Развитие теории и комплексные методы повышения эффективности функционирования электрооборудования горных предприятий
Вид материала | Автореферат диссертации |
СодержаниеРациональная организационно-технологическая система технического обслуживания горных предприятий. |
- Правила безопасности при эксплуатации электрооборудования и электросетей на открытых, 974.06kb.
- Развитие организационной культуры в контексте повышения эффективности функционирования, 297.46kb.
- Управление процессами повышения эффективности государственных инвестиций в развитие, 383.31kb.
- Методы и средства повышения качества функционирования ветроэнергетических установок, 245.79kb.
- Методические указания к выполнению контрольной работы, 513.12kb.
- Итоги работ по диагностике электрооборудования схемы выдачи мощности аэс, рекомендации, 7.77kb.
- Ебования к эффективности функционирования предприятий, поскольку только эффективное, 75.24kb.
- Руководящий технический материал ртм москва 2011 г. Аннотация, 1623.28kb.
- Кузнецова Екатерина Викторовна, 217.07kb.
- Рабочая программа учебной дисциплины "методы анализа режимов электрооборудования электростанций, 153.87kb.
Рациональная организационно-технологическая система технического обслуживания горных предприятий.
Увеличение эффективности, надежности и ресурса, а также обеспечение безопасной эксплуатации машин и механизмов тесно связано с необходимостью оценки их технического состояния. Это и определило формирование нового научного направления - технической диагностики, которое получило особо широкое развитие в последнее десятилетие. Возникает необходимость перехода на более прогрессивную систему ТО, которая уже внедряется на предприятиях ряда отраслей промышленности – ОФС. Надежность большинства механического и электромеханического оборудования напрямую определяется вращающимися узлами и деталями, испытывающими высокие динамические нагрузки и подверженными наибольшему износу. Именно с этим связано особое внимание специалистов к вопросам функциональной диагностики подобных узлов (вибродиагностики), а также спектрального анализа токовых нагрузок. Переход на прогрессивные технологии технического обслуживания связан с решением целого комплекса проблем – технических, организационных, социальных, создания автоматизированных систем управления техническим обслуживанием.
В число комплекса вопросов по повышению уровня безопасности и эффективности эксплуатации горного оборудования входят как технические, так и организационные мероприятия. Причем организационные мероприятия по существу являются технологическими аспектами и, как правило, дают наибольший экономический эффект. В то же время внедрение новых технологий возможно только на базе современных методов и технических средств неразрушающего контроля технического состояния оборудования.
В настоящее время сложилась ситуация, когда наряду с появлением высокоточных технических средств измерения и обработки режимных параметров узлов и механизмов, имеем чрезвычайно важную проблему обеспечения надежности и безопасности практически уже изношенного горного оборудования. По ГОСТ 18353-79 имеются девять видов, включающих более 50 методов неразрушающего контроля. В то же время основные фонды в горнодобывающих отраслях России уже амортизированы на 90%.
Нами проводились исследования аварийности экскаваторного парка (всего 53 экскаватора) Лучегорского угольного разреза. Для анализа технического состояния экскаваторного парка Лучегорского угольного разреза были использованы статистические материалы – ежесуточные отчеты начальников смен, в которых фиксировались причины и время простоев горного оборудования. Были проанализированы отчеты за 758 суток. Для каждого экскаватора построены диаграммы аварийности (модели технического состояния) основных узлов и механизмов в виде
МА = а Кан + b СД + с ГП + d ЦУ + е Каб + f Ко + g Пно + h ВВ + k МО +
+ l РК + m Кон + n С + f И,
где латинские буквы перед сокращениями узлов и механизмов – доля отказов узла или механизма в общем потоке аварий на экскаваторе. Например, для одного из экскаваторов (ЭШ-11/70 №10) эта модель выглядит следующим образом: МА = 18Кан + 25СД +1ГП +17ЦУ + 8Ко +10Пно +3ВВ +1МО +17С. Следует отметить, что ни одна из 53 моделей не повторяет другую, т.е. каждый экскаватор «болеет» по-своему и требует особого отношения. Получены обобщенные диаграммы экскаваторов шагающих, карьерных и роторных. Обобщенные данные аварийности экскаваторов шагающих и карьерных представлены в табл.4. Как видно из таблицы, на долю электрических машин и их систем управления приходится до 44% времени аварийных простоев у шагающих и до 54% у карьерных экскаваторов.
