7. 3 Функциональные зоны склада. Технико-экономические показатели работы склада
Вид материала | Документы |
- Задачи курсовой работы: Охарактеризовать основные технико экономические показатели, 50.17kb.
- Лекция религия и невроз, 7200.62kb.
- Зарипов Рашид Рафкатович (нижнетагильское представительство) Проверил: Нижний Тагил, 54.18kb.
- Расчет технико-экономических показателей, 151.02kb.
- Содержание работы, 275.53kb.
- Сравнительные технико-экономические показатели работы пнл 8-40 и Плуга 7-ми корпусного, 19.52kb.
- Задачи планирования их технико-экономические показатели эксплутационных затрат, 22.93kb.
- Технико-экономические показатели, 37.6kb.
- Основные технико-экономические показатели, 47.72kb.
- 3 Основные технико-экономические показатели проекта, 586.11kb.
7.3 Функциональные зоны склада. Технико-экономические показатели работы склада
Для обеспечения эффективной работы склад обычно делят на несколько зон.
Зона хранения – это часть склада, занимаемая оборудованием, предназначенным для хранения товаров. Зона хранения включает следующие площади: полезную площадь, занятую хранимыми материалами (в штабелях, на стеллажах); проезды для внутрискладских средств механизации; технологические проходы между оборудованием; противопожарные разрывы, необходимые по требованиям безопасности.
Зона сортировки и комплектования предназначена для приемки заказов, сортировки, комплектования, упаковки и маркировки отобранных грузов, их перемещения в зону погрузки.
Зоны экспедирования предназначены для учета получаемых и отправляемых грузов, проверки и составления транспортно-сопроводительной документации.
При размещении товаров необходимо исходить из частоты их заказов. Так, товары с высокой частотой заказов надо размещать в горячей зоне (вблизи зоны отгрузки); со средней частотой – в теплой (в середине склада); с низкой частотой – в холодной (вдали от зоны отгрузки). В этих зонах товары должны размещаться в зависимости от их размеров (малые, средние и крупные), что значительно снижает трудозатраты на отборку товаров при подготовке заказов.
При этом товары с ограниченным сроком годности необходимо хранить отдельно, особенно если склад небольшой и не оборудован складским модулем ERP-систем или WMS-системой. В этом случае отдельное хранение таких товаров единственно возможный способ не «забыть» о сроке годности товаров и не начать отпускать более «свежий» товар до того как распродана предыдущая партия, а также своевременно информировать о том, что отдельные товары требуют немедленной реализации.
