1 Особенности предприятия как системы
Вид материала | Документы |
- Раздаточный материал к Теме, 2609.88kb.
- Концепция системы мониторинга экономического состояния промышленного предприятия, 1358.19kb.
- Лекция Понятие предприятия и их виды, 228.06kb.
- Программа дисциплины Системы массового обслуживания Семестр, 22.38kb.
- Тема «Особенности административного, финансового и гражданского права, как отраслей, 206.64kb.
- Темы курсовых работ для специальности «Экономика и бухгалтеркий учет» по дисциплине, 10.4kb.
- Иях рыночной экономики предприятия как самостоятельные социально-экономические системы, 25.03kb.
- Темы курсовых работ по дисциплине: «Экономика предприятия». Особенности внутренней, 14.81kb.
- 3 Контроль выполнения бюджета предприятия, 166.5kb.
- Управления базой данных (субд). Неформально можно определить базу данных как некоторый, 93.97kb.
1.1.Особенности предприятия как системы
Предприятие следует рассматривать как открытую систему, которая тесно взаимодействует с внешней средой. Средой для него являются другие предприятия и организации, органы управления, зарубежные фирмы, учебные заведения - которые взаимодействуют с ним и связаны договорными отношениями или обменом информации.
Как системе, предприятию присуща комплексность, которая определяется комплексностью его задач и целей и разнообразием процессов производства и управления.
Предприятие является динамичной системой, способной изменяться, развиваться, переходить из одного качественного состояния в другое.
Предприятие саморегулирующаяся система, которая может в определенных пределах приспосабливаться к внешним или внутренним изменениям.
Предприятию как системе присуще свойство эмерджентности, т.е. появление у системы свойств, отсутствующих у ее элементов.
Чтобы все элементы системы соединить в целое, ее необходимо организовать, т.е. спроектировать, построить и обеспечить функционирование.
Реализация принципов системности при проектировании производственных систем и организации производства предполагает следующее:
- рассмотрение предприятия как особой системы, которая взаимодействует с другими в рамках рыночной экономики;
- необходимость создания на предприятии системы организации производства, охватывающей во взаимосвязи все процессы по изготовлению, реализации и обслуживанию в эксплуатации конкретных видов техники;
- применение целевого начала при разработке мероприятий по совершенствованию организации производства;
- ориентация на комплексное решение проблем экономики, техники организации производства и социальных задач коллектива;
- внедрение многовариантного проектирования производственных систем с целью выбора рациональных альтернативных решений;
использование систем оценок, критериев и нормативов эффективной организации производства в процессе ее проектирования и функционирования.
1.2.Концептуальная модель ОП на предприятии
При построении производственных систем и совершенствовании ОП используются приемы организационного моделирования. Они представляют собой метод изучения производственных систем с помощью разработки и анализа организационных моделей. Модель используется для упрощенного описания объекта производственной системы, ее подсистем.
Единство принципиальных основ организации промышленного производства позволяет разработать общую модель организации, которая может быть адаптирована к конкретным условиям.
Структура модели ОП на предприятии должна включать следующее:
формулировку целей ОП и критерии эффективности организации производственной системы.
общую характеристику системы производства на предприятии и состава ее подсистем
перечень задач организации производства в каждой подсистеме с указанием исполнителей
характеристику функций линейных руководителей и специальных подразделений в области организации производства
схему информационных потоков и документооборота в системе ОП.
Главная цель ОП – обеспечить высокую экономическую эффективность функционирования предприятий. Средствами достижения главной цели служат цели второго уровня – основные цели. Они определяются характером деятельности предприятия (удовлетворение спроса потребителей, поставка продукции по договорам, разработка новых видов продукции и др.).
Система ОП – это совокупность организационных форм, методов и правил, осуществление которых обеспечивает рациональное функционирование элементов производственной системы и их взаимодействие в процессе производства продукции. При формировании системы организации производства можно выделить частные функции организационной деятельности, сгруппировав их в виде подсистем (относительно обособленный комплекс). Основные элементы производственного процесса – орудия труда, предметы труда и сам труд.
ОП обеспечивает согласованное и эффективное функционирование этих элементов в рамках производственной системы. Для этого в системе ОП выделяются три взаимосвязанные подсистемы:
Организация труда участников производственного процесса.
Организация функционирования орудий
Организация движения предметов труда в производстве.
Согласованное взаимодействие трех подсистем достигается формированием структуры производственного процесса.
В производственном процессе есть группы процессов разнохарактерных по содержанию, принципам и методам организации. Соответственно им выделяется комплекс функциональных подсистем: организация подготовки производства и освоения новой продукции, организация основных производственных процессов, организации производственной инфраструктуры, организации работ по обеспечению качества продукции, организации материального обеспечения производства, организации сбыта и реализации продукции.
Связи организации функциональных подсистем изображены на рис.1.
Система организации производства обеспечивает интеграцию всех групп процессов в единый производственный процесс. Это реализуется системой формирования производственной структуры, системой оперативного планирования и системой экономических отношений.
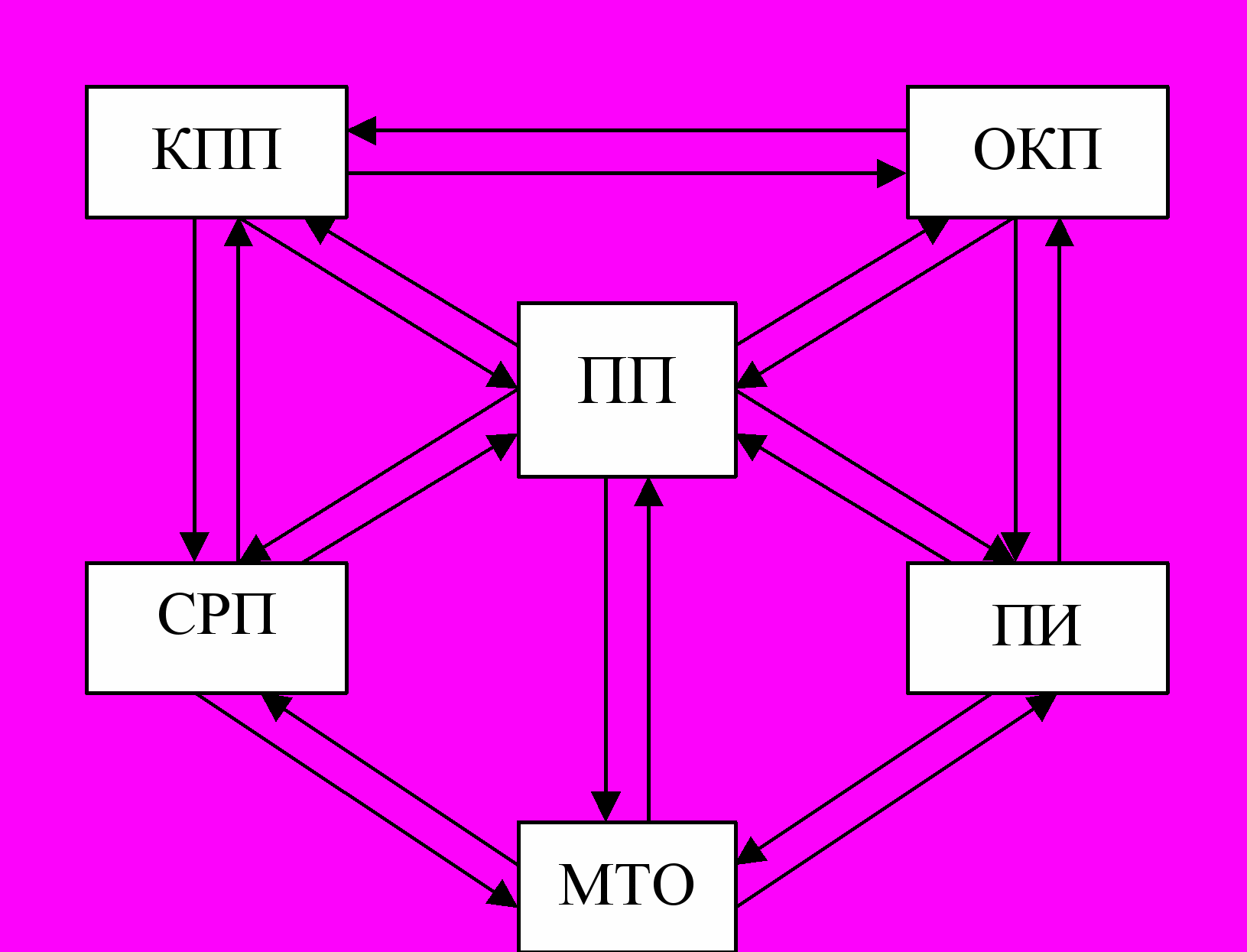
Рис.1.КПП – комплексная подготовка производства.
ОКП – обеспечение качества продукции.
ПИ – производственные инфраструктуры.
МТО – материально-техническое обеспечение.
СРП – сбыт и реализация продукции.
ОПП – основные производственные процессы.
Принципы организации подготовки производства
В основе рациональной организации процессов создания новой техники лежат общие закономерности организации производства. Тем не менее, особенности процессов создания новой техники при построении систем подготовки производства требуют учета ряда специфических правил:
- принцип комплексности означает проведение всех работ по организации производства по единому плану. Данный план охватывает все процессы от научных исследований до освоения новой техники и учитывает комплекс возникающих организационных, технических, экономических, социальных и других проблем.
Принцип специализации - закрепление за каждым подразделением видов деятельности, соответствующих его специализации.
Принцип комплектности документации и составных частей изделия - означает одновременное выполнения комплекса работ к моменту времени, когда их дальнейшее продолжение возможно только при наличии полного комплекта документации или составных частей изделия.
Принцип непрерывности работ по созданию новой продукции.
Принцип пропорциональности - требование соответствия производственных возможностей подразделений.
Принцип параллельности - означает совмещение во времени различных стадий, работ.
Принцип строгой последовательности работ и прямоточности - разработка и освоение продукции ведется с присущей этому виду работ последовательностью. Прямоточность - кратчайший маршрут движения технической документации и наименьший путь, проходимый новым изделием по всем стадиям его разработки и освоения.
Принцип научно-технической и производственной интеграции - понимается как совокупность условий, обеспечивающих достижение единой цели в результате деятельности некоторого множества специализированных подразделений.
ОРГАНИЗАЦИЯ НАУЧНО-ИИСЛЕДОВАТЕЛЬСКИХ РАБОТ
Научные исследования являются основой быстрого развития техники и открывают новые возможности для коренного преобразования производства. К НИР относятся фундаментальные, поисковые и прикладные исследования.
Фундаментальные исследования изучают объективные явления и закономерности, открывают новые пути преобразования природы и общества, производительных сил, создания техники будущего, использования новых источников энергии. Выполняются в основном в академических институтах и вузах.
Поисковые исследования направлены на создание научного задела с целью его использования в прикладных исследованиях. Выполняются при отсутствии готовых научных и технических решений. Позволяют установить возможность использования уже открытого явления, свойства или принципа в определенной практической сфере, в технике определенного назначения. Выполняются в отраслевых НИИ, ведутся академическими институтами и вузами.
Прикладные НИР обеспечивают проверку практического использования результатов фундаментальных и поисковых НИР в конкретных объектах новой техники. Ведутся научно-производственными объединениями, крупными предприятиями, отраслевыми НИИ и вузами на основе договоров с предприятиями.
Прикладные НИР могут быть направлены на создание новых изделий, материалов, технологических процессов. К НИР условно относят работы по созданию нормативно-технических, проектных и информационных документов. (Стандарты, руководящие материалы, оргпроекты, справочники, научно-информационные материалы).
Логическим продолжением прикладной НИР являются ОКР – опытно-конструкторские работы. ОКР направлены на создание новой техники конкретного эксплуатационного назначения. При выполнении ОКР разрабатываются схемы и рабочие чертежи нового изделия, изготавливаются и испытываются новые образцы.
Для поисковых и прикладных НИР характерны следующие этапы:
1. Техническое задание, 2. Выбор направления исследования 3. Теоретические и экспериментальные исследования. 4. Обобщение и оценка результатов исследований .5. Приемка НИР.
ТЗ определяет цель НИР, ее технико-экономическую целесообразность, предполагаемые результаты, содержание и порядок работ, способ реализации результатов исследований, этапы и сроки их выполнения состав исполнителей. ТЗ разрабатывает исполнитель НИР и согласует с заказчиком. При разработке ТЗ проводится анализ передовых достижений техники, используются результаты патентных исследований и научное прогнозирование, а так же требования заказчика.
На втором этапе осуществляются следующие виды работ:
- сбор и изучение научно-технической информации, патентные исследования,
- технико-экономический анализ возможных решений проблемы;
- выбор и обоснование оптимального направления НИР и способов решения поставленной задачи:
- разработка рекомендаций по методам и средствам исследований;
Результаты оформляют в виде пояснительной записки или научно-технического обзора.
При выполнении прикладных НИР второй этап отдельно не выделяют. Некоторые его работы проводят совместно с теоретическими и экспериментальными исследованиями.
На третьем этапе осуществляются следующие виды работ:
- теоретическое обоснование предлагаемых решений;
- обоснование необходимости проведения экспериментов;
- разработка методики экспериментальных исследований;
- подготовка макетов и экспериментального оборудования;
- проведение экспериментов;
- сравнение результатов экспериментов с теоретическими исследованиями и при необходимости внесение изменений в схемы, расчеты, проекты.
Прикладные НИР часто включают этап; разработки, изготовления и испытания макета оборудования. После изготовления макета проводят экспериментальные работы. Этап завершается оформлением протокола испытаний и разработкой предложений по технологии изготовления новой техники.
На четвертом этапе обобщаются и оцениваются результаты исследований. Отчет должен содержать обобщение результатов работ по всем этапам и рекомендации по разработке новой техники. На этой стадии может быть создан проект ТЗ на ОКР по результатам исследований.
Завершающий этап - приемка НИР. Этап заканчивается подписанием акта комиссией по приемке. Работы оцениваются путем сопоставления результатов с требованиями ТЗ.
Основным звеном предприятия в котором проводятся НИР являются лаборатории. Главные специалисты (главный конструктор, главный технолог, главный энергетик, главный металлург) имеют соответствующие лаборатории. Для каждой лаборатории утверждается положение, в котором излагаются цели, задачи, структура лаборатории, перечень работ. Существуют следующие виды специализации научных подразделений: предметная, функциональная и смешанная. Предметная - выполнение исследований по конкретным объектам (машины, оборудование, узлы). Функциональная - изучение отдельных характеристик изделий, материалов, процессов (антикоррозионные свойства, прочностные характеристики). Для решения конкретных задач могут создаваться творческие коллективы из специалистов разного профиля по всему циклу: теоретические исследования, ОКР, технологические работы, освоение в производство. После решения задачи коллектив распадается.
Планирование НИР
Базой планирования НИР являются научно-обоснованные прогнозы, которые определяют пути создания качественно новых изделий, оборудования, материалов на основе доступного уровня развития науки и техники и потребности изделий в планируемом периоде. Основной формой планирования НИР и ОКР является перспективный тематический план. Данный план содержит перечень тем и проблем, которые подлежат реализации в период действия плана. На основе перспективного плана составляется годовой тематический план НИР и ОКР.
Характеристика ОКР
В зависимости от сложности и объёма работ в НИР и ОКР могут участвовать несколько организаций. При этом назначается организация главный исполнитель, который координирует работу организаций и согласовывает план работ. Работа может заканчиваться изготовлением опытного образца или установочной партии и подготовкой производства к серийному выпуску (Б и А). А - требует иной системы планирования. Нужен переход к сквозному планированию всех стадий ОКГ, включая поставки на производство. Нужен единый план работ, соответствующие формы плановых документов.
1.3.Организация технологической подготовки производства.
1.4.Планирование и оперативное управление подготовкой производства
1.5.Организационная подготовка производства и освоение новых видов продукции.
2.Организация производственных процессов.
2.1.Производственный процесс и основные принципы его организации.
2.1.1.Принципы организации производственного процесса.
Принципы организации производственных процессов представляют собой исходные положения, на основе которых осуществляется построение, функционирование и развитие производственных процессов.
Принципы дифференциации предполагают разделение производственного процесса на отдельные технологические процессы, операции и закрепление их за соответствующими подразделениями предприятия.
Принципу дифференциации противостоит принцип комбинирования производственных процессов. Этот принцип предполагает объединение всех или части разнохарактерных процессов по изготовлению продукции в пределах участка, цеха или производства.
Принципы дифференциации и комбинирования распространяются и на отдельные рабочие места. В практической деятельности приоритет отдаётся экономически целесообразному принципу.
Принцип концентрации выражается в сосредоточении определенных производственных операций или функционально-однородных работ на отдельных рабочих местах, участках, цехах. При концентрации однородных работ требуется меньшее количество дублирующего оборудования, повышается гибкость производства, возрастает загрузка оборудования.
Принцип специализации основан на ограничении разнообразия элементов производственного процесса. Он предполагает закрепление за рабочим местом и подразделением ограниченной номенклатуры работ, операций, деталей.
Противоположным для принципа специализации является принцип универсализации. При данном принципе каждое рабочее место или подразделение изготавливает детали широкого ассортимента или выполняет разнородные операции.
Уровень специализации рабочего места определяется коэффициентом закрепления операции, т.е. количеством деталеопераций, выполняемых на рабочем месте за определённый промежуток времени (месяц).
Принцип пропорциональности заключается в определенном количественном соотношении элементов производственного процесса. Пропорциональность производственной мощности предполагает равенство мощностей участков или коэффициентов загрузки оборудования. Несоблюдение принципа пропорциональности ведет к появлению "узких мест" в производстве или к недоиспользованию оборудования.
Производственный процесс изготовления машины состоит из большого числа операций. Выполнение их последовательно вызвало бы недопустимо большую длительность производственного цикла. Вследствие этого отдельные элементы процесса изготовления должны выполняться параллельно, т.е. одновременно во времени. Выполнение принципа параллельности достигается следующими способами:
обработка одной детали на одном станке несколькими инструментами;
одновременная обработка деталей одной партии на данной операции на нескольких рабочих местах;
одновременная обработка деталей одной партии по различным операциям на нескольких рабочих местах;
одновременное изготовление различных деталей одного и того же изделия на разных рабочих местах.
Использование принципа параллельности ведет к сокращению длительности производственного цикла, времени пролеживания деталей и к экономии рабочего времени.
