Процессы эффективного измельчения в агрегатах с инерционным воздействием на разрушаемый материал
Вид материала | Автореферат |
- Лекция почвообразовательный процесс (2 часа), 83.13kb.
- Рекомендовано Минобразованием России для направления подготовки диплом, 100.07kb.
- Рублей работа состоит из 17 страниц, 78.01kb.
- Процессы коррозии происходят неизбежно, самопроизвольно разрушая металлы и их сплавы, 24.14kb.
- Лекция 17 Обработка металла давлением, 249.91kb.
- Информационный материал к единому дню информирования населения на тему «Борьба с коррупцией, 497.7kb.
- Роль стандартизации в развитии электронной техники, 105.64kb.
- Аний по проблеме математического моделирования изменений климата в связи с оценкой, 46.51kb.
- Практикум по рынку ценных бумаг Санкт-Петербург "Питер Пресс", 2614kb.
- Курс уп необходим для получения знаний об эффективном управлении персоналом с целью, 41.52kb.
На правах рукописи
ВАЙТЕХОВИЧ ПЕТР ЕВГЕНЬЕВИЧ
ПРОЦЕССЫ ЭФФЕКТИВНОГО ИЗМЕЛЬЧЕНИЯ В АГРЕГАТАХ С ИНЕРЦИОННЫМ ВОЗДЕЙСТВИЕМ НА РАЗРУШАЕМЫЙ МАТЕРИАЛ
Специальность: 05.02.13 – Машины, агрегаты и процессы
(химическая промышленность)
АВТОРЕФЕРАТ
диссертации на соискание ученой степени
доктора технических наук
Москва - 2011
Работа выполнена в учреждении образования «Белорусский государственный технологический университет»
Научный консультант: (если есть)
Официальные оппоненты: доктор технических наук, профессор
Бобков Сергей Петрович
доктор технических наук, профессор
Севастьянов Владимир Семенович
доктор технических наук, профессор
Тиньков Олег Васильевич
Ведущая организация Тамбовский государственный технический университет, г. Тамбов
Защита состоится «15» сентября 2011 г. В 1400 часов на заседании диссертационного совета Д 212.145.01 при Московском государственном университете инженерной экологии по адресу: г. Москва, ул. Старая Басманная, 21/4, ауд. имени Л.А. Костандова (Л – 207)
С диссертацией можно ознакомиться в библиотеке МГУИЭ
Автореферат разослан « 11 » 05 2011 г.
Ученый секретарь
диссертационного совета
к. т. н, доцент С.А. Трифонов
ОБЩАЯ ХАРАКТЕРИСТИКА РАБОТЫ
Актуальность работы. Процессы измельчения широко используются во многих отраслях промышленности, в том числе и химической. В настоящее время сложились основные тенденции в развитии помольного оборудования. В зависимости от скорости движения рабочих органов все мельницы можно разделить на тихоходные, средне- и быстроходные. Основным помольным агрегатом на отечественных предприятиях до сих пор остается барабанная шаровая мельница, являющаяся с точки зрения механики тихоходной машиной. Это металлоемкий агрегат с высокими энергозатратами на проведение процесса помола.
Анализ современного состояния технологии и техники дезинтеграции показывает, что указанные недостатки преодолимы при использовании в производстве средне- и быстроходных измельчителей. Они отличаются более высокими скоростями движения рабочих органов, а, соответственно, и измельчаемого материала. При этом возникают инерционные силы, существенно превышающие гравитационную и становящиеся основным силовым фактором разрушения материалов. В таких агрегатах значительно повышается интенсивность процесса диспергирования и требуемая производительность может быть достигнута при уменьшении рабочего объема. А это в свою очередь приводит к снижению металло- и энергоемкости измельчающих машин. Подобный эффект может быть достигнут и при использовании диспергаторов, принцип действия которых основан на разрушающих физических эффектах.
Существенный вклад в развитие теории дезинтеграции внесли отечественные специалисты Ребиндер П.А., Ходаков Г.С., Ревнивцев В.И. Конструктивным совершенствованием, разработкой методик расчета, в том числе и быстроходных измельчающих агрегатов, успешно занимались и занимаются Сиденко П.М., Андреев С.Е., Хинт Н.А., Блиничев В.Н., Богданов В.С. и другие. Коллективами под их руководством выполнен значительный объем научных исследований по проблемам измельчения материалов. Однако эти исследования носят в основном разрозненный характер, направлены на решение отдельных специфических задач для конкретных технологических процессов. Отсутствуют научно обоснованные предложения по выбору рационального способа воздействия на материал для получения продукта требуемой дисперсности с минимальными энергозатратами. Нет общего подхода к определению значения силовых факторов в измельчителях различных типов и оценке влияния инерционных сил на их величину, что особенно важно для средне- и быстроходных машин. Не установлено связи между интенсивностью воздействия рабочих органов на разрушаемый материал и эффективностью самого процесса разрушения.
Поэтому комплексные исследования среднеходных и быстроходных мельниц, поиск общих закономерностей процессов, реализуемых в них, общих подходов к расчету таких агрегатов с обязательным учетом энергетики и эффективности измельчения представляется весьма актуальной задачей.
Работа базируется на обобщении результатов личных исследований автора, полученных при выполнении ряда госбюджетных и хоздоговорных тем кафедры машин и аппаратов химических и силикатных производств: Государственной программы ориентированных фундаментальных исследований (ГПОФИ) «Строительство и архитектура», утвержденной постановлением Совета Министров Республики Беларусь, от 17.05.2005г. №512 задание 29 «Разработка теоретических основ процесса диспергирования материалов в агрегатах раздавливающего типа с проточной классификацией и создание на их основе энергоэффективных помольных установок» (ГБ 26-103, № гос. регистрации 20064128, 2006−2010 гг.); по темам, включенным в план НИР БГТУ: ГБ 98-018 «Исследование процесса разрушения твердых материалов в жидкой среде под воздействием кавитации» (№ гос. регистрации 19981012, 1998−1999 гг.); ГБ 20-029 «Исследование, моделирование и оптимизация процессов диспергирования и механической активации твердых материалов» (№ гос. регистрации 2000940, 2000-2001 гг.); по прямым заказам предприятий на хоздоговорной основе: ХД 24-066, 2004 г. и ХД 27-167, 2007 г.
Целью исследований является развитие научных основ совершенствования процессов измельчения и оптимизации измельчающих агрегатов в направлении повышения их эффективности и снижения удельных энергозатрат.
Для достижения поставленной цели необходимо:
- провести анализ теорий разрушения и дезинтеграции материалов и на его основе определить направления совершенствования измельчающих агрегатов и выбрать в качестве объектов исследования наиболее перспективные из них, обеспечивающие возможность значительного повышения эффективности; установить общий критерий оценки воздействия рабочего органа на разрушаемый материал;
- составить математические модели движения материальных потоков и рабочих органов измельчающих машин и с их использованием установить оптимальные конструктивные и технологические параметры этих машин; разработать методы и алгоритмы расчета оптимальных параметров;
- провести экспериментальные исследования измельчителей для определения направлений их рационального использования, проверки адекватности математических моделей, оптимизации параметров, не подлежащих математическому описанию;
- на основе разработанных методов и алгоритмов провести расчет и спроектировать измельчающие агрегаты с оптимальными конструктивными и технологическими параметрами; осуществить опытно-промышленные испытания и внедрение в производство оптимизированных агрегатов.
Объектом исследования в работе выбраны среднеходные и быстроходные измельчающие агрегаты и диспергатор кавитационного типа, объединенные одним характерным признаком − значительным влиянием инерционным сил на процесс измельчения материала.
Предметом исследования является движение рабочих органов машин, измельчаемого материала и несущей среды (воздуха, воды); процессы измельчения и классификации, эффективность и энергетика процессов; оптимизация процесса и параметров измельчающих машин.
Научная новизна.
- Разработана новая обобщенная методология исследований и оптимизации параметров высокоскоростных измельчающих агрегатов, основанная на изучении движения рабочих органов, несущей среды, измельчаемого материала и учете влияния инерционных сил на процесс его разрушения.
- Предложено математическое описание и алгоритм расчета траектории движения материала в зоне измельчения среднеходных мельниц тарельчатого типа с учетом активных и инерционных сил, позволяющий определить оптимальную скорость вращения тарелки из условия гарантированного попадания материала под размольные органы, обеспечивающую повышение эффективности процесса измельчения.
