С закономерным изменением качества поверхностных слоев
Вид материала | Закон |
СодержаниеСписок литературы |
- «Переходы поверхностных фаз на начальной стадии эпитаксиального роста Ge на Si(111),, 33.37kb.
- Трибоспектроскопия – инструмент для анализа качества покрытий. Компьютерное моделирование, 61.23kb.
- Изменение химического состава поверхностных слоев металлических сплавов трибологических, 95.72kb.
- Нш-6291. 2010. 3 «Термодинамические, механические, реологические и электрические свойства, 214.42kb.
- Фисун С. Ф., Запольская, 132.69kb.
- Анализ временной динамики и пространственной изменчивости качества поверхностных вод, 402.73kb.
- Методика контроля качества поверхностных и дренажных вод на осушаемых землях, 237.99kb.
- Методические рекомендации по формализованной комплексной оценке качества поверхностных, 53.08kb.
- Администрация города кемерово постановление, 307.36kb.
- Повышение социально-экономического уровня и качества жизни для всех слоев населения, 215.42kb.
Вестник Брянского государственного технического университета. 2011. № 1 (29)
УДК 621.9
В. П. Фёдоров, М. Н. Нагоркин, И. Л. Пыриков
ОТДЕЛОЧНО-УПРОЧНЯЮЩАЯ ОБРАБОТКА ПОВЕРХНОСТНЫМ
ПЛАСТИЧЕСКИМ ДЕФОРМИРОВАНИЕМ ДЕТАЛЕЙ МАШИН
С ЗАКОНОМЕРНЫМ ИЗМЕНЕНИЕМ КАЧЕСТВА ПОВЕРХНОСТНЫХ СЛОЕВ
Рассмотрены способы технологического обеспечения заданного закономерного изменения качества поверхностного слоя деталей машин на универсальных металлорежущих станках и станках с ЧПУ.
Ключевые слова: качество поверхности, закономерное изменение, отделочно-упрочняющая обработка, поверхностное пластическое деформирование, программируемая система обработки, контроллер, шаговый привод, моделирование обработки.
Современный подход к технологическому обеспечению равномерности эксплуатационных свойств по всей обрабатываемой поверхности основан на формировании заданной закономерности изменения параметров качества в пространственной области, компенсирующей соответствующие изменения эксплуатационных факторов. Успешная реализация такого подхода должна в первую очередь базироваться на анализе закономерностей воздействия факторов эксплуатации на функциональные поверхности деталей соединения.
Задача технологического обеспечения заданного закономерного изменения качества поверхностного слоя может решаться при обработке деталей как на универсальных металлорежущих станках, так и на станках с ЧПУ. Эффективность решения задачи в последнем случае возрастает в связи с возможностями компьютерного моделирования, программных средств обработки и современных технологических систем.
Универсальные металлорежущие станки не обладают требуемой технологической гибкостью [5], так как у них отсутствует возможность управления режимами обработки (скорость резания, подача и др.) в процессе выполнения технологического перехода. В этом случае возможность управления закономерным изменением качества поверхностного слоя деталей, обрабатываемых методами отделочно-упрочняющей обработки поверхностным пластическим деформированием (ОУО ППД), достигается путём применения дополнительных механических устройств (например, копиров), следящих гидравлических устройств, современной автономно управляемой технологической оснастки и комбинированных методов обработки с использованием управляемых физических воздействий на обрабатываемую поверхность (электромеханическая обработка (ЭМО) и др.).
На рис. 1 представлена схема обработки вала с закономерно изменяющимся качеством поверхности методом ППД на токарном станке с применением копира. Анализ условий эксплуатации узла позволяет установить эпюру 1 распределения внешней эксплуатационной нагрузки Р = f(X) по длине вала (рис. 1а). Требуется обеспечить равномерный и по возможности минимальный износ его поверхности. Для этого определяются требуемые параметры качества (например, поверхностная микротвёрдость Hμ, высотные параметры шероховатости R (Ra, Rz или Rmax)) для различных участков поверхности вала (ab, bc, cd, de, ef), соответствующих характерным участкам эпюры Р = f(X), т. е. регламентируется закономерность изменения параметров качества по обрабатываемой поверхности. На стадии проектирования техпроцесса определяются условия ОУО ППД (вид индентора, его геометрические параметры, скорость обработки V, величина продольной подачи Sx, СОТС и т. п.). Далее с учётом установленных нерегулируемых условий обработки рассчитываются требуемые значения регулируемого фактора для всех участков обрабатываемой поверхности из условия обеспечения требуемых значений параметров качества и строится эпюра его распределения по длине вала.
