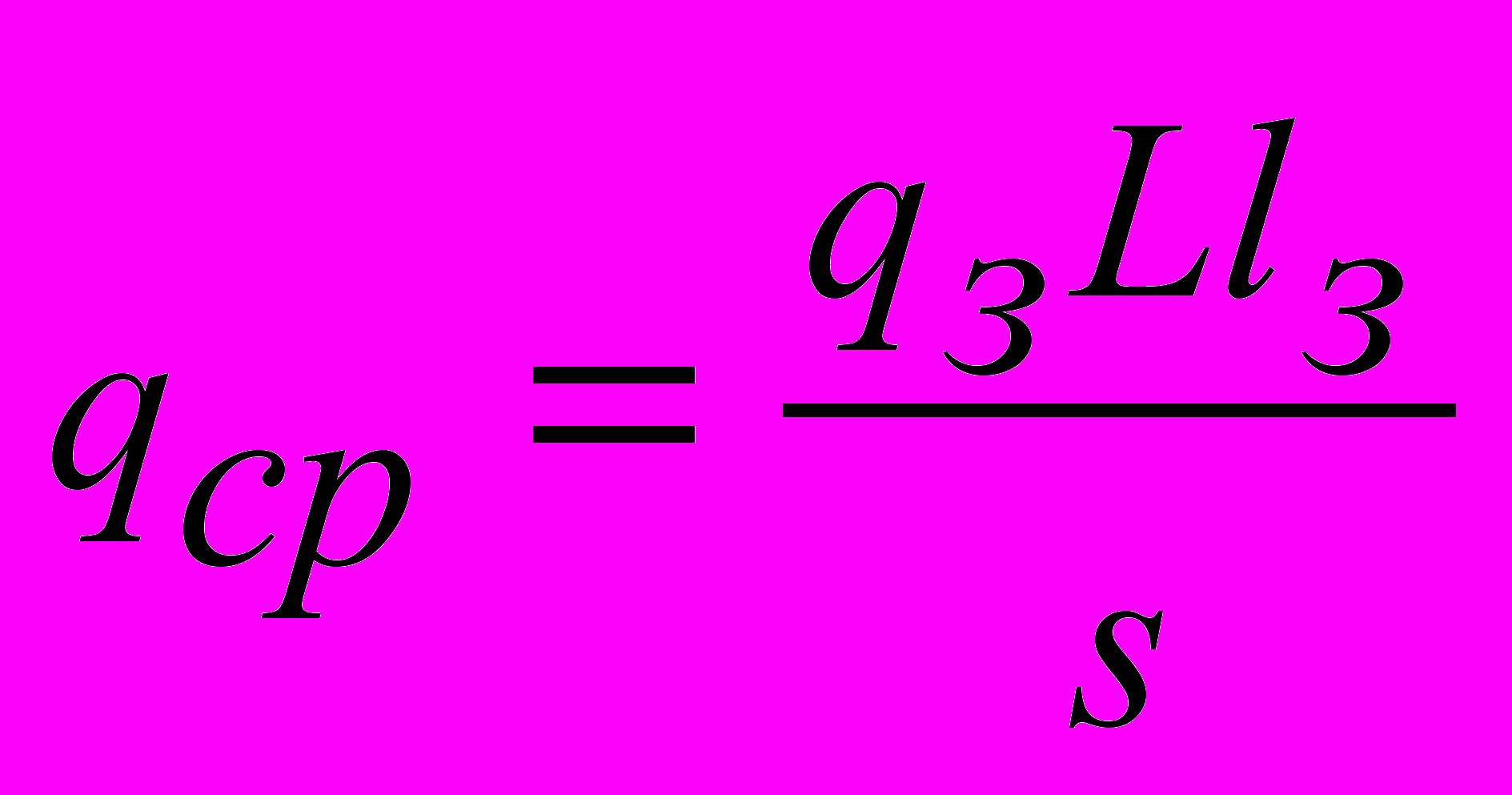
где L – длина выделенной части поверхности; s – величина продольной подачи.
