Е доли пластмасс, керамики и композитов сопровождается созданием качественно новых видов материалов, значительно превосходящих по свойствам многие металлические
Вид материала | Документы |
Содержание9. Технология термической обработки |
- «Химия и технология переработки пластмасс и полимерных композитов», 351.62kb.
- Совершенствование управления строительным предприятием на основе лизинга Введение, 1571.06kb.
- Тематика занятий по организации производства изделий из пластмасс, 131.88kb.
- Темы индивидуальных заданий (Самостоятельные работы) Классификация материалов по химическому, 25.18kb.
- Отчет о научно-исследовательской работе за 2008 год Тема нир: Разработка новых нанотехнологий, 100.77kb.
- Темы: понятие керамики, как поликристалла; классификация керамики: по химическому составу,, 135.75kb.
- Аннотация дисциплины «Конструкции из дерева и пластмасс», 112.92kb.
- Учебно-методическая карта дисциплины утверждаю, 143.22kb.
- При подготовке лекций авторами были использованы материалы из следующих источников, 28.4kb.
- Методические указания по выполнению и варианты контрольной работы (задания) для студентов, 96.95kb.
- левая кривая - начало превращения переохлажденного аустенита в зависимости от степени переохлаждения;
- правая кривая - конец превращения аустенита. Она показывает время, необходимое при данном переохлаждении для полного превращения аустенита в феррито-цементитную смесь;
- точка Н2 соответствует переохлаждению 150-200 °С ниже А1 и показывает интервал минимальной устойчивости аустенита.
8.4. Перлитное превращение
Распад аустенита состоит из двух одновременно протекающих процессов:
- перехода Feγ→ Feα (бездиффузионного процесса) и образования цементита Fe3С (диффузионного процесса).
При перлитном превращения ведущей фазой является цементит (Fe3С). Зарождение зародыша Fe3С происходит на границе зерна, далее пластинка прорастает в середину зерна, а соседние участки обедняются углеродом и образуется феррит (рис. 8.7).
С увеличением степени переохлаждения увеличивается разность энергии аустенита и перлита (ΔF = FА – FП) (рис. 8. 1). Это приводит к повышению дисперсности образующихся фаз. Структуру феррито-цементитной смеси различной дисперсности называют перлитом, сорбитом, трооститом.