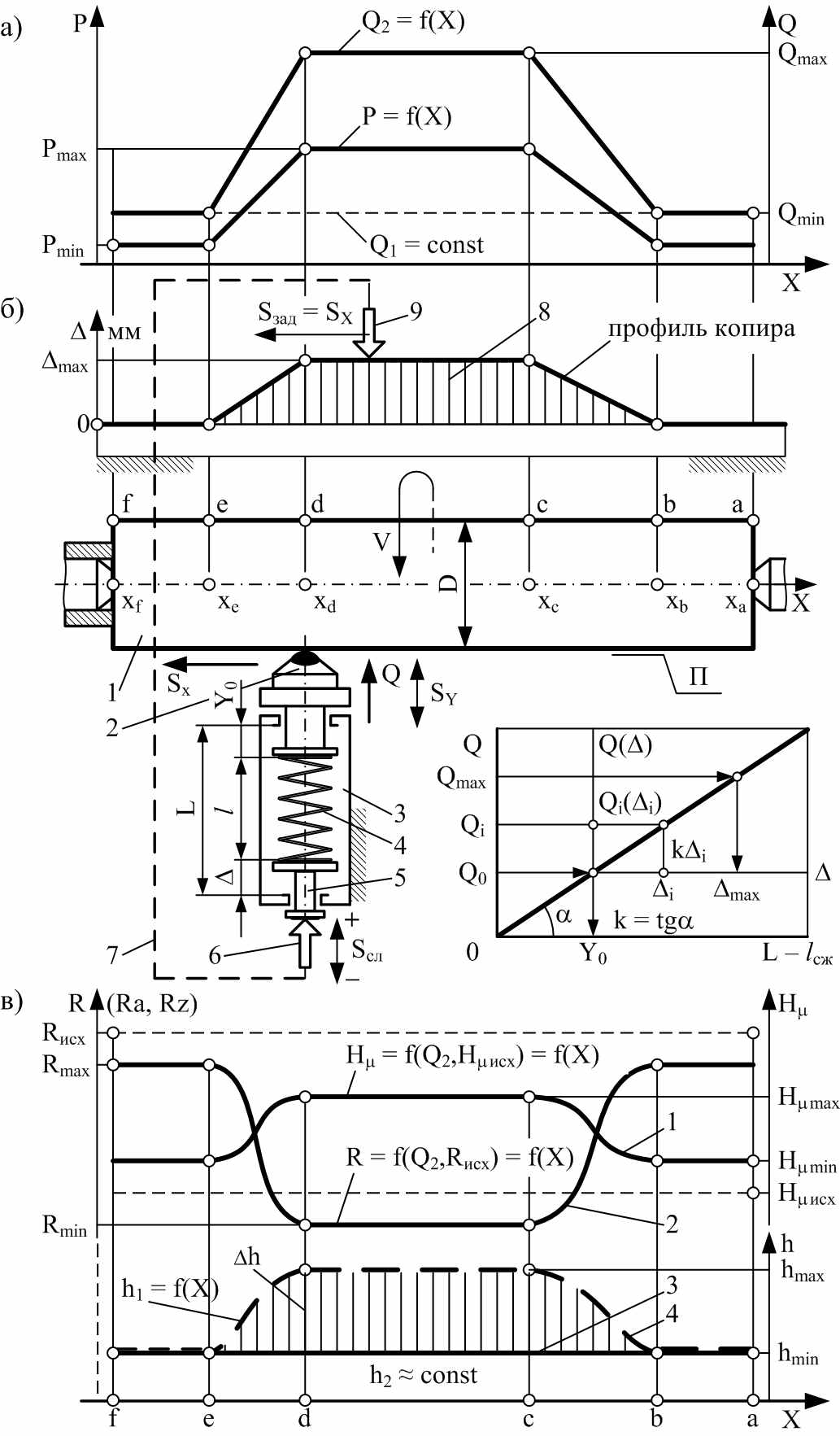
Рис. 1. Обеспечение закономерного изменения качества поверхности при ОУО ППД
на токарном станке с использованием копира: а – эпюры эксплуатационной нагрузки (P)
и технологической силы (Q) воздействия на поверхность; б – схема обработки;
в – эпюры распределения параметров качества (R, H) и ожидаемой
величины износа h по обработанной поверхности
В данном случае рассматривается алмазное выглаживание с помощью устройства упругого действия с изменением в процессе обработки силы Q воздействия индентора на обрабатываемую поверхность (эпюра распределения Q2(X) на рис. 1а). Программа обеспечения заданной эпюры изменения силы Q заложена в профиле копира 8 (рис. 1б), который рассчитывается с учётом её требуемого значения для каждого обрабатываемого участка поверхности П вала 1, жёсткости пружины 4 устройства для ППД и коэффициента усиления ε канала передачи информации от щупа 9 через механическую связь 7, толкатель 6 на регулирующий элемент (упор) 5, непосредственно воздействующий на пружину 4 (в данном случае ε = 1, так как используется жёсткая единичная механическая связь 7). В процессе обработки устройство ППД, корпус 3 которого неподвижно закреплён в резцедержателе станка, перемещается с подачей Sx, являющейся задающей подачей Sзад. Сила воздействия индентора 2 на поверхность П складывается из двух составляющих (рис. 1б): постоянной составляющей Q0 = Qmin, которая устанавливается при наладке устройства на участке ab путём предварительной деформации пружины 4 на величину y0; переменной составляющей Q(∆), которая определяется величиной ∆ дополнительного сжатия пружины 4 при перемещении упора 5 со следящей подачей Sсл.
Максимально допустимая величина ∆ дополнительного сжатия пружины 4 составляет [∆max] = L – lсж – y0, где L – длина пружины в свободном состоянии (y = 0, ∆ = 0), lсж – длина пружины в сжатом состоянии.
Формирование силы Q подчиняется закону
Qi = Q0 + Qi(∆i) = ky0 + k∆i,
где k – тарировочный коэффициент пружины 4. Тарировочный график устройства для ППД показан на рис. 1б.
В результате обработки ППД с переменной силой Q формируется качество поверхностного слоя, параметры которого изменяются с заданной закономерностью. Качественный вид закономерностей для микротвёрдости (Hμ = f(Q, Hμ исх)) и высотных параметров шероховатости (R = f(Q, Rисх)) показан на рис. 1в (графики 1, 2).
При расчёте условий обработки необходимо учитывать влияние технологической наследственности, проявляющееся через значения параметров Hμисх и Rисх, полученные на предыдущих этапах обработки. Обеспечение закономерного изменения качества поверхности в процессе обработки позволяет с достаточной степенью уверенности ожидать равномерного износа поверхности h в процессе эксплуатации (рис. 1в, график 3) при заданной неравномерной нагрузке P = f(X) (рис. 1а). Обработка при постоянных режимах привела бы к обеспечению равномерного качества поверхности и к неравномерности её износа (рис. 1в, график 4).
Обработка плоских поверхностей с закономерно изменяющимися параметрами качества может быть реализована на вертикально-фрезерном станке методом прямого копирования (рис. 2а). Обработка плоской поверхности П осуществляется устройством ППД упругого действия, включающим инденторы 2, упругий элемент (пружину) 3, ползун 4 и установленным в шпинделе 5. Обрабатываемая деталь 1 крепится на дополнительном столе 6, который перемещается по оси Z.
Сила Q воздействия инденторов 2 на поверхность П и соответствующий профиль копира ∆ = f(X) рассчитываются аналогично случаю обработки гладкой цилиндрической поверхности (рис. 1).
Закон изменения силы обработки Q = f(X) формируется за счёт дополнительной деформации упругого элемента 3 на величину ∆, которая зависит от текущего значения координаты X и передаётся от жёстко закреплённого копира 7 через ролик 8 на дополнительный стол 6 и далее по цепи: деталь 1 – инденторы 2 – упругий элемент 3. Соответствующая эпюра Q = f(X) показана на рис. 2б.
