Р. А. Сагадеев современные методы возведения монолитных и
Вид материала | Учебное пособие |
- 2. Технические характеристики, 53.54kb.
- Технология возведения монолитных зданий методические указания к выполнению курсового, 647.04kb.
- Технология возведения зданий и сооружений, 39.05kb.
- Вопросы по Технологии возведения зданий и сооружений. Пгс, 61.57kb.
- Olga Chub, 75.83kb.
- Государственный стандарт РФ гост р 52086-2003 "Опалубка. Термины и определения" (принят, 720.17kb.
- Развитие теории и практических методов возведения многоэтажных монолитных жилых зданий, 627.02kb.
- Технология бетонных работ методические указания к курсовой работе по дисциплине «Технология, 636.8kb.
- Бетонирование монолитных перекрытий область применения, 401.1kb.
- «Современные методы диагностики и лечения в реаниматологии», 25.71kb.
1 2
1.4. Безбалочные монолитные перекрытия
Перекрытие представляет собой сплошную плиту, опертую непосредственно на колонны. Колонны могут быть с капителями и без капителей. Устройство капителей вызывается конструктивными соображениями. Использование капителей позволяет создать достаточную жесткость в местах сопряжения монолитной плиты с колонной, обеспечить прочность плиты на продавливание по периметру капители, уменьшить расчетный пролет безбалочной плиты и более равномерно распределить моменты по ее ширине [10].
Безбалочное перекрытие проектируют с квадратной или прямоугольной равнопролетной сеткой колонн. Отношение большего пролета к меньшему ограничивается величиной 1,5. Наиболее рациональна квадратная сетка колонн. По контуру здания безбалочная плита может опираться на несущие стены, контурные обвязки или консольно выступать за капители крайних колонн.
Для опирания безбалочной плиты на колонны в производственных зданиях применяют капители трех типов. Во всех трех типах капителей размер между пересечениями направлений скосов с нижней поверхностью плиты принимается исходя из распределения опорного давления в бетоне под углом 450.
Размеры и очертания капителей подбираются так, чтобы исключить продавливание плиты по периметру капителей. Толщину безбалочной монолитной плиты находят из условия достаточной ее жесткости.
Безбалочное перекрытие рассчитывается по методу предельного равновесия. Экспериментально установлено, что для безбалочной плиты опасными загружениями являются как полосовая нагрузка через пролет, так и сплошная по всей площади. При этих загружениях возможны две схемы расположения линейных пластических шарниров и излома плиты.
При полосовой нагрузке в предельном равновесии образуется три линейных пластических шарнира, соединяющих звенья в местах излома. В пролете пластический шарнир образуется по оси загруженных панелей и трещины раскрываются внизу. У опор пластические шарниры отстоят от осей колонн на расстоянии, зависящей от формы и размеров капителей, и трещины раскрываются вверху. В крайних панелях при свободном опирании на стену по наружному краю образуется всего два линейных шарнира – один в пролете, один у опоры вблизи первого промежуточного ряда колонн.
При сплошном загружении в средних панелях возникают взаимно перпендикулярные и параллельные рядам колонн линейные пластические шарниры с раскрытием трещин внизу, при этом каждая панель делится пластическими шарнирами на четыре звена, вращающихся вокруг опорных линейных пластических шарниров, оси которых расположены в зоне капителей обычно под углом 450 к рядам колонн. В средних панелях над опорными пластическими шарнирами трещины раскрываются только вверху, а по линиям колонн прорезают всю толщу плиты. В крайних панелях схема образования линейных пластических шарниров изменяется в зависимости от конструкции опор.
При загружении полосовой нагрузкой для случая излома отдельной полосы с образованием двух звеньев, соединенных тремя линейными шарнирами, среднюю панель рассчитывают из условия, что сумма пролетного и опорного моментов, воспринимаемых сечением плиты в пластических шарнирах, равны балочному моменту плиты.
Монолитная балочная плита армируется рулонными или плоскими сварными сетками. Пролетные моменты воспринимаются сетками, уложенными внизу, а опорные моменты – сетками, уложенными вверху.
Применяемые для армирования безбалочной плиты узкие сетки с продольной рабочей арматурой на участках, где растягивающие усилия возникают в двух направлениях, укладывают в два слоя по двум взаимно перпендикулярным направлениям. Вблизи колонн верхние сетки раздвигают, либо в сетках устраивают отверстия с установкой дополнительных стержней, компенсирующих прерванную арматуру. Капители армируют по конструктивным соображениям, главным образом для восприятия усадочных и температурных усилий.
2. Монолитные перекрытия эффективной конструктивной формы
2.1. Монолитные перекрытия кессонного типа
Кессонные перекрытия нашли широкое применение в практике строительства ряда европейских стран, в частности, в Испании, Великобритании и других странах. Здесь при строительстве административных зданий наиболее часто применяются каркасные конструктивные системы с устройством кессонных перекрытий.
Как известно, кессонное перекрытие представляет собой ребристую конструкцию с взаимно – перпендикулярно расположенными ребрами в нижней зоне (рис.5).
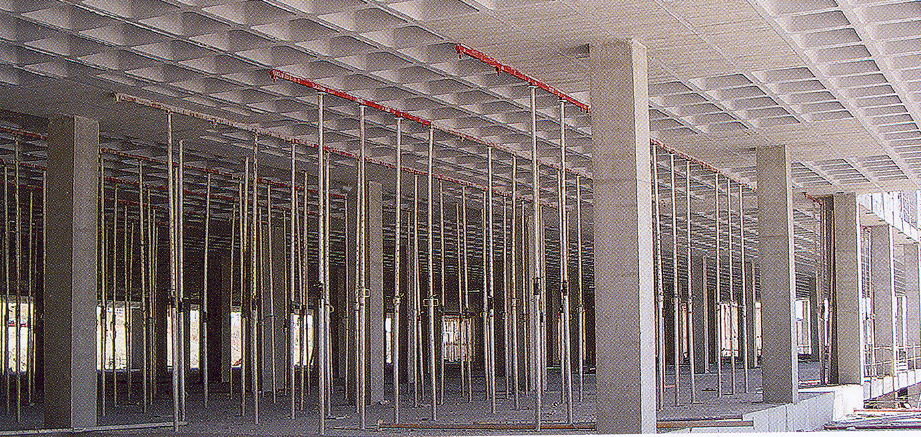
Рис.5. Монолитное перекрытие кессонного типа
В конструкции монолитного перекрытия кессонного типа бетон удален из растянутой зоны сечения, в которой сохранены лишь ребра, в которых расположена растянутая арматура. В результате удается получить значительную экономию материала по сравнению с перекрытиями сплошного сечения, либо существенно увеличить перекрываемые пролеты.