Наиболее распространенными причинами, вызывающими отказы вращающегося оборудования, являются дисбаланс – 34%, расцентровка валопроводов – 35%, дефекты подшипниковых узлов – 14%, дефекты зубчатых передач – 9%, электромагнитные дефекты – 8%. Безусловно, особого внимания заслуживают проблемы дисбаланса и расцентровки валопроводов, которые могут быть решены применением лазерных центровщиков и организацией балансировки в собственных опорах приборами, и решены эти проблемы могут быть полностью самим предприятием. Что же касается подшипниковых узлов, то здесь проблема сложнее – зависит и от качества поставляемого оборудования и от качества его эксплуатации.
Таблица 4
Обобщенные доли аварийности узлов и механизмов экскаваторов Лучегорского угольного разреза
Оборудование | Аварийность, % | |
Шагающие экскаваторы | Карьерные экскаваторы | |
Канаты | 22 | 13 |
Синхронный двигатель | 12 | 5 |
Главные привода | 11 | 35 |
Цепи управления | 11 | 14 |
Кабель | 4 | 3 |
Ковш | 16 | 4 |
Компрессорное оборудование | 3 | 1 |
Высоковольтное оборудование | 2 | 2 |
Механическое оборудование | 9 | 22 |
Стрела | 9 | - |
Прочее | 1 | 1 |
Техническая база ОФС основана на взаимосвязи между эксплуатационными параметрами и дефектами: различные дефекты имеют строго определенные диагностические признаки, появляющиеся при их возникновении, и диагностические параметры, меняющиеся по мере их развития. В качестве диагностических признаков используются технологические и режимные параметры (температура, электрическая нагрузка, давление, влажность и т.п.), а также параметры вибрации (вибрационная скорость, вибрационное ускорение, вибрационное перемещение).
За последние несколько десятилетий вибрационная диагностика стала основой контроля и прогноза состояния вращающегося оборудования. Физической причиной ее быстрого развития является огромный объем диагностической информации, содержащийся в колебательных силах и вибрации машин, работающих как в номинальных, так и в специальных режимах. Техническим обеспечением вибрационной диагностики являются высокоточные средства измерения вибрации и цифровой обработки сигналов, возможности которых непрерывно растут, а стоимость снижается.
В диссертации проведен анализ существующих видов ТО, определены характерные особенности современных технологий контроля и диагностики оборудования и, в частности, вибродиагностики. Дана классификация методов и обобщены технические средства неразрушающего контроля, применяемые в горной промышленности.
Особенностью любой технической системы как объекта диагностирования является тесная взаимосвязь электрических, электромеханических и механических устройств и элементов, отличающихся функциональным назначением и принципом действия.
Диагностический параметр (ДП) – параметр (признак) объекта диагностирования, используемый в установленном порядке для определения технического состояния объекта. Для каждого типа технической системы можно указать множество параметров, характеризующих техническое состояние системы. Большинство ДП по своему назначению могут иметь двойственную природу, являясь одновременно диагностическими и техническими (или параметрами функционального использования). Именно эти параметры чаще всего поддаются непосредственному измерению. В случае если значения диагностических параметров не поддаются непосредственному измерению, то эти значения могут быть найдены путем обработки других параметров, связанных с искомыми функциональными зависимостями.
Всю совокупность параметров технического состояния можно разделить на различные классы, в рамках которых объединяются параметры, связанные общностью физических процессов: электрические, механические, акустические, оптические, химические и др. Выбор совокупности ДП для реализации диагностирования представляет многоальтернативную задачу, определяется многими факторами, основными из которых являются: целевая функция объекта диагностирования; стратегия его технического обслуживания; задаваемый набор средств технического диагностирования; время диагностирования; стоимость средств диагностирования и самого процесса.
