І. П. Основи дефектоскопії-К.: «Азимут-Україна», 2004. 496 с. Ермолов И. Н., Останин Ю. А. Методы и средства неразрушающего контроля качества. М.: Высшая школа, 1988. Неразрушающий контроль металлов и изделий. Справочник
Вид материала | Справочник |
- Название Организации, 14.27kb.
- Аннотация дисциплины «методы неразрушающего контроля», 12.16kb.
- Государственный стандарт республики беларусь, 859.5kb.
- Неразрушающий контроль и техническая диагностика в промышленности , 23.73kb.
- Основные понятия и определения в области неразрушающего контроля, 280.3kb.
- Государственные стандарты. Неразрушающий контроль, 41.04kb.
- Комплексное исследование параметров качества биметаллических листов, 20.46kb.
- Семинар студентов, аспирантов, молодых ученых и специалистов отраслевых предприятий, 54.06kb.
- Правила аттестации специалистов неразрушающего контроля, 385.22kb.
- Неразрушающий контроль разрушает границы, 73.42kb.
Вихретоковый метод контроля.
В
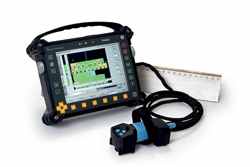
Объектами контроля являются основной металл, сварные соединения конструкций, а также детали. Вихретоковым контролем могут быть выявлены: ковочные, штамповочные, шлифовочные трещины, надрывы в элементах конструкций и деталях; волосовины, неметаллические включения, поры в поковках и прокате; трещины, возникшие в элементах конструкций и деталях при эксплуатации машин.
Вихретоковым методом не могут быть проконтролированы элементы конструкций и детали: с резкими изменениями магнитных или электрических свойств; с дефектами, плоскости раскрытия которых параллельны контролируемой поверхности или составляют с ней угол менее 10°; сварные швы без снятого усиления. При вихретоковом контроле не обнаруживаются дефекты в элементах конструкций и деталях: с поверхностями, на которые нанесены электропроводящие защитные покрытия, если дефект не выходит на поверхность покрытия; с поверхностями, покрытыми коррозией.
Выявляемость дефекта при прочих равных условиях зависит от его типа. Наилучшим образом выявляются дефекты типа усталостных трещин, ориентированные перпендикулярно контролируемой поверхности. Ширина раскрытия усталостных трещин в определенных пределах не влияет на их выявляемость (20–30 мкм), однако выявляемость очень плотных трещин резко уменьшается. Такое явление, например, характерно для закалочных трещин. Риски и надрезы по сравнению с усталостными трещинами, как правило, выявляются хуже. Заполнение полости дефекта грязью, нагаром, неэлектропроводящими окислами и т. п. не приводит к снижению их выявляемости.
Вихретоковый контроль наиболее эффективен при контроле немагнитных материалов. Возможность контроля ферромагнитных материалов и деталей из них определяется однородностью магнитных свойств, наличием локальных магнитных полюсов. Наличие локального изменения магнитных свойств материала детали может вызвать ложное срабатывание вихретокового дефектоскопа. Наличие на контролируемой поверхности зон структурной неоднородности, приводящих к изменению электропроводности, вызывает расстройку дефектоскопа. Увеличение электропроводности снижает чувствительность, уменьшение электропроводности вызывает эффект, аналогичный влиянию дефекта. Наличие на контролируемой поверхности значительных остаточных макронапряжений, возникающих в результате поверхностного упрочнения детали или под действием сжимающих остаточных напряжений, приводит к сжатию полостей трещин и других дефектов и к снижению их выявляемости. Максимальная чувствительность вихретокового вида контроля может быть достигнута при контроле деталей с шероховатостью поверхности не более Rz 20. Возможность и целесообразность контроля деталей с грубой поверхностью должна определяться в каждом конкретном случае специалистами по вихретоковому контролю.
