Анализ погрешностей обработки на токарно- копировальном станке, оснащенном следящей системой с электромагнитными муфтами
Вид материала | Документы |
СодержаниеV от электродвигателя М через коробку скоростей iv |
- Программа вступительного экзамена в магистратуру элементы теории погрешностей, 51.03kb.
- Председатель Профкома Директор моу «шсош №2» Ельшаева О. А. Дитрих Л. А. 28. 08. 2009, 63.01kb.
- Оао «ижмашстанко», 78.26kb.
- Лечение электромагнитными полями, 13.15kb.
- Интеллектуальный анализ данных в системе медис-4, 39.59kb.
- Информационные устройства и системы вопросы к зачету для студентов 4 курса по дисциплине, 27.74kb.
- Информационные устройства и системы вопросы к зачету для студентов 4 курса по дисциплине, 27.36kb.
- Реферат Отчет: страниц 30; рисунков 14; таблиц 5 Тема: вопрос 1 Токарно-винторезные, 252.46kb.
- Реферат по дисциплине "Электрооборудование" на тему "Автоматические выключатели", 437.06kb.
- При измерении размеров объектов по изображениям важным вопросом является точность получаемых, 8.51kb.
К.т.н., доцент Фидаров В.Х.
ФГБОУ ВПО «Тамбовский государственный технический университет».
Кафедра «Технология машиностроения, металлорежущие станки и инструменты».
АНАЛИЗ ПОГРЕШНОСТЕЙ ОБРАБОТКИ НА ТОКАРНО- КОПИРОВАЛЬНОМ СТАНКЕ, ОСНАЩЕННОМ СЛЕДЯЩЕЙ СИСТЕМОЙ С ЭЛЕКТРОМАГНИТНЫМИ МУФТАМИ
В универсальных токарных станках резец механически может перемещаться только по прямолинейной траектории или параллельно или перпендикулярно оси шпинделя. Поэтому на таких станках при механической подаче можно обрабатывать тела вращения, имеющие ступенчатый профиль, например, ступенчатые валы.
Переключение направления перемещения резца, например в станке модели 16К20, осуществляется посредством зубчатых муфт, расположенных в фартуке станка (рисунок 1.). Муфты переключаются мнемонической рукояткой вручную.
В последнее время с целью повышения степени автоматизации станков для переключения направления подачи в фартук станка вместо зубчатых муфт стали встраивать фрикционные электромагнитные муфты, которыми можно управлять как вручную, так и автоматически (рисунок 2). Это позволяет автоматизировать цикл работы станка, расширить его технологические возможности, встраивать в автоматические линии. На таких станках уже возможно обрабатывать тела вращения сложного профиля, если их снабдить копировальным датчиком и несложной станцией управления электромагнитными муфтами, разработанной в ЭНИМСе (экспериментальный научно- исследовательский институт металлорежущих станков), что и реализовано в станках ряда станкостроительных заводов.
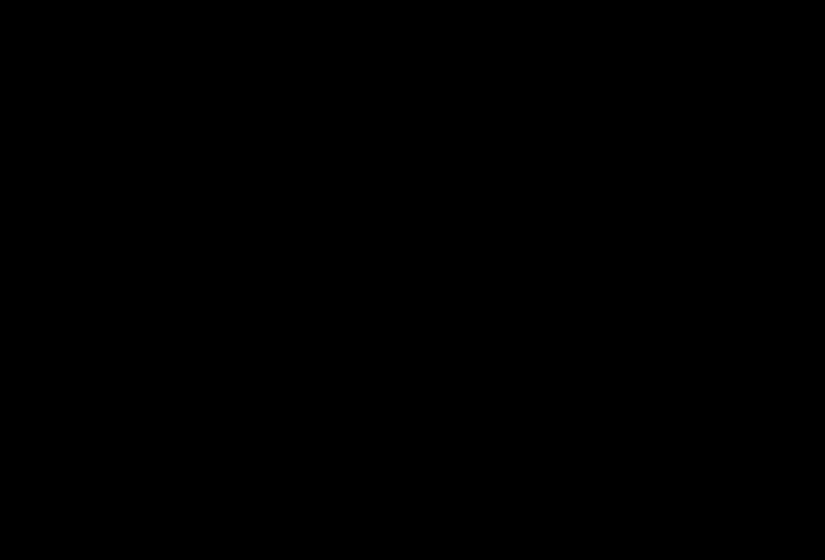
Рисунок 1. Кинематическая схема токарно- винторезного станка модели 16К20
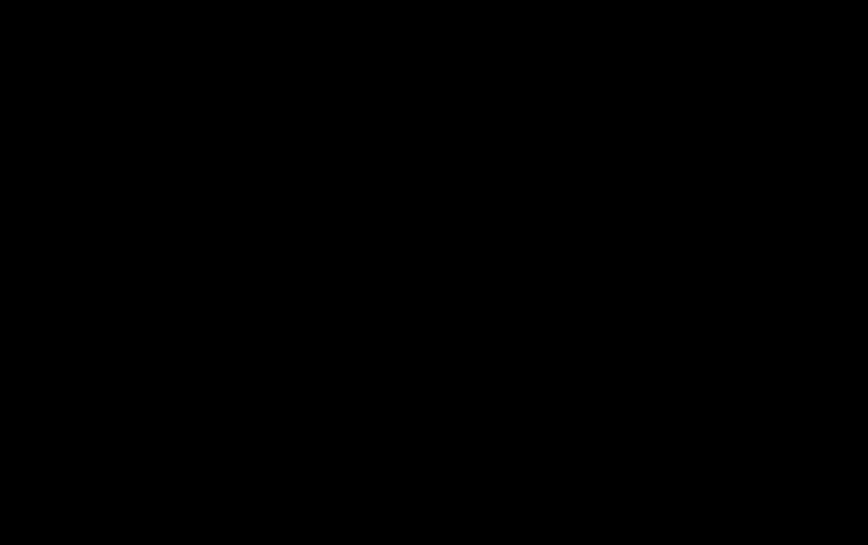
Рисунок 2. Токарно- копировальный станок модели 16К20К
