Затраты на обеспечение качества продукции и пути их сокращения тема диссертации по экономике, полный текст автореферата
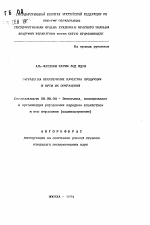
Автореферат
Ученая степень | кандидат экономических наук |
Автор | Аль-Фатлави Карим Абд Идан |
Место защиты | Москва |
Год | 1994 |
Шифр ВАК РФ | 08.00.05 |
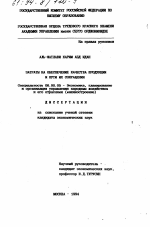
Автореферат диссертации по теме "Затраты на обеспечение качества продукции и пути их сокращения"
Г Б . йсудл(ч:Т8Ш!ый комитет российской федерации по - О ГЕЦ ' ВЫПИЕЧУ ОБРАЗОВАНИЮ
ГОСУДАРСТВЕННАЯ ОРДЕНА ТРУДОВОЮ КРАСНОГО ЭНАККНИ АКАДЕМИЯ УПРАВЛЕНИИ имени СЕРЮ ОРДКОНИКИДЗЕ
На правах рукописи
а7!ь-фатлави карим абд идан играть! на обеспечение качества продукции
и пути их сокрАдаия
Специальность 08.00.05 - Экономика, планирование и организация управления иародш/м хозяйством и его отраслями (машиностроение)
АВТОРЕФЕРАТ диссертации на соискание учсмюЛ степени кандидата экономическил наук
КООКВД - 1094
Диссертационная работа выпонена в Государственной Академии Управления имени Серго Орджоникидзе на кафедре "Производственный менеджмент в машиностроении".
Научный руководитель: кандидат экономических наук, профессор
Турусин Юрий Дмитриевич
Официальные оппоненты: доктор экономических наук, профессор
Иванов Анатолий Васильевич кандидат экономических наук, доцент Винокуров Владимир Александрович
Ведущая организация: Центр социально-экономического развития
департамента перспективного развития г.Москвы
Защита состоится " / " / 1У_1994г. в Ж часов на
заседании специализированного совета К 053.21.03 в Государственной Академии Управления имени Серго Орджоникидзе по адресу: 109542, Москва, Ряаансккй проспект, 99, вал заседаний Ученого Сонета.
С дносертагуией можно ознакомиться в библиотеке Академии
Автореферат разослан "_"_1994г.
Ученый секретарь специализированного совета кандидат экономических наук, доцент H.A. Фролова
Общая характеристика рпботн
Актуальность исссдотигия: Рыночные отношения актунлиаируют вопроси качества и издержек, связанных с его обеспечением. Тра;\и-ционное рассмотрение этих проблей состоит в том, что пов'-ганиэ качества продукции требует, как правило, допонительных затрат. Однако, необходимость укрепления полинуй предприятия на кгнугональ-ном и мировом рынке требует непоколебимого стремления достигать высокого качества при одновременном снижении себестоимости выпускаемой продукции.
Затраты на обеспечение качества продукции представляет собой, с одной стороны, один из видов затрат, вкгочичяргеся в себестоимость продукции, 6 другой стороны, эти аатраты отражают проблемы качества, так как структура и величина этих затрат вкччает в себя издержки вследствие выпуска продукции низкого качества. Работа со специальной литературой показала, что издержки вследствие выпуска продукции низкого качества колеблются от 20 до 40 X от суммы реализованной продукции. Таким образом, сокращение этих издержек приводит "к сокращению общих затрат на обеспечение качества продукции. В результате, себестоимость продукции снижается при неизменном или более высоком ее качестве.
Повышение качества продукции и сокращение потерь от брака невозможно без правильной организации учета и анализа брака. Для этой цели необходимо, прежде всего, классифицировать брак по причинам его возникновения. Брак возникает по разным причинам. Например, из-за некачественных материалов (сырья), из-аа ошибок рабочих, конструкторов и технологов и из-за нарушения технологических параметров процесса производства.
Как показало изучение специальной литературы, исследователи нарушений технологических условий производства уделяли недостаточно внимания ошибкам в организации и управлении производством при определении размеров партий деталей, сборочных единиц разных заказов и установлении сроков запуска - выпуска этих партий, и их влиянии на качество продукции. Однако, изучение этих явлений весьма пктудвно в свяаи со следующим. С одной стороны, когда размер партии деталей больше, чем их необходимое количество, или когда эти пл]>тии изготавливаются раньше установленного срока, тогда время
ожидания этих деталей увенчивается и вероятность ухудшения их качества повышается из-за нарушения технологических условий, при плохих условиях хранения или из-за чувствительности деталей к климатическим условиям. Например, при отклонении температуры или платности от их нормальных уровней. С другой стороны, когда размер выпускаемой партии деталей меньше заказа или когда партия деталей опаздывает к назначенному сроку, тогда рабочие в цехах чтобы процесс производства не останмншся из-за низкой культуры производства, используют детали, не подготовленные для данной операции. В результате, качество конечного изделия ухудшается. Бее выше кгло женное предопределило выбор темы и объекта исследования.
Целю диссертационной работы является сокращение затрат на обеспечение качества продукции за счет их составляющих, связанных с организацией и управлением производством.
Поставленная цель предопределила комплекс задач, важнейшими из которых являются:
1. Исследование затрат на обеспечение качества продукции как экономической категории, отражающей проблемы брака.
2. Анализ структуры затрат на обеспечение качества продукции по их видам, и анализ структуры издержек вследствие выпуска продукции низкого качества по видам брака на иракских предприятиях.
3. Исследование системы с точкой ваказа "Re-order point system" как традиционный метод для определения размера партии деталей и даты запуска-выпуска этих партий и ее влияния на качество продукции.
