Литейные свойства металлов и сплавов
Вид материала | Документы |
- Примерная программа дисциплины механические свойства металлов, 122.33kb.
- Ю. М. Дедков, М. Г. Слотинцева Сб. «Свойства и применение платиновых металлов и сплавов, 100.81kb.
- «производство отливок из сплавов цветных металлов», 38.25kb.
- Ться с методикой определения электропроводности металлов, экспериментальным и расчетным, 109.79kb.
- Гост 1639-78: лом и отходы цветных металлов и сплавов общие технические условия, 1661.44kb.
- 3 Технические требования, 688.9kb.
- Свойства литейных алюминиевых сплавов и области их применения. Литейные алюминиевые, 53.7kb.
- Лекция 17. Свариваемость металлов и сплавов, 106.25kb.
- Реферат по теме: «Металлы. Свойства металлов.», 196.2kb.
- Междунаро дная научно-техническая конференция «Технологии термической и химико-термической, 357.66kb.
Основы литейного производства.
Литейные свойства металлов и сплавов.
Литейными свойствами называются такие технологические свойства металла и сплава, которые определяют его пригодность для получения качественной отливки (без литейного брака). Литейные свойства металлов и сплавов зависят от их химического состава и физических свойств. Они оказывают большое влияние на выбор технологического процесса изготовления отливок.
Основными литейными свойствами металлов и сплавов являются жидкотекучесть, усадка и склонность к ликвации.
Жидкотекучесть.
Жидкотекучесть характеризует способность расплавленного сплава заполнять сложные полости формы. Величина жидкотекучести зависит от состава сплава, степени его перегрева, а также от материала формы. Жидкотекучесть наиболее высока у сплавов алюминия, оловянистых бронз, серого чугуна и кремнистых чугунов. Меньшей жидкотекучестью отличаются углеродистые и низколегированные стали, белый чугун и безоловянистые бронзы. Жидкотекучесть выше при заливке сплава в сухие формы, меньше при заливке в сырые песчаные формы и еще меньше при литье в постоянные металлические формы.
Сравнительная жидкотекучесть различных сплавов определяется с помощью специальных технологических проб. Наиболее распространена спиральная проба. Для ее проведения в литейной форме формуется спиральный канал постоянного сечения. Длина спирального канала, по которому протекает металл до затвердевания, характеризует величину жидкотекучести.
Ликвация.
Ликвация проявляется в неоднородности химического состава в различных точках отливки. Различают дендритную и зональную ликвацию. При дендритной ликвации происходит образование неоднородных по своему составу зерен сплава, а при зональной — неоднородных зон в различных частях отливки. Ликвация увеличивается при увеличении в сплаве содержания примесей, имеющих большой удельный вес, или примесей с низкой температурой плавления (S, Р и др.). При дендритной ликвации легкоплавкие компоненты скапливаются на поверхности отливок или в промежутках между затвердевающими кристаллами.
Зональная ликвация, в противоположность дендритной, увеличивается при медленном охлаждении отливки, когда создаются условия для перемещения различных фаз под действием разницы удельных весов.
Характерным для зональной ликвации является то, что наружные участки и тонкие стенки отливки, охлаждаемые в первую очередь, содержат ликвирующих примесей меньше, чем застывающие позже более массивные части.
На физико-механические свойства отливок и эксплуатационные качества литых деталей оказывают влияние и другие факторы. Одним из них является способность металлов и сплавов поглощать газы, попадающие из шихтовых материалов, окружающей среды, материала формы и т. д. Растворимость газов в расплавленном металле зависит от температуры — с понижением температуры уменьшается растворимость, и наоборот.
^ Усадка отливок.
Усадка характеризует свойство металлов и сплавов уменьшать свои размеры и объем при затвердевании и последующем охлаждении. При изготовлении модельного комплекта необходимо учитывать усадку металла отливки при затвердевании. Величина припусков на усадку отливки приведена в табл. 1.
Таблица 1. Линейная усадка отливок.
