Е доли пластмасс, керамики и композитов сопровождается созданием качественно новых видов материалов, значительно превосходящих по свойствам многие металлические
Вид материала | Документы |
Содержание4. Механические свойства металлов и сплавов |
- «Химия и технология переработки пластмасс и полимерных композитов», 351.62kb.
- Совершенствование управления строительным предприятием на основе лизинга Введение, 1571.06kb.
- Тематика занятий по организации производства изделий из пластмасс, 131.88kb.
- Темы индивидуальных заданий (Самостоятельные работы) Классификация материалов по химическому, 25.18kb.
- Отчет о научно-исследовательской работе за 2008 год Тема нир: Разработка новых нанотехнологий, 100.77kb.
- Темы: понятие керамики, как поликристалла; классификация керамики: по химическому составу,, 135.75kb.
- Аннотация дисциплины «Конструкции из дерева и пластмасс», 112.92kb.
- Учебно-методическая карта дисциплины утверждаю, 143.22kb.
- При подготовке лекций авторами были использованы материалы из следующих источников, 28.4kb.
- Методические указания по выполнению и варианты контрольной работы (задания) для студентов, 96.95kb.
3.8. Методы исследования структуры
Исследование структуры металлов может проводиться:
- методом световой микроскопии;
- методом электронной микроскопии;
- рентгеноструктурный анализ;
- рентгеноспектральный анализ;
- дополнительные методы исследования.
При методе световой микроскопии с помощью различных микроскопов можно увидеть размер, форму и взаимное расположение зерен, достаточно крупные включения, некоторые крупные дефекты кристаллического строения. Для исследования готовят микрошлифы (поверхность образца должна быть отполирована до зеркального блеска, а затем протравлена специальными реактивами).
Метод электронной микроскопии проводится с помощью электронных микроскопов, которые делятся на просвечивающие электронные микроскопы (ПЭМ) и растровые электронные микроскопы (РЭМ). Метод основан на прохождении, преломлении, рассеивании и отражении электронного пучка от поверхности исследуемого микрошлифа. При этом можно увидеть детали структуры менее 0,1мкм, однако, этот метод требует сложной подготовки образца, особенно при исследовании на просвечивающем электронном микроскопе.
Рентгеноструктурный анализ изучает строение решетки и основан на исследовании микрошлифа путем рассеивания рентгеновских лучей.
Методом спектрального анализа и аналитической химии можно определить состав сплава, при этом достигается высокая точность при определении распределения компонентов.
К дополнительным методам для определения тонкой структуры металлов и сплавов, включая дефекты типа вакансий и дислокаций, относятся:
- нейтронография;
- ядерный гамма-резонанс;
- автоионная микроскопия;
- оже-электронная спектроскопия.
4. МЕХАНИЧЕСКИЕ СВОЙСТВА МЕТАЛЛОВ И СПЛАВОВ
4.1. Упругая и пластическая деформация. Несовершенства решетки и прочность металлов.
Из свойств, которыми могут обладать материалы, механические свойства в большинстве случаев являются важнейшими. Все наиболее ответственные детали и изделия изготавливают из металлов.
Для металлов характерна металлическая связь, когда в узлах кристаллической решетки расположены положительно заряженные ионы, окруженные электронным газом. Наличие металлической связи придает материалу (металлу) способность к пластической деформации и к самоупрочнению в результате пластической деформации.
Способность металла сопротивляться воздействию внешних сил характеризуется механическими свойствами. Поэтому при выборе материала для изготовления деталей машин необходимо, прежде всего, учитывать его механические свойства: прочность, упругость, пластичность, ударную вязкость, твердость и выносливость. Эти свойства определяют по результатам механических испытаний, при которых металлы подвергают воздействию внешних сил (нагрузок). Внешние силы могут быть статическими, динамическими или циклическими (повторно-переменными). Нагрузка вызывает в твердом теле напряжение и деформацию.
Напряжение – величина нагрузки, отнесенная к единице площади поперечного сечения испытуемого образца.
Деформация – изменение формы и размеров твердого тела под влиянием приложенных внешних сил. Деформация может быть упругой, исчезающей после снятия нагрузки, и пластической, остающейся после снятия нагрузки.
Пластичность – свойство твердых тел, не разрушаясь, необратимо изменять свои внешние формы (пластически течь) под действием внешних сил или внутренних напряжений. Пластические изменения формы металлического тела называют пластической деформацией.
Пластическая деформация может осуществляться скольжением и двойникованием, обычно при участии дислокационных дефектов (рис. 4.1).
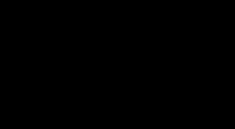
Рис. 4.1. Схема процесса скольжения и двойникования
Чем больше в металле плоскостей и направлений скольжения, тем выше его способность к пластической деформации (рис. 4. 2). Металлы, имеющие кристаллическую решетку ОЦК и ГЦК, пластичны.
