Ватости поверхности заготовки с применением электрических разрядов, магнитострикционного эффекта, электронного и оптического излучения, плазменной струи гост 3
Вид материала | Документы |
- Лекции безопасность жизнедеятельности, 718.92kb.
- Лекции безопасность жизнедеятельности, 718.75kb.
- С. А. Останин Демодуляция оптического сигнала в усилителе лазерного излучения, 47.91kb.
- План: Особенности лазерного излучения. Природа лазерного излучения, 197.08kb.
- Сточников когерентного оптического излучения (лазеров или оптических квантовых генераторов, 175.91kb.
- Отчет об изменении климата и оценки уязвимости каспийского бассейна (туркменистан), 374.52kb.
- Информационная услуга, 1216.05kb.
- Информационная услуга, 5174.37kb.
- В космосе и на земле, 89.05kb.
- Межгосударственный стандарт гост 6564-84 "Пиломатериалы и заготовки. Правила приемки,, 122.62kb.
ВИДЫ ЭЛЕКТРОФИЗИЧЕСКОЙ
И ЭЛЕКТРОХИМИЧЕСКОЙ ОБРАБОТКИ
Электрофизическая обработка заключается в изменении формы, размеров и параметров шероховатости поверхности заготовки с применением электрических разрядов, магнитострикционного эффекта, электронного и оптического излучения, плазменной струи (ГОСТ 3.1109-82).
Электрохимическая обработка основана на принципе локального анодного растворения при высокой плотности тока (20 - 250 А/см2) и малых межэлектродных зазорах (0,02 - 0,5 мм) в проточном электролите.
На практике применяют и комбинированные методы электрофизической и химической обработки. Основные методы обработки деталей с указанием достигаемых точности обработки и параметра шероховатости указаны на рис. 17.1.
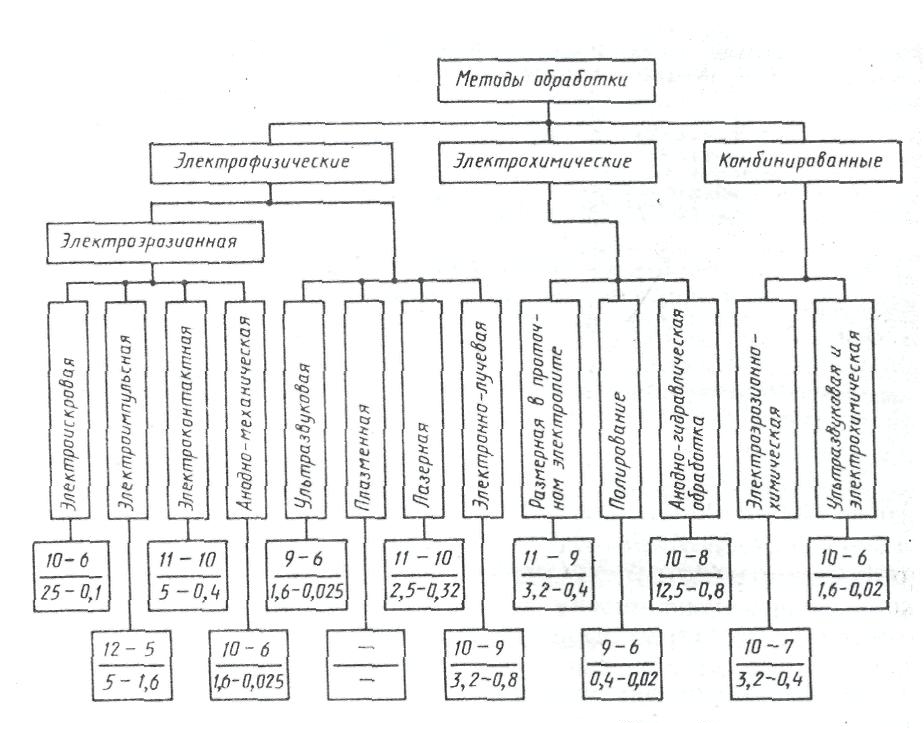
Рис.17.1. Классификация электрофизических и электрохимических способов обработки:
Цифры в числителе означают достигаемые квалитеты, в знаменателе – параметр шероховатости Ra, мкм
Электроэрозионная обработка
Разновидностями этого метода являются электроискровая и электроимпульсная обработка.