Важным моментом является время действия теплового источника. С некоторой погрешностью определим его через суммарный пройденный путь и скорость движения:
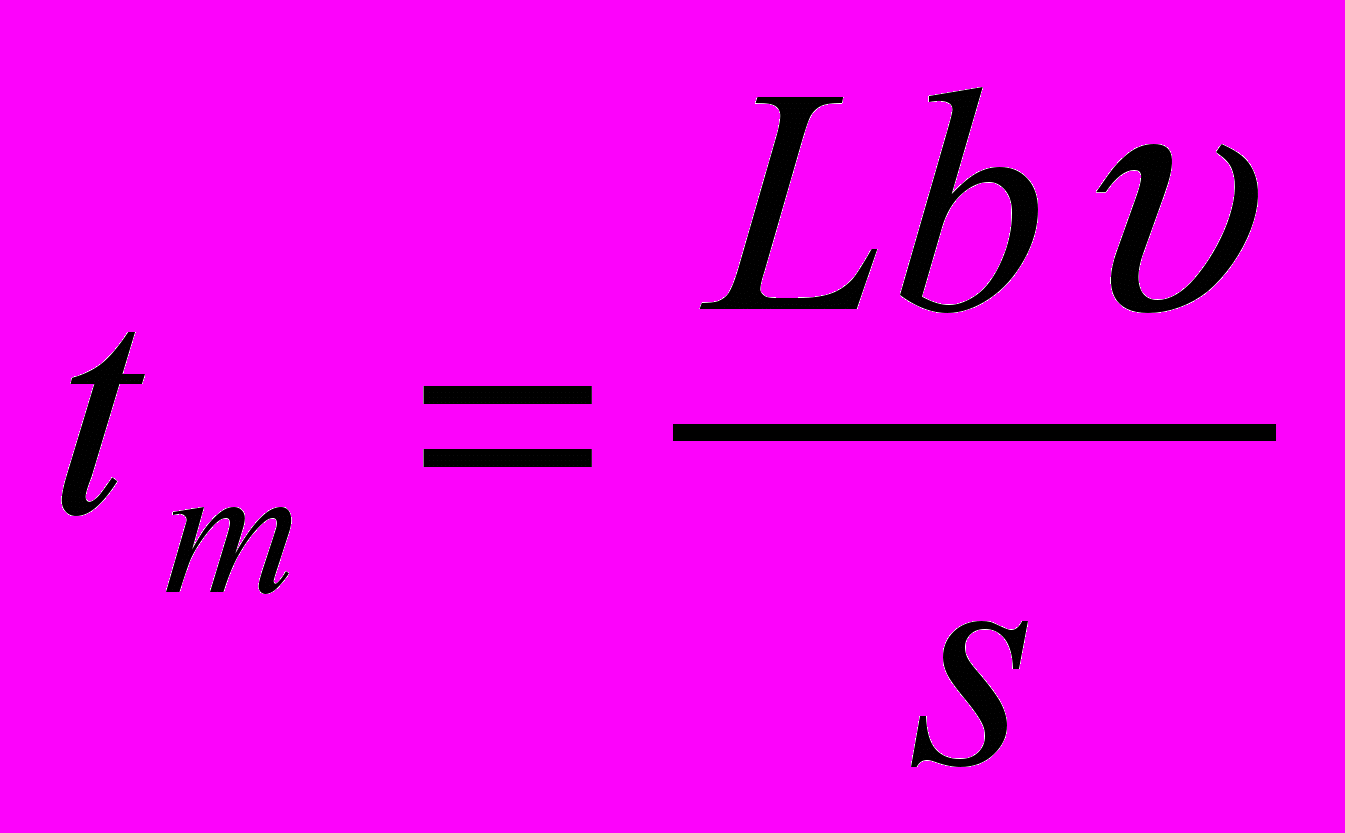
где b – ширина одной коллекторной пластины, принятой в расчетный контур; v – скорость резания.