4. Исследование механизма работы системы планирования требуемых материалов I1TM как инструмента управления материальными потоками и ее влияния на качество продукции.
5. Построение принципиальной схемы интеграции системы HTM о расчетом использования производственной мощности цеха.
6. Разработка динамического метода определения размеров партии деталей в цехах, позволяющих выявить зоны оптимальных вариантов, с помощью которых выбирается рациональный размер партии деталей.
Объект исследования. Объектом исследования послужили предприятия, занимающиеся изготовлением и сборкой изделий, где процесс производства партий деталей различных наименований в цехах органи
аован последовательно, а движение изготовления каждой партии сборочных единиц одного наименования по рабочим местам организовано паралельно.
Теоретической и методологической основой диссертации поолуги-ли труди иракских и зарубежных авторов в области управления затратами на обеспечение качества продукции и в области управления материальными запасами, статистический метод анализа затрат на обеспечение качества продукции (диаграмма Парето), фактические материалы о работе иракских предприятий и их усилий по обеспечению качества щюдукции.
Научная новизна состоит в следующем:
1. Выявлено, что 40% издержек производства вследствие выпуска продукции низкого качества связаны с недостатками в организации и управлении производством.
2. Выявлен ряд недостатков в организации и управлении производством при определении размеров партий деталей, сборочных единиц р;нн!и заказов и при установлении сроков зппус-ка-внпуска этих партий. Эти недостатки приводят к увеличения времени ожидания партии деталей, сборочных единиц в процессе производства. В результате, возрастает вероятность ухудшения их качества из-за нарушения технологических условий производства.
3. В результате проведенного анализа выявлена причина возникновения ошибки я традиционных расчетах производственной мощности, которая возникает при сопоставлении трудоемкости заказа и пропускной способности цеха, так как сопоставление толVко по обтему работ без учета их структуры приводит к зан-тенин! производственной мощности, к увеличению уровня незавершенного производства в цехах.
4. Разработана методика интеграции системы планирования требуемых материалов и планирования использования производственной мощности каждого сборочного цеха. Она основана на сопоставления производственной мощности цеха, кок ресурса времени его работы, и трудоемкости рассматриваемой работы, как времени потребления этого ресурса. Это обеспечивает надежные сроки выпонения работ, управление заделами незаверенного производства и сокращение цикла изготовления конечного изделия в целом.
5. Предлогом динамический метод определения размера партии деталей. Этот метод дает возможность выбрать рациональный размер партии деталей, сборочнмх рдчнтттт, соответствующий условиям производства и целим, к которым стремится руководство предцтигич.
R. Предложен способ определения зоны оптимальных значений размеров партии деталей на основе соотношения времени на-лдки для выпонения заказа в целом (Setup ti то) (Snj + Htj)3, технологического цикла (Run time) вштоне-ния аэказа (Rnj)3, длительности производственного цикла (Lead time) (Xnj) каждой партл к грсмсим еж.яданил каждой партии (Wn.i).
Практическая значимость работы определяется тем, что результаты исследования мо1'ут служить методологической базой для сокращения издержек на выпуск продукции низкого качества в связи с нарушением технологических условий в цехах, где движения партий деталей ранних наименований организовано последовательно и изготовление каждой партии организовано паралельно.
Объем и структура работы. Структура работы строилась в соответствии с целью и задачами исследования. Она состоит из введения, трех глав, заключения и списка литературы, изложенных на I3C листах машинописного текста, содержит 19 таблиц и 30 рисунков.
Содержание работы
fio введении обосновывается актуальность темы исследования, 1>5ормулированы его цель и перечень задач для ее реализации, обоснован вмбор облентл желедоианич, описаны методологические основы и практическая значимость исследования, раскрыты ее важнейшие научные результаты.
В перчой главе "Основные понятия - структура и сущность затрат па обеспечение качества продукции" рассмотрена сущность понятия "затраты на обеспечение качества продукции" как зкономичесно! категории. Поскольку исследование содержания экономической кате гории качества ограничено другими экономическими категориями "потребительной стоимостью" и "стоимостью товара", то понятЩ "качество продукции" как степень удовлетворения потребности обще ства относят к этапу реализации этой продукции - ибо только у по
треОителя продукция проявляет себя как потребительная стоимость. Но продукция, прошедшая начальные этапы или стадии жизненного цикла изделия (разработки, производства и обращения), обладая теми или иными полезными свойствами, представляет собой потребительную стоимость, так как при ее создании затрачен общественно полезный труд.
Из выше изложенного следует вквод о том, что качество продукции как степень удовлетворения ею конкретной потребности зависит как от свойств, обеспечивать ее полезность, так и от затрат на соадание этих свойств, то есть затрат на обеспечение качества на этапах жизненного гржла изделия.
Таким образом, величина и структура затрат на обеспечение качества продукции определяется как сумма затрат на контроль качества (затраты на предупреждение брака, которые обеспечивают випол-ение работы без дефектов и затрат на оценку качества, связанные С оценкой продукции для подтверждетет ее бездефектности), и издержки вследствие изготовления продукции низкого качества. Последние делятся на внутренние потери, когда издержки имеют место при обнаружении брака до поставки изделий внешним потребителям и внешние потери, которые имеют место когда дефект обнаруживается после получения иаделия внешним потребителями.