Существует четыре основные группы технико-экономических показателей работы склада:
-показатели характеризующие интенсивность работы склада;
-показатели характеризующие эффективность использования площадей склада;
-показатели характеризующие уровень сохранности грузов и финансовые показатели работы склада;
-показатели характеризующие уровень оптимизации склада.
К показателям, характеризующим интенсивность работы склада, относятся:
-грузооборот (товарооборот) склада – стоимость (масса) отпущенных со склада или поступивших на склад грузов за определенный период времени;
-удельный грузооборот – товаро-, грузооборот на единицу площади склада;
-средний запас – характеризует средний запас товаров за период и определяется в натуральном и стоимостном выражении;
-коэффициент неравномерной загрузки склада – отношение максимального товарооборота (грузооборота) к среднему обороту склада за период времени;
-оборачиваемость – отношение товарооборота к среднему уровню запаса за период;
-длительность оборота (средний срок хранения запасов) – отношение длительности планового периода к оборачиваемости склада;
-готовность к поставке – отношение выполненных заказов к общему числу поступивших;
-ошибки в поставках – количество и доля ошибок в поставках к общему числу выполненных заказов;
К показателям, характеризующим эффективность использования площадей склада, относятся следующие:
-вместимость – максимальная загрузка склада (измеряется в тоннах, кубических метрах и др.);
-полезная площадь склада (Sпол) – площадь склада непосредственно занятая материально-техническими ресурсами, т.е. площадь зоны хранения:
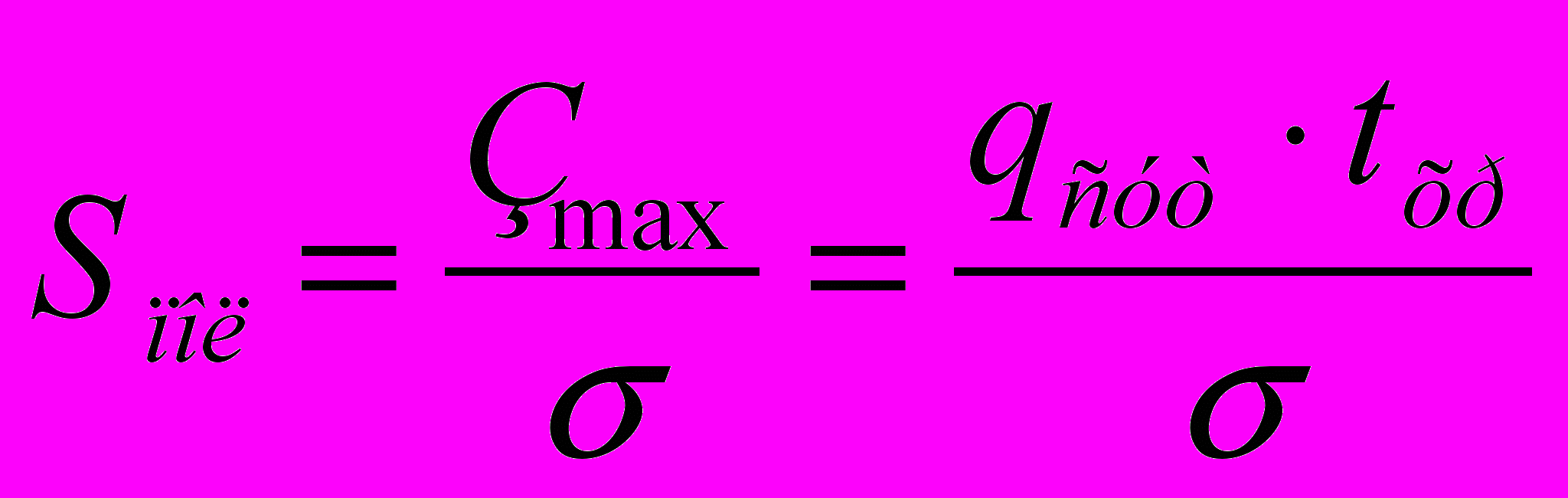
где Зmax – максимальный запас материала на складе, т; qсут – среднесуточное поступление материалов на склад с учетом неравномерности этого процесса, т/сут; tхр – средняя продолжительность хранения материалов на складе, суток;
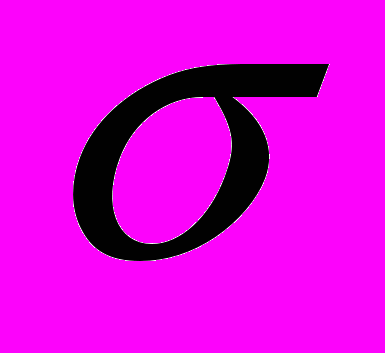
Среднесуточное поступление материалов на склад:
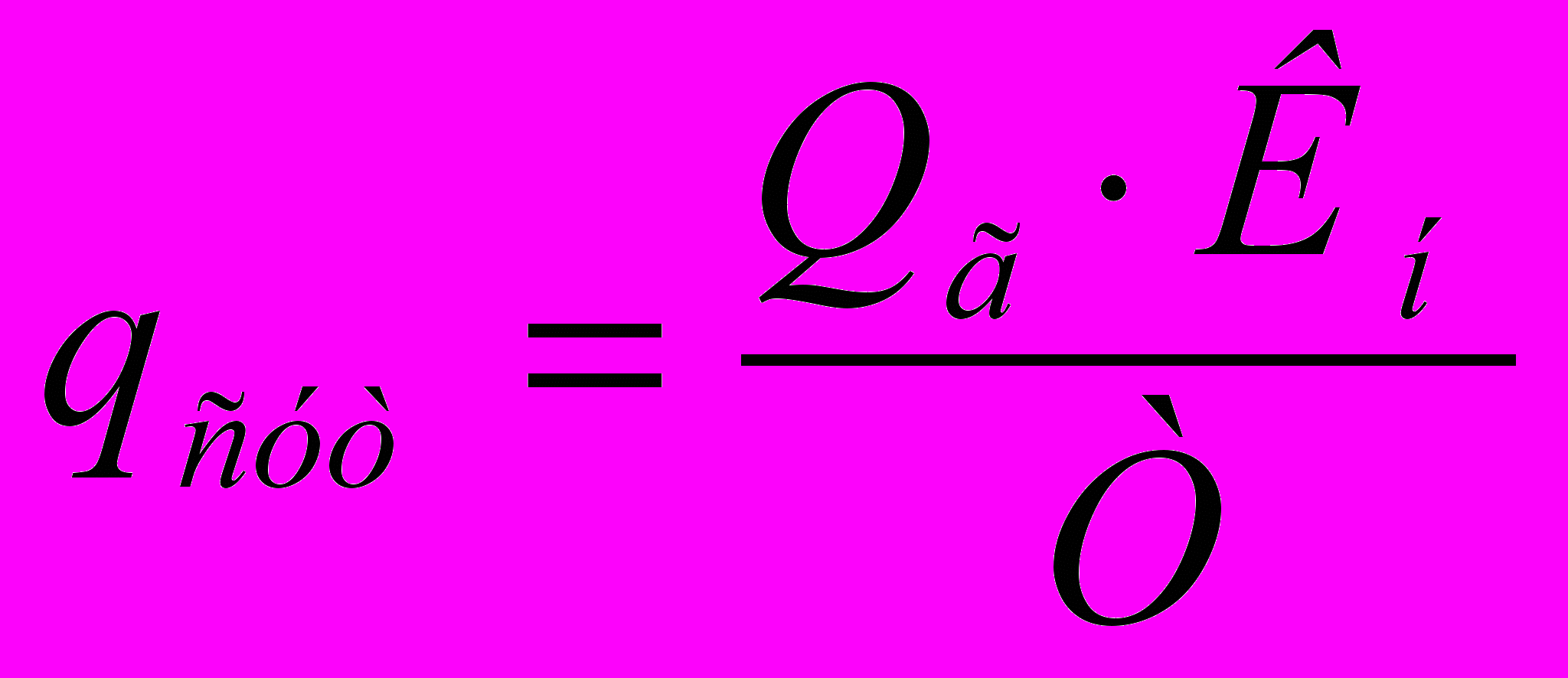
где Qг – годовой грузооборот склада, т.; Кн – коэффициент неравномерного поступления материалов на склад, определяемый как отношение грузооборота напряженного месяца к среднемесячному грузообороту (1,2-1,4); Т – количество дней работы склада.
