Задание принял к исполнению Введение
Вид материала | Курсовая |
- Задание принял к исполнению Дата, 69.4kb.
- Задание принял к исполнению / / (подпись) (Ф. И. О.), 6.91kb.
- Задание принял к исполнению Дата, 27.29kb.
- Задание принял студент задание на курсовую работу по курсу, 123.82kb.
- Власти, по исполнению публичных обязательств перед физическим лицом, подлежащих исполнению, 33.08kb.
- Порядок осуществления муниципальными бюджетными учреждениями полномочий по исполнению, 40.55kb.
- Курс 5 семестр 9 группа студент принял: преподаватель Липецк г Задание кафедры, 101.85kb.
- Первое задание 7 Второе задание 10 Третье задание 24 Четвертое задание 30 Вопросы, 344.04kb.
- Задание на курсовой проект, 167.11kb.
- Анализ экономической эффективности финансово-хозяйственной деятельности предприятия, 481.25kb.
Федеральное агентство по образованию Российской Федерации
ГОУВПО
Кафедра "Физико-химические процессы и технологии"
КУРСОВАЯ РАБОТА
по дисциплине "ФИЗИЧЕСКИЕ И ЭЛЕКТРОФИЗИКОХИМИЧЕСКИЕ МЕТОДЫ ПОЛУЧЕНИЯ ЗАГОТОВОК"
на тему "Проектирование отливки детали «Шарнир»".
студента гр. 430141
Студент Макарова А.С.
Руководитель Гнидин В.И.
Тула 2008
Федеральное агентство по образованию Российской Федерации
ГОУВПО
Кафедра "Физико-химические процессы и технологии"
Задание на курсовую работу
Студент __________________________ Группа ____________
Тема: проектирование отливки детали «Шарнир»____________________
Срок представления работы к защите "_____"__________________________________
- Исходные данные для проектирования ________________________________________
_____________________________________________________________________________
3. Перечень графического материала: чертеж детали с ТУ.
Руководитель работы __________________________________________________________
Задание принял к исполнению __________________________________________________
Введение
В настоящее время в нашей стране сложилась такая ситуация, что развитие промышленности является самой приоритетной из всех поставленных задач. Для того, чтобы Россия заняла прочное место среди ведущих мировых держав, в ней должна существовать развитая сфера промышленного производства, которая должна основываться не только на восстановлении основанных в советское время заводов, но и на новых, более современно оборудованных, предприятиях.
Среди отраслей народного хозяйства особое место занимает машиностроение. Это объясняется тем, что машиностроение является основой развития с/х, металлургии, строительства и других отраслей промышленности. Высокий уровень машиностроения является базой для укрепления обороноспособности страны и повышения благосостояния ее населения, залогом успеха в освоении космоса, в борьбе с болезнями и стихийными бедствиями.
В машиностроении существует несколько методов изготовления исходных заготовок:
- Литье. Технология получения отливок известна человечеству с древнейших времён. Её история начиналось на заре земных цивилизацией ранее 4 тыс. лет до н.э. За такой исторический период литейное производство превратилось в одну из отраслей промышленности, использующей наряду с древнейшими традициям все современные достижения науки и техники: компьютерные технологии, лазеры, электронику и автоматику, композиционные материалы, сплавы с заранее заданными свойствами, биотехнологии и др.
- Обработка давлением. Обработка, заключающаяся в пластическом деформировании или разделении. Включает в себя процессы – волочение, прессование, прокатка.
- Изготовление изделий из порошков
Производство изделия, его сущность и методы оказывают наиболее весомое влияние на технологические, эксплуатационные, функциональные и др. свойства этой продукции, а, следовательно, на его себестоимость, от которой в прямой зависимости находятся цена изделия, спрос со стороны пользователей, объемы продаж, т.е. все экономические показатели, которые и определяют финансовую устойчивость предприятия. Т.о., то как изготавливается продукция, оказывает влияние на весь жизненный цикл товара.
Целью данной курсовой работы является ознакомление непосредственно с технологическими возможностями штамповки на винтовых и фрикционных прессах (часть 1), а также выбор и обоснование способа получения исходной заготовки из латуни (часть 2).
^
Технологический анализ чертежа и ТУ детали, условий работы детали в изделии.