Однако такие станки имеют низкую производительность при требуемой точности обработки или же неудовлетворительную точность при приемлемой производительности. Поэтому повышение точности обработки и производительности копировальной обработки станков с электромагнитными муфтами является актуальной задачей для машиностроения.
В связи с этим данная работа посвящена выявлению причин возникновения погрешностей обработки, вносимых следящей системой станка с электромагнитными муфтами.
Принципиальная схема токарно- копировального станка представлена на рисунке 3.
При токарно- копировальной обработке на заготовке воспроизводится профиль, соответствующий форме копира. Это происходит следующим образом.
Заготовке, установленной в трехкулачковом самоцентрирующем патроне сообщается вращательное движение со скоростью резания V от электродвигателя М через коробку скоростей iv и шпиндель. Суппорту сообщается движение продольной подачи с постоянной скоростью Sзад от шпинделя через коробку подач iS, механизм продольной подачи фартука и передачу «зубчатое колесо (з.к.)- рейка». Переключение направления продольной подачи осуществляется посредством включения электромагнитных муфт ЭМл (влево) и ЭМп (вправо); муфта ЭМт2 служит для осуществления быстрого торможения.
Резец крепится в резцедержателе на поперечных салазках суппорта, жестко связан с корпусом копировального датчика и перемещается в продольном направлении вместе с суппортом. Поперечные салазки вместе с резцом и копировальным датчиком могут перемещаться в поперечном
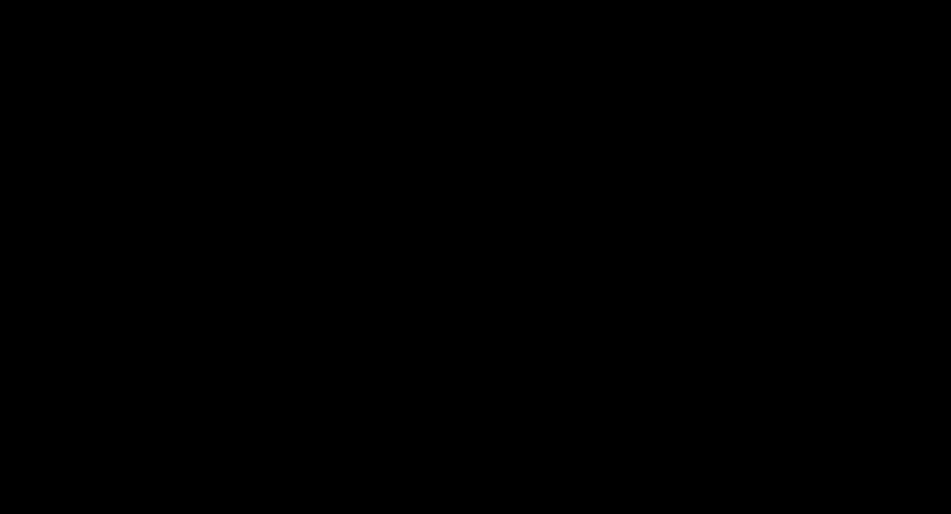
Рисунок 3. Принципиальная схема токарно- копировального станка
направлении при вращении ходового винта tх.в.. Вращение на ходовой винт передается от шпинделя через коробку подач iS и механизм фартука. При включении электромагнитной муфты ЭМв поперечные салазки с резцом и датчиком перемещаются вперед, а при включении ЭМн- назад со скоростью подачи Sсл. Электромагнитная муфта ЭМт1 необходима для торможения.
Обработка криволинейного профиля заготовки или профиля, расположенного под углом к оси шпинделя, возможна, если траектория вершины резца будет в данной точке обработки направлена по касательной к профилю заготовки, что достигается путем векторного сложения скоростей одновременно включенных подач резца в продольном Sзад и поперечном направлениях Sсл : S∑ = Sзад + Sсл , (см. рис. 4).
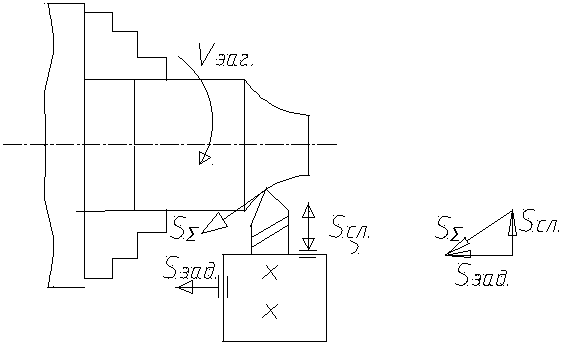
Рисунок 4. Схема обработки криволинейного контура
Однако соотношение скоростей продольной и поперечной подач при постоянном их включении строго фиксировано и не регулируется и в станке модели 16К20 составляет Sзад/Sсл=2, что будет соответствовать перемещению резца по прямой линии, наклоненной к оси шпинделя под углом α;