В главе изложен иракский и аарубежный опыт в области сокращения затрат на обеспечение качества продукции. Иракский опыт состоит в увеличении затрат на предупреждение брака, чтобы издержки вследствие выпуска продукции низкого качества снизились. Это происходит тогда, когда у предприятия ясный план по предупреждению брака и по уменьшению издержек вследствие выпуска брака. Американский опыт заключается в том, что эффективное управление качеством требует рационального баланса между затратами на оценку ка--честна и затратами на предупреждение брака, чтобы обнгие затраты на обеспечение качества продукции сократились до минимума. Японский опит в этой области состоит в использовании системы "Канбан" "Точно-вовремя" "Just in time", чтобы сразу делать все правильно. Причем делается упор на предупреждение брака, чтобы отпала необходимость в проведении столь частых текущих проверок качества работы. Благодаря деятельности кружков качества в системе "Канбан" ответственность за качество возлагается не на контролеров, а на самих изготовителей иаделия.
В главе на онове пчалияа статистических данных иракских предприятии, построена диаграмма "Парето", которая показала, что л()Х издержек производства вследствие выпуска продукции низкого качества происходит из-за ошибок в организации и управлении производством. На основании этого положения сделан bi/чод о том, что увеличение времени ожидания в процессе производства приводит к нарушения технологических у слоник производства, и как следствие, к лоярстаии.") вероятности ухудшения качества деталей. Это происходит из-за недостатков в организации и управлении производством при определении размеров партии деталей, сборочных единиц разных заказов и при установлении сроков запуска-выпуска этих партий (см.стр.4 актуальное'!л темы).
Таким образом, необходимо рассмотреть методы управления материальными потоками, которые используются для определения размеров партий деталей и сроков запуска-выпуска их партий.
Во второй главе диссертации "Методы управления материальными потоками и их влияние на качество продукции" анализируется механизм работы традиционного метода "re-order point system" так называемой "с точки заказа" определения ранмеров партии деталей п сроков запуска-г.ыпуска этих партий. Недостатки данного метода заключается в том, что он не отличает товарный запас (матер;аль-ные запасы готовой продукция) от производственного запаса (материальных запасов сырья, компонентов, комплектующих узлов и сборочных единиц) и не учитывает характер их потребления.
Особый характер потребления производственного запаса непосредственно снизан со спросом на конечное изделие, то есть потребность в таких деталях поддается прямому расчету и tie требует прогнозирования, пап это делается в системе "с точкой заказа". Кроме того, потребление деталей из производственных запасов характеризуется потребность (неравномерной) "I.ir'py deirarui" из-за выпуска этих деталей партиями и ira-за использования отдельных унифицированных деталей для производства разных сборочных единиц.
Все это приводит к увеличению материальных запасов деталей сверх из потребности. В результате, время ожидания (проложивання) этих деталей в процессе производства увеличивается и вероятность ухудшения jс: качества из-за парушешш технологииecmix условий повышается.
В главе рассмотрен механизм работы системы ПТН, которая
представляет собой методологи;л расчетом по преобразование основного графика производства готовых изделий в детальнее графики поставок сырья и компонент. Достоинством системы ПТМ является определение конкретных об-ьемон заказов на производство деталей и согласование между сроками запуска-выпуска этих заказов, чтобы выпонить план изготовления заказов на выпуск конечного изделия. А недостатки атой системы заключатся в том, что система Dili планирует сроки запуска-выпуска заказов на производство деталей, игнорируя согласование этих сроков с пропускной способностью цехов, и допускает, что производственная моиуюсть цехов позволяет выпонить эти заказы в плановые сроки.
Эффективность управления материальными запасами существенно зависит от характера взаимодействия следующих {акторов: запуск (input), загрузка (Load), производственная моцнооть цеха и выпуск (out-put), как показано на рис. 1. Из рисунка можно заметить, что возрастание уровня незавершенного производства, связанное о большим вводом, с увеличением количества заказов, поступающих в цех, приводит на первом этапе к быстрому возрастанию выпуска продукции цехом. Затем, по мере приближения уровня ввода к уровни) производственной мощности цеха, наступает период стабилизации. При дальнейшем увеличении ввода, об*ем выпуска начинает снижаться. Это связано с фактическим увеличением производственного цикла выпонения заказов, которое происходит из-за того, что заказы догое время находятся в очереди. При этом вероятность ухудшения качества деталей из-за нарушения технологических условий повышается. Чтобы этого не было, нужно четкое согласование обьака производства и производственной мощнисти.
В этой главе бил сделан важный вывод, который заключается в том, что система управления производством дожна быть нацелена на реиешго двух взаимосвязанных задач: это планщюзанс заказов на производство деталей и контроль за напонением утях иакпзом. Эту проблему предлагается решить путем шдерниаирола::!:;систепя ill:!, допоненной подсистемой 2>;н>гл\/.1 производс* ж. uWl mo-.i/Xi;^:. 3 этом случае система ТН буд^. слумяь "сорд?;ь-м" i.o::auvMii
системы управления производством.
П третьей главе "Сокращение размера партии - кик фал-
тор повышения качества проекции" рассматривается процесс интеграции системы ПТМ с расчетами использования производственной мощ-
РС- Соотношение. 3/>лacut, 0Wta4,
пРоьЧЁоЪсЛЬенкого tjau/)/! ч ПРоигвоЪсмёенчои
носкости е> jexc
ности каждого цеха путем деления объема заказа деталей на меньшие партии. Затем сопоставляются ресурсы времени использования производственной мощности цеха в часах и время потребления этого ресурса при выпонении ааказа, что обеспечивает надежное согласование сроков и объемов работ с пропускной способностью цеха.
Это воаможно при специфических условиях организации производства, а именно, при организации паралельной сборки каждой партии изделий, которая используется, например, на передовом иракском предприятии БУ при предметной специализации участков.
Процесс интеграции происходит следующим образом. На базе основного графика производства конечного изделия, система ПТМ определяет объем и дату запуска-выпуска заказов. Если производственной мощности цеха, где выпоняются эти закази достаточно, то сроки п размеры этих заказов принимаются. Если нет, то необходимо изменить содержание основного графика производства, то есть изменить либо объем заказа, либо даты начала его запуска, или то п другое одновременно.