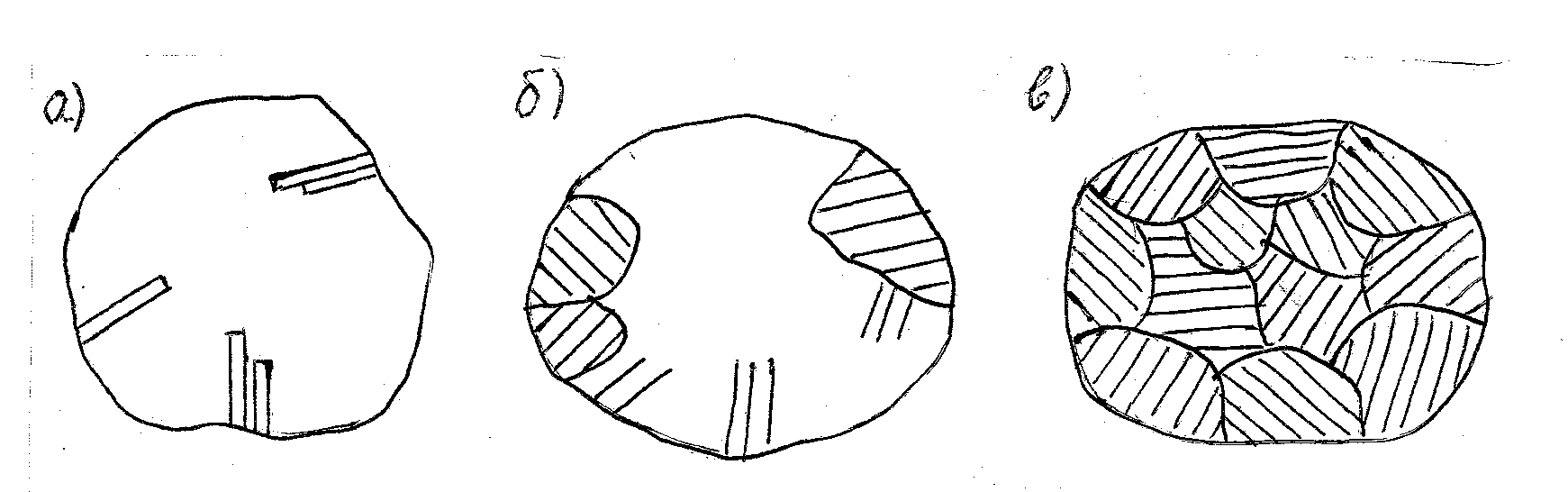
Рис. 8.7. Последовательность образования перлита в аустенитном зерне:
а - первичные пластинки цементита в феррите; б - вторичные пластинки цементита в феррите; в – колонии перлита
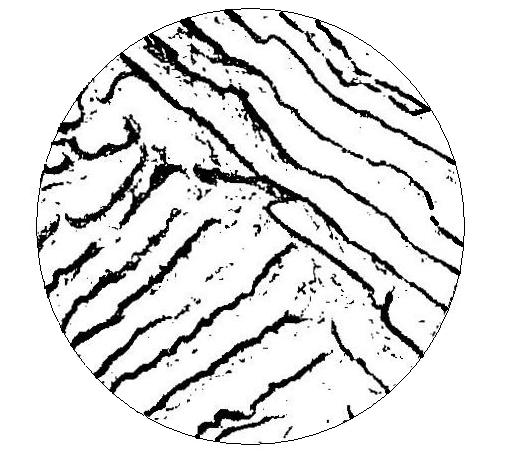
Рис. 8.8. Микроструктура перлита, (×1500)
На рисунке 8.8 по ориентировке пластин можно различить два зерна перлита (две колонии).
Дисперсность - суммарная толщина соседних пластинок Feα + Fe3С (рис. 8.9).

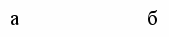
Рис. 8.9. Схема расположения пластинок цементита (а) и феррита (б) в перлите на поверхности протравленного шлифа. Стрелкой показано направление освещения под микроскопом
Дисперсность структуры определяет механические свойства стали: перлит имеет твердость 200НВ, сорбит – 300НВ, троостит – 400НВ
8.5. Бейнитное превращение
Бейнитное промежуточное превращение идет в интервале температур 550 – Мн. Образующаяся структура представляет собой двухфазную смесь кристаллов феррита к цементита. Основная особенность промежуточного превращения состоит в том, что полиморфный переход Feγ→ Feα происходит по мартенситному механизму – бездиффузионно, а образование цементита (Fe3С) – идет диффузионным путем.
Превращение начинается в интервале температур 550 – Мн с перераспределения углерода в аустените. Диффузионное перераспределение приводит к обеднению одних и обогащению других зон (скорость диффузии углерода в интервале 550 - Мн достаточна, а скорость диффузии железа стремится к нулю).
Уменьшение количества растворенного углерода приводит к повышению температуры мартенситного превращения, поэтому в обедненных углеродом зонах γ - твердого раствора происходит мартенситное превращение.
Образование концентрационной неоднородности приводит к возникновению напряжения, и процесс полиморфного превращения носит сдвиговый характер. Кристаллы феррита (Feα) пересыщены углеродом до 0,1-0,2 % получают тетрагональную решетку. При этом структура верхнего бейнита получается перистой, а нижнего - игольчатой.
