Механико-технологические основы повышения эффективности процесса центробежной очистки растительных масЕл в условиях сельскохозяйственных предприятий
Вид материала | Автореферат |
СодержаниеМногофакторный эксперимент В пятой главе H; – угла наклона образующей конуса к вертикальной оси ротора центрифуги, θ |
- Обзор отрасли: производство растительных масел, 312.19kb.
- Технология адсорбентов для очистки растительных масел на основе диатомита и бентонита, 364.16kb.
- Организация производства приборов для автоматического определения кислотности растительных, 37.44kb.
- Голосования и тестирования votum как средство повышения эффективности процесса обучения, 113.22kb.
- «Обеспечение работы белорусских промышленных и сельскохозяйственных предприятий в современных, 158.57kb.
- «Обеспечение работы белорусских промышленных и сельскохозяйственных предприятий в современных, 165.49kb.
- Организация производства мобильных установок реутилизации и очистки стоков, 800.08kb.
- А. В. Колмыков Теоретические основы установления эффективности использования сельскохозяйственных, 852.49kb.
- Метод повышения эффективности некаталитической очистки отработавших газов судовых дизелей, 266.03kb.
- Республиканский информационный материал к единому дню информирования на тему: «Обеспечение, 339.31kb.
Многофакторный эксперимент
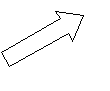
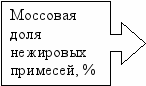
Многофакторный
эксперимент
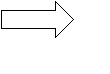
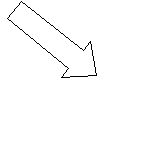
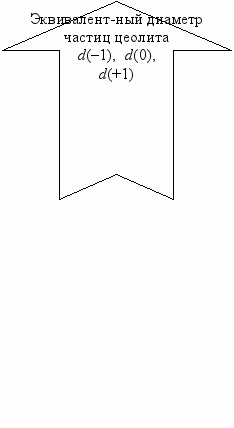
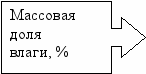
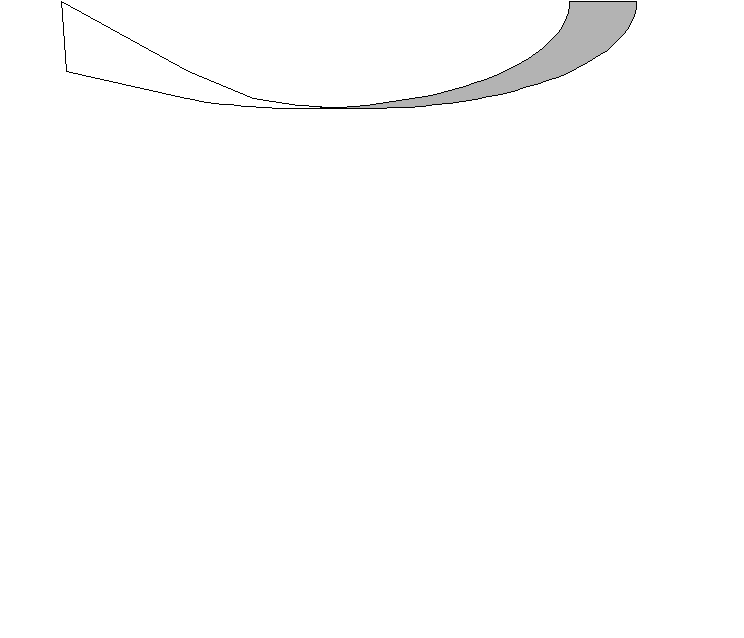
Рисунок 19. Структурная схема экспериментального исследования рабочего процесса вертикальных фильтрующих конических центрифуг
При исследовании центрифуги первого типа ВФКЦ-1 в качестве критериев оптимизации приняты: у1 – массовая доля нежировых примесей (%); у2 – кислотное число (мг КОН/г); у3 – выход соевого масла (кг/мин).
В качестве регулируемых факторов приняты частота вращения ротора центрифуги Х1(ω, с-1), высота фильтрующего слоя Х2 (h, м) и эквивалентный диаметр частиц цеолита Х3(d, м). Для каждого опыта матрицы планирования были измерены качественные показатели и выход соевого масла.
