Научно-методологические основы производства золота на заключительном этапе разработки месторождений
Вид материала | Диссертация |
СодержаниеКонцентрация соляной кислоты |
- Научно-методологические основы производства золота на заключительном этапе разработки, 857.86kb.
- Системные подходы к снижению рисков при моделировании разработки нефтегазовых месторождений, 226.76kb.
- Опросы разработки газовых и газоконденсатных месторождений и эксплуатации скважин,, 1168.58kb.
- Положение о рейтинге Кафедра разработки и эксплуатации газовых и газоконденсатных месторождений, 11.1kb.
- Повышение эффективности выработки трудноизвлекаемых запасов нефти месторождений в заключительной, 293.03kb.
- Программа по специализации «Разработка и эксплуатация месторождений», 22.51kb.
- Темы курсовых проектов по дисциплине «Теоретические основы разработки нефтяных и нефтегазовых, 11.01kb.
- Федерации научно-методологические основы управления качеством продукции высшего профессионального, 749.58kb.
- Аудиторское заключение, 341.18kb.
- Темы курсовых работ по дисциплине «маркетинг» Теоретические и методологические основы, 33.15kb.
Таблица 7
Выщелачивание золота соляной кислотой в дезинтеграторе, %
Опыты | Концентрация соляной кислоты, % | ||||||
4,0 | 6,0 | 8,0 | 10,0 | 12,0 | 16,0 | 20,0 | |
1 | 18,6 | 32,1 | 42,2 | 46,9 | 51,8 | 55,6 | 61,5 |
2 | 20,3 | 30,0 | 41,0 | 45,7 | 53,3 | 57,1 | 61,3 |
3 | 21,0 | 32,4 | 42,5 | 47,2 | 54,0 | 55,9 | 61,8 |
4 | 19,1 | 31,3 | 41,3 | 46,0 | 52,1 | 57,4 | 58,9 |
5 | 20,6 | 31,8 | 42,8 | 47,9 | 53,6 | 56,2 | 59,6 |
6 | 19,4 | 32,7 | 41,6 | 47,5 | 52,4 | 57,7 | 60,3 |
7 | 20,9 | 31,6 | 43,1 | 46,3 | 53,9 | 59,5 | 62,1 |
8 | 19,7 | 29,9 | 43,2 | 47,8 | 52,7 | 55,3 | 59,9 |
9 | 21,2 | 31,9 | 41,9 | 46,6 | 54,2 | 57,5 | 62,4 |
10 | 20,0 | 30,3 | 43,4 | 48,1 | 53,0 | 56,8 | 61,2 |
, % | 20,1 | 31,4 | 42,3 | 47,0 | 53,1 | 56,6 | 60,9 |
Исследование сорбционных процессов в электрическом поле осуществлено на хвостах переработки руд месторождения Бадран состава, %: 1,1 цинка, 0,6 свинца, 1,1 меди, 20,6 железа, 1,4 оксида кальция, 1,9 оксида алюминия, 43 диоксида кремния, 6,1 серы, 17,1 углерода, золота 1,2 г/т, серебра 240 г/т.
Исходный раствор содержал 1∙10-2 мг-экв/дм3 золота. Содержание примесей, мг-экв/дм3: Fe и Сu по 0,1; Zn, Co, Ni по 0,05. Концентрация NaCN и NaOH в растворе - по 1 г/дм3.
Для интенсификации массообмена в капиллярах сорбента использовали частоты переменного электрического поля 5-40 Гц. В качестве сорбента использовали шлам алюминиевого завода, содержащий цеолиты. В процессе выщелачивания 1 г сорбента перемешивали с 1 л раствора гидроксида кальция. Параметры выщелачивания фиксировали при пропускании электрического тока силой 0,6 А, напряжением 36 В и частотой 16 Гц в течение 30 мин. Фильтрация достигала 60 удельных объемов в час.
Установлено, что наложение электрического поля увеличивает извлечение золота в раствор за одно и то же время в 1,5 раза. Увеличение силы тока увеличивает извлечение на 10-15% (табл. 8).