При электроискровой обработке съем металла производится кратковременными искровыми разрядами между электродами - инструментом и заготовкой (за счет электрической эрозии разрушается больше заготовка).
Принципиальная схема электроискровой обработки приведена на рис. 17.2.
При электроимпульсной обработке металл снимается импульсным дуговым разрядом. Процесс осуществляется аналогично электроискровой обработке, но при обратной полярности.
Этим методом обрабатывают фасонные полости стальных штампов, пресс-формы, формы для литья, турбинные лопатки и т. д.
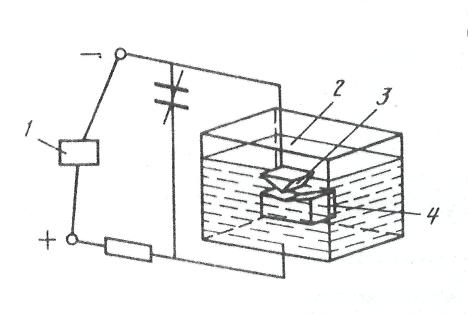
Рис.17.2. Принципиальная схема электроискровой обработки:
1 – генератор импульсов; 2 – жидкая диэлектрическая среда; 3 – электрод-инструмент; 4 – электрод-изделие.
Электроискровая и электроимпульсная обработка производится на электроэрозионных станках различного назначения: копировально-прошивочных, вырезных, электроэрозионных шлифовальных и др.
Наибольшее распространение получили копировально-прошивочные станки.
Электроконтактная обработка
Электроконтактная обработка основана на разрушении металла вследствие электротермических процессов, сочетающихся с механическим удалением образующихся продуктов.
Проходящий через место контакта инструмента и заготовки электрический ток разогревает, размягчает и плавит металл, облегчая его удаление с изделия (заготовки).
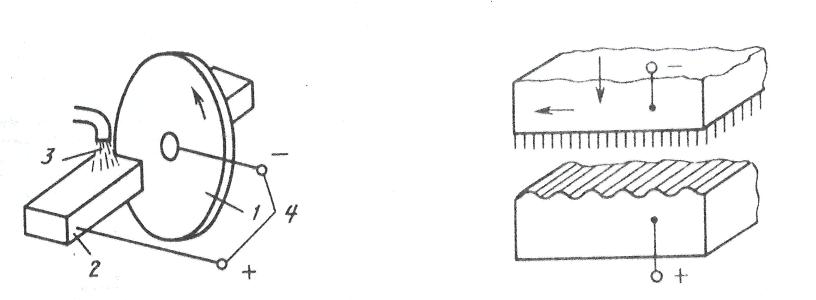
Рис.17.3. Принципиальная схема электро контактной обработки: Рис.17.4. Схема анодно-механической обработки
1 – электрод-инструмент (диск); 2 – заготовка;
3 – подача жидкости; 4 – подвод тока
Во избежание плавления инструмента его быстро вращают или искусственно охлаждают. Электроконтактную обработку применяют для удаления металла (резка, прошивание, шлифование, заточка), сглаживания гребешков неровностей и виброконтактной наплавки.
Принципиальная схема электроконтактной обработки показана на рис. 17.3. В качестве инструмента применяют диски, роликовый или чашечный инструмент (стальной, чугунный, латунный и т. п.).
Производительность метода довольно высокая: при черновой обработке (0,5 - 3) 106 мм3/мин; при точении 1000 - 10000 мм3/мин.
Анодно-механическая обработка
Анодно-механическая обработка осуществляется с помощью постоянного тока, проходящего через электролит и погруженные в него электроды. При этом происходит растворение поверхности анода заготовки и образуется пленка, которая снимается движущимся катодом (инструментом).
Операциями анодно-механической обработки являются разрезание, шлифование, затачивание, профилирование на анодно-механических станках. Инструменты - диски, ленты, профильные «шаблоны» и др.
Производительность обработки зависит от ее вида и применяемых инструментов: при разрезании диском - 2000 - 6000 мм3/мин, лентой - 3000-7000 мм3/мин.
Схема анодно-механического шлифования приведена на рис. 17.4.
Ультразвуковая обработка
Ультразвуковая обработка применяется для формообразования сложных поверхностей (отверстий любой формы, полостей, щелей и т. п.) в заготовках из твердых и хрупких материалов (закаленная сталь, твердый сплав, стекло, фарфор, алмазы и т. п.).