Принцип прямоточности - принцип организации производственного процесса, при котором все стадии и операции производственного процесса осуществляются в условиях кратчайшего пути прохождения предмета труда. Принцип требует обеспечения прямолинейного движения предметов труда по ходу технологического процесса и устранение возвратных движений. Достичь прямоточности можно путем расположения операций и частей производственного процесса в порядке следования технологических операции. Соблюдение принципа прямоточности ведет к сокращению грузооборота и уменьшению затрат на транспортировку.
Принцип ритмичности означает, что все производственные процессы и единый процесс производства повторяются через определённые интервалы времени.
Различают ритмичность выпуска продукции, ритмичность работы и ритмичность производства. Ритмичность выпуска продукции означает выпуск одинакового или равномерно увеличивающегося (уменьшающегося) количества продукции за одинаковые интервалы времени. Ритмичность работы выражается в выполнении равных объемов работ за равные интервалы времени. Ритмичность производства заключается в соблюдении двух вышеуказанных принципов ритмичности. Ритмичная работа - основа высокой производительности труда, оптимальной загрузки оборудования, гарантия высокого качества продукции.
Принцип непрерывности реализуется в таких формах организации производственного процесса, при которых все операции осуществляются непрерывно, и предметы труда непрерывно движутся с операции на операцию. Принцип полностью реализуется на автоматических и непрерывно поточных линиях. На этих линиях изготавливаются или собираются предметы труда с длительностью операций равной или кратной такту линии.
В машиностроении преобладают дискретные технологические процессы и производства с высокой степенью синхронизации операций не являются преобладающими. Однако в любом случае необходимо стремиться к сокращению до минимума перерывов в процессе производства.
Приведенные принципы организации действуют не изолированно и тесно переплетаются в каждом производственном процессе. Принципы организации развиваются неравномерно. В тот или иной период какой-либо принцип выдвигается на первый план или приобретает второстепенное значение. Так, уходит в прошлое принцип узкой специализации рабочих мест, они становятся более универсальными. Принцип дифференциации заменяется принципом комбинирования, что позволяется строить производственный процесс на основе единого потока. В условиях автоматизированного производства возрастает роль таких принципов, как пропорциональность, непрерывность, прямоточность.
3.Организация поточного производства.
4.Организация автоматизированного производства.
4.1.1.Типы автоматических линий.
Автоматическая линия - это система машин-автоматов, размещенных по ходу технологического процесса и объединенных устройствами для транспортировки деталей, накопления заделов, удаления отходов. АЛ оснащена системой управления. По технологическому назначению АЛ делятся на линии для выполнения одного вида технологических операций (механообрабатывающие, сборочные) и для выполнения нескольких видов разнородных операций - комплексные.
По количеству обрабатываемых изделий линии подразделяются на однопредметные и многопредметные.
По характеру движения обрабатываемых деталей - синхронные и несинхронные. Синхронные связаны жесткими транспортными устройствами. При остановке одной из машин останавливается вся линия. Несинхронные состоят из независимо работающих машин с гибкой транспортной связью. Машины снабжаются бункерами накопителями для хранения деталей. АЛ подразделяются на переналаживаемые и непереналаживаемые. Непереналаживаемые комплектуются специальными станками и при переходе на другое изделие требуют реконструкции. Переналаживаемые комплектуются специализированными и даже универсальными станками, способными обрабатывать широкий ряд типоразмеров деталей.
По способу транспортировки линии с непрерывной или периодической транспортировкой деталей.
4.1.2.Особенности расчета автоматических линий.
Расчёт АЛ в основном соответствует расчетам неавтоматических линий, но имеет и свои особенности. Такт АЛ - время в течение которого выдаётся деталь или группа деталей. Расчётный такт линии

где
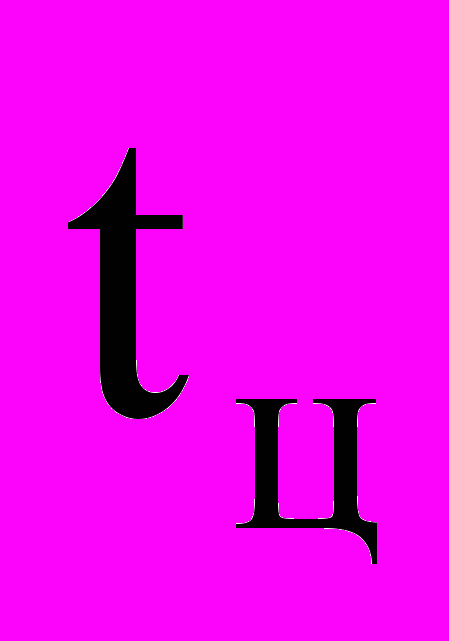
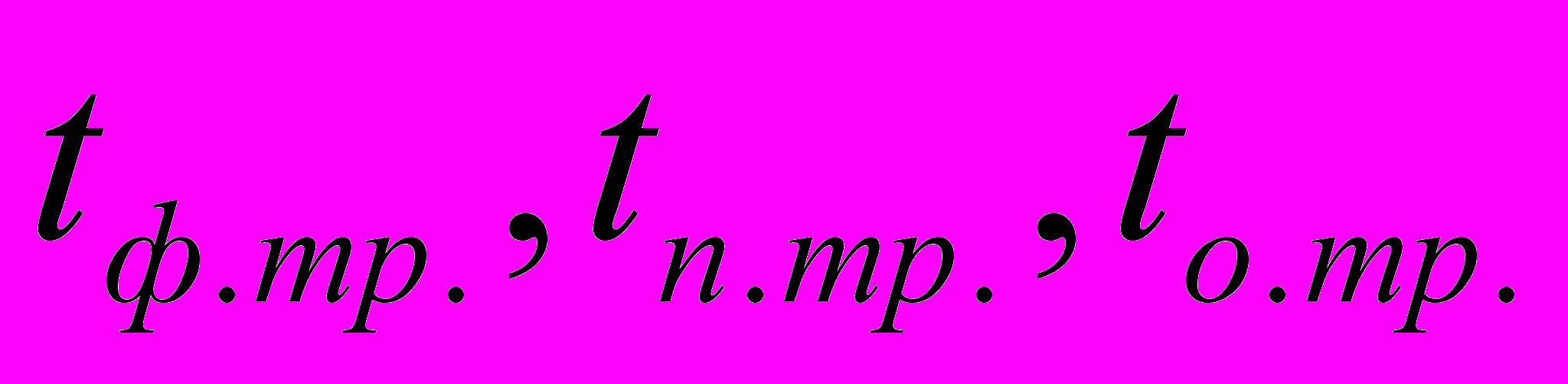
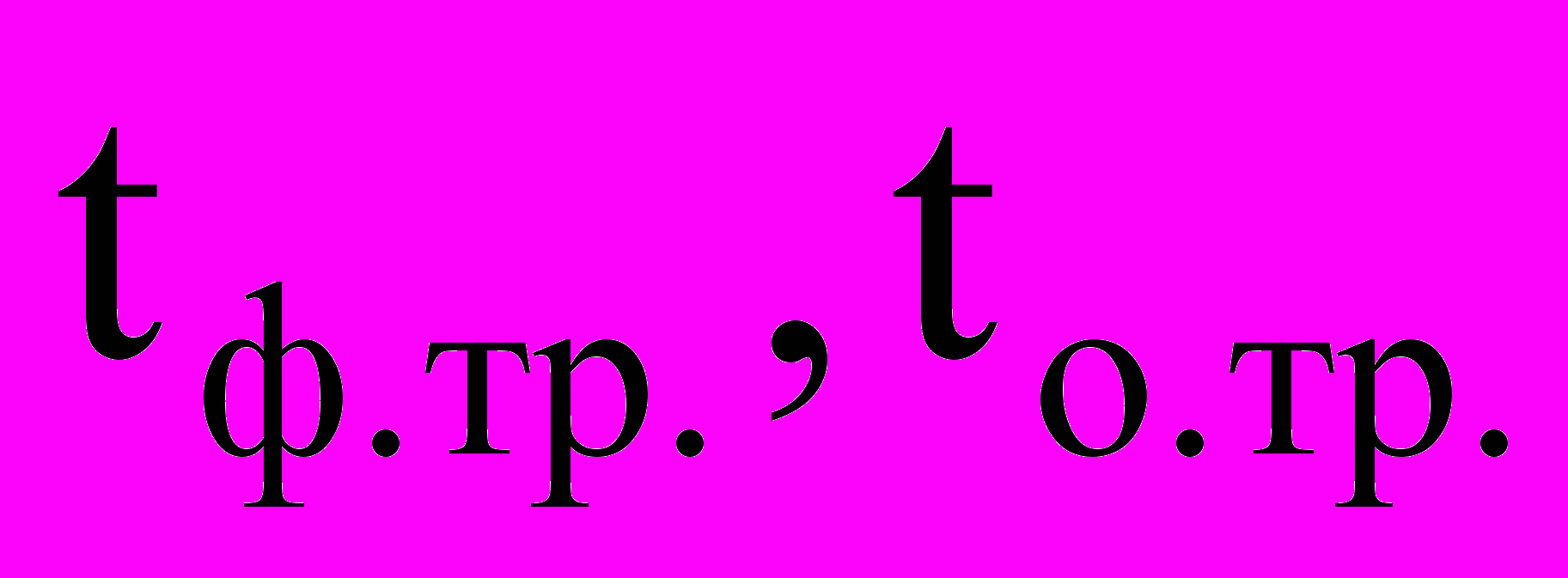
Для металлорежущего оборудования

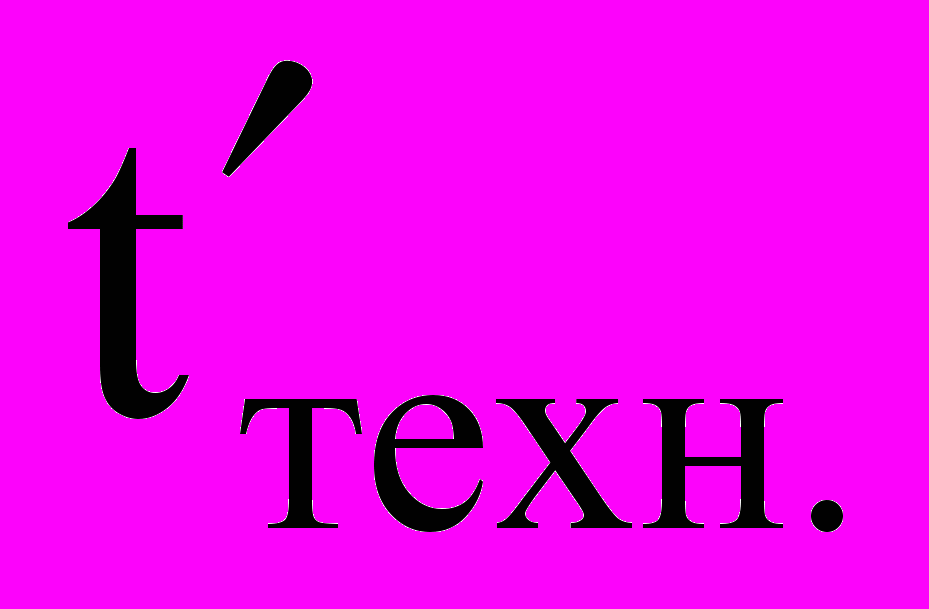
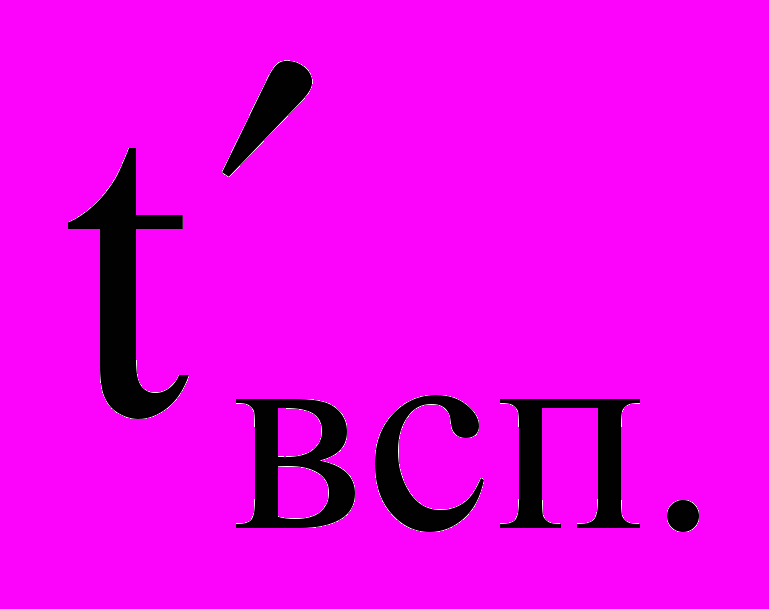
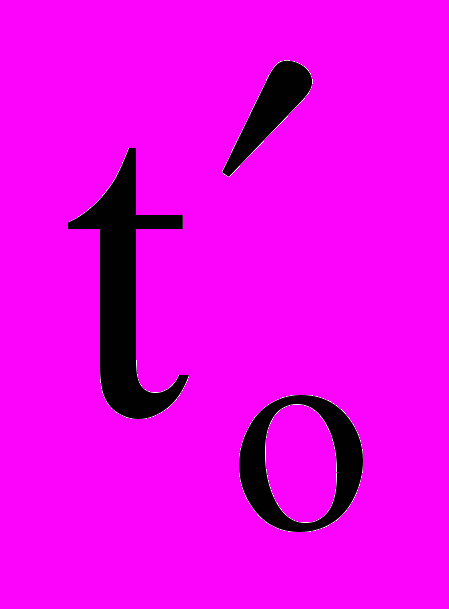
Штучная производительность для однопоточной линии
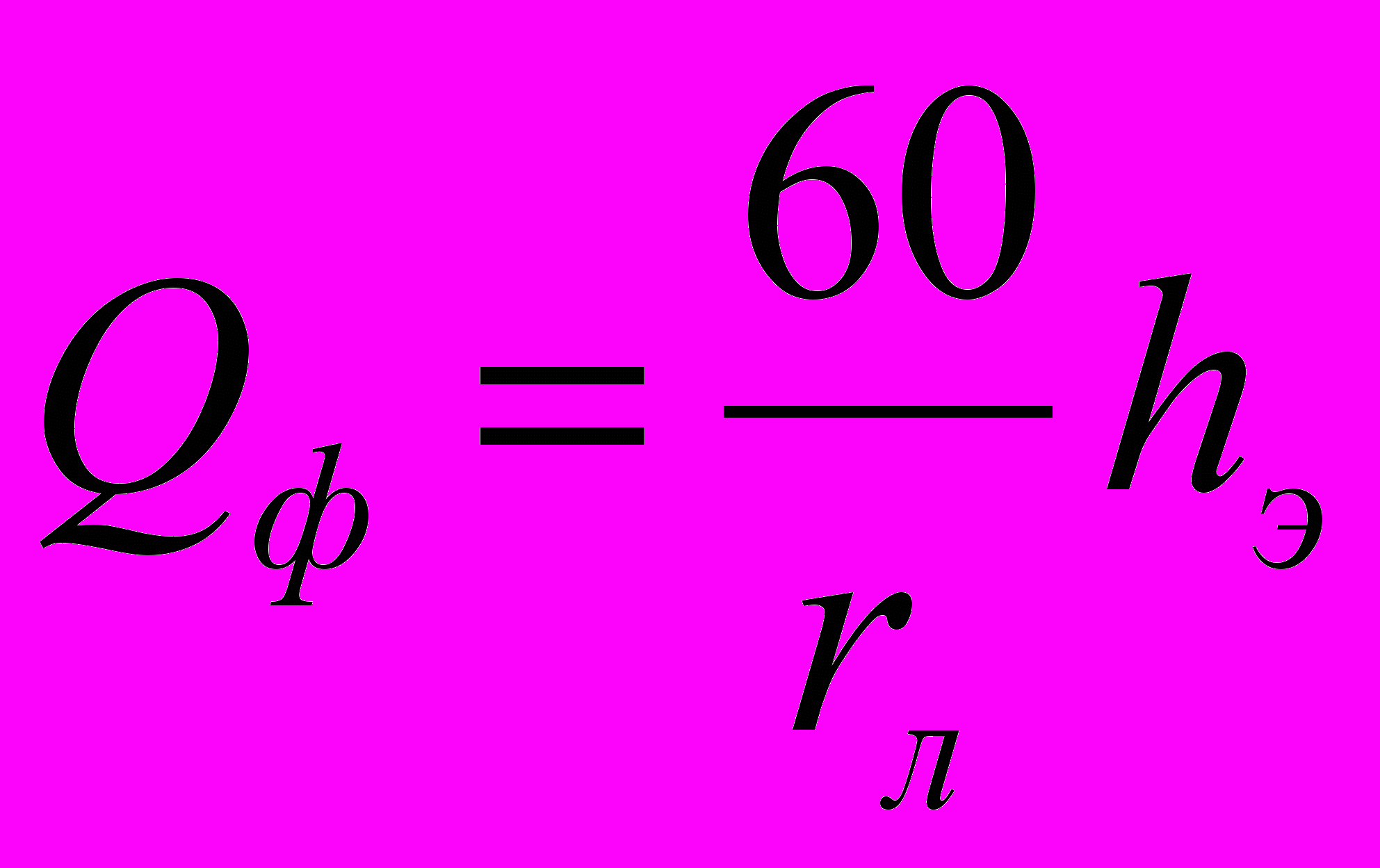
где
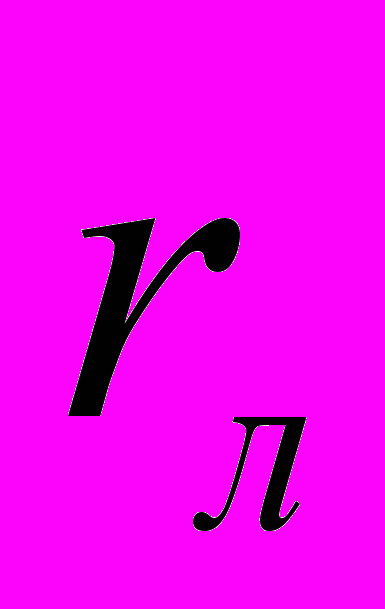
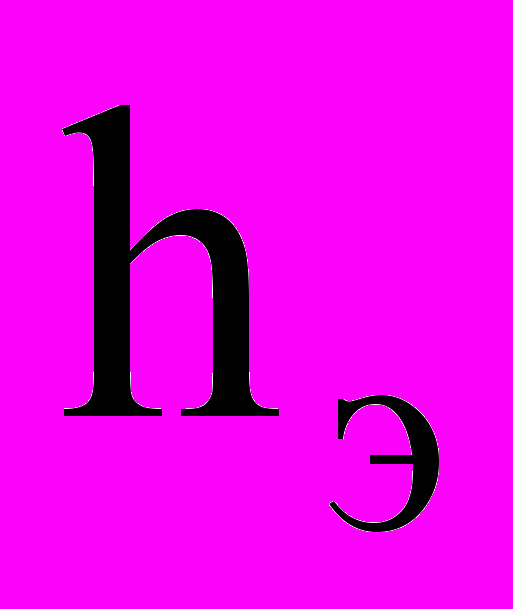
В бункерных АПЛ образуются заделы 2-х видов: компенсирующие и пульсирующие. Компенсирующие образуются, если смежные участки линии имеют разные такты работы.