8.6. Превращение аустенита при непрерывном охлаждении
Сталь, нагретая до аустенитного состояния, может быть охлаждена с различной скоростью. Наложим кривые охлаждения образцов углеродистой эвтектоидной стали на диаграмму изотермического распада аустенита (рис. 8.6) построена в координатах “температура - время”, поэтому на нее можно наложить графики скоростей охлаждения V1 < V2 < V3< Vкр < V4 (рис. 8.10)
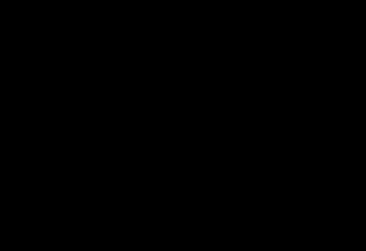
Рис. 8.10. Наложение графиков скоростей непрерывного охлаждения на диаграмму изотермического распада аустенита. Увеличение скорости охлаждения от V до Vкр
8.7. Мартенситное превращение ( III превращение)
При больших степенях переохлаждения и скоростях, превышающих Vкр, скорости диффузии железа и углерода равны нулю, ЕА>>ЕМ, поэтому превращение Feγ(С)→ Feα(С) происходит бездиффузионным путем (без изменения концентрации реагирующих фаз) за счет сдвига. Образуется мартенсит - пересыщенный, частично упорядоченный, твердый раствор внедрения углерода в альфа - железо (Feα) с тетрагональной решеткой (с/а >1) (рис. 8.11).
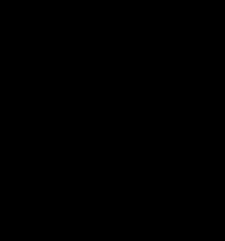
Рис. 8.11. Объемно-центрированная тетрагональная решетка мартенсита
Степень искажения решетки с/а прямо пропорциональна концентрации углерода. Поскольку мартенситное превращение состоит в перестройке решетки аустенита, в которой атомы не меняются местами (бездиффузионно), а смещаются (сдвигаются) друг относительно друга, то кристаллы имеют ориентационную связь (рис. 8.12). В углеродистых сталях существует две ориентационные связи, получившие название ориентировка Курдюмова-Закса и ориентировка Нишияма. Ориентировка кристаллов мартенсита (пластин или линз) идет по определенным плоскостям и направлениям (рис. 8.12) (направление (111) // (101)), плоскости ([101] // [111]). Следствием сдвигового механизма превращения на полированной поверхности шлифа является характерный рельеф.
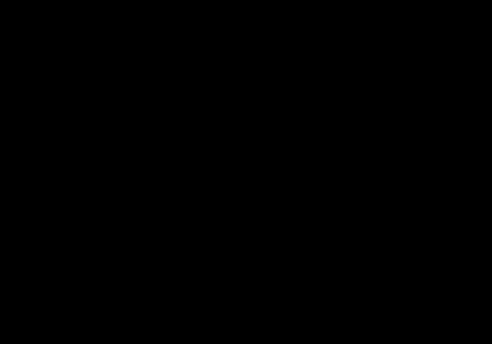
Рис. 8.12. Атомно-кристаллический механизм перестройки
Согласно теории, мартенситный кристалл образуется на плоскости сдвига в момент ее образования. Главную роль играют напряжения. Источниками напряжений являются: градиент температур по сечению; анизотропия механических свойств; неоднородность химического состава; структурные несовершенства; разная ориентировка кристаллов в пространстве; различный удельный объем аустенита и мартенсита; различные коэффициенты линейного расширения фаз.
Удельный объем аустенита при количестве углерода от 0,2-1,4 % составляет 0,12227 – 0,12528 см3/г; мартенсита – 0,12708 – 0,13061 см3/г.
Напряжения, возникающие в результате изменения температуры концентрируются в отдельных участках аустенита, образуя энергетические флуктуации. Релаксация (разряжение) напряжений происходит путем сдвига по определенным плоскостям и направлениям (рис. 8.12). В момент сдвига образуется порция мартенситных пластин (игл). Время образования порции мартенситных пластин (игл) изменяется в пределах от 0,5×10-7 до 5,7×10-8 в зависимости от размера пластин. Средняя скорость роста составляет около 103 м/с (1 км/с), близка к скорости звука в твердом теле и не зависит от температуры превращения. Кристаллы растут до определенных размеров, после чего рост прекращается.
Аустенитно-мартенситное превращение (рис. 8.13, б) проходит в интервале температур Мн – Мк (Мн, Мк – мартенситные точки: н – начало, к – конец превращения). При данной температуре с огромной скоростью образуется только определенное количество (порция) мартенсита, остается остаточный аустенит. Для возобновления процесса нужно дополнительное охлаждение.
