С. В. Абрамов ОАО союзцветметавтоматика н. Е. Мальцев, Д. В. Исаев, Р. В. Меликянц, В. Л каневский, Технология сухого помола является завершающей стадией производства цемента на цементном заводе Пик
Вид материала | Документы |
СодержаниеGE Fanuc Automation. |
- В. П. Топчаев (оао «Союзцветметавтоматика») ОАО «Союзцветметавтоматика», 14.51kb.
- Проект по открытию линии сухого производства цемента с комплексным применением клинкера, 141.51kb.
- Программа преддипломной практики студентов специальности 1-36 01 01 «Технология машиностроения», 336.91kb.
- В настоящее время в г. Бобруйске по ул. Береговой продолжается строительство канализацонно-, 17.6kb.
- Шухова 9-12 октября был проведен Международный конгресс производителей цемента «Производство, 238.63kb.
- Организация производства композитного цемента марок М600 М1200 на основе шлаков металлургического, 62.11kb.
- Применение центробежно-ударных мельниц «МЦ» при помоле цемента кушка, 76.77kb.
- Рабочая программа и методические указания к выполнению контрольной работы для заочной, 305.14kb.
- Рассказы альпинистов о восхождениях на пик Ленина, 2278.89kb.
- Программа вступительного экзамена по специальности 05. 27. 06 «Технология и оборудование, 81.6kb.
Опыт автоматизации технологического процесса сухого помола в цементном производстве.
ПО «ГЛИНОЗЕМ»
Е.А Беликов, В.А. Попов,
С.В. Абрамов
ОАО «СОЮЗЦВЕТМЕТАВТОМАТИКА
Н.Е.Мальцев, Д.В.Исаев,
Р.В.Меликянц, В.Л Каневский,
Технология сухого помола является завершающей стадией производства цемента
на цементном заводе «Пикалевский Глинозем». Основными требования, которым должен соответствовать готовый продукт, являются химический и гранулометричесчкий состав (удельная поверхность и остаток на сите).
На качество и количество произведенного продукта влияют: колебания расходов подаваемого материала, нарушение весового соотношения между расходами компонентов входного потока, колебания физических свойств и химического состава материала, изменение характеристик оборудования и др. факторы.
Для контроля качества цемента на соответствие заданной сортности производится химический и ситовой анализ готового продукта. По процентному содержанию гипса в готовом цементе корректируется соотношение гипс – клинкер и шлак – клинкер, по результатам контроля удельной поверхности - нагрузка мельницы. Концентрация гипса определяется по содержанию SO3 при химическом анализе.
Качество цемента также зависит от степени загрузки мельницы. Вредна как недогрузка, так и перегрузка мельницы. В первом случае материал слишком сильно измельчается, что повышает энергозатраты, а во втором - материал измельчается недостаточно, что снижает качество цемента.
Целью разработки и внедрения АСУ сухим помолом цементного производства является повышение качества готового продукта, снижение затрат энергии, повышение оперативности управления всем технологическим циклом.
На рис.1 показана укрупненная структура управления процессом сухого помола. Эта система обеспечивает автоматическую стабилизацию суммарного количества подаваемого на переработку материала, и заданного соотношения расходов клинкера шлака и гипса. Обеспечивается также контроль количества материала, находящегося в мельнице и представление технологическому персоналу информации, необходимой для повышения качества и оперативности управления.
Одной из наиболее актуальных задач является стабилизация химического состава готового продукта, а, следовательно, повышение его качества. Решение этой задачи достигается путем расчета требуемого соотношения расходов компонентов смеси и его автоматической стабилизации.
На химический состав готового цемента влияют влага и примеси, содержащиеся в подаваемых на переработку клинкере, шлаке и гипсовом камне. Предполагается, что наибольшее влияние на качество продукции оказывают колебания влаги в гипсе, которая может составлять от 2.5% до 7 %, и в шлаке - до 15%.
Вырабатываемая марка цемента определяет требования к его к составу. Принимаем, что требуемое содержание клинкера C10 , шлака C20 , гипса C30



Система дозирования
гипса, шлака,
клинкера



Электро
фильтры



Мельница










Контроль режима аспирации
Контроль режима загрузки
Химический
и ситовой
анализ



Блок анализа и выработки управляющих воздейсвий
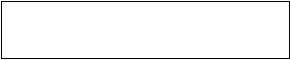