Площадь приемочной и отправочной экспедиции (Sпр):
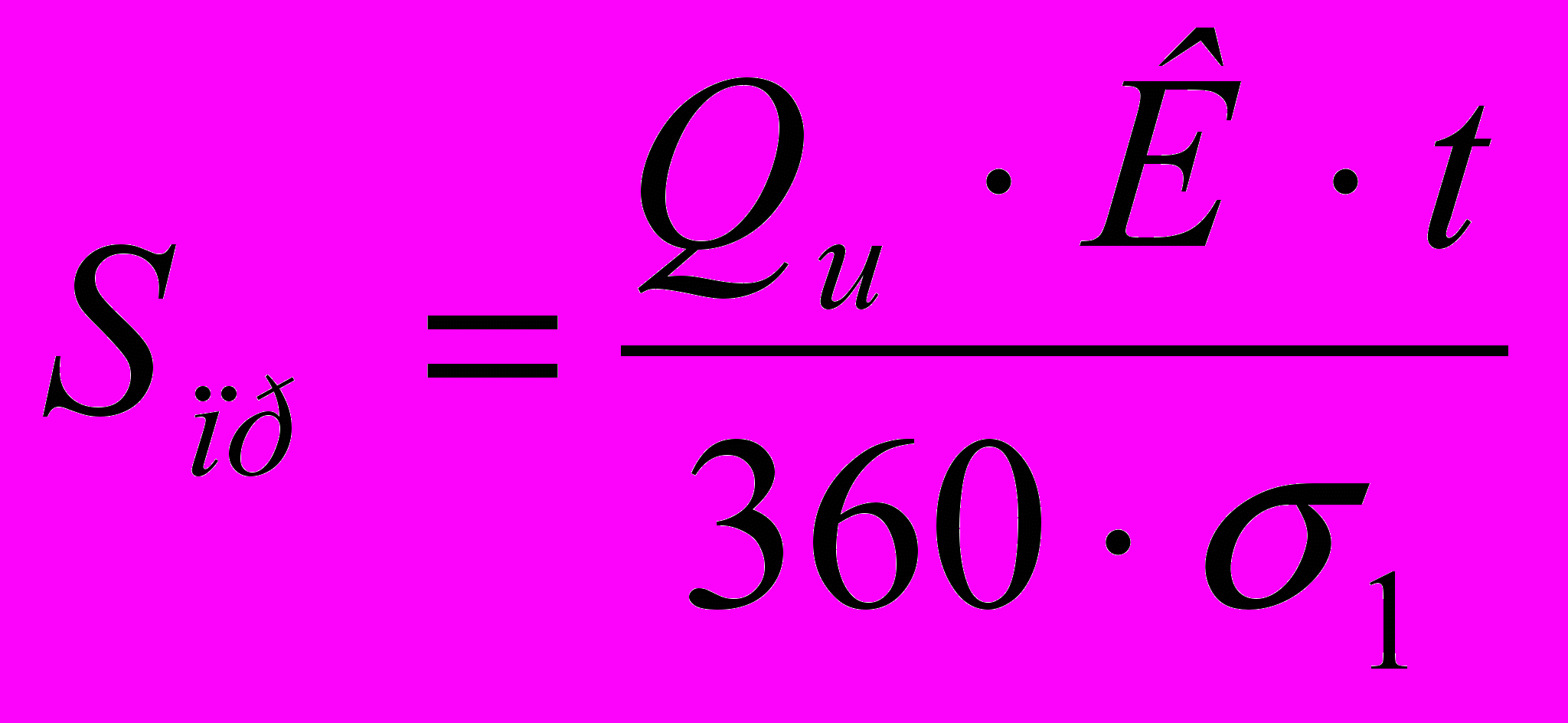
где Qг – годовой грузооборот склада, т.; Кн – коэффициент неравномерного поступления материалов на склад, определяемый как отношение грузооборота напряженного месяца к среднемесячному грузообороту (1,2-1,4); t – количество дней нахождения материала в приемочной или отправочной экспедиции (1-2 дня);
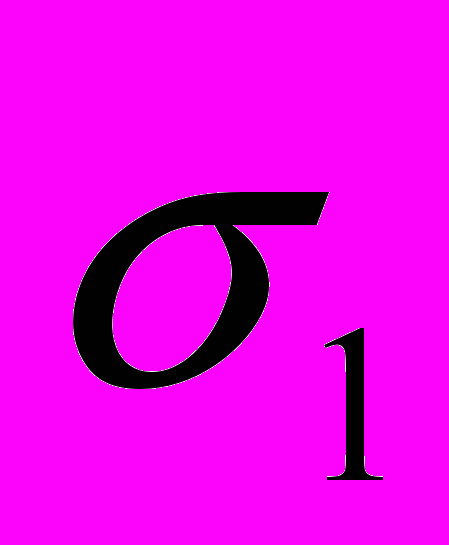
-грузонапряженность склада – допустимая нагрузка на 1 м2 площади склада;
-степень использования объема склада.
К показателям, характеризующим уровень сохранности грузов и финансовые показатели работы склада, относятся следующие:
-потери от хранения – число случаев и стоимость хищений и порчи товаров по вине работников склада;
-доля затрат на складирование на 1 м2 площади склада (нетто, брутто), на 1 м3;
-прибыль и рентабельность склада за период времени;
-уровень механизации и автоматизации и др.
К показателям, характеризующим уровень оптимизации склада, относятся следующие:
-степень охвата рабочих механизированным трудом - определяется отношением числа рабочих, выполняющих работу механизированным способом, к общему числу рабочих, занятых на складских работах;
-уровень механизации складских работ – определяется отношением объема механизированных работ к объему выполненных работ;
-объем механизированных работ – определяется как произведение грузопотока, перерабатываемого механизмами, на количество перевалок грузов механизмами;
-уровень оснащенности склада вспомогательными средствами (поддоны, тара) – отношение объема перевозок с помощью вспомогательных средств к общему объему грузооборота.
Расчет необходимого количества машин на складе осуществляется по формуле:
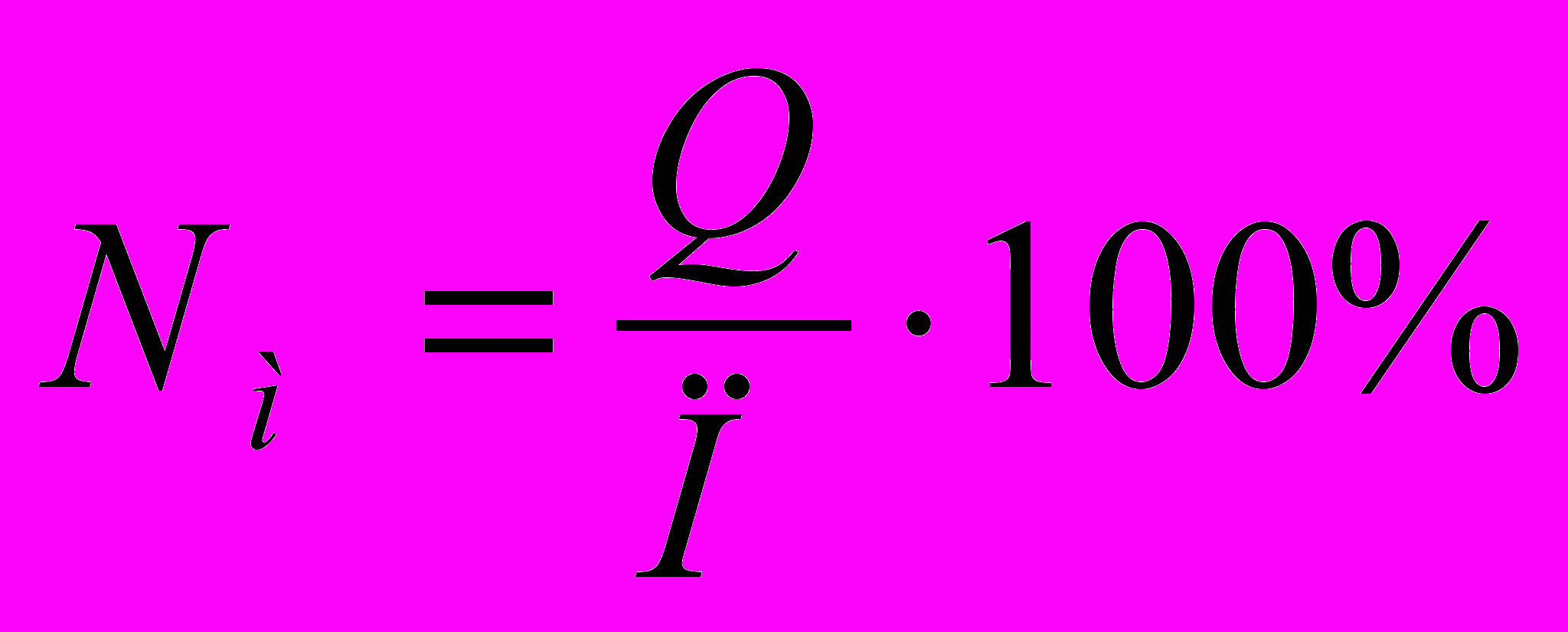
где Q – количество перерабатываемого груза за определенный период (день, смену, месяц), т.; П – производительность машины за определенный период (день, смену, месяц), т/ч.