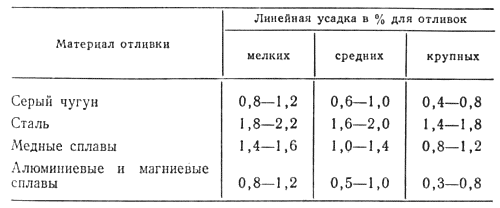
Под объемной усадкой подразумевают разницу между объемом жидкого сплава, заполнившего полость формы, и объемом отливки после ее охлаждения. Объемную усадку, как и линейную, выражают в процентах по отношению к объему отливки.
Объемная усадка равна
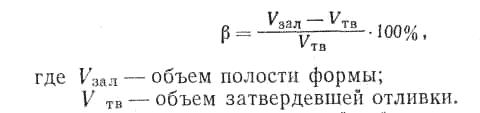
.
Линейная усадка равна

Усадка является причиной образования внутренних пустот в отливках, трещин и коробления.
Величина усадки сплава определяется его химическим составом и температурой перегрева. Так, усадка серого чугуна уменьшается при увеличении содержания С и Si или при снижении Мп и S.
Когда сечение отливки имеет простые очертания, стенки одинаковой толщины и уменьшение объема металла происходит равномерно, не встречая сопротивления со стороны материала формы или стержня, усадка проходит свободно. При получении отливок сложного профиля части формы и стержня могут противодействовать усадке, поэтому действительная ее величина может оказаться меньше по сравнению со свободной усадкой при отливке деталей простой конфигурации.
Кроме такого механического торможения усадки при остывании отливки, имеющей значительную разницу в толщинах отдельных сечений, возникает термическое торможение из-за различной длительности остывания. Механическое и термическое сопротивление усадки приводит к тому, что в металле остывающей отливки возникают внутренние (литейные) напряжения.
Литейные напряжения, вызванные термическим торможением усадки, обычно приводят к деформации, короблению, а в ряде случаев к образованию трещин ("горячие" и "холодные" трещины). Иногда эти деформации проявляются после механической обработки, когда срезание наружного слоя металла приводит к медленному перераспределению внутренних напряжений. Этим вызывается необходимость длительной выдержки (старения) деталей после грубой механической обработки. Естественное старение может продолжаться несколько месяцев. Отделочная механическая обработка после старения уже не вызывает коробления детали.
Для предотвращения «горячих» трещин нужно обеспечить технологически необходимую плотность набивки литейных форм, применять стержни только установленной конструкции и из рекомендуемых материалов, достаточно податливых в момент затвердевания сплава.
^ Газовые раковины.
Свойство металлов и сплавов поглощать газы может привести к появлению в отливке газовых раковин. С понижением температуры жидкого металла растворимость газов в нем уменьшается и они, выделяясь, стремятся удалиться из металла. Но при увеличивающейся вязкости сплава (из-за понижения температуры) и при недостаточной газопроницаемости формы или стержней эти газы могут остаться в отливке, образуя пустоты, не заполненные металлом,— газовые раковины.
Рассмотренные выше литейные свойства сплавов и их влияние на механические свойства отливок учитываются при проектировании отливки. Так, зная жидкотекучесть отдельных сплавов, нельзя проектировать отливки из них со стенками толщиной ниже некоторых предельных значений. Поэтому при литье в песчано-глинистые формы рекомендуется следующая минимальная толщина стенок (мм):
- медные сплавы — 2;
- ковкий чугун — 2,5;
- серый чугун и алюминиевые сплавы — 3;
- стальные отливки — 5.
При этом нужно помнить, что чем тоньше стенки отливки и сложнее ее очертания, тем более высокой должна быть температура заливки сплава для обеспечения заполнения формы.
Специальные виды литья.
Способы литья в песчано-глинистые формы связаны с большим грузооборотом вспомогательных материалов, отличаются большой трудоемкостью и в ряде случаев не дают качественных отливок. Поиски более совершенных технологических процессов привели к созданию таких способов литья, как литье в металлические формы (в кокиль), под давлением, центробежное литье, по выплавляемым моделям, литье в оболочковые формы и др.
Перечисленные способы позволяют получать отливки с более высокой точностью и чистотой поверхности и значительно улучшают условия труда.