Рис.1
В качестве исходных данных при решении задачи используются значения средних расходов компонентов g1, g2, и g3 (т/ч) за предшествующий химическому анализу интервал времени. Искомые расходы клинкера g1x, , шлака g2x и гипса g3x можно найти из соотношений:
g1x 2*g2x 3*g3x
-------------------- = C10 -------------------- = C20 ----------------------- = C30 (1)
g1x +2*g2x + 3*g3x g1x +2*g2x + 3*g3x g1x + 2*g2x + 3*g3x
Где, 2 - коэффициент, равный весовой доле сухого шлака в исходном материале;
3 - коэффициент, равный весовой доле сухого гипса в исходном материале.
Соотношения (1) учитывают влагу, содержащуюся в сырьевых компонентах. Влажностью клинкера поступающего после прокалки можно пренебречь, а влажность гипса и шлака учитывается при расчете.
Так как данные уравнения (1) являются зависимыми (1=C10 C20 C30), то решение этой системы не будет однозначным. Поэтому один из определяемых компонентов можно положить равным произвольному значению, например g1x = q , тогда два других расхода будут зависеть от этого параметра .
После преобразований получим:
g1x = q (2)
g2x =( q / 2 ) * C20 / C10 (3)
g3x = (q 3)* C30 C10 (4)
Так как влажность сырьевых материалов при поступлении со склада не определяется, корректировка расходов может быть произведена только после поступления данных химического анализа готового продукта поскольку до поступления результатов анализа в решении (2–4) величины коэффициентов 2, 3 и параметра q не определены.
Учитывая значения концентраций клинкера C1, гипса C2 и шлака C3 в цементе, полученные в результате химанализа можно записать:
g1 2* g2 3*g3
-------------------- = C1 -------------------- = C2 ------------------ = C3
g1 +2* g2 + 3*g3 g1 +2* g2 + 3*g3 g1+ 2*g2 + 3*g3
где g1, g2, и g3 (т/ч) средние значения расходов за предшествующий химическому анализу интервал времени.
Из этих соотношений находятся коэффициенты 2 и 3:
2 = ( g1 g2 )*( C2 C1) (5)
3 = (g1/ g3 )*( C3 C1) (6)
Параметр q можно найти из дополнительного условия, которое определяется требованиями технологического процесса получения цемента:
Можно потребовать, чтобы сохранялся расход клинкера g1x = g1 т. е. q = g1. Тогда решение принимает вид:
g1x = g1
g2x = g2 * ( C20 / C10 ) * ( C1 / C2 )
g3x = g3 * (C30 C10) * ( C1 / C3 )
Или потребовать, чтобы загрузка мельницы поддерживалась на заданном уровне Q т. е. Q = g1x + g2x + g3x. Тогда q находится из соотношения:
Q
q = --------------------------------------------------------- (7)
(1 +(1 / 2 ) * ( C20 / C10)+ (1 3)* (C30 C10) )
где 2 и 3 определяются по формулам (5,6).
Подставляя вычисленное по формуле (7) значение q в формулы (2-4), получим значения расходов клинкера , шлака и гипса в этом случае.
Влажность входных материалов, как правило, не остается постоянной во времени и корретировка соотношения расходов обеспечивает компенсацию колебаний влажности. При этом на каждом цикле пересчета исходными для расчета являются значения, рассчитанные на предыдущем интервале т. е. g1 = g1x g2 = g2x g3= g3x .
Очевидно, что значение загрузки Q определяется в зависимости от параметров технологического процесса, таких как производительность мельницы, гранулометрический состав цемента и др.
Структура системы автоматического управления подачей клинкера, шлака и гипса приведена на рис.2.
Рис.2
Задание от оператора





Дозатор
гипса
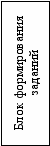
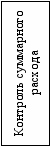



Корректировка
по химанализу
Дозатор
шлакаа




Корректировка по нагрузке
Дозатор
клинкераа

Корректировка по
разрежению


Рис.2
Алгоритм управления подачей материалов, при корректировке соотношений, предусматривает стабилизацию их суммарного расхода, т. е. стабилизируется значение Q по соотношению (7).
При внедрении систем дозирования компонентов смеси была произведена замена существовавших ранее вибрационных и тарельчатых питателей, на комплектные ленточные дозаторы, в состав которых входят все элементы, необходимые для решения поставленной задачи. Принцип действия дозатора иллюстрируется на рис.3.