Эксперименты отличаются хорошей сходимостью с данными публикаций и подтверждают эффективность технологии электро-сорбционного выщелачивания золота из золотосодержащих пульп. Скорость выщелачивания увеличивается на 25-30 %, сорбционная емкость анионита АМ-2Б возрастает в 2,5-3 раз.
Таблица 8
Усредненные результаты исследования вариантов
Время выщелачивания, ч | Концентрация в растворе, мг/дм3 | Емкость сорбента, мг/г | ||
Альтернативный | базовый | альтернативный | Базовый | |
0 | 1,20 | 1,20 | 0,07 | 0,07 |
1,5 | 1,05 | 1,08 | 1,65 | 0,75 |
3,0 | 0,82 | 0,91 | 3,10 | 2,22 |
4,5 | 0,69 | 0,74 | 6,21 | 2,31 |
6,0 | 0,49 | 0,52 | 8,3 | 2,95 |
Технологические исследования электрохимического выщелачивания золота выполнены на хвостах флотационного обогащения рудной массы месторождения Бадран. Валовое содержание сульфидов в хвостах - 10-12%, из них 9 % пирита, остальные - арсенопирит. Содержание золота в пробе 1,2 г/т, свободного золота до 50%, ассоциированного с сульфидами до 20%, в сростках до 15%.
Максимальное извлечение золота в раствор зафиксировано при параметрах: Ж:Т=3:1, NaCl-28%, ток=1000 А/м2 , V=4,7в, Т=760С, рН=2,3, Eh=1050 Мв, t=3,5 час, извлечение золота в раствор 85% .
Параметры извлечения золота из промышленных стоков обогатительной фабрики исследованы в электролизере с катодной и анодной камерами, разделенными проницаемой диафрагмой из электрически нейтрального материала. Установлено, что рН анолита определяется плотностью тока. При прочих равных условиях и плотности тока 100 и 2200 А/м2 рН анолита составил 2,3 и 1,05, соответственно. При увеличении скорости тока растворов через камеры аппарата рН анолита увеличивался (табл. 9).
Таблица 9
Зависимость рН анолита от величины анодной плотности тока
Производительность 1,2 л/ч | |||||||
А/м2 | 0,108 | 0,217 | 0,435 | 0,870 | 1,304 | 1,739 | 2,174 |
рН | 2,30 | 1,95 | 1,66 | 1,50 | 1,30 | 1,15 | 1,05 |
Производительность 3,0 л/ч | |||||||
А/м2 | 0,108 | 0,217 | 0,435 | 0,870 | 1,304 | 1,739 | 2,174 |
рН | 2,60 | 2,30 | 2,05 | 1,75 | 1,55 | 1,40 | 1,30 |
При производительности одного аппарата электрохимического умягчения 2,5 м3 /час общая жесткость раствора снижается с 29 до 10 мг-экв/дм3 в результате выпадения в осадок ионов кальция, перехода в осадок 80-90% ионов магния и 99 % ионов металлов при отношение твердого к жидкому 1:10.
Нами рекомендована модернизированная во ВНИИХТ конструкция аппарата электрохимического умягчения (АЭХУ-8) с характеристикой: производительность - 8 м3/час; диаметр - 159 мм; высота - 2110 мм; площадь мембран - 0,64 м2; плотность тока 500-800 А/м2; потребляемая электроэнергия 1,0 А ч/м3.
В качестве базового рекомендован электродиализатор конструкции института ВНИПИПТ ЭДШ-60, производительностью 60 м3/час, оснащенный ионообменными мембранами Щекинского завода. Размер мембран 500х1000 мм. Рабочая площадь мембраны 1,32 м2.
С позиций гидродинамики процесс извлечения золота на различных участках технологической цепи можно представить в виде единого гидравлического потока, в котором выделяются звенья с различающимися параметрами.
Математическая теория течений жидкости изложена в трудах Л. Д. Ландау, Е. М. Лифшица, Л. И. Седова, Н. А. Картвелишвили, Т. Г. Войнича-Сяноженского, Х. Рауза, В. В. Шулейкина, И.Д. Музаева и др.
