Автоматизация технологической подготовки производства для малых инновационных предприятий в машиностроении
Вид материала | Автореферат |
СодержаниеЧетвертая глава P включает 11 основных компонентов: P = P имеет множество значений, например описание формы пластины Pf Сi может быть поставлено в соответствие нечеткое множество A |
- Учебный план по дополнительной образовательной программе, 38.01kb.
- Методические указания по выполнению дипломных проектов для студентов специальности, 294.98kb.
- Управление венчурным инвестированием малых инновационных предприятий в российских условиях, 342.92kb.
- Семинар Проблемы и перспективы подготовки кадров для высокотехнологичного бизнеса,, 55.18kb.
- Рабочая программа по предмету «Автоматизация производства» Для профессиональной подготовки, 111.79kb.
- Концепция подготовки и проведения VIII всероссийской конференции представителей малых, 265.43kb.
- План введение критерии отнесения предприятия к категории малых предприятий правовые, 364.08kb.
- Вопросы для подготовки к экзамену по Основам технологии получения заготовок деталей, 36.75kb.
- Конкурс инновационных проектов "У. М. Н. И. К.", 185.73kb.
- Автоматизация документального и информационного обеспечения малых предприятий с применением, 297.24kb.
Таким образом, в соответствии с разделом "Система продукций" в табл. 1, для каждой вершины графа декомпозиции Q1…Qn имеем систему правил, которую в общем виде можно представить в виде множества:
R = {R1, R2,…,Rm} . (6)
В этой системе правил
Ri: если х1 есть Аi1 и х2 есть Аi2 и … и хn есть Аin , то y есть bi ,(i = 1,…,m), (7)
где х1, х2,…, хn - входные параметры нечеткой модели;
y - выходной параметр;
bi - значения выходного параметра;
Аij - нечеткие множества для задания значений входных параметров;
i = 1,…,m; j = 1,…,n.
В соответствии с табл. 1, x1 = "L", x2 = "Otn", у = Q13, b1 = "Цилиндрическая ступень", b2 = "Канавка прямая" множествами Аij являются множества, определенные термами "Незначительная", "Много меньше", "Значительная", "Соизмеримое".
Для каждого j множества Аij имеют единую область определения (т.к. формализуют термы одной и той же лингвистической переменной, связанной с параметром хj).
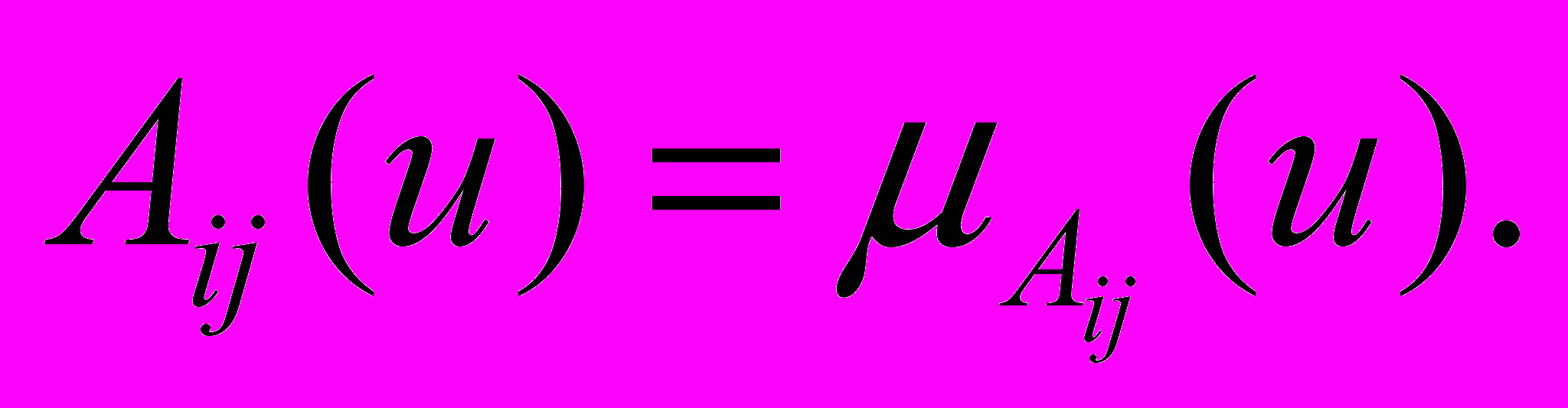
(8)
Пусть Uj - область определения множеств Аij, обозначим
Для принятия решений был разработан алгоритм приближенных рассуждений. Пусть имеется набор конкретных значений входных параметров (u1*, u2*,…, un*), где uj* Uj (j = 1,…,n), для которого надо получить значение выходного параметра.