FANUC
Тензодатчик
Сеть
3380В
Датчик








Тензодатчик











VLT2800



4 - 20мА
Инвертор

Задание от верхнего
уровня системы

скорости

Рис.3
Сигналы, пропорциональные массе материала на ленте питателя и скорости движения ленты, поступают в контроллер. По этим сигналам рассчитывается величина расхода g(т\час) и определяется рассогласование Х = g - gЗД (gЗД задание от верхнего уровня системы) Поддержание расхода обеспечивается путем воздействия на частоту вращения привода дозатора.
Э


Алгоритм формирования управляющего воздействия в функционирующей в
настоящее время системе учитывает статические и динамические характеристики объекта – потребителя смеси и ленточного питателя. В этой системе для формирования управляющего воздействия используется интегральный частотно-импульсной модулятор (ИЧИМ). На рис.4 приведена структурная схема системы автоматического управления расходом материала (САУ РМ).
Возмущ.
воздействие

g
U(t)




ЛП
gЗД








ИЧИМ
Ф
x(t)
y(t)
Рис.4
ЛП – ленточный питатель; U(t) –управляющее воздействие; Ф – фиксатор с передаточной функцией Wф(p) = K1\ p, y(t)-последовательность -импульсов на выходе ИЧИМ.
ИЧИ- модулятор (рис.5) состоит из последовательно соединенных интегратора (И) и устройства сброса (УС).


y(t)





x(t)
U(t)
И
УС

Рис.5
Интегральный частотно – импульсный модулятор описывается двумя характеристиками: модуляционной и амплитудной.
М
одуляционная характеристика ИЧИМ описывает зависимость моментов возникновения импульсов от входного сигнала (в эти же моменты времени УС обнуляет U(t)). Обозначим эти моменты как tk[x(t)], тогда
tk[x(t)]