В главе предложен динамический метод определения размера партии сборочных единиц для цеха, в котором изготовление этих партиЛ осуществляется последовательно, а гаготовленке каждой партии сборочных единиц одного наименования на рабочих нестая органиуопано паралельно.
Агоритм расчета размеров парии деталей предусматривает следующие шаги,
1. Определит номенклатуру деталей, наготавливаемых в цехе.
2. Определить варианта размеров партга при деления общего объема каждого заказа на napnci таким образом, чтобы размер каждой партии бил ранен необходимому количеству деталей для пштуска одного экземпляра конечного изделия или был кратен этому но-гпгчестяу.
3. Рассчитать технолог)мескнЛ таи "Run tivre" (Rnj) для изго-Хговления каждой партии деталей согласно всем вариантам по следующей формуле:
Rnj = Rnwt Х 1?гл Я (Knj - 1) где: Rnwt - технологический цикл для выпуска едшкцц деталей n-ого наименования (в час. пли мин.);
Rr\n - штучное время по главной, то есть наиболее
продожительной операции (в чао. или мин.); Knj - размер партии деталей n-ого наименования j-oro варианта (единица).
4. Определить последовательность приоритетов выпуска партий сборочния единиц таким образом, чтобы партия, у которой технологический цикл (Knj) наиболее длителен получила первый приоритет, ь. Рассчитать длителъниоть произнодстис;,":сгс цккп яэртяя сборочных едшшц (Xnj) по всем вариантам размеров партии о помощью следующей формулы:
Xnj = Rnj + Sn + 1'л +Х Wnj
где: n - порядковый номер данного на/шенованкп деталей выпускаемых в цехе; j - порядковый номер парианта деления общего объема заказа на части (партии) деталей n-ого наименования.
Общее количество вариантов деления общего объема наказа рассчитывается по следующей формуле:
Объем заказа на производство деталей n-ого наименования
J -------------------------------
Необходимое количество деталей n-ого наименования для выпуска одного конечного изделия
Xnj - дасггелыюстй проипводственного цикла партии деталей n-ого наименования j-oro варианта (час tum день п т.д.);
Sn - г.рамп наладки станков и время подгстор.;ш
трэбуюцееея дл выпуска нартни деталей я-пгэ г:иг;'с-нования (час.); Г.п - время транспортиром!',и выпускаемой ппрт;::: дггтпяэЛ n-ого наименования на склад (час.);.
Wnj - время ожидания партии деталей n-ого наименования j-oro варианта в процессе производства.
6. Сформировать план изготовления партии сборочных единиц каждого варианта при сопоставлении трудоемкости выпоняемых работ и пропускной способности в одинаковых единицах времени использования ресурса. Это сопоставление позволяет объективно спланировать процесс работы цеха и показать возможности управления циклами заказов и заделами незавершенного производства, как это показано на рис. 2.
Кроме этого, в главе рассмотрен процесс выбора зоны оптимальных вариантов размеров партии деталей, которые получаются динамическим методом.
Критерии этого выбора заключается в том, что увеличение размера партии деталей приводит, с одной сторопи, к сокращению времени наладки и транспортирования для выпонения заказа з целом (Snj +Х !!nj)3 к сидаенш технологического цикла выпонения всего заказа (Rnj)3. С другой стороны, это приводит к повьглетт длительности производственного цикла для выпуска каждой партии (Xnj) и времени ожидания каидой парпя! (V^nj). Таким образом, зона оятпмал&ншг вариантов определена на сснс-е соотношения эти:: факторов как показано на рис. 3.
В главе приводится расчет экономической о**0!{т/пя!0стм использования динаиического нетода определения размера пзрт)гл деталей. На иракском предприятия!, как гтсяззляо на р::с. Л, сб'^нг затраты на обеспечен:?л качества пря-укцн'! стезкста на 1СС0 динаров по сразиенш с их сунчоЛ г.о кс-пользо-аатш динамического метода.
Эти результата объясняется тем, что согласно пятнадцатому варианту время огсяатт партии сборочшпс единщ я зудаен случае не больше одного рабочего дня (см. рис. 4). Это значит, что количество брака in-aa тзхполо-
гпчесжп условий производства сократилось, го сст:, :*з~ерл-ки всздстгиз выпуска брака из-за c-^:6c: г. срггннзацзги и управлении производством при определении размеров парттс! деталей и при установлении сроков их запуска-выпуска снизились на 40Z (4000 я ЛОХ = 1600 динароз). Но одновпрменна затраты на контроль качества продушцш остались без ггзмоне-
JC/М/ Ul
g 9CO\ I
rco-600500-
ЗГО Zoe-
SS 538
Ъ66 Ь.
У/о /А
306 Бз
ПРОПУСКНАЯ
МОЫНОСТь
S s Г _ . g
новь!и перлое(
Рис. Пл^н из г oTCftjt е/'и А n*>-mut<
cSoyjOt м и SP egi/нич 4>у Б, H и jQ Соги.<к?СиС JS - киу п^риЫ йТУ
(Д"Mm))3 - ***** rui**)" к гмлияткаи J cro jnrntA (tf-чИ/Иел T>")
" tlWM XtcSPiHLAiJ (ил,
W*j - ььиЪнцл fn/WeivMJM)(yIT TVi()
Хл) - Pn^UcicnteWrti guit/ ПАРТЧЧ f'4*)
Зона ояткигьних вариантов
-)' i i- ) ! ) M M ) i' г- I i ) I ) ! ) )' ! I I I ) )! 1-1
\ 2 3 * 5 5 1 J Ш U л 1S U 15 (S 17 U И И 21 a 2Д Я г О 28 a
ЛРЧ4МГЫ
P.С 4 OntekttHu гспЫ оагимАМннк чг^чытсц mvntrо<ч пвегиа с.ео*о*ных tiл*л*
.г 5 ч-evл V.IO
затраты до использования динамического к тсда захрбтн после испсльзоЕдая доньмияеского
затрать на контроль качества
Рис. 4 : Обкие затраты на обеспечьте качества продукции до и поел, использования динамического метода определения размера партии
ния (4500 динаров). Таким образом, общие затраты на обеспечение качества продукции после использования динамического метода равно (4500 + 2400 = 6900 динаров). Это точна на кривой общих затрат на обеспечение качества продукции на рис. 4 отражает не самый лучший вариант, так как на предприятии еще есть другие причины возникновения брака, которые не рассматривались в данной работе.