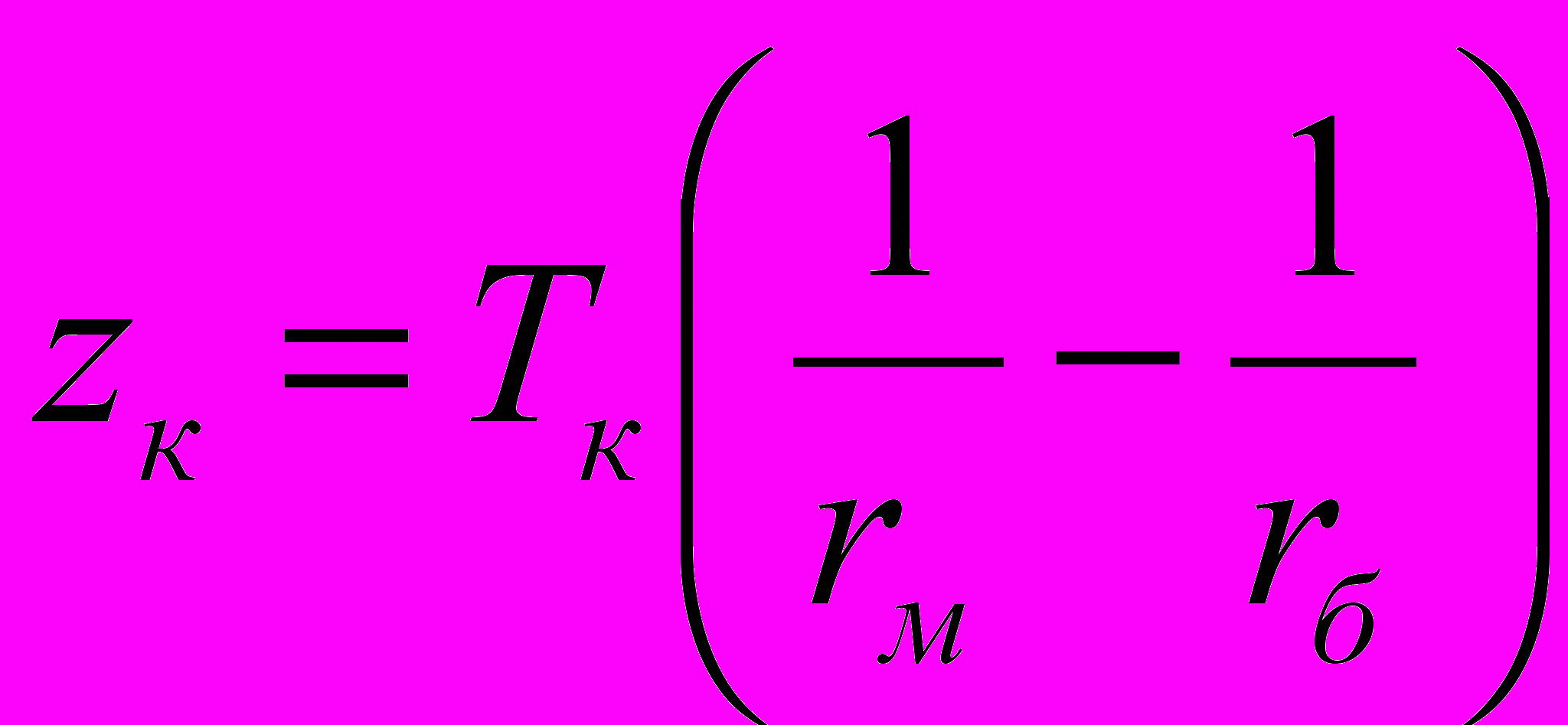

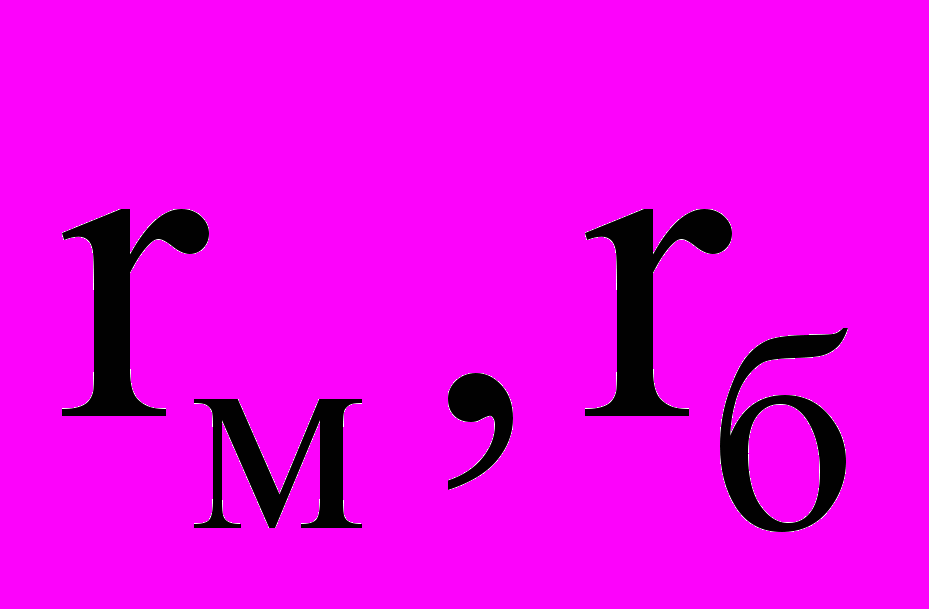
4.1.3.Организация рациональной эксплуатации автоматических поточных линий.
Для обеспечения рациональной эффективной работы АПЛ создается система их эксплуатации. Она включает в себя следующие системы:
Система технического обслуживания АПЛ. Предназначена для обеспечения нормального функционирования АПЛ и выполнения работ по техническому и организационному обслуживанию АПЛ. Работа выполняется наладчиками, операторами и другим линейным персоналом.
Система ремонта. Предназначена для сохранения АПЛ в рабочем состоянии и поддержания технических параметров оборудования. Обеспечивается службами главного механика и энергетика с привлечением линейного персонала.
Система контроля и управления качеством, продукции. Обеспечивает выпуск продукции в соответствии с техническими требованиями. Вопросы обеспечения качества решаются наладчиками АПЛ и работниками ОТК.
Система инструментального обслуживания линии. Функции: обеспечение инструментом, подготовка инструмента к эксплуатации, учет, хранение, доставка на линию. Предусмотрена регламентированная смена инструмента.
Система административно-технического управления - обеспечивает требование рациональной организации, труда и управления при эксплуатации АПЛ. Функционально подчиняется начальнику цеха.
4.1.4.Организация производства с применением станков с ЧПУ
Прогрессивным направлением автоматизации производства в машиностроении является применение станков с ЧПУ. Их использование даёт ряд технико-экономических преимуществ:
Их производительность выше производительности станков токарного типа без программного управления более чем в 3 раза, потребность в производственных площадях в 3 раза меньше. Большой эффект станки с ЧПУ дают при выполнении особо сложных технологических операций. При этом высвобождаются квалифицированные рабочие.
Главный эффект в том, что при программном управлении до 80-90% увеличивается время работы оборудования (15-20% у обычных станков).
Резко сокращается вспомогательное время, время на смену инструмента и переналадку оборудования. Переналадка заключается в замене программы, а в ряде случаев и в замене инструмента. Широкий диапазон работ делает их особенно ценными в единичном и мелкосерийном производстве. Имеется опыт включения станков с ЧПУ в поточные линии. Перспективным является такой вид оборудования как обрабатывающие центры. Они представляют собой много операционные станки с автоматической сменой инструмента. По производительности они эквивалентны 3-4 станкам с ЧПУ и 8-12 обычным станкам.
Для эффективного использования станков с программным управлением необходимо создать систему организационного обеспечения. Система организации работ станков с программным управлением должна включать следующее:
технико-экономическое обоснование применения станков с ЧПУ.
номенклатуру деталей
специальную организационную структуры системы.
надлежащее обслуживание станков.
автоматизированную разработку управляющих программ.
Специальная организационная структура сориентирована на изменения которые появляются при появлении в парке оборудования станков с ЧПУ. Такая структура включает специальные производственные цеха и участки, подразделения технического обслуживания, и специализированную технологическую службу.
Расположение станков с ЧПУ в одном цехе позволяет:
организовать более качественное их обслуживание.
управление одним рабочим несколькими станками.
создавать высокоэкономичные предметно-замкнутые участки (технологические потоки) по обработке сменных деталей.
Важный элемент структуры системы организации работ на станках с ЧПУ является отдел программного управления (создаётся на предприятиях с большим числом станков).
В его состав входят: технологическое бюро, осуществляет отбор деталей, разрабатывает маршрутную и операционную технологию, выбирает инструмент и оснастку, составляет задания для расчета программ.
Бюро программирования – разработка программ.
Бюро внедрения – отрабатывает программы и технологические процессы, осуществляет обработку контрольной партии деталей и сдаёт ее ОТК.
Важное место в системе организации работ отводится подразделениям, занятым ремонтом и обслуживанием станков с ЧПУ. Создаются при отделах главного механика и энергетика.
Ремонтом целесообразно проводить с использованием системы ППР. Система ремонтного обслуживания включает проводимые периодических проверок геометрической и технологической точности станков с ЧПУ и их аттестацию.
Значительное внимание уделяется инструментальной оснастке станков с ЧПУ. Для операций заточки и переточки режущего инструмента составляется специальные карта заточки.
Создание комплексов станков управляющих от ЭВМ идет по пути создания двухуровневых систем, с установкой ЭВМ у каждого станка.
Центральная ЭВМ выполняет функции технологической подготовки производства, учета хода производства, учета захода инструмента, управления транспортными системами.
Местная ЭВМ осуществляет ЧПУ, прием управляющих программ от центральной, передачу данных о ходе ТП, управления загрузочным устройством и т.д.
4.2.Организационные основы гибкого автоматизированного производства
ПП – позволяет за короткое время, не прерывая технологического процесса переходить на выпуск продукции произвольный номенклатуры, в пределах технических возможностей и технологического оборудования.
Степень гибкости можно определить количеством времени и дополнительных расходов при переходе на выпуск новой продукции, а также широтой номенклатуры выпускаемой продукции. Использование гибких производственных систем способствует сохранению в условиях многономенклатурного серийного и мелкосерийного производства преимуществ массового производства (непрерывность, ритмичность). Это ведет к повышению производительности труда и качества продукции.
Техническую базу гибкой автоматизированной системы представляют оборудование с числовым программным управлением, промышленные роботы, специальные транспортные средства и АСУ ТП.
Первичная ячейка ГПС - гибкий производственный модуль. Состоит из единицы технологического оборудования, оснащен автоматизированным устройством программного управления, а также средствами автоматизации технологического процесса. Она автономно функционирует, имеет возможность встраиваться в систему более высокого уровня. Средства автоматизации могут включать накопители, спутники, устройства загрузки и выгрузки, замены технологической оснастки, удаления отходов, автоматического контроля, переналадки. Из ГПМ формируются гибкие автоматизированные линии, участки и цехи.
В ГАПах реализуется такие принципы организации производства как концентрация, специализация, универсализация, пропорциональность, ритмичность, параллельность, прямоточность. Однако их роль и методы реализации меняются. Повышается роль принципа пропорциональности, т.к. увязывается пропускная способность не только основных производственных подразделений, но и сопряжённых с ним вспомогательных. Возрастает роль принципа универсализации. В ГПС отходят от принципов узкой специализации работающих (рабочие широкого профиля). В некоторой степени теряет значительный принцип прямоточности.
Появляются новые принципы. К ним относятся:
принцип интеграции производственных процессов. Появилась задача соединения основных, вспомогательных и обслуживающих процессов в единый производственный.
принцип необходимого разнообразия. Означает свободу номенклатуры изделий в рамках установленных ограничений.
принцип резервов, ориентирующий на создание экономически обоснованных резервов всех элементов производственного процесса.
принцип автономности ГАСистемы. Означает независимость от других производственных подразделений и максимальную предметную замкнутость.
принцип универсальности. Допускает возможность изменения последовательности использования оборудования при выполнении данного производственного процесса.
Особенностью ГАС является то, что одновременно с проектированием технической системы ведется разработка организационного проекта ГАС. При этом решается следующие организационные задачи.
1 Подбор номенклатуры деталей и определение характера специализации производственных подразделений.
2 Формирование рациональной производственной структуры цехов и участков, обеспечивающей интеграцию основных, вспомогательных и обслуживающих процессов.
3 Проектирование системы технического организационного обслуживания участков гибкой автоматизации (программного, материального, инструментального, информационного).
4 Проектирование системы организации технического контроля и управления качеством продукции.
5 Проектирование системы ремонтного обслуживания оборудования.
6 Разработка интегрированной системы оперативного планирования и регулирования производства, (и расчет нормативного движения предметов труда).
7 Разработка проекта организации труда всех категорий исполнителей и процедур реализации управления и обслуживания.
Появление ГАС вызывает к жизни новые технологические и производственные процессы, это требует рационализации производственной и управленческой структуры предприятия. Так создаются отделы программного обеспечения, специальные и технологические бюро, группы внедрения и отладки машинных программ. Выделяются группы электронного обслуживания оборудования, специальные ремонтные подразделения, создаются цеха и участки гибкой автоматизации. Производственная и управленческая структура совершенствуется путем формирования рациональной структуры самой гибкой системы (макроуровень) и организационной перестройки сопряженных с ней подразделений.
При переходе ГАПроизводству задача конструкторско-технологической подготовки определяет необходимость разработки конструкций и технологий их изготовления с учетом требований автоматизации.
Производственный процесс в ГПС следует рассматривать как единый комплекс, включающий технологические, транспортные, погрузочно-разгрузочные, контрольные и наладочные операции. Отсюда следует, что основными направлениями совершенствования производственных процессов в ГАС являются:
обеспечение непрерывности производственных процессов путем календарной регламентации и взаимной увязки основных, вспомогательных и обслуживающих процессов.
обеспечение максимального сосредоточения операции в ГАС по изготовлению детали.
максимальная автоматизация основных, вспомогательных и обслуживающих операций в ГАСистеме.
Значительную роль при обеспечении непрерывности играет система оперативного управления и планирования.
На качественно новом уровне в ГПС организуется система технического и организационного обслуживания. В совокупности работ по обслуживанию выполняются в рамках автоматизированной системы комплексного регламентированного обслуживания. К функциям обслуживания ГПС относятся следующее: информационная, производственно – подготовительная, инструментально – наладочная, транспортно – складская, хозяйственно – бытовая, контрольная, ремотно – профилактическая, энергетическая, информационная.
5.Организационное обеспечение качества продукции
5.1.Состояние и тенденции развития технического обслуживания производства.
В настоящее время весь комплекс работ по техническому обслуживанию выполняется самими предприятиями. Это приводит к большим нерациональным расходам. Для вспомогательных производств характерны единичный и мелкосерийный тип производства со значительными затратами ручного труда. Изготавливаемая продукция значительно дороже и менее качественная, чем на специализированных предприятиях (инструмент и запчасти в 2-3 раза дороже, чем на заводах станкоинструментальной промышленности). Недооценка роли вспомогательных хозяйств привела к существенному разрыву в уровнях техники и организации основного и вспомогательного производства.
Это привело к высокой численности вспомогательного персонала до 50% от общего числа рабочих. В ряде индустриальных стран в 2-а раза меньше.
Повышение техническое оснащенности предприятий вызывает необходимость совершенствования техники и организации вспомогательных работ. Внедрение комплексных систем механизации и автоматизации повышают сложность работ по обслуживанию оборудования. Функции обслуживания превращаются из вспомогательных в определяющие. Растут требования к квалификации персонала. При обслуживании роботов, станков с ЧПУ уровень подготовки обслуживающего персонала должен быть не ниже техника или инженера.
Решающая роль в совершенствовании всей системы тех. обслуживания принадлежит централизации и специализации однородных функций обслуживания. Это может происходить как в пределах предприятия, так и за счет расширения сети инструментальных, ремонтных заводов. Происходит и централизация транспортных услуг за счет создания крупных автохозяйств. За счет создания районных и кольцевых энергосистем достигается централизация энергоснабжения предприятий.
6.Оперативное планирование производства.
6.1.Виды систем оперативно-календарного планирования.
Под системой ОКП производства понимается методика и техника плановой работы. Они определяются степенью централизации плановой работы, планово-учетной единицей и дифференциацией плановых процессов, составом календарно-плановых нормативов, составом, порядком оформления и движения плановой и учетной документации. Под планово-учетной единицей понимается первичный объект планирования и учета: деталь, сборочная единица, комплект деталей, изделия в целом или комплекс определенных работ.
Выбор системы ОПК обуславливается типом и объемом производства, номенклатурой и техническими характеристиками изделий, степенью унификации и применяемости деталей и сборочных единиц, а также производственной структурой предприятия, цеха, участка.
Массовое производство чаще всего использует партионно-периодическую систему и систему планирования по ритму запуска. При партионно-периодической системе устанавливается определенная периодичность изготовления партий деталей и сборочных единиц в соответствии с требованиями сборки.
При планировании по ритму запуска осуществляется выравнивание производительностей производственных звеньев участка. Планово-учетная единица: изделие, деталь, сборочная единица.
В серийном производстве используется система планирования:
по цикловым комплектам (комплектно-групповая),
по опережениям,
по комплектовочным номерам,
по заделам.
При планировании по цикловым комплектам детали объединяются в группы по следующим признакам: общая периодичность изготовления, длительность производственного цикла и маршрута движения. Планово-учетная единица – цикловой (групповой) комплект деталей (детали могут относиться к разным изделиям).