При выщелачивании минералов формируются стратифицированные течения выщелачивающих потоков. Первым является поток, омывающий минералы с прожилковой минерализацией, а вторым с вкрапленной минерализацией. Каждый поток характеризуется полями скоростей и плотности.
Система дифференциальных уравнений движения растворов:
- для первого потока:
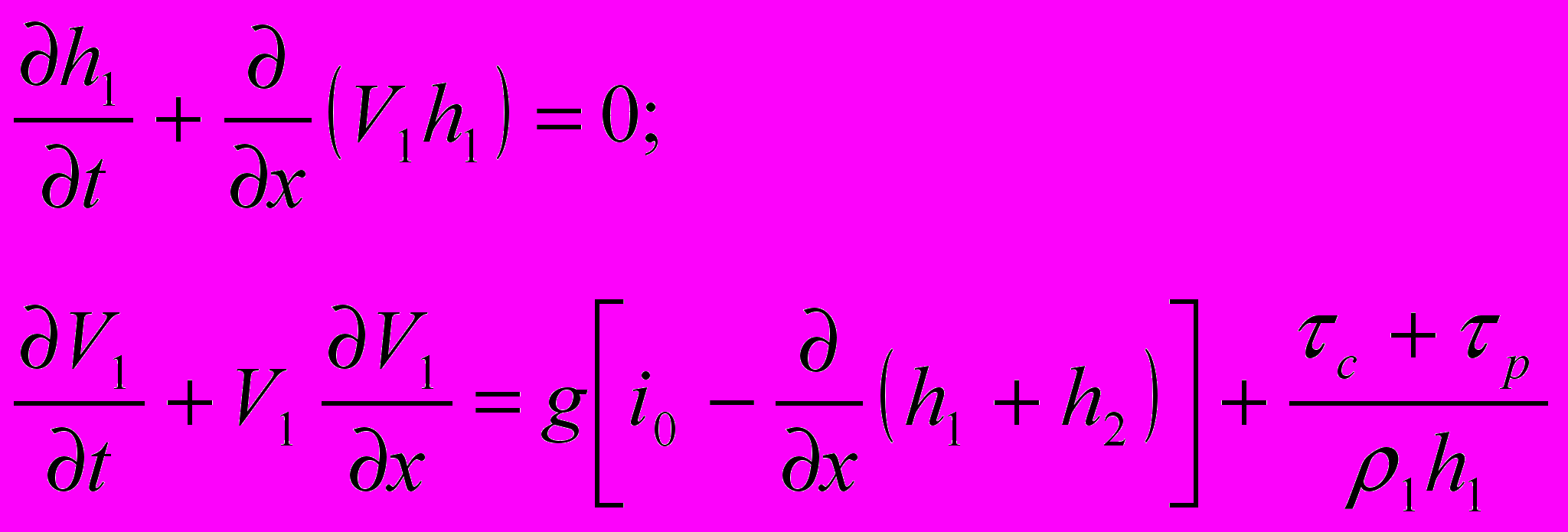
- для второго потока:
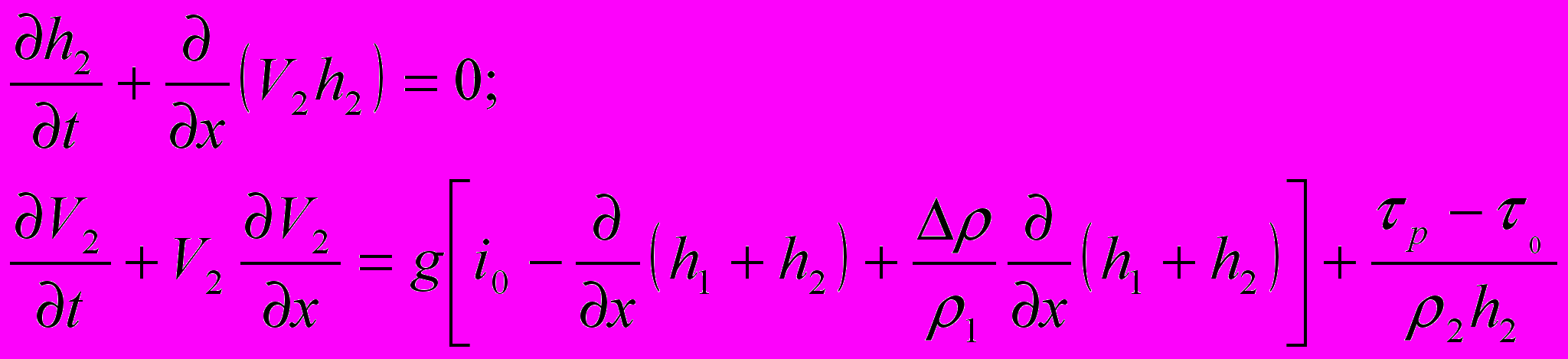
где
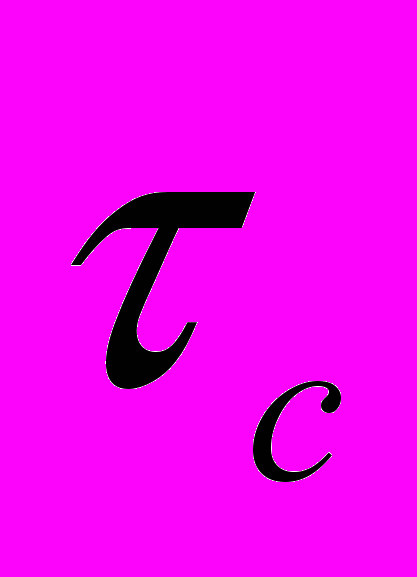

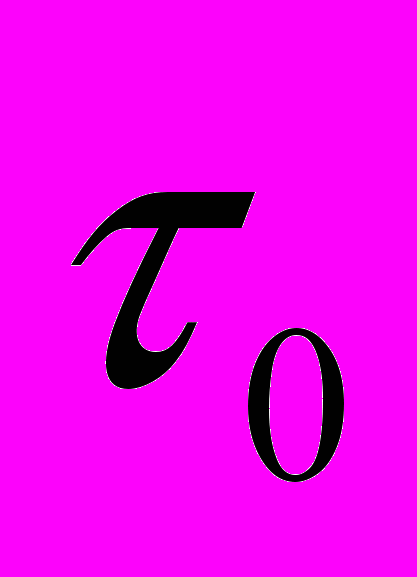
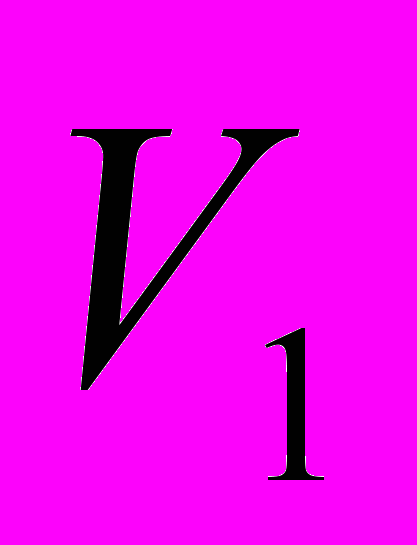
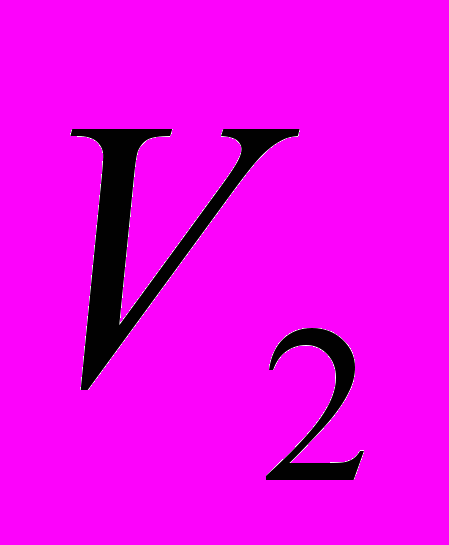
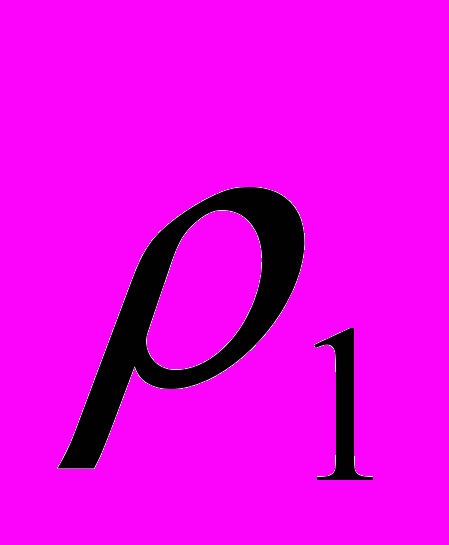
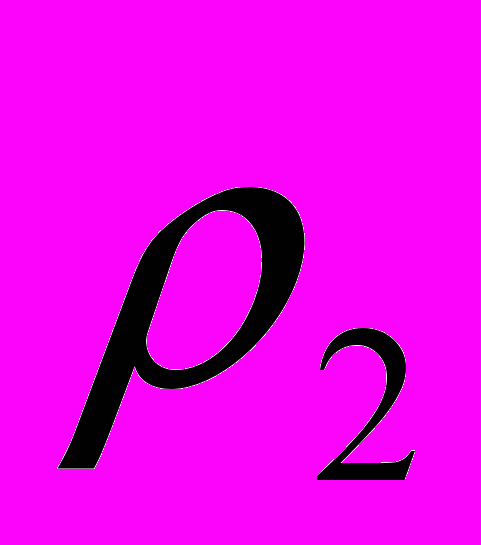
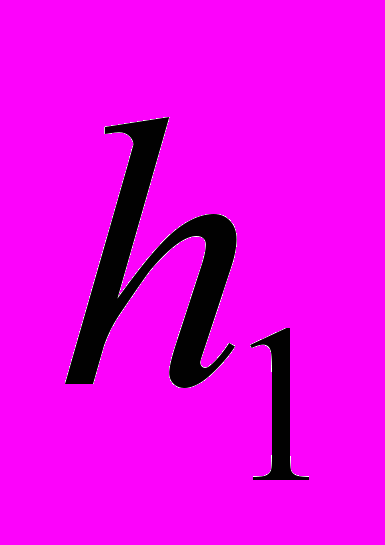
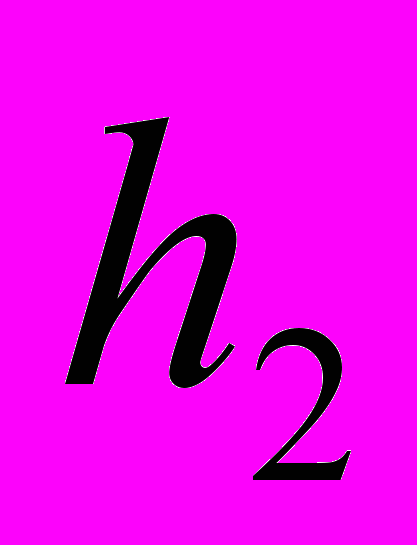
Оптимум затрат на выщелачивание достигается разделением потоков во времени и пространстве в пределах месторождения или группы штабелей на поверхности, поскольку в пределах выемочной единицы этого сделать технологически невозможно. Это позволяет сократить затраты реагентов и разброс времени на выщелачивание выемочной единицы.
Для определения пригодности отходов к выщелачиванию нами разра- ботана классификация (табл. 10).