Для оптимального сочетания факторов, при которых очищенное соевое масло имеет минимальные значения массовой доли нежировых примесей и кислотного числа были заданы области компромиссных значений критериев оптимизации (таблица 1) и экстремальных значений.
Поскольку за экстремум поверхности отклика было взято кислотное число соевого масла, то компромиссная задача по отысканию условного экстремума решалась методом Соболя-Статникова.
Таблица 1 – Области компромиссных значений
-
Уступка, %
Х1
Х2
Х3
у1
у2
у3
∆у1 = 17,8
∆у2 = 17,8
∆у2 = 17,8
0,55
- 0,25
- 0,22
0,089
0,459
2,36
В результате решения компромиссной задачи независимые переменные, влияющие на критерии оптимизации, имеют следующие значения:
– частота вращения ротора центрифуги равна 195 с-1;
– высота слоя фильтрующего материала, 175 мм;
– размеры частиц фильтрующего материала, 5,0 мм.
При оптимальном сочетании факторов кислотность соевого масла составляет – 0,459 мг КОН/г, а массовое содержание нежировых примесей – 0,089 % , выход соевого масла – 2,36 кг/мин.
На рисунке 20 представлены экспериментальные и теоретические зависимости выхода соевого масла от размера частиц фильтрующего материала, частоты вращения ротора центрифуги и высоты фильтрующего слоя.
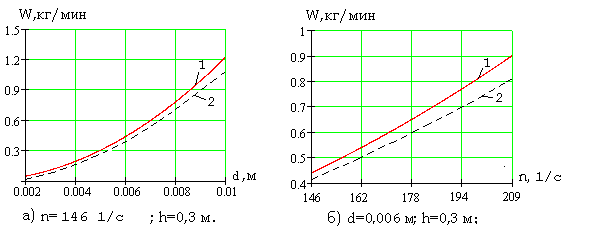
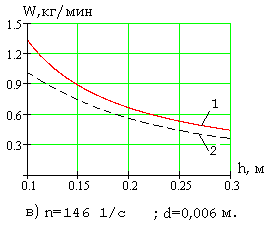
а) ω = 146 с-1, h = 0,3 м в) d = 0,006 м, h = 0,3 м г) ω = 146 с-1, d = 0,006 м
Рисунок 20. Экспериментальные и теоретические зависимости выхода соевого масла на конической фильтрующей центрифуге ВФКЦ-1 от размера частиц фильтрующего материала, частоты вращения ротора центрифуги и высоты фильтрующего слоя:1 – теоретические, 2 − экспериментальные
Из представленных графиков видно, что расчеты по теоретической формуле дают завышенные результаты, это связано с влиянием неучтенных факторов, однако, характер зависимости одинаков и расхождение данных для подобных исследований не превышает допустимые значения.
При исследовании центрифуги второго типа ВФКЦ-3 в качестве критериев оптимизации приняты: разность плотностей очищенного масла и дисперсионной фазы (Y1), плотность очищенного масла (Y2), кислотное число очищенного масла (Y3), массовая доля нежировых примесей (Y4), массовая доля влаги и летучих веществ (Y5)). Для экспериментальных исследований использовали подсолнечное неочищенное масло. Указанные качественные показатели очищенного масла определены в лаборатории НИИ химизации в соответствии с ГОСТ Р 5471-89, ГОСТ Р 5481-89, ГОСТ Р 50456-92, ГОСТ Р 52110-2003, ГОСТ Р 52465-2005.
В качестве регулируемых факторов использовались частота вращения ротора центрифуги Х1(ω, с-1), площадь отверстий на выходе очищенного масла из центрифуги Х2 (Fотв, м2), эквивалентный диаметр частиц цеолита Х3(d, м).
Для исследований использовали экспериментальную центрифугу, имеющую параметры: минимальный радиус внутренней обечайки конуса ротора rmin = 0,04 м, радиальное расстояние между внутренней и наружной обечайками ротора ℓ2 = 0,028 м, высота ротора H = 0,135 м, угол наклона 35o между образующей ротора с вертикальной осью центрифуги, суммарный конструктивный показатель kц = 0,00127 м3.