При системе планирования по опережением для каждой партии изделий устанавливается опережение по запуску и выпуску по отношению к последующему звену производства.
Планово-учетная единица – комплект (серия) одноименных изделий. Система наиболее универсальна и распространена в производстве.
Система планирования по комплектовочным номерам характеризуется тем, что изготовление деталей и сборочных единиц для данной машины начинается после поставки предыдущим цехом всех входящих в нее деталей и сборочных единиц. Планово-учетная единица – комплект деталей, сборочных единиц. Всем сборочным единицам присваиваются порядковые номера. Последний номер присваивается готовым изделиям. Требование равномерной загрузки оборудования обуславливает то, что большинство деталей комплекта выпускается раньше общего срока их готовности, т. е. пролеживает между цехами. Система используется в серийном производстве, когда число деталей, входящих в комплект невелико.
Система планирования по заделам основана на создании нормативного не снижающегося задела по каждой детали и сборочной единице. Уровень нормативного задела определяется нормативным опережением. Расчет нормативных заделов и опережений производится на основе планов-графиков работы участков, длительности производственных циклов и суточной потребности в деталях.
Планово-учетная единица – условный комплект, изготовление которого обеспечивает выпуск продукции в заданном объеме на сутки, пятидневку или изделие-представитель.
В единичном и мелкосерийном производстве распространены показания и комплектно-сборочная система планирования. При показанной системе для каждого заказа строится сквозной календарный план-график технической подготовки производства и выполнения заказа.
Планово-учетная единица для сборочных цехов – заказ, для обрабатывающих и заготовительных – комплект деталей на заказ. Для данной системы характерно пролеживание деталей и сборочных единиц ?
При комплектно-сборочной системе планирования подача деталей на сборку осуществляется в несколько очередей в виде сборочных комплектов. Для каждой очереди устанавливается состав сборочных комплектов, из которых собирается изделие. Срок подачи сборочных комплектов определяется календарным опережением начала данной очереди сборки по отношению к сроку выпуска изделий. Планово-учетная единица – комплект деталей на сборочную единицу.
Для унифицированных и нормальных деталей используют систему планирования «на склад». Цель подобного планирования поддержание запасов, гарантирующих бесперебойное снабжение сборочного цеха.
При установлении планово-учетной единицы осуществляется и выбор планово-учетного периода. Планово-учетный период – кратный месяцу отрезок времени, по истечению которого цех или участок должен отчитаться по запланированной на этот период номенклатуре продукции.
6.2.Роль и значение партии деталей
Партия деталей – количество одновременно запускаемых деталей с однократной затратой подготовительно-заключительного времени.
Между ритмом запуска партии деталей R и размером партии деталей n имеется зависимость:
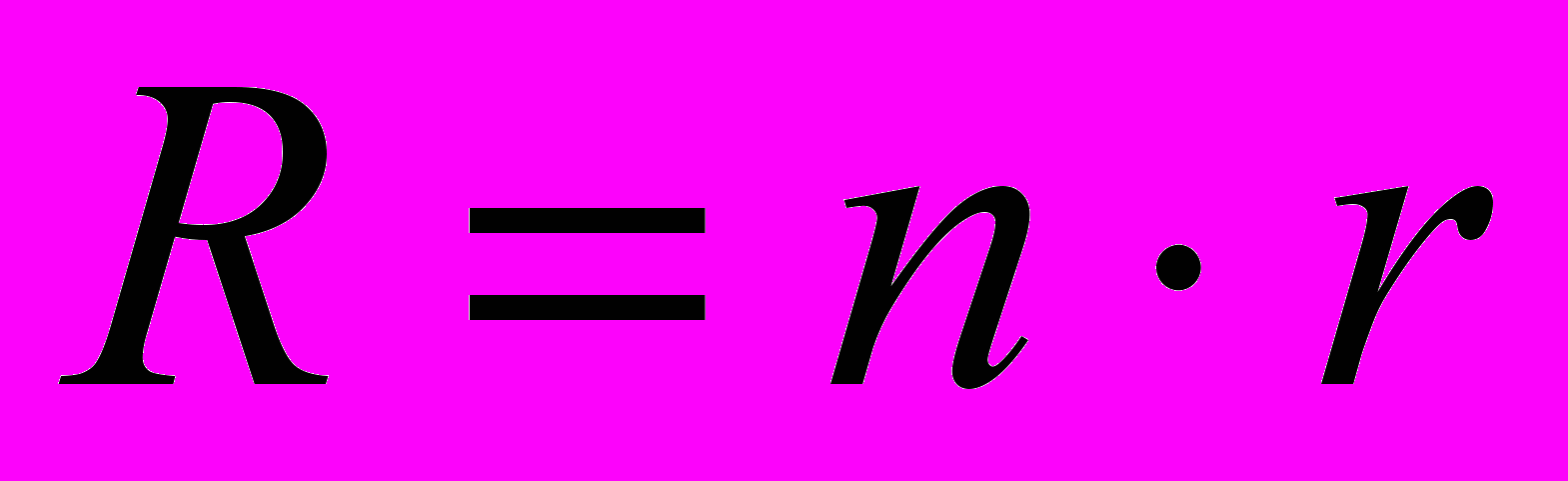
При этом
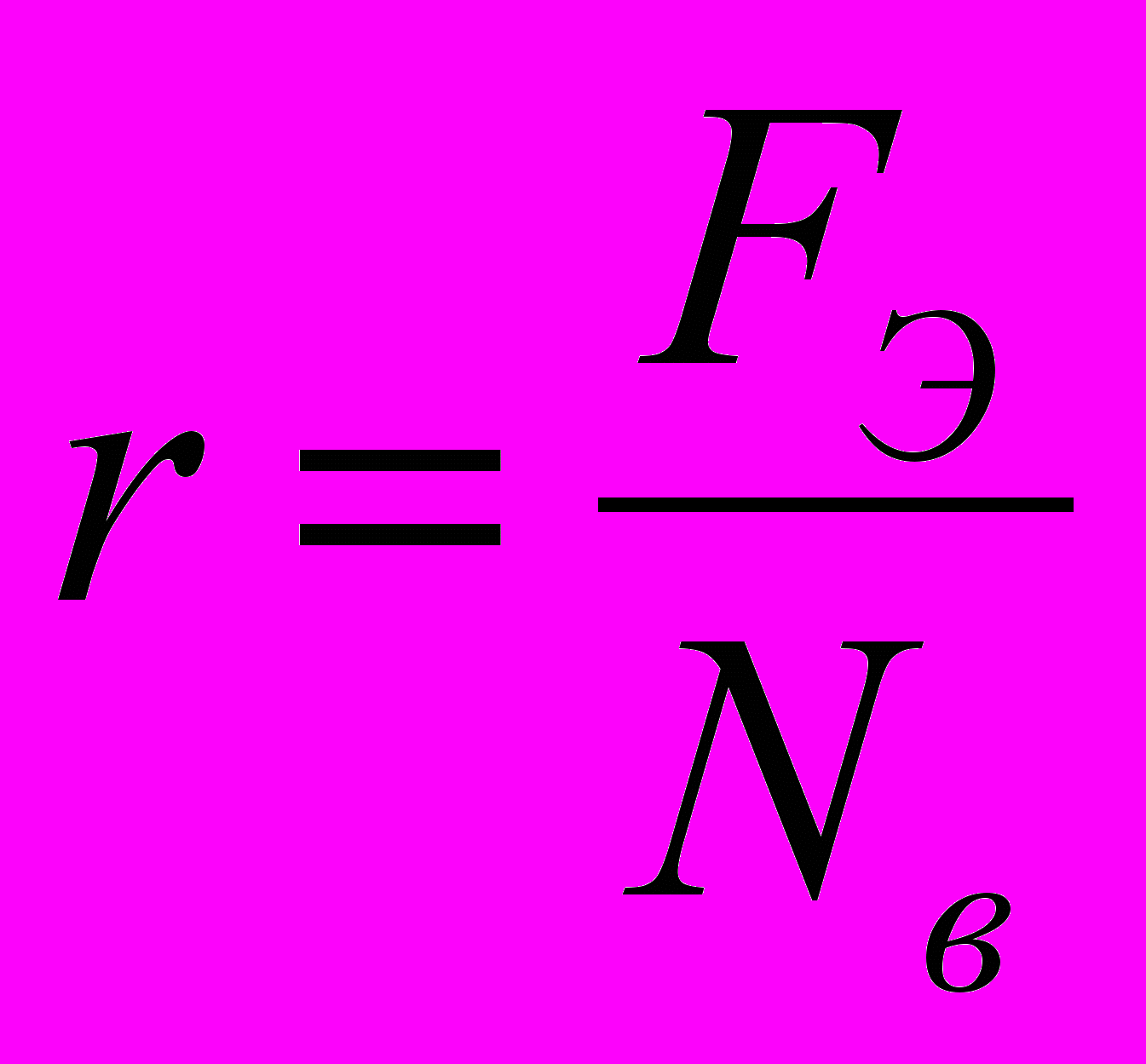
FЭ – эффективный фонд времени работы рборудования;
Nв – программа выпуска деталей.
Ритм запуска партий деталей
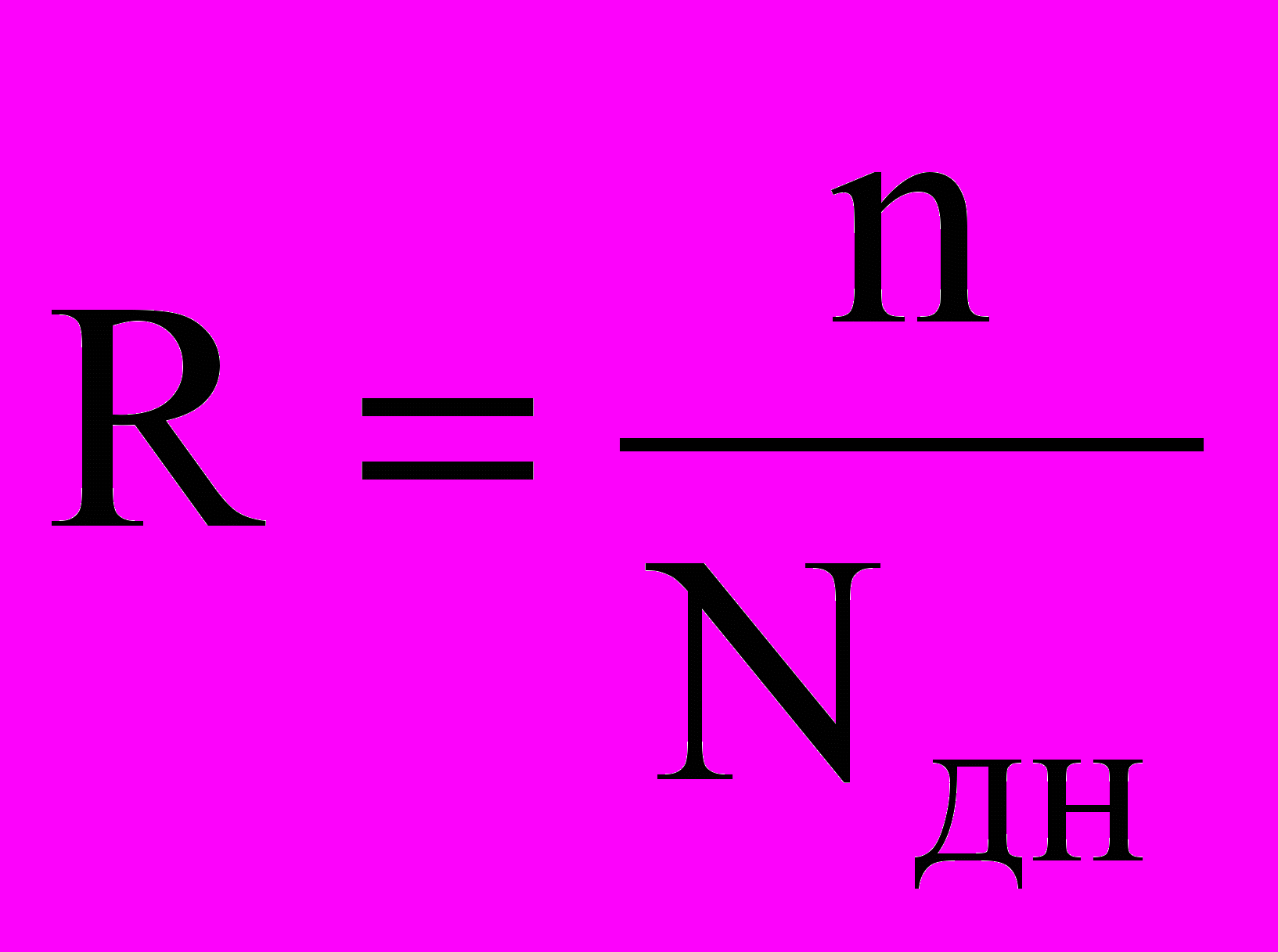
где:
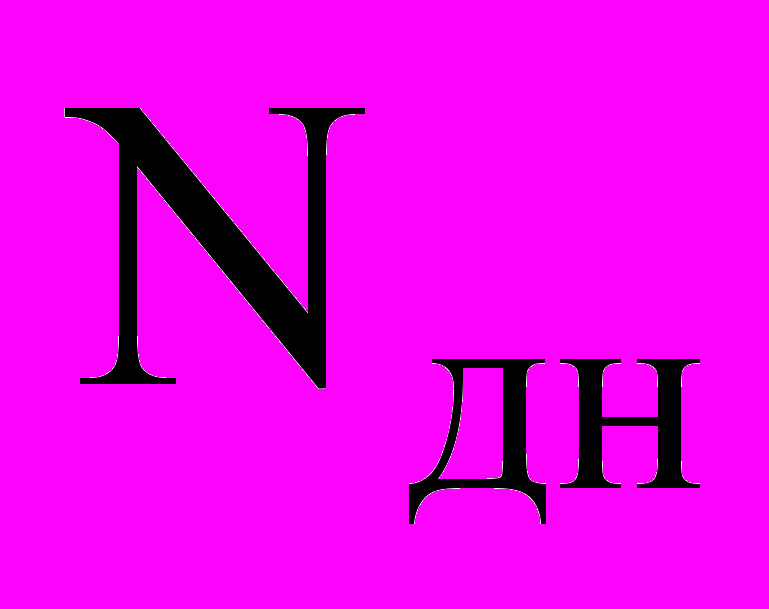
Для серийного производства среднесуточная потребность в деталях
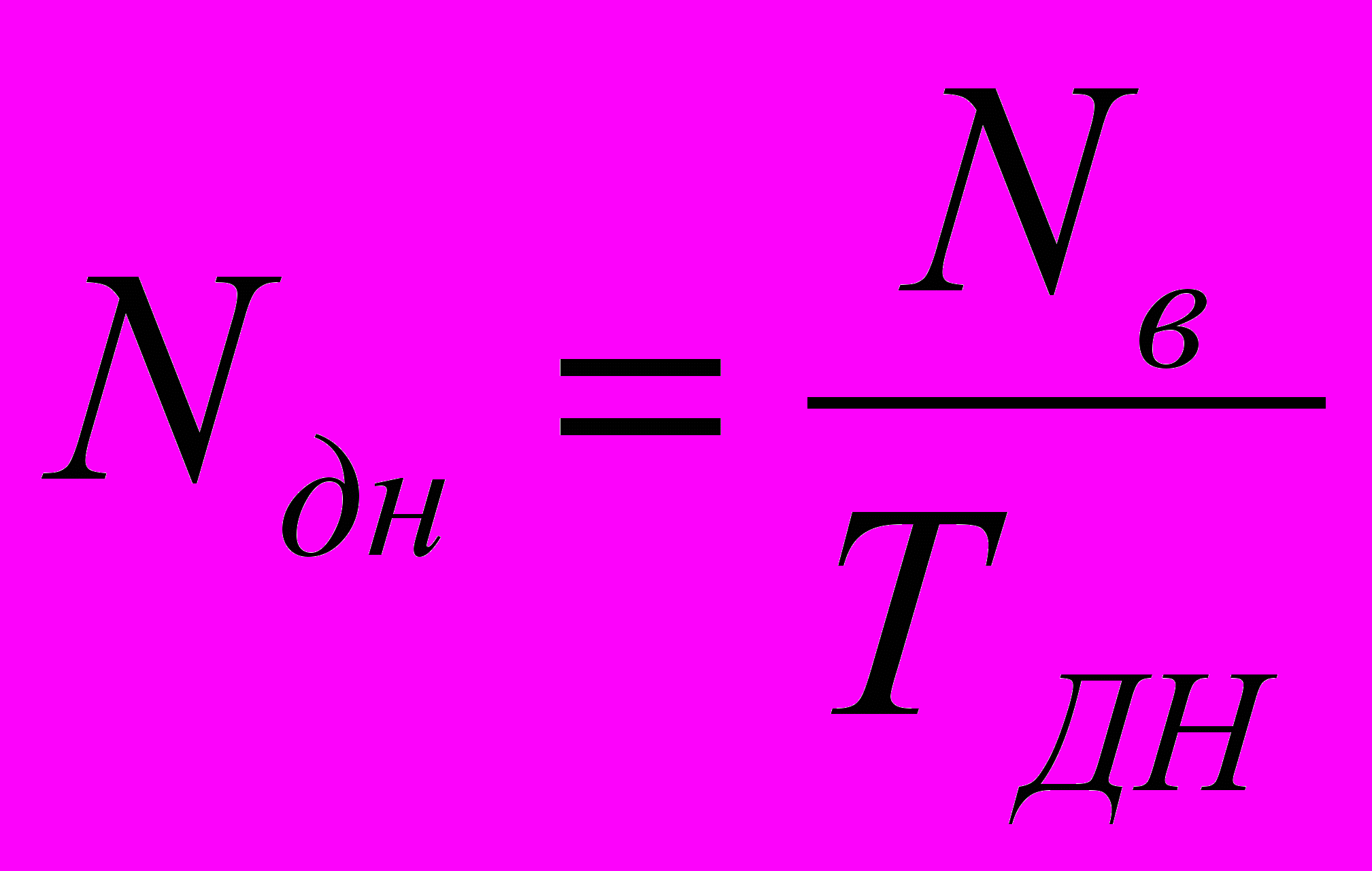
где TДН – количество рабочих дней в плановом периоде.
Определив размер партии деталей, мы получим ритм, т.к.