Таблица 10
Классификация золоторудных минералов по пригодности к выщелачиванию
Признаки | Высокая пригодность | Средняя пригодность | Низкая пригодность |
Тип руд | Окисленные | Смешанные | Сульфидные |
Минерализация | Прожилковая | Ассоциация золота с кварцем и сульфидами железа | Вкрапленная |
Форма нахождения | Свободная | Смешанная | Вкрапленная |
Образования на поверхности | Отсутствуют | Присутствуют незначительно | Присутствуют |
Содержание | Более 1,5 г/т | От 1 до 1,5 г/т | Менее 1,5 г/т |
Наличие вредных примесей | Растворимы только золотосодержащие минералы | Незначительное содержание легкорастворимых минералов | Значительное количество легкорастворимых минералов |
Эффективная пористость | Более 20% диаметра более 0,009 мм | От 1 до 20 % диаметра до 0,009 мм | Менее 1 % диаметра менее 0,001 мм |
Крупность руд | Более 60% фракций – 25 мм | Менее 40 % фракций – 25 мм | Менее 20% Фракций – 25 мм |
Крупность хвостов | Более 80 % фракций – 0,074 мм | Более 50% фракций – 0,074 мм | Менее 50% фракций – 0,074 мм |
Фильтрационные свойства | Коэффициент фильтрации 0,1-0,2 м/с | Коэффициент фильтрации от 0,08 до 0,15 м/с | Коэффициент фильтрации ниже 0,05 м/с |
Состояние руд и хвостов | Хранились более 10 лет | Хранились от 5 до 10 лет | Хранились менее 5 лет |
Запасы сырья | Более 10 лет по 300-500 тыс.т/г. | От 5 до 10 лет по 300-500 тыс. т/г. | До 5 лет по 300-500 тыс. т/г. |
Климатические условия | Круглогодичное выщелачивание | Выщелачивание большую часть года | Выщелачивание с обогревом |
Исследованиями инновационных технологий установлено:
- эффективность извлечения золота из сульфидсодержащего сырья зависит от степени ассоциации золота с пиритом и арсенопиритом и их размеров, параметров воздействия электрическим полем, электропроводности раствора, параметров рН, Еh и температуры раствора;
- оптимальное значение плотности тока для выщелачивания золота из исследованных сульфидных руд лежит в пределах 800-1000 А/м2 площади анода;
- оптимальное значение температуры электрохимического процесса растворения сульфидов лежит в пределах 60-800С. Уменьшение температуры тормозит процесс выделения атомарного хлора, а увеличение - снижает перенапряжение кислорода и уменьшает выход продуктов окисления.
Таким образом, при использовании инновационных технологий подземного, кучного, сорбционного и электрохимического извлечения металлов показатели извлечения золота из запасов техногенных месторождений улучшаются до приемлемого по экономическим соображениям уровня, а остаточное содержание уменьшается до фоновой величины.
Защищаемое положение 4. Максимальное извлечение золота при поэтапной разработке месторождения обеспечивается выходом оптимальной для выщелачивания крупности руд, дифференцировано для прожилкового и вкрапленного типа оруденения при взрывной отбойке и размещением хвостов обогащения в хранилищах из условия использования феномена природного выщелачивания.
Освоение инновационных технологий нуждается в получения руд заданной крупности с определенной достоверностью. Качественное разрушение пород, облегчающее последующее выщелачивание золота, состоит в отделении зерен полезного компонента от зерен пустой породы, что достигается при избирательном расходе энергии только на разрыв межатомных связей вдоль поверхностей срастаний.
Установлена зависимость показателя степени дробления и среднего линейного размера куска взорванной массы от удельного расхода ВВ. С увеличением удельного расхода ВВ с 0,6-0,7 до 2-2,1 кг/м3 средний линейный размер куска снижается с 10-12 до 5-6 см, а показатель степени дробления возрастает с 1,2-1,3 до 1,5-1,6.
Показатель оптимальности буро-взрывной отбойки - крупность отдельных кусков разрушенного взрывом массива. При добыче металлов выщелачиванием это требование определяется не только возможностями устройств и механизмов, участвующих в переработке руд, но и созданием условий для проникновения выщелачивающего реагента в глубь куска.