В заключении диссертационной работы определены основные достоинства использования динамического метода определения размера партии деталей, который позволяет:
A. Сократить объем производственных запасов. Это позволяет экономить на затратах, связанных с использованием площадей складских помещений и оборудования для хранения и подачи материалов.
B. Сократить количество брака и повысить качество продукции при выпуске изделий более мекими партиями. Это достигается путем сокращения времени ожидания (пролежквания) этой продукции в процессе производства, что снижает вероятность ухудшения качества продукции из-за нарушения технологических параметров, особенно в условиях жаркого и влажного климата Ирака.
В. Повысить ответственность каждого рабочего за возникновение брака. В данном случае рабочий изготавливает только одно изделие и непосредственно передает его на следующую операцию. В случае если его деталь окажется непригодной, то место возникновения брака сразу известно. В результате, рабочие уделяют больше внимания качеству изделий.
Диссертация: содержание автор диссертационного исследования: кандидат экономических наук , Аль-Фатлави Карим Абд Идан
ЗАТРАТЫ НА ОБЕСПЕЧЕНИЕ КАЧЕСТВА ПРОДУКЦИИ И ПУТИ ИХ СОКРАЩЕНИЯ
Введение
Глава I. Основные понятия, структура и сущность затрат на обеспечение качества продукции
1.1 Сущность понятия затрат на обеспечение качества продукции
1.2 Значение изучения затрат на обеспечение качества продукции
1.3 Пути сокращения затрат на обеспечение качества продукции
Глава П. Методы управлекния материальными потоками и их влияние на качество продукции
2.1 Потребности в материальных производственных запасах и характеристики традиционного метода управления ими.
2.2 Система ПТМ и механизм.ее работы.
2.3 Анализ влияния системы ПТМ на качество продукции
Глава Ш. Сокращение размера партии деталей как фактор повышения качества продукции
3.1 Динамический метод определения размера партии деталей
3.2 Практика применения динамического метода определения размера партии в це- Х ! хе N 10. 101 *
3.3 Экономическая эффективность использования динамического метода определе- i ния размера партии деталей.
Диссертация: введение по экономике, на тему "Затраты на обеспечение качества продукции и пути их сокращения"
Рыночные отношения актуализируют вопросы качества и издержек, связанных с его обеспечением. Традиционное рассмотрение этих проблем состоит в том, что повышение качества продукции требует, как правило, допонительных затрат. Однако, необходимость укрепления позиций предприятия на национальном и мировом рынке требует непоколебимого стремления достигать высокого качества при одновременном снижении себестоимости выпускаемой продукции.Затраты на обеспечение качества продукции представляют собой, с одной стороны, один из видов затрат, включающихся в себестоимость продукции, с другой стороны, эти затраты отражают проблемы качества, так как структура и величина этих затрат включает в себя издержки вследствие выпуска продукции низкого качества. Работа со специальной литературой показала, что издержки вследствие выпуска продукции низкого качества колеблются от 20 до 40 % от суммы реализованной продукции. Таким образом, сокращение этих издержек приводит к сокращению общих затрат на обеспечение качества продукции'.В результате, себестоимость продукции снижается при неизменном или более высоком ее качестве.Повышение качества продукции и сокращение потерь от брака невозможно без правильной организации учета и анализа брака. Для этой цели необходимо, прежде всего, классифицировать брак по причинам его возникновения. Брак возникает по разным причинам. Например, из-за некачественных материалов (сырья), из-за ошибок рабочих, конструкторов и технологов и из-за нарушения технологических параметров процесса производства. - 4 Как показало изучение специальной литературы, исследователи нарушении технологических условий производства уделяли недостаточно внимания ошибкам в организации и управлении производством при определении размеров партий деталей, сборочных единиц разных заказов и установлении сроков запуска - выпуска этих партий, и их влиянию на качество продукции. Однако, изучение этих явлений весьма актуально в связи со следующим. С одной стороны, когда размер партии деталей больше, чем их необходимое количество, или когда эти партии изготавливаются раньше установленного срока, тогда время ожидания этих деталей увеличивается и вероятность ухудшения их качества повышается из-за нарушения технологических условий, при плохих условиях хранения или из-за чувствительности деталей к климатическим условиям. Например, при отклонении температуры или влажности от их нормальных уровней. С другой стороны, когда равмер выпускаемой партии деталей меньше заказа или когда партия деталей опаздывает к назначенному сроку, .. тогда рабочие в цехах чтобы процесс производства не остановися из-за низкой культуры производства, используют детали, не подготовленные для данной операции. В результате, качество конечного изделия ухудшается. Все выше изложенное предопределило выбор темы и объекта исследования.Делю диссертационной работы является сокращение затрат на обеспечение качества продукции за счет их составляющих, связанных с организацией и управлением производством.Поставленная цель предопределила комплекс задач, важнейшими из которых являются: 1. Исследование затрат на обеспечение качества продукции как экономической категории, отражающей проблемы брака.Е. Анализ структуры затрат на обеспечение качества продукции по их видам, и анализ структуры издержек вследствие выпус- 5 ка продукции низкого качества по видам брака на иракских предприятиях.3. Исследование системы с точкой заказа "Re-order point system" как традиционный метод для определения размера партии деталей и даты запуска-выпуска этих партий и ее влияния на качество продукции.4. Исследование механизма работы системы планирования требуемых материалов ПТМ как инструмента управления материальными потоками и ее влияния на качество продукции.5. Построение принципиальной схемы интеграции системы ПТМ с расчетом использования производственной мощности цеха.6. Разработка динамического метода определения размеров партии деталей в цехах, позволяющих выявить зоны оптимальных вариантов, с помощью которых выбирается рациональный размер партии деталей.