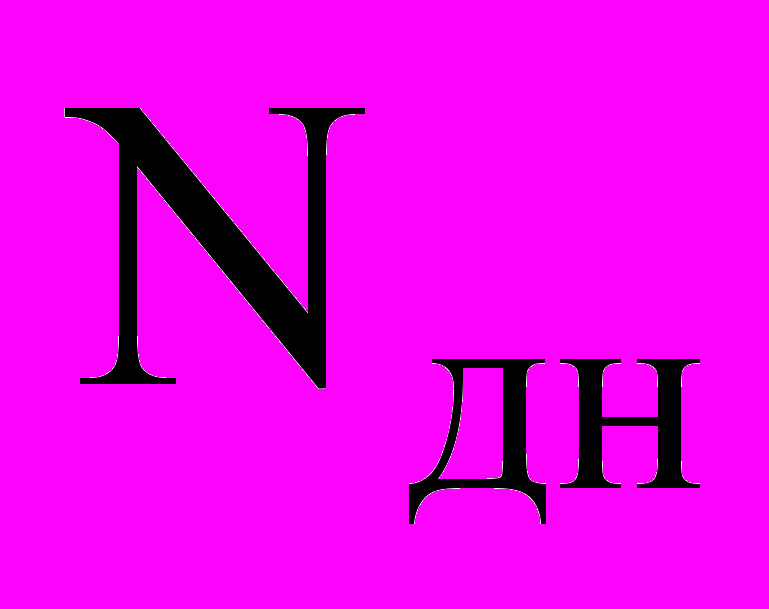
Размер партии деталей оказывает влияние на производительность труда рабочего, себестоимость обработки деталей, длительность производственного цикла и объем незавершенного производства.
Производительность труда с увеличением размера партии деталей расчет до определенного предела за счет приобретения рабочим навыков в выполнении движений и приемов. Фактическое штучное время уменьшается.
Себестоимость детали снижается при увеличении размера партии за счет уменьшения заработной платы рабочего и условно-постоянных расходов, приходящихся на одну деталь.
Зарплата уменьшается за счет снижения доли подготовительно-заключительного времени, приходящегося на одну деталь и сокращения фактического штучного времени обработки деталей. Условно-постоянные накладные расходы снижаются на единицу продукции за счет роста производительности труда и увеличения выпуска продукции.
Длительность производственного цикла и величина связывания средств в незавершенном производстве увеличивается с увеличением размера партии деталей.
Эти факторы учитываются определением оптимального размера партии деталей.
Затраты на обработку детали
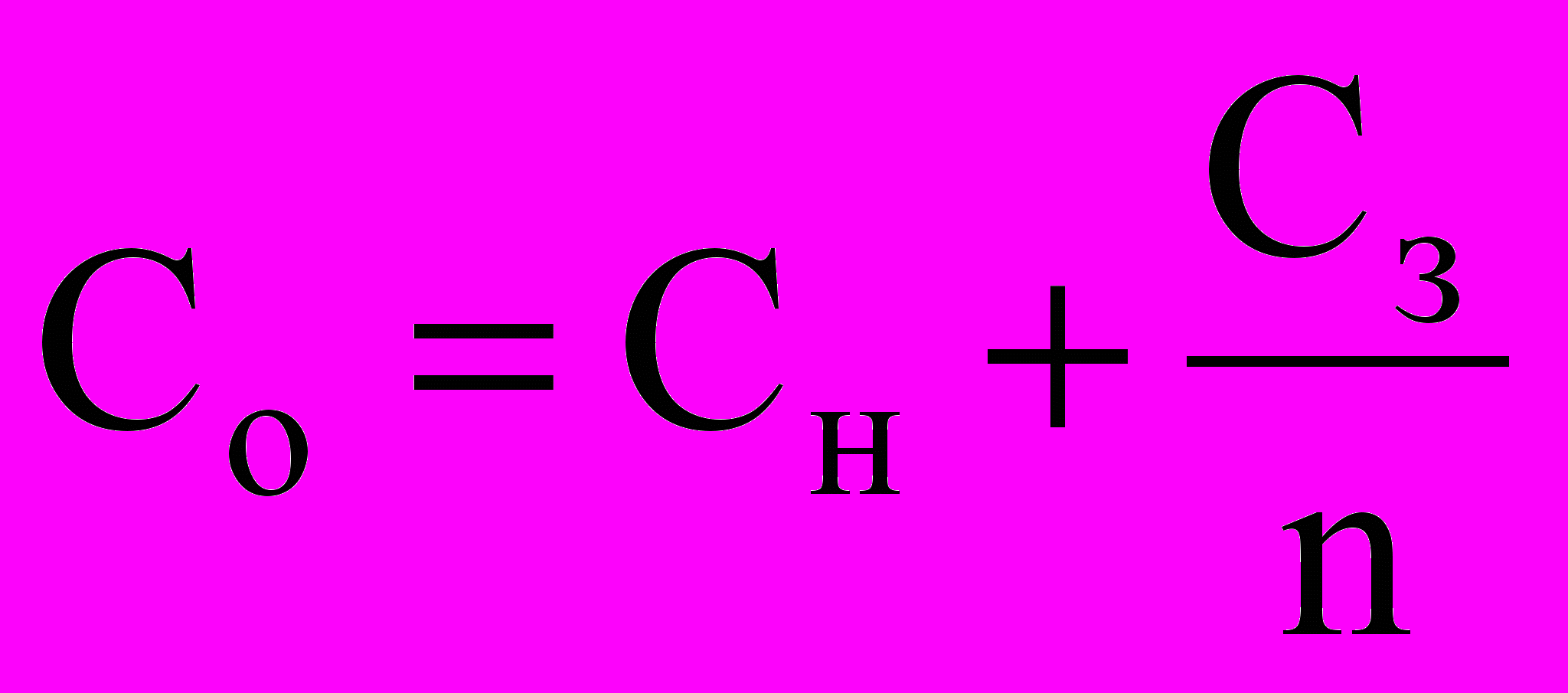
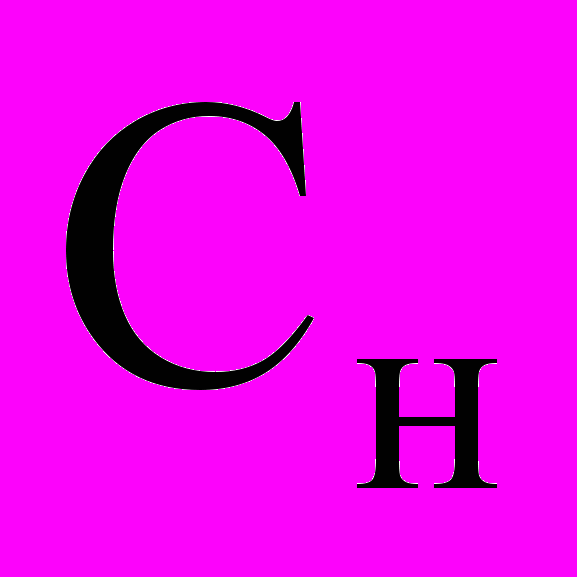
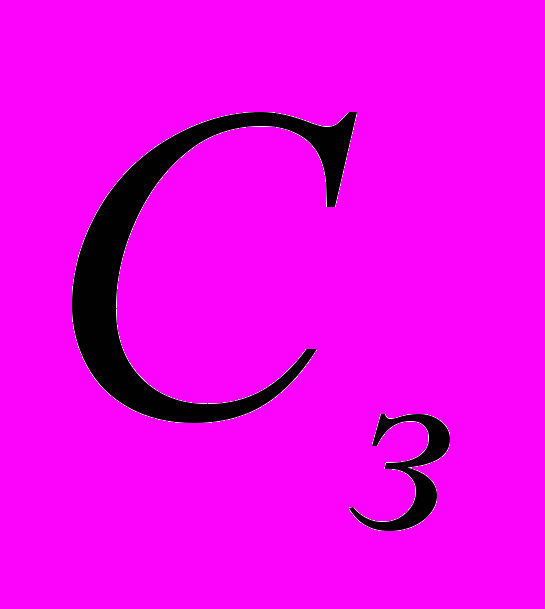
Размер средств, связанных в незавершенном производстве равен средней себестоимости одной детали, умноженной на длительность производственного цикла обработки партии деталей, и приближенно может быть посчитан.

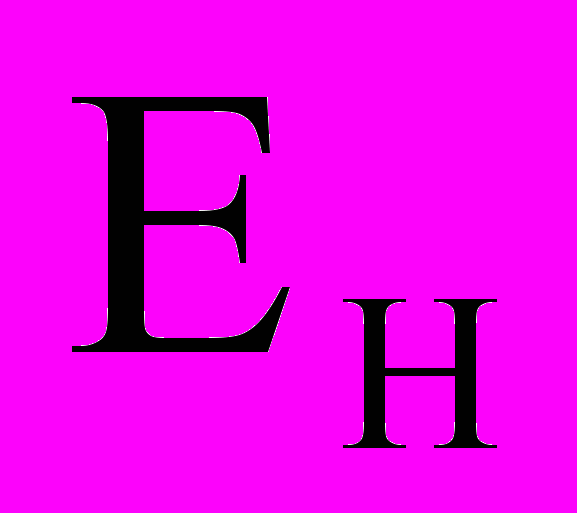
Приведенные затраты на обработку одной детали S.
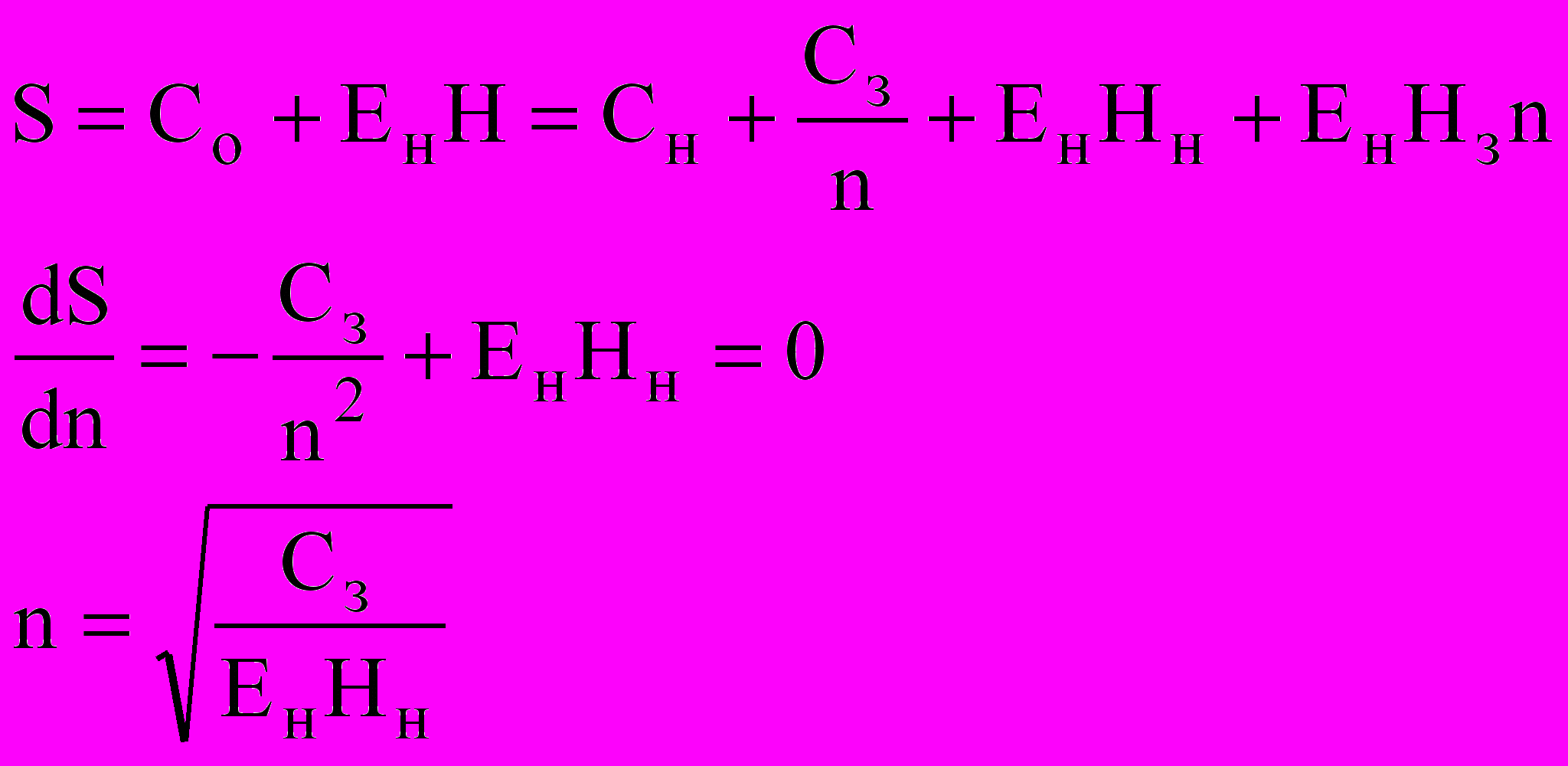
6.3.Упрощенные методы расчета размеров партии деталей
Первый метод: минимальный размер партии деталей устанавливается такой, чтобы доля подготовительно – заключительного времени tпз по отношению к штучному времени на всю партию деталей не превышала определенного процента.