Установленная зависимость изменения диаметра кондиционного куска от количества выделенных фракций с позиции полноты выщелачивания показывает, что излишнее измельчение руды чрезмерно увеличивает площадь компонентов горной массы и снижает фильтрационную способность выщелачиваемого массива. Толщина выщелачиваемого слоя зависит от скорости прохождения раствора: чем больше скорость раствора, тем меньше толщина диффузионного слоя.
Гранулометрический состав хвостов оказывает максимальное влияние на скорость фильтрации выщелачивающего раствора и на показатели выщелачивания.
На месторождениях с вкрапленной минерализацией полезный компонент в отбитой руде при дроблении распределяется равномерно по содержанию в кусках разной крупности, поэтому извлечение снижается пропорционально выходу крупных классов.
При прожилковой минерализации мелкие классы имеют более высокое содержание металла. Несмотря на относительно невысокое извлечение металлов из кусков размером +150 мм, удельные потери, приходящиеся на их долю, невелики, а в ряде случаев – гораздо меньше, чем из мелочи. Увеличение размера средневзвешенного куска отбитой руды за счет повышения выхода средних и крупных классов и сокращения удельного веса мелких классов не только не ухудшает показатель извлечения, но даже положительно влияет на показатели добычи металла на всех переделах.
Для многих жильных месторождений содержание полезного компонента в отбитой руде снижается с увеличением размера кусков. Среднее содержание в негабаритных классах (+200 мм) в 5 и более раз ниже, чем в товарном, с точки зрения выщелачивания, продукте в кусках размером от 0 до 200 мм, а суммарное количество в них металла превышает 92 % от запасов в блоке подземного выщелачивания (ПВ).
Установлено изменение содержания золота в зависимости от крупности фракций (рис. 7).
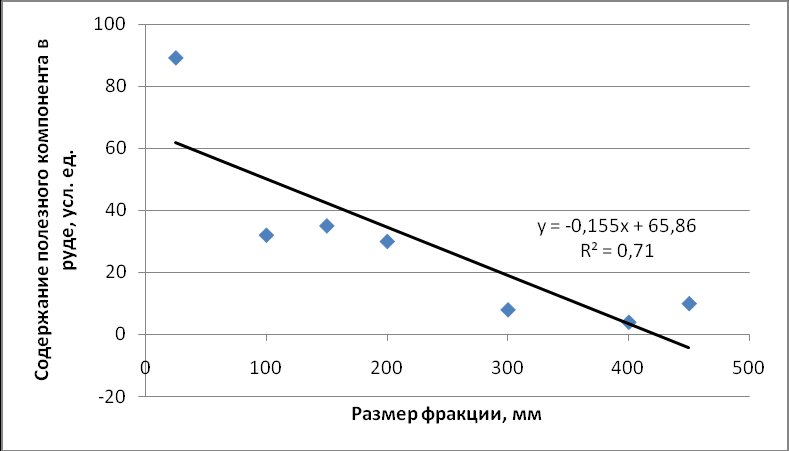
Рис. 7. Изменение содержания золота в зависимости от крупности фракций
Уровень оптимальности взрывного дробления горной массы должен определяться не только возможностями устройств и механизмов, участвующих в переработке руд, но и созданием условий для проникновения выщелачивающего реагента в глубь куска на завершающем этапе разработки месторождения.
При вкрапленной минерализации к дроблению предъявляются повышенные требования, прежде всего, ограничение выхода негабарита, которым в данном случае является величина 5 см. В этом случае предпочтительны гидрометаллургические способы выщелачивания с переводом минералов в пульпу.
При прожилковой минерализации к дроблению предъявляется требование ограничения выхода слишком малых частиц, предельной для которых является величина 2 см. В этом случае предпочтительны способы кучного выщелачивания золота с корректировкой недостатков дробления в процессе переработки (табл. 11).