Сменная производительность машины циклического действия определяется по формуле:

где Пч – часовая производительность машины, т/ч; Т – продолжительность рабочей смены, ч; Ки.в. – коэффициент использования времени смены.
Часовая производительность машины циклического действия равна:
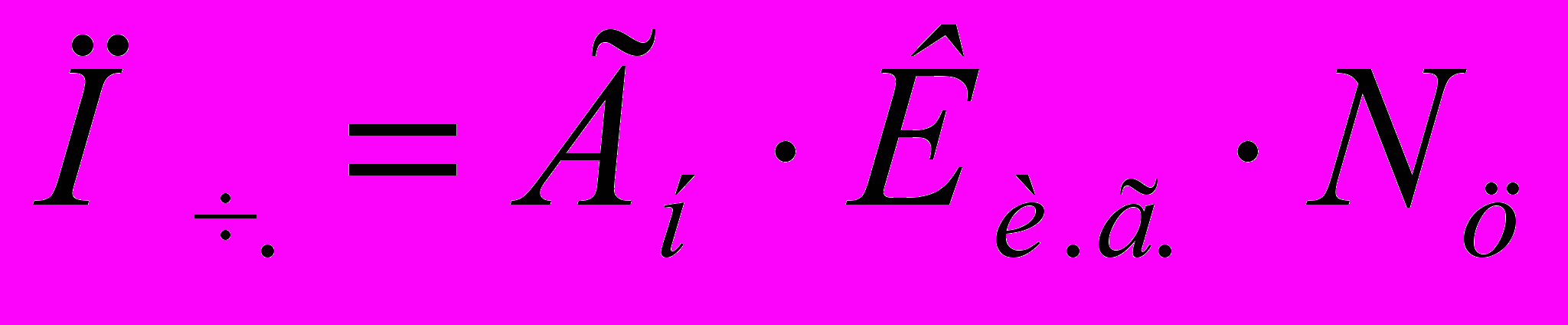
где Гн – номинальная (паспортная) грузоподъемность машины, т; Ки.г. – коэффициент использования грузоподъемности машины; Nц – число рабочих циклов машины в час.
Количество рабочих циклов машины, совершаемых за час, рассчитывают по формуле:
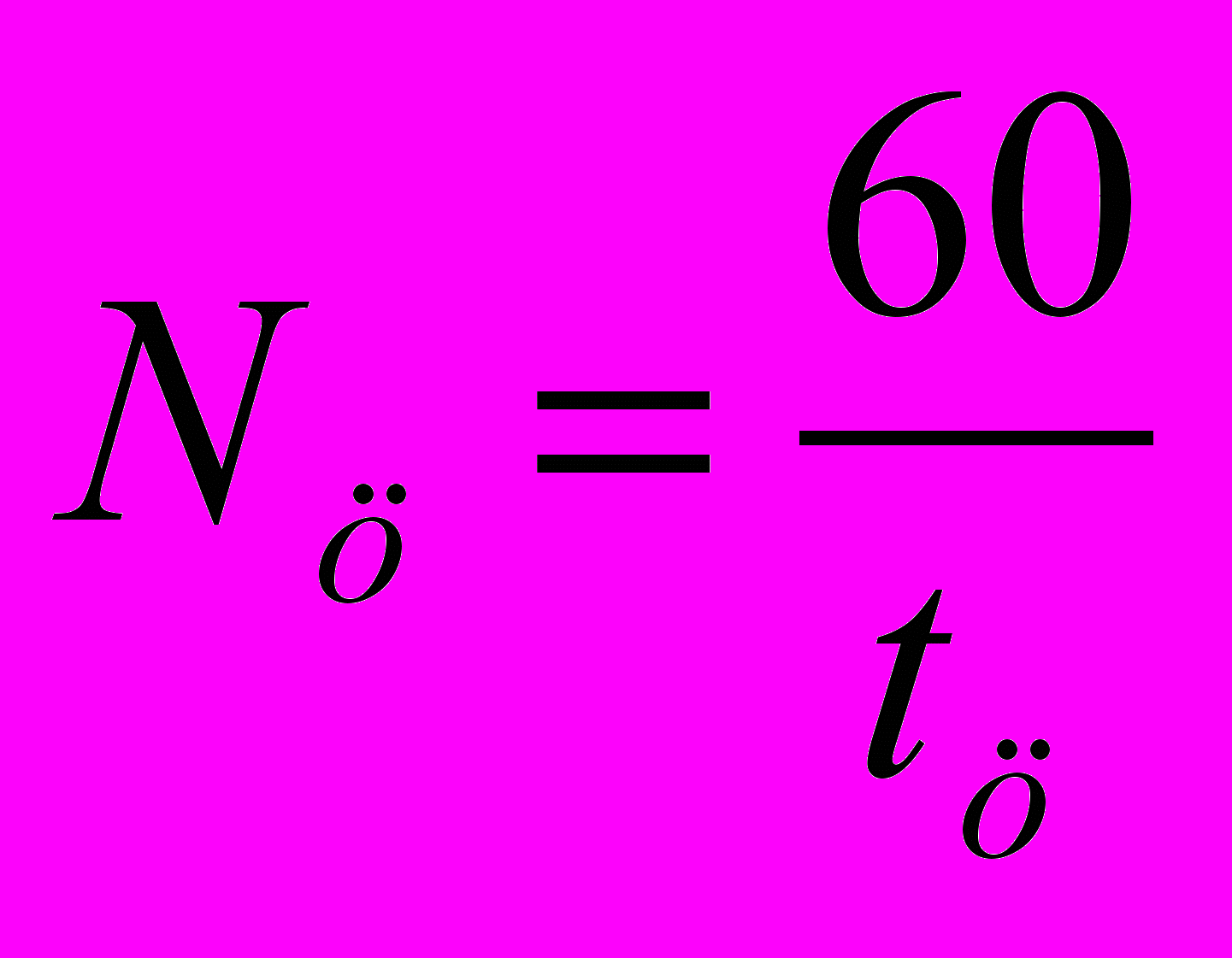
где tц – время рабочего цикла, мин.