Так как время, определенное выражением (3), является временем контакта резца с изделием на выделенной поверхности расчетного контура, являющегося лишь сектором изделия, оно не соответствует реальному времени движения резца по цилиндрической обрабатываемой поверхности. Во время отсутствия контакта резца с изделием осуществляется конвективный теплообмен поверхности с наружным воздухом. Коэффициент теплоотдачи определим по выражению (2), а время конвекции - выражением
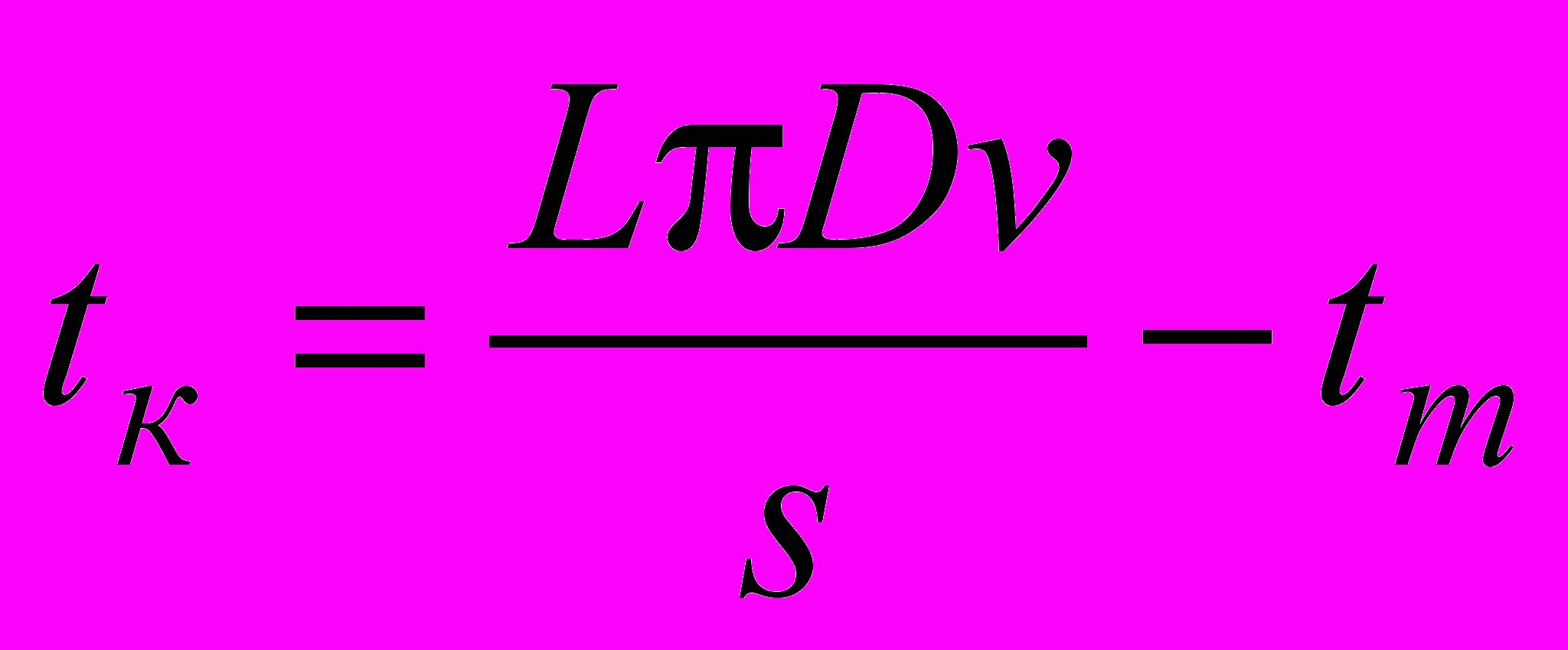
где D – обрабатываемый диаметр.