Вместе с тем эти технологические процессы не лишены недостатков. Так, некоторые из них (литье под давлением, в кокиль и центробежное) не позволяют получать отливки из всех сплавов и различной конфигурации, другие связаны с использованием дорогих и дефицитных материалов (литье по выплавляемым моделям и в оболочковые формы), в результате чего применение их выгодно только для определенной номенклатуры сложных тонкостенных отливок. Эти методы в отличие от общераспространенного литья в песчано-глинистые формы получили название специальных методов литья.
^ Литье в металлические формы (кокили).
Литье в металлические формы (кокили) обладает рядом преимуществ по сравнению с литьем в песчано-глинистые формы.
При затвердевании в металлической форме отливки получают более мелкозернистую плотную структуру металла. В связи с этим улучшаются механические свойства отливок. Они имеют большую точность размеров с минимальными припусками на механическую обработку. За счет уменьшения припуска на механическую обработку повышается выход годного литья. Использование формовочной площади повышается в несколько раз, что дает возможность без расширения литейных цехов повысить выпуск литья. Значительно возрастает производительность труда, причем рабочие быстрее приобретают необходимые навыки. Этот способ приводит к снижению себестоимости литья.
Вместе с тем производство литья в металлические формы имеет свои трудности. Так, изготовление металлических форм требует значительных затрат и продолжительного времени освоения. Высокая теплопроводность металлических форм затрудняет получение сложных тонкостенных отливок большого габарита. Невозможно получать отливки, имеющие внутренние и наружные сложные очертания.
Особенно сдерживает литье в металлические формы относительно малая стойкость кокилей и их неподатливость, что приводит к образованию трещин в отливках. Поэтому литье в кокили применяется в основном при изготовлении деталей из цветных сплавов, обладающих меньшей температурой плавления и меньшей склонностью к образованию трещин. Стойкость металлических форм при заливке алюминиевых сплавов доходит до 300 тыс. заливок, а при отливке чугунных деталей всего 150-300 заливок.
Выбор типа конструкции металлической формы в основном зависит от технических условий получения качественной отливки, ее конфигурации, веса и точности геометрических размеров. При этом следует учитывать возможность механизации, удобство и безопасность обслуживания форм, себестоимость отливок.
Формы без разъема имеют большую жесткость, меньше коробятся и применяются обычно для отливок простой конфигурации. После заливки металлом и охлаждения отливки форма на цапфах поворачивается на 90—180° и отливка выбивается.
В формах с горизонтальной плоскостью разъема одна половина формы обычно крепится неподвижно, другая при помощи приспособлений закрывает и открывает ее. Литниковая система в таких формах обычно изготовляется в песчаном стержне. После заливки и остывания верхняя половина формы поднимается и отливка выбивается. В таких формах более точно можно установить и закрепить песчаные стержни, зато затруднена выбивка отливок. Механизировать их труднее, чем другие типы металлических форм.
Формы с вертикальной плоскостью разъема применяются для простых и средних по сложности отливок. В плоскости формы располагаются полости для отливок и литниковая система. После заливки форма раскрывается и отливка выбивается.
В металлических формах чаще всего применяют прямолинейный разъем. Криволинейный разъем применяют в тех случаях, когда невозможно получить качественную отливку другими способами.
Отливки сложных очертаний и большого габарита отливаются в формах с несколькими разъемами.
Для металлических форм применяются металлические (чугунные или стальные) и песчаные стержни, при литье из цветных сплавов — металлические стержни сложной конфигурации (цельные пли разрезные), а для чугунного литья — стержни простой конфигурации с большими уклонами для облегчения выемки.
Для предохранения рабочей поверхности кокиля от воздействия жидкого металла применяются огнеупорные краски. Они изготавливаются из талька, молотого шамота, графита, огнеупорной глины, мела и раз. личных связующих материалов (жидкое стекло, патока, сульфитный щелок и т. д.).
В массовом и серийном производстве для литья в металлические формы применяют специальные машины. На машинах механизируются операции по открыванию и закрыванию форм, выемке отливки, установке и выемке стержней, выбивке отливок из формы.
^ Литье под давлением.