Различают ультразвуковую обработку свободно направленным абразивом и размерную.
В качестве абразивного материала применяют карбиды бора, кремния, алмазные порошки и др. Инструменты изготовляют из конструкционных и малолегированных сталей в зависимости от вида обработки (разрезание, сверление глубоких отверстий, шлифование, гравирование и т. п.), размеров обрабатываемой площади, твердости обрабатываемой заготовки и мощности ультразвукового преобразователя.
Ультразвуковую обработку выполняют на отечественных ультразвуковых станках, снабженных магнитострикционными преобразователями (рис. 17.5). Известны также станки с пьезокерамическими преобразователями.
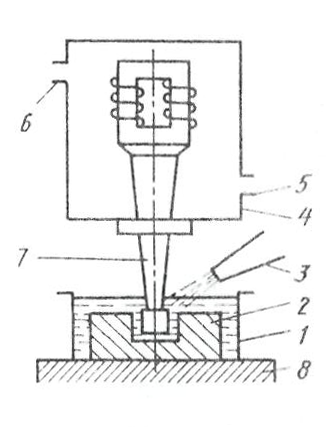
Рис.17.5. Принципиальная схема ультразвуковой обработки:
1 – ванна; 2 – изделие; 3 – подача абразивной суспензии; 4 – преобразователь;
5, 6 – вход и выход охлаждающей жидкости; 7 – инструмент; 8 – стол станка.
Производительность, точность размерной обработки ультразвуком и шероховатость поверхности после нее зависят от свойств материала (твердости и хрупкости), размеров обрабатываемых поверхностей. Производительность при обработке твердых сплавов достигает 40 - 80 мм3/мин. Отклонение диаметра сквозных отверстий, как правило, составляет 0,01 - 0,02. мм.
На практике ультразвук широко используют для очистки деталей от жировых и механических загрязнений, продуктов коррозии, лакокрасочных покрытий и т. п.
Плазменная обработка
Плазменная обработка - это обработка материалов низкотемпературной плазмой, генерируемой дуговыми или высокочастотными плазмотронами.
Плазма - частично или полностью ионизированный газ, в котором плотности положительных и отрицательных зарядов практически одинаковы.
При плазменной обработке изменяются форма, размеры, структура обрабатываемого материала или состояние его поверхности. Плазменная обработка получила широкое применение при резке заготовок, нанесении покрытий, наплавке и сварке. Резка осуществляется сжатой плазменной дугой, которая горит между анодом (заготовка) и катодом (плазменная горелка). Процесс высокопроизводительный, что позволяет применять его в поточном непрерывном производстве.
Нанесение покрытий напылением производится для защиты деталей, предназначенных для работы в особых условиях (высокие температуры, агрессивные среды, интенсивный изгиб). Покрывают детали тугоплавкими металлами, карбидами и др.
Плазменную обработку применяют также для получения;. порошков металлов, используемых в порошковой металлургии. Точность плазменной обработки и шероховатость поверхности зависят от многих факторов и еще недостаточно изучены.
Лазерная обработка
В последнее время получила распространение лазерная технология. Лазерная технология - обработка и сварка материалов излучением лазеров. Лазер - источник электромагнитного излучения атомов и молекул видимого, инфракрасного и ультрафиолетового диапазонов. Мощные лазеры позволяют производить резку, сверление, закалку и сварку различных материалов без возникновения в них механических напряжений, неизбежных при обычной обработке. Обрабатываются заготовки из материалов любой твердости, металлов, алмазов, рубинов и др. с большой точностью [7].
Для технологических целей применяют твердотельные и газовые лазеры, которые могут работать как в непрерывном, так И в импульсном режимах.
Основными характеристиками лазерного излучения являются мощность излучения (Вт), длина волны (0,4-10,6 мкм), Длительность (мс) и форма импульсов, расходимость пучка.
Лазерный луч применяют для прошивания отверстий диаметром от нескольких микрометров до десятков миллиметров и глубиной до 15 мм. Производительность лазерных установок довольно высокая: 60 - 240 отверстий в 1 мин.
Типовая структурная схема лазерной установки с твердотельным лазером приведена на рис. 17.6.