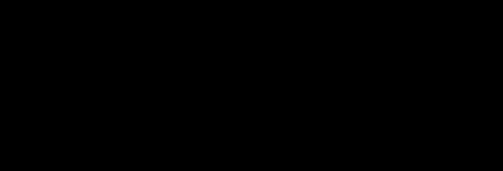
Рис. 4.2. Плоскости и направления (заштрихованные плоскости) скольжения в кристаллической решетке: а – ГЦК; б – ОЦК; в – ГПУ
Скольжение – последовательное перемещение одной части кристалла по отношению к другой в результате перемещения уже имеющихся в кристалле дислокаций или только возникающих (рис. 4.3).
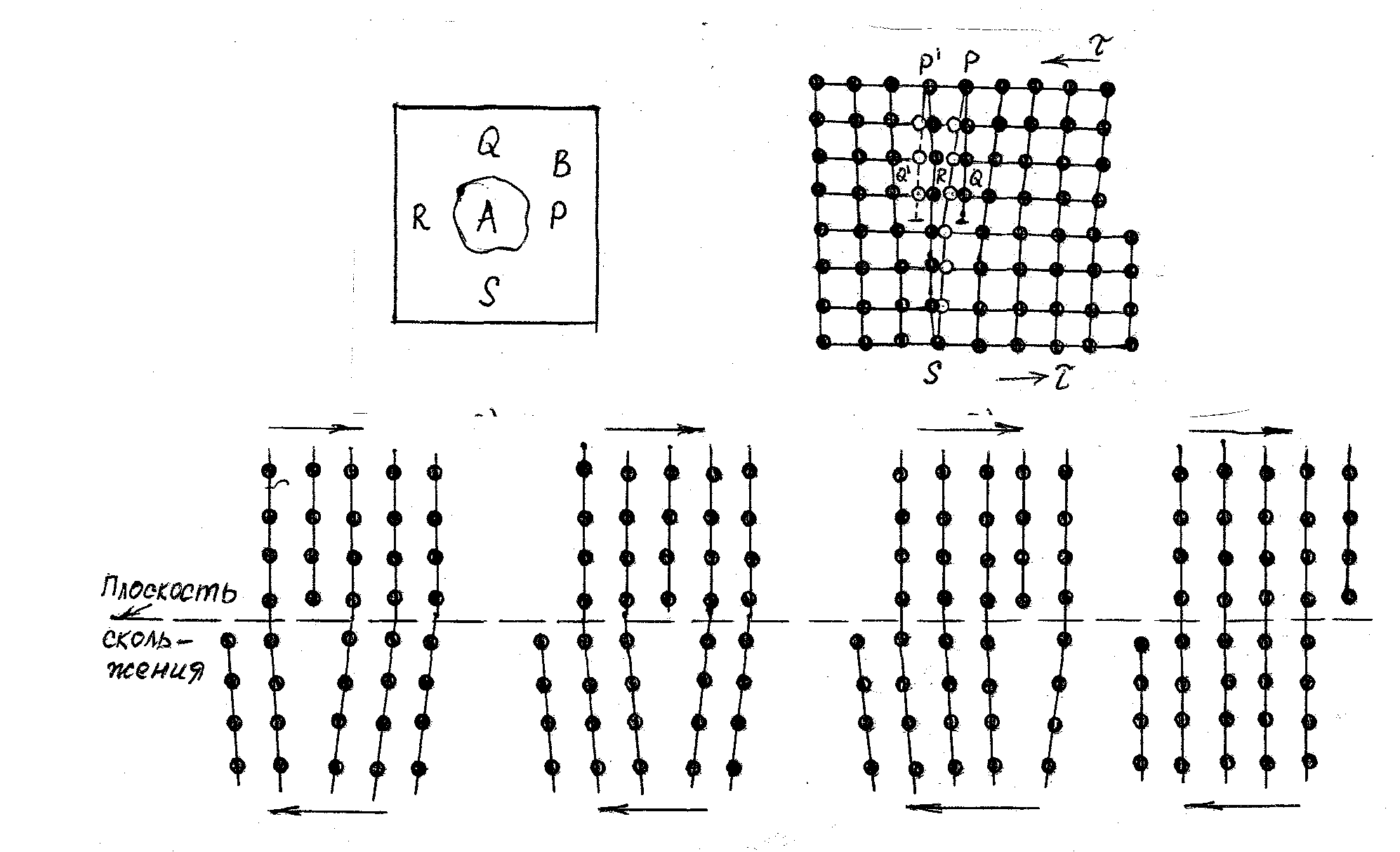
Рис. 4.3. Схема дислокационного механизма пластической деформации
Чтобы представить особенности движения дислокаций на разных стадиях деформирования, на рис. 4.4 показана кривая деформационного упрочнения, типичная для монокристалла с решеткой ГЦК.