Ролик 8, который является щупом (считывающим элементом), воздействует на поверхность копира 7 с силой 2F, равной сумме веса подвижных по оси Z частей (стол 6, деталь 1 и др.) и силы обработки Q. Такая схема обработки работоспособна, так как аналогичная ей схема получила апробацию при фрезеровании фасонных поверхностей на станках с использованием метода прямого копирования. В качестве устройств для реализации ОУО ППД по данной схеме могут быть использованы самые различные устройства, в том числе и устройства для вибронакатывания по методу Ю. Г. Шнейдера [6]. Это относится и к инденторам: в зависимости от задач обработки и имеющейся оснастки можно использовать шарики, ролики, алмазные выглаживатели.
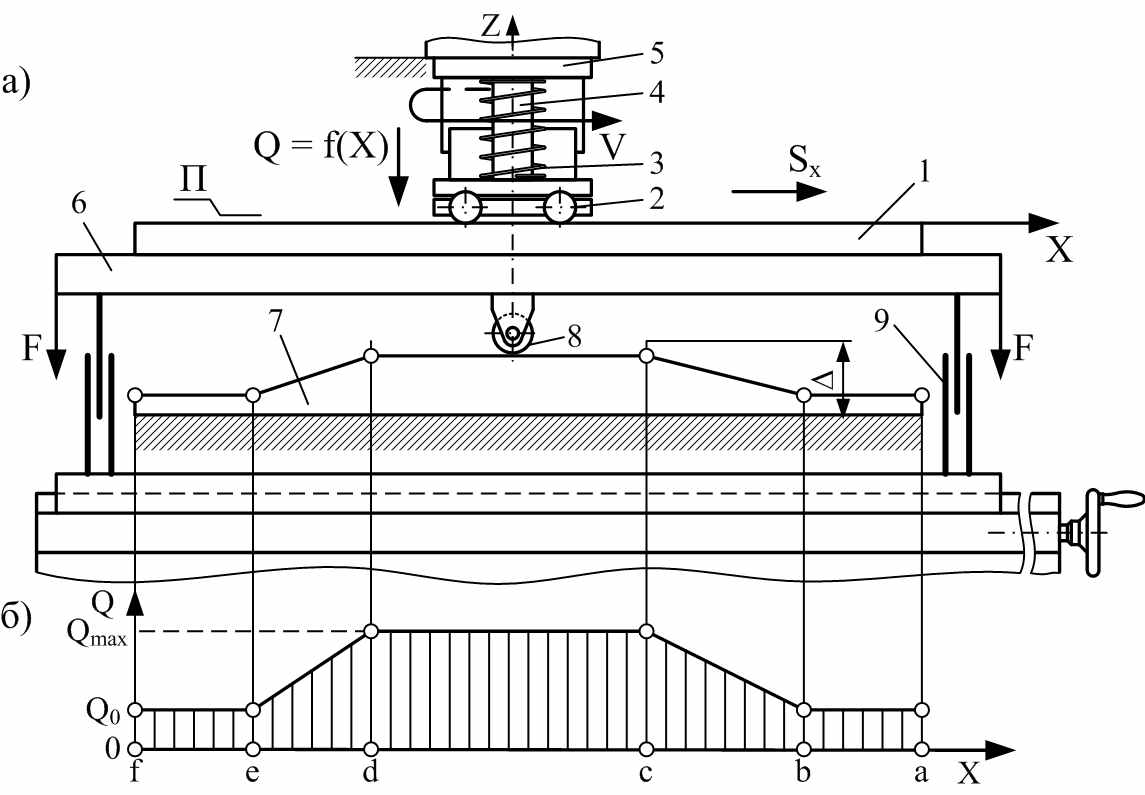
Рис. 2. ОУО ППД плоских поверхностей деталей с заданным законом
изменения качества на вертикально-фрезерном станке с использованием
метода прямого копирования: а – схема обработки; б – эпюра распределения
силы обработки Q по участкам обрабатываемой поверхности
Подобные методы обеспечения заданного закона изменения параметров качества поверхностей при ОУО ППД на универсальных станках отличаются простотой реализации, невысокой стоимостью, доступностью. Основным их недостатком является низкая мобильность, обусловленная необходимостью расчёта и изготовления копира для каждого конкретного типоразмера детали, закона воздействия на поверхность эксплуатационных факторов в её пространственной области, что связано как с материальными, так и с временными затратами. Кроме того, используемые станки для ОУО ППД должны быть конструктивно адаптированы к применению таких систем.
Вместо рассмотренных схем ОУО ППД, являющихся простейшими механическими следящими системами прямого действия, можно использовать гидравлические или электрические следящие системы.
Широкие возможности по обеспечению заданного закономерного изменения параметров качества поверхности в процессе обработки открываются при использовании программируемых устройств ППД упругого действия, которые могут автономно применяться на различном универсальном металлообрабатывающем оборудовании. Примерная блок-схема такой системы для ОУО ППД на токарных станках представлена на рис. 3.
Поверхность П детали 1 в процессе обработки подвергается воздействию индентора 2 с силой Q ± ∆Q, изменяющейся по заданному закону, обеспечивающему требуемую закономерность изменения формируемого при этом параметра качества R как функции X: R = f(X). Вид закона ∆Q = f(X) определяется на стадии технологической подготовки производства с учётом требований конструкторской документации.
В состав системы входят устройство ППД упругого действия, включающее толкатель 5, упругий элемент, установленный в корпусе 4, плунжер 3 с закреплённым в держателе индентором 2; переносной блок питания 11; шаговый двигатель 9 и программируемый контроллер 10, которые конструктивно могут составлять одно целое (например, сервопривод типа СПШ10); редуктор 7 (желательно червячный, это сокращает габариты привода (элементы 9, 10)); исполнительный элемент 6, служащий для передачи вращательного или возвратно-поступательного движения толкателю, непосредственно воздействующему на упругий элемент устройства ППД. Устройство ППД и элементы 6, 7, 9, 10 конструктивно представляют единое устройство, закреплённое в резцедержателе суппорта, который движется с задающей подачей Sx.