Технологии виброакустичекой диагностики позволяют с высокой степенью достоверности придавать определенному функциональному параметру или отклонению от него (дефекту) характерные диагностические признаки. В частности, совокупностью виброакустических признаков, определяющих техническое состояние элементов вращающегося электрооборудования - подшипников, являются характерные частоты и их амплитуды: fВР - частота вращения вала, fв - частота перекатывания тел качения по внутреннему кольцу, fн — частота перекатывания тел качения по наружному кольцу, fтк - частота вращения тел качения, fс - частота вращения сепаратора. Наличие этих гармоник и различных модулированных субгармоник в спектре виброакустического сигнала позволяет определять 13 видов дефектов подшипников: бой вала, неоднородный радиальный натяг, перекос наружного кольца, износ наружного кольца, раковины (трещины) на наружном кольце, износ внутреннего кольца, износ тел качения и сепаратора, раковины и сколы на телах качения, неуравновешенность ротора, дефекты узлов крепления, дефекты смазки, дефект муфты. Амплитуды этих гармоник позволяют судить о степени развития дефекта.
Диагностические признаки асинхронных двигателей: fВР – частота вращения ротора, fu – частота напряжения питания, fz – зубцовая частота, s – скольжение ротора - позволяют определять практически все дефекты, за исключением сопротивления изоляции – неуравновешенность ротора, бой вала, дефекты узлов крепления, статический эксцентриситет зазора, динамический эксцентриситет зазора, дефекты обмоток статора, дефекты обмоток ротора, несимметрию напряжения питания, нелинейные искажения напряжения питания.
Диагностические признаки машин постоянного тока: fВР – частота вращения якоря, fК – коллекторная частота, fп –частота пульсаций напряжения питания позволяют определять неуравновешенность якоря, бой вала (муфты), дефекты узлов крепления, дефекты обмоток якоря, дефекты системы возбуждения, дефекты щеточно-коллекторного узла, пульсации напряжения питания.
Кроме виброакустического сигнала для анализа технического состояния может быть использован спектр потребляемого тока приводного двигателя, при этом можно диагностировать связанные с двигателем и шестерни редуктора.
Таким образом, организация практических мероприятий по диагностированию технического состояния конкретных машин и механизмов требует построения соответствующей системы диагностирования. Создание системы диагностирования сопряжено с постановкой и решением целого комплекса задач. К их числу относятся задачи, связанные с исследованием кинематических и динамических свойств объекта диагностирования, определением всего множества дефектов, неисправностей, поломок, отказов и, соответственно, формированием алфавита классов диагностируемых технических состояний, поиском информативных диагностических признаков, на языке которых могут быть описаны эти классы (словарь диагностических признаков), разработкой алгоритмов и решающих правил диагностирования, разработкой требований к перечню и техническим характеристикам измерительной, анализирующей, регистрирующей, вычислительной, документирующей и т.п. аппаратуры, разработкой соответствующего математического и технического обеспечения и ряд других.
На рис.10 представлена классическая кривая надежности оборудования, которая характеризуется тремя характерными участками: зонами послепусковых отказов, случайных отказов и износа. Выравнивание данной седлообразной зависимости и, соответственно, увеличение межремонтного интервала может достигаться двумя путями: переход на обслуживание оборудования по фактическому состоянию (по сравнению с ППР и реактивным ТО) и совершенствованием системы ремонта оборудования – проактивным (ПАО).