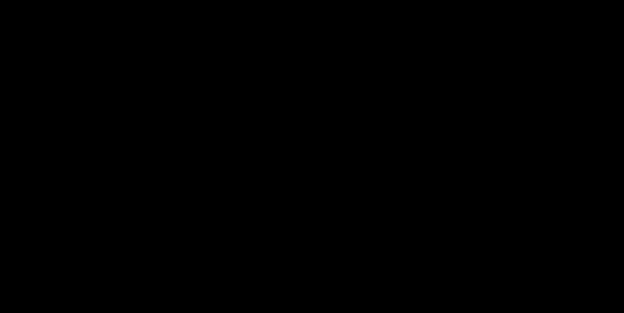
Рис. 8.13. Мартенситная кривая (а) и зависимость мартенситных точек от содержания углерода (б)
Мартенситное (А →М) превращение не идет до конца, в стали всегда остается остаточный аустенит (рис. 8. 13, а).
Положение точек мартенситного превращения зависит от состава стали. Сильно снижает положение точек Мн и Мк концентрация углерода (рис. 8.13, б).
Итак, особенностями мартенситного превращения являются:
1) бездиффузионный сдвиговый механизм;
2) ориентированность кристаллов в пространстве;
3) ультразвуковая скорость образования порции кристаллов мартенсита;
4) тетрагональность решетки (с/а);
5) незаконченность превращения А → М;
6) необратимость превращений А → М;
7) очень высокая твердость мартенсита (HRC 55-65) и хрупкость из-за повышенной плотности дефектов (дислокаций) внутри кристалла мартенсита.
8.8. Превращения в закаленной стали при нагреве (IV превращение)
Различают 4 основных превращения при нагреве закаленной стали (рис. 8.14). Все процессы идут внутри мартенситных пластин (игл) поэтому характер игольчатой структуры сохраняется до высоких температур.
Первое превращение при отпуске происходит в интервале 80-200°С и называется «двухфазным» или «гетерогенным» расплавом мартенсита. Выделяются тончайшие пластины карбида (ε - карбид или FexС), уменьшается степень тетрагоналъности с/а→1, образуется «отпущенный мартенсит». Это превращение сопровождается сокращением объема образца.
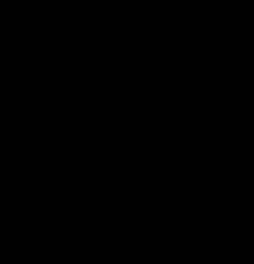
Рис. 8.14. Дилатометрическая кривая отпуска закаленной стали
Второе превращение происходит в интервале от 200 - 300°С. Одновременно идут процессы:
- образуются ε - и FexС – карбиды, когерентно связанные с решеткой мартенсита;
- остаточный аустенит переходит в «отпущенный мартенсит» (рис. 8.15) (бейнит нижний). Процесс сопровождается увеличением объема (рис. 8.14);
- продолжается выделение углерода из мартенсита (с/а→1);
- начинается карбидное обособление - образование карбида железа по схеме:
FexС→ Fe2С→ Fe5С→ Fe3С
Третье превращение происходит в интервале от 350-450°С. Увеличивается скорость диффузии, карбид железа выделяется из решетки мартенсита. Степень тетрагональности с/а →1. Образуется дисперсная смесь феррита и цементита (троостит отпуска).
Четвертое превращение происходит выше 400-450°С. Растут частицы карбида (коагуляция) и сливаются, округляются (сфероидизация). Тонкая феррито-цементитная структура троостита отпуска превращается при температуре 500-550°С в сорбит отпуска, а при более высоких температурах (600-650°С) - в перлит.