- Разработана модель разрушения материала между валком и тарелкой, учитывающая изменение степени измельчения и удельной поверхности при однократном воздействии, позволяющая рассчитать работу разрушения с учетом физических свойств материала и в совокупности с экспериментально определенными затратами на выгрузку готового продукта определить и оптимизировать общие энергозатраты на процесс измельчения в среднеходных мельницах.
- Составлена модель и математическое описание помола в замкнутом цикле для мельниц непрерывного действия в виде функций нескольких переменных, включающих такие важные параметры, как производительность, степень измельчения, кратность циркуляции, дисперсность продукта, позволяющая с использованием метода нелинейного программирования установить оптимальные значения указанных параметров.
- Предложен метод определения коэффициента загрузки ударных мельниц, основанный на решении уравнений движения частиц исходного продукта в загрузочном устройстве и в пространстве перед ударными элементами, позволяющий рассчитать максимально возможную производительность в зависимости от размеров мельницы и загружаемого в нее продукта.
- Предложена физическая модель перемещения элементов загрузки, методика определения наиболее рациональной высоты размольной камеры центробежно-шаровой мельницы, базирующаяся на решении дифференциальных уравнений движения мелющих тел и частиц измельчаемого материала с учетом их взаимодействия; методика определения высоты размольного барабана вертикальной планетарной мельницы, основанная на анализе движения измельчающих тел и загрузки, имитированной в виде сплошной среды.
- Разработан комплекс теоретических методов по определению границ режимов движения, условий отрыва, высоты падения мелющих тел, границ характерных зон загрузки в горизонтальных планетарных мельницах, с учетом взаимодействия между телами и цикличности изменения инерционных сил, позволяющих при их реализации устанавливать и поддерживать оптимальные режимы, давать оценку влияния ударного, раздавливающего и истирающего воздействий на процесс разрушения материала, оценивать степень влияния механики движения загрузки и инерционных сил на эффективность помола.
- Предложена методика и алгоритм расчета параметров каверны и длины свободного пробега кавитационных пузырьков, базирующаяся соответственно на теореме об изменении кинетической энергии потока и уравнении динамики сферической каверны, позволившие определить оптимальные размеры гидродинамических кавитационных диспергаторов, гарантирующие предотвращение их эрозионного разрушения и обеспечивающие максимальное разрушающее воздействие на измельчаемый материал.
Практическая значимость работы. Предложен общий для всех объектов исследования инерционный фактор, позволяющий оценить влияние инерционных сил, а соответственно, и скоростного режима на дисперсность продукта. Научно обосновано создание новых более эффективных конструкций измельчителей, защищенных патентами Республики Беларусь. Разработан комплекс методов и алгоритмов расчета оптимальных конструктивных и технологических параметров средне- и быстроходных измельчителей и диспергаторов кавитационного типа. Все методы апробированы при проектировании промышленных агрегатов, девять из которых внедрены в производство, два прошли промышленные испытания и ещё по двум разработаны технические проекты, переданные заказчику.
Апробация работы. Наиболее значимые результаты диссертационной работы, отражающие ее сущность, докладывались на следующих Международных научно-технических конференциях: «Высокие технологии и научно-технический прогресс в строительном комплексе Республики Беларусь» (г. Минск, 1999г.), «Интерстроймех-2002» (г. Могилев, 2002г.), «Новые технологии в химической промышленности» (г. Минск, 2002г.), «Архитектурно-строительное материаловедение на рубеже веков (г. Белгород, 2002г.), «Новейшие достижения в области импортозамещения в химической промышленности и производстве строительных материалов» (г. Минск, 2003г.), «Центробежная техника – высокие технологии» (г. Минск, 2003г.), «Новые технологии рециклинга отходов производства и потребления» (г. Минск, 2004г), «Центробежная техника – высокие технологии» (г. Минск, 2005г.), «Наука та технологіі: крок в майбутне» (г. Днепропетровск, 2007г.), «Научни дни-2008» (г. София, 2008г.), «Ресурсо- и энергосберегающие технологии и оборудование, экологически безопасные технологии» (г. Минск, 2008г.); “Moderni vymozenosti vedi - 2009” (Praha, 2008г.), “Настоящи изследвания - 2009” (София, 2008г.), “Perspektywiczne opracowania sa nauka i technikami - 2009” (Przemysl, 2009г.), “Новейшие достижения в области импортозамещения в химической промышленности и производстве строительных материалов” (Минск, 2009г.), “Ресурсо- и энергосберегающие технологии и оборудование, экологически безопасные технологии” (Минск, 2010 г.), 13 научно-технических конференциях БГТУ (1998-2010гг.).
Опубликованность результатов диссертации. По теме диссертации опубликованы 73 работы, в том числе 1 монография, 44 статьи (аннотированных ВАК России – 15, ВАК Беларуси – 14), материалы и тезисы 21 конференции, 7 описаний изобретений к патентам Республики Беларусь. Без соавторства опубликована 1 монография, 3 статьи, материалы 2 конференций.
Структура и объем работы. Диссертация (344 с) включает перечень условных обозначений, общую характеристику работы, основную часть, изложенную в 7 главах, заключение и библиографический список (27 с), состоящий из 275 использованных источников и 73 собственных публикаций соискателя. Приложение (32 с) содержит документы, подтверждающие практическое применение результатов исследований. Результаты исследований изложены на 198 с печатного текста и представлены на 144 иллюстрациях (130 с) и в 2 таблицах (2 с).
СОДЕРЖАНИЕ РАБОТЫ
В первой главе приведены результаты анализа развития теорий разрушения и дезинтеграции. Установлено, что ни одна из них не ответила на главный вопрос о взаимосвязи между дисперсностью продукта и энергетикой процесса и не представила конкретных зависимостей для расчета энергозатрат в реальных измельчающих агрегатах. Практическая значимость этих теорий заключается в том, что проанализированы основные стадии разрушения материалов, установлены факторы, влияющие на дисперсность продукта, определена доля энергии, затрачиваемая на каждой из стадий. Это позволило наметить пути снижения энергозатрат и выбрать рациональные способы воздействия, обеспечивающие это снижение. Таковыми, например, для тонкого измельчения являются раздавливание и удар. Однако для процессов сверхтонкой дезинтеграции, доведения частиц до наноразмеров приходится прибегать к более затратному способу, такому как истирание.
С учетом современных тенденций развития техники и технологии дезинтеграции в качестве объектов исследования выбраны средне- и быстроходные измельчители и кавитационный диспергатор с закруткой потока, характеризующиеся значительным влиянием инерционных сил на разрушение материала. Разработана новая методология исследования и оптимизации параметров выбранных объектов, основанная на комплексном изучении движения рабочих органов, несущей среды и измельчаемого материала. Такой подход дает возможность определить величину и направление действия разрушающих усилий в момент контакта рабочего органа с измельчаемым материалом. Для учета влияния инерционных сил введен обобщающий инерционный фактор, представляющий собой отношение модуля векторной суммы всех инерционных сил к силе тяжести Φ=
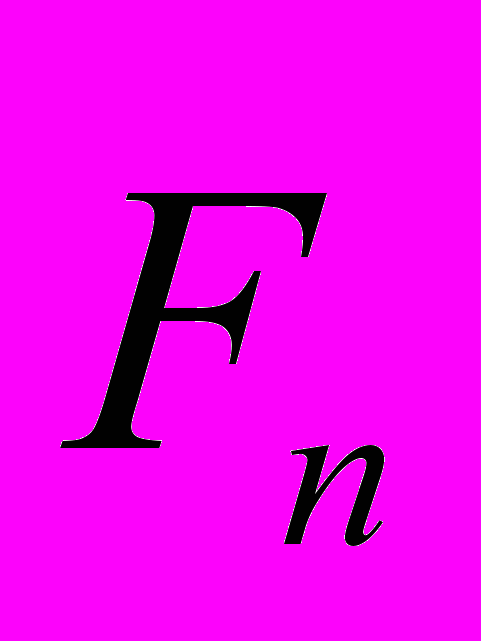
Во второй главе приводятся результаты теоретических и экспериментальных исследований среднеходных валковых мельниц. Скорость движения рабочих органов в них составляет несколько метров в секунду. Поэтому инерционные силы не настолько велики, чтобы создать в материале напряжения близкие к разрушающим. Его разрушение осуществляется за счет давления размольного валка. В свою очередь инерция является основной движущей силой при транспортировке материала во всех зонах измельчающего агрегата. Траектория и скорость движения материала на подходе к валку существенно влияют на его раздавливающую способность, а на выходе с тарелки – на условия сепарации частиц. Кроме того, эффективность измельчения, энергетика процесса зависят от кратности циркуляции материала по замкнутому контуру, которая непосредственно связана со скоростью его движения. Всё это свидетельствует о необходимости исследования движения частиц материала в различных зонах среднеходной мельницы.