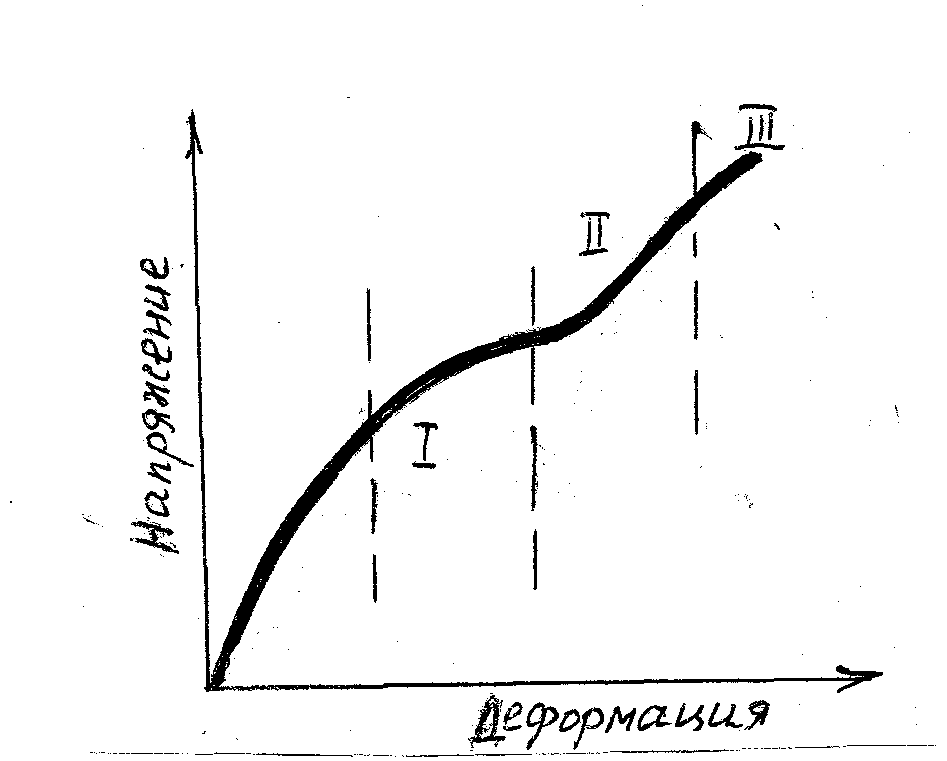
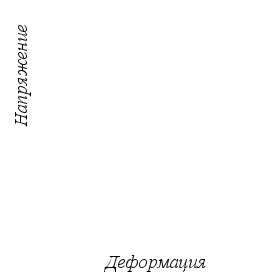
Рис. 4.4. Кривая деформационного упрочнения, типичная для монокристаллов ГЦК
Упрочняемость металла зависит от количества дислокаций, участвующих в процессе пластической деформации, и характера их движения.
На стадии I (рис. 4.4) наблюдается скольжение единичных дислокаций (ламинарное движение), торможение которых (упрочнение) осуществляется только границами субзерен и поэтому невелико.
На стадии II начинается турбулентное скольжение большого числа дислокаций. Упрочнение происходит за счет малоподвижных порогов и барьеров. Скорость упрочнения максимальная.
На стадии III скольжение идет преимущественно за счет поперечного скольжения винтовых дислокаций.
Для различных металлов степени развития этих стадий различны.
Упрочнение (наклеп) при пластической деформации обусловлено образованием малоподвижных порогов и барьеров при пересечении дислокаций, увеличением плотности дислокаций, измельчением зерна.
Формоизменение поликристаллического тела при обработке давлением – более сложный процесс. Пластическая деформация происходит в каждом из зерен, которые различно ориентированы по отношению друг к другу и к деформирующей нагрузке, различны по форме и размерам и обладают неодинаковыми физико-механическими свойствами. Кроме того, при пластической деформации поликристаллов большую роль играют межкристаллитные прослойки – границы зерен (рис. 4.5).
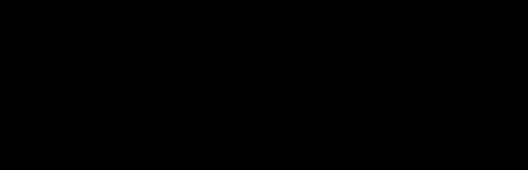
Рис. 4.5. Схема образования текстуры в поликристаллитном теле: а – расположение зерен; б – изменение формы зерен в направлении главной деформации; в - текстура
Различают два вида деформации: внутрикристаллитную (по зерну) и межкристаллитную (по границам зерен).
Внутрикристаллитная деформация осуществляется путем сдвига, скольжения, двойникования, как в монокристалле.
Межкристаллитная деформация осуществляется путем поворота, перемещения одних зерен относительно других.
Оба вида деформации протекают одновременно. Деформация начинается в зернах, плоскости скольжения которых составляют угол 45о с направлением усилия (рис.4.5 а).
При большой деформации в результате процессов скольжения зерна меняют свою форму, вытягиваются в направлении главной деформации (рис. 4.5 б) и образуют волокнистую или слоистую структуру. Такую структуру называют текстурой (рис. 4.5 в), приводящей к анизотропии свойств металла.
Металлы с ГЦК - решеткой упрочняются сильнее, чем с ОЦК- решеткой.
В результате пластической деформации с ростом плотности дислокаций возрастает предел прочности металла, образуется текстура, возрастают сопротивляемость металла деформации и твердость, уменьшается пластичность и ударная вязкость, повышаются электросопротивление и коэрцитивная сила, уменьшается магнитная проницаемость.
