Розділ ІІ ремонт гальмового обладнання вантажних та рефрижераторних вагонів
Вид материала | Документы |
- Правила охорони праці під час технічного обслуговування І ремонту вантажних вагонів, 984.98kb.
- Договір оренди вантажних вагонів, 70.99kb.
- Договір оренди вантажних вагонів, 64.92kb.
- Х а д т є. Ф. Соболєв М. Р. Захарян Конспект, 6344.59kb.
- 3304-04/5076-12 від 13. 02. 2012 Державне підприємство “Український державний центр, 67.42kb.
- Надано стислі методичні рекомендації щодо консультування та підготовки абітурієнтів, 464.3kb.
- Правила ремонта цметро 3906. Общие положения, 126.83kb.
- Годовой отчет ОАО «Желдорреммаш» за 2010, 1853.06kb.
- Типовий перелік навчального обладнання для кабінетів фізики загальноосвітніх навчальних, 251.9kb.
- На виконання вимог постанови Кабінету Міністрів України від 17., 41.18kb.
ному резервуарі перевіряти при зарядному тиску в резервуарі, а також після зниження тиску в ньому на 0,5 - 0,7 кгс/см2 і на 1,5- 2,0 кгс/см2 аналогічно п.5.2.1 розділу І Інструкції.
5.5.2. Час зниження тиску в магістральному резервуарі темпом службового гальмування з 5 до 4 кгс/см2 повинен бути в межах 4 - 6 с.
5.6. Ремонт кранів машиніста.
При невідповідності параметрів роботи зазначеним вище значенням, а також 1 раз на рік незалежно від стану, крани машиніста ремонтувати установленим порядком відповідно до діючої "Інструкції по технічному обслуговуванню, ремонту та випробуванню гальмового обладнання локомотивів та моторвагонного рухомого складу", про що в журналі ВУ-47 в АКП ставиться штамп і робиться запис з підписом працівників локомотивного депо, яке здійснювало ремонт і приймання крана після ремонту.
РОЗДІЛ ІІ
РЕМОНТ ГАЛЬМОВОГО ОБЛАДНАННЯ ВАНТАЖНИХ ТА РЕФРИЖЕРАТОРНИХ ВАГОНІВ
1. РЕМОНТ ГАЛЬМОВОГО ОБЛАДНАННЯ ПІД ЧАС ПОТОЧНОГО РЕМОНТУ З ВІДЧЕПЛЮВАННЯМ ВАГОНІВ
1.1. Поточний ремонт гальмового обладнання робити під час технічного обслуговування вагонів, які надійшли в поточний відчеплювальний ремонт. При цьому необхідно перевіряти технічний стан гальмового обладнання та запобіжних обладнань.
1.2. Несправні деталі та вузли пневматичного гальмового обладнання замінити, відсутні - установити.
1.3. Важільну передачу оглянути, виявлені несправності усунута. Замінити типовими пошкоджені та нетипові валики, шайби, чеки, гальмових колодок. На місці відсутніх, а також замість нетипових шплінтів ставити нові, стандартні.
При виявленні колодок які, виступають за кромку зовнішньої грані колеса, усунути причини дефекту. Несправні (тонкомірні) колодки замінити.
1.4. Несправні рукоятки режимних перемикачів повітророзподільників на вагонах, не обладнаних авторежимом, відремонтувати, відсутні установити.
1.5. Несправні повідки випускного клапана замінити, відсутні установити.
1.6. Гальмовий циліндр, двокамерний та запасний резервуари, повітропровід та деталі підвішування гальмової важільної передачі повинні бути надійно закріплені. Відсутні болти та гайки установити.
1.7. Пиловловлюючі сітки оглянути, очистити та продути стисну-
25
тим повітрям.
1.8. На вагонах з авторежимом перевірити відповідність положення вала режимного перемикача типу колодок; вал повинен бути установлений і закріплений при чавунних колодках на вантажному режимі, при композиційних - на середньому.
1.9. Упор авторежиму повинен розміщуватися над середньою зоною контактної планки і не мати ознак сходу з неї (вигин стержня упору, задери кромки регулюючої планки та ін.). При необхідності відрегулювати зазор між упором і планкою, який повинен бути не більшим 3 мм на порожньому вагоні.
1.10. Перевірити стан опорної балки (впевнитися у відсутності загину) та вузлів її кріплення на бокових рамах візка (наявність болтів, гайок, шплінтів, гумометалевих елементів під опорами балки). Пошкодження усунути.