Литьем под давлением называется способ получения фасонных отливок в металлических формах, при котором заполнение формы и кристаллизация металла производится под принудительным давлением. Этот способ применяется в массовом производстве для изготовления тонкостенных отливок из сплавов цветных металлов. Он обеспечивает высокую точность размеров отливок, большинство которых не требует дальнейшей механической обработки.
При литье под давлением металлические формы (пресс-формы) и стержни делаются стальными. Применение песчаных стержней в данном случае исключается, так как заполняющий форму жидкий металл под высоким давлением может их разрушить.
Литье под давлением производится на машинах различных конструкций. Машины поршневого действия с горячей камерой сжатия применяются для сплавов, имеющих температуру плавления до 450° (оловянных, цинковых, свинцовых). Эти машины бывают ручные, полуавтоматического и автоматического действия.
Производительность полуавтоматических и ручных машин составляет примерно 250 заливок в час, автоматических – около 1000. Давление на металл в поршневых машинах с горячей камерой сжатия достигает 6-75 атм.
Машины поршневого действия с холодной камерой сжатия работают по принципу впрессовывания порции жидкого металла, предварительно залитого в поршневую камеру.
Давление на жидкий металл в машинах данного типа составляет 100-1000 атм. Производительность машины — до 300 отливок в час. Эти машины применяют чаще всего для литья из алюминиевых сплавов, но можно отливать на них детали и из других цветных сплавов.
^ Центробежное литье.
Центробежным литьем называется способ получения отливок, при котором жидкий металл заливается во вращающуюся форму. Формирование поверхности отливки и процесс кристаллизации металла протекает под действием центробежных сил.
Центробежным способом получают отливки из стали, чугуна и цветных сплавов. Наибольший технико-экономический эффект обеспечивается при использовании этого способа для получения отливок типа тел вращения (трубы, втулки, гильзы, цилиндры двигателей, кольца подшипников качения и др.).
Центробежный способ литья имеет следующие преимущества: не требуется применения стержней для получения внутренней полости цилиндрических отливок; резко снижается расход металла на литниковую систему; металл в отливке получается плотным, мелкокристаллического строения, что повышает его механические свойства; резко снижается себестоимость литья.
Машины для центробежного литья бывают с вертикальной и горизонтальной осью вращения. Иногда применяются также машины с наклонной осью вращения.
Машины с вертикальной осью вращения применяются только для изготовления относительно коротких цилиндрических отливок с небольшой разницей в толщине стенки по высоте (втулки, кольца и др.).
При вертикальной оси вращения свободная поверхность отливки получается параболической.
При горизонтальной оси вращения отливки получаются со стенками одинаковой толщины и практически любой длины.
При центробежном литье металл заливается в металлические формы (изложницы), внутренняя поверхность которых покрывается огнеупорной краской. Во избежание отбела на внутреннюю поверхность изложницы может быть нанесен слой облицовки из специальной формовочной или стержневой смеси.
Для теплоизоляционных покрытий внутренних поверхностей изложниц также применяются сухие песчаные смеси с термореактивным связующим или водные растворы (суспензии) на основе сульфитного щелока. Качество отливок при центробежном литье в значительной степени зависит от скорости вращения формы и температуры заливаемого металла. Так, слишком малое число оборотов изложницы может привести к тому, что незначительные центробежные силы не удержат расплавленный металл у поверхности формы, а излишнее число оборотов усложнит конструкцию машины, вызовет ее преждевременный выход из строя и может привести к образованию трещин в отливках.
При выборе необходимой температуры заливки руководствуются следующим. В процессе охлаждения вращающейся массы металла кристаллизующийся (незатвердевший) расплав непрерывно изменяет свой состав. Вначале выпадают зерна составляющих сплава, имеющих более высокую температуру плавления, затем кристаллизуются все более легкоплавкие составляющие и некоторые неметаллические примеси. Более тяжелые частицы затвердевшего сплава под действием центробежных сил отбрасываются дальше к наружным слоям отливки. В результате увеличения времени затвердевания неоднородность сплава по сечению отливки возрастает. Следовательно, сплав необходимо заливать при температуре, близкой к началу кристаллизации. Обычно температура заливки определяется опытным путем.