С увеличением напряжений выше предела прочности возникают магистральные трещины, и материал разрушается по вязкому или хрупкому механизму.
4.2. Методы испытания металлов и сплавов
Для установления комплекса механических свойств металлов образцы из исследуемого материала подвергают статическим и динамическим испытаниям.
Статическими называются испытания, при которых прилагаемая к образцу нагрузка возрастает медленно и плавно.
4.2.1. К статическим испытаниям относят испытание на растяжение, сжатие, кручение, изгиб, а также определение твердости.
В результате испытаний на статическое растяжение, которое проводят на разрывных машинах, получают диаграмму растяжения (рис.4.6 а) и диаграмму условных напряжений (рис. 4.6 б) пластичного металла.
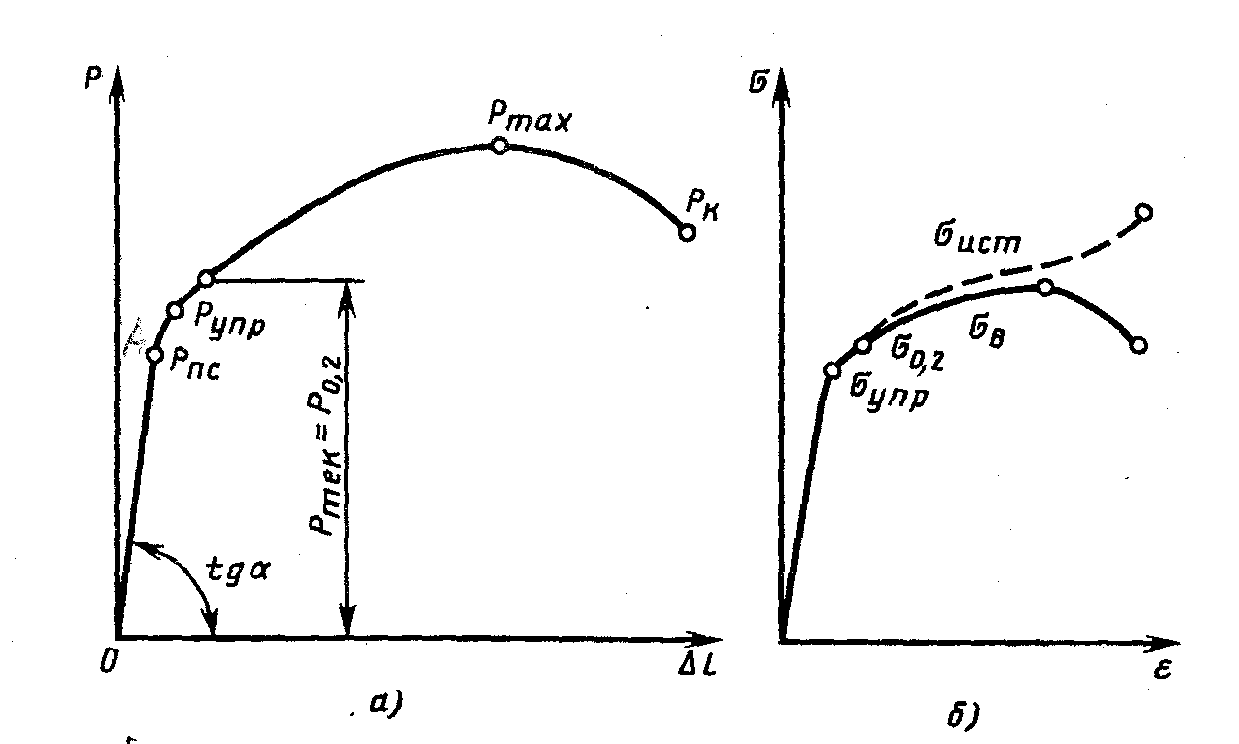

Рис. 4.6. Изменение деформации в зависимости от напряжения:
а – диаграмма растяжения пластичного материала; б – диаграмма условных напряжений пластичного материала
Из графика видно, что сколь бы ни было мало приложенное напряжение, оно вызывает деформацию, причем начальные деформации являются всегда упругими и величина их находится в прямой зависимости от напряжения. На кривой, приведенной на диаграмме(рис. 4.6), упругая деформация характеризуется линией ОА и ее продолжением.
Выше точки А нарушается пропорциональность между напряжением и деформацией. Напряжение вызывает уже не только упругую, но и пластическую деформацию.