Перекрытия, возводимые испанскими строителями с применением опалубки «Альсина», представляет собой монолитную кессонную структуру, формируемую при помощи пластмассовой опалубки – пластмассовых форм размером в плане 80х74 см и высотой от 20 до 40 см. Формы располагаются на определенном расстоянии друг от друга, образуя полости для бетонирования взаимно перпендикулярных армированных монолитных балок с расстоянием по осям 80х80см. Над формами размещают арматурную сетку, покрывая поверхность форм монолитным бетоном толщиной не менее 5 см. В результате образуется монолитная железобетонная кессонная структура общей высотой 25 – 45 см в зависимости от высоты пластмассовых форм. На участке сопряжения перекрытия с монолитной колонной устраивают сплошную монолитную железобетонную плиту (рис.10).
В местах опирания элементов перекрытия на колонны растянутой является верхняя зона перекрытия, рабочая арматура располагается в верхней зоне, поэтому в местах сопряжения перекрытия с колонной устраивается сплошная монолитная плита. Таким образом, кессонное перекрытие состоит как из участков с удаленным бетоном в растянутой зоне, так и из участков, имеющих вид сплошной плиты. В кессонной части перекрытия расстояние между ребрами в осях достигает 80 см, толщина ребер меняется снизу вверх от 10 см до 20 см, толщина сплошной верхней части перекрытия составляет 5-6 см. Высота ребер варьируется от 20 см до 40 см, пустотность кессонного перекрытия достигает 50%.
Кессонные перекрытия устраивают при строительстве общественных зданий, в которых запроектированы подвесные потолки.
Для устройства кессонного перекрытия используют специальный комплект опалубки, состоящий из телескопических стоек, металлической обрешетки, располагаемой с учетом размеров пластмассовых кессоннообразователей. По обрешетке раскладывают кессоннообразователи – инвентарные формы, имеющие незначительную адгезию к бетону и легко удаляемые после набора бетоном распалубочной прочности. Кессоннообразователи имеют небольшой вес и раскладываются и снимаются вручную. Пластмассовые формы с большой точностью фиксируются на металлических прогонах (рис.6).

Рис.6. Опалубка для устройства перекрытия кессонного типа.
Испанская фирма «Альсина» производит кессоннообразователи, имеющие форму усеченной пирамиды. Размеры пирамидальных кессоннообразователей составляют в основании 80х74 см, наклон боковых граней 18%, объем равен: 82 дм3 при высоте 20 см, 99 дм3 при высоте 25 см, 118 дм3 при высоте 30 см, 127 дм3 при высоте 35 см, 137 дм3 при высоте 40 см. Учитывая объем параллелепипеда с основанием 80х80см и высотой 20 – 40 см, пустотность кессонной части перекрытия составит: при высоте 20 см и толщине перекрытия 25 см – 82/160 = 0,51 (51%), при высоте 25 см и толщине перекрытия 30 см – 99/192 = 0,52 (52%), при высоте 30 см и толщине перекрытия 35 см – 118/224 = 0,53 (53%), при высоте 35 см и толщине перекрытия 40 см – 127/256 = 0,5 (50%), при высоте 40 см и толщине перекрытия 45 см – 137/288 = 0,48 (48%).
Из представленных данных можно видеть, что в среднем пустотность кессонного перекрытия составляет 50%. Следовательно, по сравнению со сплошной монолитной плитой высота кессонной плиты может быть удвоена при одинаковом расходе бетона. Это позволяет значительно снизить расход рабочей арматуры и увеличить перекрываемые пролеты.
Последовательность устройства кессонных перекрытий практически не отличается от устройства сплошных перекрытий, за исключением особенности укладки пластмассовой опалубки. Укладка выполняется вручную с деревянного настила, разбираемого в процессе укладки пластмассовых форм. (рис.7).
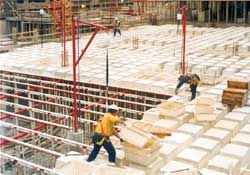
Рис.7. Раскладка пластмассовых форм по металлической обрешетке
для бетонирования кессонного перекрытия
Сравнение технико-экономических показателей, характерных для сплошной монолитной плиты и монолитного кессонного перекрытия показывает, что в результате снижения массы последнего удается увеличить толщину перекрытия с 16 до 25 см с одновременной экономией 23% бетона за счет удаления его из нижней растянутой зоны. Расход рабочей арматуры снижается на 40% (табл. 2).
Кессонное перекрытие толщиной 25 см при неизменном расходе рабочей арматуры воспринимает нормативную нагрузку 6 кН/м2 на пролете более 8 м, что позволяет уменьшить удельное количество колонн, приходящихся на единицу площади перекрытия.
Таблица 2
Технико-экономические показатели панелей перекрытий
пролетом 6 м, шириной 1,2 м, при нормативной нагрузке 6 кН/м2
Характеристика | Толщина, см | Расход бетона, м3 | Расход рабочей арматуры, кг |
Сплошная монолитная | 16,0 | 1,15 | 56,1 |
Монолитная кессонная | 25,0 | 0,88 | 33,5 |
Экономия материалов, % | - | 23,0 | 40,0 |
Увеличение перекрываемых пролетов при использовании кессонных перекрытий позволяет снизить массу несущих конструкций и уменьшить массу здания в целом.