Объект исследования. Объектом исследования послужили предпри-" ятия, занимающиеся изготовлением и сборкой изделий, где процесс производства партий деталей различных наименований в цехах организован последовательно, а движение изготовления каждой партии сборочных единиц одного наименования по рабочим местам организовано паралельно.Теоретической и методологической основой диссертации послужит ли труды иракских и зарубежных авторов в области управления затратами на обеспечение качества продукции и в области управления материальными запасами, статистический метод анализа затрат на обеспечение качества продукции (диаграмма Парето), фактические материалы о работе иракских предприятий и их усилий по обеспечению качества продукции. - 6 Научная новизна состоит в следующем: 1. Выявлено, что 40% издержек производства вследствие выпуска продукции низкого качества связаны с недостатками в организации и управлении производством.2. Выявлен ряд недостатков в организации и управлении производством при определении размеров партий деталей, сборочных единиц равных ваказов и при установлении сроков вапуска-выпуска этих партий. Эти недостатки приводят к увеличению времени ожидания партии деталей, сборочных единиц в процессе производства. В результате, возрастает вероятность ухудшения их качества из-за нарушения технологических условий производства.3. В результате проведенного анализа выявлена причина возникновения ошибки в традиционных расчетах производственной мощности, которая возникает при сопоставлении трудоемкости заказа и пропускной способности цеха, так как сопоставление только по объему работ без учета их структуры приводит к завышению производственной мощности, к увеличению уровня незавершенного производства в цехах.4. Разработана методика интеграции системы планирования требуемых материалов и планирования использования производственной мощности каждого сборочного цеха. Она основана на сопоставления производственной мощности цеха, как ресурса времени его работы, и трудоемкости рассматриваемой работы, как времени потребления этого ресурса. Это обеспечивает надежные сроки выпонения работ, управление заделами незавершенного производства и сокращение цикла изготовления конечного изделия в целом. - 7 5. Предложен динамический метод определения размера партии деталей. Этот метод дает возможность выбрать рациональный размер партии деталей,,сборочных единиц, соответствующий условиям производства и целям, к которым стремится руководство предприятия.6. Предложен способ определения зоны оптимальных значений размеров партии деталей на основе соотношения времени наладки для выпонения заказа в целом (Setup time) (Snj + Kfrij)3, технологического цикла (Run time) выпонения заказа (Rnj)3, длительности производственного цикла (Lead time) (Xno) каждой партии и времени ожидания каждой партии (Wnj).Практическая значимость работы определяется тем, что результаты исследования могут служить методологической базой для сокращения издержек на выпуск продукции низкого качества в связи с нарушением технологических условий в цехах, где движения партий деталей разных наименований организовано последовательно и изготовление каждой партии организовано паралельно.Объем и структура работы. Структура работы строилась в соответствии с целью и задачами исследования. Она состоит из введения, трех глав, заключения и списка литературы, изложенных на 130 листах машинописного текста, содержит 19 таблиц и 30 рисунков.В первой главе "Основные понятия, структура и сущность затрат на обеспечение качества прордукции" дан критический анализ существующих определений затрат на обеспечение качества продукции как экономической категории, показано их значение в отражении зффективности работы системы контроля производственного процесса и качества продукции, рассмотрен иракский и зарубежный опыт их сокращения - снижение издержек вследствие выпуска продукции низкого - 8 качества.На основе анализа статистических данных на иракских предприятиях получена диаграмма Парето, которая показала, что 40% издержек вследствие выпуска продукции низкого качества (возникновение брака) происходит из-за ошибок в организации и управлении ходом производства, которые и вызывают нарушения технологических условий.Во второй главе "Методы управления материальными потоками и их влияния на качесмтво продукции" рассматривается несовершенство традиционного метода управления производственными запасами Sistem re-order point) и его влияние на качество продукции. Это несовершенство заключается в том, что данный метод не учитывает отличие зависимой потребности от независимой потребности на продукцию.Показан механизм работы системы ПТМ и ее недостатки при применении системы на иракском предприятии. Эти недостатки заключаются в том, что система ПТМ планирует сроки запуска-выпуска заказов на производство деталей, игнорируя согласование этих сроков с пропускной способностью цеха, и допускает, что производственная мощность цехов позволяет выпонить эти заказы в плановые сроки.Но если производственная мощность цеха недостаточна для выпоне-т ния запланированных заказов, то уровень незавершенного производства в цехе растет. И это приводит к увеличению времени ожидания (пролеживания) заказов в процессе производства.-В конечном итоге, длительность производственного цикла этих заказов увеличивается тоже. Таким образом, вероятность ухудшения качества деталей повышается из-за нарушения технологических условий. Х, ; В этой главе был сделан важный вывод, который заключается в том, что система управления производством дожна быть нацелена на - 9 решения двух взаимосвязанных задач: это планирование заказов на производство деталей и контроль за выпонением этих заказов.Таким решением является использование системы ПТМ допоненной расчетами производственной мощности. В этом случае система ПТМ будет служить "сердцем" интегрированной производственной системы.В третьей главе "Сокращение размера партии деталей - как фактор повышения качества продукции" рассматривается процесс интеграции системы ПТМ с расчетами использования производственной мощности каждого цеха путем деления объема заказа деталей на меньшие партии. Затем сопоставляются ресурсы времени использования производственной мощности цеха в часах и время потребления этого ресурса при выпонении заказа, что обеспечивает надежное согласование сроков и объемов работ с пропускной способностью цеха.