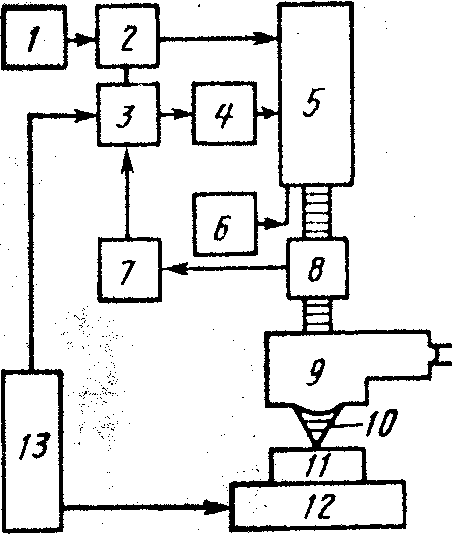
Рис. 17.6. Типовая структурная схема лазерной установки с твердотельным лазером:
1 - зарядное устройство; 2 - емкостный накопитель; 3 - система управления; 4 - блок поджига; 5 - лазерная головка; 6 - система охлаждения; 7 - система стабилизации энергии излучения; 8 - датчик энергии излучения; 9 - оптическая система; 10 - сфокусированный луч лазера; 11 - обрабатываемая заготовка; 11 - координатный стол; 13 - система программного управления.
При лазерной резке ширина реза обычно составляет 0,3- 1 мм, толщина разрезаемого материала-до 10 мм. Скорость резки зависит от толщины и свойств обрабатываемого материала и составляет 0,5 - 10 м/мин.
Единая система технологической документации
Во всех отраслях промышленности технологическая документация является тем основанием, без которого невозможно квалифицированно и с минимальной затратой труда и средств производить изделия требуемого качества, осуществлять материально-техническую организацию производства и его управление. Технологическая документация — основной источник информации для организации, управления и регулирования производственного процесса на каждом предприятии. Она сопровождает изделие в течение всего жизненного цикла и заканчивает свое существование при списании изделия, пройдя предварительно этапы проектирования, производства, эксплуатации и ремонта.
В машиностроении технологическая документация больше, чем где бы то ни было определяет взаимоотношения различных служб и производственных подразделений, является фактором, обеспечивающим ускорение технического прогресса, рост эффективности общественного производства и повышение производительности труда. Она решает две основные задачи — информационную и организационную.
Решая информационную задачу, технологическая документация обеспечивает изготовление деталей и сборочных единиц, служит средством организации труда рабочих и несет информацию для служб управления производством, в том числе используемую для определения плановой и фактической себестоимости изделия и его сборочных единиц, производительности труда, производственной мощности и загрузки оборудования участков, цехов и предприятий в целом. Являясь носителем информации о нормах расхода материалов, технологическая документация обеспечивает планирование и подготовку производства и т.д.
При решении организационной задачи технологическая документация связывает определенным образом участников производства (исполнителя, мастера, технолога), устанавливает определенные отношения между различными участками производства (инструментальное хозяйство, основное и вспомогательное производство), выполняет функцию организационной документации. Особое значение технологическая документация приобретает в условиях автоматизированного управления производством (АСУП), создавая основу информационного обеспечения и играя роль обратной связи. При стандартизации технологической документации учитывается не только ее прямое назначение, но и возможность ее использования с применением современных технологических средств. Для эффективного использования технологической документации необходима унификация.
В 1965 г. организации Госстандарта совместно с передовыми отраслями промышленности приступили к разработке Единой системы технологической документации (ЕСТД). В дальнейшем весь комплекс документов ЕСТД был существенно переработан в 1986 - 1990 гг.
В соответствии с ГОСТ 3.1001-81 ЕСТД "Общие положения", "Единой системой технологической документации называется комплекс государственных стандартов и рекомендаций Госстандарта и ВНИИЭС, устанавливающих взаимосвязанные правила и положения по порядку разработки, комплектации, оформления и обращения технологической документации, применяемой при изготовлении и ремонте изделий машиностроения и приборостроения".
Основным назначением ЕСТД является установление в организациях и на предприятиях единых правил оформления и обращения всех видов технологических документов, причем содержащаяся в них информация является частью информационного обеспечения АСУ.