1.11. Контактна планка авторежиму повинна бути надійно закріплена на опорній балці візка.
1.12. Перевірити кріплення авторежиму на кронштейні, ослаблені болти затягнути.
1.13. Зарядити гальмову систему вагона стиснутим повітрям до тиску 5,3 - 5,5 кгс/см2 , перевірити мильним розчином або приладом-течошукачем герметичність з'єднань трубопроводу та пневматичних пристроїв.
Виявлені витікання стиснутого повітря усунути.
1.14. Після закінчення ремонту перевірити роботу гальма вагона і дію випускних повідків.
Перевірку і приймання відремонтованого гальмового обладнання проводити відповідно пункту 8 розділу II Інструкції.
2. РЕМОНТ ГАЛЬМОВОГО ОБЛАДНАННЯ ПІД ЧАС ДЕПОВСЬКОГО РЕМОНТУ ВАНТАЖНИХ, ДЕПОВСЬКОМУ ТА КАПІТАЛЬНОМУ ПЕРШОГО ОБСЯГУ (КРЇ) РЕМОНТАХ РЕФРИЖЕРАТОРНИХ ВАГОНІВ
2.1. Загальні вимоги.
Під час деповського ремонту вагона повітророзподільник, вантажний авторежим, кінцеві та роз'єднувальні крани, з'єднувальні рукави авторегулятор і важільну передачу з вагона знімати та направляти для ремонту до відповідних цехів, відділень і АКП. Замість знятих ставити нові або відремонтовані.
Корпус гальмового циліндра, двокамерний резервуар, запасний резервуар, гальмовий повітропровід допускається оглядати безпосередньо на вагоні і при відсутності необхідності з вагона не знімати.
При капітальному ремонті (КР-І) рефрижераторних вагонів необхідно знімати також запасний резервуар і стоп-крани.
2.2. Повітропровід і резервуари.
26
2.2.1. Повітропровід оглянути, непридатні елементи замінити трубами по ГОСТ 8734-75 з зовнішнім діаметром 42 мм з товщиною стінки 4 мм для магістрального трубопроводу і з умовним проходом 20 мм з товщиною стінки 3,2 мм - для підводів до гальмових приладів. Для магістрального трубопроводу і підвідних труб допускається застосовувати підсилені труби по ГОСТ 3262 Нарізку на кінцях труб нарізати плашками та перевіряти різьбовим калібром.
Допускається місцеве спрацювання магістральної труби не більше 15% від товщини стінки поза різьбовими з'єднаннями і місцями кріплення. Підвідні труби повітропроводу відремонтувати відповідно до "Технічної Інструкції по ремонту підвідних труб автогальм вантажних вагонів 103-58.00.96".
Для магістрального відводу допускається застосовувати гумотекстильний з'єднувальний! рукав типорозміру Р36 по ГОСТ 25 93.
Установлений раніше з'єднувальний рукав з вагона знімати і направляти в АКП для ремонту та перевірки.
2.2.2. Запасний резервуар оглянути. Допускається наявність місцевих вм'ятин глибиною не більше 5 мм в кількості не більше трьох поза зварним швом.
Перевіряти резервуар на щільність стиснутим повітрям під тиском 6,0 - 6,5 кгс/см2 безпосередньо на вагоні з одночасним обстукуванням дерев'яним молотком масою не більше 1 кг.
При капітальному ремонті (КРІ) рефрижераторного вагона запасний резервуар ремонтувати відповідно пункту 3.3.1 розділу II Інструкції.
2.2.3. У двокамерного резервуара перевіряти:
- правильність і міцність кріплення на вагоні;
- щільність литва. Наскрізні раковини та тріщини, які пропускають повітря, не допускаються. Перевірку робити стиснутим повітрям під тиском 6,5 кгс/см2 ;
- відстань від привалкової площини для головної частини повітророзподільника до робочої поверхні кривошипа валика перемикача режимів. Вона повинна бути в двокамерному резервуарі № 295-001 для навантаженого режиму - 80+1 мм, для середнього - 87+1 мм; в двокамерному резервуарі № 295-001 для навантаженого режиму - 80,5±0,5 мм для, середнього - 85,5±0,5 мм.
Режимний валик знімати в разі необхідності його ремонту. Фільтри і сітки промити, продути або замінити новими.