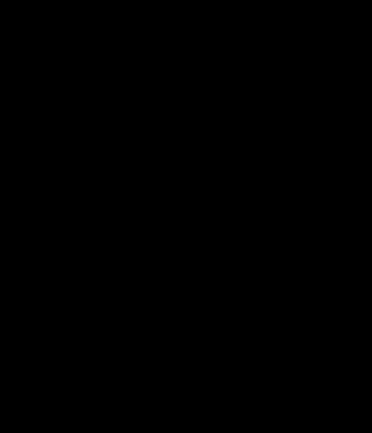
Рисунок 8.15 - Схема процессов, совершающихся при отпуске: 1 – выделение углерода из тетрагонального мартенсита; 2 – распад остаточного аустенита; 3 – снятие внутренних напряжений; 4 – коагуляция карбидных частиц
Возврат и рекристаллизация в α – Фазе (Feα) происходят в широком интервале температур отпуска. Развитие этих процессов сдерживается частицами карбидных выделений, закрепляющих отдельные дислокации, дислокационные стенки. После длительного отпуска при температуре 600°С, когда в результате коагуляции цементитных частиц закрепление границ ослабевает, происходит рекристаллизационный рост зерен миграцией высокоугольных границ. Микроструктура при этом теряет характерные морфологические признаки реечного мартенсита. Закалка + высокий отпуск называется улучшением.
9. ТЕХНОЛОГИЯ ТЕРМИЧЕСКОЙ ОБРАБОТКИ
9.1. Основные составляющие технологического процесса термической обработки
При разработке технологии термической обработки необходимо установить:
- режим нагрева детали или заготовки, в который входят температура нагрева, допустимые скорость и время нагрева;
- характер среды, где должен идти нагрев;
- условия охлаждения (выбор охлаждающей среды);
- производительность труда при термообработке;
- экономичность выбранного процесса.
Режим термообработки назначают до критическим точкам (Ас1, Ас3, Асm) диаграммы Fe-Fe3С (рис.7.1) и С - образной диаграммы превращения аустенита (рис.8.6).
Условия нагрева определяются видом нагревательного устройства, к которым относятся нагревательные печи (топливные или электрические), соляные ванны или ванны с расплавленным металлом, установки индукционного нагрева токами промышленной частоты или токами высокой частоты.
9.2. Классификация видов термической обработки
Схема классификации основных видов термической обработки показана на рис. 9.1.
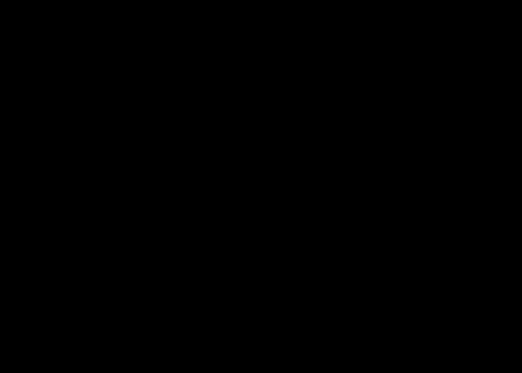
Рис. 9.1. Классификация основных видов термической обработки
Вид термической обработки определяется не характером изменения температуры во времени, а типом фазовых и структурных изменений в металле.
Собственная термообработка заключается только в термическом воздействии на металл или сплав.
Химико-термическая обработка заключается в сочетании термического и химического воздействия на поверхность.
Термомеханическая обработка заключается в сочетании термического воздействия и пластической деформации.
Отжиг I рода частично или полностью устраняет отклонения от равновесного состояния, возникающие при предыдущей обработке (литье, ковке, штамповке и т.д.), причем при его проведении не происходит фазовых превращений.
К отжигу I рода (рис. 9.1) относятся:
- гомогенизационный (диффузионный);
- рекристаллизационный и дорекристализационный;
- уменьшающий напряжения.
Цель гомогенизационного отжига - устранение ликвации (выравнивание химического состава) в отливках, в слитках, в легированной стали.
Режим гомогенизационного отжига: нагрев до 1050-1200 оС, выдержка 8-10 часов, охлаждение с печью до 200-250 оС. Продолжительность процесса около 80-100 часов (рис. 9.2).
Цель рекристаллизационного отжига – устранение наклёпа холоднокатанной стали, содержащей 0,1 – 0,2 % С.
Режим рекристаллизационного отжига: нагрев до 600-700 оС (Трекр = 0,4 Тпл по абсолютной шкале), выдержка, которая зависит от геометрии изделий (для тонких листов 25-30 мин.) и охлаждение с печью.