Не вызывает сомнений, что для увеличения межремонтного интервала наиболее эффективны капитальные вложения именно в совершенствование системы ремонта оборудования (ПАО). Если мониторинг состояния оборудования и ОФС приводят к экономии затрат службы ремонта только по мере совершенствования системы ТО предприятия, то совершенствование технологии ремонта непосредственно с момента внедрения положительно влияет на межремонтный интервал оборудования. В первую очередь, как часть стратегии ПАО на начальном периоде реализации подпрограмма нацелена на входной и выходной контроль, оценку ТС оборудования после ремонта, обеспечение минимальных дисбалансов и несоосности роторов агрегата при выводе из ремонта,
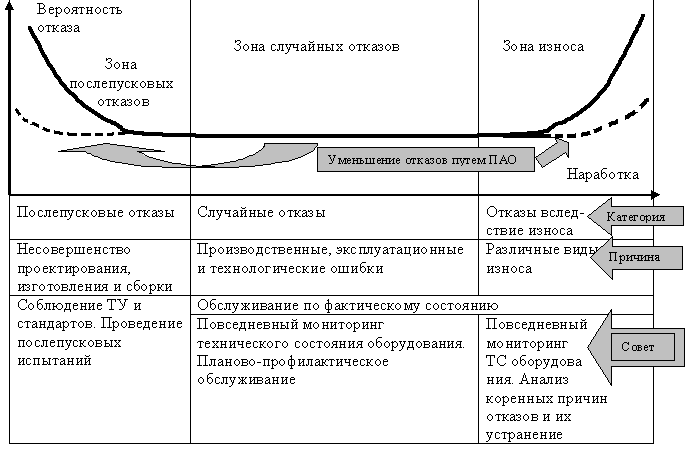
Рис.10.Схема реализации программы обеспечения
надежности функционирования оборудования
монтажа бездефектных подшипников, полумуфт и других насадных деталей в соответствии с ТУ, обеспечение расчетной жесткости опорной системы при монтаже и обеспечение систем смазки трущихся деталей. Для реализации этого необходимо превентивное внедрение в следующие технологии:
- входной контроль подшипников качения; вероятный результат - увеличение межремонтного интервала не менее чем на 5%;
- индукционный нагрев насадных деталей при монтаже; вероятный результат – увеличение межремонтного интервала не менее чем на 10%;
- применение динамометрических монтажных ключей; вероятный результат – увеличение среднего межремонтного интервала не менее чем на 7%;
- балансировка роторов в собственных опорах; вероятный результат - увеличение среднего межремонтного интервала не менее чем на 10%;
- центровка с применением лазерных датчиков; вероятный результат – возрастание среднего срока службы подшипников и муфт в три раза, возрастание межремонтного интервала на 10 – 100%;
- оценка технического состояния оборудования после ремонта; вероятный результат – только при уровнях вибрации, соответствующих оценки «отлично» - не менее чем на 15%;
- обеспечение качества смазки трущихся пар; вероятный результат – 40% подшипников выходят из строя вследствие отклонения количества смазки от номинальной величины и ухудшения качества.
Мониторинг технического состояния в сочетании с ОФС предназначен для предотвращения внезапных отказов, а ПАО – для подавления причин их возникновения. Однако реализация ПАО, даже при наличии технических средств для проведения вибромониторинга, невозможна, если только выполнять требования ГОСТов. Практически все системы мониторинга и диагностики дают информацию об общем уровне вибрации. При измерении общего уровня колебаний максимальный вклад могут давать несколько основных составляющих, например, составляющая на частоте вращения. Эта составляющая имеет, безусловно, большое значение, однако развивающиеся дефекты могут привести к росту других составляющих, уровень которых может быть значительно ниже уровня доминирующей составляющей. Таким образом, измерение общего уровня является слишком грубой оценкой, с точки зрения определения технического состояния машины или оборудования, и может быть использовано скорее для его контроля, чем для мониторинга, не говоря уже о глубокой детальной диагностике, требующей более тонких методов. Общий уровень используется для сравнения с установленными стандартами пороговыми значениями и для построения трендов, т.е. зависимостей общего уровня от времени, что дает возможность оценить, в первом приближении, скорость изменения состояния машины или оборудования. Кроме того, нормируемые по ГОСТ параметры вибрации по общему уровню носят рекомендательный характер, поскольку даже в группе однотипных машин пороговые уровни вибрации могут сильно меняться в зависимости от условий эксплуатации.