Часовая производительность машины непрерывного действия определяется по формуле:
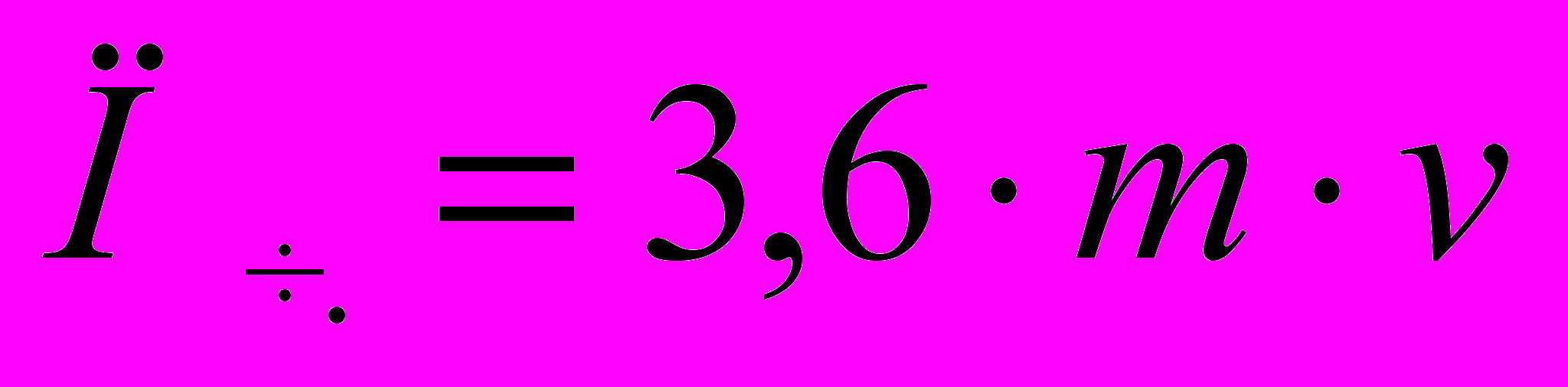
где m – вес груза на одном погонном метре несущего элемента машины (ленты конвейера, транспортера), кг; v – скорость движения ленты, м/с.
При транспортировке тарно-штучных грузов часовая производительность равна:
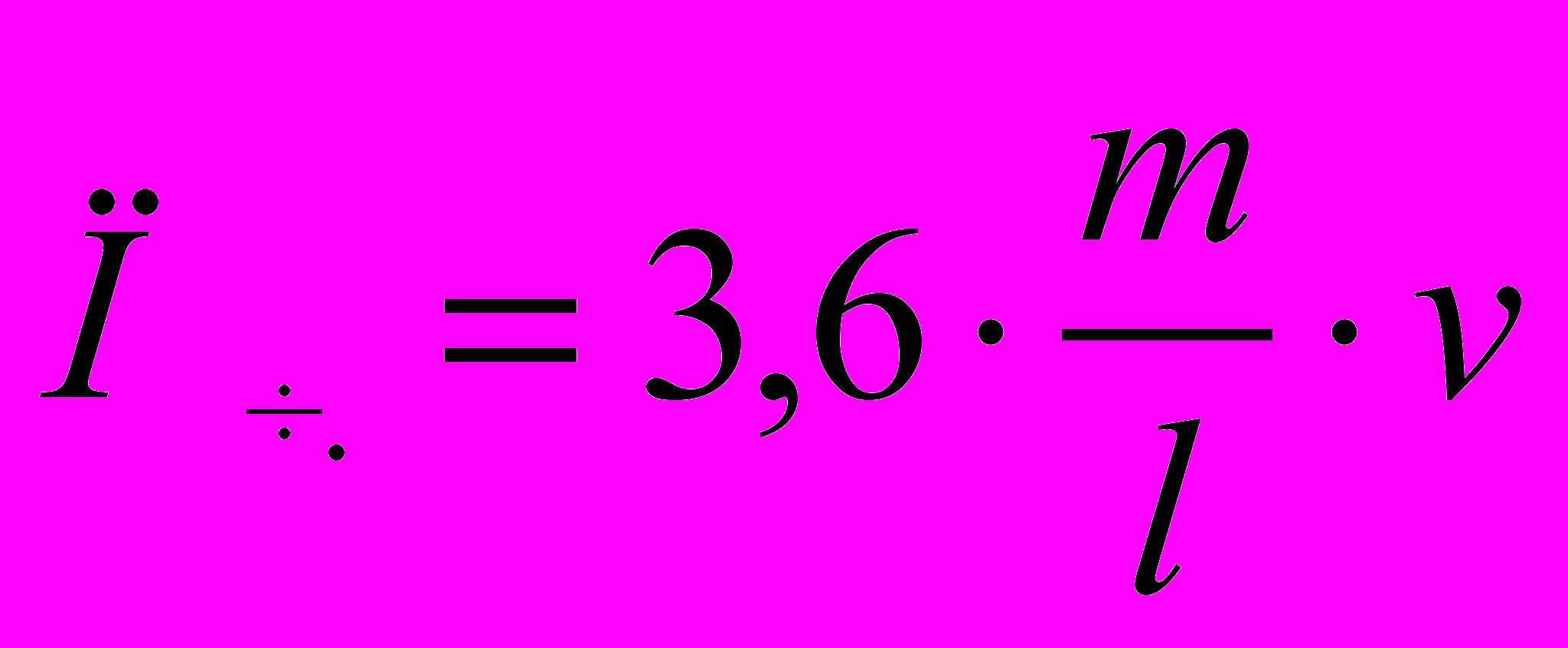
где l – среднее расстояние между единицами.