Чугунные трубы и другие изделия можно отливать центробежным способом в формы, футерованные формовочной или стержневой смесью. При этом металлическая форма служит неопределенно долгое время, так как она непосредственно не соприкасается с жидким металлом. Кроме того, футеровка обеспечивает более медленное охлаждение отливки, в результате чего поверхностный слой металла получается без отбела и таким образом отпадает необходимость в отжиге. Недостаток этого способа — наличие в цехе формовочной смеси и необходимость дополнительных очистных операций.
Центробежным способом можно получать также фасонные детали типа звездочек, зубчатых колес, турбинных дисков с лопатками, деталей арматуры и др. (рис. 3, в).
Центробежное литье широко применяется при отливке биметаллических изделий.
Для получения отливок центробежного литья созданы специальные литейные машины. В зависимости от цеховых условий металл к центробежным машинам подается мерными ковшами или через промежуточные ковши.
При работе на центробежных машинах, где одновременно с быстрым вращением изложницы заливается в нее расплавленный металл, следует особое внимание обращать на соблюдение требований техники безопасности.
^ Литье по выплавляемым моделям.
Литьем по выплавляемым моделям называется способ получения отливок в оболочковые формы, изготовляемые методом нанесения огнеупорного покрытия на легкоплавкие модели. Последние затем выплавляются, в результате чего в оболочковой форме образуются полости, соответствующие контурам будущей отливки.
Для получения высокой чистоты поверхности отливок оболочковые формы прокаливаются при температуре 900—950°. При этой же температуре форма заливается жидким металлом.
Для предотвращения деформаций и разрушения тонкой оболочковой формы последняя перед обжигом засыпается песком или другим наполнителем.
Литьем по выплавляемым моделям можно получать отливки любой сложности с различной толщиной стенок, почти или вовсе не требующие механической обработки, массой до 1,5 кг (сплавы любых черных и цветных сплавов, включая высоколегированные жаропрочные и сверхтвердые). Отливки получают с точностью размеров в среднем 4-5-го классов и шероховатостью поверхности 5-7-го классов.
Недостатком этого способа является высокая себестоимость отливок, поэтому его применяют только для изготовления таких деталей, которые невозможно получить другими методами литья (например, мелкие тонкостенные детали из труднообрабатываемых сплавов со сложной конфигурацией).
Материалом для изготовления легкоплавких моделей может служить смесь парафина и стеарина в соотношении 1:1
Легкоплавкие модели получают методом запрессовки модельного состава при температуре 42 — 43° в металлические водоохлаждаемые пресс-формы.
Процесс изготовления моделей включает подготовку пресс-форм, запрессовку в ее полость модельного состава, выдержку до затвердевания, извлечение модели и ее охлаждение в проточной воде с последующей зачисткой.
Такие «восковые» модели собираются на общем стояке, образуя своеобразную «елку». Чтобы упростить сборку, модели изготавливают в многогнездовых пресс-формах звеньями (или целой «елкой»).
Огнеупорное покрытие наносится методом окунания «елки» в ванну с обмазкой, после чего мокрая «елка» обсыпается сухим кварцевым песком. Покрытие состоит из трех-четырех слоев. После нанесения каждого слоя «елка» сушится в течение двух часов.
Модельный состав выплавляют при температуре 80— 85° С горячим воздухом, горячей водой или паром в специальных камерах. После выплавления модельного состава «елки» помещают в специальные опоки, засыпают песком и направляют на обжиг в печах при температуре 900—950° (рис. 5, в).
Заливка оболочковых форм производится из обычных литейных ковшей сразу после обжига «елок».
Выбивка форм заключается в высыпании из опок песка вместе с «елкой», для чего используются поворотные выбивные устройства.
^ Литье в оболочковые формы.
Литье в оболочковые формы применяется для изготовления сложных тонко-стенных отливок из черных и цветных сплавов.
Эти формы представляют собой сухие тонкостенные оболочки толщиной 8-15 мм, изготавливаемые из термореактивных смесей, которые затвердевают от тепла нагретых металлических моделей и стержневых ящиков.
Иногда этот метод применяют для изготовления оболочковых стержней.