2.2. Перекрытия с размещенными внутри полыми пластмассовыми шарами
Монолитные перекрытия кессонного типа не обладают ровной потолочной поверхностью и предполагают устройство подвесного потолка, что ведет к дополнительному расходу материалов и трудозатрат. Такого типа перекрытия не применяют при строительстве жилых зданий. Наиболее просто при возведении жилых зданий устраивать сплошные монолитные перекрытия. Однако это приводит к значительному увеличению расхода бетона и утяжелению конструкций здания.
Весьма эффективными с точки зрения снижения расхода материалов и обеспечения ровной потолочной поверхности являются перекрытия с круглыми и овальными пустотами. Однако такие перекрытия чаще бывают сборными, изготовляемыми на заводах ЖБИ. При возведении монолитных перекрытий заводская технология практически неприменима.
В мировой строительной практике есть примеры устройства монолитных перекрытий с круглыми пустотами, получаемыми путем размещения в них полимерных или картонных труб. Однако такая технология не нашла широкого применения, поскольку связана с дополнительным расходом материалов и достаточно трудоемка.
Решая проблему снижения массы монолитного перекрытия и одновременного обеспечения при его устройстве ровную потолочную поверхность, швейцарская фирма «Cobiax» разработала систему “Bublle Desk”. Перекрытие этой системы состоит из арматурных каркасов, внутри которых размещены полые шары, изготовленные из переработанного вторичного сырья - полиэтилена, и монолитного бетона, заполняющего все пространство между шарами и образующего над ними выравнивающий слой (рис.8)
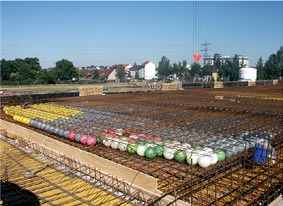
Рис.8. Устройство перекрытия по системе “Bublle Desk”
В нижней части каркасов расположены рабочие арматурные стержни, воспринимающие растягивающие усилия. В зонах пересечения перекрытия с колоннами сохраняются сплошные монолитные участки с арматурными каркасами, обеспечивающими восприятие возникающих в этих зонах максимальных усилий.
Между верхними и нижними элементами арматурного каркаса расположены полые полиэтиленовые шары, которые существенно уменьшают расход бетона. В результате облегчается конструкция перекрытия, что приводит, в свою очередь, к снижению массы этажа, который весит на 35% меньше чем эквивалентный этаж с перекрытиями из сплошного бетона. Это приводит к значительной экономии материала на здании в целом. Будучи модульной, система “Bublle Desk” может быть собрана на месте или произведена и приобретена как полуфабрикат заводского изготовления.
Достоинством предложенного решения является и значительная технологичность применения готовых модулей, изготовляемых в заводских условиях. На строительную площадку пространственные арматурные каркасы с встроенными в них пластмассовыми шарами привозят в готовом виде. Эти арматурные каркасы раскладываются на горизонтальных опалубочных настилах. Для создания защитного слоя бетона каркасы укладываются на пластмассовые фиксаторы, обеспечивающие соблюдение точного расстояния между поверхностью опалубочного настила и арматурой (рис.9).
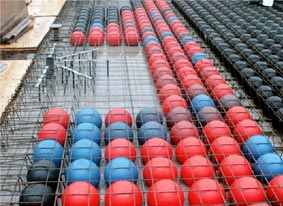
Рис. 9. Фрагмент укладки на поверхность опалубочного настила арматурных каркасов с полиэтиленовыми полыми шарами.
В местах расположения проемов в перекрытии, сопряжения перекрытий с вертикальными несущими конструкциями устраивают сплошную монолитную железобетонную плиту (рис.10).

Рис. 10. Устройство проема в перекрытии
Арматурные каркасы, располагаемые в зонах сопряжений и в местах расположения проемов, соединяются с арматурными каркасами, в которых размещены пластмассовые шары. Рабочая арматура, расположенная в нижней растянутой зоне перекрытия, также связывается с арматурным каркасом с пластмассовыми шарами.
Фирма «Cobiax» предлагает выбор между преимуществами производимых элементов заводского изготовления со своевременной поставкой и быстрым строительством, с одной стороны, и достоинствами традиционного производства работ на месте, с другой. Модульное решение “Bublle Desk” арматурного каркаса позволяет использовать стандартное оборудование и обеспечить большую часть дополнительного внутреннего заполнения, представляя несомненную альтернативу традиционного решения.
Сравнение расположения колонн в плане при традиционном методе устройства перекрытий и устройстве перекрытий по системе “Bublle Desk” показывает преимущества последнего: уменьшается количество колонн, увеличиваются перекрываемые пролеты, уменьшается расход строительных материалов (рис.11-12).
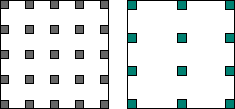
а б
Рис. 11. План расположения колонн:
а – проект с перекрытием в виде сплошной монолитной плиты,
б – проект с перекрытием системы “Bublle Desk”.
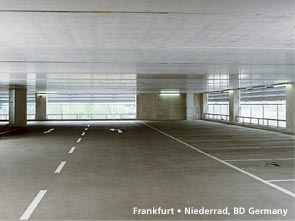
Рис. 12. Фрагмент помещения с перекрытием системы “Bublle Desk”
По данным фирмы ««Cobiax»» расход бетона на единицу площади перекрытия сокращается на 32%, экономия арматурной стали и уменьшение расхода бетона на устройство фундаментов здания составляет 20%, количество колонн уменьшается на 40%. Предлагаемая система позволяет возводить безбалочные перекрытия, в связи с чем экономия бетона на устройство прогонов и балок равна 100%, сокращение времени на устройство опалубочных работ достигает 35% (рис.13).