- Для каждого правила Ri (i = 1,…,n), вычисляется уровень его срабатывания:
i = min (i1, i2,…, in), либо i = i1i2…in , (9)
где ij = Aij(uj*) – уровень срабатывания правила Ri по j-му входу.
На основе уровня срабатывания i определяется вывод из правила Ri (нечеткая точка):

yi* = { i / bi}. (10)
- Определяется общий вывод из системы правил R:
где
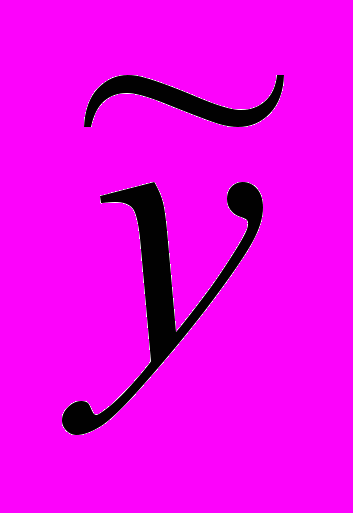
Также, в работе предложена методика сопоставления 3D-модели детали и 2D-чертежа для поиска и идентификации конструкторско-технологических элементов 2 уровня и конструкторских обозначений. Задача сопоставления 2D и 3D появляется после однозначного понимания автоматизированной системой конструкции детали из 3D-модели на основании графа декомпозиции. После завершения поиска каждому элементу 1 уровня, распознанному на основании 3D-модели, сопоставляются линии 2D-чертежа и определяется принадлежность конструкторских обозначений к конкретным КТЭ. Также, сопоставленные 3D-модель и 2D-чертеж детали используются для поиска и распознавания КТЭ 2 уровня.
Для получения параметров качества поверхности, отклонений формы, расположения поверхностей и точности детали анализируется 2D-чертеж, получаемый в формате IGES, и в автоматическом режиме распознаются конструкторские обозначения. Полученная КТМ детали в дальнейшем используется для автоматизации процедур выбора режущего инструмента и стратегий обработки на станках с ЧПУ.
Применение разработанной в диссертационном исследовании автоматизированной системы на основе метода автоматического распознавания КТЭ из 3D-модели и 2D-чертежа на основе графа декомпозиции и передачи КТМ детали в САПР ТП «ТехноПро» в условиях машиностроительных МИП позволяет существенно сократить время на подготовку исходной информации для технологического проектирования, что достоверно подтверждается соответствующими справками о внедрении на ряде МИП региона.
Четвертая глава посвящена автоматизации процедуры выбора рационального режущего инструмента для современного многофункционального технологического оборудования с ЧПУ в условиях МИП, также рассматривается автоматизация выбора стратегий обработки деталей, как новый подход к снижению производственных затрат.
Конструкции современных сборных режущих инструментов одного назначения различаются способами установки и крепления режущих элементов – пластин, т.е. структурной компоновкой и параметрами – размерами пластин, корпусных элементов или элементов крепежа. Количество возможных вариантов в ряде случаев исчисляется тысячами. Выбор подходящей конструкции инженером является постоянно решаемой технической задачей, и осуществляется, в основном, на основании однонаправленных рекламных материалов, личного или коллективного производственного опыта. Наибольшие проблемы в подборе рационального инструмента могут испытывать малые машиностроительные предприятия, в связи с отсутствием коллективного опыта.