Деталь - шарнир изготовлен из латуни марки ЛМцС 38-2-2 ГОСТ 1020-77. Из такой латуни выполняют подшипники, втулки, аппаратуру судов и другие антифрикционные детали. Содержание элементов по массе (остальное цинк): 57-60% Cu; 1,5-2,5% Mn; 1,5-2,5% Pb. Содержание примесей, не более: 0,8% Al; 0,5% Sn; 1% Ni; 0,1% Sb; 0,4% Si; 0,8% Fe; 0,05%P. Латунь достаточно устойчива против общей коррозии, но в напряженном состоянии очень чувствительна к коррозионному разрушению. Необходимо подвергать ее отпуску при 280-3000. Данная латунь обладает удовлетворительными литейными свойствами. Плотность ρ=8,47 г/см3.
^
Анализ технологических возможностей методов и способов изготовления исходных заготовок.
Деталь, изготовленную из такого материала в соответствии с ГОСТ 17711-72 можно получить литьем в кокиль, литьем по выплавляемым моделям и литьем в землю. Физические и механические свойства материала (первая цифра - литье в кокиль, вторая – в землю): предел прочности при растяжении, кгс/мм2 – 35/25; относительное удлинение, % - 8/10; твердость НRCэ – 33,5-36,0. Тип производства- мелкосерийное.
^
Литье по выплавляемым моделям
Литье по выплавляемым моделям применяется для изготовления сложных и точных заготовок практически из любых сплавов. В этом случае для каждой отливки изготавливается разовая модель с элементами литниковой системы из легкоплавкого модельного состава (на основе парафина, стеарина, церезина и других материалов выплавляемых моделей) из растворяемого (на основе солей), из газифицируемого (на основе полипропилена). Формовочная смесь в виде жидкой суспензии наносится в несколько слоев (до 12) с сушкой каждого слоя на воздухе в течение 2...4 ч. После выплавления (растворения, газифицирования) моделей и прокаливания получают прочную тонкостенную оболочку толщиной 1,5...4,0 мм.
Полученная форма не имеет разъемов и знаковых частей. Это даёт высокую точность размеров (4-11 класс) и взаимного расположения поверхностей. В качестве огнеупорной составляющей в формовочной смеси используется пылевидный кварц, благодаря чему может быть достигнут параметр шероховатости поверхности Rz - 20... 12 мкм. Заливка металла производится чаще всего сразу после прокаливания, т. е. в формы, нагретые до 900 °С. Этим создается благоприятные условия для заполнения формы и питания отливки во время кристаллизации.
Механическая обработка полученных заготовок сводится к минимуму или может быть полностью исключена. В то же время это самый сложный, самый длительный и трудоемкий способ литья. Применяется для изготовления заготовок размерами от 0,5 до 1250 мм.
Литьем по выплавляемым моделям экономически наиболее выгодно изготавливать мелкие, но сложные по конфигурации заготовки, к которым предъявляются высокие требования по точности размеров и шероховатости поверхности или которые собираются (свариваются) из двух и более элементов. Обычно льют детали из цветных сплавов, высоколегированных сталей, жаропрочных сплавов, плохо обрабатывающихся резанием или обладающих низкими литейными свойствами. Основная часть экономии при этом способе литья достигается за счет уменьшения массы заготовки и объема ее механической обработки. Литьем по выплавляемым моделям можно получать сквозные и глухие (заглушённые с одной стороны) литые отверстия. Сквозные литые отверстия диаметром d = 5 мм и длиной 1 = (4 - 6)d получают без затруднений.
^
Литье в песчано-глинистые формы.
Литейную форму, имеющую полость, в которую заливают расплавленный металл, изготавливают из формовочной смеси по модели. Модель - это приспособление для получения в форме рабочей полости будущей отливки. Модели могут изготавливаться из дерева, пластмассы или металла, размеры их должны быть больше размеров отливок на величину усадки металла и величину припуска для последующей механической обработки.