П
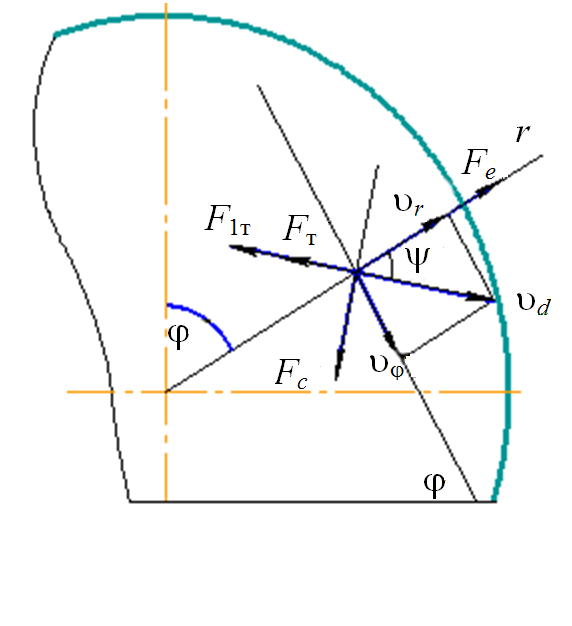

г
Рисунок 1 – Расчетная схема движения частиц по тарелке
де z – осевая координата, м; f0 – коэффициент внутреннего трения материала; ω – угловая скорость тарелки, рад/с; r – текущий радиус, м; r0 – предельный радиус равновесия (r0 = f0g/2), м.
Расчет проводился до значения осевой координаты равной среднему размеру загружаемых в мельницу кусков, что соответствует их распределению в виде монослоя. Дальнейшее перемещение измельчаемого материала по тарелке рассматривалось как движение одиночных частиц, рисунок 1. Составлены уравнения относительного движения частиц в подвижной полярной системе координат. С учетом инерционных кориолисовой и центробежной сил, силы трения материала по тарелке и впервые учтенной силы трения между частицами получили уравнения движения (2).
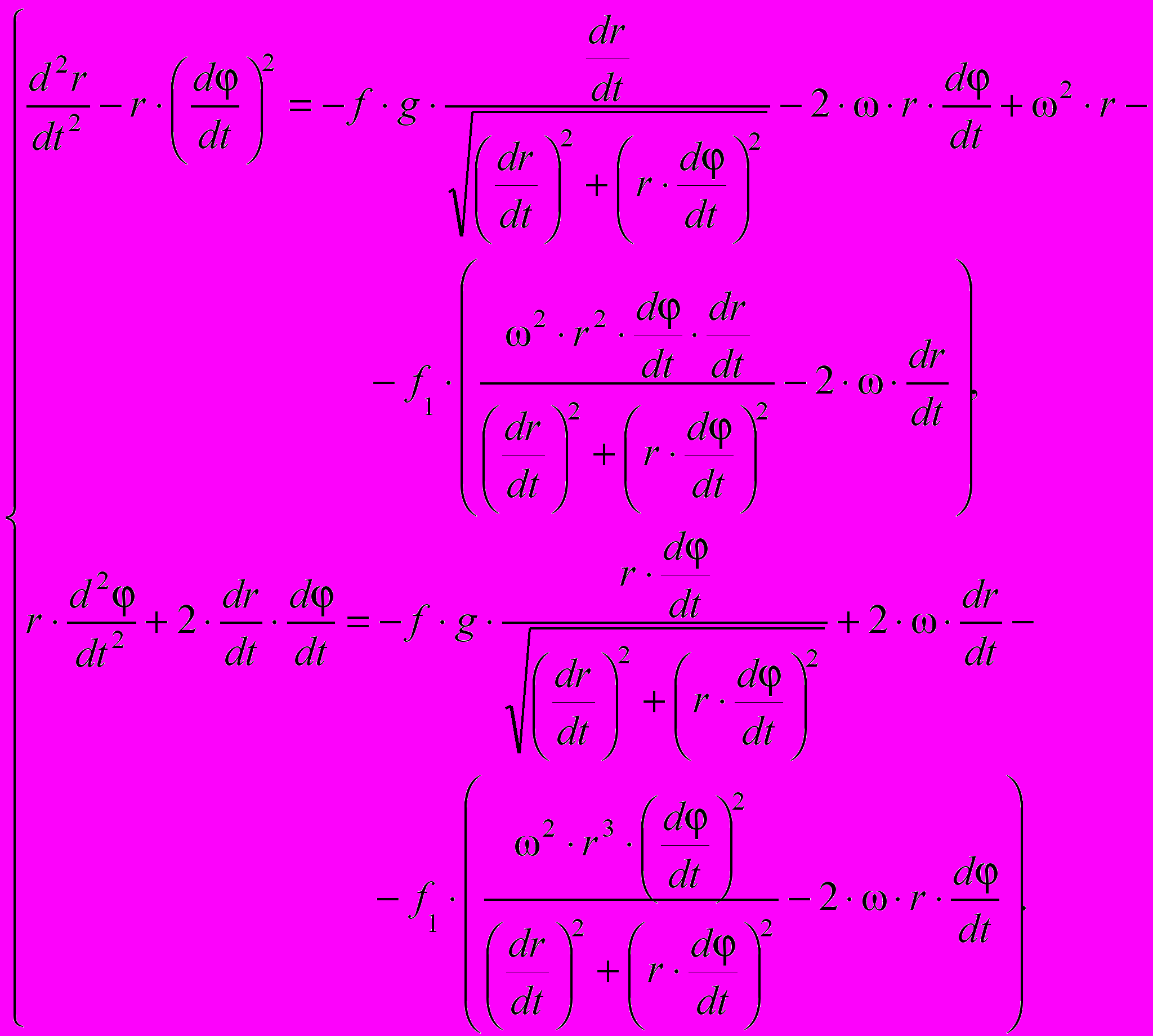
(2)
где r; φ – текущие координаты частицы в полярной системе; ω – угловая скорость тарелки (скорость переносного движения), рад/с; f – коэффициент трения частиц о тарелку; f1 – коэффициент взаимного трения между частицами.
Решение этой системы уравнений численными методами позволило реализовать две важные задачи. Во-первых, определить скорость и траекторию движения частицы на выходе с тарелки. Во-вторых, установить оптимальный диапазон частот вращения тарелки из условия гарантированного попадания материала под размольные валки. Это условие заключается в том, что радиальное перемещение частиц материала за время t = 1/zn, где n – частота вращения тарелки, мин-1, z – количество валков, не должно превышать ширины валка Δr B. Инерционный фактор при движении по тарелке изменялся в пределах Φ=210.
На выходе с вращающейся тарелки измельченный материал подхватывается воздухом и выносится в сепарационную зону. Здесь важно не допустить соприкосновения частиц со стенками корпуса над кольцевым зазором. В противном случае будет наблюдаться провал материала под тарелку. Поэтому возникла необходимость изучения траектории движения частиц материала под воздействием газового потока. Причем для обеспечения равномерного распределения воздуха в кольцевом зазоре он подавался в корпус мельницы тангенциально, приобретая при этом форму закрученного потока. Движение частиц в таком потоке характеризуется тремя составляющими: радиальной – r, тангенциальной – и осевой – z.