2.3. Гальмовий циліндр.
2.3.1. Поршневий вузол зняти з гальмового циліндра, направити в ремонт і випробувати. Деталі, які мають зломи, тріщини, замінити. Корпус циліндра оглянути, очистити, змастити. Іржу на внутрішній поверхні усунути дрібною шліфувальною шкуркою і протерти технічною серветкою.
2.3.2. Гумову манжету, яка має прориви, протертості або термін придатності, якої закінчується до наступного планового ремонту вагона, замінити.
27
Перед установленням поршня на тертьові поверхні циліндра та манжети нанести тонкий шар гальмового мастила.
2.3.3. Перевірити міцність кріплення гальмового циліндра на рамі вагона і в разі необхідності, закріпити.
2.4. Автоматичний регулятор режиму гальмування та його привід.
2.4.1. Авторежим, поперечну опорну балку зняти з вагона, замість них установити нові або відремонтовані.
Підвідні труби закріплювати не менше ніж у двох місцях на кронштейнах спеціальними накладками і болтами з гайками, зафіксованими спеціальною стопорною шайбою 12.02 по ГОСТ 13463 або контргайкою.
2.4.2. Кронштейн авторежиму повинен бути справним і міцно закріпленим на рамі вагона.
2.4.3. Новий або відремонтований авторежим установити на кронштейні і закріпити гайками в діагональній послідовності, попередньо впевнившись у нормальному стані гумової прокладки, яка повинна бути чистою і не мати затягнутих отворів.
2.4.4. При ремонті візка справну опорну балку укласти на бокові рами з підкладанням гумометалевих елементів і закріпити болтами. Гайки на болтах не затягувати, а зафіксувати з зазором 3 - 5 мм шплінтами.
2.4.5. Після підкочування візка з опорною балкою під вагон упор стержня вилки авторежиму повинен розмішуватися над середньою зоною контактної планки балки.
2.4.6. Регулювання зазору між упором авторежиму і контактною планкою здійснювати тільки постановкою регулюючих прокладок під контактну планку. При цьому зберігається розмір "б" (рисунок 10), установлений в АКП.
Установлювати регулюючі прокладки і приварювати їх зверху контактної планки забороняється.
2.4.7. На порожньому вагоні упор авторежиму може мати зазор "а" не більше 3 мм.
При правильно відрегульованому зазорі кільцева виточка на вилці авторежяму повинна виступати із корпуса не менше ніж на 2 мм ("в"≥ 2 мм). Якщо відносне положення упорного стержня і кільцевої виточки не відповідає указаним вимогам, необхідно відрегулювати зазор зніманням або постановкою металевих прокладок. Регулювати зазор на вагоні з допомогою гайки авторежиму, зашплінтованої в АКП, забороняється.