Во многих случаях изменение технического состояния элементов машин и оборудования, особенно на начальной стадии развития дефектов, не влияет на общий уровень вибрации. Так, в частности, для подшипников, появление небольших дефектов на телах качения, а также на наружной и внутренней обоймах практически не изменяет общего уровня вибрации. В то же время наличие зарождающихся дефектов является ценной информацией для обслуживающего персонала и одним из необходимых условий реализации проактивной системы обслуживания. На угольных предприятиях Дальневосточного региона присутствуют элементы мониторинга технического состояния по общему уровню вибрации либо как составляющая системы освидетельствования для продления срока службы экскаваторов. Только на Лучегорском угольном разрезе нами был реализован и получает развитие с 2007 года вибромониторинг по параметрам дефектов подшипниковых узлов преобразовательных агрегатов карьерных экскаваторов. В течение девяти месяцев 2007 года были охвачены мониторингом 38 карьерных и шагающих экскаваторов из 53 и, соответственно, более 300 подшипников преобразовательных агрегатов. По результатам испытаний бездефектных подшипников в выборке оказалось всего 20%, основная масса подшипников имеет слабые 42% и средние дефекты – 31%, нуждающихся в срочной замене – 7%.
По видам дефектов наибольшее распространение (48%) имеют дефекты наружного кольца – обкатывание, износ и раковины, далее - тела качения и сепаратор – самые слабые звенья подшипника (40%). Многие дефекты по мере развития порождают несколько других, при этом коэффициент модуляции «родительского» дефекта, как правило, снижается. Диагностика подшипников синхронного двигателя экскаватора ЭШ-11/70 №8 выявила на одном из них (3636) 22 марта дефект: «износ наружного кольца» (коэффициент модуляции m=8 – средний). Затем 28 мая этот дефект стал уже сильным (m =16), кроме того, появился дефект «обкатывание наружного кольца» (m=10 – средний) и «износ тел качения и сепаратора» (m=8 – средний). Измерения 15.06 показали снижение степени развития дефекта «износ наружного кольца» до m=7, но зато появились «раковины на наружном кольце» (m=16 - сильный). На генераторе поворота этого же экскаватора у подшипника 32330 первоначально выявлены дефекты «раковины и сколы на телах качения» (m=13) и «износ тел качения и сепаратора» (m=8). Эти дефекты сначала развились до величин коэффициентов модуляции 24 и 12, а затем наблюдается их снижение до 23 и 9, соответственно, что свидетельствует об изменении геометрии элементов подшипника. Данные обстоятельства значительно затрудняют определение остаточного ресурса подшипника. До настоящего времени не существует прогнозных моделей остаточного ресурса подшипниковых узлов горного оборудования. Вибродиагностика в угольной промышленности Дальнего Востока только начинает развиваться. Также получает развитие ПАО. Нами на Лучегорском угольном разрезе внедрена технология безразборного восстановления работоспособности подшипниковых узлов электрических машин с помощью наноматериалов - ультрадисперсного состава ССРС, инициирующего самоорганизующиеся процессы в местах трения, устраняющего дефекты и повышающего ресурс работы.
Требуемый при проведении работ по мониторингу современный комплекс средств измерений и диагностики (измерительная система) состоит из следующих частей: аппаратные средства измерений, вспомогательные устройства и каналы связи, программное обеспечение и ЭВМ. Для постоянного мониторинга используются стационарные системы, а для периодического - переносные приборы.
Стационарная аппаратура контроля состояния и мониторинга оборудования применяется для непрерывного контроля вибрации, температуры, давления и других технологических параметров (текущие контрольные измерения и отключение или сигнализация при превышении параметром допустимого значения), мониторинга и диагностики (полные контрольные измерения, анализ тенденций изменения параметра, оценка запаса работоспособности, прогнозирование остаточного ресурса и определение развивающихся и развитых дефектов). Такая аппаратура включает в себя первичный вибропреобразователь (датчик), крепящийся на объекте контроля (агрегате), предварительный согласующий усилитель, соединительный кабель, вторичный блок контроля вибрации, устройство ввода данных в локальный сервер и программное обеспечение. Вторичный блок контроля вибрации служит для проведения текущих контрольных измерений, т.е. измерения значения вибрации, индицирования текущего состояния оборудования, управления внешними устройствами (реле отключения или звуковая и световая сигнализация) при превышении текущим уровнем вибрации допустимых значений.