В проекциях на оси цилиндрической системы координат уравнения движения твердых частиц в закрученном потоке примут вид:
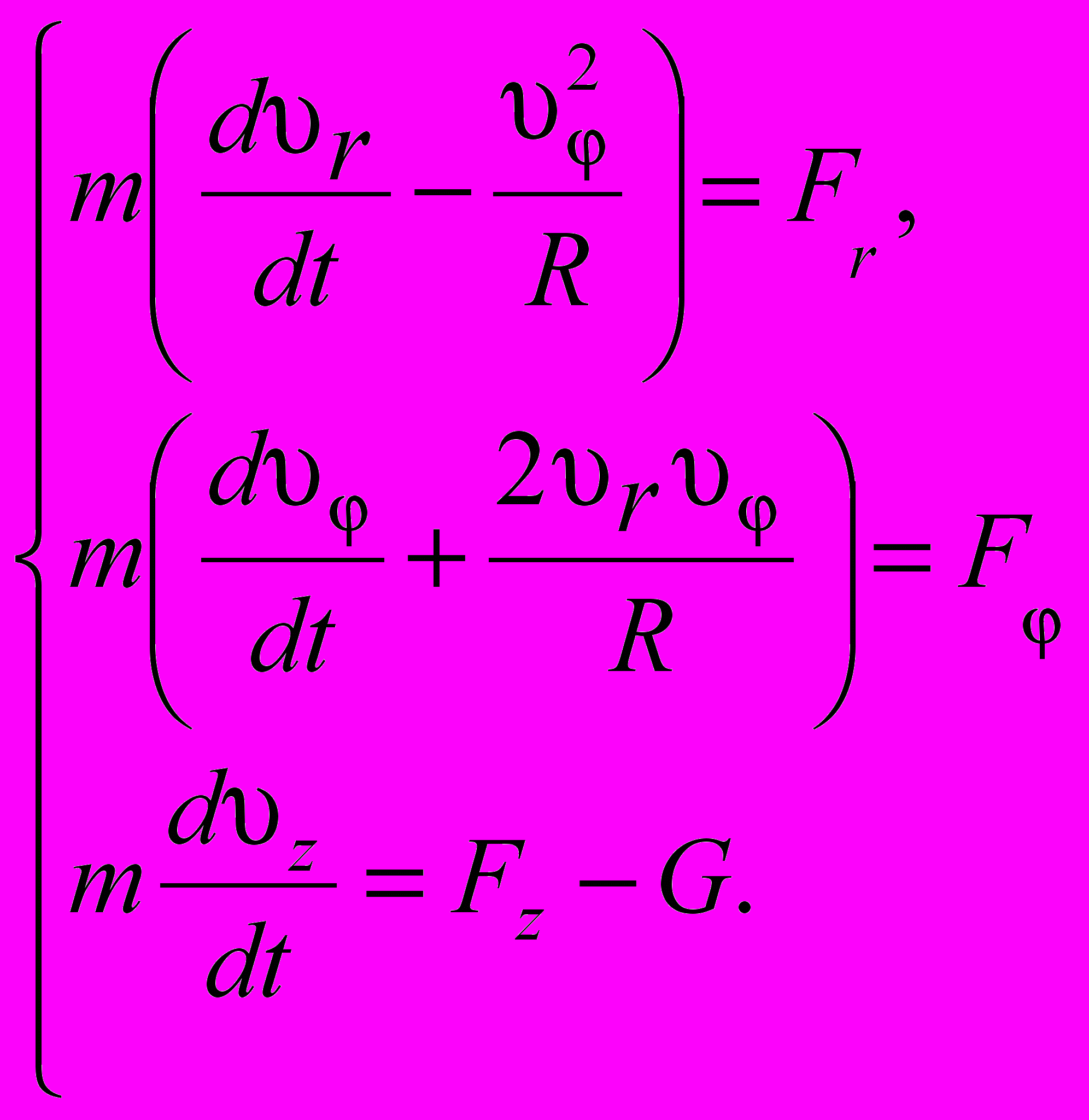
где m – масса частицы; R – текущий радиус; G – сила тяжести частицы; Fr, Fφ, Fz – проекции силы аэродинамического воздействия на оси цилиндрической системы координат.
Сила аэродинамического воздействия воздуха определялась по следующей формуле:

где ui − скорость воздушного потока в данной точке кольцевого зазора, м/с; – плотность воздуха, кг/м3; d –диаметр частицы, м; kф – коэффициент формы частицы.
Так как объемная концентрация твердой фазы в потоке с≤0,02, то коэффициент аэродинамического сопротивления рассчитывался по формуле: ξ = 24(1+0.17 Re 2/3) / Re.
Величину скорости газового потока в зоне кольцевого зазора определили экспериментально с помощью трехканального зонда. Экспериментальные данные аппроксимированы выражениями:

(5)

Решая систему уравнений (3) численными методами с помощью ЭВМ и с учетом уравнений (5), определили значения координат и составляющих скорости движения измельченных частиц в сепарационной зоне. Координаты местонахождения частиц в газовом потоке стали отправным пунктом для расчета и конструирования сепарационного устройства, предотвращающего возможные их соприкосновения со стенками корпуса с последующим провалом под тарелку. Это устройство представляет собой усеченный конус с тороидальным кольцом в верхней части.
Важным параметром для среднеходных мельниц, как и для других, являются удельные энергозатраты на проведение процесса измельчения. В тех немногочисленных работах, в которых исследовались энергозатраты для указанных агрегатов, не сделано даже попытки связать их с теоретическими аспектами разрушения и дезинтеграции.
Для оценки работы разрушения автором использовалось уравнение Ребиндера, которое имеет вид:
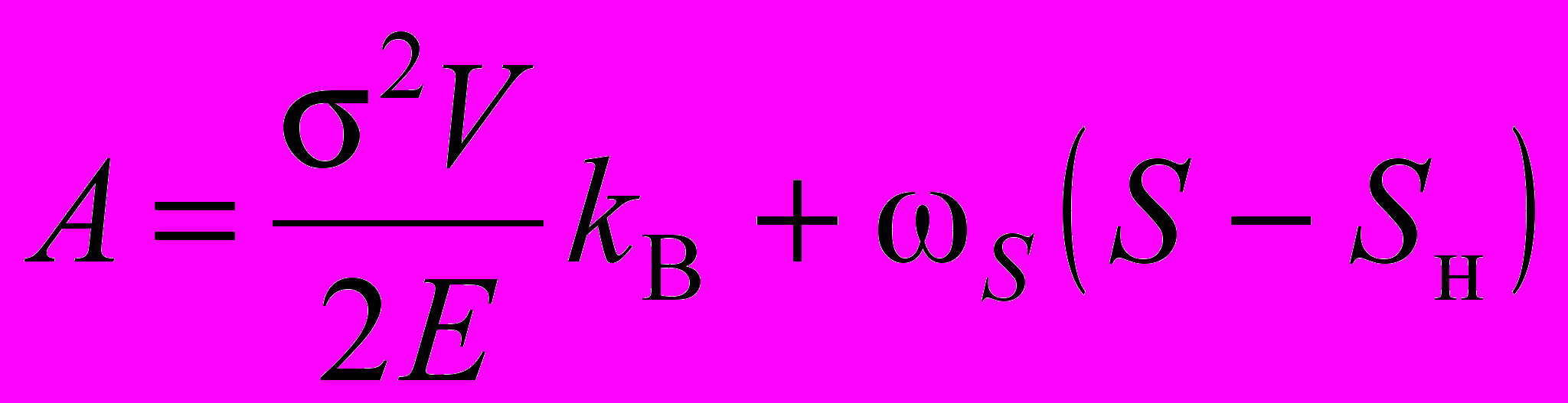
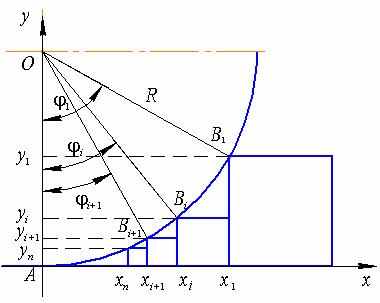
где σ, Е – предел прочности и модуль упругости материала, Па; kВ кратность воздействия; ωS – удельная поверхностная энергия, Дж/м2; Sн, S начальная и текущая поверхности измельчаемого материала, м2.
П
Рисунок 2 − Схема воздействия валка на материал
редставим процесс разрушения материала между валком и тарелкой как многоцикловой, при котором кубики размером y1 постепенно уменьшаются до yп. Тогда кратность воздействия определяется количеством кубиков, разместившихся между плоскостью тарелки (ось х) от x1 до xn и дугой АВ1 окружности валка.