При решении одной динамической тепловой задачи нельзя одновременно учесть и тепловой поток, и конвекцию на одной и той же поверхности, поэтому для каждой выделенной части необходимо решать две последовательные задачи: в одной прикладывать тепловой поток, а во второй – конвекцию. Тепловое поле, полученное при решении первой задачи, является начальными данными для второй задачи. Такой подход позволяет решить основную проблему двух одновременных граничных условий.
Результат решения двух подзадач для первой выделенной области представлен на рис.2.
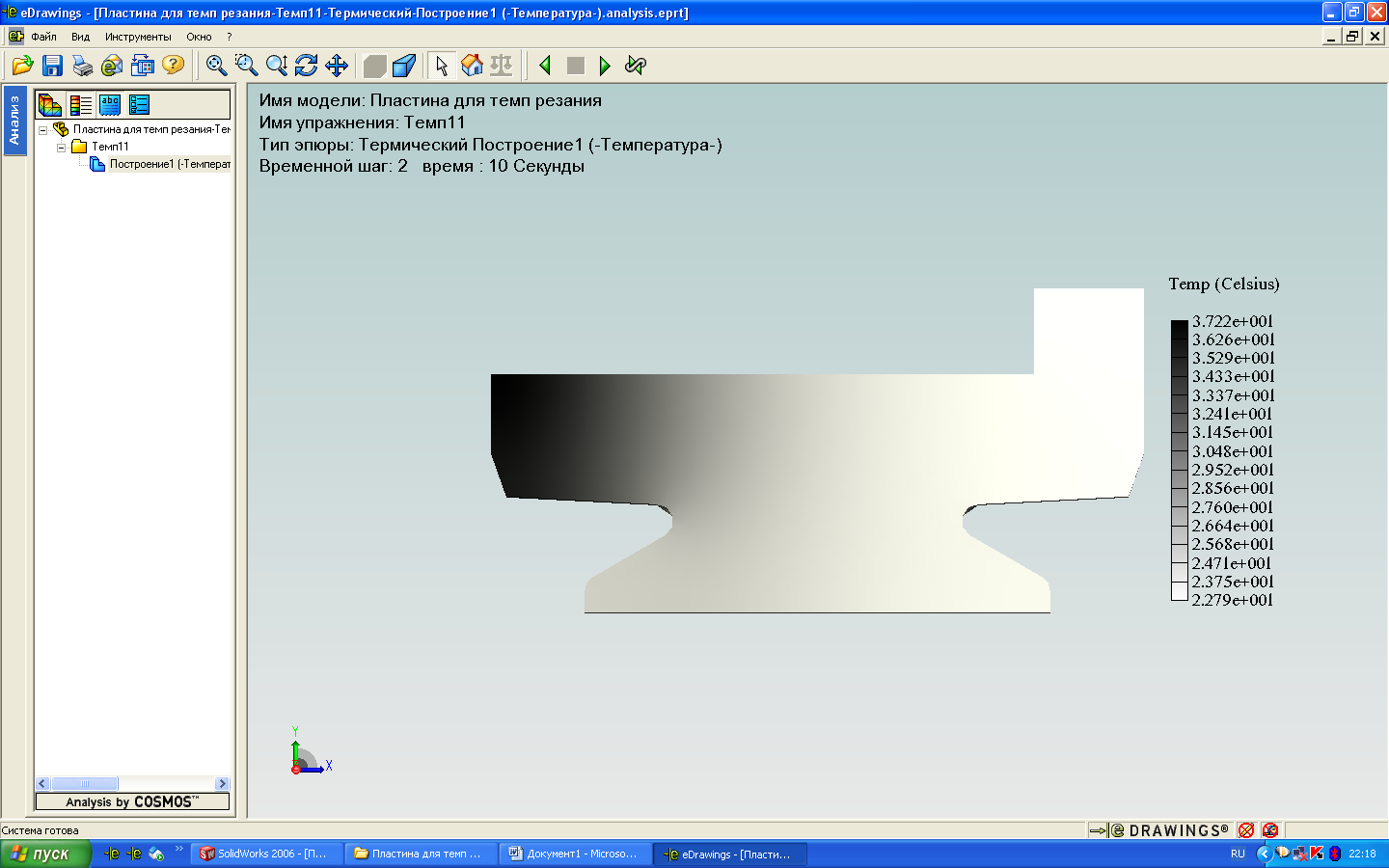
Рис.2. Тепловое поле на момент выполнения точения первой
выделенной области