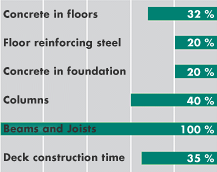
Рис. 13. Экономия материалов по сравнению
со сплошной плитой перекрытия
Производство работ по устройству перекрытия начинается как обычно с установки стоек и горизонтального настила для последующего выполнения арматурных и опалубочных работ. После раскладки арматуры и арматурных каркасов с размещенными внутри пластмассовыми шарами приступают к бетонированию перекрытия. Бетонирование перекрытия производят литой бетонной смесью, заполняющей пространство между пластмассовыми шарами и закрывающей поверхность арматуры, расположенной над шарами на толщину защитного слоя. Наиболее технологично подачу и распределение бетонной смеси выполнять при помощи бетононасоса (рис.14). Использование бетононасоса позволяет равномерно распределять бетонную смесь в полости между пластмассовыми шарами.
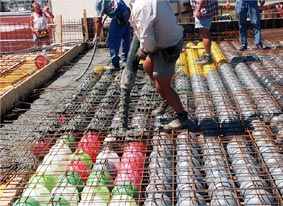
Рис. 14. Бетонирование перекрытия
Для обеспечения возможности подачи и распределения бетонной смеси по всей площади перекрытия, в том числе по его периметру, а также для снижения трудоемкости выполнения бетонных работ, строительные фирмы применяют гибкие бетоноводы, изготовленные из армированных прорезиненных шлангов из синтетических материалов. Бетонирование с применением бетононасоса дает возможность выполнять бетонирование с высокой скоростью и распределять бетонную смесь с высокой точностью. Бетонирование, как правило, выполняют захватками после выполнения арматурных и соответствующих подготовительных работ. Подвижность бетонной смеси обычно составляет 7-10см. Более подвижные смеси могут расслаиваться при перекачке, что ведет к образованию пробок. При использовании литьевой технологии и применении бетонных смесей с пластифицирующими добавками необходимо увеличивать содержание в бетонной смеси песков мелких фракций и повышать расход цемента. Например, при перекачивании бетонной смеси с суперпластификатором [11] и осадкой конуса 20-22 см расход цемента может достигать 430 кг и песка фракции мельче 0,2 мм – 200 кг.
Применение системы открывает широкие перспективы для творчества архитекторов и дизайнеров. Появляется возможность перекрывать значительные площади с размещением минимального количества опор (рис.15).
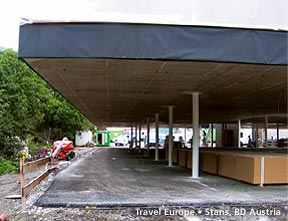
Рис. 15. Фрагмент покрытия с применением системы“Bublle Desk”
При толщине покрытия до 30 см его масса позволяет ограничиться значительно меньшим числом опорных стоек, при этом целесообразно использовать для устройства покрытия легкий бетон, например, керамзитобетон. Применение конструктивного керамзитобетона объемной массой 1700-1800 кг/м3 дает возможность снизить вес покрытия на 20-25%.
При проектировании общественных зданий, спортивных сооружений и т.п., применяя систему“Bublle Desk”, архитектор имеет возможность перекрывать большие пространства, используя нестандартные оригинальные решения (рис.16).
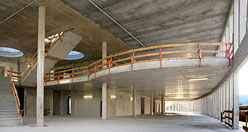
Рис.16. Возможности системы для эффективных архитектурных решений
3. Сборно-монолитные перекрытия эффективной конструктивной формы
3.1. Перекрытия кессонного типа
Сборно-монолитное перекрытие кессонного типа включает сборные пустотелые бетонные блоки размером от 0,2х0,2х0,6 м до 0,3х0,3х0,8 м и монолитный бетон. Блоки укладывают на боковую поверхность таким образом, чтобы три уложенных рядом блока образовали закрытую со всех сторон геометрическую фигуру. При использовании блоков размером 0,2х0,2х0,6 м толщина перекрытия увеличивается до 25 см: толщина слоя монолитного бетона поверх блоков составляет 5 - 6 см.
Бетонные блоки, выполняющие функцию несъемной опалубки, оставляемой в перекрытии и формирующей из монолитного бетона вертикальные ребра в растянутой зоне и сплошной настил в сжатой зоне конструкции. Перекрытие выполняется в виде сплошной монолитной плиты в надопорной зоне в местах пересечения перекрытия с колоннами. Здесь плиту дополнительно армируют стержнями, связанными с арматурой колонн. Кроме того, поверх блоков укладывают арматурную сетку, а в зоне сплошной монолитной плиты на блоки опирают концы арматурных стержней (рис.17).
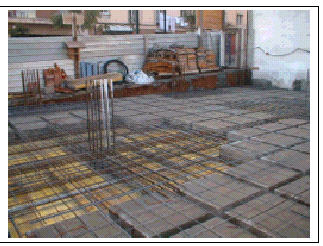
Рис. 17. Сборно-монолитное перекрытие кессонного типа
Бетонные блоки укладывают на опалубку перекрытия - деревянный настил, опирающийся на телескопические стойки, металлические или деревянные балки и обрешетку. Блоки укладывают группами на расстоянии 12-15 см друг от друга.
Сгруппированные таким образом блоки образуют полости для бетонирования вертикальных ребер в растянутой зоне перекрытия. В эти полости раскладывают рабочую арматуру – арматурные каркасы или отдельные стержни, соединенные между собой хомутами. Арматуру размещают на деревянный настил на высоте 2 см от него для образования защитного слоя бетона. В верхней зоне поверх блоков укладывают арматурную сетку, а затем укладывают бетонную смесь. Часто используют литьевую технологию с подачей бетонной смеси бетононасосом (рис.18).
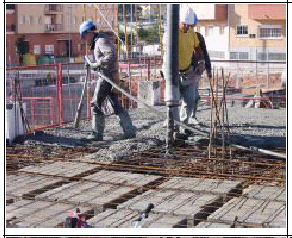
Рис.18. Бетонирование сборно-монолитного кессонного перекрытия
Применение бетононасоса для укладки смеси позволяет повысить качество заполнения монолитных ребер, расположенных между формообразующими блоками, уменьшить трудоемкость укладки бетонной смеси, повысит производительность труда рабочих. Литьевая технология, применение которой подразумевает бетонирование высокоподвижной бетонной смесью с современными пластифицирующими добавками. Уплотнение и выравнивание такой смеси требует от бетонщиков значительно меньших усилий, позволяет более качественно выполнить эти работы и обеспечить получение ровной и гладкой поверхности бетонируемого перекрытия.