где
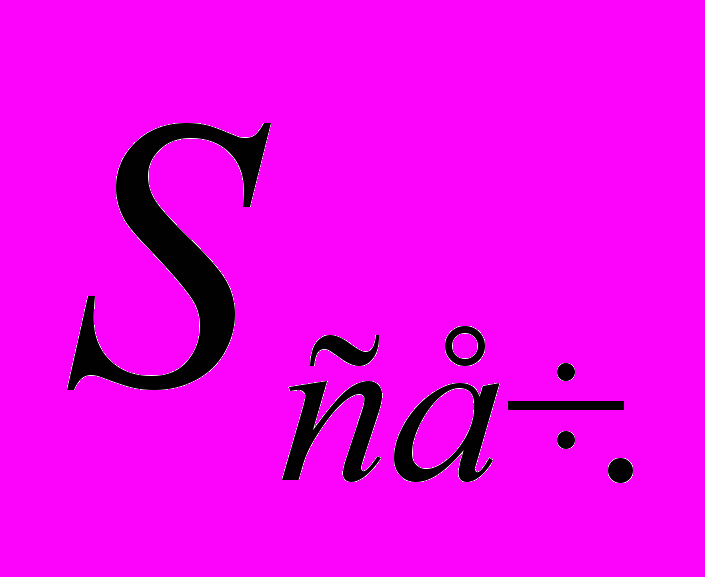
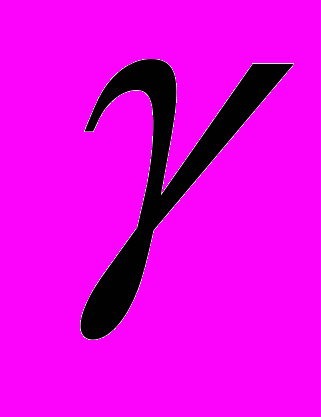
Предельный срок хранения на складе рассчитывается по формуле:
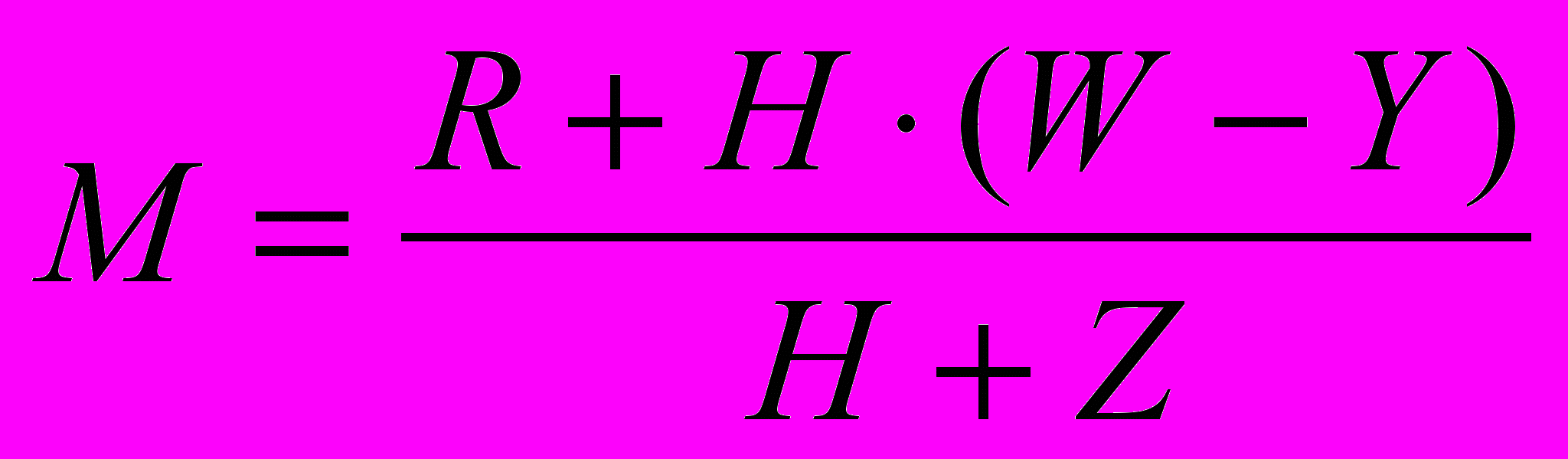
где М – критический срок по позиции, дольше которого ее хранение на складе будет убыточным, мес.; R – средняя маржинальная рентабельность продаж по этой позиции ((выручка - себестоимость товаров) / себестоимость товаров), %; Н – альтернативная доходность вложенных в запасы денег (например, проценты по депозитам в банке), % в мес.; Z – переменные затраты за месяц, связанные с обслуживанием и хранением анализируемых товаров, % от их себестоимости; W – отсрочка платежа, предоставленная поставщиком товара, мес.; Y – средняя отсрочка платежа клиентам, мес.
Продвигая свой товар на рынок сбыта, каждый распределительный склад должен определить границы рынка, где он будет иметь преимущества. Если предположить, что качество товара разных распределительных складов одинаково, то границы рынка будут напрямую зависеть от издержек на хранение единицы запасов (Схр), а также транспортных тарифов по доставке единицы запасов потребителям (Стр):
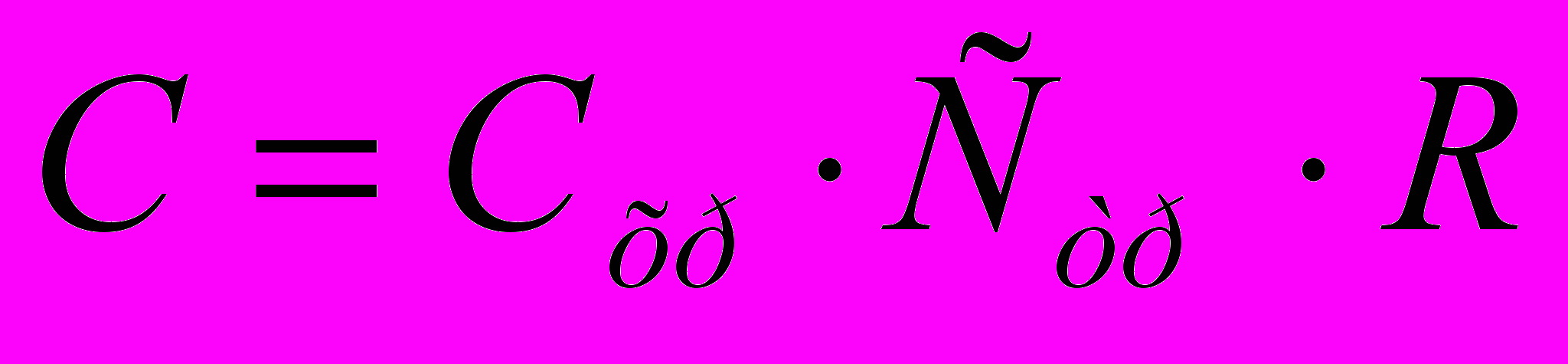
где Схр – издержки на хранение единицы запасов; Стр – транспортный тариф на перевозку груза; R – расстояние от распределительного склада до потребителя товара.