2.4.8. Контактна планка повинна бути надійно закріплена на поперечній балці відповідно прийнятої конструкції.
2.4.9. Режимний вал двокамерного резервуара повинен бути установлений і закріплений при чавунних колодках на вантажному режимі, при композиційних - на середньому
2.4.10. На вагонах з масою тари 27-45 тс регулювання приводу авторежиму здійснювати в такій послідовності:
28
- режимний вал двокамерного резервуара закріпити на середньому режимі, при цьому вагони обладнати тільки композиційними колодками;
- регулювання приводу авторежиму здійснювати на порожньому вагоні ставленням металевих прокладок із закріплюванням їх на контактній плиті балки;
- перевірку величини тиску в гальмовому циліндрі на порожньому вагоні здійснювати порядком, визначеним пунктом 8 розділу II даної Інструкції. Тиск в гальмовому циліндрі повинен бути 1,8±0,1 кгс/см2 - для вагонів з масою тари 27-36 тс і 2,2±0,1 кгс/см2 - для вагонів з масою тари 30-45 тс;
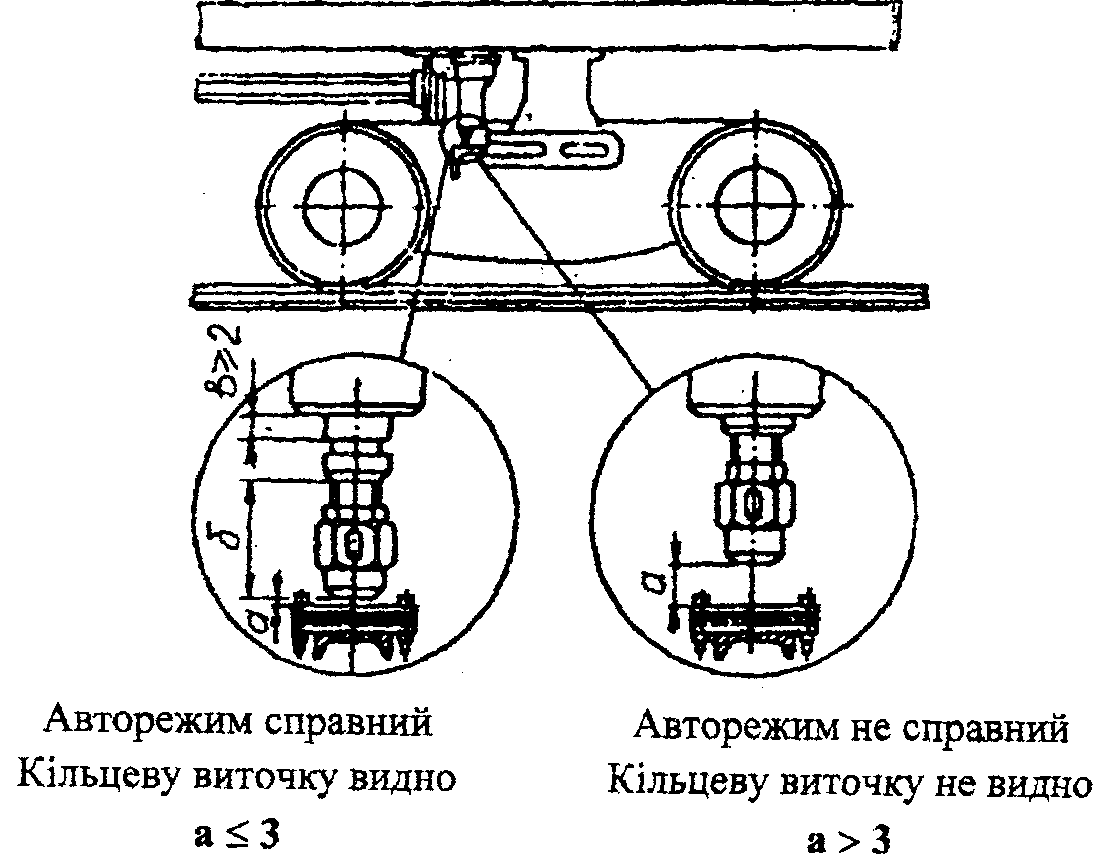
Рисунок 10 - Положення упорного стержня авторежиму відносно контактної планки
- на рамі вагонів, у яких виконане дане регулювання, поряд з надписом "Авторежим" нанести розрахункове натиснення колодок (в тоннах) на вісь і тиск в циліндрі порожнього вагона: "порожній - 5т/1,7-1,9" -на вагонах з масою тари 27-36 тс і "порожній - 6,5т/2,1-2,3" - на вагонах з масою тари 36 - 45 тс.
2.5. Гальмова важільна передача.
2.5.1. Важільну передачу рефрижераторних вагонів ремонтувати відповідно до пункту 3.4 розділу ІІІ Інструкції.
2.5.2. Важільну передачу гальма вантажного вагона розібрати не-
29
залежно від стану
2.5.3. Втулки кронштейнів бокових рам візків вантажних вагонів,
спрацьовані по діаметру більше 1 мм або які мають відколи, замінити новими
2.5.4. Підвіски гальмових башмаків вантажних вагонів ставити
нові, які виготовлені відповідно до креслень і мають клейма заводу-виготовлювача на вушку прямої вітки або відремонтовані з приведенням
всіх розмірів у відповідність з кресленнями. На вушку зігнутої вітки поста вити клеймо (номер ремонтного пункту і рік ремонту); клеймо заводу-виготовлювача і рік виготовлення на вушку прямої вітки зберігається.
2.5.5. Підвіски башмаків вантажних вагонів, у яких розмір поперечного перетину в місцях найбільшого спрацювання не менше 22 мм а розмір у кутах з підсиленим перетином не менше 25 мм, допускається від
новлювати відповідно до розмірів креслень згідно "Інструкції по зварюванню та наплавленню".