Формовочные смеси для литейных форм и стержней состоят из кварцевого песка, специальной глины, воды и ряда добавок (льняного масла, канифоли, декстрина, жидкого стекла, деревянных опилок или торфяной крошки), обеспечивающих газопроницаемость и пластичность смеси. При изготовлении формы формовочную смесь, увлажненную и тщательно перемешанную, засыпают в нижнюю опоку, предварительно установив модель отливки. Затем смесь уплотняют вручную различными приспособлениями или на специальных формовочных машинах. После уплотнения смеси модель извлекают из нижней опоки. Аналогичным образом уплотняют смесь и в верхней опоки, предварительно установив в нее, помимо модели отливки, модель литниковой системы, образующую каналы для заливки жидкого металла в полость литейной формы. Литниковая система состоит из литниковой чаши, вертикального стояка, шлакоуловителя, питателя и выпора. Литниковая система должна обеспечивать плавное поступление расплавленного металла в форму и отвод газов из формы.
Затем, установив стержни в форму, производят её сборку: верхнюю опоку устанавливают на нижнюю и фиксируют опоки штырями. В таком виде форма готова к заливке расплавом.
Плавку металла выполняют в различных плавильных устройствах. Чугун плавят в вагранках, сталь - в конверторах и электропечах, цветные металлы и их сплавы - в электрических печах и тиглях. Температуру расплавленного металла доводят до температуры заливки, т.е. на 100…150 С выше температуры плавления сплава.
После заливки расплава в литейную форму и его охлаждения, отливки выбивают из формы и очищают от формовочной смеси вручную, на вибрационных решетках или дробеструйных установках. Обрубку элементов литниковой системы выполняют дисковыми фрезами, ленточными пилами, на обрезных прессах, газопламенными или плазменными резаками. Зачистку отливок от заусенцев и заливов выполняют абразивными кругами.
Перед отправкой в механические цехи стальные отливки обязательно подвергаются термической обработке – отжигу или нормализации – для снятия внутренних напряжений и измельчения зерна металла. В отдельных случаях термической обработке подвергаются отливки и из других сплавов.
Преимуществом литья в песчано-глинистые формы является невысокая стоимость формовочных материалов и модельной оснастки. Однако этот способ литья является более трудоемким в сравнении с другими. Кроме того, литьё в песчано-глинистые формы обеспечивает малую точность размеров и большую шероховатость поверхности.
^
Литьё в кокиль
Литьем в кокиль изготавливают отливки сложной конфигурации преимущественно из сплавов с узким интервалом кристаллизации (латуни, алюминиевые бронзы), так как они менее склонны к образованию трещин при затрудненной усадке, чем сплавы с широким интервалом кристаллизации. Простые же по форме отливки (слитки, втулки с песчаным стержнем, заготовки под шестерни и др.) можно отливать из любых медных сплавов.
При литье в кокиль металл заливается в металлические формы, теплопроводность которых в 50-60 раз превышает теплопроводность песчаных форм. Кокили изготавливают из чугуна, а металлические стержни из стали. Для увеличения срока службы форм и стержней их охлаждают водой. Сложные полости в отливках выполняют песчаными стержнями. По конструкции механизмов разъема, выталкивания отливок и устройству вентиляционных каналов кокили для медных сплавов аналогичны кокилям для легких сплавов.
Заливку металла ведут в нагретые до 350—400 °С формы. Чтобы облегчать извлечение отливок и для охлаждения рабочей поверхности, полость формы перед заливкой смазывают суспензией машинного масла с 6 % графита. Так же как и при литье в разовые формы, для изготовления отливок из алюминиевых и кремнистых бронз и латуней применяют расширяющиеся литниковые системы с нижним или боковым подводом металла, обеспечивающие спокойное заполнение кокилей; для сплавов, не образующих окисных пленок, используют литниковые системы с верхним подводом металла или осуществляют заливку через прибыль.
При разработке технологии основное внимание уделяют созданию направленной кристаллизации отливок. В целях снижения величины усадочных напряжений в отливках их извлекают из металлических форм сразу же после приобретения ими достаточной механической прочности (при 500—600°С)
В зависимости от положения плоскости разъёма металлические формы выполняются с вертикальной, горизонтальной и наклонной плоскостями разъёма.
