Учебное пособие по дисциплине глубокая переработка нефти и газа содержание
Вид материала | Учебное пособие |
- Федеральный государственный образовательный стандарт среднего профессионального образования, 931.07kb.
- Методические указания и контрольные задания для студентов-заочников по специальности, 1294.44kb.
- Учебное пособие Москва 2005 ббк 60. 55 Рецензенты : д ф. н., проф, 2138.94kb.
- Геохимические методы поисков месторождений нефти и газа содержание учебной дисциплины, 74.47kb.
- И. М. Губкина Ю. И. Брагин Нефтегазопромысловая геология и гидрогеология залежей, 644.07kb.
- Учебное пособие Издательство тпу томск 2006, 2624.3kb.
- «Глубокая переработка нефтяных дисперсных систем», 122.36kb.
- Методические указания и контрольные задания для студентов -заочников образовательных, 815.61kb.
- Положение о научно-образовательном центре «Нефтегазовое дело», 89.57kb.
- «Переработка нефти», 43.95kb.
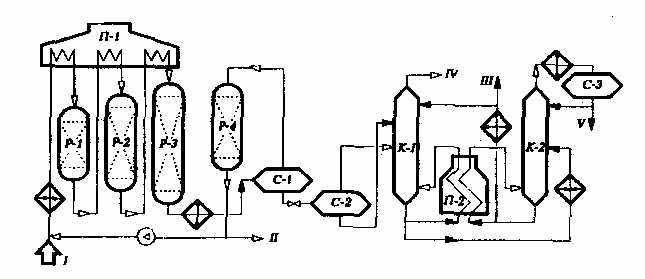
I – гидроочищенное сырьё; II – ВСГ; III – стабильный катализат; IV – сухой газ; V – головная фракция.
Рисунок 21– Принципиальная технологическая схема установки КР со
стационарным слоем катализатора
Основными реакционными аппаратами установок (или секций) каталитического риформинга с периодической регенерацией катализатора являются адиабатические реакторы шахтного типа со стационарным слоем катализатора. На установках раннего поколения применялись реакторы аксиального типа с нисходящим или восходящим потоком реакционной смеси. На современных высокопроизводительных установках применяются реакторы только с радиальным движением потоков преимущественно от периферии к центру.
Радиальные реакторы обеспечивают значительно меньшее гидравлическое сопротивление, по сравнению с аксиальным реактором.
Установки КР с непрерывной регенерацией катализатора
4 реактора риформинга (Р1) располагают друг над другом и связывают между собой системами переточных труб малого диаметра. Шариковый катализатор диаметром 1,6 мм свободно перетекает под действием силы тяжести из реактора в реактор. Из реактора четвертой ступени через систему затворов с шаровыми клапанами катализатор поступает в питатель-дозатор, откуда азотом его подают в бункер накоксованного катализатора узла регенерации.
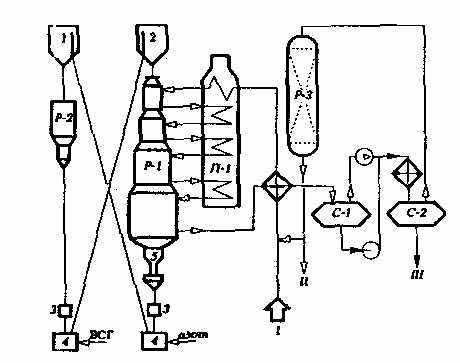
1 - бункер закаксованного катализатора; 2 – бункер регенерированного катализатора; 3 – шлюз; 4 – дозатор; 5 – разгрузочное устройство; I – гидроочищенное сырьё; II – ВСГ; III – риформат на стабилизацию.