7.5 Автоматизация управления складом
Автоматизация склада сегодня может осуществляться с помощью разнообразных решений: программ складского учета, складских модулей ERP-систем и др. Однако только WMS-системы позволяют учитывать складские операции в режиме реального времени, в то время как другие решения анализируют транзакции по факту их свершения.
Система управления складом (Warehouse Management System – WMS) – система управления, обеспечивающая автоматизацию и оптимизацию всех процессов складской работы предприятия.
Универсальной системы складской автоматизации не существует, поэтому выбор WMS-системы должен прежде всего опираться на:
-стратегические и тактические цели предприятия;
-комплекс необходимых предприятию складских операций (логистика склада, логистика запасов);
-возможность интеграции складской системы с корпоративной системой предприятия (КИС, ERP), от которой и зависит эффективность бизнеса в целом.
WMS-системы принято разделять согласно двум критериям.
1) Сфера охватываемых складских операций. Разделяют две системы – в зависимости от широты сферы поддерживаемых операций:
-обеспечивающие традиционное складское товародвижение (используются, как правило, на предприятиях с единым каналом продаж);
-обеспечивающие работу мулътиканальных дистрибуционных центров в части как оптовых, так и розничных заказов (паллетный и штучный отбор соответственно).
2) Возможность модификации и адаптации системы в соответствии с потребностями предприятия. По данному критерию выделяют три класса WMS-систем:
-начального уровня – с ограниченным набором базовых функций, минимальными возможностями модификации и объемом обрабатываемой информации;
-среднего уровня – с ограниченным набором функций, но расширенными возможностями адаптации системы под нужды бизнеса;
-комплексные – с полным набором функций и возможностью значительной модификации комплекса выполняемых задач в соответствии со спецификой предприятия.
Предприятие, где внедрена WMS-система, становится уникальным носителем знаний о внутрискладской грузопереработке, выдавая сотрудникам через радиотерминалы готовые задания на выполнение операций. В заданиях определяется оптимальный вариант выполнения той или иной операции с точки зрения схемы движения товара и производительности процесса. Ни один, даже очень опытный и профессиональный, сотрудник склада не может так оперативно и быстро принимать решения по управлению адресным складом. Система также накапливает всю статистическую информацию по складским процессам, позволяет проводить инвентаризацию без остановки работы склада и формирует развернутую отчетность в любых разрезах – как по товарам, так и по сотрудникам. Все это превращает WMS-систему в неотъемлемый инструмент принятия решений руководством предприятия.
WMS-система осуществляет мониторинг работы склада и формирует полную и подробную статистику по его сотрудникам. На основании полученных данных определяются коэффициенты трудового участия (КТУ) каждого отдельного сотрудника (бригады, смены). Такие коэффициенты интегрируются в систему КРІ (Key Performance Indicators) либо систему сбалансированных показателей (Balanced Scorecard) предприятия и являются важными показателями эффективности использования трудовых ресурсов организации. Имея в распоряжении более полные и точные данные по эффективности работы сотрудников, руководство сможет построить наиболее адекватную систему мотивации персонала склада.
Кроме того, современные WMS-системы предполагают установку, помимо специализированного оборудования для сбора данных, также и электронных табло, на которых отображаются результаты сравнения складских групп. Это позволяет сформировать элемент соревнования персонала, тем самым еще более увеличив эффективность работы склада.
Одной из важных функций, обычно закладываемых в любую современную систему управления складом готовой продукции, является контроль ее качества. Такой контроль обычно возлагается на отдел сертификации. Зачастую отсутствие полноценного взаимодействия между персоналом, осуществляющим контроль качества готовой продукции, и управляющим персоналом склада может привести к нарушению или даже полной остановке технологических процессов. Системы класса WMS дают возможность контролировать наличие сертификатов на продукцию. Использование системы WMS исключает вероятность случайной отгрузки продукции, не прошедшей контроль качества, позволяет отслеживать отбор проб, необходимых для этого контроля, и отправку проб в лабораторию сертификации. Не менее важной особенностью систем автоматизированного управления складами готовой продукции является необходимость их интеграции с уже существующими на предприятиях системами корпоративного управления классов MRP (Material Requirement Planning), ERP (Enterprise Resource Planning), CSM (Chain Supply Management).
WMS-система позволяет значительно сократить издержки предприятия посредством:
-оптимизации использования ресурсов склада;
-размещения груза в наиболее подходящем месте, снижая риски его порчи, потери и затрат на его подбор;
-рационального использования как высоты, так и всего объема складского пространства и увеличения его пропускной способности благодаря технологии динамического размещения;
-увеличения производительности труда персонала за счет снижения количества «пустых» заданий.
Система позволяет улучшить и качество клиентского сервиса за счет увеличения точности подбора и комплектации заказов. Повышение качества оказываемых услуг неизбежно влечет за собой повышение лояльности клиентуры и, как следствие, рост выручки и прибыли предприятия. В современных условиях WMS-система обеспечивает потребности автоматизации складских операций не только установившему ее предприятию. Система также способствует взаимосвязи и обеспечивает прозрачность процессов для всех партнеров в цепочке поставок организации.
Система генерирует и обрабатывает информацию в едином, понятном всем участникам цепочки поставок, формате, тем самым позволяя интегрировать и персонализировать системы всех торговых партнеров. Таким образом, информация обрабатывается в едином формате в режиме реального времени, что делает работу всех предприятий – участников поставок корректной и оперативной.