На изготовление бетонных блоков размером 0,2х0,2х0,6 м и толщиной стенок 2 см затрачивается на 62% бетона меньше, а на изготовление блоков размером 0,3х0,3х0,8 м и толщине стенок 2 см – на 65% меньше, чем на полнотелый блок соответствующего размера.
Здания, возводимые во многих европейских странах, проектируют каркасными с монолитными колоннами и сборно-монолитными кессонными перекрытиями (рис.19). Такие каркасы значительно легче в сравнении с монолитными каркасами, состоящими из монолитных колонн и сплошных монолитных перекрытий.
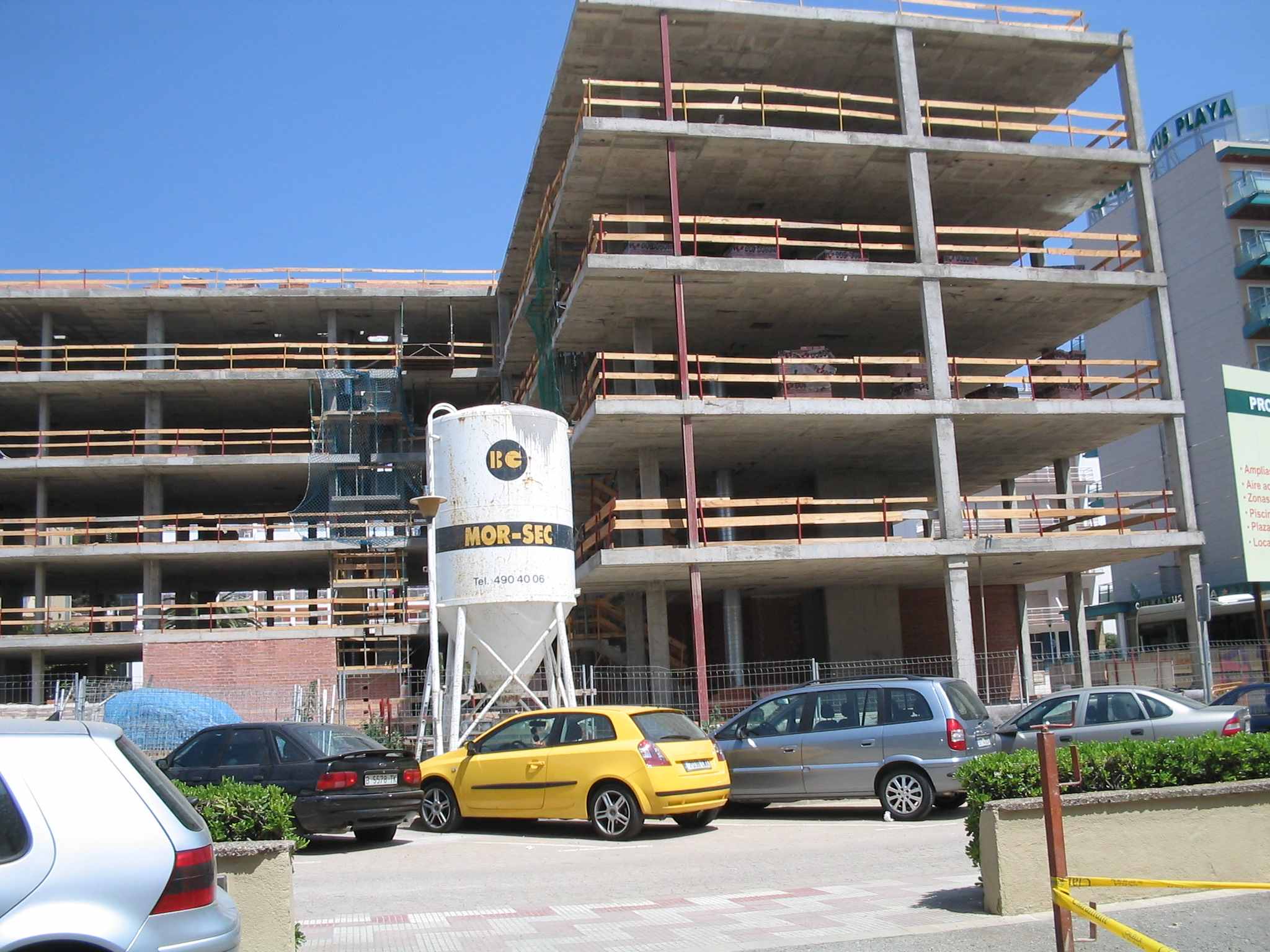
Рис.19. Каркасное здание со сборно-монолитным перекрытием
в г. Коллея (Испания)
Приведенные выше данные (табл.1) показывают, что объем бетона, затрачиваемый на устройство сплошной плиты толщиной 16 см, равна объему бетона, необходимого для устройства сборно-монолитного перекрытия толщиной 25 см. В результате площадь рабочей арматуры в растянутой зоне перекрытия уменьшается на 48,7%.
Расчет технико-экономических показателей, характеризующих расход материалов на устройство сплошных монолитных перекрытий и перекрытий сборно-монолитных с оставляемыми бетонными блоками, показывает, что при одном и том же расходе бетона на плиту длиной 6 м и одинаковой нормативной нагрузке экономия рабочей арматуры превышает 48% (табл.3).