Термореактивная смесь состоит из чистого кварцевого песка и крепителя. Крепителями служат различные термореактивные смолы. Термореактивные смолы при нагревании претерпевают ряд необратимых изменений. При комнатной температуре они представляют собой твердый порошок, при нагревании до 70—100° он расплавляется, при дальнейшем нагревании до 120—150° затвердевает, а при 160—180° переходит в необратимую твердую фазу. Эта особенность термореактивных смол используется для получения оболочковых форм.
Технологический процесс изготовления оболочковых форм состоит из нескольких основных операций. Рассмотрим более подробно каждую из этих операций.
Приготовление смеси. Смесь для оболочковых форм готовится путем перемешивания песка и порошка бакелитовой смолы.
Подготовка модельной плиты. Модельные плиты выполняются чугунными. Подготовка заключается в нагреве модельной плиты до температуры 200—240° и нанесении разделительного слоя, который необходим для предотвращения прилипания формовочной (термореактивной) смеси к моделям. Наилучшими разделительными смазками являются силиконовые эмульсии.
Применяются два основных способа получения оболочки — способ свободной засыпки и пескодувный. Примеры изготовления оболочки свободной засыпкой представлены на рис.7.
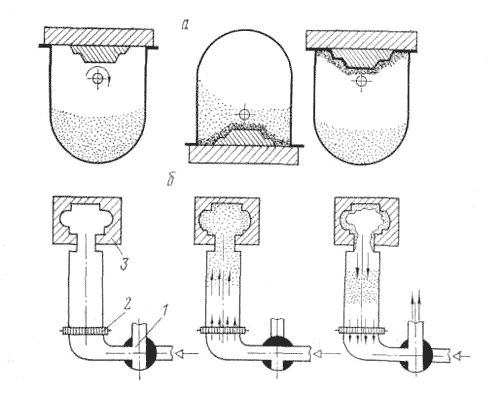
Рис. 1. Получение оболочки: 1 — трехходовой кран; 2 — решетка; 3 — стержневой ящик
На рис. 1, а представлен пример получения оболочковой корки на машине, которая имеет резервуар с термореактивной смесью, который может поворачиваться на 180°. На резервуар сверху кладется и закрепляется разогретая модельная плита, после чего резервуар поворачивается на 180° и вся смесь падает на горячую модельную плиту. Нагреваясь от плиты, термореактивная смола начинает размягчаться, и на модельной плите начинает образовываться довольно прочная корка. Так как расплавление смолы происходит по мере ее нагревания от горячей модельной плиты, то, естественно, что первыми плавятся частицы смолы, ближе всего расположенные к поверхности плиты. Таким образом, постепенно увеличивается толщина образующейся корки. При этом прогретый слой смеси обладает высокой подвижностью и под давлением вышележащего слоя дает четкий отпечаток всех контуров модели. После этого модельная плита с коркой снимается с резервуара и помещается в обжигательную печь, где в течение 1,5—2 мин. прокаливается при температуре 300—400° для окончательного упрочнения.
При получении корки пескодувным способом (рис. 7, б) смесь подается на модель или в стержневой ящик под давлением воздуха. При заливке мелких форм обычно не требуется специальных мер. Средние формы (металлоемкость свыше 10 кг) для заливки устанавливают в специальные опоки и промежутки заполняют опорным материалом. Выбивка отливок при этом способе сводится к удалению из опоки дроби и передаче отливки на операцию очистки поверхности. В механизированном производстве применяется дробеструйная очистка.
Литье в оболочковые формы имеет следующие преимущества перед литьем в песчано-глинистые формы:
- увеличивается выход годного литья за счет снижения брака и сокращения размеров литниковой системы;
- сокращается механическая обработка вследствие высокой точности геометрических размеров отливки;
- полностью ликвидируется очистка литья;
- повышается съем годного литья с 1 м2 формовочной площади;
Во всех случаях нужно учитывать уменьшение расхода металла, трудоемкость формовки, очистки и механической обработки, а также снижение потерь от брака с теми дополнительными затратами, которые вызываются установкой нового оборудования и применением более дорогих компонентов смеси.
^ Литье по газифицируемым моделям.