Таблица 11
Крупность дробления минералов для целей выщелачивания золота
Категория | Размеры, см | Недостатки | Процессы корректировки |
Вкрапленная минерализация | |||
Неприемлемая | более 10 | Весьма малая скорость выщелачивания, повышенные потери | Оптимизация параметров отбойки, дробление при обогащении |
Нежелательная | от 10 до5 | Пониженная скорость выщелачивания, потери | Дробление при обогащении |
Оптимальная | от 5 до 2 | Нет | Нет |
Мелкая | от 2 до 1 | Малая скорость фильтрации растворов, разубоживание попутными минералами | Интенсификация процесса фильтрации |
Весьма мелкая | менее 1 | Весьма малая скорость фильтрации растворов, разубоживание попутными минералами | Окомкование вяжущими веществами |
Прожилковая минерализация | |||
Оптимальная | более 2 | Нет | Нет |
Мелкая | от 2 до 1 | Малая скорость фильтрации растворов, разубоживание попутными минералами | Интенсификация процесса фильтрации |
Весьма мелкая | менее 1 | Весьма малая скорость фильтрации растворов, разубоживание попутными минералами | Окомкование вяжущими веществами |
В отличие от традиционных схем при подготовке руды к выщелачиванию параметры БВР должны обеспечивать:
- равномерное дробление с минимальным выходом негабаритных фракций;
- равномерное разрыхление взорванного слоя руды;
- полную проработку взрываемых участков массива.
Проведено моделирование управления параметрами БВР при подготовке руды к выщелачиванию. Применяемая технология подэтажного обрушения с торцовым выпуском руды предопределяла способ отбойки в зажатой среде, исключающий многорядное взрывание. Выход негабарита составлял 10% (табл. 12).
Таблица 12
Гранулометрический состав отбитой руды
Размер фракций, мм | 0-2 5 | 25-50 | 50-100 | 100-200 | 200-300 | 300-400 |
Доля фракций,% | 35,25 | 8,77 | 17,94 | 15,53 | 5,47 | 12,02 |
Для исключения отрицательного влияния структурных особенностей массива и последствий однорядного взрывания в зажиме применен вариант отбойки с использованием врубовых скважин и внутривеерного замедления.
В отбиваемом подэтаже дополнительно к вертикальному вееру скважин бурили две наклонные скважины под углом 80-85° в сторону обрушения. Взрыванием зарядов наклонных скважин создавалась врубовая полость, слой разламывался, и происходила подвижка зажимающей среды. Заряды последующих скважин работали уже на две обнаженные плоскости.
Если при базовом способе отбойки руда отделялась от массива без дробления, то в предложенном варианте происходило интенсивное дробле-
ние и равномерное размещение взорванной горной массы в призабойной зоне.
Новая технология обеспечила оптимальную степень дробления, выход некондиционных фракций +300м составил 1-2% против 10-12% при базовом способе отбойки (рис. 8).
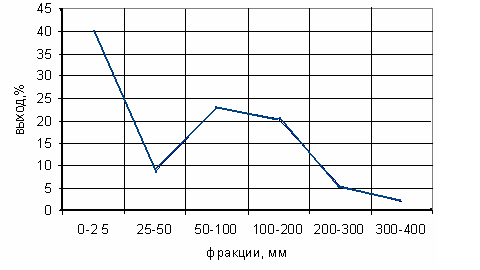
Рис.8. Показатели дробления при варианте с наклонным врубом
Подавляющее большинство хвостов первых этапов оставляется в подземных блоках в виде забалансовых руд или складируется на земной поверхности. Среднее содержание золота в отвалах окисленных золотосодержащих руд на территории России - 2,7 г/т, а в хвостах обогатительных фабрик - 1,1 г/т. Общее количество золота в хвостах примерно равно его балансовым запасам и прогнозным ресурсам коренных месторождений.
Динамика изменения качества хвостов обогащения при хранении устанавливается экспериментально с содержанием металлов в отвальных хвостах обогащения, % : золота -1,2 г/т, серебра -24 г/т; 0,5- цинка, 0,6- свинца, 1,1- меди, 10 -железа, 1,9-оксида алюминия, 43 -диоксида кремния.
Исследованы две модели, различающиеся содержанием и характером оруденения золота в хвостах. Массив формируется слоями минералов, обладающих различным содержанием металлов и электрическим потенциалом (рис. 9).
Модель №1