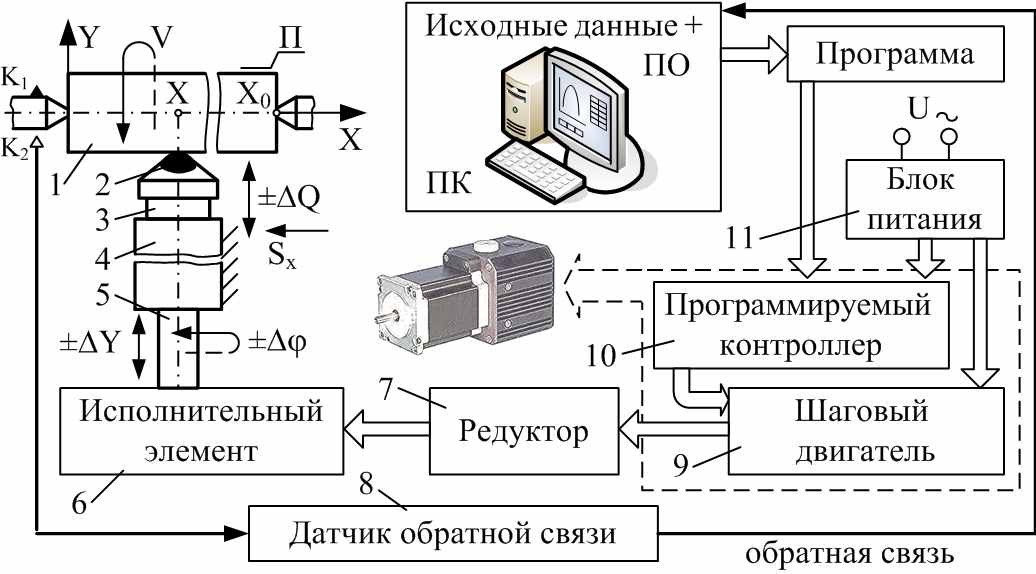
Рис. 3. Схема программируемой системы упругого действия для ОУО ППД
деталей с закономерно изменяющимся качеством на токарных станках
В соответствии с требуемым законом изменения силы Q и другими исходными данными на ПК при использовании, например, программируемого контроллера ЕМС2 разрабатывается программа управления шаговым двигателем, которая вводится в энергонезависимую память контроллера СПШ10, имеющую 8 банков программ.
Индуктивный датчик обратной связи 8 (рис. 3) подает в виде импульсов информацию о суммарном количестве N оборотов шпинделя с момента пуска, которая легко переводится в текущую координату X обрабатываемой точки поверхности (X = NSx, Sx – подача, мм/об).
При отсутствии датчика осуществляется разомкнутое управление, начало цикла которого определяется первоначальным положением индентора, а закон изменения силы Q формируется в зависимости от подачи Sx и времени t. В этом случае текущая координата определяется соотношением
X = X0 – Sxnt,
где X0 – координата начальной точки обработки; Sx – величина подачи, мм/об; n – частота вращения шпинделя, мин–1; t – время, прошедшее с момента начала обработки, с.
Эта система позволяет обрабатывать конические и фасонные поверхности, перепады высот контура которых технически обеспечиваются устройством ППД, т. е. соответствуют допустимому перемещению ползуна 3.
Программируемая система для ОУО ППД при невысокой стоимости обладает автономностью использования, высокой мобильностью, широкими возможностями решения задач инженерии поверхности в плане создания закономерно изменяющегося качества в процессе обработки. Она может использоваться в серийном, мелкосерийном, единичном и ремонтном производствах.
Для обработки поверхностей с закономерным изменением качества, включающего как геометрические и физико-механические параметры, так и формирование микрорельефов с заданной топографией, целесообразно использовать современное оборудование, оснащённое компьютеризированной системой ЧПУ типа CNC или модернизированное. Реализация ОУО ППД для формирования поверхности с закономерным изменением качества при наличии соответствующего оборудования требует разработки или использования соответствующих программ обработки. Как правило, для их составления применяется метод параметрического программирования, который максимально использует вычислительные возможности микроЭВМ, встроенной в устройство ЧПУ типа CNC. При этом механические устройства станка работают аналогично графопостроителю с той разницей, что в данном случае выходом является не чертёж, а обработанная деталь или её поверхность.
На рис. 4 представлены некоторые результаты ОУО ППД плоских поверхностей направляющих скольжения, полученных с использованием управляющих программ (УП). Микрорельефы 1 – 3 реализованы с использованием центрального индентора I марки АСПК (рис. 4а), а 4, 5 – с использованием периферийного шарикового индентора III (рис. 4а) в технологических системах повышенной технологической гибкости на базе станка FQW-400 с СЧПУ типа CNC – H646.
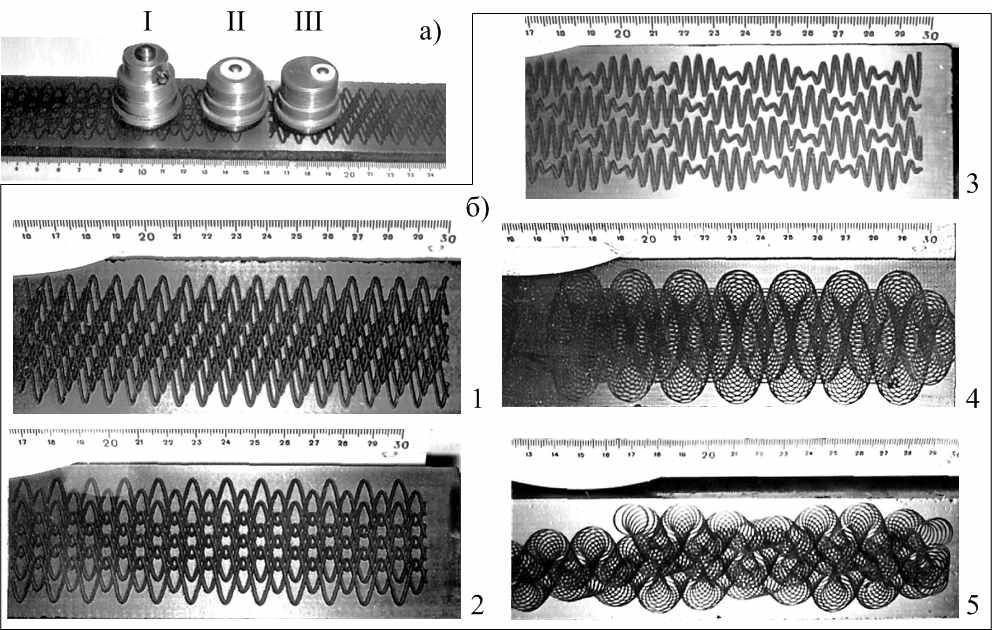
Рис. 4. Общий вид инденторов (а) и фрагменты топографий поверхностей
с микрорельефами, полученных ОУО ППД программным способом (б)
Во всех программах предусматривается управление величиной подачи и перемещения Z, т. е. силой воздействия индентора на поверхность. Таким образом, реализуется возможность управления плотностью обработки, степенью и глубиной наклёпа по поверхности, т. е. возможность её адаптации в процессе обработки к переменным условиям эксплуатации с целью обеспечения постоянства показателей эксплуатационных свойств.