Применяемые при этом способе модели изготавливаются из пенополистирола различных марок, выпускаемого в виде гранул или плит. Такие пенополистироловые модели и элементы литниковой системы остаются в собранной литейной форме. При соприкосновении с расплавленным металлом литниковая система, а затем и модель превращаются в газ, а их место занимает металл.
Для изготовления пеноцолистироловой модели из гранул они засыпаются в пресс-форму, в которой нагреваются в автоклаве в течение 10-12 мин. Гранулы пенополистирола при этом вспениваются, заполняют всю полость и образуют сплошную модель, соответствующую внутренней полости пресс-формы (рис. 2, а). После охлаждения в проточной воде модель извлекают и передают на формовку. К таким газифицируемым моделям можно присоединить литниковую систему (также из пенополистирола) путем приклеивания ее клеем (рис. 2, б).
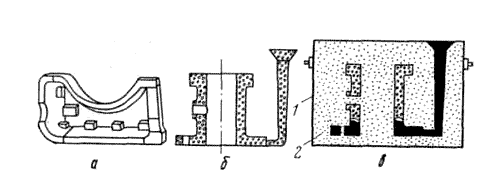
Рис. 2. Литье по газифицируемым моделям.
Склеиванием получают модели сложной конфигурации.
Модели из листов или блоков пенополистирола можно вырезать при помощи нихромовой проволоки, нагретой до 300° С. Характерной особенностью этого способа является возможность получения отливок по моделям без формовочных уклонов, с уменьшенными припусками на механическую обработку и без стержневых знаков, так как отверстия и выступающие части образуются самой моделью. При этом значительно упрощается процесс формовки. Он состоит в том, что модель с литниковой системой устанавливается в опоку / на предварительно насыпанный слой формовочной смеси и засыпается до уровня литниковой чаши формовочной смесью 2 (рис. 10, в). Уплотнение может производиться вручную или на вибрационном столе.
Разработан способ формования пенополистироловых моделей путем засыпки опоки металлической дробью с последующим наложением электромагнитного поля. Перспективным является также способ формовки пенополистироловых моделей с применением жидких самотвердеющих смесей. Все эти способы литья свидетельствуют о том, что газифицируемые модели не только уменьшают трудоемкость изготовления модельной оснастки, но и дают возможность изготавливать неразъемные формы.
Пенополистироловые модели рекомендуется применять при изготовлении крупных чугунных или стальных отливок в литейных цехах индивидуального или мелкосерийного производства. Положение модели в форме при этом способе выбирается таким, чтобы обеспечить наиболее полное удаление продуктов разложения пенополистирола из полости формы при заливке в нее расплавленного металла.
Для одновременного и плавного заполнения формы металлом следует применять сифонную литниковую систему. Поперечное сечение элементов литниковой системы рассчитывается исходя из необходимости обеспечения подъема металла в форме со скоростью 3—5 см/с для чугунного литья и 5-7 см/с — для стального.
Производство отливок по пенополистироловым моделям кроме повышения точности отливок позволяет получить экономический эффект до 80 руб. на 1 т годного литья.

^ Контроль качества отливок.
Основными способами оценки качества отливок являются: разметка, внешний осмотр, травление, керосиновая проба, гидравлическое испытание. Применяются также ультразвуковая, магнитная, рентгено- и гамма-дефектоскопия. Для определения механических свойств материала отливок могут отливаться пробные образцы.
Эти неразрушающие методы контроля в последнее время получили широкое применение как в массовом, так и в серийном производстве.
^ Магнитная дефектоскопия. В машиностроении широко применяются магнитные методы контроля для выявления волосовин, мельчайших трещин, шлаковых включений и других дефектов, расположенных на незначительной глубине или частично выходящих на поверхность.
Магнитная дефектоскопия позволяет производить сплошную проверку качества ответственных отливок вместо выборочной проверки, связанной с разрезкой или порчей деталей. Этот способ основан на том, что в намагниченном изделии магнитный поток способен частично рассеиваться при встрече препятствий типа трещин, неметаллических включений и др.