Комплекс государственных стандартов ЕСТД разбит на девять классификационных групп:
— группа 0. Общие положения;
— группа 1. Основополагающие стандарты;
— группа 2. Классификация и обозначение технологических документов;
— группа 3. Учет применяемости деталей и сборочных единиц в изделиях и средствах технологического оснащения;
— группа 4. Основное производство. Формы технологических документов и правила их оформления на процессы, специализированные по видам работ;
— группа 5. Основное производство. Формы документов и правила их оформления на испытания и контроль;
— группа 6. Вспомогательное производство. Формы технологических документов и правила их оформления;
— группа 7. Правила заполнения технологических документов;
— группа 8. Резервная;
— группа 9. Информационная база.
Одним из основных стандартов системы является ГОСТ 3.1102- 81 "ЕСТД. Стадии разработки и виды документов". ГОСТ устанавливает, что технологическая документация разрабатывается на стадии "предварительного проекта" с литерой "П", который соответствует стадиям "эскизного" и "технического" проекта разработки конструкторской документации. Дальнейшие стадии разработки технологической документации соответствуют стадиям и обозначениям конструкторской документации по ГОСТ 2.103-68 ЕСКД. Опытный образец (опытная партия) - литера 0 или 01, 02...; установочная серия, установившееся серийное или массовое производство - литеры А, Б; единичное производство — литера И и др. К технологическим документам по ГОСТ 3.1102-81 относят графические и текстовые документы отдельно или в совокупности определяющие технологический процесс изготовления или ремонта изделия с учетом контроля и перемещения, комплектацию деталей и сборочных единиц и маршрут прохождения изготовляемого или ремонтируемого изделия по службам предприятия.
В стандарте установлены следующие виды документов.
Маршрутная карта (МК) — технологический документ, содержащий описание технологического процесса изготовления или ремонта изделия (включая контроль или перемещения) по всем операциям в технологической последовательности с указанием данных об оборудовании, оснастке, материальных и трудовых нормативов.
Карта технологического процесса (КТП) — технологический документ, содержащий описание техпроцесса изготовления или ремонта изделия (включая контроль или перемещения) по всем операциям одного вида работ, выполняемых в одном цехе в технологической последовательности с указанием данных об оборудовании, оснастке, материальных и трудовых нормативах.
Если техпроцесс полностью охватывает весь маршрут изготовления изделий, то КТП полностью заменяет МК, которая (в этом случае) не разрабатывается.
Карта эскизов (КЭ) — технологический документ, содержащий эскизы, схемы и таблицы, необходимые для выполнения технологического процесса, операции или перехода изготовления или ремонта изделия (включая контроль и перемещения).
Технологическая инструкция (ТИ) — технологический документ, содержащий описание предметов работ или технологических процессов изготовления или ремонтов изделия (включая контроль и перемещения), правил эксплуатации средств технологического оснащения, описание физических и химических явлений, возникающих при отдельных операциях.
Комплектовочная карта (КК) — технологический документ, содержащий данные о деталях, сборочных единицах и материалах, входящих в комплект собираемого изделия.
Ведомость оснастки (ВО) — технологический документ, содержащий перечень технологической оснастки, необходимой для выполнения данного технологического процесса (операции).
Ведомость технологических документов (ВТД) — технологический документ, определяющий состав и комплектность технологических документов, необходимых для изготовления или ремонта изделия.
Карта типового технологического процесса (КТТП) — технологический документ, содержащий описание типового технологического процесса изготовления или ремонта группы деталей и (или) сборочных единиц в технологической последовательности с указанием операций и переходов и соответствующих данных о средствах технологического оснащения и материальных нормативов.
Операционная карта (ОК) — технологический документ, содержащий описание технологической операции с указанием переходов, режимов обработки и данных о средствах технологического оснащения.
Карта типовой операции (КТО) — технологический документ, содержащий описание типовой технологической операции с указанием переходов, данных о технологическом оборудовании и, при необходимости, о технологической оснастке и режимах обработки, технологических документов, а также некоторые другие документы.
Таким образом, из всех ранее существующих документов в ГОСТы ЕСТД вошло минимально необходимое количество.
Стандартами ЕСТД установлены формы документов общего и специального назначения.
К документам общего назначения относятся документы, общие для различных видов работ, к документам специального назначения — документы на технологические процессы, специализированные по отдельным видам работ.