С другой стороны, производителями режущего инструмента разработаны базы данных и экспертные системы для выбора инструмента. Однако такие системы не позволяют сравнить между собой однотипные конструкции различных производителей или конструкции, укомплектованные из сборочных элементов различных производителей, а также управлять процессом выбора наилучших вариантов конструкций инструментов.
Таким образом, задача выбора рационального режущего инструмента для обработки изделий на многофункциональном технологическом оборудовании с ЧПУ является актуальной и требующей решения.
В работе разработано математическое обеспечение, алгоритмы и автоматизированная система для выбора рационального металлообрабатывающего инструмента для обработки на основе данных, полученных из ГМ детали, представляемой в виде 3D-модели и 2D-чертежа (процесс получения данных рассмотрен в главе 3), с последующей передачей спецификации на выбранный инструмент в CAM-систему и САПР ТП. Проведенное исследование затрагивает большую часть применяемого в общем машиностроении токарного инструмента. Схема предлагаемого подхода к выбору инструмента рассмотрена на рис. 5.
Согласно стандартам ISO 1832:2004, обозначение режущей пластины P включает 11 основных компонентов:
P =
, (12)
где Pf - множество значений форм пластин, Ab – множество значений заднего угла пластины, Tc - множество значений класса допуска на пластины, Ls - множество значений типа пластины (обозначение фиксации), Pd - множество значений размера пластины (длина режущей кромки), Pt - множество значений толщины пластины, Re - множество значений радиуса при вершине, Cs - множество значений вида режущей кромки, Cd - множество значений исполнения пластины (обозначение направления резания), Cw - множество значений ширины фаски или обозначение стружколома, Ca - множество значений угла фаски.
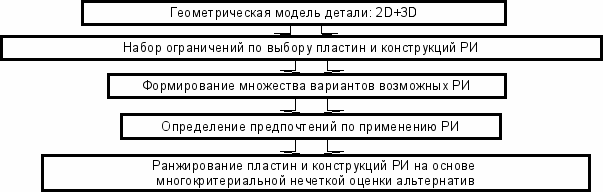
Рис. 5. Предлагаемый подход к выбору инструмента
Каждый компонент обозначения режущей пластины P имеет множество значений, например описание формы пластины Pf:
Pf={Pf1, Pf2, … Pf17} ={Ромбическая 35°,
Ромбическая 50°, … ,Восьмигранная, Круглая} . (13)
Рассмотрим задачу выбора рациональной формы режущей пластины Pf из множества выпускаемых пластин. Этот выбор осуществляется на основе степени соответствия альтернатив совокупности требований, определяемых системой 5 различных критериев Ci:
Ci={C1, C2, C3, C4, С5}. (14)
где С1 – эффективность отвода тепла; С2 – минимальная потребляемая мощность; С3 – прочность пластины; С4 – минимум возникновения вибраций;С5 – универсальность режущей пластины.
В таком случае каждому критерию Сi может быть поставлено в соответствие нечеткое множество
ACi = {µCi (Pf1), µCi (Pf2), … , µCi (Pf17)}. (15)
Здесь величина µCi (xj)
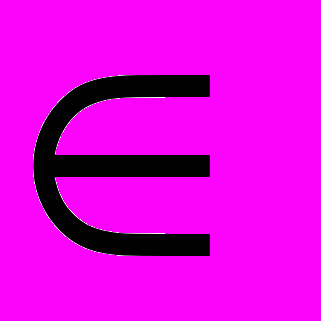
Данные этой таблицы получены на основе анализа литературных источников. Экспериментальное подтверждение табличных данных является темой для отдельного диссертационного исследования и в работе не выполнялось.