В настоящее время технологическое обеспечение качества обрабатываемых поверхностей во многом базируется на использовании физико-статистических моделей, связывающих параметры качества с условиями обработки [3 и др.]. Например, для ОУО ППД такая модель может иметь вид
Ri =
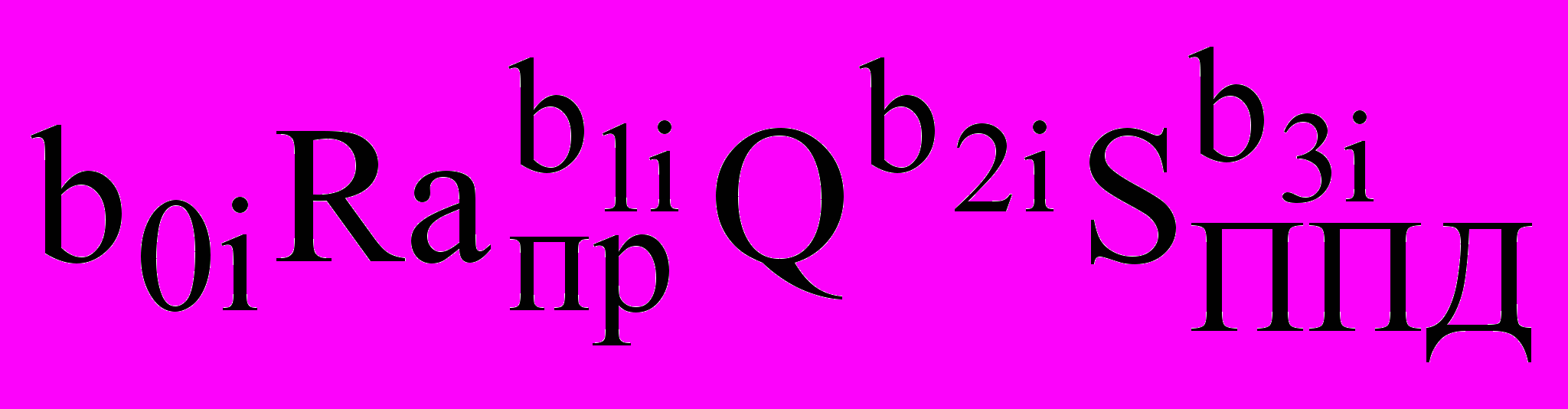
где Ri – i-й параметр качества (Ra, Rр и др.); Rапр – параметр шероховатости поверхности после предварительной обработки; Q, SППД – сила вдавливания и подача индентора при ОУО ППД соответственно; b0i …b3i – соответствующие коэффициенты модели.
Возможность управления параметром Ra после ППД (при необходимости) наиболее эффективно достигается за счёт силы Q, которая определяется в этом случае из выражения (1) в виде
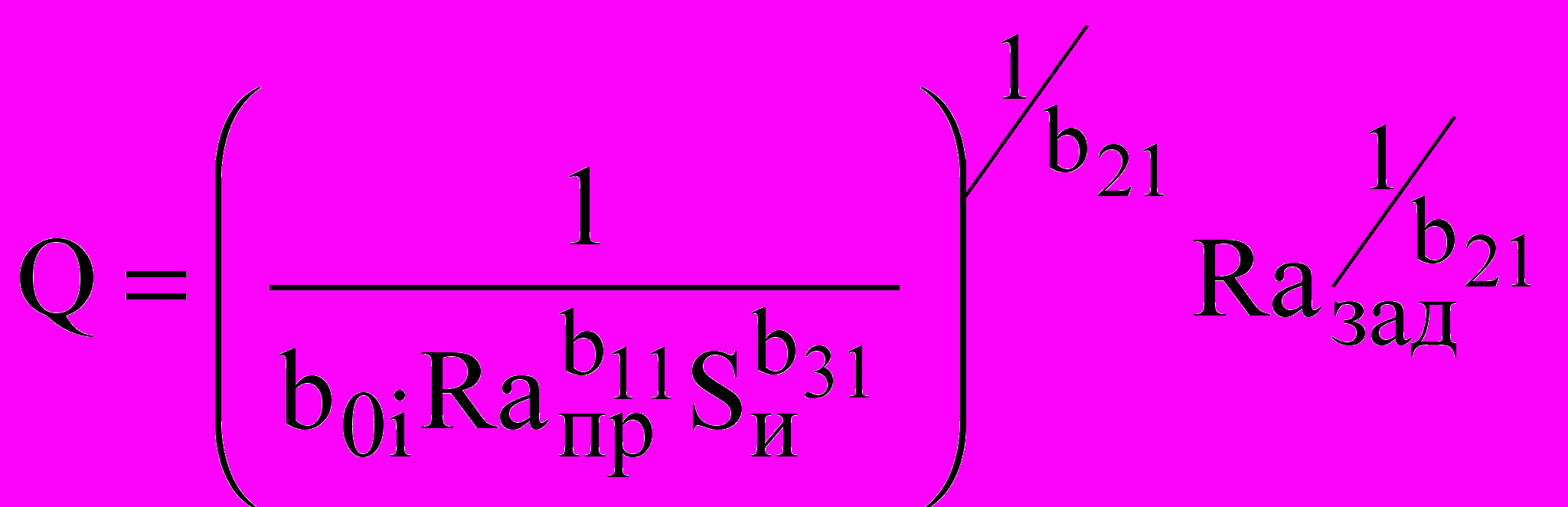