По сравнению с традиционным методом согласования производственной мощности цеха и трудоемкости выпоняемых заказов по объему работ в нормо-часах, предлагаемый метод (динамический метод определения размера партии деталей) обеспечивает более поную объективность плану выпонения заказов, и приводит к более точному определению плановых сроков и степени загрузки цеха, так как при сопоставлении учитывается соответствие структуры трудоемкости рассматриваемой работы и структуре пропускной способности цеха.Кроме того, в этой главе рассматриваются выгоды использования динамического метода определения размера партии деталей. Эти выгоды начинаются с сокращения выпускаемого размера партии деталей.Первая прямая выгода от такого сокращения заключается в уменьшении запасов в производстве и сокращении косвенных затрат, связанных с содержанием меньших площадей и оборудования для хранения и подачи материалов. Другая выгода состоит в том, что от сокращения размера партии деталей, уменьшается время ожидания (пролеживания) - 10 этих партий в процессе производства, что обеспечивает сокращение брака из-за неблагоприятных условий хранения выпоненных заказов.Это приводит к уменьшению затрат рабочего времени и материалов на передеку брака, то есть к сокращению издержек вследствие выпуска продукции низкого качества. , - II
Диссертация: заключение по теме "Экономика и управление народным хозяйством: теория управления экономическими системами; макроэкономика; экономика, организация и управление предприятиями, отраслями, комплексами; управление инновациями; региональная экономика; логистика; экономика труда", Аль-Фатлави Карим Абд Идан
ЗАКЛЮЧЕНИЕ
Проведенное в диссертационной работе исследование, посвященное сокращению ватрат на обеспечение качества продукции, позволило сделать следующие выводы.
1. Сущность затрат на обеспечение качества продукции рассматривается как объективная экономическая категория, включающая в себя издержки выпуска продукции низкого качества.
Раскрытие экономической сущности этих затрат дало возможность показать их роль в определении причин возникновения брака и его стоимости в денежной форме.
2. Результаты анализа издержек выпуска продукции низкого качества на иракском предприятии показали, что 40% этих издержек возникает из-за нарушения технологических условий в процессе производства.
Причина этих нарушений заключается в том, что увеличение времени ожидания (пролеживания) партий деталей, которое возникает из-за ошибок в планировании размеров партий деталей и дат их запуска-выпуска), Это время приводит к ухудшению качества этих деталей из-за климатических условий и при плохих условиях хранения.
3. Традиционный метод планирования изготовления деталей по "с точки заказа" (System re-order point) как система управления производственными запасами не подходит для расчета размеров партии деталей и дат их запуска-выпуска. Так как этот метод в условиях рыночных отношений не учитывает характер потребления производственных запасов деталей, необходимых для производства конечного изделия.
С одной стороны, особый характер потребления (спроса) сырья, компонентов и комплектующих узлов непосредственно связан со опросом (потреблением) на конечное изделие, то есть потребность в таких деталях поддается прямому расчету, и не требует прогнозирования, как допускает система с точкой заказа с использованием формулы оптимального размера партии (п0пт)- С другой стороны, потребление деталей из производственных запасов характеризуется скачущей потребностью (Lumpy demand) из-за выпуска деталей партиями и из-за использования отдельных деталей для производства равных сборочных единиц.
В результате, из-за этих недостатков системы с точкой заказа, размер выпускаемой партии деталей и даты его запуска- выпуска не совпадают с необходимым количеством этих деталей. Это приводит к нарушению технологических условий из-за увеличения времени ожидания (пролеживания) этих деталей в процессе производства.
4. Система ПТМ может точно рассчитать объем заказа или размер запускаемой партии деталей на основе использования понятия зависимого потребления, но ее недостаток заключается в том, что она планирует сроки выпонения заказов без согласования с производственной мощностью. В результате, количество заказов, поступающих в цех может быть больше, чем пропускная способность данного цеха. Это приводит к увеличению уровня незавершенного производства и к увеличению производственного цикла для выпонения этих заказов, так как время ожидания заказов в процессе производства увеличивается. Таким образом, нарушаются технологические уело
В работе нами предложен динамический метод определения размера партии деталей, изготовление которых организовано последовательно. Этот метод основан на следующих шагах.
А. Делить объем заказа деталей на более мекие партии, чтобы время ожидания (пролеживания) в процессе производства уменьшилось из-за сокращения технологического цикла этих партий.
Б. Нами предложена интеграция системы ПТМ и расчетов производственной мощности каждого цеха. Процесс интеграции основан на сопоставлении производственной мощности цеха как ресурса времени его работы и трудоемкости рассматриваемой работы как времени потребления этого ресурса цеха. Это обеспечивает надежные сроки выпонения работ, управление заделами незавершенного производства и уменьшение цикла изготовления конечного изделия. Таким образом, нам удается избежать причину ошибки в традиционных расчетах производственной мощности. Эта ошибка возникает при сопоставлении трудоемкости заказа и пропускной способности цеха по объему работ без учета их структуры.
Динамический метод определения размера партии деталей дает руководству предприятия разные варианты вследствие деления объема заказа деталей на мекие партии. В результате, время ожидания (пролеживания) этих деталей в процессе производства уменьшается, но общее время для выпонения заказа в целом увеличивается. Таким образом, зона оптимальных размеров партии определена на основе соотношения Бремени наладки и транспортирования, необходимого для выпонения всего заказа (Snj + Mnj)3, времени технологического цикла выпонения всего заказа (Rnj)3, длительности производственного цикла изготовления каждой партии деталей (Xnj) и времени ожидания (пролеживания) каждой партии деталей (Wnj).