Рисунок 5. Методы обхода контура при копировальной обработке
а) пилообразный (траектория вершины резца образуется в результате чередования двух взаимно- перпендикулярных подач); б) диагональный (траектория резца образуется в результате чередования одной и двух одновременно включенных передач).
При первом методе аппроксимация требуемого профиля осуществляется отрезками ортогональных прямых, соответствующих перемещениям резца в продольном Sзад и поперечном Sсл направлениях (рис. 5а); во втором- когда один отрезок прямой параллелен оси шпинделя и соответствует продольному перемещению резца Sзад, а второй располагается под углом к оси шпинделя и соответствует перемещению резца при одновременном включении продольной и поперечной подач (рис. 5б).
Из двух методов более производительным является второй, диагональный.
Копировальная обработка происходит следующим образом.
Продольная, задающая, подача Sзад включена постоянно и перемещает суппорт с закрепленным на нем жестко резцом и датчиком влево. Щуп датчика под воздействием пружины все время прижимается к копиру и его траектория при обходе контура в точности соответствует профилю копира. Траектория же корпуса датчика соответствует траектории суппорта и резца, поскольку они связаны жестко. Щуп датчика в осевом направлении имеет возможность перемещаться относительно корпуса, замыкая и размыкая при этом контакты В или Н.
При движении суппорта вдоль копира влево, в зависимости от угла профиля копира корпус датчика приближается к копиру или отдаляется от него, что соответствует относительному перемещению щупа и корпуса датчика, а следовательно- замыканию контактов В или Н.
При замыкании контакта Н подается сигнал на включение подачи назад. Сигнал поступает на станцию управления электромагнитными муфтами СУМЭ, усиливается и подается на муфту ЭМн. Муфта включается и соединяет вращающуюся ведущую часть привода подач с ведомой, осуществляя следящую подачу назад.
Поперечные салазки с корпусом датчика отходят от копира, контакт Н размыкается и отключает муфту (следящую подачу назад).
Если в дальнейшем корпус датчика опять приблизится к копиру, то опять замкнется контакт Н и весь цикл повторится; если же удалится, то замкнется контакт В, включится муфта ЭМв и будет осуществляться следящая подача вперед, а все остальное будет аналогично предыдущему циклу.
Таким образом, наличие погрешности, то есть рассогласования между требуемой и фактической траекторией резца, заложено в саму идею следящей системы с электромагнитными муфтами. При появлении рассогласования между положением копира и копировального датчика система срабатывает в сторону его устранения. Величиной этого рассогласования в конечном счете и определяется точность системы. Величина же рассогласования определяется параметрами копировальной системы. Установление зависимостей между величиной рассогласования Δ и параметрами системы, а также точностью обработки является задачей данного исследования.
Так как погрешности обработки вызываются отклонениями инструмента от линии идеального профиля (задается копиром), то рассмотрим траекторию инструмента при токарно- копировальной обработке более подробно с учетом переходных процессов при включении и отключении муфт. Выбираем наиболее прогрессивную схему обхода контура- диагональную.
Поскольку любой профиль в области малых отклонений с определенной точностью аппроксимируется отрезками прямых, то для простоты рассуждений рассмотрим обработку прямого профиля, расположенного под углом к оси шпинделя и погрешности, обусловленные работой следящей системы станка (рис 6.).
Процесс обхода прямого профиля рассмотрим в координатной плоскости XOY, проходящей через вершину резца и линию требуемого идеального профиля детали ОР, задаваемого копиром.
Задающая подача включена постоянно и сообщает исполнительному органу (ИО), то есть суппорту с резцом, движение вдоль оси OX с постоянной скоростью Vx = Sзад. Следящая подача включается периодически и сообщает движение резцу вдоль оси OY.
Двигаясь вдоль оси OX, вершина резца пересечет линию идеального профиля ОР в точке О. В этот момент замыкаются контакты датчика В (см. рис. 3) и выдается команда на включение муфты ЭМв, т.е. следящей подачи вперед, но из-за инерционности системы движение резца по следящей координате (вдоль оси OY) начнется с некоторым временем запаздывания tв, за которое ИО с резцом пройдет путь Vx* tв.
В точке А начнется разгон поперечных салазок (ПС) с резцом по следящей координате OY. В процессе разгона скорость резца будет возрастать постепенно и в течение некоторого времени tδр погрешность копирования будет увеличиваться до тех пор, пока не сравняются проекции векторов скоростей задающей и следящей подач на нормаль к профилю в данной точке.
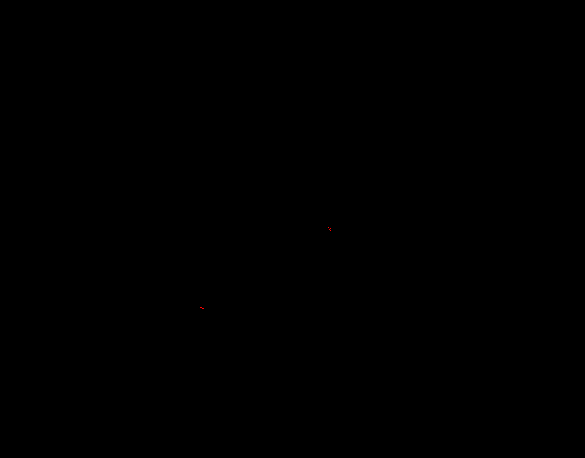
Рисунок 6. Траектория вершины резца при обходе контура.
За время tδр резец пройдет путь по оси OX- Sx= Vx* tδр, по оси OY- Sy=