Для проверки теоретических исследований была проведена серия многофакторных экспериментов типа 33 по симметричному некомпозиционному плану Бокса-Бенкина второго порядка.После обработки результатов экспериментальных данных, проведенной с помощью прикладной программы «Statistiсa-6» с использованием метода оценки Ливенберг-Маркгуарда, были получены уравнения регрессии для функций
Δρ = f (ω, d, Fотв), ρоч = f (ω, d, Fотв), K = f (ω, d, Fотв), П = f (ω, d, Fотв), В = f (ω, d, Fотв) (таблица 2).
Графическая интерпретация функции П = f (ω, d, Fотв) представлена на рисунке 21.
Гипотеза значимости коэффициентов уравнений регрессии оценивалась критерием Стъюдента, а адекватность – критерием Фишера. Уровень значимости всех критериев р<0,05.
Статистическая проверка подтвердила адекватность полученных моделей и позволила определить степень влияния каждого из факторов на критерии оптимизации и установить пределы их рациональных значений (таблица 3).
Таблица 2 – Результаты оценки адекватности математических моделей и экспериментальных данных
Критерий оптимизации | Уравнения регрессии | R2 | R | Fрасч. | Fтабл. |
Разность плотностей, кг/м3 | Y=8,3+1,13Х1+0,77Х2 –1,43 Х3+0,00027Х2Х3–0,012Х12– 0,0077 Х22 +0,014 Х22 – в кодированном виде | 0,919 | 0,844 | 10,8 | 4,10 |
ρоч.− ρf..=− 0,036ω–0,07Fотв+0,0075ωFотв+ +387,07Fотвd–0,00017ω2–0,185F2отв+ 193750d2– в раскодированном виде | 0,954 | 0,911 | 23,9 | 4,40 | |
Плотность очищенного масла, кг/м3 | Y=916,2 + 0,83Х1 + 0,045Х2 – 2,46Х3 +0,0007Х1Х2 + +0,0006Х2Х3 +0,0006Х2Х3 – 0,0087Х12 –0,0007Х22 + +0,024Х32– в кодированном виде | 0,918 | 0,842 | 8,88 | 5,40 |
ρоч = 923,3 –0,036ω– 1,07Fотв +0,0075ωFотв + +387,07ωd –0, 00017ω2 – 0,19 Fотв 2 + 193759d2 – в раскодированном виде | 0,954 | 0,911 | 16,9 | 4,80 | |
Кислотное число очищенного масла, мг КОН/г | Y3 = 1,77 + 0,232Х1 + 0,084Х2 – 0,000015Х1Х2 + +0,000007Х1Х3 – 0,000045Х2Х3 – 0,0023Х12 – – 0,000793Х22 – в кодированном виде | 0,888 | 0,788 | 7,43 | 4,80 |
K=2,78 + 0,00135ω + 0,09Fотв− 599,657d + + 0,000919ωFотв − 0,23ωd – 72,28Fотвd – 0,00001ω2 + +0,02F2 + 92812,5d2 – в раскодированном виде | 0,955 | 0,912 | 13,8 | 6,60 | |
Массовая доля нежировых примесей, % | Y4=1,43 + 0,44Х1 + 0,22Х2 – 0,23Х3 + 0,00001Х1Х2 – – 0,000004Х1Х3 – 0,000064Х2Х3 – 0,0044Х12 – – 0,0022Х22 + 0,0023Х32 – в кодированном виде | 0,951 | 0,904 | 12,6 | 5,40 |
П=0,09 +0,01ω + 0,59Fотв–299,24d + 0,4ωd – – 0,0003ωFотв – 50,29Fотвd – 0,00004ω2 – 0,04Fотв2 + + 51250,02d2 – в раскодированном виде | 0,924 | 0,853 | 7,74 | 5,40 | |