Таблица 3
Технико-экономические показатели панелей перекрытий при
пролете 6 м, ширине 1,2 м и нормативной нагрузке 6 кН/м2
Характеристика | Толщина, см | Расход бетона, м3 | Расход рабочей арматуры, кг |
Сплошная монолитная | 16,0 | 1,15 | 45,15 |
Сборно-монолитная кессонная с бетонными блоками | 25,0 | 1,15 | 28,8 |
Экономия материалов, % | - | 0,0 | 48,7 |
3.2. Перекрытия из предварительно напряженных балок, бетонных или керамических блоков и монолитного бетона
Перекрытие состоит из предварительно напряженных Т-образных балок длиной до 9 м, изготовляемых на стендах длиной до 100 м вибрационным методом с последующей резкой алмазными дисками на элементы заданной длины, и бетонных (керамических) блоков размерами до 0,7х0,25х0,25 м, опирающихся на Т-образные балки, образуя сплошной настил в нижней части перекрытия. На настил укладывают арматурную сетку и заливают бетоном, поверхность которого выравнивают под проектную отметку (рис.20).
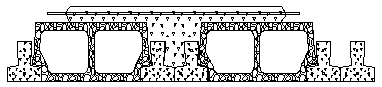
Рис.20. Сборно-монолитное перекрытие, включающее преднапряженные
ригели и блоки из мелкозернистого бетона
Такое двухслойное перекрытие из сборных элементов и монолитного бетона имеет преимущества перед традиционными решениями перекрытий из сборных многопустотных плит или сплошного монолитного перекрытия. Оно обладает достоинствами как сборного, так и монолитного вариантов: экономный расход бетона, отсутствие опалубки для бетонирования перекрытия, применение предварительно напряженных балок в нижней зоне конструкции, возможность получения из монолитного бетона гладкой высококачественной поверхности перекрытия, готовой для устройства чистых полов.
В последние годы повысилось внимание к экологически чистым материалам, позволяющим создать более комфортные условия в процессе эксплуатации зданий. Традиционно привлекательным для строительства зданий материалом является керамика. В мировой строительной практике возросло число зданий, возведенных с применением керамических блоков, причем керамические пустотелые блоки используются как для возведения стен, так и при устройстве сборно-монолитных перекрытий.
Такие перекрытия включают сборные железобетонные предварительно напряженные балки, керамические пустотелые блоки и монолитный бетон, армированный металлической сеткой из проволоки диаметром 5-6- мм (рис.21).

Рис. 21. Легкая конструкция сборно-монолитного перекрытия, включающая
железобетонные балки и керамические блоки
Керамические блоки, например, размером 40х20х20 см с пустотами, снижающими объем блока на 50-55 %, изготовляют по стандартной технологии на кирпичных заводах. Перспективно применение поризованных керамических блоков: поризация позволяет снизить массу блока на 10-15%.
Таким образом, объемная масса блока снижается до 1200 - 1100 кг/м3. В общем объеме плиты перекрытия на долю керамических блоков приходится до 65% объема. В результате масса перекрытия с заполнением керамическими блоками ниже массы перекрытия с заполнением бетонными блоками на 25-30%. Это позволяет существенно увеличить величину пролета, перекрываемую такой конструкцией.
Учитывая, что длина несущих балок, изготовляемых на длинных стендах методом непрерывного формования с последующей из резкой, достигает 12-15 м, снижение массы перекрытия позволяет уменьшить расход строительных материалов на все основные несущие конструкции здания.
Устройство сборно-монолитных перекрытий с заполнением бетонными или керамическими блоками заключается в монтаже сначала железобетонных предварительно напряженных балок, которые опираются на несущие элементы: стены или главные балки.
В тех случаях, когда главные балки изготовляются монолитными, железобетонные предварительно напряженные балки временно опираются на опалубку, которая служит для бетонирования главных балок. Торцы второстепенных балок закрепляют к предварительно установленной арматуре главных балок. (рис.22).
Монтаж выполняют с помощью легкого крана, расположенного на уровне перекрытия или автокраном. Как правило, работу выполняют два - три монтажника.
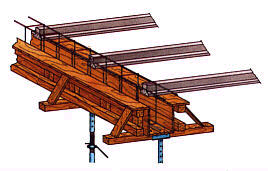
Рис.22. Временное опирание ригелей на опалубку
По окончании монтажа железобетонных предварительно напряженных балок на них укладывают керамические (бетонные) блоки, опирая их специальными выступами на полки несущих балок (рис.23).
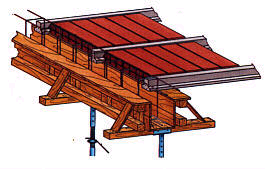
Рис.23. Уложенные керамические блоки
После того, как блоками заполнено все пространство между несущими балками и завершен монтаж сборных элементов перекрытия, приступают к процессу их объединения в единую монолитную конструкцию. Для этого вначале поверх смонтированных сборных элементов укладывают арматурную металлическую сетку с наложением ее на арматуру в торце перекрытия (рис.24).
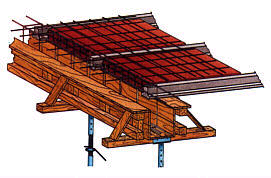
Рис.24. Размещение арматурной сетки поверх сборных элементов
Таким образом плоскость сборной части перекрытия готова к укладке бетонной смеси. Как правило, используют литую бетонную смесь с осадкой конуса 12 -15 см. Подачу смеси выполняют либо с помощью бадьи и крана, либо бетононасосом. Монолитный бетон укладывают толщиной не менее 6 см поверх сборных элементов, бетонируя при необходимости и монолитные главные балки (рис.25).
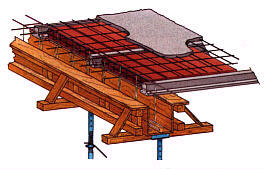
Рис.25. Монолитный бетон, укладываемый поверх сборных элементов
Тщательное выравнивание поверхности монолитного бетона позволяет получить гладкую поверхность, готовую для устройства чистого пола. После набора проектной прочности бетон объединяет сборные элементы перекрытия в монолитную конструкцию, работающую в период эксплуатации как единая система. Предварительно напряженные балки с арматурой из высокопрочной проволоки, расположенные в нижней части конструкции, воспринимают растягивающие напряжения. Монолитный бетон расположен в верхней части и работает на сжатие. Такие перекрытия чаще устраивают при строительстве малоэтажных жилых зданий, коттеджей, небольших общественных зданий.