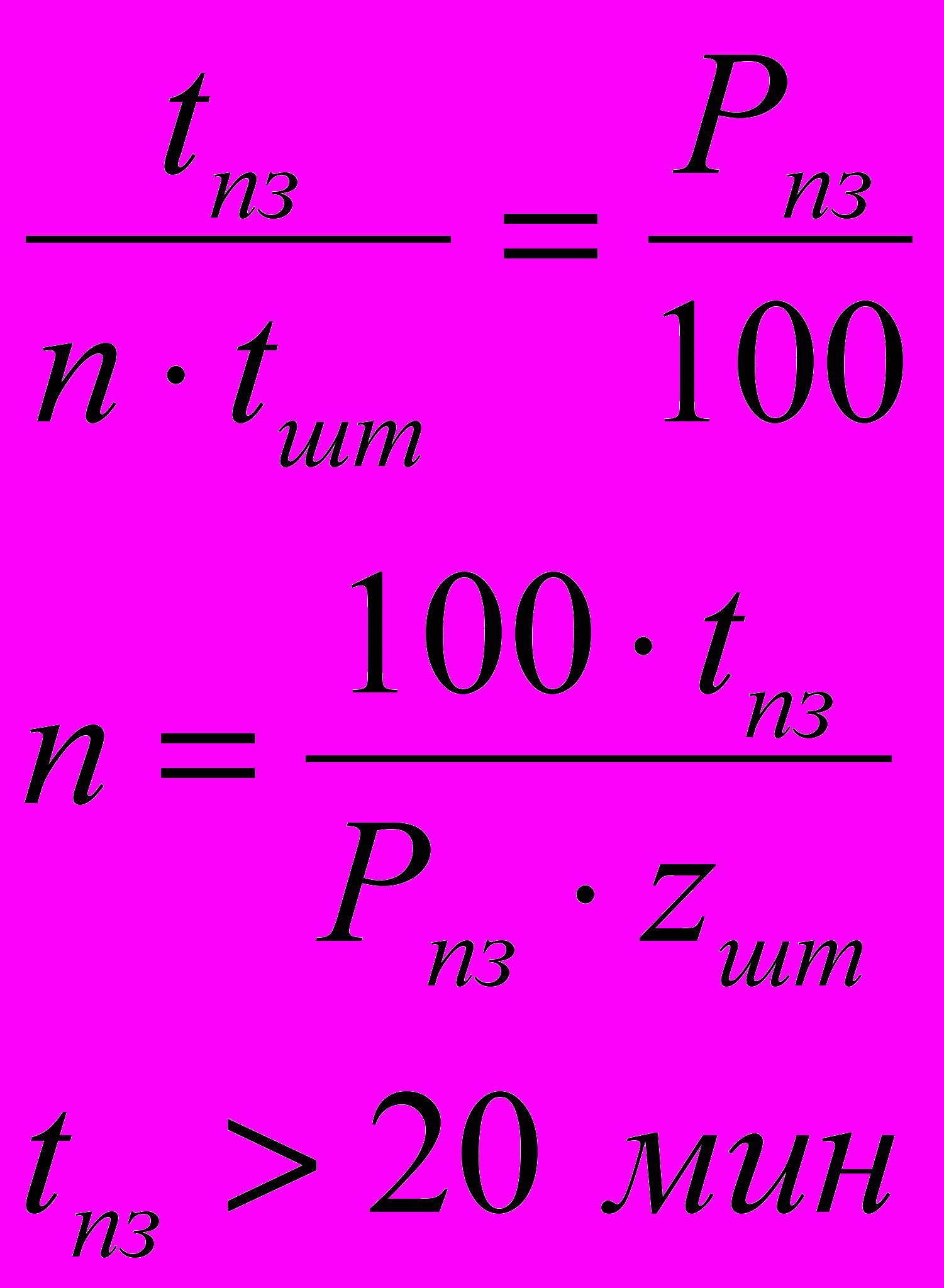
Используется, если на участке используется оборудование, требующее значительного времени на переналадку. Ведущей операцией, по которой производится расчет минимального размера партии, считают операцию с наибольшим отношением
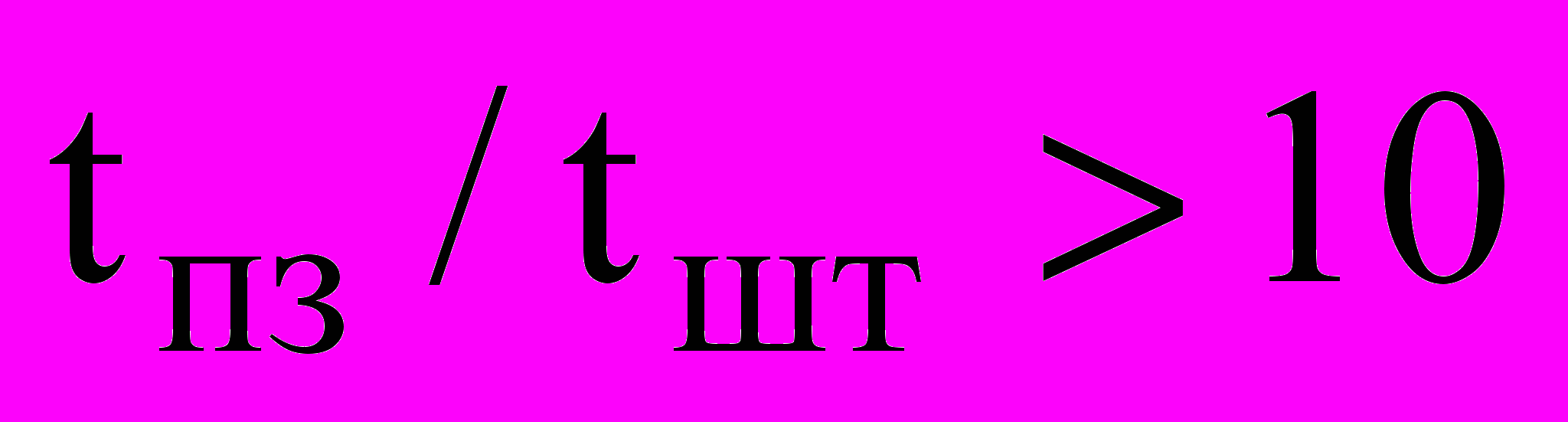
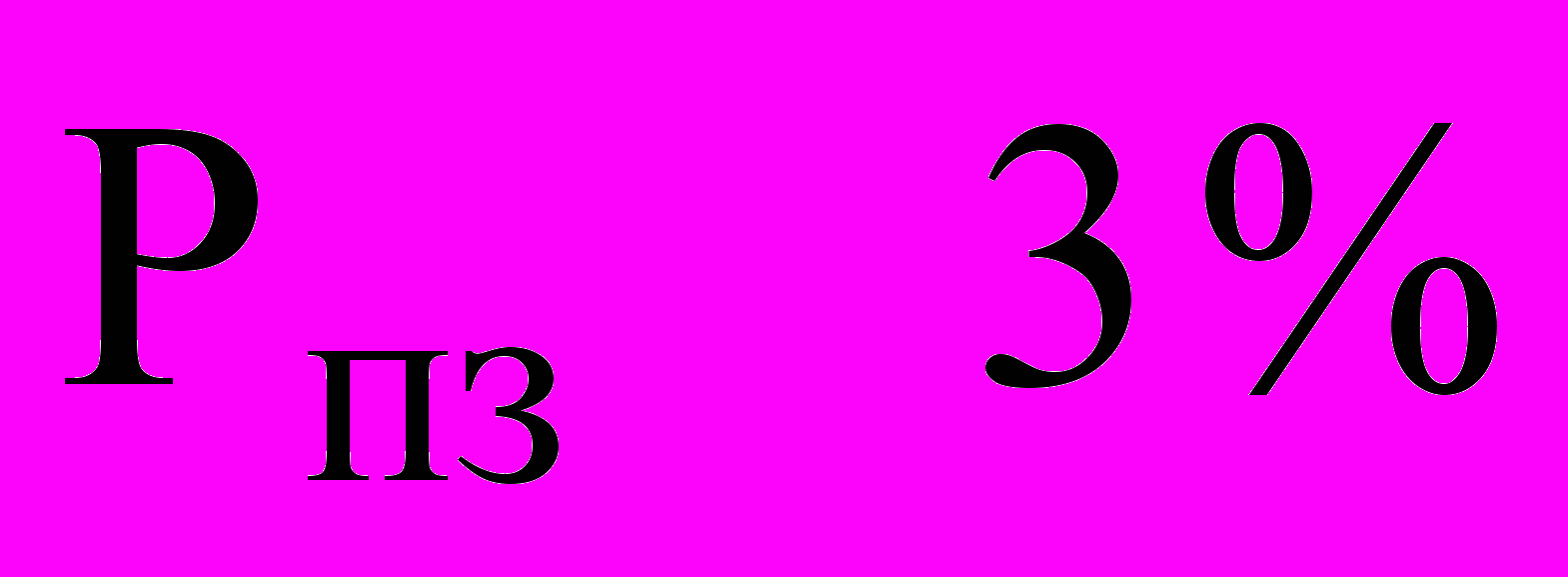
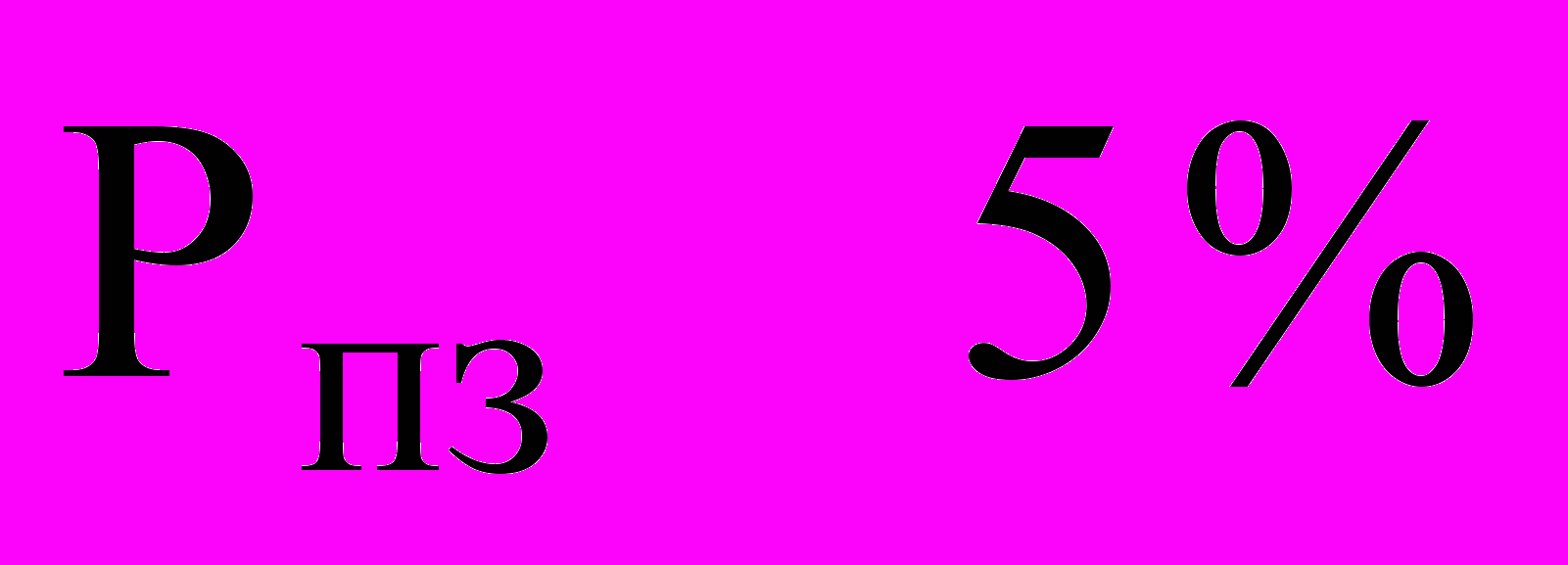
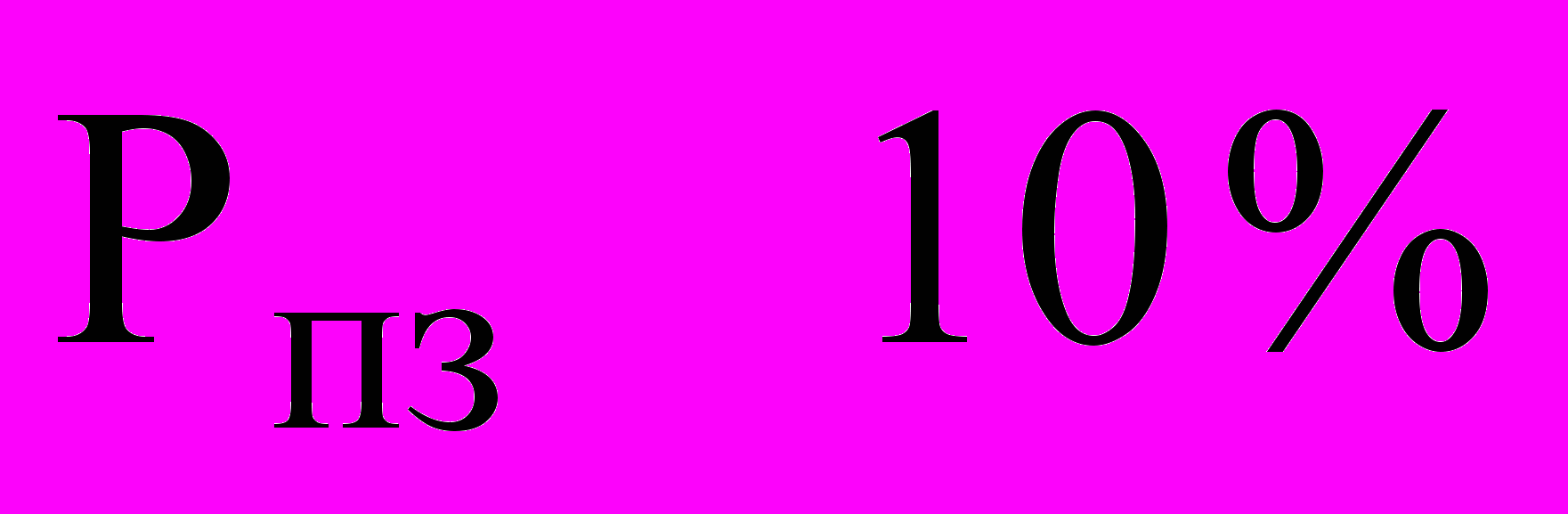
Расчет можно вести и по суммарному
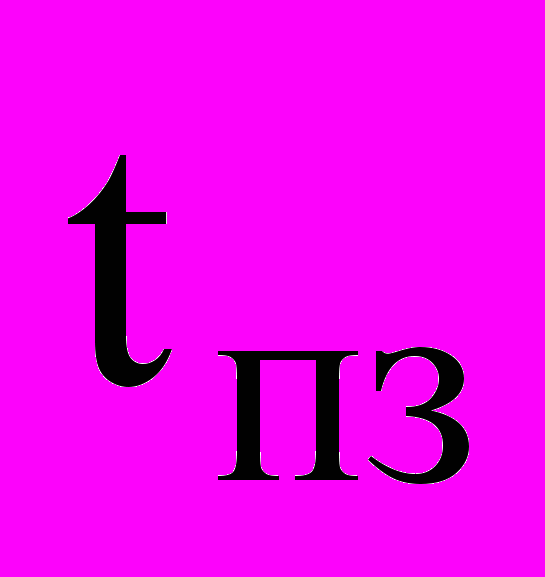
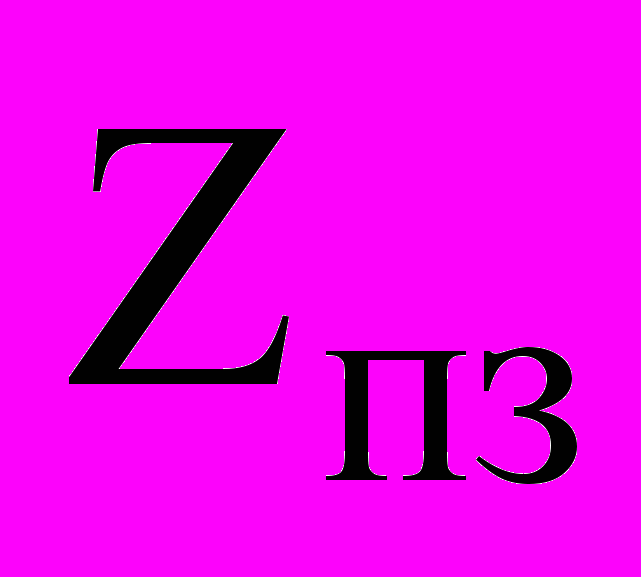
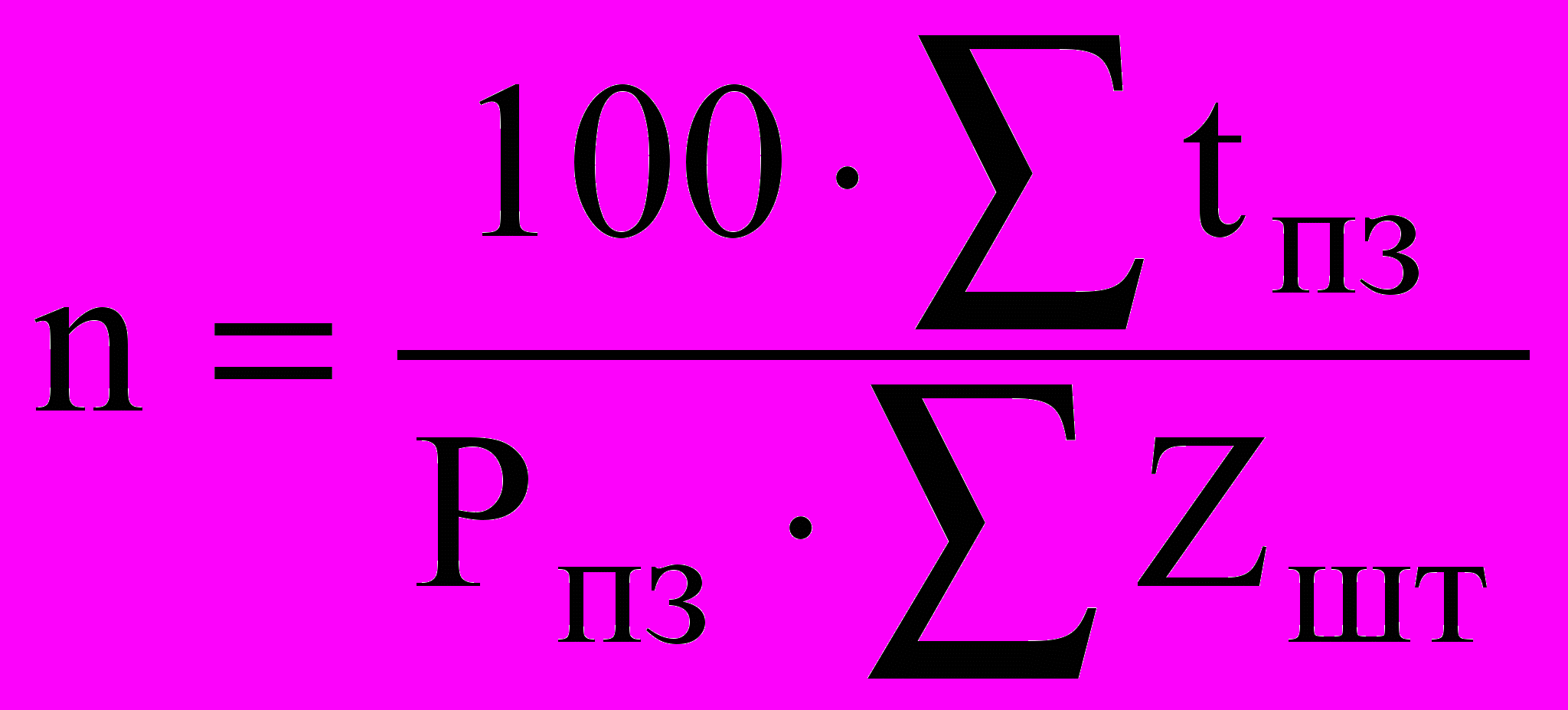
Второй метод: Размер партии деталей определяется из условия, что время обработки одной партии на любом рабочем месте не должно быть меньше смены или полу смены.
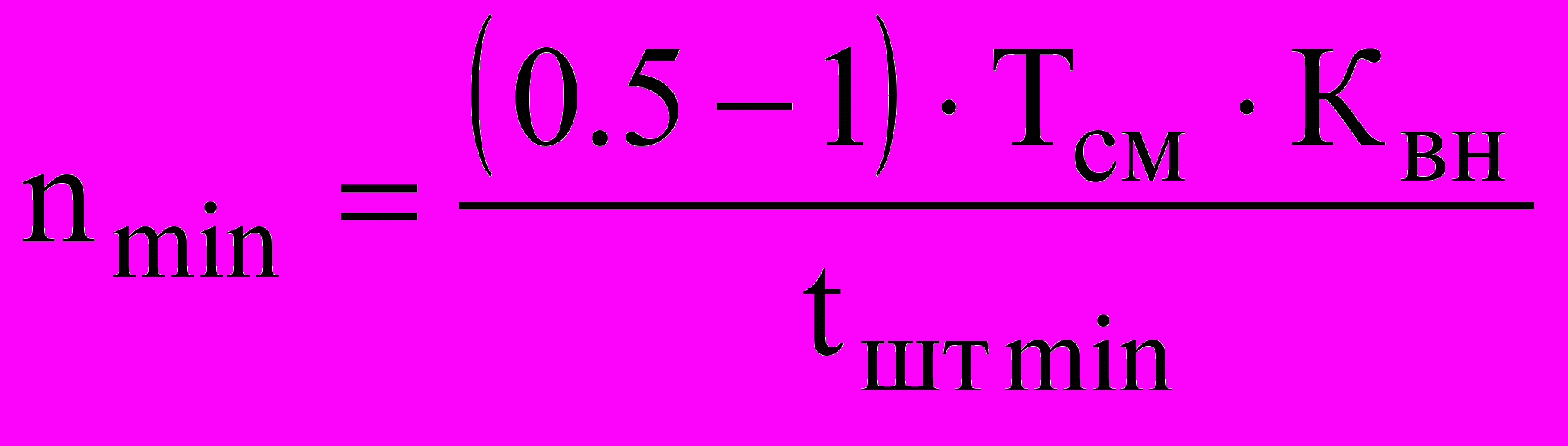
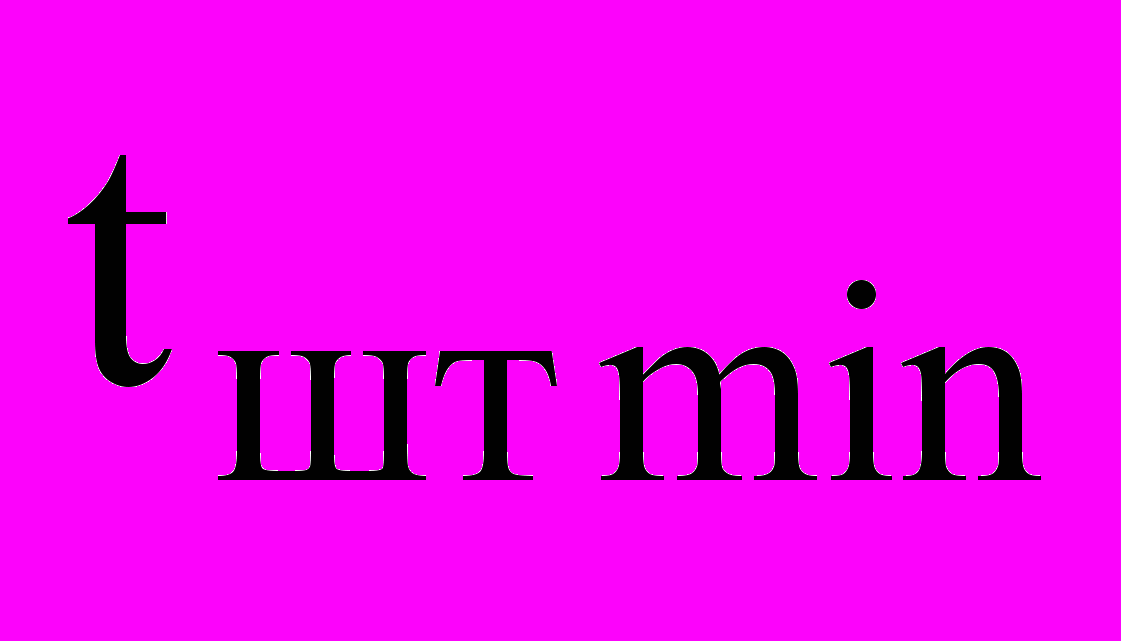
При определении размера партии по этому методу учитывается один фактор – производительности труда.