Массовая доля влаги и летучих веществ, % | Y5 = 0,00002 + 1,69Х1 – 1,82Х2 – 0,0518Х3 – – 0,00002Х1Х2 – 0,00036Х1Х3 – 0,00052Х2Х3 – – 0,0168Х12 + 0,0178Х22 + +0,00097Х32 – в кодированном виде | 0,831 | 0,691 | 23,8 | 6,60 |
В = –2,0 + 0,033ω– 0,7Fотв + 351,5d –0,0047ωFотв – – 0,1ωd – 638,6Fотвd – 0,0001ω2 + 0,4Fотв2 + + 312812,4d2 – в раскодированном виде | 0,861 | 0,744 | 19,9 | 6,60 |
Fотв·10-6, м2
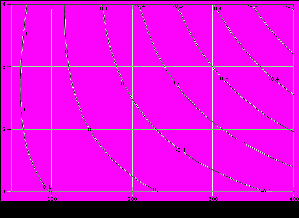
ω, с-1
Влияние частоты вращения ротора центрифуги Х1(ω) и площади отверстий на выходе очищенного масла из центрифуги Х2(Fотв) при фиксированном значении эквивалентного диаметра частиц цеолита Х3(d=0,002м) П = –0,26 + 0,014ω + 0,42Fотв −
–4,41∙10-5ω2 – 0,0003ωFотв –0,046Fотв2
d,м
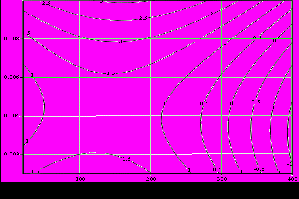
ω, с-1
Влияние частоты вращения ротора центрифуги Х1(ω) и площади отверстий на выходе очищенного масла из центрифуги Х2(Fотв) при фиксированном значении эквивалентного диаметра частиц цеолита Х3(d = 0,002 м)
П=–0,26+0,014ω + 0,42Fотв−
–4,41∙10-5ω2– 0,0003ωFотв – 0,046Fотв2
d, м
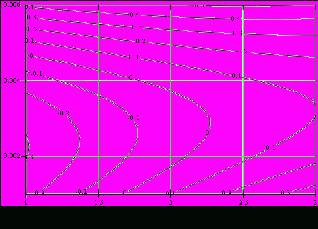
Fотв·10-6, м2
Влияние площади отверстий на выходе очищенного масла из центрифуги Х2(Fотв) и эквивалентного диаметра частиц цеолита Х3(d) при фиксированной частоте вращения ротора центрифуги Х1(ω = 150 с-1)
П=0,87 + 0,47Fотв − 304,62d –
–0,031Fотв2 − 50,29Fотвd+ 59423,08d2
Рисунок 21. Зависимость массовой доли нежировых примесей подсолнечного масла от конструктивно-кинематических факторов центрифуги
Из анализа экспериментальных исследований следует что рациональными параметрами центрифуги по критерию оптимизации (доли нежировых примесей в очищенном масле) являются: частота вращения ротора центрифуги ω<300 с-1, эквивалентный диаметр частиц цеолита d=0,002…0,004 м, площадь отверстий на выходе масла из центрифуги Fотв<2,5∙10-6 м2, при этом массовая доля нежировых примесей не превышает нуля.
Таблица 3 – Рациональные параметры анализируемых факторов процесса очистки подсолнечного масла на центрифуге ВФКЦ-3
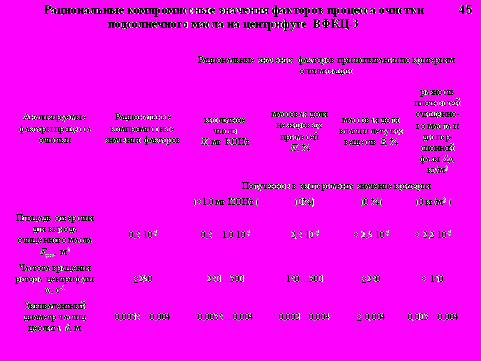
Δ ρэкс= 1,003Δ ρтеор + 0,04. (37)
Теснота связи между теоретическими и экспериментальными значениями разности плотностей характеризуется коэффициентами детерминации R2=0,95 и корреляции R=0,97 при доверительной вероятности р<0,05, что характеризует хорошую связь. Математическая модель (37) адекватна экспериментальным данным, так как расчетный критерий Фишера Fкр=96,3 больше табличного Fтабл=3,9.