Для выявления дефектов, расположенных вблизи поверхности отливки, ее зачищают, а проверяемую деталь намагничивают. В месте нахождения дефекта магнитный поток рассеивается и выходит на поверхность. Намагниченную поверхность детали поливают суспензией в виде жидкости, в которой во взвешенном состоянии находится магнитный порошок. В качестве жидкости чаще всего применяется минеральное масло, керосин или мыльный раствор. Оседающий на поверхности отливки порошок втягивается в область неоднородности вышедшего на поверхность магнитного потока (на месте дефекта отливки) и располагается в виде характерных полос или замкнутых линий. Поверхность отливки предварительно очищается дробью или металлическим песком, чтобы по ней могла свободно стекать эмульсия. Для выявления дефектов на деталях с темной поверхностью могут применяться окрашенные порошки. После испытания отливку необходимо размагнитить. Для намагничивания и размагничивания деталей и для проведения магнитного контроля наша промышленность выпускает различные типы стационарных и переносных магнитных дефектоскопов.
^ Метод ультразвукового контроля. Он позволяет обнаружить глубинные дефекты по специально подготовленной поверхности отливки. Для контроля необработанных поверхностей отливок могут применяться специальные эластичные наконечники, наполненные водой или маслом, однако точность контроля при этом снижается.
^ Контроль импульсным ультразвуковым дефектоскопом. Этот метод основан на том, что ультразвуковые волны обладают способностью распространяться направленными пучками и могут проникать внутрь металла. Это свойство ультразвуковых волн используется для контроля однородности металла с помощью ультразвуковых дефектоскопов различных типов.
При однородности детали луч всегда улавливается приемником ультразвуковых колебаний. Но если на пути звукового луча в металле встретятся раковина , трещина или другие дефекты, нарушающие однородность исследуемого тела, то произойдет отражение звукового луча, он не попадет в приемник, и получается «звуковая тень».
При одновременном перемещении излучателя и приемника по обеим поверхностям отливки при помощи такого способа можно установить размеры и форму дефекта.
Произведя подобное исследование в другой плоскости, можно определить глубину залегания трещины или раковины.
Однако наибольшее распространение получили дефектоскопы другого типа — импульсные ультразвуковые эходефектоскопы. Принцип их действия основан на том, что от излучателя в испытуемую отливку направляется узкий пучок ультразвуковых лучей в течение очень короткого промежутка времени (миллионные доли секунды). Такие звуковые импульсы посылаются с интервалами в несколько долей секунды. Рядом с излучателем (или в одном корпусе с ним) перемещается по поверхности детали приемный искатель, улавливающий отраженный (как эхо) ультразвук от противоположной поверхности или от дефектных мест внутри изделия .По соответствующему перемещению светового пятна на экране прибора определяют глубину залегания дефекта.
^ Импульсная ультразвуковая эходефектоскопия. Она позволяет обнаруживать размеры и положение раковин, трещин, расслоений и других дефектов, расположенных на глубине до нескольких десятков сантиметров, и применяется для контроля отливок несложной формы.
^ Рентгеновская дефектоскопия. Внутренние пороки в отливках могут быть выявлены также при просвечивании рентгеновскими лучами, способными проникать сквозь непрозрачные тела. Рентгеновские лучи получаются в специальных устройствах (рентгеновских трубках), в которых поток отрицательно заряженных частиц (катодных лучей), ударяясь о металлический антикатод, вызывает излучение .Проходя сквозь участок отливки, отличающийся различной плотностью (из-за раковин, пористости и т. д.), рентгеновские лучи в той или иной степени ослабляются.
Если на выходе рентгеновских лучей поместить кассету с рентгенофотопленкой, то на ней получится теневая проекция изделия, на которой полости и трещины будут видны в виде пятен.
Современные промышленные рентгеновские установки просвечива-ют стальные отливки с толщиной стенок до 100 мм, отливки из меди и ее сплавов – до 60 мм и литые детали из алюминия и его сплавов – до 300-400 мм. При этом глубина просвечивания зависит от мощности установки.
Значительно большей проникающей способностью обладают гамма-лучи, излучаемые некоторыми радиоактивными веществами. Просвечивать гамма-лучами можно стальные изделия с толщиной стенок до 500 мм .
.