Переносная аппаратура применяется для периодического контроля и мониторинга параметров вибрации и делится на два класса: виброметры и сборщики данных. Виброметры предназначены для текущих контрольных измерений, т.е. измерения виброускорения, виброскорости или виброперемещения. Сборщики данных предназначены для полных контрольных измерений и позволяют производить анализ сигнала вибрации во временной и частотной областях.
Все диагностические системы объединяются в единую систему мониторинга. Это подразумевает возможность использования диагностической информации, полученной любым из подразделений другими, заинтересованными в ее использовании. Основой компьютеризированного мониторинга является программное обеспечение, устанавливаемое на сервере.
По завершении инсталляции измерительной системы, первый шаг при пуске системы мониторинга оборудования состоит в создании компьютерной базы данных по обслуживаемому оборудованию, содержащей детальное описание всего обслуживаемого оборудования, измерительных точек, параметров для каждой измерительной точки и предварительные предельно допустимые уровни измеряемых параметров (в дальнейшем записи базы данных могут быть расширены, удалены или модифицированы). Затем создаются маршруты опроса точек измерений (для стационарной системы) и обходов оборудования, по которым будут следовать техники и производить сбор данных по каждой измерительной точке маршрута (для сборщиков данных). Маршрут определяет последовательность сбора данных (какой агрегат, какой его компонент, какая точка и в какой последовательности должны быть обследованы).
Предлагаемая к реализации иерархическая система сбора и обработки данных предполагает три уровня. На первом уровне силами сменного персонала установок проводятся текущие контрольные измерения с помощью виброметров и контрольно-сигнальной аппаратуры в соответствии с Регламентом измерений. Результаты измерений фиксируются в вахтовом журнале и/или вводятся в территориальный сервер установки.
На втором уровне проводятся полные контрольные измерения с помощью сборщиков данных (результаты измерений вводятся в сервер системы мониторинга) или стационарных систем контроля и мониторинга (результаты измерений вводятся в терминальный сервер). Контроль производится силами службы ТД. При этом должна быть обеспечена задача обнаружения изменения состояния оборудования, распознавания развивающихся и развитых дефектов, оценки остаточного ресурса оборудования, примерной оценки объемов и сроков требуемого ремонта и планирования специальных диагностических обследований.
На третьем уровне проводятся контроль и общее управление сбором данных и работой службы ТД группой планирования ремонта (руководством служб технического надзора и отделом главного механика).
Информационная система службы ремонта (группы планирования ремонта ОГМ) реализуется как отдельная подсистема управления технико-экономического планирования ремонтно-эксплуатационных мероприятий.
Система мониторинга ТС оборудования должна быть частью интегрированной автоматизированной системы управления производственной деятельностью предприятия. Она должна обеспечивать автоматизированный распределенный сбор в режимах оn-linе и off-linе и хранение диагностической информации, материальных, стоимостных, документальных потоков, действий технического персонала и состояния оборудования, предоставлять аналитическую информацию и отчеты на основе хранимых данных для оптимизации управления службы ремонта, решения задач прогнозирования и перспективного планирования производства, решения задач хозяйственного учета и оперативного управления производством.
Заключение
Диссертационная работа является законченным квалификационным трудом, в котором автором в результате проведенных исследований дано развитие теории и комплексных методов повышения эффективности функционирования электрооборудования горных предприятий, что имеет важное хозяйственное значение. Основные научные и практические результаты, выводы и рекомендации выполненной работы заключаются в следующем:
1. Разработана методика нормирования расхода электроэнергии на экскаваторные работы, базирующаяся на результатах экспериментальных исследований, а также на выявлении и количественной оценке взаимосвязей между электропотреблением и технологическими параметрами с применением методов теории вероятностей и математической статистики. Установлены однофакторные и двухфакторные энергетические характеристики экскаваторов мехлопат и драглайнов как корреляционные зависимости между электропотреблением и определяющими его технологическими факторами.