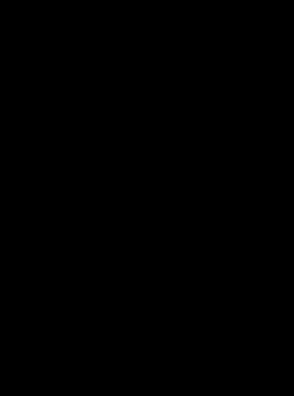
Рис. 9.2. Левый угол диаграммы Fe – Fe3 С и температурные области при термической обработке сталей
Цель отжига для снятия напряжений - снятие напряжений в деталях из углеродистой стали.
Режим отжига для снятия напряжений: нагрев до 400 – 600 оС, выдержка 2,5 мин на 1 мм толщины детали, охлаждение с печью.
Отжиг II рода основан на использовании диффузионных (нормальных) фазовых (полиморфных) превращений при охлаждении. Целесообразность отжига II рода определяется тем, насколько сильно структурные изменения влияют на свойства металла или сплава.
Различают следующие разновидности отжига второго рода: полный, неполный, изотермический, нормализационный (нормализация).
Полный отжиг используется для доэвтектоидных сталей (рис. 9.2). Режим такого отжига - нагрев до А3 + (20-30 оС), выдержка, медленное охлаждение со скоростью 100-200 оС в час до 500 оС вместе с печью, далее охлаждение на воздухе. При нагреве структура (Ф + П) превращается в мелкую структуру аустенита, при последующем охлаждении получим мелкую феррито-перлитную структуру.
Заэвтектоидные стали полному отжигу не подвергают, так как получается цементитная сетка по границам зерен перлита. Для заэвтектоидных сталей применяют неполный отжиг: нагрев до температуры между линиями А1 и Асm (рис.9.2), выдержка, медленное охлаждение (с печью). При нагреве немного выше А1 и последующем медленном охлаждении, когда еще мало зерно аустенита, концентрация которого неоднородна и в его составе содержится еще большое количество нерастворившихся карбидов, образуется зернистый перлит. Неполный отжиг для заэвтектоидных сталей называют сфероидизирующим.
Одного нагрева выше А1 и медленного охлаждения иногда бывает недостаточно для полной сфероидизации; эту операцию следует повторять несколько раз, т.е. сталь при отжиге нагревают до 730-740 оС, затем медленно охлаждают до 680 оС, затем снова нагревают до 730-740 оС и т.д. Такой отжиг называется циклическим или маятниковым, и он обеспечивает хорошую сфероидизацию цементита.
Цель такого отжига - получать структуру зернистого перлита и цементита в инструментальных сталях для улучшения обрабатываемости на металлорежущих станках. Стали с зернистым перлитом имеют твердость 160-180 НВ. Пластинчатый перлит имеет твердость 180-250 НВ.
Изотермический отжиг - нагрев стали до А3 + (20-30 оС), выдержка, быстрое охлаждение ниже А1(до 700-680 оС), при которой сталь выдерживается определенное время для полного изотермического превращения аустенита и образования феррито-перлитной структуры.
Преимущества изотермического отжига перед полным отжигом – это сокращение времени отжига и получение более однородной структуры.
Нормализационный отжиг (нормализация) (рис. 9.2) – это такой вид термической обработки, при которой сталь нагревается выше точки А3 на 30-50 оС для доэвтектоидных сталей и выше точки Асm для заэвтектоидных сталей с последующим охлаждением на спокойном воздухе.
В результате получают:
- более тонкое строение эвтектоида (тонкий перлит или сорбит);
- меньшие внутренние напряжения;
- выше твердость и прочность, чем после отжига;
- заэвтектоидные стали без грубой сетки вторичного цементита.
Главное при нормализации - экономия времени и энергии по сравнению с отжигом.
Нормализацию используют как промежуточную технологическую операцию вместо отжига или как окончательную при изготовлении сортового проката (рельсов, уголков, швеллеров и т.д.).
Для всех видов отжига применяют камерные толкательные печи, а также специальные агрегаты.
Закалка - термическая обработка с нагревом стали до температур, превышающих температуры фазовых превращений с выдержкой и последующим охлаждением металла или сплава со скоростью, превышающей критическую, с целью получения неравновесной структуры (мартенсита), либо пересыщенного раствора.