Если заданная величина Raзад является, например, функцией от длины обрабатываемой поверхности и для каждого участка хi должна составлять Ra(xi), то сила воздействия индентора Q на участке хi составит

где
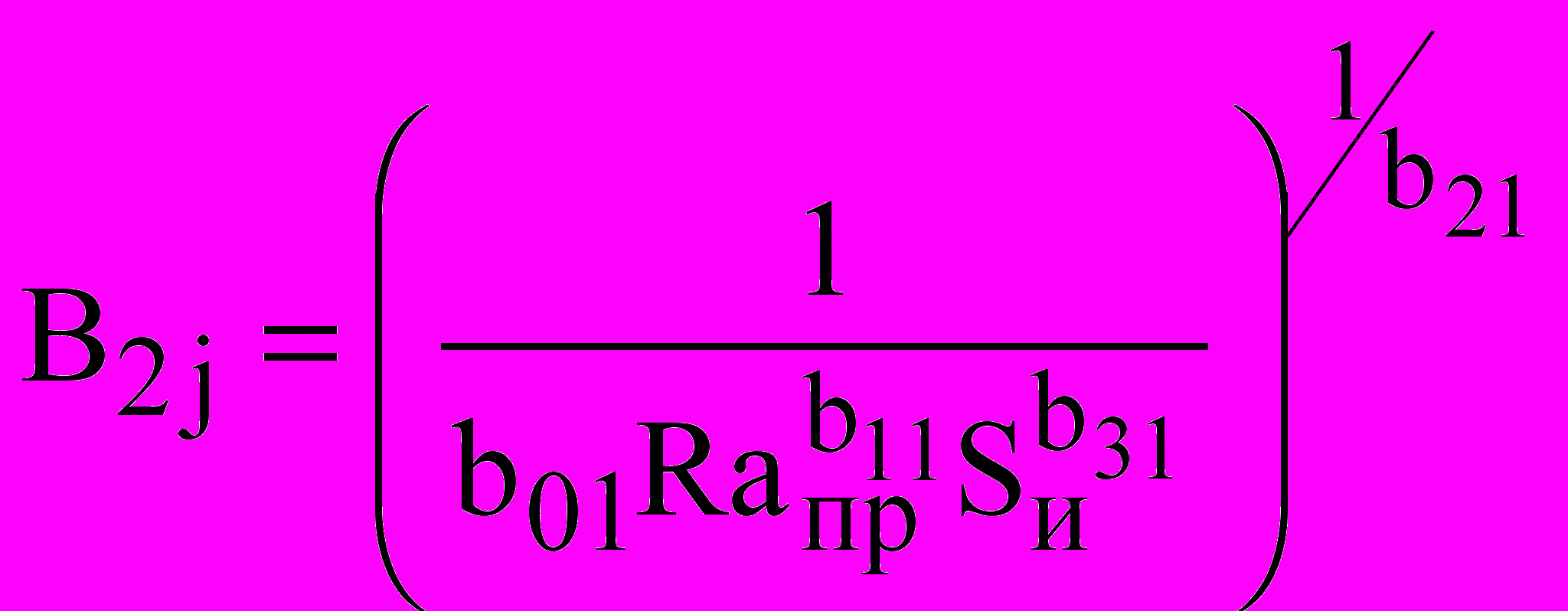
Величина B2j определяется для какого-то одного из возможных методов ОУО ППД. Значения коэффициентов b01, …, bn берутся из справочных данных, полученных методом экспресс-анализа [1] конкретной системы ОУО ППД.
Если устройство ППД упругого действия установлено по оси Z, то вместо расчёта потребной силы Q (xi) по формуле (2) целесообразно рассчитывать сразу величину необходимого перемещения по оси Z для каждого из i участков обрабатываемой поверхности:
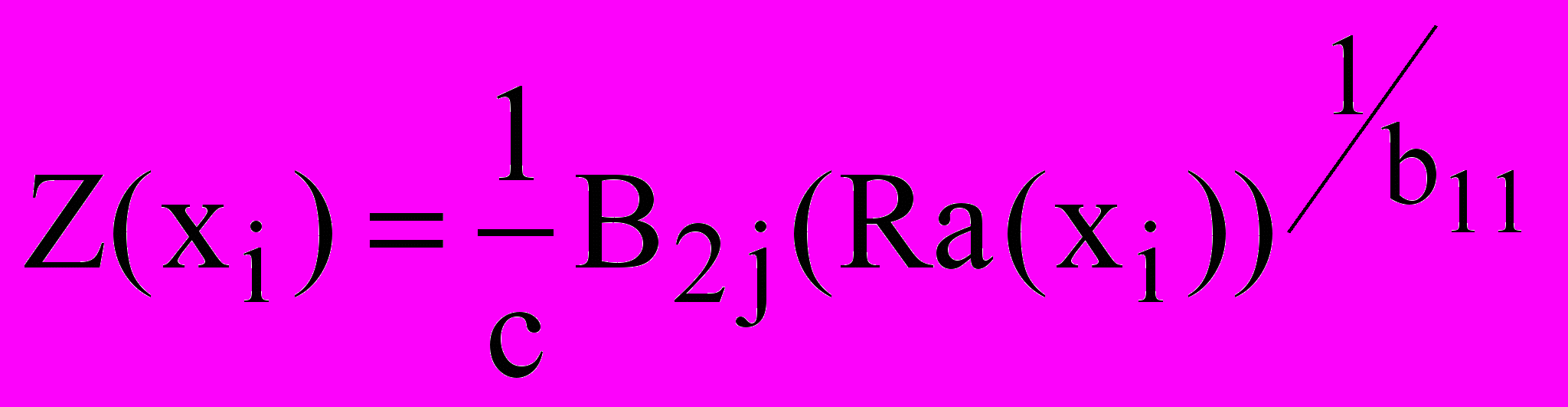
Здесь с – жёсткость пружины устройства упругого действия для обработки ППД.