В рассматриваемом случае требуется решать многокритериальную оптимизационную задачу в условиях различной важности критериев достижения максимума целевой функцией. При этом каждому критерию Сi ставится в соответствие некоторый весовой коэффициент λi ≥ 0, причем
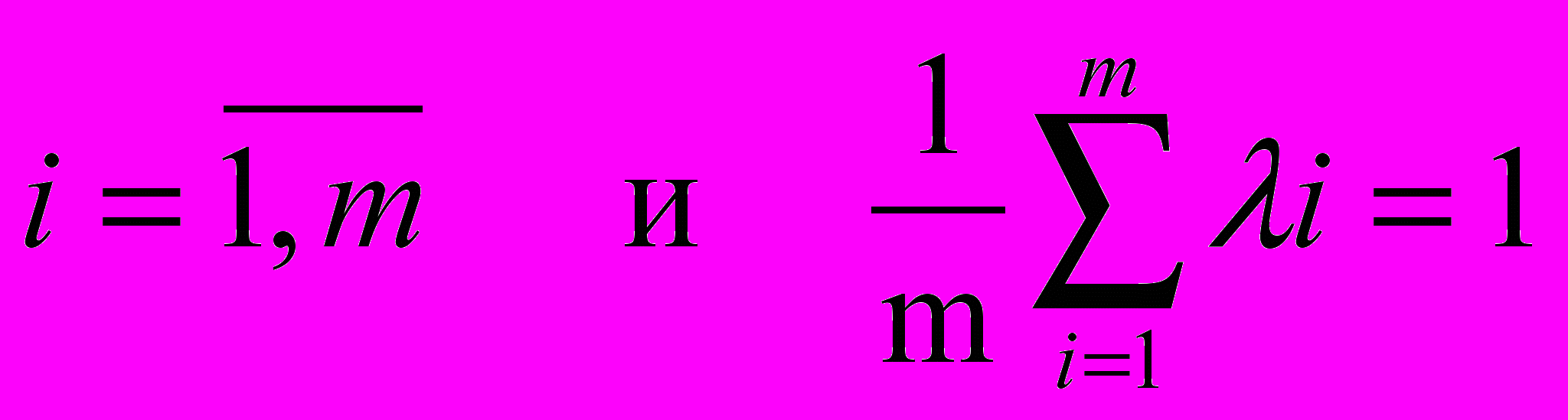
Таблица 2. Множество оценок форм пластин по критериям
Pfj | Обозначе-ние | Отвод тепла (AC1) | Мощность (AC2) | Прочность (AC3) | Вибрации (AC4) | Универсальность (AC5) |
Pf1 | V | 0,9 | 0,97 | 0,1 | 0,85 | 0,93 |
Pf2 | F | 0,78 | 0,85 | 0,22 | 0,73 | 0,81 |
Pf3 | D | 0,74 | 0,81 | 0,26 | 0,69 | 0,77 |
Pf4 | К | 0,74 | 0,81 | 0,26 | 0,69 | 0,77 |
Pf5 | Т | 0,7 | 0,77 | 0,3 | 0,65 | 0,73 |
Pf6 | Р | 0,604 | 0,674 | 0,396 | 0,554 | 0,634 |
Pf7 | Е | 0,58 | 0,65 | 0,42 | 0,53 | 0,61 |
Pf8 | С | 0,54 | 0,61 | 0,46 | 0,49 | 0,57 |
Pf9 | W | 0,54 | 0,61 | 0,46 | 0,49 | 0,57 |
Pf10 | В | 0,524 | 0,594 | 0,476 | 0,474 | 0,554 |
Pf11 | А | 0,5 | 0,57 | 0,5 | 0,45 | 0,53 |
Pf12 | М | 0,492 | 0,562 | 0,508 | 0,442 | 0,522 |
Pf13 | S | 0,46 | 0,53 | 0,54 | 0,41 | 0,49 |
Pf14 | L | 0,46 | 0,53 | 0,54 | 0,41 | 0,49 |
Pf15 | Н | 0,22 | 0,29 | 0,78 | 0,17 | 0,25 |
Pf16 | О | 0,1 | 0,17 | 0,9 | 0,05 | 0,13 |
Pf17 | R | 0,01 | 0,05 | 0,95 | 0,06 | 0,07 |
Решением исходной задачи будет такая альтернатива х, которая в наибольшей мере удовлетворяет требованиям всей совокупности критериев. Решающее правило D выбора наилучшей альтернативы в условиях многокритериальной задачи с неравнозначными критериями Сi, имеющими весовые коэффициенты λi, использует процедуру нахождения пересечения нечетких множеств