В соответствии с представленной методикой выполняются аналогичные действия для всех выделенных областей. Главным условием является взаимосвязанность всех подзадач, т.е. результат решения каждой подзадачи должен являться начальными данными для следующей. Выполнение этого условия позволяет с некоторой погрешностью моделировать тепловое поле от движущегося источника. На рис. 3 представлено тепловое поле, полученное после моделирования всех выделенных областей.
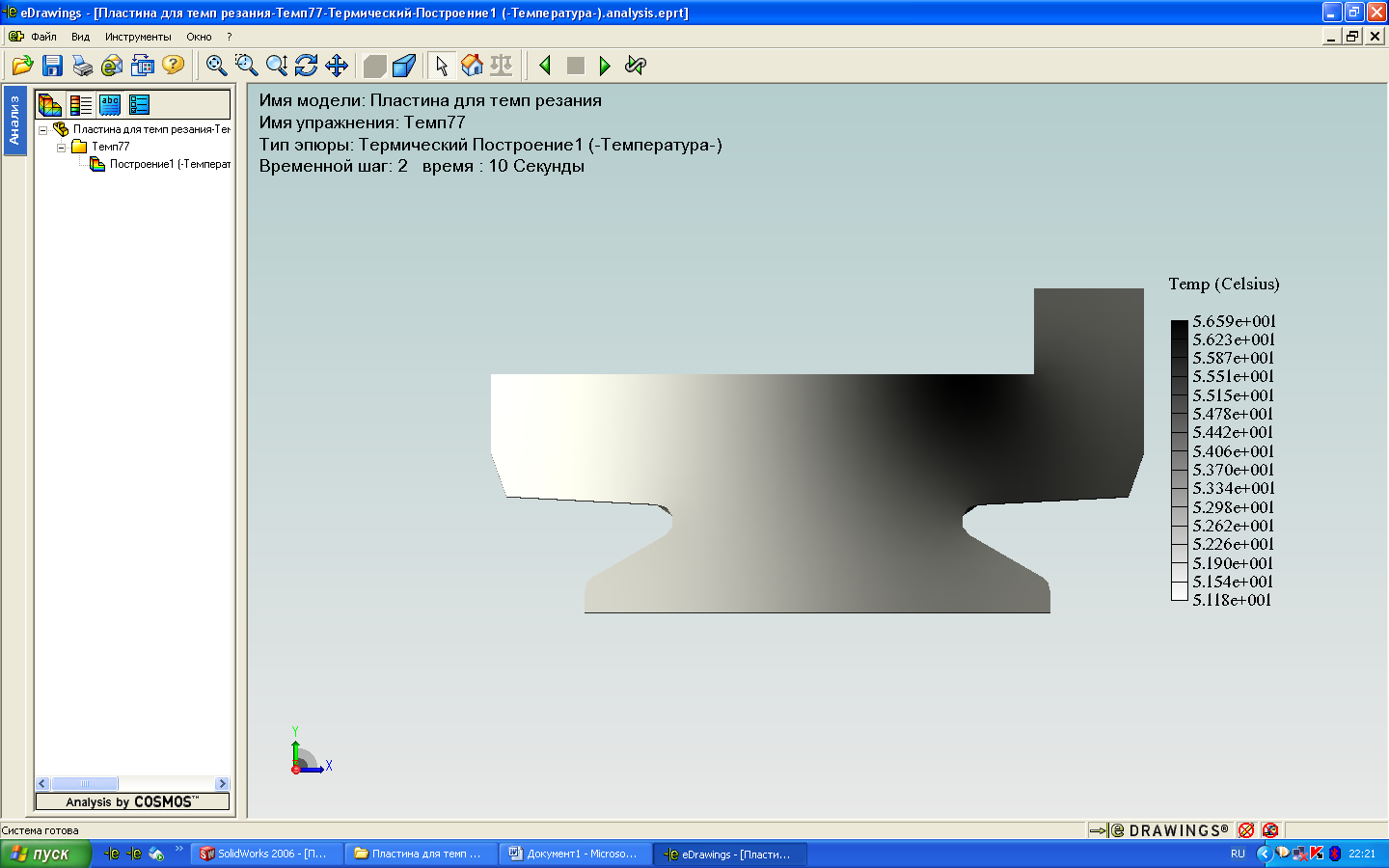
Рис.3. Тепловое поле на момент окончания обработки
Результаты, представленные на рис. 3, показывают, что в связи с высокой теплопроводностью меди тепловой фронт опережает движущийся инструмент. На момент окончания точения первой подобласти следующая подобласть уже имеет температуру около 30ºС, а на момент окончания обработки заготовка прогревается свыше 50ºС.