Возможно управление параметром Ra(xi) за счёт технологической наследственности. В этом случае шероховатость предварительно обработанной поверхности на i-м участке должна составлять

Здесь
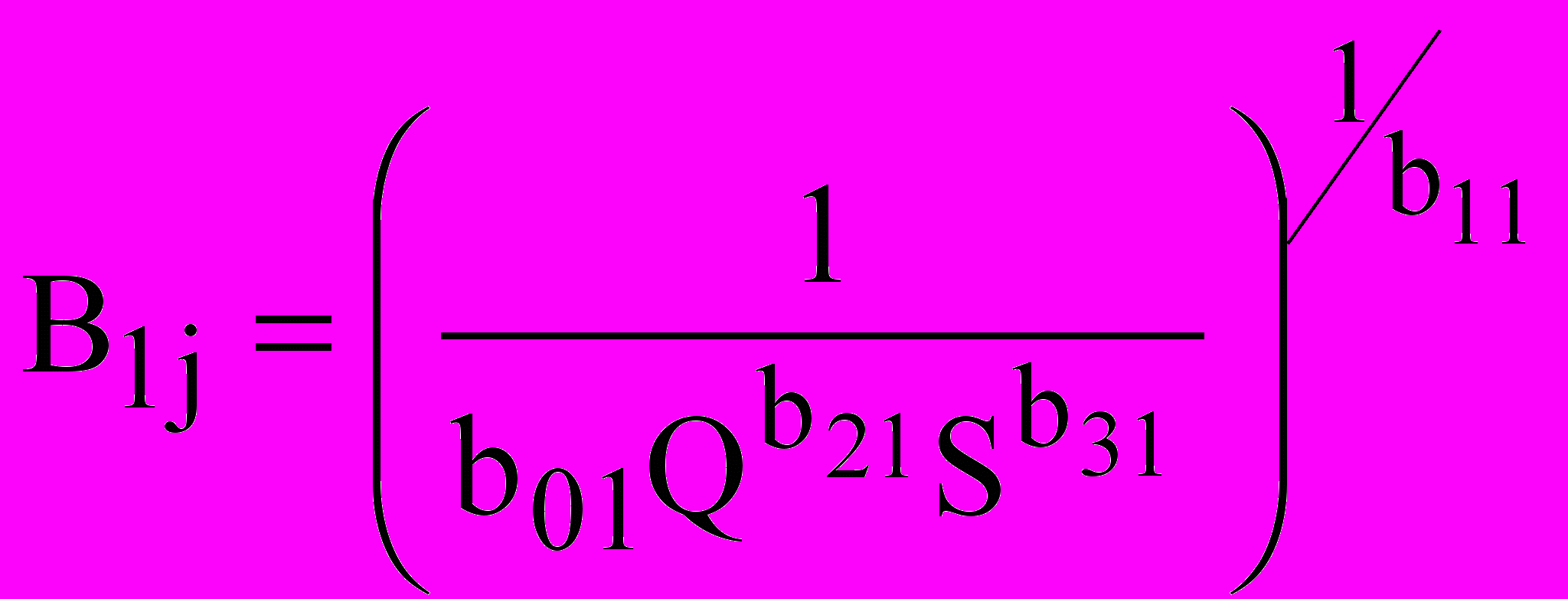
Обеспечение Raпр = f(x) достигается на стадии предварительной обработки путём программирования необходимой подачи на соответствующих участках обработки xi.
Технологическое обеспечение закономерно изменяющегося качества поверхности деталей машин тесно связано со сменой поколений металлорежущих станков, которая существенно меняет структуру, архитектуру и математическое обеспечение систем ЧПУ. Причины состоят в увеличении разнообразия функций оборудования, росте привлекательности систем ЧПУ типа PCNC в связи с множеством их преимуществ. Многолетний опыт использования предприятиями промышленного оборудования показывает, что моральное старение в 90% случаев относится прежде всего к электрической и электронной частям, а именно к электродвигателям, электроприводам, датчикам и системам числового программного управления. Механическая часть станков (станина, суппорты, шпиндельные бабки, ходовые винты и пр.) может быть при этом вполне работоспособной. Поэтому если предприятие заинтересовано в действительно эффективном и вместе с тем экономичном вложении средств, то оптимальным вариантом решения проблемы является модернизация имеющегося оборудования с целью повышения его технологической гибкости. В современных условиях такой подход оказывается экономически выгодным в сравнении с приобретением нового оборудования.
Для модернизации оборудования приемлемым вариантом является использование обычного ПК в качестве программного УЧПУ. Данный способ всё больше применяется как небольшими предприятиями, так и производителями станков. Основными проблемами при создании программного УЧПУ являются отсутствие специализированного пульта управления станком и необходимость защиты ПК для работы в промышленных условиях. Программное УЧПУ можно успешно использовать для управления шаговыми двигателями (ШД), так как управление осуществляется через имеющийся порт LPT (рис. 5). Приводы подач легко модернизировать путём установки силового шагового привода, что требует минимальных конструктивных доработок, касающихся сопряжения валов силовых ШД и редукторов приводов подач.
В

Рис. 5. Варианты работы программных УЧПУ
качестве программного обеспечения целесообразно использовать программные контроллеры (например, ЕМС2). EMC (the Enhanced Machine Controller) – это система программ для управления станками, роботами и другим технологическим оборудованием с бесплатным программным обеспечением и открытым исходным кодом. ЕМС включает в себя: графический интерфейс пользователя; интерпретатор M/G-кодов (стандарт RS-274NGC); систему контроля перемещений реального времени с режимом look-ahead; возможность работы с датчиками обратной связи (ОС), сервоприводами, шаговыми приводами и иным оборудованием; возможность быстрого создания уникальной конфигурации для станка; программный контроллер электроавтоматики (PLC) с возможностью графической настройки в виде релейно-контактных схем (ladder diagram).
EMC2 включает в себя несколько программ, облегчающих процессы адаптации, настройки и диагностики состояния оборудования. Среди них программный осциллограф HALscope, логический анализатор HAL Meter, конфигуратор лестничных диаграмм программного логического контроллера (ПЛК) Classicladder и пошаговый конфигуратор (мастер создания профиля) оборудования Step Configurator.
Система управления станка с ЧПУ модели 6Р13Ф3 («Контур-2ПТ-71/3», код программирования БЦК-5) имеет следующие недостатки: интерполятор относится к классу 2,5D; программоноситель – перфолента; отсутствует память для хранения управляющих программ; шаговые приводы с гидроусилителем (ШД-5Д – гидроусилитель ЭНИМС) требуют наличия мощной гидростанции (7,5 кВт); необходимо наличие устройств для подготовки перфоленты с УП. В связи с этим была осуществлена реконструкция путём замены СЧПУ «Контур-2ПТ-71/3» на программный контроллер ЕМС2 и шагового привода с гидроусилителем на силовой гибридный шаговый привод (СШГП). В состав СШГП входят гибридные шаговые двигатели FL11OSTH201-8004A (Мкр = 28 Нм) и драйверы SMD-78 (НПО «Электропривод») В блоке SMD-78 используются дифференциальные входы для повышения помехоустойчивости и гибкости интерфейса. Блок обеспечивает два режима управления ШД: от внешнего источника и от компьютера через LPT-порт. При модернизации станка использована оригинальная плата буферизации порта и контроля электроавтоматики.