Метод используется если
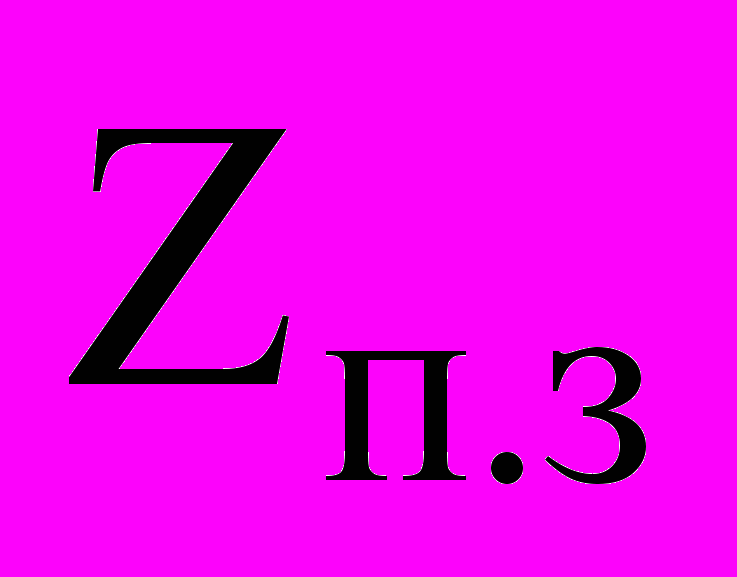
Корректировка размера партии деталей проводится с учетом требований.
Размер партии деталей должен согласоваться с размерами партии других деталей, т.е средняя продолжительность операций должна соответствовать
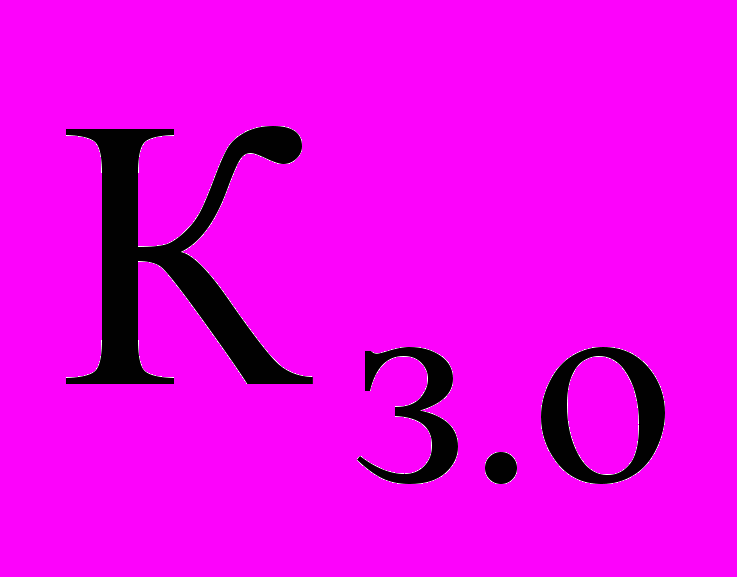
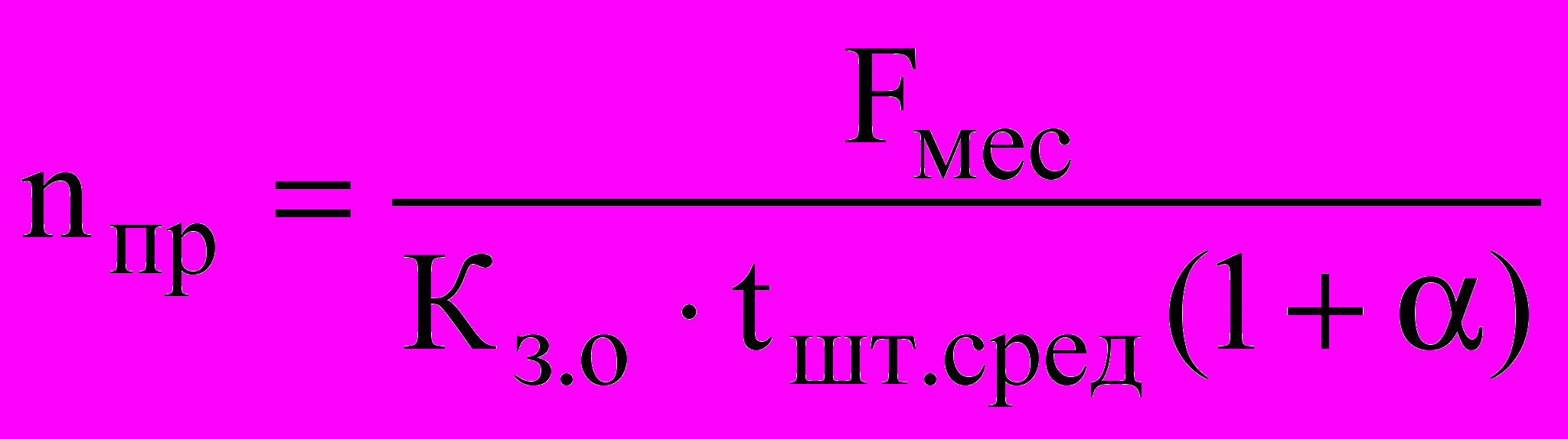
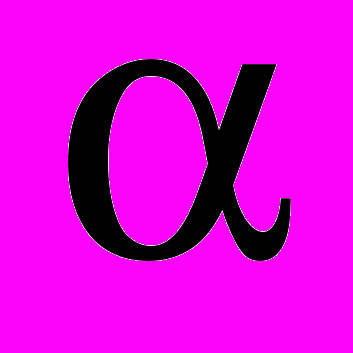
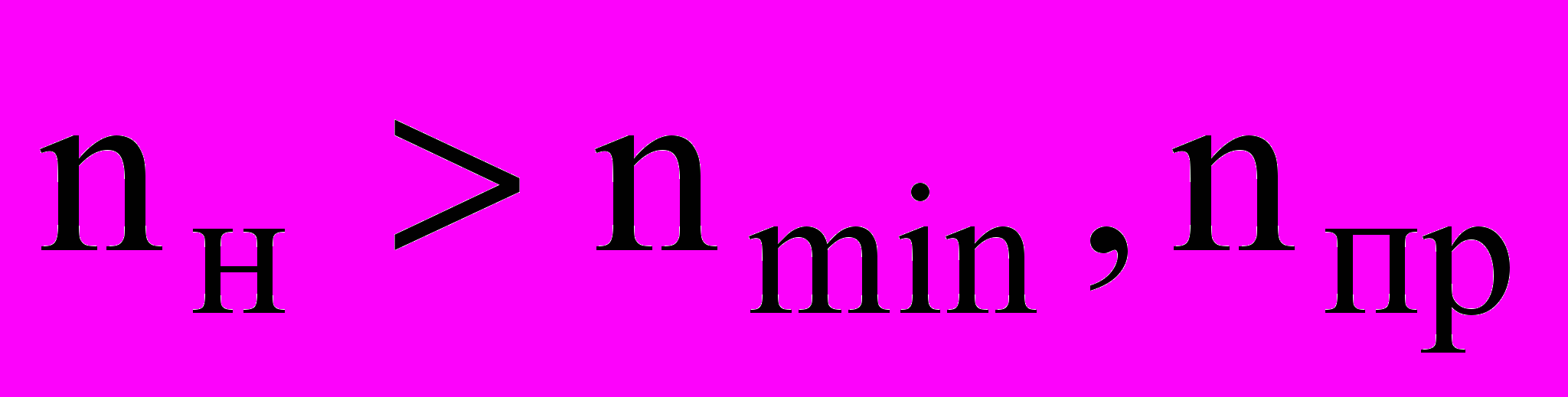
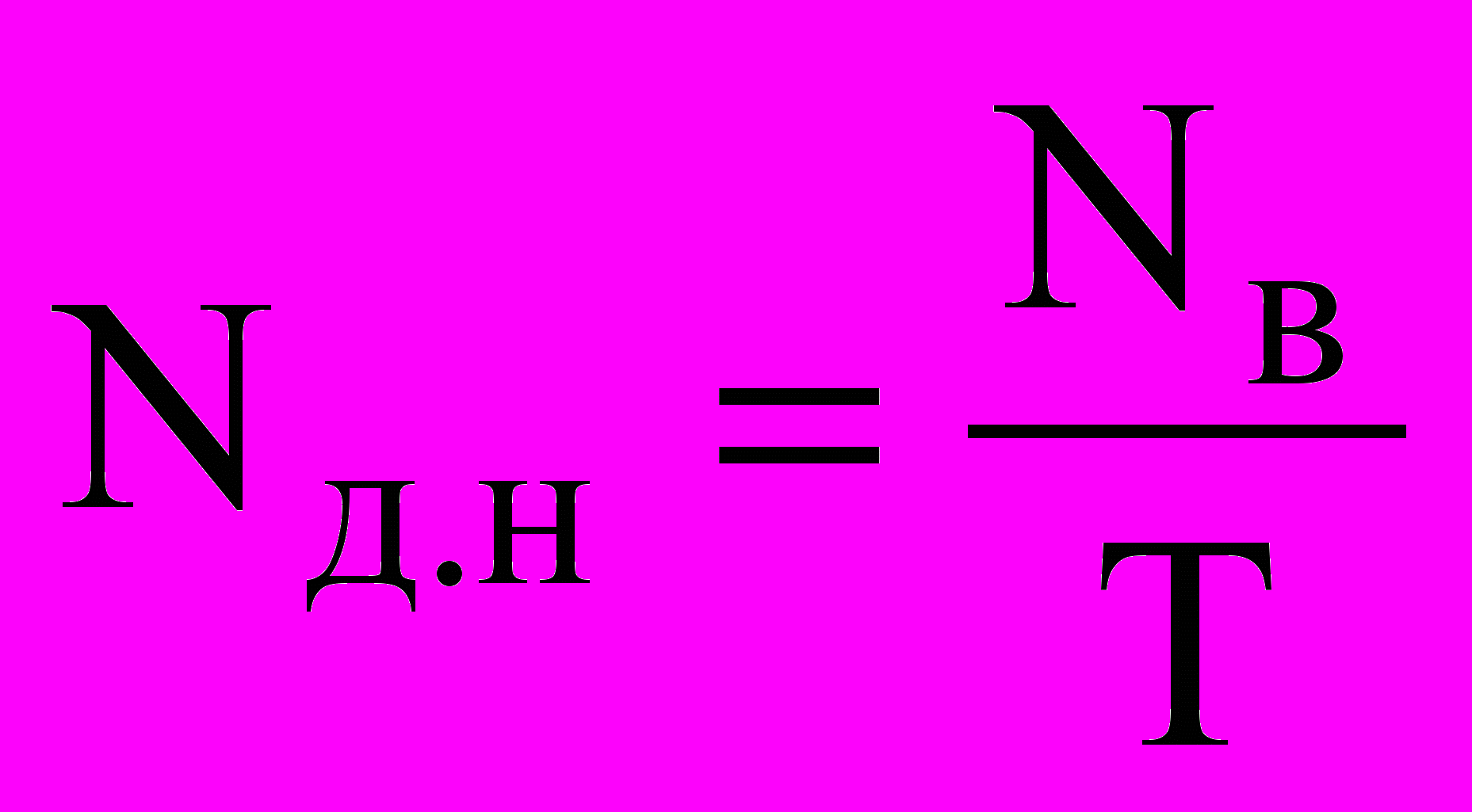
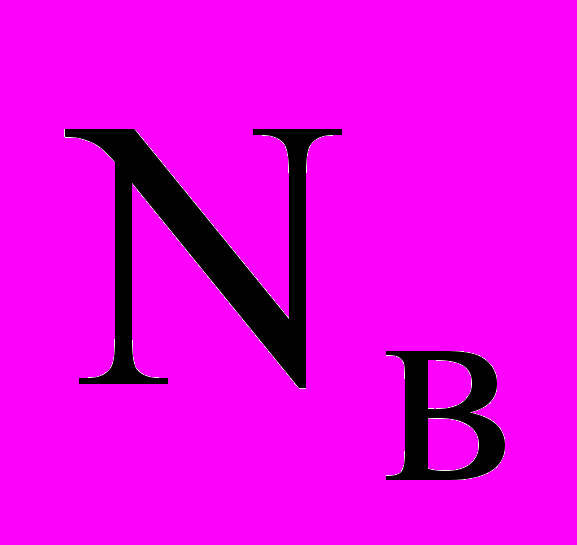
Т – продолжительность выпуска в сутки.
Размер партии деталей должен укладываться целое число раз в месячную программу по данной детали.
Периодичность запуска должна быть удобна для планирования.
Периодичность запуска:
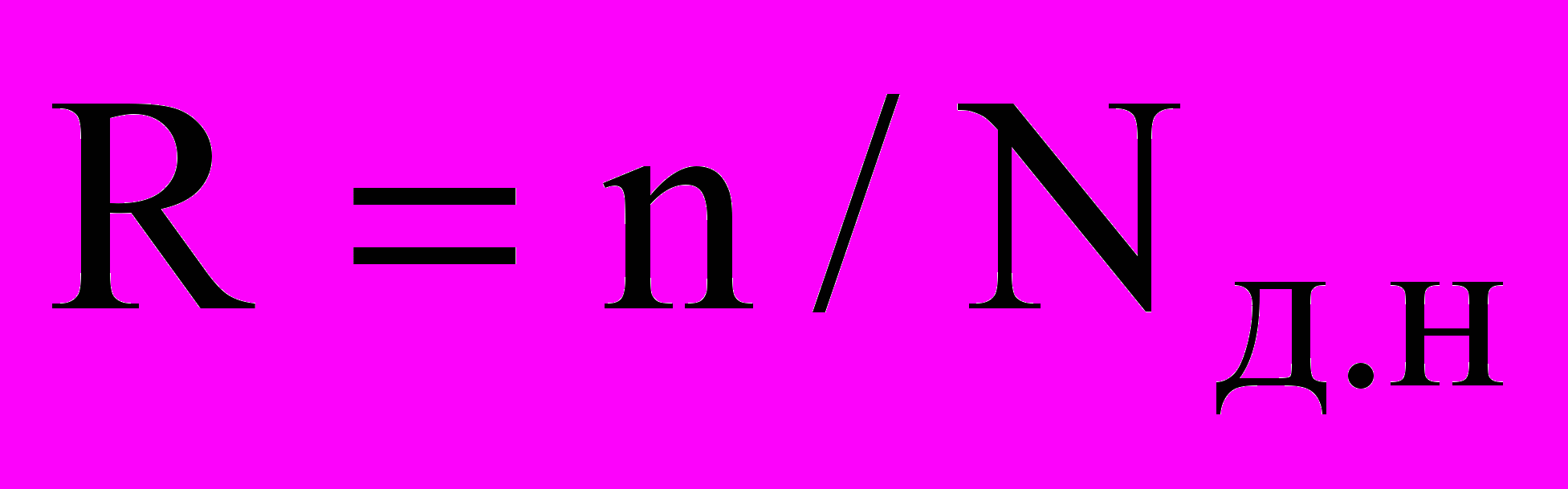
n – размер партии.
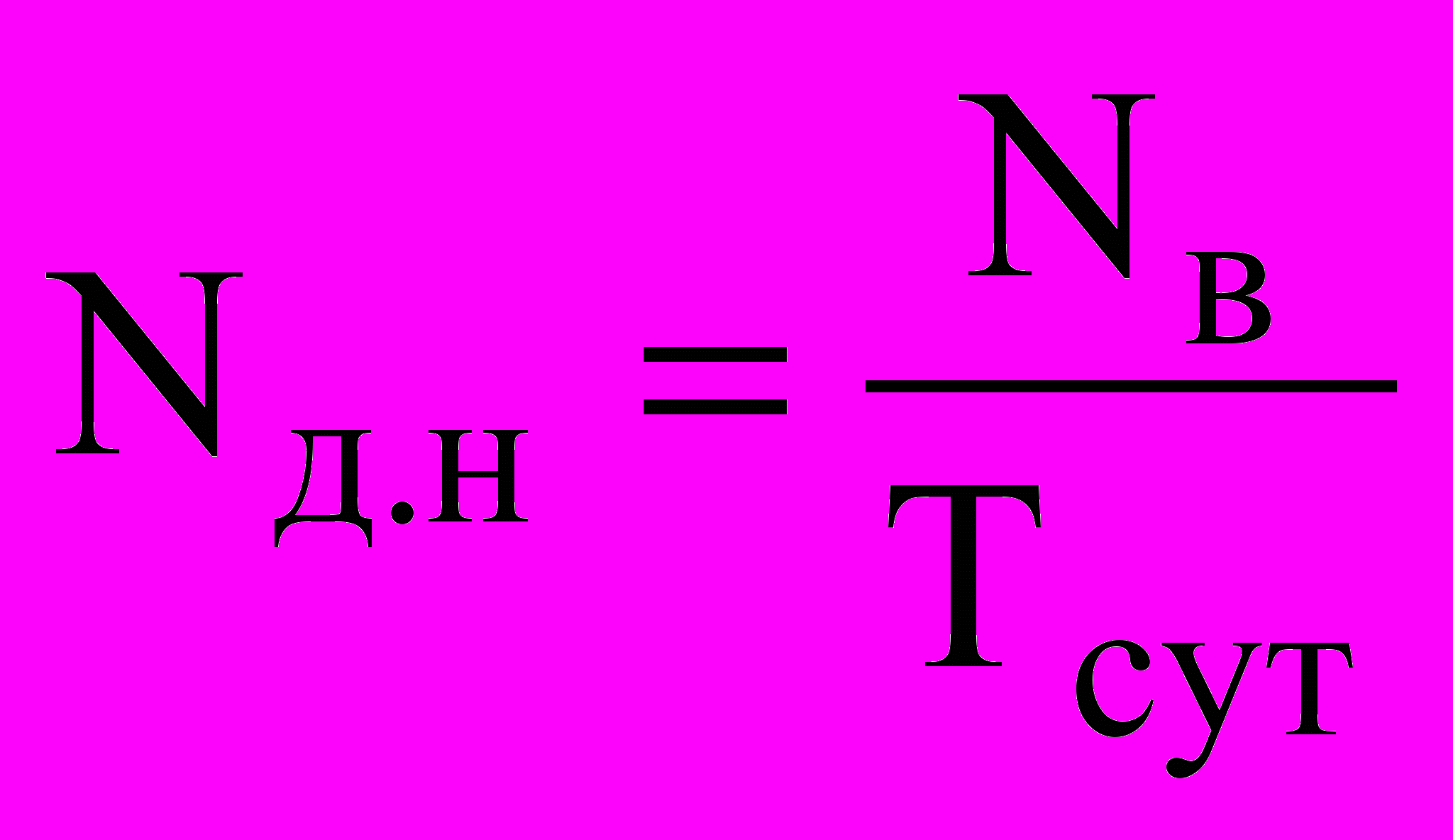
За основу унификации периодичности запуска партии деталей принимается часто однодневная потребность.