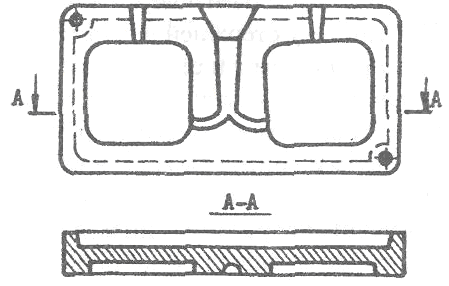
^ Рис. 1. Металлическая форма с вертикальным разъёмом
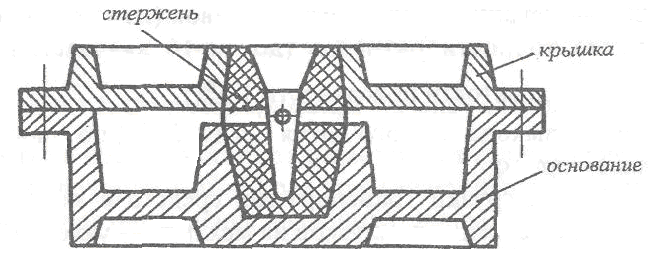
Рис. 2. Металлическая форма с горизонтальным разъёмом
Преимущества литья в кокиль:
- отсутствие формовочных смесей;
- улучшение механических свойств отливок, повышение точности отливок (до 12-16 квалитетов точности) и обеспечение низкой шероховатости;
- снижение загрузки металлорежущих станков вследствие снижения припусков на механическую обработку.
К числу недостатков относят:
- высокая стоимость изготовления металлических форм;
- потребность в дорогостоящем оборудовании;
- малая податливость форм;
- отсутствие газопроницаемости металлической формы.
^
Выбор рационального способа изготовления исходной заготовки
На основе проведенного анализа требований чертежа и ТУ на деталь и возможностей методов и способов изготовления исходных заготовок выбираем наиболее приемлемый метод литья по выплавляемым моделям, т.к. он позволит уменьшить объем механической обработки. Устанавливаем класс точности отливки – 9т (табл. П 17 [5]), степень коробления – (табл.3,33 [6])
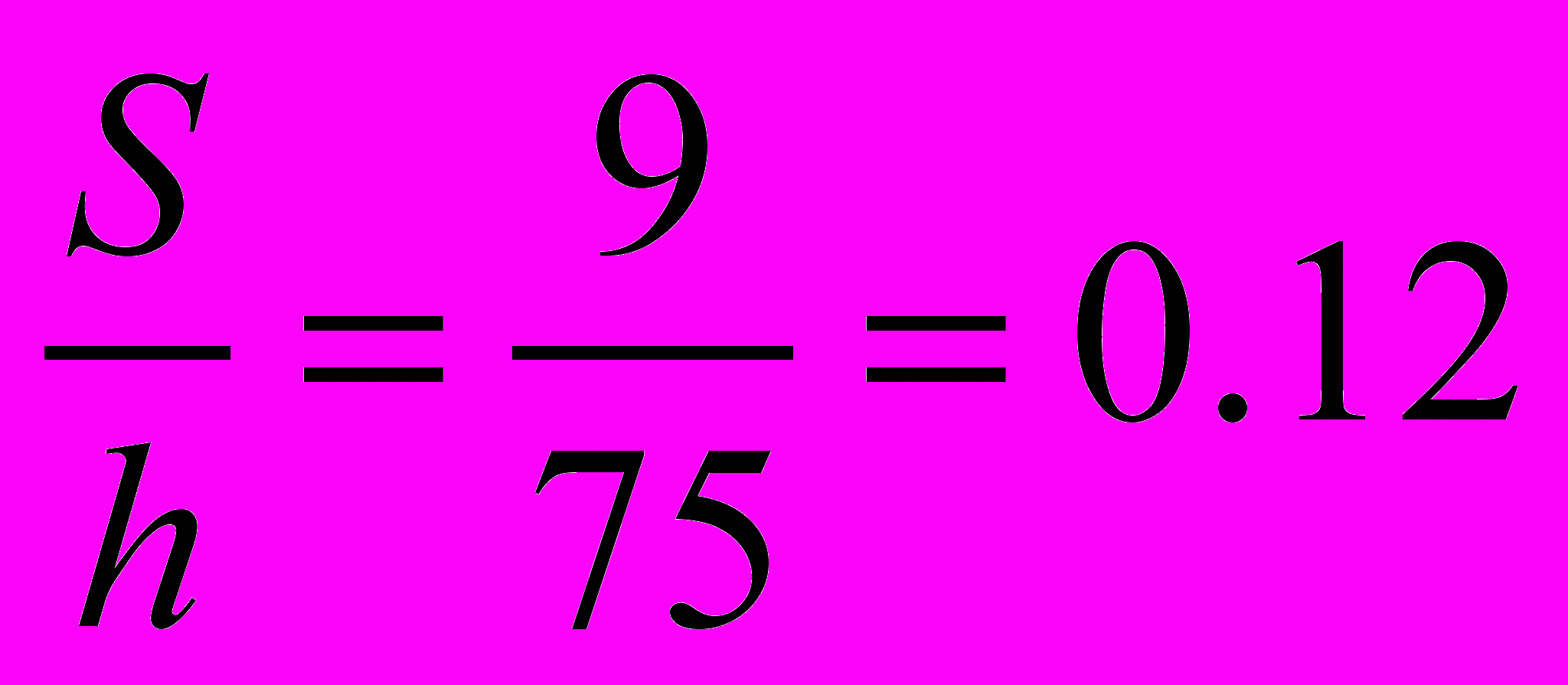
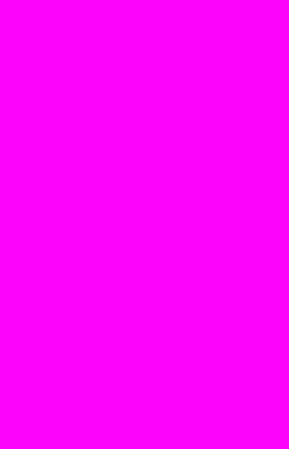
^
Выбор конфигурации и расположения поверхности разъема
Для заданной детали целесообразна плоская поверхность разъема. Наиболее рациональное расположение - по оси симметрии.
^Выбор черновых баз
Черновыми базами будут служить цилиндрическая поверхность размером 75-40=35 мм и торец Ø18.
Проектирование стенок
Для отливки, изготавливаемой литьем по выплавляемым моделям, толщина стенок определяется по табл. 3.13. Для медных сплавов Smin=2 мм. Следовательно, поверхность размером 18-9=9мм, 20-7=13 мм, а так же (Ø18-Ø12)/2=3 мм, могут быть получены литьем.
^
Установление припусков на обработку