Методы и средства контроля качества прокатной продукции
Контроль технологического процесса и качества прокатной продукции имеет большое значение. В прокатных цехах осуществляется контроль качественными и количественными методами визуально или при помощи приборов и инструментов.
Основными требованиями, предъявляемыми к методам испытаний, являются их надежность, которая выражается в повторяемости результатов при многократных испытаниях одного и того же материала, и доступность метода, т.е. возможность его использования в производственных условиях без применения сложных дорогостоящих установок или уникальных приборов. Кроме того, время испытания должно быть таким, чтобы обеспечить возможность проверки поставляемой прокатной продукции в условиях поточного производства.
В процессе приемочного контроля осуществляются оценка качества поверхности прокатной продукции и внутренних дефектов, исследование механических свойств металла и проведение его технологических испытаний.
Оценка качества поверхности производится следующими методами:
- грубая оценка - осмотр поверхности полупродукта и готового проката с местной зачисткой ее (светлением) в виде колец, зигзагообразной шлифовкой наждачным кругом или без нее;
- при повышенных требованиях к качеству поверхности изделия подвергают травлению в водных растворах кислот для полной очистки их от окалины. Простая визуальная оценка выявляет число и характер расположения дефектов, но не позволяет определить глубину их залегания.
Для выявления глубины залегания поверхностных дефектов и выявления подповерхностных дефектов применяют:
- осадку образцов круглых или квадратных сечений, в холодном и горячем состоянии высотой, равной двум-трем диаметрам до половины или одной трети первоначальной высоты;
- ступенча¬тую обточку круглых и строганных квадратных образцов до 3-5-й ступеней.
Визуальный контроль поверхности с помощью оптических приборов называется визуально-оптическим. К таким методам относятся применение систем зеркал, периодического фотографирования, дистанционная передача изображения с помощью телевизионного оборудования и др.
Оценка внутренних дефектов осуществляется макроисследованием проката, которое производится двумя путями:
- способом излома. В этом случае темплет толщиной 15-30 мм подвергается термообработке и ломается по оси под молотом. Излом рассматривается невооруженным глазом или через лупу. По балльной системе оцениваются следы усадочной раковины и рыхлости, неметаллические включения, расслой, флокены, пузыристость, волокнистость, прокаливаемость, величина зерна. На рисунке приведен пример оценки величины зерна в баллах;
-

Микроисследования проката осуществляются на полированных шлифах под микроскопом с балльной оценкой следующих дефектов:
- глубины обезуглероженного слоя;
- количества и величины неметаллических включений;
- структуры стали;
- карбидной неоднородности или цементной сетки и др.
При исследовании механических свойств применяются следующие виды испытаний:
Испытание на растяжение производят на стандартных и натурных термообработанных образцах при комнатной и высокой температурах на разрывных машинах в специальных лабораториях. Кроме основных стандартов на методы испытаний растяжением имеются стандарты на методы испытаний тонких листов и полос толщиной от 3 до 0,5 мм.
Испытание на ударную вязкость на специальном копре характеризует хрупкость стали при ударной нагрузке. В качестве образцов применяют образцы квадратного сечения 10x10 мм и длиной 55 мм, испытываемые на изгиб на двух опорах. Ударная вязкость определяется работой, расходуемой на ударный излом, отнесенной к рабочей площади поперечного сечения образца в месте надреза.
Испытание на твердость осуществляется вдавливанием стального шарика (испытание по Бринеллю), алмазного конуса (испытание по Роквеллу) или пирамиды (испытание по Виккерсу) под определенной нагрузкой и др.
Для получения технологических характеристик металла в практике производства проката используются различные виды технологических испытаний, к которым относятся: - пробы на загиб и перегиб; - на расплющивание - двойной кровельный замок; - проба Эриксена - на выдавливание (штампуемость); - на удар; на усталость; на кручение; - на осадку; - на сплющивание и т.д. При этом соответствующими ГОСТами оговариваются условия проведения испытаний.