7.6 Состояние складской инфраструктуры в Республике Беларусь
На начало 2009 г. в Республике Беларусь действовало более 7,29 тыс. специальных складских помещений, более 1 тыс. временных помещений, 29 хранилищ для картофеля, овощей и фруктов, 139 складов-холодильников и 59 магазинов-складов. Однако основная часть функционирующих в Беларуси складов по степени оснащенности и техническому состоянию относится к складам класса «С» (старые классические постройки советских времен в 2-4 этажа, имеющие автомобильную и железнодорожную рампу и грузовой лифт) и «D» (подвальные или неотапливаемые производственные помещения, ангары).
Многие белорусские предприятия нерационально используют свои складские помещения, не улавливая прямой зависимости между эффективной работой склада и результатами работы предприятия. Так, согласно официальным данным в 2009 году в Республике Беларусь использовались в качестве складов около 2 тыс. объектов общей площадью чуть более 1,65 млн. м2. Однако эти объекты сложно назвать современными, т.к. большинство из них возведено еще во времена СССР, когда задачи по созданию качественных условий хранения товаров на складах не ставились. Почти 75 % белорусских складских помещений принадлежат к самым низким классам – С и D.
Имеющиеся склады используются организациями оптовой торговли недостаточно эффективно, средний коэффициент использования емкости складов составляет 0,52 (например, в США этот показатель – 0,92–0,95). Уровень механизации погрузочно-разгрузочных и складских работ достаточно высок и составляет 95,2 %. Однако для механизации и автоматизации погрузочно-разгрузочных и складских работ используются машины и механизмы с высокой степенью износа.
О недостаточно эффективном использовании складских помещений свидетельствуют и данные сравнительной характеристики складских площадей организаций оптовой торговли и торговых площадей организаций розничной торговли. Это соотношение показывает, что с 1 м2 складов обслуживается около 1 м2 розничных магазинов.
Анализ состояния складской инфраструктуры оптовой торговли показывает, что ее техническое состояние и изношенность материальной базы не способствуют использованию современных технологий товародвижения. Так, только 1/10 складских помещений, расположенных в г. Минске и Минском районе, – отремонтированные или новые склады, относительно соответствующие требованиям к современной складской инфраструктуре.
Наибольшим спросом пользуются небольшие складские помещения площадью до 150 м2. Существует острая нехватка в таких площадях, поэтому многие предприятия строят собственные склады. Современные складские объекты в Минске принадлежат крупным предприятиям («Coca-Cola», «McDonalds», «Санта-Бремор», «ГИППО», «Vitalur», «Euroopt», «Prostor'e»), которые, в основном, строят небольшие склады – в среднем 2-3 тыс. м2 – класса «А» для собственных нужд.
Число проектов в сфере логистики, реализованных в 2009 году, по мировым меркам сравнительно невелико – белорусский рынок «прирос» всего на 18,1 тыс. м2. Производитель мороженого «Морозпродукт» в Марьиной Горке в 70 километрах от белорусской столицы возвел склад-холодильник на 4,6 тыс. м2, компания «Белрусинвест» в минской промышленном узле «Западный» построила склад на 9 тыс. м2, а компании «Комкон» завершила строительство складского комплекса на 4,5 тыс. м2.
И все же обеспеченность Республики Беларусь современными складскими помещениями крайне низка. Суммарная площадь складов класса «А» в Минске составляет всего 250 тыс. м2 (к примеру, в Риге и ее пригороде – почти 500 тыс. м2, в Вильнюсе – около 350 тыс. м2). В Беларуси на 1 тыс. жителей приходится 0,002 тыс. м2 складских помещений класса «А» и «В». Для сравнения в Москве на 1 тыс. жителей приходится около 120 м2 складов класса «А» и «В», в Будапеште этот показатель выше втрое, а в Варшаве и Праге - в 6 раз.
Основными владельцами складов, обслуживающих внешнеторговые грузопотоки, являются Белорусская железная дорога (общая площадь складов – 365 тыс. м2); Белорусский государственный концерн пищевой промышленности «Белгоспищепром» (общая площадь – 146 тыс. м2) и Белорусский государственный концерн по нефти и химии (общая площадь – 226 тыс. м2). Грузопоток, перерабатываемый на складах, по видам перевозок распределяется следующим образом: во внутриреспубликанском сообщении – около 60 %; на вывоз за пределы территории республики – 7,5 %; ввоз из-за пределов территории республики – 30 %; транзитный грузопоток – 2,5 %. По оценкам специалистов, транзитный потенциал Республики Беларусь сейчас используется только на 20-30 %, прежде всего, из-за отсутствия современной логистической инфраструктуры. В связи с чем, транзитный грузопоток составляет весьма незначительную величину.
Таким образом, в Республике Беларусь пока не получили достаточного развития современные складские комплексы класса «А» и «В», работающие по логистическим технологиям товародвижения. Организации оптовой торговли не имеют своевременного технологического и программного обеспечения, ориентированного на потребителя.
Основным направлением повышения уровня технического оснащения складской инфраструктуры в Республике Беларусь является реконструкция складов, для чего потребуются значительные инвестиции. Поэтому модернизация складов должна осуществляться поэтапно с привлечением собственных средств организаций, кредитов банков и средств инвесторов (в том числе иностранных).
Повышение эффективности использования складской инфраструктуры в Республике Беларусь возможно за счет:
-обновления средств механизации и автоматизации погрузочно-разгрузочных работ и складских операций;
-улучшения использования складских площадей за счет привлечения дополнительных товаропотоков.
В соответствии с Программой развития логистической системы Республики Беларусь до 2015 года, только в Минском районе планируется построить 3 складских комплекса класса «А». В целом же в Минске и Минском районе логистические объекты будут возведены на площади 450 га. Однако строительство указанных объектов затягивается в связи с отсутствием потенциальных инвесторов. Необходимо создать более выгодные условия для инвесторов, предложив ряд налоговых льгот, упрощенный порядок отведения земель под складские комплексы и гарантии защиты права собственности и иностранных инвестиций.
Реконструкция и модернизация складской инфраструктуры в Республике Беларусь позволит увеличить экономические и сервисные выгоды от их использования. Об экономических выгодах можно говорить, когда использование одного или более складов ведет к непосредственному сокращению общих логистических издержек. Экономические выгоды тесно связаны с основными функциями, которые выполняют склады, – консолидация, разукрупнение, перевалка, доработка (отсрочка) и накопление запасов.