В соответствии с определением операции пересечения нечетких множеств функция принадлежности искомого решения находится по зависимости:

Таким образом, в качестве наилучшей должна быть выбрана та из альтернатив хj*, для которой значение функции принадлежности µD (xj) окажется максимальным:
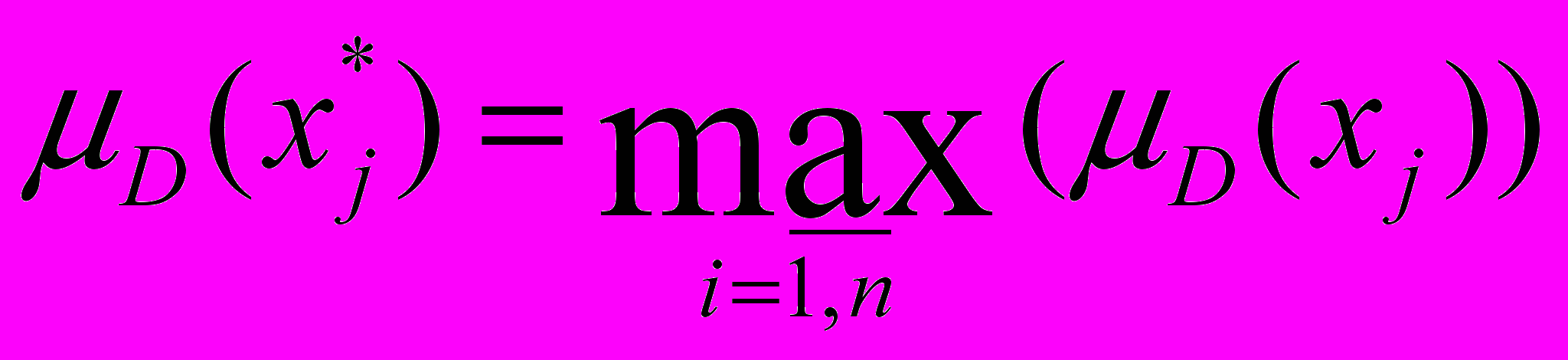
Именно эта альтернатива и является решением исходной задачи, поскольку она в наибольшей степени удовлетворяет требованиям всей совокупности рассматриваемых критериев.
Значения весовых коэффициентов определяются на основе стандартной процедуры попарного сравнения критериев. С учетом весовых коэффициентов строятся множества AλiCi:
AλiCi = {µλiCi (Pf 1), µλiCi (Pf 2), … , µλiCi (Pf 17)}. (20)
Применяя правило выбора искомой альтернативы (оптимальной формы режущей пластины), находится пересечение множеств, которое будет иметь следующий графический вид (рис. 6).
Таким образом, в качестве рациональной должна быть выбрана та из форм пластины Pfj*, для которой значение функции принадлежности µD(Pfj) окажется максимальным (рис. 6).
Для других параметров пластин, как и для державок, проведены аналогичные математические расчеты.
На основе разработанного математического обеспечения предложены алгоритмы работы системы, состоящей из 4 основных модулей:
- ввода первичной информации;
- подбора подходящего режущего инструмента;
- выбора рационального инструмента;
- модуль вывода.
Кроме того, в системе присутствуют модули, отвечающие за отображение чертежа и модели детали, база данных инструмента и ее редактор.
Результатом работы системы является отчет, содержащий необходимую информацию о рациональных инструментах и рекомендуемых режимах резания.