Требования, которым отвечают стандарты, входящие в ЕСТД:
— обеспечение преемственности со стандартами ЕСКД;
— возможности разработки, заполнения и обработки документации средствами вычислительной техники;
— снижение объема и трудоемкости разработки и унификация порядка утверждения и изменения документов;
— базирование на основе широкого применения типовых технологических процессов;
— включение правил обращения документов.
В соответствии с ЕСТД упрощается процедура оформления и утверждения технологических документов, поскольку вместо пяти-семи обязательных подписей сейчас предусмотрены только две - разработчика и контролера.
В документах сосредоточена вся необходимая для технолога информация по трудовым нормативам, ранее разбросанная по большому числу документов, например существовавшая оторванность технологического нормирования, ведущаяся в цехе или отделе технических измерений от работ проектирования, проводившегося в отделах главного технолога, главного металлурга и т.д.
ЕСТД способствует улучшению технологической подготовки производства, повышает ответственность и эффективность работы технологических служб и обеспечивает благодаря централизации высокоорганизованное массовое производство бланков технологической документации.
Внедрение ЕСТД во всех отраслях машиностроения и приборостроения повлияло на повышение эффективности общественного производства, существенно повысило уровень технологических разработок, способствовало улучшению качества выпускаемой продукции и повышению производительности труда.
Основы фотолитографии
Фотолитография объединяет в себе такие области науки, как оптика, механика и фотохимия. При любом типе печати ухудшается резкость края. Проецирование двумерного рисунка схемы ведет к уменьшению крутизны края, поэтому нужен специальный резист, в котором под воздействием синусоидально модулированной интенсивности пучка будет формироваться прямоугольная маска для последующего переноса изображения травлением или взрывной литографией.
Если две щели размещены на некотором расстоянии друг от друга, то неэкспонируемый участок частично экспонируется по следующим причинам:
1) дифракция;
2) глубина фокуса объектива;
3) низкоконтрастный резист;
4) стоячие волны (отражение от подложки);
5) преломление света в резисте.
Изображение неточечного источника в фокальной плоскости идеального объектива никогда не бывает истинной точкой, а распределяется в дифракционную картину диска Эйри. Таким образом, неэкспонируемый промежуток частично экспонируется дифрагировавшим и отраженным от подложки излучением. Из-за ограниченной селективности последующего процесса сухого травления резиста и подложки требуется получение рисунка с круглым профилем в относительно толстой пленке. Вследствие внутреннего эффекта близости (дифракционные потери) изолированные экспонируемые линии облучаются недостаточно и должны экспонироваться с большей дозой (ведет к искажению изображений линий размером более 3 мкм или неэкспонируемых промежутков размером менее 3 мкм) или проявляться с потерей толщины резиста в неэкспонируемых промежутках.
Таким образом, задача фотолитографии заключается в том, чтобы обеспечить совмещение и воспроизвести в резисте двумерный рисунок фотошаблона с точностью в пределах ±15% от номинального размера его элементов и с 5%-ным допуском на требуемый наклон краев. Послойное совмещение приборных структур должно осуществляться с точностью не хуже ±25% от размера минимального элемента. Оценка влияния проекционной оптики и системы совмещения определяется суммой среднеквадратичных ошибок переноса изображения и совмещения. Ширина минимально воспроизводимых линий при этом считается равной 4-кратной точности совмещения.
Используемые в фотолитографии источники экспонирующего излучения бывают как точечными (лазеры), так и протяженными (ртутные лампы). Спектр излучения этих источников лежит в трех основных спектральных диапазонах:
- дальний УФ от 100 до 200-300 нм;
- средний УФ 300-360 нм;
- ближний УФ от 360-450.
Существует 3 типа фотолитографических устройств:
1) теневого экспонирования;
2) проекционные с преломляющей оптикой;
3) проекционные с отражательной оптикой.
При теневом экспонировании шаблон, выполненный в масштабе 1:1, находится в физическом контакте с подложкой или отдален от нее на несколько микрометров в случае печати с зазором. Главными недостатками контактной печати являются повреждения шаблона и ограниченная совместимость.
В проекционных системах используются линзы или зеркала, позволяющие проецировать рисунок фотошаблона (масштаб 10:1, 5:1 или 1:1) на квадратное поле (20х20) или полоску (1,5 мм), которая затем сканируется по пластине.