Рисунок 22 – Принципиальная технологическая схема установки
каталитического риформинга с непрпрывной регенерацией катализатора
Регенератор (Р2) представляет собой аппарат с радиальным потоком реакционных газов, разделенный на 3 технологические зоны: в верхней при мольном содержании кислорода менее 1 % производят выжиг кокса, в средней при содержании кислорода 10 – 20 % и подаче хлорорганического соединений - окислительное хлорирование катализатора, а в нижней зоне катализатор прокаливают в токе сухого воздуха. Разобщение зон - гидравлическое.
Катализатор проходит все зоны под действием силы тяжести. Из регенератора через систему шлюзов-затворов катализатор поступает в питатель-дозатор пневмотранспорта и водородосодержащим газом его подают в бункер-наполнитель, расположенный над реактором первой ступени. Процесс регенерации автоматизирован и управляется ЭВМ. Систему регенерации при необходимости можно отключить без нарушения режима риформирования сырья.
Поскольку процесс каталитического риформинга проводят при пониженном давлениии (0,9 - 0,4 МПа), на установках каталитического риформинга с непрерывной регенерацией катализатора (КР НРК) применяют систему операции ВСГ: катализат после реакторов и сырьевого ТО подают в сепаратор низкого давления С1. Выделившиеся в нем газовую и жидкую фазы соотвественно компрессором и насосом направляют в сепаратор высокого давления С2 для выделения ВСГ с высокой концентрацией водорода. Стабилизацию нестабильного катализата осуществляют по схеме, аналогичной схемы регенерации со стацианарным слоем катализатора.
На установках со стационарным слоем катализатора при снижении давления с 3,0 до 1,5 MПa выход катализата с ОЧИМ 95 увеличился с 74,4 до 84,9 %, а выход водорода - с 1,0 до 1,9 %. На установке КР НРК при давлении 0,8 МПа выход катализата с ОЧИМ 100 достигает 83,5, а выход водорода - 2,8 %.
Таблица 20 - Выход продуктов на различных установках риформинга
Показатель | Л-35-11/1000 | ЛЧ-35-/1000 | ЛФ-35-1/1000 | |
Сырьевая фракция, 0С | 62-180 | 85-180 | 85-180 | 85-180 |
ОЧИМ бензина | 90 | 95 | 95 | 100 |
Рабочее давление, МПа | 3,0 | 3,0 | 1,5 | 0,8 |
Мощность по сырью, млн т/год | 1,0 | 1,0 | 1,0 | 1,0 |
Выход продуктов, %: | | | | |
катализат | 77,5 | 74,4 | 84,9 | 83,5 |
рефлюкс С3-С4 | 5,4 | 5,6 | 1,0 | 3,2 |
Углеводородный газ | 10,6 | 11,6 | 6,5 | 0,8 |
ВСГ | 4,5 | 6,4 | 7,1 | 12,5 |
В т. ч. водород | 0,8 | 1,0 | (1,9) | (2,8) |
Потери | 2,0 | 2,0 | 0,5 | - |
Цеоформинг - неплатиновый риформинг, используемый на некоторых мини-НПЗ, позволяет без применения водорода олучать высокооктановые автомобильные бензины типа АИ 80и АИ 93 из бензиновых фракций (н.к. 140 0С) нефтей и газовых кондесатов без предварительной гидроочистки (с содсржанием серы до 1 %). Катализаторы - высококреземные цеолиты (ИК-28, ИК-30), разработанные институтом катализа СО АН РФ - не содержит благородных и тяжёлых металлов. Одна тонна катализатора позволяет перерабатывать 5-8 тыс. т сырья. Срок его службы - 5-7 тыс. часов.
В цеоформинге протекают основные реакции:
крекинг С - С связей;
Н-перенос с образованием алканов и аренов;
алкелирование изоалканов и аренов алкенами;
изомеризация и дисттропорционирование;
гидрогинолиз сернистых соед.
Рабочие параметры:
t = 350 - 450 0С, давление 0,5 - 1,5 МПа и объемная скорость 1 - 2 ч-1.
Выход бензина: АИ 80 – 82 - 85 % или АИ 93 – 62 - 65 %.