№ п/п | Поверхность размером, мм | Допуск в соответствии с квалитетом точности размеров детали, мм | ^ Допуск в соответствии с классом размерной точности отливки, мм | Шероховатость поверхности Ra, мкм | Вывод | ||
Класс точности | Допуск | детали | отливки | ||||
1 2 3 4 5 6 7 | Ø40 75 Ø18 9 40 Ø14 Ø12 | -0,74 -0,74 -0,5 -0,43 -0,74 +0,11 +0,11 | 9т | 1,6 1,8 1,2 1,0 1,6 1,1 1,1 | 5 5 5 5 1,25 5 5 | 5 | +* +* +* +* - - - |
«+» - необрабатываемая поверхность «-» - обрабатываемые поверхности
«*» - согласовать с конструктором-разработчиком
^
Определение параметров отливки
№ п/п | Поверхность размером | Размер до базы | Допуск размера детали ТδRT, мм | Допуск размера отливки Тотл | Тд/Тотл | Вид окончательной обработки | Припуск на сторону, мм, Z0 | Размер отливки, мм |
1 2 3 | Ø14 Ø12 32 | 9 | 0,11 0,11 0,74 | 1,1 1,1 1,4 | 0,1 0,1 0,53 | чистовая чистовая черновая | 0,8 0,8 1,2 | 12,4 10,4 10,2 |
^
Определение возможности получения отверстий
- отверстие Ø14, S=9 получить можно литьем, т.к d>5.
- отверстие Ø12, S=30, d/l=12/30=0,4<0,5 – получить трудно, т.к.сложно изготовить керамическую форму удовлетворительного качества.
Назначение напусков и формовочных уклонов
Напуск назначаем на отверстие Ø12, т.к. оно получается механическим путем. Формовочные уклоны назначаем в соответствии с табл.3.15[5]
Поверхность | Размер, мм | Величина формовочного уклона |
Правый торец Левый торец Уступ | Ø18/2=9 18-9=9 9 | 30´ 30´ 30´ |
^
Назначение размеров сопряжений
В соответствии с требованиями чертежа можно назначить радиусы всех сопряжений – 3 мм
Назначение технических условий на изготовление отливки
- Твердость НRCэ 33,5-36
- Неуказанные формовочные уклоны 30´, литейные радиуса R3
- На необрабатываемых поверхностях допускаются раковины до Ø3 мм и глубиной не более 0,5 мм
- Точность отливки 9т-3-14-10 по ГОСТ 26645-85.