Для современного производства проката характерна тенденция широкого распространения методов обнаружения дефектов металла с помощью приборов без его разрушения, которые получили название неразрушающих методов контроля. Их применяют для выявления как поверхностных, так и внутренних дефектов, они могут быть использованы непосредственно в потоке со скоростью, соизмеримой со скоростью обработки.
Самый простой и дешевый метод контроля качества поверхности прокатанного металла - визуальный. Ему предшествует полное или местное удаление окалины с контролируемой поверхности. Визуальный контроль весьма трудоемок и несовершенен.
Метод контроля, основанный на проникающих свойствах жидкости, иногда с добавкой красителя или люминофора, применяют для выявления дефектов на передельной заготовке, трещин на рабочих валках, для контроля качества поковок типа шайб-дисков.
Магнитный метод основан на свойстве магнитного потока локализоваться около дефектов. Дефект распознают либо визуально по картине распределения ферромагнитного порошка, нанесенного предварительно в виде пасты или суспензии, либо с помощью феррозонда - магниточувствительного преобразователя напряженности магнитного поля в электрический сигнал.
Ультразвуковой метод контроля позволяет обнаруживать и определять несплошности и трещины всех типов - от микро¬скопических до раковин, расслоений, газовых пузырей и т.п., практически на любой глубине и в любых металлических материалах. Этот метод основан на способности отражения ультразвуковых колебаний от поверхности раздела сред с различным акустическим сопротивлением. Узкий пучок ультразвуковых колебаний, введенный в достаточно однородную среду, распространяется прямолинейно, пока не достигнет границы упругой неоднородности (трещины, раковины, шлакового включения или противоположной грани изделия). На границе неоднородности ультразвуковых колебаний отразятся, образуя за неоднородностью область так называемой ультразвуковой тени. При помощи специального приемного устройства обнаруживаются дефекты внутри изделия. На практике используют дефектоскопы типа УДЦ-25, УДМ-1М, ДПХ-003 и др.
Наиболее универсальным является электроиндуктивный метод (метод вихревых токов), который применяется для контроля поверхностных дефектов, твердости, фазового состава, глубины обезуглероженного слоя и т.п. Метод основан на свойствах вихревых токов отражаться и возвращаться в испытательную катушку. Отражение и преобразование энергии зависит от свойств контролируемого металла, следовательно, ток в катушке будет нести информацию о свойствах металла и наличии дефектов в нем.
Получает применение, главным образом, в обжимном производстве рентгене- и гамма-дефектоскопия.
Большое распространение в производстве проката получил метод статистического контроля, заключающийся, в экспериментальном и статистическом исследовании уровня качества проката. С помощью статистических (математической статистики) методов изучается зависимость механических свойств проката от содержания химических элементов в стали и технологических факторов производства.
Данные этих зависимостей заносят в таблицы, по которым оценивают, прогнозируют показатели качества проката.
Значительный эффект получается от внедрения статистического метода контроля, который достигается за счет сокращения объема трудоемких механических испытаний и снижения расхода металла на пробы. Ускорение процессов контроля при внедрении статистического метода контроля сокращает цикл производства, снижает загруженность складов готового проката, повышает оперативность поставки готового проката потребителям.
Одним из важнейших факторов повышения качества прокатной продукции является получение объективных и достоверных данных при помощи контрольно-измерительных приборов (дефектоскопов). Наличие таких данных дает возможность воздействия как на процесс производства прокатной продукции (с точки зрения качества), так и на контроль качества. Таким образом, качество прокатной продукции тесно связано со знаниями об измерениях, методах и средствах их единства и способах достижения необходимой точности, т.е. с метрологией.
При производстве прокатной продукции нет буквально ни одного этапа производства, который мог быть успешно реализован без применения методов и средств измерений.
Такое влияние измерительной техники на отдельные этапы и направления производства продукции требует особой ее подготовленности. Малейшее отклонение уровня развития измерительной техники от объективно необходимого оптимума сразу же отрицательно отражается на показателях качества и эффективности производства продукции, вызывает значительные потери материальных средств и ресурсов.