Состав высокооктанового бензина: алкены < 5%, арены 20 - 25 и 50 – 55 %, изоалкены и цикланы 60 - 70 и 40 – 50 % соответственно АИ 80 и АИ 93, сера - 0,05 %. Цикл безрегенерационной работы реактора составляет 10 суток.
Контрольные вопросы
1. Назначение процессов каталитического риформинга.
2. Какова роль водорода в процессах каталитического риформинга?
3. Химизм и термодинамика процесса каталитического риформинга.
4. Состав катализаторов риформинга.
5. Промоторы катализаторов каталитического риформинга. С какой целью производится хлорирование катализаторов риформинга?
6. Почему сырьё каталитического риформинга подвергают глубокой гидроочистке и осушке?
7. Влияние технологических параметров на качество риформата.
8. Влияние фракционного состава сырья на выход риформата.
9. Распределение объёма катализатора по реакторам.
10. Принципиальная схема установки со стационарным слоем катализатора.
11. Принципиальная схема установки с непрерывной регенерацией катализатора.
Тема 4.5.3 Каталитическая изомеризация лёгких алканов
Целевым назначением процессов КИЗ в современной нефтепереработке является получение высокооктановых изокомпонентов автомобильных бензинов или сырья нефтехимии, прежде всего изопентана для синтеза изопренового каучука.
Высокая эффективность КИЗ заключается в том, что в качестве сырья используются низкооктановые компоненты нефти - фракции н.к. - 62 0С и рафинаты каталитического риформинга, содержащие в основном н-пентаны и н-гексаны. Это сырье (а также фракции С5 и С6, получаемые с ГФУ) изомеризуется в среде водорода в присутствии бифункциональных катализаторов.
Высокие детонационная стойкость и испаряемость продуктов изомеризации углеводородов С5 и C6 обусловливают их исключительную ценность в качестве низкокипящих высокооктановых компонентов неэтилированных автомобильных бензинов. Значение КИЗ особенно возросло в последние годы в связи с потребностью производства высокоокановых бензинов с ограниченным содержанием аренов и бензола.
Теоретические основы
Реакции изомеризации алканов являются обратимыми, протекают беч изменения объема, с небольшим экзотермическим эффектом (6 - 8 кДж/моль). Поэтому термодинамическое равновесие зависит только от температуры: низкие температуры благоприятствуют образованию более разветвленных изомеров (преимущественно диметил-производных) и получению, следовательно, изомеризата с более высокими октановыми числами. При этом равновесное со-держание изомеров при данной температуре повышается с увеличением числа атомов углерода в молекуле н-алкана.
Таблица 21 - Состав (% моль) равновесных смесей алканов С4 - С5
Углеводород | 27 0С | 127 0С | 227 0С | 327 0С | 527 0С |
С4: н - бутан изобутан | 19,0 87 | 35,0 65,0 | 46,0 56,0 | 54,0 46,0 | 61,0 39,0 |
н-пентан метилбутан диметилпропан | 3,0 44,0 53,0 | 12,0 65,0 23,0 | 18,0 69,0 13,0 | 25,0 67,0 9,0 | 31,0 63,0 6,0 |
н-гексэн метилпентаны диметилбутаны | 2,0 9,0 89,0 | 7,0 23,0 70,0 | 11,0 37,0 52,0 | 19,0 42,0 39,0 | 25,0 46,0 29,0 |
в т.ч. ДМБ | 84,0 | 61,0 | 41,0 | 29,0 | 20,0 |
На бифункциональных катализатоpax, обладающих дегидро-гидрирующей и кислотной активностями, изомеризация протекает по следующей схеме:
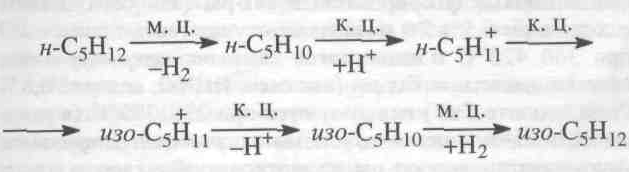
Вначале происходит дегидрирование н-алкана на металлических центрах катализатоpa. Образовавшийся алкен на кислотном центре превращается в карбений-ион, который легко изомеризуется. Изомерные карбоний-ионы, возвращая протон кислотному центру катализатора, превращаются в соответствующие алкены, которые затем гидрируются на металлических центрах катализаторов изомиризации.