Представленная на рис. 4.6 зависимость между приложенным извне напряжением и вызванной им относительной деформацией характеризует механические свойства металлов:
- наклон прямой ОА (рис. 4.6а) показывает жесткость металла или характеристику того, как нагрузка, приложенная извне, изменяет межатомные расстояния, что в первом приближении характеризует силы межатомного притяжения; тангенс угла наклона прямой ОА пропорционален модулю упругости (Е), который численно равен частному от деления напряжения на относительную упругую деформацию (Е= / );
- напряжение пц (рис. 4.6б), которое называется пределом пропорциональности, соответствует моменту появления пластической деформации. Чем точнее метод измерения деформации, тем ниже лежит точка А;
- напряжение sупр (рис. 4.1б), которое называется пределом упругости, и при котором пластическая деформация достигает заданной малой величины, установленной условиями. Часто используют значения остаточной деформации 0,001; 0,005; 0,02 и 0,05%. Соответствующие пределы упругости обозначают s0,005, s0,02 и т.д. Предел упругости – важная характеристика пружинных материалов, которые используют для упругих элементов приборов и машин;
- напряжение s0,2, которое называется условным пределом текучести и которому соответствует пластическая деформация 0,2 %. Физический предел текучести sт определяется по диаграмме растяжения, когда на ней имеется площадка текучести. Однако при испытаниях на растяжение большинства сплавов площадки текучести на диаграммах нет Выбранная пластическая деформация 0,2 % достаточно точно характеризует переход от упругих деформаций к пластическим, а напряжение s0,2 несложно определяется при испытаниях независимо от того, имеется или нет площадка текучести на диаграмме растяжения. Допустимое напряжение, которое используют в расчетах, выбирают обычно меньше s0,2 в 1,5 раза;
- максимальное напряжение sв, которое называется временным сопротивлением, характеризует максимальную несущую способность материала, его прочность, предшествующую разрушению, и определяется по формуле
sв = Р max / Fo
Допустимое напряжение, которое используют в расчетах, выбирают меньше sв в 2,4 раза.
Пластичность материала характеризуется относительным удлинением и относительным сужением :
= ( lк – lо) / lо * 100,
= ( Fо – Fк) / Fо * 100,
где lо и Fо – начальные длина и площадь поперечного сечения образца;
lк - конечная длина образца;
Fк – площадь поперечного сечения в месте разрыва.
4.2.2. Твердость – способность материалов сопротивляться пластической или упругой деформации при внедрении в него более твердого тела, которое называется индентором.
Существует разные методы определения твердости.
Твердость по Бринеллю определяется как отношение нагрузки при вдавливании стального шарика в испытуемый материал к площади поверхности полученного сферического отпечатка (рис. 4.7а).
HB = 2P / D D - D2 – d2,
где Р – нагрузка, кгс;
D – диаметр шарика, мм;
d – диаметр лунки, мм
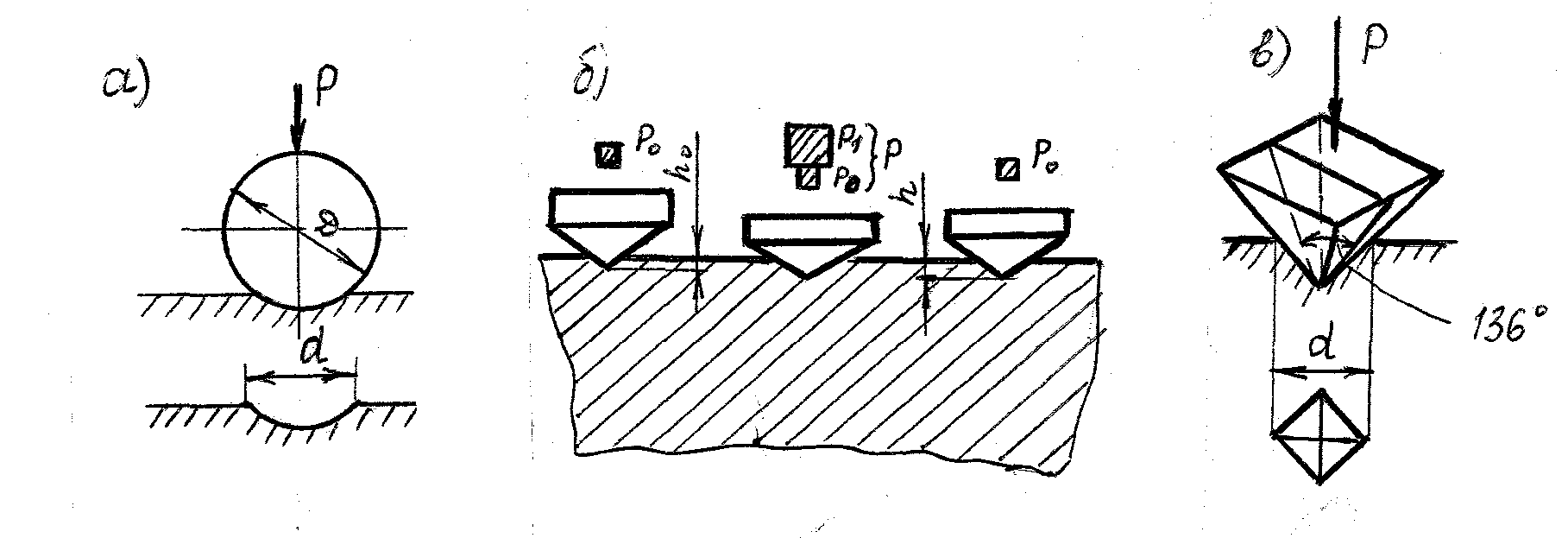
Рис. 4.7. Схемы испытания на твердость: а – по Бринеллю; б – по Роквеллу; в – по Виккерсу
Твердость по Роквеллу определяется глубиной проникновения в испытуемый материал алмазного конуса с углом при вершине 120о или закаленного шарика диаметром 1,588 мм (рис. 4.7.б).