В связи с этим перед метрологией стоят задачи, которые можно определить следующим образом:
- обеспечение единообразия и высокого качества средств измерений, находящихся в эксплуатации;
- единство, правильность, сопоставимость и достоверность результатов измерений при заданной точности;
- постоянная подготовленность методов, методик и средств измерения к практическому их применению и др.
Лекция 4. Физические методы дефектоскопии
Эти методы широко используются в современном машиностроении, так как с их помощью можно быстро и без разрушения исходных металлических полуфабрикатов, заготовок и изделий контролировать их качество — присутствие в них различных дефектов. Из многих известных физических методов наибольшее распространение получили ультразвуковой, радиационный и магнитный.
Ультразвуковая дефектоскопия
Ультразвуковая дефектоскопия основана на способности ультразвуковых колебаний отражаться от границы раздела двух сред, имеющих различную плотность, и включает регистрацию отраженных колебаний, препятствиями для распространения которых в металле могут явиться наряду с противоположной поверхностью изделия также различного рода дефекты.
Для дефектоскопии обычно применяют колебания с частотой 1 – 5МГц, что позволяет уверенно выявлять отражение ультразвуковой волны от несплошностей, размер раскрытия которых в тысячи раз меньше ее длины, а минимальная площадь составляет 1 мм2.
Ультразвуковые колебания имеют высокую направленность распространения по законам геометрической оптики, а также весьма незначительное затухание, которое в металлах обусловлено главным образом рассеянием и проявляется лишь в достаточно крупнозернистых структурах (когда длина волны и диаметр зерна соизмеримы) или при наличии крупных включений.
Различают продольные и поперечные ультразвуковые волны. Благодаря явлению трансформации, которое испытывает ультразвуковая волна при переходе из одной среды в другую, можно, меняя ее угол падения, обеспечивать распространение в контролируемом материале либо только продольной, либо поперечной ультразвуковой волны, а, следовательно, управлять траекторией распространения падающей и отраженной волны в металле.
Для создания акустического контакта между преобразователем и изделием наносят слой жидкости (воды, минерального масла, растворов солей). Различают прямой и наклонный преобразователи, являющиеся источниками соответственно продольных и поперечных колебаний, а также раздельно – совмещенный, в котором разделены функции источника и приемника продольных ультразвуковых волн. По величине амплитуды дополнительного импульса можно оценить размер дефекта, а по его удалению от начала развертки – глубину залегания дефекта в металле. При использовании наклонного преобразователя донное отражение ультразвуковой волны искателем не улавливается, а фиксируются лишь дополнительные импульсы в том случае, если на пути распространения волны встречается дефект.
При ультразвуковой дефектоскопии дефекты оцениваются путем сравнения результатов определения дефектов в контролируемом изделии и в эталонном образце.
Возможности ультразвуковой дефектоскопии для проведения неразрушающего контроля металлических изделий весьма широки. Можно контролировать изделия практически неограниченных размеров (при толщине металла до 2 м), различной формы, обнаруживать как объемные, так и плоскостные дефекты, причем в последнем случае независимо от их ориентации в изделии.
Ультразвуковой дефектоскоп – это электронно-акустическое устройство, предназначенное для возбуждения-приема ультразвуковых колебаний с целью обнаружения нарушений сплошности или однородности материалов и измерения их характеристик. Дефектоскоп преобразует колебания в вид, удобный для вывода на соответствующий индикатор. Он снабжен сервисными устройствами для настройки и сохранения параметров контроля и измерения параметров принятых сигналов.