Активные центры, как мегаллические, так и кислотные, в отсутствие водорода быстро отравляются в результате закоксовывания катализатора.
Для подавления побочных реакций крекинга процесс проводят под повышенным давлением при циркуляции ВСГ.
В современных бифункциональных катализатоpax КИЗ н-алканов в качестве металлических компонента используются платина и палладий, а в качестве носителя - фторированный или хлорированный оксид алюминия, а также алюмосиликаты или цеолиты, внесенные в матрицу оксида алюминия.
Алюмоплатиновые фторированные катализаторы (отечественные ИП-62 с содержанием 0,5 % Pt) позволяют осуществить процесс изомеризации при 360 - 420 0С и называются высокотемпературными.
Металл-цеолитные катализаторы (отечественные ИЦК-2, содержащие 0,8 % Pt на цеолите CaY) используются при 230 – 380 0С (в зависимости от типа цеолита) и названы среднетемпературными.
Алюмоплатиновые катализаторы, промотированные хлором (такие как НИП-66, НИП-74 и платиносодержащие сульфатированные оксиды (Zr, AI)), применяются при 120 - 150 0С и названы низкотемпературными.
Наибольшее распространение в современной нефтепереработке получают низкотемпературные процессы КИЗ н-алканов С4 - С6 на основе алюмоплатиновых катализаторов, промотированных хлором, которые вытесняют ранее построенные высоко- и средне- температурные процессы.
Таблица 22 – Сравнительная характеристика различных типов катализаторов изомеризации
Наименование | Фторированые катализаторы | Цеолитные катализаторы | Хлорированные катализаторы | Сульфированные оксиды | ||
СИ-2 | Аналоги СИ-2 | |||||
Глубина изомеризации С5, % | 50-52 | 54-62 | 65-75 | 70-75 | 68-72 | |
Глубина изомеризации С6, % | 1-2 | 12-16 | 24-28 | 28-34 | 20-27 | |
Выход С5+, % масс. | 95-97 | 95-97 | 98 | 98 | 95-97 | |
Допустимое содержание в сырье, ррm | - S - N - Н2О | до 100 1-3 до 100 | до 10 1 до 20 | <0,5 <0,1 <0,1 | 1-5 1-2 до 20 (50) | 1 1 10-20 |
ОЧИМ изокомпонента*, пункты | - «за проход» - с рециклом н-С5 - с рециклом i-С6 - с рециклом н-С5 и С6 | 70-72 73-75 - - | 76-78 78-81 81-83 83-85 | 82-84 84-85 86-88 90-91 | 83-85 85-86 87-88 90-92 | 81-83 84-85 86-87 89-90 |
Относительные эксплуатационные затраты* | - «за проход» - с рециклом с низкооктановых гексанов | 1,5 нет данных | 1,2 5 | 1,1 3,3 | 1,0 3 | 1,1 3,6 |
Относительные капитальные затраты процесса* | - «за проход» - с рециклом с низкооктановых гексанов | 1,6 нет данных | 1,2 4,0 | 1,3 2,0 | 1,0 1,5 | 1,4 2,2 |
* для сырья с 40 % пентанов
Основные параметры процесса
Температура. С повышением температуры скорость реакции изомеризации возрастает до ограничиваемого равновесием предела. Дальнейшее повышение теипературы приводит лишь к усилению реакций гидрокрекинга с образованием легких газов. При этом возрастает расход водорода, а выход изомеров снижается.