Конус или шарик вдавливают двумя последовательными нагрузками:
- предварительной Ро = 10 н;
- общей Р = Ро + Р1, где Р1 – основная нагрузка.
Твердость обозначается в условных единицах:
- для шкал А и С HR = 100 – (h – ho) / 0,002
- для шкалы В HR = 130 – (h – hо) / 0,002
Для определения твердости используется алмазный конус при нагрузке 60 Н (HRA), алмазный конус при нагрузке 150 Н (HRC) или стальной шарик диаметром 1,588 мм (HRB).
Твердость по Виккерсу измеряют для деталей малой толщины и тонких поверхностных слоев, полученных химико-термической обработкой.
Эта твердость определяется как отношение нагрузки при вдавливании в испытуемый материал алмазной четырехгранной пирамиды с углом между гранями 136о к площади поверхности полученного пирамидального отпечатка (рис. 4.7.в):
HV = 2P * sin /2 / d2 = 1,854 P/d2,
где P – нагрузка, кгс;
= 136о – угол между гранями;
d – среднее арифметическое длин обеих диагоналей, мм.
Величину HV находят по известному d согласно формуле или по расчетным таблицам согласно ГОСТ 2999-75.
Микротвердость, учитывая структурную неоднородность металла, применяют для измерения малых площадей образца. При этом вдавливают пирамиду как при определении твердости по Виккерсу, при нагрузке Р = 5-500 Н, а среднее арифметическое длин обеих диагоналей (d) измеряется в мкм. Для измерения микротвердости используется металлографический микроскоп.
4.2.3. Сопротивление материала разрушению при динамических нагрузках характеризует ударная вязкость. Её определяют (ГОСТ 9454-78) как удельную работу разрушения призматического образца с концентратором (надрезом) посередине одним ударом маятникового копра (рис. 4.8): КС = К / So ( К – работа разрушения; So – площадь поперечного сечения образца в месте концентратора).
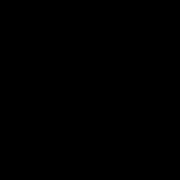
Рис. 4.8. Схема испытаний на ударную вязкость
Ударную вязкость (МДж/м2) обозначают KCU, KCV и KCT. Буквы КС означают символ ударной вязкости, буквы U, V, T – вид концентратора: U-образный с радиусом надреза rн = 1 мм, V-образный с rн = 0,25 мм; T – трещина усталости, созданная в основании надреза; KCU – основной критерий ударной вязкости; KCV и KCT используют в специальных случаях.
Работа, затраченная на разрушение образца, определяется по формуле
Ан = Р * l1( cos - cos ),
где Р - масса маятника, кг;
l1 – расстояние от оси маятника до его центра тяжести;
- угол после удара;
- угол до удара
4.2.4. Циклическая долговечность характеризует работоспособность материала в условиях многократно повторяющихся циклов напряжений. Цикл напряжений – совокупность изменения напряжения между двумя его предельными значениями max и min в течение периода Т (рис. 4.9).
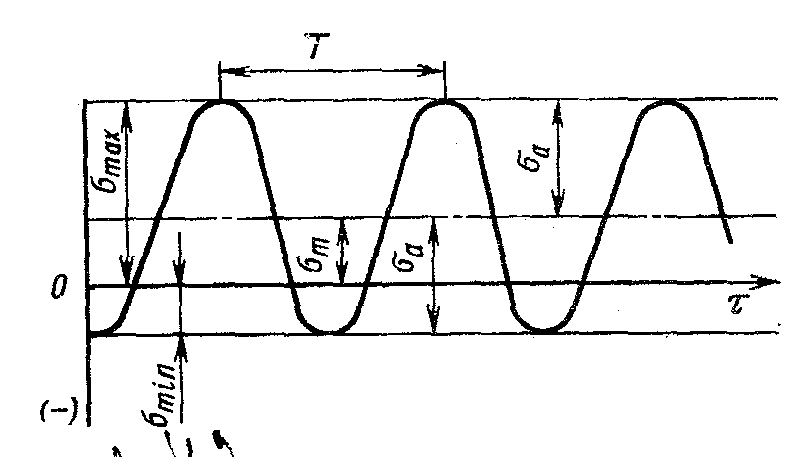
Рис. 4.9. Синусоидальный цикл изменения напряжений
Различают симметричные циклы (R = -1) и асимметричные (R изменяется в широких пределах). Различные виды циклов характеризуют различные режимы работы деталей машин.
Процессы постепенного накопления повреждений в материале под действием циклических нагрузок, приводящие к изменению его свойств, образованию трещин, их развитию и разрушению, называют усталостью, а свойство противостоять усталости – выносливостью (ГОСТ 23207 – 78).
На усталость деталей машин влияют ряд факторов (рис. 4.10).