Результат закалки - повышение твердости и прочности.
Температура нагрева под закалку для доэвтектоидных сталей: А3 + (30-50 оС). Если нагрев проводится в интервале температур А1 – А3, то происходит неполная закалка. В этом случае оставшийся в структуре остаточный феррит ухудшает свойства доэвтектоидной стали.
Заэвтектоидные стали нагревают до температуры А1 + (40-60 оС ) и после охлаждения получают мартенсит с включениями вторичного цементита. Такая структура обеспечивает высокую твердость и износостойкость режущего инструмента.
Если температура нагрева заэвтектоидной стали выше Асm (рис. 9.2) то после закалки получают дефектную структуру грубоигольчатого мартенсита.
Время нагрева при закалке зависит от типа нагревательных устройств, размеров детали, химического состава (теплопроводности) стали, способа загрузки деталей в нагревательное устройство.
Скорость охлаждения при закалке устанавливают в зависимости от того, какую структуру в детали необходимо получить. Скорость охлаждения зависит от охлаждающей среды, формы изделия, теплопроводности стали.
В качестве охлаждающих сред применяют воду (при разных температурах от 18-50 °С), 10 %-ный раствор NaOH в воде, 10 %-ный раствор NaCl в воде, минеральное масло, спокойный воздух.
9.3. Способы закалки
В зависимости от состава стали, формы и размеров детали и требуемых в термически обработанной детали свойств выбирают оптимальный способ закалки, наиболее просто осуществимый и одновременно обеспечивающий нужные свойства.
Чем сложнее форма термически обрабатываемой детали, тем тщательнее следует выбирать условия охлаждения, потому что чем сложнее деталь, тем больше различие в сечениях детали, тем бớльшие внутренние напряжения возникают в ней при охлаждении.
Чем больше углерода содержит сталь, тем больше объёмные изменения при превращении, тем при более низкой температуре происходит превращение аустенита в мартенсит, тем больше опасность возникновения деформаций, трещин, напряжений и других закалочных пороков, тем тщательнее следует выбирать условия закалочного охлаждения для такой стали.
К основным способам закалки относятся:
- Закалка в одном охладителе (рис. 9.3, кривая 1) – наиболее простой способ. Нагретую до определенных температур деталь погружают в закалочную жидкость, где она остается до полного охлаждения. Применяют этот способ при закалке несложных деталей из углеродистых и легированных сталей. При этом для углеродистых сталей диаметром более 2-5 мм закалочной средой служит вода, а для меньших размеров и для многих легированных сталей – масло.
Для уменьшения внутренних напряжений деталь иногда не сразу погружают в закалочную жидкость, а некоторое время охлаждают на воздухе, «подстуживают». Такой способ закалки называется закалкой с подстуживанием (рис. 9.3, кривая 5).
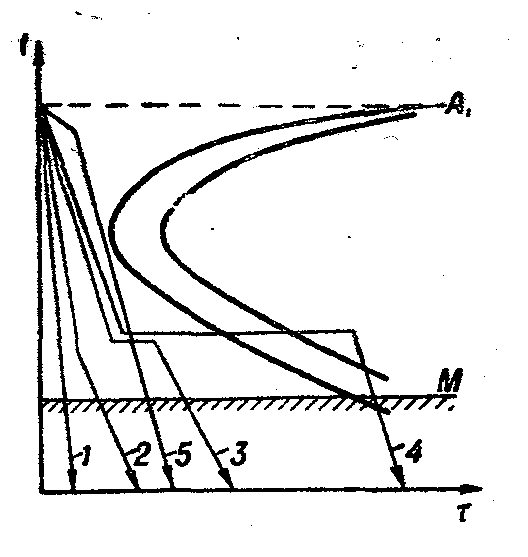
Рисунок 9.3 - Схема режимов охлаждения при различных способах закалки: 1 – непрерывная закалка в одном охладителе; 2- прерывистая закалка, или закалка в двух средах; 3 - ступенчатая закалка; 4 - изотермическая закалка; 5 – закалка с подстуживанием