7. Определены выгоды использования динамического метода определения размера партии деталей, которые заключаются в следующем.
A. Сократить объем производственных запасов. Это позволяет экономить на затратах, связанных с использованием площадей складских помещений и оборудования для хранения и подачи материалов.
Б. Сократить количество брака и повысить качество продукции при выпуске изделий более мекими партиями. Это достигается путем сокращения времени ожидания (пролеживания) этой продукции в процессе производства, что снижает вероятность ухудшения качества продукции из-за нарушения технологических условий особенно в условиях жаркого влажного климата Ирака.
B. Повысить ответственность каждого рабочего за возникновение брака, потому что рабочий изготавливает только одно изделие и непосредственно передает его на следующее рабочее место. В случае если его деталь окажется непригодной, то место возникновения брака сразу известно. В результате, рабочие уделяют больше внимания качеству изделий.
Диссертация: библиография по экономике, кандидат экономических наук , Аль-Фатлави Карим Абд Идан, Москва
1. Родионов Б.Н., Саломатин Н.А., Осадчая Л.Г. и другие. Организация, планирование и управление машиностроительным производством. М.: Машиностроение, 1989.
2. Harrington H.J. The improvement Pross, How American Leading1 companies Improve Quality, Mc Graw Hill Book Company, New York, 1987.
3. Будищева И.А., Шготкин Я.Д. Регулирование затрат на обеспечение качества продукции . М.: Издательство стандартов, 1989.
4. Schrocder P.Q. Operation management, Decisign Making: in Operation Functions, Mc Grew Hill Book Company, New York, 1985.
5. Bill Chamber, Managing- Quality Cost Defined, European Organiration for Quality control, VOL, XXVII. N 2 (May), 1984.
6. Jack campanella and Frank J.Corcoran, Principles of Quality cost, Quality Progress, VOL, XV. N 4 (April), 1983.
7. Lee Blank & Jorge Solorzano, Using Quality Cost Analysis for Management Improvement, Industrial Engineering,
8. Vol.10, N 2 (February), 1978.
9. European organization for Quality control (EOQC) Glossory, 1976.
10. American Sociaty for Quality control (ASQC), Quality Control and Reliability management, Milwaukee, ASQC, 1969.
11. Glenn, E.N. & Harry G.R. Modern Quality Control, California, Benriger Brue & Giencoc, Inc. 1977.
12. Grosby, Philp В., Quality is free, New York, Mc Graw -Hill, 1979.
13. Juran J.M. & Frank M.G., Quality Planning- and Analysis, New York, Mc Graw Hill,Inc., 1970.
14. Groocock J.M., The Cost of Quality. London, Sirdsaac pitman and Sons Ltd, 1974.
15. ASQC, Guide for Reduciny Quality Cost, 1980.
16. Шеремет А.Ю., Силин A.H. Качество продукции, Экономический словарь. М.: 1990.
17. Kaoru Ishikawa. What is total Quality control. The Japanese way for Reducing production lost, Tokio, 1980.
18. AL- Ubaidi M.B., Analysis efficiency Cost of Quality, in partial ful fulfilment of Master Degree of bussiness administration, Unversity of Bagdad, 1986.
19. Макино Т., Охаси M., Доке Х.Х. Контроль качества с помощью персональных компьютеров. Пер. с яп. А.Б. Орфенова. Под ред. Ю.П. Адлера М.: Машиностроение, 1991.
20. Mongon, Yasuniro, "Adaptable Kanban system Helps Toyota Maintain Just-in-time Production", Indastrial Engieering, May, 1981.
21. Walleac T.F., ARICS Dictionary 4th-ed., American production and Inventory control Society, Wasington D.C., 1980.
22. Orlicky J. Material Requirements Planning, Mc Graw Hill Book Company, New York, 1975.
23. Al-Fatlwy, Kareem, The Impict of the Bill of Matirals (B.O.M) on the implementation of matirals requirements planning, in partial Ful fulfilment of Master Degree of bussiness administration, AL-Mustansiriyah University, 1988.
24. Monks J. G., Operation Management, Mo Graw Hill Book Company, New York, 1985.
25. Adem G. E. & Ebert R. J. Production and operation Management, Concepts, Models and Behavior, New Jersey, Prentic -Hall, Inc., 1982.
26. Anderson J. C. et al, Materials Requirement Planning system, the state of the Arty Rroduction and Inventory management, Vol. 23 N 4, 1982.
27. Wemmerlov I., Design Factors In MRP, A Limited survey, Production and Inventory managment, Vol. 7 N 4, 1976.
28. Tersine R.J., Principles of Inventory and materials management, New York, Elseviver Science publishing Co., Inc., 1984.
29. Sunn Q.T. Computer Application in Manufacturing, New York, Industrial press Inc., 1981.
30. Mether H. & Possel G. Priority Fixation versus throughput production and inventory management, Vol. 19, N 3, 1978.
31. Makell P.G. & Emory W.Z. CAD/CAM. Computer-Aided Design and Manufacturing, Prentice-Hall, Inc., Englewood cliffs, New Jersey, 1984.
Похожие диссертации
- Управление затратами на качество продукции в системе калькуляционного учета
- Организационно-техническое обеспечение качества продукции в кожевенной промышленности
- Совершенствование управления торгами для обеспечения качества продукции, поставляемой для государственных нужд
- Социально-экономический механизм защиты прав потребителя в обеспечении качества продукции
- Учет затрат на обеспечение качества продукции