Координаты любой точки соприкосновения определяются по формулам xi = Rsini; yi = R − Rcosi. При этом должно выполняться условие xi − xi+1 = yi+1. Для любой последующей точки контакта можно записать:
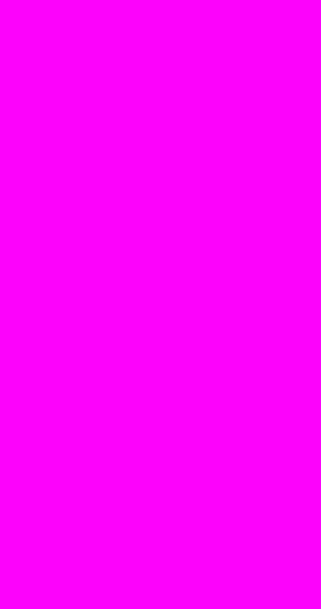
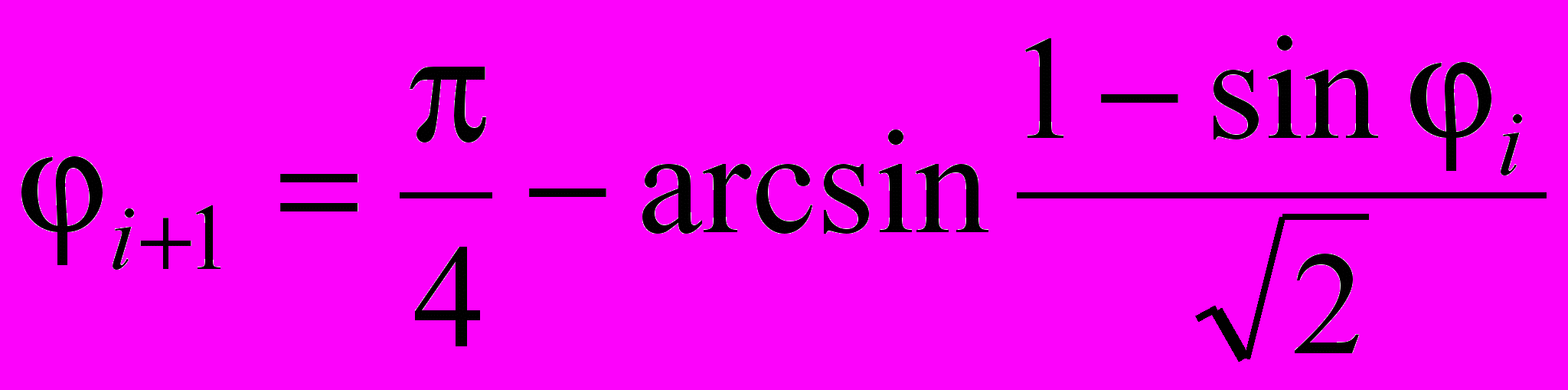
Рассчитав таким образом поверхность при каждом цикле воздействия, определим конечную поверхность Sn, соответствующую yn, и определим работу разрушения по уравнению (6).
Полная работа за один оборот
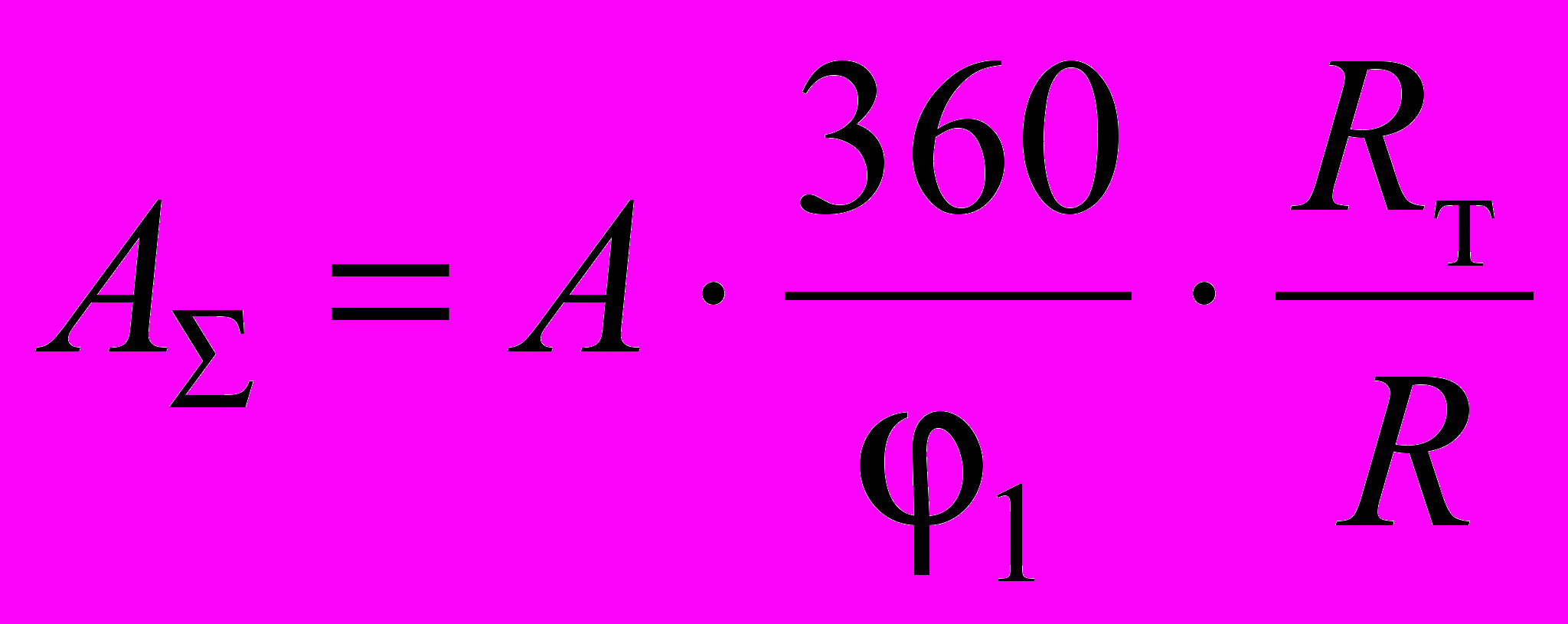
где Rт – радиус беговой дорожки тарелки; R – радиус валка, м.
М
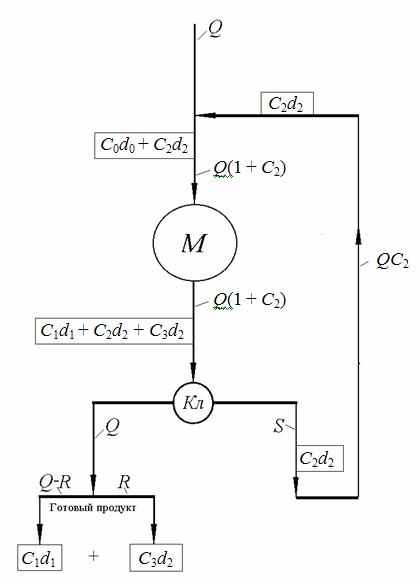
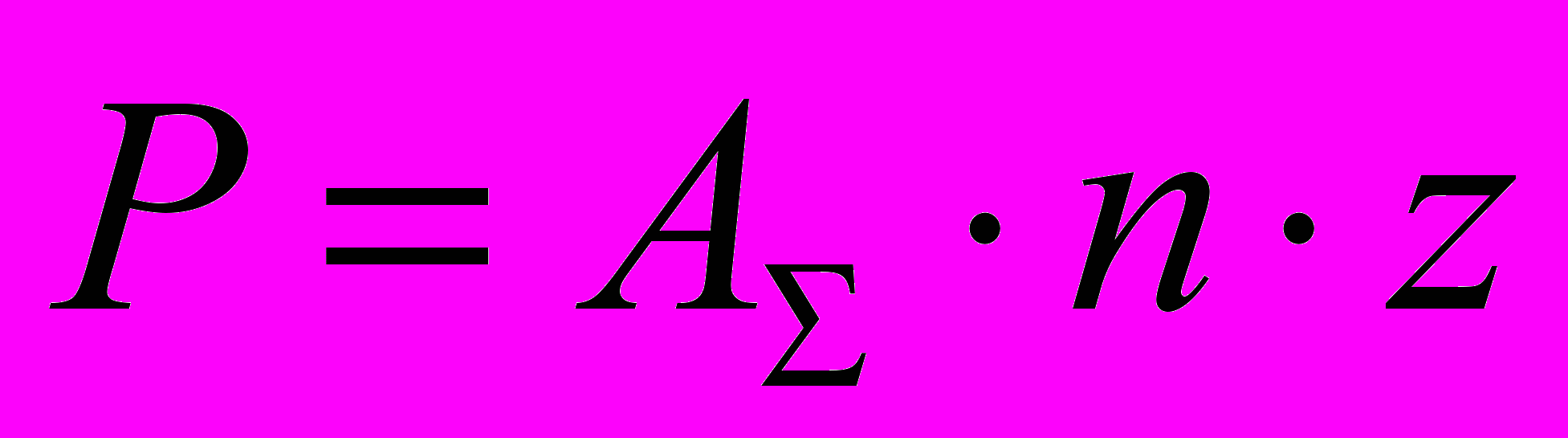
В
Рисунок 3 − Модель замкнутого цикла среднеходной мельницы
торой важной составляющей общих энергозатрат в мельнице данного типа являются затраты на пневмотранспорт измельченного продукта, которые зависят прежде всего от гидравлического сопротивления всего агрегата вместе с сепаратором. Экспериментально определено гидравлическое сопротивление в зависимости от скорости газа на полное сечение мельницы и угла установки лопастей проходного сепаратора. Установлено, что в оптимальном скоростном режиме и угле открытия лопастей 20−30˚ гидравлическое сопротивление мельницы не превышает 1000 Па и энергозатраты на пневмотранспорт втрое меньше чем на разрушение материала валками. Общие энергозатраты без учета системы аспирации и подачи материала в мельницу не превышают 10 кВт · ч/т, что сопоставимо с зафиксированными в промышленных условиях.