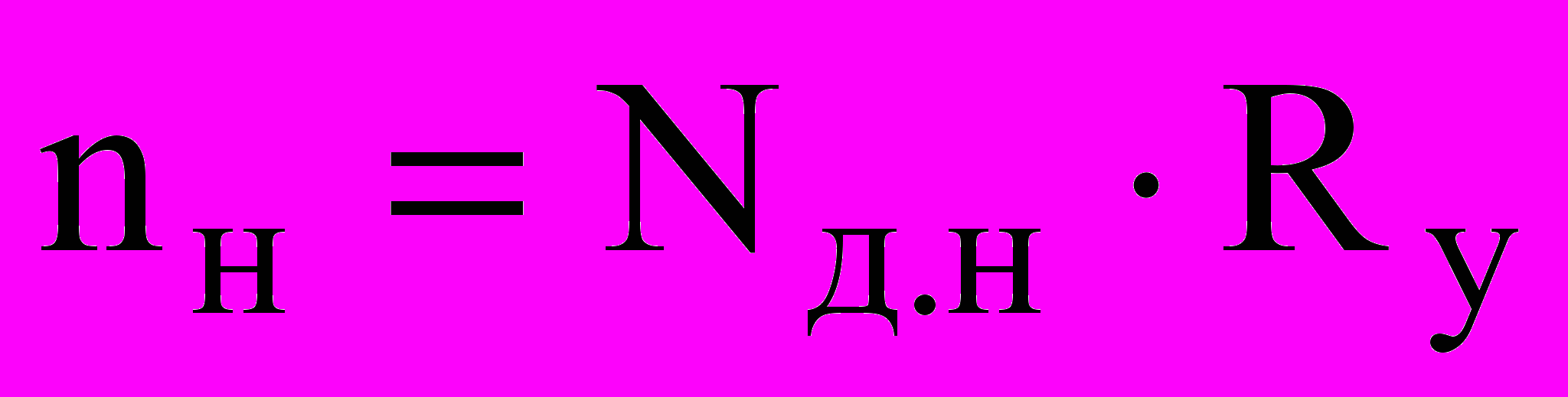
При выборе нормативного размера руководствуются рядом унифицированных периодичностей.
Нормативный размер партии нужен для решения следующих задач:
Регламентации периодичности переналадок оборудования и изготовления одноименных деталей.
Определения нормативных длительностей производственных циклов и календарных опережении.
Построение календарных планов, определяющих сроки запуска, выпуска деталей и комплектования для сборки.
Установления нормативного среднего уровня незавершенного производства и величины переходящих заделов на конец планового периода.
Ряд унифицированных периодичностей запуска деталей в производство.
Периодичность запуска.
Размер нормативных партий.
1 2 3 4 22/5 22/4 22/3 11 22 33 44 66 88
132 264
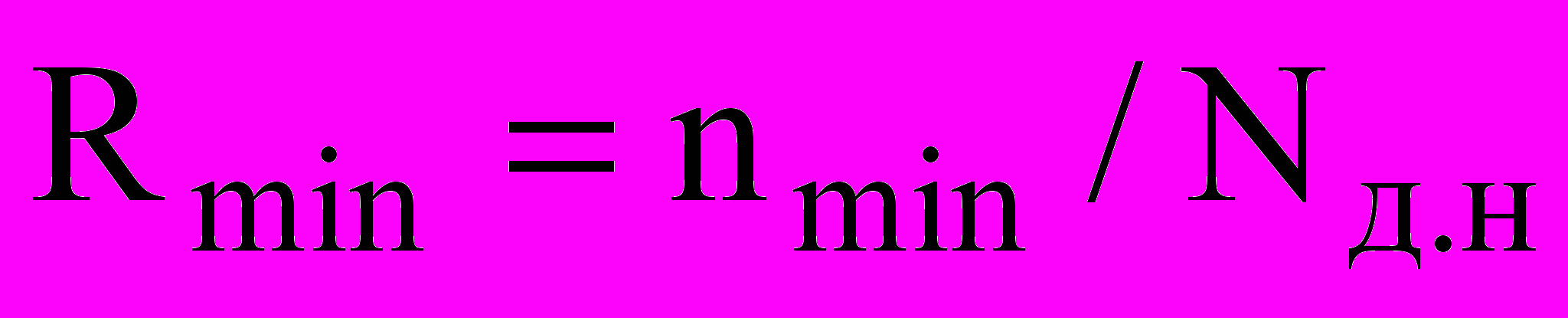
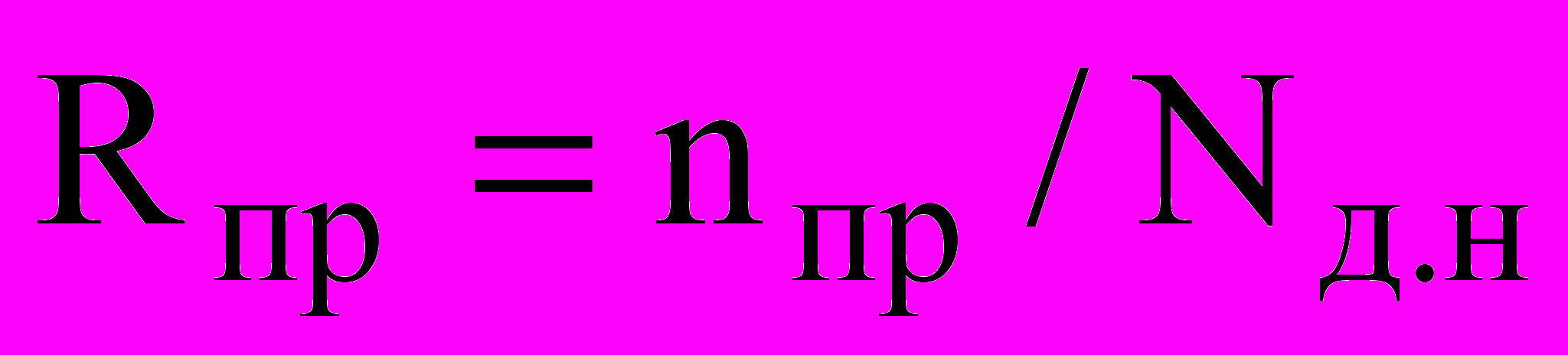
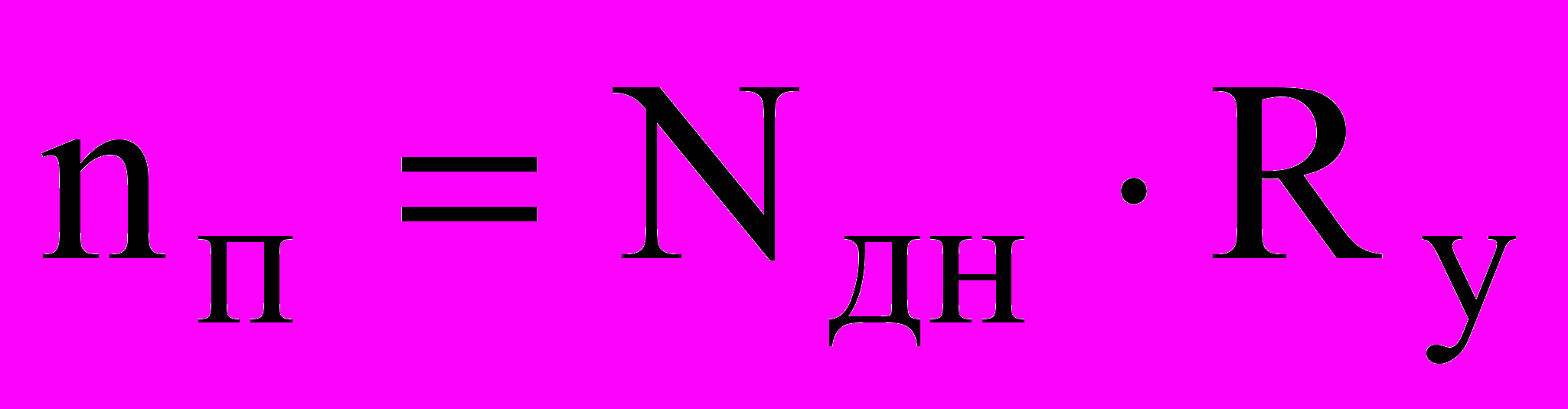
6.4.Диспетчирование производства
Диспетчерирование предназначается для централизованного контроля за ходом основного производства и его регулирования; оно призвано обеспечить выполнение плана при равномерной, ритмичной работе всех производственных звеньев.
Особенности организации диспетчерской службы во многом определяются производственной структурой предприятия и типом производства. Так, в условиях опытного производства оперативный контроль выполнения работ осуществляется по ленточным или сетевым графикам. В последнем случае устанавливается степень отставания или опережения фактических сроков выполнения работ от ранних сроков их начала. В единичном и мелкосерийном производствах необходим строжайший контроль за сроками выполнения заказов, своевременным их комплектованием необходимыми деталями, согласованием процесса производства с технической подготовкой заказа. В серийном и массовом производствах повышается уровень централизации диспетчерской работы, создается более разветвленная структура диспетчерской службы. В серийном производстве контролируется запланированный ритмичный выпуск изделий по графику, запуск и выпуск комплектов деталей соответственно комплектовочным номерам машин, нормативный уровень заделов. В массовом производстве диспетчерская служба обеспечивает заданный ритм производства, контролирует ритмичный выпуск изделий, регулирует уровень заделов.
Диспетчерская работа на предприятии возглавляется главным диспетчером, который имеет в своем подчинении группы сменных и ведущих диспетчеров. Ведущие диспетчеры контролируют ход производства закрепленных за ними конкретных заказов или изделий. Сменные диспетчеры осуществляют текущее регулирование производства, анализируют причины отставания, разрабатывают мероприятия по ликвидации этих отставании, обеспечивают производство необходимым материалом, заготовками и инструментом.
В состав ПДБ цеха входят сменные и старшие диспетчеры. Согласно сменно-суточному заданию они подготавливают все необходимое для осуществления производственного процесса на закрепленных за ними участках. Сменные диспетчеры ведут текущее регулирование производства: контролируют прохождение деталей, лимитирующих выполнение плана на текущие сутки, наблюдают за «узкими» местами производства и т. п.
Контроль исполнения решений по межцеховым и внутрицеховым претензиям, приказов руководства, решений диспетчерских совещаний, срок выполнения которых более двух суток с момента поступления на диспетчерский пункт, должен осуществляться с помощью картотек контроля. При сроке исполнения менее двух суток — с помощью диспетчерских журналов. Помимо этого в любом журнале (заводском или цеховом) оформляется сдача-приемка смен сменными диспетчерами. Диспетчерский журнал оформляется в виде общей тетради с пронумерованными страницами. В нем указываются дата, смена, содержание претензий, кем дано распоряжение (принято решение), кому дано распоряжение (исполнитель), содержание распоряжения, срок исполнения, делается отметка о выполнении.
Структурная схема, организации диспетчирования на предприятиях массового производства представлена на рис.
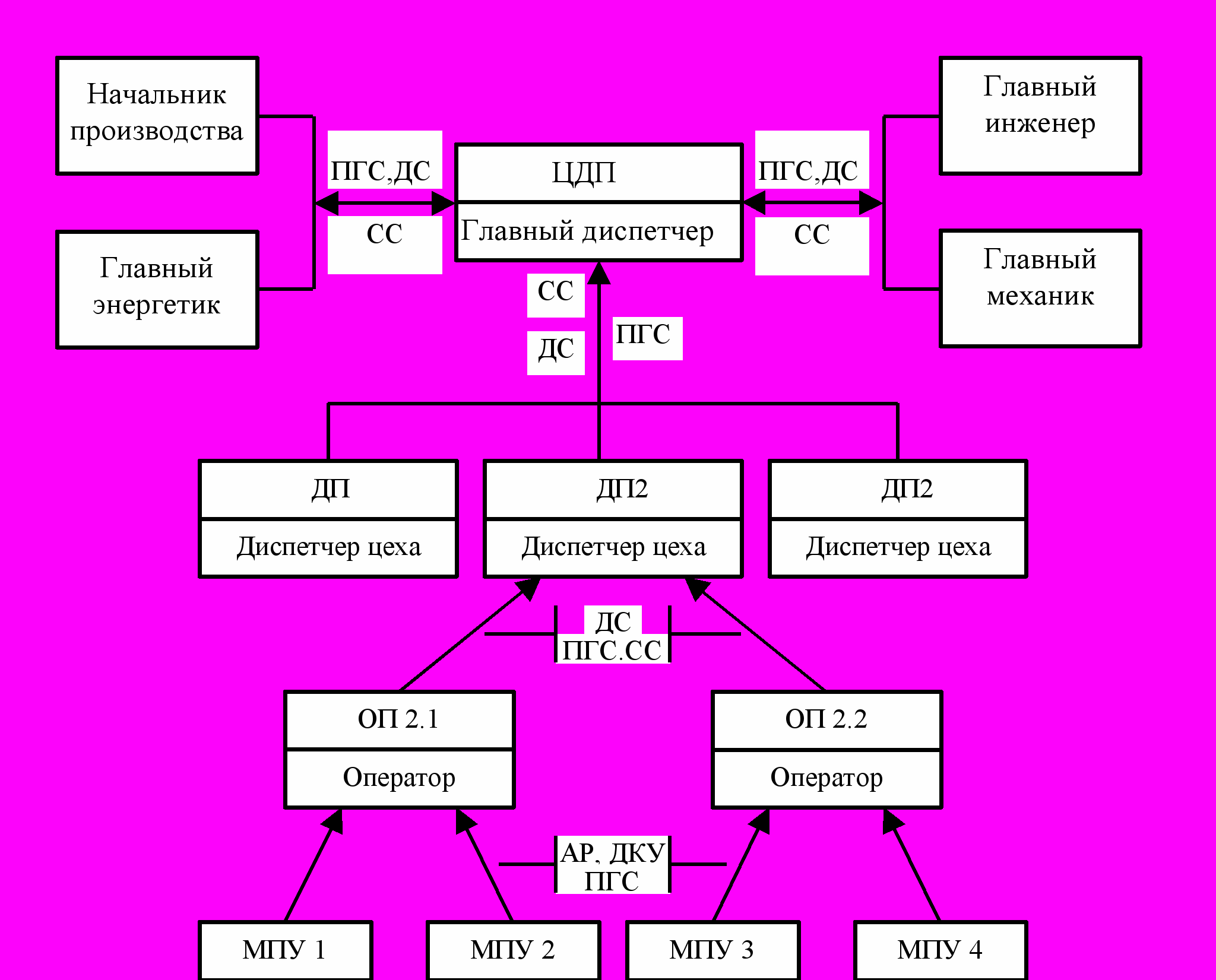
Местные посты управления (МПУ) предназначаются для управления отдельными механизмами и технологическими агрегатами. Щиты МПУ оборудуются средствами автоматического контроля, регулирования, управления и сигнализации. Обслуживаются МПУ мастерами, бригадирами или аппаратчиками, которые сигнализируют о неисправностях механизма и отклонениях в выпуске продукции. Операторские пункты (ОП) представляют собой нижнюю ступень системы сбора, передачи производственно-технологической информации и управления объектом. Операторские пункты обычно создаются на участках, станочных линиях и призваны обеспечить поддержание стабильного технологического процесса и ритмичную работу оборудования. Они оснащаются средствами контроля и автоматического регулирования, аппаратурой дистанционного управления, сигнализацией и средствами связи. Операторы, занятые на ОП, входят в штат участников и административно подчинены диспетчеру цеха. В функции оператора входит подготовка по документированным данным машинных носителей, установление через абонентский пункт связи с ЭВМ и передача информации.
Сменные операторы поддерживают связь с диспетчером 1 цеха, информируя его обо всех нарушениях и изменениях в технологическом процессе и принятых мерах по их устранению. В некоторых случаях функции оператора выполняются сменными мастерами или бригадирами. Диспетчерские пункты (ДП) представляют собой основное место сбора производственно-статистической информации, необходимой для определения технико-экономических показателей процесса. Основной задачей управления на этом уровне является распределение и координация информационных потоков цеха. В ДП устанавливаются щиты с мнемосхемами объектов производства, приборные щиты, средства передачи информации и связи. Основанием для контроля за ходом производства служат нормативные графики работы» Работа в ДП выполняется диспетчером цеха, который административно подчинен начальнику цеха, а методологически — диспетчеру завода. Сменные диспетчеры следят за выполнением сменных заданий, осуществляют координацию работ участков цеха. Центральный диспетчерский пункт (ЦДП) осуществляет непрерывный контроль за ходом выполнения сменных и суточных плановых заданий цехами и предприятием в целом, выявляет отклонения от запланированного хода производства, систематизирует отчетную информацию о выполнении плановых заданий и состоянии оборудования, организует межцеховые грузопотоки, запасы сырья и материалов. Руководство ЦДП осуществляется главным диспетчером завода и штатом сменных диспетчеров.