2 Технология фотолитографии
2.1 Обработка подложек
Весь процесс фотолитографии можно представить в виде схемы (схема 1):
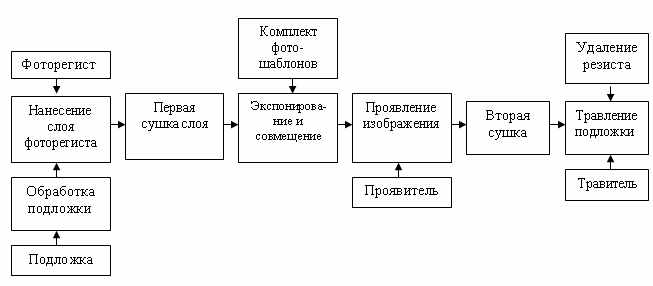
Схема 1- Процесс фотолитографии
Начинается процесс фотолитографии с обработки подложек. В производстве современных полупроводниковых приборов чаще всего используются кремниевые подложки, на поверхность которых нанесены пленки двуокиси кремния, примесно-силикатных стекол (фосфоро- и боросиликатных) металлов (алюминия, молибдена).
Для оценки качества подложки применяют визуальный контроль и измерение угла смачивания каплей воды. При визуальном контроле в темном поле микроскопа при увеличении около 200Х фиксируют поверхностные загрязнения, проявляющиеся в виде светящихся точек. Контроль осуществляется обычно в 5 областях, допустимое количество точек в поле зрения микроскопа зависит от сложности прибора: для больших интегральных схем, например, допускается не более 1-2 светящихся точек.
Измерения угла смачивания каплей воды производят с помощью установки контроля угла смачивания (УКУС). На подложку наносят каплю чистой воды, и на экране проектора измеряют угол, образуемый ею с плоскостью подложки. Этот угол дает косвенную информацию об адгезии слоя фоторезиста, указывая на степень смачиваемости подложки водными растворами травителей. Чем меньше этот угол, тем, больше подтравливание под защитными участками; чем больше угол смачивания водой, тем лучше качество фотолитографии.
В настоящее время методику измерений угла, образуемого каплей воды с плоскостью подложки, довольно широко применяют для оценки характеристик поверхности пластин кремния; достаточно высокая чувствительность методики позволяет контролировать нарушения процессов окисления и диффузии, загрязнения пластин, изменения их свойств при хранении и т. д. Среднеквадратичная ошибка метода не превышает ±2,6% в интервале значений углов от 15 до 55° , т. е. метод в достаточной мере воспроизводим и точен.
На поверхности двуокиси кремния могут находиться силоксановые (Si-О-Si), силанольные (Si-ОН) группы или молекулы адсорбированной воды, причем если вода образовала с поверхностью окисла прочные связи (например, водородную связь), то удалить ее очень трудно. Соответственно угол смачивания водой меняется от 50-55° для чистой силоксановой поверхности, полученной окислением в сухом кислороде, до 30-32° для окисления в парах воды под давлением. При хранении окисленных пластин на воздухе происходит медленное уменьшение угла смачивания из-за адсорбции воды: исходное значение в 55° падает до 42-45° через 2 ч и до 39-41° через 24 ч. Резко понижает угол смачивания обработка окисла в воде, кислотах (азотной или серной) и особенно в растворах, содержащих плавиковую кислоту.
На окисленные подложки, полученные обычным термическим окислением в сухом кислороде или парах воды, фоторезист лучше всего наносить сразу (в течение 1ч) после окисления без каких-либо дополнительных обработок. Если подложки долго хранились или окисел с самого начала был гидрофильным, желательна термообработка. Минимальная температура обработки в сухом азоте в течение 1ч составляет 700°С. Обработка в том же режиме, но во влажном кислороде малоэффективна (угол смачивания около 25°). Наилучшие результаты дает короткая (5 мин) обработка при температурах выше 1000°С, причем среда почти не играет роли. Обработка под ИК лампой типа ЗС-3 в течение 30 мин также позволяет получить большие углы смачивания.