3.3. Вентилируемые перекрытия
Перекрытия над подвалом и над последним этажом целесообразно устраивать с пассивной или активной вентиляцией. Это связано с решением вопроса снижения проникновения в помещения вредных газов, в частности, газа радон [7].
Радон – канцерогенный тяжелый газ (в 7,5 раз тяжелее воздуха), не имеет вкуса и запаха, является естественным источником радиации и находится в окружающей среде. Радон вместе со своими продуктами радиационного распада ответственен за 75% годовой эффективной эквивалентной дозы облучения, получаемый людьми от земных источников радиации. Большую часть этой дозы человек получает от радионуклидов, попадающих в его организм вместе с вдыхаемым воздухом, особенно в непроветриваемых помещениях.
Радон высвобождается из земной коры повсеместно, но его концентрация в наружном воздухе существенно различается для разных районов земного шара. Но в любых странах основную часть облучения от радона человек получает, находясь в закрытом помещении. В зонах с умеренным климатом концентрация радона в закрытых помещениях в среднем примерно в 8 раз выше, чем в наружном воздухе.
Радон концентрируется в воздухе внутри помещений лишь тогда, когда они в достаточной мере изолированы от внешней среды. Просачиваясь внутрь помещений через фундамент и пол, радон накапливается внутри здания, увеличивая риск возникновения рака легких.
Исследования, проведенные учеными во многих европейских странах и в США, показали, что просачивающийся сквозь пол радон представляет собой главный источник радиоактивного облучения людей в закрытых помещениях. Концентрация радона в верхних этажах многоэтажных домов, как правило, ниже, чем на первом этаже. Скорость проникновения исходящего из земли радона в помещения фактически определяется толщиной и целостностью (количеством трещин и микротрещин) междуэтажных перекрытий. Этот вывод подтвердился, например, при инспекции домов, построенных на регенерированных после добычи фосфатов землях во Флориде, а в домах с земляными подвалами, стоящих прямо на земле в Чикаго, были зарегистрированы концентрации радона в 100 раз превышающие его средний уровень в наружном воздухе, хотя удельная радиоактивность грунта была самая обычная. В Хельсинки максимальные концентрации радона, более чем в 5000 раз превосходящие его среднюю концентрацию в наружном воздухе, были обнаружены в домах, где единственным его источником мог быть только грунт. Здания с уровнем радиации, в 500 раз превышающими типичные значения в наружном воздухе, были обнаружены в Великобритании и США.
К значительному повышению концентрации радона внутри помещения могут привести меры, направленные на экономию энергии. При герметизации помещений и отсутствии проветривания скорость вентилирования помещения уменьшается. Это позволяет сохранить тепло, но приводит к увеличению содержания радона в воздухе. Особенно это касается Швеции, где дома герметизируются особенно тщательно. Долгие годы считалось, что в этой стране не существует проблем, связанных с чрезмерным содержанием радона внутри зданий. Однако в дальнейшем выяснилось, что на каждый гигаватт-год электроэнергии, сэкономленной благодаря герметизации помещений, шведы получают дополнительную дозу облучения в 5600 чел.-Зв.
Итальянская фирма «Понтароло Инжиниринг» разработало конструкцию вентилируемого перекрытия, существенно снижающего риск проникновения в здание вредных газов, и прежде всего, газа радон. Предложенная конструкция позволяет аккумулировать проникающий сквозь фундамент и подвальный этаж газ и удалять его из перекрытия.
Вентилируемое перекрытие представляет собой разновидность кессонного перекрытия, в котором кессоннообразующие элементы - пластмассовые короба соединены между собой в единую систему (рис. 26).
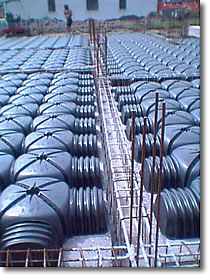
Рис.26. Пластмассовые элементы вентилируемого перекрытия
Они выполняют роль формообразующих вкладышей, заполняющих значительное пространство конструкции перекрытия и формирующих кессонную структуру. Они обеспечивают вентиляцию перекрытия, являясь сообщающейся системой, аккумулирующей газы для их последующего удаления из конструкции.
Если устраивается опорное вентилируемое перекрытие пола цокольного этажа, пластмассовые элементы раскладывают непосредственно на выровненной грунтовой площадке (рис. 27).
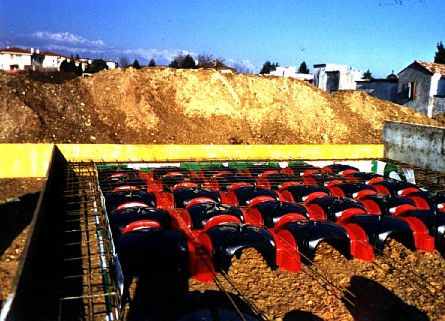
Рис.27. Опорное вентилируемое перекрытие пола цокольного этажа
Если устраивается вентилируемое перекрытие над подвалом или над последним этажом здания, пластмассовые элементы - вкладыши раскладываются на поверхности опалубочных щитов. Все пластмассовые элементы – вкладыши герметично соединяют между собой пластмассовыми соединительными патрубками, в результате создается вентилируемое пространство внутри плиты перекрытия. Между пластмассовыми вкладышами размещается арматура, чаще в виде арматурных каркасов, объединенных между собой хомутами. После выполнения опалубочных и арматурных работ осуществляют контроль герметичности вентилируемого пространства и приступают к подготовке к бетонированию конструкции (рис. 28)
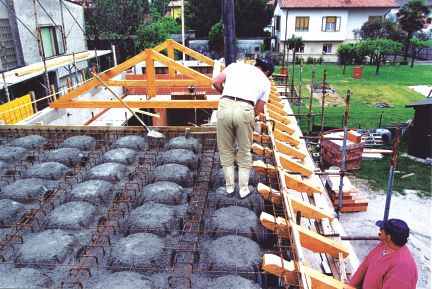
Рис. 28. Устройство вентилируемого перекрытия над последним этажом
Бетонирование конструкции выполняют высокоподвижной или литой бетонной смесью, подавая смесь краном или бетононасосом (рис.29).