Такая модернизация станка 6Р13Ф3 реализована на кафедре «Технология машиностроения» Брянского государственного технического университета (с участием инженера А. А. Малкина). Общие материальные затраты на проведение модернизации составили около 100 тыс. руб. в ценах 2009 г. Эта сумма ушла на приобретение трёх силовых шаговых электроприводов и персонального компьютера и не учитывает зарплату персонала. При резком повышении технологической гибкости оборудования отпала необходимость использования гидростанции Г48-44 (общая мощность – 8,6 кВт, ёмкость – 200 л масла), трубопроводов для масла, гидроусилителей, стойки с ЧПУ «Контур-2ПТ-71/3», что дало экономию занимаемой площади, электроэнергии, улучшило экологические показатели участка. Реализованная в процессе модернизации станка 6Р13Ф3 система (EMC2 + силовой ШП) наряду с программированием с клавиатуры ПК позволяет осуществлять программирование с помощью CAM-систем, которые избавляют технолога-программиста от необходимости проведения математических вычислений, обеспечивают его типовыми функциями, автоматизирующими ту или иную обработку.
Используется пакет программного обеспечения Adem, который на основе моделей DEM CAM решает широкий спектр задач по формированию управляющих программ для фрезерной и других видов обработки.
Обработка заготовки на станке после модернизации осуществляется при последовательной реализации следующих этапов: 1) подготовка чертежа детали; 2) импорт в CAM-модуль; 3) создание твердотельной модели; 4) создание переходов; 5) задание места обработки переходов; 6) выбор инструмента и режимов; 7) расчет траектории движения инструмента; 8) расчет полной траектории движения инструмента; 9) конвертация языка CAM-модуля в язык СЧПУ станка; 10) коррекция УП после пробных прогонов; 11) загрузка и верификация УП в системе ЧПУ станка (EMC2); 12) тестовая обработка детали.
Трёхмерная визуализация позволяет осуществлять предварительное моделирование процесса обработки, что важно при решении задач инженерии поверхности. Открытость программного обеспечения EMC2 обеспечивает возможность его обновления через сеть Internet и возможность использования модернизированного на его основе оборудования в составе виртуальных предприятий.
В результате модернизации улучшились характеристики станка: максимальная потребляемая мощность приводов подач снизилась с 10 до 3 КВт, также снизилась потребляемая мощность системы ЧПУ; повысился общий КПД системы управления; уменьшился общий шум из-за отсутствия гидростанции; увеличился диапазон рабочих подач; улучшилась динамика перемещения осей (повысилось ускорение); повысилась безопасность работы за счёт программных ограничений перемещений и программного анализа УП перед её выполнением. Появились новые технологические возможности: перемещение осей синхронно со шпинделем (подача на оборот) за счёт использования датчика оборотов шпинделя; компенсация радиуса инструмента и его длины; ручное программирование; визуализация отработки УП (рис. 6) и отображение траекторий перемещений виртуального станка для отладки программ и получения навыков работы с ПО; использование встроенных CAM-модулей для построения 3D-профилей из растрового изображения с последующим экспортом в виде управляющей программы ЕМС; использование встроенных CAM-модулей прямого импорта 2D-чертежей из CAD-систем и преобразования в управляющую программу с заданием основных технологических параметров; использование внешних CAM-модулей, таких, как Mastercam, Adem. Это обеспечивает решение следующих задач: подготовка чертежа в CAD-системе; создание твёрдотельной модели в САМ (Adem), проектирование технологии обработки детали и создание управляющей программы в виде G-кодов; загрузка программы обработки детали в ЕМС2, настройка привязки осей к системе координат детали; обработка модели детали; плавное изменение подачи инструмента во время отработки управляющих программ. Примеры визуализации реальной обработки поверхностей при создании на них топографии с синусоидальными регулярными микрорельефами показаны на рис. 6.
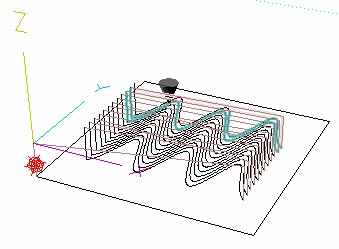
а)
б)
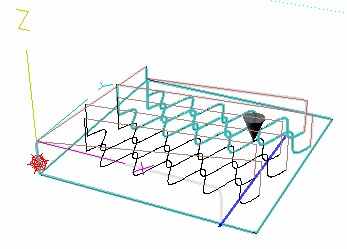
Рис. 6. Визуализация обработки поверхностей на экране монитора в системе EMC2 при создании
топографии на основе непересекающихся (а) и пересекающихся (б) синусоидальных регулярных рельефов
Описанная модернизация позволяет решать самые разнообразные технологические задачи обработки деталей машин, задачи инженерии поверхностей по обеспечению закономерного изменения их качества методами ОУО ППД. При этом на одном рабочем месте при минимальных затратах решаются задачи моделирования поверхностей, разработки и отладки управляющей программы, обработки функциональной поверхности детали и др.
СПИСОК ЛИТЕРАТУРЫ
- Инженерия поверхности деталей / А. Г. Суслов, В. Ф. Безъязычный, Ю. В. Панфилов, В. П. Фёдоров [и др.]; под ред. А. Г. Суслова. – М.: Машиностроение, 2008. – 320 с.
- Одинцов, Л. Г. Упрочнение и отделка деталей пластическим деформированием: справочник / Л. Г. Одинцов. – М.: Машиностроение, 1987. – 328 с.
- Суслов, А. Г. Технологическое обеспечение и повышение эксплуатационных свойств деталей и их соединений / А. Г. Суслов, В. П. Федоров, О. А. Горленко [и др.]; под общ. ред. А. Г. Суслова. – М.: Машиностроение, 2006. – 448 с.
- Фёдоров, В. П. Технологическая устойчивость и параметры контактного взаимодействия индентора с поверхностью при финишной обработке ППД устройствами упругого действия / В. П. Фёдоров // Инженерный журнал. Справочник. – 2006. –№ 4. – С. 4 – 8.
- Фёдоров, В. П. Управление качеством обработки поверхностей трибоэлементов в комбинированных системах повышенной технологической гибкости / В. П. Фёдоров, В. В. Нагоркина, Е. В. Ковалёва // Вестн. БГТУ. – 2006. – № 2. – С. 30-41.
- Шнейдер, Ю. Г. Технология финишной обработки давлением: справочник / Ю. Г. Шнейдер. – СПб.: Политехника, 1998. – 414 с.
Материал поступил в редколлегию 24.11.2010.