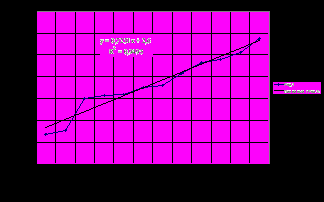
Рисунок 22. Зависимость теоретической (линейный ряд 1) разности плотности очищенного подсолнечного масла и дисперсионной фазы от экспериментальной (ряд 1)
Результаты исследований позволили сформулировать требования к параметрам вертикальных конических фильтрующих центрифуг, подтвердили обоснованность теоретической базы рабочего процесса рафинации растительных масел в принципиально новых конструкциях центрифуг.
Экспериментальными исследованиями подтверждены основные теоретические положения: адекватность математических моделей процесса очистки растительных масел на центрифугах первого и второго типов и математических моделей технологической линий. Подтверждены математические модели оценки индекса производительности, объема рабочего пространства, площади осаждения, мощности привода центрифуги, оценки качественных показателей очищенных растительных масел, параметров фильтровальной перегородки и зависимость качественных показателей очищенных масел от основного параметра математической модели – разности плотности, достоверность принятой теории очистки растительных масел при движении элементарного объема в межобечаечном пространстве ротора.
Достоверность полученных результатов подтверждается строгостью теоретических исследований и использованием современных методов обработки экспериментальных данных.
В пятой главе «Реализация и эффективность результатов исследования» приведены основные направления реализации результатов.
Результаты исследований и сформулированные на их основе предложения и новые технические решения использованы при создании экспериментальных образцов конических вертикальных фильтрующих центрифуг, а также их технической документации.
Краткая аннотация внедрения результатов исследования приведена на странице 6 автореферата.
Научные разработки по теме диссертации привели к новым техническим решениям, которые использованы в конструкции рекомендуемой вертикальной конической фильтрующей центрифуги ВФКЦ-4 (рисунок 23). Принципиальное отличие данной центрифуги − конструктивно- кинематические особенности рабочего органа.
В центрифуге ВФКЦ-4 предусмотрено устройство для центробежной выгрузки отработанного цеолита, что упрощает эксплуатацию. Устройство состоит из регулируемого по высоте кольца 12, расположенного в пространстве между обечайками 5 и 11. Перед выгрузкой цеолита диск устанавливается в верхнем положении и открывает отверстия в цилиндрической части наружной обечайки 5.
Конструкция вертикальной фильтрующей конической центрифуги, предлагаемой на основании проведенных исследований, позволяет заменить многостадийный процесс очистки в одном техническом средстве и получить масло, соответствующее требованиям нормативных документов.
В соответствии с методологической базой разработан порядок расчета вертикальной конической фильтрующей центрифуги. Схема расчета параметров вертикальных конических фильтрующих центрифуг приведена на рисунке 24.
На схеме ротора (рисунок 23) показаны основные конструктивные параметры центрифуги, подлежащие расчету: минимальный радиус rmin внутренней обечайки ротора 11, максимальный радиус rmax внутренней обечайки 11, минимальный радиус Rmin, наружной обечайки ротора 5, максимальный радиус Rmax наружной обечайки 5, угол наклона образующей конуса ротора относительно вертикальной оси центрифуги θ. Необходимо также рассчитать высоту ротора Н центрифуги и радиальное расстояние ℓ2 между внутренней 11 и наружной 5 обечайками ротора.