Согласно ГОСТ 23049, в зависимости от области применения дефектоскопы делятся на приборы общего назначения и специализированные. В зависимости от функционального назначения дефектоскопы подразделяют на следующие группы:
1. Для обнаружения дефектов (пороговые дефектоскопы, обычно вместо экрана имеют светодиодный индикатор, показывающий факт превышения сигналом порогового уровня);
2. Для обнаружения дефектов, измерения глубин их залегания и измерения отношения амплитуд сигналов от дефектов;
3. Для обнаружения дефектов, измерения глубин их залегания и измерения эквивалентной площади дефектов по их отражающей способности или условных размеров дефектов;
4. Для обнаружения дефектов, распознавания их форм или ориентации, для измерения размеров дефектов или их условных размеров.
По конструктивному исполнению дефектоскопы подразделяются на стационарные, переносные и портативные.
По степени участия дефектоскописта в процессе контроля различают ручные, механизированные и автоматизированные дефектоскопы.
Условное буквенно-цифровое обозначение отечественных дефектоскопов состоит из букв УД (для дефектоскопов общего назначения) или УДС (для УЗДС), номера группы назначения и порядкового номера модели. Например: УД2-12 относится ко второй группе, а УД3-103 «Пеленг» – к третьей.
Радиационная дефектоскопия
Все методы радиационной дефектоскопии основаны на различиях в поглощении ионизирующих излучений средами с различной плотностью.
Присутствие в контролируемом веществе внутренних дефектов приводит к изменению интенсивности выходящего потока излучения. Иными словами, выходящий из контролируемого изделия поток излучения содержит в себе информацию о наличии или отсутствии в нем внутренних дефектов. Поскольку в зоне несплошности металлов поглощение ионизирующего излучения происходит в меньшей степени, пучок излучения, прошедший по дефектному участку, на выходе будет иметь более высокую интенсивность. Различие в интенсивности отдельных зон выходящего потока излучения может быть с высокой чувствительностью обнаружено с помощью рентгеновской пленки (методом радиографии), визуально на экране (методом радиоскопии) или с помощью электрических сигналов (методом радиометрии).
В качестве ионизирующего излучения используют рентгеновское (рентгеновскую дефектоскопию) или γ-излучение изотопов (гамма-дефектоскопию). Оба вида излучения являются разновидностью электромагнитных волн, различающихся по длине, причем с уменьшением длины волны возрастает энергия излучения Е и его проникающая способность.
В табл. 1, 2 приведены используемые в радиационной дефектоскопии источники излучения и проанализированы возможности указанных выше методов.
Таблица 1. Основные характеристики источников гамма-излучения
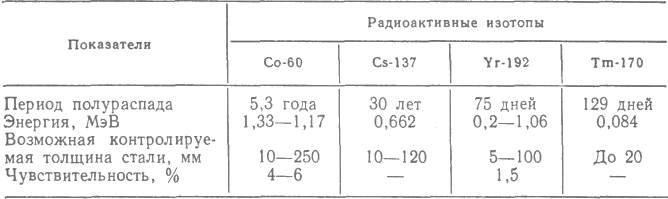
Таблица 2. Области эффективного применения источников ионизирующего излучения в радиационной дефектоскопии
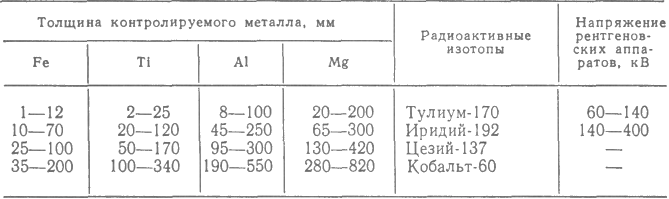
Методы радиационной дефектоскопии позволяют выявлять самые разнообразные дефекты в сталях и сплавах (преимущественно объемные типа пор, раковин, непроваров), а также трещины, направление которых в металле совпадает с направлением просвечивания в диапазоне углов 0 – 12°. При рентгеновском и гамма-контроле дефекты оценивают путем обмера линейных размеров выявленных дефектов на рентгене- и гамма-пленках.