2.5.6. Підвіски башмаків, які мають розмір в поперечному перетині по діаметру менший 2,2 мм, а в кутах з підсиленою частиною менший 26 мм, а також підвіски, в яких під час дефектоскопії виявлені тріщини незалежно від стану, ремонтувати і ставити на вагон не дозволяється.
2.5.7. Всі відремонтовані підвіски гальмових башмаків повинні бути перевірені дефектоскопом і на вушку зігнутої вітки поставлено клеймо ремонтного пункту та дата ремонту.
2.5.8. Гумові втулки підвісок ставити нові.
2.5.9. Валики підвісок, спрацьовані по діаметру більше 1 мм замінити.
Дозволяється неплавка валиків підвіски башмаків з обов'язковою наступною обробкою на токарному верстаку.
2.5.10. Втулки важільної передачі, при зазорі в шарнірному з'єднанні по діаметру 3 мм і більше замінити новими по ТУ 086.025-96
2.5.11. Гальмові башмаки відновлювати до розмірів креслень. Паз для вушка колодки з розмірами 45, 50мм і більше відновлювати наплавленням до номінальних розмірів відповідно 42 +2 і 47+2 мм.
Башмаки, які мають товщину перемички для чеки 5,5 мм і менше, до ставлення на вагони не допускаються. Необхідно приварити нові пере мички товщиною 71+1-0,5 мм.
Допускається наплавлення і наступна обробка спрацьованих поверхонь башмака в місцях прилягання колодок до розмірів креслень.
2.5.12. Тріангелі ремонтувати відповідно з типовим технологічним процесом. Тріангелі, які мають зломи швелера, до ремонту і установки на вагон не допускаються. При складанні тріангеля відстань між башмаками установлювати по найменшому допустимому розмірі 1517 ± 3 мм.
Гальмові башмаки установлювати так, щоб при незакріпленій
30
гайці вони не коливалися на балці. Зазор між натискною площиною цапфи тріангеля і передньою стінкою отвору в башмаку усовувати ставленням з натягом сталевої прокладки розміром 80 х 80 мм.
Спрацьовані натискні поверхні цапф тріангеля наплавляти стійкими проти спрацювання електродами з наступною механічною обробкою. Щиріша цапфи після обробки наплавленої поверхні повинна бути 46 ± 1 мм, висота - 80 мм.
Нарізку на кінцях тріангеля перевіряти калібром. Якщо зазор по діаметру вздовж нарізки більший 0,8 мм, при наявності більше трьох пошкоджених або зірваних ниток нарізки, відновити її наплавленням з наступною обробкою.
Діаметр отвору в наконечнику відновлювати до розміру 35 ± 2 мм креслення. Допускається ставити наконечник, який має спрацювання отвору не більше 2 мм по діаметру.
2.5.13. Після ремонту та випробування на вузькій стороні розпірки тріангеля, ближче до струни, на зачищеному місці нанести дату ремонту (місяць, рік) і клеймо ремонтного пункту.
При цьому раніше поставлені клейма, крім клейм заводу-виготовлювача, зачистити або забити.
2.5.14. На розпірці тріангеля повинна бути установлена скоба пристрою для рівномірного спрацювання гальмових колодок, виготовлена із прутка діаметром 16 мм, яка має робочий охоплюючий розмір 226+2 мм, відповідно до проекту ПКБ ЦВ МПС № МІ 180.000.
Допускається на тріангелях, які мають на тильному боці балки гак заводського виготовлення, застосовувати скобу із стального прутка діаметром 16 мм, з робочим охоплюючим розміром 144 мм, яка установлюється на зазначений гак. Приварювання гака в депо не повинно допускатися.
Скоби, які мають зломи віток, тріщини по зварювальному шву, протертості глибиною 3 мм і більше, а також виконані не відповідно до креслень, до ставлення не повинні допускатися.
2.5.15. Гальмові колодки ставити нові, закріплювати типовими чеками. На колодки повинен бути сертифікат якості.
2.5.16. Деталі стоянкового гальма очистити і перевірити. Допускається при необхідності наплавлення спрацьованих поверхонь і приварювання нових частин стержня.
2.5.17. Гальмові тяги, які мають тріщини, до ставлення на вагон не повинні допускатися. Довжина гальмових тяг і розпірок повинна відповідати розмірам креслень. В процесі складання важільної передачі на вагоні при нових колодках і повномірних колесах тяги з важелями, з'єднувати крайніми отворами в головках. При неповномірних колесах тяги з'єднувати з важелями на відповідні отвори в головках тяг і сергах. Укорочувати тягу зменшенням її довжини забороняється.