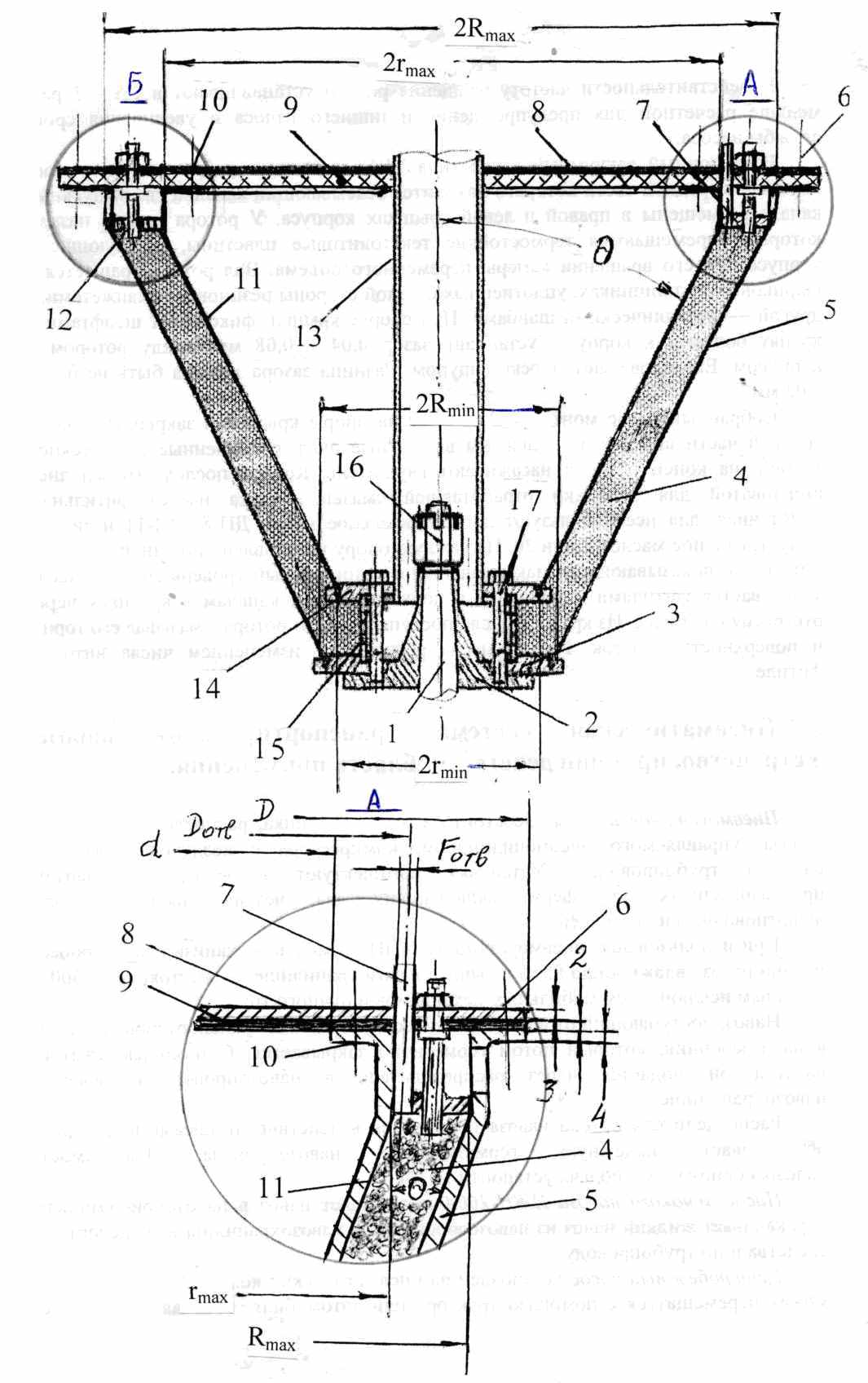
Рисунок 23. Схема ротора рекомендуемой центрифуги: узел А – крепление кольца центрифуги в сборе с отверстиями для вывода масла; 1– вал привода; 2 – основание ротора; 3 – диск для крепления наружной обечайки ротора; 4 – фильтрующий материал (цеолит); 5 − наружная коническая обечайка ротора; 6 – болты крепления наружной обечайки ротора; 7 – трубка для вывода масла; 8 – крышка ротора; 9 – прокладка; 10 – болты крепления внутренней обечайки ротора; 11 – внутренняя коническая обечайка ротора; 12 – кольцо в сборе; 13 – заливной цилиндр; 14 – диск для крепления внутренней обечайки ротора; 15 – перфорированная втулка; 16 – гайка крепления ротора; 17 – болты сборочные
В результате расчета по предложенной схеме (рисунок 24) и решения оптимизационной задачи по программе Delta RO Optimiz получены конструктивные параметры рекомендуемого ряда вертикальных фильтрующих конических центрифуг для очистки растительных масел.