Магнитная дефектоскопия
Магнитная дефектоскопия основана на различии магнитной проницаемости разных сред. Нарушение сплошности металла (пора, раковина, непровар, трещина), неметаллические включения представляют собой области с весьма малой магнитной проницаемостью и потому могут быть обнаружены в изделиях из ферромагнитных материалов. При намагничивании подобных изделий вблизи дефектов наблюдаются возмущения магнитного потока, его однородность нарушается из-за огибания силовыми линиями препятствий, а в некоторых случаях (выходящая на поверхность трещина, приповерхностный дефект) появляются потоки рассеяния (рис. 3). При этом для намагничивания контролируемого изделия оказываются достаточными магнитные поля напряженностью 8 – 16 кА/м, а в ряде случаев (для материалов с коэрцитивной силой более 1,6 кА/м) можно использовать и остаточную намагниченность. Таким образом, выявление дефектов методами магнитной дефектоскопии фактически сводится к обнаружению полей рассеяния или участков поверхности изделия с повышенной плотностью магнитного потока. На практике чаще применяют магнитопорошковый, индукционный и магнитографический методы выявления дефектов.
Метод магнитного порошка основан на способности ферромагнитных частиц у-Ре2О3 или Ре3О4 притягиваться в местах наличия магнитных потоков рассеяния (рис. 4). Для намагничивания в этом случае используют как переменное, так и постоянное магнитное поле; магнитные порошки применяют в сухом виде
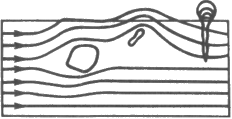
Рис. 3. Схема, иллюстрирующая нарушение однородности магнитного потока вблизи дефектов и образование полей рассеяния
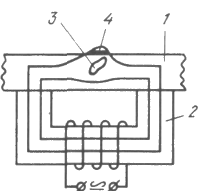
Рис. 4. Схема осуществления магнитно-порошкового контроля: 1 — изделие; 2 — электромагнит; 3 — дефект; 4 — место скопления частиц порошка
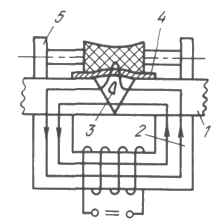
Рис. 5. Схема проведения контроля индукционным методом:
1 — изделие; 2 — электромагнит; 3 — дефект; 4 —-искатель
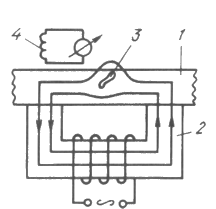
Рис. 6. Схема проведения магнитографического контроля:
1 — изделие; 2 – электромагнит; 3 —дефект; 4 — магнитная лента; 5 —- ролик
Индукционный метод основан на явлении электромагнитной индукции. При намагничивании изделия в переменном магнитном поле в местах дефектов на его поверхности появляются переменные поля рассеяния, которые создают индуктивную э. д. с. в катушке специального искателя (рис. 5). Сигнал о дефекте в виде э. д. с. усиливается и попадает на индикатор, которым может быть гальванометр, лампочка и др.
Магнитографический метод заключается в фиксации полей рассеяния на магнитной ленте (изделие намагничивается при этом в постоянном магнитном поле) и в воспроизведении сделанной записи дефектов с помощью электроннолучевой трубки (рис. 6).
Важным достоинством магнитной дефектоскопии является возможность автоматизации процесса контроля; операция контроля легко может быть встроена в технологический процесс изготовления детали. Тем не менее, применение этого метода ограничено по ряду причин: контролируются ферромагнитные материалы с толщиной стенки изделий не более 16 мм; выявляются преимущественно объемные дефекты размером не менее 5 % толщины материала и только те трещины, которые выходят на поверхность изделия.
При магнитных методах контроля дефекты оценивают как путем сравнения с эталонным образцом, так и путем непосредственных обмеров дефектов, обнаруженных в результате контроля (магнитопорошковый контроль).
Лекция 5 Методы исследования и испытания металлов.