Заключение
19 век знаменуется тем, что в литейное дело, как и в другие области промышленности, впервые проникает наука. Литейное дело с дедовскими приемами и секретами работы постепенно превращается в литейное производство с научным обоснованием технологических процессов.
Среди работ первостепенной важности в области науки о металлах в 19 в. следует назвать работу русского ученого Д.К.Чернова – основоположника современного металловедения, без которого невозможным было создание тех высокопрочных и специальных марок сталей и других сплавов, являющихся основой машиностроения в наше время.
Однако, в старой, дореволюционной России машиностроение было отсталым участком народного хозяйства. Поэтому и литейное производство не получало такого развития, которое оно получило после октябрьской революции. Одновременно с бурным развитием машиностроения почти заново создано литейное производство. Освоены новые литейные процессы – центробежное литье, кокильное литье, отливки под давлением. Рассматривая исторический процесс совершенствования литейного производства в СССР, а также и в зарубежных странах, можно отметить следующие основные направления его развития в области литейных сплавов и металлургических процессов, в области технологии и в области механизации.
В области литейных сплавов, применяемых для фасонного литья, процесс литейного производства характеризуется, прежде всего, научным изучением чугуна как литейного материала и повышением его прочностных свойств.
Кроме усовершенствования чугуна как литейного материала, в ходе развития литейного производства исследуются и совершенствуются свойства и методы получения ковкого чугуна и сталей для фасонного литья, а также цветных металлов. Особенно большие успехи достигнуты в освоении легированных сталей, обладающих различными особыми физическими, химическими, электрическими и механическими свойствами. Наконец, реактивная техника наших дней потребовала создания и освоения еще более новых, особых жаростойких и сверхтвердых литейных сплавов типа виталиума и др.
В области технологии литейного производства внимание было направлено главным образом на разрешение проблемы точности отливок и снижения трудоемкости. Сюда относят такие средства, как научные изучения и улучшение формовочных и стержневых материалов с применением новых их видов, внедрения повседневного и непрерывного лабораторного контроля этих материалов в производстве, развития машинной формовки по металлическим моделям и стержневым ящикам, а также специальных методов литья: кокильного, литья под давлением, центробежного. В последнее время возможности получения точных и хорошего качества отливок еще более расширились благодаря разработанным методам скоростной формовки с применением быстросохнущих смесей и продувки форм углекислотой, применению для крупных отливок, оболочковых форм на основе химически твердеющих смесей. В литейном производстве в настоящее время работает очень много разнообразнейших технологических и транспортирующих машин и устройств, механизирующих все звенья и операции технологического процесса, начиная от разгрузки прибывающих в цех сырых материалов и кончая контролем готовых отливок. Дальнейшее направление развития в этой области заключается в разработке и широком внедрении автоматизации литейного производства, вплоть до комплексной сквозной автоматизации с созданием автоматических линий, пролетов и цехов, что уже и наблюдается в действительности.
В данной работе были описаны возможные способы получения заготовки. Исходя из ТУ и типа производства, а также материала заготовки выбран наиболее эффективный и экономически выгодный способ ее получения. Спроектирован чертеж отливки.
^
Библиографический список:
- Курдюмов А.В. Литейное производство цветных и редких металлов. М.: Металлургия, 1982. – 352 с
- Технология литейного производства. Литье в песчано-глинистые формы./ Трухов А.П. М.: Академия, 2005. – 524 с
- Анурьев В.И. Справочник конструктора-машиностроителя. М.: Машиностроение,1980. – 728 с
- ГОСТ 26645-85 Отливки из металлов и сплавов.
- Гнидин В.И., Щукин А.С., Березин А.О. Изготовление изделий литьем: учебное пособие. – Тула: ТулГУ, 2007. – 152 с.
Оглавление:
Введение | 3 |
| 5 |
| 5 |
| 5 |
| 6 |
| 8 |
| 10 |
| 11 |
| 11 11 11 12 12 12 12 13 |
| 14 |
Приложение | |
| 15 |
| |
| |
| |
| |
| |
| |
| |
| |
| |
| |