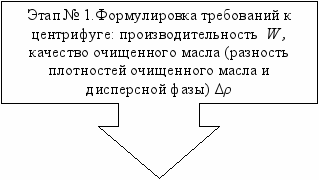
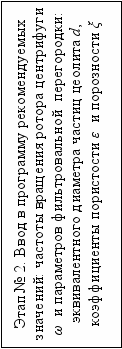
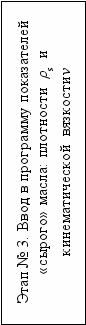
Этап № 4. Оптимизация конструктивных параметров по программе Delta RO Optimiz:
– минимального и максимального радиусов внутренней обечайки ротора центрифуги rmin, r max;
– минимального и максимального радиусов наружной обечайки ротора центрифуги Rmin, Rmax;
– высоты ротора H;
– угла наклона образующей конуса к вертикальной оси ротора центрифуги, θ;
– радиального расстояния между наружной и внутренней обечайками ротора ℓ2


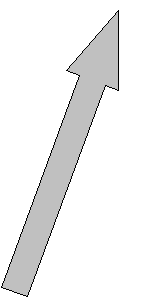
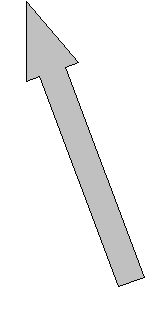

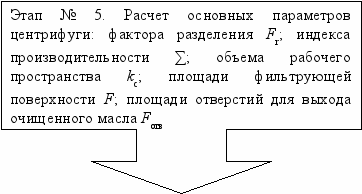
Этап № 6. Расчет технико-экономических показателей
Рисунок 24. Схема расчета параметров вертикальной конической фильтрующей центрифуги
В связи с конструктивными особенностями ротора центрифуги предложены математические модели расчета мощности привода.
Мощность, затрачиваемая на привод барабана с учетом его размерных характеристик
Nб=[ω2ρπ(H/Sinθ0) ℓ2(2rmin+Htg θ0 + ℓ2)] /(1000τµо),
где µо − коэффициент потерь энергии на перемещение массы масла в барабане при разгоне,
τ − время разгона, с.
Мощность, затрачиваемая на трение в подшипниках
Nт = ρπ ℓ2 (H/Sinθ0)(2rmin+ Htg θ0 + ℓ2) υƒ/1000,
где υ − окружная скорость точки на поверхности шейки вала, м/с, ƒ − коэффициент трения.
В связи с незначительной величиной мощностью, затрачиваемой на трение в подшипниках, пренебрегаем.
Мощность, затрачиваемая на трение барабана о воздух
Nв = 0,18 ∙10 -4 L( Rmin Rmax,) 2 ω3.
Суммарная мощность центрифуги (кВт)
NΣ =[ω2ρπ(H/Sinθ0) ℓ2(2rmin+Htg θ0 +ℓ2)] /(1000τµо)+ 0,18 ∙10 -4 L( R′min R′max,) 2 ω3.
После разгона мощность, потребляемая центрифугой
Nр = 0,25Nб + Nв .
По полученным формулам рассчитывается мощность привода размерного ряда центрифуг.
Предложена технологическая схема очистки растительных масел с использованием конической фильтрующей центрифуги, позволяющая получить максимальный технологический эффект.
Заключительным этапом расчета является оценка технологического эффекта в соответствии с разработанной новой методикой.
Значимость и перспективность научных исследований в области рафинации растительных масел оценивается, прежде всего, в соответствии с нашими исследованиями технологическим эффектом, отражающим влияние процесса очистки в разработанных центрифугах на качество получаемого масла.
Расчет технико-экономических показателей подтверждает целесообразность использования новых технических решений, так как улучшается качество очищенного масла.
Разработанный модельный ряд центрифуг при очистке масла на экспериментальной технологической линии по сравнению с базовой позволяет добиться снижения удельных эксплуатационных затрат на 25 %, энергоемкости на 66%, металлоемкости в 6,5 раза.
Годовая экономия эксплуатационных затрат составляет 47,9 тыс.р., годовой экономический эффект равен 271,2 тыс. р., срок окупаемости капитальных вложений составляет 2,8 года.
В результате проведенных расчетов и экспериментальных исследований основные положения можно сформулировать следующим образом.
300>