Давление. Хотя давление не оказывает влияние на равновесие реакции изомеризации н-алканов, оно существенно влияет на кинетику целевых и побочных реакций процесса.
Данные о влиянии давления на изомеризацию н-гексана при мольном соотношении H2:C6H14 = 4:1 и постоянном времени контакта приведены ниже:
Давление, МПа 0,63 2,2 2,2 4,9 4,9
Температура, t 0С 316 316 344 318 345
Степень превращения, % мольн. 60,7 32,0 65,6 14,5 33,5
Выход изогексанов, % мольн. 49,8 31,3 59,2 13,1 31,0
Селективность 0,82 0,98 0,90 0,91 0,93
Повышение давления при прочих равных условиях снижает глубину, но повышает селективность изомеризации. Увеличение парциального давления водорода снижает скорость дезактивации катализатора в результате торможения коксообразования. Однако повышение давления свыше 4 МПа нецелесообразно, т.к. при этом коксообразование практически не меняется.
Объемная скорость подачи сырья. При постоянной степени превращения объемная скорость и температура оказывают влияние на скорость изомеризации. Для увеличения объемной скорости вдвое требуется повышение температуры процесса примерно на 8 – 11 0С.
Установки каталитической изомеризации (КИЗ) пентан - гексановой
В современной мировой нефтепереработке распространение получили модели процессов изомеризации:
1) однопроходные, состоящие из двух параллельно работающих реакторов и колонны стабилизации (например, в ОАО НУНПЗ);
2) с рециркуляцией непревращенных н-пентанов;
3) с рециркуляцией непревращенных н-гексанов (например, в ОАО «Комсомольский НПЗ», ОАО «Уфа-нефтехим», ОАО «КиришНПЗ»).
фракции бензинов.
Поскольку степень превращения С5 – С6 – алканов на высокотемпературном катализаторе типа ИП-66 составляет около 55 %, изомеризацию на промышленных установках осуществляют с ректификацией смеси и церкуляцией непревращённого сырья. Исходное сырьё изомеризации подвергают предварительной гидроочистке и осушке. Установка изомеризации состоит из двух блоков: ректификации и изомеризации.
В блоке ректификации производится выделение изомеров из смеси исходного сырья и стабильного изомеризата.
Реакторный блок состоит из двух параллельно работающих секций: в одной осуществляется изомеризация н-пентана, а в другой - н-гексана.
Технологическая схема установки изомеризации
Смесь исходного сырья, рецеркулирующего стабильного изомеризата и тощего абсорбента поступает на разделение после подогрева в теплообменниках в колонну К1. Из этой колонны сверху отбирается изопентановая фракция, подвергающая дальнейшей ректификации в бутановой колонне К2, где происходит отделение целевого изо-пентана от бутанов. Нижний продукт этой колонны направляется на фракционирование в изогексановую колонну К4, с верха которой отбирается второй целевой продукт процесса – изогексан.
Отбираемая с верха К3 пентановая фракция, содержащая около 91 % масс. н-пентана, смешивается с водородосодержащим газом и после нагрева в трубчатой печи П1 до требуемой температуры поступает в реактор изомеризации со стационарным слоем катализатора Р1.
Парогазовая смесь продуктов реакции охлаждается и конденсируется в теплообменниках и холодильниках и поступает в сепаратор С5. Циркулирующий ВСГ из С5 после осушки в адсорбере Р2 компрессором подаётся на смешение с сырьём. Изомеризат после стабилизации в колонне К5 направляется на ректификацию вместе с сырьём. Из газов стабилизации в абсорбере К6 извлекается изопентан подачей части гексановой фракции, отбираемой из К4. Балансовое количество гексановой фракции поступает в анологичную секцию изомеризации (при низком содержании н-гексана в сырье его изомеризуют в смеси с н-пентаном).