МЕТАЛЛОГРАФИЧЕСКИЕ ИССЛЕДОВАНИЯ
Макроскопический анализ
Макроанализ заключается в определении строения металла путем просмотра его излома или специально подготовленной поверхности невооруженным глазом или через лупу при небольших увеличениях — до 30 раз. Это позволяет наблюдать одновременно большую поверхность и получить представление об общем строении металла и о наличии в нем определенных дефектов.
В отличие от микроскопического исследования макроскопический анализ не определяет подробностей строения и часто является предварительным, но не окончательным видом исследования. Характеризуя многие особенности строения, макроанализ позволяет выбрать те участки, которые требуют дальнейшего микроскопического исследования. С помощью макроанализа можно определить:
1. Нарушение сплошности металла: усадочную рыхлость, газовые пузыри и раковины, пустоты, образовавшиеся в литом металле, трещины, возникшие при горячей механической или термической обработке, флокены, дефекты сварки (в виде непровара, газовых пузырей, пустот);
2. Дендритное строение и зону транскристаллизации в литом металле;
3. Химическую неоднородность сплава (ликвацию);
4. Неоднородность строения сплава, вызванную обработкой давлением: полосчатость, а также линии скольжения (сдвигов) в наклепанном металле;
5. Неоднородность, созданную термической или химико-термической обработкой.
Поверхность, подлежащую макроанализу, изучают непосредственно (по виду излома) или шлифуют и подвергают травлению специально подготовленными реактивами. На шлифованной поверхности не должно быть загрязнений, следов масла и т. п., поэтому ее перед травлением протирают ватой, смоченной в спирте. Подготовленный образец называют макрошлифом.
Большое значение для успешного выполнения макроанализа имеет правильный выбор наиболее характерного для изучаемой детали сечения или излома (см. ниже).
Способы макроанализа различны в зависимоcти от состава сплава и задач, поставленных в исследовании.
1. Для выявления дефектов, нарушающих сплошность металла, флокенов, строения литой стали, волокон катанной стали применяют реактивы как глубокого, так и поверхностного травления.
После травления макрошлиф приобретает рельефную поверхность с отчетливо видимыми осями дендритов (литая сталь), ликвационной зоной и трещинами (если они были в изломе или если в металле обнаружились флокены). Для этих целей чаще применяют поперечные макрошлифы (темплеты).
Травление производят в вытяжном шкафу; макрошлифы вынимают из реактива щипцами или рукой, защищенной резиновой перчаткой.
Для поверхностного травления чаще всего применяют реактив Гейна, содержащий (на 1000 мл воды) 53 г хлористого аммония NH4Cl и 85 г хлористой меди CuCl2.
При погружении макрошлифа в реактив (на 30–60 с) происходит обменная реакция: железо вытесняет медь из водного раствора, и она оседает на поверхности шлифа; на участках, недостаточно защищенных медью (поры, трещины, неметаллические включения), происходит травление. Затем макрошлиф вынимают, слой осевшей меди снимают ватой под струей воды и протирают макрошлиф досуха, чтобы предохранить его от быстрого окисления на воздухе.
Реактив Гейна более отчетливо выявляет характер ликвации и полосчатость деформированной стали, но менее резко выявляет структуру литого металла и трещины, особенно вызванные флокенами. Для последних целей более пригодны указанные выше реактивы глубокого травления.
2. Определение химической неоднородности. С помощью макроанализа, в отличие от химического анализа, нельзя определить количественное содержание примесей, но можно установить неоднородность распределения их в металле. Для этой цели макрошлиф следует вырезать из катанной или кованной стали в продольном направлении. Распределение серы определяют следующим образом (способ Баумана). Фотографическую (бромосеребряную) бумагу на свету смачивают или выдерживают 5–10 мин в 5 %-ном водном растворе серной кислоты и слегка просушивают между листами фильтровальной бумаги для удаления излишнего раствора. После этого на приготовленный макрошлиф укладывают фотобумагу и слегка и осторожно, не допуская смещения бумаги, проглаживают рукой или резиновым валиком для удаления оставшихся между бумагой и макрошлифом пузырьков воздуха, так как эти пузырьки оставляют на фотобумаге белые пятна и маскируют результаты анализа. Фотобумагу выдерживают на макрошлифе 2–3 мин.