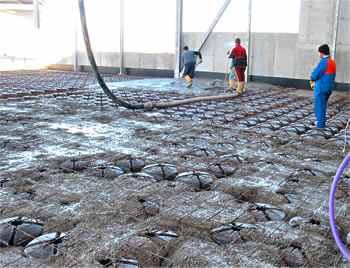
Рис.29. Бетонирование вентилируемого перекрытия
с помощью бетононасоса
Вентилируемое перекрытие функционирует как эффективная пассивная вентиляционная система.
Как известно, существуют активные и пассивные вентиляционные системы. Активные системы используют механические устройства для удаления загрязненного воздуха и подачи чистого воздуха с целью удаления вредного газа. В эффективной пассивной системе используется потенциал естественного движения воздуха. Эффективная пассивная система включает три компонента: проницаемый вентиляционный слой, клапаны по периметру перекрытия, газовые мембраны.
В процессе эксплуатации вентилируемого перекрытия вредные газы, включая газ радон, попадают из грунта или окружающего воздуха через проницаемый вентиляционный слой в вентиляционное пространство, расположенное внутри перекрытия. Вентиляционное пространство, образованное соединенными между собой пластмассовыми элементами, аккумулирует вредные газы, которые в дальнейшем удаляются из перекрытия через вентиляционные трубы, сообщающимися с окружающей средой
(рис. 30).
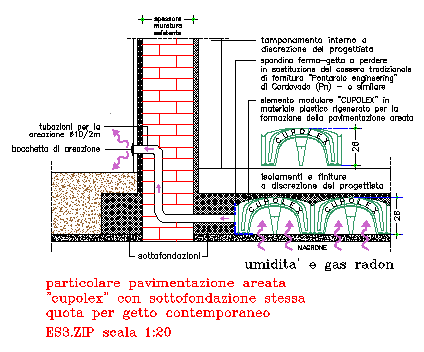
Рис.30. Процесс удаления вредных газов из вентилируемого перекрытия
При разработке эффективной пассивной системы принимают во внимание следующие факторы:
- направление движения воздуха, которое будет использоваться в работе системы,
- скорость и доминирующее направление ветра,
- опасность удаляемого газа с учетом его концентрации за определенный промежуток времени (например, разрешенная концентрация взрывоопасного газа метан под зданием школы равна 1%)
Вентилируемые перекрытия нашли широкое применение при строительстве зданий в Италии и других европейских странах. Применение вентилируемых перекрытий позволяет комплексно решать ряд экономических и экологических проблем:
1. Улучшаются условия пребывания людей в помещениях, создается более комфортная среда в процессе эксплуатации зданий, снижается риск заболевания.
2. Успешно решается вопрос утилизации бытовых отходов, поскольку пластмассовые элементы, используемые при устройстве вентилируемых перекрытий, изготовляются из отходов бытовой тары.
3. Возводятся облегченные кессонные перекрытия, позволяющие снизить массу самой конструкции и массу здания в целом.
Литература
1. Бетонные и железобетонные работы. М., Стройиздат, 1987.
2. Байков В.Н., Сигалов Э.Е. Железобетонные конструкции. М. Стройиздат, 1986.
3. Вильман Ю.А. Технология строительных процессов и возведения зданий. Современные прогрессивные методы. М., Ассоциация строительных вузов. 2008.
4. Казаков Ю.Н., Рафальский Ю.Е. Новые зарубежные строительные технологии. Санкт-Петербург. «ДЕАН», 2007.
5. Красновский Б.М., Сагадеев Р.А. Монолитный бетон на индустриальной основе. М., 1986.
6. Михайлов К.В., Волков Ю.С. Бетон и железобетон в строительстве. М.,
Стройиздат, 1987.
7. Радиация. Дозы, эффекты, риск. Перевод с английского Банникова Ю.А. М., «Мир», 1988.
8. Рамачадран В., Фельдман Р., Бодуэн Д. Наука о бетоне. М., Стройиздат, 1986.
9. Ратинов В.Б., Розенберг Т.И. Добавки в бетон. М., Стройиздат, 1998.
10. Рекомендации по рациональному применению конструкций из монолитного бетона для жилых и общественных зданий. М., ЦНИИЭП жилища, 1993.
11. Рекомендации по применению полифункциональных модификаторов на основе суперпластификатора С-3 при изготовлении морозостойких бетонов из высокоподвижных и литых бетонных смесей. М., 1989.
12. Руководство по конструированию бетонных и железобетонных конструкций из тяжелого бетона. М., Стройиздат, 1987.
13. Сагадеев Р.А. “Строительство монолитных и сборно-монолитных зданий”. Учебное пособие. М., ГАСИС, 2005.
14. СНиП 2.03.01-84. Бетонные и железобетонные конструкции. М., 2003.
15. СНиП 3.03.01 - 87. Несущие и ограждающие конструкции. М., 2000.
16. Фоломеев А.А. Снижение материалоемкости железобетонных конструкций. М., Стройиздат, 1984.
17 . Хаютин Ю.Г. Монолитный бетон. М., Стройиздат, 1991.
18. Шмидт О.М. Опалубки для монолитного бетона. М., Стройиздат, 1997.
19. Aswad A., Tabsh W. Probablistic analysis of hollow core slabs subjected to edge loads. A.C.I., U.S.A., 2001.
20. The Hollow Core Floor Desine and Application. ASSAP, Verona-Italy, 2002.
Р. А. Сагадеев
Современные методы возведения монолитных и
сборно-монолитных перекрытий
Учебное пособие
_______________________________________________________________
Подписано к печати 5.10.2008 г. Объем 1,5 п.л. Тираж 50 экз.
_______________________________________________________________
ГОУ ДПО ГАСИС