Одновременно с энергозатратами оценивалась и эффективность измельчения по величине удельной поверхности. Приемлемую для производственных условий удельную поверхность 2500–3500 см2/г можно получить при угле установки лопастей 30–35º. Но с уменьшением угла удельная поверхность может быть доведена до 5000–6000 см2/г.
Важным для среднеходных мельниц, работающих в замкнутом цикле, является оптимизация параметров этого цикла: степени измельчения, эффективности сепарации, кратности циркуляции материала, производи-тельности мельниц и др. В работе предложена схема замкнутого цикла (рису-нок 3) и ее математическое описание. Согласно данной схемы эффективность сепарации Е = С2 / С2 + С3, где С2 – доля циркулирующей загрузки, С3 – доля крупной фракции в готовом продукте.
Для определения степени измельчения с учетом эффективности сепарации получено уравнение:
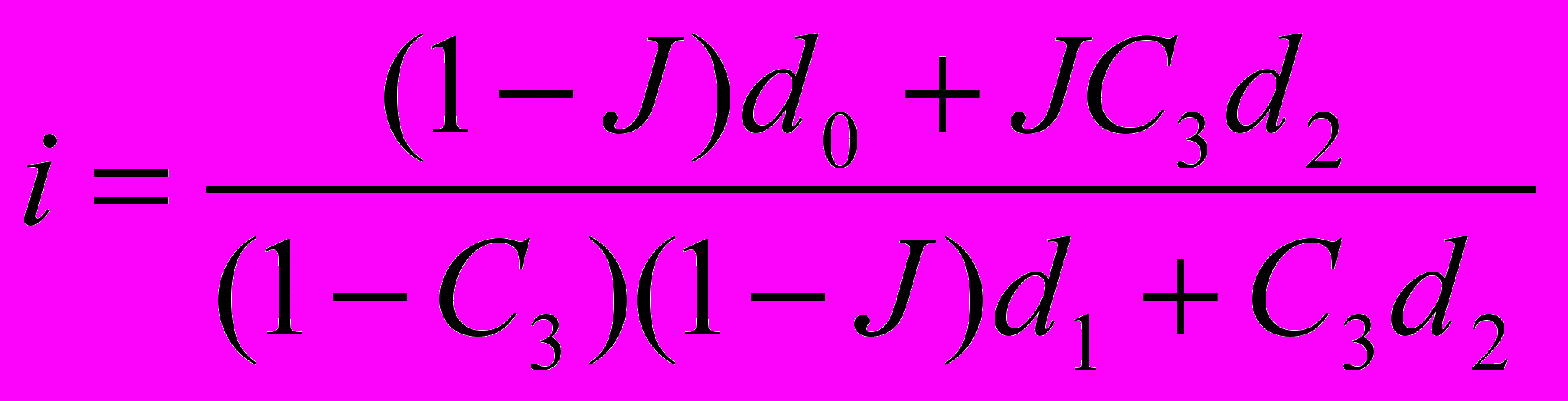
Таким образом, получена зависимость целевой функции i в явном виде от пяти параметров. Задача решена методами нелинейного программирования и установлены оптимальные параметры для достижения максимальной степени измельчения.
Однако степень измельчения − это качественный показатель, и его недостаточно для проведения полного анализа работы мельницы. Необходим учет количественных показателей, главным из которых является производительность. Для расчета производительности среднеходной валковой мельницы можно использовать следующую зависимость:
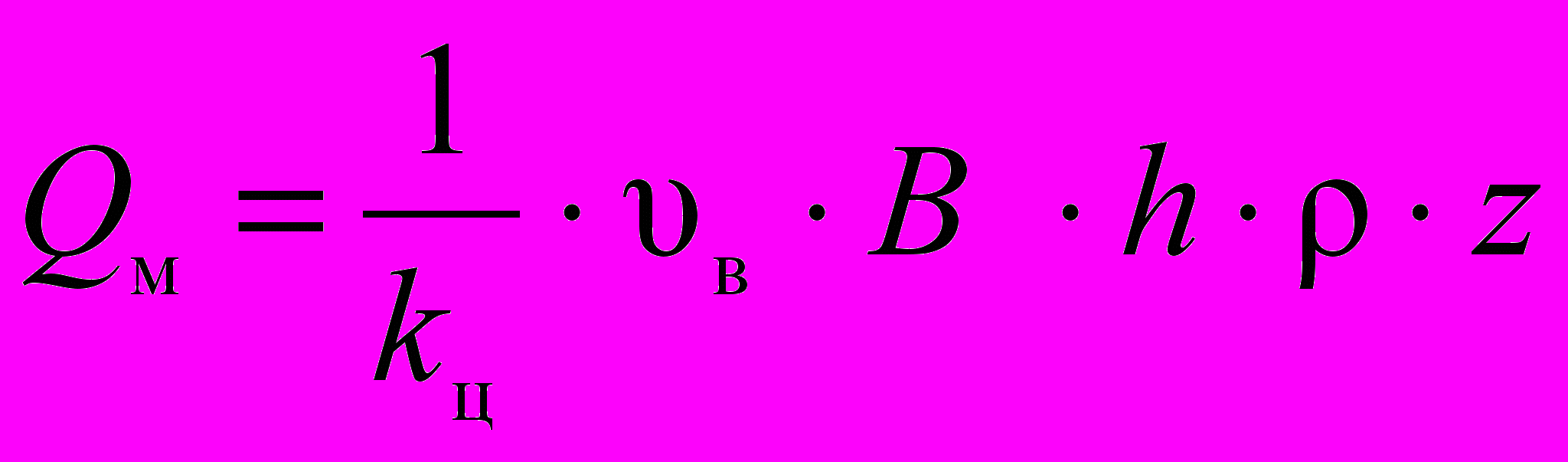
где kц – кратность циркуляции; в – окружная скорость валка, м/с; B – ширина валка, м; h – толщина слоя материала под валком, м; – плотность материала, кг/м3; z – число валков.