y
tk-1
(t) = KИ x()d = ; при k = 1, 2, … (8)
Это нелинейное рекуррентное уравнение позволяет последовательно вычислять моменты времени tk , если известны моменты tk-1.
Амплитудная характеристика ИЧИМ описывает зависимость амплитуд импульсов от входного сигнала. Из описания принципа действия модулятора следует, что амплитуда импульсов y(t) на его выходе постоянна, а меняется только их знак.
y[x(t)] = sign Uk[x(t)] (9)
В соответствии с принятым алгоритмом работы САУ РМ, рассогласование x, интегрируется по соотношению (8) до того момента пока значение выходной координаты интегратора не достигнет заданного в программе значения (знак соответствует знаку рассогласования x) и в этот момент фиксируется импульс, генерируемый ИЧИМ [1]. Этот импульс, преобразуется звеном с передаточной функцией Wф(p)= К1/р, при этом U(tk)=U(tк-1)+ U(tk), здесь U(tk) – результат преобразования импульса фиксатором Ф (рис.4). Переменная величина U(t) в САУ РМ имеет размерность тока, подаваемого на вход инвертора для корректировки скорости движения ленты питателя.
Эта система имеет три параметра настройки: KИ, и К1. Параметры KИ и определяют интервалы между импульсами на выходе ИЧИМ, т.е частоту замыкания нелинейной импульсной САУ РМ. Эти параметры являются эквивалентом коэффициента интегрирования при ПИ - законе регулирования линейной непрерывной САУ. Параметр K1 – определяет величину U(tk) и является эквивалентом коэффициента усиления регулятора.
Значения параметров настроек определяются исходя из динамических и статических характеристикам ленточных питателей, которые в свою очередь зависят от абсолютных величин скорости ленты, диапазона, в котором изменяется этот параметр, величин возмущений, определяемых характером колебаний физических свойств материала, амплитудой изменения заданий и рядом других факторов.
Описанный алгоритм функционирования САУ РМ обуславливает ее преимущества по сравнению с линейными как непрерывными, так и импульсными системами. Эти преимущества заключаются в том, эта система, практически, не имеет зоны нечувствительности на входе регулятора т.к. даже при малых значениях x управляющее воздействие будет сформировано по соотношению (8), при этом частота этих воздействий оказывается низкой, что также улучшает качество работы системы. Кроме того формирование управляющего воздействия по соотношению (8) исключает реакцию системы на знакопеременное отклонение x при высокой частоте смены знака, а также при относительно небольших амплитудах знакопеременных отклонениях рассогласования x. Абсолютные значения этих частот и амплитуд определяются настройками системы. Это свойство системы также снижает частоту управляющих воздействий, что повышает качество работы САУ РМ.
Эта система также формирует данные о количестве дозируемого материала за выбираемые интервалы времени (час, смена, сутки и др.), сравнивает их с нормативными данными (заданными значениями), и обеспечивает поддержание требуемого соотношения расходов дозируемых компонентов.
Для оценки качества работы САУ РМ был проведен анализ ее функционирования.
Методика анализа заключалась в оценке статической ошибки системы и среднеквадратичного отклонения от фактических значений средних расходов. Учитывая, что мельница как объект управления является инерционным объектом, качество управления должно определяться по сглаженным (усредненным за выбираемый интервал времени) значениям расходов компонентов смеси. Интервал усреднения определяется динамической характеристикой мельницы по каналу «качество смеси – качество цемента на выходе мельницы». Учитывая реальное время пребывания материала в мельницах сухого помола, этот интервал усреднения принят равным 10 минутам. Таким образом, при анализе качества работы системы, определялись отклонения от задания усредненных за 10 минут расходов материалов (т.к. отклонение от задания среднего расхода с положительным знаком на этом интервале не может быть скомпенсировано отрицательным отклонением на следующем).
Для более полной оценки исходные массивы были обработаны по алгоритмам как скользящего, так и дискретного усреднения.
В качестве исходных для анализа были обработаны массивы данных, полученные в режиме промышленной эксплуатации системы.
Анализ функционирования действующей системы дал возможность сделать следующие выводы:
Система обеспечивает стабилизацию расходов гипса, шлака и клинкера, при этом статическая ошибка составляет g - gзд =3,174 -3,15 = 0,024т\час, или 0,76%, а СКО – 0,06т\час или относительное СКО – 1,9%.
Гранулометрический состав цемента существенно зависит от нагрузки (количества материала, находящегося в агрегате), Этот параметр контролируется с помощью 3х - канального Виброметра типа 25-38 фирмы Брюлькер.
. Зависимость нагрузки мельницы от входного потока носит нелинейный характер и в зависимости от его значения система может находиться в устойчивом или неустойчивом состоянии. Учитывая, что производительность мельницы, естественно, возрастает при увеличении нагрузки, нагрузку целесообразно увеличивать, однако ее недопустимо большой рост может привести к неустойчивому состоянию, при котором
резко снизится качество и может наступить аварийный режим. Поэтому при выходе нагрузки за допустимое значение, предусматривается выдача соответствующего сигнала оператору. В этом случае снижается задание на суммарный входной поток, без изменения соотношения расходов клинкера, шлака и гипса, такое же управляющее воздействие осуществляется и в том случае, когда анализы грансостава свидетельствуют об укрупнении частиц. Расчет корректировки задания на суммарное количество материала по результатам химического анализа предусматривается программным модулем GRAN.
Учитывая влияние на качество работы мельниц разрежения до и после электрофильтров, в системе предусматривается управление режимом аспирации с целью стабилизации разрежения на выходе мельницы и после электрофильтров.
В состав АСУ сухого помола для стабилизации химического состава шихты разработан программный модуль CHEM. Этот модуль получает информацию о величинах текущих расходов клинкера, шлака, гипса и результатах химанализов готового продукта. Запускается модуль в момент поступления очередных данных по химическому составу. Эти данные сравнивается с требуемым химсоставом цемента и, если отклонение фактического содержания серы от требуемого превышает допустимую величину, в модуле (по соотношению 7) рассчитывается задание на корректировку соотношения расходов клинкера, шлака и гипса.
При создании АСУ ТП сухого помола использованы программируемые контроллеры GE Fanuc Automation. Программное обеспечение разработано на базе пакета FIX и предусматривает вывод на экран графиков изменения параметров за различные интервалы времени (час, смена, сутки и др.). Информация необходимая оператору-технологу для ведения технологического процесса выводится на экран дисплея в виде различных видеограмм. На рис.6 приведена видеограмма, которая выводится на экран при запуске системы.
Рассмотрению вопросов автоматического управления загрузкой мельниц и режимом аспирации будут посвящены последующие публикации.
В результате внедрения АСУ процессом сухого помола основные показатели качества работы мельниц существенно улучшились за счет уменьшения колебаний химического и гранулометрического состава цемента.
Использованные источники
1. В.Л. Каневский, Ю.С. Попков и др. «Использование интегральной частотно-импульсной модуляции при автоматизации металлургических процессов» Москва «Металлургия» 1976