где

Затем резец будет двигаться при одновременно включенных следящей и задающей подач со скоростью S∑= Sзад+ Sсл в сторону уменьшения рассогласования (погрешности) и в точке С пересечет линию идеального профиля. Здесь датчик выдаст команду на отключение следящей подачи, но из-за инерционности системы торможение ИО начнется с некоторым временем запаздывания tз . За это время резец пройдет путь по оси OX- Sx= Vx* tз; по оси OY- Sy=

В точке Д начнется процесс торможения следящей подачи по оси OY. В течение некоторого времени tδТ, пока не сравняются проекции скоростей следящей и задающей подач на нормаль к профилю, погрешность (рассогласование) будет возрастать. За время tδТ резец пройдет путь: по оси OX- Sx= Vx* tδТ, по оси OY- Sy=


Отклонения траектории вершины резца, измеренные по нормали к профилю детали в данной точке, являются динамическими погрешностями копирования. Обозначим полную погрешность через Δ, тогда
Δ= Δв + Δо,
где Δв и Δо – погрешности копирования из-за перебегов при включении и отключении следящей подачи соответственно.
В свою очередь Δв = δв + δр; Δо = δо + δт,
где δв и δо- погрешности из-за запаздываний в системе при включении и отключении следящей подачи соответственно;
δр и δт – погрешности копирования из-за инерционности процесса разгона и торможения при включении и отключении следящей подачи соответственно.
Как видно из рисунка 6
δв = OA*


δо =



При включении следящей подачи формирование погрешности δр будет происходить до тех пор, пока угол между осью OX и вектором результирующей скорости подачи

Vx*


Поскольку задающая подача в переходном процессе при включении следящей подачи увеличивает рассогласование (см. рис. 6), а следящая уменьшает, то для погрешности δр можно записать
δр = δx – δy = Vx* tδр*



При отключении следящей подачи в переходном процессе задающая подача способствует уменьшению погрешности δт , а следящая- увеличению, поэтому δт = δyт - δxт =



Время tδТ находится из соотношения
Vx*


Итак, теперь мы можем найти полную погрешность копирования, т.к. известны все его составляющие:
Δ = Δв + Δо = δв + δо +δр +δт = δв +δо +δx + δyт - δy - δxт .
Задачей дальнейших исследований является установление зависимости погрешностей копировальной обработки от статических и динамических характеристик следящей системы с электромагнитными муфтами и разработка метода оптимизации этих характеристик с целью повышения точности токарно- копировальной обработки.