В связи с образовавшимися в процессе обработки градиентами температуры могут возникнуть существенные тепловые деформации изделия. Для их вычисления необходимо решать задачу определения напряженно-деформированного состояния. Исходными данными будут являться результаты, полученные при решении тепловой задачи. Напряженно-деформированное состояние можно моделировать для любой из решенных тепловых задач.
Однозначность решения обеспечивают следующие граничные условия:
1. Боковые поверхности пластины не имеют возможности перемещения в перпендикулярном направлении. Это ограничение компенсирует связи, имеющиеся в цельной конструкции и отсутствующие в расчетном контуре.
2. Сопрягаемые крепежные поверхности («ласточкин хвост») пластины не имеют возможности перемещения в осевом направлении. Это ограничение компенсирует связи с нажимными конусами, отсутствующими в расчетном контуре.
На рис. 4 и 5 представлены результаты моделирования напряженно-деформированного состояния, соответствующие тепловым полям, представленным на рис. 2 и 3.
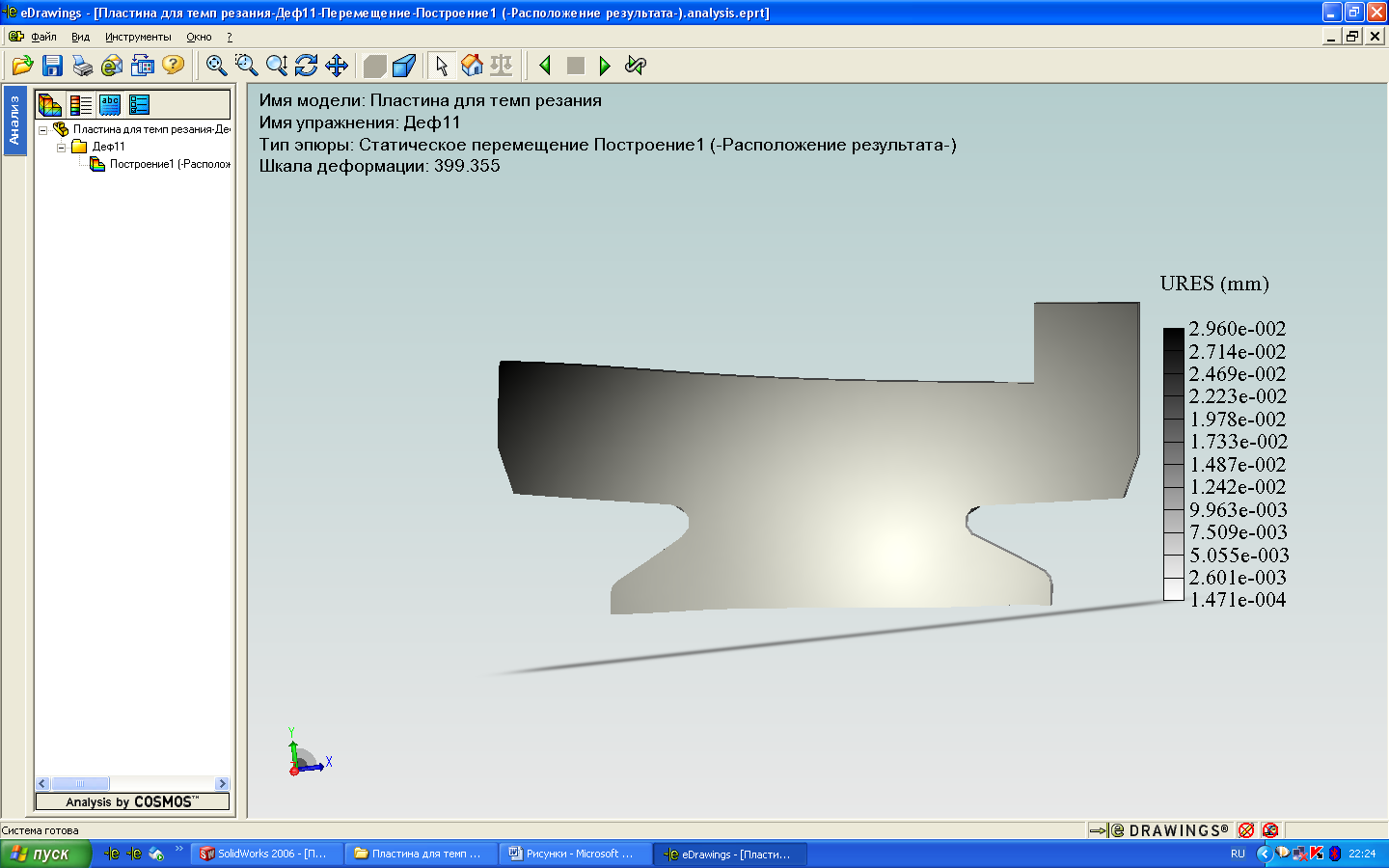
Рис.4. Поле перемещений на момент выполнения точения
первой выделенной области
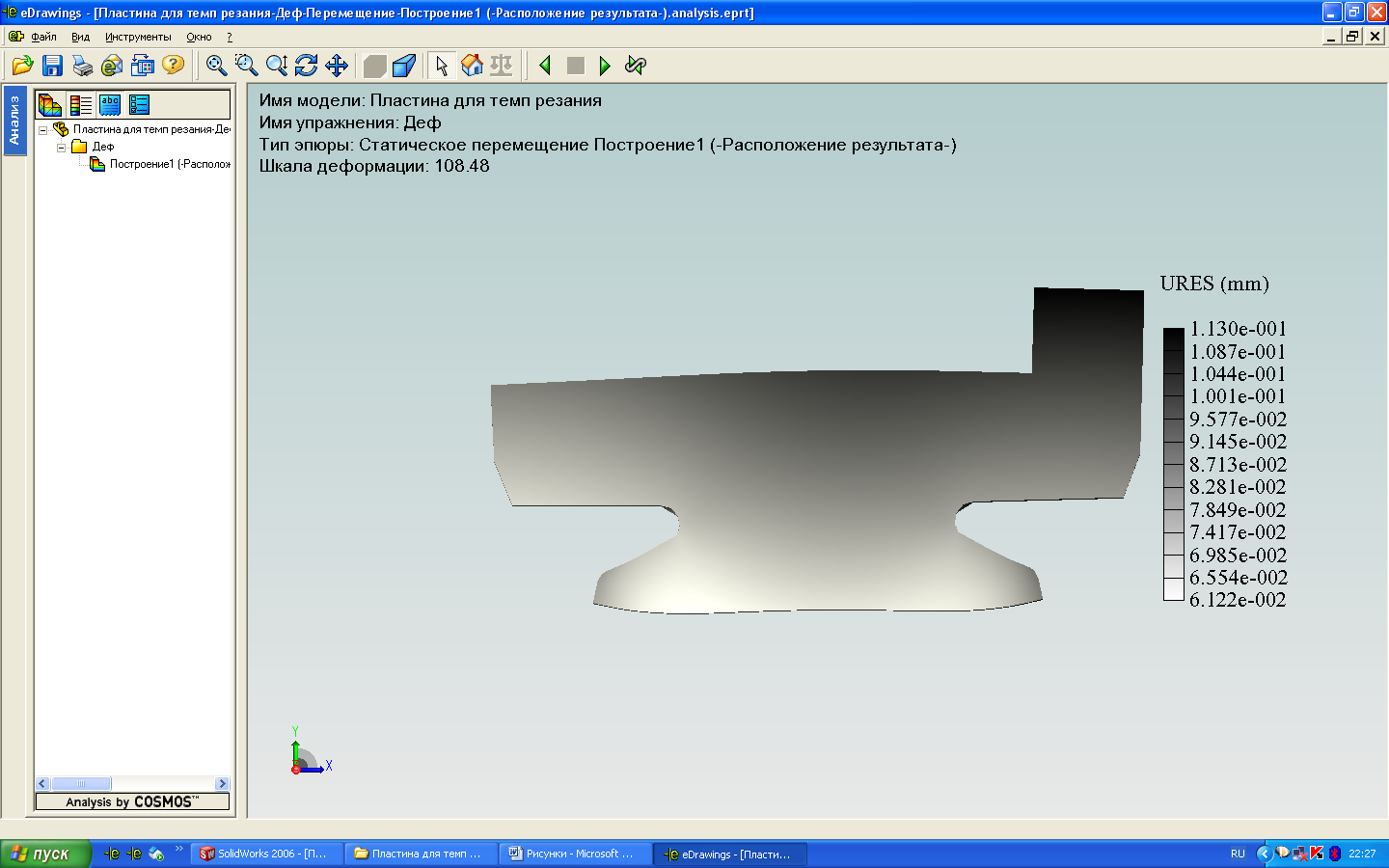
Рис.5. Поле перемещений на момент окончания обработки
Перемещение обрабатываемой поверхности под действием нагрева в начале обработки составляет 12…30 мкм, а в конце обработки достигает 80…100 мкм. В связи с этим может возникнуть погрешность формы обрабатываемой поверхности – конусность. Величина полученной погрешности может удовлетворять только получистовой обработке и неприемлема для окончательной чистовой. Изменяя технологические параметры обработки, можно добиться уменьшения данной погрешности.
Представленная методика позволяет моделировать погрешность от тепловых деформаций в процессе резания и исследовать влияние технологических параметров на ее величину. Используя оптимизацию технологических параметров, можно обеспечивать требуемую точность обработки.
СПИСОК ЛИТЕРАТУРЫ
- 1.Алямовский, А.А. SolidWorks/COSMOSWorks. Инженерный анализ методом конечных элементов/ А.А.Алямовский. – М.: ДМК Пресс, 2004. – 432 с.
- Резников, А.Н. Теплофизика резания/ А.Н. Резников. – М.: Машиностроение, 1969. – 288 с.
Материал поступил в редколлегию 16.04.09.