2.5.18. У важільній передачі не допускати перекоси підвісок і головок гальмових тяг у важелях.
31
2.5.19. Кронштейни для закріплення і підвішування гальмового обладнання повинні бути справні і міцно закріплені на рамі. Кронштейни, які мають пошкодження зварювальних швів, ремонтувати з попередньою вирубкою дефектних місць, наступним їх заварюванням і обробкою.
Замість несправних кронштейнів установлювати справні, які відповідають типу вагона та візка.
2.5.20. Запобіжні та підтримуючі пристрої, що попереджують падіння деталей важільної передачі на колію, повинні бути справні і закріплені відповідно кресленням. Установлювати запобіжні скоби з відступами від креслень забороняється.
Несправні запобіжні пристрої ремонтувати згідно кресленням, непридатні замінити новими.
2.5.21. При складанні важільної передачі гвинти шарнірні з'єднання змащувати вісьовим маслом, на валики установлювати типові шайби і нові шплінти. Повторно використовувати шплінти не дозволяються.
2.5.22. Важільну передачу регулювати так, щоб вихід штока гальмовою циліндра при повному службовому гальмуванні на вантажному режимі повітророзподільника складав 75-125 мм при чавунних колодках, 50-100 мм при композиційних колодках на середньому режимі повітророзподільника. Регулювання виходу штока здійснювати перестановкою валиків на тягах і сергах, при цьому забезпечити підбір величин у відповідності з рисунками 1 і 2, а на вагонах, які мають регулятор гальмової важільної передачі, крім того, шляхом установки його відповідно до пункту 5.6 розділу П Інструкції. При цьому горизонтальні і вертикальні важелі установлювати так, щоб при гальмуванні горизонтальні важелі з боку мертвої точки розміщувались приблизно під кутом 90° до осі гальмового циліндра, а вертикальні важелі мали нахил 5 - 10° від вертикалі в бік надресорної балки.
З.РЕМОНТ ГАЛЬМОВОГО ОБЛАДНАННЯ 1ПД ЧАС КАПІТАЛЬНОГО РЕМОНТУ ВАНТАЖНИХ ТА КАПІТАЛЬНОГО (КР- 2) РЕМОНТУ РЕФРИЖЕРАТОРНИХ ВАГОНІВ
3.1. Загальні вимоги.
Під час капітального ремонту вантажних та рефрижераторних вагонів все гальмове обладнання знімати і направляти у відповідні ремонтні цехи та АКП. Замість знятого гальмового обладнання установити нове або відремонтоване.
3.2. Повітропровід та арматура.
3.2.1. Магістральний повітропровід повинен бути виготовлений з безшовних стальних труб по ГОСТ 8734-75 зовнішнім діаметром 42 ± 0,4 мм з товщиною стінки 4 ± 0,4 мм суцільним , звареним, а також на муфтових з'єднаннях не більше ніж в трьох місцях для вантажних вагонів, для рефрижераторних вагонів в кількості, зазначеній в технічній документації
32
на цей тип вагона. Зварювання дозволяється робити як нових, так і труб, які були в експлуатації, при цьому між трійником і кінцевими кранами дозволяється не більше трьох стиків.
Мінімальна відстань між кінцем труби і зварювальним з'єднанням повинна бути 0,5 м. Розміщувати зварювальні стики в місцях згинів повітропроводу забороняється.
Стикування труб робити способом газопресового зварювання згідно з Інструкцією № И32 ВНИИЖТ 0 503/2-86 або "біжучою дугою" по технології, узгодженій з ЦВ. Допускається використання старопридатних труб із спрацюванням не більше 15% по товщині стінки поза різьбовими з'єднаннями та місцями кріплення.
Допускається на магістральному повітропроводі 8-вісноі цистерни зварювання труб робити приварюванням з'єднувальної втулки відповідно конструкторській документації.
Допускається повітропровід ремонтувати без демонтажу його з вагона відповідно до ТУ 32 Укрзалізпром-014-94 "Повітропровід 4-вісних вантажних вагонів. Капітальний ремонт".
3.2.2. Підвідні труби повітропроводу застосовувати нові безшовні по ГОСТ8734.
Допускається підвідні труби ремонтувати відповідно до "Технологічної Інструкції по ремонту підвідних труб автогальма вантажних вагонів, Т. 106.96 КПКТБ(в)".