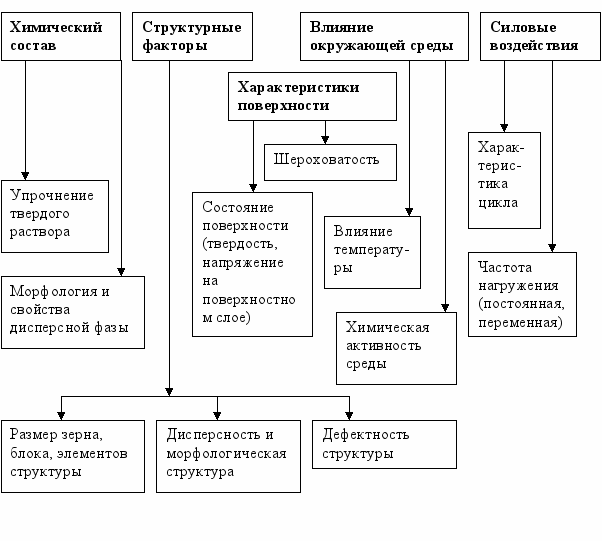
Рис. 4.10. Факторы, влияющие на усталостную прочность
Разрушение от усталости по сравнению с разрушением от статической нагрузки имеет ряд особенностей:
- оно происходит при напряжениях, меньших, чем при статической нагрузке, меньших пределах текучести или временного сопротивления;
- разрушение начинается на поверхности (или вблизи от нее) локально, в местах концентрации напряжений (деформации). Локальную концентрацию напряжений создают повреждения поверхности в результате циклического нагружения либо надрезы в виде следов обработки, воздействия среды;
- разрушение протекает в несколько стадий, характеризующих процессы накопления повреждений в материале, образования трещин усталости, постепенное развитие и слияние некоторых из них в одну магистральную трещину и быстрое окончательное разрушение;
- разрушение имеет характерное строение излома, отражающее последовательность процессов усталости. Излом состоит из очага разрушения (места образования микротрещин) и двух зон – усталости и долома (рис. 4.11).
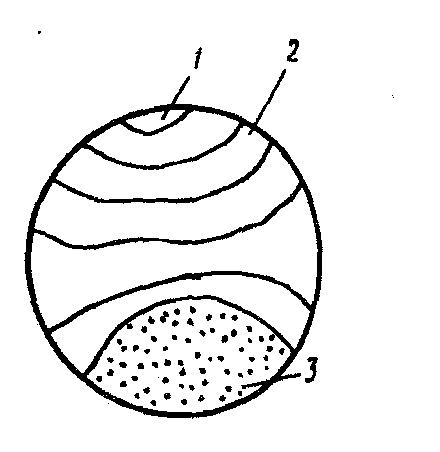
Рис. 4.11. Схема излома усталостного разрушения: 1 – очаг зарождения трещины; 2 – зона усталости; 3 – зона долома
4.3. Конструкционная прочность металлов и сплавов
Конструкционная прочность металлов и сплавов – это комплекс прочностных свойств, которые находятся в наибольшей корреляции со служебными свойствами данного изделия.
Сопротивление материала хрупкому разрушению является важнейшей характеристикой, определяющей надежность работы конструкции.
Переход к хрупкому разрушению обусловлен рядом факторов:
- природой сплава (типом решетки, химическим составом, величиной зерна, загрязнением сплава);
- особенностью конструкции (наличием концентраторов напряжений);
- условиями эксплуатации (температурным режимом, наличием нагрузки на металл).
Существует несколько критериев оценки конструкционной прочности металлов и сплавов:
- критерии, определяющие надежность металлов против внезапных разрушений (критическая температура хрупкости; вязкость разрушения; работа, поглощаемая при распространении трещины; живучесть при циклическом нагружении);
- критерии, определяющие долговечность материала (усталостная прочность; контактная выносливость; износостойкость; коррозионная стойкость).
Для оценки надежности материала используют также параметры: 1) ударную вязкость KCV и КCT; 2) температурный порог хладноломкости t 50. Однако эти параметры только качественные, непригодные для расчета на прочность.
Параметром KCV оценивают пригодность материала для сосудов давления, трубопроводов и других конструкций повышенной надежности.
Параметр KCT, определяемый на образцах с трещиной усталости у основания надреза, более показателен. Он характеризует работу развития трещины при ударном изгибе и оценивает способность материала тормозить начавшееся разрушение. Если материал имеет KCT = 0, то это означает, что процесс его разрушения идет без затраты работы. Такой материал хрупок, эксплуатационно ненадежен. И, наоборот, чем больше параметр KCT, определенный при рабочей температуре, тем выше надежность материала в условиях эксплуатации. KCT учитывают при выборе материала для конструкций особо ответственного назначения (летательных аппаратов, роторов турбин и т. п.).
Порог хладноломкости характеризует влияние снижения температуры на склонность материала к хрупкому разрушению. Его определяют по результатам ударных испытаний образцов с надрезом при понижающейся температуре.
На переход от вязкого разрушения к хрупкому указывают изменения строения излома и резкое снижение ударной вязкости (рис.4.12), наблюдаемое в интервале температур (tв – tх) (граничные значения температур вязкого и хрупкого разрушения).