Фосфоросиликатные стекла, в отличие от двуокиси кремния, имеют резко выраженную гидрофильную поверхность - угол смачивания водой равен 13-15° и соответственно качество фотолитографии намного хуже. Поверхностные свойства фосфоросиликатных стекол зависят от соотношения пятиокиси фосфора и двуокиси кремния. Обычно создастся фаза, богатая пятиокисыо фосфора, например, при получении эмиттерных слоев с высокой поверхностной концентрацией, при геттерировании примесей и т. д. Пятиокись фосфора гигроскопична и активно поглощает влагу. Возможно также образование на поверхности стекол гидроксильных групп по следующей схеме: координационное число фосфора уменьшается с 5 до 4 при построении фосфоросиликатного стекла; появляется немостиковый кислород, который легко связывается с протоном, возникающим при окислении, в гидроксильную группу. Следует стремиться к тому, чтобы концентрация пятиокиси фосфора не превышала требуемой. Поскольку каждый атом фосфора связывает ион натрия, для стабилизации параметров прибора достаточно обеспечить концентрацию фосфора в стекле не выше 1017-1018 см-3. Качество же фотолитографии при этом резко улучшается. К сожалению, регулировать содержание пятиокиси фосфора в стекле трудно и обычно оно намного выше. Можно рекомендовать получение фосфоросиликатного стекла разложением смеси четыреххлористого кремния и фосфина (50:1) при температуре 250-550°С. Качество фотолитографии на фосфоросиликатном стекле можно улучшить, обработав его в органосиланах.
Оптимальными режимами обработки считаются следующие: выдержка в 10%-ом растворе диметилдихлорсилана (1 мин), промывка в чистом трихлорэтилене (1 мин) и термообработка при 450°С на воздухе (45 мин). Эта обработка резко снижает отклонение размеров (примерно на порядок) при травлении и уменьшает влияние перетравливания.
Диметилдихлорсиланы охотно реагируют с водой, образуя гидроксильные соединения – силиколы. Силиколы неустойчивы, они отдают гидроксильные группы, превращаясь в силиконы, которые склонны к полимеризации, причем скорость, с какой образуются цепи, зависит от характера органического радикала. Диметилдихлорсилан быстро полимеризуется в цепи, строение которых аналогично силоксановым цепям на поверхности кремния. Во влажной среде свободные связи силоксановой цепи насыщаются гидроксильными группами и гидрофобная силоксановая поверхность превращается в более гидрофильную силанольную. Дальнейший контакт с влагой приводит к тому, что на поверхности адсорбируются молекулы воды.
Строение фосфоросиликатного стекла аналогично строению двуокиси кремния. Фосфор может сам образовывать стекло в «пустотах» двуокиси кремния. «Лишний» по сравнению с двуокисью кремния атом кислорода обусловливает большую гигроскопичность фосфоросиликатного стекла, так как к нему легко присоединяется протон, образуя гидроксильную группу. Поверхность фосфоросиликатного стекла гидрофильна, углы смачивания водой малы и качество фотолитографии низкое. При обработке двуокиси кремния или фосфоросиликатного стекла в диметилдихлорсилане происходят следующие реакции. Сначала отщепляются гидроксильные группы, и вместо них присоединяются цепочки силиконов.
Все свободные связи на поверхности заняты органическими радикалами, так что ни вода, ни резист ее не смачивают. Увеличивая концентрацию диметилдихлорсилана в растворе или повышая температуру раствора, достигают более полной замены гидроксильных групп.
При термообработке происходит разрыв связей между кремнием и органическими радикалами. Для разрыва изолированной связи Si-С достаточно превысить 350°С, но, очевидно, требуемое качество поверхности достигается при более высоких температурах, порядка 400-450°С. Поверхностные свойства фосфоросиликатного стекла и двуокиси кремния становятся похожими. Высокотемпературную термообработку стекол вряд ли можно рекомендовать, так как их геттерирующие свойства теряются. Полезна инфракрасная сушка в течение 30 мин, увеличивающая у фосфоросиликатных стекол угол смачивания водой от 15 до 35°.
Пленки алюминия характеризуются большим разбросом поверхностных свойств, часто резист плохо смачивает поверхность подложки. Изменения поверхностных свойств алюминия, вероятнее всего, связаны с условиями напыления, когда пленку загрязняют остатки вакуумного масла и материал испарителя. Одним из средств борьбы с нестабильностью свойств пленки является напыление алюминия электронно-лучевым методом из капли расплава.