Сернистые включения (MnS, FeS), имеющиеся в поверхностных участках металла, реагируют с серной кислотой, оставшейся на фотобумаге:
MnS(FeS) + H2SO4 → MnSO4(FeSO4) + H2S
Образующийся сероводород непосредственно против очагов своего выделения воздействует на кристаллики бромистого серебра фотоэмульсии:
H2S + 2AgBr → 2HBr + Ag2S.
Темные участки сернистого серебра, образующиеся на фотобумаге, указывают форму и характер распределения сульфидов.
Снятую с макрошлифа фотобумагу промывают под струей воды, фиксируют 20–30 мин в растворе гипосульфита, после чего промывают примерно 10 мин в воде и просушивают.
Если в стали и чугуне содержится повышенное количество фосфора, то он в отдельных участках, вследствие значительной ликвации, может также участвовать в реакции с бромистым серебром, образуя фосфиды серебра темного цвета.
Определение ликвации углерода и фосфора. Для этой цели используют указанный выше реактив: 85 г CuCl2 и 53 г NH4Cl (на 1000 мл воды).
Способ определения ликвации фосфора и углерода основан на неодинаковом травлении участков с различным содержанием этих элементов. Участки, обогащенные углеродом и фосфором, окрашиваются в более темный цвет. Лучшие результаты достигаются для стали, содержащей менее 0,6 % С. В стали с более высоким содержанием углерода осадок меди, выделяющийся при травлении, плохо смывается с поверхности шлифа.
3. Определение неоднородности строения, созданной обработкой давлением (полосчатость). Направление волокон, созданное обработкой давлением, хорошо выявляется реактивом состава: 85 г CuCl2 и 53 г NH4Cl (на 1000 мл воды), т. к. волокна металла и особенно их пограничные участки, отличающиеся по структуре и содержанию примесей, обладают неодинаковой травимостью.
4. Определение неоднородности в структуре, созданной термической и химико-термической обработкой.
А. Определение толщины закаленного слоя. Для этой цели закаленный образец ломают. Слой, получивший закалку, отличается по виду излома (более мелкозернистый, а при закалке без перегрева — фарфоровидный излом). Более точно толщину закаленного слоя определяют после шлифования образца по излому (перпендикулярно оси) и травления в течение 3 мин в 50 %-ном растворе соляной кислоты при 80 °С. Закаленный слой получает более темную окраску.
Б. Определение толщины цементированного слоя. Образец после цементации и закалки, как и в предыдущем случае, ломают. Наружный цементованный и закалившийся слой имеет более мелкое зерно и при выполнении цементации и закалки без перегрева отличается матовым фарфоровидным (шелковистым) изломом. По толщине этого слоя судят о глубине цементации.
Толщину цементованного слоя можно определять более точно шлифованием места излома (перпендикулярно оси) и травлением в течение 1–2 мин в реактиве состава: 2 г Cu Cl2 × 2H2O и 1 мл HCl (на 100 мл спирта). Мягкая нецементованная сердцевина покроется красноватым налетом меди вследствие вытеснения ее железом из реактива, тогда как цементованный слой останется нетронутым.
Последовательность операции макроанализа
При необходимости полного макроскопического исследования и определения как нарушений сплошности металла, так и дефектов строения, целесообразно придерживаться следующей последовательности: сначала производят травление реактивом состава: 85 г CuCl2 и 53 г NH4Cl (на 1000 мл воды), являющимся общим реактивом и позволяющим выявить строение металла; полученные результаты зарисовывают или фотографируют. Затем образец снова шлифуют и определяют распределение серы по отпечатку на фотобумаге. После этого производят глубокое травление для определения нарушений сплошности и флокенов.