Для магістрального підводу допускається застосування гумотекстильного з'єднувального рукава типорозміру Р36 по ГОСТ 2593-75.
Установлений раніше з'єднувальний рукав з вагона знімати і направляти в АКП для ремонту і перевірки.
3.2.3. Нарізку на кінцях труб перевіряти різьбовим калібром. Дозволяється нарізати нарізку клупами та плашками на різьбонарізних верстаках. Нарізання нарізки різцем на токарно-гвинторізних верстаках забороняється.
Допускається виготовлення нарізки методом накатування.
3.3. Резервуари.
3.3.1. Запасний резервуар оглянути. Допускається наявність місцевих вм'ятин глибиною не більше 5 мм в кількості не більше трьох. Резервуари продути стиснутим повітрям під тиском 6,0 - 6,5 кгс/см2 та піддати гідравлічному випробуванню на міцність тиском 10,5 кгс/см2 2 протягом 5 хв: просочування води через стінки та шви не допускається. Випробувати на щільність стиснутим повітрям під тиском 6,5 кгс/см2 протягом 3 хв. у ванні з водою або омилюванням, при цьому утворення бульбашок не допускається. Після закінчення випробувань на циліндричній частині запасного резервуара нанести білою фарбою дату (число, місяць, рік) та пункт перевірки шрифтом висотою 21 мм відповідно до альбому "Знаки і надписи на вагонах вантажного парку залізниць колії 1520 мм". Результати випробувань зареєструвати в книжці обліку періодичного ремонту автоматичних гальм форми ВУ-68.
33
3.3.2. У двокамерного резервуара перевіряти:
- щільність литва; наскрізні раковини та тріщини, які пропускають повітря, в будь-якій частині резервуара не допускається Перевірку робити стиснутим повітрям під тиском 6,5 кгс/см2, застосовуючи спеціальні пристрої, які закріплюються на привалкових фланцях резервуара •
- відстань від привалкової площини фланця для головної частини повітророзподільника до робочої частини поверхні кривошипу валика перемикача режимів. Ця відстань повинна бути в двокамерному резервуарі № 295-001 для навантаженого режиму 80+1 мм, для середнього – 87+1 мм, в двокамерному резервуарі № 295М-001 для навантаженого режиму 80,5'± 0,5 мм, для середнього - 86,5 ± 0,5 мм.
Режимний валик витягти для огляду та ремонту. Під час установлення відремонтованого валика нанести на поверхні тертя тонкий шар мастила.
Очистку двокамерного резервуара робити продуванням стиснутим повітрям під тиском 6,0 - 6,5 кгс/см2 . Дозволяється обстукувати резервуар дерев'яним молотком масою не більше 1 кг.
Допускається ремонт двокамерного резервуара заваркою відповідно до" Інструкції по зварюванню і наплавленню".
Фільтри старанно очистити, промити, продути або замінити новими.
Допускається двокамерний резервуар ремонтувати відповідно до ТУ 32 Укрзалізпром-006-93 "Капітальний ремонт двокамерного резервуара вантажних вагонів без демонтажу його з вагона".
3.4. Гальмовий циліндр.
3.4.1. Гальмовий циліндр розібрати. Корпус та кришку, в яких є тріщини, спрацювання або відколи, замінити або відремонтувати відповідно до "Інструкції по зварюванню і наплавленню".
3.4.2. Придатний корпус циліндра оглянути, промити, очистити. віддалити іржу на внутрішній поверхні дрібною шліфувальною шкуркою та протерти технічною серветкою і змастити гальмовим мастилом згідно таблиці 2.
3.4.3. Прокладку задньої кришки замінити.
3.4.4. Вузол поршня з передньою кришкою розібрати та відремонтувати. Перевірити висоту пружини у вільному стані; якщо просідання більше ЗО мм пружину замінити новою.
Перевірити стан фільтра, пилозахисного ущільнення в передній кришці циліндра, очистити, промити та протерти їх.
Під час складання зовнішні поверхні цих деталей змастити гальмовим мастилом. Установити гумову манжету, з часу виготовлення якої пройшло не більше трьох років. Змащувальне кільце поршня очистити та змастити гальмовим мастилом. Під час складання циліндра поверхні тертя та гумову манжету змастити тонким шаром гальмового мастила згідно таблиці 2.
3.4.5. Після ремонту та повного складання циліндра перевірити
34