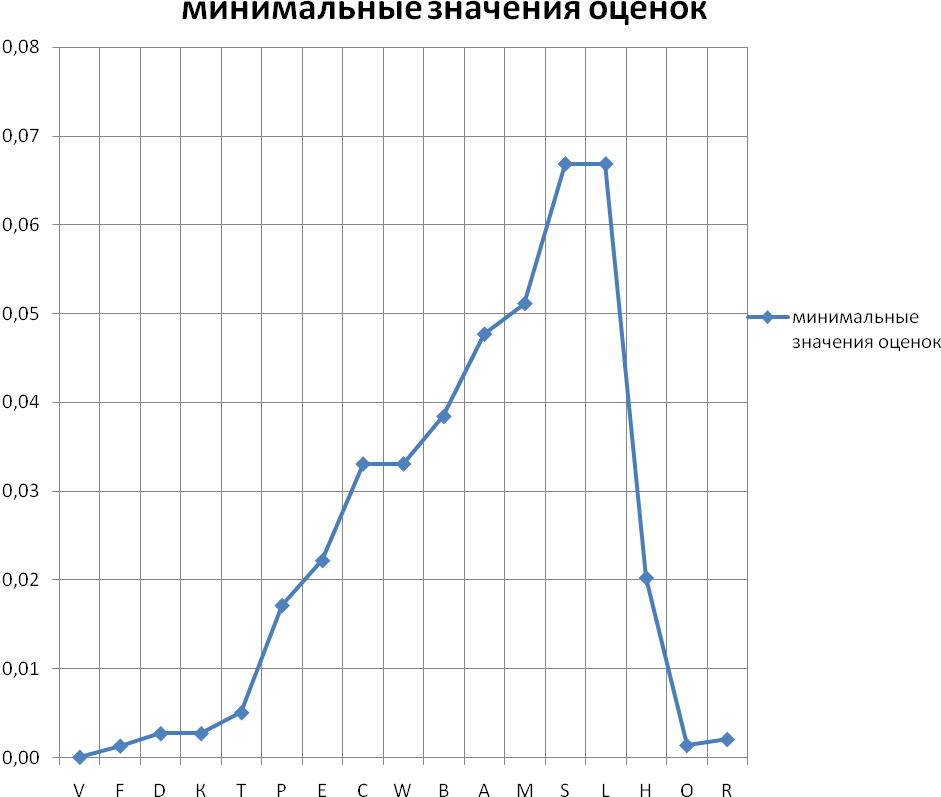
Форма пластины, Pf
µD(Pfj)
Рис.6. Минимальные значения оценок.
При технологической подготовке производства изделий машиностроения одной из важных задач является выбор стратегии обработки деталей. Предпосылками проведения исследований в этой области деталей являются:
- значительное распространение и использование многофункциональных станков с ЧПУ;
- увеличение номенклатуры деталей, которые обрабатываются за один установ;
- потребность в сокращении сроков подготовки производства деталей;
- универсальные CAD/CAM системы больше нацелены на решение геометрических задач и очень мало могут помочь пользователю при решении технологических задач, таких как назначение режимов резания, выбор стратегий обработки, подбор инструмента и т.д.;
- недостаточная интегрируемость современных САПР ТП с CAD системами и неспособность данных систем обеспечить сквозную подготовку производства в рамках концепции CALS;
- в САПР ТП и CAM-системах отсутствует математический аппарат выбора стратегий обработки детали.
Стратегия обработки может пониматься двояко: с одной стороны, под стратегией понимается последовательность обработки поверхностей и выбор инструмента, будем называть ее инструментальная (табл. 3), а с другой стороны – траектории движения инструмента при обработке, будем называть ее кинематическая (табл. 4). В работе рассматриваются оба названных понятия. Выбор стратегий обработки заготовок актуален как для МИП, так и для средних и крупных машиностроительных предприятий.
В табл. 3 для примера приведены только 5 инструментальных стратегий обработки КТЭ из нескольких десятков возможных (в сочетании). Научная проблема выбора инструментальной стратегии обработки возникла сравнительно недавно, с появлением широкого выбора инструмента с новыми возможностями. В отечественной науке этому вопросу уделялось мало внимания по причине ограниченного выбора инструмента для выбора стратегий. В работах Цветкова В.Д. и других авторов упоминается понятие «маршрут обработки поверхности (МОП)», частично схожее с предложенным понятием «инструментальная стратегия обработки». Под МОП понимается последовательность видов обработки (например точение, шлифование, полировка), а под инструментальной стратегией обработки понимается выбор конкретных инструментов и способов их применения. Поэтому, несмотря на схожесть инструментальной стратегии обработки и МОП, принято решение применять первое понятие.
Главный вопрос исследования инструментальных стратегий обработки – «при какой инструментальной стратегии обработки себестоимость детали будет минимальна?»
Исходные данные ID для выбора стратегии обработки можно описать в виде набора:
ID = | (21) |