Рис. 4.12. Влияние температуры испытания на процент вязкой составляющей в изломе (В) и ударную вязкость материала KCV, KCT
Строение излома изменяется от волокнистого матового при вязком разрушении (t tв) до кристаллического блестящего при хрупком разрушении (t tх). Порог хладноломкости обозначают интервалом температур (tв – tн) либо одной температурой t50, при которой в изломе образца имеется 50 % волокнистой составляющей, и величина КСТ снижается наполовину.
О пригодности материала для работы при заданной температуре судят по температурному запасу вязкости, равному разности температуры эксплуатации и t 50. При этом, чем ниже температура перехода в хрупкое состояние по отношению к рабочей температуре, тем больше температурный запас вязкости и выше гарантия от хрупкого разрушения.
4.4. Пути повышения прочности металлов
Принято различать техническую и теоретическую прочность. Техническую прочность определяют значением свойств: предела упругости (0,05); предела текучести (0,2); предела прочности (в); модуля упругости (Е); предела выносливости (R).
Под теоретической прочностью понимают сопротивление деформации и разрушению, которое должны были бы иметь материалы согласно физическим расчетам с учетом сил межатомного взаимодействия и предположения, что два ряда атомов одновременно смещаются относительно друг друга под действием напряжения сдвига.
Исходя из кристаллического строения и межатомных сил можно ориентировочно определить теоретическую прочность металла по следующей формуле:
теор G / 2,
где G – модуль сдвига.
Теоретическое значение прочности, рассчитываемое по указанной формуле, в 100 – 1000 раз больше технической прочности. Это связано с дефектами в кристаллическом строении, и прежде всего с существованием дислокаций. Прочность металлов не является линейной функцией плотности дислокаций (рис. 4.13).
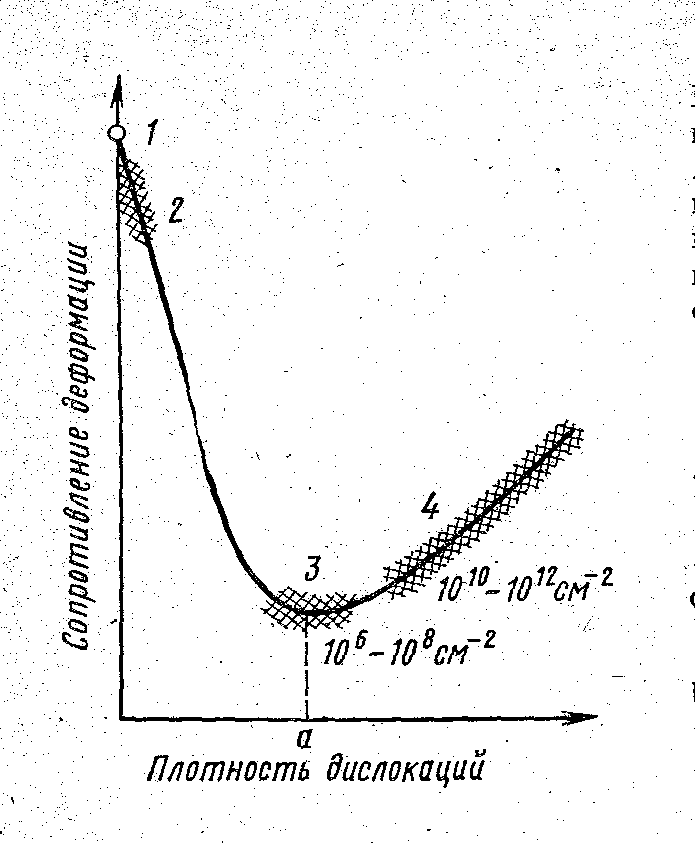
Рис. 4.13. Схема зависимости сопротивления деформации от плотности и других дефектов в металлах:1 – теоретическая прочность; 2-4 – техническая прочность (2 – усы; 3 – чистые неупрочненные металлы; 4 –сплавы, упрочненные легированием, наклепом, термической или термомеханической обработкой)
Как видно из рисунка 4.13, минимальная прочность определяется некоторой критической плотностью дислокаций а, приближенно составляющей 106 – 108 см-2. Эта величина относится к отожженным металлам. Величина 0,2 отожженных металлов составляет 10-5 – 10-4 G. Если а 1012 – 1013 см-2, то в этом случае могут образоваться трещины.
Если плотность дислокаций (количество дефектов) меньше величины а (рис.4.13), то сопротивление деформации резко увеличивается и прочность быстро приближается к теоретической.
Повышение прочности достигается:
- созданием металлов и сплавов с бездефектной структурой, т.е. получение нитевидных кристаллов («усов»);
- повышение плотности дефектов, в том числе дислокаций, а также структурных препятствий, затрудняющих движение дислокаций;
- создание композиционных материалов.
4.5. Влияние нагрева на строение и свойства деформированного металла (рекристаллизация)
Пластическая деформация (рис. 4.14) приводит к созданию неустойчивого состояния материала из-за возросшей внутренней энергии (внутренних напряжений). Деформирование металла сопровождается его упрочнением или так называемым