Кратность циркуляции можно определить исходя из общего количества циклов воздействия на материал до его полного разрушения. Это количество циклов k определяется по следующей формуле: k = 3∙lg(i) / lg(a), где а –объемная степень измельчения при однократном воздействии. В свою очередь, для среднеходной валковой мельницы общее количество циклов равно k = kц · kв, где kв – количество циклов воздействия валка на материал за один проход его по тарелке мельницы. С точки зрения оптимизации по разработанной схеме, все параметры, кроме кратности циркуляции, можно считать постоянными величинами. Обозначим их константой , и окончательно формула для производительности примет вид
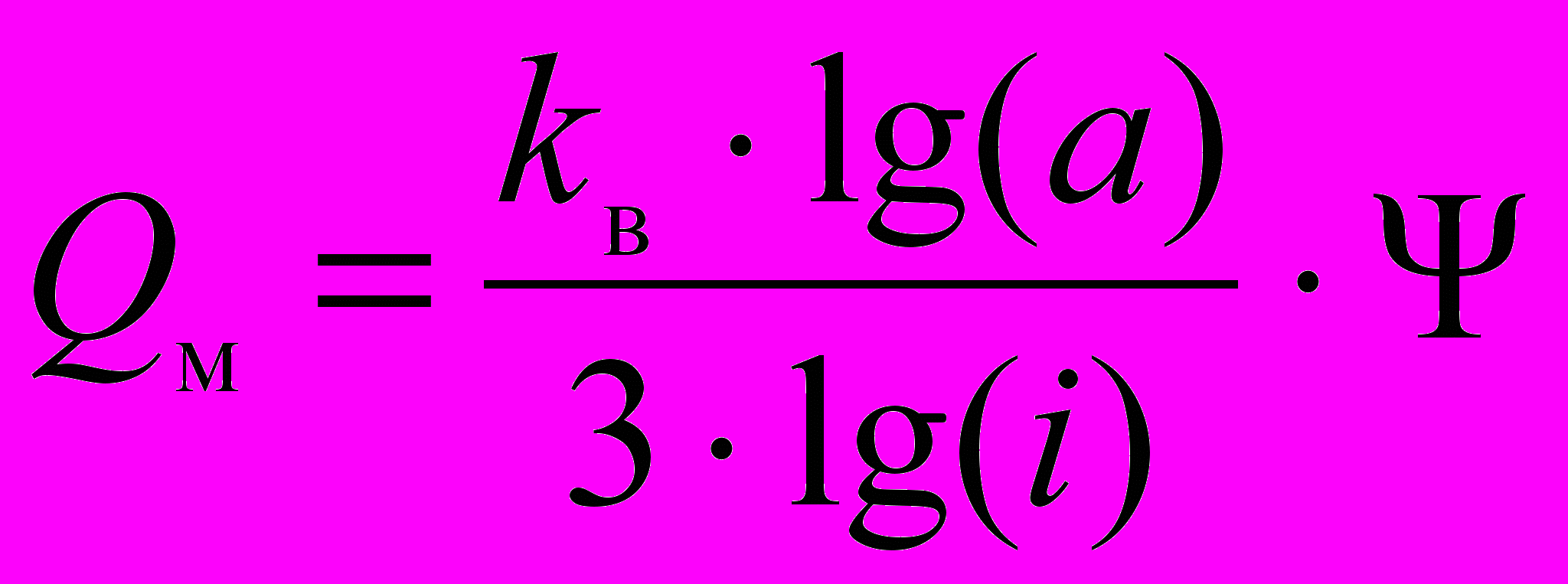
Апробация предложенного метода проведена для оптимизации параметров полупромышленной валковой мельницы. При решении поставленной задачи с помощью ЭВМ была найдена максимальная производительность Qм = 370 кг/ч помольного агрегата при оптимальном значении кратности циркуляции kц = 6. При этом степень измельчения достигала i = 70.
Третья глава посвящена изучению процесса измельчения в мельнице ударного действия дезинтеграторного типа. Проведена оценка разрушающей способности по величине инерционного фактора. Разрушение материала в случае прямого удара начнется при Φ≥50, что говорит о значительно большем влиянии инерционных сил на процесс измельчения в мельницах ударного действия по сравнению со среднеходными. Эффективное измельчение происходит при Φ≥180, а для механической активации его значение должно быть Φ≥300.
Определены преимущества многорядного бильного измельчителя перед другими ударными мельницами и намечены направления его использования. Одним из них является механическая активация, в частности вяжущих веществ. Проведена обработка цемента марки М400 в дисмембраторе, показавшая увеличение удельной поверхности цемента с 2500 см2/г до 4700 см2/г. Образцы, сформованные из активированного цемента, показали увеличение прочности на 30−35% во все сроки твердения. При достижении равнопрочности образцов расход активированного цемента на 15% ниже чем обычного.
Н
Рисунок 4 − Изменение гранулометрического состава бетаина гидрохлорида: 1 – исходный; 2 – 4 – после обработки в дисмембраторе при скорости 10, 25, 50 м/с соответственно
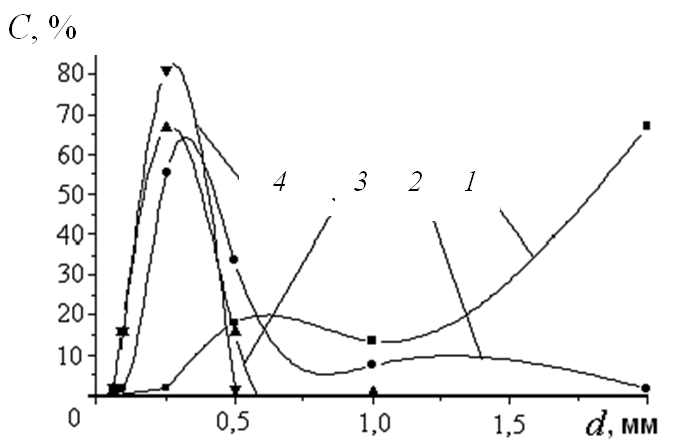
В связи с этим предложено две конструкции дисмембраторов, защищенных патентами Республики Беларусь, с компактным встроенным классификатором. Пробные опыты по измельчению материала отмечены устойчивой работой дисмембратора с классифицирующей камерой в широком диапазоне скоростей и значительным увеличением удельной поверхности готового продукта.
При загрузке материала в дисмембратор в виде аэросмеси существенно возрастает скорость его движения в загрузочном патрубке и в предпальцевом пространстве, что сопровождается значительным инерционным воздействием. Это приводит к неравномерности распределения материала в межпальцевом пространстве и как следствие к снижению эффективности измельчения и производительности. Для управления процессом измельчения возникла необходимость в разработке методики определения коэффициента загрузки. С целью реализации указанной задачи составлены математические модели движения частиц в загрузочном патрубке (12) и в предпальцевом пространстве. Сила аэродинамического воздействия определялась по формуле (4) как и в среднеходных мельницах. Специфика движения материала в дезинтеграторе отличается его значительно большей концентрацией в воздушном потоке, которая учтена путем изменения коэффициента аэродинамического сопротивления.
Определенные в результате решения системы уравнений (12) скорости и ускорения частиц явились начальными условиями для расчета их распределения в предпальцевом пространстве, математическая модель для которого подобна предыдущей. Отличие заключается в том, что движение рассматривается в одной плоскости Оxy и не учитывается сила трения.