2. Разработана методика определения соответствия измеряемых режимных параметров их фактическим значениям на основе созданной схемы включения многопараметрической системы измерения и регистрации и полученных графиков изменения активной мощности в различных режимах работы.
3. Разработана методика проведения и обработки результатов многопараметрических экспериментальных исследований на основе созданной системы регистрации режимных параметров электрооборудования угольных разрезов. Экспериментально определены параметры электропотребления в различных режимах работы карьерных одноковшовых экскаваторов. Показано, что фактические нагрузки значительно отличаются (в некоторых случаях в два раза) от номинальных, всегда в сторону уменьшения.
4. Теоретически обоснованы параметры режимов возбуждения синхронных двигателей преобразовательных агрегатов в соответствии с их фактическими нагрузками и необходимой генерируемой реактивной мощностью, требующейся для индуктивной нагрузки фидерной линии. Для карьерных экскаваторов разработана методика построения U-образных и рабочих характеристик, позволяющих определять рациональные режимы генерации и перераспределения реактивной мощности в фидерных линиях.
5. Проведен тепловой расчет, рассеивающей и нагрузочной способности, получены аналитические зависимости для выбора параметров высоковольтных экскаваторных гибких кабелей, позволяющие значительно увеличить эффективность их использования в соответствии с фактическими сроком службы, токовыми нагрузками, сезонными температурами окружающей среды и технико-экономическими показателями предприятия. Практически для всех карьерных экскаваторов имеется возможность уменьшать сечения навешиваемых кабелей для летнего сезона как минимум на одну, а для зимнего – на две ступени.
6. Проведен анализ влияния режимных параметров сети на нагрузочные потери электроэнергии. Показано, что активные нагрузочные потери составляют наибольшую часть общих потерь электроэнергии и учитывают потери вследствие изменения режимных параметров сети.
7. Разработан способ определения относительных и регистрации абсолютных потерь электроэнергии по значению активной мощности, канализируемой головным участком, и эквивалентного коэффициента потерь, определяемого топологией сети. Разработана методика определения эквивалентного значения коэффициента потерь сети. Способ определения относительных потерь позволяет судить об эффективности функционирования системы электроснабжения горного предприятия.
8. Проведены теоретические исследования режимов чувствительного элемента фильтровой защиты – фильтра напряжения обратной последовательности. Обоснован выбор управляющего сигнала защитного устройства и использование в качестве чувствительного элемента неуравновешенного фильтра напряжения обратной последовательности. Разработана схема и сконструировано устройство для защиты трехфазных электроустановок от анормальных режимов работы с самоконтролем исправности. Опытные образцы устройства защиты прошли испытания в условиях разреза «Павловский – 2».
9. Обоснована необходимость разработки многоканального, многофакторного защитного устройства от анормальных режимов работы технологического комплекса. Разработан принцип построения универсального защитного и диагностического устройства технологического комплекса, рассчитана схема и сконструировано многоканальное, многофакторное устройство защиты от анормальных режимов работы компактно расположенных электроприемников технологического комплекса, обладающее самоконтролем исправности. Опытный образец пятнадцатиканального защитного устройства прошел апробацию в условиях дробильного комплекса Лучегорского угольного разреза.
10. Дано обоснование необходимости разработки и внедрения новых технологий технического обслуживания горного оборудования – по его фактическому состоянию и проактивной с применением современных способов и технических средств неразрушающего контроля. Предложены параметры виброконтроля и разработана рабочая методика вибромониторинга вращающегося горного оборудования. Проведены экспериментальные исследования и определены статистические параметры различных дефектов подшипниковых узлов преобразовательных агрегатов карьерных экскаваторов.
11. Предложены мероприятия по реализации проактивной системы технического обслуживания: безразборное восстановление работоспособности подшипниковых узлов электрических машин.
12. Предложена поэтапная система мероприятий перехода на систему обслуживания по фактическому состоянию, структурная схема системы мониторинга оборудования карьерных экскаваторов, реализуемая как отдельная подсистема управления технико-экономического планирования ремонтно-эксплуатационных мероприятий.