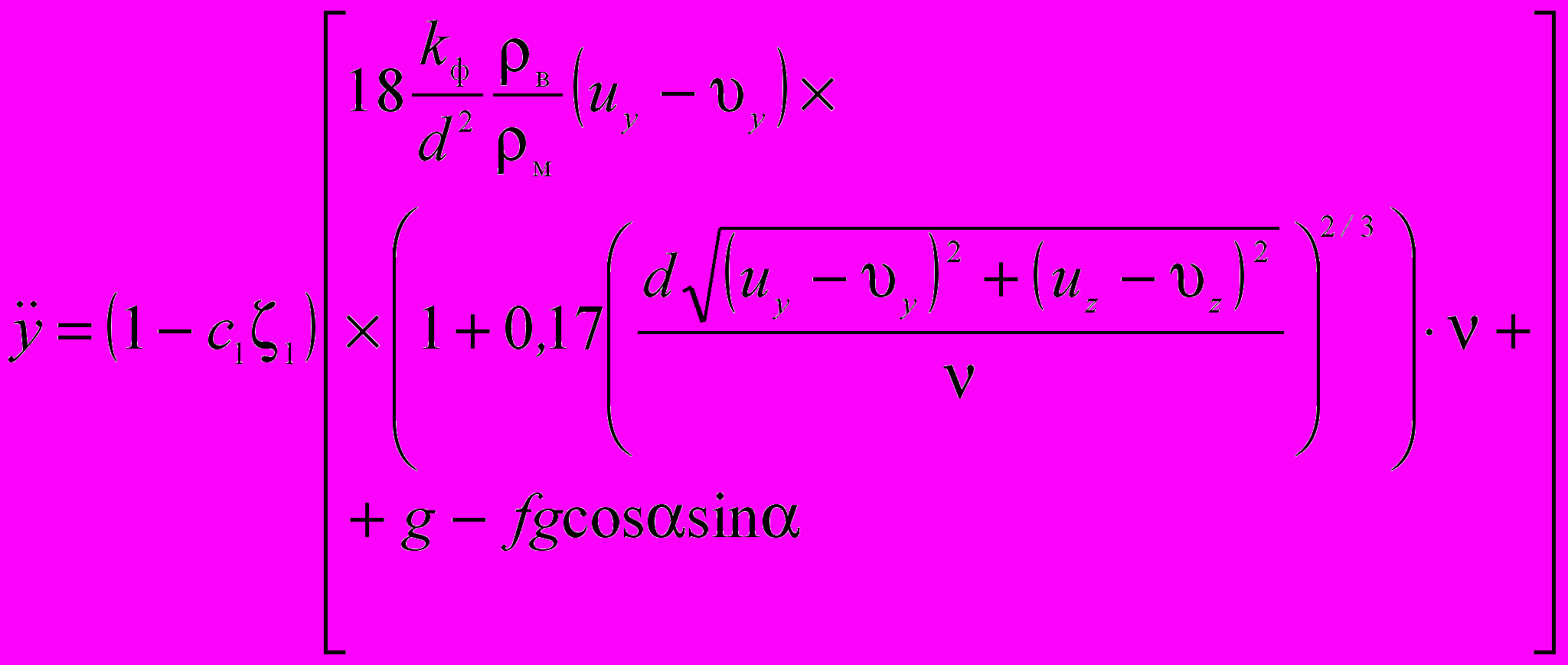
(12)
;
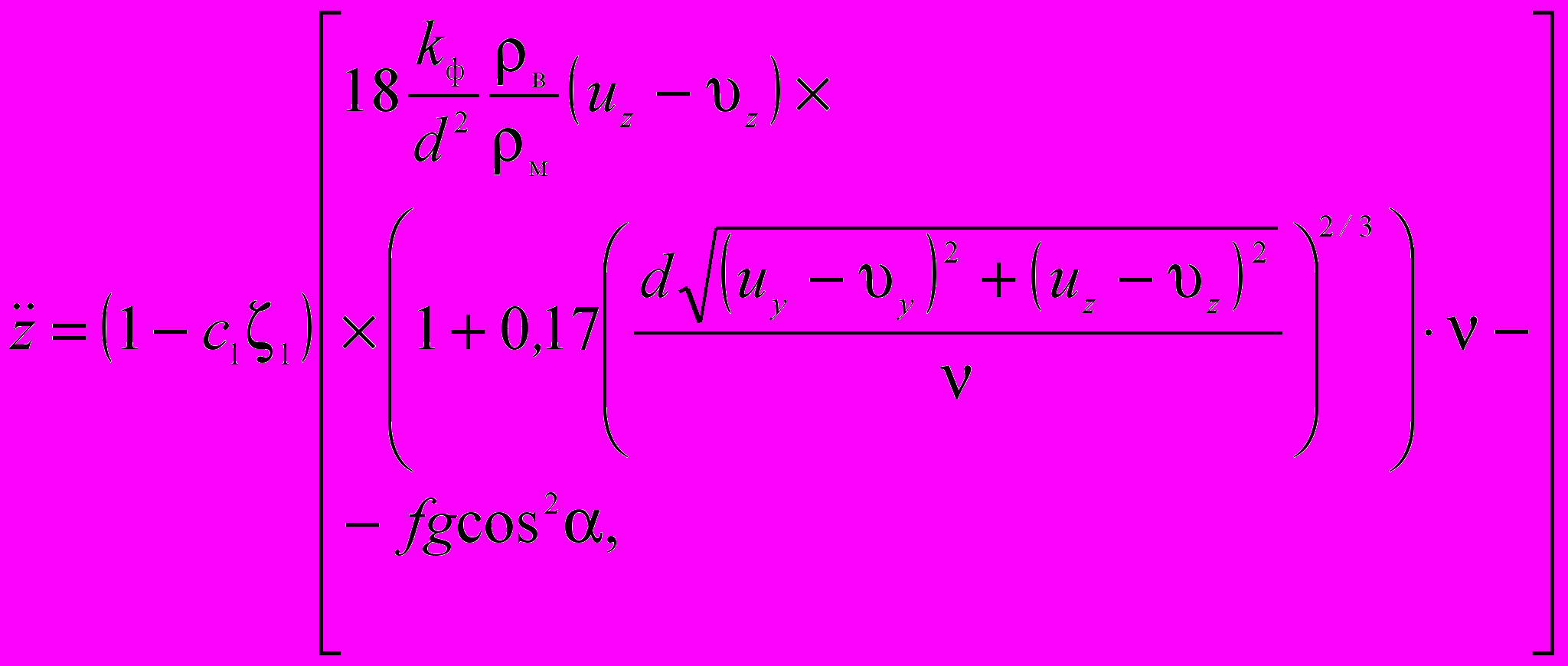
где u, скорости воздуха и частиц соответственно; ρВ ρм – плотность воздуха и материала; ν – кинематическая вязкость воздуха; kф – коэффициент формы; d – диаметр частиц; с1 – концентрация твердой фазы; α – угол наклона загрузочного патрубка; ξ1 – коэффициент аэродинамического сопротивления.
Последовательный расчет по двум указанным зонам дал возможность определить распределение частиц исходного продукта в межпальцевое пространство. На рисунке 5 показано распределение частиц размером более 82,8 мкм при частоте вращения 6000 мин-1.
Коэффициент загрузки kзагр = θ / 360, где θ – сектор ротора, заполненный материалом. Итоговая формула для определения производительности выглядит следующим образом:
Q = kзагрс2[lp(Dн − )−lpSk]n (13)
Адекватность модели подтверждена экспериментально
В
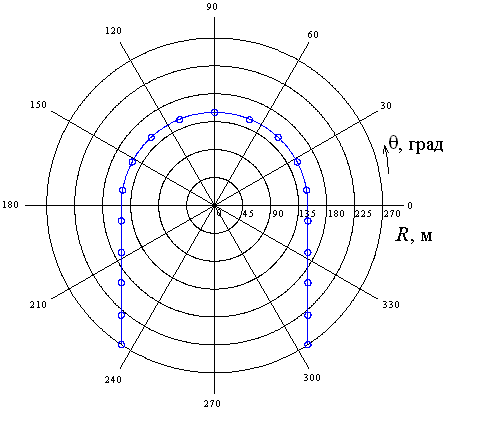
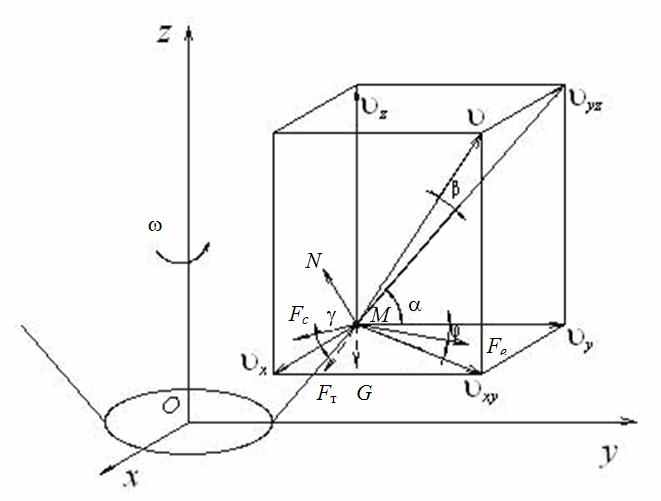
Рисунок 5 − Распределение частиц по сечению роторам при наклонном вводе
В
А
четвертой главе приведены результаты аналитических исследований движения мелющих тел и материала в скоростной центробежно-шаровой мельнице. Характерным признаком этих мельниц является наличие быстро вращающегося вертикального ротора. За счет этого измельчающие тела и материал вовлечены в интенсивное движение в вертикальной плоскости. Таким образом, шаровая мельница превращается в быстроходную, и определяющее влияние на специфику движения загрузки и на разрушающее воздействие оказывают инерционные силы.
В
Рисунок 6 − Расчетная схема центробежно-шаровой мельницы